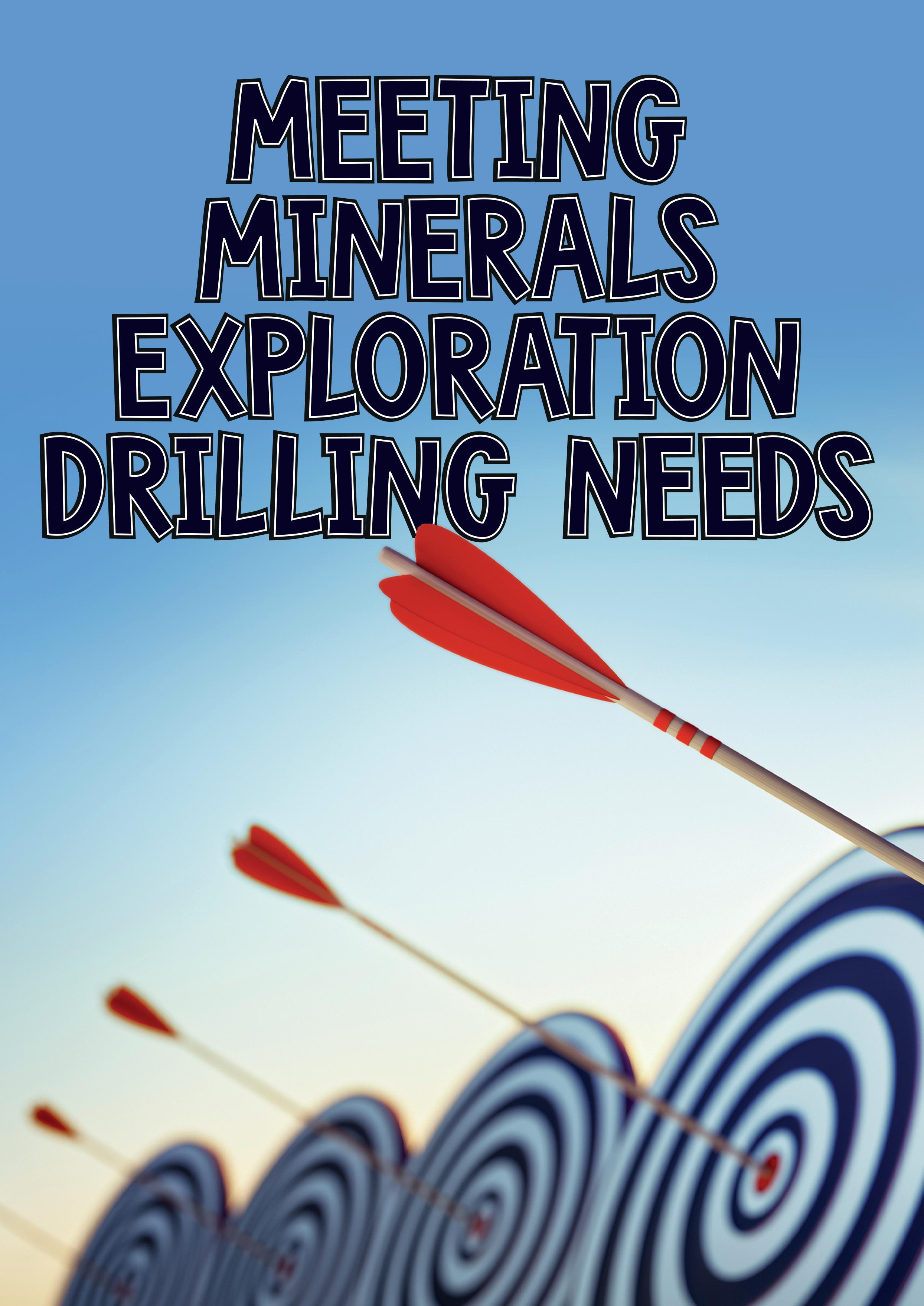
5 minute read
Meeting Minerals Exploration Drilling Needs
Dave Harper, Geodrill, Canada,
provides a comprehensive look at the technical advances and specialised approach needed for minerals exploration drilling.
By its nature, mining occurs in geographies where harsh weather conditions and physical boundaries provide multiple challenges. From an operational perspective, meeting and solving these challenges can be daunting. Once the rig fleet is mobilised to site, this is when the real challenges begin: the drill crews are required to drill to the highest international standards, while ensuring that customers’ objectives are met.

