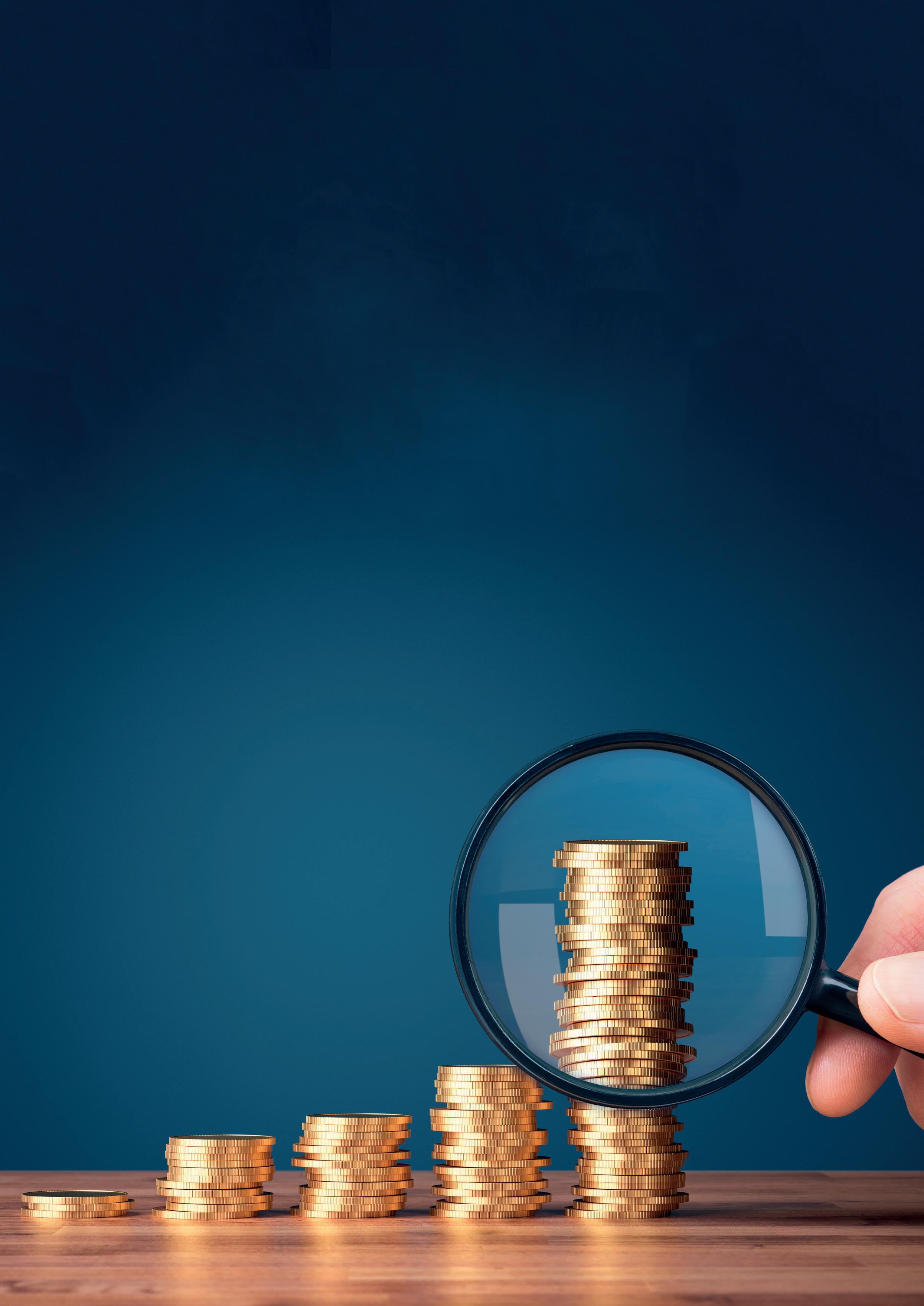
5 minute read
A Proven Investment
Industries all across the world have felt the societal and governmental pressures to operate from an eco-friendlier perspective. No longer are the days where profit is the single biggest indicator of a company’s health. The evolution of business has brought with it a need to not only profit, but to do so with the least impact on the environment. Globally, the mining industry has been tasked with the responsibility of reducing air-born particulate matter and improving greenhouse gas (GHG) emissions, both of which are affected by the quarrying, crushing, and manufacturing processes.
