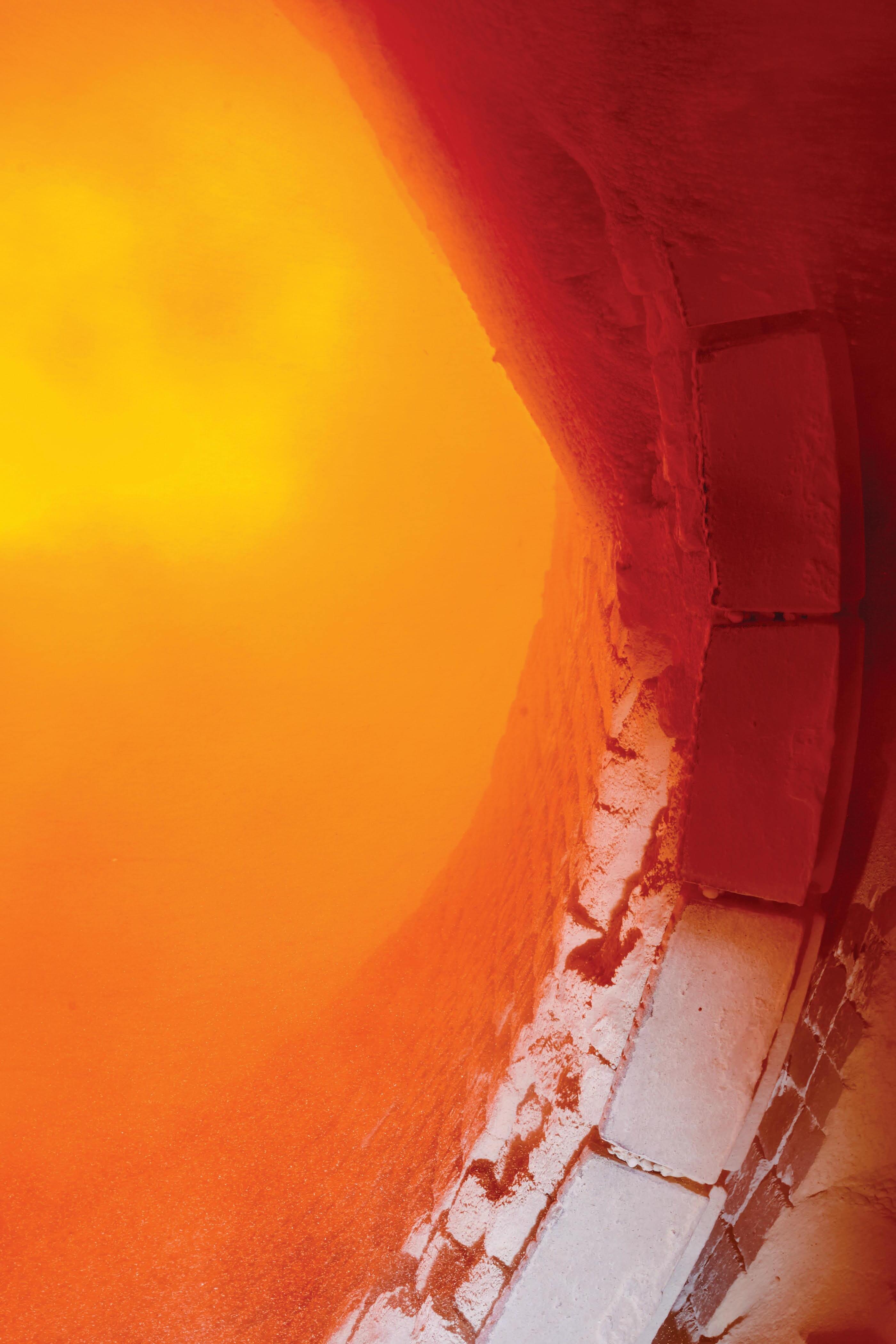
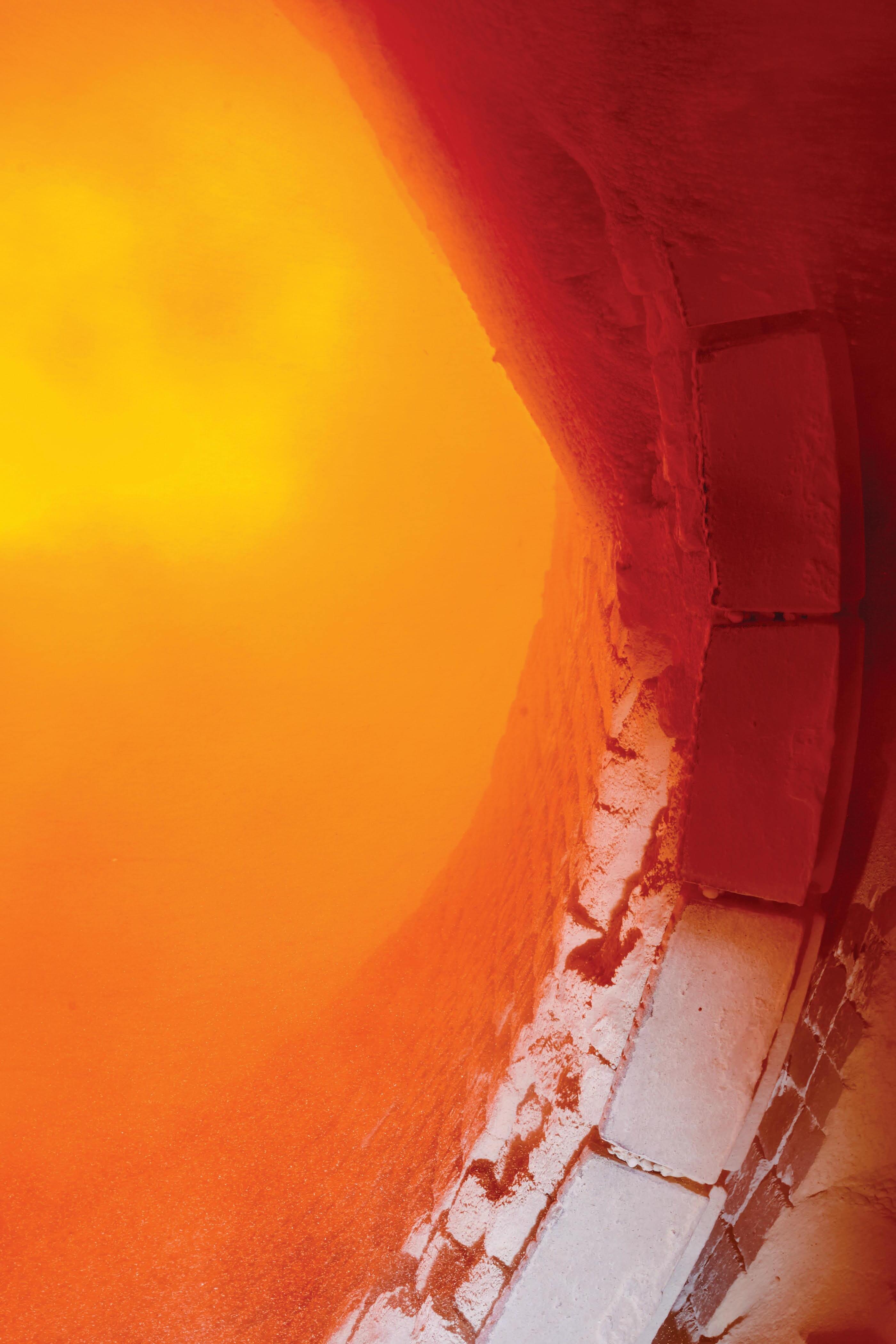
Art ificial Intelligence
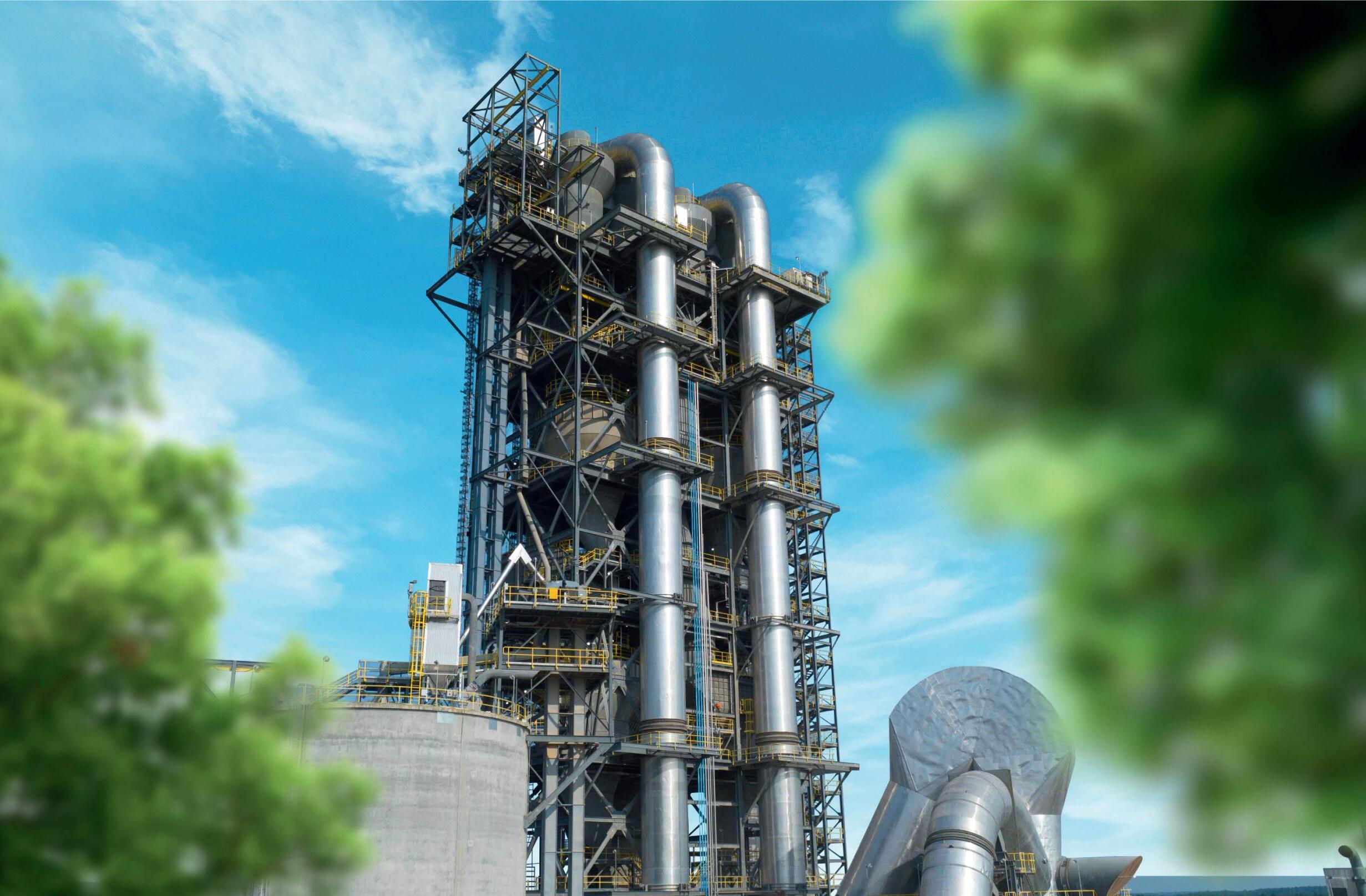
Enabling carbon capture with oxyfuel
Carbon capture is a critical technological pathway for cement decarbonization. That’s a challenge. But there are ways to make it easier. Like converting to oxyfuel combustion. Oxyfuel raises the CO2 concentration in cement plant exhaust gases and makes capturing that CO2 much more cost-efficient.
Here at KHD we’ve been involved in oxyfuel development since 2010. We also come with a long history of excellence in innovation, plant design, and process engineering. So, when it comes to implementing oxyfuel at your cement plant, we are your expert partner.
Discover more on our website or connect with our experts to discuss your specific oxyfuel application needs and let’s deliver Cement beyond Carbon together.
CONTENTS
03 Comment
05 News
REGIONAL REPORT
10 Year Of The Dragon?
SILOS & STORAGE
39 Supporting Silos
Martin Wuerth, Wuerth Consulting Engineers, discusses a cost-effective silo repair method that can extend silo lifetime by more than 30 years.
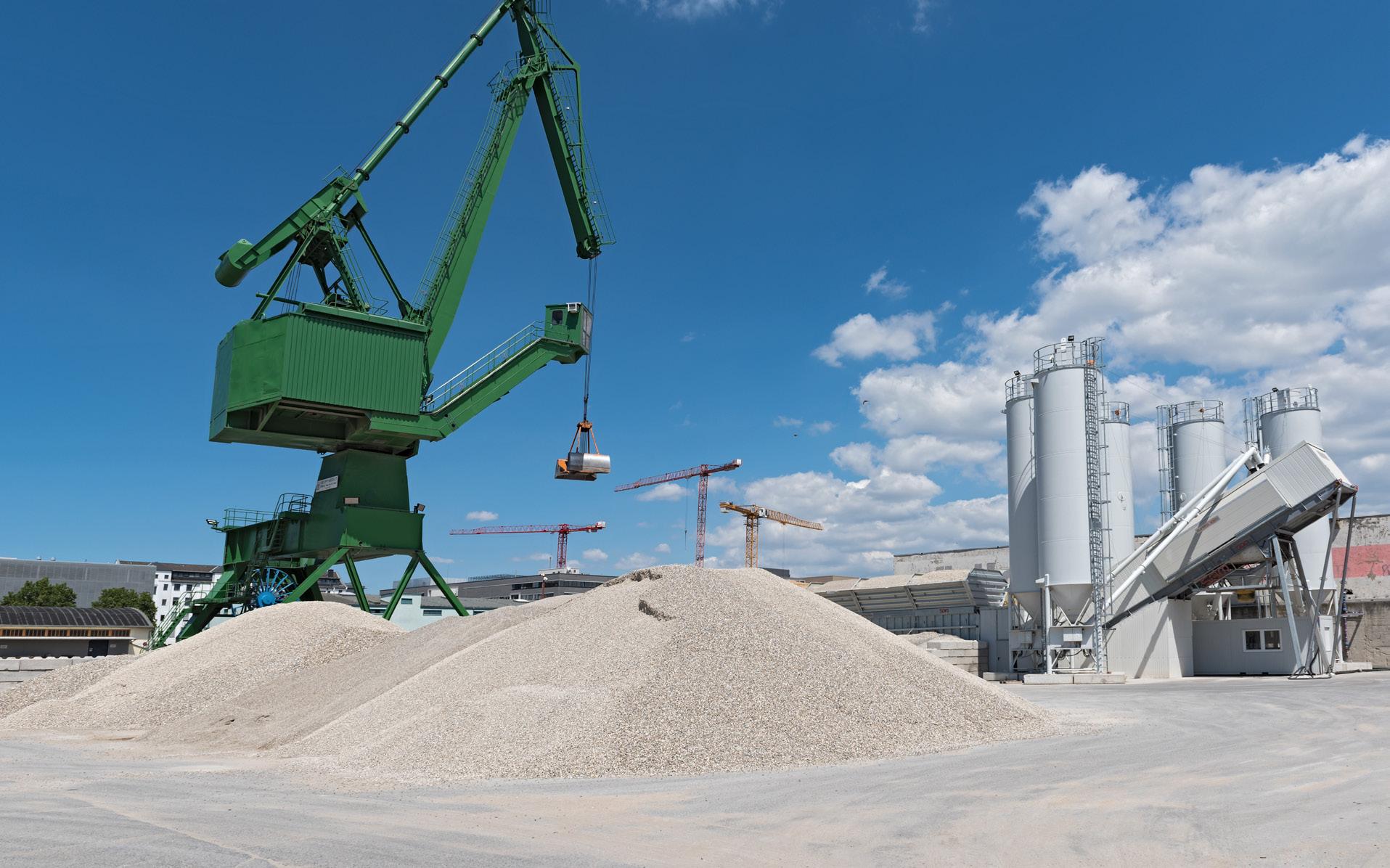
David Bizley, Senior Editor of World Cement, provides a brief overview of some of the factors facing the Chinese economy and the consequences for the construction and cement sectors.
REFRACTORIES
16 Sustaining Cyclone Efficiency
Preecha Chokjarearnsuk, HASLE Refractories, discusses the role of dip tubes in preheater cyclones and reveals how a new generation of ceramic vortex finder has performed for the ADBRI Birkenhead cement plant in Australia.
SOFTWARE, AUTOMATION & PROCESS CONTROL
22 Artificial Intelligence Turns Cement Production Green
Mark Israelsen, Quantum IR Technologies, explains how the use of AI analytics can help to reduce energy consumption and emissions in cement kilns.
26 Autopiloting The Cement Process
Fayez Boughosn and Ighnatios Maatouk, ES Processing, explore the benefits of autopiloting the cement manufacturing process.
30 All Eyes On AI
Chris Kiddle, AVEVA, explores the growing role of AI in the cement industry and considers both the benefits and the risks.
35 MPC, It’s Easy As ABC Juliano de Goes Arantes, Rockwell Automation, explains how cement producers can conquer their most complex processes with MPC.
ON THE COVER
CARBON CAPTURE
44 Capturing Tomorrow
Prateek Bumb, Carbon Clean, emphasises the importance of carbon capture for the cement industry to achieve net-zero goals.
48 Beyond Emissions
Jens Kristian Jørsboe, Jimmy Andersen, Christian Riber, and Burcin Temel McKenna, Ramboll, discuss the various carbon capture technologies and their advantages and disadvantages.
DECARBONISING CEMENT & CONCRETE
55 Advancing Mechanochemical Activation
A. Thomas, S.C. Liew, M. Pagels, & P. Suraneni, Carbon Upcycling Technologies, explore the use of enhanced mechanochemical activation to transform materials into SCMs.
61 CO2 Capturing Concrete Additives
Tim Sperry, Carbon Limit, explains how merging direct air capture (DAC) technology with carbon mineralisation can help diminish the carbon footprint associated with cement and concrete production.
The use of AI in the cement industry is increasing at a rapid pace with a focus on moving to more efficient management.
Mark Israelsen of Quantum IR Technologies outlines the capabilities of AI solutions when it comes to reducing energy consumption and emissions in cement kilns on pg. 22.
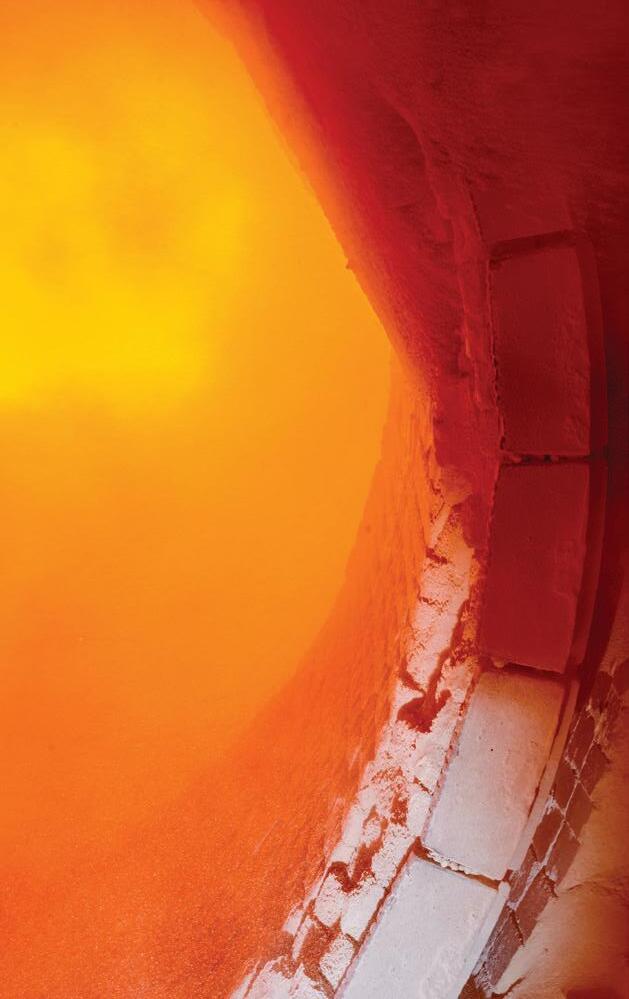
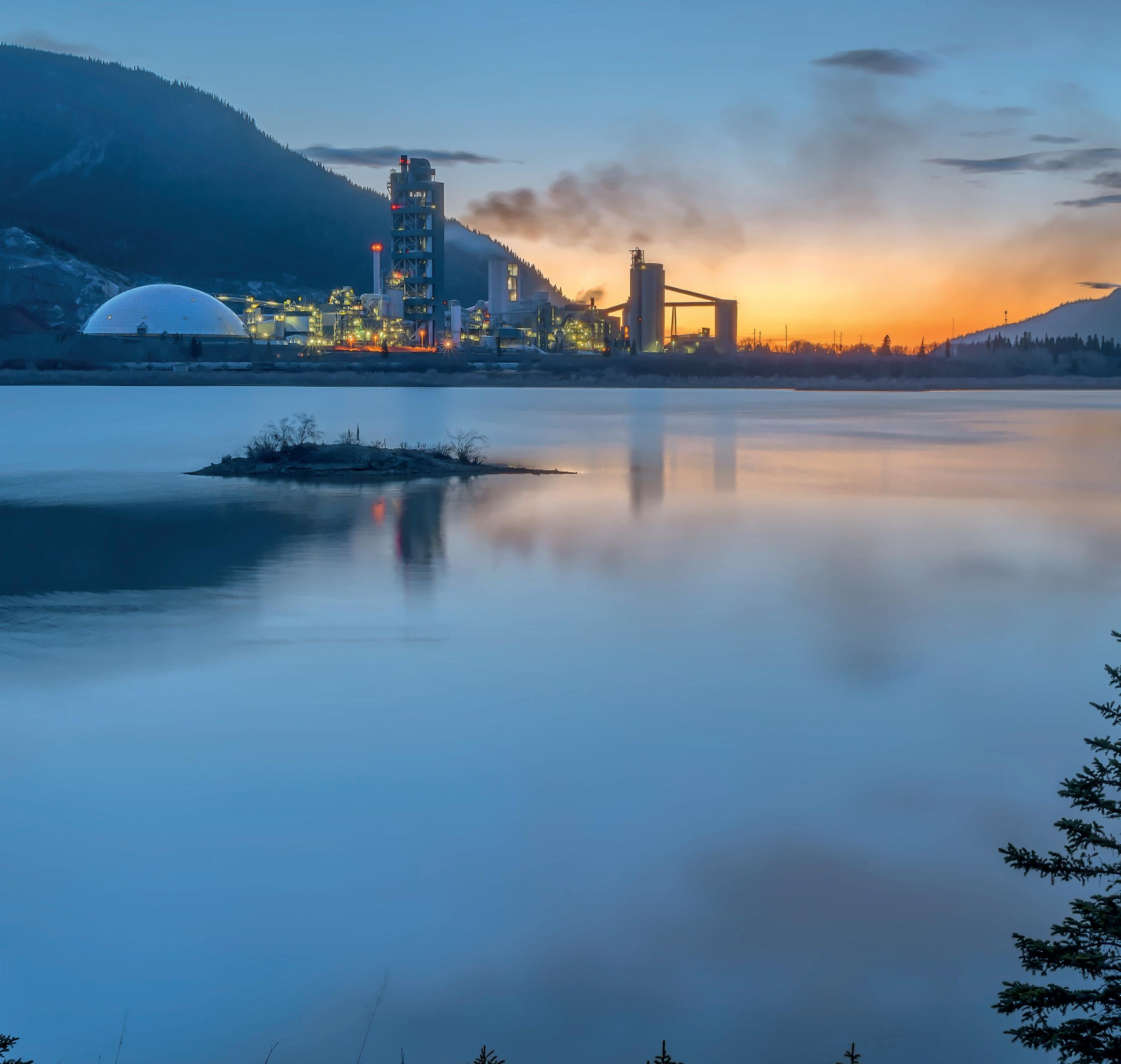
WE MOVE INDUSTRIES
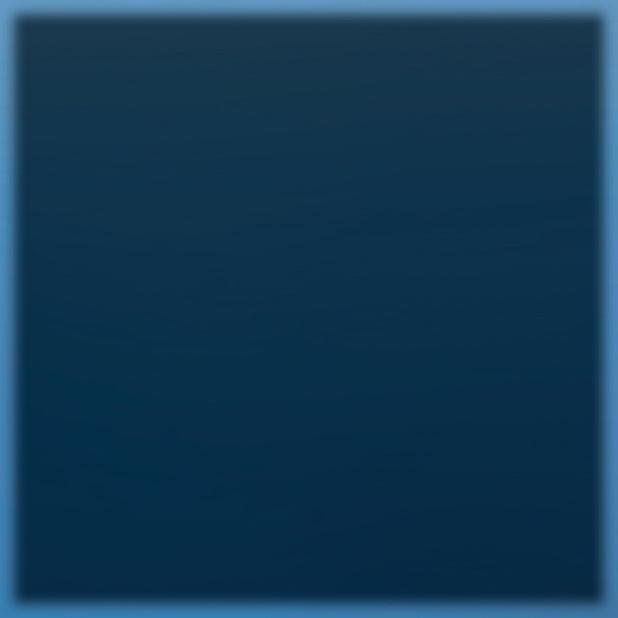
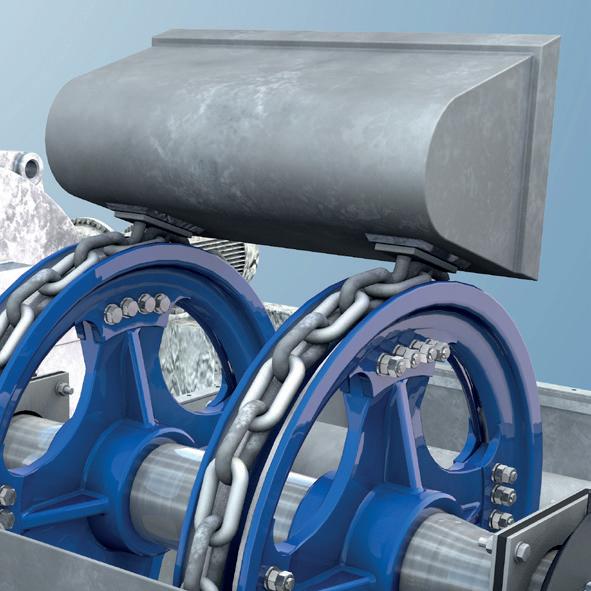
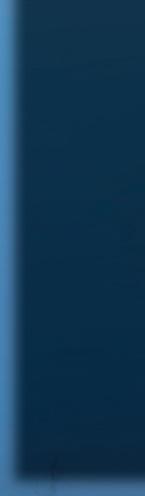
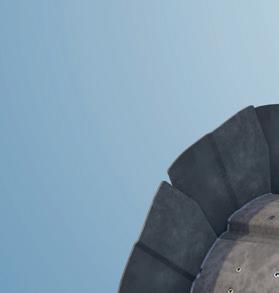
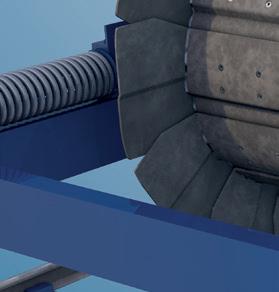
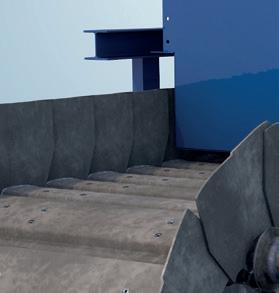
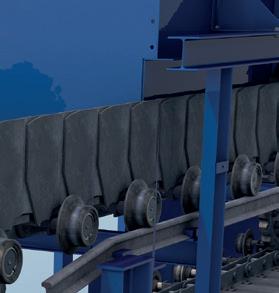
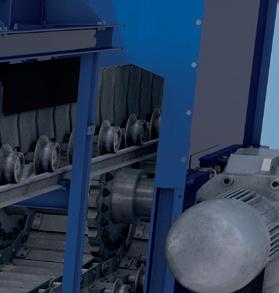
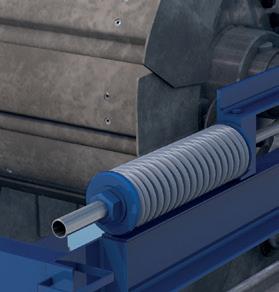
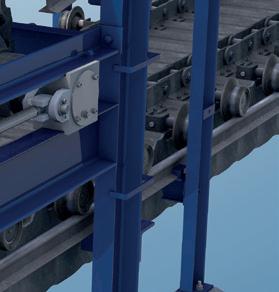

