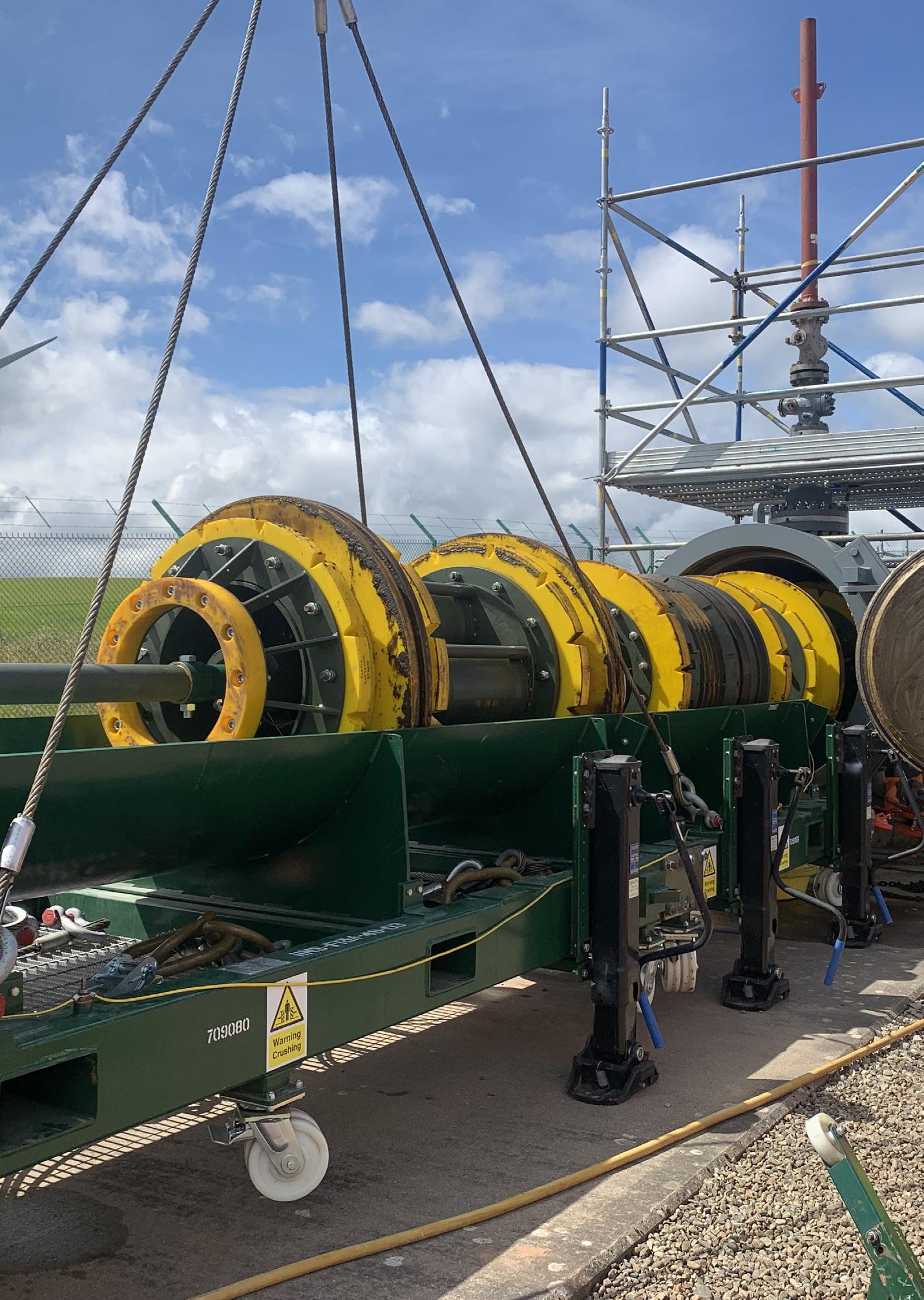
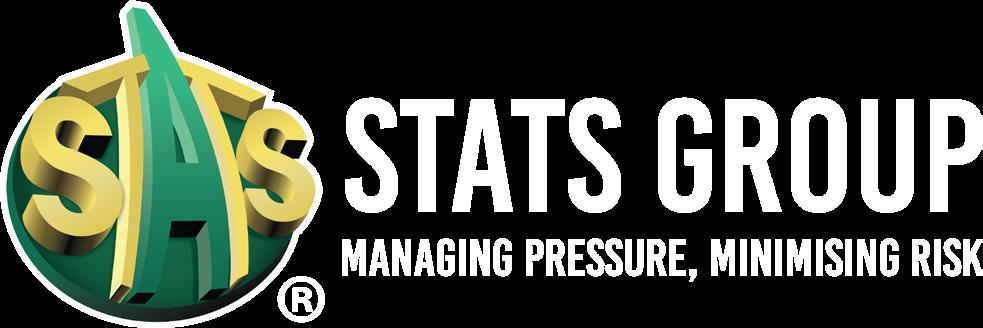
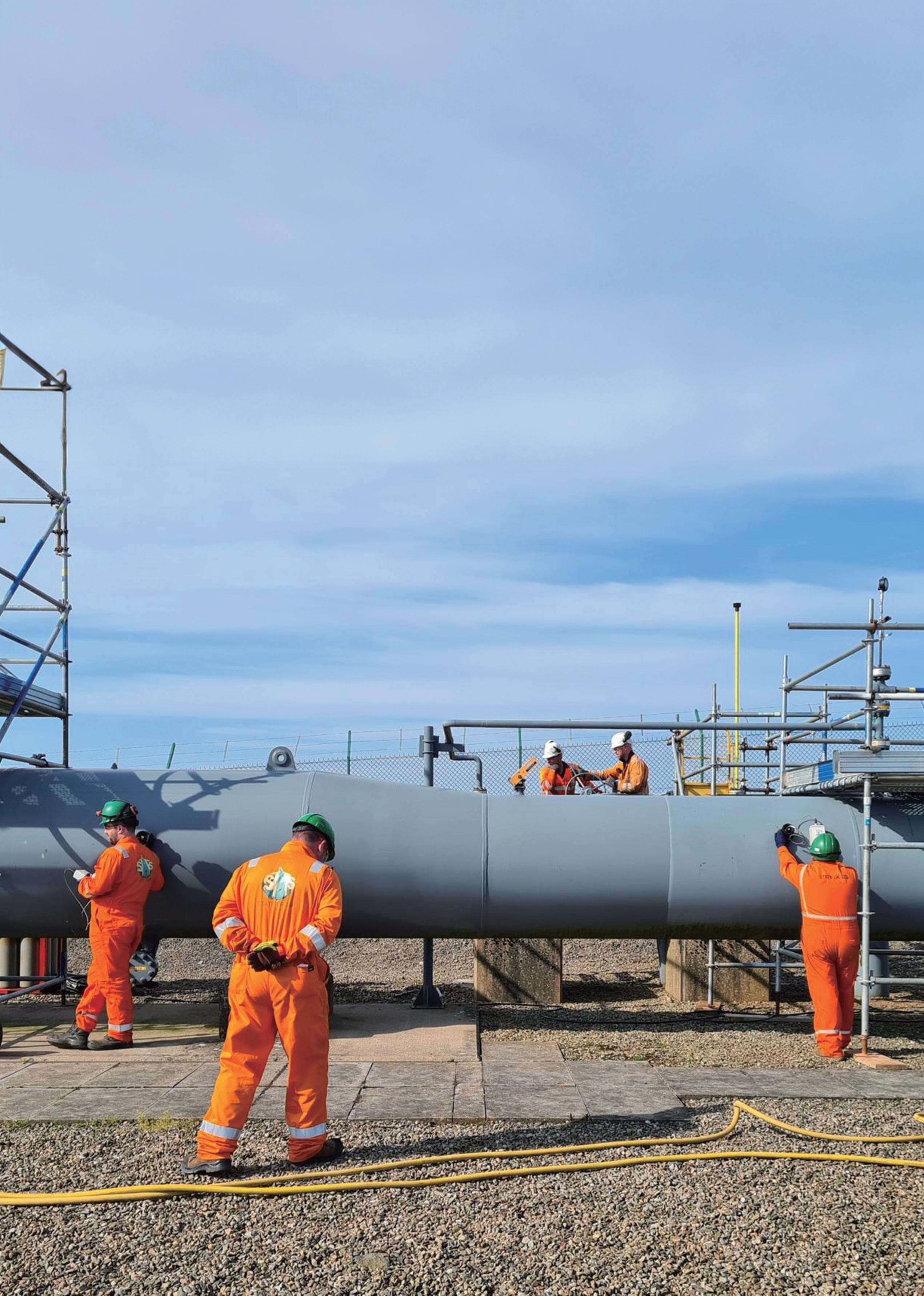
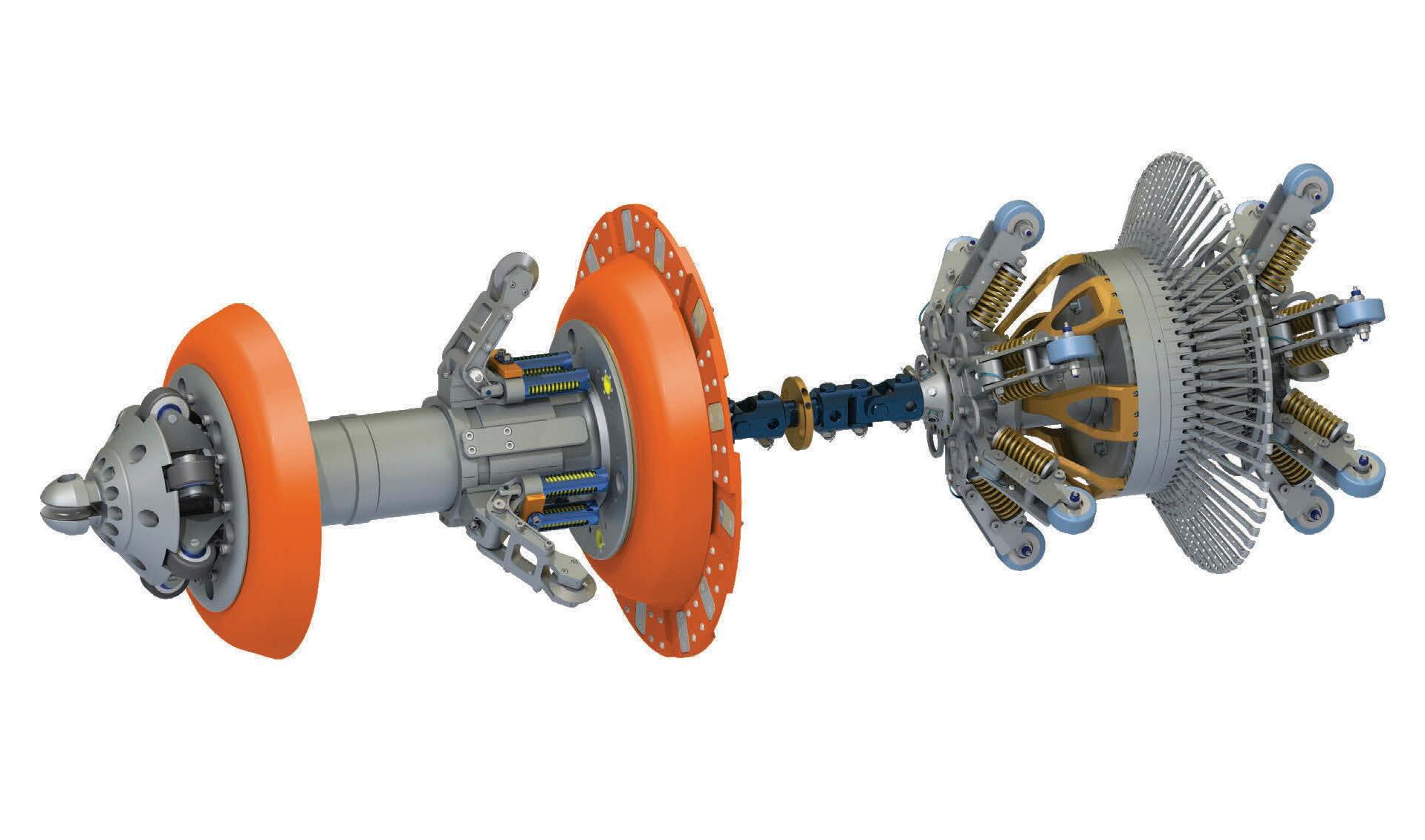

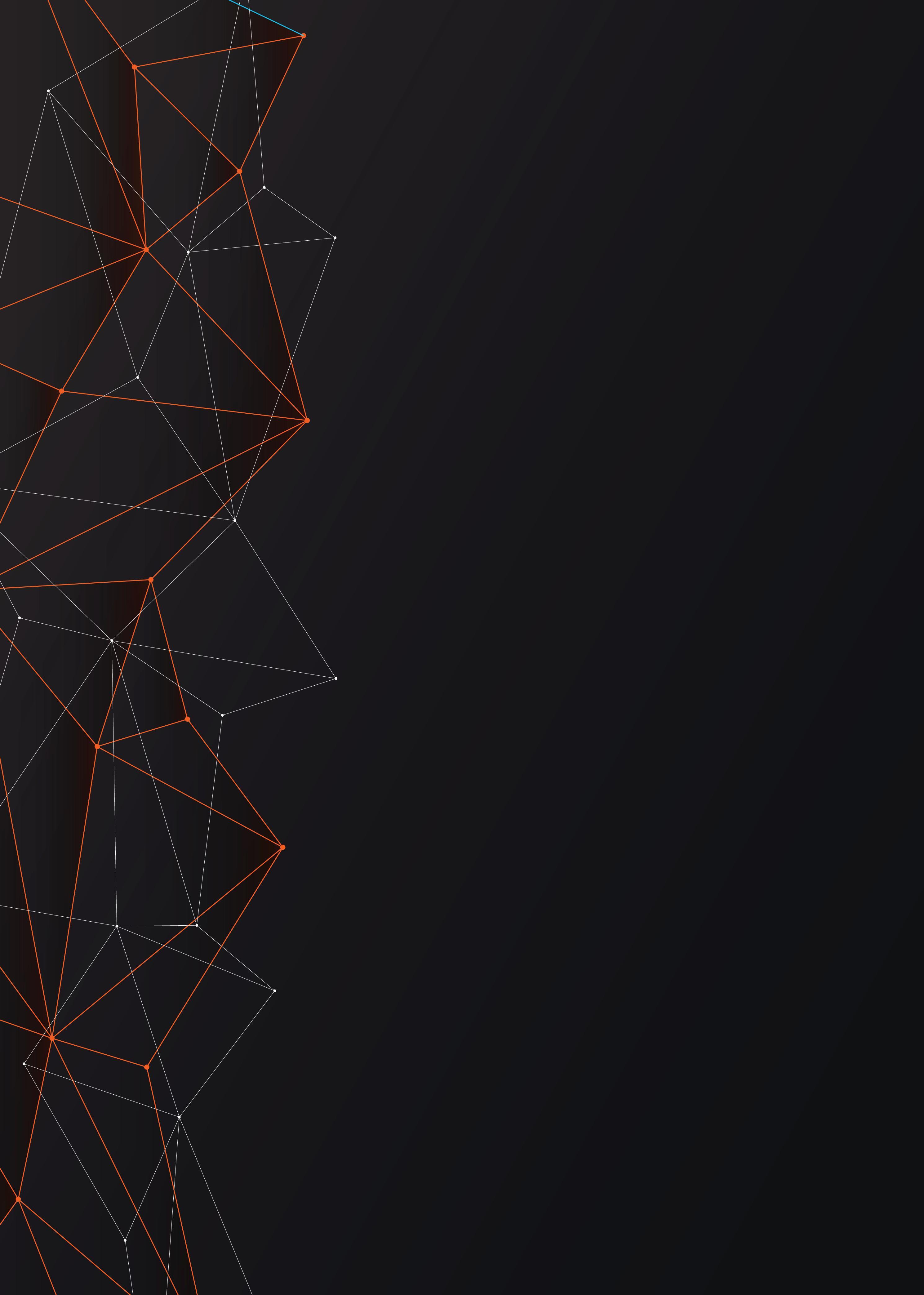
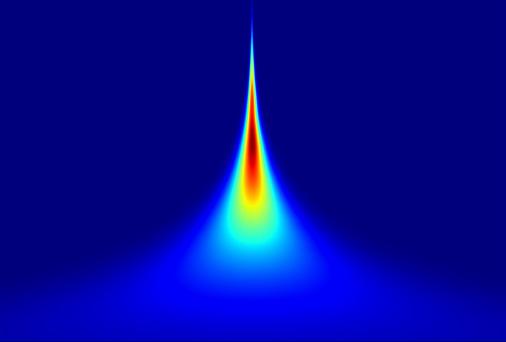
WORLD PIPELINES | VOLUME 24 | NUMBER 05 | MAY 2024
03. Editor's comment
05. Pipeline news
Contract news and updates on the Trans Mountain pipeline project and the European agreement to protect North Sea infrastructure.
KEYNOTE: ENVIRONMENT
07. Waking up to the methane problem
Mark Naples, Managing Director, Umicore Coating Services, describes spreading awareness about methane emissions and how to manage the threat through data advancements, specifically the use of gas detection technology as a critical turning point.
10. Capturing new CO2 transport solutions
Mathew Aneke, Senior Energy Transition Consultant, Penspen, UK, introduces anthropogenic CO2 pipeline systems and outlines how to effectively address the challenges they present.
15. Harnessing new technology for safety and sustainability
Josh Pendleton, Skipper NDT, France, discusses employing new technology in pipeline integrity management to ensure the continued safe and environmentally friendly delivery of energy, whilst mitigating the increasing risks of incidents to nearby environments and communities.
NDT AND PIPELINE STEELS
21. Hydrogen's butterfly effect
Martin Connelly, Technical Director, Liberty Pipes (Hartlepool) Ltd, UK.
LEAK DETECTION AND PROCESS CONTROL
28. Elevating pipeline performance with advanced AI Stuart Mitchell, President and CTO, PipeSense.
EXTREME ENVIRONMENTS
33. A collaborative effort for CGL
John Hunt, Michels Canada.
