
7 minute read
Shining A Spotlight On Shotcrete Spraying
Rick Kraft, Getman, USA,
outlines the development process involved in making the latest evolution of shotcrete spraying solutions a reality.
Not long ago, the underground mining industry relied on a pool of very skilled and experienced shotcrete operators. Today, there is a shortage of skilled operators for spraying concrete, and equipment must evolve to fit the skills of a new generation.
After years of development, Getman Corp’s new ProShotTM Concrete Sprayer was introduced in the summer of 2021, with a prototype working in a western-based US mine. The ProShot has been specially designed to use available technology to compensate for a deficit in operator experience. Extensive resources were dedicated to
its development, including process screen capabilities that allow complete and accurate shotcrete process information to assist operators in applying quality sprayed layers.
Application benefits
The ProShot is user friendly and uncomplicated. New operators are comfortable using touch screen technology in daily life, and thus can easily move through screens and options with minimal shotcrete experience.
ProShot uses numerous control area network (CAN) modules, which minimise the number of wires laid out across the machine. Instead of large multiplex bundles passing across the articulation and through the cab, Getman’s design eliminates excessive wires. While CAN is not new technology (over 20 years old), it is proven as particularly effective in this application.
ProShot was designed by operators and for operators – with emphasis on it being intuitive, safe, and easy to maintain. An example of the ProShot’s intelligent control layout and fluid operation is a button in the machine’s dosing enclosure to turn rear driving lights on/off so operators may eliminate climbing in and out of the cab. Additionally, forward and reverse lights may be flashed from the steering joystick trigger control while driving to alert other vehicles at crosscuts and intersections.
Essential facts
n Key specifications: § Telescopic boom extension: 2.6 m (8.4 ft). § Coverage envelope with telescoping boom parallel (H x W x D): 5.4 m x 8.5 m x 3 m (17.7 ft x 27.9 ft x 9.8 ft). § Stainless steel chemical tank: 1040 l (275 gal.) capacity. § Fuel tank with self-closing cap: 227 l (60 gal.) capacity. n Boom mounted on centreline of chassis. Boom strength allows for effective concrete spraying at full kinematic boom coverage using 2 ½ in. hose. n Modular engine compartment permits ease of access for engine maintenance. n Easy to access operator cabin mounted mid-frame to reduce exposure to rebound and provide good operator visibility. n Nozzle assembly easily disassembles for cleaning without special tools. n ProShot’s innovative in-cab 10 in. touch screen provides real-time information about the machine.
With Bluetooth and Wi-Fi capabilities, software revisions are available and accessible via a customer’s smartphone. n The Getman dosing management system provides live spray process information and data acquisition, visible on three 7 in. exterior displays. n Chemical additive dose may be changed via remote, with five preset rates and changes visible on process displays. n An optional OptiME Lidar Scanner is available with the ProShot. The OptiME scans the surface and creates a digital map to determine the thickness of the sprayed layer. The process includes the following steps: boom unfolding, pre-spray scan, nozzleman sprays area, nozzleman performs post-spray scan, then reviews the coverage of the area. Software produces an overlay of both scans in a real-time report for the operator to review and adjust spraying accordingly. n The ProShot features the Schwing 301 concrete pump, designed for pumping low slump material.
Mine operations and method1
The ProShot pilot unit now works in New Afton mine, located approximately 346 km (215 miles) northeast of Vancouver, British Columbia. New Afton is the underground extension of the original Afton Mine, which served as an opencast mine from 1977 – 1997. Development of the underground workings, including the construction of a new mill and other infrastructure began in 2009, with production starting in June 2012.
The New Afton deposit is mined using the block-caving method. Ore is transported by a load haul dump (LHD) loader from the drawpoints on the extraction level to an ore pass that directs the ore to the haulage level down below. The ore is then loaded onto an LHD loader and into a haul truck that transports the ore to an underground gyratory crusher. From there, the crushed ore is conveyed to surface.
Owned and operated by New Gold Inc., New Afton currently processes approximately 13 000 tpd. It produced 98 000 oz of gold and 87 million lbs of copper in 2016. Based on current production rates, proven and probable reserves will allow mining to continue through 2024.
Case study
Current production levels at New Afton are at a depth of over 1 mile. During the summer of 2021, the operation was using three sprayers in various working conditions. A development contractor brought a ProShot to the mine and when New Gold saw it, they wanted to test the machine. Testing began with large-volume rehabilitation sprays. Existing machines were assigned to shoot production levels, as production level sprayers must be certified to meet a certain compressive strength. Criteria level must be met before a sprayer can be certified to spray in production areas.
As the ProShot began rehab spraying, all three existing machines went down. Consequently, New Gold took the ProShot down to the production area to try ‘test’ sprays as primary ground support. Concurrently, the ProShot sprayed test panels which normally take 28 days to cure. 2 hr beam test panels were also sprayed and successfully passed the initial test, allowing ProShot to spray primary ground support. The Getman ProShot now sprays production levels two shifts a day, every day. ProShot passed the tryout and met the challenge.
To appreciate the challenge in full, it is important to understand that concrete transporters are filled at the surface and then travel down a long ramp system in the mine to get to the bottom. With a set number of transporters to travel the distance, it is a long process.
Additional product differentiators of ProShot include: n It is easy to learn and operate; operators recognise it as ‘intuitive’. n Ease of maintenance (adjustable components are easily accessible). n Clear visibility from the cab. n Equipped with informative diagnostic screens for machine analysis. n Electrical harnesses and connectors are carefully routed to eliminate water ingress. n Strength of design – the purpose-built design features the hose mounted in an easy-to-access area, running alongside the chassis, making it to remove and disconnect. n Longer uptime. n Impressive serviceability/reliability.
