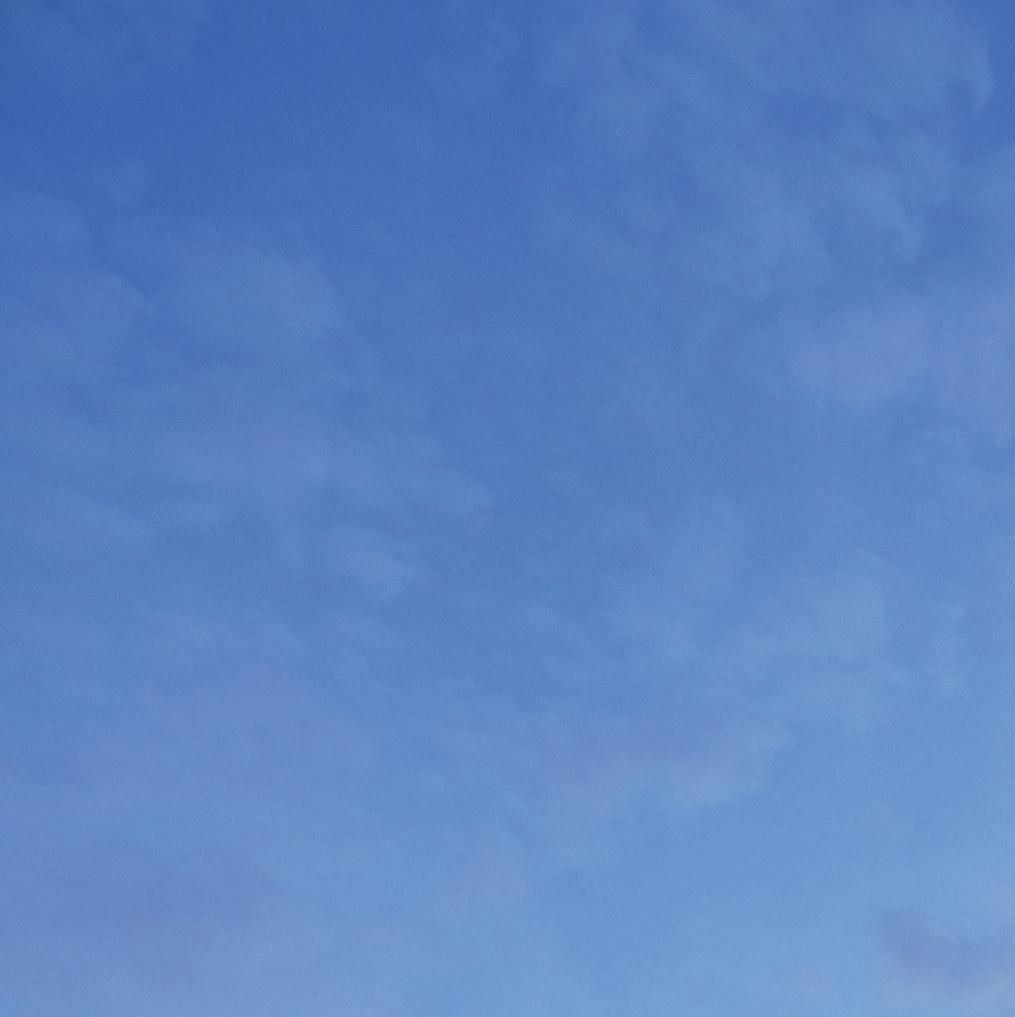