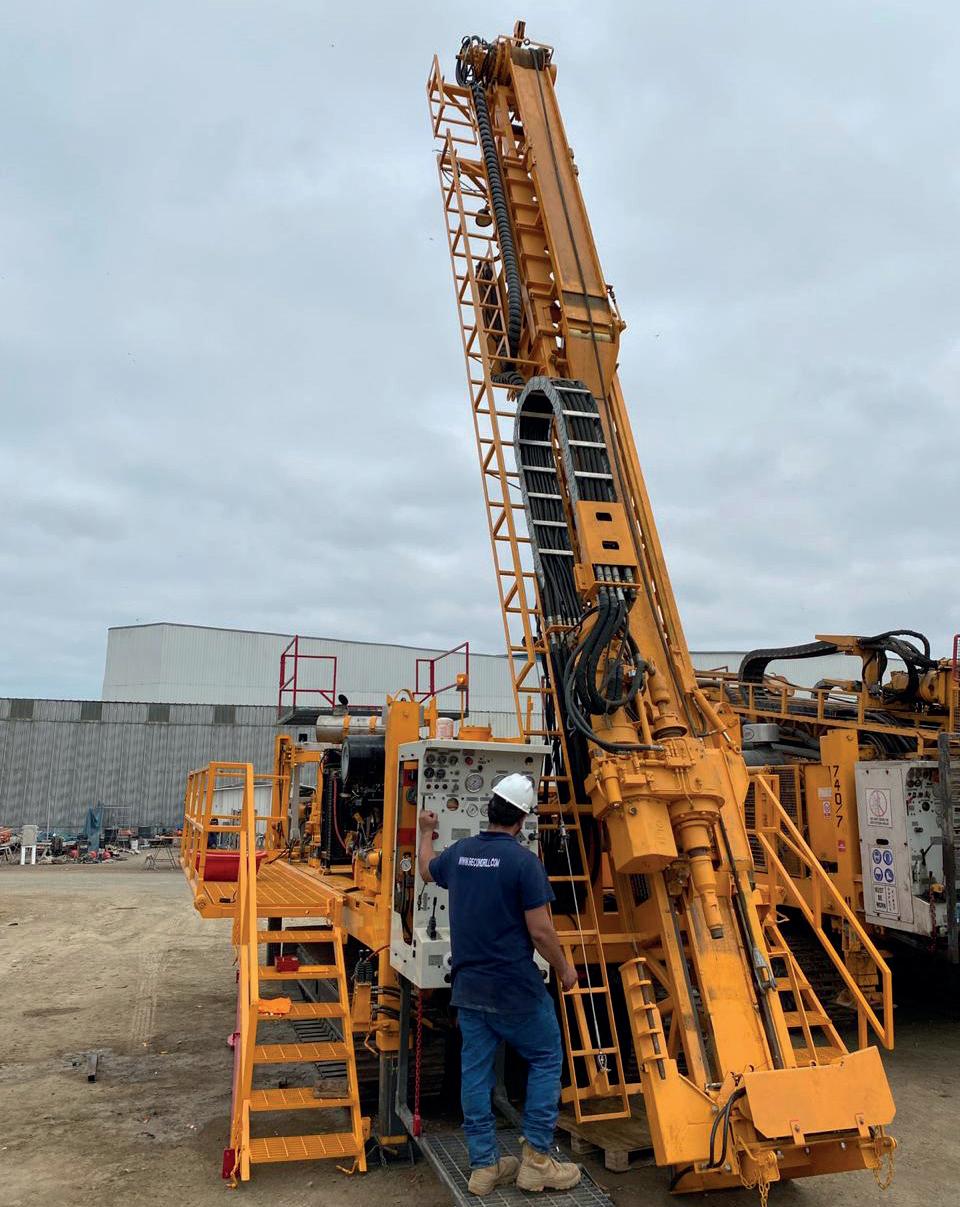
Figure 1. Drilling in Egypt.
Figure 2. On-site in Peru.
Geodrill achieves this by investing significant capital to deliver a modern well-maintained fleet of high-performance drill rigs and support equipment, and by delivering the right expertise in accuracy, reliability, and safety. Some issues with working remotely include understanding how to deliver mechanical availability in order to minimise downtime (which is costly), and maximising other efficiencies, such as ensuring the health and safety of drill crews, by providing training in the field.