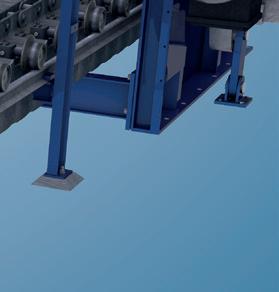
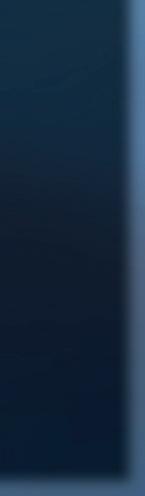
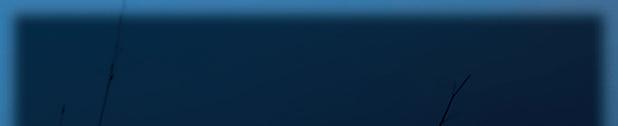
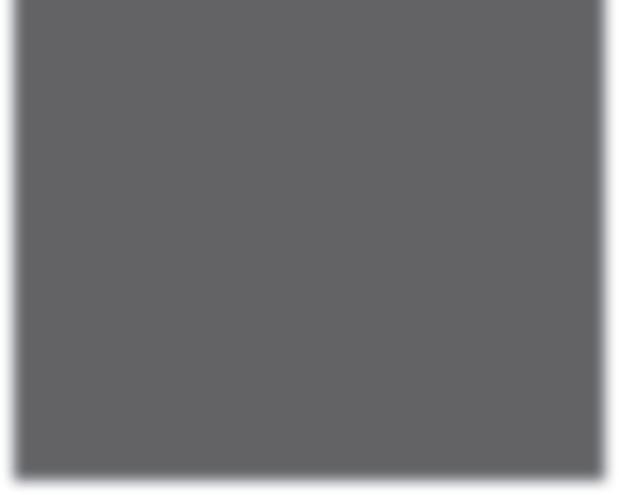
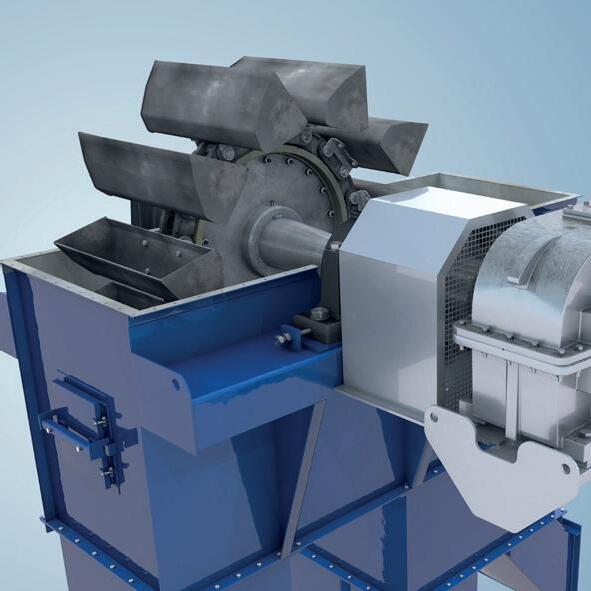
HEKO offers the whole range of chains, rollers, sprockets and scrapers for reclaimers. HEKO products are proven in thousands of bucket elevators and conveyors, worldwide.
Our components for the cement industry: central chains, link chains, reclaimer chains, sprockets, bucket elevators and clinker conveyors.
MORE THAN
COMMENT
rod.hardy@palladianpublications.com
Sales Manager: Ian Lewis ian.lewis@palladianpublications.com
Sales Executive: Louise Graham louise.graham@palladianpublications.com
Events Manager: Louise Cameron louise.cameron@palladianpublications.com
Digital Events Coordinator: Merili Jurivete merili.jurivete@palladianpublications.com
Digital Administrator: Nicole Harman-Smith nicole.harman-smith@palladianpublications.com
Administration Manager: Laura White laura.white@palladianpublications.com Reprints reprints@worldcement.com
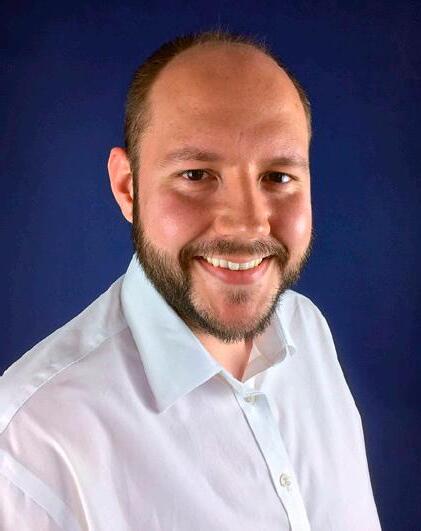
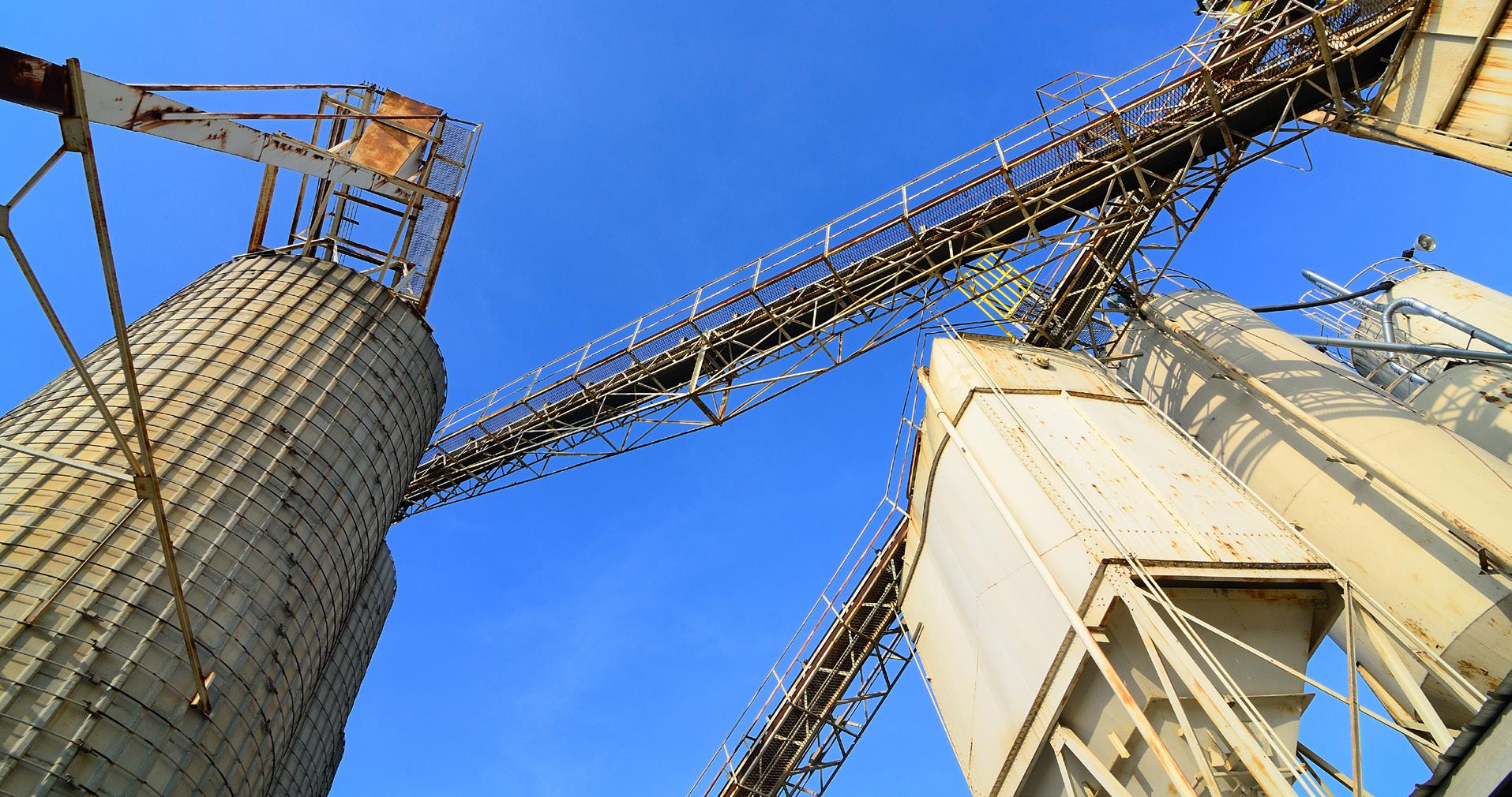
TCBP019982
SUBSCRIPTIONS
Annual subscription (published monthly): £160 UK including postage/£175 (€245) overseas (postage airmail)/US$280 USA/Canada (postage airmail). Two year subscription (published monthly): £256 UK including postage/£280 (€392) overseas (postage airmail)/US$448 USA/Canada (postage airmail). Claims for non receipt of issues must be made within 4 months of publication of the issue or they will not be honoured without charge.
Applicable only to USA and Canada: WORLD CEMENT (ISSN No: 0263-6050, USPS No: 020-996) is published monthly by Palladian Publications, GBR and is distributed in the USA by Asendia USA, 17B S Middlesex Ave, Monroe NJ 08831.
Periodicals postage paid at Philadelphia, PA and additional mailing offices. POSTMASTER: send address changes to World Cement, 701C Ashland Ave, Folcroft PA 19032
Copyright © Palladian Publications Ltd 2024. All rights reserved. No part of this publication may be reproduced, stored in a retrieval system, or transmitted in any form or by any means, electronic, mechanical, photocopying, recording or otherwise, without the prior permission of the copyright owner. All views expressed in this journal are those of the respective contributors and are not necessarily the opinions of the publisher, neither do the publishers endorse any of the claims made in the articles or the advertisements. Uncaptioned images courtesy of Adobe Stock. Printed in the UK.
Palladian Publications Ltd 15 South Street, Farnham, Surrey GU9 7QU, UK Tel +44 (0)1252 718999
Email: mail@worldcement.com Website: www.worldcement.com
May 2024 World Cement
DAVID BIZLEY, SENIOR EDITOR
he march towards net-zero cement production continues apace. One of the latest headline-grabbing stories comes from Holcim and the news that it has begun construction of one of the world’s first carbon-neutral cement plants in Lägerdorf, Schleswig-Holstein, Germany.
The plant, which is expected to be commissioned in 2028, will rely on technology from thyssenkrupp Polysius and Linde Engineering to enable carbon capture on an industrial scale, almost completely eliminating CO2 emissions from the site. The process gas is to be processed into high-purity CO2 and can subsequently be used as a starting material in the chemical industry or as a raw material in other industries, or even stored if needed. This process will be able to cut CO2 emissions from the Lägerdorf plant by around 1.2 million tpy.
Elsewhere in green cement news, TITAN’s Roanoke cement plant in Virginia, USA, has received an award from the US Department of Energy (DOE) worth US$61.7 million to support the first-of-a-kind development of a calcined clay production line. The award comes as part of the US$6.3 billion ‘Industrial Demonstrations Program’, which is managed by DOE’s Office of Clean Energy Demonstrations (OCED) and is primarily focused on CO2 reduction. Bill Zarkalis, President & CEO of Titan America, stated: “We are honoured to be selected for this first-in-the-nation initiative in spearheading the production of reduced emissions cement, helping lead our industry toward a net-zero future through deep decarbonisation technologies.”
Leonidas Canellopoulos, TITAN’s Chief Sustainability and Innovation Officer, added: “This initiative aligns with our Green Growth strategy’s focus on advancing cementitious materials, harnessing innovation and novel technologies. Building upon the successful pilot test conducted at our Patras plant in Greece, we are now scaling up the development of low-carbon calcined clays. Our dedication to sustainable solutions propels us as we stand among the frontrunners in leading the charge towards decarbonising the industry.”
If you want to hear more about these kinds of projects in person, but missed the chance to join the World Cement team in Lisbon for EnviroTech 2024, then be sure to register your interest for next year’s show at: www.worldcement.com/envirotech2025 today.
Following the same formula of high-quality presentations, expert-led panel discussions, and multiple networking opportunities, all located within a luxury venue, EnviroTech is an unmissable experience for those wishing to be at the forefront of the decarbonisation discussion.
And if you can’t wait until then, World Cement will be hosting the fifth edition of our flagship virtual ‘Optimisation’ conference on 22 October. Featuring a keynote presentation from Cementos Molins’ new Chief Technology Officer, Javier Sueiras, and technical presentations from industry leaders on topics such as digitalisation, AI, machine learning, and process optimisation. Stay tuned for more details, including a registration link, coming soon.
Ship unloaders
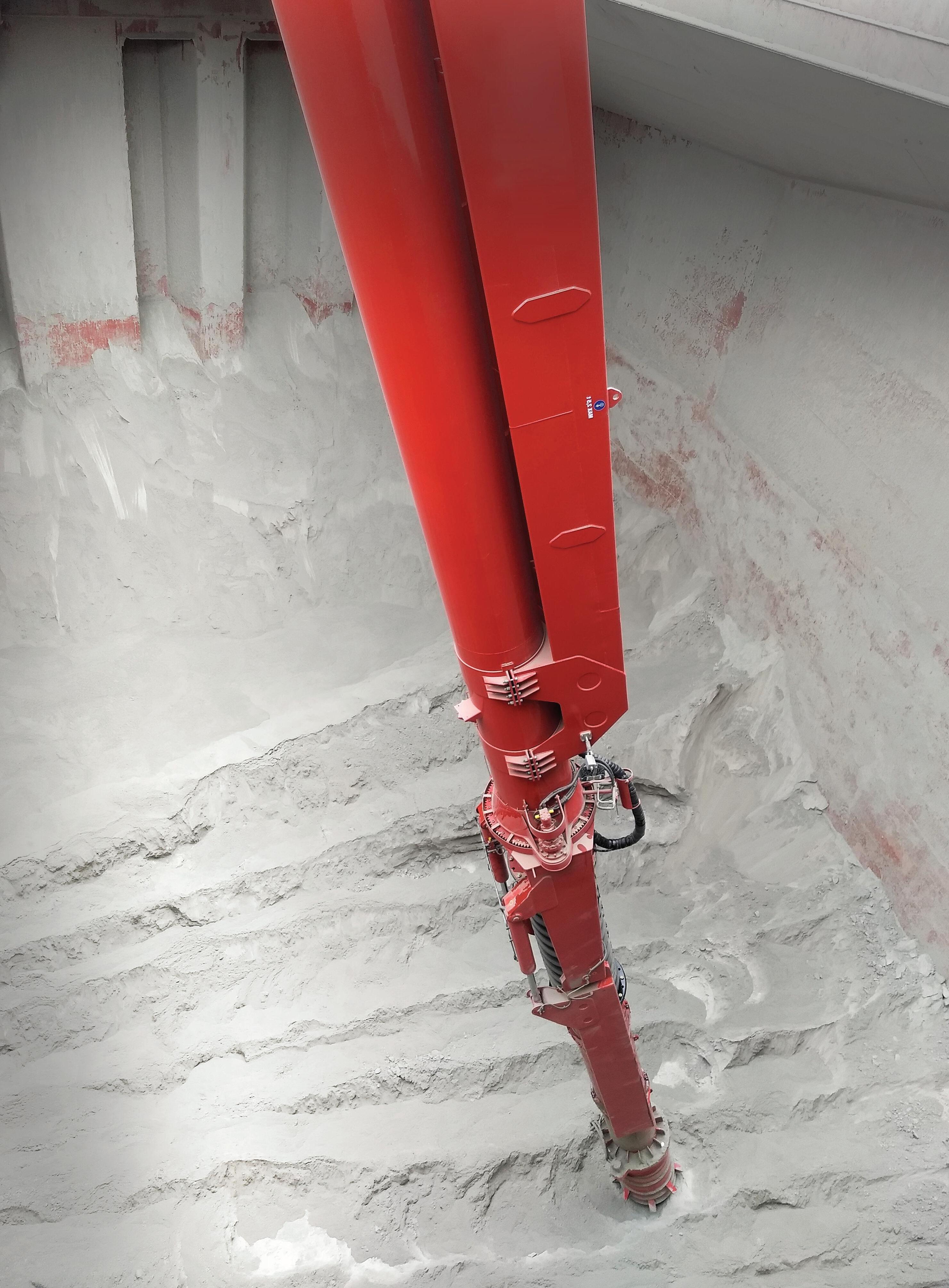
Road mobile ship unloaders
The answer to your bulk handling questions
Storage & reclaim
Convey units
Truck loading
Ship loaders
Groundbreaking ceremony for new CO2-neutral cement plant
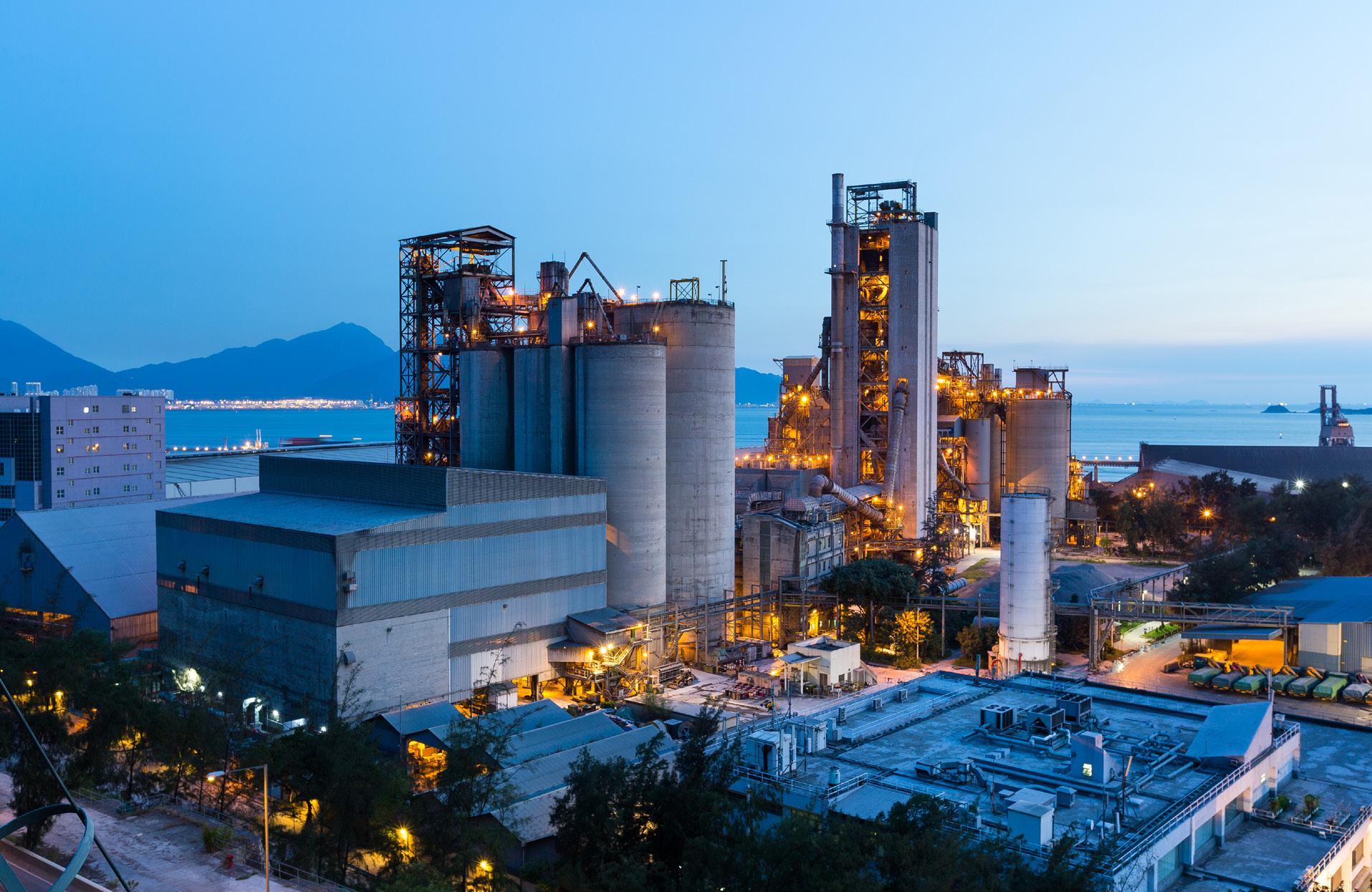
One of the world’s first climate-neutral cement plants is taking shape: Vice-Chancellor and Federal Minister of Economics Dr. Robert Habeck and the Minister President of Schleswig-Holstein, Daniel Günther, together with Holcim Germany CEO Thorsten Hahn, have initiated the ‘Carbon2Business’ innovation project in Lägerdorf.
By 2028, the site will be home to a cement plant that uses a new technology to capture CO2 on an industrial scale, enabling the greenhouse gas to be almost completely captured from the exhaust air. The CO2 will then be processed for use as a raw material in industry.
To this end, Holcim Germany is building a new kiln line using pure oxygen to burn cement clinker and a CO2 processing unit at the Lägerdorf plant. With this technology, Holcim and its project partners thyssenkrupp Polysius and Linde Engineering are advancing CO2 capture on an industrial scale and contributing to the development of a CO2 economy in Germany.
Federal Minister Robert Habeck: “The cement industry is facing a particularly big challenge when it comes to decarbonisation. Here in Lägerdorf, it is shown how it can be done: decarbonising production and boldly implementing climate-neutral production of cement and concrete. The fact that carbon dioxide can not only be captured, but also used as a raw material, is a prime example of green transformation.”
“Today we are giving the go-ahead for another innovative German industrial project. The prototype for the decarbonisation of the cement industry will be built on an industrial scale in Lägerdorf. This shows once again that the future is climate-neutral. And this future begins here in Schleswig-Holstein, the number one state for energy transition”, said Daniel Günther, Minister President of Schleswig-Holstein.
“We’re laying the groundwork for a sustainable world through cement”, asserts Thorsten Hahn, CEO of Holcim Germany. “Cement is essential for our cities, factories, homes, bridges, and beyond. As we transition towards renewable energy, we must also construct the foundations and structures for wind turbines and railway tracks. With our climate-neutral cement plant, we ensure that this vital building material remains accessible without further harm to
the atmosphere.” CO2 emissions are an inherent part of cement production. The burning process releases the majority of CO2, approximately two-thirds, from the minerals themselves. Even with the utilisation of renewable energy in operating the cement kiln, these emissions persist. Hahn emphasises, “Through this groundbreaking project, we’re fostering sustainable prosperity. By capturing and repurposing CO2 as a valuable raw material, we’re mitigating climate impact and facilitating the development of new value chains.”
In Lägerdorf, Holcim, alongside project partners thyssenkrupp Polysius and Linde Engineering, is erecting a second-generation oxyfuel kiln and a CO2 Processing Unit (CPU). Unlike conventional methods, this kiln will utilise pure oxygen instead of ambient air, yielding a process gas enriched with CO2. Subsequently, this gas undergoes purification and processing within the CPU. Holcim Germany’s investment in this climate-neutral cement plant totals in the mid three-digit million euro range. Additionally, the EU is providing funding support to the tune of approximately €110 million for the project.
Carbon is an important raw material for sectors such as the chemical industry, where it is used to make plastics, tyres, speciality chemicals and medicines. Due to climate protection measures and the phase-out of fossil fuels, the industry will need new sources in the future. Captured and processed CO2 (carbon capture and utilisation/CCU) can fill this gap.
The successful development of this market necessitates adequate infrastructure, encompassing pipelines, intermediate storage facilities, and transshipment hubs for shipping, alongside legal regulations for transportation. Hahn remarked, “The German government and the EU are addressing these issues in their carbon management strategies. As a partner, we stand ready to collaborate with policymakers to propel Germany’s CO2 economy forward.”
Holcim Germany has set ambitious decarbonisation goals. Alongside the climate-neutral cement plant in Lägerdorf, scheduled to commence operations in 2028, test projects are presently underway at other cement plants in Höver (Lower Saxony) and Beckum (North Rhine-Westphalia). These facilities are also slated for conversion, integrating technologies for capturing and processing CO2
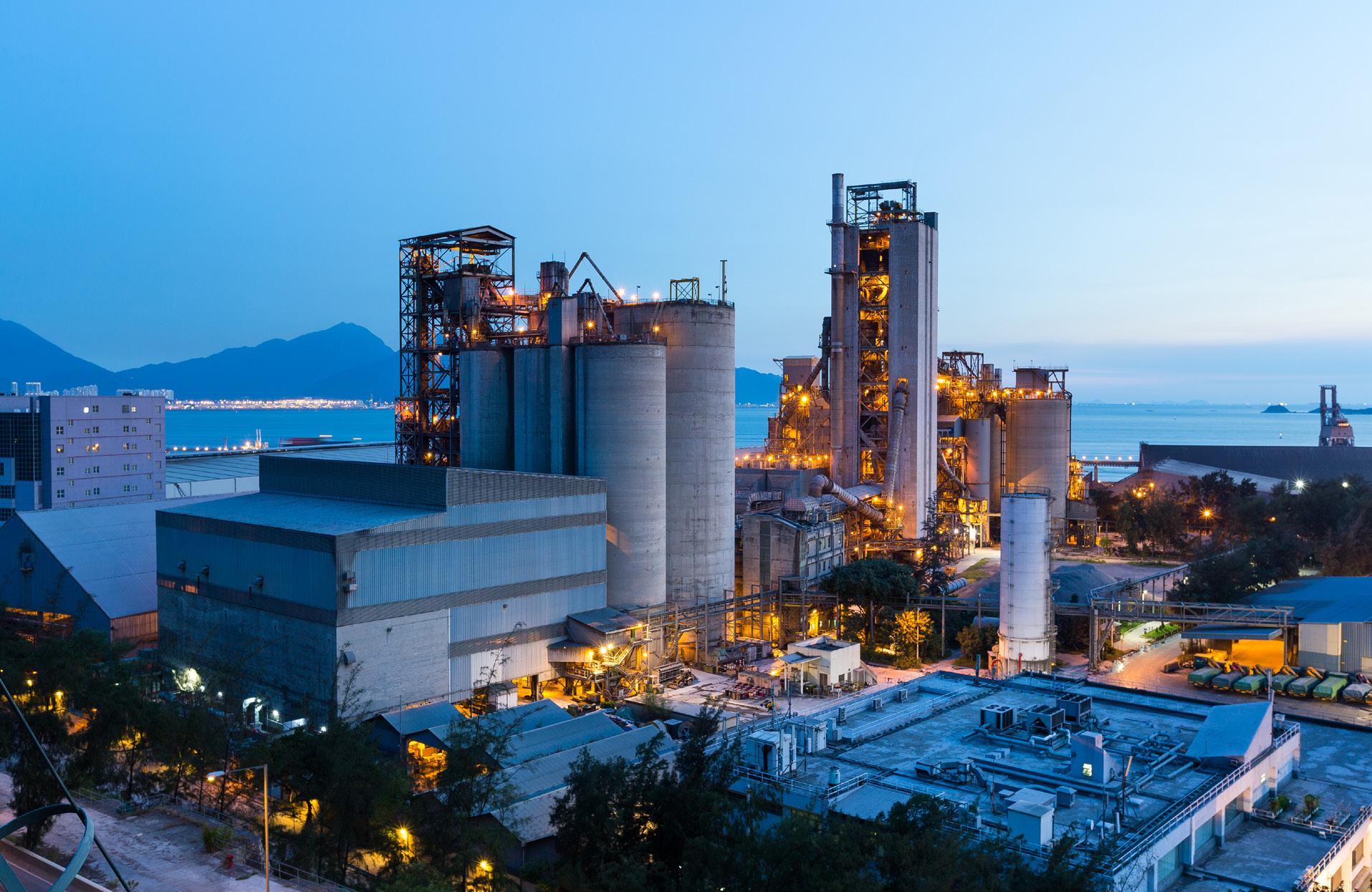
Frankfurt, Germany www.achema.de
HILLHEAD 2024
25 – 27 June, 2024 Buxton, UK www.hillhead.com
FICEM TECHNICAL CONGRESS
02 – 04 September, 2024 Guatamala www.ficem.org
SOLIDS Dortmund 2024
09 – 10 October, 2024 Dortmund, Germany www.solids-dortmund.de
VDZ CONGRESS
06 – 08 November, 2024 Düsseldorf, Germany www.vdz-online.de
AUCBM AICCE27
26 – 28 November, 2024 Tunis, Tunisia www.aucbm.net
Network of 450 scientists and industry leaders from around world meet in Switzerland
Academics and industry players from around the world are gathering in Lausanne, in Switzerland, to drive forward critical research into making concrete, the world’s most used human-made material, carbon neutral.
They are taking part in the Innovandi Global Cement and Concrete Research Network (GCCRN) annual gathering. The network brings 450 researchers and scientists from more than 40 world leading universities and academic institutions, together with business-leaders from some of the industry’s top manufacturers and suppliers. They are collaborating on critical research and initiatives focused on achieving net-zero concrete, in line with the GCCA’s 2050 Roadmap.
Universities attending include the renowned EPFL in Lausanne, which is hosting the event, researchers from South East University and Wuhan University in China, University of Toronto, Indian Institute of Technology in Delhi, University of Cape Town, Imperial College London and University of São Paulo.
Claude Loréa, Cement, Innovation and ESG Director at the Global Cement and Concrete Association (GCCA), said: “Innovation, collaboration and research are all vital to helping our industry decarbonise, in line with the GCCA’s Net Zero Roadmap. And our Spring Week gathering – our biggest yet – provides the key opportunity for our industrial and academic partners to meet face-to-face with PhD students, Postdocs and researchers from all over the world. This amazing global community is coming together with one focus in mind – to decarbonise the world’s essential building material, concrete.”
Concrete is vital for modern infrastructure, including homes, hospitals, bridges, tunnels, roads and so much more, but it currently accounts for 7% of the world’s CO2 emissions. That is why its leading manufacturers recently came together to commit to decarbonising this essential material.
Dr. Davide Zampini is Vice President of Global Research and Development at CEMEX, and the GCCRN’s Industrial Chair. He said: “If we are to reach our goal of net-zero concrete by 2050, then we cannot do so alone. We need to explore as well as harness solutions and collaboration well beyond our industry. That’s why Spring Week is so important.”
During Spring Week, attendees will exchange ideas, conduct workshops, review progress and discuss next steps for ongoing and future research.
Karen Scrivener is the GCCRN’s Scientific Chair, and Professor and Director of the Laboratory of Construction Materials at the EPFL in Lausanne, which is hosting the week. She said: “Everyone here at EPFL is proud to be hosting this year’s Spring Week, anticipated as our largest gathering yet, marking a significant milestone in our journey toward net-zero research.”
Research topics which will be discussed during the week, include: the use of AI in decarbonisation; new materials and processes for manufacturing cement, including sourcing and improving the use of alternatives to clinker (the most carbon intensive element of the manufacturing process), as well as further development on the use of calcined clays; concrete recycling; the use of renewable energy and kiln
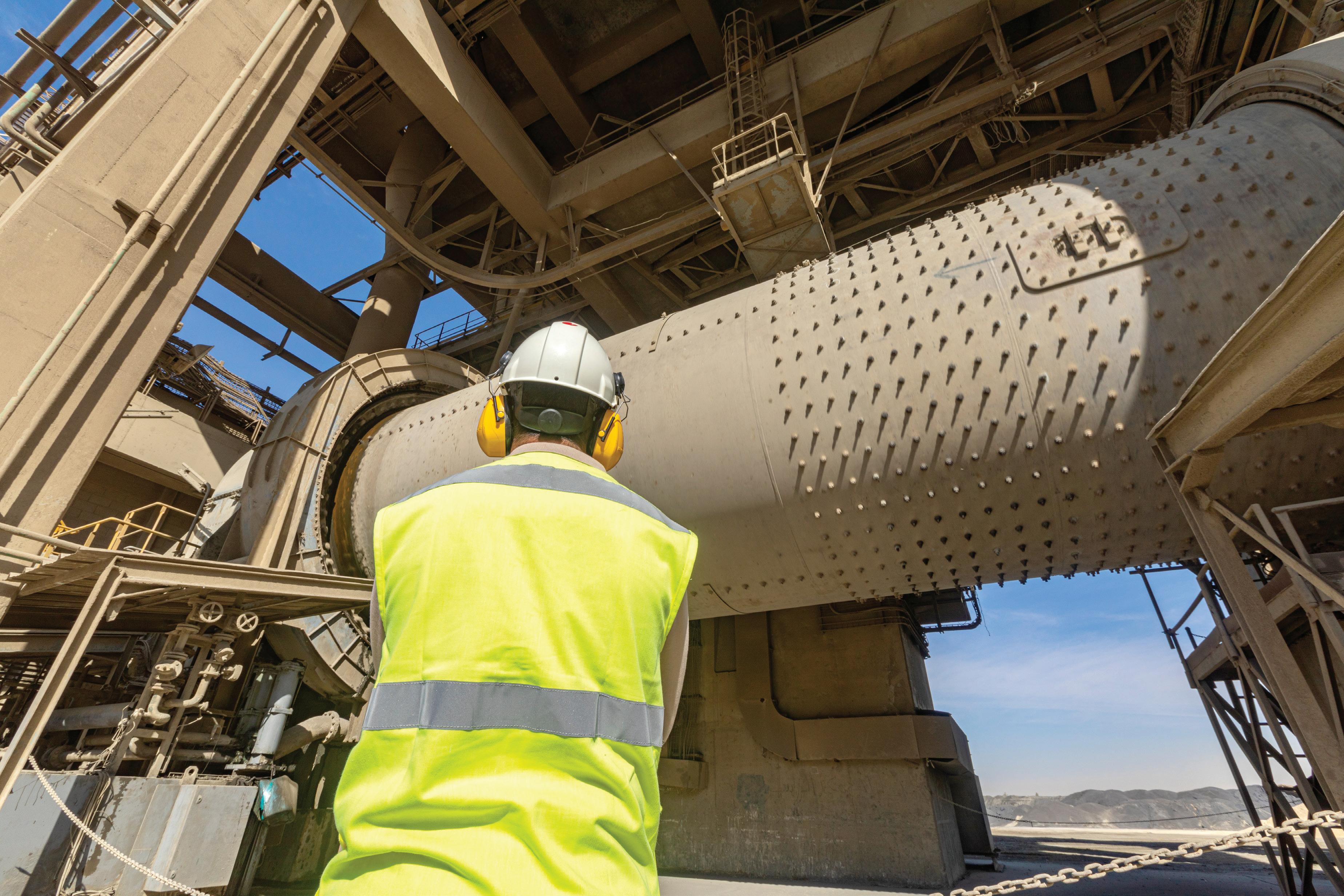
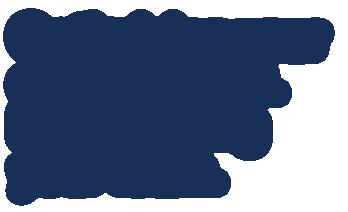
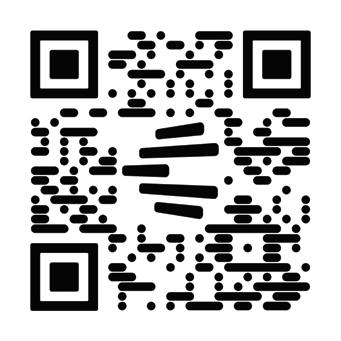
electrification; and further development of carbon capture, use and storage (CCUS).
TITAN America has been selected by the US Department of Energy
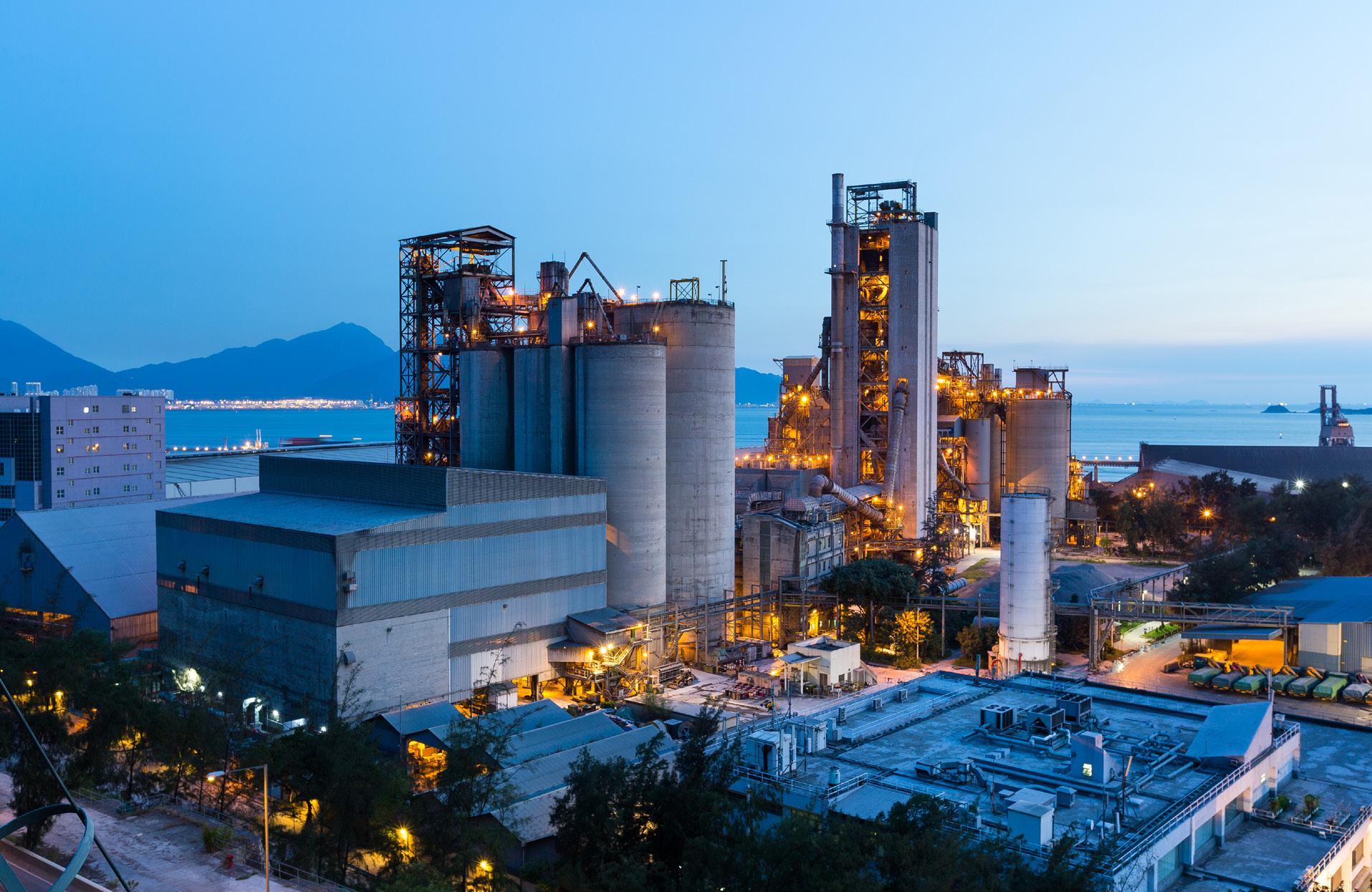
TITAN’s Roanoke cement plant, in Virginia, USA, has been selected for negotiations by the US Department of Energy (DOE) for an up to US$61.7 million award to support the first-of-a-kind deployment of a calcined clay production line.
The implementation of this cement technology will substantially reduce CO2 emissions and become a model for building more sustainable infrastructure in the USA and across the group. Upon successful completion of negotiations, TITAN will support the project with additional investments.
The selection of TITAN’s project underscores the company’s dedication to reducing CO2 emissions throughout the organisation, aligning closely with its ambitious goal of achieving net-zero concrete by 2050. This move is also in line with the group’s Green Growth Strategy 2026, aimed at expanding the range of low-carbon cementitious products offered to customers. The technology from this project is poised to set a new standard for building bridges, hospitals, schools, and other critical infrastructure projects.
Bill Zarkalis, President & CEO of Titan America, stated: “We are honoured to be selected for this first-in-the-nation initiative in spearheading the production of reduced emissions cement, helping lead our industry toward a net-zero future through deep decarbonisation technologies.”
The project is part of the US$6.3 billion Industrial Demonstrations Program, which is managed by DOE’s Office of Clean Energy Demonstrations (OCED) and is primarily focused on CO2 reduction.
Leonidas Canellopoulos, TITAN’s Chief Sustainability and Innovation Officer, added: “This initiative aligns with our Green Growth strategy’s focus on advancing cementitious materials, harnessing innovation and novel technologies. Building upon the successful pilot test conducted at our Patras plant in Greece, we are now scaling up the development of low-carbon calcined clays. Our dedication to sustainable solutions propels us as we stand among the frontrunners in leading the change towards decarbonising the industry.”
Christian Myland to be the new CEO of thyssenkrupp Polysius
thyssenkrupp has announced the appointment of Christian Myland as the new Chief Executive Officer of thyssenkrupp Polysius, effective 1 June 2024. He succeeds Pablo Hofelich, who has decided to take on a new professional challenge outside thyssenkrupp.
Christian Myland brings more than 16 years of corporate experience to his new position. In addition to various roles and management functions in Germany and abroad – including at thyssenkrupp Steel Europe AG and thyssenkrupp Steel Americas as well as in thyssenkrupp’s automotive business – he has spent seven years as CFO and five years as CEO at Uhde High Pressure Technologies (UHPT).
Miguel López, CEO of thyssenkrupp AG: “Christian Myland has stabilised and modernised our Uhde High Pressure Technologies business unit with its global project activities, sophisticated technologies and in-house production in Hagen and significantly improved its performance – both in new business and in the service business. He is therefore ideally qualified for his new role at thyssenkrupp Polysius. At the same time, we would like to thank Pablo Hofelich for his valuable work and wish him all the best for the future.”
Breedon Group provides AGM trading update
Breedon Group plc, provided the following trading update ahead of the group’s Annual General Meeting.
Trading during the first quarter was impacted by the ongoing macroeconomic uncertainty and reduced construction activity due to wet weather conditions. This led to softer volumes which were partially offset by resilient pricing. As a result, revenue reduced by 5%, or 9% on a like-for-like basis, when compared to the first quarter of 2023.
Highlights:
f In Great Britain trading conditions were particularly affected by the wet weather. The company completed two bolton acquisitions; Eco-Asphalt, a well-connected asphalt plant in the North West, and Phoenix Surfacing which enhanced the company’s surfacing capability in the Midlands.
f Ireland had a strong tendering season and is well positioned for the rest of the year, supported by
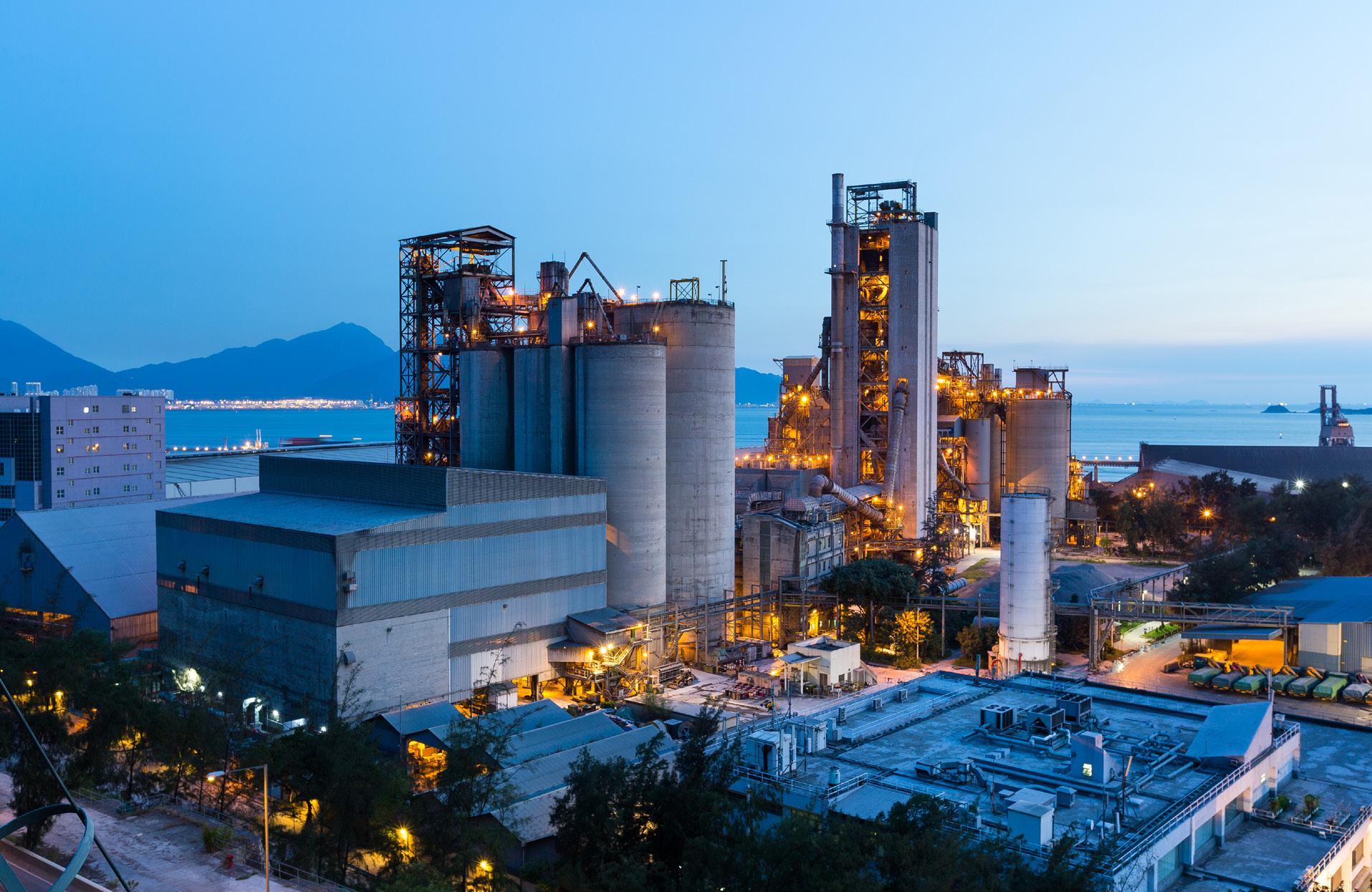
healthy housing and infrastructure markets and the return of the governing Assembly to Stormont.
f Cement delivered two scheduled kiln maintenance shutdowns, on time and within budget, and continued to expand the use of alternative fuels and the provision of lower clinker content products.
f The company launched its third platform in the USA with the acquisition of BMC, which completed on 7 March 2024. The first weeks of trading under its ownership have been encouraging, the integration is progressing well and the outlook is positive.
Rob Wood, Chief Executive Officer, commented: “I am encouraged by our strategic progress in the first quarter. Whilst there were fewer trading days due to the timing of Easter, and it was impacted by exceptionally wet weather, seasonally it is the least significant trading period for Breedon and our industry.
“We have laid good foundations for the remainder of the year; progressing pricing, pursuing efficiencies, completing two bolt-on acquisitions and launching our third platform by entering the US market. Although the economic landscape remains uncertain, I am confident our discipline and focus, coupled with our strong customer relationships, will see us deliver against our unchanged expectations for 2024.”
Cementir Group launches newer lower carbon white cement
Cementir has launched a new Aalborg White® Cement with a lower carbon footprint, D-Carb®, which presents a 15% reduction in CO2 emissions when compared with CEM I 52.5R.
D-Carb is the first white cement in the market to match a lower-carbon footprint with high performances at early ages. It is available in European markets before being launched globally.
“We are thrilled to introduce D-Carb, our new umbrella brand for lower carbon cements, as part of Cementir Group’s ongoing commitment to address environmental challenges and climate change”, says Michele Di Marino, Chief Sales, Marketing, & Commercial Development Officer of Cementir. “As a leading white cement producer, the successful rollout of D-Carb is pivotal in advancing our ‘net-zero emissions’ ambition. Embracing a customer-centric approach, the unveiling of this
product is eagerly anticipated. D-Carb, integrating lower-carbon, high performance and unique aesthetic value underscores our resilience in facing challenges in our decarbonisation efforts. We believe that D-Carb will further support stakeholders in the value chain with lower-carbon finished products aligned with sustainable building standards.”
The synergy between well-known Aalborg White clinker and pure limestone has been optimised by choosing a fit-for-purpose grinding aid to achieve comparable performances to the CEM I 52.5R at early ages, meeting the strict requirements of construction timelines.
D-Carb also inherits the extra properties given by the Aalborg White clinker used, extremely low alkali and low chloride content, ensuring reliable quality and durability of the finished products.
“Performances and white colour are key features of D-Carb, and exploring suitable raw materials and their combinations have been crucial in the product assessment. This has resulted in the accurate selection of pure, very light limestone from a stable source, improving and stabilising whiteness. Additionally, leveraging limestone fineness and particle size distribution, D-Carb ensures enhanced and consistent rheology, ideal for wet-cast applications, such as self-compacting concrete. These distinctive rheological properties allow for concrete finishes resembling marble surfaces. Moreover, the enhanced synergy and compatibility between cement and admixture cater to a wide range of white cement applications”, explains Stefano Zampaletta, Group Product Development Manager.
Leveraging on its peculiar performances achieved by D-Carb and after a specific testing programme on site, customers are able to replace CEM I 52.5R in their manufacturing processes, especially when early age performances are the main targets. Cementir will support this sustainable transition with its technical experts to guide users in adopting D-Carb product and integrating it into their production processes.
The introduction of D-Carb marks a profound impact on the building and construction sectors, offering a vital solution for decarbonising practices within the industry, while enhancing Cementir’s portfolio of lower-carbon products. Cementir Group continues its broader decarbonisation efforts for low-carbon products, ongoing assessments are in progress to strengthen the D-Carb range with additional sustainable solutions.
Year of the dragon?
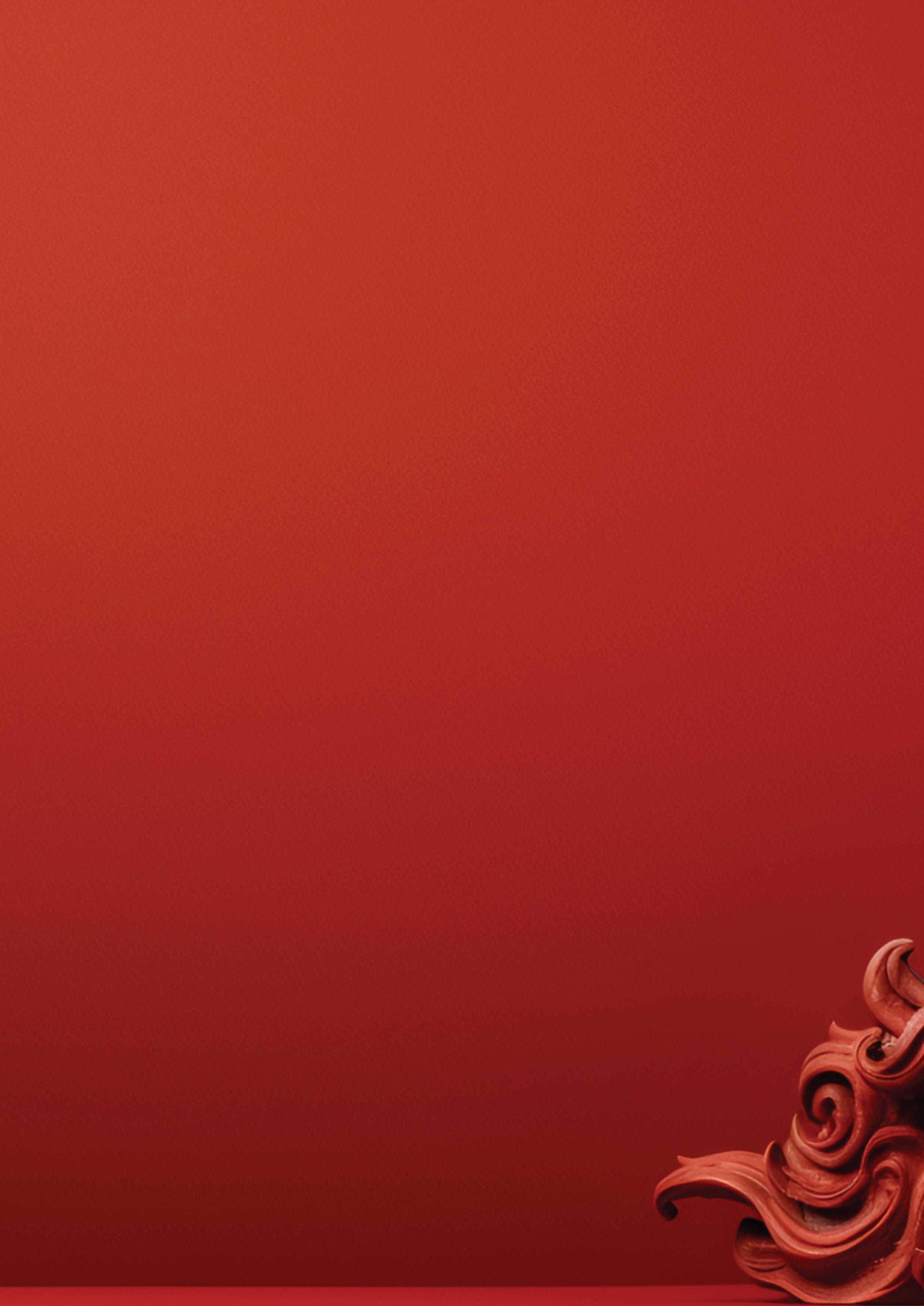
David Bizley, Senior Editor of World Cement, provides a brief overview of some of the challenges facing the Chinese economy and the consequences for the construction and cement sectors.
Since the late 1970s, the Chinese economy has undergone a remarkable transformation. The market-oriented reforms first brought in under the leadership of Deng Xiaoping allowed China to rapidly evolve from an almost entirely agrarian society into a global economic powerhouse.
Today, China stands as the world’s second-largest economy by nominal GDP, wielding considerable influence in global trade and finance. However, challenges such as income inequality, environmental degradation, and demographic shifts loom large, posing complex hurdles to sustaining its economic momentum in the future.
This article aims to provide a brief outline of the current economic situation in China, with a focus on the construction and cement sectors.
Economic miracle
Since China’s economic reforms began back in 1978, the country has achieved an average GDP growth of over 9% per year, lifting almost 800 million people out of poverty over that time. The country has also made major improvements to healthcare, education and other public services over that time period. The World Bank reports that China is now an ‘upper-middle-income’ country. However, despite the rapid growth and the elimination of extreme poverty in 2020, a little over 17% of the population still live on less than US$6.85 a day, placing them under the poverty line for upper-middle-income countries.
As of today, the Chinese economy is second only to the United States in nominal terms, and actually the largest when adjusting for purchasing-power-parity. Much of this
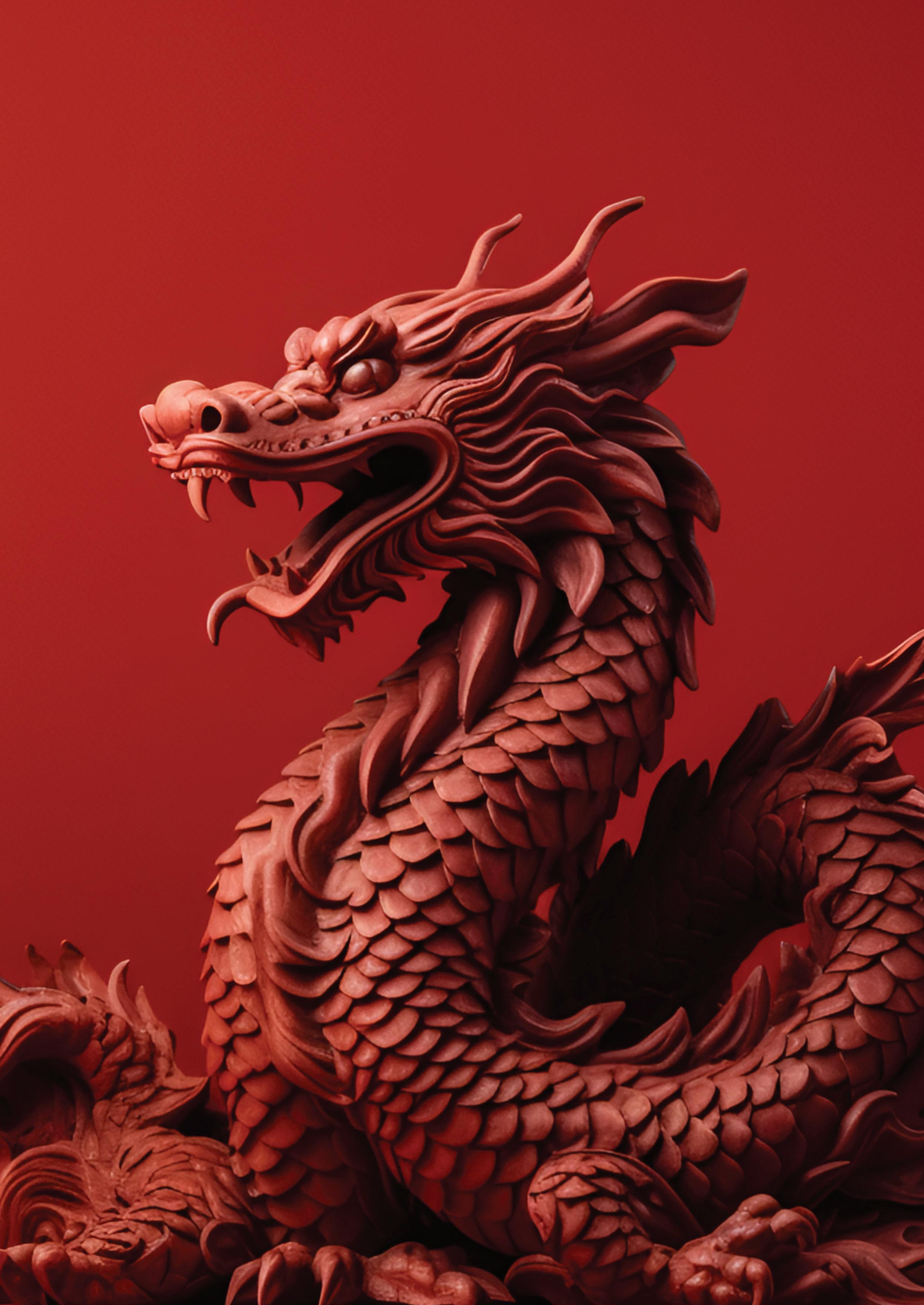
extraordinary economic rise is due to economic policies that focused largely on two key pillars: internal investment and export-oriented manufacturing. Internal investment, particularly in vast infrastructure projects, has been a cornerstone of Chinese economic growth, with the country investing heavily in high-speed rail, highways, ports, bridges, dams, and more. Meanwhile, the focus on export-oriented manufacturing has converted the country into a modern-day ‘workshop of the world’ and has made it the leading global supplier of a whole range of goods, including textiles, electronics and heavy machinery. China is also expanding into emerging technologies, including solar panels and electric vehicles.
Headwinds
Challenges, however, are looming. Though successful for decades, China’s key economic policies appear to be reaching their limits. And as the country approaches what the World Bank refers to as ‘structural constraints’, such as unfavourable demographics (including a declining labour force), a shift in approach from manufacturing and investment to high value services and consumption will be necessary.
Adding weight to this argument, The Financial Times reported in January of this year that Chinese manufacturing had undergone its fourth consecutive month of contraction, despite the efforts of policymakers to boost prospects. The non-manufacturing index recorded minor growth, but it too was sluggish, recording a rise of just 0.3 points, which analysts attributed to a long-running property downturn, weakened export demand and low investor confidence. The Financial Times also quoted Zhiwei Zhang, president and chief economist of Pinpoint Asset Management as saying: “Economic momentum remained muted as the deflationary pressure persists.”
In terms of demographics, China faces another major, seemingly intractable challenge. The country’s National Bureau of Statistics recently announced a second consecutive year of population decline with a decrease of 2.08 million recorded for 2023, marking a significant acceleration following the decline of 850 000 recorded for 2022. This trend, if it continues, poses a considerable challenge for the future of the Chinese economy – fewer people means fewer workers, fewer customers, and a lower tax base. And, as the population continues to age, the costs of elder care and retirement benefits will burden already strained local governments. The UN has forecast a population decline of over 100 million by 2050, with a possible reduction to below 1 billion by the end of the century.
Another area of concern for the Chinese economy is ongoing tension with the West. Specifically, concerns relating to Chinese support of Russia and worries over access to advanced technologies, have resulted in various US sanctions. These have added a further dampening factor to China’s post-COVID recovery and risk hindering technological development. At the time of writing, it has just been announced that the US is drafting additional sanctions targeting certain Chinese banks in response to their commercial support of Russian military production.
Despite these headwinds, the Chinese economy still recorded GDP growth of 5.2% in 2023, slightly above the target of 5%. The IMF predicts that ongoing stimulus efforts will see the Chinese economy achieve GDP growth of 4.6% this year, reflecting the impact of stronger than expected growth in 2023 and increased government spending.
Shaky ground
China’s construction sector, particularly with regard to residential construction, has been embroiled in an ongoing crisis for the last three years. The origins of the crisis are largely attributed to a legislative crackdown in 2021 which regulated the amount of leverage that could be taken on by developers, thus limiting their borrowing. This ultimately triggered the default of the heavily leveraged residential construction giant, Evergrande, in late 2021 and sent shockwaves throughout the rest of the sector. According to IA Cement, there have been US$29 billion worth of company defaults since 2021.
Though an outright collapse of the sector was avoided as a result of government intervention, the decline was significant and is still ongoing with UBS estimating that the sector now represents just 22% of Chinese GDP, down from 25% a few years prior. IA Cement notes that national real estate development declined 9.3% in the second half of 2023, with the area of newly constructed housing falling by 23%. The figures for the first quarter of 2024 are not looking much brighter either, with the National Bureau of Statistics reporting a further decline of 27.8% in the total area under construction, with the area of commercial real estate declining by 19.4% y/y. Putting it simply, Sheng Laiyun, deputy commissioner of the National Bureau of Statistics, said: “The investment and sales of real estate in the first quarter are indeed not very optimistic. The real estate market is still in a process of adjustment.”
The picture is somewhat brighter for public works, with IA Cement reporting a growth rate of 5.9% in the first 10 months of 2023, with further (albeit) slower growth forecast for this year. Specifics include a 25% increase in expenditure on rail projects, a 6% increase in water conservation
projects, and stable expenditure levels on highways.
Cement
The mixed fortunes of the Chinese construction sector have, naturally, had an impact on the outlook for the country’s titanic cement sector, which is responsible for roughly half of the entire world’s cement production. Indeed, Fitch Ratings notes that, in addition to the volatile construction sector, Chinese cement production faces greater challenges than other heavy industries, such as steel and aluminium, including reduced interaction with the profitable manufacturing and renewable energy sectors, and an ongoing shift away from concrete and towards steel structures.
Facing these challenges then, it is perhaps little surprise that the cement sector has reported consistent negative growth since May 2021. Although the pace of decline slowed in 2023 compared to 2022, IA Cement notes that a recovery in March – April of 2023 was short-lived, with output in the first 10 months of the year declining by 1.1% to its lowest level since 2011.
The sector’s malaise is being borne out in company results. CNBM’s Basic Building Materials Group reported a 63.6% decline in profit in its 2023 Annual Report, blaming “insufficient demand, weakening expectations and weakening off-peak season characteristics” across the entire cement sector. This result helped drag down CNBM’s overall revenue for the year by 10.1%, with after tax profits falling by 32.5%. The company has recently issued a profit warning stating that first quarter 2024 losses are likely to have more than doubled y/y, with an expected decline of approximately US$180 million, driven by lower selling prices for its key products, worsening performance of associate companies, and higher currency losses.
Another national cement enterprise, Tianrui Group Cement Co., also posted negative results for 2023, announcing a more than 30% decline in sales from US$1.6 billion to less than US$1.1 billion, with a full-year loss of US$87.7 million. The news marks a concerning reversal of the company’s profit of US$62 million from a year prior. Indeed, the company appears to be in some form of financial difficulty after being recently suspended from trading on the Hong Kong Stock Exchange after it fell in value by 99%, cutting market capitalisation to just US$18 million.
Summary
China, its economy, and by extension, the cement sector, face a range of significant structural challenges in the years ahead, including demographic and environmental issues. Exactly how China will deal with these challenges remains to be seen, but the impact is likely to be felt across the globe.
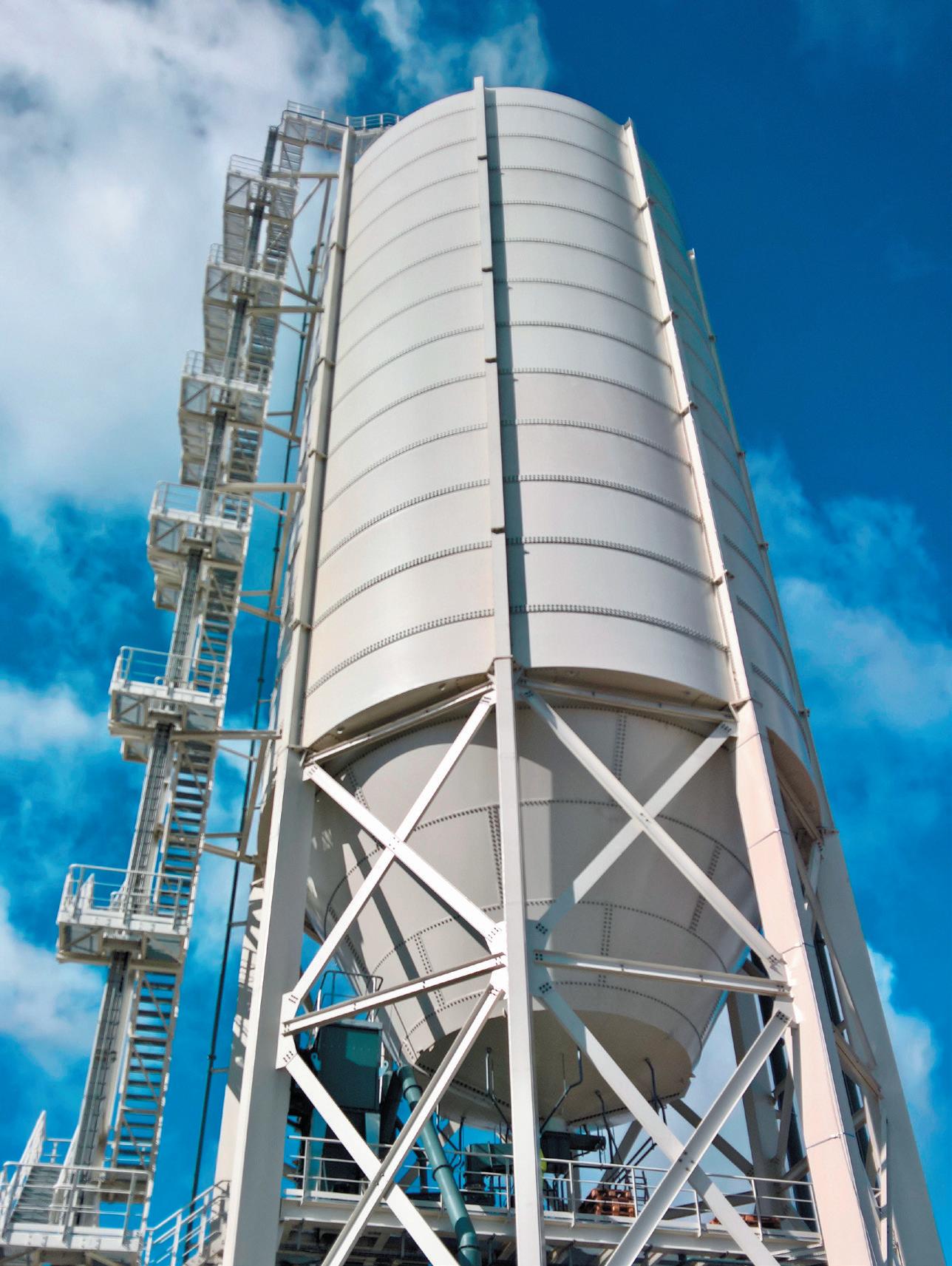

The Modern Way
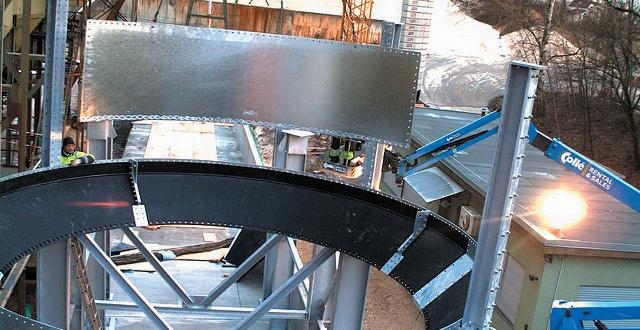
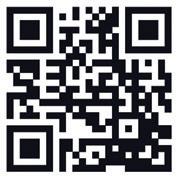
CEMTEC®
DESIGNED FOR PERMANENT MEASUREMENT
CEMTEC advantages
• Probe gas entrance inside the rotary kiln
• Plunger prevents blockages at sample gas entrance
• Large filter surface for dust-free gas sample
• Gas sample above water dew point temperature
• Suitable for hot/wet or cold/dry flue gas analysis
Probe gas entrance inside rotary kiln

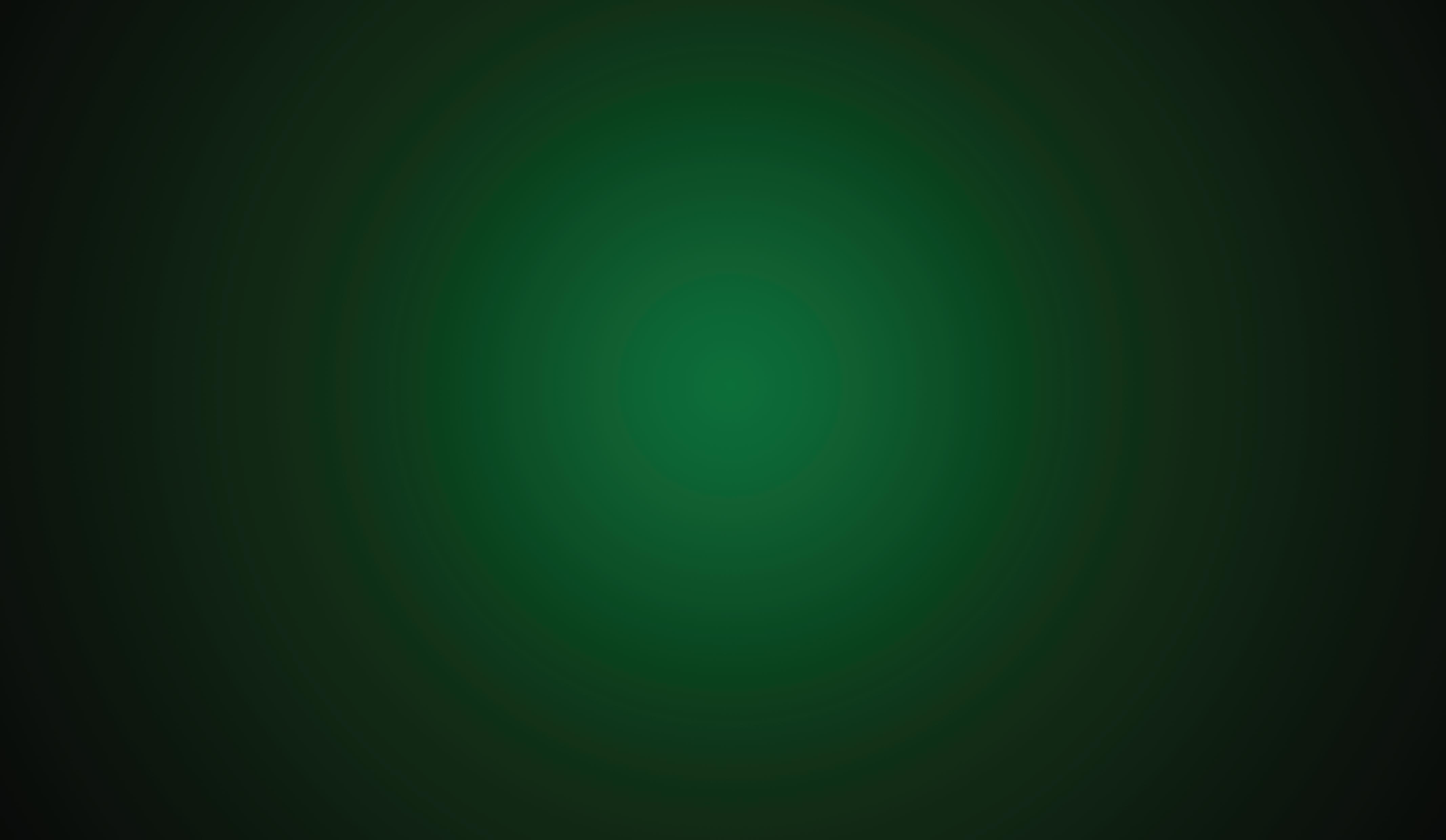
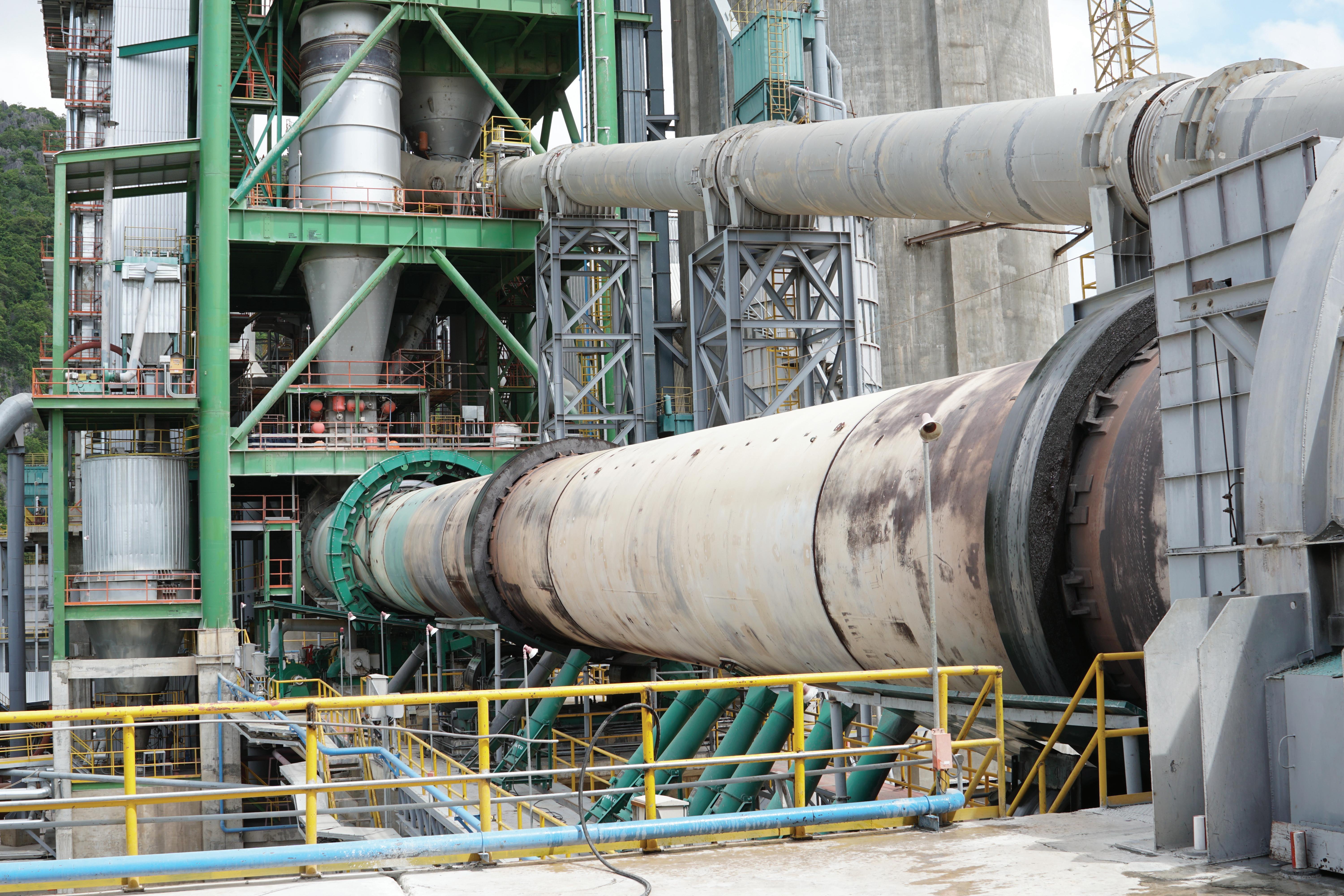
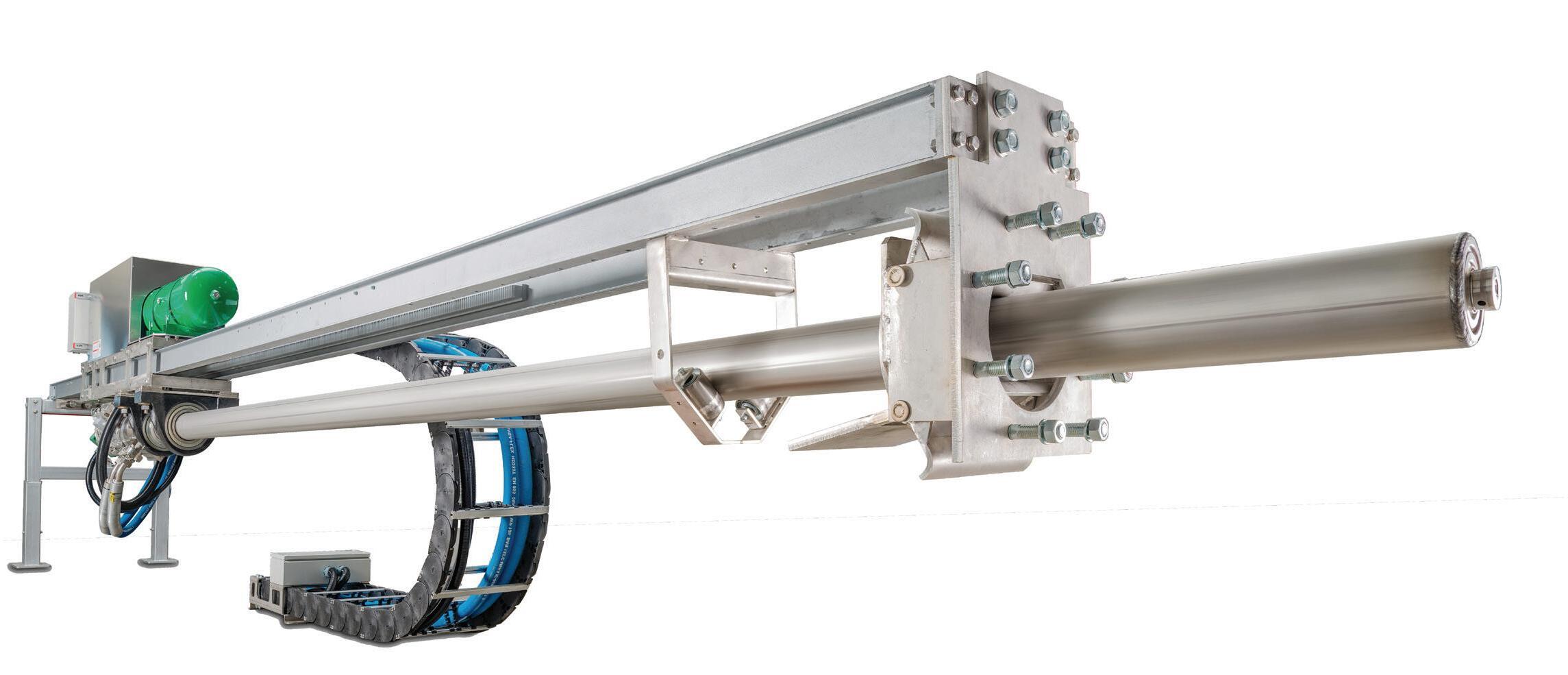
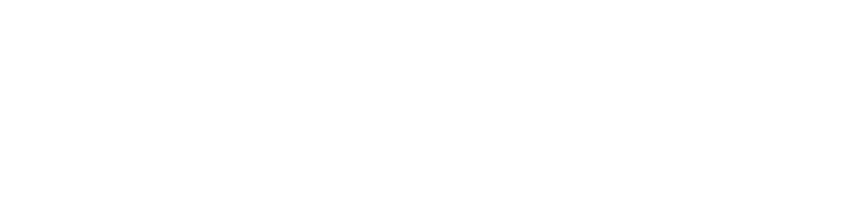
Reliable and maintenance-free gas sampling system for the rotary kiln inlet.



