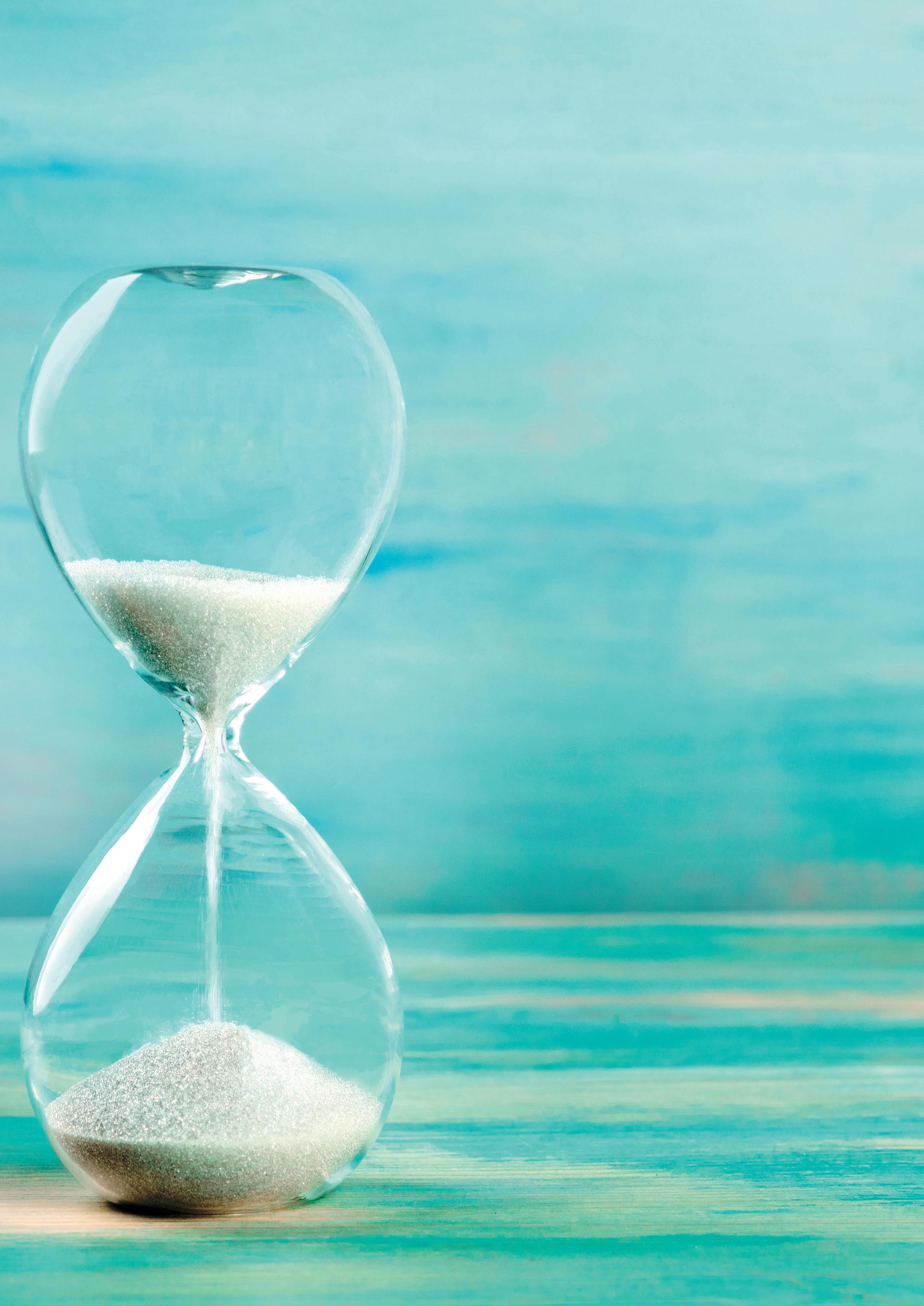
9 minute read
Slashing Cycle Times
Uwe Wyink, Hugo Bras, and Precious Jere, Master Builders Solutions, consider why new demands and new technology in hard rock mining mean that cementitious grouts are under more pressure to perform than ever.
The most commonly used grout for cable bolts in hard rock mines is ordinary portland cement (OPC). It is tried and tested, well understood by those working with it, and widely available.