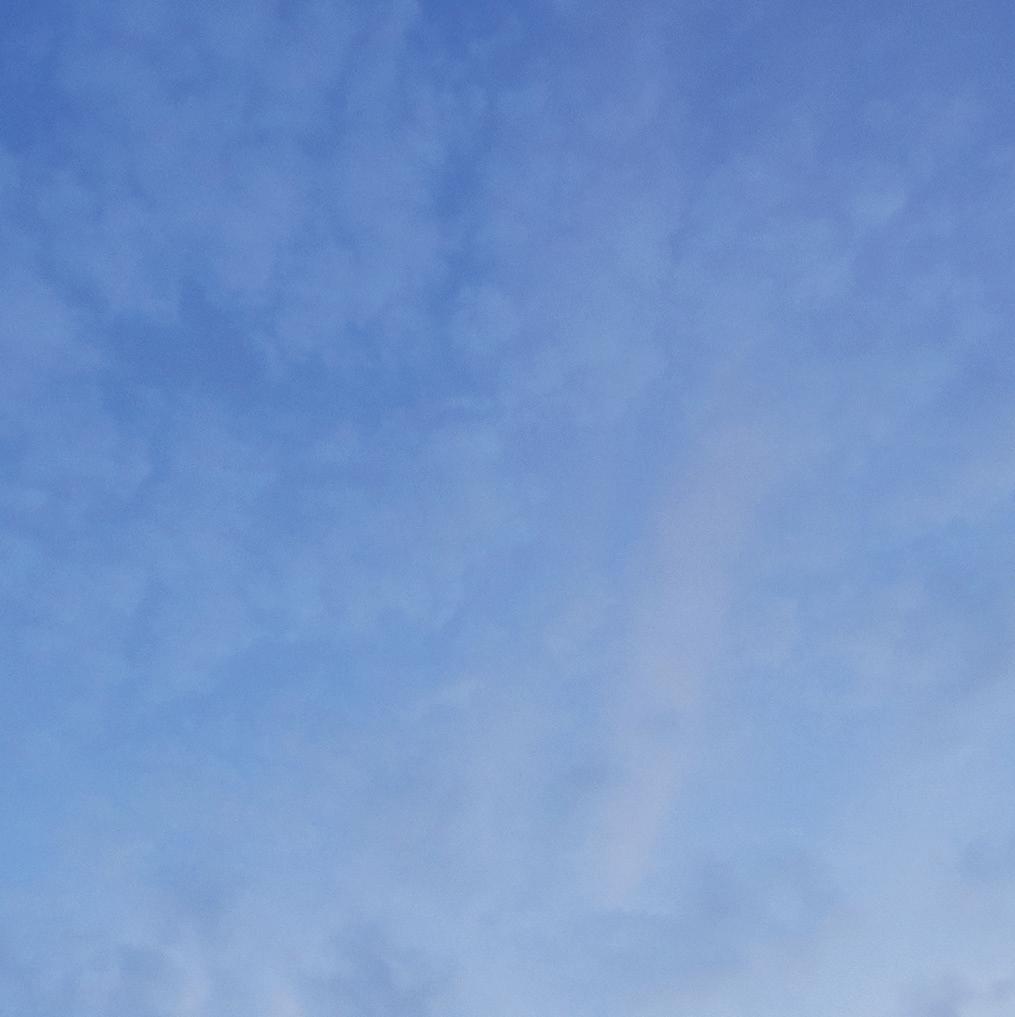