37. Productive pipe handling scenarios
Alyson Cram, Vacuworx, USA.
43. Protecting lives on pipeline sites
Andrew Vana, Manager of Specialised Services, RMI, USA.
SYSTEMS AND SOFTWARE
46. Ensuring secure access to the right data
Morgan Bowling, Seeq Corporation, USA.
COVER STORY
51. The trials of a new inline isolation tool
Kirsty McDermott, National Gas, Andy Fuller, Pipeline Integrity Engineers, Neil Mackay, STATS Group, UK, and Wes Gardner, STATS Group, Canada.
AWARD WINNERS: YPI
55. Recognising young achievement
Kah Soon Chia, ROSEN Group, and Blake Villarrubia, Audubon Engineering.
COATINGS AND CORROSION
59. Is DCVG obsolete? New shifts in corrosion detection
Markus Büchler, SGK, Switzerland, and Mark Glinka, EMPIT GmbH, Germany.
ON THIS MONTH'S COVER
Reader enquiries [www.worldpipelines.com]
The successful deployment of
System, near Aberdeen, UK. The
National
sealed a 56 km long, 48 in, pipeline, ensuring a leak-proof and fail-safe isolation. It maintained full pressurisation at 55 bar while an isolation joint was replaced and welded in place. This approached prevented the pipeline from being vented and cut carbon dioxide emissions by 95% compared with venting pipeline contents to atmosphere. www.statsgroup.com
MANAGING EDITOR
James Little james.little@palladianpublications.com
EDITORIAL ASSISTANT
Isabel Stagg isabel.stagg@palladianpublications.com
SALES DIRECTOR
Rod Hardy rod.hardy@palladianpublications.com
SALES MANAGER
Chris Lethbridge chris.lethbridge@palladianpublications.com
SALES EXECUTIVE
Daniel Farr daniel.farr@palladianpublications.com
PRODUCTION DESIGNER
Kate Wilkerson kate.wilkerson@palladianpublications.com
EVENTS MANAGER
Louise Cameron louise.cameron@palladianpublications.com
DIGITAL EVENTS COORDINATOR
Merili Jurivete merili.jurivete@palladianpublications.com
DIGITAL CONTENT ASSISTANT
Kristian Ilasko kristian.ilasko@palladianpublications.com
DIGITAL ADMINISTRATOR
Nicole Harman-Smith nicole.harman-smith@palladianpublications.com
ADMINISTRATION MANAGER
Laura White
laura.white@palladianpublications.com
Palladian Publications Ltd, 15 South Street, Farnham, Surrey, GU9 7QU, UK
Tel: +44 (0) 1252 718 999
Website: www.worldpipelines.com Email: enquiries@worldpipelines.com
Annual subscription £60 UK including postage/£75 overseas (postage airmail). Special two year discounted rate: £96 UK including postage/£120 overseas (postage airmail). Claims for non receipt of issues must be made within three months of publication of the issue or they will not be honoured without charge.
Applicable only to USA & Canada: World Pipelines (ISSN No: 1472-7390, USPS No: 020-988) is published monthly by Palladian Publications Ltd, GBR and distributed in the USA by Asendia USA, 701C Ashland Avenue, Folcroft, PA 19032. Periodicals postage paid at Philadelphia, PA & additional mailing offices. POSTMASTER: send address changes to World Pipelines, 701C Ashland Avenue, Folcroft, PA 19032
The NIS2 Directive is new, EU-wide, legislation that provides legal measures to boost the level of cybersecurity in the European Union. These EU cybersecurity rules modernise the existing legal framework to keep up with increased digitisation and an evolving cybersecurity threat landscape. Qualifying organisations must comply by 17 October 2024, or face penalties. Designed to bring about a high common level of cybersecurity, the Directive seeks to improve the resilience and incident response capacities of public and private entities, competent authorities and the EU as a whole.
The clock ticks for businesses identified by the member states as operators of essential services in energy, transport, water, banking, financial market infrastructures, healthcare and digital infrastructure.
One of the aims of the Directive is to bring about a ‘culture of security’, but how do we define such a culture? A security culture typically refers to the values that determine how people are expected to think about and approach security in an organisation.
I have written about the need for strong password usage in the past (anyone still using ‘password123’?) and along with that we need “regular security training and awareness programmes, stringent access restrictions, risk assessments, incident response plans, and a focus on continuous improvement”. 1
Do your senior staff members and directors set the tone for the company’s cyber policy? The NIS2 Directive requires energy companies to implement appropriate technical and organisational measures to prevent, detect and respond to incidents that could impact the security and continuity of energy supply. This includes measures to protect critical infrastructure, data protection and privacy, and the availability of energy services. 2
There is much to say about how human behaviour needs to inform policy on this matter. When I spoke to Mark Breese at Yokogawa RAP for the Palladian Energy Podcast in 2022, we discussed contractor safety and digital control of work systems. We gave the podcast episode the description: ‘making it easier to do the right thing than it is to do the wrong thing’, and I think this is key in the realm of cyber safety too. In a world where we work so fast, where we type and fire off emails, we approve things on the hoof, we move from one task to the next: there must be processes in place to save us from ourselves!
The World Economic Forum reports that “some 82% of cybersecurity breaches in the last year were due to a human element. The disruptive Colonial Pipeline ransomware hack that took down the largest fuel pipeline in the US and led to shortages was the result of a compromised password and password reuse”. 3
Building the kind of culture that can prevent (or at least limit) human error, takes concerted effort and repetition of values and standards. Living in a state of vigilance is hard to sustain, but our resilience to bad actors depends on us being able to assess threat on our best, and worst, days.
1. https://cybeready.com/category/the-complete-guide-to-creating-a-security-culture
2. https://nis2directive.eu/energy
3. https://www.weforum.org/agenda/2022/11/how-user-experience-and-behavioural-science-can-guide-smartcybersecurity
SENIOR EDITOR Elizabeth Corner elizabeth.corner@palladianpublications.comFounded in 1933, we cut our teeth in onshore and offshore pipeline construction. Now we are evolving our leading welding and coating solutions for today’s global energy and wider infrastructure sectors.
On 9 April, 2024, Britain and other major European countries with maritime borders on the North Sea, signed an agreement to work together to protect underwater infrastructure, including from possible Russian attacks, according to Reuters.
The six countries involved – Belgium, Britain, Denmark, Germany, Norway and the Netherlands – signed a joint declaration they said would allow them to share information.
Threats to undersea cables and pipelines have become a security focus for Western European countries following the September 2022 explosions on the Nord Stream 1 and 2 pipelines, built to ship gas from Russia to Germany across the Baltic Sea.
In May 2023, NATO had said Russia may sabotage undersea cables to punish Western nations for supporting Ukraine, while global security risks have risen further following the Gaza war.
“The North Sea is the powerhouse driving Europe’s renewable and net zero ambitions, helping to bolster energy security on the continent. So, it’s crucial we protect its critical energy infrastructure now and in the future,” Andrew Bowie, British Minister for nuclear and renewables, said.
“Strengthening ties with our key northern European neighbours as we have today will do just that, ensuring the infrastructure is resilient against those who may seek to threaten or disrupt it,” he added.
After four years and more than CAN$34 billion in costs, the Trans Mountain oil pipeline expansion will go into commercial service on 1 May 2024, Bloomberg has reported.
The Crown corporation behind the massive project provided the start date in an update posted to its website on Wednesday 3 April, 2024. “The commencement date for commercial operation of the expanded system will be 1 May 2024,” Trans Mountain Corp. said in the update.
“Trans Mountain anticipates providing service for all contracted (oil) volumes in the month of May.”
The company also confirmed in its statement that it has resolved the construction-related difficulties that had slowed the project’s progress in recent months. Trans Mountain Corp. had encountered an ‘obstruction’ when trying to pull the pipe into the horizontal hole that had been drilled for it in an area of the Fraser Valley between Hope and Chilliwack, B.C.
The Association for Materials Protection and Performance (AMPP), the global authority in materials protection and performance, recently published ‘Guide 21569-2024, Guidance on Implementing Corrosion Control Methodologies to Align with New PHMSA Regulatory Procedures,’ a comprehensive document developed by Standards Committee SC 15 - Pipelines and Tanks, aimed at bolstering the safety and integrity of onshore gas transmission pipelines.
In response to the US Department of Transportation Pipeline and Hazardous Materials Safety Administration (PHMSA)’s revised Federal Pipeline Safety Regulations, AMPP’s Guide 21569-2024 offers a detailed roadmap for pipeline operators to implement corrosion control requirements for onshore gas transmission as required in Part 2 of the PHMSA Gas Mega Rule.
The PHMSA revisions encompass an array of enhanced safety measures, including improved repair criteria, integrity management, cathodic protection, and management of change, all intended to mitigate risks associated with pipeline corrosion and ensure compliance with the most current safety standards.
“I’m very proud to have served as Document Project Manager for this development team comprised of an incredible group of industry pipeline subject matter experts across the
The setback forced the company to remove the pipe temporarily to address the issue, but on Wednesday 3 April Trans Mountain Corp. said it has resolved the challenge and the section of pipe has been successfully installed.
To complete the expansion project, “there are several remaining steps including obtaining outstanding approvals from the Canada Energy Regulator,” the company said.
“With the appropriate approvals and completion of remaining construction activity, Trans Mountain will commence transporting crude oil on the expanded system.”
The Trans Mountain pipeline, which was bought by the federal government in 2018, is Canada’s only oil pipeline to the West Coast. Its expansion will increase the pipeline’s capacity by 590 000 bpd to a total of 890 000 bpd, improving access to export markets for Canadian oil companies.
country,” said Kimberly-Joy Harris, a retiree from Enbridge Pipelines with more than 30 years leading pipeline integrity and corrosion programmes and Vice Chair of the AMPP Board of Directors. “Our main goal was to assist US natural gas pipeline companies with a guidance document that aligns with the new PHMSA Regulatory Mega Rule requirements related to integrity management, repair criteria, cathodic protection, and management of change, all to prevent and reduce failures. In addition, this document will be very useful globally to assist pipeline companies with improving their integrity programmes and reducing failures.”
Guide 21569-2024 caters to US gas transmission pipeline operators while providing critical insights for international counterparts aiming to improve their corrosion control measures.
This guide emerged from the industry’s need for a cohesive approach to comply with the new corrosion control, operations, maintenance, and integrity management PHMSA regulations that went into effect for transmission pipelines placed into service after 24 February 2024. It presents practical strategies for incorporating these requirements and leverages established practices to protect pipeline assets.”
Strohm wins third and largest ever TCP ‘Jumpers On Demand’ contract
6 - 9 May 2024
Offshore Technology Conference (OTC) 2024 Houston, USA www.2024.otcnet.org
11 - 13 June 2024
Global Energy Show 2024 Calgary, Canada www.globalenergyshow.com
26 - 27 June 2024
Hydrogen Technology Conference & Expo 2024 Houston, USA www.hydrogen-expo.com
26 - 29 August 2024 ONS 2024 Stavanger, Norway www.ons.no
9 - 13 September 2024 IPLOCA convention Sorrento, Italy www.iploca.com/events/annual-convention
17 - 20 September 2024
Gastech 2024 Houston, USA www.gastechevent.com
24 - 26 September 2024
International Pipeline Conference & Expo (IPE) 2024 Calgary, Canada www.internationalpipelineexposition.com
23 - 24 October 2024
Hydrogen Technology Expo Europe 2024 Hamburg, Germany www.hydrogen-worldexpo.com
23 - 24 October 2024
Subsea Pipeline Technology (SPT) 2024 London, UK https://sptcongress.com
ExxonMobil Guyana has awarded Strohm a TCP ‘Jumpers On Demand’ contract for the supply of TCP for the Whiptail project.
This brings the project count for the Netherlands-based manufacturer to three for ExxonMobil Guyana, following previous awards for the Yellowtail and Uaru projects. This latest award marks the largest commercial award for pipe supply in the company’s 16 year history.
The TCP for Whiptail will be produced at Strohm’s manufacturing facility at its headquarters in The Netherlands and used for water and gas (WAG) injection. The technology will be supplied to ExxonMobil Guyana in a single, continuous length along with associated pipe handling equipment. This concept and delivery method allows the individual 24 jumpers to be cut to the
Under the agreement, DeepOcean will be responsible for work on subsea pipelines, structures and high-voltage cables for offshore renewables and oil and gas fields, reports GlobalData.
The four year agreement will be applicable for Equinor’s operations on the Norwegian Continental Shelf and for planned international projects, as well as for contingency work for Pipeline Repair and Subsea Intervention (PRSI) Pool members.
Earlier this year, Equinor selected DeepOcean for inspection and surveying of its North Sea pipelines.
The Croatian government has announced plans to construct two natural gas pipelines totalling €400 million (US$430 million) to improve the country’s gas supply security and facilitate deliveries to neighbouring Hungary and Slovenia.
The projects include the construction of a 122 km gas pipeline from Bosiljevo to Sisak to Kozarac, valued at €322 million, and a 36 km pipeline from Lucko to Zabok, valued at €78 million, Economy Minister Damir Habijan said during a weekly cabinet session.
The pipeline will enable the planned expansion of the LNG terminal on the Croatian Adriatic island of Krk, which will increase its capacity from 2.9 billion to 6.1 billion m3/yr of gas, he added.
desired length, terminated, and tested onsite in Guyana, providing flexibility to the end-user. The jumpers, made of carbon fibre and PA12 polymer, will be installed at water depths over 1600 m and will operate in the region of 10 000 psi.
Gavin Leiper, Strohm’s Vice President Americas and Global Field Services Group, said: “This latest award brings us to a total of over 70 jumpers across three developments in Guyana’s Stabroek block. Not only is this our largest award to date, but it also means we will be terminating TCP and supporting ExxonMobil Guyana and its co-venturers for at least the next five years under our field service group contract. We look forward to deepening our relationship with ExxonMobil Guyana and our Guyanese partners.”
• DNV: Cross-border energy networks can cut US$800 billion from ASEAN’s decarbonisation cost
• Henkel closes acquisition of Seal for Life
• Rupture on TC Energy gas pipeline sparks wildfire
• Pembina completes acquisition of Enbridge assets
• EACOP coating plant commissioned in Tanzania
• Uganda and China to discuss oil pipeline investment
Mark Naples, Managing Director, Umicore Coating Services, describes spreading awareness about methane emissions and how to manage the threat through data advancements, specifically the use of gas detection technology as a critical turning point.
Around 5300 years ago, mankind experienced one of its first major revolutions with the beginning of the Bronze Age. 2100 years after that, the world was transformed again through the discovery of iron and steel. And now, another resource is prompting a fundamental shift in the world around us – data.
As the planet grapples with the escalating threat of climate change, data will provide the solution. Over the last few years, concerted efforts have been made to improve the monitoring of methane emissions, particularly those caused by the oil and gas sector. The launch of programmes like the IMEO Methane Alert and Response System (MARS) at last year’s COP28 climate summit, and the increasing use of satellites capable of providing almost real-time quantitative data on emissions, will significantly enhance the level of information available on where emissions are occurring – a vital step in closing an increasingly apparent gap in our understanding of this problem.
The information gathered so far paints a picture very different to the one reported by many energy suppliers. Early findings suggest there are large discrepancies between reported and measured emissions. Whether this is due to under-estimation, poor monitoring, or occasional wilful misrepresentation, the outcome remains the same; vast quantities of harmful and polluting gas are being released into the atmosphere with no official indication of its quantity or location.
Curtailing this threat now will be key to protecting people, profits, and the planet. Every ounce of methane that is stopped from leaking prevents potential harm to public health, limits global warming, and can be captured and sold. With advances in monitoring technology, the equipment is in place to gather empirical data on emissions, enabling businesses to be held
accountable, policymakers to target regulation, and action to be taken on the ground to prevent further damage.
All that is required is for this technology to be matched by the willingness to engage.
Accountability
The data gap around methane was made apparent by an incident in February this year, when Kazakhstani authorities announced that Buzachi Neft, the owner of a well linked to one of the worst recorded methane leaks in history, will be fined the equivalent of US$774 000. The well, located in the Mangistau region of Kazakhstan, is thought to have released 127 000 t of methane over six months between June and December 2023 – the equivalent to greenhouse gas emissions caused by more than 717 000 petrol cars in one year.1
Satellite monitoring identified that high concentrations of methane were visible on 115 occasions during the six month period. However, the company’s response highlights an ongoing issue; Buzachi Neft initially denied suggestions about the scale of the leak, claiming only a negligible amount of methane was contained within the well and any leaks would have burnt up on exit. Instead, it suggested that satellites could have mistaken other gases, such as water vapour, for methane.
This discrepancy between what is often reported and what monitoring picks up is a significant issue for the oil and gas industry. According to the International Energy Agency (IEA), the global energy sector was responsible for almost 135 million t of methane emissions in 2022. Coal, oil, and natural gas operations alone were each found to be responsible for around 40 million t of emissions, and another 5 million t in the form of leaks from
end-of-use-equipment. Combined, this means the sector is responsible for almost 40% of total methane emissions that can be linked to human activity.
Self-reported figures from the industry differ. In 2021, the 72 companies that at the time made up the Oil and Gas Methane Partnership 2.0 (The United Nations’ flagship reporting and mitigation programme) reported just 1.3 million t of emissions. A year later, and with 20 additional members, the OGMP 2.0 reported just 1.6 million t.
Clearly, this discrepancy makes effective action difficult. Without knowing where the worst emissions are occurring, action – both on the ground and in form of regulation – cannot be optimally targeted. If monitoring does not improve, emissions will continue to increase, alongside all the environmental and health damage that will bring.
Reducing methane emissions from oil and gas operations is widely recognised as one of the best short-term opportunities to make progress on global environmental targets. Since the Industrial Revolution, methane has accounted for around a third of all recorded global warming. Although methane is more potent at trapping heat in the atmosphere than CO2, it also degrades much more quickly. CO2 can remain in the atmosphere for hundreds of years, meaning that even if emissions were completely stopped today, the effect would not be seen for centuries.
In contrast, methane only takes around a decade to break down, meaning reducing methane emissions today will have a faster, more immediate impact than addressing other areas of emissions.
The energy sector accounts for almost 40% of all methane emissions caused by human activity, with agriculture and landfills responsible for much of the rest. This places a responsibility for addressing leaks squarely on the shoulders of oil and gas producers.