Features
• Cyclic plunger movement with 7000 N
• Probe insertion/retraction force 20000 N
• Cyclic anti-stick probe rotation with 700 Nm
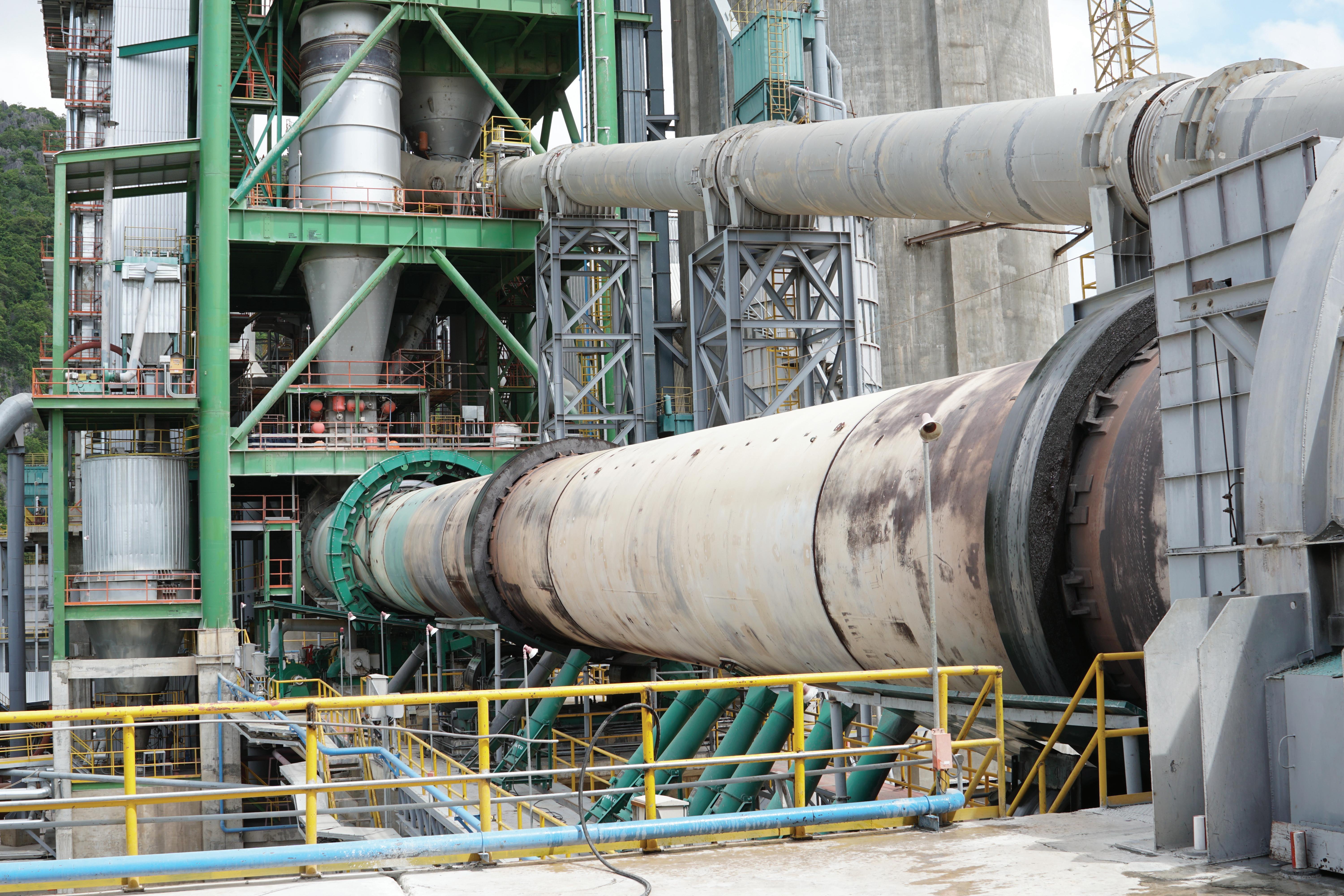
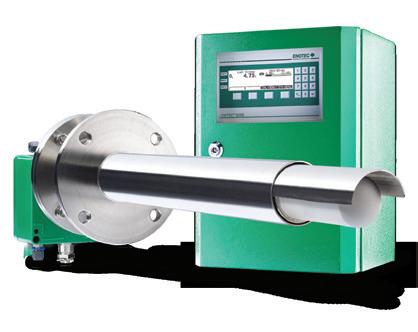
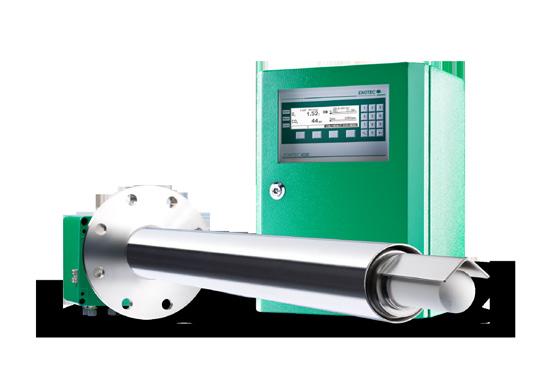


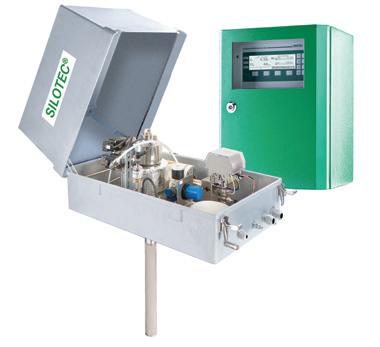
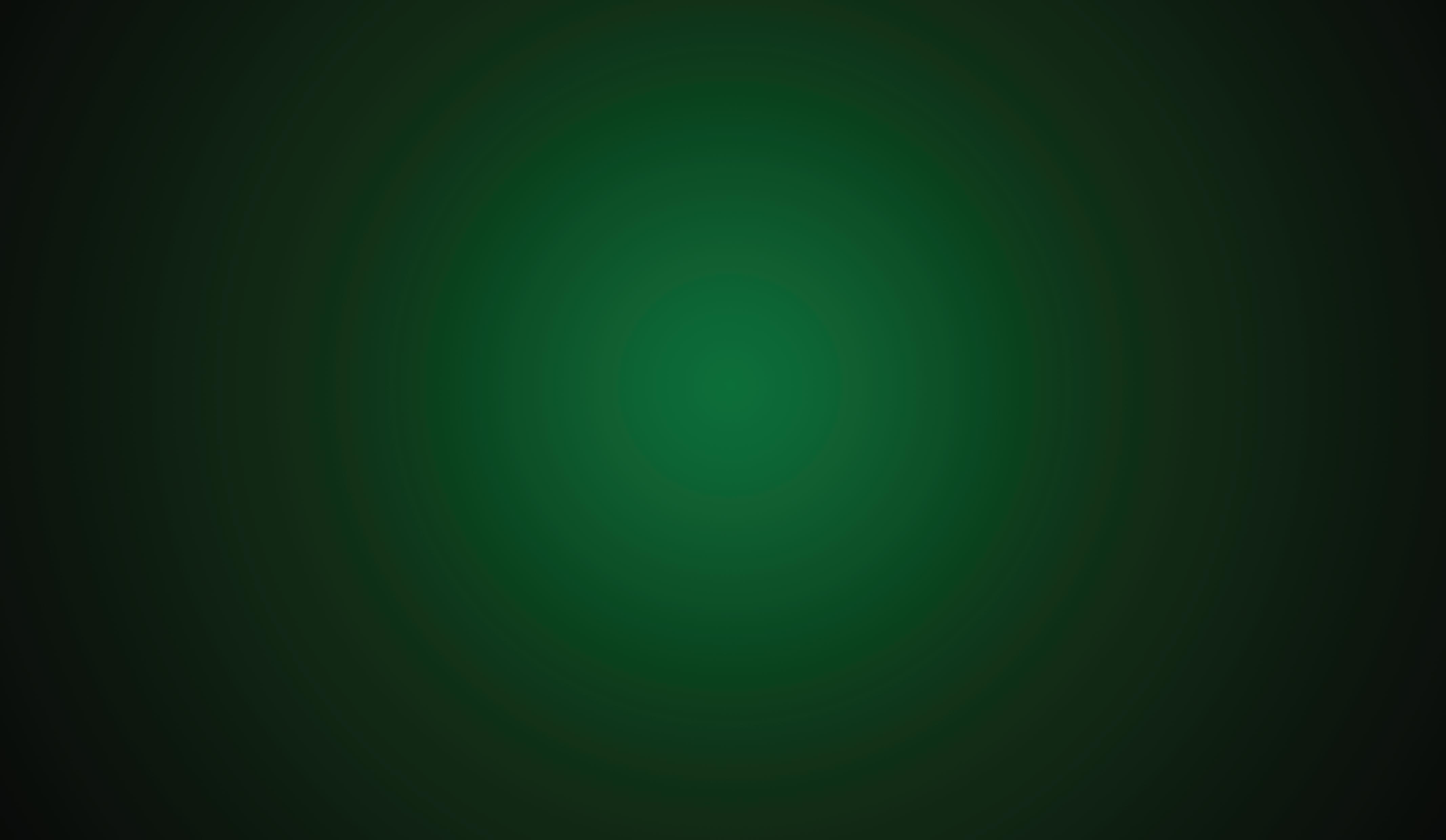


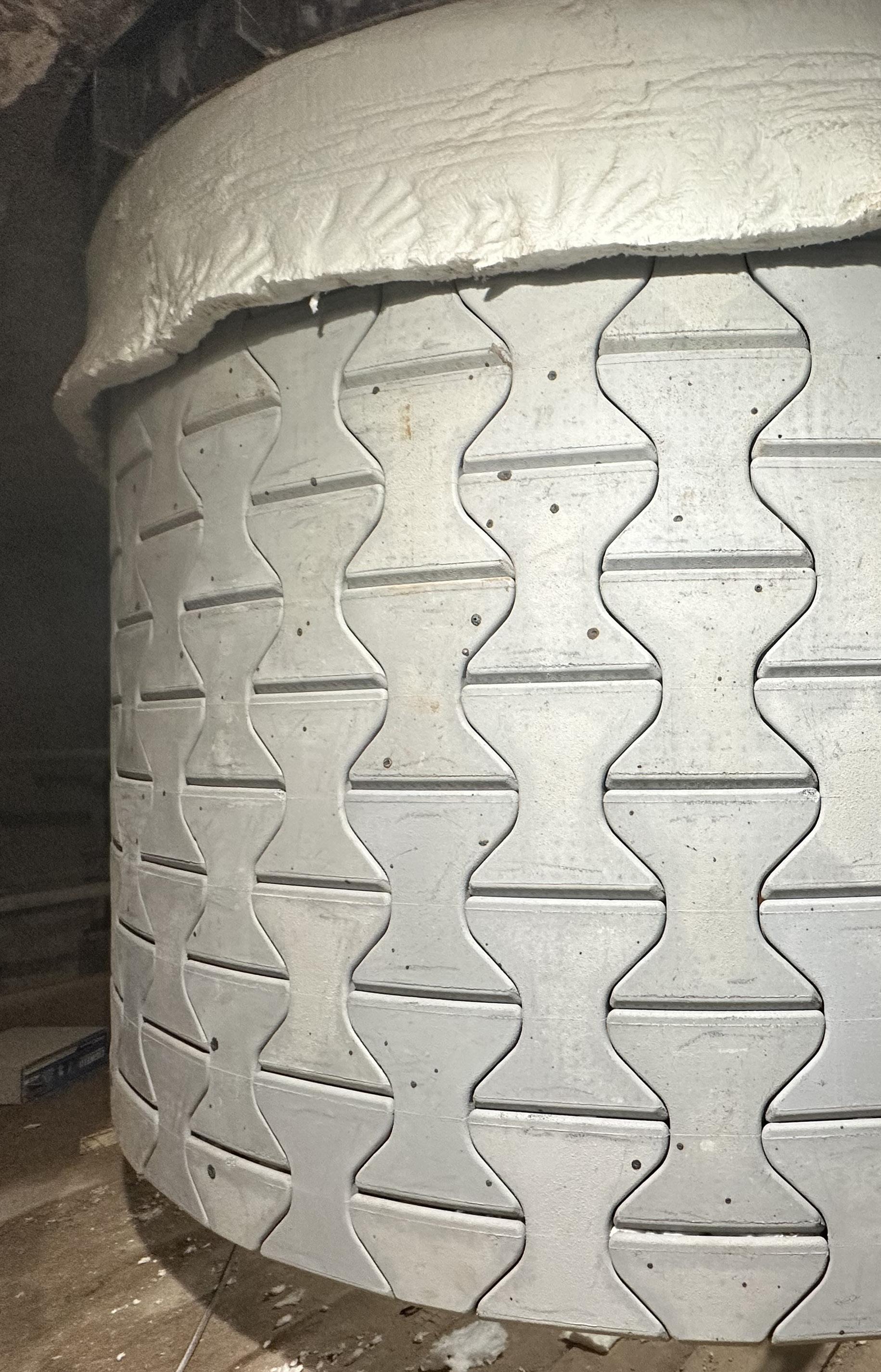
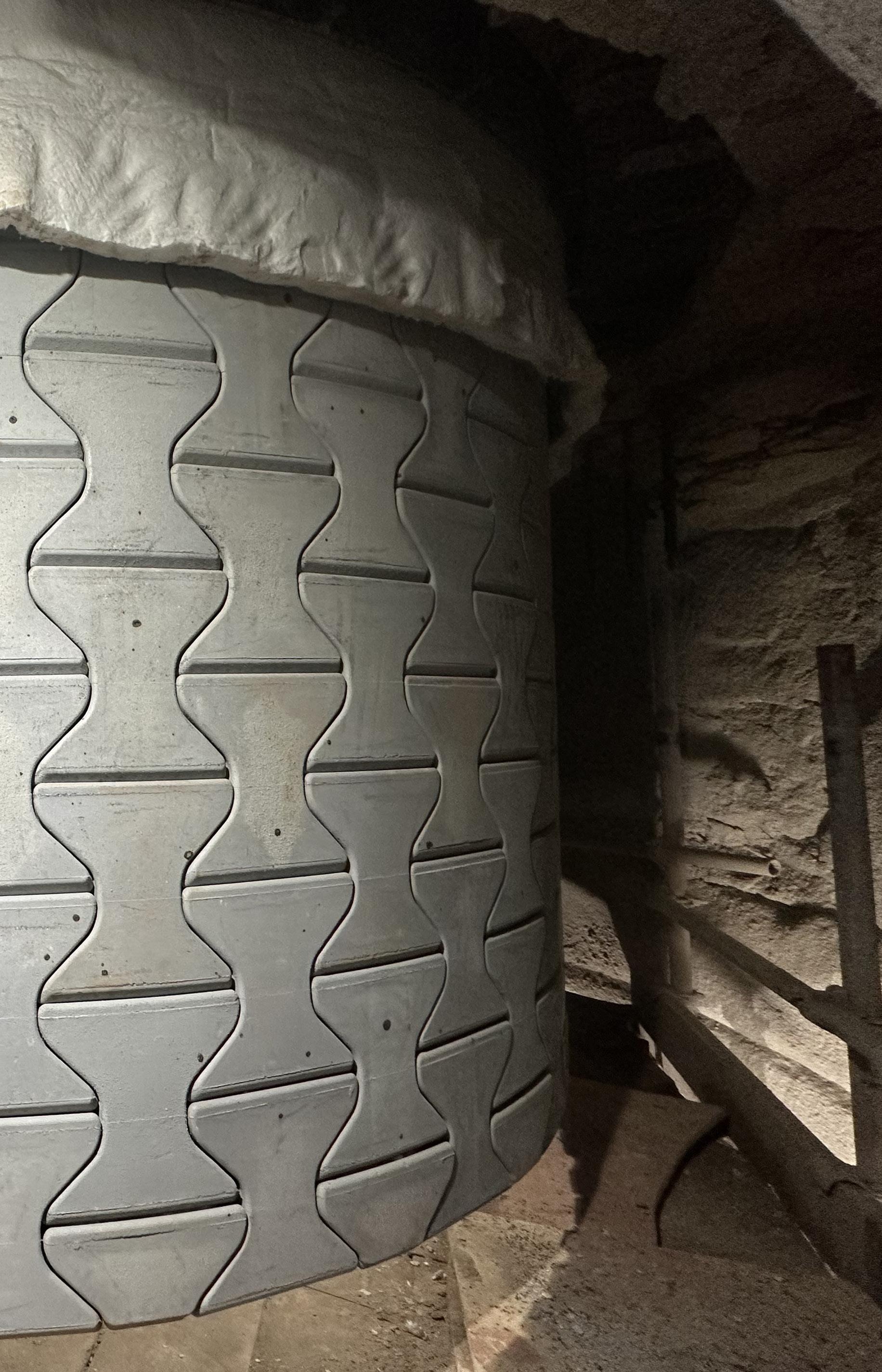
Sustaining cyclone efficiency Sustaining cyclone efficiency
Preecha Chokjarearnsuk, HASLE Refractories, discusses the role of dip tubes in preheater cyclones and reveals how a new generation of ceramic vortex finder has performed for the ADBRI Birkenhead cement plant in Australia.
Cement clinker manufacturing is a highly energy-intensive process, with energy costs typically accounting for 15 – 40% of total production costs. This proportion is expected to rise due to anticipated carbon taxes and increased competition for alternative fuels (AF), making energy consumption reductions imperative for economically viable cement production amid the global transition to greener practices.
Over 85% of the energy utilised in cement production is typically consumed as heat input in the rotary kiln and calciner. While coal and other fossil fuels remain prevalent globally, there is a growing
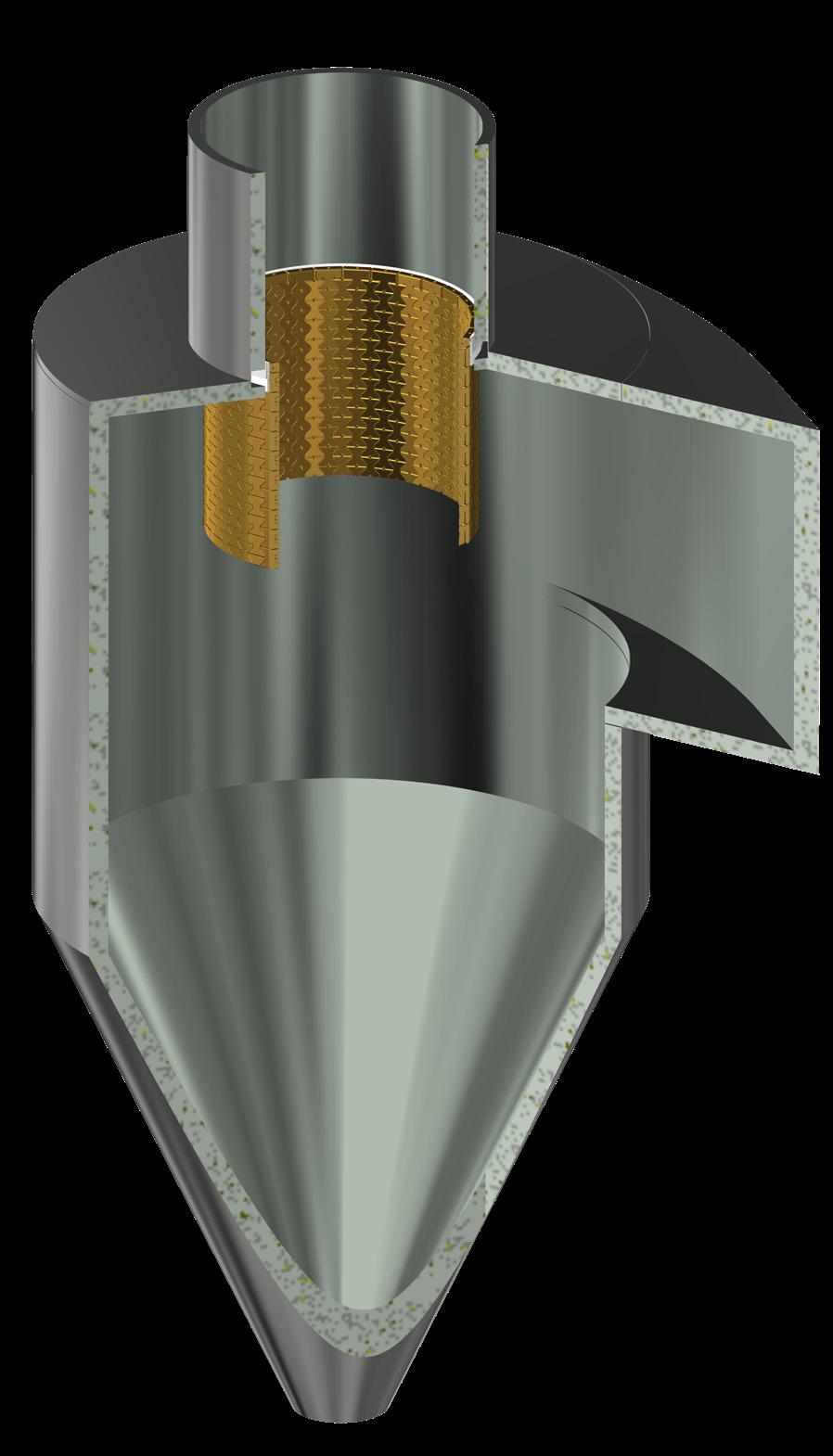
Vortex finders are installed in preheater cyclones to improve the separation between the raw meal and the hot gas, thereby increasing the heat efficiency of the preheater process. But many plants run without it due to issues with short lifetimes.
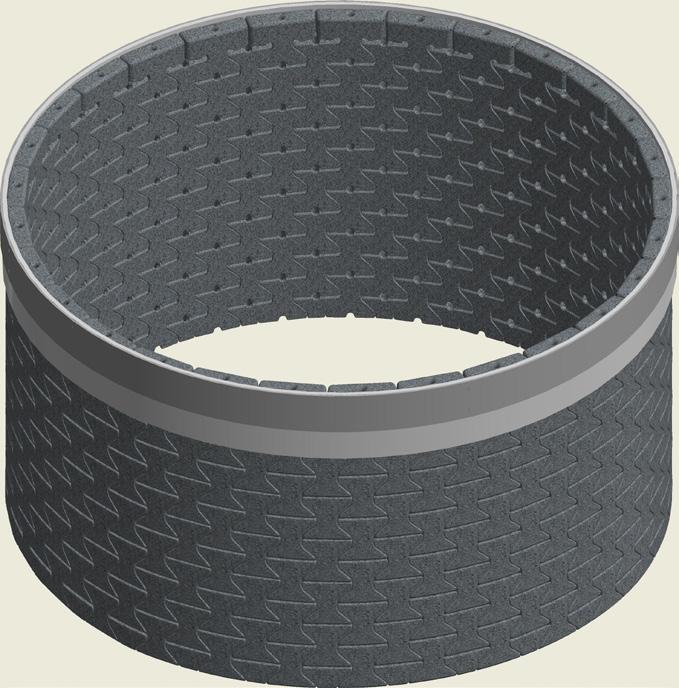
trend towards using AF such as waste materials, biomass, and other low-carbon fuels. However, increased usage of these fuels presents challenges in maintaining process stability, including temperature and pressure fluctuations due to unsteady combustion, as well as ensuring the longevity of refractory linings, imposing higher maintenance costs.
Efficiency gain with dip tube
One component especially impacted by the intensified usage of AF is the dip tube, also referred to as a thimble or vortex finder, in the lowest stage cyclone of the preheater tower. Its function is to define the flow field in the cyclone and prevent the entering particles from shortcutting the cyclone. A missing or damaged dip tube results in a significantly lower separation efficiency, which in turn lowers the heat recovery efficiency of the entire preheater tower, as a large portion of the preheated raw material particles is not entering the kiln but sent back to the upper cyclone stages. Consequently, the operating temperature in all cyclone stages increases, entailing a higher overall fuel demand. The additional fuel requirement may be in the range between 1 – 1.5% of the total fuel consumption when the dip tube is entirely absent in the lowest stage.
Troubled steel dip tubes at elevated temperatures
Today, most dip tubes are made of heat-resistant Cr-Ni-alloyed cast steel. In light of increased AF usage, steel however has some considerable disadvantages, which may limit the performance and lifetime of the dip tube. Firstly, steel is a ductile material and, hence, prone to deformation, especially at elevated temperatures. Higher mechanical and thermal loads from AF combustion can accelerate the deformation and creep of the commonly used steel dip tubes. Secondly, burning AF increases the concentration of various corrosive species in the gas phase, such as halides, acids, and alkali salts. In order to avoid intensified corrosion damage, higher alloyed steels have to be used, which results in both significantly higher investment costs and higher emissions of carcinogenic chromate (Cr(VI)), which are hazardous gasses posing health risks to maintenance personnel. In turn, many cement plants choose to run without any dip tube in the lowest stage cyclone.
A new vortex finder