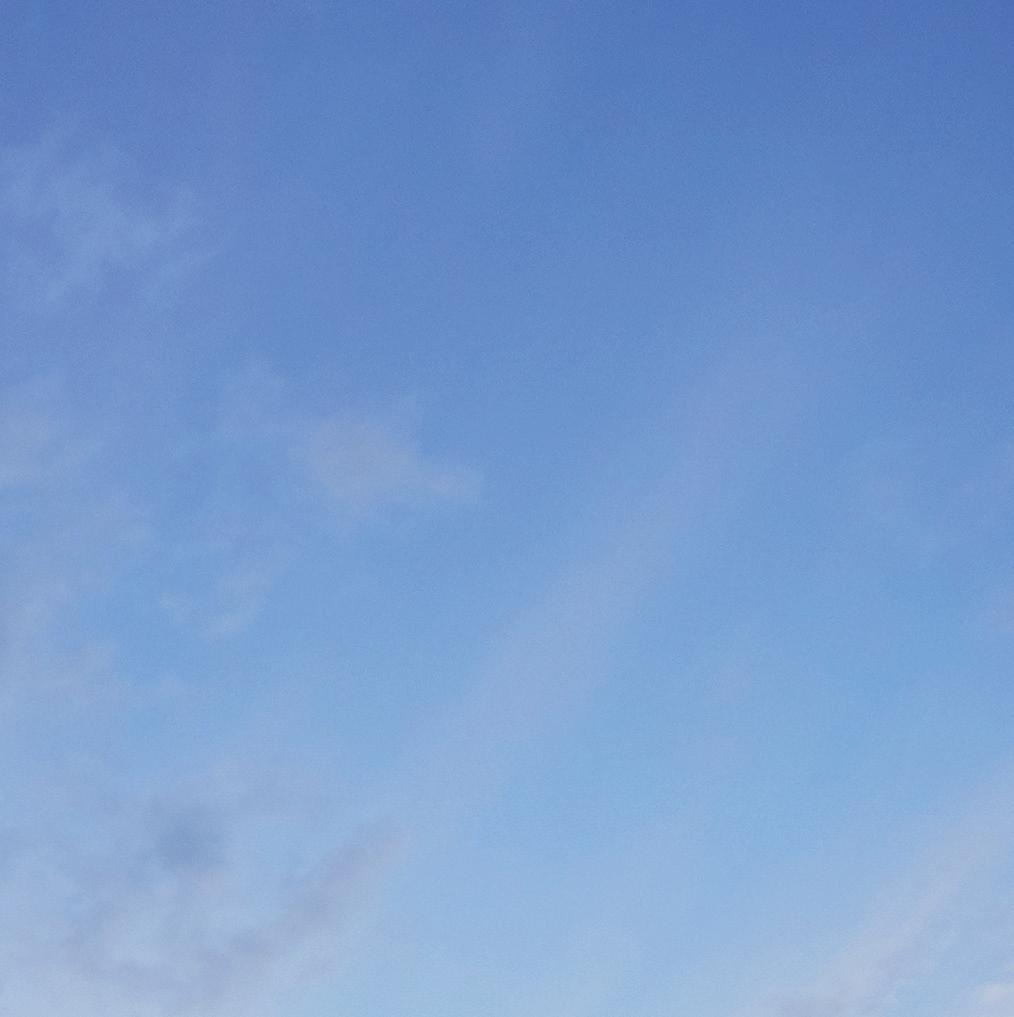
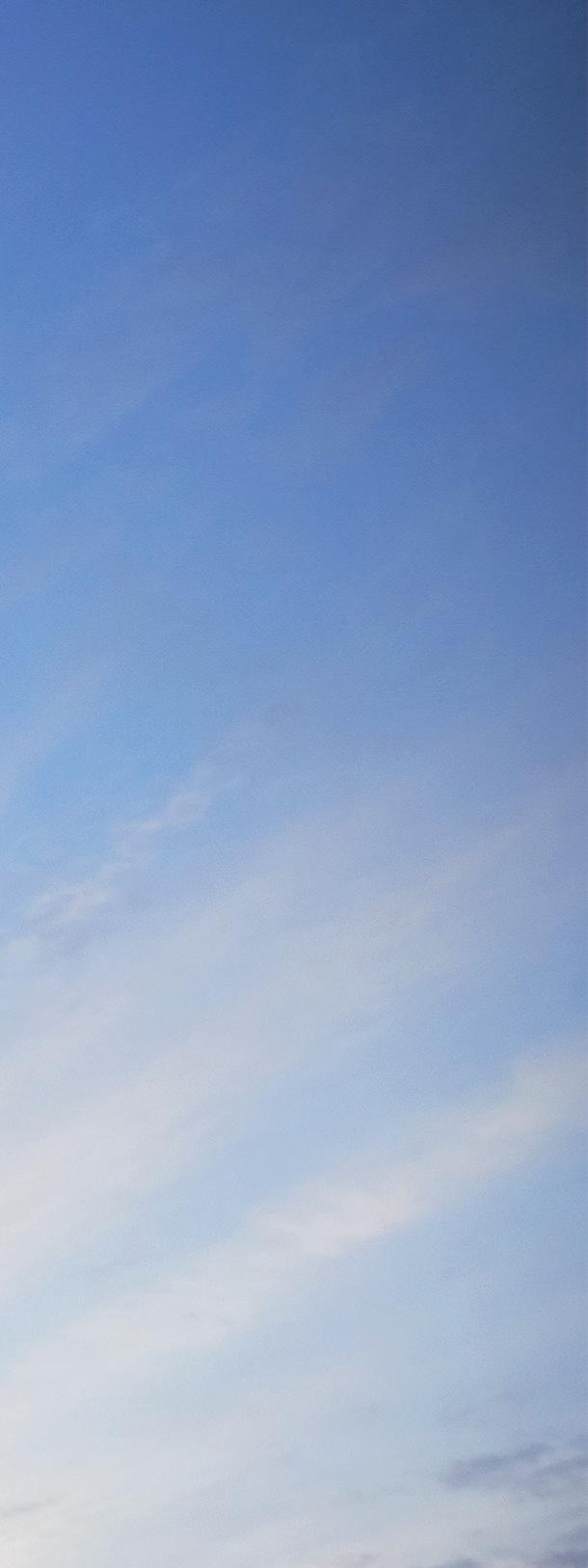