Exploration drilling services
The company’s fleet of multi-purpose rigs are popular because of their versatility – they perform reverse circulation (RC) and core drilling and can be switched interchangeably while over the same hole, i.e. RC pre-collar with diamond drilling (DD) tail. Geodrill’s leading speciality service is providing pre-collar to depths of approximately 400 m RC, then completing the hole with core drilling to depths of up to 2000 m. Another specialty service is deep multi-intersectional directional drilling. The concept was originally based on an oil field technology: the deep directional method involves drilling a deep parent (or mother) hole with a series of branch holes (daughters) accurately to the target depths and pierce point co-ordinates. This provides time and cost efficiencies by eliminating the need to repeat the top section of the hole. Depending on the application and topography, the rigs can be either truck or crawler mounted. Multi-purpose rigs all fitted with on-board compressors are supplied with booster and auxiliary compressors for depths where high water ingress is expected.
The importance of training
When operating a fleet of multi-purpose, core, air-core, grade control and underground drill rigs, the need for specialised training and experienced decision making is critical to success. The company has therefore established training facilities for providing on-the-job training for its drill crews. Sites with workshops and supply bases are readily available to provide storage, drilling rig repairs, equipment and inventory of spars, and consumables to the efficiencies by minimising trucking, shipping, etc. The ability to mobilise to drill sites with minimal delay ensures cost efficiencies. Geodrill has established centrally located workshops to promote client satisfaction through reliable operational performance. In addition, within the workshop in Ghana, for example, is a manufacturing facility with the capacity to produce ancillary equipment, such as RC drill rods and RC wire-line drill subs, in-house – reducing downtime and reliance on suppliers for these items. The well-resourced, centrally located workshops further reduce downtime, as the company can quickly reach most of its current customer sites. With a geographic footprint spread across two continents, the company has established a ‘hub and spoke’ model with Ghana as the hub, and Cote d’Ivoire, Burkina Faso, and Mali in
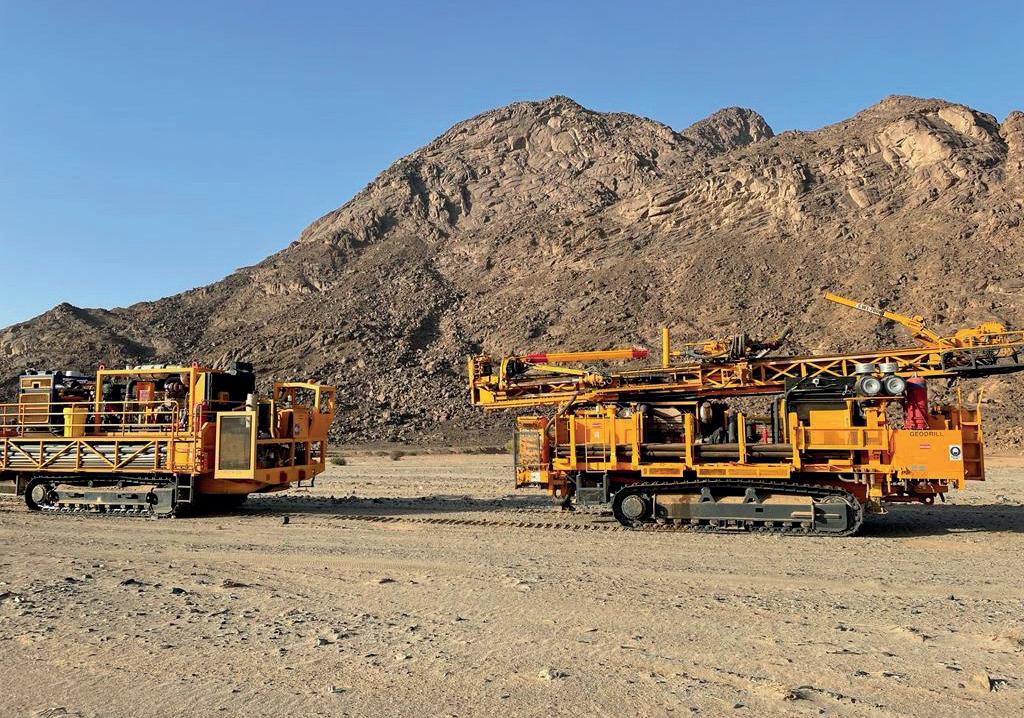
West Africa; Egypt in North Africa; and Peru in South America, the spokes.