That is not to mention methane’s potential to adversely affect human health. Methane is a major contributor to groundlevel ozone, a pollutant that has been linked to numerous health conditions and around one million premature deaths every year.2 In workplaces, it can also form potentially explosive mixtures in the air that pose a serious threat to health and safety. This makes it even more important that companies know whether methane is a risk at their facilities, and where emissions are concentrated, so staff and machinery can be protected from harm.
What is more, failing to act on methane could be harming profits. According to the IEA, around 80% of methane emissions could be avoided at no net cost, due to the market value of captured gas offsetting the cost of leak prevention. As energy prices remain high, failure to capture and sell this gas is resulting in potential profits literally vanishing into thin air.
Thankfully, awareness of the threat that methane emissions pose and the importance of monitoring them appears to be growing. Around the world, significant commitments are being made to act on methane by the energy sector and governments alike. The recent COP28 summit saw promising steps announced that
could make a real difference in this struggle, with multiple new signatories to the Global Methane Pledge including several noted super-emitters.
More than 150 nations have now signed up to this pledge aiming to cut anthropocentric methane emissions by 30% by the end of the decade. These countries were joined by representatives from oil and gas companies based around the world. Combined, their commitment could help to curtail the growing problem.
Among the outcomes of COP28 were more than US$1 billion in grant funding to support action against methane. More exciting, however, is the launch of the Data for Methane Action Campaign, which aims to improve the collective understanding of emissions by basing it on empirical measurements rather than estimations. This programme will provide energy suppliers with the tools and funding they need to develop their understanding of their emissions profiles. For the first time, it will be economically feasible to monitor emissions from energy operations and produce accurate data that will help the sector scale up its efforts.
Although large-scale monitoring operations often rely on satellite technology, technological advances mean that businesses today have access to a wide range of on-the-ground equipment that can help them begin building their own data on emissions. Foremost among this technology are high-performance infrared sensors, which pass lasers through a filter inside a sampling chamber to measure the attenuation of incoming light and determine the precise concentrations of gas that are present. Changing the filter in this equipment means different wavelengths of light reach the detector, enabling it to be used to check for different kinds of gases.
At Umicore, we help OEMs simplify their gas detection systems while helping to drive advancements that let them use their devices in ways they had never previously considered. With more than 35 years’ experience in thin film design and manufacture, our custom infrared designs offer the perfect tools for building a clear profile of greenhouse gas emissions.
Technology such as this is helping businesses fill in the picture on methane emissions and better focus their mitigation attempts. Combined with other methods, action on methane by the oil and gas sector today could cut human-caused emissions by as much as 45% within 10 years. If achieved, this would stop global temperatures from warming by almost 0.3°C by 2045.
This may sound like a relatively insignificant amount, but it would represent 20% of progress towards the target of limiting global temperature rises to 1.5°C and would go a long way to helping achieve targets set out under the Paris Agreement.
As businesses move beyond estimations into a world of empirical measurement, a true revolution on methane is within reach. Modern technology is enabling accurate tracking in emission changes, providing a level of understanding that will make the industry more accountable, help guide regulations, and support companies with their own growth goals. Although there remains much work to be done, a clearer picture is emerging of where and how emissions are produced, where leaks are occurring – and how they can be fixed.
References
1. https://www.epa.gov/energy/greenhouse-gas-equivalencies-calculator#results
2. https://www.ccacoalition.org/short-lived-climate-pollutants/troposphericozone
PETROLATUM
VISCO-ELASTIC COATINGS
PROTECTIVE OUTERWRAPS
LIQUID EPOXY COATINGS
BITUMEN TAPE WRAP SYSTEMS
DENSO™ are leaders in corrosion prevention and sealing technology. With 140 years’ service to industry, our mainline and field joint coating solutions offer reliable and cost effective protection for buried pipelines worldwide.
HEAT SHRINKABLE SLEEVES
BUTYL TAPE WRAP SYSTEMS
United Kingdom, UAE & India
USA & Canada
Australia & New Zealand
SOIL-TO-AIR
INTERNAL PIPE LININGS
of South Africa www.denso.net
Carbon capture, utilisation and storage (CCUS) is one of the most versatile methods of reducing carbon emissions, as it can tackle both the production of emissions as well as removing CO2 from the atmosphere.1
As the world gradually transitions to a low-carbon economy, CCUS is generally acknowledged as one of the major technologies required to tackle CO2 emissions and the associated climate change issues.
Investing in CCUS technology has therefore emerged as a pivotal strategy to mitigate the effects of climate change on the planet. Quick and effective implementation of CCUS requires careful investment and design work, in order to accelerate the technologies available and to stay on track for net-zero ambitions.
One key element of the CCUS value chain is the transportation of the captured CO2 from point sources to the storage site for sequestration. Among the CO2
transport technologies, pipeline transport is the most widely used large-volume CO2 transport system today, as it is scalable, low-cost, and relatively safe.
Recently, there has been a significant increase in the number of CO2-related projects requiring pipeline transport of anthropogenic CO2 captured from different industrial sectors for storage in aquifers and other geological formations.
Anthropogenic and natural CO2 transport via pipeline – the key differences and issues caused by contaminants Although there have been many lessons from CO2 transport via pipelines, most of these facilities transport CO2 captured from natural sources, which have limited and well-defined impurities. On the other hand, CO2 sources from human activities (otherwise known as anthropogenic CO2) contain a wide range and high concentration of impurities (contaminants). These impurities
significantly affect the thermophysical and transport properties of CO2, impacting the reliable and safe operation of the CO2 pipeline transport system.
To ensure the reliable and safe operation of the pipeline transport system, a pipeline designer has to systematically analyse the impact of contaminants and, where necessary, set an allowable limit for the individual contaminants based on key process parameters, such as site environmental conditions, interaction between contaminants in the CO2 stream, toxicity of the contaminants and pipeline construction material.
Setting this allowable level of contaminants in the CO2 stream has significant commercial implications for the entire CO2 transport system. Setting stringent limits will mean further purification of the captured CO2 which adds to the overall cost of the system, but setting relaxed limits may result in integrity and operational issues (corrosion, slugging,
Mathew Aneke, Senior Energy Transition Consultant, Penspen, UK, introduces anthropogenic CO2 pipeline systems and outlines how to effectively address the challenges they present.
blockage etc) which also has underlying safety and commercial implications.
Thus, it is important for the pipeline designer to find the balance between the acceptable level of impurities to ensure the reliable and safe operation of the CO2 pipeline transport system.
To benefit from economics of scale, most CCUS projects usually comprise of clusters where the CO2 is gathered from point source emitters in gas phase using pipelines. The gas phase CO2 is subsequently sent to a centralised hub where the CO2 is compressed to dense phase for final transport to storage sites.
As an illustration, let’s assume an industrial cluster comprising of the following energy intensive industries:
) Chemical industry manufacturing glycol.
) Natural gas processing plant with acid-gas removal unit.
) Oxyfuel combustion/gas fired power plant.
) Other energy intensive industries such as cement, iron, or steels industry.
) Hydrogen production via steam methane reforming.
If CO2 is captured from the effluent streams using amine-based carbon capture technology (which is currently the most matured CO2 capture technology), the following contaminants will be expected to be present in the captured/effluent CO2 stream at varying concentrations (Table 1).
Understanding the challenges caused by the contaminants
Depending on their concentration, the identified contaminants affect the thermophysical and transport properties of the CO2
Let’s use the case of water and hydrate as an illustration. Hydrate (ice-like solid substance) formation in the CO2 pipeline could result in pipeline blockage. Water, as you can see in Table 2, contributes to hydrate formation in the pipeline as well as corrosion. The tendency at which hydrate could be formed depends on the concentration of water in the CO2 stream and the operating temperature and pressure in the pipeline. For a given pipeline operating temperature and pressure, increase in the water content of the CO2 will increase the chances of hydrate forming in the pipeline and vice versa. Thus, the pipeline designer should understand the pipeline operating conditions and ensure that the water content of the CO2 in the pipeline is limited to a level at which hydrate formation in the pipeline can be minimised and/ or eliminated to avoid any operational issues with the pipeline transport system.
Some design considerations that could help to address challenges in anthropogenic CO2 transport pipelines
Avoid liquid drop out in gas phase CO2 pipeline
For economic reasons, CO2 transport pipelines are usually made of carbon steel. One major operational issue to avoid while conveying gas phase CO2 stream in carbon steel pipelines is liquid dropout/ accumulation in the pipeline, as this may lead to corrosion and issues such as slugging. Liquid formation in gas phase CO2 pipeline is caused by the operating temperature and pressure of the pipeline and the concentration of contaminants with tendency to impact on the CO2 dew point, as shown in Table 2. In most cases, the pipeline’s operating pressure and temperature are constrained by the design and environmental conditions.
As a result of this, the key considerations for the pipeline designer to avoid liquid drop out and eliminate the associated operational and integrity issues is to limit the concentration of the contaminants that impact the CO2 dew point. The focus of this strategy should be on heavier contaminants such as H2O, heavy hydrocarbons, TEG, Amine and BTEX as they tend to have the most impact on the CO2 dew point.
Eliminate and/or minimise reactions among contaminants
Reactions among the key contaminants in the anthropogenic CO2 stream can result in the following:
) Acid formation.
) Salt formation.
) Hydrate formation.
The formation of these products will result in operational challenges in the pipeline and the pipeline
When safety is your top priority, make GripTight Test & Isolation plugs from Curtiss-Wright your go-to solution. Confidently test open-end pipe, pipelines and pressure vessels & isolate/test flange-to-pipe weld connections.
• Patented gripper design for increased safety in high-pressure applications
• Eliminates welding end caps for pressure testing pipe spools and piping systems
• Test flange-to-pipe welds without pressurizing entire systems
• Standard pressure ratings up to 15,000 PsiG (1034 BarG)
• Isolate & monitor upstream pressure and vapors during hot work
• ASME PCC-2 Type I, III & IV Testing Devices
designer should ensure that their formation is minimised to ensure safe and reliable operation of the CO2 transport pipeline.
Acid formation
Depending on the industrial cluster, anthropogenic CO2 streams may contain impurities such as oxides of sulphur, oxides of nitrogen, oxygen, hydrogen sulphide, ammonia, and water, as shown in Table 2. These contaminants have been proven through experimental studies to be reactive at pipeline operating conditions. It has been established through these studies that these species react to produce nitric and sulphuric acids.
Although these reactions have been found to be more kinetically favoured under dense phase transport conditions than gas phase, the solubility of the acids are very low in gas phase pipeline operating conditions and any acid formed will create a separate liquid phase which can then contribute to pipeline corrosion and embrittlement. Analysis has shown that limiting the concentration of reactants such as O2 and H2O will reduce the tendency at which acid and the associated corrosion is formed in the pipeline.
Salt formation
In addition, CO2 reacts with ammonia to form solid compounds such as carbonate and bicarbonate. These solids may become deposited and/or build up in the pipeline, thus increasing the pressure drop and cost of CO2 compression.
Since CO2 is the major component of the pipeline, the focus of the pipeline designer should be to reduce the concentration of ammonia in the CO2 stream. Most of the ammonia in the CO2 stream comes from amine degradation and can be eliminated via proper operation of amine-based CO2 capture process.
Hydrate formation in the pipeline
As mentioned earlier, CO2 tends to form hydrate at low temperatures. Hydrate formation can lead to operational issues
such as pipeline blockage and increase in the pipeline pressure drop, which can also lead to safety implications. This can be eliminated by limiting the water content of the CO2 stream, which can be achieved by drying the CO2 stream.
Toxicity consideration
The pipeline designer should also consider the set of contaminants in the CO2 stream that pose a hazard to health when it is exposed to individuals, and set their concentration level accordingly. Typical examples of such contaminants includes hydrogen sulphide and mercury. The concentration level of such contaminants should be set in such a way that their health hazard is lower than that of the CO2 itself. A dispersion analysis should be carried out to ascertain the dispersion and consequences of such contaminants during CO2 release.
Contaminants that directly attack pipeline material
Some of the contaminants contained in the CO2 stream may attack the pipeline material. For instance, hydrogen causes carbon steel embrittlement while carbon monoxide can contribute to stress corrosion of carbon steel. The pipeline designer should identify contaminants that are capable of attacking the pipeline material and set their concentration level accordingly to minimise their impact.
What does this look like in practice?
The ideal scenario is to have a pure CO2 stream with no impurity. However, achieving this will mean purifying the CO2 stream to remove all the contaminants. Doing this is practically challenging and also both capital and energy intensive. To reduce the cost of the process, the realistic approach is for the pipeline designer to carry out detailed analysis to set the acceptable limit of these contaminants in the anthropogenic CO2 stream based on the CO2 transport pipeline operating conditions in order to ensure reliability, safety, and integrity of the pipeline transport system, which needs to be monitored. These acceptable limits are used to formulate the CO2 stream specification for the pipeline transport system. The CO2 specification becomes contractually binding and every CO2 emitter injecting CO2 into the pipeline is expected to meet the specification before their CO2 is allowed in.
For this reason, many anthropogenic CO2 transport pipelines are designed with peculiar CO2 specifications, which are obtained through rigorous analysis to ensure the reliable and safe operation of the pipeline transport system.
References
1. https://www.iea.org/reports/ccusin-clean-energy-transitions
Josh Pendleton, Skipper NDT, France, discusses employing new technology in pipeline integrity management to ensure the continued safe and environmentally friendly delivery of energy, whilst mitigating the increasing risks of incidents to nearby environments and communities.
In North America, there are more than 800 000 miles of gas and liquid gathering, midstream and transmission pipelines and 2.3 million miles of gas distribution pipelines that deliver energy to local and international end users. Many of these pipelines have been operating for over 50 years and will be needed for several decades with the continued demand of the energy they deliver. Pipelines are more efficient than
other methods of energy transportation and have significantly lower environmental and safety impacts than trucking and shipping.
While pipelines play a significant role in North America’s energy infrastructure, their potential for environmental impact needs to be carefully managed and mitigated through effective regulation, monitoring, and responsible operational practices. And although pipelines have clearly demonstrated that they are the safest and most reliable method of transporting energy, they can and do fail. Pipeline operators continue to look for ways to improve the safety and reliability of their assets to keep failures to a minimum. When operating safely they effectively deliver large amounts of low cost, reliable energy with low environmental and safety impacts.
The continuance of safe and reliable pipeline operations poses several challenges that pipeline operators must address and continually improve upon through the development, validation and application of new technology and engineering solutions. In concert with these challenges, operators are also charged with adapting to new regulations, public expectations and shareholder demands add complexity and pressure to maintain and improve both safety and reliability and to minimise both the likelihood and consequence of incidents.
With our ongoing reliance on pipelines for energy coupled with the complex challenges involved and potential for
environmental impact operators must be constantly working to stay ahead of potential threats so that their associated consequences can be avoided or minimised. Innovation plays a large role in the improvement of pipeline integrity management and can have a significant impact both on the ongoing safe and low impact delivery of energy and minimise potential environmental impacts resulting from incidents.
Pipeline integrity management (PIM) programmes are charged with managing and mitigating a myriad of threats and consequences. Many of these have direct ties to the environment they directly traverse and that which they can indirectly effect. As regulations and societal expectations continue to focus on improving the management of our natural environment, pipeline operators must focus on continually improving their integrity management programmes to keep pace.
While not exhaustive some of the key challenges which operators face are discussed in the following section.
) High consequence areas: Pipelines in high consequence areas (HCA) are defined for gas transmission pipelines by the proximity of population near the pipeline and for liquids transmission pipelines by the proximity of population, drinking water sources, commercially navigable waterways, and sensitive environmental areas. HCA pipelines require higher levels of inspection, monitoring and mitigation which can pose challenges for resource prioritisation, deployment and decision making.
) Geohazards: Managing pipelines operating in areas susceptible to geohazard threats is a formidable task which is compounded by several factors:
• Changes in the frequency and intensity of significant weather events are affecting buried pipeline environments in new ways and rapidly.
• There are limited options to pipeline operators for direct measurement of below ground pipeline locations.
• They can be co-located within an HCA.
The inherent complexities of subterranean environments demand innovative solutions and advanced technologies to ensure proactive monitoring and effective risk mitigation strategies.
) Water crossings: Water crossings are typically active hazards particularly during flooding events. Recent changes in weather have resulted in an increase of extreme events with heavy rainfall, overland flooding, and coastal flooding. These events have a direct impact on pipelines that cross them. Riverbed scour, bank erosion and river avulsion can lead to significant pipeline failures.
As with geohazards, water crossings are also often co-located within HCAs.
) New construction: The construction of new pipelines continues to be a formidable challenge, characterised by high costs, regulatory hurdles and often faces concern
Figure 1. NPMS map of regulated pipelines in the US.from the public. The intricate interplay of diverse stakeholders, including regulatory bodies and public interest groups, further complicates the endeavour, which leads to fewer new projects being planned and approved and the rising importance of finding improvements in managing ageing pipelines. When possible, there are often legacy assets (below and above ground) that need to be properly accounted for in construction planning to prevent costly unplanned interruptions during construction.
) Decommissioned and abandoned assets: In addition to the challenges with operating pipelines, legacy assets, notably decommissioned and abandoned pipelines, and wells, can serve as potential conduits for subsurface water erosion and methane or CO2 leaks.
Meeting these challenges requires integrity management programmes that:
• Address all potential threats and consequences to their pipeline assets.
• Understand and control the probability of failure and potential consequences.
• Have complete, accurate and current data about the health of the assets being managed.
• Address all regulatory and operational requirements, including HCAs.
• Can adapt and address rapid changes due to environmental events and their effects (flooding, heavy rainfall, geohazards, erosion, etc).
Beyond the establishment of a robust integrity management structure and analysis methodology the data to support it is the most critical component of any PIM plan. Understanding pipeline integrity threats and consequences is impossible to achieve without having the necessary data to characterise the pipeline and surrounding environment. This data includes pipeline operational data, maintenance data, inspection data, patrol data, design data, operational history, and incident history.