Federal mandates, such as PM10 and PM2.5, place responsibilities on all mining operations to control and contain respirable dust particulates 10 micron and 2.5 micron in size. This is done to prevent potential respiratory illness, such as silicosis and other cardiovascular impacts. Fugitive dust, small particulate matter suspended in air, is a health and safety hazard that must be controlled per the federal mandates mentioned above.
Although controlling respirable dust is a major concern, many operations find it difficult to associate the tangible savings associated with proper dust control, therefore making the addition of a dust control system a cost with little to no direct return. Foam dust suppression is a unique method that targets these particulates unlike conventional water sprays, while adding little moisture. This promotes significant water savings, while also providing tangible savings in areas of operation. With the push for environmentally friendly manufacturing, foam suppression is strongly suited to meeting current industry expectations, while providing savings to offset the cost of the application.
The returns
As discussed previously, fugitive dust has to be controlled. However, some methods, such as water sprays, require as much 80 – 90% more moisture than foam dust suppression to be added during crushing and
Ian C. Galyan, Seaco Technologies, Inc.,
USA, illustrates how foam dust control is an investment with proven and immediate returns.
sizing in order to provide equal control of PM10 and PM2.5 particulate. Foam dust suppression is a unique method targeting 100 micron and smaller particles with only 0.2 – 0.4% moisture added in total. With limited moisture addition and flexibility of treatment points, foam dust suppression allows for easy adaptation for operations ranging from 100 – 7000 tph.
Dust control is typically sustained throughout the crushing and sizing processes and into the reclaiming of stock piles, preventing the need for supplemental down-stream. By significantly reducing the overall amount of moisture required for dust control, one is also reducing the additional Btu cost and amount of carbon dioxide (CO2) if material drying is required prior to processing or shipping.
Btu and CO2-e reductions
For example, through the install of foam dust suppression, a calcium carbonate supplier gained the ability to eliminated the use of a diesel fed rotary dryer required when dust control was attempted by water sprays. The process change would net the manufacture US$179 000 savings in drying fuel costs and reduce their carbon emissions by 1 340 000 lbs CO2-e per year. Supplementally, production rates increased as a considerable percentage of material lost to wind-blown fugitive dust was returned to the process stream, improving their profit margins of the finished material.
Case study
These savings and return on investment (ROI) are well demonstrated in the cement industry. Senate Bill 596 requires the California cement industry to develop methods of cement production to reduce GHG emissions to 40% below the levels observed in 1990, by 2030. SB596 imposes a US$20/t of CO2-e. This may seem like a minimal cost of doing business, however, when you scale it up to the volumes of CO2 produced by the cement manufacturing process, approximately 0.9 lbs CO2 per pound of cement in an operation can incur additional costs of US$18 million per year for a facility producing 1 million tpy of cement.
Taking the same facility producing 1 million tpy of cement, and considering typical 25 – 27% shrinkage, the quarry would need to produce approximately 1.35 million t of limestone. Replacing a typical water spray and surfactant water spray system with foam dust suppression provides an additional 0.6% savings in CO2 emissions, and on average US$127 000 – US$158 000 in additional Btu costs.1
In 2030, with the proposed tax of US$20/t of CO2-e, these savings would increase to between US$215 000 – US$259 000 per year.1 In areas of drought restriction and scarcity of water, a change to foam dust suppression reduces water requirements by 4 532 000 – 5 180 000 gal. per year for an operation of this scale.1 Most cement manufactures typically produce between 1 – 4 million tpy at a single cement plant.