A second ProShot began work at New Afton in April 2022. Both machines now serve in a primary production ground support role. Following these successful results, New Gold is considering the purchase of additional ProShot machines to support their operations.
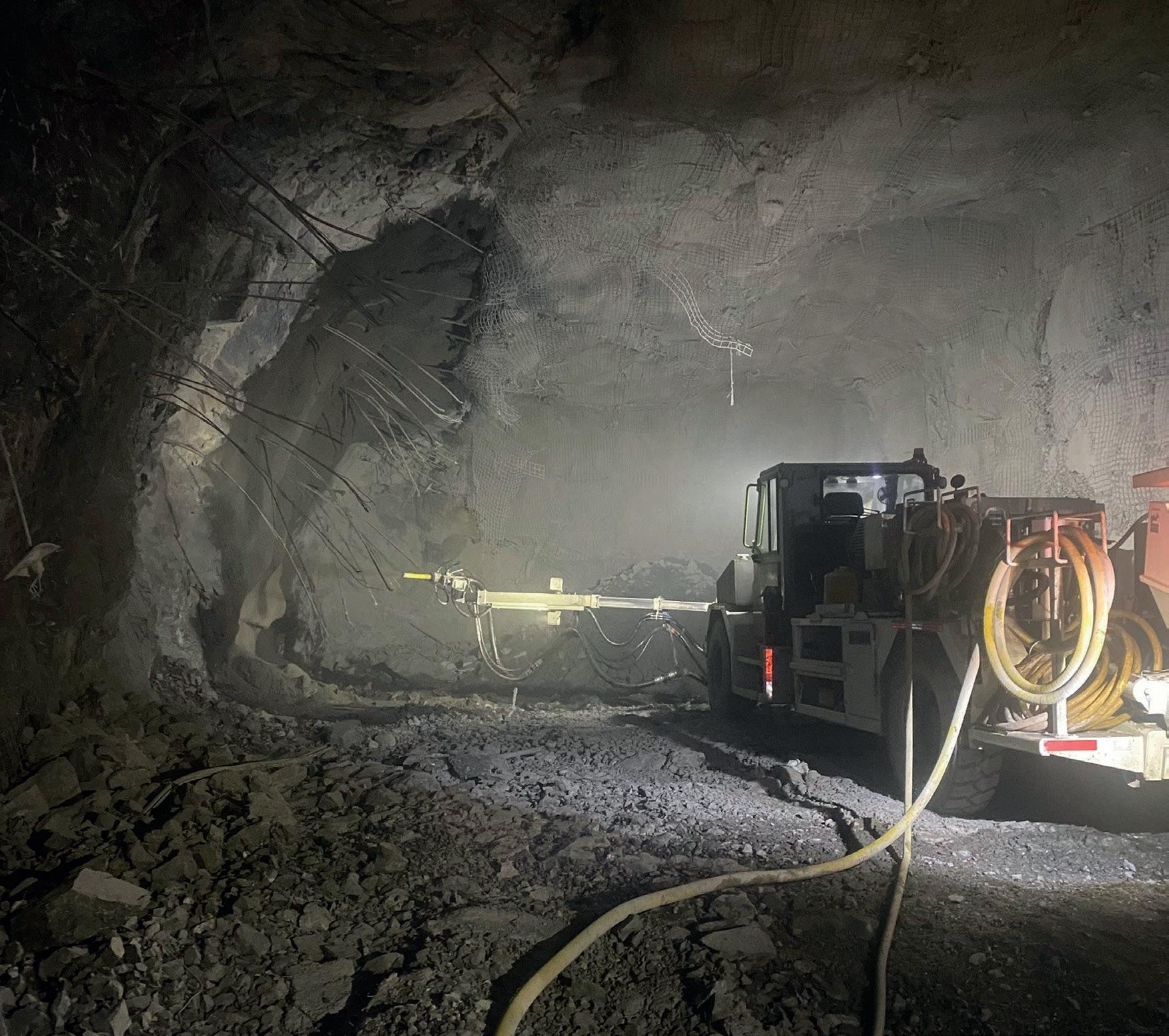
Figure 1. ProShot spraying in a rehab area to prevent further fall of ground.
Figure 2. The ProShot applied 60 m3 of shotcrete to stabilise a large remuck gallery inside the New Afton mine.
Thinking about the future
Operators often ask how the ProShot spraying solution could be developed further and what is next for shotcrete machines in the mining industry. In truth there are several possibilities: n Alternative power solutions – diesel electric over hydraulic and battery electric. n Awareness of what operators need to understand about the spray process, by making it easier with special tools (such as providing real-time information for successful spraying). Getman’s goal is to provide a machine that communicates all the key variables. Thus, ProShot was designed with maximum utility for inexperienced operators. n Laser scanning systems – now in use, with software continuing to advance. n Machine reliability – robust, user friendly, smart technology. The more complex the machine, the more difficult it is to operate. Recording data related to spraying volume and dosage, and then supplying that data to the operator is realistic.
Using that data to help the operator make smart decisions could help product development evolve to remote operation.
Conclusion
Getman dedicated extensive resources over several years to the development of its ProShot technology. The development of previous iterations of shotcrete sprayers led to new ideas and ongoing progress towards the goal of developing the best machine on the market. Increased automation is emerging as the roadmap for future development.
References
1. Information courtesy of the Mineral Resources Education
Program of British Columbia – https://mineralsed.ca/learningresources/bc-mineral-resources-map/bc-operating-mineprofiles/new-afton-mine/