The completeness, quality and currentness of this data poses a significant challenge for operators to manage. Operators face the opposing challenges of very large amounts of new data (inline inspection (ILI) for example) to be integrated with older datasets (historic ILI, historic excavations, and repairs, etc.) or situations where current data can be difficult to gather at a level of completeness and quality suitable for decision making. To reiterate this point, collecting accurate and complete data is essential.
With reference to the challenges listed in the section above some of the specific data required are as follows:
) High consequence areas: Pipelines within HCAs must have accurate and current data as to the exact XYZ location of the pipeline, in addition to current operating data, inspection data and patrol data as well
as data on any potential change to the conditions of the pipeline and surrounding environment.
) Geohazards: Pipelines traversing areas with the presence of geohazards must also have accurate and current data as to the exact XYZ location of the pipeline in addition to ongoing monitoring of the surrounding environment (soil, rainfall, erosion, etc.). Having current, and frequent highquality data as to the exact location and geometry of the pipeline, along with regular bending strain analysis enables the operator to understand change and the rate of change to the pipeline in geohazard areas so that appropriate mitigation can be applied.
) Water crossings: Pipelines crossing dynamic water bodies rely on accurate and current data as to the exact XYZ location of the pipeline in addition to information about the water body itself (riverbed, level, flow, bank changes, etc). Having the ability to collect XYZ data regularly and accurately for the pipeline allows the operator to track and analyse trends in changes to key factors and predict issues before they cause harm.
) New construction: Many new construction projects are considered as brownfield projects which have the potential to be impacted by existing, legacy assets with poor records or no records at all. These assets are often below ground and when encountered unexpectedly during construction can cause costly delays and change orders. Pre-project data collection can mitigate this challenge and allow construction teams to plan accordingly.
) Decommissioned and abandoned assets: Decommissioned and abandoned assets are challenging to both owners and regulatory bodies. Having technology that can efficiently and effectively locate and map these assets is the initial step in the process of assuring they are properly decommissioned and pose no ongoing safety or environmental hazard.
Accurate pipeline position data can be difficult and costly to collect in all these situations and locations, however the rise of drone-based, non-intrusive systems for locating and mapping underground assets and de-commissioned infrastructure offer operators innovative and cost-effective solutions to tackle these challenges reliably and accurately. These technologies enable continuous enhancement of integrity management programmes, thereby ensuring the protection throughput of critical economic infrastructure as well as the ongoing safety of the environment and people.
By integrating new technologies with comprehensive pipeline integrity management programmes, pipeline operators can consistently enhance their capacity to tackle growing challenges from environmental factors and stakeholders. This approach ensures the continual safety and reliability of our crucial energy transportation infrastructure.
Taper Lock Grips
Double Block & Monitor Isolation
The Remote Tecno Plug® provides fail-safe double block and monitored isolation of pressurised pipelines while the system remains live and at operating pressure.
Monitored Zero-Energy Zone
Martin Connelly, Technical Director, Liberty Pipes (Hartlepool) Ltd, UK, discusses how hydrogen, as the smallest molecule, can have a big effect in the energy transition, highlighting the importance of steel selection in ensuring the structual integrity of pipelines when transporting it.
s more and more plans are developed for transmitting high pressure hydrogen gas either on its own or as a blend with methane as part of the global energy transition, the industry has been hard at work looking at the effects on structural integrity of such gases at higher pressures.
Hydrogen transport isn’t a new problem; it’s been managed for many years. The processes of steel making and welding can result in deleterious hydrogen causing embrittlement, as can hydrogen from sour service gas/oil when in operation. The difference now is that with the advent of both ‘pure’ and blended hydrogen service being considered at higher pressures than previous hydrogen lines,
questions need to be asked and answered before a position on structural integrity can be established. The emerging position seems to be getting repeated consistently; with appropriate operating restrictions, much of the existing gas transmission networks can be repurposed, and that where this isn’t possible, modern and commercially viable steels are available that can provide adequate assurance of structural integrity.
Embrittlement
The model for hydrogen embrittlement is both complex and simple depending on the how deeply it is considered. In simple terms, it can be viewed as a classic ‘three bubble’ diagram (Figure 1 and 2).
If the hydrogen source is fixed by the gas composition/ pressure, and the stress/strain controlled by the desired operating envelope (diameter, wall thickness, pressure etc), the only way to separate the bubbles and mitigate the chance of hydrogen embrittlement is to consider the appropriate microstructure. In many cases this is fixed (i.e. when considering repurposing), but there are several microstructures which would work for new build
lines. At the same time, embrittlement can be avoided for a wide range of microstructures if the operating envelope is reduced sufficiently. These two basic approaches are captured in the main design code for hydrogen service pipelines, ASME B31.12 (2023), as ‘option A’ and ‘option B’; option A involves maintaining a lower operating pressure (controlling the stress/strain bubble), and option B allows for higher pressure with materials more proven to resist hydrogen embrittlement (controlling the microstructure bubble).
When applying option B, the designer needs to consider material selection, and this is where ASME B31.12 is gradually changing, being led by evolving views on fracture control on hydrogen pipeline designs within the industry.
Current fracture control concepts – fracture initiation/start of growth
Fracture control involves many complicated aspects of fracture mechanics, and many of these are captured in very complex and detailed codes (e.g. BS7910 etc). However, to simplify things, one can consider focusing on fracture initiation first and fracture propagation second. The linepipe industry has been looking at hydrogen effects on fracture initiation for many years, with a focus on testing a variety of materials in several environments. There are two main approaches to fracture initiation testing which are being heavily discussed at present:
) Linear elastic fracture mechanics (LEFM): epitomised by the ASTM E1681 bolt loaded compact tension test piece.
) Elastic-plastic fracture mechanics (EPFM): epitomised by the ASTM E1820 dynamically loaded compact tension test piece (although single edged, notched bends can also be used).
Both methods involve exposing a sample of the material to a desired hydrogen atmosphere under either a static load (E1681) or a dynamic load (E1820). The static load approach is checking for any crack extension of the fatigue pre-crack in the test media at a fixed stress intensity, which amounts to a pass/fail binary result, whereas the dynamic load test generates considerably more useable data, with the ability to feed such data into a much more detailed and in-depth structural integrity assessment. However, the correct choice of which test to apply depends on the required loading being experienced by the sample.
This is an area where the design code (ASME B31.12) is currently falling short. The defined fracture toughness stated in ASME B31.12 which a material in a hydrogen atmosphere must attain to be able to follow option B is 55 MPa.m1/2. The code then suggests that when testing to LEFM concepts using ASTM E1681, the actual stress intensity that should be applied needs to be at least twice the required fracture toughness; this equates to 110 MPa.m1/2. The problem with this approach is that most gas service line pipe materials are going to be in the grade range of API 5L X42 – API 5L X70, which when considering an overlapping of stress intensity and the stress/strain curve, results in the applied stress intensity of 110 MPa.m1/2 being well into the plastic zone of the material, and therefore it is no longer valid to consider LEFM testing (i.e. EPFM testing should be applied), as Figure 3 visualises.
While many materials have been tested this way, and with positive results, there is a decoupling and ‘flaw’ in the approach, and EPFM testing is not only more correct, it yields more usable
Figure 1. ‘Unsafe’ three bubble representation of H2 embrittlement. Figure 2. ‘Safe’ three bubble representation of H2 embrittlement.100 % safety. 100 %
Corrosion protection with outstanding strength and abrasion resistance
FORTIDE®-HT
For very high temperatures up to +150 °C
FORTIDE®-ST For standard temperatures up to +95 °C
FORTIDE®-TL For chemical-resistant tank & pipe lining
FORTIDE®-WS For application on wet surfaces
The new FORTIDE® Epoxy coatings guarantee the 100 % Made in Germany quality from industry leader DENSO. All FORTIDE® products are free of VOC & isocyanates and fully comply with ISO 21809-3. Benefit from a unique range of corrosion protection solutions: DENSO® Petrolatum tapes, DENSOLEN® PE/Butyl tapes, DENSOLID ® Polyurethane coatings, DEKOTEC ® Shrink sleeves, SEALID ® All-in-1 – and now FORTIDE ® Epoxy coatings. denso-group.com
FORTIDE® Epoxy coatings for lifelong safety.
data and as such is becoming notably more common in terms of the type of test that is required to be conducted. The downside of this approach is that the global capacity for conducting the EPFM test in the required hydrogen atmosphere is quite restricted. Furthermore, work by various end users and mutual industry groups (e.g. EPRG, PRCI etc) is revealing the criticality of the purity of the gas environment (notably the O2 and H2O levels). This is due to the effects of corrosion at the crack tip in terms hydrogen permeation through an oxide scale.
Liberty Pipes has undertaken the static tests detailed in ASME B31.12, testing locations in the pipe body, seam weld and heat affected zone (HAZ) of 38 in. OD x 28.6 mm WT API 5L X65MOS PSL2 material, and has shown in previous publications that no crack growth occurred even at applied stress intensities of up to 118.96 MPa.m1/2. While this is ‘code compliant’, the focus should be
more on the EPFM tests conducted on both sour service and nonsour (ferritic/bainitic vs ferritic/pearlitic microstructures) materials from a wide variety of manufacturers and operators using ASTM E1820. The E1820 tests also continue to show acceptable performances, suggesting that most line pipe steels within the ‘modern era’ will be suitable.
The main challenge when conducting either type of testing is addressing the emerging desires of many operators to control the aforementioned O2 and H2O levels; the emerging views suggest that values for O2 should be controlled to 2 ppm max and to 10 ppm max for H2O. These are challenging demands, and require robust purging procedures as well as very careful design of the testing apparatus seals and the strain rate consistency/ extensometry. This aspect is a whole separate topic, and is being developed into industry guidelines by various entities at present.
In addition to this issue of applying the correct testing technique with an appropriate gas, variations as to how to test are emerging, with DNV considering variations that involve applying increasing stress intensities for periods to see where the threshold is for when crack growth initiates (the so-called ‘Constant K’ approach).
In summary on the testing for fracture initiation or start of crack growth, it could be said that official industry code requirements for hydrogen service need to change to reflect what is emerging as best practice given the disconnect current codes seem to have. This is an important factor, as the majority of data suggests that even a small amount of hydrogen can result in a notable decrease in threshold stress intensity, and that increasing concentration of hydrogen purity doesn’t seem make things much worse (Figure 4).
There is a strong need for a correct, value driven and standardised approach to fracture mechanics testing of line pipe materials in hydrogen, and this is being addressed by the industry across a number of forums.
When turning to fracture propagation (fatigue), things are simpler, but still not simple. The same equipment used for fracture toughness testing is typically also used for fatigue investigation (typically conducted to ASTM E647) to investigate the traditional three stages of crack growth (Figure 5). When tested, the key factors looked at are:
) Stress Intensity Factor Range, ΔK = K max – K min
) Stress Range, R =
) Test Frequency, f
These aspects are used to check and see whether a material follows any previously predicted curve, typically to see how a different environment would compare with ‘in air’ data (Figure 6). When testing a relatively wide variety of steels, published data to date has shown that the effect of hydrogen seems to be relatively consistent across the variety of steels, in that it has a similar effect on fatigue regardless of grade, hydrogen concentration or, more importantly, microstructure (Figure 7).
This seems to be the case for a number of potential techniques for conducting the test, such as increasing ΔK testing or decreasing ΔK testing. In the end, the fatigue aspect is felt to be of slightly lesser concern than fracture initiation from a defect, and the focus of most bodies of work is and has been on the initiation aspect. That being said, there may very well be interesting publications due out in the next six months which could mean the above statement may have to be revisited.
Steel selection – new build vs repurposing
Two fundamental questions that will need to be asked are “what type of steel can I use?” and “what type of steel should I use?”; these may not have the same answers. The types of steel available for newbuild match those deployed over the last 40 years, albeit with modern steels being cleaner and slightly better in most aspects. Figure 8 shows the three main types of steel deployed/ available.
The published data (a good example being C Kalwa, Technology for Future and Ageing Pipelines, Gent, Belgium, March 29, 2022) shows that all three steels can perform adequately when considering fracture initiation and propagation. However, the current industry position on this is not clear, with a great deal of testing of all three of the above types (and even older, more vintage steels) currently being conducted. A greater mass of data correlated to a more robust characterisation of steel type is probably warranted before a clear position emerges.
The more pertinent question is how to repurpose and when to build new; the transition to hydrogen will require the ability to repurpose with limited new build, simply to manage the financial impact. This must be done safely, and to a defined and recognised practice. Repurposing is not the main concern of the pipe manufacturing community, so this section will focus on steel selection when considering newbuild.
In the view of Liberty Pipes, when newbuild is considered, the default for the embryonic period of hydrogen transmission should be to consider sour service type steel (i.e. the third variety in Figure 8). As this has a proven track record in being sufficiently resistant to hydrogen, it represents a fundamentally safer option providing other design aspects can be met. For lower pressure transmission (option ‘A’ from ASME B31.12), perhaps the repurposing is an easier consideration, but the demand to both increase pressure and flow rate due to hydrogen’s lower caloric potential compared with natural gas may result in some repurposing proposals not being viable. For those that are viable, experience may eventually yield enough data and proof for consideration of steels with lesser but still adequate resistance to hydrogen.
The selection of sour service type steel could result in another ‘clash of codes’, albeit probably only in Europe. The third type of steel (of which sour service steel is one of the main variants) has certain mechanical properties indicative of strain capacity which would not meet current regulatory requirements in Europe. The transverse yield/tensile (Y/T) ratio (checked when conducting tensile release testing during manufacture) for ferritic/bainitic steel (i.e. sour service) is notably higher than for the traditional onshore service European ferritic/pearlitic steel, and this would force a position where the regulated requirements for Y/T ratio would need to be relaxed. The current maximum values defined by ISO 3183 Annex A, and a variety of European operators specifications
Figure 6. Published FCG data on example X52 steel, San Marchi et al, PVP2021-62045. Figure 7. Collated FCG data from SNL and NIST for a variety of base microstructures.were developed back in the 1960s/1970s and were appropriate for the earlier ferritic/pearlitic steels. However, the use of Y/T ratio as a proxy/indicator for strain capacity (e.g. resistance to fracture during denting) is possibly antiquated, or at least there are alternative considerations which could be applied. Getting these requirements changed is not an easy challenge, as many of them are ensconced in law or regulations, but this will require appropriate prioritisation if hydrogen transmission is going to adopt a safety first approach. As hydrogen resistance is more of a binary condition of the steel (it is or it isn’t), and as a higher Y/T ratio can be managed more easily through design and geometry, it remains the view of Liberty Pipes that sour service steel for newbuild hydrogen service is the best choice, and will offer a longer term degree of safety.
With the statement before that newbuild hydrogen transmission lines should consider sour service steel, what is the readiness of the manufacturing base to deliver on this? Unsurprisingly, it is more than ready. Sour service line pipe for subsea service has been broadly offered across the industry for the last 40 years,
While still widely available, it is conversely the ferritic/pearlitic steel used onshore in Europe that may reduce in availability as it is only required in Europe; the rest of the world doesn’t have the same Y/T restrictions, and has moved en masse over to more modern steels with better properties. As steel companies are always looking to reduce cost, complexity and variability in steel ‘recipes’, the parochial nature of the ferritic/pearlitic steels in onshore Europe may lead to a preference for more globally acceptable and suitable steel and alloying concepts.
This article documents a few of the challenges presented to the industry when considering moving over from transmitting CH4 to transmitting H2 or H2/CH4 blends. While testing approaches are still in development, and full scale evaluations are well underway to correlate with smaller scale testing, it is becoming more clear that the areas of repurposing and newbuild are distinct from each other. The current steel types for CH4 distribution onshore in Europe may have some conceptual restrictions if switched to H2, but the capability is likely there to achieve a safe balance. It is the newbuild lines where a decision must be made; what level of
Under increasing pressure to reassess its infrastructure and output amidst evolving industry and societal standards and conversations, pipeline operators in the oil and gas industry are on the hunt for innovative and alternative methods of pipeline leak detection.
With 4.8 million km of natural gas pipelines stretching across the US, there is nothing new about the need to reduce unplanned leaks or spillage. However, now, between governing regulatory bodies and firms, stakeholders, activist groups, and, often critically, the consensus of the wider general public, there are more eyes on the global oil and gas industry than ever before. Despite each group’s varying motivations, from financial loss to health and safety risks to environmental implications and impact, minimising emissions is the unanimous goal.
According to data from the US Department of Transportation Pipeline and Hazardous Materials Safety Administration (PHMSA), between 2019 and 2023, pipeline issues and leaks released almost 274.7 million m3 of gas into the atmosphere. Currently, with the federal court ruling that large, accidental, or unexpected leaks are exempt from being included within the greenhouse gas tracker, these emissions are not being traced back to the oil and gas industry – at least not officially. This, however, is set to change.
No room for error
Under targets by the Biden Administration and the US Environmental Protection Agency (EPA), there is an aim to crack down on industry emissions with large-scale financial
implications for those not complying, resulting in fees of US$900 - US$1500 per metric tonne for emitters who exceed a set threshold. Unless corrected, as well as continuing to be hugely detrimental to the environment, once the regulation materialises (expected in 2025), there will too be additional unnecessary – and avoidable – costs for operators. To avoid this, companies are required to be more stringent with pipeline leak monitoring and detection.
These recent figures from PHMSA for emissions and the potential costs soon to be introduced at a federal level paint a worrying picture for operators and highlight the challenges companies face surrounding leak detection and pipeline monitoring – especially for those responsible for ownership and operation of legacy pipelines. Although the cause of
routine pipeline leaks can be far-reaching, either one sole factor responsible or a combination, the usual suspects include faulty equipment, punctures, corrosion, or severe weather. Something many of these issues are traced to is ageing infrastructure.
In a prior 2023 report from PHMSA, despite efforts made since the 2011 ‘Call to Action’ to accelerate the repair and rehabilitation of ageing and high-risk pipeline infrastructure, many of the cast and wrought iron pipelines in the US were installed over 60 years ago. These pipelines are still heavily active, delivering natural gas across the country despite the increased risk – a result of the degrading components of iron alloys, natural ageing, and the evolving demand for energy transportation. Investment and evaluation in the infrastructure and how we monitor it is essential.
Stuart Mitchell, President and CTO, PipeSense, examines the vital role that disruptive solutions such as AI and IoT must play in accelerating change within pipeline leak detection and monitoring for the benefit of the industry, its operators, and the wider environment.