However, some mines are turning their backs on tradition to work with pre-formulated grouts that behave differently. This change is partly driven by a switch to automated bolting and grouting machines, which perform more efficiently with engineered grouting systems. Productivity gains and a reduction in failures and rework mean that the increase in material costs for pre-formulated grouts is more than offset by savings made elsewhere.
Why bolts fail
The role of a rock bolt is to help take loads from the ground which are no longer supported by the rock that has been removed in the mining process. They are not needed everywhere; it depends on the type of rock and on the stresses and strains in the strata. Geologists and engineers set parameters which determine the type of rock support that is needed at different points in the mine.
Grout is installed to fill the gap between the bolt and the rock, as well as any fissures that run from the bolt hole. It is a vital part of the system because it transfers the load from the rock to the bolt. If the gap around the bolt is not properly filled for any reason, the loading on the bolt will not be uniform, which could mean that an overloaded section of bolt will fail at some point.
One problem with OPC grouts is that they shrink as they cure, creating space between bolt and rock. This can also allow water to run through the bolt holes, increasing the pace of corrosion of the rock bolt and bringing more water into the mine, weakening the installed ground support.
Ground water in mines can sometimes be very aggressive, leading to relatively fast failures due to bolt corrosion. For instance, if the water contains sulfates, it is not uncommon for friction bolts to fail within six months. Even where a bolt is fully encapsulated by OPC grout, the water can make its way through the material to corrode the bolt.
The outcomes from bolt failures are delays during the mine development process and mining at best, and loss of human life at worst. Any safety-related incidents must be reported and possibly investigated by the authorities, depending on the region and its legal requirements. Fatal accidents may well involve the police and even the closure of a section or the entire mine for a period.
Even where accidents are avoided, slips require significant amounts of remedial work. If the incident has taken place at an important location strategically, the cost of delays will be even greater.
As resources, such as lithium, nickel and copper, become scarcer, deposits in challenging ground become more attractive. This also means that bolts will be required more often to provide additional support – and that their failure could be even more costly and dangerous.
Case study: comparing re-entry times in Australia
The time it takes for the grout around a rock bolt to reach the required strength has a huge impact on cycle times, and hence on the productivity of the mine.
A hard rock mine in Australia carried out a comparison of the time taken to create an intersection, using three different types of grout: standard OPC grout, a pre-formulated fast-setting grout, and a pre-formulated ultra-fast setting grout.
One of the challenges when creating an intersection is that it requires two phases of bolting and grouting. While the grout is curing each time, it is not safe for plant or people to pass through that junction point. This can mean that mining activity in the original drive, as well as in the branch drive, is halted.
With the OPC grout taking around 12 hrs to reach a safe strength, the high-strength grout taking 8 hrs, and the ultra-high grout taking just 2 hrs, the difference in cycle times over two phases is significant. A cycle using high-strength grout takes 40 hrs rather than 48 hrs, effectively saving one whole shift. The ultra-fast, high-strength grout cycle takes 28 hrs, saving 20 hrs.
Move to automation

Figure 1. Three-way intersection: Phase 1.
Figure 2. Three-way intersection: Phase 2. When more bolts are required, it can make economic sense for mines to invest in automated processes – e.g. switching to one machine that can drill the bolt hole, as well as install the cable from a roll mounted on the machine that also contains a pump for injecting the grout around the bolt. However, using OPC with these machines increases the risk of breakdowns and delays.
When the temperature underground is high, the open time for OPC grouts tends to fall dramatically. This can mean that the grout hardens inside the machine, resulting in clogging and downtime while mechanics are called to repair and restart these expensive pieces of kit. To avoid clogging, operators must spend significant amounts of time on cleaning and maintenance, which prolongs cycle times.
Another challenge – which can apply to grout installed traditionally too – is ensuring that OPC grout is pumpable. In practice, this means that water is added until the consistency looks correct, but this increases the water-cement ratio, which in turn leads to bleeding, lower strength grout, and shrinkage. The other tension between using automatic bolting machines and OPC grout is that, while the aim of automation is to increase productivity, traditional grouts generally require a 24 hr wait before re-entry is possible. It is not safe to work in an area that has just been bolted until the grout has reached a predetermined unconfined stress – usually 25 MPa. There can be other repercussions from a grout that takes 24 hrs to gain a safe strength. The ground can keep moving until the grout is hard enough, particularly in situations where there are high stresses and strains in the rock mass, which could lead to problems.