The HASLE Ceramic Vortex Finder provides an alternative to steel dip tubes. It is assembled on-site by individual ceramic elements, which interlock to form a stable tube suspended from a steel support ring welded to the roof casing of the cyclone.
To overcome the drawbacks of traditional steel dip tubes at elevated temperatures, a Ceramic Vortex Finder (CVF) was developed by HASLE Refractories during the 1980s. The CVF
consists of pre-cast and pre-fired refractory elements, which interlock to form a stable tube suspended from a steel ring welded to the roof casing of the cyclone.
Recently, a new generation of the CVF (GEN3-CVF) has been developed, which has been specially designed to cope with the harsh operating conditions in cement plants using AF. Following a thorough development phase involving laboratory as well as field tests, the GEN3-CVF is a general overhaul of the existing CVF product line with both new-shaped elements and a unique high-performance refractory material.
Australian plant looking for dip tube alternatives
Nestled on the LeFevre Peninsula in southern Australia, the ADBRI Birkenhead cement plant enjoys a picturesque setting, surrounded by the captivating panorama of the St. Vincent Gulf and the Adelaide cityscape. With a rich history spanning more than a century, this 4000 tpd plant operates predominantly on natural gas. But the plant also incorporates a substantial amount of refuse-derived fuel (RDF) – on average 40% – which is charged into the calciner.
The cement plant operates a dual-string preheater design merging into one calciner unit and subsequently the kiln. This design includes a single lowest-stage cyclone at the exit of the calciner where the operating temperature is maintained at 850 – 900˚C. In the late 2000s, the plant initially trialled generation 1 of the HASLE CVF in the lowest stage cyclone. This, however, yielded mixed results with the GEN1-CVF experiencing operational lifespans down to six months. Notably, a contributing factor to the short lifetimes was the usage of AF in the calciner which was also increased during that period.
Faced with these challenges, the plant decided to run without any dip tubes in the lowest stage cyclone to minimise the risk of unscheduled shutdowns, as no dip tube solution could reliably operate for a full campaign at that point in time.
A new generation with high-performance castable
The ceramic elements for Generation 3 of the HASLE Ceramic Vortex Finder are made from a newly developed
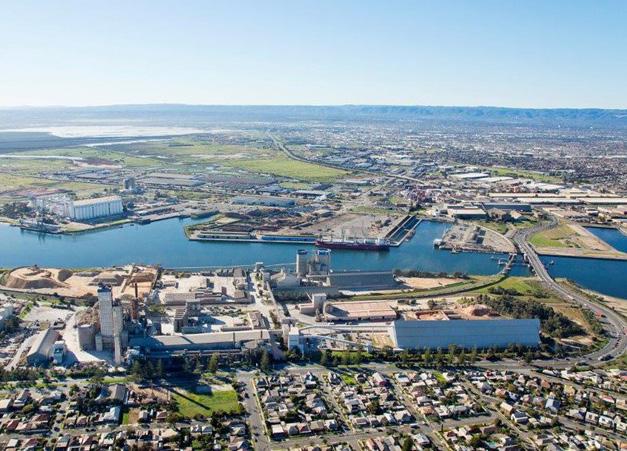
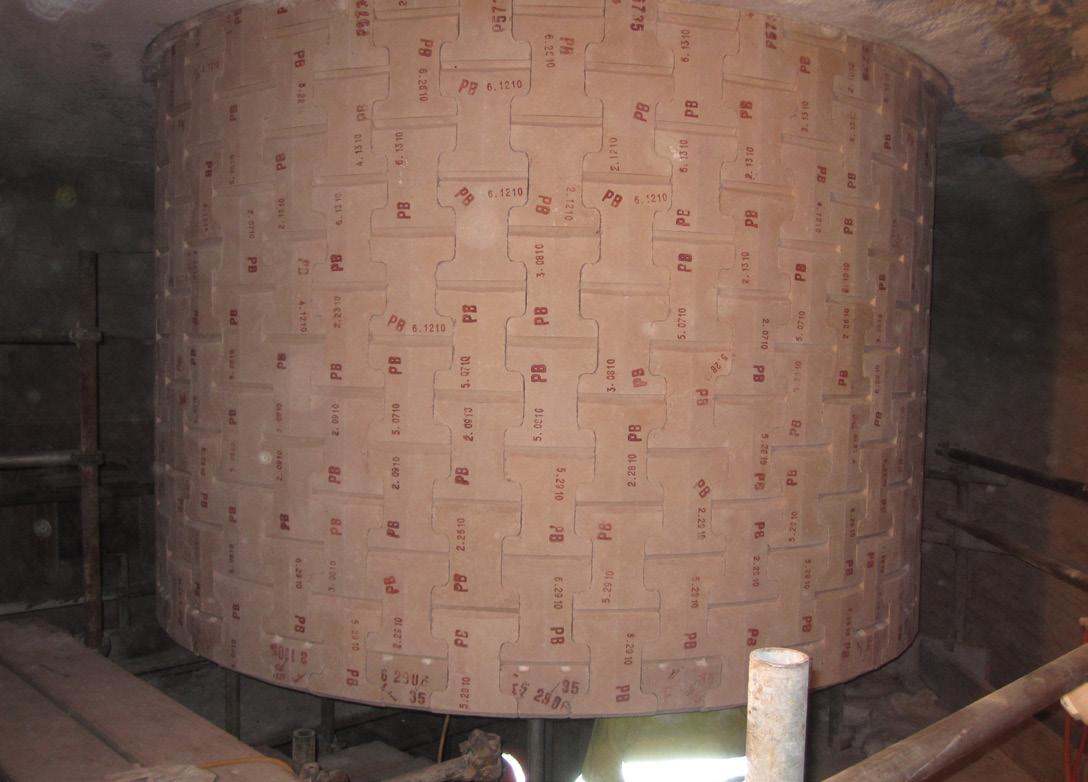
in the 1980s by HASLE Refractories,
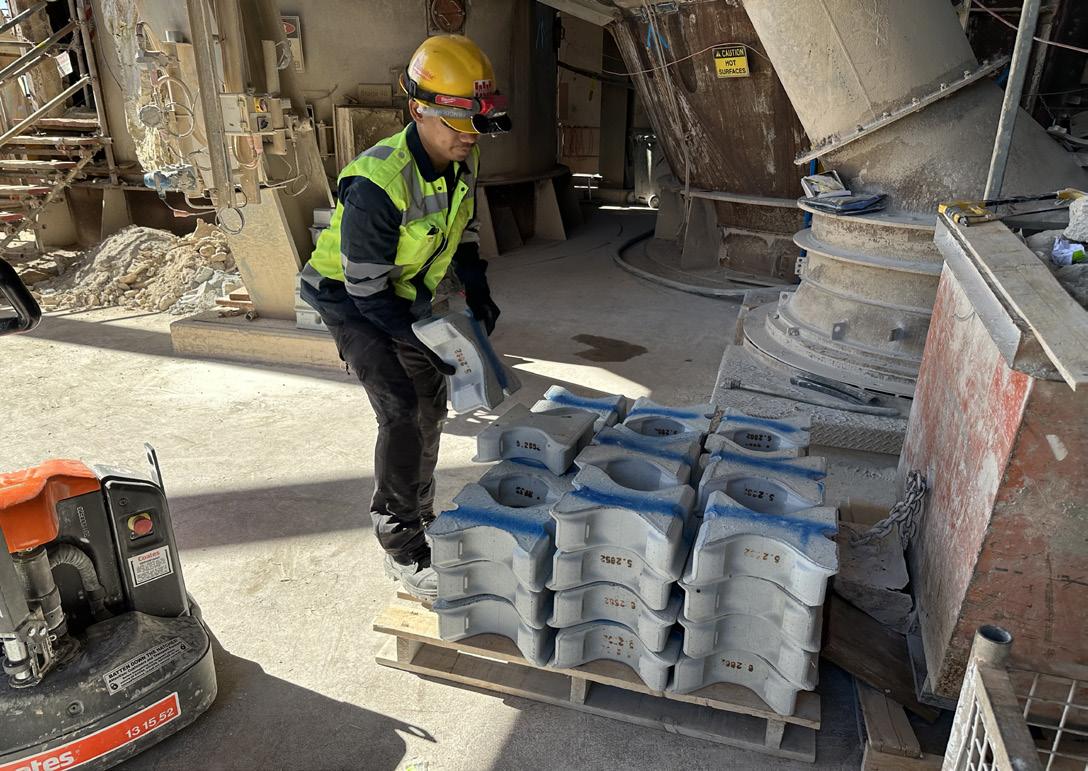
Due to the individual elements’ low weight of 6 – 19 kg, no heavy lifting equipment is required for handling, and it is possible to use the existing manholes for the installation.
The ADBRI Birkenhead plant, nestled by the St. Vincent Gulf and Adelaide’s skyline, boasts a rich history spanning more than a century. Developed the first generation of the Ceramic Vortex Finder was also installed at the ADBRI Birkenhead plant. Here an installation in 2009 is shown.high-grade castable with pure synthetic and high-performance raw materials to ensure against impurities. Nanoparticles are included for high fracture toughness and optimal strength. In addition, the materials used provide high
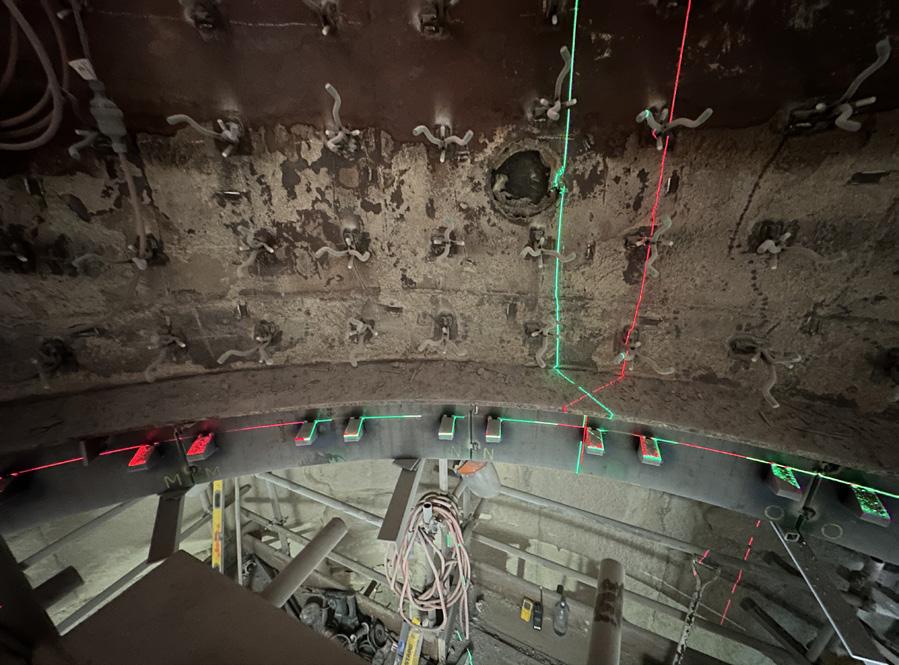
The alignment and level of the steel supporting are verified, prior to the installation of Ceramic Vortex Finder in the lowest stage cyclone at the ADBRI Birkenhead plant in Southern Australia.
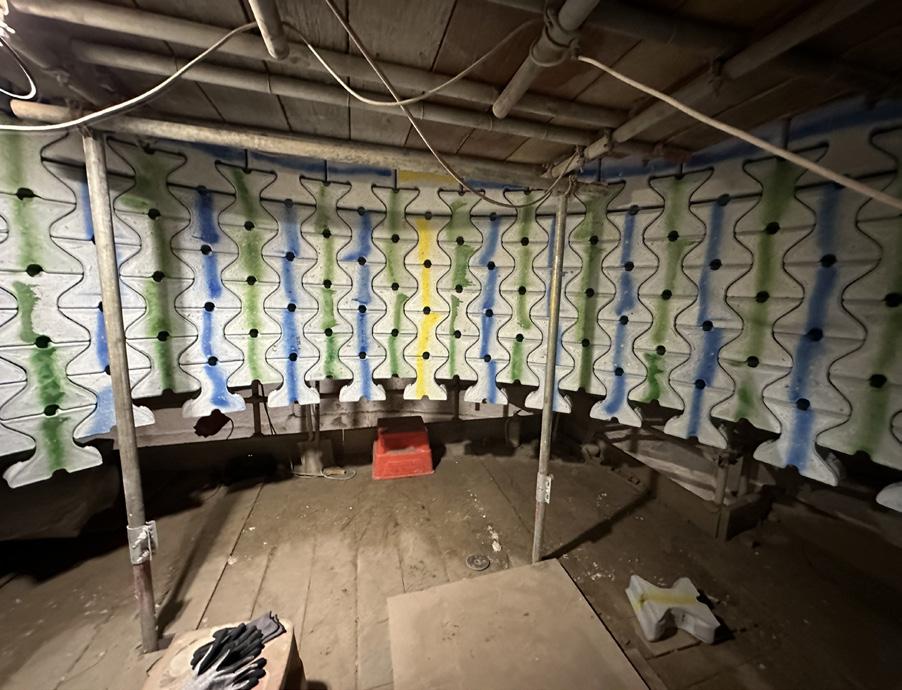
Assembling the GEN3-CVF; the top row of ceramic elements is placed on the brackets of the steel support ring; the remaining elements are suspended from the elements in the top row.
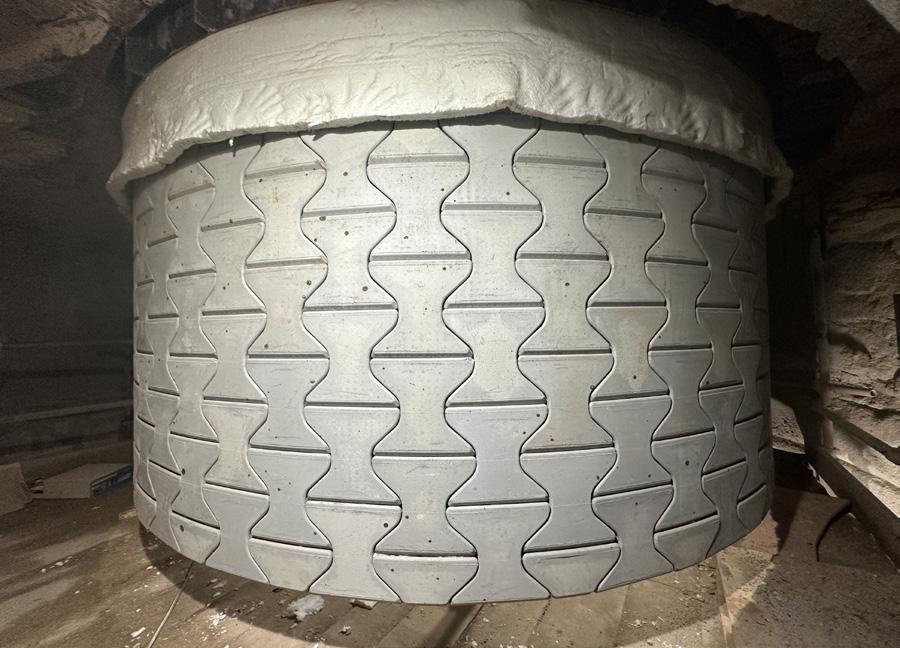
resistance to chemical attacks, making the CVF suitable for plants burning high levels of AF.
The GEN3-CVF elements are manufactured under strictly controlled conditions at HASLE’s factory in Denmark. Firstly, the shapes are carefully cast and cured in specialised moulds to obtain a smooth surface and their unique profile. Subsequently, they are pre-fired to elevated temperatures to achieve maximum strength.
The result is a dip tube capable of withstanding temperatures up to 1200˚C without deformation or creep and that exhibits high dimensional stability. This ensures that the CVF does not buckle, maintaining a high separation efficiency throughout its service life. Furthermore, the small-sized ceramic elements minimise the risk of cyclone blockage in case of falling elements as they can pass through the feed pipe, allowing operations to continue.
The CVF has a high level of corrosion resistance against all common corrosive substances in the gas phase as well as a high abrasion resistance. Additionally, only the precast refractory elements are in contact with the hot gas phase reducing the chromate emissions significantly.
A new trial
In light of the introduction of the GEN3-CVF in 2022, HASLE engaged in discussions with the management at the Birkenhead plant. Seeing potential for operational process benefits and equipped with a more robust dip tube solution, a trial in the lowest stage cyclone was initiated. Beyond the projected fuel savings, the primary goal is that the CVF will contribute to an enhanced RDF combustion. This, in turn, aims to reduce the amount of unburnt fuel carried down to the kiln inlet area, consequently minimising undesirable build up in that area.
Flexible installation
The HASLE Ceramic Vortex Finder was installed in the lowest stage cyclone, at the ADBRI Birkenhead plant in January 2023, featuring a diameter of approximately 3.7 m and a length of 2 m. The installation was assisted by an experienced supervisor from HASLE, supporting the work effort of the local installation team.
The installation sequence began with welding the steel support ring to the roof casing. Subsequently, ceramic fibre blankets were placed against the steel ring to allow adequate space for thermal expansion. Following this, the assembly itself took only a few hours. The assembly process was initiated by placing the top row of ceramic elements onto the brackets on the steel support ring. The remaining CVF elements were suspended
The CVF (Gen3) fully assembled in the lowest stage cyclone at ADBRI’s Birkenhead plant.from the elements in the top row. Thanks to the low weight of each individual element (ranging from 6 – 19 kg), no heavy lifting equipment is required for handling, and it is possible to use the existing manholes for the installation. Lastly, the final row of CVF elements was securely locked in place with a heat-resistant sealant.
The CVF is structured as a modular system of precast, ceramic elements, providing adaptability to individual operating conditions and cyclone dimensions. Its standardised shapes with different angles interlock through advanced tongue-and-groove joints and offer variable diameter options up to 7.5 m and lengths up to 5 m.
Surpassing one year lifetime in lowest-stage cyclone
After a complete year of continuous operation, the CVF at the Birkenhead plant underwent a comprehensive inspection during the annual shutdown in January 2024. Initially, the plan was to replace the existing CVF with a new one. However, the inspection revealed that the current CVF was in excellent condition. The thorough examination indicated no signs of damage, leading to the decision to extend its operational life for another 12 months, bringing the lifespan up to two full campaigns.
Experiences from Europe
The GEN3-CVF has also been applied in cement plants with even higher proportions of AF usage. A 5000 tpd cement plant in Germany, operating on 82 – 95% RDF, was facing short lifetimes of its steel dip tubes in the lower stages of the preheater. In the lowest stage cyclone operating at around 950˚C, the dip tube typically only had a 2 – 3 month lifespan, before it was necessary to switch it due to heavy corrosion from the burning of AF. Consequently, the plant decided to explore the GEN3-CVF, with the latest installation reaching a one year lifetime. It achieved a significantly longer lifespan compared to the steel dip tube previously used, and is now able to run a full campaign. Further up in the preheater, the plant also successfully deployed a CVF in the second-lowest stage cyclone operating at temperatures up to 850˚C, which has now achieved a three year lifetime and continues to be in operation.
About the author
Preecha Chokjarearnsuk is the Head of Sales and Technical Support for Southeast Asia and Australia at HASLE Refractories, Thailand. Preecha holds a bachelor’s degree in industrial engineering from Mahidol University and has 15 years of experience working with refractories in high temperature industries.
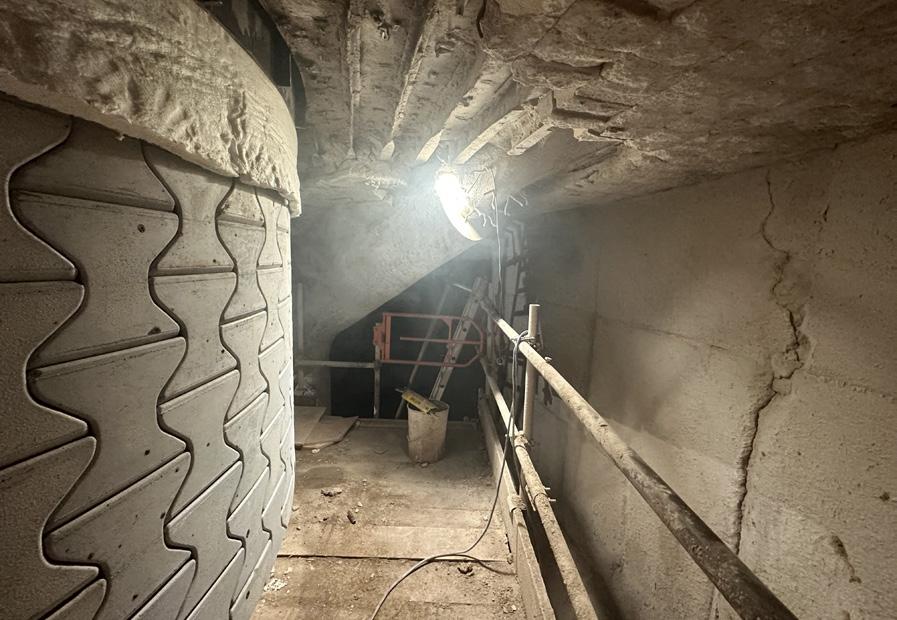
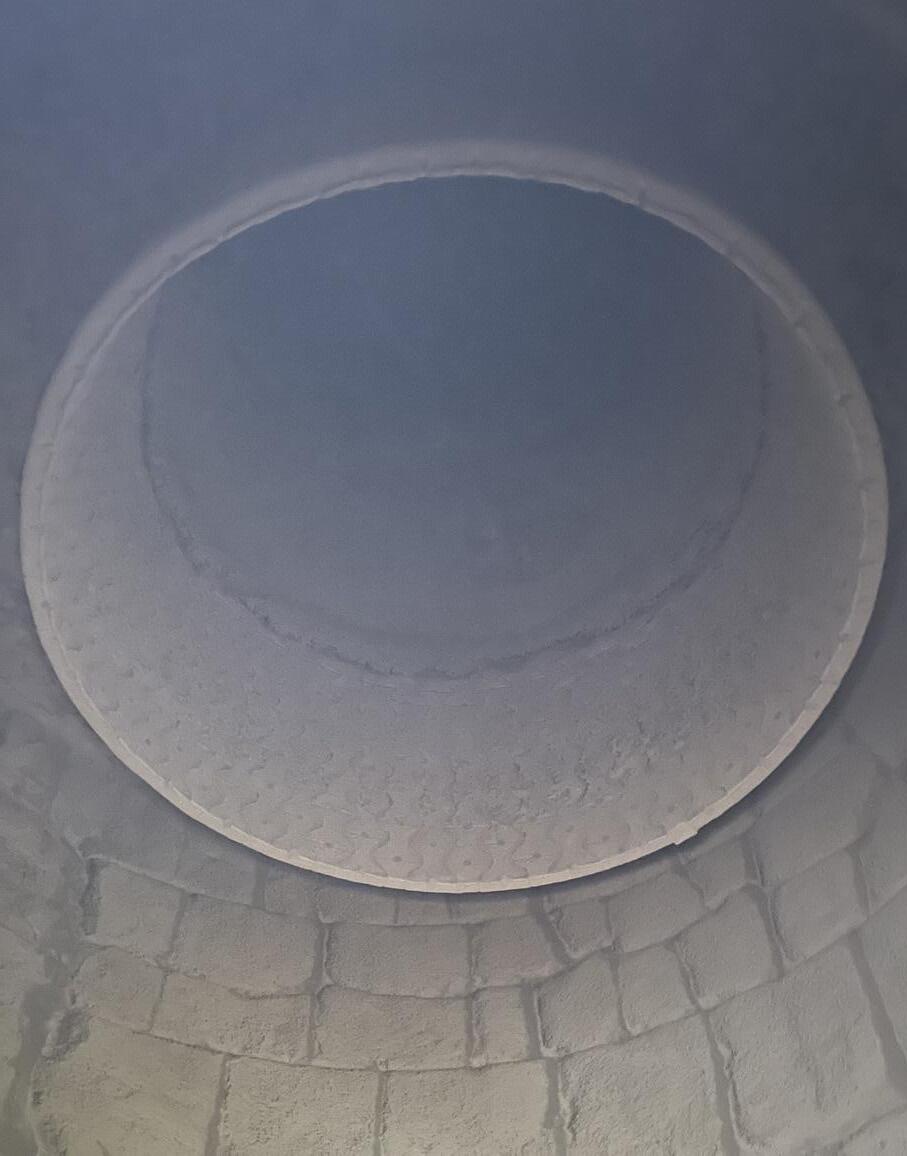
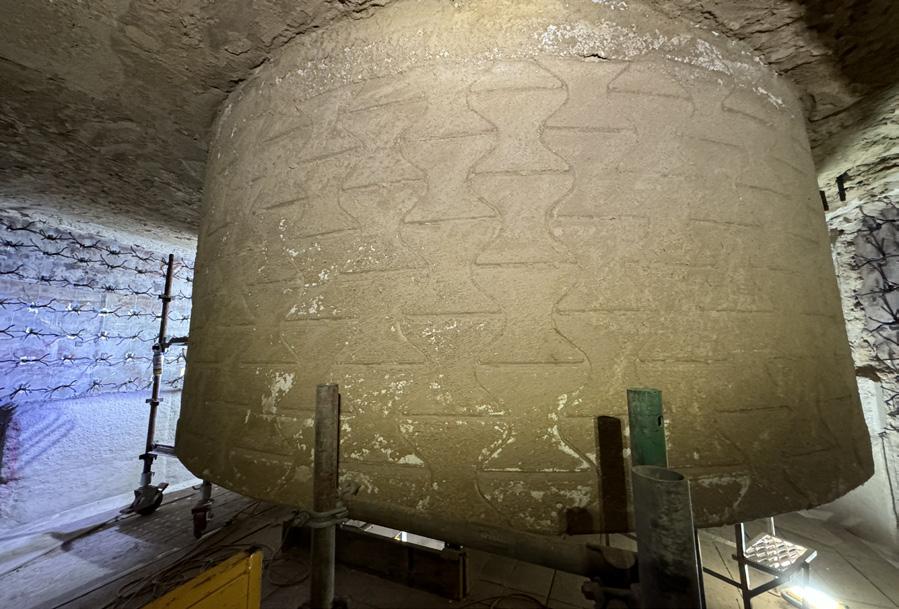
After a year of operation, the CVF in the lowest stage cyclone at the ADBRI Birkenhead plant underwent a comprehensive inspection. It was found to be in excellent condition with no visible damage, leading to the decision to continue its operation.
Scaffolding is often required to access the installation area in the cyclone roof. The CVF at the ADBRI Birkenhead plant after four months of operation.
Artificial intelligence turns cement production green
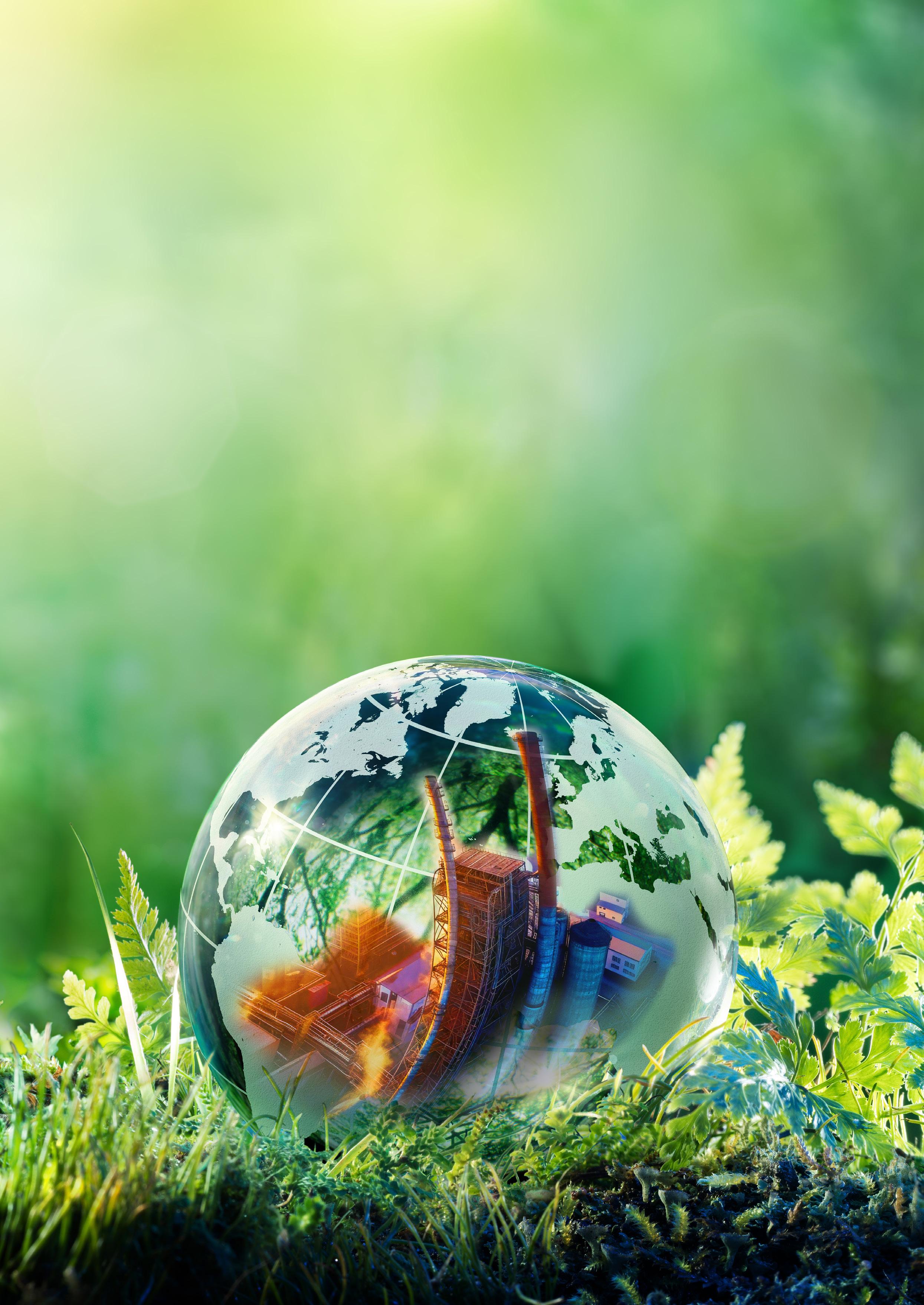
Mark Israelsen, Quantum IR Technologies, explains how the use of AI analytics can help to reduce energy consumption and emissions in cement kilns.
Artificial intelligence (AI) is revolutionising cement production by driving advancements towards more sustainable and efficient practices. As the world grapples with the pressing need to mitigate environmental impacts, the cement sector, known for its substantial carbon footprint, is turning to AI to lead the charge in reducing emissions and energy consumption. By harnessing the power of advanced analytics, AI is capable of processing and correlating millions of data points in real-time. This wealth of information provides cement operators with prescriptive insights that enable them to fine-tune kiln operations for peak performance and to implement predictive maintenance strategies. Such optimisation not only reduces energy usage but also extends the life of equipment, thereby contributing to a more environmentally friendly and cost-effective production process.
Energy in global cement production
The cement industry, known for its substantial energy requirements, occupies a significant position as one of the most energy-intensive sectors worldwide. It accounts for a notable portion of total industrial energy use, with its energy consumption primarily rooted in the production processes required for cement manufacturing. These processes encompass a range of operations from quarrying and crushing to grinding, blending, and the operation of rotary kilns. The industry’s energy use is characterised by both direct and indirect
consumption; the former pertains to energy directly utilised in production processes, while the latter refers to energy needed for powering auxiliary equipment and facilities.
Energy consumption relies heavily on fossil fuels, including coal, oil, and natural gas, being the predominant sources of energy for the cement sector, essential for generating the thermal energy required in cement kilns for clinker production. Additionally, electricity plays a critical role in operating the diverse array of machinery, equipment, and lighting found within cement plants. Factors such as kiln technology, equipment, facility age, and efficiency, as well as the nature of the processed raw materials, influence the industry’s energy consumption levels.
Production methods like the wet and dry processes – with the latter being more energy-efficient due to reduced heat requirements – further delineate the industry’s energy usage patterns. The industry’s energy consumption intensity, often measured per ton of clinker or unit of cement produced, sheds light on plant energy efficiency and highlights potential areas for enhancement.
As a result, the industry faces the challenge of reducing its environmental impact while meeting the growing demand for cement. Adopting energy-efficient technologies, including alternative fuel (AF) usage, waste heat recovery systems, and advanced kiln designs, offer significant potential to curb energy consumption and associated carbon emissions. The exploration and implementation of
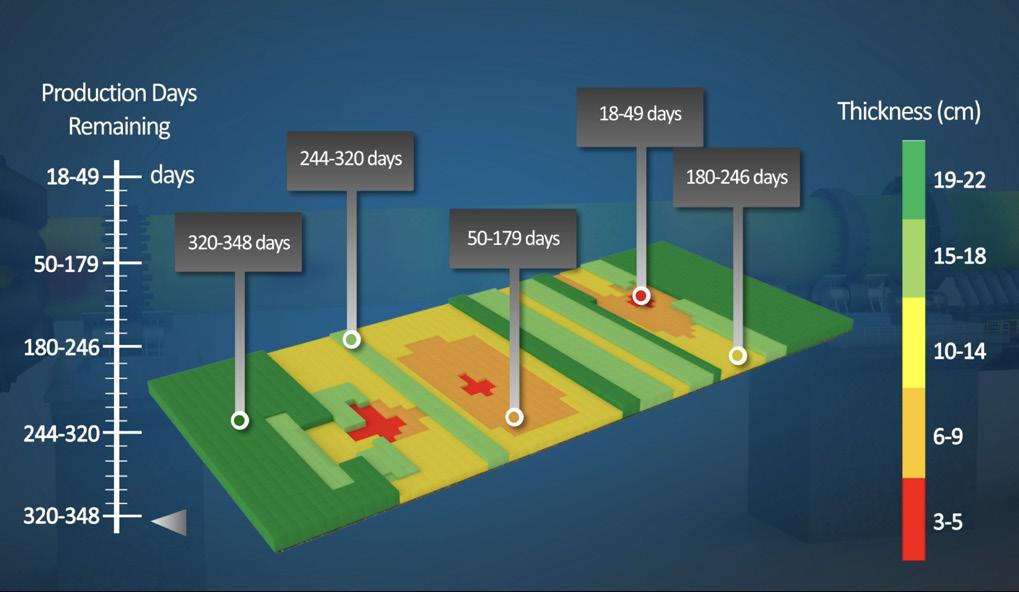
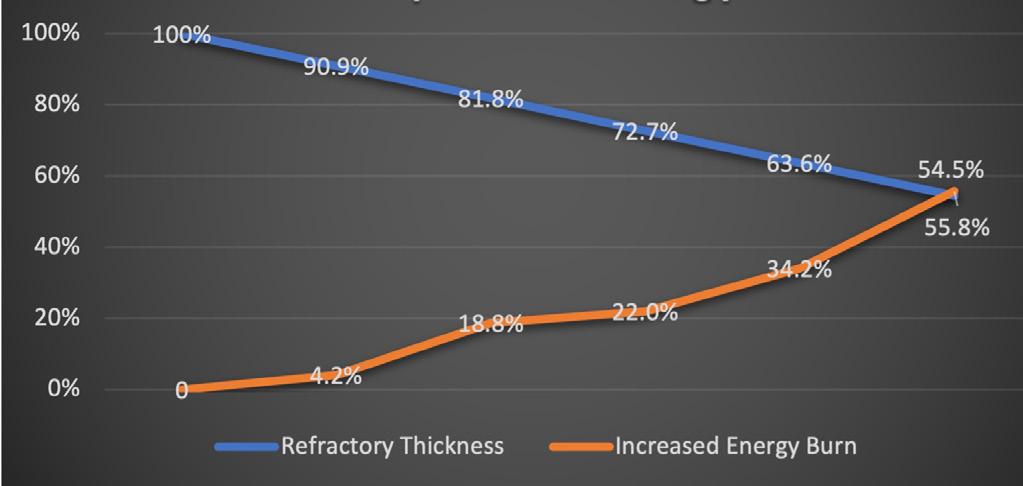
AF (e.g., biomass, municipal solid waste, and tyres) and raw materials (such as industrial by-products or natural pozzolans) are strategies aimed at reducing the energy footprint and promoting sustainability within the industry.
While the cement industry’s high energy intensity presents considerable environmental challenges, opportunities abound for reducing energy consumption through technological innovation and sustainable practices. These efforts are pivotal not only for minimising the sector’s environmental impact but also for advancing towards a more sustainable and energy-efficient future.
AI optimises kiln refractory life
AI optimisation of the kiln refractory is a critical advancement in the cement production industry, offering a strategic approach to emissions reduction and energy efficiency. With a precise focus on the management of kiln refractories, AI systems are equipped with advanced sensors that continuously monitor refractory thickness, delivering real-time data that drills down to the level of individual bricks. This granular level of monitoring is instrumental in assessing the refractory’s rate of deterioration, which directly influences the thermal efficiency of the kiln.
AI’s predictive capabilities play a vital role in forecasting the lifespan of the refractory lining, giving operators a clear estimate of the number of production days remaining before maintenance is required. By predicting the optimal time for refractory replacement, AI significantly mitigates the risk of unforeseen kiln shutdowns, which are costly in terms of both production loss and energy waste. The proactive management of the refractory life not only extends the operational period between maintenances but also maximises the revenue potential of the kiln by ensuring it remains in service for the longest possible time.
Furthermore, maintaining the integrity of the refractory lining through AI optimisation translates to better insulation of the kiln. This, in turn, decreases the amount of energy needed to reach the high temperatures required for clinker production, leading to a direct reduction in emissions. The energy savings are twofold: they lower the overall environmental impact of cement production and simultaneously result in significant cost savings for the producers.
AI integrates refractory, energy and emissions optimisation
The integration of AI-based analytics into the monitoring and optimisation of cement kiln operations represents a significant leap forward in the pursuit of sustainability and efficiency in the cement production process.
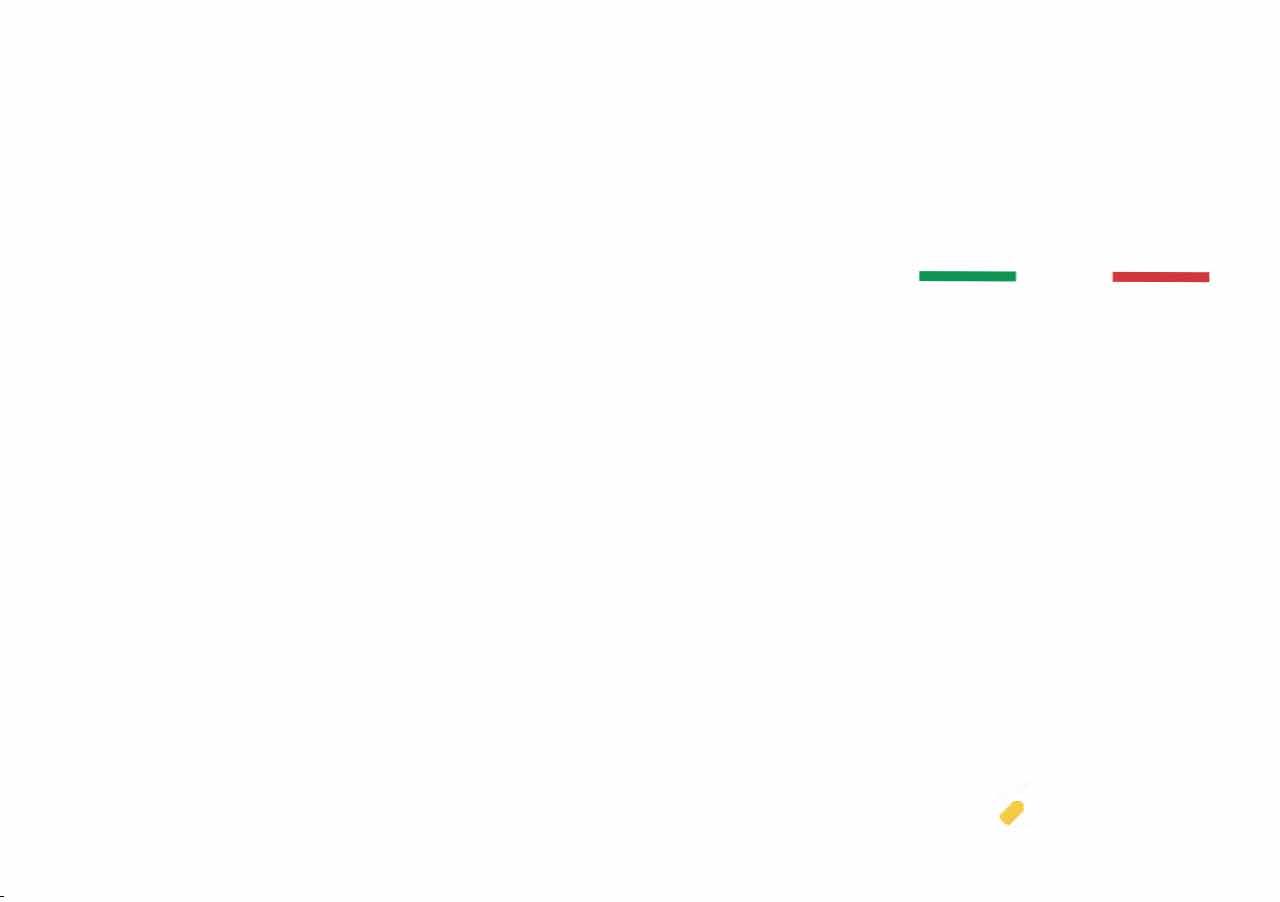
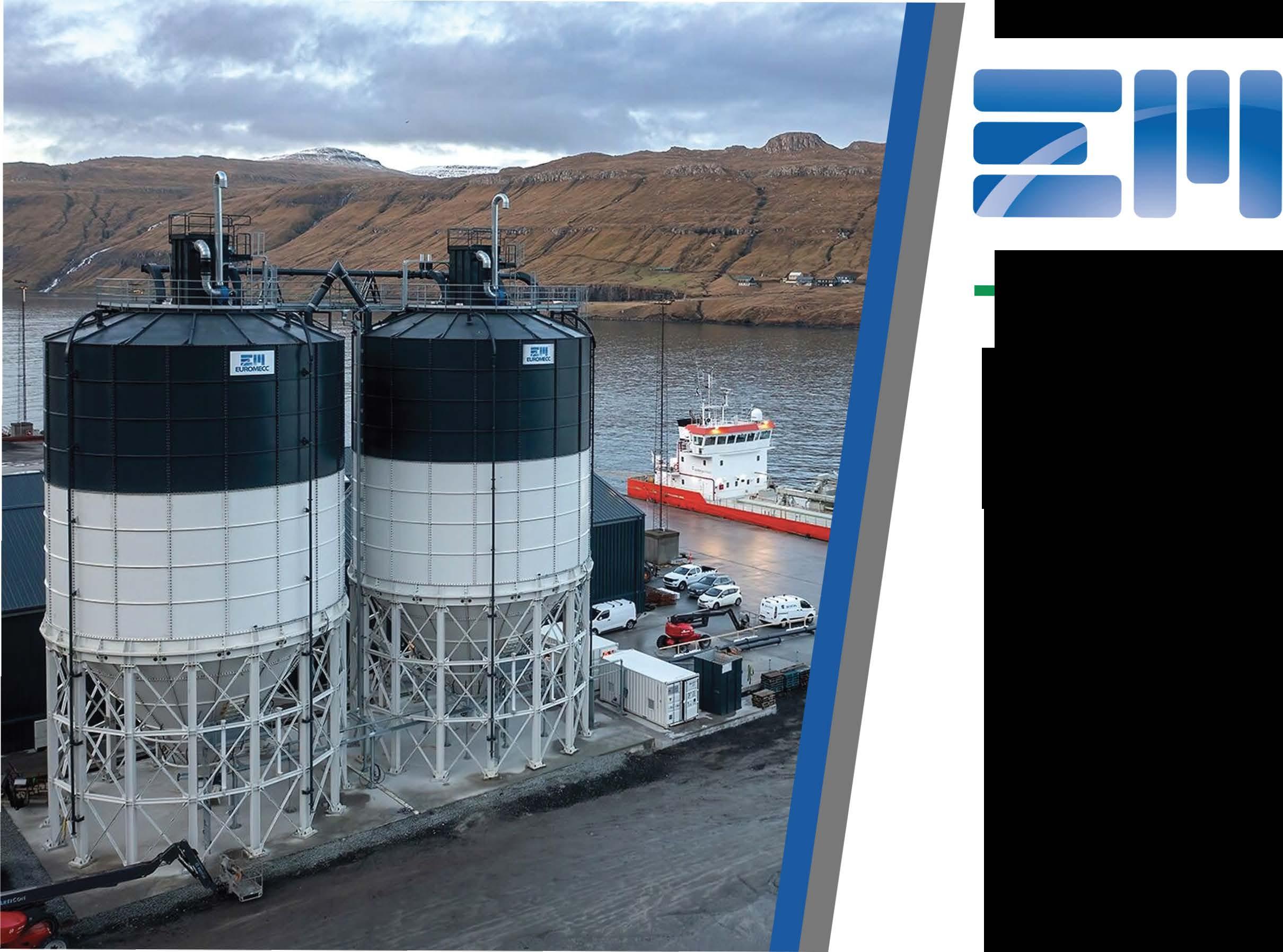
These advanced analytics systems are adept at continuously monitoring the energy emitted through the kiln shell, thereby providing a comprehensive view of the kiln’s thermal performance. By assessing the heat loss and correlating it with the energy required to maintain optimal internal temperatures, AI analytics offer a nuanced understanding of the kiln’s energy dynamics.
This capability extends to calculating the additional energy consumption necessitated by any inefficiencies in the kiln’s thermal management, including suboptimal refractory thickness or uneven wear. Importantly, these systems can also estimate the consequent increase in CO2 emissions resulting from the excess energy usage. Such insights are critical, as they highlight the direct link between operational efficiency, energy consumption, and GHG emissions within the cement manufacturing process.
AI analytics play a pivotal role in synthesising this data into actionable intelligence. By leveraging advanced algorithms and machine learning techniques, these systems can generate an analytical curve that maps the interplay between energy consumption, refractory thickness, and emissions. This curve serves as a powerful tool for identifying the point of optimal energy usage, where the kiln operates at peak efficiency with the lowest possible emissions profile.
The implications of this technology are profound. By providing a clear visual of the relationship between these key operational parameters, Quantum IR AI analytics enable plant managers and engineers to make informed decisions aimed at optimising production. This includes determining the ideal timing for refractory maintenance or replacement, adjusting operational parameters to minimise heat loss, and selecting the most efficient fuel mix to reduce energy consumption and emissions.
Moreover, the predictive capabilities of AI-based analytics facilitate a proactive approach to maintenance and operations. By forecasting potential inefficiencies and recommending pre-emptive actions, these systems can help avoid unplanned downtime and ensure the kiln operates within its optimal energy and emissions envelope.
In essence, AI-based analytics offer a comprehensive solution for enhancing the sustainability of cement production. By optimising energy consumption, extending the life of critical kiln components, and minimising emissions, this technology supports the cement industry’s transition towards more sustainable and environmentally friendly practices.
About the author
Mark Israelsen is the founder and CEO of Quantum IR and holds over 10 AI-based patents in the cement and petrochemical industries.
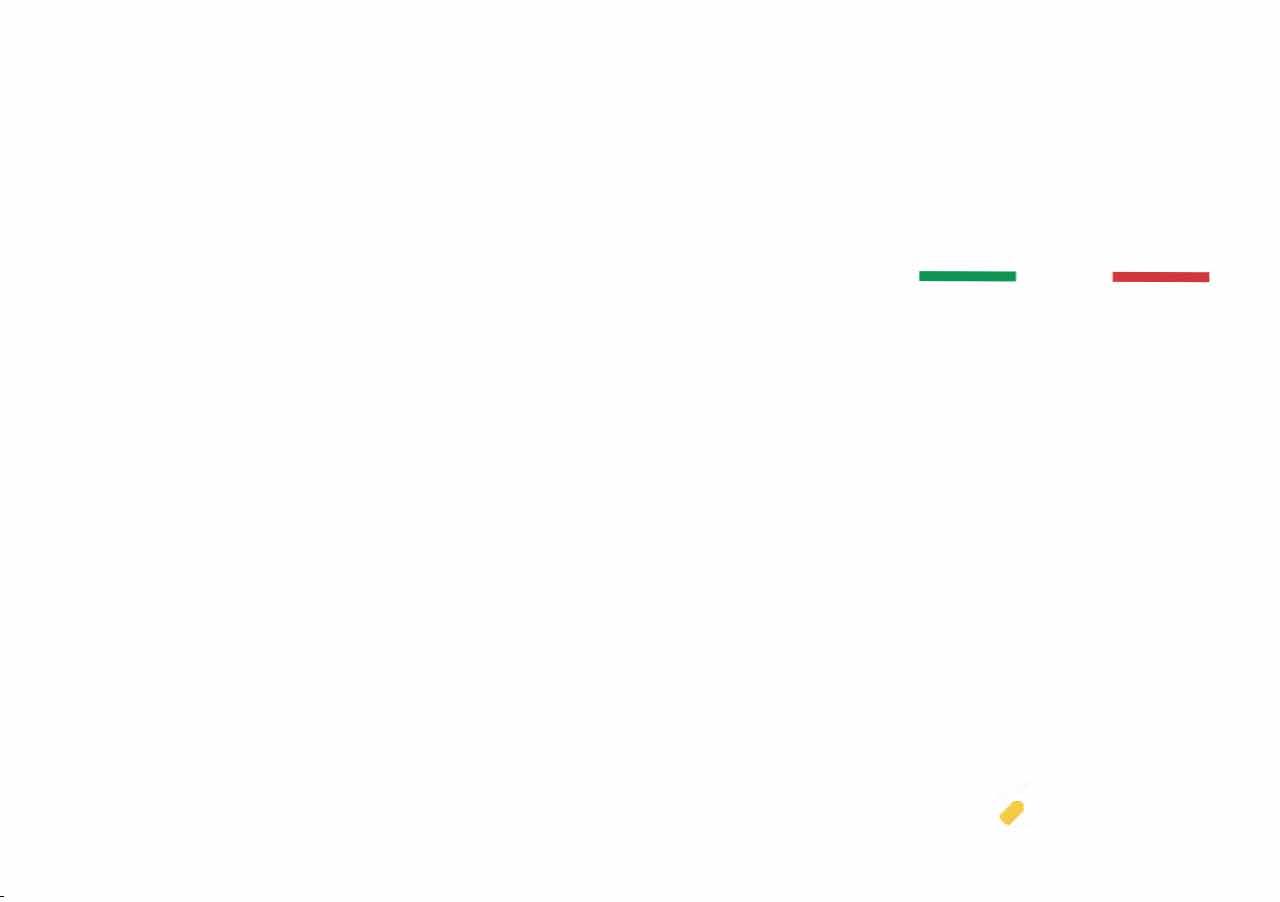
• BULK MATER IALS STORAGE & HANDL ING SO LU TIONS
• MAR INE TERMINALS
• ECO-HOPPERS
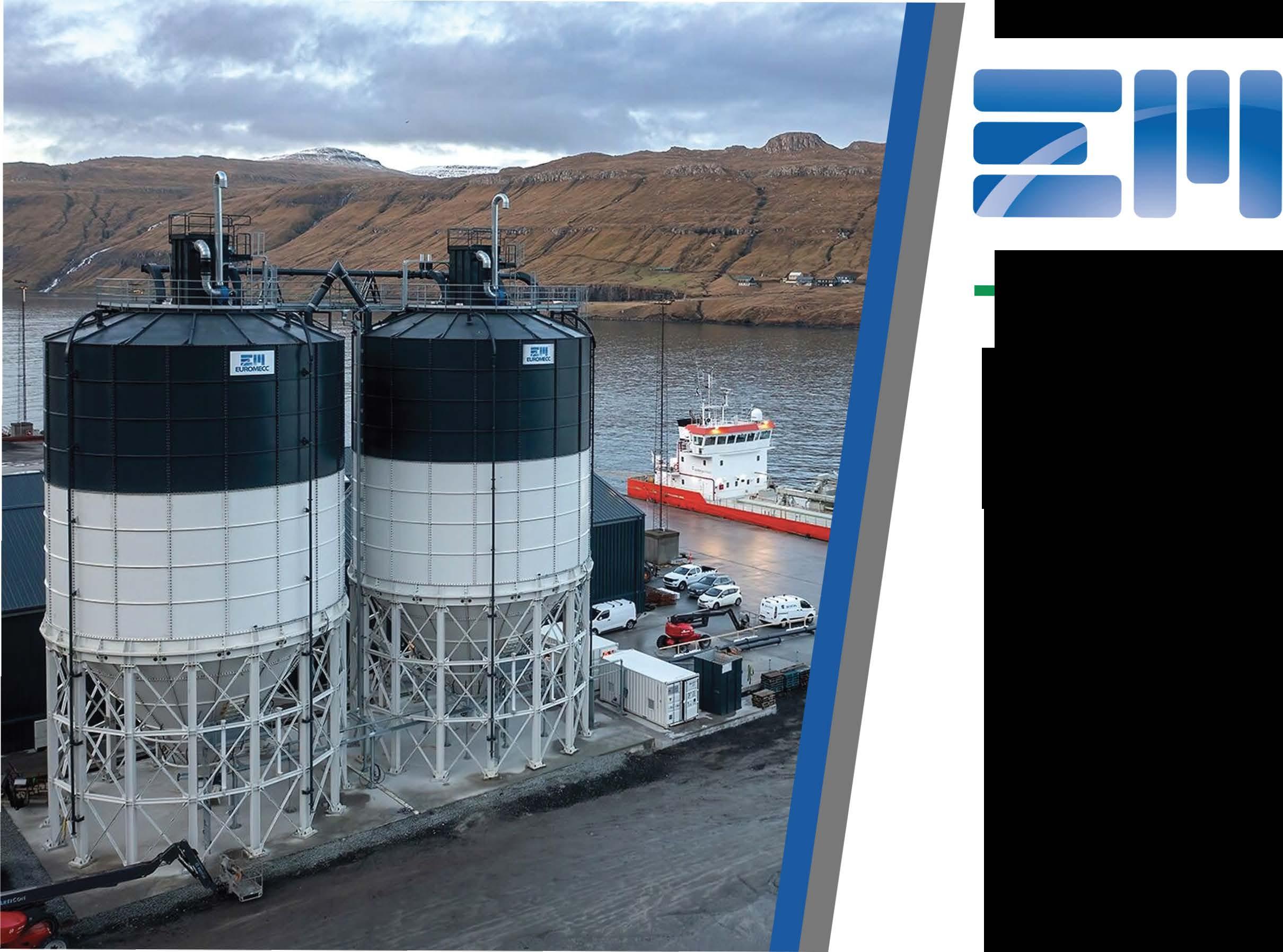
• TURNKEY INSTALLAT IONS
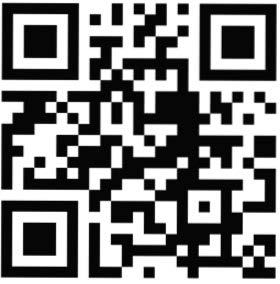
SCAN THE QR-CODE AND VISI T OUR WEBSI TE TO FIND OU T MORE
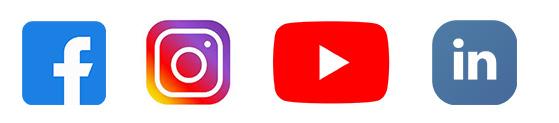
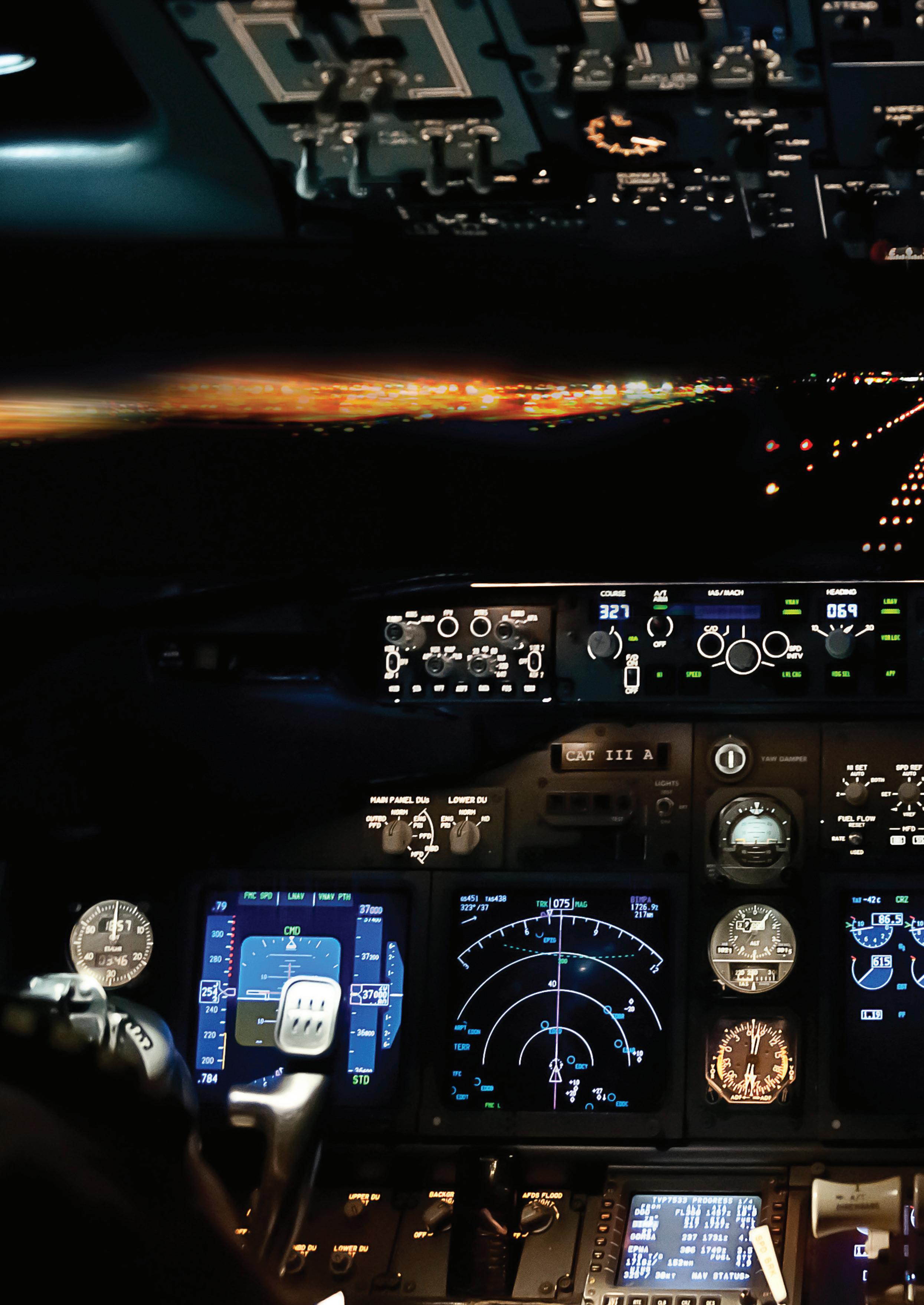
Autopiloting the cement process
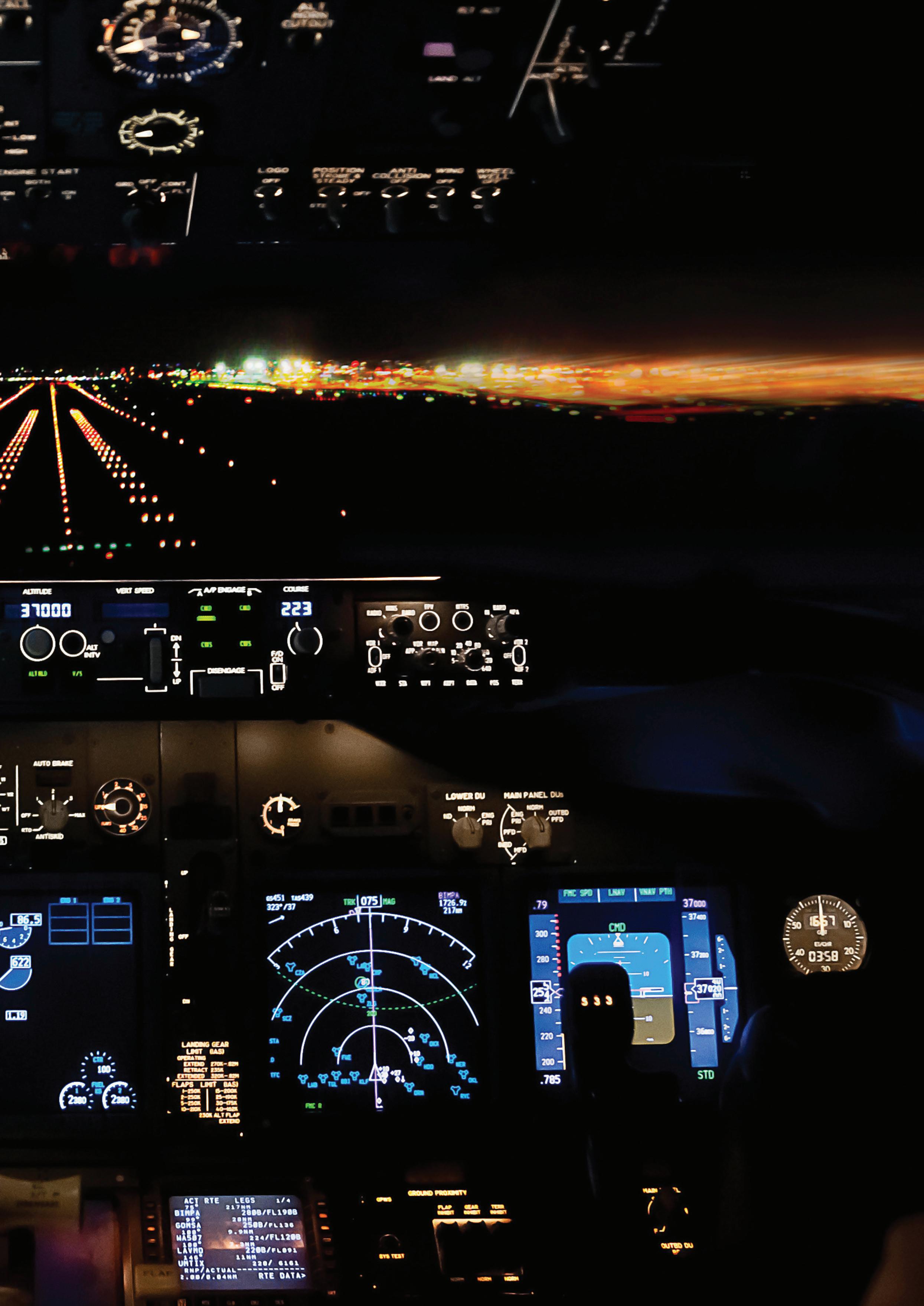
Fayez Boughosn and Ighnatios Maatouk, ES Processing, explore the benefits of autopiloting the cement manufacturing process.
The cement industry is being reshaped through various challenges such as climate engagement initiatives, digitalisation, energy costs, and market volatility.
ES Processing developed its first APC-AI CMO as a ball mill autopilot, introducing artificial intelligence (AI) and advanced process control as new levers for cement manufacturing, continuously optimising the mill grinding process.
The company’s CMO (cement mill optimiser for ball mills), VMO (vertical mill optimiser) and KPO (kiln process optimiser) solutions are field proven and have consistently evolved with the latest technology.
Autopilot solutions
The CMO, VMO and KPO solutions represent a complex combination of AI, machine learning and advanced process control, able to predict product quality every 30 seconds instead of performing routine sampling every hour or more. They then perform the proper actions on the kiln and mills’ manipulated variables every 30 seconds. Predictions are continuously adapted to the new process conditions such as quality of throughput material, feed rates, rejects, pressure, etc.
These solutions help transform the cement manufacturing process into proactive, autopiloted operations, embedding continuous accurate predicted product quality into
a continuous decisions matrix of process optimisation.
Process optimisers
The processes in cement manufacturing, especially clinkerisation and grinding, are highly nonlinear and unstable, with directly impact product quality, plant performance, and operational costs. Therefore, the main target behind ES Processing’s advanced optimisers (CMO/VMO/KPO) is to enhance the production of uniform clinker/cement at the targeted quality. These solutions optimise the product quality, significantly reducing variations, whilst boosting the output and stabilising the overall process.
The CMO, VMO, and KPO solutions act as autopilot systems for the cement kilns and mills, enhancing the clinker reactivity and the cement fineness whilst ultimately increasing overall production and reducing the specific energy consumption.
They also continuously determine the optimum setpoints for the mill/kiln manipulated variables in order to establish a seamless operation while ensuring product quality and optimum performance.
Each solution’s main strategy is to provide inferred quality measurements, at a high frequency (every 30 seconds), to be used as a decision support system, helping to implement proper adjustments to selected manipulated variables. This speeds up operations with increased stability by reducing the traditional dead time caused by the lack of continuous quality analysis.
These solutions are composed of a complex combination of: f Soft sensors: These are very sophisticated but stable models formed by combining multiple data-based algorithms adopted from machine
learning and based on linear and non-linear identification techniques, PLS and genetic algorithms. They determine the best correlation between different process parameters and product quality results and thus are able to predict very accurately the main product quality indicators (blaine, residue, C3S, free lime) every 30 seconds.
f MPC: This is a highly complex multivariable model based on transfer functions built according to impulse tests results performed on each equipment. It is able to handle complex plant dynamics including long-dead times and non-minimum phase behaviour, constraint handling, hierarchical and weighted optimisation and predictive control. Thus, it can adjust the process manipulated variables every 30 seconds.
With this combination, the plant is consistently pushed to achieve its operational targets, driven by the continuous prediction of quality product and process reactions, along with the optimal adjustments of operating conditions. It is like having a dozen of the best highly-skilled operators continuously monitoring all process parameters, including online product analysis, and working simultaneously together to adjust the process parameters every 30 seconds to optimise the entire process.
Product quality prediction
The product quality has always been the weakest part of the chain in cement manufacturing due to many factors including: process time delay, sampling challenges, analysis accuracy as well as operation techniques.
Through understanding that the continuous monitoring of product quality helps to optimise the

CMO & VMO solutions, for horizontal and vertical mills, are maximising the performance of the cement process.
processes, ES Processing introduced its soft sensors to predict, every 30 seconds, the clinker/cement quality. Numerical data-based algorithms, adopted from machine learning and AI, build the core of the soft sensors. Adapting engineering correlations between the plant historical process and quality data, the soft sensors are used to infer cement fineness (blaine and/or residue) and clinker quality (C3S and/or free lime) from a defined set of inputs that show a strong correlation with the outputs.
Eventually, these soft sensors act as real-time product quality measurement devices, providing continuous feedback to the control systems even in the absence of laboratory data. Once laboratory measurements become available, the soft sensors use the results to dynamically improve and tune their predictions.
A chess strategy for advanced process control
Under normal operation, the CCR operator checks the product quality analysis and, based on other process indicators, selects a combination of actions on the kiln/mill. Technically, a skilled operator would have to decide and make calculated adjustments by using their experience to understand the possible process reactions. For improved performance and stable operation, a computational tool is required to exploit the current process indicators and past conditions of the plant in order to predict precisely the future plant behaviour and calculate a combination of control moves.
The MPC module of the CMO/VMO/KPO solutions, built based on advanced numerical algorithms derived from the plant data, applies
the famous chess-game strategy, consisting of taking continuous and simultaneous actions (every 30 seconds) on the different manipulated variables of the mill/kiln while always predicting the process reaction for the next 120 moves (one hour of operation).
Eventually, the MPC actively controls and stabilises the mill/kiln in real time, aiming to produce a uniform product at the best targeted quality along with an optimised performance resulting in increased volumes at lower costs.
About the authors
Fayez Boughosn is the founder and CEO of ES Processing. Fayez started his career as an Automation & Process Control Engineer for Holcim, where he worked with Siemens to develop one of the most advanced cement production lines of the time. Moving on as a Siemens Solution Partner, he led numerous challenging process control projects worldwide. Coupling his passion to innovate with his cement industry experience, Fayez founded ES Processing in 2007.
Ighnatios Maatouk is the Process expert & APC Projects Manager at ES Processing, managing the most challenging projects of advanced process control and AI solutions for cement plants’ optimisation. Ighnatios started his career as a site engineer for power plants and afterwards served in engineering managerial roles in the cement industry for Holcim as Process Performance Manager. Ighnatios’ ambitions for bringing innovation and AI solutions to the cement Industry led him naturally to join ES Processing in 2018. KPO
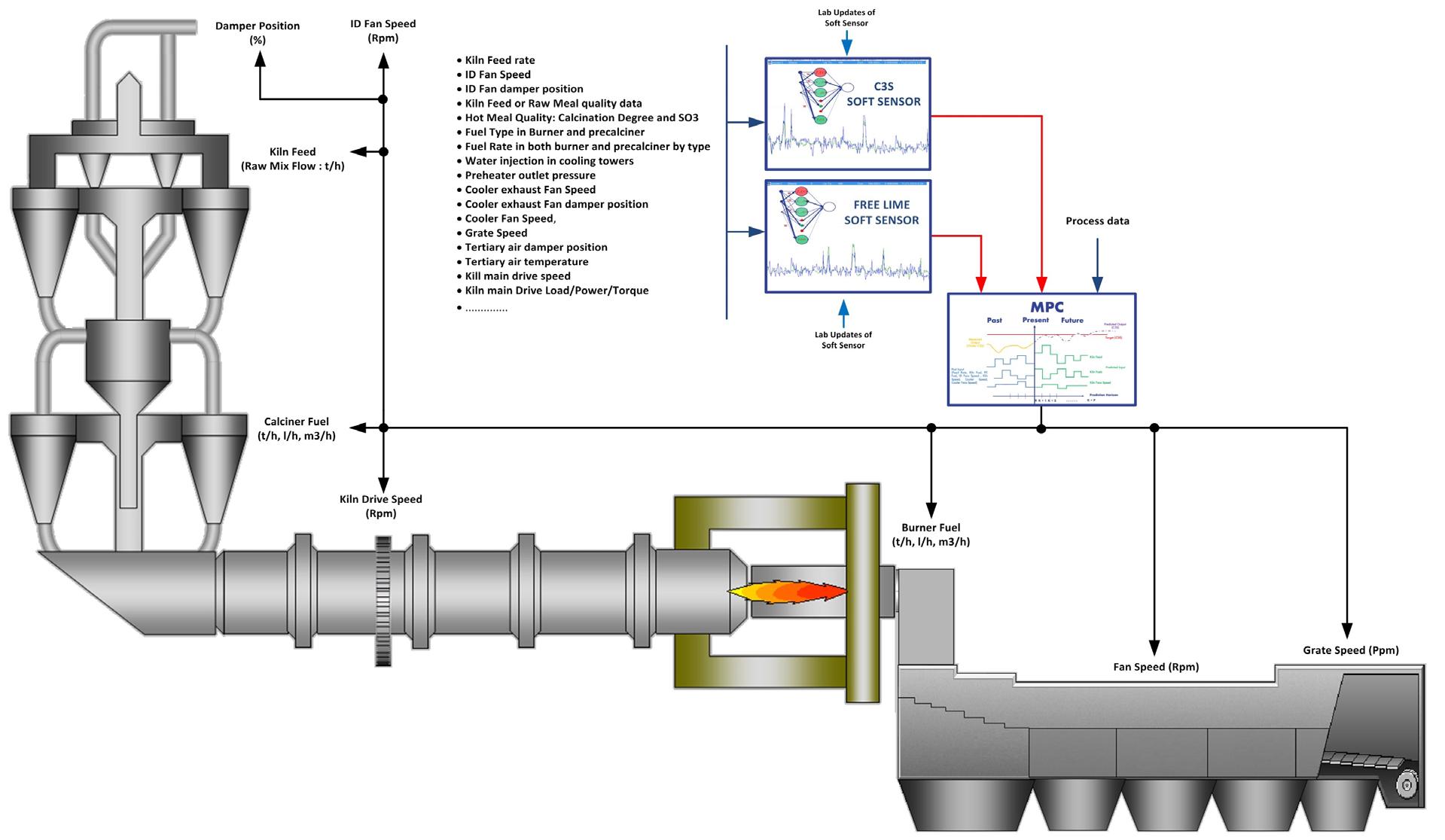
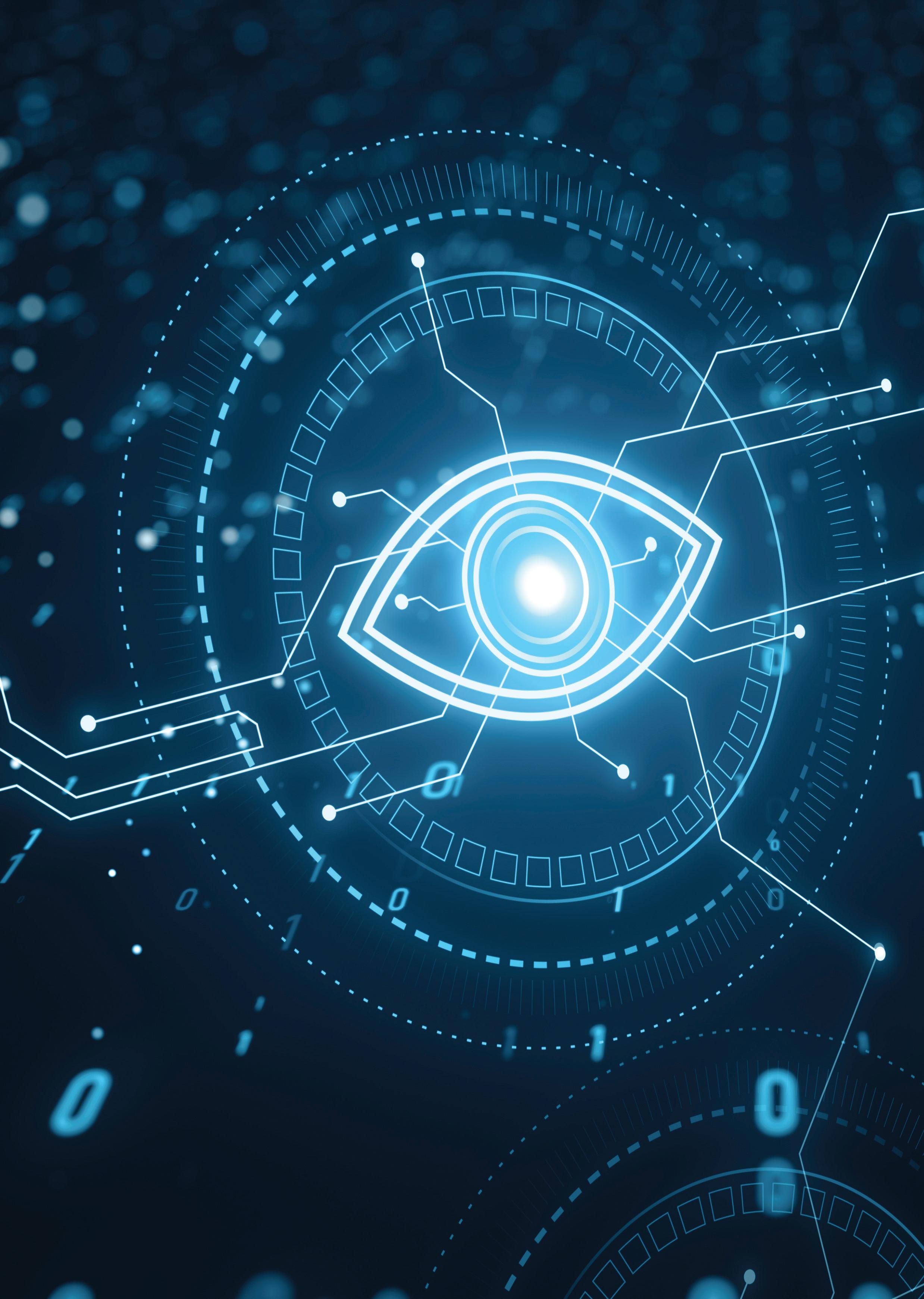