In the 2010s, according to PHMSA, there were up to 3000 serious pipeline incidents, resulting in a US$7 billion bill for the industry. Whilst reports indicated that within the 20 costly incidents, a supervisory, control, and data acquisition (SCADA) system was in place, leaks were only detected approximately 50% of the time. Previous reporting within the Cross Country Pipeline Risk Assessments and Mitigation Strategies in 2018 found that within the US, the leak detection systems were effective less than 20% of the time.
Whilst there are varying leak detection practices and methodologies in place across the industry, as the surrounding circumstances evolve and seek innovation, it’s time for pipeline leak detection to do the same. Even previously advanced techniques, such as fibre optic sensing have become difficult to justify on ageing or difficult to reach and manage pipelines due to the significant cost to implement. The future of industry infrastructure looks increasingly to the potential of digitalisation and the Internet of Things (IoT).
The culmination of more than a century of combined industry experience in the selection, development, and deployment of integrity management technologies for onshore and offshore pipelines, PipeSense utilises advanced artificial intelligence (AI) analysis techniques to address pipeline operational challenges.
Understanding that the first line of defense will always be within the responsible management and maintenance of existing pipeline infrastructure, spontaneous leaks are inevitable. The key lies in reacting to leaks and stopping them promptly and efficiently. As a data acquisition and analysis specialist, PipeSense offers real-time leak detection and the ability to determine leak location with the utmost precision.
PipeSense is responsible for developing advanced leak detection technologies and integrating a state-of-the-art hardware and software system alongside its AI-based pipeline monitoring solutions. These solutions are further employed for hydrotest monitoring, real-time pig tracking, detection of pre-existing pipeline leaks, and identification of pipeline blockages.
Presenting a non-invasive, IoT-based method for rapidly determining the presence and location of spontaneous leaks in pressurised lines transporting oil and gas, PipeSense has digitalisation at its core – harnessing the power of AI and IoT to enhance pipeline performance.
Combining a proven methodology of negative pressure wave (NPW) sensing with advanced signal processing to minimise false positives and accurately identify the presence of small spontaneous leaks within seconds of their occurrence, PipeSense is localising leaks within 20 - 50 ft in long distance transmission pipelines.
Included in its solutions is the IoT-based leak detection system PipeGuard (Figure 2). Flexible enough to be layered with existing leak detection or monitoring systems, PipeGuard can monitor entire pipeline systems or laser its focus on highly sensitive areas regardless of the variation or challenge. Labelled as a disruptive solution for pipeline leak detection,
Figure 1. PipeSense’s custom built, Houston-based, full-scale pipeline for testing and demonstration.PipeGuard provides leak event notification within just 2 - 3 min. and reduces the risk of false positives to near zero.
Simple to install on new or existing pipelines, Field Processing Units (FPUs) are typically installed every 15 - 20 miles, with high-speed pressure sensors connected to available small bore pipeline branch connections. Additional contact temperature sensors are used on lines subject to bore temperature variations to improve location accuracy.
Utilising 1 kHz pressure data sampling combined with local data analysis edge computing and advanced machine learning techniques, PipeGuard is developed to provide accurate and robust leak detection in line with the innovative requirements needed for industry transformation –powered by AI.
By combining IoT and AI-based methods, PipeSense is creating opportunities for new engagement models that have the potential to minimise or eliminate significant upfront capital investment on the part of end-users.
With PipeGuard, PipeSense distributes sensors – attached to the pipeline via a small-bore branch – to collect pipeline data 24/7 so that any leak can be immediately detected and processed in real-time using a combination of edge and cloudbased processing. For the client, these notifications are distributed via a clear and concise pipeline mapping system, based on a Docker container architecture, that features near realtime leak notification of leak events with highly accurate GPS location. Operators are then notified of pipeline operational events via accessible communication chains such as text, email, a web-based application, and the SCADA/DCS interface.
The use of a highly portable Docker container-based approach has been critical in addressing operator’s cyber security concerns. The approach adopted by PipeSense means that the remote back-end processing can be located either in a secure cloud instance hosted by the client (or PipeSense), a client’s own secure virtual server, or even a physical server located on the premises with the end client.
Traditional negative pressure wave leak detection relies upon detecting a pressure pulse created within the pipeline contents when a spontaneous
leak occurs. This pressure pulse travels upstream and downstream in the pipeline contents whilst being sampled by the distributed pressure sensors attached to the pipeline. Once confirmed by local data processing to be a leak event, the time-stamped data from each sensor location is transmitted to a common cloud location where the fluid speed of sound is combined with the leak event time stamps to calculate the leak location.
Negative pressure wave-based leak detection systems have always been noted for their ability to detect leaks quickly compared to the more commonly used mass balance type systems. Detection can readily be in the 2 - 5 min. range.
Detects holidays, pinholes, and other discontinuities using continuous DC
w i t h i n t h e
c o m p a c t w a n d h a n d l e e l i m i n a t i n g t h e n e e d f o r a s e p a r a t e b a t t e r y b o x
n B u i l t - i n C e r t i f i e d Vo l t m e t e r a n d Vo l t a g e C a l c u l a t o r f e a t u r e
n I n d u s t r y s t a n d a r d c o n n e c t o r s a n d a d a p t o r s p r o v i d e c o m p a t i b i l i t y w i t h
n e a r l y a l l e x i s t i n g e l e c t r o d e s
No shoulder bag required!
Also available with Pulsed DC
High voltage Holiday Detector
Stick-type with Pulsed DC
Wand-style with Continuous DC
They are also known for being a more cost-effective solution compared to external leak detection approaches, such as the use of fibre optic-based sensors.
The shortcomings of this signal threshold-based approach have always been its ability to detect the smaller pressure responses associated with leak events over longer distances without causing the system to provide false positive alarms caused by detecting normal pipeline operations as a leak event. This is especially true when trying to use this approach for gas pipelines.
PipeSense has developed a new leak detection technique that combines high speed pressure sensing with AI-based image processing to provide a solution to this challenging problem.
Utilising pressure data sampled at one thousand samples per second, the system still utilises a more traditional threshold-based approach to screen the pipeline pressure data for abnormal pressure events. Each distributed field processing unit along the pipeline that detects the abnormal pressure event sends a small packet of data to a common cloud location. These packets of data are then converted into a frequency image. Using advanced AI-based techniques, this image is then compared to a database of over 30 000 images representing a wide range of pipeline leak events and
other abnormal pressure events from a variety of pipeline configurations and contents (Figure 4).
It is not until this final stage that an abnormal pressure event can be now categorised as a leak event or some other typical pipeline normal or abnormal operational event. The result is that the PipeSense PipeGuard AI-based approach can remain sensitive to even small abnormal pipeline pressure events, without producing false positive alarms.
Not satisfied with this singular use of AI, PipeSense also utilises AI to improve leak location accuracy. Using combinations of controlled ‘training’ pressure releases from along a pipeline length, PipeSense deploys AI to detect changes in leak signal magnitude and, using further regression analysis, accurately determine leak location, accurate to less than 50 ft in its system testing.
Utilising the same hardware platform, and similar AI-based approaches, PipeSense has provided industry-leading pipeline leak detection and additionally detects and accurately locates leaks in real-time during hydrotest, tracks pipeline pig location and speed in real-time, finds pipeline blockages, and even detects and locates pre-existing pipeline leaks.
PipeSense was already monitoring an existing client’s 50 mile length of liquid propane pipeline for leak events using its original advanced negative pressure wave threshold-based technique. Although performance was encouraging, with all test leaks detected and location being accurate to within a maximum of 106 ft, the client had experienced a handful of false positives over the initial implementation phase and the first year of operation.
After the same client approached PipeSense to expand the monitoring of that pipeline to a 100 mile section, it was the ideal opportunity to implement the brand-new AI-based approach. Using previously collected data over two years, PipeSense tested the new software solution before installation to monitor what performance improvements were implemented, resulting in encouraging feedback.
The new AI-based system successfully detected all previous physical test leak releases. However, there was not a single false positive notification. Sensitivity was maintained whilst troubling false positives were eliminated. Leak location had also been improved, reducing the predicted leak location to within a maximum of 50 ft from the previous 106 ft.
PipeSense also supplied a new version of its web-based client interface, providing the client with the flexibility of deployment and maintaining the clean and effective display of system operation without the requirement of extensive client interaction.
Increasingly, AI is becoming more and more prevalent across diverse industries. Whilst it will remain a necessity to have the expertise and insight to effectively implement AI-backed solutions for the best possible results, to enhance pipeline performance, and to support changing industry requirements, those who can balance the potential of disruptive solutions can pave the way for safer and more efficient pipeline leak detection and monitoring.
Figure 3. PipeSense’s pipeline monitoring and leak detection process.Combining industry-leading abrasion resistance with unmatched flexibility, our range of epoxy solutions are built tough, easy to apply and designed to last. Whether its HDD or field joint coatings, we’ve got the solution.
Combining industry-leading abrasion resistance with unmatched flexibility, our range of epoxy solutions are built tough, easy to apply and designed to last. Whether its HDD or field joint coatings, we’ve got the solution.
Michels Canada combined technical construction skills with community outreach initiatives to deliver a 65 km pipeline spread on Canada’s West Coast, joining a network of other leading contractors in contributing to a massive and significant project. The Coastal GasLink (CGL) pipeline will move natural gas from producers in British Columbia and Alberta to new LNG facilities where it will be exported to overseas markets. In its 670 km (416 miles) entirety, CGL is expected to have the capacity to move 2.1 billion ft3/d of natural gas and potentially deliver up to 5 billion ft3/d. Natural gas is one of the world’s cleanest and safest energy sources.
CGL will enhance global energy security and allow international markets to replace higher carbon emitting fuels, such as coal, contributing to a reduction in global greenhouse gas emissions. The project also provides significant benefits to Canadians, including remote and Indigenous communities along the route.
John Hunt, Michels Canada, outlines the complexities of delivering a 65 km pipeline spread in hilly, remote and sensitive terrain, as part of the Coastal GasLink pipeline project.
Michels Canada joined the CGL team in 2022 to replace a contractor that was no longer working on Section 6, a 48 in. diameter spread running south of the communities of Burns Lake and Houston in northern BC’s Lakes District, a coniferous and mountainous terrain with more than 300 wilderness fishing lakes.
Part of the Michels family of companies, Michels Canada is an energy and infrastructure contractor performing energy, infrastructure and power work across Canada. Michels is a leader in energy and infrastructure construction throughout North America with specialised trenchless construction operations in Australia and Europe.
Safe construction of a 65 km spread in a remote, hilly, environmentally significant area requires a monumental effort involving more than 1000 people throughout the project’s duration, including 750 people during peak operations. In an area where remote wilderness is much more prevalent than commercial development, more than 600 people took temporary residence at the project’s central hub, 7-Mile Camp. Another 215 Michels personnel were located at the Huckleberry Camp to the west. Michels Canada leaned into its experience on other large pipeline construction projects to develop safe procedures for transporting personnel, equipment and supplies to temporary yards and to geographically challenging rights-of-way.
As with other large-scale projects in Canada, building meaningful relationships with Indigenous and local community leaders and residents was an important component in the ability to build a safe, reliable pipeline. From the start, Michels Canada focused on optimising relationships and sourcing Indigenous community members for subcontracting and employment opportunities. Community engagement and fundraising initiatives provided opportunities for collaboration and interaction.
Michels Canada’s project approach ensured all construction activities met primary objectives of safety and injury-free principles, responsible environmental stewardship, schedule, quality and reliability. Successful projects are achieved through a well-supported culture of safety, training and field-level engagement. Establishing a culture of safety, environmental compliance and quality is achieved by effectively implementing health, safety, environment and quality policies, procedures, and standards across all levels of the organisation, from Senior Management to frontline workers. The construction management team ensured all policies, procedures and standards were clearly understood and practiced by each team member. As a result, Michels Canada received the project’s 2022 Extraordinary Legacy Award for Health and Safety for an exemplary safety record.
The Section 6 terrain was challenging with key fish-bearing streams, saturated glacial lacrustine subsoil and in an area receiving higher than average rainfall and snowfall. Throughout the project, the team mitigated the impact and challenges with respect to fish-bearing streams, mountains and glacial meltwater sediments while contending with higher-than-average rainfall and snowfall. Although Michels Canada is recognised as a global leader in horizontal directional drilling, conventional construction methods were used for all stream crossings on Section 6. Michels Canada developed and executed plans to isolate work zones, install pipe and reclaim ground at all crossings.
The majority of Spread 6 was accessed by radio-assisted forest service roads used and maintained by the forest industry. Michels Canada used buses to bring work crews to specific job locations to minimise traffic on the roads. Pickup trucks and semi-tractors were equipped with radios to maintain communication with other up- and down-road vehicles to mitigate transportation
Figure 2. Strict attention was given to protect waterways on the right-of-way. Figure 3. A pipe string is carefully lowered into a trench.Once a pipeline is in production, debris within the system can be more extreme, with sand or scale or wax deposits. This can require more specialist pigs to be used, where designs are more focused and offer the ability to be adjusted as part of a progressive cleaning programme.
Propipe pigs are designed specifically for each pipeline and offer optimum performance to maintain maximum production pressures and flow.
Bypass
testing facilities and the Trident pig tracking range are available.
risks. All drivers were trained to drive slowly and be prepared to encounter unannounced vehicles without in-cab radios.
Michels Canada has a long history of engaging with Indigenous and local communities on all projects from direct labour workforce, to subcontract and supply opportunities. Michels Canada looked for ways to engage Indigenous subcontractors and suppliers meaningfully and drew on our past experience and network of Indigenous contacts to make this a priority.
Michels Canada was proud to join a prime contractor group on CGL with unprecedented Indigenous and local procurement, services and employment. Michels Canada signed six Indigenous economic development partnerships on Section 6. The
agreements were with Atsiyan Services LP (Stellat’en First Nation), Kyah Development Corporation, (Witset First Nation), Yinka Dene Economic Development Limited Partnership (Wet’suwet’en First Nation), Natanlii Development Corporation (Skin Tyee Nation), Hunust’ot’en Investment Corporation (Nee Tahi Buhn Band) and Ts’il Kaz Koh Development Corporation (Ts’il Kaz Koh First Nation).
Community involvement
Michels Canada partnered with CGL and other contractors to raise hundreds of thousands of dollars to support local non-profit organisations via a bottle recycling programme. In Burns Lake, the community which served as the home base for Section 6 construction, recycling bins were set up in lodges to encourage workers to recycle bottles and donate proceeds to local organisations. Matched by GCL’s employee giving programme, Build Strong, donations were given to a programme that delivers dry goods, fruits, vegetables, starches and other essential items to those in need and to a volunteer organisations dedicated to providing children of any gender from ages 5 to 18 with opportunities to participate in competitive or recreational hockey.
As another initiative, Michels Canada organised the Burns Lake Centennial Ice Fishing Derby to celebrate the community’s 100th birthday and thank the many people who welcomed the crews while they built Section 6. To raise the donation to an even more impactful amount, CGL donated a matching grant of CAN$66 255, bringing the fundraising total to CAN$134 695. The funds were donated to eight community organisations.
9-13 September 2024
Alyson Cram, Vacuworx, USA, explains how the applications for vacuum lifting extend beyond oil and gas to hydrogen and new energy blends.
For 25 years, Vacuworx has been a global leader in material handling solutions, particularly in the oil and gas industry. The company’s vacuum lifting technology has been used widely across North America and internationally, with the addition of offices in Australia, Europe, South America and South Africa.
The flagship RC Series features impressive standard lift capacities ranging from 22 000 - 55 000 lb, making it the ideal solution for large diameter major
energy and infrastructure projects, as well as material handling at port facilities, pipe mills, storage yards and manufacturing facilities.
The need for heavy-duty material handling solutions is present in every area of the oil and gas industry, as well as new energy infrastructure arenas, including the use of fibre reinforced polymer (FRP) pipelines, which have been identified among the potential solutions for hydrogen distribution. In the USA alone, there are already approximately 1600 miles of hydrogen pipelines currently operating according to the US Department of Energy, with Europe and other international regions rapidly expanding hydrogen pipeline research, development, and plans.
The high initial cost required for new pipeline construction, whether for oil, natural gas, or alternative energies like hydrogen, can present barriers when looking to expand and install pipeline networks. For hydrogen pipelines specifically, adapting part of the established natural gas infrastructure to accommodate hydrogen – which would involve converting existing natural gas pipelines to carry a blend of natural gas and hydrogen – is another possibility.
According to the US Department of Energy, converting entire pipelines currently dedicated to natural gas requires significant modifications. 1 However, converting natural gas pipelines to carry a 15% blend of hydrogen only requires modest modifications, thus removing a large portion of the upfront expenditure.
Among existing and readily available material lifting technologies, for improved safety and more efficient and productive pipe handling scenarios, vacuum lifting can be extended to nearly all dimensions or types of pipes. Customers who use Vacuworx have consistently finished projects early, reduced injuries on the job site, and lowered insurance costs.
Offering a contemporary solution to common lifting methods like hooks, slings, chains, or grapples, the RC Series and its proprietary technology include 360˚ of rotation and wireless remote-control operation, allowing operators
complete control over the system from the cab of the excavator or host machine.
Additionally, one of the hallmark features of the RC Series, or any Vacuworx product, is the proprietary pad seal used on the vacuum pads. It is a testament to Vacuworx’s problem-solving abilities and commitment to efficiency. The pad seal is both soft and robust, creating an airtight seal on the load while removing the risk of damaging the coated steel pipe – a common occurrence when making metalon-metal contact during time-consuming, traditional lifting practices.
The modular design of the RC Series encourages seamless integration with excavators, backhoes, cranes, and other heavy equipment, representing versatility at its core design. Its compatibility with a vast range of host machines is facilitated by quick disconnects, available for virtually any equipment meeting the hosting requirements. The nature of the quick disconnects enables easy and fast transferability and reuse of the RC Series, allowing contractors to start on new projects with little to no delay, optimising operational efficiency.