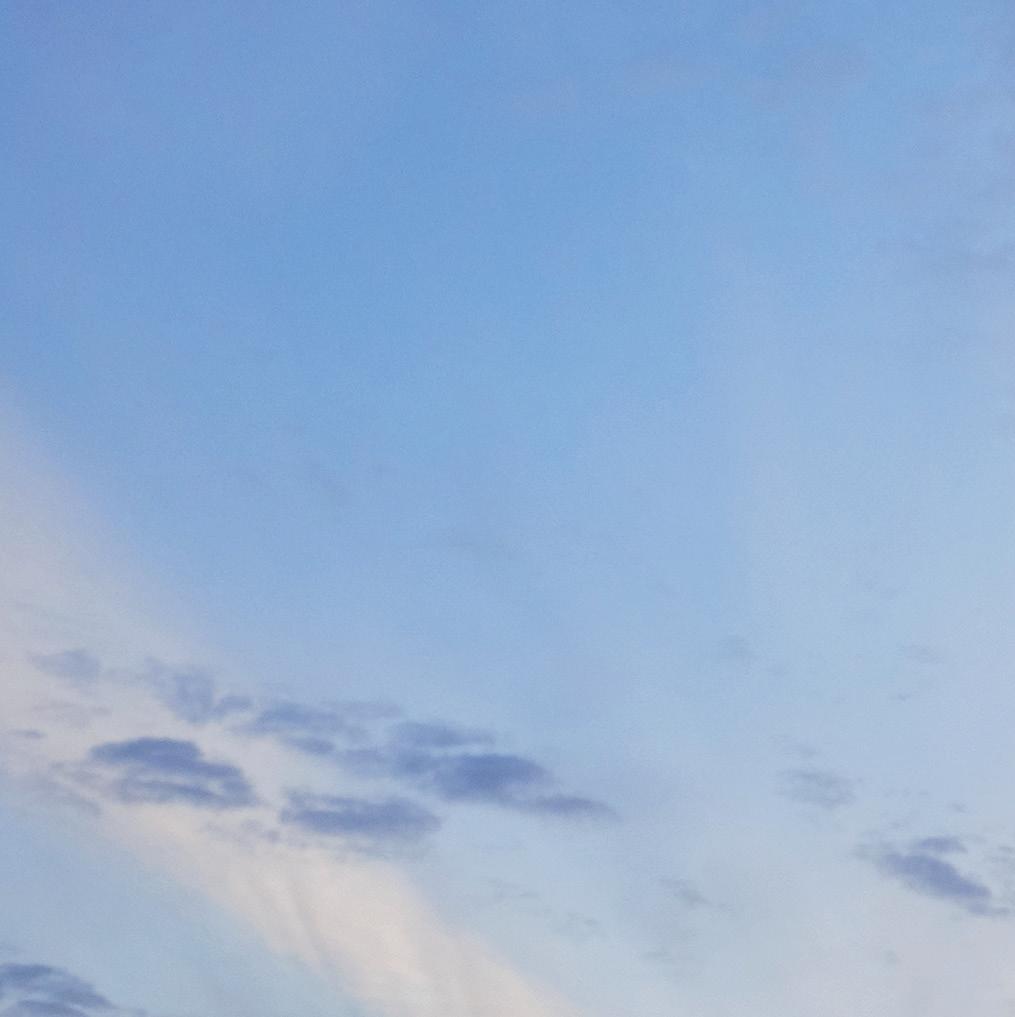
