September 2023
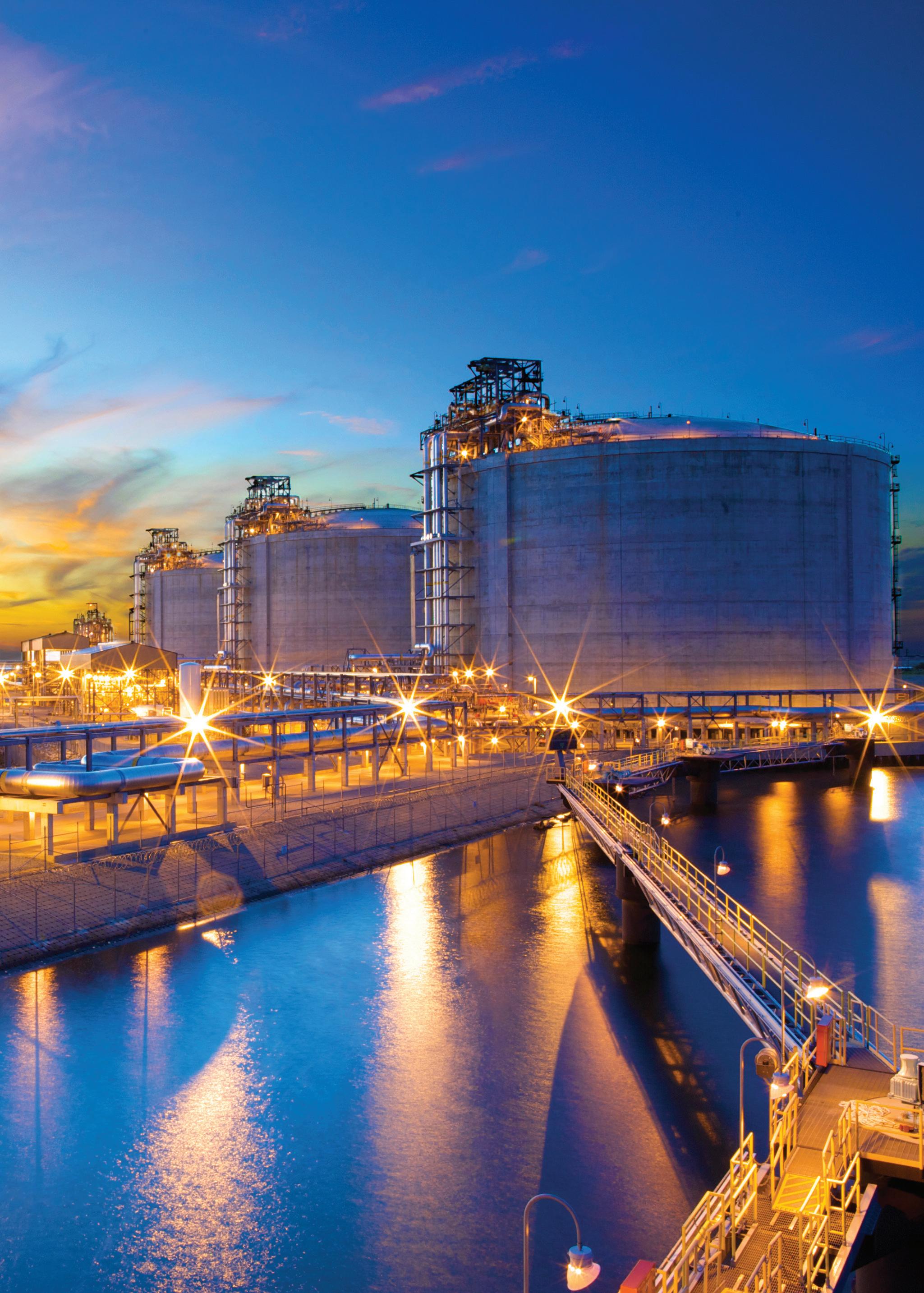
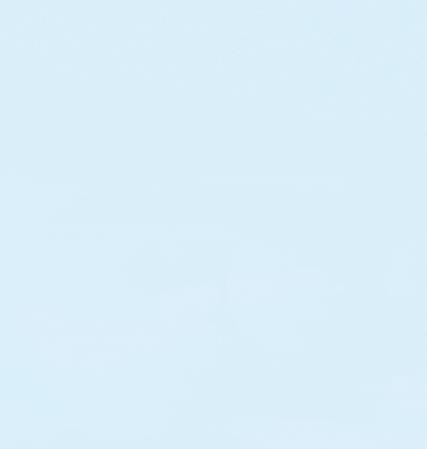
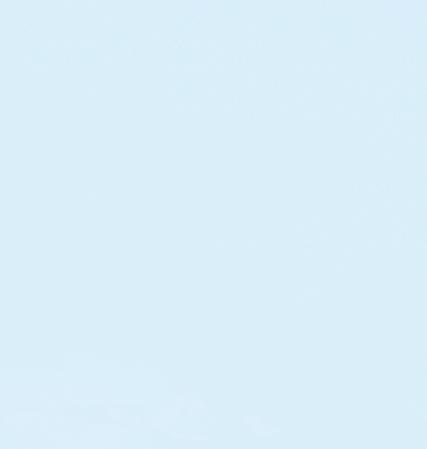
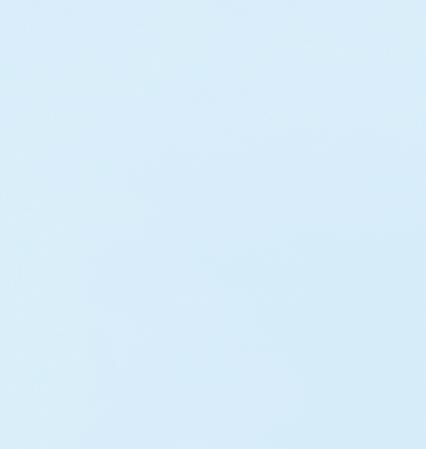
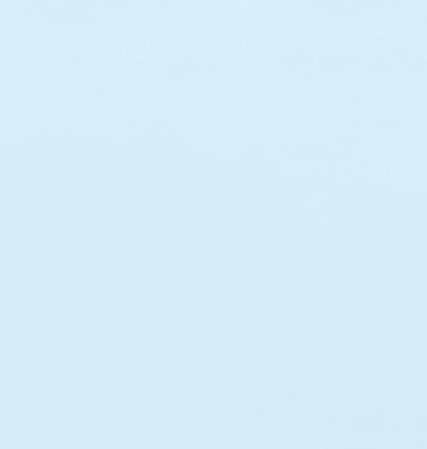
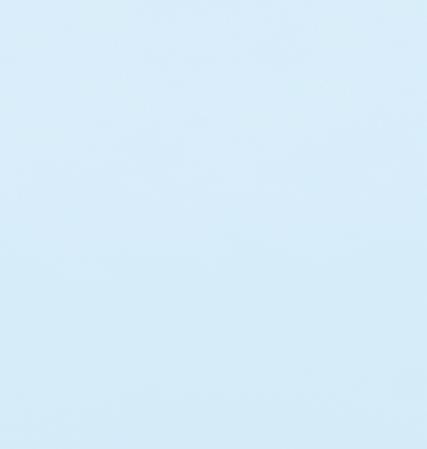
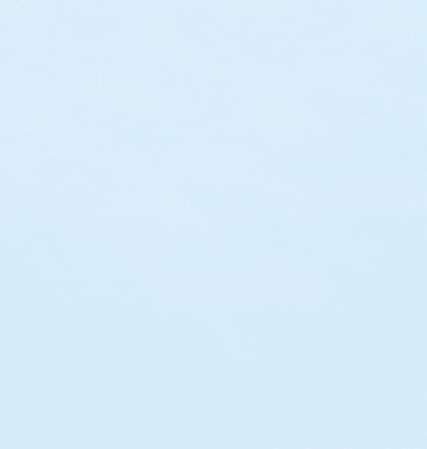
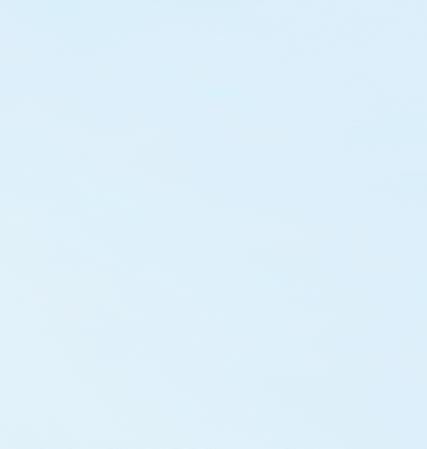
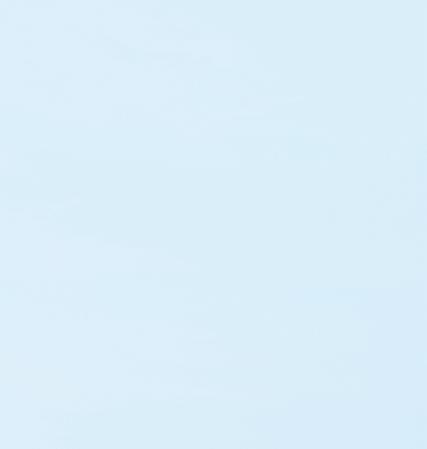
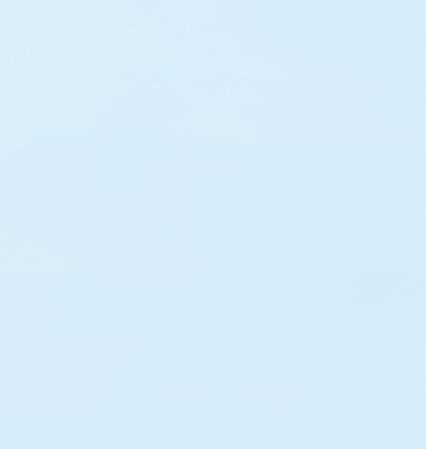
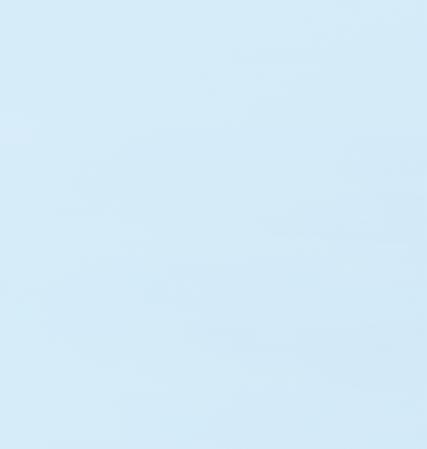
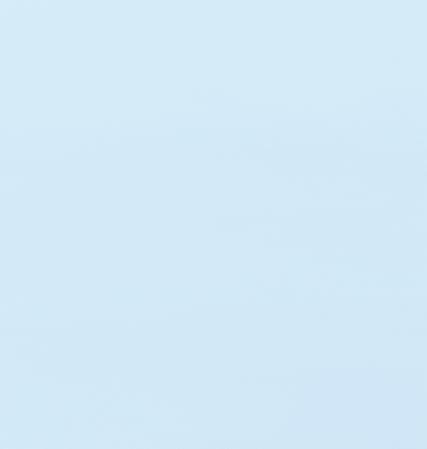
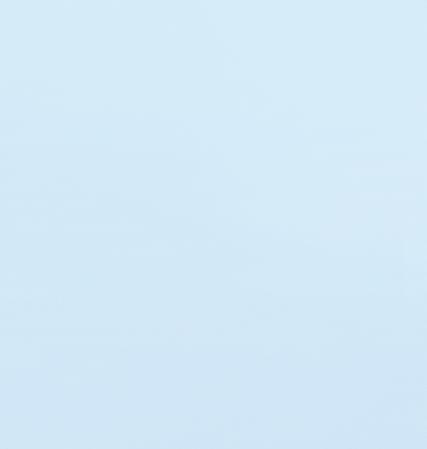
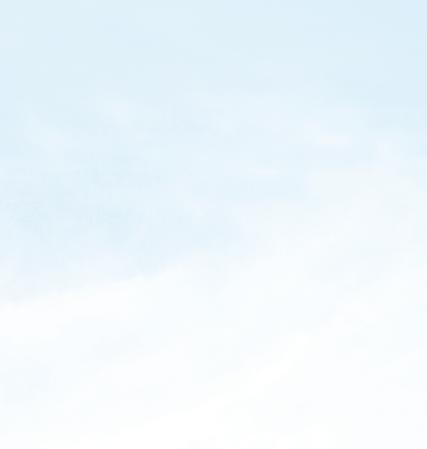
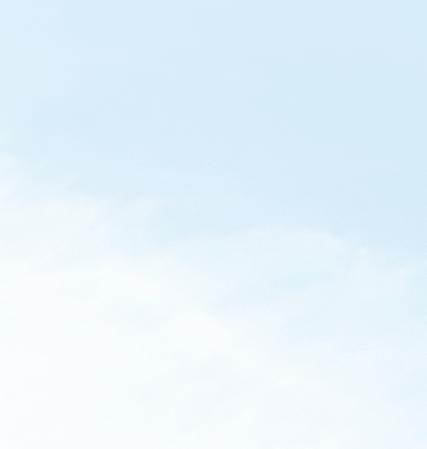
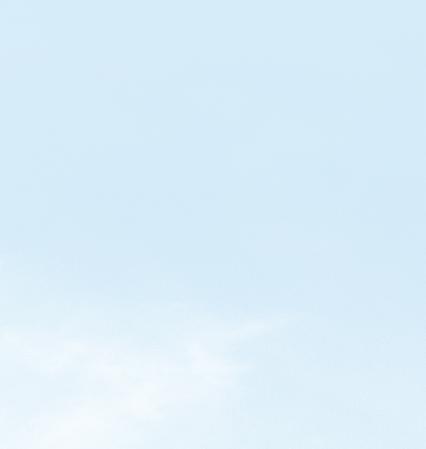
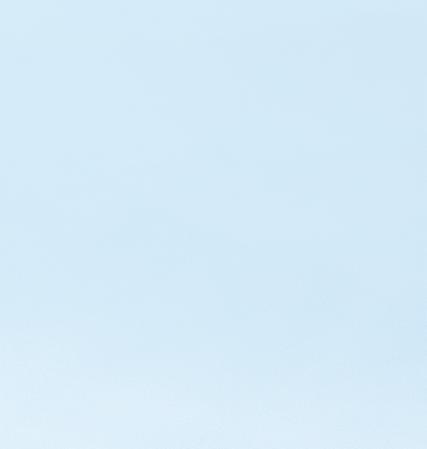
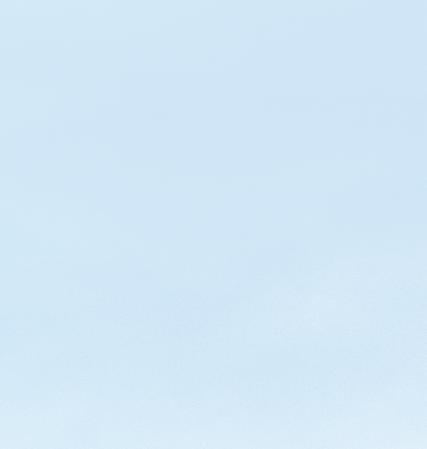
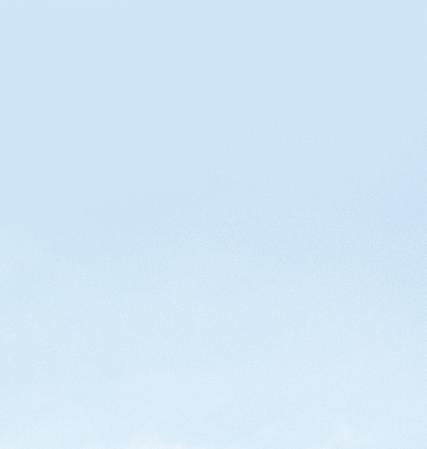
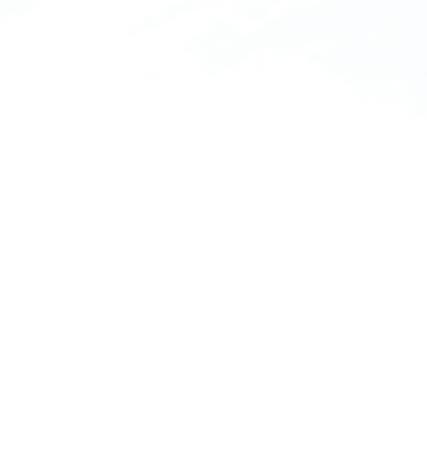
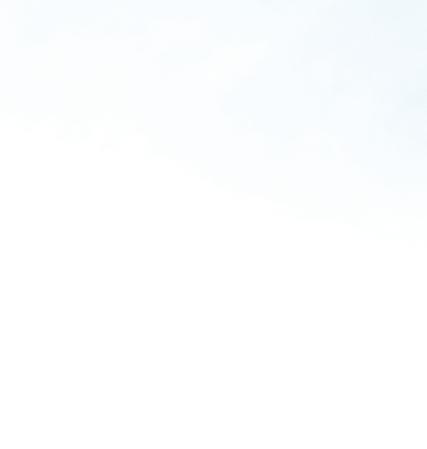
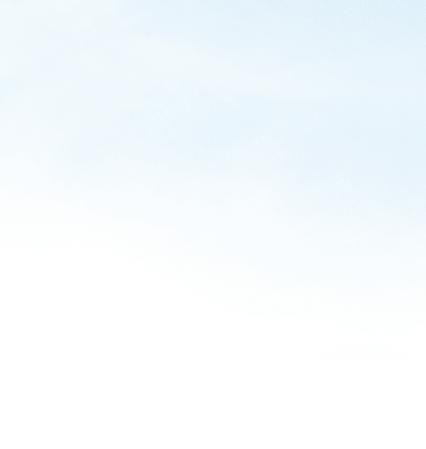
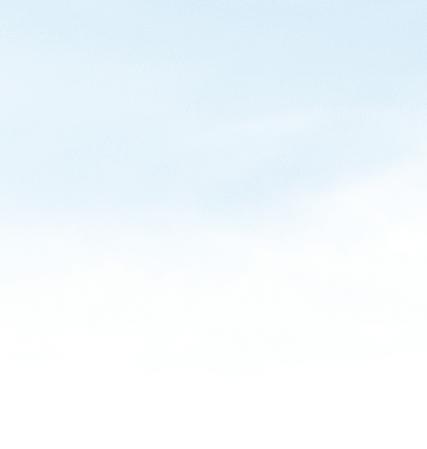
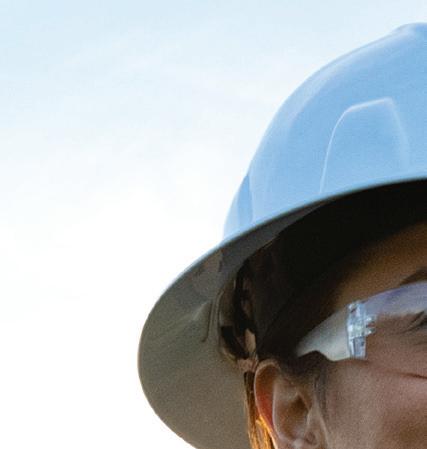
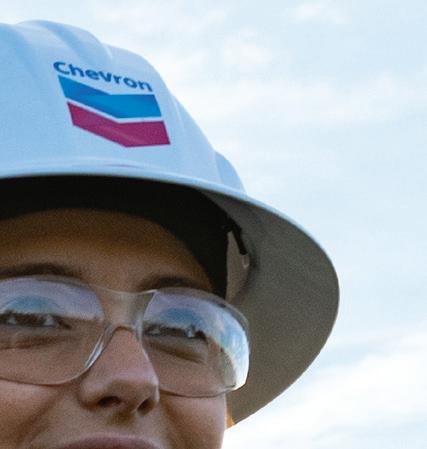
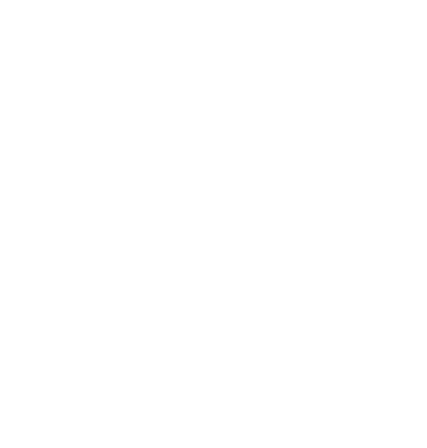
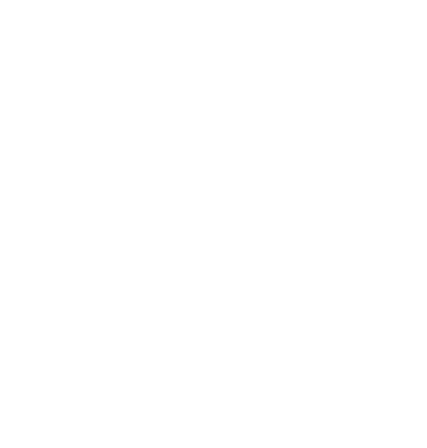
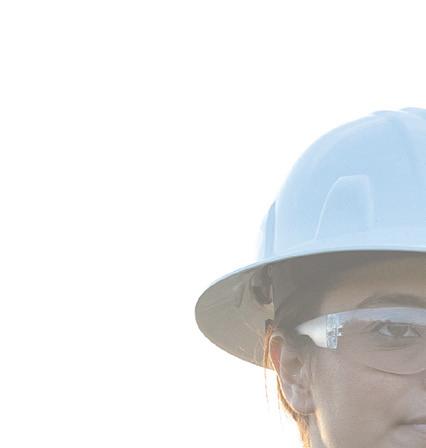
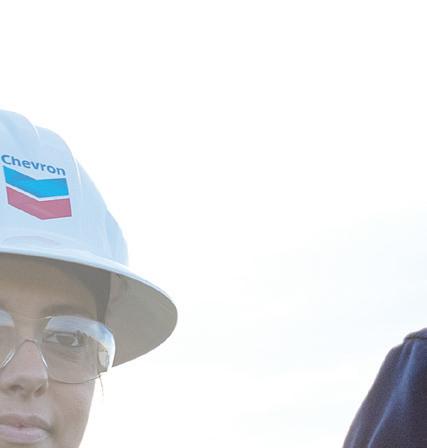
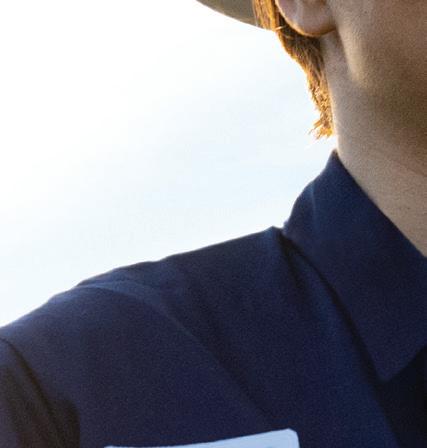
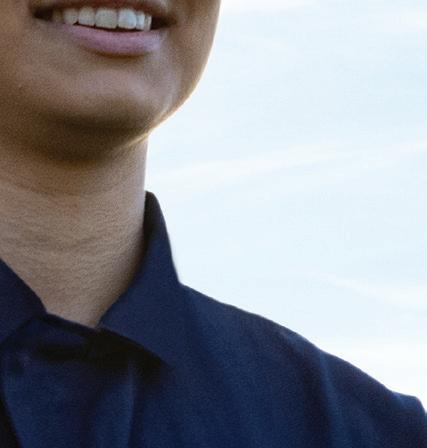
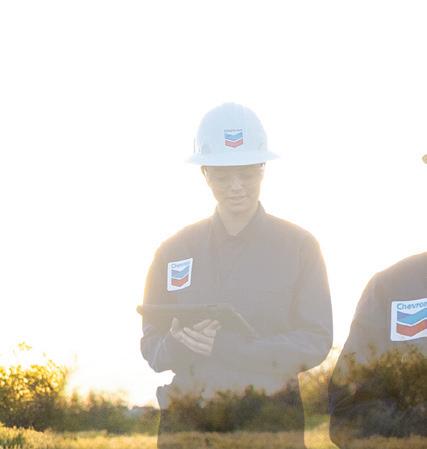
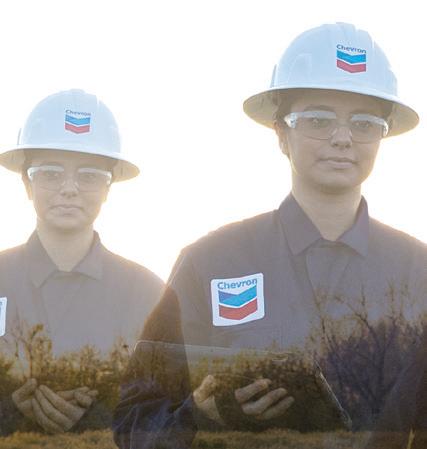
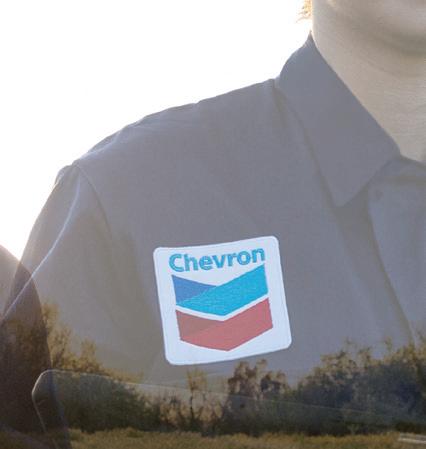
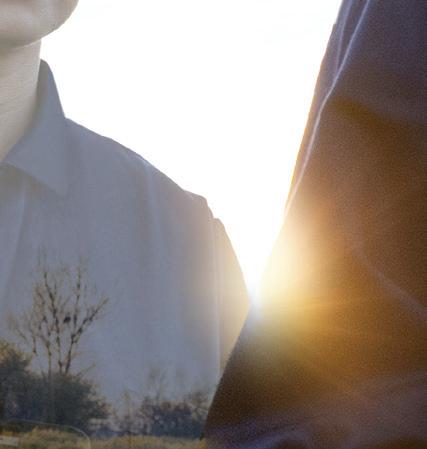
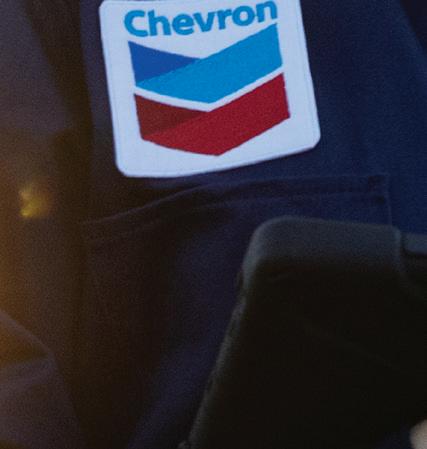
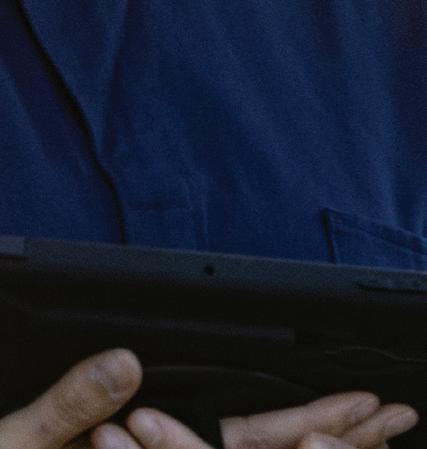
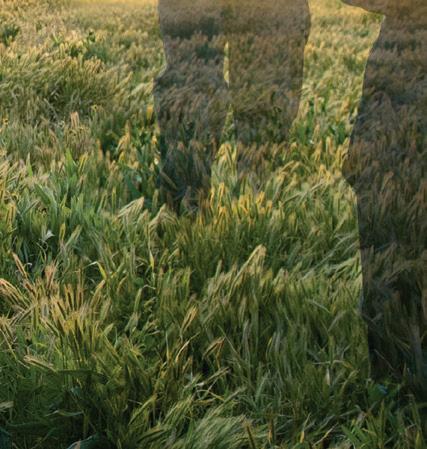
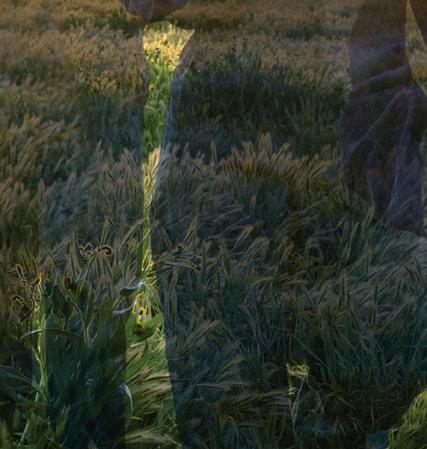
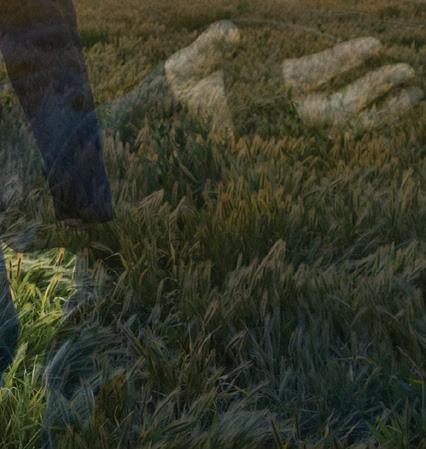
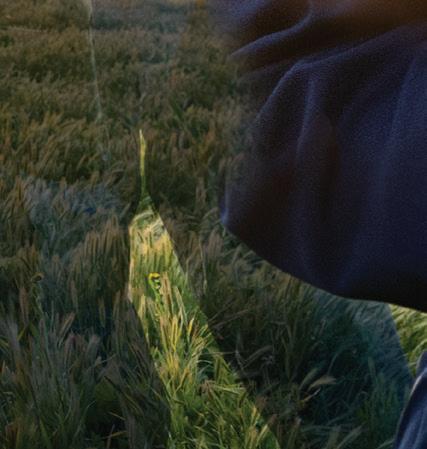
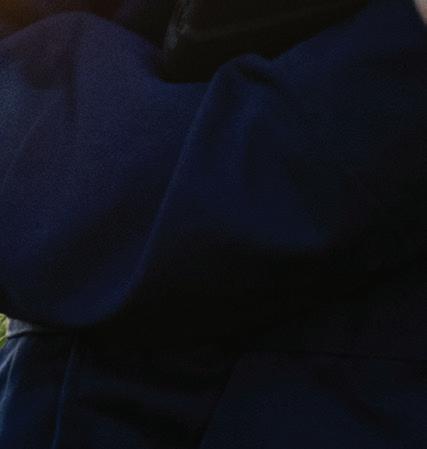
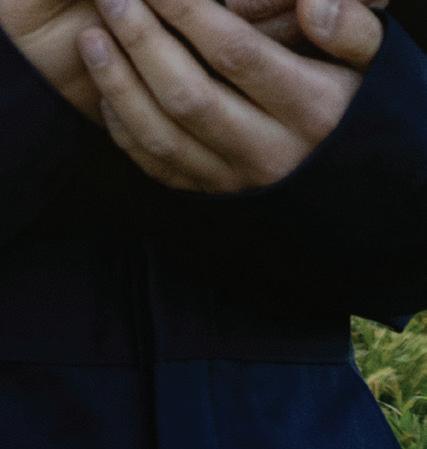
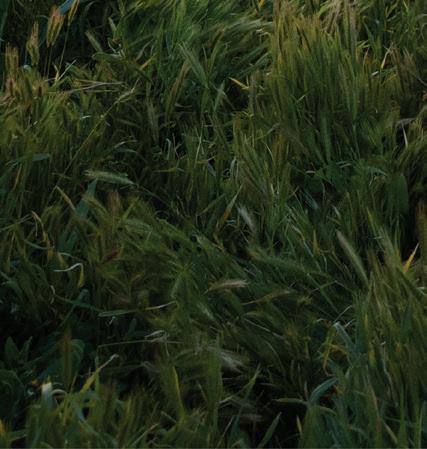
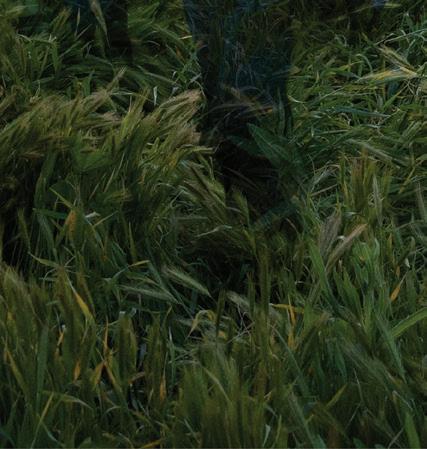
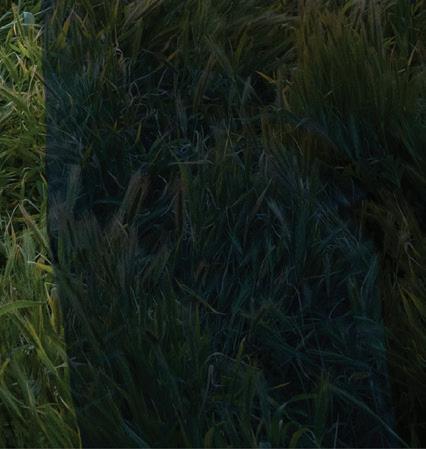
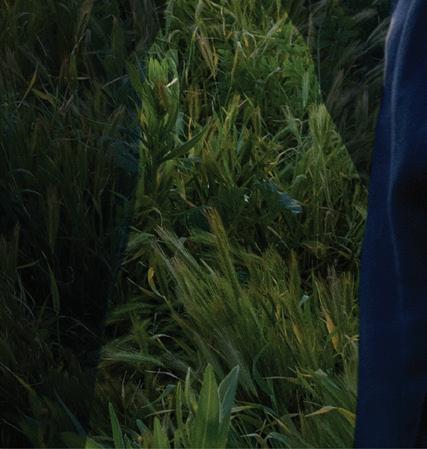
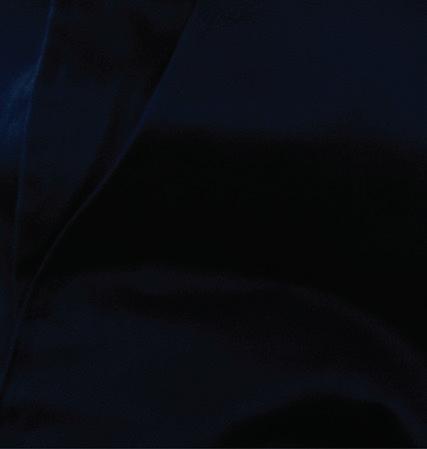
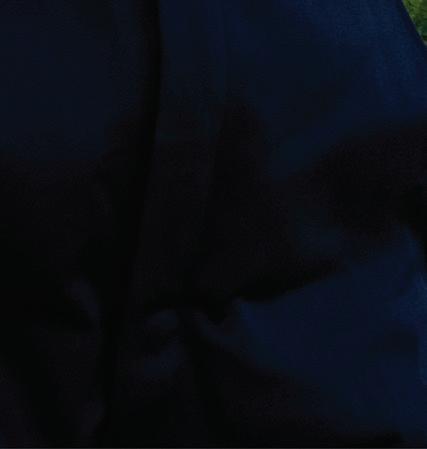
September 2023
03 Comment
04 LNG news
16 LNG contracting trends in 2023 –where to from here?
Jessica Ham, Special Counsel, and Jason Bennett, Partner, Baker Botts L.L.P., take stock of the LNG contracting trends from 1H23, and look ahead to where the road leads during the remainder of 2023 and into 2024.