Diving deeper into the modular capabilities of the RC Series, its specialised pads for lifting pipes showcase adaptability. These curved pads are intentionally designed to cater to standard pipe sizes and materials, ranging from steel to HDPE, cast iron, fibreglass, clay, and beyond. Their curved configuration, in tandem with guide wheels, ensures precise positioning onto the pipe, guaranteeing secure placement. This approach fosters a positive engagement with the load, compared to the potential hazards presented by other lifting techniques, which may shift or loosen during operation and endanger workers on the job site.
The RC Series continues to solidify its position as industry leading machinery by extending its capabilities beyond curved pads. The unit accommodates flat and custom pads tailored to handle an assortment of materials, including saw cut concrete, precast concrete and culverts, steel plate, and composite mats. This flexibility empowers customers to deploy the equipment across various stages of a project, while minimising the need for additional equipment. By offering a comprehensive range of pad options, the RC Series maximises efficiency and adaptability for construction tasks of varied nature and scale.
When the RC Series was first brought to market, the units were exclusively offered with a diesel engine. Since then, Vacuworx has expanded the series to include hydraulic options for all five versions of the vacuum lifting system, permitting the customer to choose the appropriate unit based on their needs and preferences.
Diesel is a common fuel used worldwide, especially in sectors such as transportation, agriculture, construction, and industrial machinery. In fact, the US construction sector relies on diesel technology to power more than threefourths of all heavy construction equipment, according
Midwestern’s M12H, M18H & M24H are the newest addition to our winch attachments. These winches are designed for hoisting purposes on excavators with lift capacities of 12,000/18,000/24,000 lb and attaches with a quick coupler to the excavator stick. The attachments use existing cab controls for all winch functions, ties into the auxiliary hydraulic circuit, and are easy to install. Make your equipment more versatile by adding on one of our hoist winches.
MIDWESTERN - built for the toughest jobs.
to The Energy Technology Forum. 2 While diesel usage varies by region and depends on factors like policies and environmental requirements, it remains a key component of the global energy mix. Its popularity stems from its high efficiency, and widespread availability. Diesel engines are also known for their durability and long lifespan, making them well-suited for heavy-duty applications, and making it an obvious choice when first introducing the RC Series to the market 25 years ago.
Later, Vacuworx expanded the power source options for their vacuum lifting technology by introducing RC Series ‘H’ models. Leveraging the hydraulic system of the host machine presents an innovative approach to efficiency and sustainability by eliminating fuel costs, emissions, and noise pollution. This pioneering design integrates seamlessly, tapping into the host machine’s hydraulic power for operation. By removing traditional fuel, these models not only reduce operational expenses, but their silent operation heightens their appeal. But it doesn’t stop there. As technology, innovation, and customer feedback continue to evolve, alternative power options are being developed.
The RC Series offers a secure solution for material handling by eliminating the need for hazardous and time-consuming manual material handling lifting tasks, all while ensuring the integrity of the lift.
By removing personnel from potentially dangerous areas, these systems have become crucial in reducing workplace accidents and injuries. Moreover, the commitment to rigorous quality management processes and ISO certifications is evident in the design of the device. In fact, Vacuworx maintains its dedication to upholding the highest standards of quality and safety, consistently complying with global safety and engineering standards, including OSHA, ASME for Below-the-Hook Lifting Devices, CE, and more.
Vacuum lifting technology is one key to limiting manual handling requirements and the amount of contact pipeline
installers are exposed to. While the hard costs associated with material handling are largely unavoidable, the cost of equipment and the human resources required can be alleviated by investing in systems that put a priority on safety. Improved ROI is evident through efficiency gains and the ability to speed up the lifting and installation process, fewer lost workdays, lower insurance premiums, and fewer unexpected stalls in productivity.
The flagship RC was developed and precision engineered to allow for easier manipulation of pipe – for safer, more productive, efficient, and precise handling that causes less human strain. From the design phase through engineering and fabrication, inspection, testing and validation processes, Vacuworx approaches every vacuum lifting system by emphasising quality and continuous improvement.
At Vacuworx, a heavy focus is placed on customer feedback and involvement. Further development of the RC Series is continuously driven by the practical needs and insights derived from engaged customers, and demonstrative of how focused innovation can lead to transformative results. This device has been validated through diverse in-field trials and experiences across the globe, with multiple case studies to support.
The secret to success for Vacuworx and its customers is their strong prioritisation of workplace safety initiatives and contributions to industry solutions that reduce risks stemming from material handling activities. Accomplished in part by eliminating the need for hooks, chains, or slings – even entire gangs of construction workers – adopters of the RC Series technology have repeatedly recognised the need for fewer personnel.
By integrating the RC Series into their operations, customers significantly reduce hazardous lifting practices and improve efficiency factors of their pipeline installation productions. Fewer tagline operators, fewer people climbing on trucks or standing on top of loads, fewer workers overextending their bodies or bending forward, fewer humans being asked to perform in harm’s way – the RC Series’ contribution is significant.
Over the years, alternative fuels have increased in popularity as the demand for cleaner energy grows. Most recently, hydrogen has emerged as a promising clean energy carrier. The development of hydrogen pipeline infrastructure is gaining momentum worldwide, with funding for research and development efforts increasing alongside.
In response to this growing demand, Vacuworx’s RC Series stands ready to support the development of alternative energy infrastructure. With its advanced technology, the RC Series is fit to lift nearly all pipes regardless of material or energy being transferred and is slated to play a crucial role in shaping the future of clean energy infrastructure worldwide.
References
1. https://www.energy.gov/eere/fuelcells/hydrogen-pipelines
2. https://enginetechforum.org/construction
ABC. See it. Believe it. Trust it. To advertise email Chris Lethbridge at chris.lethbridge@worldpipelines.com or Daniel Farr at daniel.farr@worldpipelines.com
Andrew Vana, Manager of Specialised Services, RMI, USA, discusses providing health, safety and environmental support to varied and remote pipeline construction projects.
Research indicates that the length of gas transmission pipelines currently under construction is enough to circle the earth oneand-a-half times, representing an 18% increase over the last year. This unprecedented growth means it is now more critical than ever that organisations ensure that
robust health, safety and environmental practices are in place to protect the health and wellbeing of the workforce on mainline pipeline construction projects.
Trenching, excavation and controlled, planned, scheduled, or coordinated explosive operations on pipeline sites mean that workers are constantly exposed to an
extremely hazardous working environment. The combination of harsh weather conditions, steep inclines, confined spaces, pipeline leaks, failed excavation attempts, and use of various machinery along the pipeline all pose a unique set of challenges that must be addressed to mitigate risk and operational delays. When coupled with the remoteness of project worksites which are constantly moving through various private properties, deserts and even mountain ranges, not being able to simply call 911 can implicate complex logistical challenges for medical providers. Without the proper foresight, site planning and approach from an experienced safety and medical provider, worksites have the potential to be extremely dangerous.
RMI supports organisations to protect staff wellbeing and lower operational costs by providing highly qualified and experienced medical and safety support staff to varied and remote pipeline construction projects around the globe. Placing medical, safety and environmental staff to provide both primary and emergency medical care, we work with organisations that prioritise the protection of the health and welfare of the workforce and are invested in the value
that professional health and safety provision delivers for the continuity of their operations.
Any medical and safety service provider operating on mainline pipeline projects should have experience in providing adaptable, high quality onsite care in remote working conditions. At RMI, all our safety inspectors hold the OSHA 500 qualification as a minimum, a high level industry certification which reflects exceptional dedication and experience in the pipeline industry. Individuals with this certification are authorised to conduct OSHA’s Outreach Training Programme through industry sessions that provide training to workers on the recognition, avoidance, abatement, and prevention of safety and health hazards in workplaces, along with information regarding workers’ rights, employer responsibilities, and how to file a workplace safety complaint.
Since emergency response is a core component of RMI services, safety inspectors are trained to either a basic or high level in emergency medical service skills. In addition to this, they are trained and experienced in medicine specific to industrial work, such as primary care training and occupational health and safety awareness training. This additional level of knowledge enables our providers to supplement the skillset of the project’s existing workforce.
Having the constant presence of a medical and safety professional who interacts regularly and builds trusted relationships with the workforce also helps personnel to feel comfortable when reporting medical conditions and reduces fear of the immediate threat of dismissal. This pressure can be eased further by ensuring that the organisation has the resources to manage commonly reported conditions or any other illness that occurs onsite. Enabling swift communication and response is essential to prevent some of the potentially life-threatening injuries sustained on pipeline construction sites.
The responsibilities of a safety inspector cover far more than just medical care; RMI’s onsite experts hold team safety meetings each morning, known as ‘Toolbox Talks’, where they are able to review the projects that will be taking place on that day, clarify who is involved, and discuss any evacuation or extraction plans if necessary. Regular briefings like these are essential to preparing the workforce and manage any potential risks.
A high quality medical and safety professional is one who is involved with all levels of construction operations, from the moment the first shovel hits the dirt through to running gas through the pipeline. At RMI, our specialists consist of highly experienced individuals who have developed some of the largest safety programmes in the pipeline industry, and are often responsible for reviewing the overarching safety strategy for projects through to delivery, which ensures that the highest standard of care is already in place.
Figure 1. One of RMI’s mobile treatment centres (MTC) onsite.A good example of the value of the medical services we provide is illustrated by RMI’s onsite provision for a large pipeline project in Texas, delivering medical support for its 2200 strong workforce since 2009. As the project is an extensive one, our highly-experienced team consists of occupational health physicians, onsite paramedics, and multiple emergency medical technicians. The team ensures the onsite workforce is healthy and immediately supported in any medical emergency.
As the location of the project moves, RMI medics are deployed to set up and outfit multiple onsite clinics for the workforce, including two Mobile Treatment Centres (MTC). These four-wheel drive clinics allow our medical staff to provide treatment in remote environments that standard emergency vehicles are unable to reach. In addition to a treatment area, storage and hand washing facilities, the MTC is equipped with first aid supplies and emergency response equipment, including an automated external defibrillator, trauma management equipment, and a backboard and litter for patient transport. This equipment ensures that our onsite medics are well prepared to respond to any type of medical emergency, no matter where the project is situated or how remote the location.
Despite the industry’s recognised workplace pressures, the stigma regarding mental health remains. Workers endure prolonged periods of time away from family and friends, and long shift patterns can make it difficult for them to maintain healthy habits. This combination of factors can be challenging on employees’ mental health and can increase the likelihood for any pre-existing health problems to become amplified onsite.
While varying degrees of mental health support for workers are already in place across the sector, there is still more that can be done. As a long-standing global provider of health and safety services to the pipeline industry, RMI remains committed to mental health support. Our safety inspectors promote simple practices of self-care, optimal sleep hygiene and rest, a varied and wholesome diet, regular exercise, and avoiding excessive phone use in between shifts.
It is paramount that workers feel well enough in themselves to complete the work at hand, and, in an industry which involves the frequent use of heavy equipment, all health and safety professionals should ensure that workers are getting enough sleep and that they’re not becoming complacent in order to prevent avoidable injuries.
Beyond the wellbeing of the workforce, it’s equally as important for pipeline construction projects to continually review the environmental impact of their work. RMI’s staff provide environmental support in the form of monitoring and advising on key areas such as potential leaks, naturally occurring asbestos, or the qualities of drilling fluids. While the majority of materials in the industry are environmentally safe, it remains good practice to have someone who understands these challenges to help protect local biodiversity.
Although health, safety and environmental procedures can take time to introduce, develop and implement, organisations should prioritise considering all of these to improve and maintain the wellbeing of their most important asset: the workforce. Consulting with industry experts and securing locally relevant health experts to implement safety campaigns will help manage the challenges of maintaining safety best practice on pipeline projects, improving workers’ health and job performance, as well as reducing unnecessary recordables.
OUR BALL VALVES GO BEYOND THIS DISPLAY AND YOUR EXPECTATIONS!
1/8’’ - 56 ‘‘
CLASS 2500 AND HIGHER
Over the last two decades, growing quantities of data and better operational insights have benefited the process industries with profitable results. However, one large obstacle still frequently looms for pipeline operators, refineries, and petrochemical plants around the world: operational silos, which create barriers among departments, teams, and functions. The challenges presented by these silos become more pronounced when looking across the fence line for opportunities to collaborate with third-party business partners and vendors.
It is common for process manufacturing facilities to partner with outside companies – including original equipment manufacturers (OEMs), process chemical suppliers, catalyst vendors, reactor technology providers, and more – to optimise operational efficiency. While sharing information with these stakeholders traditionally had its challenges, new digital solutions are enabling better collaboration than ever before.
Modern technologies are providing access to disparate data sources in secure and centralised software ecosystems for plant personnel and external stakeholders, empowering outside subject matter experts (SMEs) to contribute equipment analysis and process insights. This expertise helps detect issues and provide early warnings of potential failure, a significant shift from the lookback analysis most of these specialists had grown accustomed to performing with access to limited datasets.
With enhanced monitoring and collaboration, all stakeholders benefit from increased trust, better working relationships, and increased workforce efficiency. The combination of these benefits improves overall production and product quality, while reducing equipment downtime.
Vendors often include performance monitoring services in the commercial arrangement when selling their technologies to refineries and petrochemical companies. Historically, this monitoring was executed retroactively, and in the few cases when live data was examinable, the data set was typically narrow. This created only after-the-fact and/or partial insights, informing recommendations for operating units efficiently to prevent upsets. Additionally, many issues that could have been mitigated with earlier insight were not identified until they created larger problems, such as reduced production quantity, quality, or compromised equipment integrity that could cause process safety or environmental incidents.
The greatest challenge to near-real-time performance analysis is providing safe and secure access to live time series data outside of the plant that can be fed to multiple third-party organisations.
Morgan Bowling, Seeq Corporation, USA, explains how advanced analytics solutions can help improve operational efficiency and increase business value for petrochemical companies, refineries, and pipeline operators.
The datasets of interest are often too large to share via email or traditional inter-organisational communication means. Historically, this was sometimes alleviated by USB data exchange – which carried its own set of security concerns – or file upload to a shared drive, such as Dropbox or SharePoint. But no matter the method, the data being shared was outdated before an export was sent to the third party, and even more so by the time an SME recipient was able to review it. Without an efficient and secure alternative, hindsight analysis became the norm, leaving SMEs with no ability to provide timely insights on live operations.
If third parties had access to end users’ process historians, these issues could be somewhat alleviated, but several security concerns remain with direct external access to such a critical information store and plant asset. Constrained by the datasets an end-user representative engineer provides them with, vendors can experience a ‘Goldilocks’ effect. While in some cases they may receive a ‘data dump’ – for example, a spreadsheet with little context, but seemingly unlimited rows and columns of information that bury relevant signals, requiring time-consuming filtering – in others, they may receive an incomplete dataset, preventing the ability to troubleshoot root causes in the process.
In both of these situations, the SME spends significant effort wrangling and cleansing data, or composing follow-up data refinement requests to the end user, leaving little to no time to perform meaningful analysis. Thus, vendors spend the bulk of their time manually manipulating data, rather than creating insights that drive business value.
Advanced analytics solutions, like Seeq, remove the manual work, and enable secure and continuous data sharing across fence lines. Additionally, these solutions help break down silos within a plant or across an enterprise, centralising information to provide context and facilitate sharing with the right parties (Figure 1).
The software as a service (SaaS) platform and built-in security components of these solutions enable users to create customised databases – sometimes utilising pre-defined structures in a process historian, such as AVEVA’s PI Asset Framework – for each thirdparty stakeholder, limiting access to relevant tags for particular analyses. For ad hoc analyses, end users can also choose to limit the time range of the data provided to external organisations.
At process manufacturing industry conference ‘Conneqt 2023’, a major US petroleum refining company shared how it empowered over 10 business partners, and more than 50 third-party collaborators, to access process data in near-real-time using Seeq. This solution enables teams to set up user groups, providing access to just the defined data sets and tags relevant to recipients’ equipment and technologies. Administrators can revoke access just as easily as it is granted to provide the right stakeholders access to the right data sets at only the right times.
Once third parties gain access to required data, they can begin digging into plant operations. Advanced analytics solutions provide intuitive self-service software tools required for cleansing, contextualising, and analysing large and complex data sets, minimising the time required to discover critical process insights about vendor-supplied equipment and technology.
For example, reactor technology provider Crystaphase is leveraging Seeq to monitor distribution in a client’s reactors to compare performance across different reactor cycles. Using the software’s Capsule feature to identify each cycle, the company can compare differences between product quality and feed during each run (Figure 2). This information is then used to provide recommendations for increasing product quality.
With access to this data, Crystaphase can combine reactor sample data collected from material inside the reactors with time series data from different reactor cycles. Combining these disparate data sets from multiple sources empowers SMEs to seamlessly identify the root cause of pressure drop limitations on certain cycles. In one instance, an alternate feed source supplying the reactor with contaminants was determined as the cause of pressure drop issues.
Enabling business partners like Crystaphase to simply perform analytics is one thing, but performing analytics at full scale is crucial to driving maximum value for all parties involved. For example, Honeywell UOP – an American multi-national company developing technology in the petroleum refining, gas processing, petrochemical production, and major manufacturing industries – deployed a monitoring project via templates for 40 different
Figure 1. Seeq, an advanced analytics solution, combines the data from numerous subsystems to create enterprisewide insights and facilitate data sharing specific to the level required by each software user.technologies by leveraging the open application programming interface (API) provided in Seeq. After the API was configured, implementation teams were able to swiftly deploy monitoring to new units at their times of installation with the simple press of a button.
In addition to adding value for end users, the API improves efficiency for OEMs and technology providers in the support they provide. For example, Chad Bjorklund, Director of Software Engineering – Connected Solutions at Honeywell UOP, testified, “Just from an efficiency standpoint alone, we’ve seen US$1.5 million in savings.” Thanks to these improved workflows, the company’s teams now spend most of their time working directly on detailed analyses instead of manually wrangling data.
Honeywell UOP’s approach enabled monitoring capabilities for over 3000 customers, and before the end of 2023 the company plans to deploy another 6000. After deploying templates for monitoring at scale, it will shift focus toward triaging alerts from key process indicators using Seeq’s case management tools to prioritise customers requiring technical assistance.
By combining their technology expertise and the point and click tools in these software applications, business partners can automate reports for clients to reference daily, helping them optimise operations. This means vendors who used to receive data and process it to create client insights every few months can now provide automated insights to their clients each day. Access to data combined with self-service advanced analytics enables vendors to detect issues and generate alerts before disturbances impact production, reduce quality, or cause unplanned downtime.