All eyes on AI
Chris Kiddle, AVEVA, explores the growing role of AI in the cement industry and considers both the benefits and the risks.
Few industries are exempt from the wave of artificial intelligence (AI) sweeping across the digital landscape. The cement industry is not exception when it comes to recognising the power of AI and the opportunity it presents to the sector. Early use cases promise prolonged efficacy. Positive impacts are being seen through the cement manufacturing portion of the supply chain from energy efficiency, improved carbon capture, increased uptime, automated performance enhancements of plant control, matured usage of applications in the supply chain optimisation via integrated planning and AI suggestions to performance variables to name a few examples of use.
With the promise of optimising production processes, reducing energy consumption,
enhancing quality and improving supply chain management via AI, are cement companies actually achieving higher operational efficiency, cost savings, and environmental sustainability?
This article plans to explore the opportunities AI presents in cement manufacturing; consider it a snapshot in time, with AI posing several promising opportunities for future applications.
Why AI?
But firstly, why is AI critical to cement production? McKinsey noted that companies have several options to decarbonise cement: “Optimistically, our analyses show that CO2 emissions could be reduced by 75% by 2050. However, only a small portion (around 20%) will come from operational advances, while the remainder will need to come from technological innovation and new growth horizons.”1
While this is not the only reason, it is widely agreed there is no direct path to net zero for the cement industry at this time, so while technological investment races to solve this dilemma, it is critical to meet social expectations and increasing pressures such as lowering embodied carbon in the construction sector. To continue to be the construction material of choice, improving production capacity while reducing energy
consumption via means such as increasingly efficient production is critical.
From an operational architecture perspective, the cement industry is being propositioned by the application of AI to the process control layer.
This could be due to the improved computation power and increased training speed of deep neural networks, and the explosion of IIOT in the sector, which is driving a proliferation of available data and vast data storage facilities, using a combination of on-site, hybrid, and cloud architecture options.
Fit-for-purpose algorithms, combined with prescriptive actions, have proposed to make AI-infused analytics a regular part of operations oversight. Optimisation occurs when there is more access to data.
The application of security best-practices and requirements for IT environments are already being applied to AI systems. However, the opportunity to leverage open AI models (still considered to be in their infancy) and connecting this technology with production systems and sensitive corporate data that could be exposed to malicious cyber-attacks is not a supported practice that AVEVA has seen.
The use of open AI appeals far more to the scientists amongst us all, yet the quality of the source data and concerns regarding intellectual property are just a few known issues from amongst a litany of problems that face this rapidly maturing use case.
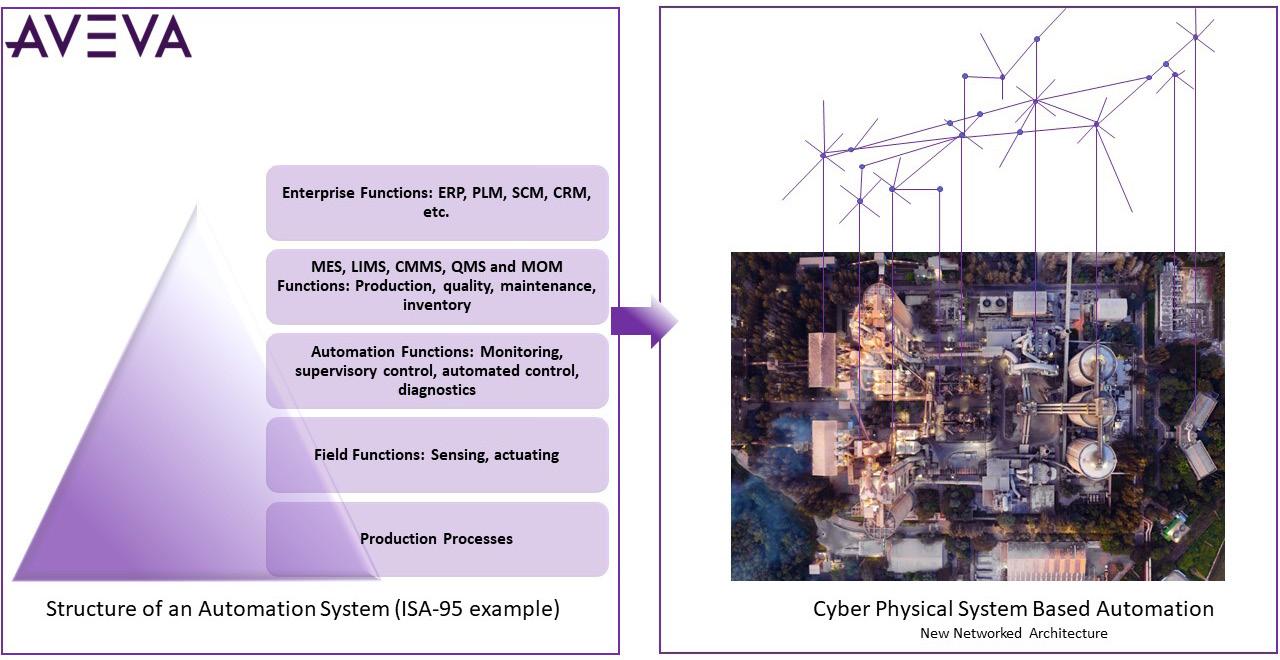
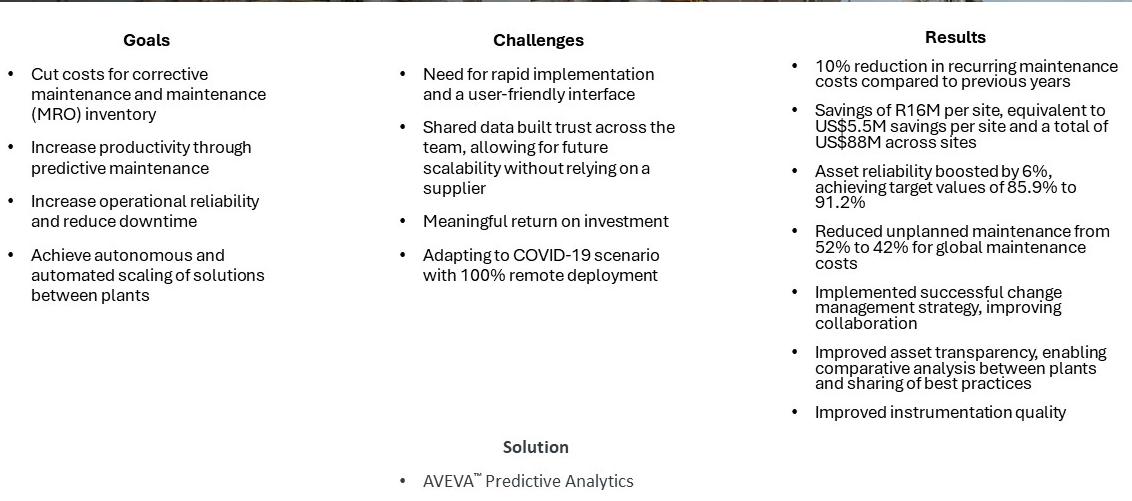
There is a risk that “the rapid adoption, deployment, and use of AI capabilities can make them highly valuable targets for malicious cyber actors. Actors, who have historically used data theft of sensitive information and intellectual property to advance their interests, may seek to co-opt deployed AI systems and apply them to malicious ends.”2
So, as industry embraces the opportunities presented by AI, it is critical to remember the fundamental building blocks of enablement; even beyond security the area of primary importance is establishing a solid data infrastructure. This is key to unlocking the power of AI. The challenge that AI presents in respect to integration into a
Integrating AI into a company’s data infrastructure is key to unlocking the technology’s potential.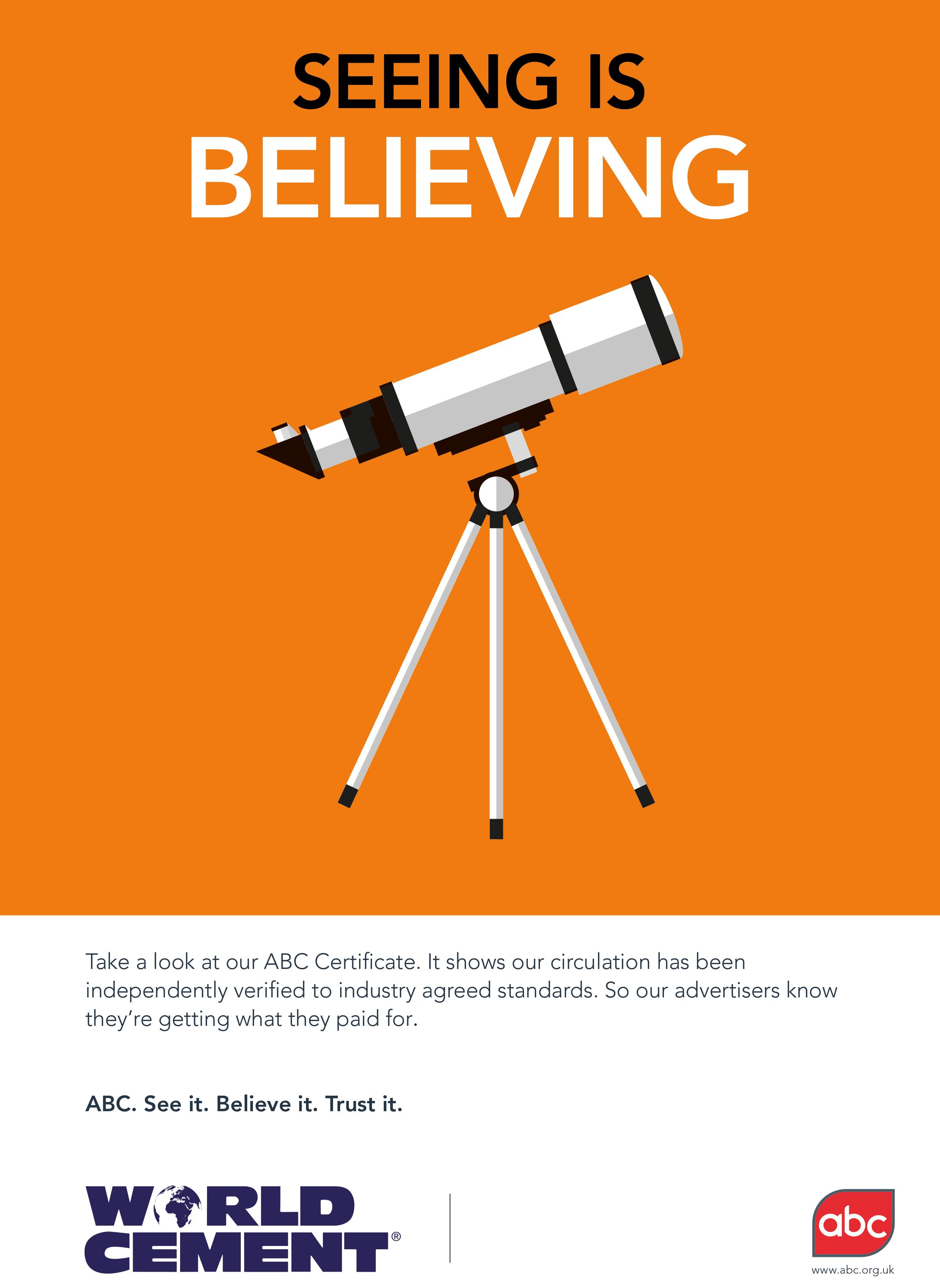
company’s data infrastructure is becoming more unique than the work of a control systems engineer or even what a business user would undergo when defining compliance to industry standards such as ISA95. It is expected to be a vastly different world in the future, and concepts such as Industry 4.0/Smart manufacturing networked architectures should be considered.
AI use-cases in the cement industry AI uses include examples like Nuvoco Vistas Corp, which has found that by “analysing data from sensors and cameras, AI algorithms can identify deviations from standard parameters such as particle size, chemical composition, and colour. This real-time analysis enables cement suppliers to adjust their production process, ensuring consistent product quality.”3
In keeping with the material movements, advances are also being seen in vendor hardware and software offerings with the likes of plant controllers: “Plant controllers can now simultaneously manage multiple control variables to optimise the plant’s performance. EcoStruxure Plant Advisor – Process Intelligence goes beyond a standard business intelligence (BI) dashboard by incorporating self-learning to recommend appropriate actions to help optimise a process. As a result, mining and cement plants can improve their overall equipment effectiveness (OEE) and water and energy consumption, while also increasing throughput.”4
In terms of looking at asset predictive behavioural analysis and prescriptive optimisation results, Votorantim Cimentos wanted to better understand their asset performance and implement a condition-based maintenance programme by using machine learning to predict asset behaviour.
“Using AVEVA Predictive Analytics we wanted to realise a vision of our next-generation plant operations, using data to shape our decision-making. Because AVEVA’s software is agnostic we were able to click in the systems within days, and see benefits within weeks, driving unparalleled optimisations that spanned our entire operations and our network of plants.”5
Boston Consulting notes that a competitive advantage exists for first movers in the adoption of Industry 4.0 and two of the five identified steps include:
f Analytics-driven predictive maintenance.
f Predictive quality analytics.
With respect to predictive quality models that make use of machine-learning algorithms to correlate the quality of each production batch with the relevant production parameters, these can result in a “predictive model that transforms the necessary quality of the final product from an output of the process into an input that guides decision making at every step of the way.”6
Based on the power of this competitive advantage, S&P Global anticipates that leaders in carbon emissions reductions will be better off than their less-efficient competitors because their marginal cost of cement production will be lower, thus increasing their competitive edge in the sector.
Summary
The points discussed in this article are only a subset of AI applications seen in the cement manufacturing process. The broader supply chain is experiencing a similar adaptation of evolving AI solutions.
To quote Milan Kundera, “A worker may be the hammer’s master, but the hammer still prevails. A tool knows exactly how it is meant to be handled, while the user of the tool can only have an approximate idea.”
The adaptation of AI should be performed with those that developed it and in the ways that it was intended, in order to provide maximum value. Developing the knowledge of the tool’s capabilities is a key factor for AI success. AI is revolutionising the cement industry by improving efficiency, reducing costs, and supporting the development of a sustainable path forward. This article has explored various AI applications in cement manufacturing, such as optimising energy usage, enhancing quality control, and predicting maintenance needs. Additionally, it has emphasised the importance of robust cybersecurity measures and data infrastructure to support successful AI implementation.
Overall, the transformative potential of AI in cement production and its role in addressing industry challenges are perfectly aligned. The adoption of AI in a controlled manner should expedite value realisation for the industry at financial, social, and environmental levels.
References
1. ‘Laying the foundation for zero-carbon cement’ – https:// www.mckinsey.com/industries/chemicals/our-insights/layingthe-foundation-for-zero-carbon-cement
2. ‘Deploying AI Systems Securely’ – https://www.cyber.gov. au/resources-business-and-government/governance-anduser-education/artificial-intelligence/deploying-ai-systemssecurely
3. ‘The Role of Artificial Intelligence in Cement Industry Transformation’ – https://nuvoco.com/blog/blog-the-role-ofartificial-intelligence-in-cement-industry-transformation
4. ‘Schneider Electric launches new scalable IIoT and AI solution for mining and cement industries’ – https:// www.se.com/ww/en/about-us/newsroom/news/pressreleases/schneider-electric-launches-new-scalableiiot-and-ai-solution-for-mining-and-cement-industries6279c9a3cd0c7b34f370a374
5. ‘Votorantim Cimentos – Cement Producer Transforms Operations Within One Year’ – https://www.aveva.com/en/ perspectives/success-stories/votorantim/
6. ‘Why Cement Producers Need to Embrace Industry 4.0’ – https://www.bcg.com/publications/2018/why-cementproducers-need-embrace-industry-4?linkId=61303862
MPC, it’s easy as ABC
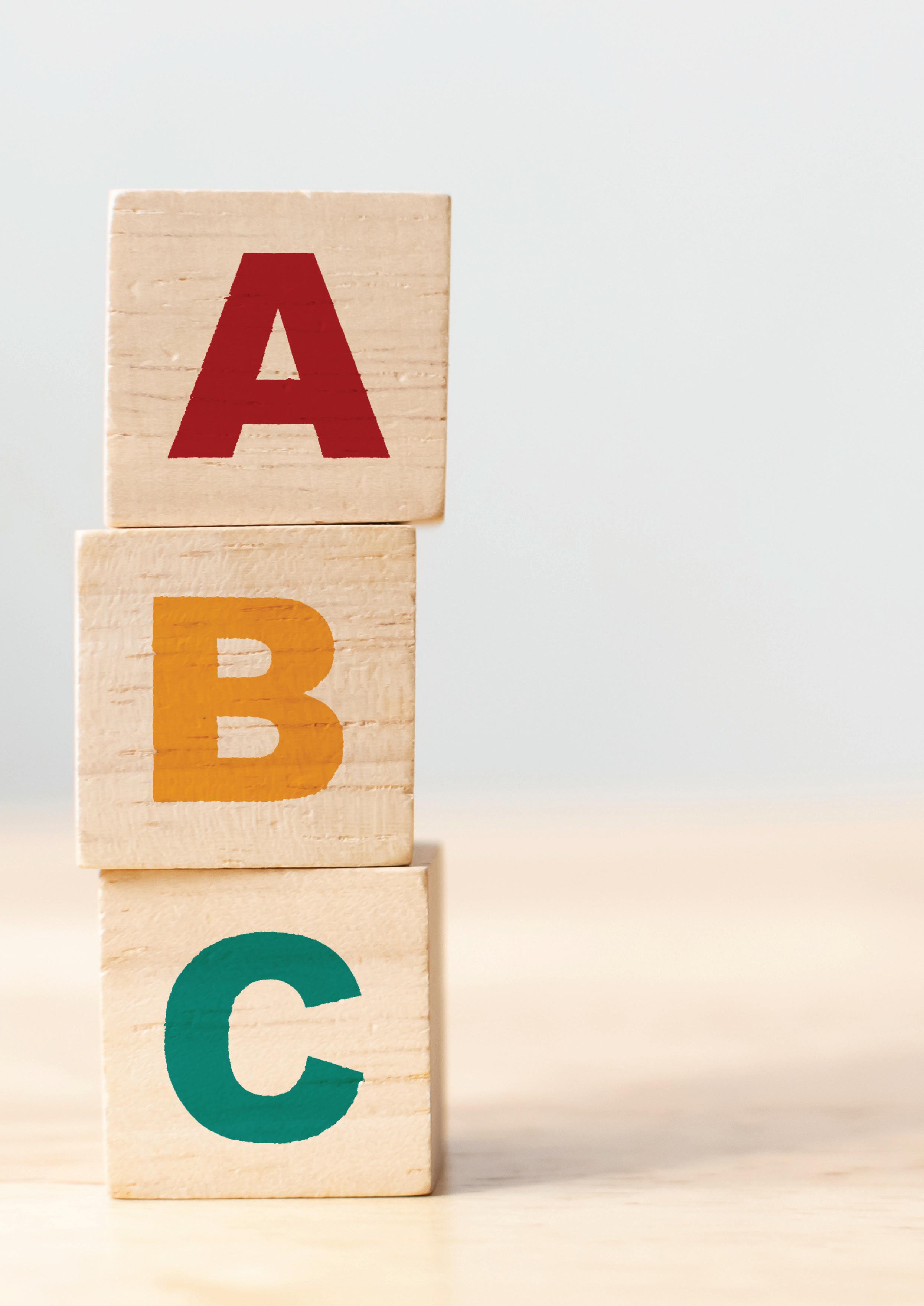
Juliano de Goes Arantes, Rockwell Automation, explains how cement producers can conquer their most complex processes with MPC.
The familiar challenges of cement production – such as high energy costs, raw material variability and process inefficiencies – are only intensifying as producers lose skilled workers to retirement, and adjust their operations to be more sustainable. But some cement producers are finding a way to optimise production even as they navigate disruptive change by using model predictive control (MPC).
Variability and uncertainty in the production process become less of a concern when a cement producer shifts from basic regulatory control to MPC. This is because MPC technology models the production process and accounts for the many different variations that can occur within it. The technology then proactively adjusts setpoint targets on its own. This creates an automated, closed-loop control system that can optimise production in real-time while lightening the load of human operators.
Cement producers have used MPC technology in recent years to boost productivity, improve
quality, reduce energy usage and emissions, and more. And these results are often achieved without needing major capital investments or infrastructure overhauls, because the technology can be deployed on top of the DCS or PLC layer that they already have in place.
From reactive to proactive control
Like other complex continuous-control applications, cement production involves a lot of variables that go unseen by operators. And when operators cannot see what is happening in production in real-time, it is all but impossible for them to optimise processes.
Instead, they just try to keep processes stable by reacting to the limited insights that are available to them.
MPC technology makes a more proactive control approach possible. The technology can access and monitor the many variables that a human operator cannot see, while also monitoring PID controller activity. This data is then fed into models that also leverage process equations, operator knowledge, plant test data and historical production data.
Equipped with all this information, MPC technology can assess current and predicted operational data, compare that data to desired results, and update the setpoint targets for a process. By doing this continuously, the technology can push a process to its constraints while maintaining safety margins.
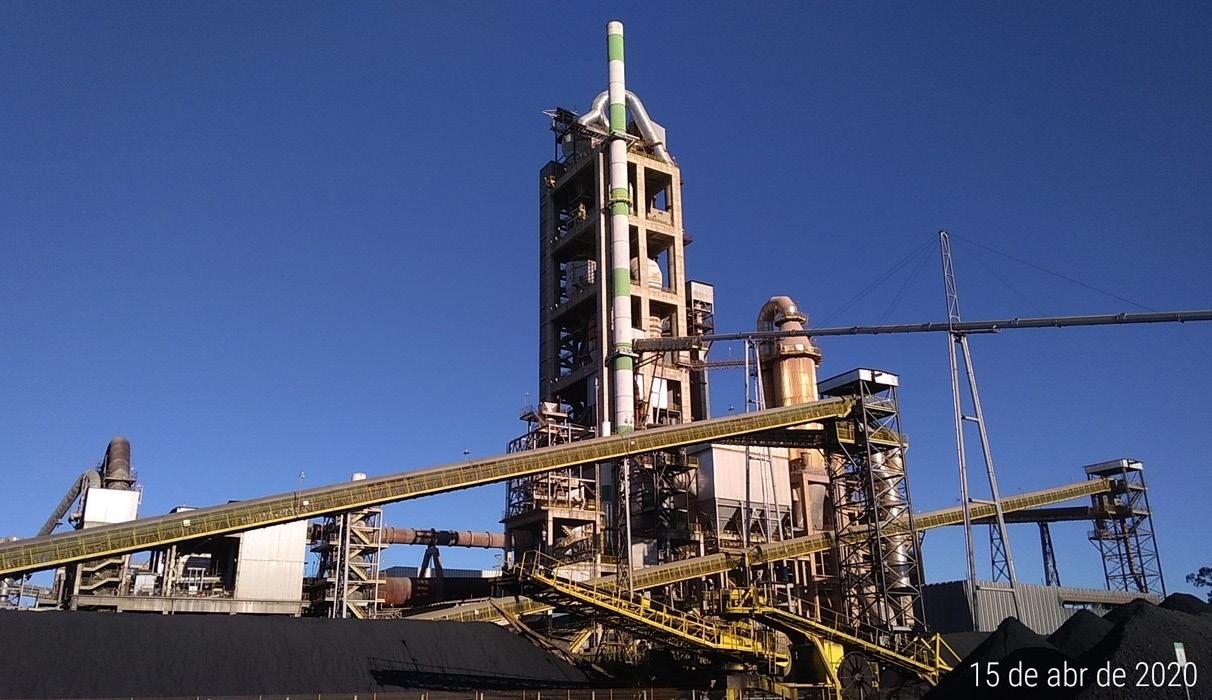
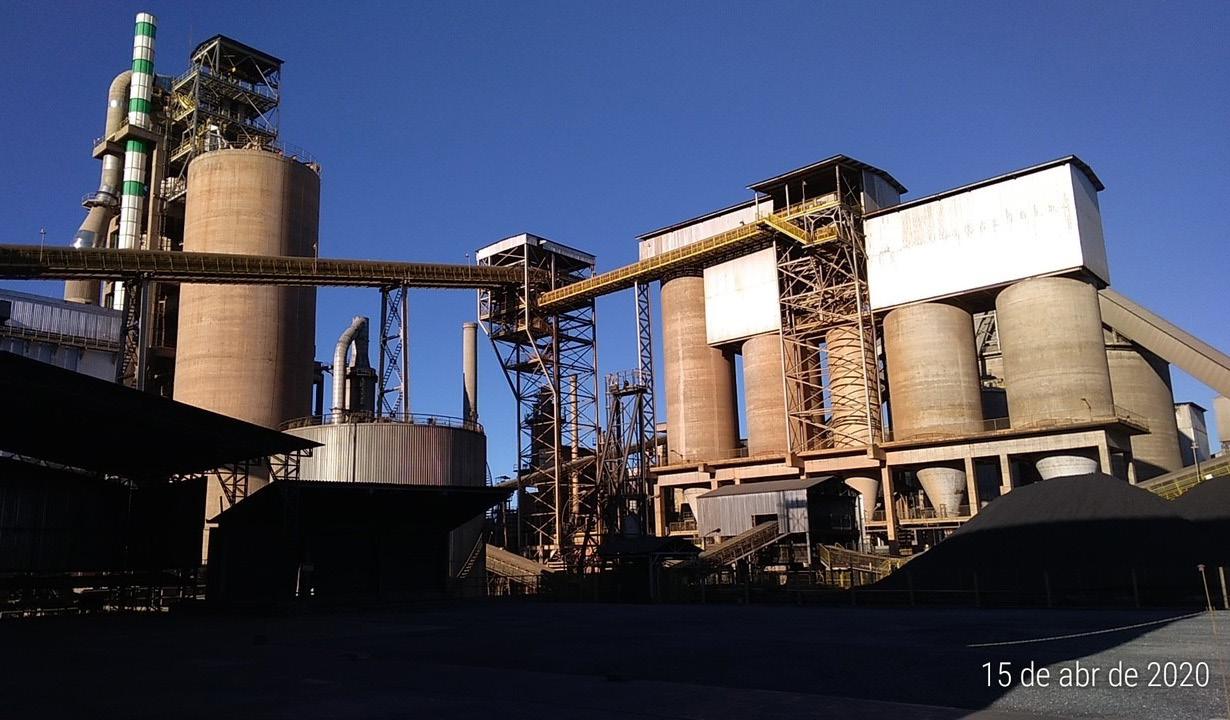
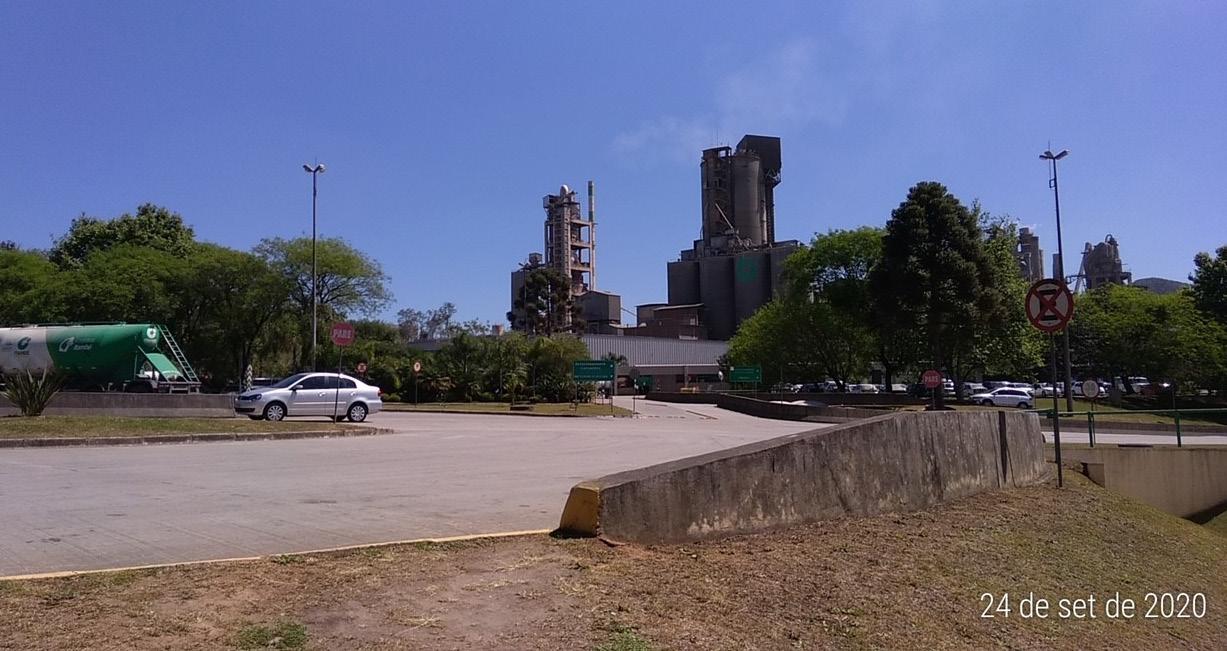
In this role, MPC technology essentially becomes a cement plant’s best operator. It can access and analyse a volume of data that would overwhelm a human operator if they could access it in the first place. And it can operate non-stop, without concern about fatigue setting in or needing a minute off.
This can free up human operators from both tedious and intensive aspects of process control, allowing them to focus on supervising and optimising operations at a higher level. This transition to more value-added work has the potential to boost employee morale and make it easier to attract and retain new employees at cement plants.
MPC technology can further support cement production by creating virtual online analysers (VOAs) or soft sensors. These are inferential measurements that estimate process variables that are difficult to measure online. They can be used to provide continuous feedback of quality parameters that typically require lab sampling to measure and as a backup measurement for critical variables.
Cement applications for MPC MPC technology can be used throughout a cement plant to optimise the applications that prove the most troubling to control, including:
Kilns
This is where cement producers have realised some of the biggest returns
Cimento Itambe kiln line 3. Cimento Itambe finish mills building.from using MPC technology. Today, the complex reactions that happen in cement kilns are not well understood. Fuel source variability and uncertainty about raw material characteristics, for instance, can make it difficult to reduce energy costs, stabilise operations and maximise production capacity.
MPC technology understands these variables and is able to predict and control multiple process parameters in real-time, while continuously updating control actions based on actual process values. Kiln operations can then be optimised by maintaining clinker quality requirements with minimum fuel consumption and a stable temperature.
Blending
Material blending can directly impact kiln operations. In particular, raw material variability and chemistry variations that occur in the blending process can lead to unstable kiln operation. The blending process is also often controlled manually, which can introduce the potential for errors.
MPC technology can reduce blend variability to improve kiln and end-user performance downstream. Automated control of the blending process can also help reduce blend costs and improve raw material resource usage.
Grinding and crushing
Cement grinding is a power-intensive process, and cement producers can struggle to grind and crush their product to a consistent size and hardness. Efficiencies may also vary because of changes in operating habits from shift to shift, and because of changes in clinker grindability or grinding aid composition.
MPC technology can account for process disturbances and other influences to help consistently grind product to a specific size while maximising capacity, which can help minimise energy costs. The technology can respond to different feed properties, like hardness, particle size, and grade.
Real-world applications
Brazil-based Cimento Itambe’s story is likely a familiar one to other cement producers. The company has enjoyed more than four decades of success producing cement for the civil construction sector. But the company also had some issues it wanted to address in its production processes. Specifically, the company wanted to standardise operational processes, increase equipment availability and reduce energy usage in its operations. To help meet these goals, the company deployed MPC technology in two phases.
In the first phase, Cimento Itambe used the technology to optimise control for its kilns. This helped the company increase productivity by 3% in each of its kilns. The company also saw a 2% reduction in the amount of energy used by the
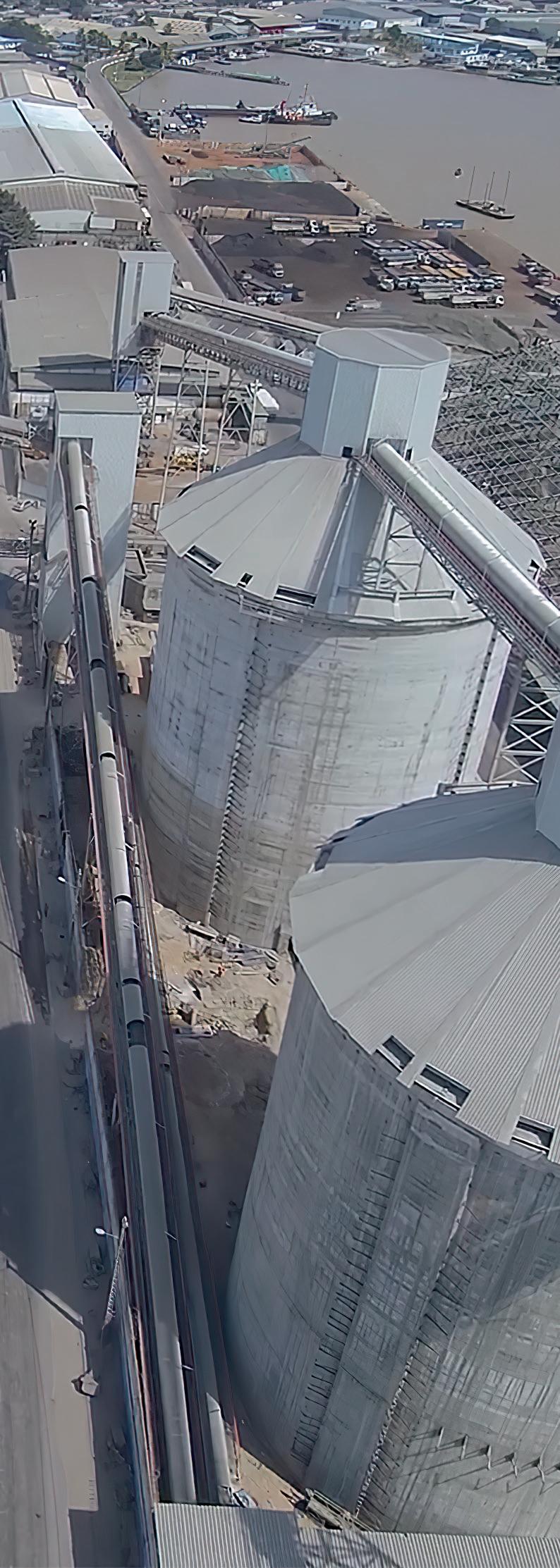
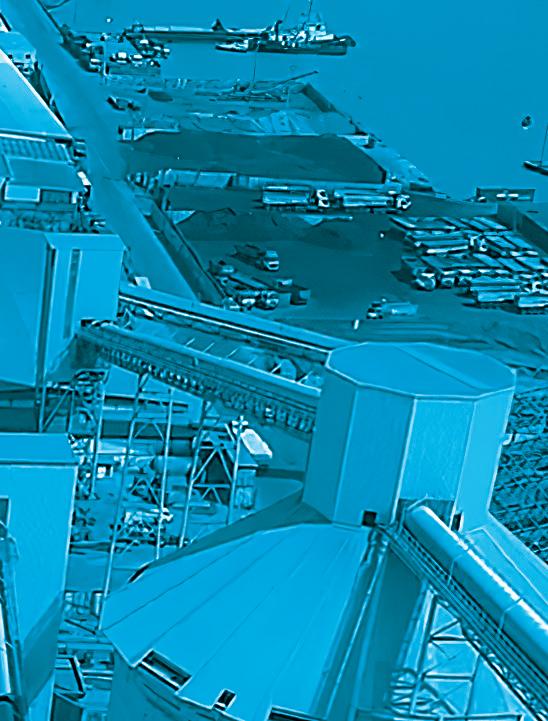
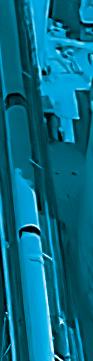
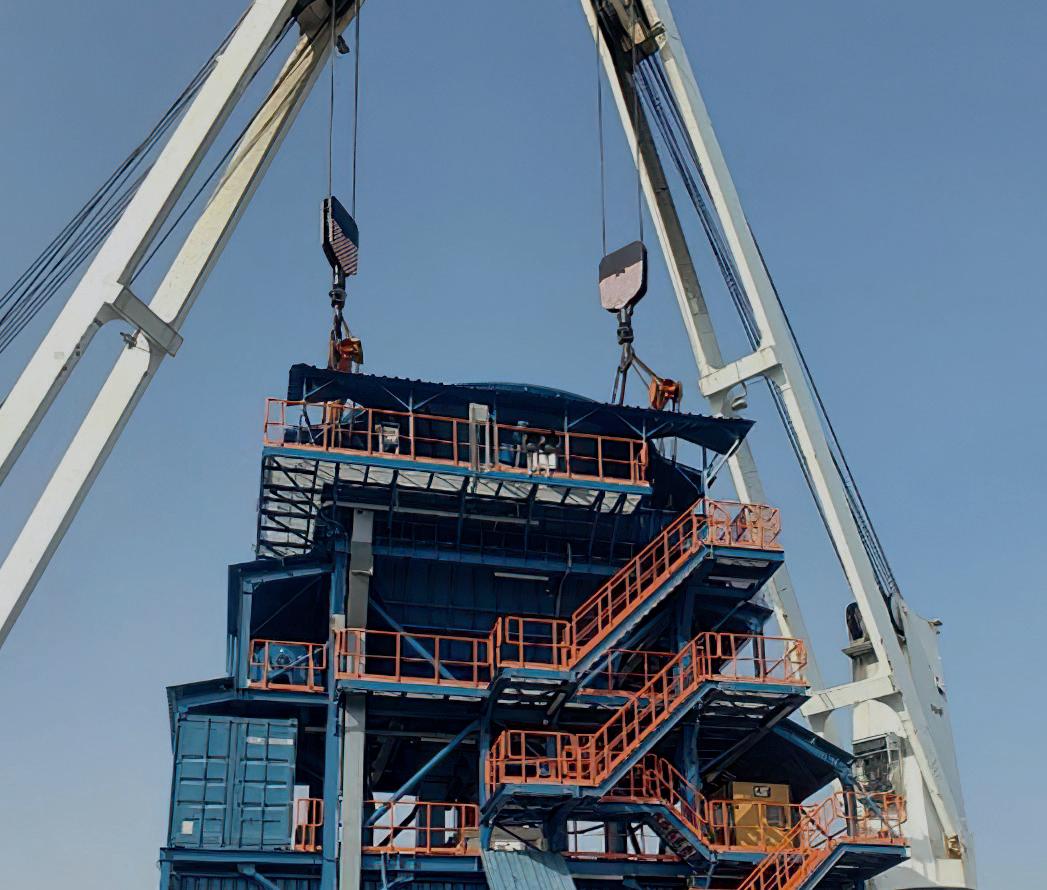
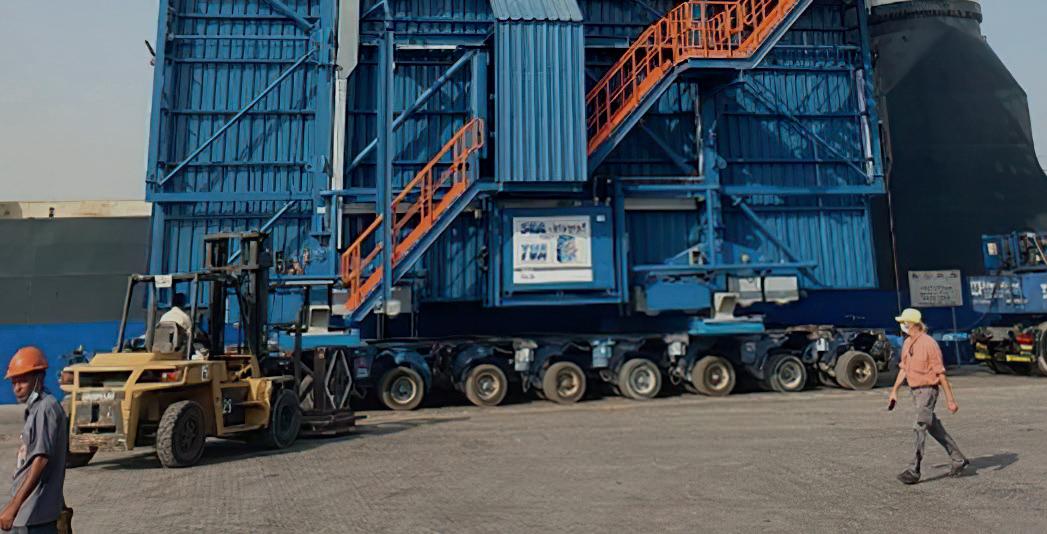
Wherever you need him: the new InterHop
Highest
fast truck loading and dust free operation – the raw material receiving hopper InterHop guarantees all of this! 30 tons of material can be unload–ed in less than 30 seconds. Truck loading is possible as well as direct feed via belt conveyor to raw material silo. The InterHop impresses with a flexible design. It is a tailor-made solution developed according to the client’s requirements.
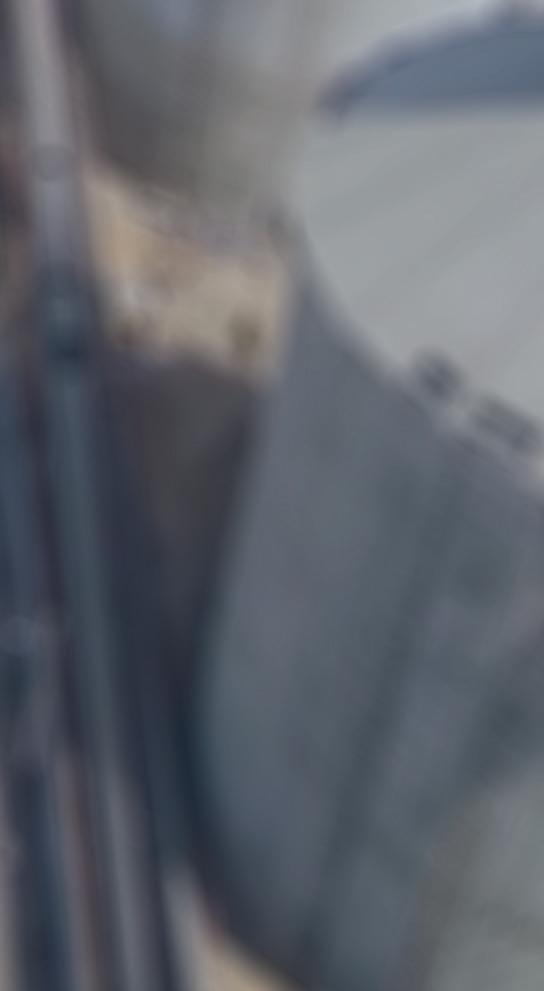
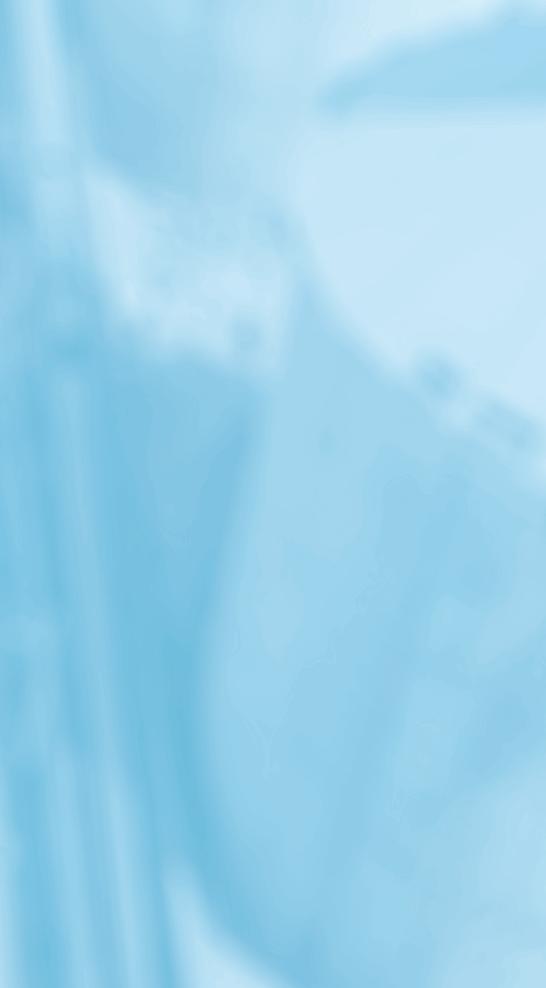
kilns as a result of more stable temperatures. This helped enhance clinker quality and reduce the risk of cyclone blockages.
In the second phase, the company deployed MPC technology to optimise control of its cement mills. The results were similar to those in the kilns.
Productivity in the mills increased by 5 – 10%, while energy usage decreased by 5%. The company also experienced fewer disruptions in feeding or stops related to high vibrations, and having access to real-time data helped speed up decision making.
In Europe, Croatian cement producer NEXE is still in the early stages of its MPC deployment. The company is using the technology in combination with alternative raw materials and fuels to help drive reductions in its carbon footprint. Such efforts are becoming more common today as cement producers strive to operate more sustainably. MPC technology can help by maintaining quality levels when introducing new materials and by managing the variability of new fuels to keep operations stable.
NEXE has seen early signs of savings and efficiency gains from its MPC project and predicts a payback period of less than one year.
What to consider before deploying MPC
Ideally, a couple of key elements will already be in place in a cement plant before a producer begins an MPC project.
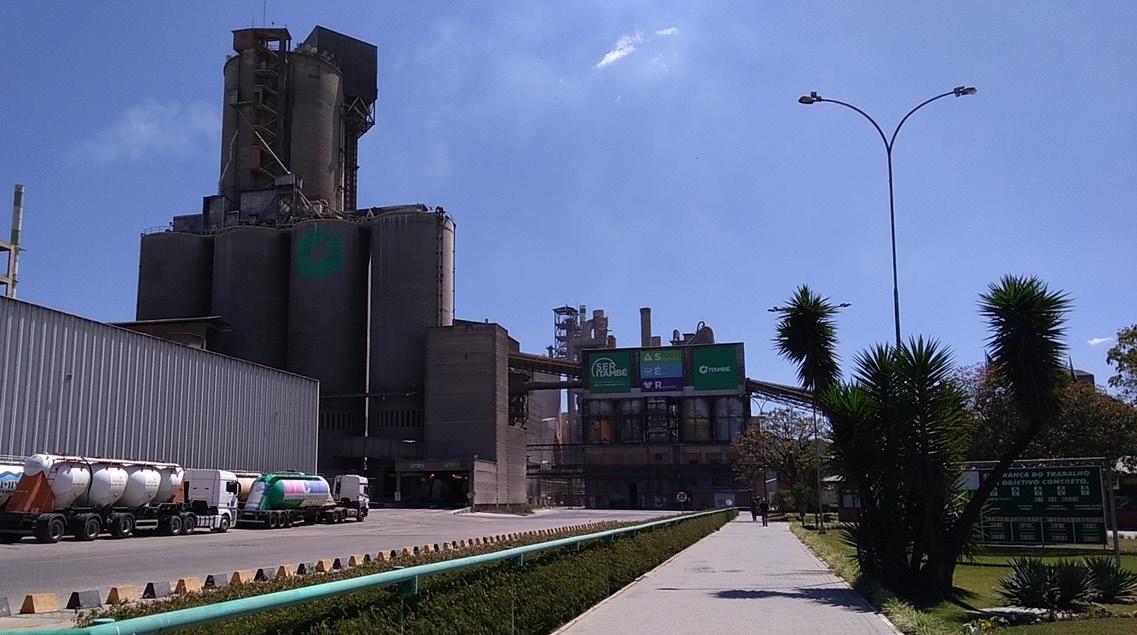
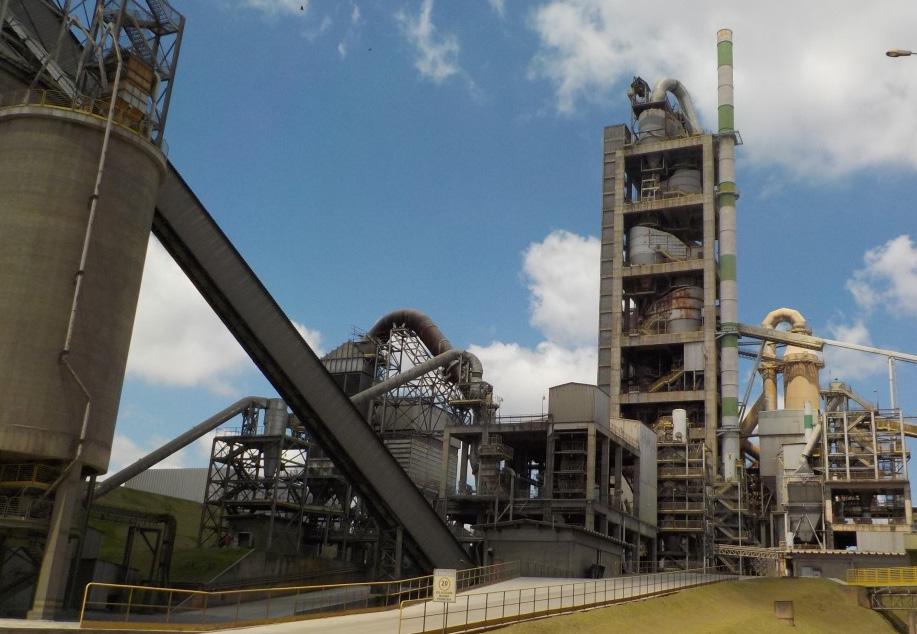
First, because MPC provides closed-loop control of a production process, automation technology should already be in place to control the process.
Also, MPC technology is like any other AI or machine learning technology in that it requires good, reliable process data to be successful. Some producers begin down the path of deploying MPC technology only to discover near the start line that their measurements do not provide consistent and accurate representations of what is really happening in their processes.
Producers should also keep in mind that the MPC technology alone is not a means to an end. It requires site-specific information like historical data, plant test data and process knowledge to create custom models for the processes that are being optimised. A cement producer should either have the process expertise to capture this knowledge or work with an MPC supplier that has it.
Another key point to remember is that MPC projects must be supported to sustain their success for the long haul. Any process, raw-material and fuel changes, for example, must be captured in the technology or its performance will degrade. Process or automation engineers can manage this task, or it can be outsourced to the MPC supplier.
A growing role for AI and ML
In addition to MPC, a growing number of AI and machine learning technologies can help cement producers meet growing expectations to do more with less.
For example, smart drives with built-in predictive maintenance capabilities can help cement producers reduce costly and disruptive unplanned downtime. The drives use advanced physics-of-failure models to track the life consumption of critical components and can generate alarms when those components are nearing the end of their lives and require maintenance.
Computerised maintenance management systems (CMMS) are also now using AI tools to help producers get ahead of downtime. The tools use machine learning to understand how equipment behaves under normal conditions and AI algorithms to identify and alert users when failure risks are detected.
Conclusion
For cement producers that are not yet using AI or machine learning, MPC is a logical place to start. It is easy and affordable to implement when the right infrastructure is in place. And it can put a cement plant on the path to more stable production, reduced energy usage and higher throughput in as quickly as a few weeks.
Cimento Itambe shipping area.Supporting silos Supporting silos Supporting silos
Martin Wuerth, Wuerth Consulting Engineers, discusses
a cost-effective silo repair method that can extend silo lifetime by more than 30 years.
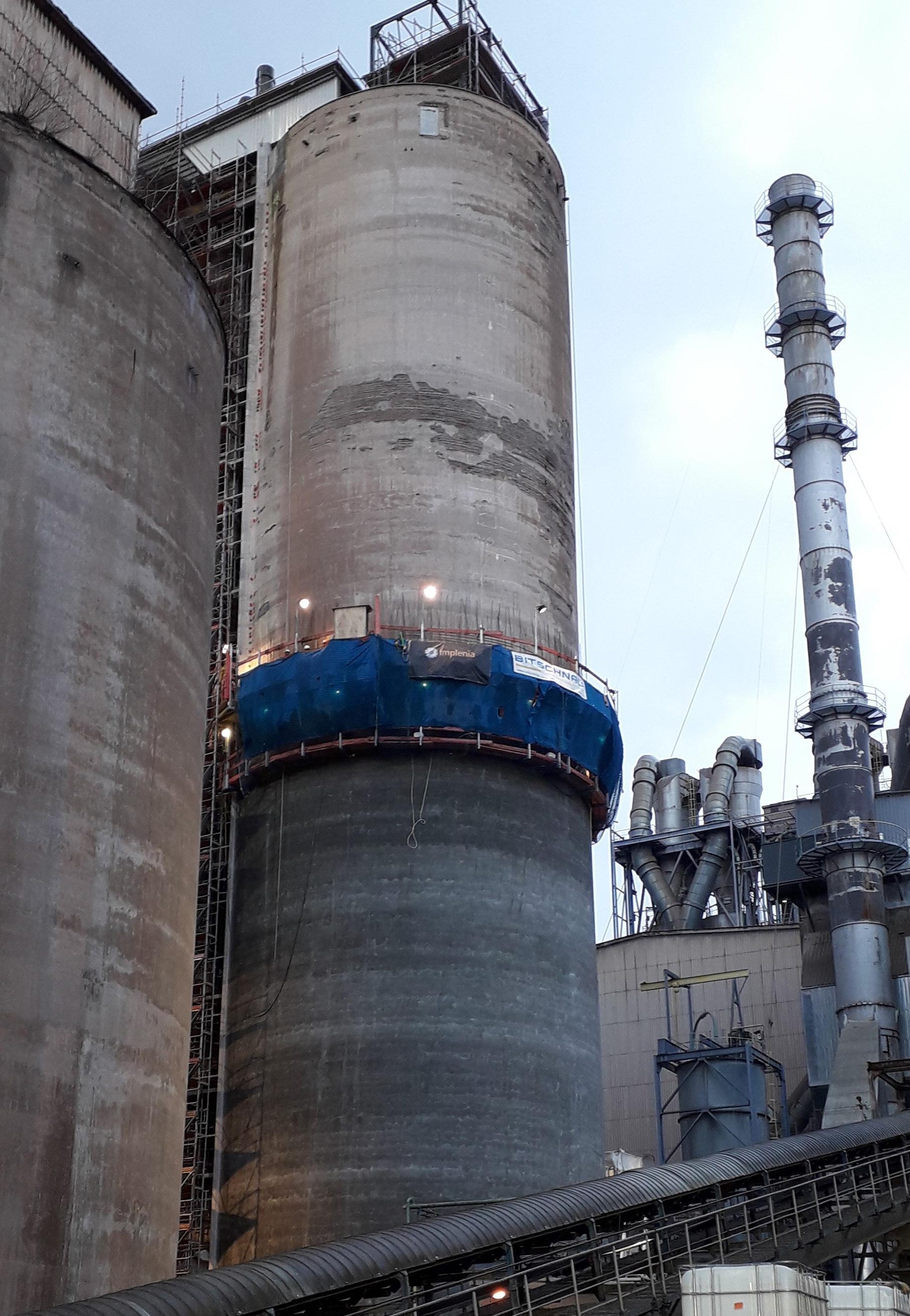
EEvery single building has a service lifetime. If they are not managed, the time will come when the structure will eventually collapse. Silo structures collapse three times more often than all other civil structures and this phenomenon is worldwide. Even very sophisticated structures like soccer stadiums, bridges and skyscrapers are safer than silos! There are two main reasons for this:
f Firstly, the live load of a silo is approximately 90% of the total load, whereas, the live load of a bridge or building is less than 50%. In other words, a silo structure operates much closer to its service limit than other buildings.
f Secondly, maintenance is different. Buildings and bridges are used by people, who often detect cracks and corrosion at an early stage. Public or private buildings are also observed
by facility managers who take care of their buildings. However, who takes care of silos in a cement plant? Often, nobody. As long as the equipment is running, everything is presumed to be all right.
Service lifetime
Service lifetime is the time in which the rebar and post tensioning can hold the bulk material inside a silo. Bad concrete quality, high and low temperatures, acid rain, design flaws or corrosion will limit the service lifetime.
A proper concrete layer over the rebar overlapping makes sure that the tension force in the rebar can be transmitted between one rebar to the other. The chosen concrete cover is not only important for this transmission, but also for the protection of the rebar from acidic environmental influences.
To calculate the remaining service lifetime, an important aspect to consider is the depth of carbonation in the concrete cover. Carbonation is the zone of concrete at the surface which
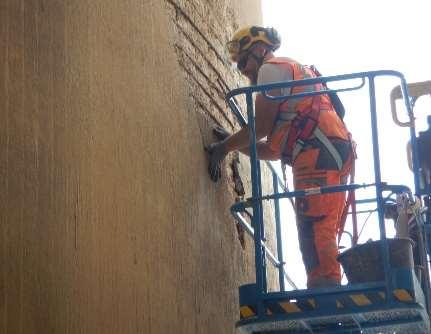
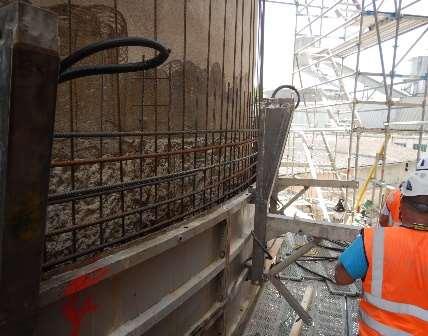
has changed from a natural base to an acid. Air pollution, salt water and acid rain speed up this process. If the carbonation zone reaches the rebar, the steel starts to corrode until there is no iron left.
Depending on the results of an investigation, the remaining service lifetime can be calculated and estimated.
On average, the carbon depth of a 50-year-old concrete surface is around 20 mm. Since this 20 mm is also used for the rebar concrete cover, the lifetime of an old silo structure is limited to 50 years on average. This process is easy to detect because after the carbon depth reaches the rebar, the rebar is no longer protected and starts to corrode. Seeing as corroded steel needs more space, the concrete cover will flake off. At this point, it is clear that the condition of that structure will be limited.
What kind of repair solution is required?
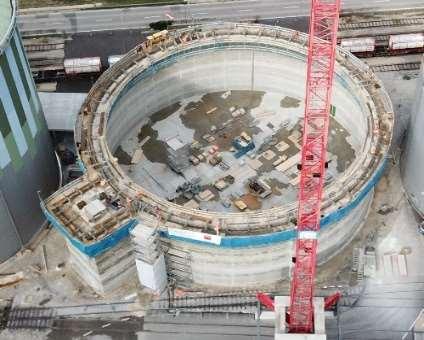
If the owner is not satisfied with the calculated remaining service lifetime, the structure must be reinforced. For the repair, the results from the design analysis and the concrete cover and carbonation depth are required. If the design analysis is not to satisfaction, the rebar must be reinforced in combination with a concrete repair solution.
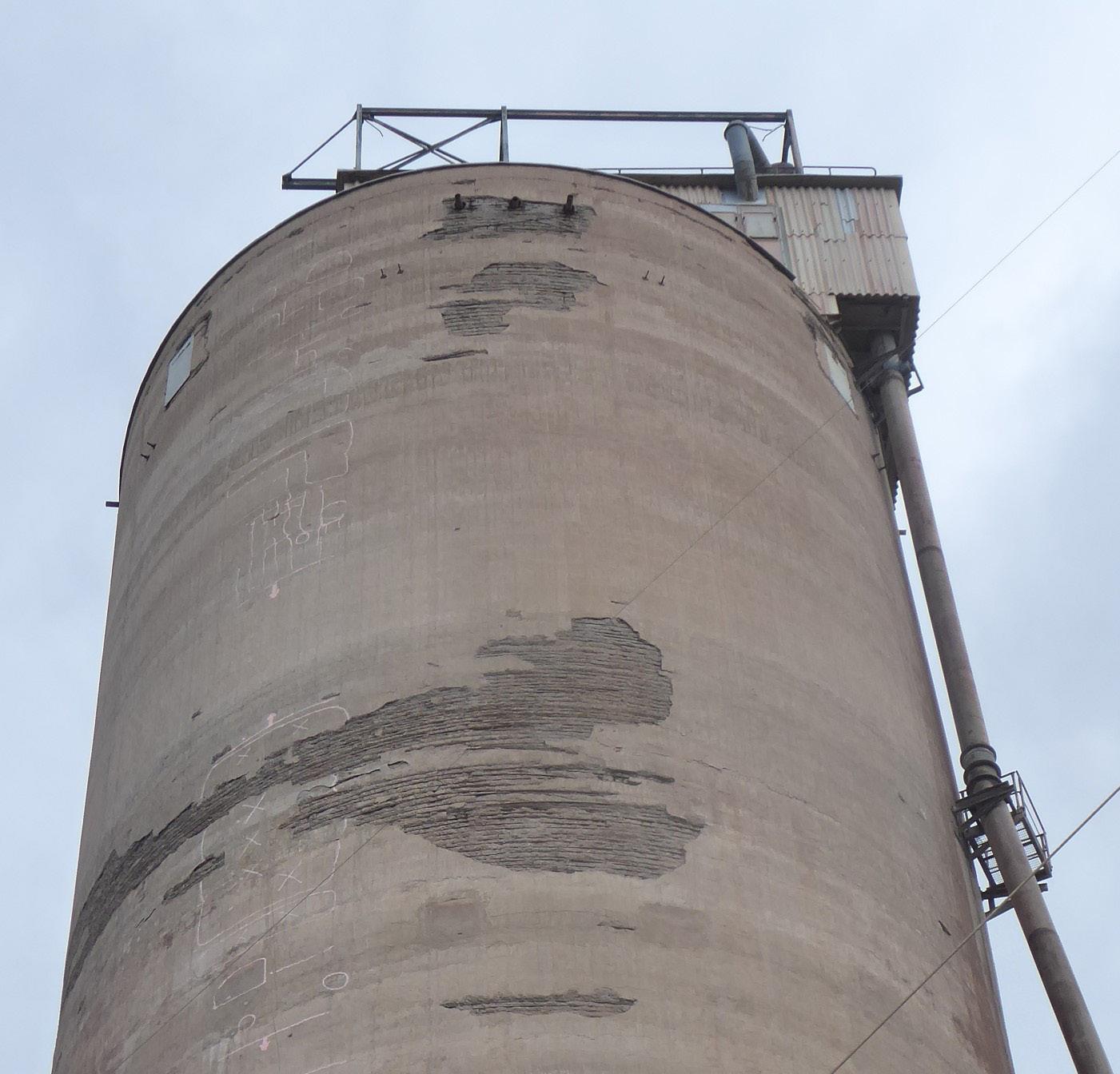
Not only is the condition of an existing silo important in order to select a type of repair, but also the silo’s height, to choose the most economical method. For example, a traditional soft repair, which involves hydro-jetting the concrete surface, sandblasting the corroded rebar and backfilling the missing concrete cover with modified mortar or shotcrete, has a height limit. The costs for scaffolding, hydro-jetting as well as for sandblasting increase with height squared. Up to a height of 25 m, a soft repair is cheaper than a new shell. When a silo has a height of over 35 m, a new shell is cheaper and much quicker than a soft repair. For a height between 25 – 35 m, it is worth checking on the local market, to ascertain which solution is more economical.
New shells for homosilos in Karsdorf (Germany)
Opterra Germany asked Wuerth Consulting Engineers to plan a repair of its two 65 m
high homosilos, built in 1969 in Karsdorf, East Germany. Figure 2 shows the condition of the silos after running the plant for over 50 years.
Even a brief glimpse at the outer concrete surface of the shell (Figure 2) shows that the silo has a major corrosion and concrete cover problem. The recalculation of the silo shell based on the current silo codes showed also that the safety factor against shell collapse during operation was just 1.0 instead of 1.5 – 1.75.
The reduction of the safety factor was based on the corroded rebar, the missing concrete cover for the rebar overlapping joints, as well as the ‘new’ code regulation for the load case extract bulk material.
The client uses these homosilos for clinker production. Kiln shut down for more than 2 – 3 weeks during winter is not possible. In the summer, the plant runs for 24 hours, 7 days a week.
The client investigated a location next to the existing homosilos with the aim of building new ones and then sending the raw meal later on over these new homosilos. In theory everything was perfect with this replacement project, however, the costs for such a solution would have come to €10 million more than a heavy silo repair. This circumstance made it easy for the
client to decide to add new shells on the existing silos, extending their lifetime by 25 – 35 years.
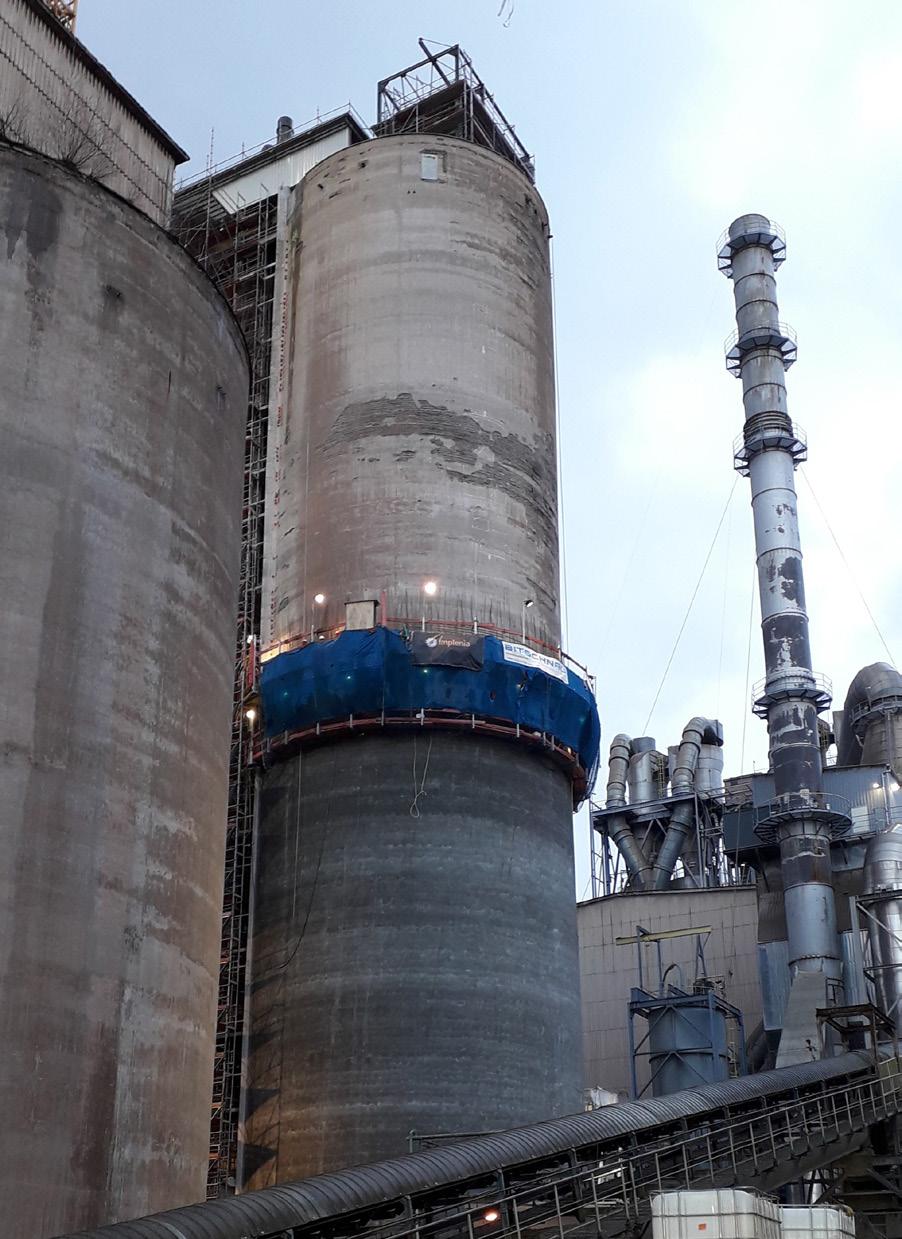
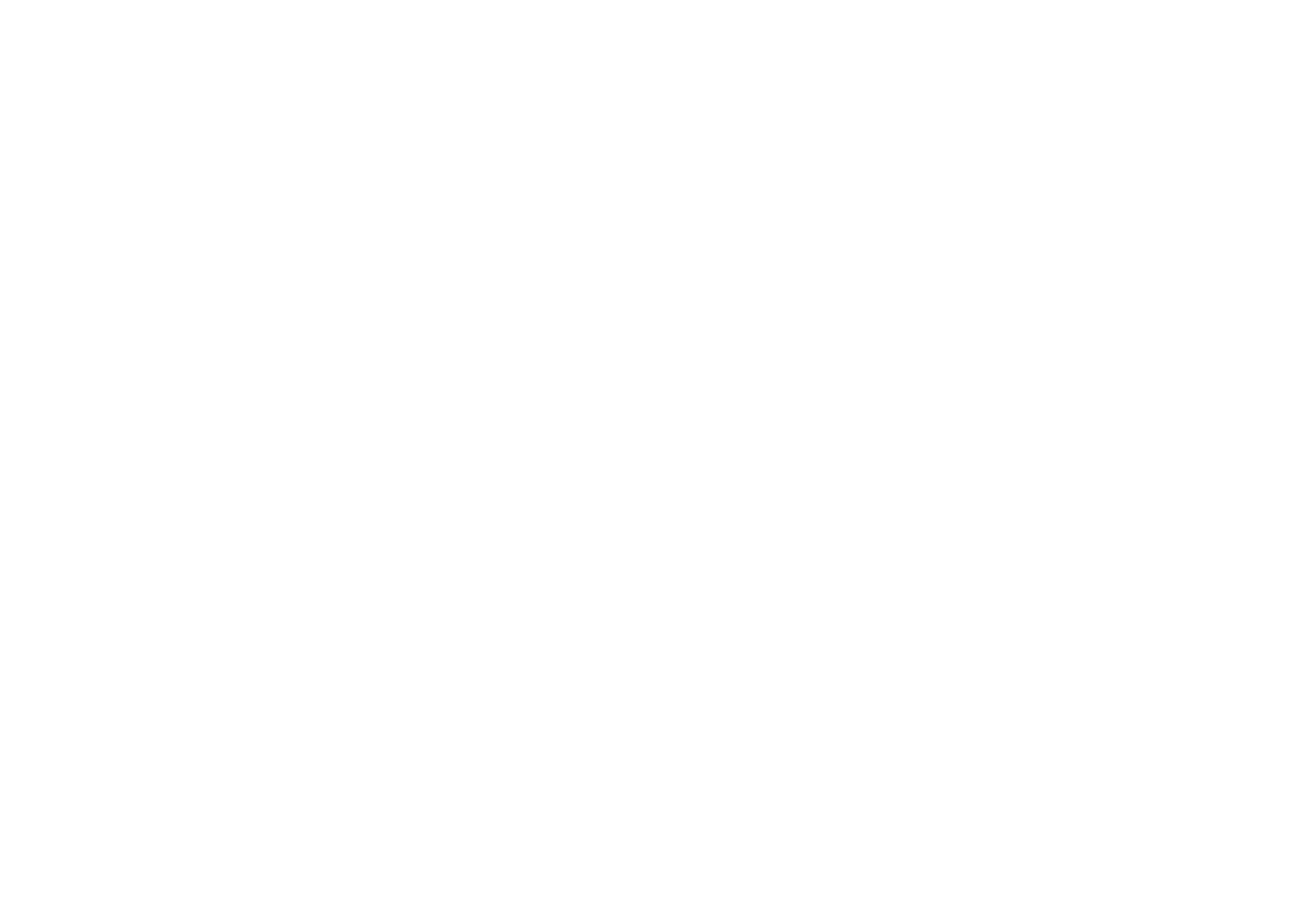
A soft repair with mortar was not adequate owing to the height of the silo (scaffolding costs) and also considering that the structure must be reinforced to fulfil the current codes (requiring a safety factor > 1.50).
A redesign of the silo structure was required to calculate the reinforcement in the new shell as well as to check whether the foundation had been reinforced or not according to the additional dead load weight of the new shell.
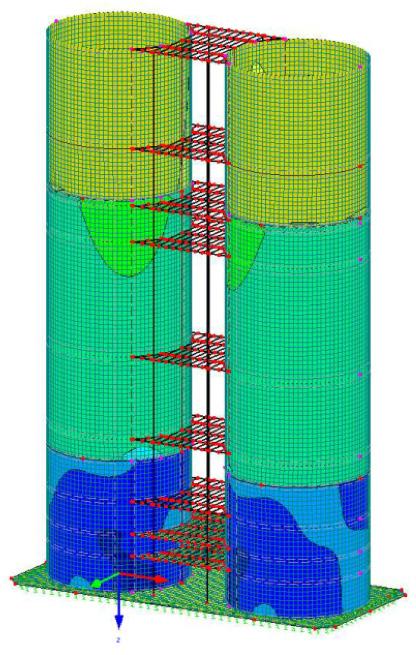
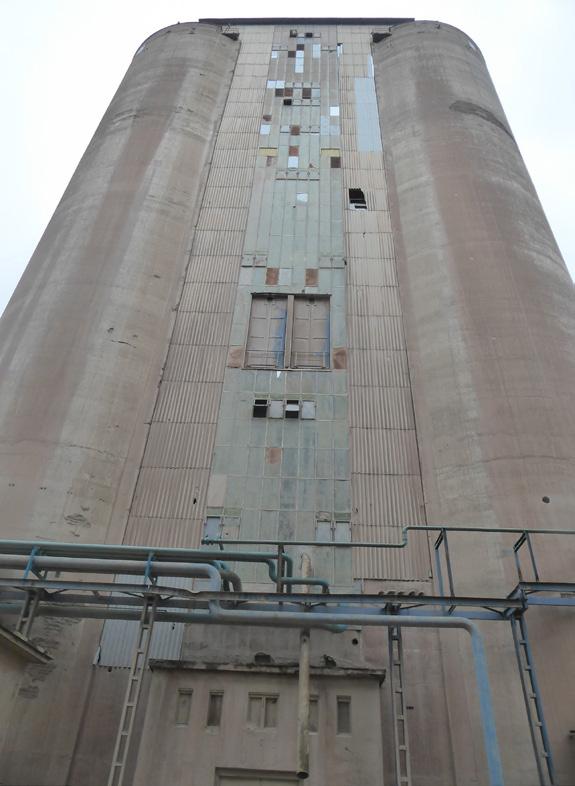
The execution of this silo repair took two weeks per silo, plus lead and follow up time of approximately one month. The first silo was made in November 2021 and the second was made in March 2022.
It is relatively simple and easy to add to the old silos a second shell outside (or inside if required), yet, there are a lot of potential problems to consider in order to realise such a project. The main problems to solve are the deviations of the existing silos and the available space around the silo.
Since slipform work today is very different to how it was conducted 50 years ago, and the procedure of a one-sided slide platform (slipform) is technically very sophisticated, the job needs to be tackled by a professional.
The new shell made by quite stiff formwork (required because of a one-sided scaffolding platform) must follow the existing deviations in a vertical and circumferential direction made many decades before with a flexible formwork system fixed in the centre of the silo circle by cables.
The slipform procedure needs clear space around the silo structure. Considerations must also be made as to what to do with the existing platforms, supports, nearby columns and pipelines. This is the main challenge for the engineering team – to find easy and possible solutions to these questions. Understanding the process of slipforming with one-sided platform formwork is the main key for a successful project implementation.
The numbers of engineers and slipform contractors for such projects are limited. However, since they have, together, around 15 – 20% of the contract value, the local market with different civil contractors can still compete, placing the client in a good position for negotiation.
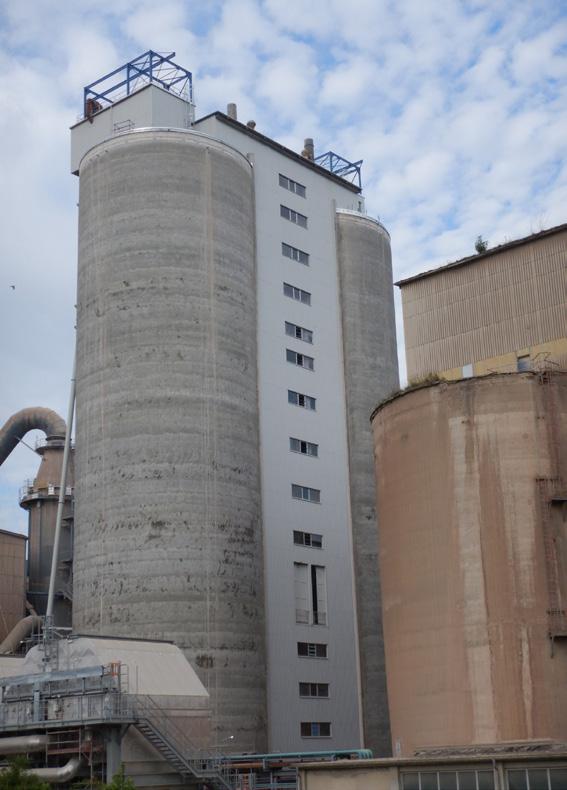
Conclusion
Many cement producers are in a situation where they have to replace or repair old silos but need them for production. No pace near the production line is available for a new building and transporting the bulk material away and back is expensive and the investment costs are high.
When old silo structures are retrofitted with a new shell, this offers a quick and cheap solution, whilst maintaining undisturbed production capacity. With such an investment, old facilities can be operated safely and easily for the next 25 – 35 years. This represents just a fraction of the costs of investing in new built facilities.
Figure 5. Left: Silos before repair. Right: After repair.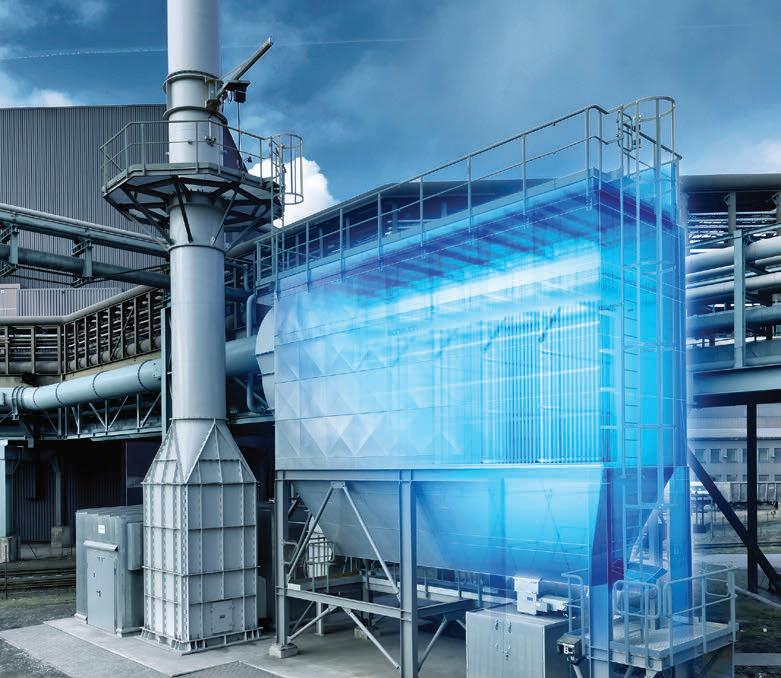
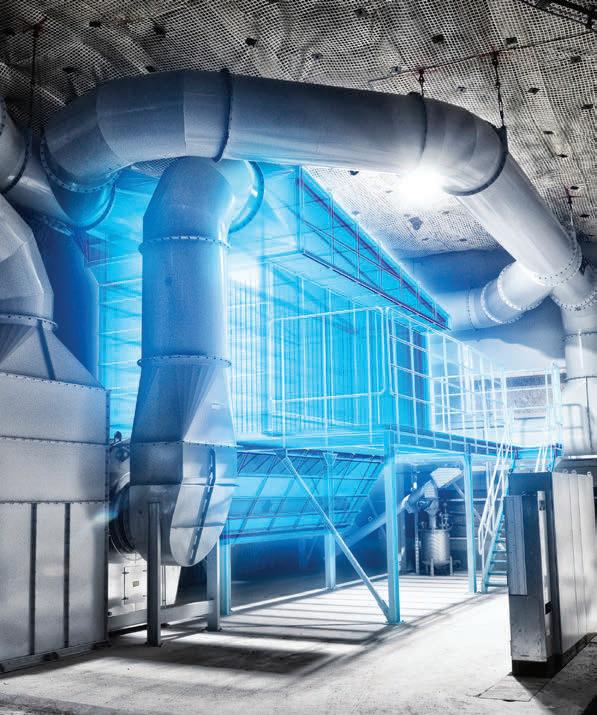
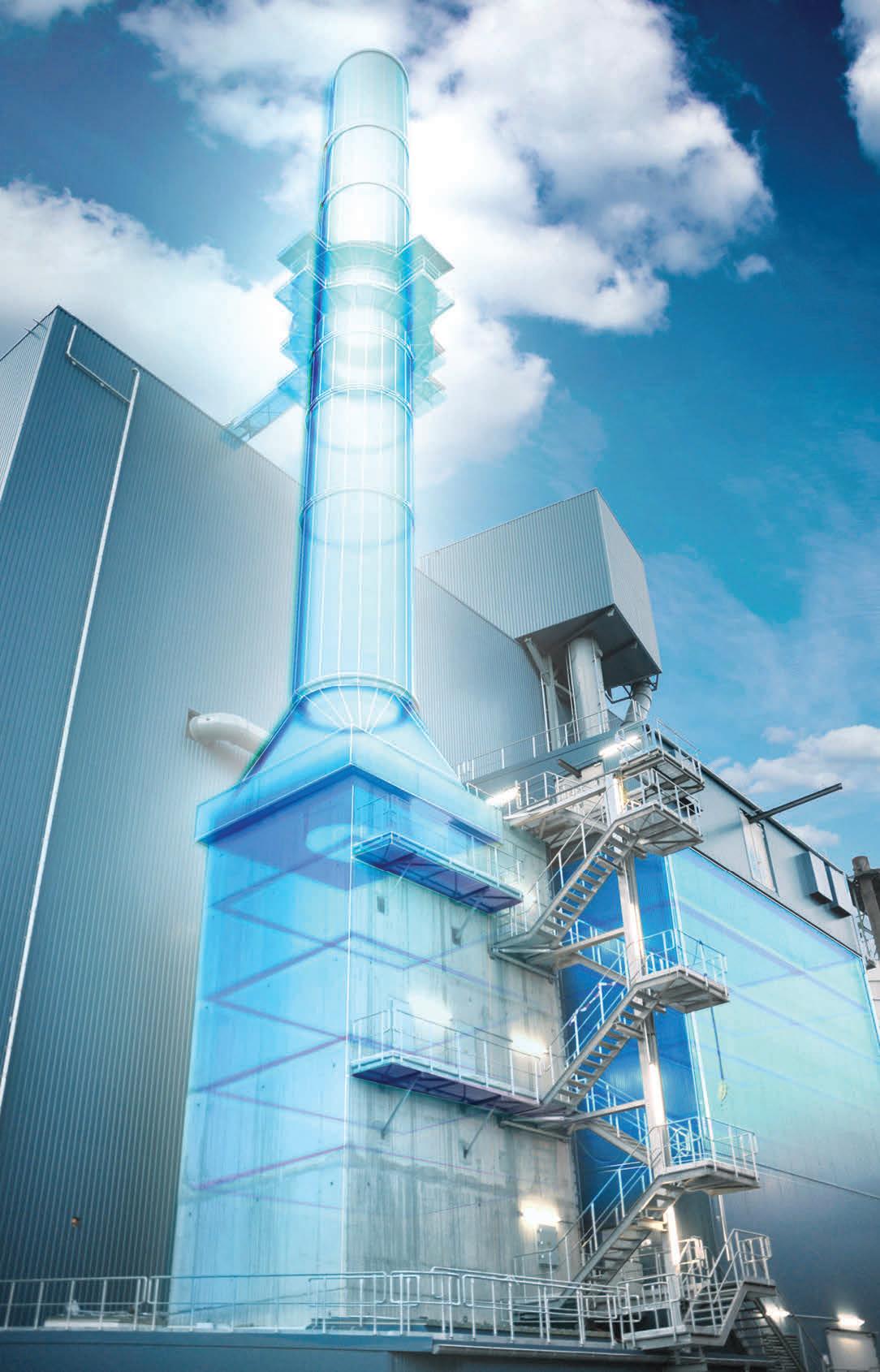
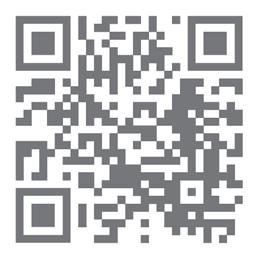
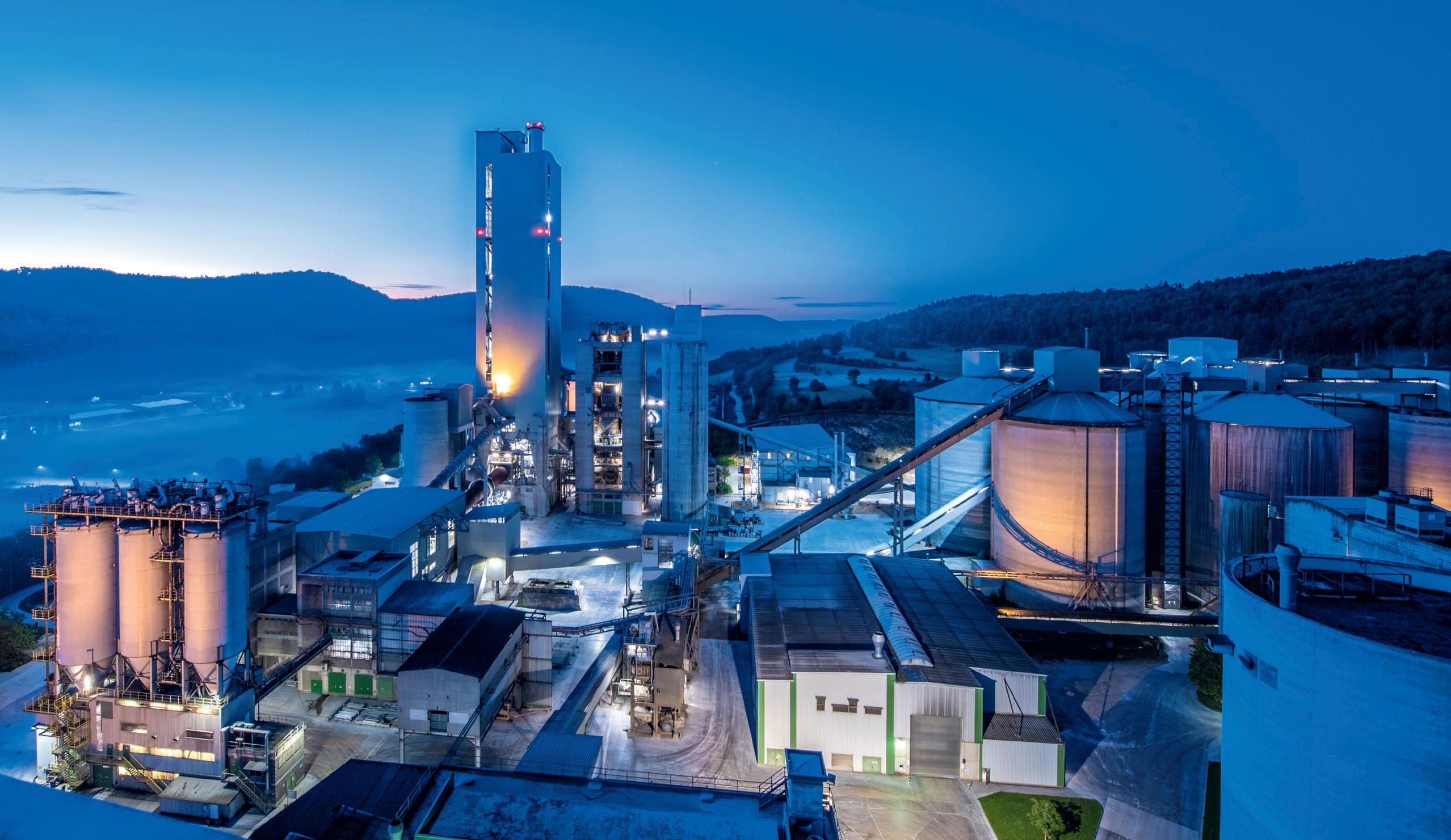
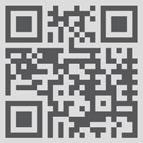
Prateek Bumb, Carbon Clean, emphasises the importance of carbon capture for the cement industry to achieve net-zero goals.
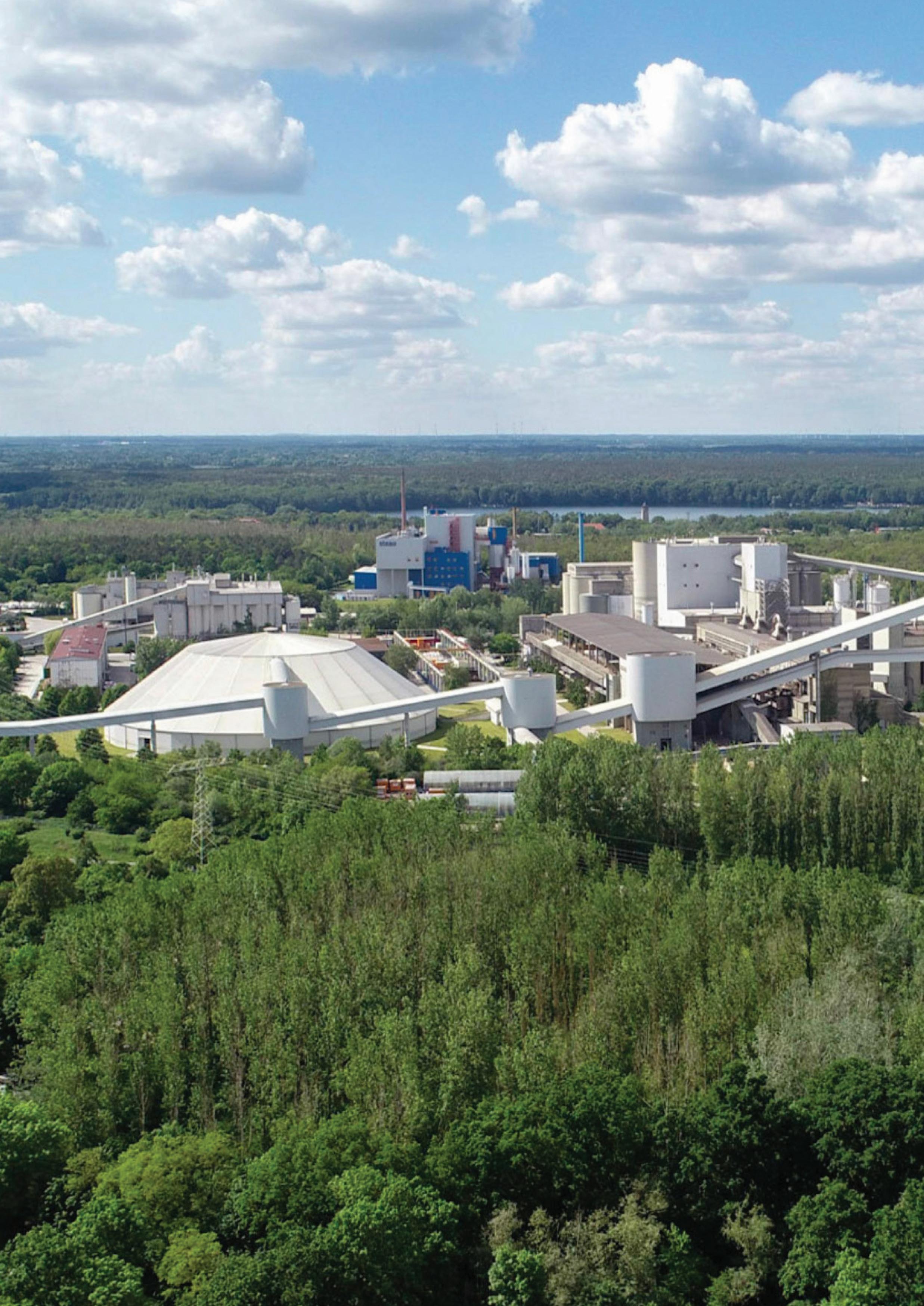
Cement and concrete are the most commonly used industrial materials in the world today, with concrete the second most consumed substance after water. Combined, cement and concrete are responsible for 7% of global CO2 emissions or 2.6 billion tpy. The decarbonisation of these essential industries is therefore crucial for the global energy transition, while continuing to support the ongoing pivotal role cement and concrete play in powering economic growth.
Demand for cement is only set to increase over the coming years as growing economies continue to heavily rely on this industrial material for their development. This includes the need to construct 13 000 buildings each day between now and 2050 to support an expected population of 7 billion people living in cities. The Global Cement and Concrete Association (GCCA) predicts demand for cement will increase by 48% from 4.2 billion to 6.2 billion t by 2050. Meanwhile, the International Energy Agency (IEA)’s Net Zero Scenario argues that global cement production needs to fall to 3.9 billion t by 2050 to meet targets. It is therefore essential to develop new and existing technologies to reduce emissions and support hard-to-abate sectors – this includes carbon capture, utilisation and storage (CCUS).
There is a key role for CCUS in the decarbonisation of the cement sector, where significant amounts of CO2 released during the calcination process can be directly captured. Industry is aware of this opportunity, with CCUS accounting for 36% of planned reduction levers in the GCCA 2050 Cement and Concrete Industry Roadmap for Net Zero Concrete.
However, while the production of cement has become more sustainable over the years – innovation has been slow. Progress is heading in the right direction, with an increasing number of cement and concrete suppliers moving away from traditional carbon-intensive production processes. Nevertheless, producing cement is energy intensive, using 60 – 130 kg of fuel oil, depending on the type of cement and process used, and 110 kWh of electricity for every tonne of cement produced.
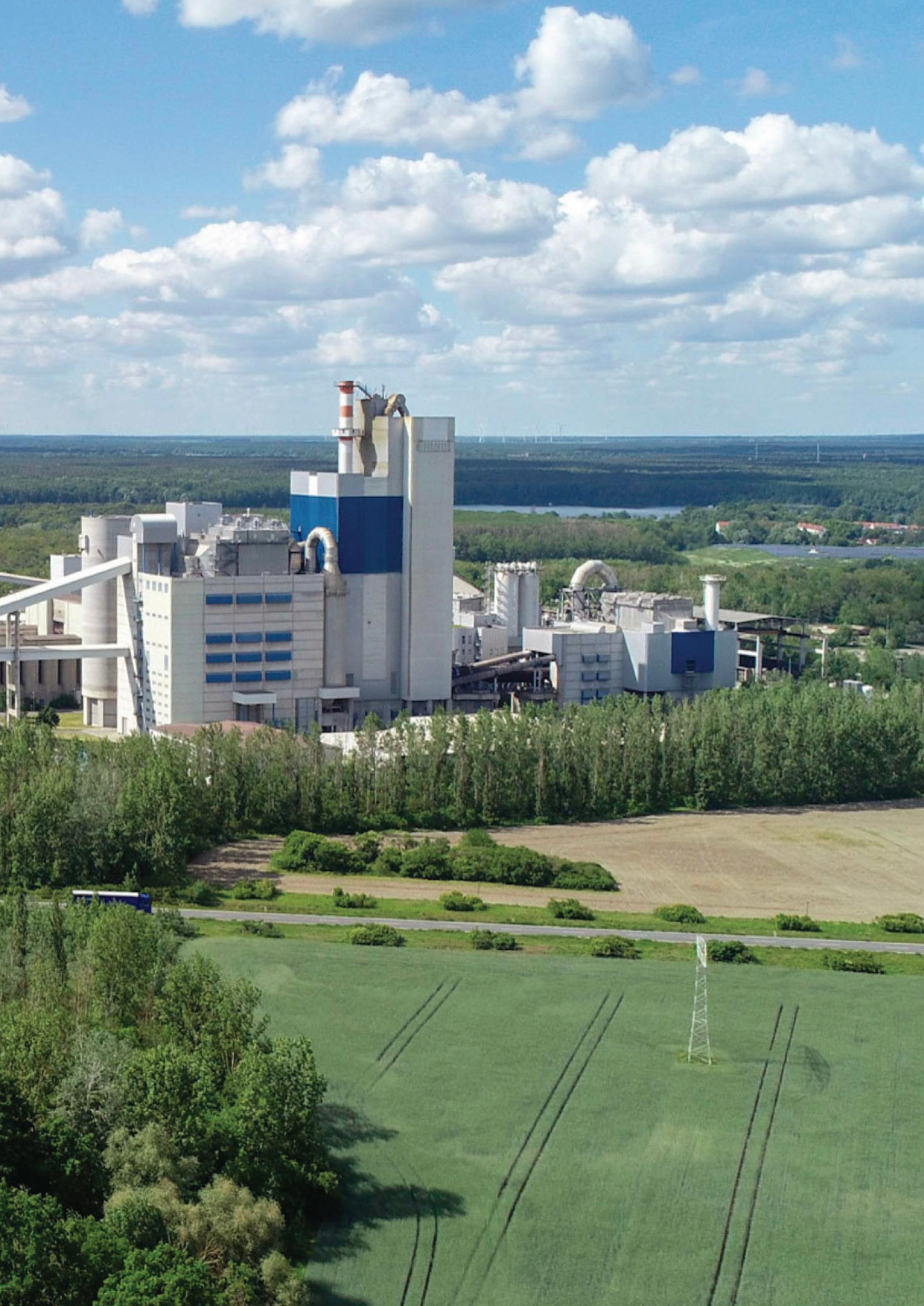