20 How to fast-track an FSRU project
Andy Loose, Worley.
26 Building for the future of LNG Sempra Infrastructure.
29 Evolving LNG carriers
Carlos Guerrero, Bureau Veritas Marine & Offshore, France.
34 Making waves in Brazil
Serdar Kumbasar, Karpowership, Brazil.
39 Mercury absorbent's ability to air-load
Azuin Roslan, Mark Kent, and Ekaterina Novakova, Johnson Matthey.
46 Thermometers, assemble!
Dietmar Saecker, Endress+Hauser, Germany.
51 Resonating with in-tank density measurement
Joe Goodbread, PhD, and Sunil Kumar, PhD, Rheonics GmbH.
55 Dynamic metering: unlocking LNG’s potential
Mike Shepherd, Alderley, UK.
60 Measuring up
Steve Price, Programme Director for MAMII for Safetytech Accelerator, and Sunny Uberoi, Head of Public Affairs, MiQ.
65 Early fault detection of air-cooled heat exchanger
Mike Hastings, Brüel & Kjær Vibro, Denmark.
69 Navigating emissions in the maritime industry
Roar Hernes, Tunable, Norway.
SEPTEMBER 2023
74 The journey to autonomous operations in LNG
John Colpo, Marketing and Business Development Director, Honeywell.
81 Innovating for tomorrow
Bhupesh Thakkar, General Manager, LNG, Bechtel.
86 Methane emissions in LNG engines
Kati Lehtoranta, VTT, and Clémence Contant and Ciara Kristensen, REVOLVE.
93 Dual-fuelled solutions
Jonathan Blicher and Abdoulaye Diouf, GTT, France.
101 Gastech 2023 preview
LNG Industry previews a selection of companies that will be exhibiting at this year’s Gastech in Singapore from 5 – 8 September 2023.
113 Getting on the same level
Helena Hjortsberg, Manager of Solutions for Tank Gauging at Emerson, Sweden.
119 New trends in LNG storage
Jeff Garrison, Yogi Meher, and Mark Butts, CB&I.
124 Bio-LNG moving shipping along the pathway to net zero
Régine Portocarero, Global Business Development Marine LNG at Titan.
131 Preparing for the future
Johannes Dziuba, TGE Marine Gas Engineering, Germany.
Sempra Infrastructure’s LNG facilities and development projects on the Pacific and Gulf Coasts of North America serve the energy diversification and energy transition
Learn more at https://semprainfrastructure.com
September is that time again in the LNG industry calendar which sees industry experts from all around the globe come together to discuss business opportunities, new technology, and innovative ideas. It is, of course, time for Gastech, which this year is hosted by Singapore. Last year saw a record attendance of 39 467 international industry professionals, and the attendance for this year is expected to reach over 40 000.1
Asia is a growing market for the LNG industry, as much of the continent tries to move away from coal to less carbon intensive fossil fuels. Many projects on the West Coast of North America (including Alaska Gasline Development Corporation’s Alaska LNG 2 and Mexico Pacific’s Saguaro Energía 3 ) offer a competitive advantage over more distant alternatives due to their close proximity to Asia. This means they can serve the market quickly, free of any risks or time delays associated with the Panama Canal.
There have also been some recent developments in Singapore in regards to LNG. Maersk and Hong Lam Marine Pte Ltd have recently conducted the world’s first ship-to-container bio-LNG bunkering operation at the Raffles Reserved Anchorage in Singapore, with the support of the Maritime and Port Authority of Singapore. This was also Singapore’s first methanol bunkering operation. 4 As one of the biggest and busiest maritime ports in the world, this bunkering operation proves to be a significant milestone for the country’s development towards a multi-fuel future, and Singapore’s commitment to meet the new marine fuel needs of international shipping as the industry moves away from more traditional fuels to alternative fuels, such as LNG, bio-LNG, ammonia, hydrogen, etc.
In addition, Himalaya Shipping has recently bunkered
Managing Editor James Little james.little@palladianpublications.com
Senior Editor Elizabeth Corner elizabeth.corner@palladianpublications.com
Deputy Editor Jessica Casey jessica.casey@palladianpublications.com
Editorial Assistant
Théodore Reed-Martin theodore.reedmartin@palladianpublications.com
Sales Director Rod Hardy rod.hardy@palladianpublications.com
two of its ships, Mount Norefjell and Mount Matterhorn, with LNG in Singapore. A newcastlemax running on LNG helps reduce carbon emissions by 43% compared to a standard capesize ship 5 –something of importance considering the new, stricter environmental regulations that are being introduced in the shipping industry.
With COP28 approaching, and an ever-increasing spotlight on the environmental impacts of the oil and gas industry, Gastech 2023 will be looking at how industries can come together to make a positive, proactive contribution in the global fight against climate change. The 51 st edition will see a new addition: the Climatetech zone. The Climatetech zone will provide a showcase for existing climate technologies available for development at scale, as well as new and emerging technologies. 6
The LNG industry is still very much a topic of discussion, and its role in the future energy mix is becoming more prominent. With so much to discuss, the September 2023 issue of LNG Industry is, again, our largest issue to date. Make sure to visit our stand (E327) to discuss editorial and advertising opportunities for 2024, and to collect your bumper copy packed with articles on technology, LNG bunkering, metering and monitoring, LNG terminal design, and much more, as well as our Gastech 2023 Preview, which features a handy guide to help you navigate the event.
As the LNG industry continues to grow, change, and develop, the team here at LNG Industry will be with you every step of the way, keeping you informed and continuing to showcase and celebrate the work of key players in the industry through a range of insightful articles, news, webinars, and more.
References available upon request.
Sales Manager
Will Powell will.powell@palladianpublications.com
Production Manager
Calli Fabian calli.fabian@palladianpublications.com
Digital Events Manager
Louise Cameron louise.cameron@palladianpublications.com
Digital Events Coordinator Merili Jurivete merili.jurivete@palladianpublications.com
Digital Administrator
Leah Jones leah.jones@palladianpublications.com
Administration Manager
Laura White laura.white@palladianpublications.com
HD Hyundai is working with Korea's largest LNG carrier, Hyundai LNG Shipping, to validate eco-friendly and digital ship technology.
HD Hyundai has announced that its affiliates, HD Korea Shipbuilding & Marine Engineering, HD Hyundai Heavy Industries, and HD Hyundai Global Services, have signed a memorandum of understanding with Hyundai LNG Shipping to verify the performance of the Artificial Intelligence Cargo Management System (AI CHS) at the HD Hyundai Global R&D Centre in Pangyo, Gyeonggi-do.
AI CHS is a solution that predicts and manages LNG boil-off gas in real time by considering weather forecasts, wave height, etc. Under the agreement, Hyundai LNG Shipping's 174 000 m3 LNG carriers built by HD HHI will be equipped with the world's first AI CHS prototype. LNG carrier cargo holds are insulated to maintain cryogenic temperatures below -163˚C, but depending on the external environment, about 0.085% of the total LNG cargo per day spontaneously vaporises and produces evaporated gas. Until now, the amount of evaporated gas generated was predicted based on the outside temperature only, so there were limitations in accurate prediction.
HD's AI cargo operation system can identify routes with less evaporated gas in advance by considering various variables such as weather forecasts and wave height, providing shipowners with optimal operation scenarios. As a result, it is expected to contribute to reducing operating costs and reducing carbon emissions. The system will also be serviced through HD Hyundai Global Services' Integrated Smart Ship Solution.
Maersk and Hong Lam Marine Pte Ltd have successfully conducted the world’s (and Singapore's) first ship-to-containership methanol bunkering operation of a Maersk container vessel at the Raffles Reserved Anchorage in Singapore, with the support of the Maritime and Port Authority of Singapore (MPA), government agencies, and research institutes.
Maersk’s container vessel – the world’s first container vessel sailing on green methanol – was successfully refuelled with approximately 300 t of bio-LNG via Hong Lam Marine’s Singapore-registered tanker, MT Agility, for its onward maiden passage to Copenhagen. MT Agility had earlier taken bio-LNG stored at Vopak terminals. The container vessel will be named in a ceremony in September 2023.
In preparation for the bunkering operation in Singapore, MPA worked with over 28 agencies, partners, and institutes to organise table-top exercises and workshops, before carrying out a ground deployment exercise. A separate hazard identification and hazard and operability study workshop was conducted to identify potential risks and develop corresponding prevention, control, and mitigation methods.
During the methanol bunkering operation, researchers from the Cambridge Centre for Advanced Research and Education in Singapore flew drones equipped with methanol detector with plume modelling capabilities and infrared camera from MPA’s patrol craft MPA Guardian to augment the detection of potential methanol leaks into the atmosphere and methanol flames in an event of an accidental leak.
REV LNG, LLC and the Hamilton-Oshawa Port Authority (HOPA) recently provided LNG to the Fure Viten, a Furetank vessel under charter by Petro-Nav Desgagnés, and is the first European-owned vessel to receive LNG at Hamilton and represents more than 40 bunkering operations completed by Petro-Nav Desgagnés and REV LNG at HOPA since 2020.
In addition to the current Fure Viten charter, Desgagnés’
LNG-fuelled fleet includes five Canadian-flagged tankers all operating in the Great Lakes, St. Lawrence Seaway system, Eastern Canada, and the US, as well as the Canadian Arctic. Four of the five LNG-fuelled ships are sister ships designed and built by Desgagnés, while the Gaia Desgagnés, along with the Fure Viten and one additional chartered-in vessel, the Ramelia, are three sister ships designed and built by Furetank.
From Kenai first producing and importing LNG to Japan in 1969 to starting up 17 new large-scale LNG trains on-time in Australia and the U.S. Gulf Coast over the past eight years, the Optimized Cascade® process provides more than 110 million metric tons per year of the world’s LNG supply capacity and is licensed in 27 trains around the world.
• Industry-leading performance, efficiency, and operational flexibility
• Predictable execution, startup and operation
• Scalable train design from 1.5 to 7 MTPA
• Wide feed gas composition capability
The Optimized Cascade® process now provides more EPC Contractor choices for our clients
To learn more, visit lnglicensing.conocophillips.com.
Global container shipping leader, MSC, has joined the SEA-LNG coalition to support cross-industry collaboration and accelerate the use of net zero fuels at scale.
In recent years, MSC Mediterranean Shipping Company has made investments in LNG-fuelled vessels in the different sectors it operates within. For example, in the cruise sector, the company has launched MSC World Europa and MSC Euribia, whose maiden voyage was powered by bio-LNG.
As the world’s largest ocean carrier, MSC endeavours to be a steward of the world’s oceans and has invested substantially in ship design, cutting-edge technologies and digital applications to improve energy efficiency. The company continues to focus on improving energy efficiency and is taking actions today to properly support meeting its target of complete net decarbonisation by 2050.
MSC is actively exploring a range of alternative fuels and propulsion solutions that will help the business move even closer towards net zero. It sees cross-industry collaboration as crucial to scaling these solutions for the maritime industry, and is also an active partner and member of the Methane Abatement in Maritime Innovation Initiative (MAMII) and the Society for Gas as a Marine Fuel (SGMF).
Qingdao McDermott Wuchuan Offshore Engineering Co., Ltd (QMW) has officially commenced construction on the Woodfibre LNG Project.
The Woodfibre LNG Project is a Canadian investment by Pacific Energy, a clean energy development company, part of the Royal Golden Eagle Group. The project has a planned capacity of 2.1 million tpy of LNG and will be the world's first net-zero emission LNG project during both the construction and operation phases.
QMW undertakes the construction of 18 modules totalling 34 359 t. The scope of work includes module fabrication design, bulk material procurement, modules construction, mechanical completion, and pre-commissioning, weighing, loading-out, and sea-fastening. The project is scheduled for delivery in 3Q25.
the energy terminal operator, AB Klaipėdos Nafta (KN), has concluded the annual Klaipėda LNG terminal capacity allocation procedure, with the LNG terminal's 6 TWh regasification capacity for the 2024 terminal gas year allocated to four customers from Lithuania and Estonia.
In 2024, a total of about 34 TWh of natural gas is expected to be regasified, with cargoes to be delivered by 34 conventional LNG carriers. Most of the natural gas (24 TWh) will be delivered to customers from Lithuania, Latvia, and Poland, which booked long-term LNG terminal capacity last year. A further 4 TWh of capacity from the spot market will be allocated over the next year, based on the need to import natural gas to ensure the isolated operation of the electricity system and, in the absence of such a need, to meet natural gas demand on a case by case basis.
From the beginning of the year until 23 July 2023, the LNG terminal has received 20 large scale LNG carriers, and the same number of LNG carriers is planned to be received by the end of the year. During this period, 2.9 million m3 of LNG were delivered, with the majority (48%) coming from Norway. In 2023, natural gas was also imported from the US, Nigeria, and Algeria. About 37 TWh of natural gas is planned to be regasified at the Klaipėda LNG terminal this year.
X Tamboran awards Wood contract for NTLNG concept select
X Mexico Pacific concludes long-term SPAs with ConocoPhillips
X Nikkiso Clean Energy & Industrial Gases Group enters co-operation with NEA Brasil
Follow us on LinkedIn to read more about the articles www.linkedin.com/showcase/lngindustry
12 September 2023
WEBINAR – Singapore LNG Journey to the Cloud
Online
www.lngindustry.com/events/ webinar--singapore-lng-journey-to-the-cloud
25 – 28 September 2023
Turbomachinery & Pump Symposia 2023
Texas, USA
https://tps.tamu.edu
02 – 05 October 2023
ADIPEC 2023
Abu Dhabi, UAE
www.adipec.com
31 October – 03 November 2023
Americas Energy Summit & Exhibition 2023
Louisiana, USA
www.americasenergysummit.com
28 November – 01 December 2023
The 23rd World LNG Summit & Awards
Athens, Greece
www.worldlngsummit.com
11 – 12 March 2024
10th International LNG Congress (LNGCON 2024)
Milan, Italy
https://lngcongress.com
OLT Offshore LNG Toscana's auctions for the allocation of annual and multi-year capacity without expression of interest, from gas year (GY) 2027/2028 to gas year 2032/2033, ended 26 July 2023.
The regasification capacity was offered in slots of 155 000 liqcm, three slots were allocated for each GY starting from 2027/2028 until 2032/2033, for a total of 18 slots.
Therefore, in addition to 100% of the capacity already allocated up to GY 2026/2027, a total of 29% of the regasification capacity allocated in the GY 2027/2028 and 2028/2029, as well as 24% in the GY 2029/2030 to 2032/2033 is reached.
It is also recalled that the awardees in the GY 2032/2033 have the priority, no later than 30 September 2026, for purchasing capacity for the following GY (beyond the current useful life of the terminal), at the award price conditions and for the same number of slots.
The effective allocation of regasification capacity associated with the GY starting from 2033/2034 is subject to the actual decision of OLT to extend the useful life of the terminal that will be communicated to the requesting user by the end of the GY 2028/2029.
The European Commission has approved, under EU State aid rules, a €40 million German support measure for the construction and operation of a new land-based LNG terminal in Brunsbüttel.
Germany notified the Commission of its plans to support the construction and operation of a new LNG terminal located in Brunsbüttel, with an annual capacity of 10 billion m3. The terminal comprises import, storage, and distribution facilities, and it is planned to start operating by the end of 2026.
The beneficiaries of the measure are the German energy operator, RWE, and the Dutch energy network operator, Gasunie. German LNG Terminal GmbH (GLNG) will build and operate the LNG terminal. GLNG will have three shareholders: the German government through the investment and development bank KfW with a 50% stake, Gasunie with a 40% stake, and RWE with a 10% stake.
The amount of aid disbursed under the measure will depend on the annual returns but is expected to amount to €40 million. KfW plans to exit the project after 15 years of operation of the LNG terminal, when the preferential dividend distribution mechanism will stop.
The LNG terminal will be constructed taking into account the technical specifications necessary to allow its conversion into a terminal for the import of renewable energy carriers (e.g. renewable hydrogen or renewable hydrogen derivates), thereby avoid a lock-in of gas. The terminal will be converted after 15 years of operation, at the latest by 2043.
The Commission assessed the measure under EU State aid rules, in particular Article 107 (3)(c) of the Treaty on the Functioning of the European Union, which enables Member States to support the development of certain economic activities subject to certain conditions, and the 2022 Guidelines on State aid for climate, environmental protection, and energy.
Chart’s LNG power generation solutions provide natural gas to hundreds of thousands of homes. This is one way Chart facilitates LNG as a safe, clean-burning fuel for energy, transportation and industry.
As a significant part of PetroVietnam GAS' (PV Gas) production and business plan for 2023, the operations and maintenance (O&M) of Cuu Long, Nam Con Son 2, and PM3 Ca Mau pipelines, and the commissioning of its LNG value chain consisting of Thi Vai LNG Terminal, Thi Vai – Phu My LNG pipeline, low-pressure gas distribution station, and truck loading station hold paramount importance to ensure the national energy security and expand development opportunities for Vietnam’s gas industry.
In celebrating the 33rd anniversary of PV GAS’ establishment, the company and its units, Labour Unions and Youth Unions, have launched a movement stimulating ‘Implementing quality and on-schedule maintenance and commissioning of the LNG value chain’. They are committed to completing 100% of the tasks within the designated timeline, and making sure pipelines are capable of receiving gas immediately once suppliers resume supply, as well as on-time LNG commissioning process completion with absolute safety.
PV GAS and its units are collaborating with the authorities to have logistical support and actively taking care of the participants in the O&M and commissioning, helping them come up with initiatives and solutions, overcome obstacles, and efficiently accomplish assigned tasks with standardised quality. They have guaranteed that all union members will comply with the regulations on Occupational Safety and Health, Fire and Explosion Control, and Disease Prevention. The participants are aiming to complete the O&M and commissioning in 2023.
The Norwegian government has approved the Snøhvit partners' plans for the future operation of Snøhvit and Hammerfest LNG, subject to certain conditions. The approval entails onshore compression from 2028, and electrification of the plant from 2030.
Compared to the partnership's application, the authorities have postponed the start of electrification by two years, from 2028 to 2030. The plant will continue to run on gas turbines during this period. The approval opens for maintaining the gas turbines for back-up power from 2030 to 2033. The need for this will be assessed by 2028 at the latest.
Electrification of Hammerfest LNG will replace today's gas turbines with electricity from the grid. This reduces carbon dioxide emissions from the plant by around 850 000 tpy. This is the most substantial individual emission reduction decision that has been made aimed at decarbonising oil and gas production in Norway. The project is an important contribution towards the energy transition.
The Snøhvit partners are investing NOK 13.2 billion (2022) in the Snøhvit Future project.
The approval of Snøhvit Future ensures continued operation on Melkøya. Today, 350 permanent employees and 150 contractors and apprentices work at the plant, and the ripple effects in Northern Norway have been documented by Bodø Science Park at almost 900 person-years of employment.
The Snøhvit Future project triggers an increased need for power and a strengthened grid. The government has also approved Statnett's licence application for a power cable (420 kV) between Skaidi and Hyggevatn, and Equinor's licence application for a power cable (132 kV) between Hyggevatn and Melkøya.
Air Products, has signed agreements with Bechtel Energy Inc. to supply its proprietary LNG process technology and equipment to NextDecade’s Rio Grande LNG Phase 1 Project in the Port of Brownsville, Texas. The project will include three natural gas liquefaction trains employing Air Products’ liquefaction equipment with a production capability of approximately
17.6 million tpy of LNG.
Air Products’ coil-wound heat exchangers (CWHEs) and AP-C3MRTM LNG Process technology have been selected for their proven reliability for large scale LNG production. The CWHEs will be manufactured at Air Products’ LNG equipment manufacturing facility in Port Manatee, Florida.
In mid-July, leaders from the global LNG industry visited Vancouver to discuss the future of the industry at the LNG 2023 conference. Countries such as South Korea and Japan are seeking Canada’s lower-carbon and secure LNG sources. Coastal GasLink, together with LNG Canada, will provide the first direct path for Canadian LNG to reach the nation’s allies and replace coal-fired power plants.
Coastal Gaslink have installed 630 km of the planned 670 km LNG pipeline in Canada. Crews are busy completing distinct work fronts such as water crossings and steep slopes. To date, more than 92% of all classified water crossings are complete, and steep slope areas such as Cable Crane Hill and the Raised Bore, continue to make significant strides forward.
Fulkrum, a leading provider of inspection, expediting, auditing, and technical staffing services, has been awarded a seven-figure contract for the provision of third-party inspection services on Sempra Infrastructure’s Port Arthur LNG (PALNG) Phase 1 project in Port Arthur, Texas, the US.
The PALNG project is a pioneering initiative in the field of natural gas liquefaction, set to transform the energy landscape in the US. Fulkrum's selection as the third-party inspection agency on this landmark project is a testament to the company's unrivalled expertise and track record in delivering high-quality inspection services.
Under the terms of the agreement, Fulkrum, has received an initial order from Sempra Infrastructure, valued at US$1 million. This initial purchase order covers services to be rendered through to the end of 2023, and the total contract value to Fulkrum is estimated to be just under US$5 million for the duration of the project.
In a major step towards bolstering Nigeria's energy security and promoting the utilisation of its abundant gas resources, the NNPC Ltd and UTM Offshore Limited have signed a heads of terms agreement for the construction of Nigeria’s first indigenous floating LNG (FLNG) project.
Describing the FLNG project as a "must-do" initiative for Nigeria, the NNPC Ltd Group CEO, Mele Kyari, OFR, expressed the company’s readiness to secure gas feedstock towards the project.
The Group Managing Director, UTM Offshore Ltd, Julius Rone, explained that apart from significantly cutting down on gas flaring and supporting the country's commitment to reducing carbon emissions, the project would also create over 7000 job opportunities, contributing to the nation's economic growth and development.
In his remarks, NNPC Ltd’s Executive Vice President, Gas, Power & New Energy, Mohammed Abdulkabir Ahmed, said the project aligned perfectly with NNPC Ltd’s goals of ensuring energy availability, affordability, and sustainability while also generating revenue through exports.
X Nesma & Partners Contracting Company Ltd acquires Kent
X JERA begins commercial operation at Anegasaki Thermal Power Station New Unit 3
X Himalaya Shipping Ltd commences LNG bunkering
Follow us on LinkedIn to read more about the articles www.linkedin.com/showcase/lngindustry
Sometimes the things you can’t see make all the difference. Our integrated team of consultants, engineers, technicians, and construction professionals leverage our extensive history and expertise in mid-scale LNG technology and pioneering work in FLNG EPC to seamlessly bring our modular designs to life. Our modular LNG solutions enable fast-to-market results, so you can arrive at your destination on your terms, regardless of the technology, processes, or path.
The invaluable difference:
• Minimize interfaces and reduce prolonged onsite installation time and manpower
• Flexibility in compressor driver selection, cooling medium, and capacity from 1–2 MTPA per train
• Utilize the same modular philosophy for gas treating, heavies removal, product and boil-off handling
• Complete modular solutions for onshore and offshore applications between the pipeline and storage tank
Woodside has established a strategic relationship with LNG Japan, which involves three elements: equity in the Scarborough joint venture (JV), potential LNG offtake, and collaboration on opportunities in new energy.
Woodside has entered into a sale and purchase agreement with LJ Scarborough Pty Ltd (LNG Japan) for the sale of a 10% non-operating participating interest in the Scarborough JV (the transaction).
The purchase price is US$500 million, subject to adjustments. LNG Japan will reimburse Woodside for its share of expenditure for the Scarborough project from the transaction effective date of 1 January 2022. On completion of the transaction, expected in 1Q24, the estimated total consideration comprising the purchase price, reimbursed expenditure and escalation is approximately US$880 million.
Completion of the transaction is subject to conditions precedent, including: Foreign Investment Review Board approval, National Offshore Petroleum Titles Administrator approvals, and Western Australian Government approvals.
As part of the broader strategic relationship, Woodside and LNG Japan Corporation have entered into a non-binding heads of agreement for the sale and purchase of 12 LNG cargoes per year (approximately 0.9 million tpy) for 10 years commencing in 2026.
Woodside has also entered into non-binding agreements to collaborate with Sumitomo Corporation and Sojitz Corporation on global opportunities in new energy which could include ammonia, hydrogen, carbon capture and storage (CCS), and carbon management technology. Following completion, Woodside will hold a 90% interest in the Scarborough JV and remain as operator. Scarborough gas will be processed at the Pluto LNG facility, where Woodside is currently constructing Pluto Train 2. Woodside is also operator of the Pluto Train 2 JV and holds a 51% participating interest.
The European Commission has recently signed a joint statement alongside global partners, which reinforces continued efforts towards the reduction of methane emissions arising across the value chain of LNG, from production to consumption. The joint statement was signed by the European Commission, Japan, the US, the Republic of Korea, and Australia in Tokyo at the LNG Producer-Consumer conference, co-organised by Japan and the International Energy Agency’s (IEA) Task Force on gas and clean fuels market monitoring and supply security (TFFS). Commissioner for Energy, Kadri Simson, was represented by Ditte Juul Jørgensen, Director-General for Energy at the European Commission.
This initiative builds on already strong co-operation between the EU and other global leaders on methane abatement across the natural gas value chain. The EU continues to be a global leader in tackling methane emissions, spearheading the Global Methane Pledge and the Joint Declaration from Energy Importers and Exporters on Reducing Greenhouse Gas Emissions from Fossil Fuels alongside the US, while implementing the EU Methane Strategy at the EU level. Fulfilling its commitments at both EU and international levels, the EU continues to play a prominent role globally in methane emissions monitoring, reporting and verification (MRV) and methane emissions abatement.
The European Commission has reaffirmed its commitment to taking action on reducing methane emissions in the LNG supply chain on a number of fronts, including through:
• Continued collaboration with global partners as well as the IEA, the International Methane Emissions Observatory, and the Greenhouse Gases Supply Chain Emissions MMRV international working group.
• The creation of a globally aligned methane emissions assessment framework for LNG projects.
• Continued support for international public-private coordination on GHG reduction in LNG, especially on methane, and to work with LNG producers and consumers globally.
Following on from a busy 1H23, this article will consider the LNG contracting trends seen so far in 2023, and look ahead to where the road leads during the remainder of 2023 and into 2024. Energy security, managing the cascading effects of price volatility, expanded but changing sources of US LNG, and continued decarbonisation efforts remain key themes.
Energy security remains a key focus globally, and Baker Botts expects that this will continue for the remainder of 2023 (and well into the future). The Russian invasion of Ukraine and the ongoing conflict brought the issue of energy security and diversity of gas supplies into sharp focus, and has resulted in significant change to the European energy markets in particular, which raced to procure LNG (and develop additional import infrastructure) to replace piped natural gas from Russia. Realignment of global supply chains along political lines, with Russia and China being sidelined in various industries by OECD countries, has heightened concerns around energy security in the short and long term. The flow on effects of changes to European gas markets rippled across the globe, as developing and price-sensitive LNG import markets felt the impact of the resulting price shocks and cut back on gas supplies.
For buyers, this has meant an increased focus on getting the balance right in terms of the diversity of their supply portfolio and on the stability of supply arrangements, as well as on seller shortfall liability under LNG sale and purchase agreements (SPA). Particularly as spot prices have outpaced term LNG prices over recent years, there have been arbitrage opportunities for sellers (particularly ex-ship sellers), and the cost to a buyer of procuring a quantity of replacement LNG has often exceeded the seller’s liability arising as a result of the shortfall (which is typically capped for ex-ship sales). Other flexibility provisions, such as diversion and quantity flexibility (UQT/DQT) clauses, have also been under the microscope. Unsurprisingly, sanctions and trade restrictions clauses have also been a focus as the conflict escalated and buyers have focused even more closely on the potential for geopolitical conflict to interrupt energy supplies.
2022 saw record high spot prices as JKM (the Japan-Korea Marker, the spot benchmark for North Asia) reached record highs (averaging approximately US$33.9789/million Btu for the
and Jason Bennett, Partner, Baker Botts L.L.P., take stock of the LNG contracting trends from 1H23, and look ahead to where the road leads during the remainder of 2023 and into 2024.
calendar year),1 as well as extreme price volatility that has continued into 2023.
While price volatility is expected to continue in the near term, prices have swung in the opposite direction over recent months, with JKM dropping to two-year lows of less than US$9.00/million Btu (at the time of writing). This price movement has encouraged some price-sensitive buyers to return to the market, in some cases reversing their previous switch to lower cost fuels during the high prices of 2021 and 2022. In particular, some buyers from South and South-East Asia have re-emerged after withdrawing from the spot market during the highest price periods of 2022 and are seeking cargoes for the first time in months. For example, 1H23 has seen Bangladesh seek spot cargoes for the first time in eight months in January 2023, and further cargoes in the following months.
Price volatility has caused FOB buyers to re-consider the arbitrage against Henry Hub for US cargoes, at least in part, as buyers have begun to seek TTF and JKM-linked LNG supplies from the US again. While Baker Botts sees no definitive trend away from the long-term trend of US cargoes priced based on an escalating fee, plus Henry Hub pricing for gas, extreme volatility has caused buyers to seek alignment of some portion of their US portfolio with TTF and JKM, and American gas suppliers seem inclined to consider accepting a form of netback payment, if properly structured.
Extreme price volatility has also contributed to a re-think of contracting strategies that rely heavily on spot LNG procurement. Despite briefly falling out of favour with some buyers (prior to the COVID-19 pandemic in particular), term LNG procurement has been rebounding from 2021 onwards (with data from the International Group of LNG Importers [GIIGNL]’s 2022 annual report showing that ‘long-term’ sale and purchase agreements represented almost 64% of the total volume of LNG sales contracted in 2021).
Baker Botts’ experience shows that this trend has continued through 2022 and 2023, as the views of many buyers on the benefits of a flexible procurement strategy with significant exposure to the spot market have been reframed in light of the Ukraine/Russia conflict and due to the resulting energy market shocks and extreme price volatility, with many LNG buyers now seeing the relative rigidity of mid and long-term supply through the lens of security and stability of both supply and pricing. This is also reflective of the supply available, as LNG project
developments are principally marketed on a term basis to underpin financing and support final investment decisions.
One such example is India. Although currently one of the world’s largest importers of LNG, India’s procurement strategy to date has included a significant reliance on spot LNG purchases to secure baseload and seasonal supplies. Many analysts expect that this will need to change, in order to ensure access to longer-term LNG and natural gas supplies to support India’s growing energy needs. Chinese buyers also appear to be favouring entry into additional LNG purchases under long-term supply agreements, despite the sharp drop in China’s LNG imports in 2022 due to COVID-19 lock-downs. China is buying more LNG on a term basis as it seeks supply stability, including Sinopec entering into a 27 year, 4 million tpy supply arrangement with Qatar late in 2022 and other Chinese entities repeatedly following suit during 2023.
With the launch of Sempra Infrastructure Partners’ Port Arthur LNG Phase 1 and Venture Global’s Calcasieu Pass LNG Phase 1 and Plaquemines LNG, as well as the rapid development of expansion projects for both companies, the continued development of Driftwood LNG, the progress made by FLNG projects in the Gulf of Mexico, and the recent announcement of TotalEnergies’ investment into Rio Grande LNG, US LNG appears to remain the hottest area for LNG liquefaction project development, but not the only one. European direct buyers, aggregators and trading houses have led the way in supporting the offtake required for development of those projects in 2022 and 2023, and this trend is expected to continue.
LNG demand in emerging markets in Asia fell during 2022. However, as prices swing back in favour of buyers, price-sensitive demand in Asia is rising. More activity from Asian buyers is being seen, including in South East Asia. While Chinese LNG imports dropped in 2022, demand appears to be rebounding in 2023 as China recovers from the effects of the COVID-19 pandemic and returns to ‘business as usual’ following the end of its zero-COVID policy. There are already a number of Chinese buyers in the market securing long-term supplies, but not from the US.
There have also been new markets coming online in 2023, demonstrating the potential for further growth in South-East Asia. The Philippines has imported its first LNG shipment (at AG&P’s Philippines LNG terminal), and PetroVietnam has procured a
commissioning cargo for its Thi Vai LNG terminal in Vietnam. Vietnam has also released the long-awaited Power Development Plan 8, which supports a significantly increased role for LNG in the country’s energy mix going forward (growing to almost 15% of the country’s energy mix by the end of the decade).
In 2022, Europe invested heavily in the fast-tracked development of new LNG import terminals (particularly in Germany and the Netherlands, as well as Italy and France), to dramatically increase in its capacity to import LNG and allow for diversification of its energy mix and replacement of Russian piped natural gas (according to Shell’s LNG Outlook 2023, European LNG imports increased by 60% in 2022). As much of this infrastructure was developed using FSRU solutions, the result of such activity is an extremely tight market for LNG vessels and FSRUs (both new-build and conversions) for the next 2 – 3 years.
Despite energy security concerns and market volatility over the last 12 months, the industry focus on emissions reduction and decarbonisation of the value chain has remained, but price shocks and the supply/demand gap has meant that a number of major economies also increased their use of less-clean fuels, particularly coal. If LNG prices remain at lower levels, this could encourage greater fuel switching back to LNG in cost-sensitive economies, with corresponding emissions impacts.
Natural gas remains a critical component of the energy transition, and efforts to decarbonise the LNG industry through measures such as methane leak reduction and carbon capture and storage continue, and are increasingly being encouraged or required through government policy. For example,
Indonesia recently issued regulations intended to encourage and support the installation of carbon capture utilisation and storage (CCUS) facilities in connection with upstream exploration and production activities in the country. The Inflation Reduction Act has also provided strong support for the development of low-carbon energy infrastructure in the US, including by subsidising the cost of developing CCUS facilities to support reduced emissions targets.
Monitoring greenhouse gas emissions associated with cargoes of LNG sold and purchased has also become more common, and the ability to provide this data to buyers (and, in some cases, to offset or mitigate the associated greenhouse gas emissions) has become a selling point, in light of growing government and corporate commitments to decarbonisation efforts. In 1H23, the first ‘carbon neutral’ cargo to be delivered using GIIGNL’s Monitoring, Reporting and Verification and Greenhouse Gas Neutral Framework (published in 2021) was delivered (by Shell, sourced from the Gorgon LNG plant and delivered to Taiwan for CPC). Baker Botts expects this trend to continue, despite the apparent pressures of energy security across the globe.
Baker Botts expects an active LNG sales and trading market to continue for the remainder of 2023, and throughout 2024.