Doing it differently
Pre-formulated grouts are engineered to overcome the problems that can come with OPC grout. The goal is to provide a grout with a much faster re-entry time and, at the same time, a sufficiently long open time to prevent damage to automated bolting and grouting machines.
Rather than a re-entry time of 24 hrs for OPC grout, pre-formulated grouts can provide a
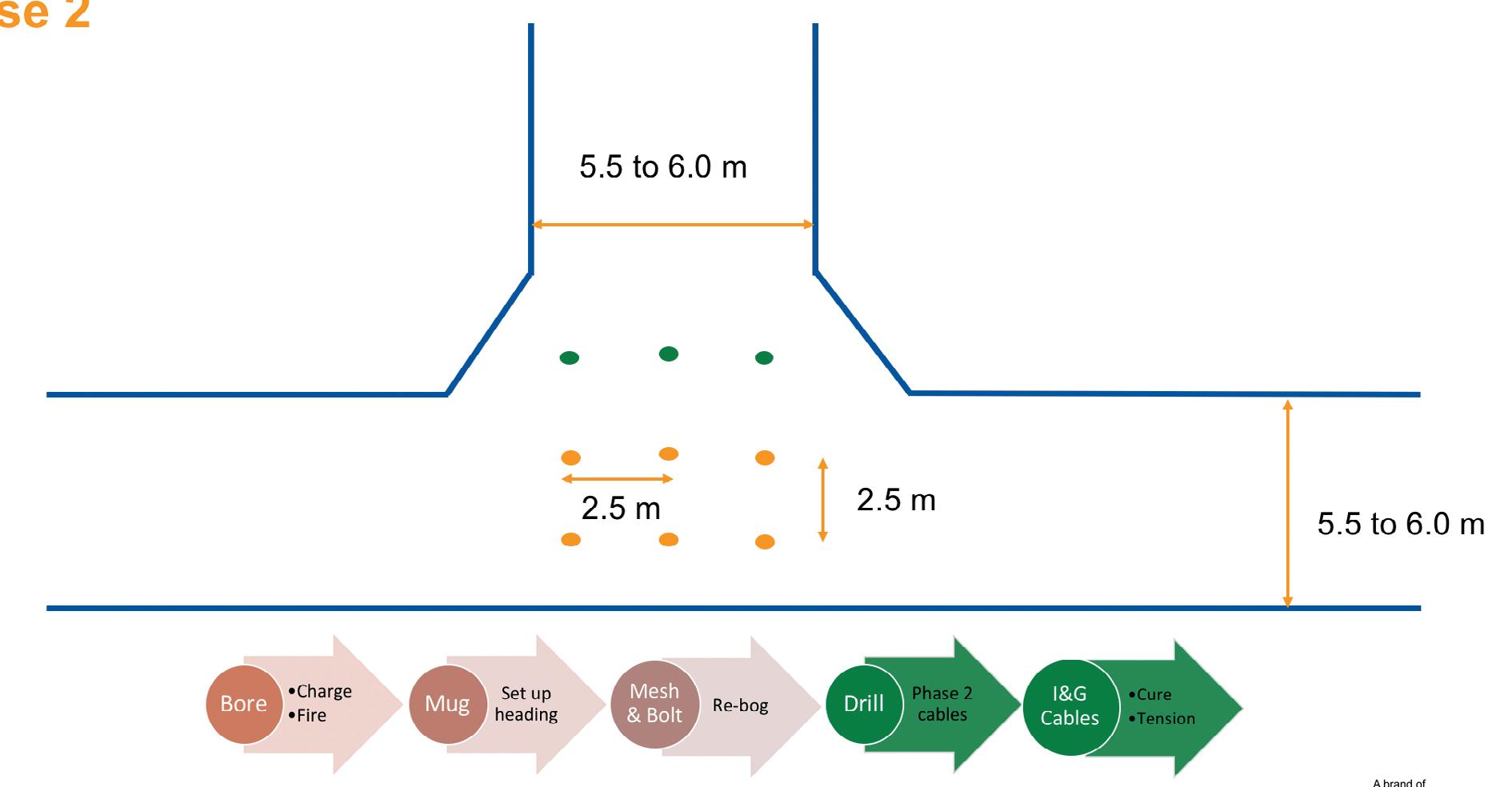
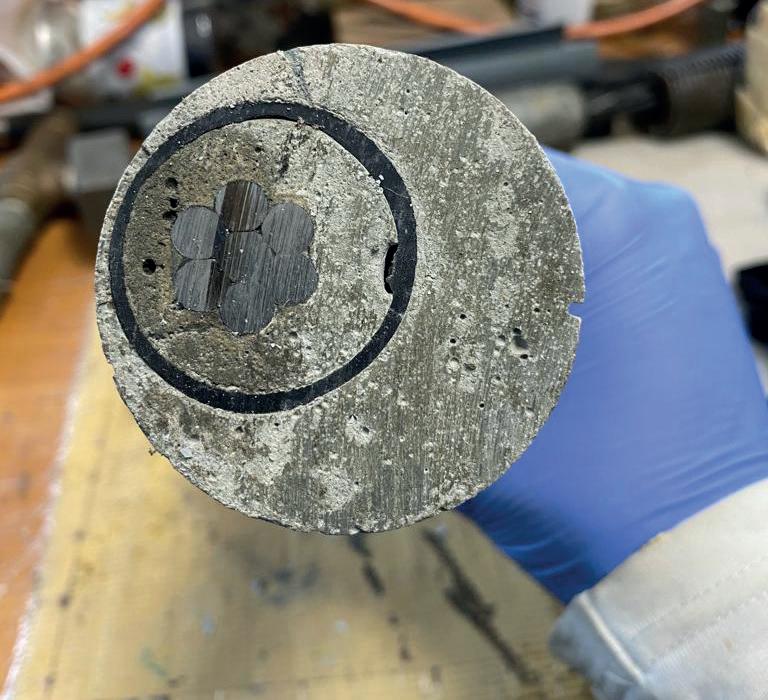
Figure 3. Rock bolt performance depends on the gap around a rock bolt being fully filled – achieved here with pre-formulated grout. If there are voids, the load from the rocks will be unevenly transferred, and the bolt could fail.

Figure 4. When grout made with OPC cures, it shrinks and cracks. That crack becomes a weak point, making loading on the bolt uneven and allowing water to get to the bolt and into the mine.
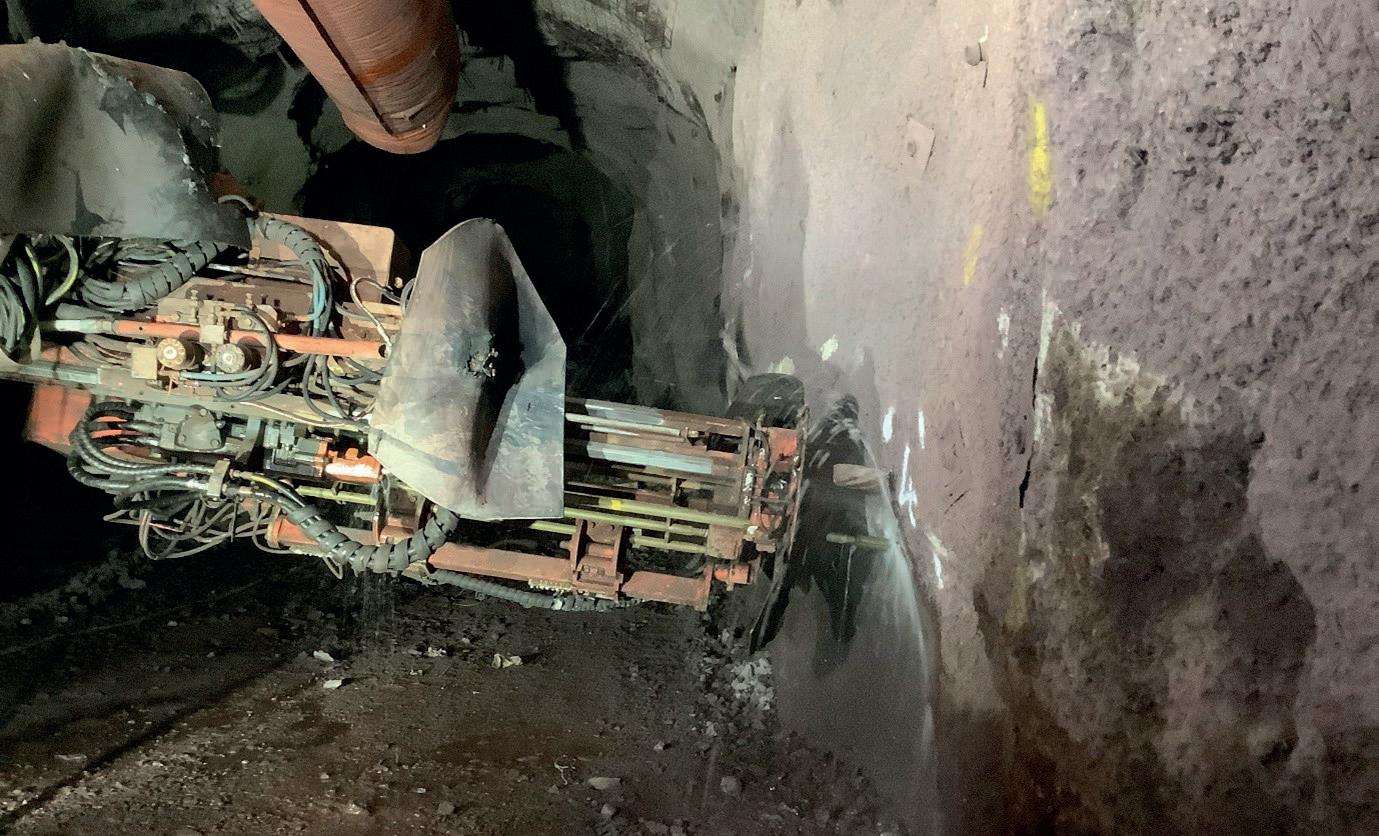
Figure 5. The choice of grout for rock bolting in mines has a profound impact on cycle times. Whereas traditional OPC take 24 hrs to cure, pre-formulated ones take 8 hrs or less. re-entry time of 8 hrs, which has significant implications for cycle times and productivity. Even faster re-entry times can be achieved with pre-formulated grouts (as low as 2 hrs), although these are at the cost of a shorter open time; lower than 1 hr.