A complex challenge
The challenge for cement is uniquely complex, balancing energy needs, combined with increasing regulation and decarbonisation targets across the public and private sector. The Mission Possible Partnership estimates that of the US$1.42 trillion future investment required to fund the cement and concrete industry in the Net Zero Scenario between 2022 and 2050, 13% should be focused on CCUS infrastructure and 27% on carbon capture equipment
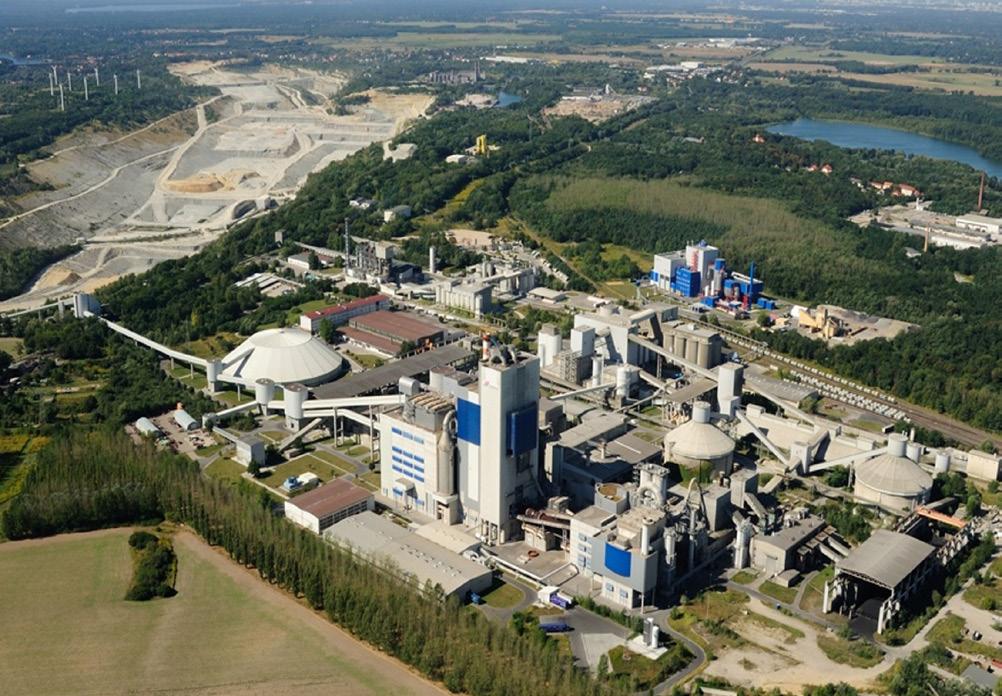
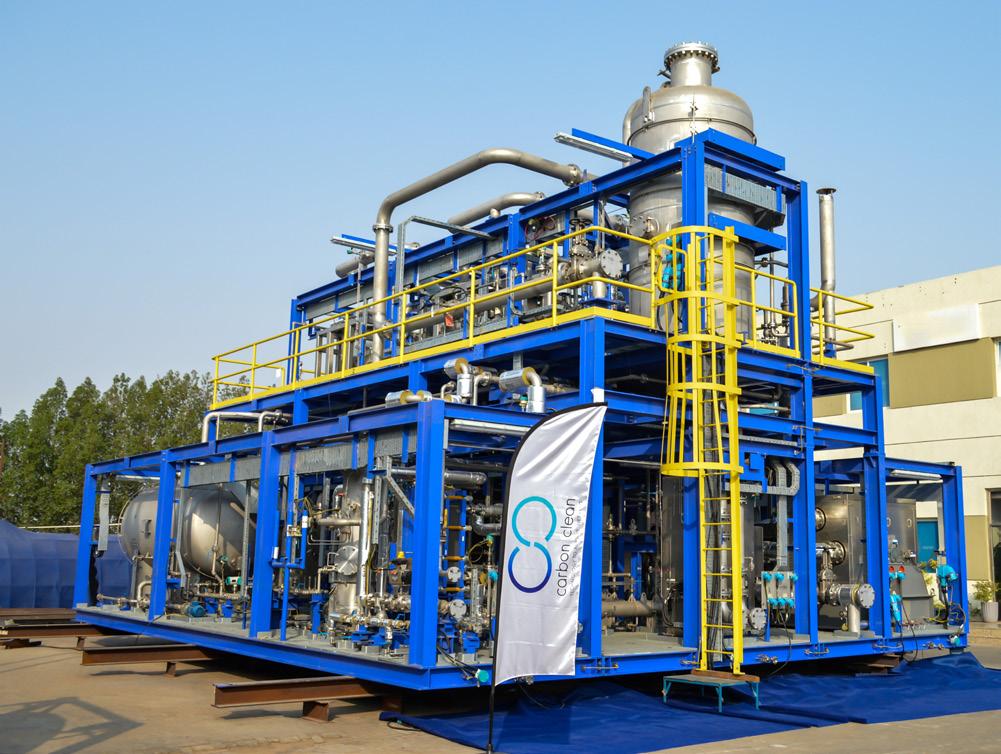
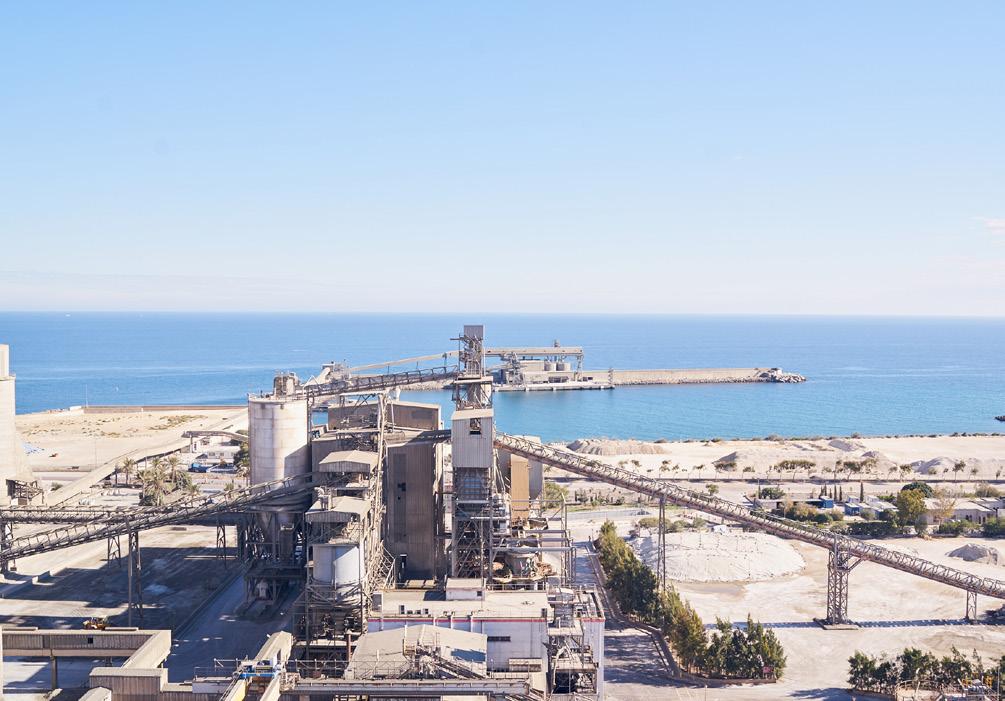
Meanwhile, important developments are under way, including the sector joining the First Movers Coalition in 2022, backing a deal for low-carbon concrete and cement. In the agreement, companies pledged to purchase at least 10% near-zero carbon cement and concrete per year by 2030. It is an ambitious goal, and one that has been met with scepticism for that reason. Success hinges on greater collaboration across the industry globally, particularly for the implementation and scale-up of CCUS.
There is a large challenge ahead to deliver this potential. The IEA estimates 170 million tpy of cement emissions will need to be captured to hit net-zero targets. Massive increases in the speed and scale of deployment are therefore needed in the next five years. Around a third of cement plants in the US and just over half in Europe have CO2 emissions below 2000 tpd, presenting multiple opportunities for modular and semi-modular CCUS solutions.
This is why Carbon Clean’s point-source carbon capture technology is making an impact, facilitating a truly global collaboration with the cement sector. The company’s CaptureX semi-modular technology that containerises around 80% of the plant and proprietary amine-based solvent is a tried and tested industry preference for carbon capture, having been used in 49 sites around the world.
Case studies
The technology has been implemented in Carbon Clean’s collaboration with Taiheyio Cement Corporation in its Kumagaya plant, located in Saitama, Japan. The 10 tpd capture plant is the country’s first-of-its-kind demonstration facility and features Carbon Clean’s CaptureX semi-modular technology, enabling highly efficient and cost-effective CO2 capture from industrial flue gases of rotary kilns used for cement production. To ensure minimal site disruption, the carbon capture technology was preinstalled in a shipping container allowing for turnkey delivery as well as quick installation and commissioning. This longstanding partnership demonstrates how CO2 capture and carbon recycling technology for cement kilns will contribute to the future of the cement industry.
A similar project is happening in Europe, where Carbon Clean’s CaptureX technology is being implemented by Holcim in Almeria, Spain. The semi-modular solution will be capturing CO2 from the flue gas of rotary kilns for cement production. When fully operational, this site will capture 192 tpd of carbon dioxide, which will then be recycled and used for accelerated crop production. This is an excellent example of utilisation (the ‘U’ in CCUS).
Finally, Carbon Clean is working closely with Cemex, one of the world’s largest cement producers, to take part in the transformation
Cemex cement plant in Rüdersdorf, Germany. CycloneCC industrial unit, UAE.of Rüdersdorf into the first carbon-neutral cement facility by 2030, made possible by the Carbon Neutral Alliance. Carbon Clean is currently in discussions with Cemex to scale up carbon capture and expand into carbon utilisation with green hydrogen, demonstrating the ability of CCUS to decarbonise heavy industry and repurpose CO2.
A new carbon capture technology
As Carbon Clean continues to scale, one interesting development is CycloneCC carbon capture technology, which is fully modular, prefabricated, and skid-mounted. The size and cost of carbon capture technology have historically been significant barriers to adoption. CycloneCC overcomes these barriers and combines Carbon Clean’s advanced APBS-CDRMax® solvent with rotating packed beds (RPBs), resulting in equipment 10 times smaller and an overall footprint up to 50% smaller. Most importantly for a sector that will require wide-reaching investment, CycloneCC allows hard-to-abate industries to reduce both CAPEX and OPEX by up to 50%.
Carbon Clean has thus amassed more than 100 active patent assets to date across 18 patent families covering 30 countries. ADNOC has selected CycloneCC for a carbon capture project at Fertiglobe’s plant located in the Al Ruways Industrial Complex in Abu Dhabi – the first deployment of an industrial unit anywhere in the world. The modular technology is also currently being deployed in
North America. Once commercialised, Carbon Clean will prioritise scaling projects.
This is a perfect fit for the cement sector as most cement players have multiple plants with common features enabling further standardised customisation making the technology much more cost competitive compared to conventional solutions.
Conclusion
Through Carbon Clean’s collaboration with industry leaders and its expert understanding of the challenges ahead, it is clear that carbon capture will be crucial to unlocking decarbonisation for the cement sector. To achieve net-zero targets, players across the ecosystem must work together to support at-scale deployment. Point-source carbon capture technology will be one of the most efficient, reliable and cost-effective ways to decarbonise an industry that is under increasing pressure to deliver on its ambitious targets.
About the author
Prateek Bumb co-founded Carbon Clean in 2009 and is Chief Technology Officer. He is the principal innovator of the company’s carbon capture technologies, including its breakthrough modular CycloneCC solution. He is responsible for developing and delivering Carbon Clean’s technology roadmap and leading the project engineering team. He is also a member of the Board.
•
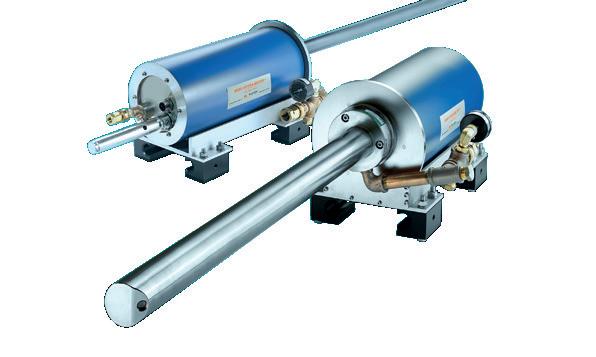
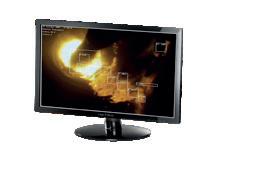
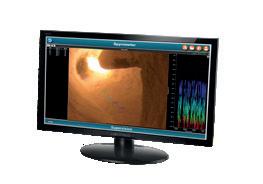
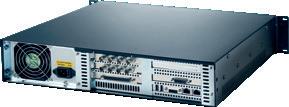
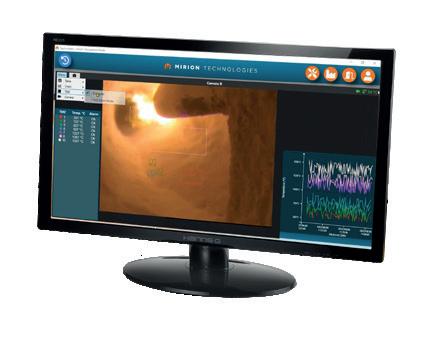
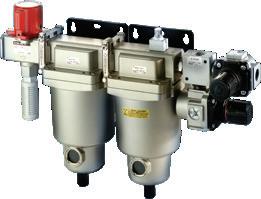
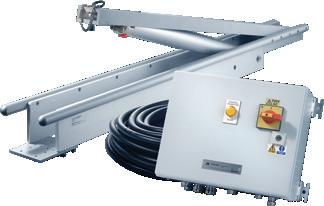
Beyond emissions
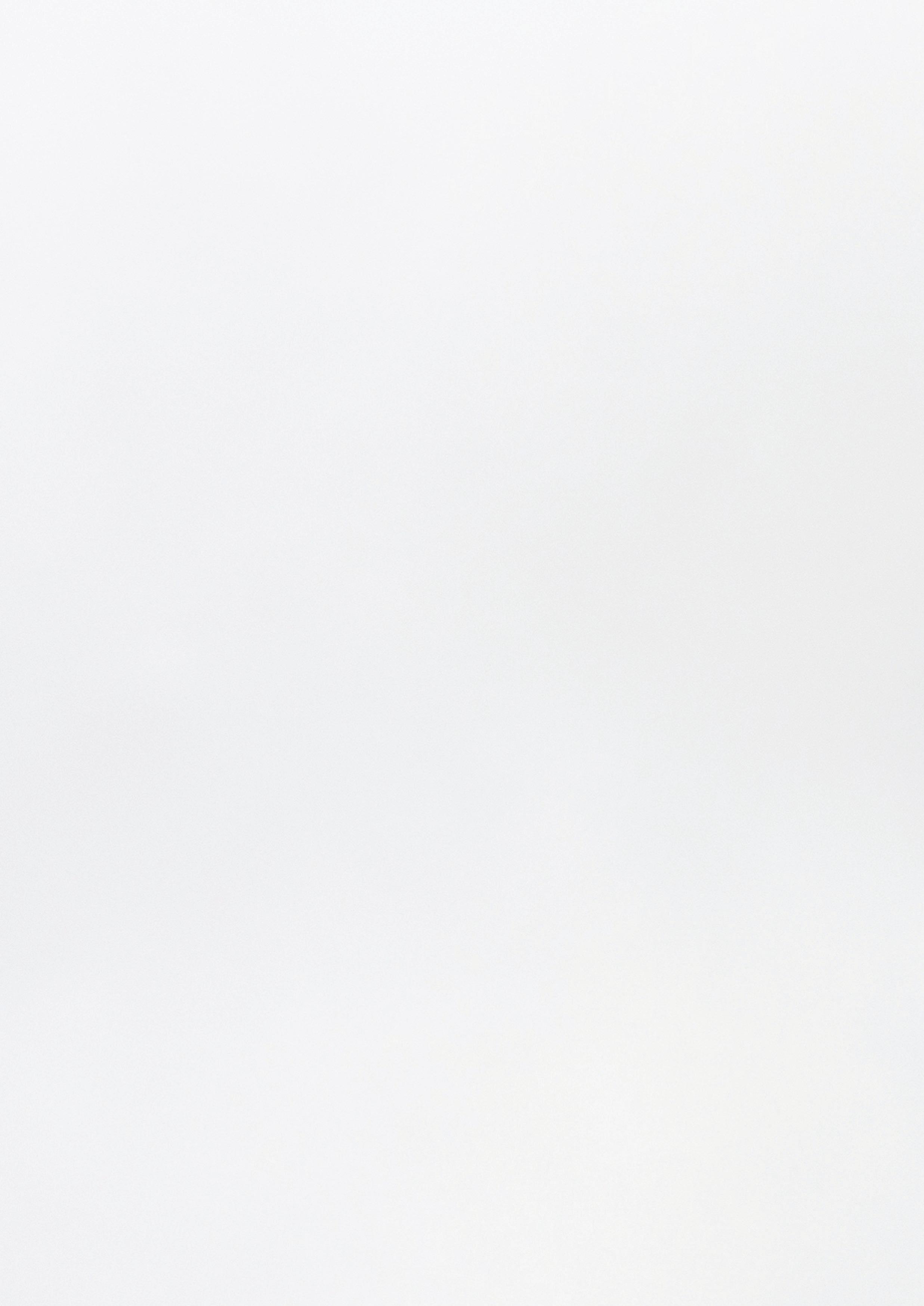
Jens Kristian Jørsboe, Jimmy Andersen, Christian Riber, and Burcin Temel McKenna, Ramboll, discuss various carbon capture technologies and their advantages and disadvantages.
Cement production is the foundation of global construction, indispensable for infrastructure projects ranging from towering skyscrapers to intricate road networks. However, the production of cement is emission-intensive and has a large environmental footprint. Despite significant progress, challenges remain in the widespread decarbonisation of cement production, where technical feasibility, cost considerations, and policy support are among the key factors. This article sheds light on the challenges and opportunities in achieving a more sustainable cement industry.
Ramboll is a global engineering consultancy with 18 000 experts based around the world. The carbon capture team has conducted over 125 studies ranging from feasibility to FEED, Balance-of-plant, and EPCM studies including projects being built in various geographies. Ramboll provides services for the whole
value chain of CCUS: carbon capture, liquefaction, transport via rail or pipelines, utilisation into methanol or aviation fuel, storage and regulatory advisory.
Options for the mitigation of greenhouse gas emissions
The deployment of carbon capture in the cement industry is a significant area of interest when it comes to reducing greenhouse gas (GHG) emissions. According to the Global Cement and Concrete Association, cement production is responsible for approximately 7% of the global carbon dioxide (CO2) emissions. This is due to the calcination process, which releases CO2 from limestone (calcium carbonate) during clinker production. The production of clinker also requires high temperatures and combustion of fuels to provide energy for the process. Therefore, the