1. KIM, M., SAHU., S., YEP, E., and DUTTA, R., ‘Weakening LNG prices spur renewed spot demand in South Asia’, S&P Global Commodity Insights, (16 February 2023), www.spglobal.com/commodityinsights/en/market-insights/ latest-news/lng/021623-weakening-lng-prices-spur-renewedspot-demand-in-south-asia
In the year preceding Russia’s invasion of Ukraine, Germany sourced over half of its natural gas supply from Russia. But as the conflict escalated in February 2022, Germany set in motion a plan to eliminate its dependence on Russian natural gas.
The task was twofold. Germany had to find sufficient alternative supplies of natural gas to power millions of homes, businesses, and manufacturing facilities. And they had to establish the infrastructure to access these alternative supplies for the winter of 2022 – 2023, when demand for heating and power was expected to peak.
This triggered an urgent effort to build the infrastructure to import billions of cubic metres of natural gas in a timeframe few thought possible.
Germany is well-connected to other gas-supplying countries on the European mainland. That is why it previously received natural gas through pipelines, such as the Nord Stream network that runs beneath the Baltic Sea from Russia.
To replace its natural gas imports from Russia, which added up to tens of billions of cubic metres each year, Germany needed to import large volumes of natural gas in a different way.
The German government acted quickly to charter five FSRUs to meet this challenge. These floating units – to be positioned across Germany’s northern coastline – would be able to receive LNG from cargo ships and feed it into local gas grids. This meant
natural gas deliveries could arrive in Germany from anywhere in the world, rather than just by pipeline from the European mainland.
The primary challenge, given an available FSRU, was to design and construct the marine and land infrastructure required to send gas into the grid for winter 2022 – 2023.
There are two key reasons why FSRUs were well-suited to Germany’s energy security challenge: speed and flexibility.
FSRUs are moored to a marine berth, where they transfer LNG from an LNG carrier in a ship-to-ship configuration using
the carrier’s cargo pumps. The high-pressure LNG pumps on the FSRU then transfer LNG to the vaporiser at the desired pressure, to deliver natural gas into the local gas network for consumption in homes and industries.
FSRUs are particularly suited to time-critical projects since they can be either built from scratch or repurposed from an existing LNG carrier. But, in either scenario, an FSRU is almost always faster to engineer, construct, and commission than a fixed onshore storage and regasification terminal. Attaining the required permits for an FRSU is often faster too.
The other key advantage of FSRUs is flexibility. When operational, they are fixed in place. But they are not necessarily permanent infrastructure, as they are towable to another berth
With Germany’s energy security at stake, FSRUs were needed, and quick. Andy Loose, Worley, explains how the company worked around the clock to deliver an FSRU in months, rather than years.
location if the need arises. This is not possible for a fixed import terminal.
And, if Germany’s natural gas demand shifts significantly over the coming years, these FSRUs are less likely to be stranded infrastructure of no use in another location.
In June 2022, Worley was awarded an EPC contract to deliver one of Germany’s five new FSRUs.
The goal was to achieve first gas by the following winter of 2022 – 2023. There was no concept or FEED phase to define what was needed, or exactly how the FSRU would look. The objective was simply to deliver an FSRU to Germany and target first gas during the next winter.
At first glance, an FSRU terminal project (as depicted in Figure 1) looks relatively straightforward to execute. However, each FSRU project brings unique challenges, both expected and unforeseen.
There are many steps to delivering a fast-track FSRU project. The first is securing an FSRU. At the time of crisis, the governments and energy supply companies in Europe acted quickly to either charter or purchase existing FSRU vessels.
The next element is identifying a suitable port location for an FSRU that has both government and local authority support. It is advantageous to have an operating port with a suitable existing berth, as this will normally enable shorter permitting timelines. If the FSRU requires a new jetty, this will extend the project timeline because more surveys are required to gather geotechnical data and support the environmental impact assessments.
A flexible contract between the owner and contractor with a highly collaborative approach is essential so risks are understood and appropriately managed. All parties must be aligned with the common objective of achieving first gas with a total focus on schedule, rather than cost. With this established, the next step is to tackle the technical and execution challenges of a project.
In selecting a suitable site for a fast-track FSRU project, it helps if the berth has sufficient depth, with allowance for the tidal range.
A sufficient depth is approximately 15 m, otherwise additional dredging may be required which can take extra time to permit and organise. It is also important to consider the safe movement of other shipping traffic in busy waterways and the access route for LNG carriers delivering cargoes.
After identifying a suitable location, the next consideration is the utilities and services required to operate the FSRU. The regasification process requires warm water. FSRUs often utilise their own seawater pumps to provide the water to vaporise the LNG onboard. However, in northern European locations, the seawater is typically too cold in winter to deliver gas at the preferred 10˚C. Vaporising 7.5 billion m3/y of natural gas requires around 130 MW of heat. If there are large industrial sites nearby, it could be possible to utilise a warm water supply from them.
The FSRUs can run their own gas engines to produce the power needed on the vessel during normal gas send-out operations. This process requires 15 – 20 MW in total. This external power could come from a low-carbon source – rather than gas – to reduce the carbon footprint of an operation.
In selecting the site, it is also important to consider the connection to the gas distribution system. Having a short connection from the FSRU to a large capacity grid avoids the need for any major infrastructure upgrades, which would also impact on the project timescales.
If Worley had followed a normal project scheduling path, the company would not have been able to deliver gas from this FSRU in winter 2022 – 2023. But the solution to this timeline challenge could not just be a small tweak, either. It required a very different execution sequence from other large projects, which usually consist of an engineering phase, then procurement, followed by construction in strictly sequential order. The plan had to involve out-of-sequence working and reverse engineering based on what critical components the company could procure.
Procurement is one of the defining challenges for a fast-track project, with the greatest impact on the schedule. From the start of this project, Worley’s procurement team worked to immediately identify the long lead items and make inquiries to the market.
This is where collaboration between contractor and owner is key. When procuring equipment based upon preliminary engineering, there has to be
acceptance of the risk of change and potential rework. To minimise this risk, it is important to work with trusted suppliers and partners. These suppliers and contractors may be sole sourced to accelerate the procurement process. Similarly, there is need to accept supplier standards to reduce lead times.
FSRU terminals typically use high-pressure gas loading arms for connection to the FSRU. However, these are a specialist long lead item. Unless these loading arms are already available, high-pressure gas hoses offer shorter delivery times.
To support the fast-track execution, Worley worked closely with its Rosenberg Worley team in Stavanger to fabricate the various high-pressure piping skids and steel structures required for the FSRU vessel. Collaborating with Rosenburg simplified the interface between engineering and fabrication, which further shortened timelines. Rosenberg’s experts also assisted with the procurement of critical bulk items that would otherwise have delayed the construction and commissioning phases.
Worley also took full control of all logistics and freight to avoid any unnecessary delays in equipment and materials. This included air-freighting the control room – which was built in Türkiye – utilising an Antonov aircraft. Similarly, the company utilised a helicopter to install the new vent stack onto its foundation. This operation took only 11 mins. from lifting to bolting down.
In a fast-track project, it is still necessary to follow the required permitting processes, as well as any third-party verification work and project safety studies including a quantitative risk assessment (QRA). As these activities happen in parallel, planning is crucial to account for any late surprises.
No construction work at site can commence until the suitable permits are authorised. This is a critical milestone for any fast-track project. Worley received the required permits in October, just as temperatures were plummeting. These freezing conditions made groundworks and preparing foundations more difficult, but not impossible.
Although an existing port and berth is helpful for a fast-track FSRU project, it still creates challenges for brownfield work during construction. Existing operations must continue in working ports, so this requires careful planning and segregation of all construction activity. Data can be scarce for older facilities too, so surveys are often necessary to identify underground obstructions and to digitally map existing systems.
Worley was able to deliver first gas from the FSRU into the grid system less than nine months after commencing work on the project. It placed the first purchase order in month two, and commenced fabrication in month three. The project team met its deadline to have the FSRU in operation in time to deliver natural gas into the grid for the second half of the winter season.
FSRU projects are not usually as technically complex as other energy facilities, such as liquefaction plants, refineries, or offshore platforms. However, the team learned a lot from the ambitious task to design, build, and commission one on such an ambitious schedule.
One of the main learnings from this project was how quickly the industry can deliver new infrastructure, by embracing a more agile approach to engineering projects – it is not always necessary to follow a strictly sequential process. Worley’s success in delivering this FSRU in eight months also depended on close collaboration between all the involved parties and across all disciplines, from engineering to procurement to construction.
While this project is related to the supply of hydrocarbons for short-term energy security, these learnings are applicable to almost any project. When companies collaborate and embrace new and different ways to deliver complex energy infrastructure, the industry can make the most ambitious projects real.
Unrivaled technologies from Air Products empower the LNG industry to produce the cleanest, most reliable, most affordable energy.
Unrivaled plant performance means the highest efficiency and reliability, and the lowest total cost of ownership.
Unrivaled support and services from our responsive experts optimize plant performance and equipment life.
For over 60 years, Air Products has been advancing LNG technology, producing solutions that fuel our world.
empra Infrastructure, headquartered in Houston, is focused on delivering energy for a better world by developing, building and operating, and investing in clean power, energy networks, and LNG and net-zero solutions that are expected to play a crucial role in the energy systems of the future. Through the combined strength of its assets in North America, the company is connecting customers across the globe to modern energy infrastructure to source and transport renewables and natural gas, while advancing carbon sequestration and clean hydrogen.
The company executes its goals through three business lines:
� Clean power: With a focus on safe and reliable integration of North America’s power grids, Sempra Infrastructure operates more than 1600 MW of energy projects in Mexico, with significant cross-border renewable energy development opportunities.
� Energy networks: The company owns and operates natural gas transmission and distribution pipelines in Mexico and the US, in addition to ethane pipelines, liquefied petroleum gas (LPG) transportation and storage, and a network of refined products storage terminals in Mexico. Through its energy networks, it helps meet energy needs and promote growth and development of the markets that it serves.
� LNG and net-zero solutions: The company’s LNG facilities and net-zero development projects on the Pacific and Gulf coasts of North America serve energy security and energy transition ambitions by facilitating affordable, reliable, and lower-carbon intensity energy.
Three key trends support these opportunities: decarbonisation, energy security, and the reshoring of manufacturing to North America, all of which bring confidence to the long-term growth profile of the business. Energy needs in North America continue to grow as a result of a strong nearshoring of investments and relocation of regional value chains trend, especially in Mexico. For example, the InterAmerican Development Bank believes Mexico can increase its export platform by US$35 billion thanks to these processes.
In addition, Mexico recently surpassed China to become the largest trading partner of the US. Given Sempra Infrastructure’s position as a leading player in North American energy infrastructure, the company is well-positioned to support growing energy demand within Mexico. More recently, the company received several positive regulatory approvals for some of its assets in Mexico, including in its energy networks and clean power business lines.
Through the combined strength of its assets in North America, the company is dedicated to enabling the delivery of cleaner energy and strengthening energy security for its customers. Sempra Infrastructure’s four sustainability pillars – enabling the energy transition, driving resilient operations, achieving world-class safety, and championing people – are at the core of the company’s commitment to sustainability.
Collectively in 2023, the Sempra Infrastructure project teams have achieved more than 11 million hours worked without a lost-time incident. Sempra Infrastructure’s health and safety policies reflect the company’s commitment to establish safe work practices by implementing adequate preventive measures for people, facilities and processes, and a workplace that is free from uncontrolled known hazards.
Sempra Infrastructure currently has 28 million tpy of LNG export facilities in operation or under construction, and more than 34 million tpy of LNG export projects under development. Through its strategy of building out a dual-coast platform that allows the company to efficiently deliver LNG to customers from both the Atlantic and Pacific regions, Sempra Infrastructure is building one of the largest LNG export infrastructure portfolios in North America, making the company one of the leading developers of LNG projects on the continent.
The Energia Costa Azul (ECA) LNG project, located north of Ensenada in Baja California, Mexico, was the only LNG export project in the world to have reached final investment decision (FID) in 2020. The project’s strategic location on Mexico’s West Coast positions it to connect Asia, the Pacific Basin, and international LNG markets, as well as potential markets on the west coast of Mexico to abundant natural gas supplies of the US western states.
ECA LNG Phase 1, which is currently under construction, is designed to be a single-train liquefaction facility with a nameplate capacity of 3.25 million tpy of LNG and will use two existing storage tanks and be served by Sempra Infrastructure’s proposed Rosarito Pipeline Expansion project.
The company is also developing the proposed ECA LNG Phase 2 project, which is expected to be comprised of two trains and one LNG storage tank, and will produce approximately 12 million tpy of export capacity.
The proposed Vista Pacifico LNG project is projected to be a mid scale facility with approximately 2 million tpy of export capacity. The proposed project would be located
Sempra Infrastructure provides insight into the company’s export facilities in North America.
in Topolobampo, Sinaloa, Mexico, and is being developed by Sempra Infrastructure in collaboration with Mexico’s Federal Electricity Commission (CFE). The development of the proposed Vista Pacifico project could allow CFE to optimise excess natural gas pipeline capacity and could promote economic growth and development in the region, with a view toward strengthening CFE’s position in the global LNG market.
Sempra Infrastructure, along with its Cameron partners, continues to pursue the development of the proposed Cameron LNG Phase 2 project. They have informed Bechtel that it had been selected to perform additional value engineering work for the FEED process on the proposed Phase 2 project, and the parties are negotiating the terms and conditions for a definitive EPC contract, positioning the company to take up a FID after satisfactorily finalising the additional FEED work, negotiating the final EPC, and securing project financing and any required regulatory approvals.
The proposed Hackberry Carbon Sequestration project, expected to be one of the first world-class carbon sequestration operations in North America, is being designed to advance the company’s net-zero solutions by producing cleaner LNG for Cameron LNG and potentially other
Sempra Infrastructure was formed two years ago with a view towards creating a larger platform to capture new opportunities that support the energy transition and invest in the energy systems of the future. The integration of two separate Sempra subsidiaries, previously known as Sempra LNG and IEnova, enabled increased business optimization and, most importantly, the consolidation of decades of energy infrastructure development and operating expertise under a single, self-funding platform. With its expanded scale, Sempra Infrastructure is strategically positioned to capture investment opportunities and cultivate portfolio synergies that help support the growth of North American energy markets.
third-party customers. With the development of this project, carbon dioxide (CO2) would be captured at Cameron LNG and transported by pipeline to a compression facility on land owned by LA Storage, a subsidiary of Sempra Infrastructure. It will then be permanently stored in a saline aquifer with a capacity of up to 2 million tpy of CO2.
In 2021, the company commenced the permitting process by filing an application for a Class VI Injection well permit from the U.S. Environmental Protection Agency. Additionally, applications were filed with the U.S. Army Corps of Engineers and the Louisiana Department of Natural Resources. Development of the project continues, which could be transformative to the industry and enable offtakers to ship lower carbon-intense LNG from the Cameron LNG facility.
The Port Arthur LNG Phase 1 project, which is currently under construction, represents a US$13 billion investment in new energy infrastructure in Texas that will stimulate local, regional, and national economies by creating US jobs, supporting small businesses and strengthening the US natural gas sector’s leadership position as a reliable partner in building energy security that can support allies in Europe and the rest of the world.
The project is designed to include two natural gas liquefaction trains, two LNG storage tanks and associated facilities with a nameplate capacity of approximately 13 million tpy.
Since the company affirmed a positive FID in March 2023, the Phase 1 development project has achieved more than 2.7 million hours worked without a lost-time incident.
Perhaps most importantly and uniquely, the Port Arthur LNG Phase 1 project can deliver significant value not only for Sempra Infrastructure but also for the local community, opening up substantial avenues for further growth opportunities. To further optimise Port Arthur’s location along the Sabine-Neches Waterway, the company recently proposed the development of a flagship energy hub that showcases the value of Sempra Infrastructure’s world-class integrated capabilities. Sempra Infrastructure can leverage development and operational expertise across its portfolio to enhance the total value of Port Arthur, by adding additional LNG production and export capacity, carbon sequestration and hydrogen production, all of which would position Port Arthur to be a flagship hub for the energy transition.
The proposed Port Arthur LNG Phase 2 project is envisioned to have a nameplate capacity of 13 million tpy, bringing the combined total capacity of the facilities to 26 million tpy.
In addition, the company plans to leverage the integrated capabilities of its business segments to develop the proposed Louisiana Connector pipeline, gas storage facilities, Titan Carbon Sequestration facility and an early-stage hydrogen project — all located in the Port Arthur region. This comprehensive development approach is part of the company’s growing energy infrastructure portfolio and is expected to capture a larger piece of the economics from the Port Arthur footprint.
The collective impact of these efforts would bring additional investment to the Port Arthur local community, Jefferson County and the broader Gulf Coast region.
Carlos Guerrero, Bureau Veritas Marine & Offshore, France, discusses how LNG carriers have evolved, with innovative containment systems, propulsion, and reliquefaction systems, to drive developments beyond traditional boil-off gas economics.
The operating profile of modern LNG carriers has changed – flexibility is now more important, with ships calling at different loading and offloading terminals, and requiring high fuel and energy efficiency. Where early LNG carriers were contracted for long periods (typically over 15 years) and predetermined routes, modern vessels are chartered for relatively short periods and may travel numerous and changing routes. This requires greater flexibility in terms of ship size, onboard equipment, propulsion systems, and cargo management.
Steam turbine driven ships have evolved into dual-fuel diesel electric (DFDE) ships, and from there more recently
into two-stroke dual-fuel powered vessels. Two-stroke engines offer major propulsive efficiency, and the dual-fuel capacity allows for the use of different kinds of fuels. This offers much needed flexibility for LNG carriers and improves cost-optimisation for shipowners.
LNG carriers are designed to avoid too much or too little LNG evaporation (boil-off gas [BOG]), so the demand for fuel flexibility has driven the development of a second wave of more energy efficient BOG re-liquefaction or LNG-subcooling systems, which are being installed on most new LNG carrier projects today. By handling BOG efficiently, ships can arrive at port with more of their cargo intact, providing greater
flexibility and making this technology attractive to charterers and shipowners.
The last few years have seen further evolution. A new wave of very large LNG carriers on order is proposed for US and Qatar liquefaction projects – including a couple that recently entered service – with plans to accelerate the development of liquefaction terminals to meet demand. Disruption to European gas supplies is another contributing factor, although LNG demand is still driven by Far Eastern countries. However, attributing any technical development in the LNG carrier design to a single socio-political event does not paint a full picture. Firstly, the Ukraine conflict has impacted the LNG sector most heavily, while LPG remains practically unscathed. Secondly, while it is mainly European supply that is disrupted, the trend in gas carrier size is global. The fact is that larger vessels are proving to be one of the necessary features of the future maritime world, since economies of scale and efficiency are driving the initiatives.
Demand for cleaner energy has grown at an unprecedented pace, as countries worldwide seek to reduce harmful emissions and explore new ways to achieve carbon neutrality and decarbonisation. On the road from fossil energy to renewable energy, LNG has emerged as the key bridge as the cleanest fossil fuel available. Bio-LNG or
e-methane also need to be considered as potential future fuels.
An increase in LNG trade and design optimisation has led to investment in large scale LNG carriers with cargo capacities over the standard 174 000 m3. These vessels can deliver liquefied gas to onshore LNG terminals, FSUs, and FSRUs. Carrying as much as 200 000 m3, they can also transport larger cargoes over longer distances. This may enable greater flexibility in transcontinental operations, which is crucial in a fluctuating energy market, provided the terminal compatibility is not compromised. Additionally, these high-capacity vessels are designed with four cargo tanks, which makes them simpler to handle and reduces associated CAPEX and OPEX compared to similar existing Q-Flex carriers.
BOG economics continues to play a vital role in powering large scale LNG carriers. A delicate balance must be maintained between the propulsion system and cargo containment system to ensure that fuel consumers and gas combustion unit use the right amount of BOG.
In the case of insufficient BOG, LNG cargo either must be vaporised to produce boil-off, or oil-based fuels must be used as an alternative. An overabundance of BOG will lead ships to either reliquefy BOG, sub-cool LNG, or burn excess gas in gas combustion units or boilers. To balance out BOG production and gas fuel consumption, ship operators have often adapted their speed to produce the needed amount of BOG for travelling a given distance.
However, as shorter charter contracts have become the norm and spot trading increases, demand has risen for more flexible LNG carriers that can operate efficiently under a different set of criteria. Shipowners and shipyards have therefore become more innovative, matching the right reliquefaction or subcooling system with evolving propulsion and thermal efficiency of cargo containment systems.
The requirements of the IMO’s short-term climate goals are now being felt by the industry as it adapts to the requirements of the EEXI and CII regulations. These are exerting greater pressure on shipowners and cargo owners to increase energy efficiency and decarbonise their operations. In some cases, particularly for older steam turbine powered vessels, the initial response is to slow the vessel down. This is just one method of improving fuel efficiency through operational measures, one that is rooted within the scope of BOG trade-offs, but one that will not remain viable on its own for long. While it may be the most economical solution for aging vessels, increasingly stringent targets, taking effect annually through the CII regulations, will demand a more sophisticated response for vessels expected to remain operational beyond this decade.
As industry-wide mandates to decarbonise continue to increase, long-held practices such as reducing speed or employing a ‘sail fast then wait’ (SFTW) strategy will become more difficult to justify and maintain. SFTW is particularly undesirable as it can lead to significant additional fuel consumption as vessels speed across oceans, only to idle outside congested ports or terminals. Bureau Veritas has joined an initiative that aims to eliminate the practice.
The Blue Visby project seeks to end SFTW by combining digital technology to stagger and optimise arrivals for groups of vessels travelling to the same port, and a contractual architecture which introduces a sharing mechanism that encourages adoption. These changes have the potential to reduce total greenhouse gas (GHG) emissions by 15% on average, according to the Blue Visby Consortium.
Along with operational measures to reduce GHG emissions, shipowners are looking into clean technologies to bring the efficiencies required to meet CII requirements this decade. While few net or zero-carbon fuel options are available, fuel reduction technologies such as shaft generators that enable main engines to produce electricity, air lubrication that reduces friction along the hull, and wind-assisted propulsion technologies on deck can provide shipowners with immediate benefits, since the technology is mature enough.
These solutions are de-coupling the economics of efficiency from BOG considerations. Shipowners can reduce fuel consumption significantly with these technologies, and combined with onboard reliquefaction or sub-cooling, there is less need to tap into the LNG cargo as an energy source.
However, there are still trade-offs. Wind-assist solutions, for example, will provide better payback on routes where there are suitable winds, with the North Atlantic likely to provide greater efficiency gains than the Indian Ocean, for example. There is limited space on deck for the installation of rotors or sails, and visibility from the bridge must be considered. Navigation lights must also be clearly visible, and these safety considerations could limit the scope of such installations.
Onboard carbon capture is gaining attention as an exhaust emissions abatement solution. It may be considered by the IMO in the coming years and be adopted into MARPOL Annex VI regulations, because it can help recover part of the carbon dioxide (CO2) generated by the engines on board. It is therefore likely to be a next step for the decarbonisation of LNG carriers. However, as the CO2 captured from the exhaust needs to be stored on board –most solutions are looking at liquefied CO2 storage – it is expected that this solution will be better suited to short-range sailing where frequent offloading limits the amount of storage space needed on board.
New fuel opportunities are expected to roll out in parallel with new clean technologies, and they will lessen the relative importance of BOG management as an emissions abatement and efficiency strategy. Biofuels are already being used, and they are a viable option for pilot fuel or main fuel depending on the operational profile. Their use can have a positive impact on CII ratings, and little (if any) vessel modifications are required, so they are expected to be a popular choice, particularly this decade.
The use of hydrogen mixed into other fuels continues to be researched. Engine manufacturers are progressing in developing systems to blend a certain percentage of hydrogen into these fuels. Pure hydrogen-fuelled internal combustion engine technology is also possible in theory. In particular for gas carriers, IMO regulations, such as the International Gas Code and, in general, SOLAS or the IGF Code for other type of ships, will need to be updated to incorporate these developments (although IMO is working currently to produce guidelines), so there is still much work to be done before the use of hydrogen-based fuels can be expanded across the merchant cargo fleet.
There is a change in power on the horizon – nuclear power for commercial ships. It is too early to predict its feasibility, because there are technical and political challenges to overcome. Everything changes with this form of power generation – safety protocols, crew training, systems maintenance – and some authorities may not allow such vessels into their ports or territorial waters.
It would also seem an unlikely choice for LNG carriers. While the use of BOG as fuel may diminish to a certain extent with new technologies and fuels, it is unlikely to be completely replaced in the foreseeable future. Additionally, assuming a reasonably good LNG charter market going forward, LNG carriers are less likely to be scrapped and replaced with new designs before 20 years of age. In 2022, there was only one LNG carrier sold for recycling, and only a handful were scrapped in the previous two years, although the trend may slightly change from 2023.
The retrofit at large scale of new technologies, such as air lubrication and wind-assisted propulsion systems or propulsion conversions, will depend on shipyards availability, which is not really granted due to the record number of projects.
In the short term, then, it is likely that operational measures will predominate as the solution for improving efficiency and reducing emissions to meet climate goals. Adoption of clean technologies will be gradual and parallel to the uptake of new fuels, although it is expected that BOG will still be used on board LNG carriers. Over time, the importance of BOG will progressively diminish for those vessels with onboard liquefaction, as both a strong market for LNG and greater efficiency onboard will weaken the economics for burning it in the carriers’ engines. Will there be a change to onboard carbon capture, hydrogen fuel, or nuclear-powered propulsion? That is a question for the next decade or two.
Our pre-constructed, turnkey solution minimizes risk and gives you total control over business growth strategies. Even the 1-MTPA range is now viable and easy—with zero-emissions liquefaction process and 20–30% lower CO2 overall including power generation. Our solution is up to two years faster than traditional stick-built approaches, and it requires significantly fewer on-site personnel and less site time. So, it can be quickly commissioned and scaled up by one or more modules at a time—any time you want.
Tip the scales in your favor with our LNG modules.
bakerhughes.com/lng-solutions
s the world races towards net zero and the transition to diverse and cleaner fuels accelerates, renewable energy capacity has been expanding rapidly.
The technology is crucial to slashing carbon emissions, and countries such as Brazil have emerged as pioneers in the sector. The nation has become a global frontrunner in hydropower expansion and has invested heavily in it. Between 1970 and 2020, Brazil’s electricity generation surged tenfold, with hydropower accounting for approximately 90% of its total consumption, according to the World Bank.1
This has meant that Brazil now has one of the least carbon-intensive energy industries in the world, an impressive feat for a middle-income, developing economy.
However, in 2021, Brazil’s Paraná River Basin had an unprecedented drought, its most severe dry spell in almost a century. As a result, agricultural production plunged,
Serdar Kumbasar, Karpowership, Brazil, details how LNG can be utilised to deliver electricity quickly to countries that need it.
river-borne shipments of food and fuel were restricted, and fresh water supplies for 40 million people across the region were impacted.
The natural disaster also severely curtailed Brazil’s hydropower generation, its largest source of energy by far, forcing it to import electricity from neighbouring countries, boost domestic output of fossil fuels, and switch to using more expensive options in the search for innovative supply solutions.
Eventually, a power tender was held and the companies that could offer a fast and flexible solution were called upon to help. The challenge was that any winning bidder would need to begin supplying the nation’s grid with power within months, a much shorter timeframe than usual, meaning that installation and implementation of chosen projects would have to be rapid, while also being safe and flexible.
Karpowership is the world’s largest owner and operator of floating power plants. Its unique solution, Powerships, have all the necessary infrastructure onboard and can simply be plugged into a nation’s power grid, often in as little as 30 days after contract signing. So, the company responded to Brazil’s call for emergency electricity and is now supplying 560 MW to the country’s grid, enough to keep the lights on for approximately 2 million households.
The deal, Karpowership’s first transatlantic LNG-to-power contract, was to supply four floating power plants, known as Powerships, in Port of Itaguai, Rio de Janeiro, Brazil. An FSRU would also accompany the vessels to store and regasify the fuel.
The Powerships would be supplied with natural gas through the FSRU, located in the Port of Itaguaí, for a period of 44 months. In a highly competitive market for securing LNG, floating solutions such as FSRUs can offer huge cost and scheduling advantages over lengthy construction timelines for traditional land-based facilities.
An FSRU used in combination with a Powership offers a flexible, cleaner, innovative, and fast energy solution that is particularly well-suited to emergency situations like Brazil’s.
Karpowership is a highly experienced operator of floating infrastructure and flexible energy solutions, with Powership projects up and running in 13 countries around the world.
Although the company is accustomed to operating in challenging conditions, the Brazilian project presented an array of unprecedented technical, engineering, and weather-related hurdles which the company had to navigate under extreme time pressure.
From the weather conditions to the unique infrastructure to the timeframe that Karpowership was given, this project was testing on every level.
One of the biggest challenges was installing and maintaining 15 km of transmission lines, used to transmit the electricity from where it is generated offshore to where it is needed on land. This was no easy feat.
For the project in Brazil, the transmission lines had to start far from their land connection point, with the closest vessels anchored 4 km away from the shore. This meant that Karpowership had to lay almost 4 km of offshore transmission lines, navigating unpredictable sea conditions, bad weather, and delicate marine life and vegetation. As well as the offshore transmission lines, approximately 11 km also had to be laid on land.
Protecting Sepetiba Bay’s unique marine life was crucial to ensuring that Karpowership complied with its environmental obligations throughout this project. One such priority was vegetation.
The project involved the construction of 41 transmission towers, seven of which were offshore. For one
of the structures at sea, the team had to double the length of the transmission line to protect sensitive and delicate vegetation. Another transmission tower was moved approximately 150 m northwest of its originally planned location to avoid this de-vegetation and prevent damage to its ecosystem. These changes in the transmission towers led to modifications in the design and engineering of the remaining parts of the transmission line which had to be done as built.
There are always a multitude of challenges involved in installing floating infrastructure at sea and ensuring that all the assets and power generation equipment remains secure and operational. The most unpredictable of which is the weather.
During the installation phase, engineers had to contend with the tides, winds of up to 120 km/h, and even passing traffic on the busy shipping route.
Hundreds of studies had to be carried out for multiple different authorities in Brazil to ensure that maritime traffic would not be impacted throughout the lifetime of the project. This was due to Powerships being located close to a canal, a narrow stretch of waterway in which many ships enter every day. This meant that even mooring the ships was quite challenging and involved multiple additional checks, including from Brazil’s maritime authorities.
Meanwhile, the project had to be installed during a period when storm activity in the South Atlantic region typically peaks, and it had to be completed before the next dry season approached. This meant that several installation and implementation days were lost due to bad weather,
while the project already had to be completed to a very tight deadline.
While Karpowership tried to stay close to an existing water channel to minimise the impact of swells, the towers and transmission lines all had to be installed in rough sea conditions. Being a busy transit route for ship traffic, nearby ships also created waves which caused further challenges during construction.
The infrastructure also had to withstand all possible weather conditions during the years-long operation phase while ensuring that the Powerships were moored securely as well.
The team needed to assure Brazil’s authorities that all operations were safe all while ensuring that gas flows of up to 90 million ft3/d could be consistently achieved.
There were also crucial technical, infrastructural, and environmental guidelines set by the government that had to be followed. These included ensuring the maritime safety, protecting subsea vegetation and other marine life, all of which Karpowership successfully delivered on.
Then there were the project stakeholders who all had to be engaged with, alongside the installation and environmental assessments. Understanding the needs of each stakeholder while also demonstrating that Karpowership had adhered to all regulations and local and international standards, all while working to bring the project online, were all key factors in its success.
Brazil’s crucial and ambitious plans to cut carbon emissions led to huge investments in hydropower. But, with global warming and climate change, it has become a must to combine the weather-based energy policies with thermal when the country experienced its most impactful drought in almost a century, diversification of the nation’s power supply was crucial. Ultimately, it was a gas-fuelled, one-of-a-kind energy project that was needed to keep the lights on.
From unpredictable weather and sea conditions to complex infrastructure to racing against the clock, Karpowership’s project in Brazil was an unprecedented challenge from start to finish.
While the company never had any doubt that it had the technical capabilities to bring the operations online, squeezing years’ worth of planning and construction into just several months was undeniably a challenge. But the hard work paid off and the facility is now operational, providing a cleaner, stable, and reliable source of power.
The project was ground-breaking from an engineering point of view and served to demonstrate the company’s confidence in its technical capabilities. When it comes to the end of its 44-month lifespan, all the infrastructure will be decommissioned and the Powerships will be re-deployed, leaving zero environmental trace.
Karpowership, however, intends to remain in Brazil for the long haul, where it sees huge opportunities to invest in low-carbon energy and a productive partnership with the country.
Elemental mercury is a very toxic compound that affects the human nervous system and kidneys, and bioaccumulates in the surrounding ecosystems. In addition, mercury can compromise plant equipment integrity through liquid metal embrittlement (causing cracks) and amalgams (alloys with metals like aluminium). The latter can cause very severe safety incidents in gas processing plants, with risk to life and extensive financial implications.
It is thus a requirement that mercury is removed from natural gas before it is converted into LNG or transported via a pipeline. With the lowest carbon footprint of all fossil fuels, LNG is a critical enabler towards a decarbonised world, and this is reflected in its on-going growth in demand.
The most effective technology to remove mercury utilises copper sulfide (CuS) absorbents via an irreversible chemical reaction as follows:
Hg + 2CuS –> HgS + Cu2S
The high reactivity of CuS gives rise to the fastest mercury removal kinetics and the highest absorbent capacities of all technology options. This combination allows for the longest bed lifetimes and the smallest mercury removal unit vessel footprints. The technology also offers a sustainable solution for mercury removal, reducing the overall environmental footprint as part of well-designed flowsheets.
Once the mercury is captured by CuS-based absorbents, the mercury is locked away into the absorbent structure as safe, chemically inert, and non-volatile mercury sulfide. At the end of the lifetime of the charge, the spent absorbent can be safely handled and sent for the responsible disposal of the captured mercury.
Conventionally, mercury removal absorbents are loaded under inert conditions. High-purity nitrogen is required during loading to prevent self-heating reactions due to CuS oxidation. Run-away exotherm
Azuin Roslan, Mark Kent, and Ekaterina Novakova, Johnson Matthey, consider the air loading capability of an absorbent as a means for improved mercury removal operation.
caused from an uncontrolled oxidation could lead to very significant damage to the plant and hazards to personnel.
While loading under inert atmosphere is well-established industry practice, gas processors often talk about the difficulties and risks associated with the use of high-purity nitrogen. Using over 30 years of experience of supplying mercury removal absorbents, Johnson Matthey challenged itself to develop a CuS absorbent with high performance and no self-heating potential, allowing for loading in an oxygen-containing atmosphere.
PURASPECTM 1193 and 1194 were launched at the start of 2023 as high-performance mercury absorbents that also offer the capability to be air-loaded. This new technology has been made possible by advancements in the understanding of how to enhance mercury removal kinetics while inhibiting oxidation kinetics.
The product launch was carried out following an extensive safety and performance testing. An important customer in Japan has already successfully loaded PURASPEC 1194 under air. The absorbent charge has been in operation for more than six months and continues to operate as designed.