Over the last decade, advancements of digital technologies have driven increased data analysis and collaboration between end users and their business stakeholders, removing data access barriers and building new levels of trust between the organisations. Vendors can now access the data required to ensure their products are working in the most effective ways possible for end users, while plant personnel can take full advantage of the technical services provided with purchased equipment and technology.
Process engineers must carefully prioritise their work each day because most working environments require them to act as ‘jacks of all trades’, and their time is too valuable to be consumed with manual data wrangling activities. Leveraging modern technologies, including advanced analytics solutions, they can now optimise entire process units from front to back with significantly reduced effort.
Secure access to data and analytics tools mutually benefits end users and vendors, freeing up valuable engineering time on both ends, while improving collaboration and reducing the frustrations of the data-sharing ‘Goldilocks’ effect. Instead of too much or too little data, SMEs can dial in the ‘just right’ solution to identify insights that provide the most business value.
Kirsty McDermott, National Gas, Andy Fuller, Pipeline Integrity Engineers, Neil Mackay, STATS Group, UK, and Wes Gardner, STATS Group, Canada, discuss the first use of an inline isolation tool in a high pressure UK gas pipeline and how approval, testing and live trials were used to gain assurance on new technologies.
Operators can often encounter difficulties in isolating sections of their pipeline to facilitate essential safe repair or maintenance activities. Traditional methods of performing maintenance or improvement work on an in-service pipeline include blanking or blinding
a pipeline section from the pressurised system, venting and purging or displacing the hazardous substance, or using intervention (hot tap installed) isolation tools to provide the required isolation. Depending on the infrastructure in place, it may not be possible to disconnect and blind or blank off the
pipeline, isolation valves may not be double block and bleed or do not sufficiently hold pressure, or there may be a downstream requirement which limits the duration in which a pipeline can be out of service, among various
other reasons isolating and performing maintenance on a pipeline can be challenging. Inline isolation plugs (pigs) offer an alternative when facing this issue, providing fully proven and monitored dual seal barriers that ensure the safe breaking of containment on pressurised systems in compliance with the highest industry standards.
National Gas
National Gas owns and operates the National Transmission System (NTS), a network of high-pressure gas transmission pipelines covering the UK, balancing the flow of highpressure natural gas between import terminals and the regional gas distribution networks, gas storage facilities, international interconnectors, power stations and other large industrial customers. The NTS consists of over 7500 km of buried pipelines and over 650 Above Ground Installations (AGIs).
As part of the innovation fund incentive on regulated gas transmission companies, National Gas explored the opportunity to investigate, and where viable, trial inline isolation tools for onshore pipeline use. Such tools propose to provide a non-intrusive method to interrupt product flow and isolate pipeline sections which require repair or maintenance, removing the necessity to perform hot work on a live pipeline or vent and flare pipeline inventory. Product flow in the pipeline is halted using an expanding packer to seal in the pressure and a series of mechanical grips to maintain the necessary resistive force and prevent tool slippage. The technology has been used commercially offshore, however offshore pipelines are designed with heavier wall thicknesses, such that the pipe-wall stresses induced by the tools when active remain acceptable. The acceptability of the tools for thin-walled onshore pipeline use had not yet been confirmed suitable for use by National Gas on its pipelines in the UK.
With a significant volume of remedial work planned on the NTS, particularly associated with valves and isolation joints, National Gas view inline isolation tools as potentially providing considerable benefit. If the technology could be verified for onshore use, it would provide another tool for pipeline maintenance going forward.
Research has previously been completed by the Pipeline Research Council International (PRCI) in the US, reviewing tools on the market, however National Gas required this work to be extended. The ultimate decision and output of the work requires changes to National Gas policies and procedures to support the operation of inline isolation tools in business-as-usual operation.
A review was carried out, aimed at understanding the current range of inline isolation tools and their applicability for use on National Gas Transmission pipelines; and assessing the potential impact inline isolation tool operation would have on current policies and procedures.
Figure 1. 48 in. Remote Tecno Plug installation, National Transmission System. Figure 2. 48 in. Remote Tecno Plug deployment, near Montrose, UK.The studies were split between five individual sections and detail specifically:
) A state-of-the-art review of the PRCI onshore inline isolation tool research work.
) A detailed summary of National Gas’s initial requirements for inline isolation.
) A review of the capabilities of inline isolation tool vendors with respect to National Gas’s requirements.
) An assessment of the impact of inline isolation tools on National Gas’s policies and procedures.
) An outline of the requirements for field trials of inline isolation tools in an onshore setting.
The previous PRCI study showed that inline isolation tools from current manufacturers can be used to isolate a 610 mm diameter, 9.525 mm wall thickness, grade X70 pipe at 108.6 bar(g) pressure, under laboratory conditions, for a period of 2 hours, with no slippage of the tool or leaks past the seals. Additionally, there was no plastic deformation of the pipe recorded.
Consequently, the study provided a promising outlook for the future use of inline isolation tools on thin-walled onshore pipelines. The study, however, left several questions unanswered, which required further consideration before the tools can be considered validated for onshore use.
It was therefore recommended that further work should be considered regarding:
) The use of the tools in the field, outside of laboratory conditions, paying particular attention to the presence of stresses (construction, thermal, ground loading etc.) which could occur in addition to internal pressure loading.
) The maximum length of time an isolation tool can safely be used in any one application.
) Whether the level of internal damage to the pipe wall is affected by the length of time the tool is in use.
) The use of the tool on pipelines with different diameters, wall thicknesses, grades, and pressures and how this affects stresses, damage and plastic deformation.
) Whether the damage caused by the tool to the internal pipe wall could contain microcracking or otherwise grow under the normal cyclic stresses of pipeline operation and what effect this has on the fatigue life.
) Whether internal pipe damage could occur in combination with plastic deformation in certain pipelines following tool use and what effect this would
have on the burst strength and fatigue life of the pipeline.
) Whether the tool can be used effectively on pipe sections with pre-existing damage, including low quality seal welds, and what the limits for this would be.
) Whether the tool can be used effectively in the same place on multiple occasions and what effect this would have on the level of plastic deformation, damage, burst strength and fatigue life.
National Gas outlined comprehensive requirements for inline isolation tools, addressing various factors such as pipe geometries, isolation pressures, material compatibility, and construction specifications. The tools must align with safety standards, considering data on potential pipe section conditions to assess the impact of tool operation stress.
In discussions with STATS Group and other vendors, it was determined that proposed tools require a pipelinespecific review for deployment suitability. While multiple vendors demonstrated capabilities within National Gas’s requirements, the need for additional off-field testing and vendor assessments was emphasised. The absence of detailed data on potential pipeline damage in the tool’s operation area was acknowledged, requiring further evaluation during the vendor assessment.
A policy review assessed potential impacts on National Gas’s existing documents. While minimal updates were needed for specified documents, two options were considered: drafting a standalone document or detailing supplementary requirements in existing documents. A field trial was recommended as a pilot exercise to shape supplementary requirements after trial completion, streamlining future document revisions.
It was identified that inline isolation tools have been used on offshore and onshore liquid/gas pipelines. However, given that its application is not widespread, e.g. in comparison to inline inspection, it is considered appropriate to conduct controlled offline and online trials for what would be National Gas’s first application of this technology.
An offline trial took place at STATS Group’s Aberdeenshire facility using a spool which is representative of the planned location of the online trial. Upon successful completion of the trial a report was issued to recommend future use of the technology, procedure requirements and progress with planning for the online trial.
National Gas appointed DNV to support them during the offline trial with a mock-up installation testing the STATS Remote Tecno Plug inline isolation tool. DNV conducted a comprehensive strain gauge assessment during factory and field tests. Various materials, such as X65 and X80, were evaluated, with strain gauge readings indicating strain responses during tool deployment and retrieval. The results highlighted the importance of limiting isolation pressures due to increased stresses during tool engagement. Additionally, the assessment emphasised the need for cautious pressure management, especially in high-stress pipeline sections.
Assessing damage caused by the isolation tool’s gripping system, the study concluded that while grooved damage occurred, it did not compromise pipeline integrity. Metallurgical assessments demonstrated that the toolinduced damage did not extend beyond acceptable limits and did not adversely affect pipeline products.
A live field trial of STATS Remote Tecno Plug technology was conducted at St Cyrus, near Montrose in Scotland. The Remote Tecno Plug successfully sealed a 56 km long, 48 in. pipeline, ensuring a leak-proof and fail-safe isolation. It maintained full pressurisation at 55 bar in the initial use of the isolation tool on the National Transmission System. The technology offered secure double blocking and monitored isolation, allowing safe and efficient maintenance activities, such as welding.
The field trial enabled additional measures to be undertaken to understand integrity threats from the
deployment, setting, un-setting and lasting (potential) defects left on in the pipe wall and structure.
In addition to operational phase tests, extensive integrity tests, independently evaluated by specialist engineering third parties, DNV and Pipeline Integrity Engineers (PIE), were conducted to ensure the technology’s reliability and safety. This work will allow for future projects to consider isolation tools in different applications.
These additional measures have demonstrated and given assurance that the use of the Remote Tecno Plug has not presented any unacceptable integrity threats to National Gas’ pipeline from its use. An inline inspection of the pipeline section will be conducted in the near future as a final assessment in the sequence of activities.
The working process (as detailed by the procedure) should generally be taken as a success and the good communication between all stakeholders helped overcome issues as they were identified, to the credit of all involved.
The launch procedure for the isolation tool is broadly in line with established inspection tool deployment processes, with the additional requirements for detailed location confidence in the launcher. The tool travel, setting, un-setting and the final retrieval back to the site are novel to onshore operations. These will require detailed updating of National Gas’s procedural documents.
Based on the live field trial project managers estimated that traditional venting techniques would have emitted 233 t of gas. However, the Remote Tecno Plug reduced emissions to 9.5 t, saving carbon dioxide released into the atmosphere, but also resulting in significant cost savings of over £100 000 of gas not wasted.
The UK has a legal obligation to reach net-zero emissions by 2050 to address climate change, but gas is still integral to the UK, keeping the lights on and industries fueled. It’s also important for the country’s energy security, making it resilient to demand spikes or pressures on the system. The gas industry is working to ensure energy demand continues to be met, while making improvements where possible to help reach climate targets – including the implementation of new technology like the Remote Tecno Plug.
Kirsty McDermott, Senior Engineer at National Gas, said: “Using plugs like the Remote Tecno Plug can greatly reduce emissions from temporary pipeline isolations. Carrying out the trial work allowed us to interrogate the integrity of our pipelines and ensure they continue to deliver energy to where it’s needed across the UK.”
Neil Mackay, STATS Group Senior Business Development Manager, said: “This was the first use of our innovative pipeline isolation plug technology on the National Transmission System. Further to this major step forward for onshore gas in tackling emissions during maintenance activities, additional existing technology on the market can be used to ensure pigging activities are performed with zero emissions, something which I believe should and will be adopted by wider pigging operations in net-zero committed nations.”
Elizabeth Corner speaks to the two winners of the PPIM 2024 YPI Award for Young Achievement: Kah Soon Chia (ROSEN Group) and Blake Villarrubia (Audubon Engineering).
Kah Soon Chia, Technical Solutions Specialist, ROSEN Group
Elizabeth Corner: Congratulations Kah Soon! What are your thoughts upon winning this award?
Kah Soon Chia: I am humbled for being nominated for such a prestigious award let alone winning it. To be associated with John Tiratsoo, one of the biggest contributors to the pipeline industry is definitely one of the highlights of my career. It motivates me to continue pushing boundaries and contributing to the pipeline industry.
EC: Can you describe your current job role in one sentence?
KSC: As a Technical Solutions Specialist for pipeline integrity, I help operators by tailoring the right asset care solutions for their
pipelines in consideration of their respective challenges, threats and risks.
EC: What has been your career highlight so far?
KSC: Being part of a team of design engineers to implement the use of aluminium sprayed coating on to a riser and spool tie-in section to reduce significant end expansions for an offshore pipeline in Southeast Asia. This was aided by an unconventional sliding wye tie-in which I help designed.
Four years into my career, I was asked to lead tenders across Asia Pacific. It was rewarding to manage very experienced multi-discipline Leads towards successful tender submissions and awards. It taught me budget, time, and people management.
I also contributed to the founding of YPP Malaysia and kickstarted the first few events leading towards the creation of the Pipeline Engineering Series in Kuala Lumpur.
EC: Who are your mentors or role models in the pipeline industry?
KSC: I’ve been fortunate to have met a lot of amazing people throughout my career including Hernando Caceres, John Stearns and Razwan Arshad. All of them have provided guidance and support towards my career and achievements.
Hernando Caceres (ROSEN VP Asia Pacific) was a friend long before we became colleagues. He introduced me to the field of integrity management and has been a strong supporter of my growth within my company and in YPP Malaysia.
John Stearns (now retired) is a true role model and mentor for engineering and project management. He was a Project Director for a long list of landmark development projects globally.
Razwan Arshad (ROSEN Global Business Field Manager –Integrity Solutions) accelerated my growth in pipeline integrity management and entrusted me with project and contract management responsibilities for key engineering projects across the region.
EC: What is your message to other young pipeline professionals. What makes this industry rewarding and attractive for young professionals?
KSC: This is the right industry to be in, and it also happens to be future-proof. Irrespective of the direction of the energy industry, pipelines will continue to play a vital role in the transportation of conventional and future fuels. A body (industry) can’t function without its circulatory system (pipelines).
I believe we can expect a lot of new and exciting pipeline projects in the future as the world focuses on energy transition. These projects will present new challenges and a need for new ideas. It is the perfect time and opportunity for young and innovative professionals to be part of this industry.
EC: What are your hopes for the future?
KSC: Being the first person to win the John Tiratsoo Award from Southeast Asia (SEA), I hope this achievement will inspire more pipeline professionals from the region to pursue excellence in their respective roles and to give back to the industry. May there be many more award winners and aspiring pipeline professionals
from SEA in the future. As future leaders of the industry, we play a vital role towards our industry’s long term energy transition and decarbonisation goals.
EC: What does a typical working day look like for you?
KSC: There really isn’t a typical day, besides turning on my laptop and then looking at my emails. Every day I would say is quite different in the nature of my role as a technical solution specialist. ROSEN deals a lot with inspections and integrity management related to pipeline assets and there are times when the client is aware of what is needed to ensure the right kind of integrity management of their assets. And there are times when things have not really turned out the way as planned, and they’re giving us an emergency call asking us to be involved and to recommend the best possible solution for their problem.
EC: I wonder what your career path has been to get here. Was it always going to be pipelines?
KSC: My first role was as a subsea pipeline engineer, so everything was offshore and I was focusing more on the greenfield side of things. So I did field development, and pipeline design from conceptual studies all the way up to what we would call as-built design, which means the pipeline has been installed and we just have to make sure that all documentations and drawings are consistent with what is out there. Then I met somebody from ROSEN and they were interested in looking for pipeline engineers. And I started to shift my role more to what we call the brownfield side of things, dealing with existing assets and integrity management.
EC: What would you say is the best thing about working with pipelines?
KSC: The interesting thing is that for something that is just so rigid, so cylindrical, there are just so many parameters, so many options, and so many conditions which can dictate the way in which a pipeline can work. Someone taught me at the beginning of my my job here at ROSEN that, instead of looking at things from a perspective of an engineer, you look at it from a perspective of a doctor. And you think as a pipeline engineer, you’re technically considered as a cardiologist for the industry. Yes, we can have the platforms, the wells, the reservoirs and the refineries, but we need the circulatory system.
EC: What is on your wish list for your pipeline career?
KSC: In the next five years I’d like to try and gain more experience in what the energy transition has to offer to the pipeline industry.
Blake Villarrubia, Project Manager, Audubon EngineeringElizabeth Corner: Congratulations to you, Blake! What are your thoughts upon winning this award?
Blake Villarubia: I felt extremely humbled and grateful to be recognised among such an accomplished group of individuals who have also demonstrated outstanding achievements. It is comforting to know that organisations exist to help recognise young professionals and all of their accomplishments and dedication towards the industry’s future.
June 11-13, 2024 Calgary, Alberta
globalenergyshow.com
Register for free at: www.worldpipelines.com
EC: Can you describe your current job role in one sentence?
BV: I am a Project Manager and Professional Engineer for Audubon Engineering, where I lead teams of industry professionals to execute various aspects of midstream projects, from conception to completion.
EC: What has been your career highlight so far?
BV: While I thoroughly enjoy my daily project work, my career highlight has to be through my involvement within industry organisations. Being involved in several organisations such as the INGAA Foundation, SGA, and YPP USA has allowed me to make impacts that have helped secure our industry’s future by ensuring talent is attracted and retained with it.
EC: Who are your mentors or role models in the pipeline industry?
BV: My industry mentors include Phil Gary, Travis St. Pierre, Max Hengst and Kevin Block, all at Audubon Engineering. Other mentors are Paul Amato at Iroquois Natural Gas and Suzanne Ogle at the Southern Gas Association. My industry role models are Toby Rice and Susan Waller.
EC: What is your message to other young pipeline professionals? What makes this industry rewarding and attractive for young professionals?
BV: This industry has a strong focus on career development and knowledge building for young professionals. There are support
systems within just about every company and organisation in the industry that young professionals can rely on to guide them and help them understand the industry and further their careers. Additionally, this is an exciting time to join the industry, there are significant technological developments ongoing to help establish a sustainable energy future. You have the chance to get in on the ground floor.
My advice for anyone looking to join the industry or new to the industry: get as involved as you can. Whether it is in technical organisations such as API or ASME, trade organisations such as INGAA or SGA, or young professional organisations like YPP USA or local groups, getting involved will bolster your network and career, give you a broader view of the industry, and enhance your sense of purpose.
EC: What are your hopes for the future?
BV: My hopes for the future are that this industry continues to focus on sustainable and responsible practices through fostering research on technological advancements, establishing new collaboration and partnerships, and maintain a skilled workforce through continuous nurturing that reflects the strength and resilience of our industry.
EC: I wonder what your career path into pipelines was and whether you always wanted to work in pipelines or you just sort of ended up there?