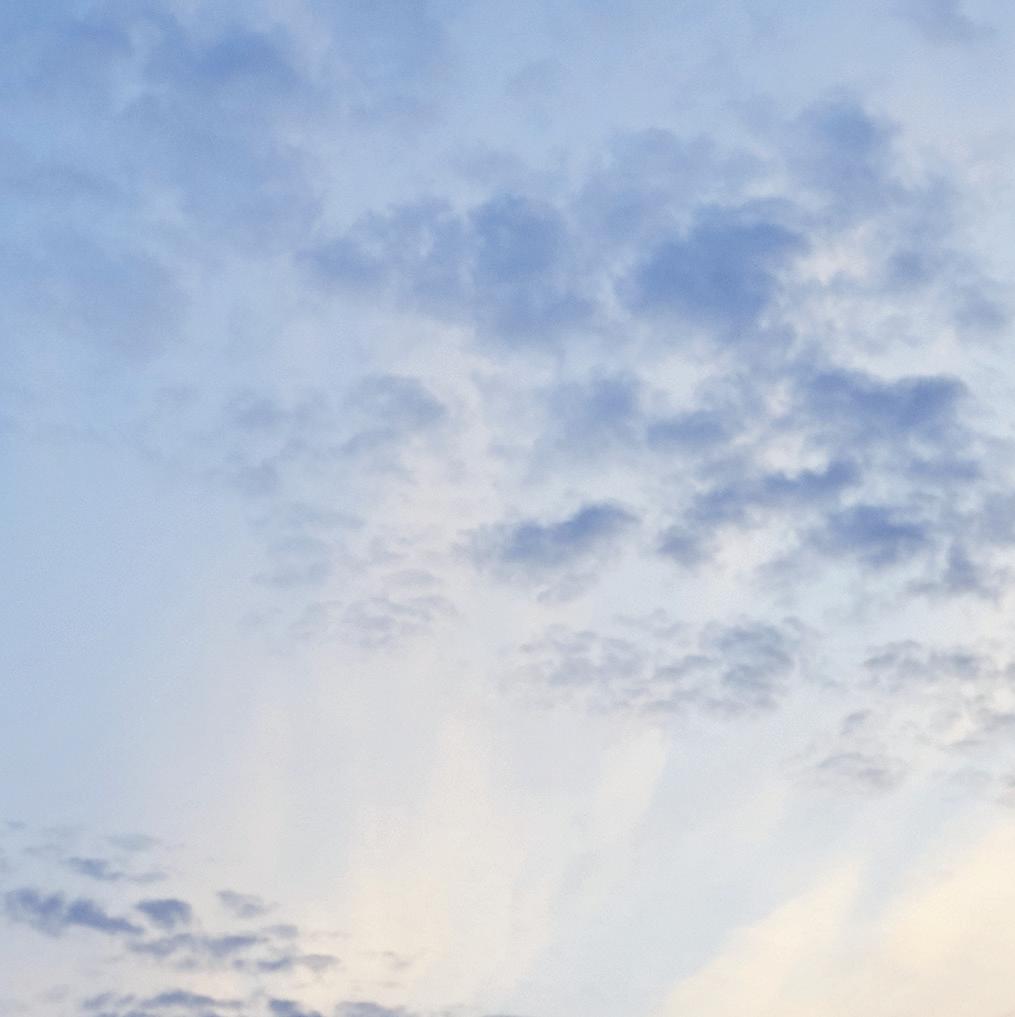