Loading under air atmosphere removes the potential danger of nitrogen asphyxiation to personnel. Nitrogen will displace oxygen in enclosed spaces, potentially leading to asphyxiation if appropriate precautions (such as personal protective equipment, training etc.) are not taken.
Loading under an oxygen-containing atmosphere provides the flexibility to choose between air or plant-grade nitrogen. Operators can select the approach that best aligns with their established procedures and safety guidelines regarding handling hazardous material.
Availability of high-purity nitrogen or, more often, liquid nitrogen can be challenging in remote or offshore locations. Using ambient air for loading the absorbent simplifies the logistics and reduces the reliance on specialised nitrogen supply infrastructure.
Safe handling of nitrogen during absorbent loading requires specialist catalyst handling crews. Contacting such crews adds an extra layer of complexity and cost to the loading process. This is in addition to the cost of liquid nitrogen that can be high depending on location and minimum tanker size. Therefore, loading under air atmosphere allows for a more streamlined and cost-effective approach, reducing the overall operational expenses.
The self-heating characteristics of PURASPEC 1193 and 1194 absorbents were thoroughly evaluated by the company’s own technical experts working in conjunction with a world-leading third-party testing and certification company. Tests were designed based on widely recognised methodologies for classification of hazards of goods for transportation. Further, the conditions of these tests were made more challenging to ensure that risks specifically associated with air loading of the absorbent were appropriately considered and tested for. The experimental work was conducted by the third-party testing and certification company using PURASPEC 1194 material – this product grade was expected to be more prone to oxidation if any was to occur.
The 1 l wire basket test is based on the standard test for substance self-heating classification, according to UN DG Code and CLP/GHS.1 The sample is exposed in air while being heated for 72 hr, and the exit temperature of the sample is continuously recorded. If the sample temperature increases more than 60˚C above the set temperature of 140˚C, the sample material is classified as ‘self-heating’ within GHS and for Transport (Class 4.2).
Under these test conditions, no exotherm was observed. As it is known that high humidity in certain geographical regions can increase the exotherm potential, an additional test was carried out using (i) water saturated air (at 70˚C) and (ii) set temperature of 220˚C. Figure 1 shows the results.
The results clearly show that the PURASPEC 1194 exhibits no exotherm due to self-heating at 220˚C, and humidified air as the sample temperature did not deviate from the oven temperature for the full duration of the test.
To eliminate any concerns about the sensitivity of this method, a standard (140˚C) test was run on a reference sample, which represents a conventional CuS-based mercury absorbent (Figure 2).
Significant exotherm of 130˚C was recorded on the reference sample, which was broadly independent on the
level of humidity of the air. While this is a strong re-assurance of the accuracy of the test results, three additional testing methodologies were utilised by the third-party company to re-affirm the inertness of PURASPEC 1194 towards self-heating during air loading operations. All of these results showed no evidence of self-heating for PURASPEC 1194.
A mercury removal testing programme was carried out to ensure that the exposure to air during the loading does not negatively impact the inherent performance
of the absorbent. Typically, absorbents’ performance is characterised in terms of capacity and kinetics as each of these directly impacts the life cycle utilisation and cost of the absorbent.
Figure 3 shows the results for cumulative mercury absorption in a long term (205 days online) gas phase mercury removal test. PURASPEC 1194 retains the long-term mercury removal capacity of traditional Johnson Matthey’s CuS-based absorbents, allowing for direct replacement with no process changes or equipment modifications. Accelerated performance tests were also carried out to probe any changes in kinetics that could occur following an air loading process. Firstly, samples of commercially produced PURASPEC 1194 absorbent were taken from drums which had been stored for three months to account for typical transportation and storage time prior to loading at customer sites. These were then placed into open dishes where the material was well-spread to ensure very high contact with air and left for 14 days (Figure 4). This treatment would exacerbate any deactivation due to exposure in air following a typical plant start-up.
Figure 5 shows the changes in rate constant of PURASPEC 1194 with time of sample exposure in air starting from when the drum was first opened. The results show that there is no notable change in the mercury removal kinetics of PURASPEC 1194 in an accelerated air exposure simulating the air loading process.
The increasing demand for natural gas/LNG and the stringent safety and quality regulations require purification solutions that are efficient in removing mercury to very low levels in a cost-effective and easy to operate manner. Air loading is an important capability to supplement the high inherent performance of an absorbent.
PURASPEC 1194 has been proven to retain its high capacity and fast kinetics, following safe loading of the absorbent in an oxygen-containing atmosphere. This has also been demonstrated at a full-scale plant environment at Johnson Matthey’s customer in Japan.
The absorbent does not undergo any exothermic reactions or generate heat when exposed to air or oxygen-containing nitrogen. This inert behaviour towards self-heating ensures the stability and integrity of the absorbent, providing a secure environment for handling and transportation. Laboratory testing under accelerate conditions showed excellent performance in the removal of mercury following exposure to air, which combined with its inherent high water carry-over resistance would ensure a long and reliable life of the absorbent.
Eliminating the requirement for high purity nitrogen loading makes the overall operation safer, more cost-effective and logistically easier to manage especially in remote and offshore locations.
References
1. UNECE: Recommendations on the Transport of Dangerous Goods – Model Regulations (Rev. 21) and CLP Regulation (EC) No 1272/2008 on the classification, labelling and packaging of substances and mixtures.
The LNG industry is constantly evolving, and we can help you lead the way. The expertise of Atlas Copco Gas and Process and CPC Pumps International Inc. provides custom-engineered compression and expansion technology that boosts your productivity throughout the LNG value chain.
Across our history, we have engineered advanced process equipment that delivers maximum efficiency in modular, compact packaging. We offer end-to-end centrifugal compressors, screw compressors, turboexpanders, companders™ and centrifugal fluid pumps customized for every LNG application, from small scale to large scale, onshore and off.
Scan the respective QR Codes to learn more about the solutions.
Atlas Copco Gas and Process CPC Pumps International Inc.The comprehensive component design to complete the system design, manufacture, and installation capability.
Maximum service life thanks to these advanced features to produce exceptional efficiencies across the entire system.
Cryogenic insulation for Nitrogen, Oxygen, Argon, Helium, Natural Gas, Carbon Dioxide, Hydrogen
Stainless Steel Inner Pipe Come
The inner and outer pipe is constructed of 300 series stainless steel. Insulation is a low vacuum with multiple layer insulation (MLI).
The patented design builds on a conventional globe configuration by incorporating numerous unique features that decrease heat leak and increase the service life of the valve. Rated Working Temperature -452° F to 150° F. Vacuum jacketed available. Compatible with liquid nitrogen, argon, oxygen, hydrogen, helium and LNG.
In cryogenic and liquefied gas applications, like LNG, it is essential to have precise temperature measurements throughout the process. This is particularly important when using ultrasonic flowmeters or differential pressure methods to measure the flow rate, as well as when determining the energy content of the liquid using a Raman spectrometer.
To achieve the necessary accuracy, it is crucial to adhere strictly to specific installation guidelines. However, these guidelines often conflict with the stability of the overall construction. Therefore, it becomes necessary to implement additional measures to ensure the mechanical strength of the construction while still maintaining the required level of accuracy in temperature measurement.
The typical process thermometer in the oil and gas industry is designed to withstand high mechanical forces in rough
environmental situations. The assembly consists of a standard measuring insert (e.g. the standard Pt100, RTD) in a bar stock thermowell made of stainless steel or Nickel alloy. The stability of the thermowell against the process pressure and the vortex induced vibration must be examined with a wake frequency calculation according to ASME PTC.1 In high load situations, this normally leads to a short but thick thermowell.2
In cryogenic applications short and thick thermowells lead to a conduction of heat energy through the metal from the ambient environment into the process, from where it is transported away by the process medium. As the primary temperature measurement element (like a Pt100) is placed close to the tip of the measuring insert, its final position is in a certain distance from the thermowell’s outside tip. Embedded inside this energy path, the RTD primary element can only indicate the value it has itself. The typical installation error in a cryogenic application
Dietmar Saecker, Endress+Hauser, Germany, maps out how thermometer assemblies can be optimised for usage for LNG.
is positive, the thermometer shows a value which is higher than the fluid temperature (Figure 1).
The amount of heat which is conducted into the process can be reduced by a thin thermowell, because it provides a smaller area for the heat conduction. In an electrical equivalent this can be understood as a higher resistance. Another equivalent is offered by the external insulation of the piping, which is reducing the ‘voltage’ of the heat current. Especially the vacuum insulation will help to operate the process wall at a deeper temperature level.
The inner process wall will be on a temperature level which is somewhere in between the environment and the process. It provides a starting point from which the gradient inside the thermowell starts in the direction of colder temperatures. According to this model the final mistake of the temperature measurement reading can be reduced by the installation of a longer thermowell.
That means the perfect thermometer for a cryogenic application would be long, thin, and installed into a vacuum insulated piping system.
Long and thin thermowells cannot offer the necessary strength against flow induced vibration and bending.
Long thermowells have resonance frequencies that can already be induced by slower flow rates. As a result, the traditional thermowell installation, with a fixed connection only on one side (according to ASME PTC)1, is not suitable for long and thin thermowells. A better solution could theoretically be provided by a so-called ‘velocity collar’. But this installation method fell out of the ASME standard because it only works properly if the thermowell collar (delivery of the instrumentation supplier) fits perfectly to the nozzle (delivery of the piping supplier). This usually does not work well enough, it either offers too much space to stop the vibration or it is so tight that the thermometer cannot be installed in the nozzle.
This installation problem can be avoided if the thermowell and the support structure, which protects the thermowell from any movement in x + y direction, are manufactured together with tight tolerances.
Typically, thermometers in cryogenic applications are exposed to drastic temperature shocks, when the liquified gas hits the assembly during the start-up phase of the plant (e.g. LNG ship bunkering). A long and thin thermowell will reduce its length suddenly and at a different velocity as the surrounding piping system.
That means a thermowell with velocity collar system fixed to the nozzle and to the thermometer at the same time would create immense pressure and tension forces during start-up and shutdown of a cryogenic plant.
Consequently, the design, which prevents the movement and vibration of the thermometer in the x and y directions, must at the same time provide the ability to compensate for the movement of thermal expansion in the z direction.
A long and thin thermometer assembly can be used in a cryogenic application only if it is protected against flow-induced bending and vibration in the x-y layer, while at the same time it still has the possibility to compensate heat shrinking effects. To achieve this, a basket with defined inner tolerances needs to be welded to the inside of the nozzle (Figure 3). This first part provides the space for a second part of this sliding basket in it.
This inner part can move up and down (limited by a screw) but, due to tight tolerances between both segments, means it cannot move ‘horizontally’. The inner basket provides an inner thread for the installation of the thermowell. Both parts of the basket have holes through which the gas can flow. This avoids a
Proservo NMS81:
Most accurate tank gauging instrument (±0.4mm) for SIL3 applications runs independent of boil-off gas.
We understand how you need to reduce complexities at your plant. Do you want to learn more? www.endress.com/oil-gas
You strengthen your plant’s safety, productivity and availability with innovations and resources.
Promass F 300: Mass flowmeter provides highest measurement performance for gases under demanding process conditions.
Field Xpert SMT77: Tablet PC allows mobile device configuration and plant asset management, even in hazardous areas Ex Zone 1.
pressure difference between the upper and lower parts that would hinder movement. However, there is also a second function of this design which can be described as a ‘temperature anchor’.
The moveable block is completely immersed in the LNG. The holes allow a small flow that refreshes the LNG in the cavity around the stem. The heat flow of the ambient temperature towards the tip is almost blocked as the LNG remains around the anchor. Excess heat would therefore lead to additional vaporisation of the LNG which would enhance the cooling of the anchor, until the equilibrium temperature at operating pressure is reached.
The final temperature gradient in measurement tip connected ‘below’ this anchor (according to Figures 1, 3, and 4) can be expected as a ‘vertical’ line at the process temperature, so that the influence of the sensor position inside the assembly becomes almost irrelevant. In total, the optimised LNG thermometer assembly operates similar to a thermostatic bath for calibrating temperature tips.
Additionally, it is suggested to install a pressure tapping point along the side of the outer nozzle. This position offers a connection to attach an LNG pressure measurement transmitter, bypassing the vacuum insulation piping system.
After welding the outer basket to the nozzle, the inner part can be inserted and fixed with the screw. After that, the nozzle can be completed and closed by welding the conical roof together with the attached pipe, which ends with a threaded connection at the top.
Now the vacuum insulating piping system can be constructed and welded around this inner structure.
The thermowell can be installed from the top. The threaded connection needs to be screwed into the inner part of the sliding basket. This will also lift this basket by a few millimetres. As a result, shrinking or expansion differences between the thermowell and the piping can now move freely up or down inside the inner basket relative to the outer part.
Finally, the long and thin measuring spring-loaded measuring insert can be installed into the thermowell, so the thermometer is ready for operation.
The spring-loaded measuring insert is pushing itself against the inner tip of the thermowell. The measuring insert can be de-installed during the process without any change of pressure neither from the LNG nor the vacuum insulated piping system. This makes it easy to perform regular re-calibrations of the measurement inserts.
In conclusion, the construction allows for easy installation and recalibration of the thermometer in cryogenic and LNG applications – ensuring accurate temperature measurement without compromising the integrity of the system. This optimised thermometer design from Endress+Hauser (patent pending) has been successfully installed at several positions inside the VSL’s LNG flowmeter calibration rig inside the Rotterdam harbour area.5
A summary of the four years of operation of these thermometers was published during the European Flow Measurement Workshop in March 2023.6
A comprehensive list of this article’s references can be found on the LNG Industry website at: www.lngindustry.com/special-reports
Measurement of density stratification is an essential component for forecasting and warning of potentially catastrophic rollover events in LNG tanks. Despite the proven value of density measurements, the particular challenges presented by the LNG environment calls for special instruments to maintain sufficient accuracy while operating at nearly -200˚C. Sensors for LNG measurements must also operate safely and reliably under these conditions.
Key requirements for an LNG density measurement system include:
Joe Goodbread, PhD, and Sunil Kumar, PhD, Rheonics GmbH, describe recent developments in density sensors for LNG tank conditions.
� Density accuracy 0.001 g/cc, resolution 0.0001 g/cc.
� Certified for explosion safety at LNG temperatures, as well in potentially explosive atmospheres in the vicinity of LNG equipment.
� Built-in temperature measurement accuracy better than 0.1˚C, resolution 0.01˚C.
� Compact form factor allowing easy installation on tank-monitoring equipment.
� Construction materials that remain durable and functional at cryogenic temperatures.
This article will consider some of the factors that influence the stability and accuracy of resonant density sensors, show how these sensors can be uniquely suited to measurement of LNG density under in-tank conditions, and describe some of the options that are available for integrating sensors into existing tank monitoring systems, including hardware and software options.
Resonant sensors measure density by means of a simple physical principle. The simplest mechanical resonant system is a mass suspended from a spring, where the top end of the spring is connected to a massive support structure (Figure 1). If one pulls on the mass and then releases it, it will bob up and down with a frequency determined by the elasticity of the spring and the weight of the mass. The stiffer the spring, the faster it will oscillate. The more massive the weight,
the slower it will oscillate. If this simple device were immersed in a tank, one could potentially measure the density of the LNG in the tank.
When the mass of the weight is increased, the oscillation frequency decreases, inversely proportionally to the square root of the mass. If the mass is immersed in a fluid, it must push fluid ahead of it in order to move – think of a swimmer kicking and stroking to push water mass ahead of them, or the force of impacting the water surface when diving off a board. The mass of the fluid that the weight pushes ahead of it depends on several factors, the most important of which is the shape of the weight. The greater the frontal area of the weight compared to its total mass, the greater the effect will be on the frequency. A flat plate will experience a greater change in frequency than a slender rod of the same weight.
The second factor is the spring stiffness. In order for the frequency of the resonator to be an accurate measure for the fluid’s density, the temperature of the spring must be constant and accurately known. For materials such as 316L stainless steel, the temperature dependence of its spring constant is both stable and well known. Therefore, for a given mass and a spring whose stiffness is a known function of temperature, its resonance frequency depends only on the density of the fluid and the temperature of the spring. For this reason, it is essential to have an accurate temperature measurement in intimate contact with the resonator in order to achieve sufficiently accurate density measurements.
A third factor that can contribute to the accuracy of a resonant density measuring system is the way that the resonator is connected to its surroundings – in this simple model, the support from which the spring is hung. For this resonator, the spring exerts a force on the suspension. Unless the suspension is extremely stiff and massive compared to the resonator spring and weight, the suspension will also influence its resonance frequency in ways that are difficult to quantify.
The Rheonics SRD-LNG has a balanced torsional resonator as its sensing element. The business end of the sensor is the wing-shaped tip mounted on a slender tube that is anchored in the probe body. This tip is caused to vibrate around the axis of the tube – a torsional vibration – which causes the tip to displace fluid ahead of it, as shown in Figure 2. This displaced fluid, together with the torsional inertia of the tip, corresponds to the weight in a simple harmonic resonator. The denser the fluid, the greater the mass of fluid that the torsionally vibrating tip displaces. As in the simple resonator, this decreases the frequency of the torsional resonator.
The vibrating tip is mounted on a thin-walled stainless steel tube, which serves as the spring in the resonator. Its elasticity depends on the temperature of the fluid in which it is immersed. The lower the temperature, the higher the frequency. These are the only two factors that influence the resonator’s frequency for a very low viscosity fluid such as LNG. So, if the temperature of the resonator is known, then its measured frequency can be adjusted for its actual temperature, and there is a direct measure for the fluid’s density.
By knowing how the resonance frequency depends on temperature, the accuracy of the temperature sensor that is
necessary to achieve the specified density accuracy can be determined. Taking these two factors into account results in a density accuracy of at least +/- 0.001 g/cc and a resolution of better than 0.0001 g/cc for the SRD-LNG.
The compact size of the SRD-LNG offers an advantage in density accuracy in this aspect – due to its small size, the temperature of the entire resonator is very close to completely uniform, meaning that the temperature measured at the tip is an accurate predictor of the temperature correction of the frequency.
Finally, the most important feature of a resonant sensor is its mechanical connection to the system in which it is installed. Many resonant sensors require very massive bodies to counteract the forces generated by the vibration of the resonator. And a massive body means that it is very difficult to ensure uniform temperature throughout the whole resonant measuring element. The SRD-LNG’s compact construction is made possible by a patented symmetric resonator construction that makes the sensing element self-balancing – the torsional vibration of the sensing tip is balanced out by a second mass, in the body of the probe, that oscillates in the opposite direction to the tip, so that the vibrational forces are nearly balanced at the point where the resonator joins the body (covered by US Patent 9,267,872).
This construction, besides making the sensor insensitive to how it is mounted, guarantees a uniform temperature for the whole resonator system, permitting extremely accurate temperature compensation and very high stability,
repeatability and accuracy of the density measurements. It is possible to obtain an overall density accuracy of better than 0.001 g/cc when the SRD-LNG is completely immersed in LNG.
A final consideration is the method used to determine the resonance frequency of our density measurement resonator. One way is to displace the weight and measure the frequency of oscillation when the weight is released. An alternative –and more accurate – method is to drive the resonator with an oscillating force and use its response to adjust the frequency of the driving force – essentially letting the resonator control its own excitation frequency.
Looking at the response of the SRD-LNG as a function of frequency (Figure 3), it is clear that its amplitude peaks at its resonance frequency. At the same time, the phase of its response referred to the driving force goes through a transition of 180˚, with a value of exactly of 90˚ at its resonance frequency. When the density increases, both the amplitude and phase curves are shifted to lower frequencies. These characteristics enable the proprietary SRD-LNG electronics unit to keep the sensor operating at its resonance frequency, to track changes in density, and together with the built-in temperature sensor, to correct the measured frequency for temperature effects, and to calculate the actual value of density to better than 0.001 g/cc.
The company’s SRD-LNG’s proprietary electronics unit is outfitted with a variety of interfaces permitting connection to the operator’s data collection, control, and warning systems. These include USB, Ethernet/IP, Modbus TCP, Profinet, Modbus RTU, and 4 – 20 mA analogue outputs with HART. The SRD-LNG is delivered with a software package that simplifies monitoring and logging of the sensor’s output signals. In addition, the electronics unit is fitted with a memory card that functions as a system historian, capable of recording months of continuous data that can be accessed over the electronics unit’s USB connection.
The SRD-LNG for LNG applications is certified intrinsically safe for installation in Zone 0 hazardous areas. Both ATEX and IECEx certificates are supplied with each unit. Intrinsic safety is guaranteed by the very low operating voltage and current of the devices, in addition to a relaxed ingress protection (IP) rating of 54. The probe is hermetically sealed and constructed entirely of 316L stainless steel, which is immune to embrittlement at cryogenic temperatures. If the probe is connected through the specified Zener diode barriers, it is safe for operation in Zone 0 with IECEx specification (Ex ia Ga IIC Tx X) and ATEX specification (II 1G Ex ia IIC Tx X).
Density sensors, such as Rheonics’ SRD-LNG, can offer innovative sensor technology for accurate and reliable measurement of LNG density. The compact size and immunity to mounting conditions make the company’s sensor simple to integrate into either new designs, or existing measurement systems in marine and onshore LNG installations. Its large assortment of data interfaces makes it easy to connect to virtually any data and control system, and it is certified under both ATEX and IECEx norms to be intrinsically safe, even in the case of accidental mechanical damage.
LNG is a critical fuel supporting all aspects of the energy transition and the energy trilemma. The trilemma being the summary of the three challenges faced by energy supplies, namely sustainability (decarbonising energy sources), security (ensuring the reliability of energy supplies), and affordability (minimising the costs of energy to consumers). LNG provides many of the solutions to these challenges.
With well-established production and distribution methods that are flexible, reliable, and affordable, this tried-and-tested, energy dense,
Mike Shepherd, Alderley, UK, outlines how dynamic metering can maximise the value and efficiency of LNG.
and globally transportable fuel is the go-to energy solution. The flexibility of its supply being highlighted by how LNG companies were able to deliver an additional 66% of LNG to Europe in 2022 in the absence of Russian pipeline gas.
LNG is the transition fuel that can support the move away from more carbon intensive energy sources such as coal and crude oil; it is the energy the world needs today, and what the world will need for decades to come. Therefore, accurate measurement is key to quantify and manage the opportunity for LNG in the energy transition.
With the increasing global demand for LNG, a global drive to reduce emissions, and a need to maximise the benefits from all available energy sources; the question remains: are the measurement processes used for LNG the most suitable for today’s rapidly changing environment?
The primary measurement unit for LNG is its energy value, and confident analysis of the chemical properties of LNG is essential. This is best done using online automated gas chromatography techniques as part of an integrated dynamic metering solution. The gas chromatograph will automatically calculate the calorific/energy value of the LNG as it is loaded onto the tanker via the measurement system.
Online gas chromatography of LNG has been a challenge in the LNG industry as the super cooled liquified gas needs to be rapidly warmed to convert it into a representative gas sample, to pass through the
gas chromatograph in order to determine the quantities of methane, propane, butane, etc. This is so an accurate energy or calorific value can be calculated; however, achieving a truly representative sample has been problematic.
Fortunately, recent innovations and improvements on the design of specialised LNG sampling systems have overcome many of these issues, however, the pursuit for accurate LNG measurement performance encompasses more than the use of high precision analytical instrumentation.
Taking into consideration the significant temperature challenges of transporting cryogenic LNG at approximately -162˚C, particularly in sometimes plus 50˚C environments, the key components for an effective measurement system are:
� Careful mechanical and insulations designs.
� Appropriate isolation philosophies.
� Suitable instrumentation selection.
� Robust automation and controls.
� A fully integrated dynamic metering system.
Dynamic metering, also referred to as live flow measurement, plays a critical role in the accurate measurement and control of all forms of media in the energy industry, yet it is under-utilised in LNG applications.
It is well recognised that metering systems are the cash register of most global energy operations, however, dynamic fiscal measurement is also critical to safety, operational efficiency, regulatory compliance, and asset management, as well as being a lever to support the deployment of digital and automation technologies which can make dynamic metering an indispensable tool in the LNG industry.
A typical dynamic LNG measurement system is shown in Figure 1. In this representative diagram, the fiscally measured raw feed gas is delivered into the LNG processing train, where the refrigeration and processing is done to chill the gas into LNG, before progressing through to the storage tanks and ultimately loading onto the tanker for international sale.
During this LNG process, there can be unquantified hydrocarbon losses through flaring, the unmeasured consumption of gas for power generation and general fugitive emission losses, etc. – losses that a proper integrated measurement philosophy, with its associated automation and control systems, can help to quantify and minimise.
Once the LNG production process is complete, the super chilled LNG is measured and stored in large heavily insulated tanks. At this point there is inevitable warming of the LNG in the tanks and the consequential release of boil-off gas (BOG) which needs to be controlled and
measured whilst it is recirculated into the process train for re-refrigeration.
Normally, the point of fiscal measurement is on the pipelines from the tanks to the tanker loading system as this is where the effective custody transfer and ownership change takes place. During the loading process, the tanker is chilled and filled, and the consequential BOG is recirculated back into the LNG train for refrigeration once again.
Throughout the loading process, automated sampling of the LNG will be conducted by online gas chromatography to measure the caloric value of the loaded LNG – calorific value being the primary method of selling a cargo.
Dynamic fiscal measurement of the loading LNG and BOG returns is automatically calculated to ensure that the final stored volumes are correct once loading is complete.
Dynamic fiscal metering systems provide highly accurate live measurements of LNG flow rates, composition, and energy content. This precision ensures proper billing and custody transfer, and minimises revenue loss and disputes
trustworthy data for financial transactions and decisionmaking processes.
Safety is paramount, and dynamic metering systems can contribute to the safety of LNG operations by providing
Furthermore, real-time data from dynamic metering systems facilitates emergency response planning, ensuring the safety of personnel and surrounding environments.
Dynamic metering systems offer significant benefits in terms of operational efficiency for LNG facilities. Real-time data on flow rates, composition variations, and energy content allow operators to optimise processes and ship loading systems, and reduce venting, boil off gas, and general poor performance. By closely monitoring and analysing flow rates, operators can identify and rectify inefficiencies, such as inappropriate pressure drops, leaks, or bottlenecks, and this data can be used to improve overall system performance.
The LNG industry is subject to stringent regulations and quality specifications. Dynamic fiscal metering ensures compliance with these regulations and contractual obligations.
Accurate flow measurement guarantees adherence to contractual terms, preventing disputes, and potential financial penalties. Moreover, precise measurements of energy content enable compliance with environmental regulations and emissions standards, promoting sustainability and minimising environmental impact.
Dynamic metering systems equipped with data logging capabilities also facilitate the generation of comprehensive audit trails, simplifying regulatory reporting, and compliance verification processes.
Dynamic metering systems play a crucial role in effective asset management for LNG facilities. By continuously monitoring flow rates, pressures, and temperatures, operators can identify abnormal operating conditions, diagnose equipment malfunctions, and optimise maintenance schedules. Timely identification of issues helps prevent catastrophic failures, reduces downtime, and extends the lifespan of critical components.
Additionally, dynamic metering systems provide valuable data for predictive maintenance strategies, allowing operators to plan maintenance activities proactively, optimise resource allocation, and maximise the operational availability of their assets.
Over the years, dynamic metering technologies have witnessed significant advancements, enhancing their performance and reliability in the LNG industry. Some notable technological developments include:
� Digital signal processing: Advanced digital signal processing algorithms have improved the accuracy and stability of flow measurements. These algorithms enable compensation for temperature and pressure variations, enhancing the reliability of the measurements.
� Multiphase flow measurement: Multiphase flow meters enable the measurement of gas, liquid, and solid phases simultaneously, making them potentially suitable for the measurement of LNG flow as there can be instances where there is both a gas and a liquid flowing through the pipework. These meters employ advanced algorithms to separate the individual phases and determine their respective flow rates accurately.
� Non-intrusive measurement techniques: Non-intrusive measurement techniques, such as ultrasonic flow meters and optical-based sensors, provide accurate flow measurements without physically contacting the fluid. These techniques minimise pressure drops, which is crucial for stable LNG measurement, ensuring uninterrupted and reliable measurement.
� Integrated digital automation and control: Dynamic metering systems have become increasingly integrated with automation and control systems, enabling seamless data integration, remote monitoring, and control. This integration allows for more efficient operation, data analysis, and decision-making, leading to improved overall system performance.
With the increasing emphasis on maximising value – achieved through enhancing efficiency/reducing costs – industries, including the hydrocarbon industries, are increasingly turning to the automation of as many processes and procedures as possible.
Automation provides the opportunity for real-time performance and process monitoring for operators and technicians. This supports effective and efficient control through live monitoring of measurement and process events, better utilisation of resource through informed decision-making, and facilitates condition and performance-based maintenance routines that ensure the optimum ongoing integrity and performance of assets and equipment.
In dynamic metering systems, much of the automation capability is managed by the supervisory computers. This provides a platform for integrating the communication interfaces; hosting the HMI, remote operated valves and controls interface via graphical representations of the metering package; numerous reporting systems; and analytical packages such as condition-based management, instrument validation and calibration, and performance-based maintenance management systems, all of which are crucial to gain a full understanding of the measurement system.
Energy operators, producers, and distribution companies all face the same challenges: How do companies maximise efficiency and performance? How do companies reduce their costs and emissions?
The Fourth Industrial Revolution is shaping every aspect of life through Cloud computing and artificial intelligence. Many modern dynamic measurement systems
and their instrumentation are digitally enabled, however often these data sources are underutilised. By connecting physical assets such with digital systems, businesses can generate accurate insights, respond in real-time to challenges, perform remote surveillance, and become more efficient. This is also true for the huge energy sectors – and dynamic metering is potential solution for key data sources having flow, pressure, temperature, and process composition available in one system.
Seamlessly interfacing with dynamic metering systems and data transmission points, intelligent digital flow measurement solutions, such as Smart Asset Management from Alderley, bring all flow measurement data together, and, through powerful and proprietary intelligent calculation tools and cloud-based processing capabilities, transforms measurement data into remotely accessible insight.
This helps operators to improve efficiency and performance, reduce costs, and reduce emissions by:
� Providing real-time insight on an assets’ performance, including emissions and carbon dioxide calculations.
� Proving flow measurement system performance and compliance through technically defensible data and traceable and auditable calculations.
� Supporting decision-making and resource allocation through live, remotely accessible updates and performance modelling.
� Reducing unproductive and unnecessary labour costs by enabling skilled engineers to focus on improving performance rather than collecting and assessing data.
� Increasing reporting speed and accuracy, including the validation of production reporting to help speed-up customer invoicing and improve transaction times and cash flow.
� Helping operators to maximise maintenance windows through predictive and performance-based maintenance routines.
Dynamic metering of LNG offers numerous benefits to the energy industry, ensuring accurate measurement, enhanced safety, operational efficiency, regulatory compliance, and improved asset management. Technological advancements have further improved the performance and reliability of dynamic metering systems, making them indispensable for the LNG sector.
As the LNG industry continues to grow and evolve, dynamic metering will play a pivotal role in optimising operations, increasing safety, and driving sustainable practices. By embracing the advantages of dynamic metering technologies and leveraging their full potential through digitalisation and automation, LNG operators can achieve higher levels of efficiency, reliability, and profitability in their operations.
Two concepts: Direct Reliquefaction or Subcooling
• Plug and play modular design
• Turn-key projects
• Cost efficient redundancy to meet uptime requirement
• Energy efficient Stirling cycle
• Small footprint 1.6 sqm (17,2 sqft) per unit
Stirling Cryogenics
+31 40 26 77 300
info@stirlingcryogenics.eu
www.stirlingcryogenics.eu
ethane is a potent greenhouse gas (GHG), and one that significantly contributes to climate change – its impact is more than 80 times greater than carbon dioxide (CO2) over a 20-year period. It is therefore unsurprising that minimising methane emissions has become a priority for many industries that utilise it, particularly the shipping industry.
In recent years, the shipping industry has built an increasing number of ships powered by LNG – so much so in fact, that most of these ships will use LNG as an energy source by the end of the decade.
While methane converts to carbon dioxide and water when burnt completely, unburnt methane can enter the atmosphere directly, negating the efforts of reducing emissions in the first place. The shipping industry faces a serious challenge in measuring and tackling this ‘methane slip’. Technologies to address methane slip exist, but the problem cannot truly be tackled without knowing the extent of it. To reduce methane emissions, they need to be measured accurately.
Many in the shipping industry see LNG as a crucial transitional fuel, bridging the gap between carbon-intensive oil, and future zero-carbon alternatives which are not yet commercially viable.
Using LNG as a fuel helps shipping address environmental concerns – shipping currently produces around 3% of the global CO2 footprint – and also comply with stringent emission regulations. The International Maritime Organization (IMO), the UN agency that regulates shipping, has pushed for cleaner marine fuels. However, there are also strong commercial and societal pressures across the value chain to accelerate the reduction of GHG emissions from shipping.
LNG offers several unique advantages compared with traditional marine fuels. Unlike heavy fuel oil and marine gas oil, LNG combustion not only produces lower levels of CO2 but also almost eliminates sulfur oxides and particulate matter emissions, both of which are areas where shipping is tightly regulated.
Unfortunately, an uncomfortable truth which stands in the way of these advantages being fully realised must be faced.
r n g iThe effectiveness of LNG as a ‘bridge’ fuel towards a net-zero future diminishes considerably if the issue of measuring and abating methane emissions remains unaddressed. Shipping has made great strides over the past few decades – developing technologies for engines and exhaust systems, among others – which have the potential to slash emissions. But the industry is still sailing blind without transparent measurement.
Steve
MAMII
Uberoi,
of Public Affairs, MiQ, analyse how the shipping industry is rising to meet the challenge of methane slip.
Measuring and categorising methane slip will add vital nuance to discussions around the benefits and applications of LNG. Companies and providers must have a consistent way of measuring methane emissions which will allow society, and policymakers, to understand LNG’s true environmental impact.
The concept of well-to-wake considers methane emissions from the entire supply chain, starting from the well where natural gas is extracted, to the point of combustion in ships’ engines (the wake). This offers the chance to empower markets and ultimately channel investments to new technologies that can reduce methane slip, and aid other transition fuels.
Well-to-wake analysis will also help identify critical points in the supply chain where methane emissions can be reduced, leading to a more accurate evaluation of LNG’s overall environmental impact. By focusing on emissions across the entire lifecycle, industry stakeholders can implement targeted strategies for emissions reduction and promote sustainable LNG adoption.
And for shipping, maintaining tight control over methane emissions is critical to ensure that LNG’s overall GHG footprint is reduced as much as possible in comparison to conventional marine fuels.
The Global Methane Pledge, embraced by more than 100 countries at COP26, called for a minimum 30% reduction in global methane emissions by 2030 compared to 2020 levels –a pivotal step in combatting climate change.
But to address methane emissions effectively, companies must possess a detailed understanding of their emission sources and employ robust mitigation practices and technologies.
Certification initiatives play a crucial role in ensuring the accuracy and transparency of methane emissions measurement along the LNG supply chain. Independent certification standards are needed to assess and grade gas based on their methane emissions performance. These certifications will incentivise businesses to improve their emissions records and adopt measures to mitigate methane slip.