emissions from cement production come primarily from the process and fuel consumption for the calcination process.
There are various options available to cement producers to reduce their environmental impact:
f Energy efficiency improvements: Implementing energy-efficient technologies and practices can reduce the energy consumption of clinker production, thereby lowering CO2 emissions. This includes optimising kiln operations, improving heat recovery systems, and minimising energy waste.
f Alternative fuels (AF): Substituting traditional fossil fuels with AF such as biomass, waste-derived fuels, and non-recyclable plastics can reduce the CO2 emissions from clinker production. These AF often have some biogenic carbon content and can help lower the overall fossil carbon footprint of the cement manufacturing process.
f Lower carbon products: Blending clinker with supplementary cementitious materials such as fly ash or slag can reduce the amount of clinker needed in cement production.
f Oxyfuel combustion: The cement kiln and/or calciner can be designed to use pure oxygen instead of air. This results in a flue gas stream with higher CO2 concentration, making it easier to capture.
f Carbon capture and storage (CCS): This method captures CO2 from the flue gases emitted during cement production. Carbon capture technologies are more widely applicable and can be retrofitted to existing cement plants.
While there are diverse options available, there are limitations to these approaches. For example, the energy efficiency of the cement plant has typically been optimised, and further optimisation or improvements may require considerable investments. AF vary in terms of their availability and quality, and the infrastructure for supplying them must be established.
Substituting clinker with supplementary materials can affect the performance and quality of the final cement product, potentially impacting properties such as strength, durability, and setting time. The availability and cost of supplementary materials, such as fly ash and slag, can vary regionally, limiting their widespread adoption as clinker substitutes.
These general improvement approaches reduce emissions but there will always be inherent release of CO2 during the calcination process.
Oxyfuel combustion aims to produce a highly concentrated CO2 stream by using pure oxygen for the combustion process. However, the false air ingress in the cement plant will pollute the highly concentrated CO2 product and an added carbon capture unit might be needed.
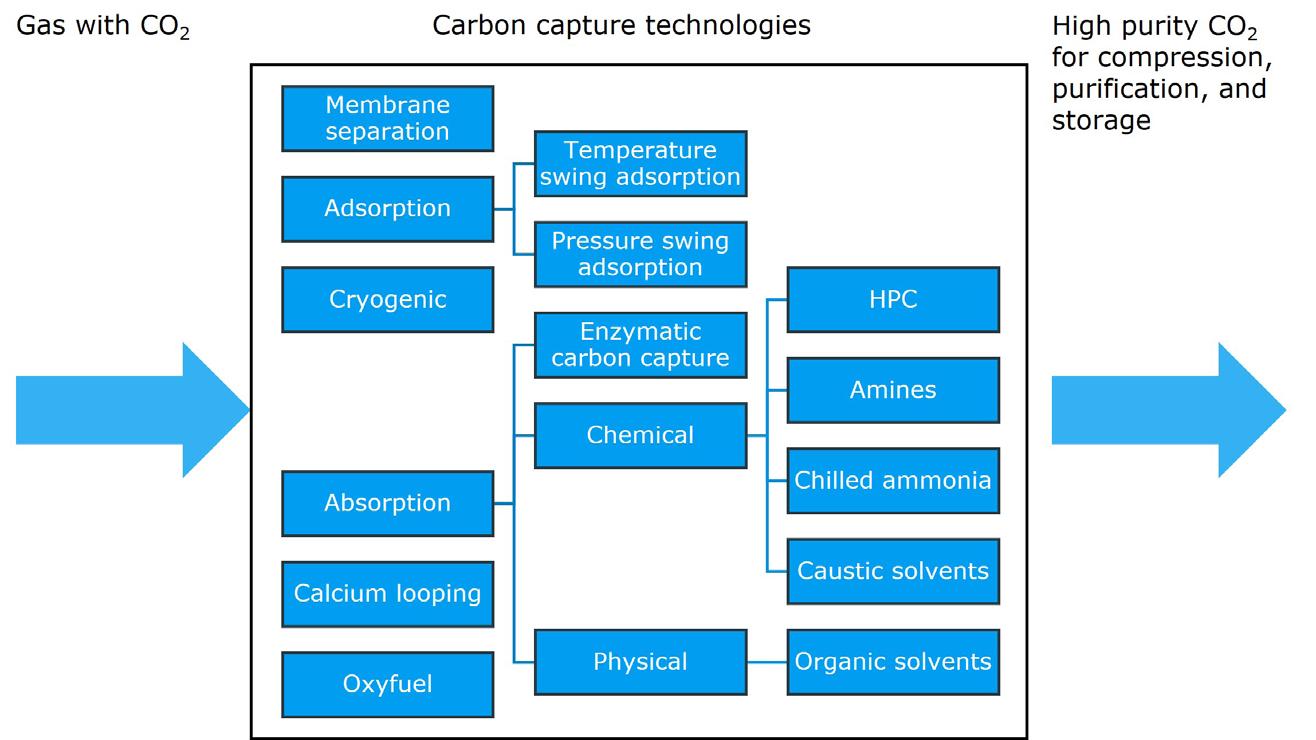
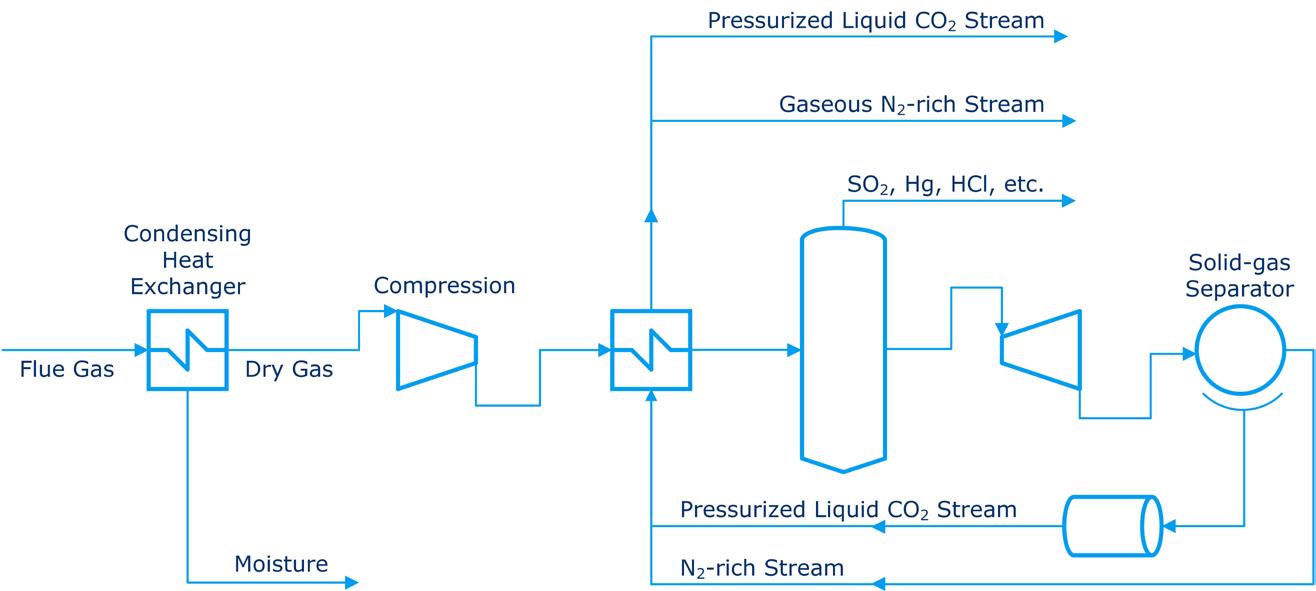
CCS technologies are still relatively new as an application for cement plants and may require further development and optimisation to achieve widespread deployment.
CCS implementation can be expensive, and the scale of deployment needed to achieve significant emission reductions in the cement industry may pose logistical and economic challenges. Finding suitable storage sites for captured CO2 and ensuring their long-term integrity and security can be challenging. However, carbon capture technologies offer a significant reduction in CO2 emissions, as it is possible to capture most of the CO2 from the flue gas released from cement production.
Overview of carbon capture technologies
Carbon capture technologies can be used to capture CO2 emissions from various industries like cement, power
Figure 1. Overview of carbon capture technologies.generation, steel, biogas plants, and refineries.
Currently, there is a wide array of carbon capture technologies available. The high CO2 concentration in the flue gas from cement production is an advantage as the carbon capture technologies benefit from higher CO2 concentrations. Another advantage is that cement plants are large CO2 point sources, which allows for economies of scale, thereby reducing the capital investment per ton of CO2. Moreover, the cement plants are operated at a steady base load thereby incurring low variation of CO2 emissions. The location of cement plants can, however, be challenging for CO2 infrastructure.
An overview of the carbon capture technologies is given in Figure 1.
Each carbon capture technology has advantages and challenges, including energy consumption, cost, scalability, and environmental impact. The carbon capture technologies apply either a chemical or physical separation principle.
The physical separation processes include adsorption, membrane separation, and cryogenic separation. Adsorption processes involve passing flue gases through a solid material, known as an adsorbent, which can selectively capture CO2 Common adsorbents are either activated carbon or zeolites. Once the adsorbent is saturated with CO2, it is regenerated by changing temperature or pressure, releasing the captured CO2 for storage or utilisation. Membrane separation uses semi-permeable membranes to selectively separate CO2 from flue gases based on differences in molecular size and solubility. Cryogenic separation involves cooling the flue gas to extremely low temperatures to condense and separate CO2 from other gases.
Physical separation processes are widely applied for removal of CO2 from biogas (biogas upgrading), which has a slightly higher concentration of CO2 compared to flue gas from cement production. The physical separation processes can also be combined in hybrid systems to take
advantage of their complementary strengths and to obtain higher CO2 purity. However, there are limited references for these processes for large-scale application.
Currently, the amine-based absorption process is the most mature carbon capture technology with references for large-scale application. In this process, the flue gas, containing CO2, is directed through an absorber column, and contacted with an alkaline solution denoted as solvent. The CO2 reacts and is absorbed into the solvent. The solvent with the absorbed CO2 is regenerated in a stripping column, typically conducted at elevated temperatures. Once the CO2 is released, the regenerated solvent is returned to the absorber column to capture more CO2 from the flue gas. The released CO2 can then be compressed and transported for storage or utilisation.
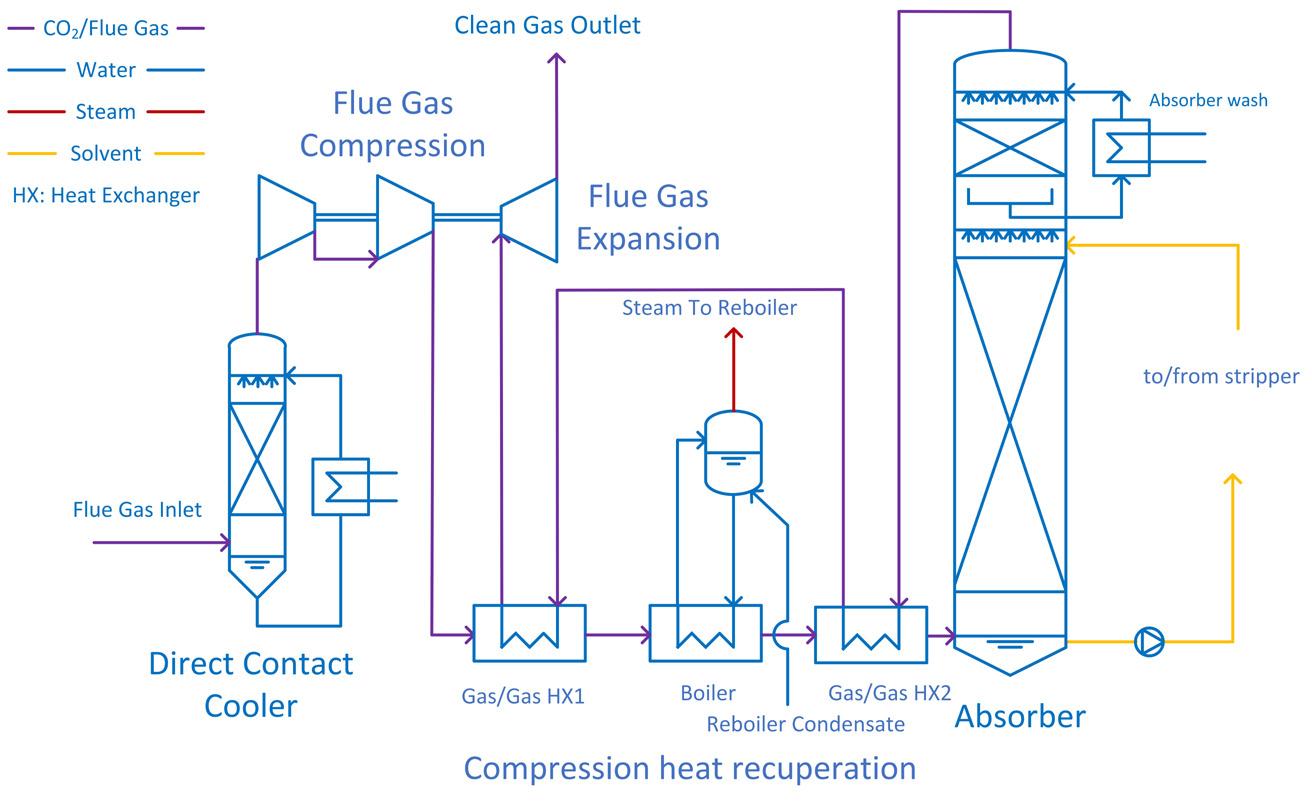
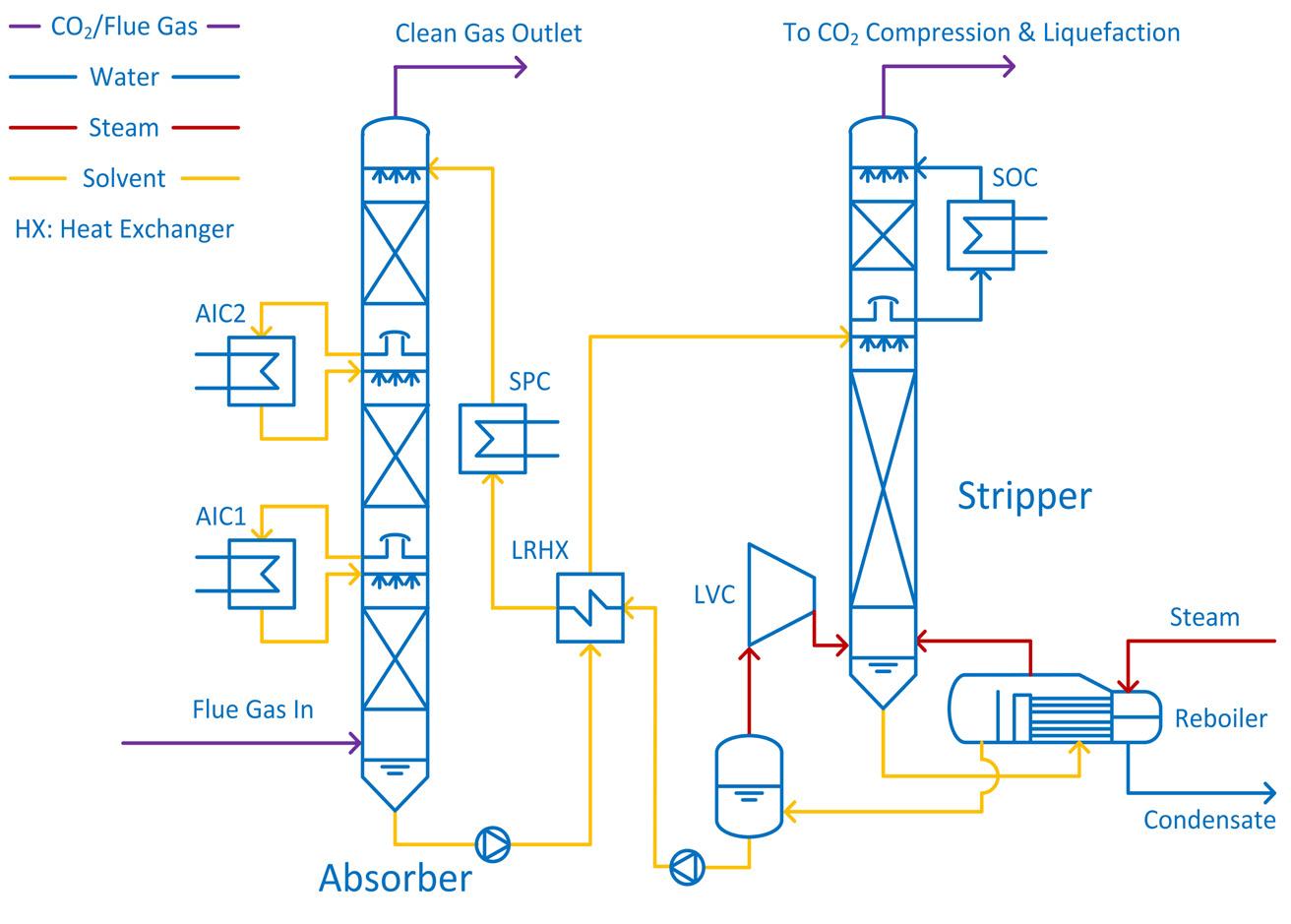
Cryogenic carbon capture
Cryogenic carbon capture is a physical separation process that separates CO2 by cooling the gas stream to very low temperatures, typically between -100 and -135˚C. The process diagram of the cryogenic separation is illustrated in Figure 2. In the flow diagram, the water content of the gas stream is removed by condensation. The gas stream then undergoes compression and subsequent cooling to achieve conditions where CO2 desublimates, becoming solid from its gas phase, and the CO2 can then be removed.
Due to costs associated with compression of the flue gas, the cryogenic carbon capture process greatly benefits from high CO2 concentrations in the treated flue gas such as in the case for cement production. The cryogenic separation process may also be coupled with pressure swing adsorption, membrane separation or oxyfuel to increase the CO2 concentration prior to the cryogenic separation.
Cryogenic carbon capture has several advantages including high capture rate of above 95%, high CO2 purity, and, relatively, energy requirements are potentially low compared to other carbon capture technologies. Cryogenic carbon capture is a tail-end technology that only requires access to sufficient power and cooling, and a low energy penalty can be ensured with heat integration. However, it also has challenges, such as high capital costs associated with the cryogenic equipment and has limited references in large-scale application.
Hot potassium carbonate (HPC) carbon capture
The HPC solution reacts with CO2 in the flue gas, forming potassium bicarbonate (KHCO3) when water is present. The HPC process is an example of a chemical absorption process for carbon capture. The chemical absorption process includes an absorption column and a regeneration column. The flow diagram, excluding the regeneration vessel, is illustrated in Figure 3.
HPC offers high CO2 capture efficiency (removal rates typically exceeding 90%), low thermal energy requirements, and can handle fluctuating CO2 concentrations and flow rates in industrial flue gases.
The potassium carbonate solution has lower affinity towards CO2 compared to other solvents and therefore requires an elevated partial pressure of CO2 in the absorber column. The elevated partial pressure of CO2 is obtained by compression of the flue gas to obtain a CO2 partial pressure of approximately 1 bar. The compression of the flue gas requires electrical energy, however a lot of the thermal energy needed in the desorption process can be recuperated from the compression step as shown in Figure 3.
The HPC process benefits from the high CO2 concentrations in the flue gas from cement production. Considering a typical CO2 concentration of 20%, the flue gas must undergo compression to only 5 bar compared to 7 – 8 bar for solid fuel combustion plants such as biomass or waste-to-energy facilities. Further, HPC does not need much steam, which cement plants do not have. The HPC is therefore a good fit for carbon capture from cement plants.
However, challenges associated with hot potassium carbonate carbon capture include the corrosive nature of potassium carbonate solutions, reduced reaction speed over time, and the need for efficient heat integration and solvent regeneration to minimise energy consumption and operating costs. Ongoing research and development efforts focus on addressing these challenges and improving the overall performance and cost-effectiveness of the technology. The maturity of the technology is the main drawback, as the flue gas compression has not been displayed or confirmed/verified for post-combustion applications.
Optimisation of the amine-based carbon capture process
Amine-based carbon capture is widely used and offers several advantages such as high CO2 capture, scalability making it suitable for large-scale applications, and compatibility with existing industrial infrastructure, easing retrofitting to existing plants. However, challenges associated with amine-based carbon capture include a high energy consumption for solvent regeneration, solvent degradation, and potential corrosion issues. Efforts continue to focus on reducing the energy requirements of the process,
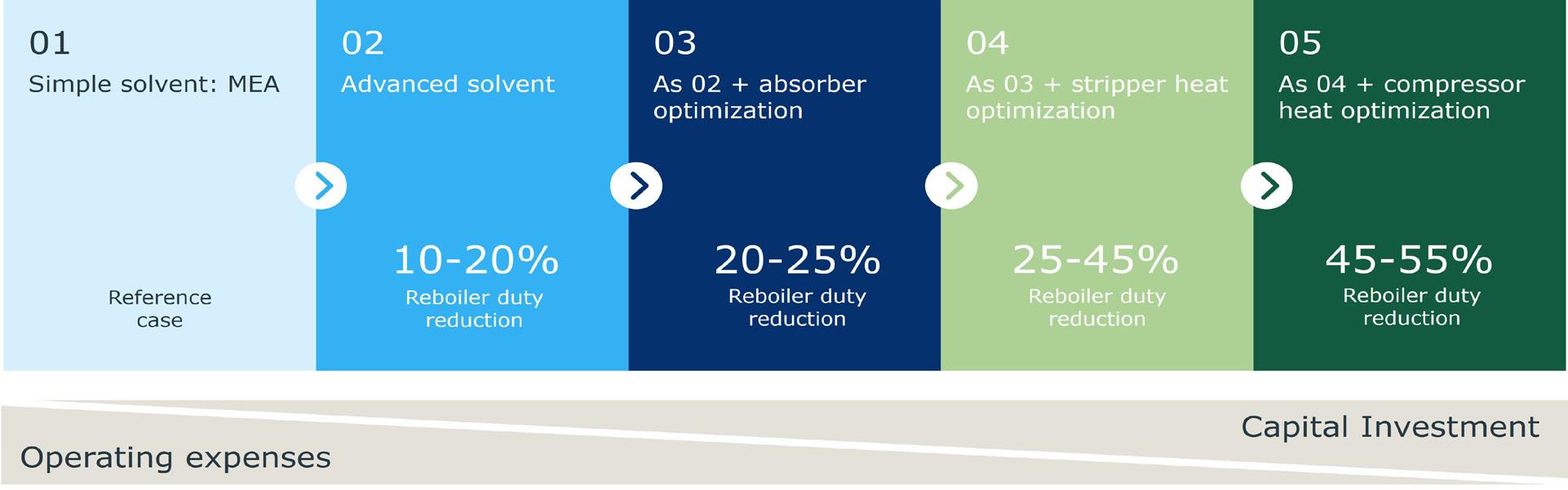
especially reboiler duty, and improving the solvent resistance towards degradation.
One approach to improve amine-based carbon capture is to use alternative amines or blends of amines. The traditional amines include monoethanolamine (MEA), diethanolamine (DEA), and methyldiethanolamine (MDEA). In recent times, amine blends have been developed such as AMP-PZ (CESAR1) and AMP-DMSO. Furthermore, there are advanced supplier designed amines commercially available: MHI (KS-1™, KS-21™), OASE®blue, ACC™ S21 & S26, APBS-CDRMax®, CANSOLV DC-103, or Econamine FG PlusSM. The development of these new amine solvents has resulted in 10 – 20% lower energy consumption, more stable solvents, and less make-up/reclaiming needed. However, these new solvents are more expensive and careful emission control may be required depending on flue gas NOx levels, and the temperature and pressure in the absorber column.
Another approach to reduce the energy requirement of the carbon capture process is internal carbon capture improvements. There are various approaches for optimising the flow diagram of carbon capture. Some improvements include absorber intercooling (AIC), lean vapour compression (LVC), or mechanical recompression systems (MVR). A flow diagram of the amine-based carbon capture with AIC and LVC is illustrated in Figure 4. By using AIC, the solvent can absorb more CO2, consequently reducing the reboiler duty. The LVC configuration flashes the hot regenerated solvent from the reboiler to provide additional stripping steam. This reduces the amount of necessary reboiler duty, but it comes at the expense of compressor power costs.
Amine-based carbon capture at cement plants faces different challenges such as the availability of steam, and the cleaning and cooling of the flue gas to make it suitable for carbon capture. The need for steam can be reduced by optimisation of the heat integration and by implementation of heat pumps and steam fans. The amine-based carbon capture can thereby be considered with varying complexity. Different cases of the amine-based carbon capture process are shown in Figure 5, where the expected reduction in the reboiler duty is included.
To supply the carbon capture plant with heat, waste heat can be recovered from both calciner flue gas and clinker cooler gas through large waste heat recovery (WHR) units, also called boiler units. WHR allows for some steam production to be used directly in the carbon capture reboiler. It can also be used to upgrade hot water with heat pumps and steam fans to provide a significant amount of steam for the reboiler. The potential energy available in a standard cement kiln process allows for approximately 30 – 40% of the energy needed to be delivered as steam, and 40 – 100% of the energy needed to be delivered as hot water. By optimisation of the amine-based carbon capture process and using WHR, it is thereby
almost possible to cover the heat demand for the amine-based carbon capture facility without investing in a dedicated steam producing system.
Carbon capture in the cement industry
According to IEA, the cement sector is the third-largest industrial energy consumer and the second-largest industrial CO2 emitter globally. To get on track with the Net Zero Scenario, emissions from cement production must fall by an average of 3% annually by 2030. Carbon capture is crucial for the cement industry as it offers a pathway to mitigate the significant GHG emissions associated with its production. Currently, there are many projects working on improving ways to capture carbon emissions from the cement industry. Some methods, like cryogenic and membrane technologies, are being developed, but they have not been tested on the scale needed for cement production yet. Oxyfuel technology is also receiving a lot of attention, although it requires a larger interaction with the main process than post-combustion technologies. Finally, there are also other carbon capture technologies only focusing on the calcination part of cement production, which may become feasible.
There are various technologies available for carbon capture and some may see implementation on a large-scale in the future, but the carbon capture technology with the most large-scale references is currently the amine-based capture technology. This technology is commercially available, can be retrofitted to an existing cement plant, and there are various options for heat integration to reduce the operating costs of the technology. By adopting carbon capture and through the continued innovation of emissions reduction technologies, the cement industry can make significant strides towards decarbonisation and sustainable production of cement.
About the authors
Burcin Temel Mckenna, Head of Department, is Global Head of Carbon Capture at Ramboll serving optimal customer outcomes for system integration in CCUS projects within Waste-to-Energy, Cement and Biomass.
Christian Riber, Business Development Manager, has been leading more than 35 CCS projects for the past seven years and has profound knowledge of the entire CCS value chain.
Jimmy Andersen, Lead Carbon Capture Consultant, has more than 10 years of experience in the power plant industry and has comprehensive knowledge of operation and optimisation of the carbon capture process.
Jens Kristian Jørsboe, Consultant, has more than five years of experience within carbon capture technologies and a strong background in process modelling and optimisation.
Global coverage of the cement industry
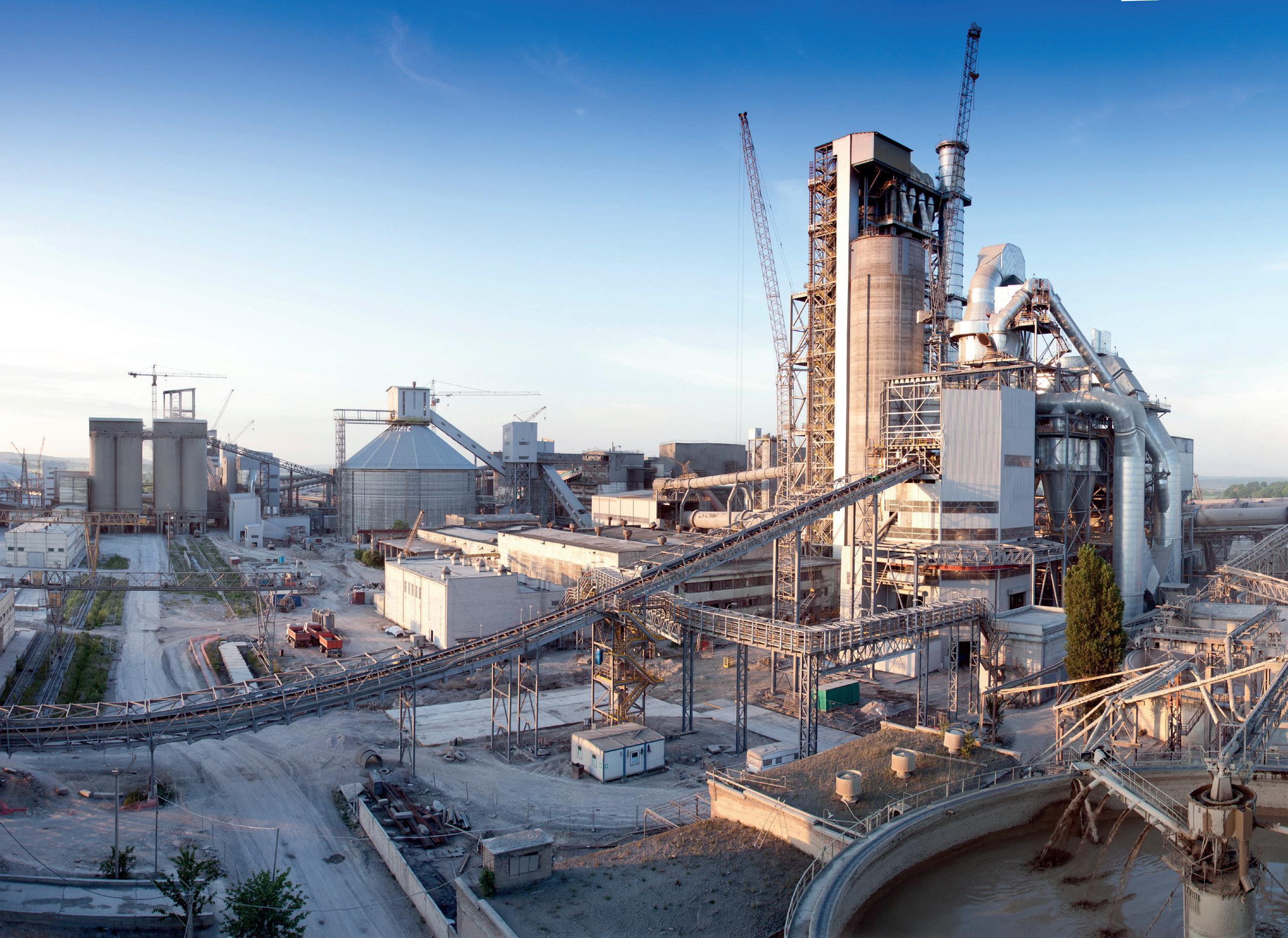
• International cement news
• Regional reports
• Market analysis
• Event previews and reviews
• In-depth technical articles
• In-depth regional analysis by key players in the industry
• Comprehensive technical reviews on all aspects of cement production, from the quarry face to despatch


Advancing mechanochemical activation
TA. Thomas, S.C. Liew, M. Pagels, & P. Suraneni, Carbon Upcycling Technologies, explore the use of enhanced mechanochemical activation to transform materials into SCMs.
he 2020s have been deemed the ‘decade to deliver’ by the Global Cement & Concrete Association (GCCA) in their Net Zero Concrete Roadmap. GCCA member companies have committed to a 25% reduction in net emissions, relative to a 1990 baseline, by the end of the decade. To meet this ambitious target, alternative materials are critical to enabling low-carbon cement and concrete. However, as the energy transition accelerates across various industries like energy and steel, the availability of traditional supplementary cementitious materials (SCMs) like fly ash and ground granulated blast furnace slag (GGBFS) is dwindling and cement supply chains are becoming more volatile, uncertain,
and international. Consequently, future SCM supplies will most likely be imported from slower-to-transition nations to North American and European markets, as is already beginning to happen globally.
With 2030 CO2 emission reduction targets looming, the cement and concrete industry faces a pressing need to develop new SCM sources that are local, abundant, and can be produced with low energy consumption.
An overview
Carbon Upcycling Technologies (CUT) is a carbon capture and utilisation company that manufactures low-carbon, engineered SCMs from captured CO2 and upcycled industrial wastes or natural minerals. The company has developed expertise in the transformation of non-traditional, inert materials into enhanced SCMs through its proprietary Mechanically Assisted Chemical Exfoliation (MACE) process.
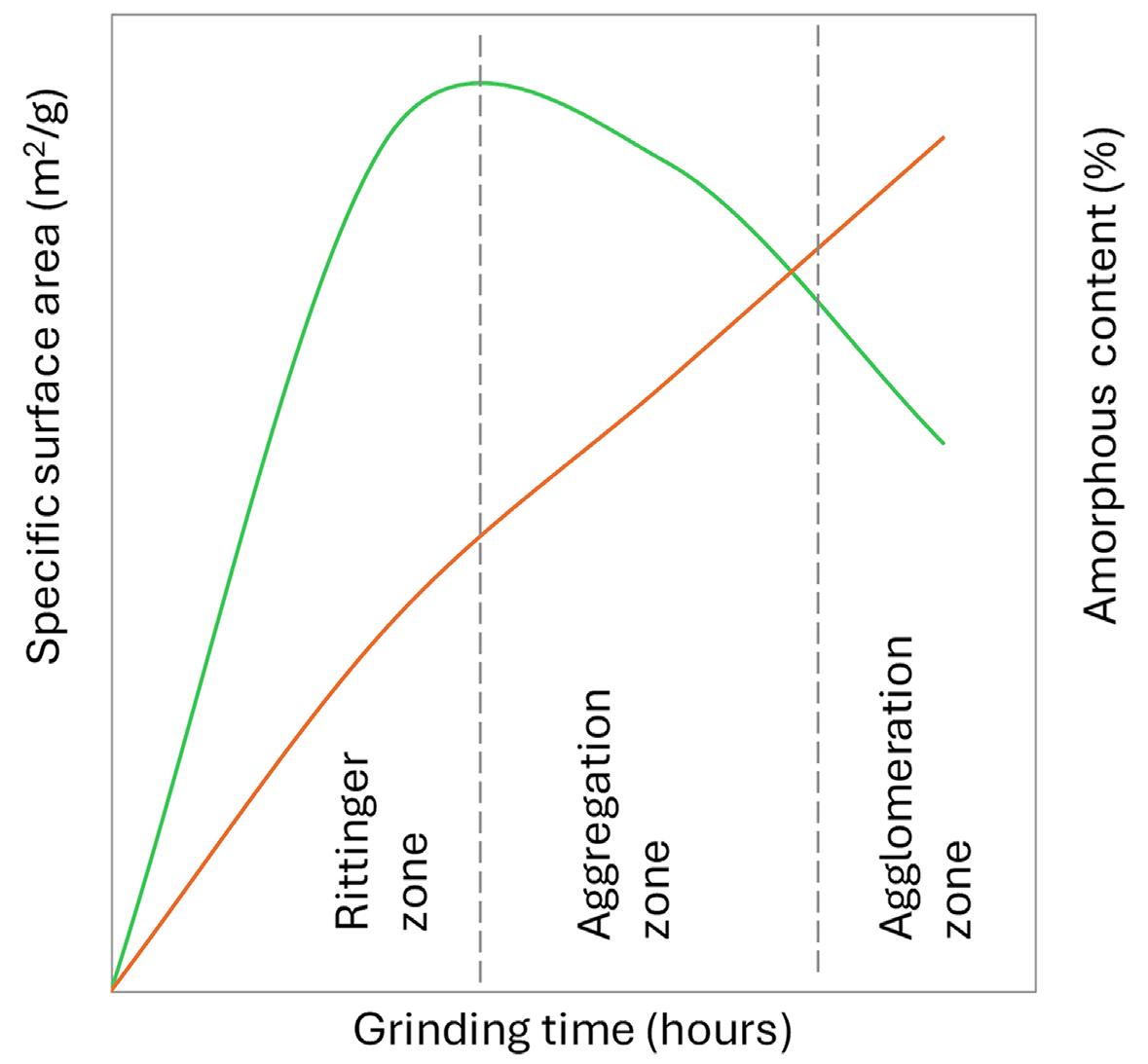
Figure 1. Illustrative curve of specific surface versus grinding time in MCA.1 The specific surface area increases and then reduces with grinding time due to agglomeration. Amorphous content increases with grinding time.
Mechanochemical activation (MCA) is a chemically-facilitated grinding process, that breaks down highly crystalline materials, increasing their amorphous content, and producing reactive cementitious materials. CUT’s proprietary process uses CO2 to increase the processing efficiency of conventional MCA.
Furthermore, when materials rich in calcium and magnesium are utilised, an opportunity for carbon capture arises, as CO2 can be trapped as carbonates. CUT’s technology, a dry, low-pressure system, is implemented at cement plants and other emission points to directly capture CO2 from kiln flue stacks.
Feedstock, alongside flue gas, enters the reactor, where it undergoes grinding and exfoliation, transforming into a SCM while mineralising CO2. This continuous process upgrades inert or off-spec materials, such as clays, steel slags, quarry fines, processed mineral residue, and landfilled ashes, into valuable local sources of enhanced SCMs.
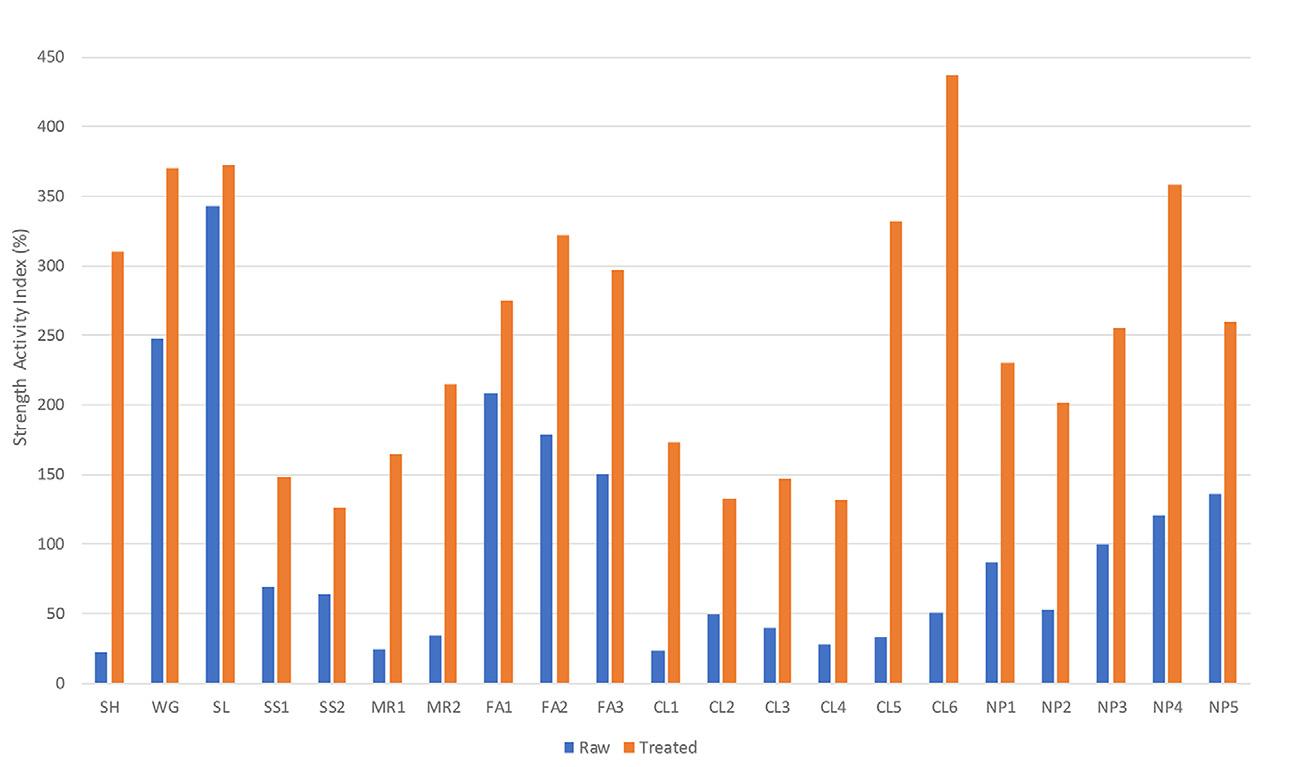
Figure 2. Heat release summary for all raw and treated materials. SH is shale, WG is waste glass, SL is GGBFS, SS is steel slag, MR is mineral processing residue, FA is fly ash, CL is clay, LK is low kaolinitic clay, HK is high kaolinitic clay, and NP is natural pozzolan. In all cases, the treated materials show large increases in reactivity compared to the raw materials.
To date, CUT has activated over a hundred different materials with diverse chemical compositions. CUT is currently working with two large international construction material companies to produce reactive SCMs from the aforementioned materials to enable blended cements. CUT has operated a mill for the past three years for a Canadian ready-mix plant to process Class F fly ash, producing over 3000 t of CO2-enhanced SCMs that have been used in a slew
of construction projects across Western Canada.
Mechanochemical activation MCA is different from conventional grinding. In conventional grinding, the surface area increases and the particle size reduces. However, the material structure is not modified chemically (beyond the occasional contamination from grinding media). Conventional grinding processes are often thought to follow von Rittinger’s Law which states that the energy needed for the grinding process in powders is directly proportional to the increase in surface area that results.1 In other words, the material surface area is directly proportional to the grinding time.
There are many theories relating to MCA. The Avvakumov model, as shown in Figure 1, suggests that initially (stage 1), behaviour similar to Rittinger’s Law governs where the specific surface area (SSA) increases. In stage 2, agglomerative processes limit the increase in surface area, however, the mechanical energy results in a chemical/structural change of the material, resulting in a structural breakdown of the crystalline phases into highly amorphous products. In stage 3, the SSA further reduces, while the amorphous content further increases.1 The increased disorder in the amorphised material and the increased surface area contribute to the increased reactivity and transformation of inert materials into SCMs.
Clays and MCA
Clays have long been considered one of the most promising sources to produce new SCMs at scale. They are abundantly available across the world, and commensurate in volume with the billions of tonnes of cement production that is projected to expand by over 50% by 2050.2 The main technology available to activate clays into reactive SCM involves the relatively energy-intensive thermal process of calcination. In calcination, clays are heated to 700 – 900˚C to induce dehydroxylation of the clay minerals’
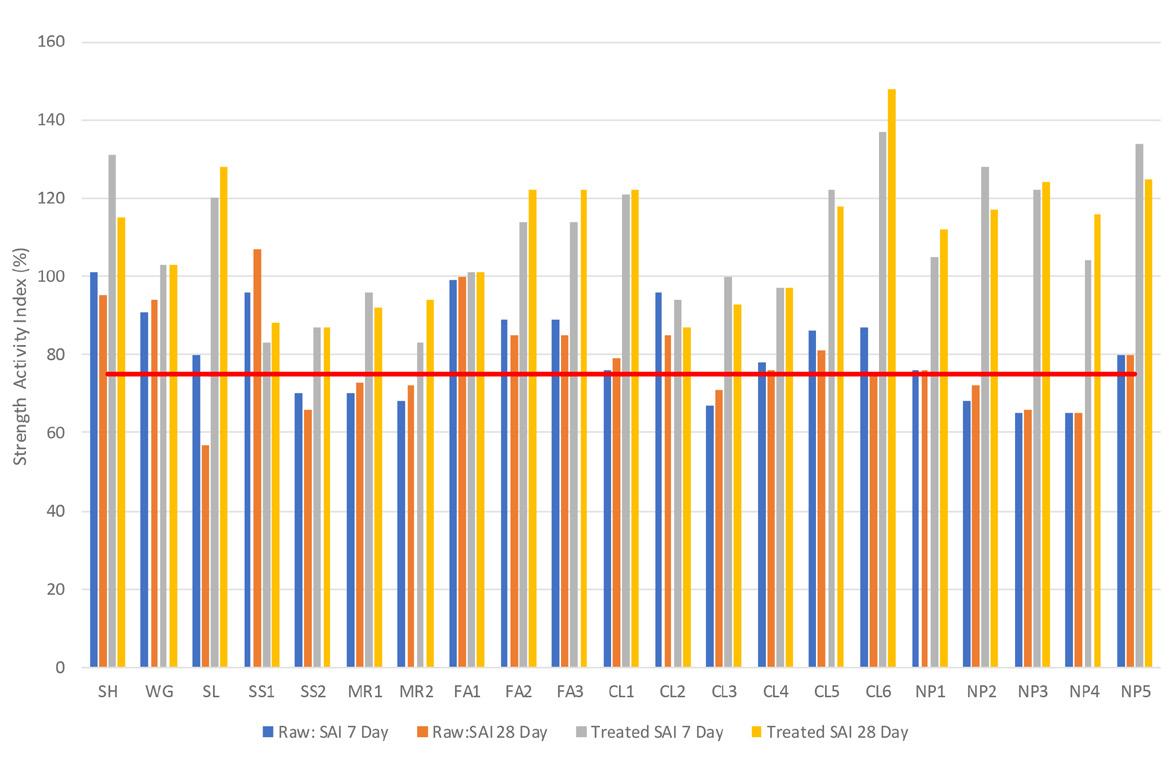
Figure 3. SAI summary for all raw and treated materials. Most treated materials show a significantly increased SAI at 7 and 28 days, compared to the raw materials.
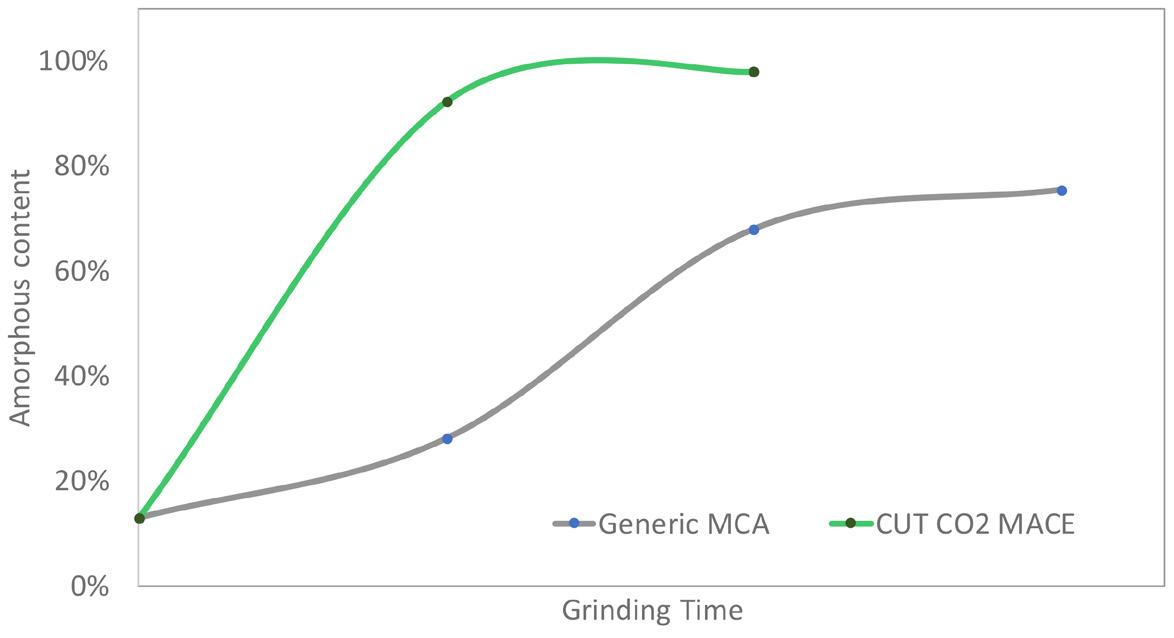
Figure 4. Comparison of amorphous content versus grinding time between MCA and CUT CO2 MACE. The MACE process achieves greater amorphous content compared to MCA at similar processing times.
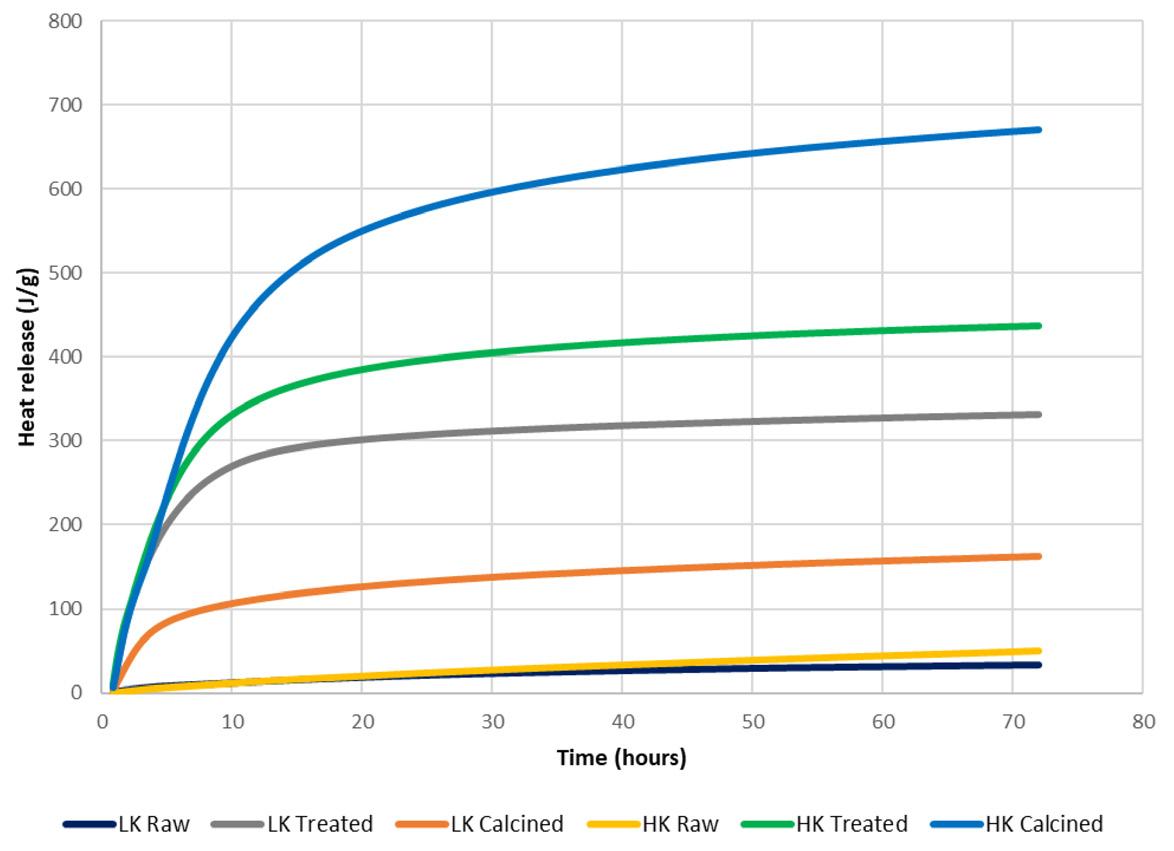
Figure 5. Reactivity of raw, calcined, and CUT MACE activated clays. Both calcination and MACE increase the raw material reactivity significantly. MACE is more effective than calcination for low-kaolinitic clays, while for high-kaolinitic clays, it is the other way around.
structural disorder. The resulting calcined clays exhibit reactivity suitable for SCM use, however, effectiveness is proportional to the kaolinite content in the clay, being generally ineffective below 30%.3 Despite being less energy intensive than cement production, calcination still relies on fossil fuel combustion. Clay calcination also has other challenges, generally producing off-colour products with high water demand in cements and concrete.
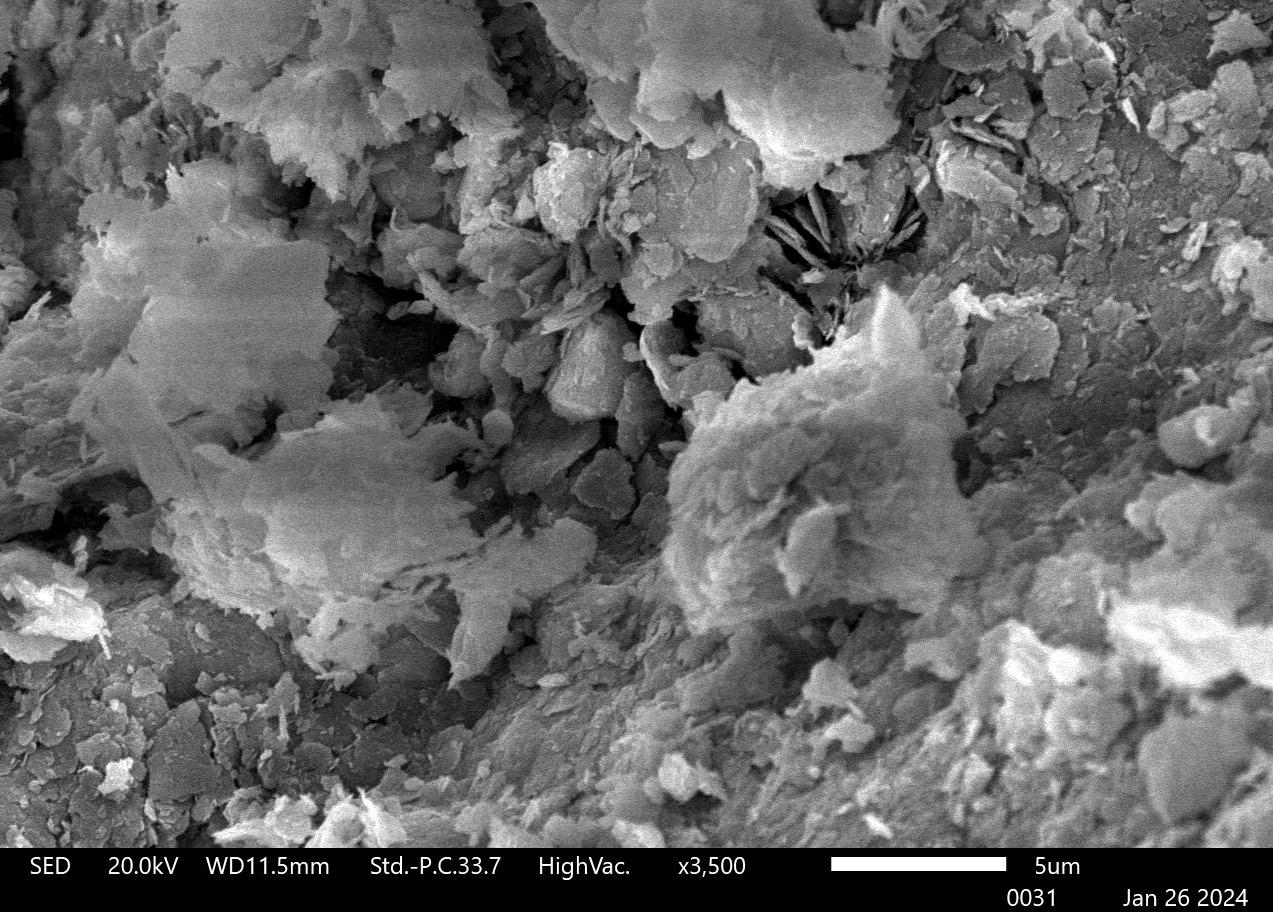