BV: It kind of fell into my lap, honestly. I graduated as a civil engineer from LSU and my sister was in the industry. She helped me get an internship for an environmental consulting firm, and I fell in love with it. I joined UPI in 2014 and worked on a couple of major greenfield transmission pipeline projects and really cut my teeth on some big projects. I moved into a project engineering role and then ultimately moved over to Audubon at the beginning of 2020.
EC: What would you say is kind of the best thing about the pipeline sector about working in the pipeline sector?
BV: I would say safety is is paramount for every operator I’ve ever worked with. We start each and every meeting with a safety moment. You can tell that everyone cares about the communities that that we’re servicing.
EC: Do you belong to any other pipeline groups or networking groups?
BV: I’m quite involved in a lot of organisations. I spent some time as the Secretary for Young Pipeliners International (YPI). We helped get started five or six other YP groups, including China, Malaysia, and Nigeria. I’ve been involved in YPP USA since February 2019 in various leadership roles, and right now I’m their industry chair. I work a lot with other industry organisations like the INGAA Foundation, PRCI, ASME, API, SGA, APGA, and AGA.
Talent attraction, retention and knowledge transfer are subjects that I’m pretty passionate about.
EC: Do you have a career goal or aspiration within the pipeline industry?
BV: To make a great and positive impact to the industry and communities we serve by being a force for positive change.
Markus Büchler, SGK, Switzerland, and Mark Glinka, EMPIT GmbH, Germany, draw conclusions from measurements and assessments of different coating integrity techniques on buried pipelines, namely the newly developed current magnetometry inspection.
For the assessment of external corrosion protection, coating integrity evaluation methods are often carried out on buried pipeline systems. In contrast to the commonly used direct current voltage gradient measurement (DCVG), the newly developed current magnetometry inspection (CMI) offers significant advantages. For the operator, the question
Buried pipelines are usually protected from integrityrelevant wall thickness reductions with external corrosion protection consisting of a combination of a coating and cathodic protection (CP). The effectiveness of CP must be demonstrated based on ISO 15589-1 by means of the measurement of the IR-free potential (E IR-free) on individual coating defects by means of the intensive measurement (IM) that is based on a combination of a close interval potential survey (CIPS) and a direct current voltage gradient (DCVG). Additionally, the requirements of the ISO 21857, with respect to stray current interference and the ISO 18086 must be taken into consideration. The task now is that the determination of the EIR-free potential on modern pipelines is difficult due to the high quality of the coating and the associated small coating defects. The small voltage gradients usually prevent the calculation of the E IR-free on modern pipeline systems. As a result, demonstrating compliance with normative and legal requirements is often complex. This is further complicated by the often increased AC and DC interference. 1
Given these difficulties with respect to the assessment of the E IR-free, a DCVG survey is often performed with increased potential swing (i.e. at a significantly more negative on potential) to demonstrate the absence of major coating defects on the external pipeline coating. By excavating and re-coating, a direct proof of the corrosion state and the restoration of the local defect-free condition is achieved. It is observed that only in very few cases the excavation of the thus identified coating defects was actually necessary from an operational perspective. In most cases the exposing of the coating defect reveals that CP was effective and that the metal at the coating defect did not suffer from active corrosion. Therefore, the assessment of pipeline integrity is often carried out using inline inspections (ILI) with magnetic flux leakage (MFL) or ultrasonic (US) measurement. These provide direct information on wall thickness reduction and are therefore able to deliver optimised integrity assessments. Correspondingly they reduce the number of unnecessary excavations.
However, ILI can only be applied on appropriately designed pipelines in the transmission network. In the distribution network or for unpiggable lines, no alternative methods exist for fault location and excavation to date. The technology developed in Germany by EMPIT for evaluating pipeline integrity based on CMI now offers an alternative and innovative possibility for a more in-depth assessment of pipeline integrity and the effectiveness of corrosion protection.
arises regarding the comparability of the methods. Therefore, measurements were carried out with both DCVG and CMI to draw conclusions about the transferability of the respective measurement results. These results and an evaluation are discussed in this article.
The corrosion protection by means of CP is based on electrical currents. These can be directly detected with electromagnetic measurements, which makes it possible to precisely locate coating defects. There is no need to increase the potential swing by shifting the on-potential (Eon) to more negative values. Therefore, it is possible to precisely locate coating defects without increasing the risk of alternating current corrosion and coating disbondment due to increased cathodic polarisation. Furthermore, the method fundamentally offers the possibility to capture additional
Figure 1. Schematic measuring principle of DCVG, where the CP rectifier is used as the current source. Figure 2. Schematic measuring principle of alternating CAM, where in addition to the CP, a transmitter/signal generator injects the alternating current signal into the pipeline.relevant parameters, which are necessary for evaluating effective corrosion protection at each coating defect. Thus, the procedure has the potential for a comprehensive description of the corrosion-relevant characteristics of a defect. This article presents the measuring principle as well as field experiences with its application.
For ensuring the integrity of cathodically protected buried pipelines, methods such as DCVG in combination with exposure and repair of coating defects, IM (based on combined CIPS and DCVG), and ILI for detecting wall thickness losses due to corrosion are used. Although ILI is widely recognised as a tool for ensuring the integrity of pipelines and preventing corrosion damage, many pipelines are designed in such a way that ILI is not possible, leading to these pipelines to be classified as unpiggable. These pipelines can only be assessed for the effectiveness of corrosion protection by direct evaluation of external corrosion (external corrosion direct assessment, ECDA). The methods applied for ECDA typically involve connecting an external power source, with direct current (DC) or alternating current (AC) between the pipeline and an earthing system. Consequently, at the existing coating defects, there is a current transfer between the electrolyte and the pipeline. This current is associated with a voltage gradient (VG) in the soil. The voltage gradient can be easily determined by measuring the voltage between two electrodes placed on the soil surface above the pipeline. Depending on the type of source (AC or DC), the method is referred to as DCVG or ACVG.
The schematic measurement setup is shown in Figure 1. These voltage gradient-based methods have significant drawbacks. The most important is that an electrolytic contact of the electrodes to the soil is required. Additionally, other buried metallic structures as earthing systems or other pipelines influence the measured voltage gradient, leading to erroneous results. In a typical urban environment with asphalt surfaces and a significant number of buried metallic structures, conducting these measurements based on voltage gradients and interpreting the data is challenging. Furthermore, increasingly dry conditions make voltage gradient measurements difficult or even impossible. The need for electrolyte contact is overcome by the method of current attenuation measurement (CAM). This method is based on measuring the electromagnetic field generated by the AC current fed into the pipeline by the signal generator. The schematic setup is shown in Figure 2.
The measured electromagnetic field is proportional to the current in the pipeline and therefore allows for an assessment of the current distribution along the pipeline. Defects can be identified by a decrease in the pipeline’s current. The resolution of the method is mainly influenced by the resolution limitations of the CAM and the amplitude of the leakage current from the pipeline through the defect into the soil. Large leakage currents can readily be detected
with state-of-the-art CAM devices. However, the smallest defects, which are frequent in the case of high-quality coated pipelines, are generally not detectable. Additionally, CAM is significantly affected by metallic components near the pipeline that disturb the electromagnetic field, severely limiting the detection of the smallest coating defects, especially in urban areas. Accordingly, CAM solves the problems with
or very dry surfaces, but can usually
paved Figure 4. Measurement setup for the CMI. The trailer on the left contains the signal generator. The sensor arrays are integrated into the portable detector (yellow), and above the detector is the Starlink antenna, which sends the large amount of data directly to the cloud for immediate processing. Figure 5. Results of defect localisation with CMI and DCVG, with the signal strength normalised to the highest value. The vertical line at about 800 m marks the position of the test coupon.only be applied for larger coating defects remote from other buried infrastructure.
The identification and localisation of coating defects is a key aspect of ECDA, and the reliability of ACVG, DCVG, and CAM is significantly affected by external conditions, especially by metallic components in the soil. However, even if these methods show very high reliability in identifying defects under ideal conditions, they do not provide information about the effectiveness of cathodic protection. The presence of a defect only indicates contact between the pipeline and the soil and thus the possibility of corrosion. But in the case of pipelines protected with CP, the increase in pH (increase in alkalinity) at the steel surface and the subsequent formation of protective films over the surfaces of the anodes reliably prevent corrosion as has been reported by Robert Kuhn. 2 The relevance of protective surface films for the effectiveness of CP has later been emphasised by Leeds. 3,4 This accumulation of alkalinity and the associated film formation is particularly enhanced for well-bedded coating defects in sand and/or in water with increased hardness that results in the formation of calcareous deposits. 5 In the case of these ideal bedding conditions the accumulation of alkalinity and the generation of conditions conducive to passivation are ensured. This good bedding and the formation of protective oxide layers in the form of passivation steel as a result of the installed CP significantly contribute to the corrosion protection of defects. Accordingly, it is not economically sensible in pipeline operation to eliminate all coating defects through excavation and coating repair. Instead, a method is required that not only allows for the identification of coating defects but also provides further information about bedding conditions, the presence of calcium carbonate layers, the increase in pH, the formation of protective oxide layers, the size of the defects, and their spread resistance. Based on this information, a comprehensive assessment of the corrosion situation can be made, and the number of excavations can be significantly reduced.
The newly developed CMI, like CAM, is based on alternating currents. These currents are generated using a measurement technique controlled by AI and an intelligent signal generator. Therewith, dynamically adjusted frequencies are then applied to the pipeline. This offers improved possibilities for evaluating corrosion protection, summarised as follows:
) The signal generator uses at least four frequencies ranging from 2 - 2000 Hz, allowing for frequencydependent capture of spread resistance and phase shift, which provides insights into ohmic and capacitive contributions to current flow from the pipeline through the coating defect into the soil. These data can provide relevant information with respect to the formation of protective layers on the steel surface.
) Magnetic field detection is not limited to a few parallel sensors; multiple sensor arrays are used, capturing vectorial components of the field in all three spatial directions (Figure 3). This allows for precise 3D location and depth determination of the pipeline, and detection of small field components perpendicular to the pipe with high precision.
) Communication between the signal generator and detector allows for targeted variations in frequency and amplitude at identified defects, to provide further descriptions of bedding conditions and pH values in the soil.
CMI enables high-precision identification of coating defects without having to shift the E on in a negative direction in order to increase the potential swing. In the case of CMI this is possible thanks to significantly increased use of up-to-date technology with respect to the signal current generation, the number and precision of the sensors as well as the data storage and processing. This is evident from the required equipment (Figure 4). Instead of a signal generator of the size of a battery-operated briefcase for SAM, an entire trailer is needed. Additionally, the geometrically defined arrangement of numerous sensor arrays requires a much larger detector. This detector provides exact position data in relation to location, distance from the ground surface, and inclination. The CMI data assessment and evaluation is performed with a lateral resolution of 1 cm at a measurement frequency of over 100 kHz along the pipeline. The resulting big data volumes are sent via a Starlink antenna to the cloud for direct processing.
Therefore, CMI represents an advancement of CAM, utilising all most advanced technologies available today. This new approach is expected to provide for the first time the information required to significantly reduce the number of operationally unnecessary excavations. This not only leads to cost savings but can also greatly reduce excavation work in urban areas and the associated noise emissions and traffic disruptions.
In order to evaluate the reliability of both DCVG and CMI, measurements were carried out on a section of the Transitgas AG pipeline (Figure 4) using both methods. This pipeline section, built in 1973, runs from the southern bank of the Rhine River to the Wallbach station, with a length of about 1433 m. The pipeline has a nominal diameter of 36 in. (914.4 mm) and a wall thickness of 12.7 mm. The corrosion protection consists of a bituminous coating with a thickness of about 5.5 mm.
The E on was approximately -2 VCSE. A reduction of the E on in the negative direction was not performed in order to prevent any negative effects with respect to AC corrosion or disbondment of the coating. For objective control of the reliability of both methods, a coupon with 1 cm2 was installed at a depth of about 80 cm.
The data provided by the CP contractor is shown in Figure 5. It is clear that CMI identified a significantly larger number of coating defects including the 1 cm2 coupon (vertical line at about 800 m in Figure 5). The two coating defects identified by means of DCVG are confirmed by CMI. However, a number of additional coating defects as well as the 1 cm2 coupon were not detected by means of DCVG under the given measurement conditions.
The results in Figure 5 demonstrate CMI’s high resolution in localising defects without increasing the potential swing by significantly shifting the Eon in cathodic direction. To verify the plausibility of the measurement results, an excavation of a defect on a pipeline with 3LPE coating in Switzerland was carried out. This defect was identified by CMI but was not confirmed by DCVG. The results of the excavation are shown in Figure 6.
It was found that the CMI indicated the presence of two distinct coating defects, each with size of about 0.1 cm 2 (Figure 6, left). After removing the coating, it became clear that there was a large-scale disbondment of the coating with a surface of about 12 cm 2. Based on the available information the minor metal loss associated with the local corrosion effects, the voluminous corrosion products, and the disbondment of the coating are associated with AC corrosion. The visual appearance of the corrosion site is consistent with the typical effects described in references 1, 6 and 7, and DVGW GW 28 B1 in the case of a pipeline exposed to AC interference. 1,6,7,8 The corrosion effects at smallest coating defects, the formation of voluminous corrosion products, the large-scale disbondment of the coating, and limited corrosion are characteristic for AC corrosion.
The occurrence of AC corrosion clearly indicates that the pipeline section under investigation could be at risk due to AC interference (Figure 6). It has been reported that more negative Eon potentials can accelerate the corrosion process. 6 Therefore, from the perspective of pipeline integrity, it is ideal to perform high-resolution coating
defect detection without further accelerating alternating current corrosion and coating disbondment at more negative Eon.
The setup shown in Figure 2 is not only capable of detecting coating defects. More importantly, the continuous measurement of the electromagnetic field with high lateral resolution also enables the high-precision localisation of the 3D position of the pipeline as well as its burial depth.
Since the measurement resolution with CMI is significantly enhanced in terms of the number of sensors, data acquisition rate, lateral measurement interval, and the use of multiple frequencies, the method also allows for a precise determination of pipeline position and associated anomalies.
The excavation shown in Figure 6 was not only undertaken due to the detected coating defect. Rather, CMI identified a pipe bend that should not be present at that location according to the pipe book. During the excavation, this pipe deformation was indeed confirmed (Figure 7).
The slight deformation of the pipe in Figure 7 clearly demonstrates the high measurement resolution in terms of pipeline positioning that can be achieved with CMI, due to the large number of sensor arrays and the high lateral measurement resolution of 1 cm along the pipeline. These measurements illustrate that CMI significantly surpasses the capabilities of DCVG and provides additional important information regarding pipeline integrity assessment. The accurate capture of the pipeline’s exact position and the determination of changes in position and geometry over the years are just some of the key advantages of CMI.
Mechanical stresses in the pipe resulting from shifts in pipeline position are particularly relevant when repurposing pipelines for hydrogen transport. With CMI, it is possible to estimate mechanical stress and locate defects in a single measurement run. This allows operators to efficiently assess and document the condition of the facility for its transformation, a crucial element for safe continued operation with hydrogen.
The method, in combination with appropriate numerical simulation, allows for the quantification of the current passing into the soil through the defect and the calculation of the pipe to soil potential. This immediately allows for calculating the spread resistance of the identified coating defects for the various applied frequencies, providing crucial insights into the corrosion-relevant conditions at each defect. Notably, these methods enable a further evaluation of the large number of identified defects without the need for their costly excavation. These capabilities of CMI will be further investigated in a research project funded by the German Gas and Water Association (DVGW) starting in March 2024.
The measurements performed with CMI allow for important conclusions regarding the capabilities both in terms of defect localisation and further evaluation of pipeline integrity. The discussed results can be summarised as follows:
) CMI enables high-resolution localisation of coating defects on pipelines without shifting the E on potential in a cathodic direction. This allows for maintaining optimal CP conditions during measurement, which is significantly advantageous for corrosion protection: increased risk of alternating current corrosion or enhanced coating disbondment can be prevented.
) CMI’s reliability in defect detection under normal CP conditions is significantly higher than that of DCVG. The defects detected by CMI were confirmed by DCVG indications, in the excavation, and with the test probe/coupon.
) The number of defects identified with CMI is typically significantly higher than those of DCVG. While this may seem unfavourable from an operational perspective, CMI’s capability for further evaluation of the corrosion protection of the defects leads to a more reliable identification of defects, better assessment of the state of external corrosion protection. Correspondingly the assessment of further corrosion relevant parameters does not require additional excavations. Instead, the identification of the most corrosion relevant coating defects usually allows for more targeted excavations.
) The additional determination of the seamless 3D pipeline position and geometry provides an important means to verify existing data and obtain digitised XYZ coordinates.
) From the pipeline trajectory the pipe displacements can be directly calculated. This allows for deriving mechanical stresses, which may be particularly relevant when using the pipeline for hydrogen transport.
Based on the available results, CMI is a reliable method that provides essential integrity-relevant information, extending far beyond the mere identification of coating defects.
1. M. Büchler, “On the mechanism of cathodic protection and its implications on criteria including AC and DC interference conditions”, Corrosion 76, 451 (2020).
2. R. J. Kuhn, “Galvanic Current on Cast-Iron Pipes”, Industrial and Engineering Chemistry 22, 7 (1930).
3. J. M. Leeds, “Cathodic-Generated Film Protects Pipe Surface –Part 1”, Pipe Line Industry 4, 39 (1992).
4. J. M. Leeds, “Cathodic-Generated Film Protects Pipe Surface –Part 2”, Pipe Line Industry, 37 (1992).
5. U. Angst et al., “Cathodic protection of soil buried steel pipelines – a critical discussion of protection criteria and threshold values”, Materials and Corrosion 11, 9 (2016).
6. M. Büchler, “Alternating current corrosion of cathodically protected pipelines: Discussion of the involved processes and their consequences on the critical interference values”, Materials and Corrosion 63, 1181 (2012).
7. M. Büchler, D. Joos, “AC-corrosion on cathodically protected pipelines: A description of the involved processes, the risk assessment and a new normative approach”, Ochrona przed Korozja 61, No. 8/18, 204 (2018).
8. DVGW GW 28-B1, “Determination of AC corrosion risk of cathodically protected steel pipelines and protection measures; Supplement 1: Modified criteria for AC voltage and on potential” (2018).