Typically, pre-formulated grouts contain high-performance additives, which aim to shorten or prolong the open and curing time of the grout. They can also incorporate additives to protect against corrosion and viscosity modifying agents to improve the rheology for better flow during the pumping process. Finally, the grout could also contain additives to make the grout thixotropic – so that it does not run out of overhead bolt holes.
From a safety perspective, the addition of the plasticiser to improve flowability means that bolts are more likely to be fully encapsulated, removing the risk of uneven loading and failure. Easily pumpable grout also reduces the wear and maintenance requirements for the pump and lines. Less resistance in the pumping lines also means that lower pumping pressures are needed, and hence less energy is expended.
Where aggressive conditions such as sulfates in the ground water exist, pre-formulated grouts can be engineering to guard against corrosion. The addition of a corrosion inhibitor prevents water migrating through the grout to corrode the bolt.
Environmental considerations
There are three major environmental benefits from switching from OPC to pre-formulated grouts: savings on materials, savings on energy, and the reduction of water inflows into the mine. All of these gains will ultimately reduce the whole-life carbon footprint of the mining operation.
It is well-established that the manufacture of cement is one of the biggest emitters of carbon. So, reducing the volume of cement in the grout, and reducing the quantity of grout used over the lifetime of a mine, have a positive impact on the embodied carbon of a support system.
Pre-formulated grouts reduce the volume of grout used in two ways. First, because there will be fewer rehabilitations needed due to rock bolt failures, the overall demand for grout will be reduced. Second, because it is supplied in water-resistant paper sacks, there will be no loss of grout due to moisture; contrast this with OPC grouts, where between 5 – 10% of material could be lost when bags stored at the bottom or top of a pile get wet and are unusable.
Better encapsulation of the bolts will reduce the amount of groundwater that drips into the mine. This means that less energy is required to pump water from the mines, fewer resources are needed to treat it, and the risk of contamination of local water bodies with mine water is reduced.
Although pre-formulated grouts have been available for many years, their use is still limited, especially in hard rock mines. Current research and development programmes aim to improve the technology further. For instance, Master Builders Solutions is creating a new generation of pre-formulated grouts which will deliver the same performance in terms of re-entry time and open time, whatever the rock type or temperature.
With these new developments in hand, mine owners and operators have the opportunity to boost productivity, while delivering lower whole life costs, less whole life carbon, and safer working environments.