Mechanochemical activation, in contrast, can activate clays with kaolinite content below 30%.1,3,4 Kaolinitic and other clays are activated by MCA as the energy leads to rupture of Al-O-Si and other bonds, changes in Al coordination, and surface changes of Al/Si ratio, which result in amorphisation due to a loss of order.1 Using CUT technology, it is possible to activate a range of clays, including those with kaolin contents as low as 5%. Compared to calcination, the process requires less energy, and can result in products with higher reactivity and reduced water demand requirements.
Reactivity measurements
SCMs are incorporated into concrete due to their pozzolanic and latent hydraulic reactions, leading to increased formation of C-S-H, which enhances densification and transport properties, ultimately improving durability. Reactivity, indicating the extent of these reactions, is measured through various methods such as selective dissolution heat release, calcium hydroxid consumption, and strength tests. Reactivity is closely associated with later-age strength and durability, albeit being a simpler measurement. In this study, reactivity was assessed using the modified R3 test, akin to ASTM C1897 R3 test.5
Results using enhanced mechanochemical activation
Figure 2 provides a summary of the results, showing the heat release of the raw (pre-processing) and treated (post-processing) materials for 21 different materials.
Significant changes in reactivity post-treatment are evident in Figure 2, with increases sometimes being three to thirteen times (200 – 1200%) or more than that of the initial reactivity. The threshold for inert materials has been suggested to be around 100 J/g SCM. All treated materials shown here pass the threshold. Most raw materials shown here, do not.
For the same materials, Figure 3 shows the ASTM C311 strength activity index (SAI) data at 7 and 28 days, respectively. Most materials show a significantly increased SAI value post-processing at both 7 and 28 days, including several materials that show values of more than 100% SAI.
Enhanced mechanochemical activation for clays
Table 1 shows the mineral composition determined by x-ray diffraction (XRD) for two sources of clay, low and high in kaolinite
Figure 6. LK clay raw SEM image. Figure 7. LK clay CUT SEM image.content, denoted LK and HK, respectively.
CUT’s CO2 enhanced MACE process effectively lowers the kaolinite content in both cases, with the treated materials showing almost no residual kaolinite content and increased amorphous content. The reduced kaolinite content and increased amorphous content drives increased reactivity (which as discussed earlier is linked to concrete strength and durability). The treated materials have a reactivity of between 330 – 440 J/g SCM, compared to the inert raw materials, which have a reactivity of between 34 – 50 J/g SCM.
Figure 4 shows a comparison of the evolution of the amorphous contents for the two processes. CUT’s process achieves greater SSA and amorphous content than conventional MCA, even at considerably lower processing times.
The CUT process diverges from typical MCA, featuring significant amorphisation in the Rittinger zone. This prolonged zone leads to reduced processing times and energy, along with higher surface area and reactivity compared to conventional MCA. Process kinetics are also altered, with amorphous content increasing more rapidly in the MACE process. CO2 enhancements can be understood by examining clays as an illustrative example.
In the presence of CO2-rich gas under specific pressure conditions, carbonic acid can form through a reaction with the water released by clay dehydroxylation, or from water added to the system. These acid-derived protons penetrate and attack the structural OH groups within the unmodified clay layers.
Simultaneously, the grinding action continuously comminutes the material further, increasing the SSA, and exposes the unaltered layers. This self-propagating cycle of dehydroxylation and acid formation leads to an efficient process that produces a mixture of amorphous, porous, protonated, and hydrated aluminosilicates with high reactivity. It is also possible that the CO2 acts as a lubricant between layers, or as a grinding aid, which reduces the inherent agglomeration and extends the Rittinger zone.
As with other materials (Figure 2), after CUT’s MACE process there is a significant increase in the reactivity of the clays.
Figure 5 shows reactivity results comparing the raw materials to the CUT treated materials and their calcined counterparts. The raw clays are inert, with heat release below 50 J/g SCM. For LK and HK clays, the heat release increased by 888% and 771%
after the MACE process, with the activated reactivity values being 332 and 437 J/g SCM, respectively. For the HK clay, as expected, calcination gives high reactivity (670 J/g SCM) whereas for the LK clay, the reactivity is low, 162 J/g SCM. For low kaolinitic clay sources, MCA, and specifically MACE provide far greater reactivity than calcination. In other words, MACE can more reliably activate clays, regardless of their kaolinite content, when compared with calcination.
Figures 6, 7, 8, and 9 illustrate the changes in the clay microstructure before and after CUT’s MACE process. Both LK and HK clays show a structural change from large flaky particulates to smaller and rounder particulates. The particle size reduction and SSA increase is evident from the micrographs.
In MCA, the increased SSA contributes to the increased reactivity, as does the amorphisation (arguably, amorphisation is more crucial, as inert materials cannot be activated simply through particle size reduction). In addition,
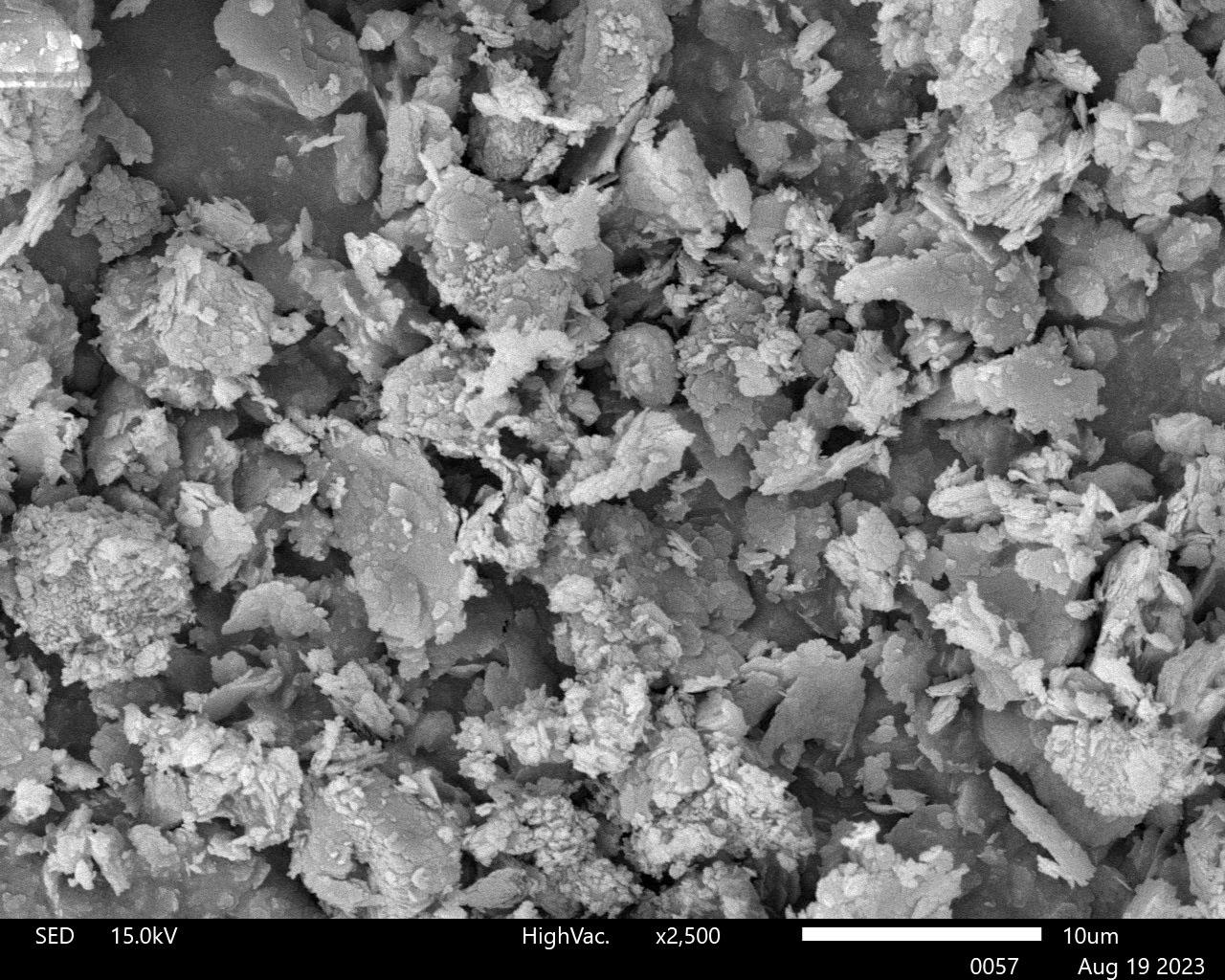
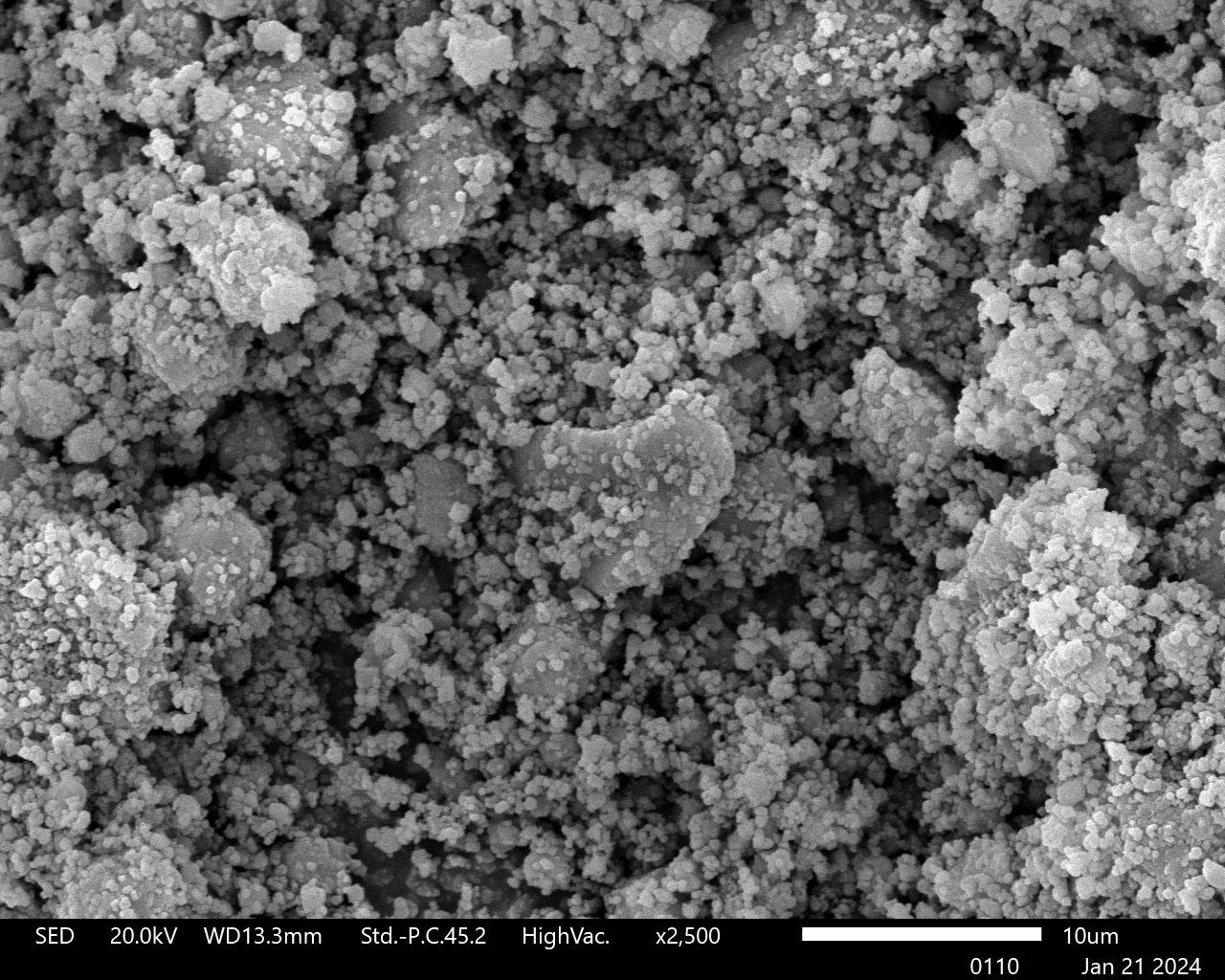
due to the spherical particles, the water requirement is lower than with calcined clays. The increased water/superplasticiser demand can often limit replacement levels of calcined clays in practice, hence this reduced demand is a major advantage of the MACE process.1,4,6
Market potential
To decarbonise rapidly, the cement sector needs to fundamentally decouple cement manufacturing from fossil fuel combustion. Advancements in low-carbon heating technologies are promising, but there are already viable and imminently actionable pathways to creating cementitious material that bypass the need for energy-intensive thermal and electrical processes.
The global south, where most of the impending demand for cement is projected to rise, requires low-carbon cement to be cost-effective at target cost range of between US$20 – 50/t at scale.
Technologies capable of activating local, readily available alternative feedstocks, such as low-kaolin clays and new steel slags, commensurate with the market demand for clinker production are critical to achieving these production costs. By adopting CO2-embedded SCMs, cement manufacturers have an unprecedented opportunity to reconstruct themselves from major heavy emitters into generators of high-quality carbon credits, an invaluable future commodity.
Conclusions
As the energy transition makes the cement supply chain for conventional SCMs such as fly ash and GGBFS fundamentally vulnerable, Carbon Upcycling’s MCA process stands out as a pivotal solution for local, circular SCM production and carbon sequestration.
The CO2 enhanced process results in specific surface area, amorphous content, and activation comparable to conventional MCA using lesser energy and shorter processing time.
A significant increase in reactivity is achieved for numerous feedstocks, when comparing treated and raw materials.This increased reactivity is driven by increases in amorphous content and specific surface area. MACE activated clays and other materials show reduced water demand, when compared to calcined clays, which is at least partially due to the spherical particles generated. By enabling the use of diverse materials and carbon mineralisation through an all-electric, low-energy pathway, CUT’s process has established a scalable and economically viable pathway to meaningfully reducing the
emissions of the cement industry in this critical decade of climate action.
References
1. TOLE, I., HABERMEHL-CWIRZEN, K. and CWIRZEN, A., ‘Mechanochemical Activation of Natural Clay Minerals: An Alternative to Produce Sustainable Cementitious Binders–Review,’ Mineralogy and Petrology, Vol. 113 (2019), pp. 449 – 462.
2. TANAKA, N. and STIGSON, B., ‘Cement Technology Roadmap: Carbon Emissions Reductions up to 2050,’ World Business Council for Sustainable Development, (2009), pp. 1 – 36.
3. MAIER, M., BEUNTNER, N., and THIENEL, K.C., ‘Mineralogical Characterization and Reactivity Test of Common Clays Suitable as Supplementary Cementitious Material,’ Applied Clay Science, Vol. 202 (2021), p. 105990.
4. SOURI, A., KAZEMI-KAMYAB, H., SNELLINGS, R., NAGHIZADEH, R., GOLESTANI-FARD, F., and SCRIVENER, K., ‘Pozzolanic Activity of Mechanochemically and Thermally Activated Kaolins in Cement,’ Cement and Concrete Research, Vol. 77 (2015), pp. 47 – 59.
5. SURANENI, P., ‘Recent Developments in Reactivity Testing of Supplementary Cementitious Materials,’ RILEM Technical Letters, Vol. 6 (2021), pp.131 – 139.
6. FERRARI, L., BORTOLOTTI, V., MIKANOVIC, N., BEN-HAHA, M. and FRANZONI, E., ‘Influence of calcined clay on workability of mortars with low-carbon cement,’ NanoWorld J, Vol. 9(S2) (2023), pp. S30 – S34.
About the authors
Dr. Markus Pagels is the Research and Development Manager at Carbon Upcycling Technologies. He is a chemist with over two decades of experience in oil and gas and chemical industries.
Dr. Prannoy Suraneni is Assistant Professor at the University of Miami and Principal at Miami Concrete Consulting LLC. Along with his team, he works on supplementary cementitious materials and coastal infrastructure.
Alex Thomas is the Operation Manager at Carbon Upcycling Technologies’ US laboratory. His focus is on supporting the research and development of new materials for use as supplementary cementitious materials.
Sip Chen Liew is the Senior Research and Development Associate at Carbon Upcycling Technologies. He is a chemist with over a decade of experience in energy and carbon management research.
Tim Sperry, Carbon Limit, explains how merging direct air capture (DAC) technology with carbon mineralisation can help diminish the carbon footprint associated with cement and concrete production.
It has been 200 years since the invention of Portland cement, originating from the 1824 patent by Joseph Aspdin (‘An improvement in the Mode of Producing an Artificial Stone’). Mr. Aspdin described in his patent ‘the calcination of limestone’, which was quarried on the Isle of Portland in Dorset, England at that time. The first rotary cement kilns became operational by the end of the 19th Century. It is worth noting that, since the 11th Century, until the mid-19th Century, the atmospheric CO2 levels had remained below 285 ppm.1 However, since the start of direct measurements of atmospheric CO2 by the Scripps Institution of Oceanography in 1958 (315 ppm), (then continued by NOAA (National Oceanic and Atmospheric Administration) at their Mauna Loa Observatory), the CO2 levels today
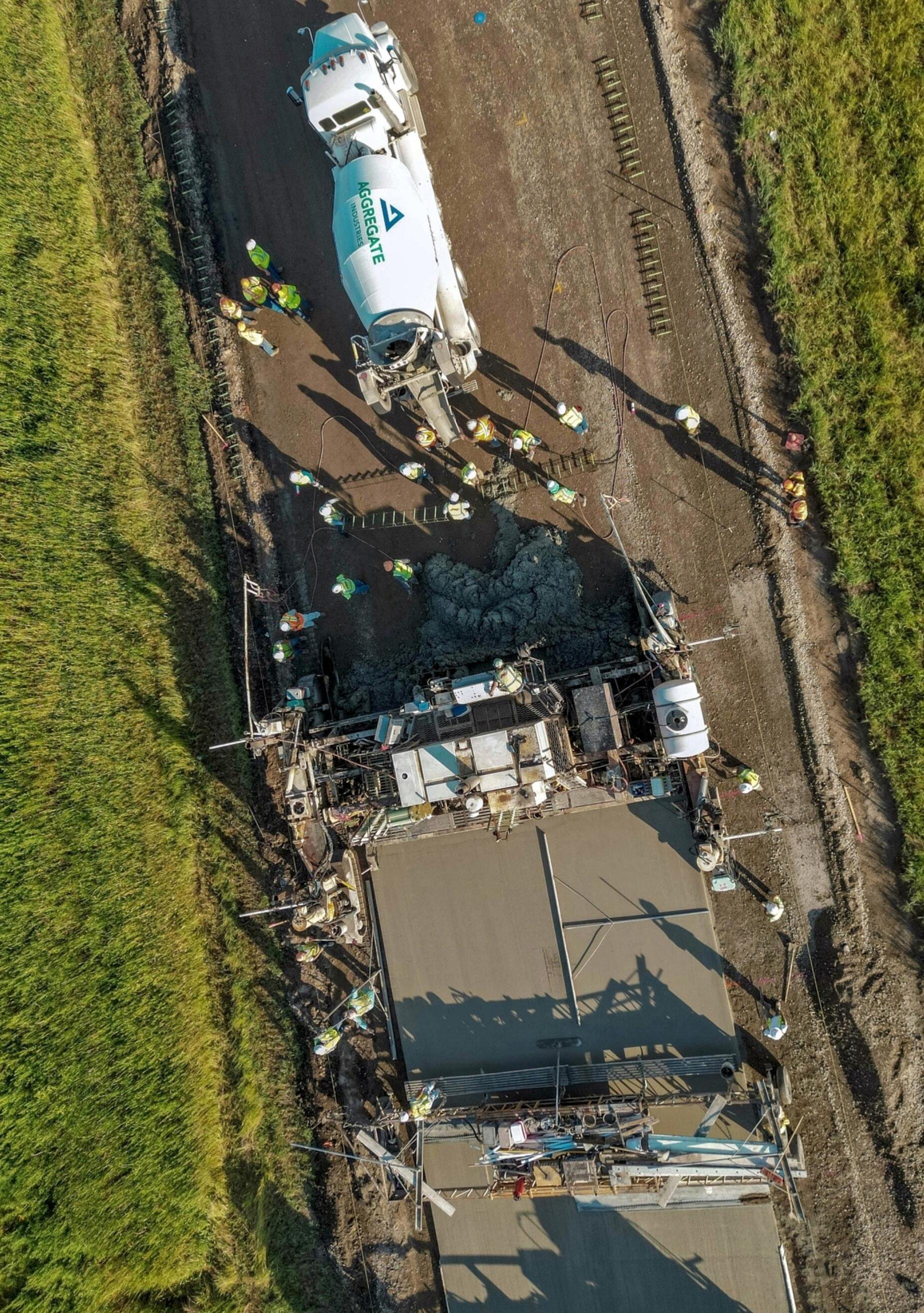
CO2-capturing concrete additives
have reached 425 ppm; a 34.9% increase observed in only 66 years.2
The production of Portland cement clinker has a high Ca/Si mole ratio, to form the major hydraulic crystalline phases of alite, C3S, belite, C2S, tricalcium aluminate and C3A in the clinker exiting the cement kiln. It is still based on the calcination of limestone quarried near the rotary cement kilns and is estimated to account for 8% of total global CO2 emissions. Portland cement is the only synthetic material globally produced at a level of around 4.1 billion t – a production rate which has remained the same since 2013.3 Its production in rotary cement kilns is well-established and fast – raw material which enters a cement kiln, exits in less than 45 minutes (a modern cement kiln typically produces about 8000 – 10 000 tpd of clinker). Moreover, concrete made with this cement (i.e., the milled clinker with functional additives) is durable to such an extent that the waste concrete


is estimated not to degrade in landfills over the next 10 000 years.
Concrete is the second most consumed material (after water) today on the planet. Rotary cement kiln operations produce CO2 emissions as a result of the calcination of inexpensive limestone and the burning of fossil fuels (to obtain the high temperature flame, at approximately 2000˚C, inside the kiln).4 Some have even conducted modelling to show that concrete may absorb atmospheric CO2 at a slow pace over its entire service life (from 60 to 100 years).5 Portland cement-based concrete is expected to remain in use for a long time. To combat the consequent emissions, transforming this concrete into an effective direct air capture (DAC) material is a potential solution.
A carbon-capturing technology for concrete
Carbon Limit is a Florida-based climate technology company, developing CaptureCrete®, a powder-based solution. CaptureCrete merges DAC technology with carbon mineralisation to significantly and effectively diminish the carbon footprint associated with concrete production. It is a powder drop-in solution, available in two different forms (CaptureCrete SCM and CaptureCrete Admixture), which puts carbon-capturing technology into the hands of cement and concrete manufacturers. They can license the formula from Carbon Limit to source the raw materials, blend the additive on-site and integrate it in their concrete manufacturing processes.
When integrated into concrete, CaptureCrete acts as a catalyst, facilitating the absorption and sequestration of CO2 molecules into the concrete matrix. This process is achieved through a unique combination of natural minerals and CO2-reactive materials, enabling carbon dioxide sequestration in concrete through a two-step process:
f CO2 molecules are drawn from the atmosphere into concrete due to their chemical affinity with CaptureCrete materials.
f The captured CO2 molecules undergo a series of chemical and physical bonding processes, which ultimately result in permanent mineralisation in the form of stable carbonate phases by reaction with the cement hydration phases.
The concrete prepared by using CaptureCrete undergoes dual carbonation, i.e., pre-cure at the point of manufacturing (nothing beyond the standard concrete manufacturing practices) and post-cure (at the ambient) as concrete starts capturing CO2 from the atmosphere. In other words, the concrete with CaptureCrete effectively turns into a super sponge that captures CO2 from the air around it and stores it internally in a solid form, where CO2 can no longer be a pollutant to
the environment. With this capability, CaptureCrete lowers the carbon footprint of urban development without sacrificing the performance or durability of traditional concrete.
A supplementary cementitious material
CaptureCrete SCM is a supplementary cementitious material (SCM), comprised mostly of natural feedstocks produced by open-pit mining and industrial-scale processing, which replaces up to 30% of cement (ordinary Portland cement (OPC) or Portland limestone cement (PLC)) by mass. CaptureCrete SCM, due to its lower carbon footprint compared to OPC or PLC, creates an initial carbon footprint reduction by avoiding CO2 emissions when replacing cement. In one of Carbon Limit’s major pilot projects, CaptureCrete SCM was used in a concrete pavement (570 pcy total cementitious, 0.42 water-cementitious ratio, 500 psi flexural strength at 28 days, 5 – 8% air), and it met all requirements for fresh and hardened properties. It significantly exceeded the control concrete in terms of compressive strength, bulk electrical resistivity and rapid chloride permeability.
An admixture
CaptureCrete Admixture is added to concrete batches up to the level of 1.0% by weight of the cementitious materials and it is comprised of raw feedstocks that do not require any synthesis processes. In third-party tests, CaptureCrete Admixture has been certified to meet all the requirements of ASTM C494 – Type S in terms of fresh concrete properties, early and long-term mechanical properties, and durability.
High quality carbon credits
Carbon Limit’s forward carbon credits have been validated by Bureau Veritas under Covalent’s Certificate Standard and are available for pre-purchase. Every time CaptureCrete is used in concrete, it generates high quality carbon credits of 1000+ year permanence. VCUs (verified carbon units) may be issued for the greenhouse gas emission reductions and removals associated with Carbon Limit’s CaptureCrete right from the project’s start date. The quantification of captured and avoided CO2 is generated for each mix and applications where Carbon Limit’s licensees use CaptureCrete.
Overall benefits
In addition to reducing concrete’s carbon footprint, whilst maintaining a high performance, CaptureCrete is a versatile solution compatible with many different applications and mix designs, ranging from ready-mix concrete, concrete blocks, Stucco mortar and other cement-products, as shown in Figure 1. Furthermore, the global
accessibility of the raw materials facilitates the adoption of CaptureCrete, and thanks to the licensing model, scalability can be achieved rapidly. Finally, the technology is cost-competitive, as the addition of CaptureCrete (both the SCM and Admixture), only adds a modest cost addition per ton of concrete, which can be further offset by the revenues generated from carbon credits.
Case study: Lightweight concrete sidings
One of Carbon Limit’s licensees uses CaptureCrete SCM at 30% replacement in lightweight concrete sidings, thereby generating both CO2 avoidances and removals. The images in Figure 2 show three mortar cube samples that were exposed
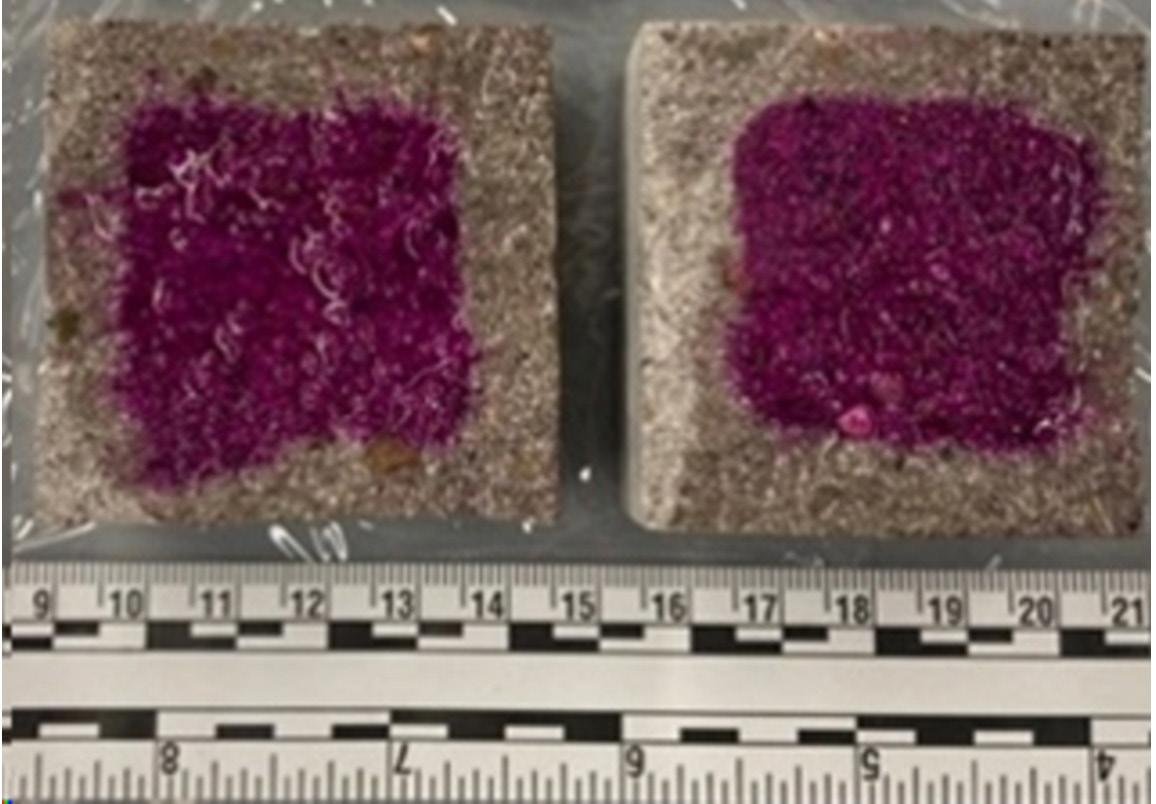
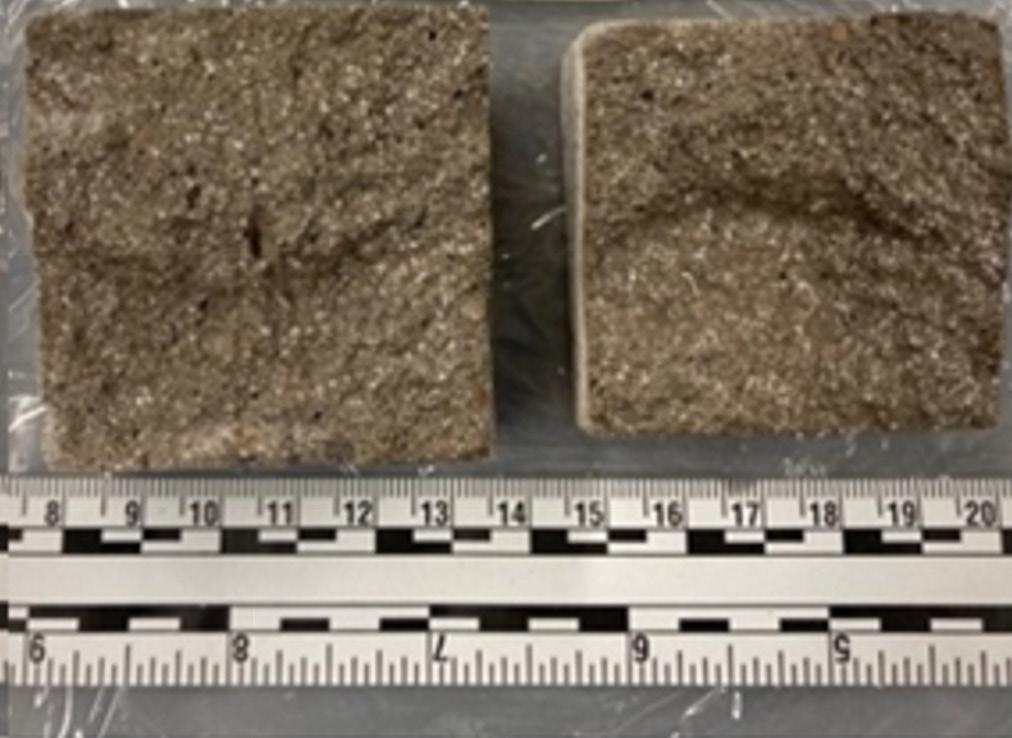
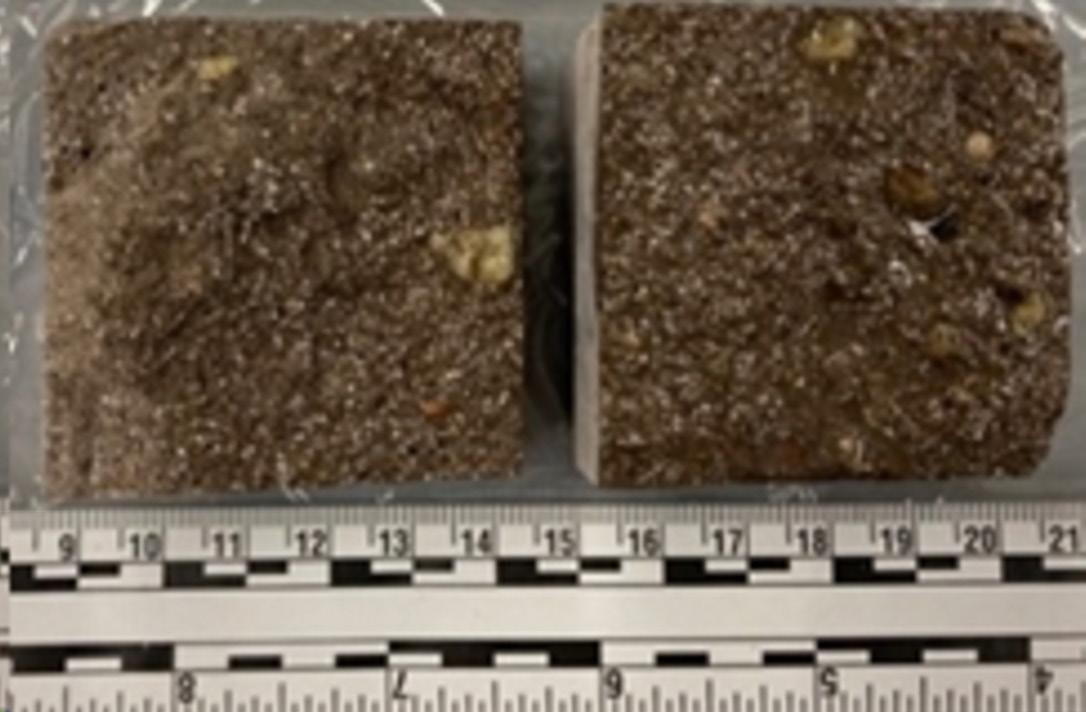
Control, 28% carbonation, (Middle) 1% CaptureCrete Admixture, 100% carbonation, (Bottom) 30% CaptureCrete SCM, 100% carbonation.
to the same amount of CO2 (accelerated carbonation; 50°C, with 20% CO2, for six days). A phenolphthalein solution was used to assess the extent of carbonation. The areas which are not pink in colour are the carbonated areas while the remaining pink area is not carbonated. CaptureCrete visibly enhances CO2 penetration and mineralisation in concrete as the control sample still showcases pink non-carbonated bulk area while both CaptureCrete specimens are fully carbonated.
A solution against climate change Technologies like CaptureCrete are important, as they serve to combat climate change by countering the consequences of human action. Innovation is necessary to alter our planet’s climate change trajectory, which often seems perilous when looking at the above-mentioned CO2 metrics. However bleak some of the numbers may seem, exciting new technologies are being unveiled that serve to turn what was once
from the air. The Carbon Limit technology works pre-cure and post-cure to decarbonise and capture harmful carbon emissions with a nature-based cement replacement made of non-calcined active minerals and materials that are highly reactive to CO2. This reactive nature pulls CO2 from the environment around the concrete pour and permanently captures it.
References
1. ‘Global CO2 levels’ – https://www.2degreesinstitute. org/ and https://www.co2levels.org/
2. NOAA, ‘Trends in Atmospheric Carbon Dioxide’ –https://gml.noaa.gov/ccgg/trends/
3. Statistica, ‘Production Volume of Cement Worldwide from 1995 to 2023,’ https://www.statista.com/ statistics/1087115/global-cement-production-volume/
4. TENNIS, P, ‘Portland-Limestone Cements: History, Performance, and Specifications,’ Portland Cement Association – https://onlinepubs.trb.org/onlinepubs/ webinars/121113.pdf)
5. XI, F., et al., ‘Substantial Global Carbon Uptake by
AD INDEX
ABC www.abc.org.uk
CemAI www.cemai.com
Coomtech www.coomtech.com
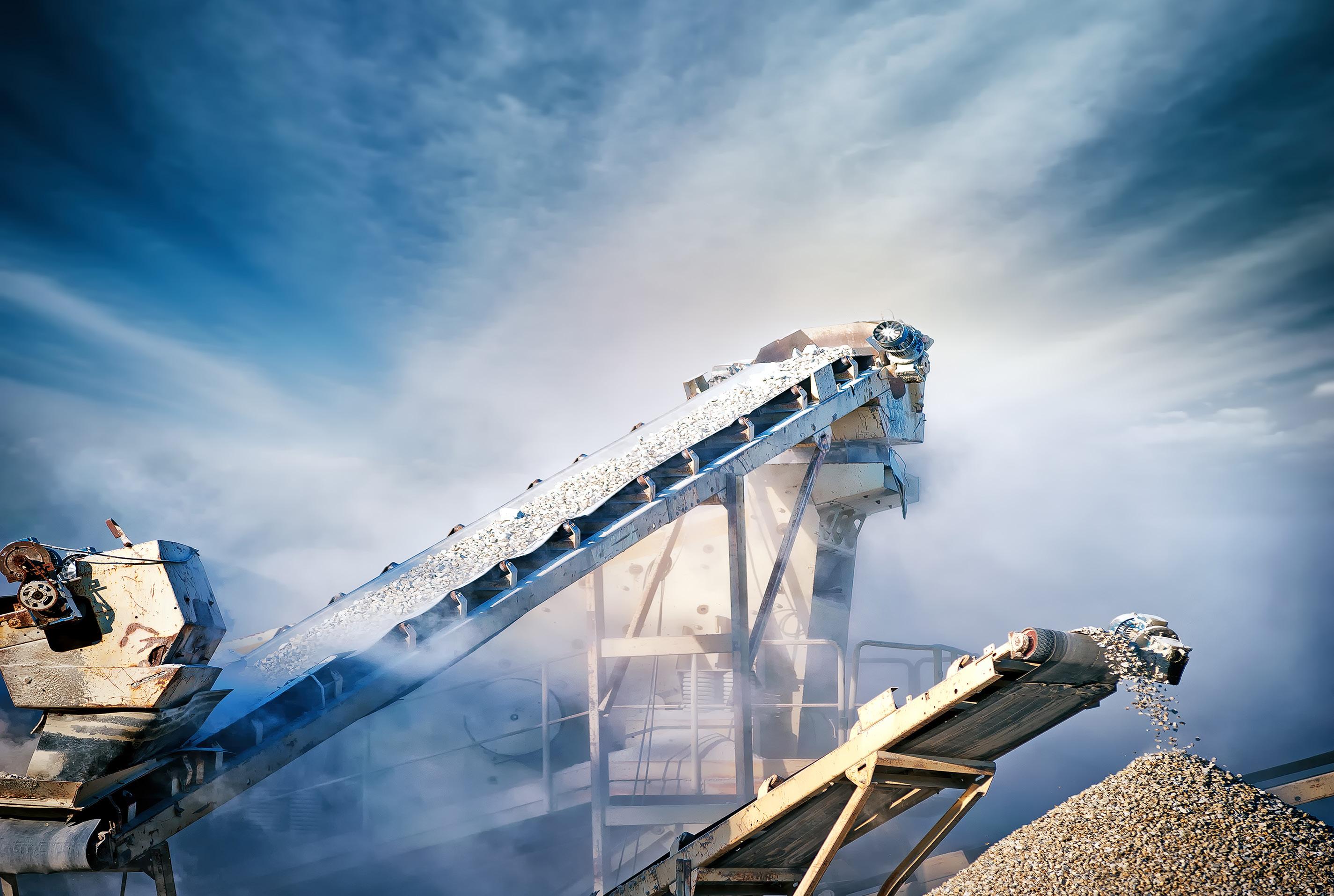
Dracyon Corp. www.drayconcorp.com
ENOTEC www.enotec.com
Euromecc www.euromecc.com
Geometrica www.geometrica.com
HEKO www.heko.com
InterCem www.intercem.de
KHD Humboldt Wedag www.khd.com
Mirion Technologies www.mirion.com
Quantum IR www.quantumir.com
Scheuch USA, Inc. www.scheuchna.com
Silobau Thorwesten www.thorwesten.com
Van Aalst Bulk Handling www.vanaalstbulkhandling.com
VDZ Congress www.vdz-congress.org
World Cement www.worldcement.com
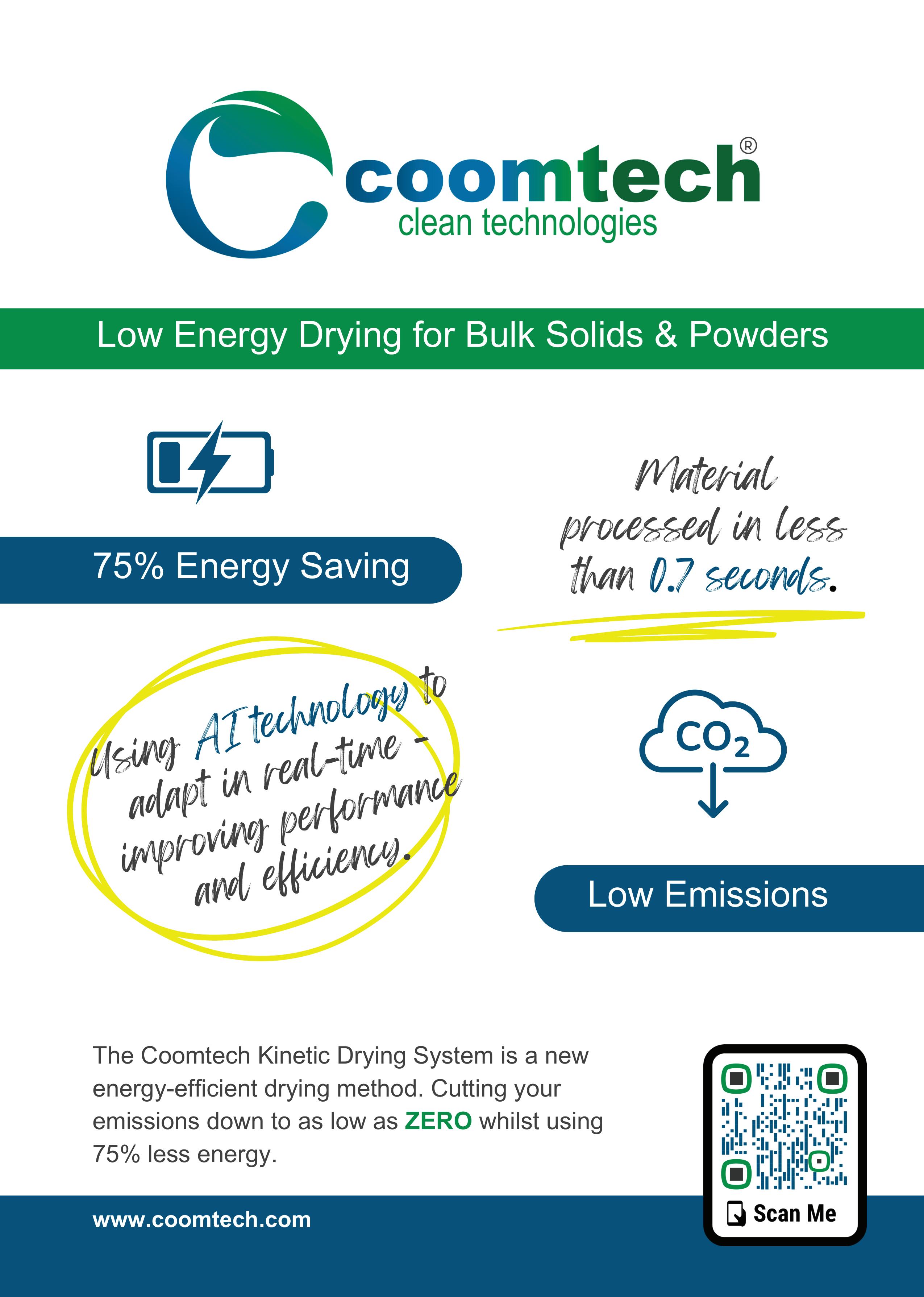
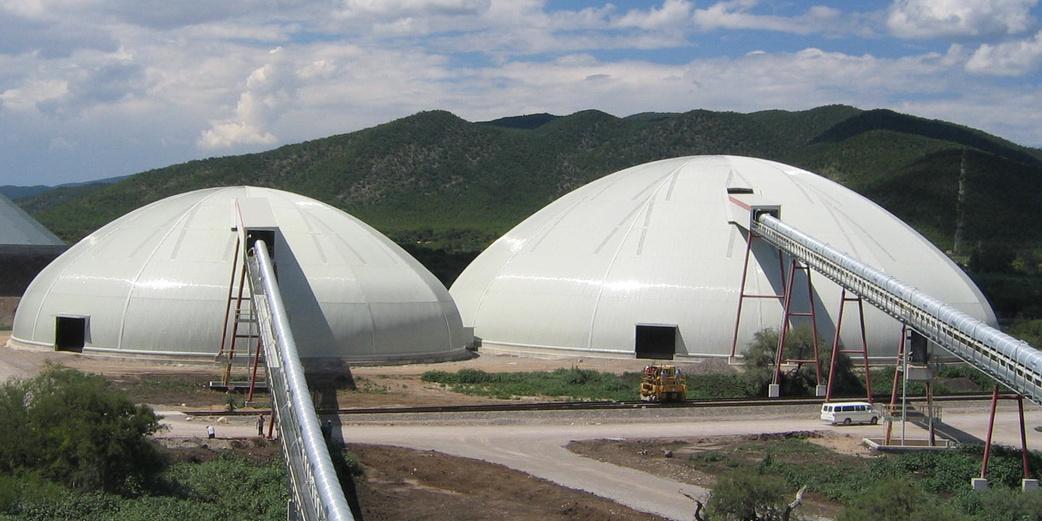
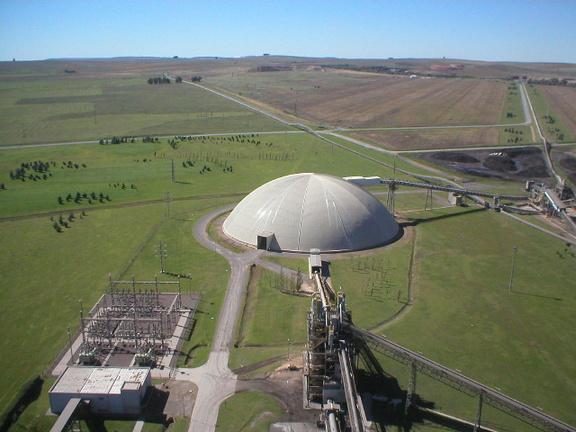
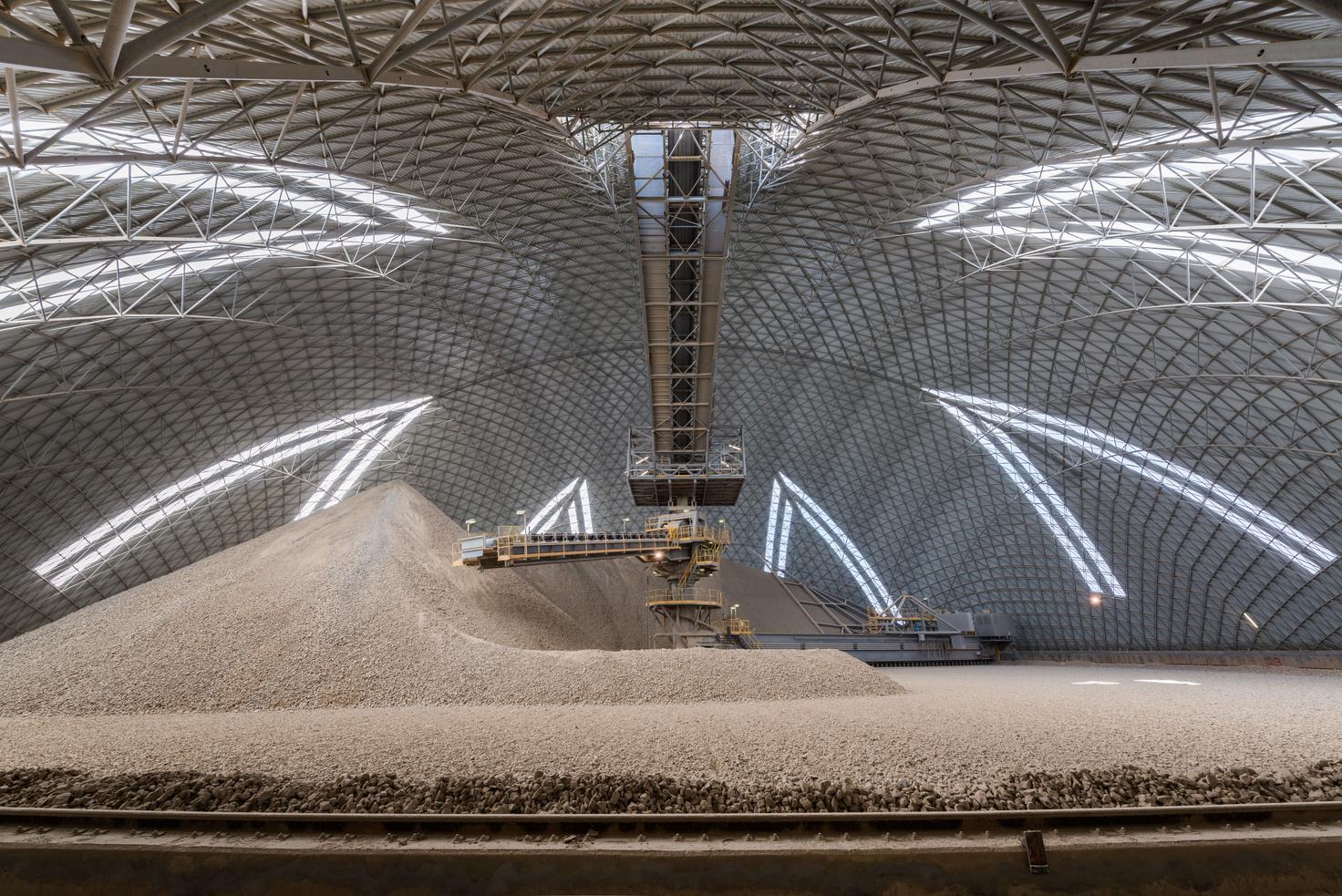
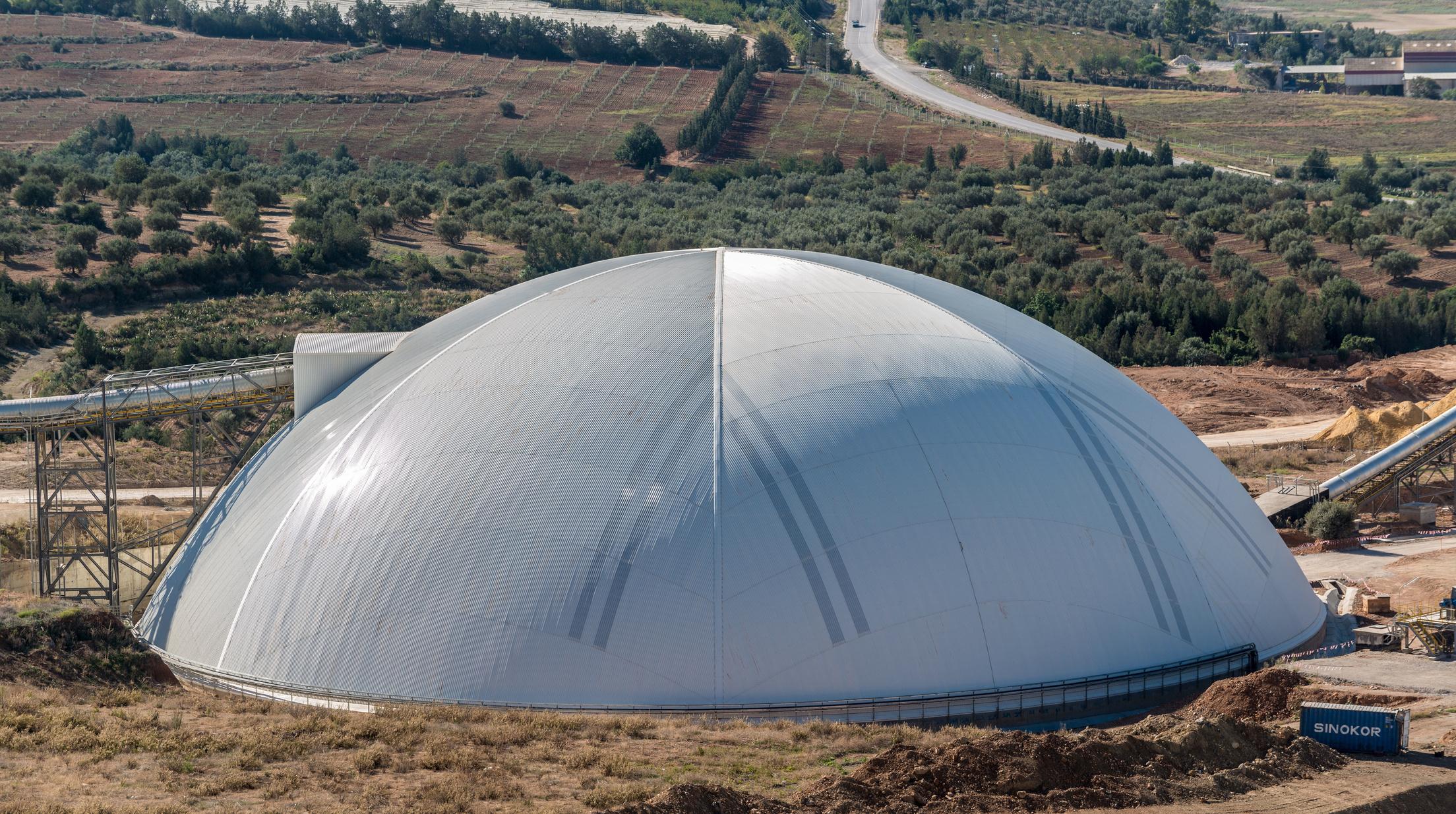

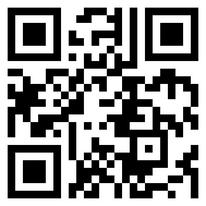