It is crucial that as an industry, and across the wider maritime value chain, certification standards that cover the entire production facility are embraced, including all equipment and wells. The transparency provided by a credible certified gas marketplace will remove barriers to achieving climate change goals and deliver economic opportunities.
In 2022, the Methane Abatement in Maritime Innovation Initiative (MAMII) was set up as a cross-sectoral technology accelerator to measure and manage methane emissions.
MAMII is led by Safetytech Accelerator and its members include major maritime and energy players such as: Capital Gas, Celsius Tankers, CoolCo, Global Meridian Holdings, Mitsui OSK Lines, TMS Cardiff Gas, and United Overseas Management. Others include Carnival Corporation & Plc, Lloyd’s Register, Knutsen Group, Maran Gas Maritime, Mediterranean Shipping Company, Seaspan Corporation, and Shell.
The calibre of membership and rapid growth in its first year demonstrates the industry’s determination to address the methane emissions challenge. But its immediate key learning was that shipping needs a definitive standard to track both the volume and the well-to-wake impact of methane slip.
If something is measured, it can be understood. By differentiating producers based on their methane performance, certification standards will incentivise businesses to improve their emissions records, benefitting both the climate and their own operations.
Emissions measurement organisation MiQ, for example, has developed a global solution to combat methane emissions. It provides a not-for-profit and independently audited certification standard that grades gas based on its methane emissions.
Its ‘standard’ is a rulebook used by independent, highly qualified third-party auditors for assessing how well a producer or facility is doing in terms of managing methane emissions from its operations. These auditors provide an A to F grade for methane emissions to the facility they are certifying, based on methane intensity, monitoring technology deployment, and company practices, which is then reviewed regularly.
Innovation such as this is needed to create transparency on methane emissions. Ultimately, it will mean that buyers, investors, regulators, and other stakeholders can finally compare the environmental impact of different batches of natural gas, which will be crucial to unlocking a more competitive and beneficial LNG market.
The integrity and credibility of the certified gas market rely on transparency. Buyers must have confidence that the natural gas certificates they acquire or trade are credible and represent genuine efforts to reduce methane emissions.
Facility-level certification ensures that the entire production facility, including all equipment and wells, undergoes rigorous assessment and meets the independent certification standard. Adopting an independent certification standard across all aspects of a facility helps ensure that transparency is fostered, paving the way for a credible certified gas market that benefits both the planet and offers competitive advantage to the best prepared.
The failure of certain carbon offset markets has taught us valuable lessons. Cutting corners and allowing cherry-picked certifications can rapidly erode the progress made in building markets. To ensure the long-term success of the certified gas market, it is crucial to prioritise accuracy, transparency, and comprehensive certification practices. This approach will effectively address methane slip, reduce GHG emissions, and foster economic growth.
The challenges posed by methane slip in the shipping industry demand immediate attention. And to address this issue effectively, shipping will need accurate measurement tools to gauge the scale of the problem. The industry knows it has the technology to tackle this accordingly.
Comprehensive certification practices are equally important, as exemplified by MiQ, to encourage methane emissions reduction and building a credible certified gas market for the shipping industry and the future of the global energy value chain.
By prioritising transparency, integrity, and facility-level certification, the maritime industry can navigate its way to a more transparent LNG future.
Admittedly, at first glance, you can’t tell what’s inside the new VEGAPULS 6X radar sensor: A high-precision level instrument that doesn’t care if its measuring liquids or bulk solids. Only its colour gives you a hint that it’s going to be great to use. VEGA. HOME OF VALUES. www.vega.com/radar
Mike Hastings, Brüel & Kjær Vibro, Denmark, highlights how costly air cooler failures and consequential downtime can be avoided by monitoring these machines with a simple yet effective predictive monitoring solution.
he air-cooled heat exchanger, or fin-fan, cools a medium (such as natural gas) through finned tube bundles to maximise the surface area for cooling. This optimises heat removal efficiency and ensures a compact design.
Air as a cooling medium is more cost-effective than using water. There are no detrimental thermal effects on rivers and lakes, and dry air is non-corrosive and there is an endless supply. The energy and operation requirements to cool with air is also less than what is offered by other cooling media.
The air-cooled heat exchanger is used in a wide range of petrochemical and power industries, often in groups of several hundred units for a single process. In the oil and gas sector, it is widely used in LNG production, refineries, and natural gas processing. Air coolers can be in hazardous and non-hazardous areas.
Air coolers are generally motor driven by belt, but can also be connected to a gearbox. Many times, control is done through a variable speed motor.
There are various physical configurations for the air cooler, such as vertical or horizontal position, and the air supply can be by forced air or induced air draft. For a forced draft air cooler, the fan is located below the bundle and
pushes the across the finned tubes. For an induced draft configuration, the fan is located above the bundle and sucks air through the tubes. There are advantages and disadvantages for both configurations, and the optimal choice depends on the application.
The induced draft configuration protects the bundles from temperature changes due to the weather and has the added advantage of having a natural draft effect below. On the downside, the induced draft air cooler requires more power if the medium is fairly hot. Moreover, the fan blades are also not so accessible for maintenance. The forced draft, however, provides better access to the fan and upper bearing for maintenance, but the bundle is completely exposed to weather elements.
There are several factors that can influence how efficiently the air coolers provide optimal cooling capacity. From an operational point of view, even weather conditions can
influence the efficiency of the air cooler performance, such as outside ambient temperature, wind speed, and direction.
Deposits is another factor, and they can form both inside and outside the tube bundles and on the blades. These deposits will also reduce the cooling capacity. If a tube is blocked by deposits, this can lead to a leak.
Many air cooler failures, however, can be attributed to dynamic mechanical faults, such as loose belts, defect rolling element bearings, and imbalance.
Defect bearings can affect how efficiently the air cooler is operating. For an induced-draft machine, if the fan shaft bearings fail catastrophically, the entire fan/shaft assembly could collapse on the tube bundle, causing extensive lost production and repairs. Bearings can fail prematurely due to a number of factors, such as lack of lubrication, contamination, prolonged operation with imbalance/misalignment, etc.
Imbalance (caused by blade deposits, faulty bearings, or other damage) can further stress the bearings and other components and lead to a premature failure of these components.
Vibration monitoring is the primary method for fault detection for air coolers. The potential failure modes that can be detected by vibration include imbalance, misalignment, belt drive defects, motor defects, fan deposits/damage, lubrication problems, and bearing faults.
A machine condition monitoring strategy is typically employed for this purpose. Protection monitoring can be used to avoid a catastrophic failure, but the trips can be untimely and numerous for such a large installation with many air cooler banks, which is no benefit for reducing downtime and maintenance costs. Early fault detection by condition monitoring allows maintenance to be cost effectively planned ahead of time, especially if there are several air coolers that require maintenance at nearly the same time.
For the number of potential failure modes that can be detected by vibration, perhaps the rolling-element bearing (REB) faults are the most difficult to detect at an early stage of development because of their relatively low energy contribution to the overall vibration signal. The slow speed of the air coolers makes detection even more difficult.
Typically, there are two accelerometers permanently mounted on each air cooler in one of the following ways:
z One accelerometer on the motor and the other on one of the bearings.
Function Measurement/plot
Narrowband fault detection
Blade passing frequency (BPF) and harmonics
Tracking filters
ISO overall
Residual value (RV) – RMS of BPF sidebands
z One accelerometer on each bearing, where the bearing closest to the motor can also pick up motor faults (Figure 2).
Broadband fault detection
High frequency crest factor (HFCF) –Peak/RMS
Envelope condition unit (ECU) – FFT filter 3k-10kHz, RMS of Envelope filter 1-300Hz
Frequency spectrum
The optimal sensor mounting configuration depends on the application. Whatever the case, both of these sensor installations are intended to provide a comprehensive monitoring capability for the most important air cooler faults. In the case of Figure 2, the specialised bearing fault detection and diagnostic measurements for this purpose are shown in Table 1. It is important to remember, however, that accurate instrumentation and sensors must be used for any low-speed application. An example of a bearing fault diagnosis is shown in Figure 3.
Diagnostic plots
Envelope spectrum
Time waveform
Air coolers can have a number of different operating states due to climatic conditions and process control. Wind speed
and direction, variable frequency motor drives, auto-variable fan pitch and other climatic and control schemes can vary the load and speed of the fans considerably, consequently resulting in entirely different vibration signatures. Therefore, this can make it difficult to get a repeatable measurement if these operation and process factors are not taken into account. As a result, it is important for the monitoring system to allow for individual alarm limits to be set up for different speed and process operating regimes, thus giving early fault detection without the risk of false alarms.
There are a number of different condition monitoring systems that can provide the monitoring techniques described in this article, and these can be grouped according to how the data is stored and managed:
z Off-premise monitoring system: Monitoring hardware (if wireless sensors are used) and software is remotely located, as well as the database servers.
z Enterprise based on-premise monitoring system: Historian database servers.
z Standalone system: Proprietary database and monitoring server, either permanently installed or portable monitoring solution.
Aside from data management, each of these solutions can offer similar or different levels of fault detection techniques, diagnostic insights, automatic decision support, services, ease of implementation, etc.
The merits of each monitoring solution depend on the application, but it can be summarised that early fault detection and diagnostics is imperative no matter which solution is selected. This gives lead-time for planning maintenance.
Some end-users prefer using portable data collectors for these non-critical or semi-critical machines, but it is dangerous, tedious work for operators to climb up on the structure and take measurements for so many machines. Moreover, portable devices cannot detect fast developing faults such as lack of lubrication.
Others may consider using a permanently installed system, either as a field monitor or as a rack-based system, but decide the capital investment and installation cost is too expensive. Moreover, very basic or outdated legacy systems may not even have the proper measurement techniques needed for giving early fault detection or reliable diagnostics.
For an application that has several hundred air cooled heat exchangers, the off-premise solution with wireless sensors offers clear advantages over the other solutions with regards to capital investment and implementation (i.e. installation, configuration, commissioning, upgrade).
Moreover, diagnostic support together with actionable insights based on artificial intelligence and verified by specialists can be remotely offered as well, which can compete even with the rack-based systems.
For applications that require on-premise installations for fault detection and diagnostics, the standalone proprietary system and the historian-based data management system offer clear advantages. The advantages with a historian-based system is that there is no duplication in servers and more data is accessible. Historian-based condition monitoring and analytics is also easier to access and more transparent than through a proprietary system.
If there is no historian, then the standalone proprietary system, as a field monitor or rack-based system is the best solution.
No-one knows PCHEs better than Heatric. Since 1989 our innovative Printed Circuit Heat Exchanger (PCHE) has been designed to enable the latest pioneering applications and cutting-edge processes. Future-proof your process with Heatric.
Confidently test open-end pipe, pipelines & pressure vessels without welding, and isolate & test flange-to-pipe weld connections with GripTight Test & Isolation plugs from Curtiss-Wright.
• Standard pressure ratings up to 15,000 PsiG (1034 BarG)
• Patented gripper design for increased safety in high-pressure applications
• Eliminate welding end caps for pressure testing pipe spools and piping systems
• Test flange-to-pipe welds without pressurizing entire systems
• Isolate & monitor upstream pressure and vapors during hot work
• ASME PCC-2 Type I, III & IV Testing Devices
The maritime industry is currently on a mission to reduce greenhouse gas emissions. Ship owners are seeking short-term solutions, such as running vessels on reduced carbon fuels like LNG, and long-term solutions that allow for next-generation fuel alternatives. There is a clear drive to improve fuel efficiency, to reduce the cost and environmental footprint of vessels. The International Maritime Organization (IMO) and the EU have also enacted new wide-reaching regulations that have reduced emissions but increased shipping owners’ costs.
According to DNV,1 the trend of ordering larger ships with alternative fuel propulsion is continuing, with fossil LNG being the dominant fuel. Approximately 5.5% of the total gross tonnage of vessels in operation in 2022, and one-third of the gross tonnage on order, can or will be able to operate on alternative fuels. This statistic also includes LNG carriers. Furthermore, there has been a growing interest in ammonia as an alternative fuel. However, the key emission concern with LNG is methane (CH4), while nitrous oxide (N2O), also known as laughing gas, is an emission concern from ammonia-fuelled engines.
Basic calculations are the standard practice for monitoring and reporting emissions from shipping today. However, forward-thinking ship owners will seek ways to reduce their carbon impact and minimise costs.
Direct measurement provides more accurate results compared to calculations, which rely on assumptions and estimates.
Roar Hernes, Tunable, Norway, explains how to go from guesswork to direct measurement in regards to greenhouse gas emissions in the maritime industry.
If only carbon dioxide (CO2) is within the scope of calculating emissions, the fundamental explanation is logically fuel consumption. The actual CO2 emissions are, however, dependent upon the engine’s performance and rate of combustion at different loads. For LNG and ammonia-fuelled engines, where the emissions concern is CH4 and N2O, it is much more complicated and challenging to find representative calculation factors to apply to all operational conditions. This is because these emissions are a direct result of the whole propulsion installation and how it is operated and not fuel consumption only.
Measuring emissions in real time provides immediate data that can be used to adjust operations, whereas calculations have limitations as they are based on assumptions and historical data. Traditional emissions calculations and reporting methods are often manual, complex, and time-consuming, requiring back-office employees to do most of the work. On the other hand, direct measurement can be mostly hands-off and automated, combined with a software data platform, with a fraction of the operational costs associated with emissions calculations. Finally, the most important benefit of access to real-time data is the opportunity to link the data to operational behaviour and implement immediate actions that can reduce emissions and fuel costs and improve the Carbon Intensity Index (CII).
Regulations such as IMO’s mandatory greenhouse gas (GHG) emissions reduction requirements mandate the use of direct measurement methods.2 The EU also explicitly allows for documenting, reporting, and verifying GHG emissions based
on direct measurements.3 As long as calculations are accepted for reporting emissions, the penetration of emission monitoring systems is expected to be relatively small. However, many ship owners are likely to adopt direct measurements once IMO makes it mandatory. For those looking to stay ahead of the curve, 2023 is the year to act and introduce direct measurements.
Measuring emissions builds transparency and trust with stakeholders, such as regulators, customers, investors, and insurance underwriters. Ship owners who measure and openly share their GHG emissions levels and the impact of different improvement initiatives are likelier to gain trust with key stakeholders and improve their operating margins over time.
Measuring emissions holds ship operators accountable for their GHG emissions and encourages them to adopt cleaner technologies and practices. In short, the old saying ‘you get what you measure’ will be proven true.
As the shipping industry is expected to deliver less GHG emissions, an obvious starting point on the journey is to start measuring the current levels and actions with the most significant saving potential for reducing GHG emissions and fuel consumption.
Various technologies can be used to measure emissions from ships. The most common is a continuous emissions monitoring system (CEMS): These systems can measure the emissions of GHG in real time. A CEMS system uses sensors to measure the concentration of the gases in the exhaust gas, and a separate flowmeter measures the flow. As new and alternative fuels are introduced, one of the key advantages of a CEMS system is that all relevant GHG and combustion gases can be detected.
An extractive system for sampling exhaust gas involves taking a sample of the exhaust gas and transporting it to an analyser. The sample is collected with a probe inserted into the exhaust gas stream, which draws a small amount of gas out of the stream and transports it to the analyser. The advantage of this system is that it allows for accurate measurement of the exhaust gas composition, since the sample can be analysed in a controlled environment within the analyser.
On the other hand, an in-situ system for sampling exhaust gas from ships involves measuring the composition of the exhaust gas directly in the exhaust stream, without taking a sample. This is usually done using a sensor placed directly in the exhaust stream.
The choice between an extractive and in situ system depends on the specific application and requirements of the measurement. In-situ systems
Johnson Matthey offers the PURASPEC™ range of premium performance absorbents for both mercury and sulphur removal.
Johnson Matthey’s PURASPEC 1065 sulphur removal and PURASPEC 1198 mercury removal absorbents are the solution to your impurity removal challenge:
• Reduces the cost per kilogram of impurity removal
• A comprehensive, expert service that takes care of all aspects of operation, maintenance, and disposal
• 25% higher impurity removal pick-up over its predecessor
• Reduces frequency of hazardous impurity bed changeouts
Johnson Matthey’s expert PURACARE ™ service takes care of all aspects of operation, maintenance, and absorbent disposal; for guaranteed peace of mind, from cradle to grave.
We are delighted to be exhibiting at Gastech this year. Please visit our team in the Hydrogen Zone, stand A422
are more likely to be preferred if the monitoring requirement is for a single parameter in a ‘clean’ gas flow. However, an extractive system allows for more flexibility in terms of gases to be identified and quantified.
The two most common methods to calculate the mass are using the known volume data from the engine or measuring the flow by differential pressure with a so-called DP transmitter. The best solution for an LNG carrier is a DP transmitter, which measures the differential pressure of the exhaust gas and uses the data to calculate the volume flowing through the stack. Combining the flow data and the gas concentration from the analyser provides continuous data on the mass emitted by the different gas components.
An LNG carrier would typically have six measurement points – two for the main engines and four for the auxiliary engines. To avoid having six independent analysers, the gas analyser system will typically include a stream switcher altering measurements between the different stacks. The number of sample points to connect to one gas analyser system depends on the measurement frequency required by ship owner and regulations. The ship will typically be installed with one or two analyser systems for an LNG carrier to cover the necessary measurements.
Gas analysers identify and measure the concentration of various gases in a mixture. Chief among these are analysers based on infrared spectroscopy.
In essence, infrared spectroscopy is the detection of the spectral ‘fingerprints’ of gases. Various molecules absorb infrared radiation at wavelengths that are characteristic of the chemical composition of the molecule, as radiation energy is
converted to molecular vibrations.The presence of a particular gas can be determined by scanning through the infrared spectrum and detecting the absorption level at wavelengths associated with that specific gas molecule.
The analyser to be integrated as part of such a system must include measurements of all relevant gases in the stream as they do interfere with each other.This is important both to get the real numbers, as well as ensuring that the ship is operated optimally,considering all emissions.All essential GHG gases should be monitored and reported, and the system should have the flexibility for upgrades to include emission gases expected to be part of the exhaust gas when new fuel types are introduced and adopted by the shipping industry.
The Tunable emission gas analyser uses infrared (IR) absorption spectroscopy.The analyser is designed for use with industry-standard cold-dry extractive sampling systems. It does not require any consumables or calibration gases.The sample gas is analysed directly as it flows through the optical path within the analyser.The measurement principle is illustrated in Figure 1.
A key component is a widely-tuneable micro-electromechanical (MEMS) filter capable of continuously scanning the wavelength of the infrared light from 3– 6 μm.Wide scanning allows all exhaust gas components of interest to be identified and quantified and minimises cross-interference.The MEMS chip is highly robust, has a long lifetime, and is insensitive to vibrations.Furthermore, the quick response of the MEMS filter enables dynamic changes in the mixture to be measured,even when sampling relatively small volumes.By introducing MEMS technology, it is possible to measure all relevant GHG gases, including carbon monoxide, carbon dioxide, sulfur dioxide, nitrogen monoxide, nitrogen dioxide, and methane, with only one analyser and no moving parts.This makes the technology highly robust to operate on vessels which are prone to heavy vibration.
The shipping industry will continue looking for ways to reduce emissions to save fuel and carbon tax costs.This process will require a better understanding of actual emissions and how different improvement initiatives contribute to the decreased production of GHG.Many software companies already focus on developing data analytics systems and performance improvement programmes.To take full advantage of these systems, it is critical to have access to reliable emissions data, which the ship operators only get through the installation of an online emission analyser.
1. ‘Maritime Forecast to 2050’, DNV, www.dnv.com/maritime/ publications/maritime-forecast-2022/index.html
Figure 3. Global warming potential measures the relative warming impact of one unit mass of greenhouse gas relative to CO2. Therefore, a global warming potential value of 28 means 1 t of CH4 has 28 times the warming impact of 1 t of CO2 over a 100-year timescale. Source: ‘AR5 Synthesis Report: Climate Change 2014’, The Intergovernmental Panel on Climate Change, (2014).
2. ‘2016 Guidelines for the Development of a Ship Energy Efficiency Management Plan (SEEMP)’, Marine Environment Protection Committee, (28 October 2016), wwwcdn.imo.org/localresources/ en/KnowledgeCentre/IndexofIMOResolutions/ MEPCDocuments/MEPC.282(70).pdf
3. ‘Regulation (EU) 2015/757 of the European Parliament and of the Council of 29 April 2015’, Official Journal of the European Union, (2015) https://eur-lex.europa.eu/legalcontent/EN/TXT/PDF/?uri=CELEX:32015R0757&from=EL
The LNG industry has experienced significant changes in recent years, with a shift towards fewer long-term agreements (LTAs) and a rapid rise in spot cargoes to 30% by 2017, after which growth in spot-trade slowed. This evolving landscape has created volatility and challenges for traditional business models in the industry. Furthermore, experts predict that peak LNG demand may occur as early as 2035,1 further intersecting new LTA’s. Also, there appears to be a reliability epidemic with 13% of global name-plate capacity off-line or approximately 600 cargoes missing from ADP’s each year.2,3
However, amidst these challenges, the application of digital transformation technologies offers promising solutions. Integrated operations, remote operations, digital twins, industry autonomous and other Industry 4.0 concepts can revolutionise the LNG sector by optimising efficiency, increasing reliability, reducing costs, and improving safety. In fact, Woodside’s successful 2022 implementation of remote operations at its Pluto LNG facility demonstrates that LNG liquefaction plants can be transformed to operate remotely and still achieve name-plate capacity: in the case of Pluto LNG 114% of name-plate.4
‘Nothing is certain but change’ is a well-known saying and indicates that the process of planning a transformation must itself change and transform as new scenarios occur that impact the LNG industry. Accordingly, a Maturity Model for Industrial Autonomous has been proposed by Honeywell CTO, Jason Urso5, to help envision, categorise, plan, and roll-out improvements to operations in industries similar to LNG. The vision may well stretch out to full autonomous operations which may appear to reach too far; however, the benefits result from advancing even small steps at a time.
Industry autonomous has parallels in daily life. There, it is fast approaching the
John Colpo, Marketing and Business
Development Director, Honeywell, identifies the key challenges faced by the LNG industry and the potential solutions provided by digital transformation technologies.
‘driverless’ car, where there also exists a tiered autonomous rating up to Level 5 full-self-drive (FSD). Per the left-hand side of Figure 2, think of the ‘car’ technology as separate solutions which, when working together, enable the driverless car.
Now think of the ‘LNG plant’ as having separate solutions which, when working together, enable autonomous operations. Industrial applications of autonomous look to integrate devices and systems, including machine intelligence to improve the overall business opportunity and improve the user experience for staff and stakeholders. Just as the autonomous car can drive one to their destination as well as a top racing driver and avoid accidents, industry autonomous also enables staff to perform and strives to avoid downtime and accidents better than any alternatives.
A significant cohort of the LNG community will have reached ‘controlled and optimised’ operations including the implementation of a centralised control room with a modern integrated control and safety system (ICSS), an CCR operator training system (OTS) and model-based advanced process control (APC). Accordingly, ‘intelligent operations’ is the next ambition.
A good place to start is maintenance, with it accounting for anywhere from 15 – 40% of operating costs.6 In addition, unplanned maintenance destroys more than 5% of industry LNG capacity7 and causes excess flaring. Leading LNG operators have recently moved towards reliability centred maintenance (RCM) with predictive maintenance, simplified equipment to reduce high-frequency maintenance activities, reduced overall staff counts, and implemented semi-annual campaign maintenance. In predictive maintenance, sensor measurements are combined with precise algorithmic formula to predict the exact just-in-time (JIT) moment when maintenance actions should be taken.
Integrating operations that are non-mission-critical is another transition that is part of this level. That includes co-locating staff who perform supervisory, planning, and activities that are performed on a daily to monthly frequency at a central location, such as head office. In the simplified ISA95 model (Figure 3), traditionally, each LNG asset would duplicate staff and technology stack all the way from field devices to ERP, or at least the level below ERP. Activities and systems at the upper levels are less mission-critical, hence the transition to centralised operations including co-location, consolidation, and sharing of skilled staff. To enable a consolidated team to operate over a wider scope of assets, it is advisable to remove high-frequency, data gathering activities and allow staff to focus on higher value tasks. Workflows and systems would be reviewed to achieve management-by-exception (MBE) principles. Arguably, Shell plc is the most visible champion of MBE in LNG and upstream industry with its exception-based-surveillance (EBS) regime8 becoming widely adopted as a key component of Shell’s WRFM process improvement and benchmarking regime.
Solutions to deliver significant improvements in LNG supply chain performance can also be platformed by intelligent operations, such as was achieved by QatarGas with the support of Honeywell.9
Remote operations is the current frontier where progressive LNG and upstream operations are piloting ever more complex assets for normally unmanned installations (NUI). Equinor’s Valemon Asset was recently at the forefront of complex assets that are NUI.10 Today, there is currently no FPSO (a type of large floating platform) that is completely NUI, nor is any baseload LNG liquefaction asset fully NUI. The current high-point for baseload LNG remote operations was achieved by Woodside’s Pluto LNG assets in 2022, where operations staff
were largely re-located and co-located in the Pluto remote operations centre (PROC), Moorditj Danjoo, approximately 2000 km in the family-friendly city of Perth, Australia.11 A recent paper by Woodside’s Remote Operations Manager indicates material benefits in the areas of location, with stronger corporate connections; family and lifestyle benefits, diversity benefits, training benefits, and digital technology benefits. The road to integrated operations was implemented in stages beginning with a ‘Pluto Support Centre’ in 2015 with many aspects shown in level 2 autonomous, a pilot remote operations lab in 2020 during the COVID-19 pandemic, trialling Level 3, and final ROC implementation mid-2022.
For LNG enterprises looking for similar transitions, it would a appear that a similar staged approach for change management would mitigate organisational and technical risks.
Key elements in the technology ISA95 stack requiring focus are the mission-critical and safety-critical systems indicated in the ‘control’ layer. To achieve remote operations, it is required to reproduce the HMI Workstations typical of integrated control and safety systems (ICSS) in the new location with similar performance characteristics, such as speed-of-response to alarms. If not already, the ICSS must be made to integrate all mission-critical and safety-critical systems including the distributed control systems (DCS), emergency shutdown systems (ESD) and fire and gas systems, as well as other integrated subsystems such as process CCTV, ECMS (electrical controls), downstream or upstream SCADA, subsea and so on. Leading ICSS systems, such as Honeywell’s Experion PKS®, can provide a ‘single pane of glass’ across multiple systems to simplify operations and training.
The human machine interface (HMI) workstations enable human operators to respond to process or equipment events
within seconds, whereas the underlying control devices operate automatically within milliseconds. Fortunately, it is not a requirement to relocate the control devices as the communications requirements would be challenging to achieve with present-day technology. LNG operators should look for ICSS technology that is easy to ‘divide and stretch’ across a wide area network (WAN) with sufficient resilience, fault-tolerance, and no-loss of history during communications upsets.
Equipment should be simplified further to remove high-frequency maintenance tasks; APC should be implemented to stabilise processes and equipment, resulting in lower operator loads and reduced production deferment events; and workflows should be reviewed to streamline using techniques such as operator role complexity analysis (ORCA). With fewer staff on site requiring multi-skilling and diminished specialisation, It is important to provide solutions to support workers performing their rounds with mobile applications that enable documentation, video, and analytical exchanges with both data systems and centrally located experts. OTS are generally implemented in LNG assets, but usually left to degrade. With consolidated staffing, it will become mission-critical to be able to quickly introduce new operators which can manifestly only be achieved with a high-fidelity digital twin OTS of the LNG processes, equipment, and control systems (DCS, ESD, etc.).
Enterprises with multiple similar LNG assets can benefit from consolidation of all IT and OT into a templated ‘single pane of glass’ view of each asset that allows for individual skilled staff to operate across assets with reduced effort and higher impact.
To this point, there has been little or no mention of the Industrial Internet of Things (IIoT) or Industry 4.0 as Level 4 is where this technology belongs. Due to a goal of IoT being ease-of-implementation, it should be expected that Level 4 solutions are going to be implemented ahead of lower level solutions to some extent.
The goal of Level 4, resilient operations, is to lock in gains, avoid deterioration over time, avoid dependence and failure on individual assets and people, and sufficiently build fault tolerance into not only automation controllers, networks, and computer servers, but even process equipment and staffs.
Duplication of equipment including computers is the traditional method of avoiding the consequence of failure of one node or component bringing down an entire train or asset. Large equipment could be prohibitively expensive to duplicate and so an n+1 approach may be used where smaller equipment is deployed in
parallel and only a small fraction of capacity is idle. Recently, the adoption of computer ‘virtual machines’ made this possible within IT infrastructure. Even more recently, Honeywell introduced HIVE® (Highly Integrated Virtual Environment) in Experion PKS that virtualises and makes re-assignable all aspects of the ICSS from servers, HMI, and controllers down to input/output (I/O) channels. Extensive adoption of cloud techniques also supports remote engineering, remote testing, and commissioning of ICSS. HIVE also supports a stretched version of ISA95 that approaches ‘edge to cloud’ architectures with optional mission-critical control being cost-effectively executed at the location of remote I/O channels adjacent to field devices.
Knowledge capture becomes key when consolidating staff, thus digital twins find even greater relevance to both on-boarding new staff, but also retaining knowledge as intellectual property. With fewer experienced staff, knowledge can be generated with advanced analytics that is possible with machine learning (ML) tools that are surprisingly easy to implement.
Of course, a greater IT footprint increases the cyber risks and tasks, so a step up of the deployment of cybersecurity solutions to mitigate and bring risk to acceptable levels is required.
Business process outsourcing (BPO) is another optimisation technique that is enabled by extensive cloud implementation. Industries adjacent to LNG, such as gas pipelines, have embraced BPO to a greater basis and proved the value that could be leveraged by LNG to the extend of outsourced hosting of ICSS/SCADA and even third-party control rooms12 and operations within.
Recent advances in remote operations and IoT solutions are actionable and proven. Immersive field simulators (IFS) that provide a 3D digital twin of the asset and equipment can feasibility be scanned at the asset and configured to provide training and route guidance for field workers. AI with ML is already available with LNG process and equipment templates. For example, Management-by-Exception at an LNG asset can be improved with Honeywell’s Forge Production Insights to provide predictive analytics for process deviations, guided root cause analysis (RCA), and several other tools, all supported by state-of-the-art AI.
Drones and robots continue to intrigue all stakeholders and many use-cases have been proven in LNG and upstream to support operations that would be difficult or dangerous for humans, such as inspections in areas rated hazardous. Several concepts for robotic loading arms for LNG ship and truck loading are currently under development.
FSD may possibly be achievable in complex LNG assets in the future, but the present frontier of local workers in a remotely operated facility would appear to be shrinking from 100+ and approaching the single digits, depending on asset complexity.13 For the present, some manual processes involving shipping.
Being autonomous at all levels also has benefits and applications in emissions reduction strategies where solutions can be implemented to optimise for reduced fuel consumption in LNG processes, autonomously detect and mitigate fugitive emissions, and can often provide improved
payback and earlier actionability that may be missing from more radical strategies, such as carbon capture and storage.
The LNG industry faces significant challenges due to a decline in long-term agreements and an increase in spot trade, leading to volatility and uncertainty. Furthermore, the industry must adapt to meet the expected peak LNG demand as early as 2035. Digital transformation technologies offer a promising solution to these challenges: integrated operations, remote operations, digital twins, and other Industry 4.0 concepts have the potential to revolutionise the LNG industry by optimising operations, reducing costs, and improving safety. Woodside’s successful implementation of remote operations at the Pluto LNG facility showcases the feasibility and benefits of such transformations. By embracing digital transformation, the LNG industry can navigate the evolving landscape and pave the way for a sustainable and efficient future.
1. ROBINSON, M., ‘Natural gas’ place in the energy mix ‘stable until 2035’, Investors’ Chronicle, (23 May 2023), www.investorschronicle.co.uk/news/2023/05/23/naturalgas-place-in-the-energy-mix-stable-until-2035/
2. ‘WILLIAMS-DERRY, C., and REYNOLDS, S., ‘Despite high prices, the global LNG industry has struggled to keep plants online’, Institute for Energy Economics and Financial Analysis, (14 December 2022), https://ieefa.org/ resources/despite-high-prices-global-lng-industry-hasstruggled-keep-plants-online
3. ‘LNG trade and liquefaction utilisation rate, 2015 – 2025’, International Energy Agency, www.iea.org/data-andstatistics/charts/lng-trade-and-liquefaction-utilisationrate-2015-2025
4. ‘Pluto LNG’, Woodside Energy, www.woodside.com/whatwe-do/operations/pluto-lng
5. URSO, J., ‘Preparing for the Future: How Industrial Autonomy Can Lead the Way’, Honeywell Process Solutions, (29 April 2022), www.processindustryinformer. com/how-industrial-autonomy-prepares-manufacturersfor-future/
6. LÖFSTEN, H., ‘Measuring maintenance performance – in search for a maintenance productivity index’, Department of Industrial Dynamics: Chalmers University of Technology, (1998), www.sciencedirect.com/science/ article/abs/pii/S092552739800245X
7. MALARET, F. J., ‘Understanding RAM analysis and typical availability values for LNG plants’, Gas Processing & LNG, (01 April 2015), http://admin.gasprocessingnews.com/ articles/2015/04/understanding-ram-analysis-and-typicalavailability-values-for-lng-plants/
8. MORONEY, T., (Shell plc), ‘EBS Allows Shell To Dive Deep’, HartEnergy, (22 April 2014), www.hartenergy.com/ exclusives/ebs-allows-shell-dive-deep-20099
9. ‘World’s largest integrated LNG Supply Chain Management System implemented’, The Pioneer: QatarGas, No.115, (November 2007), p.7.
10. ‘Norway’s first platform to be remotely-operated from land’, Equinor, (9 November 2017), www.equinor.com/news/ archive/09nov2017-valemon-remote
11. FERNANDO, S., ‘The road to integrated operations’, The APPEA Journal, (11 May 2023), www.publish.csiro.au/ AJ/AJ22261
12. HORNE, D., ‘Why organizations are outsourcing pipeline control room services’, ProcessWest, (16 April 2019), www.processwest.ca/features/why-organizations-areoutsourcing-pipeline-control-room-services/
13. Author’s opinion based on recent trends and industry discussions.
LNG remains the most effective transitional fuel as the world continues to drive toward renewable sources of energy. Recent geopolitical events have highlighted the importance of energy security and communities around the world are seeking more energy sources. The industry is working to meet the four ‘A’s of energy security: availability, affordability, accessibility, and acceptability, and one of the fastest possible ways to do this is by replacing coal
and crude-oil-powered energy sources with stable, cleaner sources like LNG.
For 125 years, teams at Bechtel have been helping bring projects to life and have built a legacy of leadership, innovation, and progress. Since 1898, Bechtel has delivered more than 25 000 projects in 160 countries and on all seven continents. But as new challenges and opportunities arise, it is clear that a better world still has to be built.
Bhupesh Thakkar, General Manager, LNG, Bechtel, outlines how modern innovation can equip the LNG Industry for a more efficient future.
Bechtel is at the forefront of new technologies, processes, and services that are decarbonising existing facilities, improving integration and data centricity, and increasing the productivity and longevity of LNG plants long beyond their anticipated years of service.