Material loss
Some material loss can exceed 6% of the process stream. This product already carries the expense of removal of over-burden, drilling, blasting, haulage, and crushing. Without proper dust suppression, this can be a complete loss or, at minimum, an additional cost to preform house keeping to return it to the process stream. In many cases, the fugitive material may result in damage to surrounding equipment as it accumulates causing damage to rollers, belts, and electrical equipment.
At times, wind-blown fugitive dust limits operations as it can reduce visibility preventing haul truck and mine operators from safely travelling on the impacted roadways.
Maintenance and housekeeping
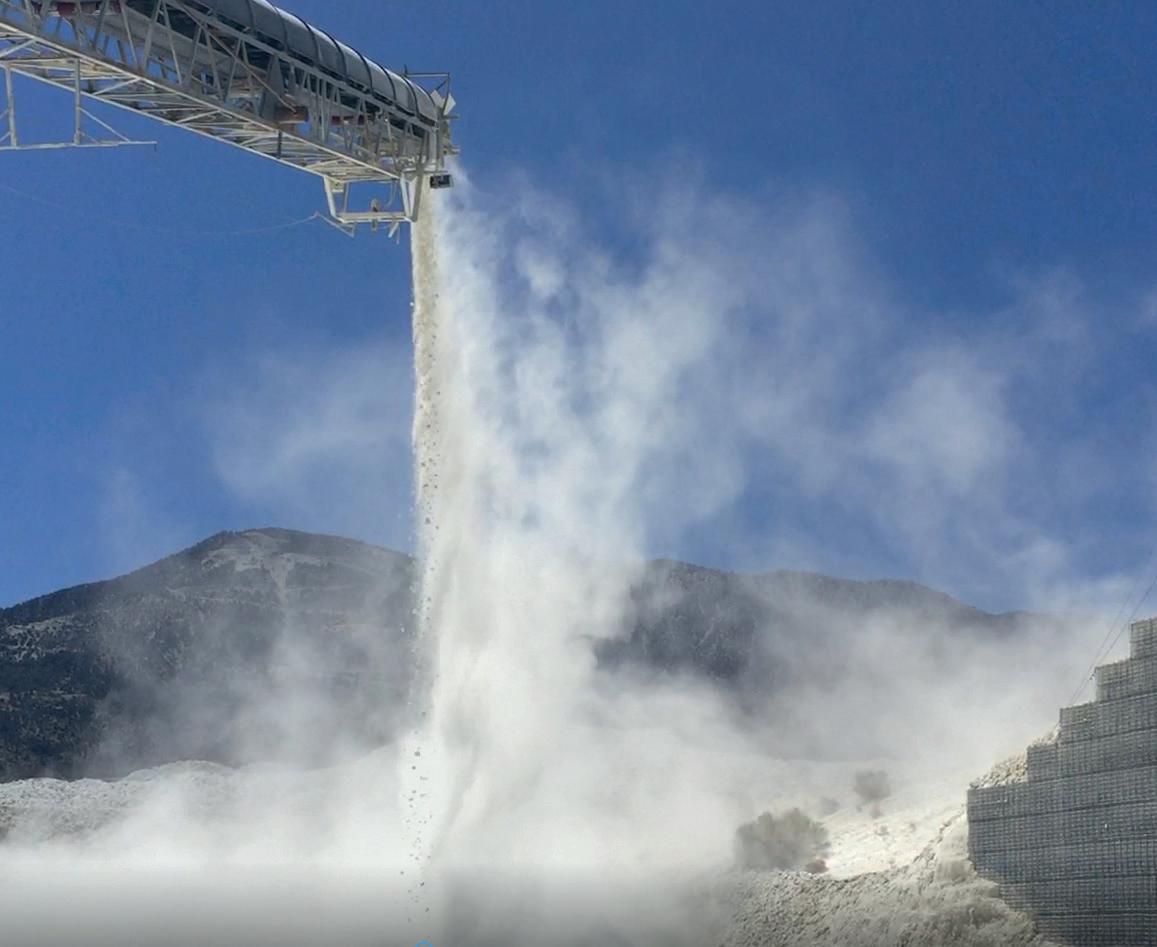
Additional benefits of foam dust suppression include reduced wear of hardened crushing surfaces, superior material flow and the chemistry itself, which aids in lubricating belts and increasing flexibility and lifespan. Many applications see a reduction in general housekeeping, as well as reductions in electrical maintenance, due to cooling systems and electrical contact remaining clean. Although these costs are often not considered, they become quite tangible as down-stream benefits are realised by those who utilise foam dust suppression for dust control. Typical treatment costs are less than US$00.10/t, making this a very Figure 1. No treatment (left) and with foam dust suppression (right). economical solution to reducing Btu and CO2-e.