A specialised CNC machining centre for the manufacturer of drill rods and consumables reduces the need to ship parts from out-of-country, which in turn minimises downtime and increases efficiencies.
The facility also encompasses a drill academy for developing local skills. Training and development programmes allow personnel with the required skills and knowledge to perform drilling and maintenance to the highest international levels. Safety with the production system has been developed to exceed all applicable government and client standards.
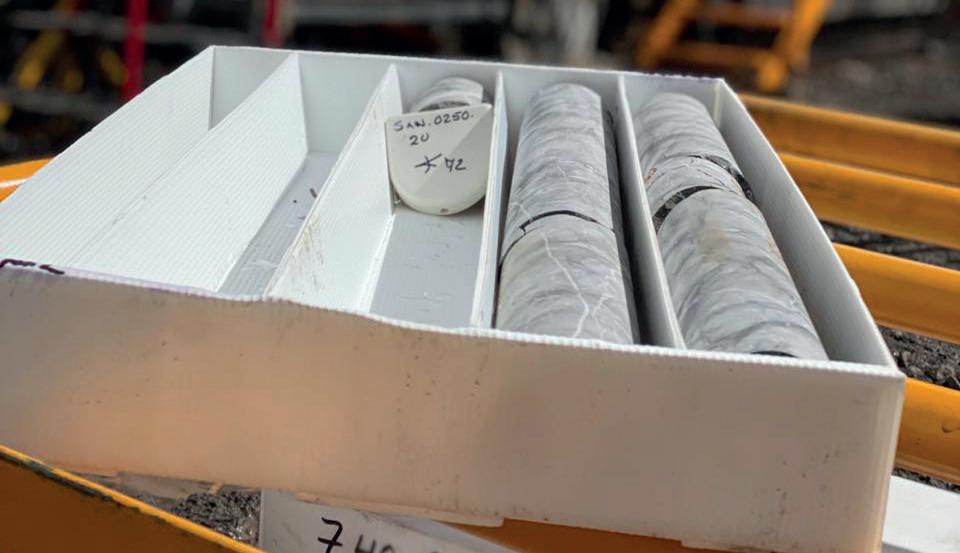
Figure 3. Drill samples from Peru operations.
Case studies
In 2022, the company signed three significant contracts with Centamin Plc, Endeavour Mining Plc, and Perseus Mining.
The Centamin project will require 350 000 m of underground gold exploration and mine DD and RC grade control, utilising five drills over five years at its flagship Sukari gold mine in Egypt. In the case of the Endeavour and Perseus projects, both programmes involve a combination RC (RC0 and DD core using multi-purpose drill rigs). RC is the popular choice of geologists because it can drill economically and efficiently to depths of between 400 – 500 m. RC drilling produces a hole size 140 mm dia. and is generally faster than DD. RC drilling produces high quality rock chips rather than a core sample, yet is more economical than DD core drilling.
The RC method produces samples from depth by pulverising rock – using compressed air and a percussion RC hammer – and returns it to surface through an inner tube, collecting it through a cyclone then into a sample bag. RC is often used in conjunction with a multi-purpose rig to drill RC pre-collars with core tails. Geodrill provides this method extensively for exploration and resource drilling.
ESG in the mining industry
In the mining industry, it goes without saying that environmental, social, and governance (ESG) are essential to the fabric of the community no matter where operations exist.
As a company, Geodrill recognises that the environment, and perhaps, more specifically, climate change is one of the greatest threats facing the world today. For example, as part of its effort to reduce its carbon footprint, the company recently added solar panels to its Accra head office. Another project includes an eco-friendly bus shelter made completely from recycled and up-cycled plastic waste, a first for Africa.
In terms of social license, Geodrill has always given to sports and education initiates, and regularly donates to various organisations and charities. Building further on the social aspect, Geodrill employs 1200 personnel, most of whom started with a low skills base and worked their way up to become highly trained technicians.
In recognition of its efforts, Geodrill has received several significant ESG awards – most notably the AAMEG Best Workforce Industry Development Initiative and the Millennium Excellence, aka the King’s award, which is the highest recognition of a foreign company in Ghana.
Conclusion
With increased geopolitical and inflation risks, commodity prices for both precious and base metals have moved up and down the dial. However, the outlook for exploration remains strong as producers at all levels – from junior to large bellwether names – stay focused on developing their prospects further.