The company also supports global LNG capacity having designed and built 30% of the world’s LNG capacity, helping to replace other fossil fuels, reduce carbon emissions, and give developing regions greater access to more efficient energy sources.
To support the shift toward decarbonisation, Bechtel is currently working with customers to construct 13 LNG trains that will deliver more than 45 million tpy in capacity, with an additional eight trains totalling 11 million tpy under limited notice to proceed. As the company ramps up to meet the growing demand for LNG, more than 35 million tpy is in FEED design and future development phases. The trains within this scope utilise Chart IPSMR, COP OCP, and APCI AP-C3MR technologies.
Bechtel offers specialised LNG services that deliver solutions to support customers wherever they are in their energy transformation journey, whether their goal is to increase access to renewable energy sources, improve energy efficiency, or decarbonise their existing infrastructure across the project lifecycle.
The company is committed to supporting the LNG industry in its transition to cleaner technologies, with a focus on safety, sustainability, and innovation.
Customers rely on Bechtel to deliver reliable, full-cycle services for LNG projects. Bechtel Plant Support Services (PSS) provides decarbonisation, sustainability, and plant optimisation solutions with a focus on collaboration from the first engagement.
The PSS business is focused on developing viable decarbonisation solutions – in particular, the electrification of existing brownfield LNG facilities. The company recognises the complexities and possibilities associated with decarbonisation initiatives, and is fully dedicated to assisting its customers in reaching their sustainability objectives. The team is equipped and able to offer comprehensive assistance and guidance at every stage of the process, starting from feasibility studies all the way to the design and implementation of electrification systems.
Electrification offers a promising pathway to reduce carbon emissions in the LNG industry. By replacing existing liquefaction gas-fired turbines with electric motor drives, operating plants can significantly decrease their reliance on fossil fuels and transition to cleaner energy sources. This shift not only aligns with global efforts to combat climate change but also helps enhance operational efficiency and reduce maintenance requirements.
Bechtel’s approach to electrification recognises that successful implementation requires careful planning, stakeholder engagement, and collaboration with regulatory authorities. The team works with clients to assess the feasibility of electrification, considering factors such as power supply availability, grid integration, and regulatory compliance. Through the company’s robust engineering capabilities and understanding of local regulations, Bechtel has developed tailored solutions that seamlessly integrate while adhering to safety standards and environmental regulations.
The company’s safety processes and procedures are adapted and augmented to address the unique challenges of decarbonisation. Decarbonisation initiatives often involve
extensive retrofitting, which introduces potential risks and schedule pressures. Bechtel prioritises the safety and wellbeing of people and communities, and actively seeks execution methodologies that minimise risks and vulnerabilities.
The success of decarbonisation efforts relies on the collective effort the company of all stakeholders. Bechtel believes in the power of collaboration and long-term partnerships. The company works closely with customers, fostering open communication and knowledge-sharing to ensure the successful implementation of sustainable solutions. Through its experience and expertise, the company can provide practical and effective recommendations for facility optimisation, technology advancements, and decarbonisation initiatives.
As governments commit to ambitious climate policies, customers rely on companies like Bechtel to engage early on
Bechtel is committed to enhancing the quality of life for families near its projects and offices and building local capability for the long term by creating a skilled workforce, elevating local businesses, and conducting business sustainably.
Recently, the company announced that NYFL-Tutt Bryant, a Ngarluma Yindjibarndi Foundation’s Equipment Services business, will supply crawler cranes for Woodside Energy’s Pluto Train 2 project in Karratha, Western Australia.
NYFL-Tutt Bryant is providing eight 200 – 300 t crawler cranes at the construction site and will service and maintain the cranes throughout the contract. NYFL-Tutt Bryant is a partner organisation of Murujuga Aboriginal Corporation, with many shared members.
This engagement represents Bechtel’s ongoing commitment to support local and Indigenous businesses, both through increased opportunities and investment in the local economy.
projects and incorporate technologies to help them achieve their energy efficiency and decarbonisation goals.
Bechtel’s LNG Technology Center of Excellence plays a key role in working with clients to explore and integrate design improvements, innovations, and efficient project execution models that target certainty of outcome from concept to completion while meeting the growing environmental demands of the energy industry. The service connects customers with Bechtel specialists well versed in several diversified technologies who focus on analysing and implementing sustainable technologies that create optimal solutions with lasting value.
Bechtel is responsible for the world’s first applications of gas turbines and aeroderivative gas turbines, as well as GT Power augmentation technologies in LNG liquefaction, both of which have helped develop the LNG industry and driven it to higher thermal efficiencies. Currently, the company is exploring utilising gas turbines within additional scopes to improve LNG plant efficiency and further reduce carbon emissions.
The company has pioneered the application of new engine types, including the LM6000 family of gas turbines, and is evaluating the use of larger aeroderivative engines. The use of high efficiency aeroderivative engines with high thermal efficiencies helps customers meet their decarbonisation goals by significantly reducing greenhouse gas (GHG) emissions and other pollutants.
Another major initiative is the use of gas turbine power augmentation to use evaporative cooling and inlet air chilling for LNG plants. The need for these technologies arises to counter the drop in gas turbine power output (and consequent loss in LNG production) as ambient temperature increases. By cooling the inlet air to the gas turbine by either evaporative cooling or inlet chilling, the gas turbine power output can be flattened over ambient temperature, and LNG production can be stabilised over the year.
A newer innovation is the use of gas turbine exhaust heat for either steam production or the heating of hot oil for process needs. This waste heat recovery technology improves the thermal efficiency of an LNG facility and reduces GHG emissions. Bechtel’s LNG Center of Excellence is also studying the use of combined cycles to boost plant thermal efficiency to the 50% mark.
There is not one solution or one technology. There are different requirements, paths, and solutions for every project – but the destination is still the same. Engaging early with an EPC is crucial, because it allows the customer to leverage proven strategies and models for building projects as efficiently and cost effectively as possible while opening more pathways.
What started as a spark in 2019 has grown into a bright and vibrant flame as the Power Play Awards is in its fifth year of shining a light on the accomplishments of remarkable women and men who uphold the importance of supporting and empowering others in the workplace. Once again, there was tremendous support from our Power Play community.
Nominations for the 2023 awards are in and our esteemed judges have narrowed down the impressive field to three finalists for each of the award categories.
Congratulations to all nine 2023 finalists! The winners of the Power Play Awards will be announced at a ceremony during the Gastech Exhibition and Conference in September.
Decarbonising maritime transport is one of the shipping industry’s biggest challenges, and LNG is considered the best available alternative fuel in the transition to the widespread use of renewable and low-carbon fuels.
With its composition of mostly methane meaning that it has a higher hydrogen-to-carbon ratio compared to traditional fuels like diesel, LNG emits significantly less carbon dioxide (CO2) when combusted in a low-pressure dual-fuel engine.
Kati Lehtoranta, VTT, and Clémence Contant and Ciara Kristensen, REVOLVE, discuss the findings of a new study by the GREEN RAY project surrounding methane slip.
It also produces negligible amounts of particle emissions, nitrogen oxide (NOX) and sulfur – small enough to achieve the Tier III NOX and sulfur limits set by the International Maritime Organization (IMO), which has set
stringent rules and designated emission control areas onboard vessels to encourage the continued swift uptake of alternative fuels and technologies to lower greenhouse gas (GHG) outputs. In addition, bio-based and synthetic LNG, while not
expected to begin provisional rollout until the end of 2023, will present a further step towards meeting clean fuel targets.
Now, with March 2023 marking the agreement of the FuelEU Maritime regulations as part of the EU’s Fit for 55 package, decarbonisation goals are even more ambitious.1 Vessels above 5000 t operating in European ports will be obliged to reduce their GHG emissions by as much as 80% by 2050 – a significant step up from the IMO’s 50% 2050 goal.
The IMO DCS data reported that the total use of LNG as maritime fuel was 12.62 million t in 2021.2 Out of all combusted maritime fuel, this represents a share of 5.9%. Most of the total LNG combusted was by LNG carriers (78.9%) followed by gas carriers (16.9%), while the remaining vessel types represented 4.2% of all LNG combusted in 2021.
From its current market share of 5.9%, LNG’s steep rise is clear: a recent report states that around 20% of the total vessel orders in 2021 were LNG-fuelled.3 The most common engine type for LNG vessels is the low-pressure dual fuel (LPDF) concept. Out of the 614 vessels with an identified LNG engine, over 83% comprised low-pressure dual-fuel engines. 350 of these were four-stroke engines and 157 were two-stroke engines. The remaining 96 vessels used high-pressure dual-fuel (HPDF) engines.
As LNG demand and usage continue to increase, there is an urgent need to address its one key downfall in the path to decarbonisation: methane slip.
Methane slip is caused when the LNG injected into an engine cylinder is not entirely combusted. The unburned fuel, which mostly consists of methane, escapes the engine cylinder and ends up entering the atmosphere primarily through the exhaust stack.
Two key characteristics determine the impact of GHGs on the climate: the length of time they remain in the atmosphere and their ability to trap heat. Methane has a much shorter atmospheric lifetime than CO2 – around 12 years compared to centuries – but its molecular capacity to absorb infrared radiation, or heat, far exceeds that of CO2. Trapping heat in the atmosphere at 25 times the rate of CO2 means that methane acts as a dramatic accelerant of global warming, and with it accounting for 20% of all anthropogenic GHGs after CO2 (making it the second most abundant GHG), it is imperative to address its increasing environmental impact in the shipping industry.
Currently, there is limited open-access information quantifying methane slip levels from the LNG engines in use on board existing vessels. In general, there have been only a few emissions studies conducted onboard vessels operating with dual-fuel engines, indicating an urgent need for deeper research in the area if we are to successfully identify and abate methane slip.
GREEN RAY is an EU-funded project, aiming to reduce methane slip with the help of both on-engine technologies and an exhaust after-treatment. With its end goal of developing three innovative technologies that can be installed on new and existing ships, the project is working to reduce the negative environmental impacts of maritime transport.
One important task in the first stage of the five-year project is to define a database reference for measuring and comparing methane emissions from the most deployed forms of LNG engines: two and four-stroke low-pressure dual-fuel (LPDF) types, to bridge the current gap in information on their emissions profiles.
In addition to collecting existing data of methane slip measurements from scientific literature, the GREEN RAY team carried out the first of their own studies onboard an operating LNG vessel in December 2022, measuring GHG emissions, including methane, from both a standard four-stroke LPDF engine, and a new combustion concept engine developed by the project’s partners. This study’s results, while summarised below, were first published in full detail in the 14th edition of the Atmosphere journal.4
For over 100 years, Emco Wheaton has been synonymous with premium loading systems. Engineered for safety and efficiency, our systems feature a heavy-duty construction, provide the highest levels of performance, and transfers seamlessly diverse liquid and gaseous products.
Even in harshest marine environments Emco Wheaton Marine Loading Arms provides a safe transfer of Gas. Whether you use High Pressure Marine Loading Arms for Compressed Natural Gas between Floating Storage and Regasification Units (FSRUs) and the onshore gas grid and support the fast utilization of LNG for stabilizing the national natural gas distribution system. Or LNG marine loading arms that has been designed for any kind of application where it is essential to keep the product pipe consistently the same size for either economical or technical reasons.
The LNG design includes a support structure for the standpost, primary, and secondary arm that separates any mechanical loads imposed to the product pipe, except the deadweight and the internal pressure loads. This ensures optimum operational safety And low weight of the arm as well as lowers wind loads imposed to the jetty structure.
The pantograph balanced, mechanical link design provides stability and strength without compromising safety, handling, or ease of use. Made from various materials, Emco Wheaton’s range of marine loading arms are available in either manual or hydraulic operation versions. A comprehensive range of accessories and equipment is also included. Our marine loading arms help you minimize maintenance requirements and lower your operating costs and will be built in Kirchhain, Germany.
Studies were made onboard Aurora Botnia, Wasaline’s RoPax ferry, operating the route between Vaasa (Finland) and Umeå (Sweden). This modern, state-of-the-art ferry was built in 2021 and began operation in the autumn of 2021. The ferry is operated by four Wärtsilä 31DF engines. These are medium-speed four-stroke marine engines and have eight cylinders, with a power of 550 kW per cylinder. One of the engines was piloting a new combustion concept while the others were standard setups built in 2021.
Measurements were taken from the exhausts of two different engines: the engine piloting the new combustion concept and one of the engines with the standard 31DF setup. LNG was used as the primary fuel and marine diesel oil (MDO) as the pilot fuel.
Both engines were measured while the vessel was operating on its normal route, under engine load levels of 10%, 25%, 50%, 75%, and 90%. The engine loads were calculated with an accuracy of ±2%.
Figure 2 presents the calculated methane emissions in g/kWh for both engines at varying engine loads, measured with two parallel instruments to improve the validity of the results.
The new combustion concept engine is represented in blue and the standard engine in orange.
Two things are clear from the graph; firstly, lower methane levels were consistently recorded at higher engine loads, especially when compared to the lowest engine load of 10%, with both engines. Secondly, a clear trend demonstrates that
the new LNG combustion concept produced lower levels of methane across all engine loads.
Methane slip levels measured onboard LNG-powered vessels equipped with four-stroke LPDF engines have previously been published in only six studies. The methane slip results from previous studies display high variation both depending on the engine load (as was also observed in the GREEN RAY study), and between the different studies (meaning between different vessels and engines). Altogether, methane slip varies from close to 1 g/kWh to over 100g/kWh. At engine loads of 50% and higher, the variation within the previous studies is between 1 – 13 g/kWh. The results from the standard engine in GREEN RAY’s study are clearly on the low end of this scale, with values below 4 g/kWh at loads of 50% and higher.
This analysis allows a more global assessment of GHG emissions from LNG as a marine fuel and contributes to providing a more comprehensive outlook of the climate impacts of maritime transportation as an industry.
Other pollutants were measured during this study, including NOX, carbon monoxide, formaldehyde, and particle emissions. To learn more about the results gained from these measurements, read the Atmosphere journal article in full.
In May 2023, GREEN RAY began measurements onboard the MSC World Europa in the Mediterranean to produce an equivalent set of these initial results. These experiments will continue to draw and improve upon the limitations noted in previous studies, working towards the most comprehensive emissions measurements and the best available solutions.
Within the GREEN RAY project, the technology development on methane slip reduction in four-stroke engines continues, focusing on the largest four-stroke engines on the market and the demands from cruise ships, larger ferries, and gas carriers. The other engine technology that is being developed for the project is focused on two-stroke engines.
The final technology that the project is developing is a methane abatement catalyst (MAC) system which will be installed on a ship’s exhaust. This can be deployed on existing engines and can also act as a supplement to the engine technologies, capturing any residual methane that escapes the engine despite the improvements made by more efficient combustion processes.
The integrated application of GREEN RAY’s technologies, at the end of the project’s timeframe, is set to reduce methane slip by up to 90% for the engine technologies and over 80% for the MAC – an ambitious set of goals, but one which seems within reach based on the promising results achieved so far.
1. 'EU Green Deal: Agreement reached on cutting maritime transport emissions by promoting sustainable fuels for shipping', European Commission, https://ec.europa.eu/ commission/presscorner/detail/en/ip_23_1813, (18/05/2023).
2. 'Amendments to the annex of the protocol of 1997 to amend the international convention for the prevention of pollution from ships, 1973, as modified by the protocol of 1978 relating thereto', IMO Data Collection Systems, (04/06/2023), www.imo.org/en/ ourwork/environment/pages/data-collection-system.aspx
3. PLEVRAKIS, G., KOUTSOURAKIS, P., et al., Setting the course to low carbon shipping: Zero Carbon Outlook, (2022), p.8.
4. LEHTORANTA, K., KUITTINEN, N., VESALA, H., KOPONEN, P., 'Methane emissions for a State-of-the-Art LNG-powered vessel', Atmosphere, Vol. 14, (2023), p.825.
The pipe for offshore cold fluid transfer
• EN1474-2 certified
• Endless production
• Vacuum insulated
• D ouble containment design with corrugated pipes
BRUGG Rohrsysteme GmbH
• C orrugated pipes made of 316L
• No intermediate joints
• L NG, Ammonia, LH 2
• Up to 8 inch fluid pipe
Adolf-Oesterheld-Straße 31 · 31515 Wunstorf · Germany
T +49 5031 170-0 · cryo@brugg.com · bruggpipes.com
he Mark III technology for fuel tanks has demonstrated its relevance and performance for LNG dual-fuelled (DF) vessels, saving cargo space while optimising vessel energy consumption, thanks to improved thermal performance. In view of expanding the penetration of LNG as a marine fuel, the company has developed an efficient long-range design for LNG DF oil tankers and dry bulkers, as well as passive and active solutions for increasing the operational flexibility of the vessel while optimising the vessel LNG fuel consumption and CII rating.
LNG-fuelled ship (LFS) technology keeps gathering momentum in the maritime industry. The revolution has already taken off. With more than 800 large LNG-fuelled vessels projected to be at sea by 2025, LNG is overtaking
scrubbers and becomes the preferred choice as an alternative to conventional propulsion.
GTT has been at the forefront of this transition, leveraging its widely recognised technologies and expertise in LNG. Mark III technology equips most of the large LNG dual fuel container vessels, from medium size (7000 TEU) to ultra large CV (23 000 TEU), as well as Ponant’s iconic polar exploration cruise ship Le Commandant Charcot and several LNG bunker vessels.
GTT recently expanded its portfolio of solutions to offer owners more flexible and reliable LNG-fuelled vessels, from the design of innovative solutions for bulkers and oil tankers to the development of passive and active solutions to further improve the performance of the fuel tank and of the overall DF vessel.
LNG propulsion still has a limited share for some ship types, especially large tankers and bulkers, even though this solution makes sense for these ships as they usually have long-range and fixed trades. In order to offer the market a relevant and competitive solution, in conjunction with Finnish ship designer, Deltamarin, GTT has recently developed two designs of LNG DF crude oil tankers, both for suezmax and very large crude carriers (VLCCs) (Figure 1).
The companies studied different arrangements and solutions for the tank’s position, which was finally located for both the suezmax and the VLCC on the aft part of the vessel, behind the accommodation and partly integrated inside the hull. This compromise maintains the same cargo capacity as for a conventional tanker with a limited impact on the engine room arrangement while aiming at a large LNG capacity. The VLCC design features a 12 500 m 3 LNG tank and the suezmax design a 5500 m 3 LNG tank (Figure 2), thanks to the space optimisation offered by Mark III technology.
Such a long-range design feature enables the vessel to make a return trip with a single bunkering operation in order to optimise voyage duration and to bunker at the cheapest location, but also to minimise additional fixed costs such as fixed bunkering fees, etc.
The LNG tank is located in a tight compartment surrounded by a complete steel structure, which protects it from any external damage such as green water or salty atmosphere. Compared to the type C design with the LNG fuel tank in front of the accommodation, the Mark III design comes without any visibility issue but also without any impact on the cargo lines located on deck.
The ship’s energy efficiency has been studied with the latest simulation tools and a holistic approach, resulting in not only a vessel using LNG as fuel but also the best efficiency with the lowest emissions in this ship size class.
Both designs were reviewed by several Classification Societies and received approvals in principle (AiPs): the VLCC design by ClassNK and DNV and the suezmax tanker design by DNV. Class reviews included the study of the vessel stability, machinery arrangement, and hazardous areas.
Compared to conventional oil fuelled tankers, there are many advantages in adopting long-range LNG-fuelled tankers. Thanks to its long-range capabilities, such an asset comes with a high trading flexibility for the shipowner and the charterer, able to efficiently operate under chart party as well as in the spot market. The large fuel tank capacity is also seen as an advantage during second hand reselling negotiations. Besides, these Mark III LNG fuel tankers take full advantage of the GTT Mark III system, with higher thermal performance and larger useful volume without compromising the cargo capacity. This Mark III solution with the fuel tank behind the accommodations is also applicable for smaller tankers (aframax/LR2) and for dry bulkers, with designs developed and validated for newcastlemax and very large ore carrier (VLOC).
LNG fuel tanks using Mark III technology, fitted for instance on container vessels, will typically have a design pressure of 0.7 barg. Based on decades of experience acquired on LNG carriers, and return of experience of the first Mark III containerships in service, this standard 0.7 barg design is well suited to LNG fuel applications and provides sufficient operational flexibility.
However, the smaller size of LNG fuel tanks compared to LNG cargo tanks means that limited modifications to a conventional 0.7 barg
Mark III LNG fuel tank can permit going to 1 barg or even up to 2 barg (for tanks of limited height) operations. This gives operators greater flexibility for specific applications.
Offering an increased pressure range has several advantages:
z Increased holding time (with and without gas consumption), particularly useful for cold ironing or in case of long idling phases.
Unmatched suite of products to support the world's current and future storage needs
Turnkey project delivery, from concept to commissioning
Know-how and specialized skills to design and build projects anywhere in the world
Industry-leading hydrogen storage expertise
z The ability to bunker LNG with warmer temperatures (from ‘lower quality’ supply chain) when necessary.
z Greater flexibility with regards to high transfer rates and vapour return management.
z Minimise the risk of wasting boil-off gas (BOG) during low consumption phase or venting BOG in case of emergency.
All technological components have been developed by GTT and validated in order to apply increased pressure in the Mark III fuel tank. The impact on the fuel tank design is actually limited, and mainly concerns the reinforcement of the steel structure surrounding the fuel tank and the tank interfaces, especially the dome(s) – the area where all the pipes penetrate in the tank. Applying a maximum design pressure of 1 barg keeps the typical Mark III LFS combined rectangular dome, with slightly increased top cover thickness.
Going to 2 barg design pressure requires the use of a circular dome as for type C tanks, with a limited diameter. GTT has developed a dedicated combined dome, designed to handle gas and liquid pipe crossings (Figure 3). This allows a limited vertical footprint, ideal for reducing the impact on the vessel design.
From a regulatory perspective, going beyond the limits set by the IMO IGF Code requires the use of the prescriptive requirements of the ‘Alternative Design’ approach and going through a methodical and
formatted process, in order to demonstrate that the level of safety is at least equivalent.
The ‘Alternative Design’ process was successfully applied to Ponant’s LNG-fuelled exploration cruise vessel Le Commandant Charcot, now in operation (Figure 4). It consisted in submitting a technical validation to the classification society, Bureau Veritas, and the Administration (French Flag), justifying an equivalent level of safety between a 2 barg and a conventional 0.7 barg Mark III LNG fuel tank design. In addition, an IGF Code conformity matrix and risk analyses were performed, verified by Bureau Veritas and submitted to the Administration. Finally, the Administration submitted the ‘Alternative Design’ description to the IMO.
The baseline is now set to apply this alternative design, offering enhanced flexibility for many types of LNG-fuelled vessels, from cruise ships to car carriers (PCTC) or container vessels, bulkers and tankers. The maximum design pressure ranges from 1 – 2 barg depending on the vessel type, tank size, and operational profile.
With evolving environmental rules, LNG-fuelled ships are required to be more energy efficient and emit less hydrocarbons; two-stroke high-pressure engines often appear as the engines of choice for LNG-fuelled ships’ main propulsion due to low methane slip and high power efficiency. With such high-pressure engines, finding a reliable, cost effective, and easy way to operate BOG management systems often appears as a complex equation, which the has sought to solve by offering an active BOG management solution called Recycool TM
Indeed, if the auxiliary engines cannot consume all the BOG from the LNG fuel tank for a long period, the main engines have to consume such excess gas in order to avoid venting to the atmosphere or any waste in a gas combustion unit/oxidiser/gas boiler. Such a process of natural gas consumption in main engines typically requires the implementation of a high-pressure compressor, with 300 bar delivery pressure, which comes with several issues:
z High cost of operation to produce 300 bar.
z High wear and tear frequency of compressor internals as gaskets, piston rods, bearings, etc. leading to high maintenance frequency and reduced availability.
z CAPEX due to multiple compression stages and material selection.
z Other implications such as requested spare parts, 300 bar piping system, requested power load on installed electric switchboard system.
In this context, the company has collaborated with several fuel system integrators to introduce a simple, low CAPEX solution, capable of securing BOG management and improving operability of any LNG-fuelled vessel running with a two-stroke high pressure engine. Such a system is a boil-off recondensor called Recycool.
The Recycool principle consists in recovering the cold power available when LNG is sent to two-stroke high pressure engines in order to reliquefy BOG whenever there is an excess before sending it back to fuel tank. In fact, two-stroke high pressure engines require LNG to be heated to +45˚C from cryogenic conditions, leading to a high amount of cold energy being available. This cold is recovered in two locations: before the high-pressure pump and in a pre-cooler located between the high-pressure pump and the high-pressure vaporiser.
Recycool is an integrated system, which makes it compact and able to reach very high efficiency. As an outcome of fruitful discussions with equipment makers, the pre-cooler and the high-pressure vaporiser have been combined into one single system, making Recycool even more compact and competitive (Figure 5).
To optimise the operations of Recycool, the BOG has to be sent to the high-pressure skid via oil-free compressors. In addition, the LNG fuel gas pump has to work with a delivery pressure high enough to avoid cavitation at high-pressure pump inlet. In operation, Recycool will help store cold inside the LNG fuel tank in order to reduce the BOG quantity when the main engines are not
running anymore (e.g. idling, bunkering, cargo loading/unloading). As a result, any excess BOG is removed or at least significantly reduced, providing flexibility to operators while improving OPEX and CII rating.
When combined with a shaft generator (PTO), a dedicated study on a 15 000 TEU LNG-fuelled container ship has shown that Recycool improves LNG fuel system OPEX savings from 2% (PTO only) to 5% (PTO + Recycool). By limiting the burden on auxiliary engines, the methane slip will also be reduced.
Some system integrators (currently Nikkiso ACD and Cryostar) propose Recycool in their high-pressure skids. Shipyards will deal with integrators who in turn will interface with GTT to optimise and fine-tune the Recycool integration in the high-pressure skid, considering project specificities.
Recycool can be proposed on any LNG-fuelled vessel equipped with a high-pressure engine, regardless of the LNG fuel tank technology, e.g. Type A, Type B, Membrane, Type C. Recycool can be safely and easily disconnected whenever required without impacting fuel supply to the high-pressure engines.
Improved ship design, passive, and active solutions for fuel gas handling: all these developments, bringing higher value to the LNG-fuelled ship, will certainly be important components for the new generation of LNG DF vessels. They will further enhance operational flexibility and improve CII rating while ultimately reducing costs for the operators.
While the properties of hydrocarbons are well understood, and have a long history of industrial use, the hydrogen economy is still in its infancy. Reliable design and directoperational experience are still limited, so new standards and proven technologies that can address these unique hazards are required.
PPG’s global capabilities and respected protective coating range enable us to provide coating solutions for the clean energy segment. We offer a complete coating portfolio for corrosion protection, chemical resistance, and passive fire protections (PFP) for hydrocarbon and hydrogen (H2) facilities.
For H2 facilities utilizing steam methane reformer (SMR) process units, PPG coating solutions address H2 environments with a full product offering, including globally recognized brands such as PPG SIGMAZINC™, PPG SIGMAFAST™, PPG SIGMADUR™, PPG NOVAGUARD™, PPG HI-TEMP™ and PPG PITT-CHAR™. Please contact your PPG representative for guidance and product selection.
Since its introduction in 2019, the PPG PITT-CHAR NX coating has established itself as a leading passive fire protective (PFP) coating for many major LNG projects. Commonly referred to as the transition energy source, LNG is expected to remain as the primary low carbon hydrocarbon source and economically preferred option when combined with carbon capture systems.
As with hydrocarbon fuels, there is potential for jet fires to occur in H2 facilities, which will require the protection of critical structures and equipment using PFP coatings. H2 fires are expected to burn hotter and, due to the higher volumetric outflow, can burn much faster than most hydrocarbons currently in use.
To further strengthen PPG’s position as a coating solution leader, PPG identified the need to generate baseline performance in H2 fire environments using its PPG PITTCHAR NX PFP coating. The data will improve the industry’s understanding of H2 fire impact on PFP with the common goal of improving H2 fire safety standards, which will provide safety engineers with a reference point for future specifications.
A H2 fire hazard differs depending on the form in which it is being handled, with the most common forms being cryogenic liquid, cryo-compressed (CcH2), Hydrogen/ Natural Gas blends (typically up to 25% H2) and very highpressure storage in cylinders at pressures of 350 to 700 bar (5,000 to 10,000 psi) with the latter being preferred for a range of applications from fuel-cell vehicles to power for data centers.
The fires from leaks at very high pressure are of particular interest as they may be extremely erosive and little, or no, research had been carried out on their effects on PFP material.
Hydrogen (H2) is one of a few low carbon energy sources recognized as reaching established net-zero goals. Consequently, it continues to attract strong interest. Even if partially realized, the hydrogen economy equates to a greater number of hydrogen production and handling facilities.
PPG commissioned a third-party test facility to undertake hydrogen jet fire testing using their High-Pressure Hydrogen Release (HPHR) facility.
The hydrogen jet fire tests performed were intended to replicate the thermal and erosive effects from a leakage at very high pressure that could impinge on adjacent tanks or structures. Four tests were successfully completed with pressure and temperature data, video, photographs, and infra-red camera imagery to document and reinforce the resulting data.
Two tests were carried out on bare steel plates (similar to the material used in the ISO 22899-1 jet fire test standard). These tests showed that, although the hydrogen fires were relatively short in duration (depressurizing in approximately five minutes), the steel reached critical core temperatures of 400°C in less than one minute, less than half the time of the standard jet fire test, thereby risking failure of impinged tanks or structures before safe distances could be established or active fire protection solutions enabled.
Two further tests were conducted where the PPG PITTCHAR NX coating had been applied to the steel specimen. These tests demonstrated that the protective coating was quick to react to the heat of the hydrogen flame and was capable of resisting the highly erosive high-pressure jet, thus maintaining the steel temperature to below 100°C (212°F) for the full duration of the release.
PPG coating solutions are leading the industry when it comes to testing hydrogen PFP coating systems and focusing on the safety of the facility and its personnel. Contact your local PPG representative for further information.
For more information, visit www.ppgpmc.com or contact:
Asia Pacific
+86-21-6025-2688 ppgpmc.ap@ppg.com
Europe, Middle East and Africa
+32-3-3606-311 customers@ppg.com
Latin America
+57-1-8764242 ext. 201 ppgpmcandean-ca@ppg.com
North America (US & Canada)
+1-888-9PPGPMC PMCMarketing@ppg.com
The test results show that the PPG PITT-CHAR NX coating performs to the highest standard in a high-pressure hydrogen jet fire environment, effectively reducing the heat transfer to the substrate.
Stand B384
Understanding the complexities and technical requirements of transporting, handling, and storing gas are essential to enable safer operations for a rapidly growing maritime sector. ABS specialists will be on hand at Gastech 2023 to discuss how the company is supporting the industry from guidance on floating LNG storage, liquefied carbon dioxide carriers, onboard carbon capture, advanced technologies, and decarbonisation solutions. ABS provides industry-leading classification services, as well as technology support for the pioneers of the next generation of innovative vessels.
Listen to ABS specialists in the Shipping & Marine Theatre, or visit the company’s booth.
Stand A250
As a leader in hydrogen and LNG technology and providing proprietary technologies in the turboexpander and membrane industries, Air Products has its finger on the pulse of the energy transition. Worldwide, Air Products is taking real action, generating a cleaner future by developing and executing first mover projects, providing real sustainability benefits to bring lower carbon forms of energy to the world. The company is working hard to generate a cleaner energy future, collaborating and innovating solutions that help solve pressing energy and environmental challenges.
Stand C272
Aragon is a leading engineering and EPC company headquartered in Bergen, Norway, offering environmentally-sound systems and solutions to the global energy industry.
Aragon has broad expertise within topside and process plant design for offshore natural gas compression and treatment, floating LNG, system design, and energy optimisation.
As part of the energy transition, Aragon has gained a significant track record over the years and is offering services for designing and implementing solutions for the production and logistics of hydrogen, ammonia, methanol, bio-LNG, and other derivatives, as well as providing carbon capture and utilisation solutions.
Aragon believes in a sustainable energy future and enables project developers, energy companies, technology licensors, and other industry players to realise their projects from concept study level to turnkey solutions.
Stand C470
Driving energy efficiency for a cleaner, more sustainable world, Aspen Aerogels® has been delivering innovative thermal solutions for over 20 years.
As proven leaders in aerogel technology, Cryogel® Z has been specified and used in nearly 50 major LNG liquefication and regasification projects around the world.
Cryogel Z insulation combines exceptional thermal performance in an easy to install, flexible blanket design. Aspen Aerogels has a proven record of delivering value beyond insulation.
Learn how Cryogel Z insulation can:
z Maximise yield.
z Minimise maintenance costs.
z Condense construction schedule.
z Reduce noise.
z Increase plant safety.
Whether for design, construction, operations, or maintenance, Cryogel Z is a top choice for cold conservation applications.
Stand A312
Great ideas transform industries. Atlas Copco Gas and Process helps its customers prepare for tomorrow by designing, building, and servicing turbocompressors, gas screw compressors and turboexpanders for the oil and gas, power generation, and industrial gases industries.
The company is dedicated to helping customers handle today’s pressures while creating a sustainable future. The company is a division of the Compressor Technique
business area, headquartered in Cologne, Germany, with additional production centres in the US, China, and India.
Stand C310
Baker Hughes is an energy technology company that provides solutions to energy and industrial customers worldwide. Powered by the industry’s only end-to-end technology portfolio, and enabled by their people and scale, the company focuses on designing, manufacturing, testing, and installing gas technology solutions that serve the entire gas value chain including, on/offshore, pipeline, LNG, gas storage, and gas distribution. The company aims to reduce the carbon intensity of its operations, unlocking the adoption
of CCUS solutions, serving the entire hydrogen value chain and applying proven low-carbon technology to help its customers meet their environmental goals, and innovating for the future of energy.
Stand D210
For 125 years, extraordinary teams at Bechtel have been bringing to life inspiring projects, building a legacy of leadership, innovation, and progress. But as new challenges and opportunities shape the future, the company knows that a better world still has to be built. At Bechtel, they live for a challenge. Its people are excited by tomorrow and the possibilities it holds to change lives and create a more prosperous, sustainable, connected, secure, and equitable world.
Stand DE43
Bibby Marine provides innovative, practical, and safe accommodation solutions, owning and operating two different classes of vessels. The company’s floating accommodation solutions, floatels, offer a flexible, affordable, and comfortable accommodation option for even the most remote projects. Its walk-to-work service operation vessels, the Bibby WaveMaster 1, and Bibby WaveMaster Horizon offer innovative solutions for the workforce of the offshore energy sector.
The maritime sector plays a key role in collective efforts to deliver a cleaner and more sustainable future. Bibby Marine is keen to work with partners to accelerate the decarbonisation of the maritime sector through offering innovative maritime solutions.
Stand B270
Black & Veatch helps its clients navigate the challenges and opportunities presented by the energy transition while helping maximise the value of their gas reserves. The company’s EPC solutions focus on LNG/FLNG with PRICO® technology, gas processing, hydrogen, biofuels, ammonia, fertilizers, chemicals, and carbon capture solutions. The company’s modular approach enables fast-to-market results.