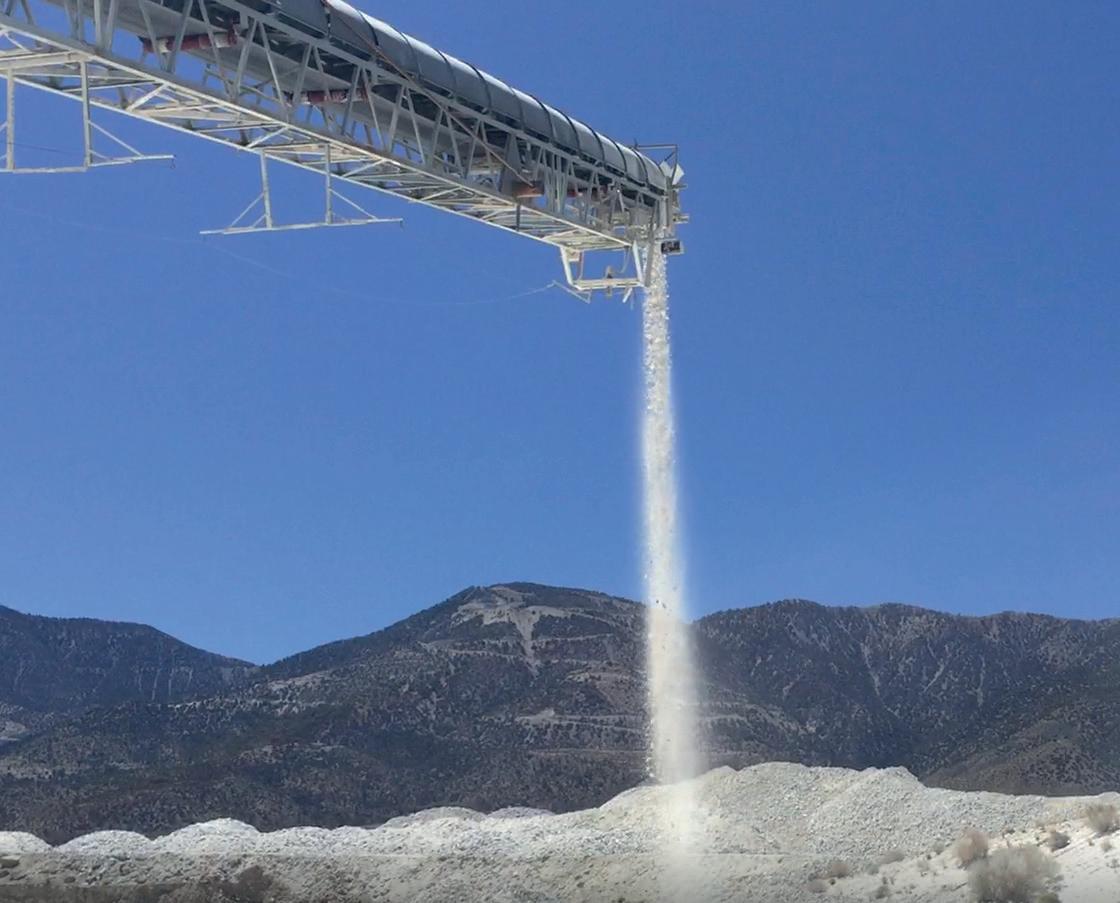
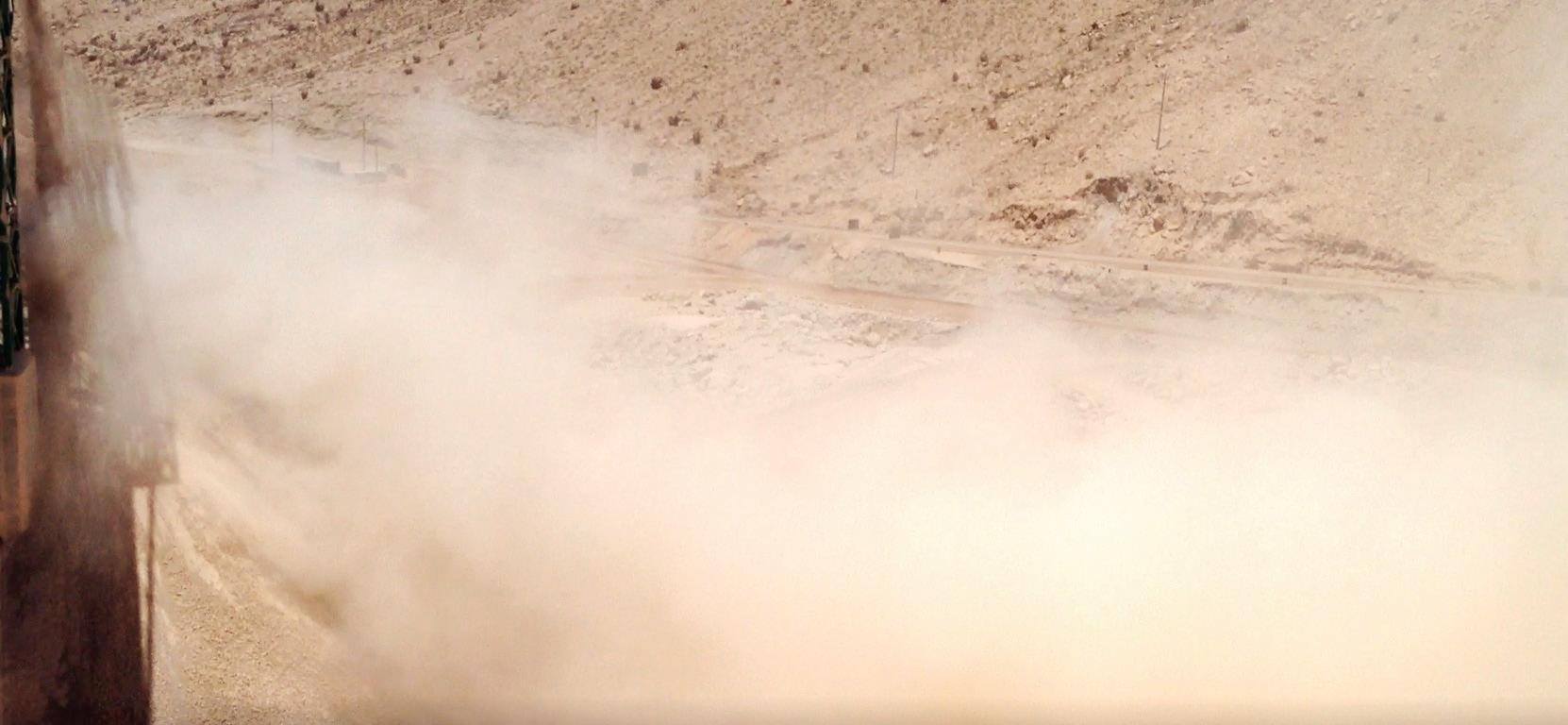
Figure 2. Wind-blown material loss >6%. Conclusion
As the mining industry continues to develop methods increasing their environmental stewardship, simple steps can be taken now, with immediate ROI, to reduce operations costs, greenhouse gas emissions, water consumption, and operational costs with the application of foam dust suppression.
Notes
1. US$2.57 – US$3.20/million Btu, 1140 Btu/lb water and 205.4 lbs CO2-e/million Btu for bituminous coal.