Stand A212, Hall 2
Burckhardt Compression creates leading compression solutions for a sustainable energy future and the long-term success of its customers. Together with its brands (PROGNOST, SAMR Métal Rouge and Shenyang Yuanda Compressor) the company is a global manufacturer that covers a full range of reciprocating compressor technologies and services. Its customised and modularised compressor systems are used in the chemical and petrochemical sectors, gas transport and storage, hydrogen mobility and energy sectors, and industrial gas sectors as well as for applications in refinery and gas gathering and processing.
Bergen Pipe Supports provides customers with a one-stop solution for key engineering applications such as Cryogenic Piping, Storage, Transportation and Critical fire barrier applications.
Our comprehensive range of products includes.
• High-density polyurethane foam supports,
• Engineered composites for thermal insulation/isolation with various resin formulations suitable for pipe surface temperature ranging from -196°C to +350°C.
• high-performance Comlin elastomers for corrosion, vibration and acoustic isolation.
• Proven track record globally for various projects in design, manufacture and delivery of cryogenic solutions complying with ASME/ANSI and CINI standards.
We will be exhibiting at Gastech 2023 taking place 5-8 September at Singapore EXPO. Please join us there! Visit our stand D291 to meet the team, and find out about our latest products, solutions and services.
Stand A156
The company’s deep cryogenic expertise and proven track record makes Chart the ideal project partner to deliver LNG and hydrogen as secure, clean, safe, and affordable fuel alternatives. It has a broad portfolio of complementary products and technologies, and what makes Chart unique is the ability to integrate all of these products to deliver highly engineered solutions used across the entire liquid and gas molecule value chain from helping those that produce, to storage and transport, to end users. The acquisition of Howden furthers Chart’s global leadership position in highly-engineered process technologies and products serving the Nexus of CleanTM
Stand D350
Chevron Corporation is one of the world’s leading integrated energy companies. It believes affordable, reliable, and ever-cleaner energy is essential to achieving a more prosperous and sustainable world. Chevron produces crude oil and natural gas; manufactures transportation fuels, lubricants, petrochemicals, and additives; and develops technologies that enhance its business and the industry. The company is focused on lowering the carbon intensity in its operations and
growing lower carbon businesses along with its traditional business lines.
Stand 167, Norwegian Pavilion
ECOnnect Energy believes in making clean energy accessible globally. ECOnnect Energy is an independent Norwegian technology company assisting the energy and maritime markets with the jettyless IQuay® transfer solution. The IQuay solution features a floating jettyless system for the loading, discharge, and bunkering of gas, LNG, ammonia, and carbon dioxide without the need for environmentally-invasive, time and cost-intensive fixed marine infrastructure. With innovative technology, ECOnnect Energy is committed to providing low-impact solutions for the uptake of clean energy.
Stand A120
Endress+Hauser is a global leader in measurement instrumentation, services, and solutions for industrial process engineering. The company provides process solutions for flow, level, pressure, analytics, temperature, recording and digital communications, optimising processes in terms of economic efficiency, safety, and environmental impact. Endress+Hauser Optical Analysis is the global leader in spectroscopic instrumentation for chemical composition and concentration analysis. The company’s offerings harness the powerful analytical information of Raman spectroscopy, tuneable diode laser absorption spectroscopy (TDLAS), and quenched fluorescence (QF) to help its customers understand, measure, and control their laboratory and process chemistries.
Stand A90
Excelerate Energy, Inc. (NYSE: EE) is changing the way the world accesses cleaner forms of energy by providing integrated services along the LNG value chain with the objective of delivering rapid-to-market and reliable LNG solutions to customers. The company offers a full range of flexible regasification services from FSRUs to infrastructure development to LNG supply. The company’s integrated LNG solutions remove the roadblocks that routinely hinder gas and power projects in markets across the globe. As a leading provider of innovative LNG solutions, Excelerate Energy is committed to empowering countries with energy independence and accelerating the transition to a clean energy future.
Stand C170
Gas and Heat is a leading company in the design, construction, supply, and installation of liquefied gas containment and handling systems for both marine and onshore installation. Gas and Heat has offered its support to owners/charterers since the early stages, when the potential investment was still yet to be conceived. Currently, innovative solutions inspired to project sustainable, safe, and efficient operations, increasingly reducing the negative environmental footprint, are the pillars that
underpin the final investment decision. Gas and Heat supports yards during the installation onboard of the cargo tanks, as well as during the commissioning and gas trial. The company is strongly committed to serving the rapidly growing market of replacing conventional fuels with ammonia, methanol, hydrogen, and bio-LNG in maritime, inland waterway, and terrestrial environments.
Stand A320
Heatric, a division of Parker-Meggitt, is a world leader in printed circuit heat exchangers (PCHEs) for the traditional hydrocarbon and emerging energy industries. Up to 80% smaller than alternative heat exchangers, each Heatric PCHE is robust, lightweight, and bespoke in design – engineered to customers’ specific requirements to maximise output and process efficiency. Heatric PCHEs are suited to multiple applications; from onshore liquefaction and regasification, to floating storage and transport in marine shipping. With 30+ years’ experience and 3000+ exchangers in operation globally, Heatric has the expertise to enable projects.
Stand B115
HEROSE is a German engineering company and provides safety around the world for the handling of technical gases, steams and liquids. With 150 years of experience in the development, manufacture, and sale of valves with a high level of innovation and modern production with certified quality management, the company is one of the world’s leading manufacturer and supplier of valve solutions for cryogenic technology within the applications of air gases, LNG, and hydrogen.
Each valve is personally tested and adjusted especially to the customer’s needs.
Stand A422 (Hydrogen Zone)
Removing sulfur and mercury from LNG is critical to meet safety standards and sales specifications. With 40+ years of experience in gas processing, Johnson Matthey’s PURASPECTM absorbents combined with its PURACARETM cradle-to-grave service are proven to provide a highly efficient, easy to operate and economic solution. Johnson Matthey’s leading expertise in purification and syngas chemistry are at the core in fulfilling the company’s mission of ‘catalysing the net zero transition’ by developing catalyst technologies for sustainable fuels and chemicals.
Visit Johnson Matthey at stand A422 for further discussions on these topics.
Stand B164
LNT Marine is a technology and service provider within the maritime industry specialised within LNG tank systems and cryogenic insulation. The company provides design and engineering for marine solutions based on proprietary energy efficient technologies and offer system supply as well as technical support and installation services. LNT’s proprietary technologies includes the award-winning LNT A-BOX® containment system, ammonia-ready LNG fuel tank systems and spray foam insulation systems for various types of gas carriers and fuel tanks.
Stand C450
Mexico Pacific’s anchor project, the Saguaro Energía LNG Facility, is a 3 train, 15 million tpy West Coast North American LNG export facility located in Puerto Libertad, Sonora, Mexico. The Saguaro Energía LNG Facility achieves significant cost and logistical advantages, including the lowest landed price of North American LNG into Asia, leveraging low-cost natural gas sourced from the nearby Permian Basin and providing a significantly shorter shipping route that avoids Panama Canal transit for Asian markets.
More information can be found at https://mexicopacific.com.
Stand D207
MIB is a world leader in the supply of emergency release systems, and specifically in the supply of turnkey transfer solutions for the gas industry. Since the early 1970s, MIB’s ongoing engineering developments have allowed the company to provide the highest standard of equipment for the safe transfer of LNG, LPG, and other cryogenic and refrigerated, as well as high pressure, gaseous fluids. This result has been made possible thanks to the continuous close liaison with major oil and gas companies, vessel and terminal owners and operators, and to the company’s focus to match the ever increasing and stringent demands of this industry.
Stand C432
Nikkiso Clean Energy & Industrial Gases is a global provider of value-engineered equipment, services, and solutions. The company’s technologies range from specialty pumps to liquefiers for manufacturing, clean energy, transportation and utility industries. Its expertise in cryogenics extends from LNG to hydrogen, ammonia, and carbon dioxide. Nikkiso designs, manufactures, and maintains ammonia pumping systems, heat exchangers, process plants, and capture facilities.
Stand C200
Saipem is a leading company in the engineering, drilling, and construction of major projects in the energy and infrastructure sectors, both offshore and onshore.
Saipem is ‘one company’ organised into five business lines: Asset Based Services, Energy Carriers, Offshore Wind, Sustainable Infrastructures, and Robotics & Industrialised Solutions. The company has nine fabrication yards and an offshore fleet of 29 construction vessels (of which 26 owned and three owned by third parties and managed by Saipem) and 13 drilling rigs, of which nine are owned.
Always oriented towards technological innovation, Saipem is now committed to supporting its customers to accompany them on the energy transition path and net zero with increasingly digital means, technologies and processes geared towards environmental sustainability. Listed on the
Milan Stock Exchange, it is present in over 70 countries around the world and employs over 30 000 people of 130 nationalities.
Stand C150
Sempra Infrastructure, headquartered in Houston, is focused on delivering energy for a better world by developing, building and operating, and investing in clean power, energy networks, and LNG and net-zero solutions that are expected to play a crucial role in the energy systems of the future.
Through the combined strength of its assets in North America, Sempra Infrastructure is connecting customers across the globe to modern energy infrastructure to source and transport renewables and natural gas, while advancing carbon sequestration and clean hydrogen.
With a continued focus on sustainability, innovation, world-class safety, championing people, resilient operations, and social responsibility, Sempra Infrastructure’s more than 2300 employees play a vital role in the company’s contributions to the global energy supply chain.
Stand D02
Stirling Cryogenics designs and manufactures cryogenators. A single Stirling cryo can produce approximately 1 tpd of LNG,
or manage 1 tpd of boil-off gas (BOG). When put in parallel, the Stirling proposition is capable of reaching capacities of up to 20 tpd in a standardised plant. This is a very suitable size for the biogas industry.
Liquefaction of biogas cannot be done properly without gas purification, so together with Stirling Cryogenics’ sister company from Italy, Hysytech Srl, the companies have engineered an integrated gas purification and liquefaction plant. This plant is turnkey and requires only to connect electricity and gas feed as input and on the output side the connection to the LNG storage tank.
To date, Stirling Cryogenics is involved in 15 commercial bio-LNG projects since the beginning of 2020 spread out over the whole of Europe: Italy, Germany, France, Sweden, and the UK. As well as seven maritime BOG management projects and two onshore BOG projects for LNG terminals. The projects range from as small as 1 tpd to 10 tpd. The market is still very young, but there has been a growing number of projects since 2021.
Stand A171
TB Global Technologies Ltd is a Japanese marine loading arm (MLA) manufacturer, providing reliable MLAs for more than 60 years.
The first LNG to Japan was offloaded by the company’s MLA in 1969 from Polar Alaska to the Tokyo Gas Negishi terminal. Presently, MLAs for ship-to-ship applications such as FSRU and floating LNG, with automatic connection system ‘CHOKUSEN’, is available. The world’s first rigid MLA for liquefied hydrogen completed its first unloading at Kobe, Japan, in February 2023. Advanced safety system considering ammonia’s toxic property is also under development. TB Global Technologies is ready to contribute to the society for decarbonised future.
Stand D270, Hall 5
Technip Energies is a leading engineering and technology company for the energy transition, with leadership positions in LNG, hydrogen, and ethylene as well as growing market positions in blue and green hydrogen, sustainable chemistry, and carbon dioxide (CO2) management.
In LNG, Technip Energies brings its clients’ ground-breaking projects to life, integrating technology and expertise. The company is committed to enhancing customer performance and accelerating the energy transition by offering solutions to reduce CO2 emissions from liquefaction and export terminals.
In Qatar, the company is delivering the world’s largest LNG projects, including a large CO2 carbon capture and sequestration facility that reduces CO2 emissions by around 25% when compared to similar LNG facilities.
Technip is also opening new frontiers in natural gas liquefaction with SnapLNG by T.ENTM, an innovative pre-engineered and standardised modular solutions delivering low-carbon LNG, in a new way, with accelerated time to market.
TGE Marine has over 40 years of experience, more than 250 gas tankers, more than 400 cargo and fuel gas tanks, more than 100 fuel gas systems, and one crew.
Since 1980, the company is the leading liquefied gas systems’ provider for:
z LNG/liquefied ethylene gas (LEG)/liquefied petroleum gas (LPG)/ammonia (NH3) gas carriers.
z Bunker vessels for cryogenic gases.
z Fuel gas systems (LNG, ethane, LPG, NH3 and future fuels).
z NH3 and carbon dioxide, including floating units.
The company’s passion for innovation provides support to the industry, with technical solutions for a sustainable future.
Stand B312
Worley Limited is listed on the Australian Securities Exchange (ASX: WOR) and is a professional services company of energy, chemicals, and resources experts helping its customers shift their operations towards a more sustainable future. The company employs 50 000+ people across 46 countries, all driven by a common purpose: delivering a more sustainable world.
Worley works with its customers at every stage of their project – from initial concepts to sustaining and enhancing their assets while working to fulfil ambition to be recognised globally as the leader in sustainability solutions.
Stand A502
ZALUX is a European leader in luminaires with a high degree of protection for industrial and challenging applications. For the past 40 years, the company has been setting the benchmark for sustainability in its products, which can be used in the harshest of environmental conditions. The new STRONGEx range is ideal for a wide range of oil, gas, and petrochemical facilities in Ex Zone 1 and Zone 2, and is designed to reduce energy consumption, with extend lifecycle and lower maintenance. The company will also be showcasing its forthcoming addition to the ACQUEx range at Gastech.
Learn more at www.zalux.com/atex-lighting
Gauging at Emerson, Sweden, addresses how radar level measurement instruments and tank management software can work together to help operators improve safety and operations, while reducing maintenance costs.
The LNG industry is growing rapidly worldwide as the transition from oil to cleaner natural gas accelerates. Liquefication is needed because the areas where natural gas is produced are often very far away from where it is eventually used, necessitating compression for transport, typically via ships. With growing use comes a need for increased storage capacity, at both LNG plants and shipping terminals. This is typically done using full-containment cryogenic tanks, which are large, complex structures with capacities ranging from
30 000 – 200 000 m 3 , and up to 60 m (200 ft) in height (Figure 1).
These vessels include an inner liquid containment steel tank, an outer concrete (or steel) tank for secondary containment control, and thermal insulation between the two to avoid liquid boil-off during storage. This unique structure of two vapour spaces, one outside the tank’s fixed suspended deck and another inside it, presents a
level measurement challenge. In addition, these two large spaces have different requirements for a suitable operating environment, so temperature control is vital to avoid unwanted boil-off resulting in vaporised product. The normal storage temperature for LNG is -158˚C (-252˚F), but it boils at -110˚C (-166˚F).
Level measurement in these tanks has traditionally been performed using either a float and tape method,
or servo technology, with both these mechanical technologies relying on a float or displacer device matched to the density of the fluid so that it stays at the fluid interface. This device is physically connected via a mechanical link to a sensor/transmitter so its location can be detected within the vessel. The combination of moving parts and exposure to tank fluids results in higher maintenance requirements than a non-contacting level technology, such as radar. These mechanical level measurement technologies can only provide a single data point, tank level, with no secondary process variable, status, or diagnostic data available.
To address these and other issues, mechanical level measurement technologies are being replaced with roof-mounted radar gauges. This type of gauge transmits microwave signals towards the surface of the process media, which are reflected as an echo back to the gauge. In addition to not requiring any physical contact with the surface, radar gauges do not need inside-tank components that would require maintenance, and they can provide myriad data points to a host system via a digital link.
This host system is often a dedicated tank management software, which captures the tank measurement signals, performs inventory management calculations, and informs operators of status and any developing issues. Inventory is based on calculations that yield a liquid equivalent reading by taking temperature and density of the process media into account. Tank management software algorithms, along with device diagnostics, can also be shared with asset management tools to reduce maintenance costs, as well as reducing worker exposure hours.
Making reliable measurements, including for safety integrity level (SIL)-rated systems when needed, under these conditions can be challenging. Fortunately, suppliers continue to develop and improve level sensing technology to meet this challenge.
To reliably measure the level in a full containment tank, a radar gauge needs a sufficiently strong reflected signal, and one way to accomplish this is by focusing the signal using a 100 mm (4 in.) diameter still-pipe to guide the radar, resulting in a strong, undisturbed echo from the surface of the process media.
Radar gauge based on two-wire frequency modulated continuous wave (FMCW) technology transmit a radar signal with increasing frequency over time to create a signal sweep. The resulting signal echo reflected from the surface is picked up by the antenna. Because the frequency of the transmitted signal constantly varies, the echo frequency always differs slightly to the transmitted signal at any given moment. The difference between these frequencies is directly proportional to the echo delay, i.e., the distance from the transmitter to the surface, which enables the very accurate measurement of the level required for inventory management.
The sensitivity of transmitters based on FMCW technology is more than 30 times higher than those based on pulse radar technology used on conventional tanks and vessels. Typically, the radar sweep is controlled
Emerson’s integrated solution for LNG and other refrigerated gas storage ensures accurate and reliable level, density and temperature measurement and improves overall inventory management. The Rosemount™ Tank Gauging System enables leak detection, monitors stratification, and predicts the risk of roll-over incidents.
Learn more at www.Emerson.com/RosemountLNG.com
by a crystal oscillator to achieve measurement accuracy of 0.5 mm (0.002 in.), along with a 180% reduction in volume uncertainty when compared with mechanical measurement methods.
Upgrades of legacy tank measurement systems to take advantage of radar technology’s accuracy and lower costs of ownership are often desired, but there may be practical limitations making it cost-prohibitive. For example, deploying separate radar instruments for both the tank gauging system and the overfill prevention system where only one tank opening is available would require tank modifications and taking the tank out of service, which is often not feasible. This problem can be solved by using a two-in-one radar level gauge, which consists of two separate and independent transmitters, both using a common antenna connected to an associated still pipe.
This type of migration is not trivial, but assistance is available from trusted automation suppliers as some of these companies can design and deliver an entire tank gauging system, for either upgrades or new installations, including services the provision of onsite experts.
Though important, managing inventory is no longer enough as other tank management software system capabilities are required, such as predicting abnormal situations, like rollover due to stratification.
Stratification occurs when two separate layers of LNG are formed within a tank. This stratification can potentially lead to a dangerous release of boil-off vapour, referred to as rollover. As a preventative action to detect stratification, LNG tank measurement systems can include software solutions to calculate when a rollover might occur by adding multipoint measurements to monitor tank temperature and density profiles.
Temperature is typically measured using four-wire calibrated cryogenic multiple spot temperature sensors, and these measurements are used to:
z Assist with stratification detection to prevent rollover.
z Provide an input for leak detection calculations.
z Support controlled tank cool down.
z Perform temperature compensation for tank volumes.
In the past, performing inventory management and other functions has typically required separate software systems, but newer solutions combine these capabilities into one integrated system, which cuts costs, improves ease-of-use, and accelerates operator training (Figure 2).
In addition to managing precursor situations such as rollover, an overfill prevention system (OPS) is needed to prevent spills. Due to the volatility of LNG and the associated risk of fire or explosion, an OPS often requires safety instrumented functions, with SIL ratings of SIL-2 and SIL-3 for level instruments, and an associated 2-out-of-3 voting system to trigger safety instrumented system alarms.
To provide this functionality while meeting other needs, three level instruments are typically installed on an LNG storage tank: one supporting the basic process control system, a secondary and redundant instrument for inventory measurement, and a third providing information for the OPS (Figure 3).
There is a misconception that industry standards require the level measurement technology used to support the tank gauging system to be different from the one used for the OPS, such as radar for one and an alternate technology for the other. This is typically referred to as diverse separation; however, IEC 61511 permits use of the same technology for both measurements. This is known as identical separation and is a widely used practice.
Fortunately, the two-in-one radar level instrument, when connected with its cables separated in different cable trays and with different power sources, can be used for both continuous level measurement and as an independent overfill prevention sensor, while also fulfilling the identical separation dual channel requirements of IEC 61511. Compared with using different technologies, this identical separation method provides the advantage of reducing complexity, and the likelihood of human error, during installation, operation, and maintenance.
Overfill prevention is a safety system, and it thus requires periodic proof-testing to ensure it will function properly when a safety demand occurs. These proof tests have traditionally been carried out by technicians in the field and verified by a worker in the control room, requiring a minimum of two and typically three staff to complete this recurring task. This time-consuming and labour-intensive method requires workers to climb tanks and access the level instruments, increasing exposure hours and putting their safety at risk.
However, new technology within the latest radar level instruments now enables operators to undertake partial proof-testing remotely by inputting a straightforward sequence of settings and commands from their interface in the control room. This eliminates the need for workers to climb tanks and be exposed to tank contents, thereby providing significant benefits in terms of reducing risk, saving time, and improving efficiency.
Gasum is the biggest distributor of LNG in the Nordic countries, with its Lysekil facility used for the storage and distribution of LNG for production processes in nearby industries. The terminal has a 42 m high, above-ground concrete storage tank with a 30 000 m 3 capacity.
Most of the LNG comes from the Gasum liquefaction plant in Norway, transported using the company’s own ships, which are also used for ship-to-ship transfer. Liquefied product is also distributed via company-owned trailers. Gasified product is distributed to a neighbouring refinery via a pipeline.
If the refinery had to shut down because of an interruption in its energy supply, it would cost several million dollars. It is therefore critical to maintain an uninterrupted energy supply, and a dependable tank management system based on trustworthy level measurements is a key part for providing the required level of reliability and safety.
Radar technology is Gasum’s preferred choice to provide level measurement because it requires minimum maintenance, along with other benefits. The storage tank
at the facility uses three Rosemount 5900S radar level gauges, each with an LNG antenna, with the entire assembly suitable for operation at cryogenic temperatures (Figure 4). The application is set up so that it requires alarms from at least two of the three gauges to shut down the process, thereby avoiding a false alarm that could interrupt production and affect profitability.
Since installing the radar-based solution, Gasum has been satisfied with its accuracy and reliability. There have been no unplanned shutdowns, and no maintenance requirements that involved having to open the cryogenic tank. Plant personnel can proof-test the level instruments remotely from the control room, making this procedure quicker and safer.
Gasum’s experience, and the fact that this technology has been used on more than 8000 LNG and LPG tanks worldwide in almost 40 years of service, demonstrates that radar instruments perform well when measuring liquefied gases in cryogenic or refrigerated tanks.
Radar level measurement technology – when integrated with a dedicated tank management software system –supports reliable, safe, and cost-effective LNG systems around the world, at lower cost and with greater reliability than traditional mechanical technologies. To implement such a system, either for new installations of upgrades, it is often wise to consult with an experienced supplier, one that can not only provide the required hardware and software, but also the associated design and support services.
At Timm by Wilhelmsen, we take mooring safety to the next level with our high performance Acera™ HMPE fiber ropes designed with the industry-leading Snap Back Arrestor safety feature that reduces the risks of snap back incidents.
Your safety is our priority. We are dedicated to simplifying your compliance journey and providing a total mooring solution approach that covers services, documentation, technical support, and the Line Management Plan application, ensuring compliance and safe mooring operations.
New industry standards for low temperature and cryogenic storage have been developed over the past few decades. These include the design of double-wall storage structures, testing, utilisation of load bearing insulation systems, and air raising of field-erected tank roofs, which were led by CB&I.
The company continues to innovate LNG tank designs and project delivery models to reduce risk, improve project construction schedules, and optimise overall project economics for customers. These innovations include scalable tank offerings that meet customer storage needs over a wide range of tank capacities.
Modular tanks provide the benefit of minimising the amount of site activities, shifting the majority of the tank construction work to a high quality, low-labour cost facility, within a well-controlled environment. This approach significantly reduces costs and helps advance the overall construction schedule.
The company has developed a mid scale modular tank design and execution plan for modularisation, delivery, installation, testing, and commissioning, which:
Jeff Garrison, Yogi Meher, and Mark Butts, CB&I, explore how LNG storage tanks have developed with the changing industry.
� Constructs tank module off-site in low-cost labour location.
� Transports the tank module including base slab/pedestal foundation, pump tubes, top platform, and topsides piping to grade to site.
� Installs the tank module on piles or prepared slab-on-grade.
The tank is designed for wind, seismic, projectile, blast, and dropped objects loading.
Transportation is the key for delivering modular tanks of this size and configuration.
The company can provide transport of modular tanks by vessel or truck, transporting up to two tanks per open deck module transport vessel.
CB&I uses self-propelled modular transport (SPMT) for ground transport of its modular tanks, in which the tank/slab overhangs SPMTs due to narrow roads. This transportation method was developed to balance the load on all SPMTs and avoid overloading/cracking the base slab.
There are many things to consider when designing a modular tank built offsite, shipped to site and installed in its final location, including:
� Tank size based on height and weight limitation restrictions.
� Restrictions on road widths complicate the ground transportation.
� Balancing the loads on all SPMTs without cracking the slab.
� Specialised tank bottom insulation system designed for ground and sea transport.
� Maritime experts required to confirm the mid scale modular tank-imposed loads can be accommodated by the ship deck.
CB&I’s modular tank design allows each tank to be customised for project specific requirements:
� Tank design to be validated for site-specific seismic loading.
� Tank topside design to be based on project specific P&IDs.
� Foundation design for site-specific soil conditions.
� Resistance of steel outer container to site specific external hazards such as wind, blast, and projectile loading.
� Development of tank marine transportation under pressurised condition.
In addition to mid scale solutions like the modular concept, the LNG industry also demands ever-increasing large scale storage solutions for 200 000+ m3 capacity full containment tanks. CB&I has decades of experience providing large scale storage solutions, upscaling to ensure its full containment tanks are evolving to match industry needs. This has added substantial capacity over this time frame, with many tanks 160 000 m3 and larger. Such examples around the world include large scale storage solutions located in Milford Haven, Wales, the UK; Quintana, Texas, the US; on Elba Island, Georgia, the US; and Barrow Island, Australia.
With experience gained over many decades designing and building some of the world’s largest LNG tanks, CB&I has helped reduce LNG tank construction schedules by 30 – 40%. Reduced construction schedules translate to reduced project risk for facility developers and owners. With the industry moving to ever larger tank capacities, the company is leveraging its design experience with large tank sizes
and fast construction schedules to offer designs greater than 200 000 m3, even up to 320 000 m3 in some cases. The purpose is to leverage advanced construction technology and schedule performance to offer the industry even greater economies of scale using the company’s proven project delivery model. As the industry considers scaling tank capacity up to 320 000 m3, the company’s focus is concrete full containment tank configuration as most appropriate for very large tank sizes, considering tank internal design pressures and other design requirements.
A full containment refrigerated liquefied gas storage tank system consists of an inner primary container designed to store the refrigerated product during normal operation, and a secondary liquid container designed to contain the product during an emergency leak from the primary liquid container. The primary container is composed of cryogenic steel suitable for the product temperature, while the secondary container is composed of either the same grade cryogenic steel or reinforced and prestressed concrete.
A full containment tank system as defined by API 625 shall have both primary and secondary liquid containers that are capable of independently containing the liquid product.
� The secondary container may need to resist external hazards such as an external explosion overpressure blast wave, projectile impact, or external fire.
� The secondary liquid container shall be capable of both containing the liquid product and controlling the vapour
release in the event of product leakage from the primary liquid container.
A full containment tank system shall be compliant with facility and tank design codes as well as any local regulations. Typical codes that apply include:
� NFPA 59A – ‘Standard for the Production, Storage and Handling of Liquefied Natural Gas (LNG).’
� API Standard 625 – ‘Tank Systems for Refrigerated Liquefied Gas Storage.’
� API Standard 620 – ‘Design and Construction of Large, Welded, Low-pressure Storage Tanks.’
� BS EN 14620 Parts 1 through 5 – ‘Design and manufacture of site built, vertical, cylindrical, flat-bottomed steel tanks for the storage of refrigerated, liquefied gases with operating temperatures between 0˚C and -165˚C.’
Many factors drive the ability to design very large LNG tanks, including local environmental requirements such as wind and seismic loading, and operating requirements such as operating pressure. Factors can also include upset conditions such as adjacent tank fire and projectile and blast loading. With so many potential design considerations, the company’s initial feasibility study for 320 000 m3 storage tanks is based
on basic design conditions with a focus on constructability of large structures.
CB&I’s research and development team completed design work to confirm a very large standard configuration full containment concrete LNG tank can be designed using current day code and standards requirements for the nominal design conditions defined in Table 1.
The conceptual geometry for 320 000 m3 storage is a natural extension of CB&I’s experience with very large diameter tanks coupled with experience building very tall structures. This experience allows the company to combine these diameters and heights in the same structure to achieve 320 000 m3 storage. Some of the company’s experience in constructing large low temperature and cryogenic (LT&C) tanks includes:
� Two 151 000 m3 full containment concrete LNG tanks, Quintero Bay, Chile, with an outer tank diameter of 80.4 m.
� Five 155 000 m3 full containment concrete LNG tanks, Milford Haven, Wales, the UK, with an outer tank diameter of 94 m.
� Four 159 000 m3 double wall full containment steel LPG tanks, Juaymah, Saudi Arabia, with an outer tank diameter of 98 m.
� Three 160 000 m3 full containment concrete LNG tanks, Yuedong, China, with an outer tank diameter of 82 m.
� Two 180 000 m3 full containment concrete LNG tanks, Barrow Island, Australia, with an outer tank diameter of 87 m.
� Three 190 000 m3 full containment concrete LNG tanks, Isle of Grain, the UK, with an outer tank diameter of 90.8 m.
� Two 200 000 m3 full containment concrete LNG tanks, Gulf Coast, the US, with an outer tank diameter of 89.8 m.
Evaluations on constructability must consider both diameter and height. The main constructability issues include air raising a large diameter roof, concrete placement on such a large roof, and environmental loads, such as wind, for some locations.
The company’s Construction Technology group ensures customers benefit from the latest technology, equipment, and construction methods across our global job sites. This group also maintains relationships with major construction equipment suppliers to assure an efficient flow of supplies and minimal downtime.
This group is instrumental in CB&I’s ability to design and construct large tanks, including this 320 000 m3 conceptual design.
CB&I’s latest innovations in LNG storage tank design offers a modular double steel full containment tank in an effort to minimise the amount of site activities, shifting the majority of the tank construction work to a high quality, low-labour cost, well-controlled environment. The company continues to innovate scalable tank offerings so as to meet customers’ needs for large LNG storage exceeding 200 000 m3 all the way up to 320 000 m3. CB&I continues to innovate the LNG storage tank designs to offer scalable and modular options to customers to help improve the schedule and economics.
LNG gives shipowners a pathway to decarbonisation so they can futureproof their ships. They can choose LNG to tackle emissions right now and then transition to liquefied biomethane (bio-LNG) to further reduce emissions as production continues to scale up. They can then switch to hydrogen-derived e-methane, produced using renewable energy once it becomes available. Along this pathway, there is no need to change the engines powering their ships or the fuel distribution and bunkering infrastructure they rely on. Now, in 2023, this pathway is assured because bio-LNG production is starting to scale up significantly.
The feedstock for bio-LNG is domestic and agricultural waste, for example, household waste, sewage sludge, and manure. There are more than enough of these second-generation feedstocks available to scale up production and meet the shipping industry’s bunkering needs. According to a recent study commissioned by SEA-LNG and conducted independently by the Maritime Energy and Sustainable Development Centre of Excellence (MESD CoE) at Nanyang Technological University Singapore (NTU Singapore) – bio-LNG could cover up to 3% of the total energy demand for shipping fuels in 2030 and 13% in 2050. If it is considered as a drop-in fuel blended with fossil LNG, bio-LNG could cover up to 16% and 63% of the total energy demand in 2030 and 2050 respectively, assuming a 20% blending ratio.
Titan has started work on multiple bio-LNG production and liquefaction plants. For example, the FirstBio2Shipping project – a collaboration between Titan, Attero, and Nordsol – received €4.3 million in EU funding in 2021 and construction started in 2022. The plant, located at the Attero facility in Wilp, the Netherlands, will produce approximately 2400 tpy of bio-LNG, with the first set to be produced in early 2024.
Attero will process domestic biowaste into 6 million m3/y of biogas. Nordsol and Attero will jointly produce 2400 tpy of high-purity bio-LNG and 5000 tpy of liquid bio-CO2 from this biogas. Titan, the exclusive long-term off-taker, will supply the bio-LNG to the shipping industry to reduce its GHG emissions. The produced bio-LNG will reduce GHG emissions by 92% compared to conventional maritime fuel, representing more than 87 500 t of CO2-e net absolute emissions avoided during the first 10 years of operation.
Additionally, Titan, the Port of Amsterdam, BioValue, and Linde Engineering have partnered to build the world’s largest bio-LNG plant. Once fully operational, the plant can produce up to 200 000 tpy of bio-LNG. The first bio-LNG from this plant is expected in 2025 and the bulk of the
Régine Portocarero, Global Business Development Marine LNG at Titan, provides a status update on the LNG pathway to net-zero shipping and details the company’s work scaling up the supply of bio-LNG.
bio-LNG produced will be supplied to the bio-LNG-powered vessels of Titan’s launching customer. The plant will be located adjacent to Titan’s berth in the Port of Amsterdam. The bio-LNG will substitute fossil fuels, avoiding about a million tpy of CO2 equivalent, equal to the annual emissions of about 25% of all diesel cars in the Netherlands.
BioValue, one of the largest biogas suppliers in the Netherlands, will supply a significant part of the biogas required for the total bio-LNG production. For this, BioValue will construct a new biogas plant adjacent to the bio-LNG plant. The remaining biogas will be sourced from other production installations throughout Europe that are connected to the existing gas grid. This hybrid sourcing setup enables the scale required for impactful decarbonisation of the marine industry. Meanwhile, Linde Engineering will perform the engineering based on its proprietary liquefaction technology.
Bio-LNG is currently more expensive than conventional LNG, but with economies of scale, scope, and learning, costs and prices are expected to come down. According to the SEA-LNG study (Figure 1), the average cost for delivered bio-LNG is forecasted to fall by 30% by 2050 compared to today’s values, mainly driven by the reduced cost of producing biomethane in large-scale anaerobic digestion plants. This will make bio-LNG one of the cheapest sustainable alternative marine fuels, compared to bio-LNG and electro-fuels, including e-ammonia and e-methanol. It will therefore be a cost-effective substitute for oil-based fuels and further enhance the environmental performance of LNG.
By using waste feedstock, bio-LNG production can capture methane that would otherwise be released into the atmosphere. Therefore, the outcome is a fuel that is potentially net-negative in GHG emissions, not just net-zero. By assisting with the recycling of waste, bio-LNG production also aids in waste management and supports the circular economic model that most environmentalists and economists agree is critical to making the economy more sustainable.
This is in addition to how LNG is already contributing towards achieving the industry’s decarbonisation goals today.
LNG is a lower-emission fuel that is already playing an integral role in achieving the International Maritime Organisation (IMO’s) clean air and GHG targets.
According to the second lifecycle GHG emission study on the use of LNG as a marine fuel from Sphera – a peer-reviewed well-to-wake study of LNG emissions updated in 2021 –LNG offers a 23% reduction in GHG emissions compared to VLSFO.
The negligible amount of sulfur in LNG means sulfur oxide (SOX) emissions are reduced close to zero, and nitrogen oxide (NOX) emissions can be reduced by up to 95% to meet the IMO Tier III limits. LNG also virtually eliminates particulate matter (PM), including black carbon or soot, which is a growing environmental concern.
The resulting local air quality improvements are another often overlooked benefit of LNG. SOX, NOX, and PM emissions have been proven to have a significant impact on health. By eliminating these local vessel emissions, the health and safety of passengers, crew, and port residents are improved. This is just one of the reasons that LNG has particularly gained momentum in the cruise sector.
Safety is another major benefit of using LNG. Safety must not be taken for granted, especially as new fuels and technologies emerge. Seafarers have extensive experience safely working with LNG, so despite challenges posed by its flammability and cryogenic nature, LNG has been shipped and bunkered around the world for over 50 years without any major incidents at sea or in port. Simply, this is because rigorous safety standards, best practices, and training have been implemented over decades. Almost all of this work also gives bio-LNG and hydrogen-derived e-methane a head start too.
With LNG bunkering and infrastructure well established, shipowners have a clear long-term pathway to adhering to upcoming and increasingly stringent regulations, such as the EU’s ‘Fit for 55’ package which is paving the way to climate neutrality in Europe by 2050. LNG will give ship operators a competitive advantage over those using oil-based marine fuels within the EU’s Emissions Trading System (ETS), while bio-LNG goes a step further and can provide a long-term competitive advantage over even traditional LNG.
Bio-LNG also provides advantages in voluntary carbon markets. Titan and partners are offering carbon insetting, so it is possible to compensate for the emissions of a voyage either in full or partially. The system allows the transparent transfer of environmental benefits, decoupling carbon reduction from specific transport activity, and enabling the greening of overall transport activity. It is particularly relevant involuntary carbon markets and for highlighting cargo owners concerned about their Scope 3 emissions.
In the past year, vessel orders reflect the confidence shipowners have in the benefits of LNG, with 2022 LNG-fuelled vessel orders virtually the same as
those in 2021, the record year to date. This is despite exceptionally high LNG prices last year. While vessel orders for methanol-fuelled ships have been closing the gap in recent months, there is still a strong production line of LNG-fuelled ships coming soon.
Approximately 20% of deadweight tonnage on the orderbook is LNG dual-fuelled and some sectors, such as car carriers, are seeing a remarkably high degree of LNG penetration – with the latest data from Clarksons showing that 93% are LNG dual fuel. Based only on existing orders, DNV forecasts the number of LNG-fuelled ships will reach 876 by the end of this decade. However, if current growth trends continue, the industry can expect to see 2000 – 4000 LNG-fuelled ships in operation by 2030.
This growth is being reflected in the LNG bunkering market too. Shipowners who switched to VLSFO during the price spike are now returning to LNG. This optionality is a major benefit for owners but from an environmental perspective, it is encouraging to see a return to higher LNG bunkering demand.
In order to meet industry demand for LNG, Titan has expanded its LNG infrastructure and bunker vessel fleet. Most recently, it chartered the 8200m 3 Alice Cosulich LNG bunker vessel from Fratelli Cosulich. Additionally, the company purchased two LNG carriers from Seapeak, the Titan Unikum and Titan Vision, which are being retrofitted with bunkering capabilities. Both sister vessels have a cargo capacity of 12 000 m 3. The two new additions to the fleet allow Titan to deliver fuel to a wider range of LNG-powered vessels, and expand its assets into other locations around the world including South-East Asia and the Mediterranean. Titan’s established FlexFueler001, FlexFueler002, Green Zeebrugge, and Optimus round out its fleet which is a mix of owned and chartered vessels. Synthetic and biogenic fuels have the same chemical composition as their fossil-derived precursors, so these vessels will continue to service the industry as bio-LNG and hydrogen-derived e-methane gain ground in the market. E-methane can be made using carbon captured from industry or the atmosphere and hydrogen created using renewable energy to achieve an overall net-zero product. It will be the next form of methane (or LNG) to have production scaled up to meet growing market demand.
While LNG and bio-LNG are currently the focus of Titan’s bunkering operations, and the company recognises the LNG pathway to decarbonisation as a practical, lower-cost, and lower-risk option, it does remain open to supplying other viable clean fuels. Each low-emission, zero-emission, and net-zero fuel has its nuances but they are all expected to essentially require similar capabilities to supply. This was part of the rationale for Titan’s sustainability strategy update and name change last year.
The LNG industry continues to lead the way in many respects: improving local air quality, reducing GHG emissions now, scaling up the supply of net-zero bio-LNG and e-methane, and forming partnerships across the LNG value chain to name a few. All of this work goes to ensure that LNG, bio-LNG, and e-methane will continue to play a key role in shipping’s evolving fuel mix.
LNG as a stepping stone to future fuels, standardisation, and deploying more services to clients are among the key drivers behind current and future developments of the LNG bunker fleet.
The shipping industry is currently at a crossroads as it considers what alternative fuels it will need to deploy to reach net zero emissions. LNG as a fossil fuel is a transit technology; however, with the status it now has and the technology it uses, it will be in the market for the next 15 – 20 years at least and is likely to bridge the gap to using future fuels, especially with the potential for synthetic and bio-LNG.
The market for LNG as a ship fuel is continuing to strongly grow. DNV’s Alternative Fuels Insight (AFI) platform
shows that there are currently 911 confirmed LNG-fuelled ships (consisting of both the current global fleet and existing orders). Of these, 512 ships are on the orderbook. Some 36% of the current fleet operates globally, with this figure set to swell as 78% of LNG-fuelled ships on order will operate globally, according to DNV’s AFI.
The LNG bunkering infrastructure has rapidly developed to support this growing fleet. AFI statistics show that there are 43 bunker vessels/barges under operation, with 21 on the global orderbook, due for delivery between 2023 – 2025, and 21 potential bunker vessels/barges under discussion.
This shows how far LNG bunkering has come since 2013, when the first bunker vessel consisted of the small, converted vessel, Seagas, to bunker Viking Line’s
Johannes Dziuba, TGE Marine Gas Engineering, Germany, evaluates how the bunker ship fleet is transitioning from first and second to third-generation vessels.
Viking Grace. This was followed by the deployment of small scale LNG carriers to carry out ship-to-ship transfers, until 2017, when the first three purpose-built bunker vessels came onto the market.
These vessels, having started in Europe, and then expanded to the US and Asia, are now all over the world – apart from two blind spots: The Persian Gulf and Panama Canal. For the former, while LNG supply is geographically close in Qatar, there are no bunker vessels there yet. However, as LNG bunkering infrastructure continues to develop, this area is expected to see LNG bunker ships in the future. Meanwhile, LNG bunker vessels will probably arrive at the Panama Canal soon, potentially with LNG from the US.
From conversions, including Seagas, to the first generation of bunker vessels in 2017 that were purpose-built for bunkering, the industry has now entered the era for second-generation vessels. These vessels are client focused, more streamlined, and therefore less complex and expensive than the extremely versatile but intricate first generation, which were still exploring what was needed of them.
Increasingly, second-generation vessels are including services other than just bunkering, with ever more offering gassing-up and gas-freeing services. A driving factor for development is to speed up these processes. When a client vessel is underway for three weeks, even just half an hour of lost time can count. Any hour saved is of real value for an owner. Therefore, there is a focus on qualifying new equipment and deploying new combinations of equipment that can save time.
One example is related to producing nitrogen on board the bunker vessel. Different systems can be used for this, including pressure swing adsorption (PSA) plants, membrane systems and having containerised liquid nitrogen, before vaporising it. Replacing the cargo atmosphere with nitrogen means warming the natural gas and the tank structure up from a very cold temperature, from -140˚C and lower to at least 10 – 15˚C. This is time consuming because the heat transfer from nitrogen to the steel structure of the tank is very poor. New equipment solutions could push through more nitrogen at a warmer temperature, therefore speeding up the process. If a PSA plant was to push through the same quantity of nitrogen, the plant would need to be huge, and the process would be very energy consuming.
Standardisation is an overriding theme within the bunker vessel sector, and this would also speed up processes and boost operational efficiency, as well as make these vessels more cost efficient. The prices of bunker vessels are still high due to their very specialised equipment.
Achieving equipment and processes standardisation means that bunker vessel owners would know what they would get in term of bunkering, as would clients, and familiar interfaces would increase ease of operations and efficiency. It would help abolish the current need for complex studies to work out whether bunker vessels are compatible with the receiving ships or not.
An example is when it comes to bunkering cruise vessels. Their overhanging life boats makes the operation complex as bunker ships cannot come alongside. If the industry could create a more streamlined approach, it would make it easier for both bunker and client vessel owners to find a solution to this issue.
Another example relates to flow meters and gas analysers, which have been increasingly deployed to help calculate how much energy content is transferred in the bunkering process, overtaking the traditional approach of measuring the cargo volume before bunkering and then afterwards calculating out the quantity transferred. Having the flow meter work continuously during the operation and online simultaneous analysis of the gas boosts the efficiency of the measurement process.
However, the challenge is that multiple standards are used for the calibration and certification of the different
equipment pieces of the flow meters and gas analysers, making it a complex process. In addition, to certify the whole system means that a certified surveyor has to go on board and check both the equipment and their arrangements. Again, this is a complex process with no common standard, where even an official certificate might not be accepted by everyone. Applying a common standard to these systems that is adhered to globally would speed up the whole bunkering process.
On the receiving ship side, moves to standardise can be seen as there is a requirement that bunker station specifications are according to The Society for Gas as a Marine Fuel (SGMF) guidelines. But herein lies another challenge: there are different entities and standards for both the bunker and receiving sides. These varying standards for each type of vessel means they might not all fit together, creating a need for a larger exchange of knowledge and experience so that different organisations become
more aligned. This is already starting to happen, with members of each side coming together, but the stronger this theme becomes, the better it will be for everyone involved in terms of flexibility, standardisation and cost.
There have recently been several milestone bunker vessel orders that reflect both the current trends in the market, as well as catering to the growing number of LNG-fuelled vessels.
In 2022, Canada-based owner, Seaspan, contracted Chinese shipyard, Nantong CIMC Sinopacific Offshore & Engineering Co. Ltd, for three 7600 m 3 LNG bunker vessels. TGE Marine is designing and supplying the cargo handling and fuel gas systems for the trio of vessels.
The vessels will serve various types of clients and will each be equipped with two International Maritime Organization (IMO) Type C cylindrical tanks and an LNG sub-cooling system to facilitate cargo conditioning during transit, operation and anchorage. The customised ship-to-ship transfer system will enable bunkering of LNG-fuelled vessels fitted with varying tank types (including Type C, membrane and vacuum insulated), in addition to cooling-down and warming-up the client’s systems.
Due to operate from 2024 onwards off the west coast of Canada, these vessels represent a landmark for the west coast of North America as they are the first dedicated LNG bunker ships to be built for that region. Seaspan has a fleet of LNG-powered ferries which have recently piloted the use of renewable natural gas (RNG).
China has also recently seen some ground-breaking bunker vessel projects, to cater to the increase of LNG-fuelled vessels there. Nantong CIMC Sinopacific Offshore & Engineering Co., Ltd is building a 12 000 m 3 LNG bunker vessel for China National Offshore Oil Corporation (CNOOC). TGE Marine has been awarded the contract to design and supply the cargo handling and fuel gas system. The bunker vessel will supply its cargo to any LNG-fuelled vessel in Chinese waters and it will be equipped with two IMO Type C cylindrical tanks with a design pressure of 4.5 barg. An LNG sub-cooling system will also be fitted in order to condition the cargo to -163˚C.
Highlighting the drive to save energy, the shipyard and TGE Marine have together developed a cold recovery system to use the low temperature of the cargo for the ship’s air conditioning system, thereby reducing the overall power consumption. While such features have regularly been seen in cruise ships, this is an innovation for the bunker vessel sector, and one that the industry will see more of as boosting energy efficiency becomes ever more important, especially in the face of EEDI, EEXI, and CII measures.
This LNG bunker vessel is poised to be the second largest in China, after the 30 000 m 3 LNG carrier Hai Yang Shi You 301, also owned by CNOOC, was converted from a gas carrier to a bunker vessel last year. TGE Marine supplied the cargo handling system, fuel gas system and
tank design – the largest Type C tanks on the market at the time – to the original ship in 2015.
Looking ahead, the drive to use alternative fuels to meet zero emissions targets suggests that LNG bunker vessels that will be able to cater to these fuels in the future will be developed.
The industry has already seen this move from the fuel gas system side. Höegh Autoliners’ eight new Aurora class car carriers will have LNG containment and fuel gas supply systems that will be delivered with ‘Ammonia Ready’ and ‘Methanol Ready’ class notations. TGE Marine is designing and supplying this equipment. The stainless-steel material being used for the tank in these vessels is key, as it is able to handle the different characteristics of these fuels.
Being multi-fuel ready can be expected to develop on the LNG bunker vessel side too, as the shipping industry aims to future-proof vessels by preparing for the fuels of the future.
Certainly, a major topic for ship owners when it comes to discussing the development of new LNG bunker vessels, is, how can these vessels be made more flexible for future conversion to ammonia or methanol.
When it comes to ammonia, designing a bunker vessel is not an issue – ammonia-capable carriers have been on the market in excess of 40 years. The challenge comes from the receiving vessel side. Ammonia is very toxic and creating a fuel gas supply system that is inherently safe, is one of the biggest challenges. Today, rules and regulations for the use of ammonia as fuel are still under discussion at
IMO and other key organisations and regulatory bodies in the marine industry.
There is one current bunker vessel theoretically capable of carrying ammonia as cargo: Anthony Veder’s Coral Methane, the world’s first combined LNG/LEG/LPG carrier which was converted into a bunker vessel in 2018. The 7500 m 3 bunker vessel has tanks of stainless steel, and adding ammonia to its cargo list would be relatively easy (with some modifications to the cargo handling system). TGE Marine supplied the gas handling and fuel supply systems and tanks for this project.
LNG will be in the market for at least the next 15 – 20 years – and for much longer when it comes to synthetic and bio-LNG forms – emphasising the importance of standardising the bunker fleet and its operations. The results of this will be also beneficial for the development of bunker vessels for alternative fuels.
Because the question of what fuels will be used in the future is key to bunkering, and shipping in general, this topic will lead the industry from second-generation to third-generation LNG bunker vessels, creating a fleet that is prepared for a second life with a different fuel. While the second-generation bunker vessels are purpose built, third-generation vessels are likely to be more flexible, enabling them to be ready for different fuels.
However, once the shipping sector has decided on which future fuels will be used, then the industry is likely to see another generation of vessels that has moved back to being tailored to their customers’ needs.
The LNG industry in 1997 was very different to how it is today. Many changes have been developed and implemented in an industry known for its stringent safety measures and procedures.
Although there had been a few LNG ship-to-ship transfers carried out then, they were never envisaged as something that was ever going to become mainstream. Fast forward over 25 years, and there is now genuine intrigue as more and more people within the industry look to LNG ship-to-ship (STS) as a solution for their LNG project needs.
Historically, LNG ships were on long-term charters between the Gulf and the Far East and cargo transfers involved loading and unloading LNG via terminals, which had limitations in terms of accessibility and capacity. But how did the industry get from there to here? How has the industry changed?
Stuart Goddard, CEO of STS Marine Solutions, UK, delves into what the future might hold for the ever-changing LNG industry.
Firstly, the evolution of LNG carriers must be looked at. LNG carriers have become larger and more efficient, allowing for increased cargo capacity, and reducing transportation costs. The first LNG carriers were developed in the 1950s. These early vessels used spherical tanks to store LNG. Spherical tanks were chosen for their ability to withstand the low-temperature and high-pressure conditions of LNG. These ships were relatively small, with capacities ranging from a few thousand cubic metres to around 30 000 m3. In the 1960s, the development of membrane-type LNG carriers revolutionised the industry. These ships used a membrane system, typically made of metal alloys or composite materials, to store LNG. The membrane acted as a barrier between the cargo and the ship’s hull, allowing for more efficient use of space. Membrane-type carriers offered larger cargo capacities and improved safety compared to spherical tank designs. As the demand for LNG grew, so did the need for larger LNG carriers. Over time, vessel sizes increased significantly. Initially, LNG carriers had capacities of around 30 000 – 40 000 m3 However, modern LNG carriers can now exceed 200 000 m3 of cargo capacity. This increase in size has allowed for more efficient transportation of LNG, reducing costs and improving economies of scale. This has facilitated the need for STS transfers to optimise logistics and deliver LNG to markets that may not have access to the required LNG infrastructure.
Secondly, FSRUs have also become popular in regions without fixed LNG infrastructure. FSRUs often rely on STS transfers to receive LNG cargoes from LNG carriers for regasification and subsequent delivery to onshore pipelines. STS Marine Solutions is working with several companies in this sector, with others enquiring about providing consultancy and assurance services as companies look towards those with industry-recognised experience in the field. Most FSRU terminals look to adopt a double-bank STS approach as it is the fastest and most cost-effective solution. This involves a visiting LNG carrier mooring alongside an FSRU with a dedicated hard arm system to act as the interface between the two ships, but these tend to require a large amount of re-engineering of vessels leading to increased costs and dry dock time.
The more common approach adopted in recent years is the use of dedicated STS transfer systems using hoses. The relatively lower cost, lead time, and flexibility of these systems is the major driving factor for FSRU operators, with STS Marine Solutions providing more and more client consultancy on the specification, provision, operation, and maintenance of such systems. The company has also been working with several companies to offer full-service provision for open water STS services to allow for breakbulk, trade route optimisation, and double bank STS arrangements at terminals. With most Russian gas now being predominantly backfilled with US, West Africa, and Middle East cargoes, traders, shippers, and importers are looking into the most cost-effective solution to offset the large costs of shipping cargo from further afield. STS services around the Mediterranean, Suez, and the Far East in locations, such as Subic Bay, are seen as the perfect solution for STS Marine Solutions clients with infrastructure being made available in these locations.
Another area that has seen the demand for LNG STS transfers increase is the growth of LNG as a marine fuel and LNG bunkering operations. LNG bunkering is seen as a promising solution to reduce emissions from the maritime sector and comply with stricter environmental regulations. As the infrastructure for LNG bunkering continues to expand and technology advances, the use of LNG as a marine fuel is expected to increase, promoting a cleaner and more sustainable shipping industry. This sector has seen significant advancements in STS transfer infrastructure, including specialised bunkering vessels and dedicated LNG bunkering terminals.
However, with this growth in demand, the concern remains: when looking at LNG STS operations – how does the industry ensure it remains a safe and viable option, whilst also giving flexibility?
The first improvement in LNG STS transfers are the technological innovations which have enhanced the safety and efficiency during operations. Planning using systems, such as Optimoor simulations, has allowed for better planning of operations, minimising the risks associated with having vessels alongside one another. The equipment used has also greatly improved. From the transfer hoses to the electrically controlled ESD systems, vessel drift-off systems and Emergency release couplings, everything involved in the facilitation of the transfer has evolved over the years.
The current systems in use today mimic the functionality of a shoreside ESD system, allowing cargo transfers to be carried out safely and efficiently, but ensuring there is no compromise on the safety of the operations. The systems are also highly flexible and can be put on a plane or a ship at short notice to facilitate operations anywhere in the world. This portability of the equipment has also meant that it gives vessel owners and operators an emergency backup in the unforeseen event it happens to any of the fleet of vessels they control. This allows vessel owners to have some peace of mind that in the event of anything happening the vessel will be able to get the cargo off safely and efficiently in line with best industry practices.
Safety regulations and industry standards have also been developed and refined over the years to ensure the safe handling of LNG during STS transfers. These include guidelines for risk assessment, emergency response planning, and training of personnel involved in LNG operations. STS Marine Solutions has been involved in the setting up and development of LNG STS transfers from the outset, utilising its experience in carrying out oil STS operations to develop robust procedures to ensure the practices put into place would maintain the solid safety reputation that the LNG industry has always garnered. Over the years, the company has seen developments in the industry from the equipment being used to the development of the pre-operational requirements which are key to ensuring a successful operation.
It is not a question of just putting two ships together and fitting the equipment; there is as much, if not more, preplanning involved in every operation. Each operation is run through a stringent set of checks with not only the vessels involved, but also the owners and operators. This is because this can sometimes be a new operation for them, so one of the key things is ensuring that anyone who is involved is comfortable with what is being proposed. This normally starts with a nomination then, as a service provider, the company would then reach out to ensure that all parties are aware of the proposed operation and then they are happy with that proposal.
Then comes the assurance side of the operation; it needs to be ensured that the vessels are not only compatible with each other, but that they are compatible to carry out STS operations, from a mooring perspective, down to a cargo handling perspective. The company needs to ascertain if there are any issues with the vessels involved and, if so, whether these issues affect the operation in any way. Then, a proposed mooring arrangement from one of the mooring masters is looked at before being shared with each of the masters of the vessels to ensure that it can be done and that the masters are happy with the arrangement.
There is then a joint plan of operations to complete, which normally involves not only the vessels, but also the owners and operators. This develops into a detailed document that covers all aspects of the operation from the very beginning approach to when the vessels are all clear.
From all of the developments over the years, none is more important than the work that is completed before any STS
takes place. This work ensures that any operation is fully risk assessed and completed with a set of parameters that everyone is aware of, and an understanding from all parties of what will happen if the unexpected does occur.
One of the biggest roles of a service provider is to provide the comfort that the operation will be successful, but in the unlikely event that it is not, then the officers and crew can rely on an experienced team to be backing up the operation. It is not just about the people onboard, but also about the team that backs them up. It is not about the mooring master or the superintendent, it is about the operator and the assurance team, the HSSEQ coordinator to the accountant. Part of carrying out successful STS operations is ensuring that the people are part of that team and that they are integrated into the process from the very beginning.
So, in an ever-changing industry, the question is what is next? This is not an easy question to answer as where the industry is currently is not somewhere that people thought it would be. So, what is the next thing that will move the industry forwards? Is it down to the use of ammonia or hydrogen as a fuel, or is it the use of the equipment currently used for STS being used for shoreside installations as a quick alternative to the building of a full scale LNG facility? In this industry, the next innovation is just around the corner, but what that will be is a mystery to most. What is clear, however, is that companies such as STS Marine Solutions are excited to see what the future holds, and how it will be involved with developing it.
The LNG bunkering market was initially developed in Norway in 2002, to deliver this new bunker fuel to small ships, such as offshore supply vessels (OSVs), fishing vessels, and coastal ferries. However, recent environmental regulations, put in place by international and local (both national and regional) regulatory bodies, have driven shipowners to build new ships or to convert their existing ones to operate on LNG. As such, traditional bunker fuels, like heavy fuel oil (HFO), marine diesel oil (MDO), or marine gas oil (MGO), are being displaced. This choice of LNG as a marine fuel has necessitated the growing need for LNG bunker vessels (LBVs) to support large deep-sea ships that cannot receive sufficient bunkers by road tanker.
At present there are only 30 small scale LNG carriers in service, all built in European, Japanese, or Chinese yards since the early 1990s. These have LNG cargo capacities ranging from 1100 – 45 000 m³, but none have been specifically designed and built for ship-to-ship LNG bunkering operations.
In 2018, there were only five dedicated LBVs in operation, both newbuilds and conversions. However, this rapidly increased to 21 at the start of 2023, and when LNG bunker barges (LBBs) are included, this number increases further to 40 vessels operating worldwide, including the likes of northern Europe, the Mediterranean, the US, Canada, South Korea, Japan, Malaysia, China, Singapore, Brazil, and Australia. Initially, these dedicated
LBVs were introduced to service medium to long-term charter parties but with utilisation also supplemented by ad-hoc opportunities, and one existing LBV was designed specifically to service only one dedicated ferry service. The 33 LBVs currently on order and under construction range from 3000 – 18 000 m³ in LNG capacity, and in January 2023 a 30 000 m 3 LNG carrier was converted to the world’s largest LBV.
The evolution of the LNG-fuelled fleet was initially relatively slow, but, since 2010, the number of LNG-fuelled ships has increased between 20% and 40% per year. At the beginning of 2017, approximately 100 LNG-fuelled ships were in service. This has since rapidly increased, with vessels numbering over 350 at the start of this year,
many of which of which are large tonnage ships like tankers (100, with 92 on order), container ships (43, with 175 on order), RO-RO and RO-Pax ships (32, with 16 on order), bulk carriers (18, with 50 on order), and car carriers (10, with 119 on order). In addition, there are 13 cruise ships in operation with a further 26 on order; this specific sector requirement is driven by local and national environmental regulations, and by cruise operators wishing to exhibit a ‘greener’ outlook. These cruise ships will require a larger bunkering capability in ports away from general trading routes.
It is predicted that the number of LNG-fuelled ships will exceed 800 by 2025, and possibly be significantly in excess of 2000 by 2030. Therefore, there has been a clear
and significant evolution since the first LNG-powered ships, which incorporated only a few hundred cubic metres in storage capacity, to the ultra large (over 23 000 TEU) container ships of today, which have an LNG fuel capacity of 18 600 m³.
LNG bunkering for larger ships requires a dedicated service within a major port, or at least a smaller adjacent one within close proximity. Such services are typically driven by the needs of a major LNG user or producer, thus new bunkering hubs are typically developed, leveraging the existing bulk LNG infrastructure. Most of the world’s top bunkering ports are now offering LNG bunkering, with LNG bunkers being obtainable at 185 ports worldwide, and a further 50 facilities planned for 2025.
As the number of LNG consumers (receiving ships) increases, the number of LBVs required will obviously also need to increase to supply the growing demand. It is likely that a range of LBV types will be developed to suit individual port and regional requirements, which is borne out by the variation in the existing and planned fleet. Smaller ports may well utilise a multi-fuelled bunker vessel that can carry, for example, LNG (predominantly methane [CH 4 ]) together with, conventional fuel oils MGO, MDO, HFO (C n H 2n+1 ), and/or possibly also methanol (CH 3 OH), or ammonia (NH 3 ) to remain competitive.
The development and design of LBVs is still a comparatively new and evolving sector. Due to the relative
infancy of the concept, at present there are no fixed and industry accepted designs because different operators require, or are perceived to require, something different. The shipping industry is currently to some degree ‘feeling its way’ or ‘learning by mistakes’, as when many of the current LBVs were being specified, procured, and built, no-one knew what the future was going to be, and, in some instances, did not even know with any certainty how the receiving ships, to which they would be bunkering LNG, could possibly be configured.
It is difficult for shipowners to produce a shipbuilding specification for an LBV which is as robust and mature as that which they would issue to shipyards for more established ship types, such as coastal or small scale feeder LNG carriers of a similar capacity. The only current exception to this, and thus an avenue for reducing uncertainty, is if an LBV is being procured to solely bunker only one or two specific types of ship, the requirements for which are well known and fixed. However, such dedicated operational scenarios are the minority and if the utilisation of such a complex and expensive asset, namely the LBV, is to be maximised it is likely it will still have to service other ships with differing configurations and requirements – these are probably conflicting and are unknown or cannot be predicted with any certainty when the shipbuilding specification is being produced.
This inability of shipowners to produce a shipbuilding specification with any certainty is a major issue for many shipyards as one of their primary goals is to propose a low-risk compliant technical response which has commercial advantage over its competitors. This obviously requires an unambiguous specification. In addition, designs offered by shipyards to shipowners are often what the shipyard wants to build (to suit their production processes and throughput), rather than what the shipowner wants and needs. In addition, shipyards typically may not fully appreciate the operational profile and novel aspects of a new and specialised ship type.
On the one hand we have the shipowner, who may not be able to bound the operations of the ship to be procured, or have the required resources to guide design development. On the other hand, there is the shipyard, which may not have the resources or time to interrogate and question a shipbuilding specification and assess its validity to be transposed into a cohesive design. This will then lead to issues when trying to develop a ranked set of dominant design drivers and requirements in order to down-select solutions for incorporation into the building blocks for an operationally effective ship design.
The solution to this is not straightforward but is achievable given time, as the LNG bunkering sector matures. It will require the determination of all stakeholders (trading ship operators, LBV shipowners, ship designers, shipbuilders, industry organisations, regulators, etc.) to collaborate.
Compatibility of the LBV with the receiving ship(s) is the key operational issue in designing a near-optimal and robust LBV, the primary driver being alignment; hence, it is paramount that there is a thorough understanding of
the type, size, and configuration of ships to be bunkered, which as outlined previously is currently difficult. A comprehensive and robust compatibility study is required, and is therefore a vital element in the overall ship design process for a LBV, or LBB. As discussed previously, such analyses and resultant potentially complex, non-standard, and expensive solutions and arrangements are not what most shipyards would ideally wish to embrace, as they may not suit their production processes and capabilities or overall yard schedules. However, shipyards together with shipowners, are learning quickly that LBVs are different to both traditional oil bunker barges and also coastal trading and small scale feeder LNG carriers.
Therefore, both parties need to understand with certainty and to some depth what the design must achieve in operation, and then take up additional investigations, design, and engineering to address this.
With this in mind, the LBV hull must of course be of sufficient size and configuration for the following:
� LNG cargo capacity and chosen containment and cargo systems, and possibly additional capacity etc. for other liquid and/or cryogenic fuels.
� Cargo configuration – number and distribution of tankage.
� Navigational constraints for operations in certain ports and waterways – length, breadth and operational draught, and maybe also air draught due to bridges, etc., and possibly implications regarding line of sight.
� Limiting or good dimensional relationships regarding global strength, intact stability, motions especially roll, freeboard (regulatory and for survivability), etc.
� Internal topology – subdivision is critical not only for damage stability performance, but also for efficient operation and maintenance.
� Water ballast capacity and system – number and distribution of tanks, and is constant draught required or even desired during bunkering evolutions to minimise freeboard change, or can a ‘ballast free’ design be facilitated with maybe only trimming ballast.
� Bunkering and transit environments – possible requirement for a low wash hull form for operation in restricted waters with very good slow or zero speed manoeuvrability characteristics, good motions whilst bunkering for safety and operations, etc.
� Mooring and enlarged multiple fendering systems, and operations of these.
� Bunkering systems and allowance for station (manifolds) offsets, together with bunkering and crew transfer operations.
� Machinery, propulsion, and manoeuvring systems for very good slow or zero speed manoeuvrability, possibly incorporating some degree dynamic positioning (DP).
� Accommodation block, invariably including enhanced crewing levels over those for small scale feeder LNG carriers; storing and associated laydown areas etc.; lifesaving appliances (LSAs), etc.
The three key and unique aspects driving the design of LBVs, in addition to standard ship design drivers, are:
� Parallel middle body (PMB) length – to facilitate safe and efficient mooring operations. The outcome is quite often the development of a longer LBV,
with non-typical dimensional ratios compared to traditional coastal trading or small scale feeder LNG carriers or oil bunker barges. Such a design will have a significantly larger operational envelope and hence potential utilisation and earning potential advantage over a slightly shorter LBV of typical dimensional ratios which may have a marginal advantage on first (construction) cost, manoeuvrability, etc.
� Manifold(s) location and alignment – typically, LNG bunkering has to be undertaken with the LBV moored side-by-side with the receiving ship, hence LBVs are typically fitted with midship manifolds, potentially more than one set at different heights above the waterline (or main deck), with associated equipment and craneage to facilitate hose handling. A number of newbuild LBVs have high-reach cranes and long LNG hoses and associated storage reels to accommodate bunkering high freeboard receiving ships in the open-air on their main deck. However, ‘gun port’ doors located in the side shell above the waterline, as is standard for bunkering of fuel oil, etc. has now emerged as the preferred option for cruise and container ships, etc. negating the requirement for such craneage and hoses. Receiving ships with LNG bunker manifolds on the bow or stern also exist, hence requiring LBVs to have additional manifolds at the extreme bow and/or stern with associated craneage etc. to facilitate hose handling which could obviously lead to issues related to relative locations of the LBV and receiving ship PMBs and the location of the fenders on the LBV. At present tandem mooring has not been adopted, even when there are very difficult and complex bunkering operations, however given time LBV designs will probably evolve to facilitate tandem bunkering operations as this would by default eliminate the required parallel body length issue required for safe mooring.
� Access from the LBV to the receiving ship – access from the LBV to the receiving ship is obviously a major safety issue in preparing for and concluding mooring and bunkering operations. Typical solutions involve the utilisation of ladders or man-riding cranes. The current adoption of ‘gun port’ doors located in the side shell of the receiving ship is assisting this situation.
As alluded to above, the design of an LBV is not just an exercise of taking an existing design for a small scale feeder LNG carrier, adding some cranes and fenders etc. and simply adapting the cryogenic cargo system to export LNG. It is so much more as it is still a relatively little-known, very advanced, and evolving ship type which is operationally and technically unique with very specific and different design drivers in addition to the standard applicable ship design ones.
The design and capacity of LBVs varies vastly at present due to current perceived demands, charters etc. and is obviously to some degree influenced by the current and proposed shore infrastructure. Hence, the design of LBVs will also change as local infrastructure develops as well as with the evolution of the design of receiving ships, to be bunkered with LNG.
Due to the complexity of LBVs, they attract a cost penalty as compared to standard small scale feeder LNG carriers of the same capacity. Therefore, in the development of a robust solution for bunker operations the utilisation of purpose-built LBVs must be closely considered and managed with care to justify the investment needed.
Consequently, this requires some new thinking and collaboration on behalf of both the LBV owners (and the operators of potential receiving ships) and ship designers. In addition, the development of an operationally robust LBV requires the sometimes-significant adaption of current marine technologies and incorporation and marinisation of some new ones to both the hull and its systems.
Explore the world of Bernoulli Marine Limited, a distinguished leader in Naval Architecture and Marine Advisory services. With an impressive track record spanning over 30 years, our team boasts unparalleled expertise in engineering, supervising, and delivering successful marine and offshore oil
Everyone wants to get what they paid for. LNG Industry is independently verified by ABC, because we want our advertisers to know they’re getting the exposure they’ve been promised.
ABC. See it. Believe it. Trust it.
Approximately 45% of the attendees for Gastech will be coming from Asia, followed by 21% from North America
Singapore comes from the Sanskrit name ‘Singapura’, which means ‘lion city’
There will be over 750 exhibitors at Gastech 2023, hosted by Singapore
There are 20 international country pavilions at Gastech 2023
The lyrics of Singapore’s national anthem are printed on the back of the S$1000 note
Singapore consists of 64 islands
Jewel Changi Airport is home to the world’s tallest indoor waterfall
Gastech 2023 is being co-hosted by ExxonMobil, Chevron, Venture Global LNG, and Shell
Gastech is returning to Singapore for the first time since 2015
There will be over 40 000 international visitors attending Gastech in Singapore
There are four official languages in Singapore: Malay, English, Chinese, and Tamil
Singapore is the only country in the world that has banned chewing gum
Singapore is the largest port in Southeast Asia, and one of the busiest in the world
The Singapore Sling was first created in 1915 by a Raffles bartender, and is widely regarded as the national drink
SIMPLIFY DESIGN
SHORTEN SCHEDULE REDUCE DOWNTIME
Cryogel® Z insulation has been specified and used in nearly 50 major LNG liquification and regasification projects around the world.
Whether your project is specification and design, installation and construction, or operations and maintenance, Cryogel Z saves time, and time is money.