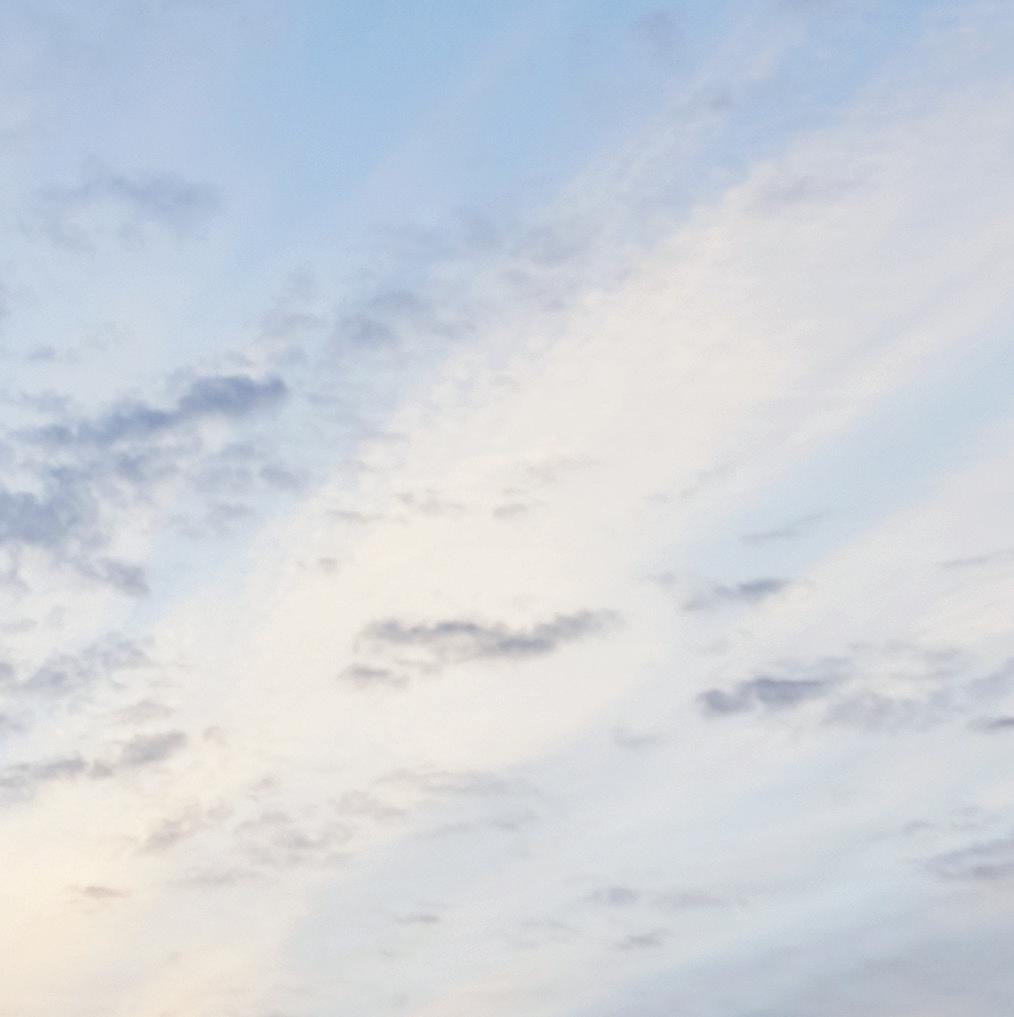
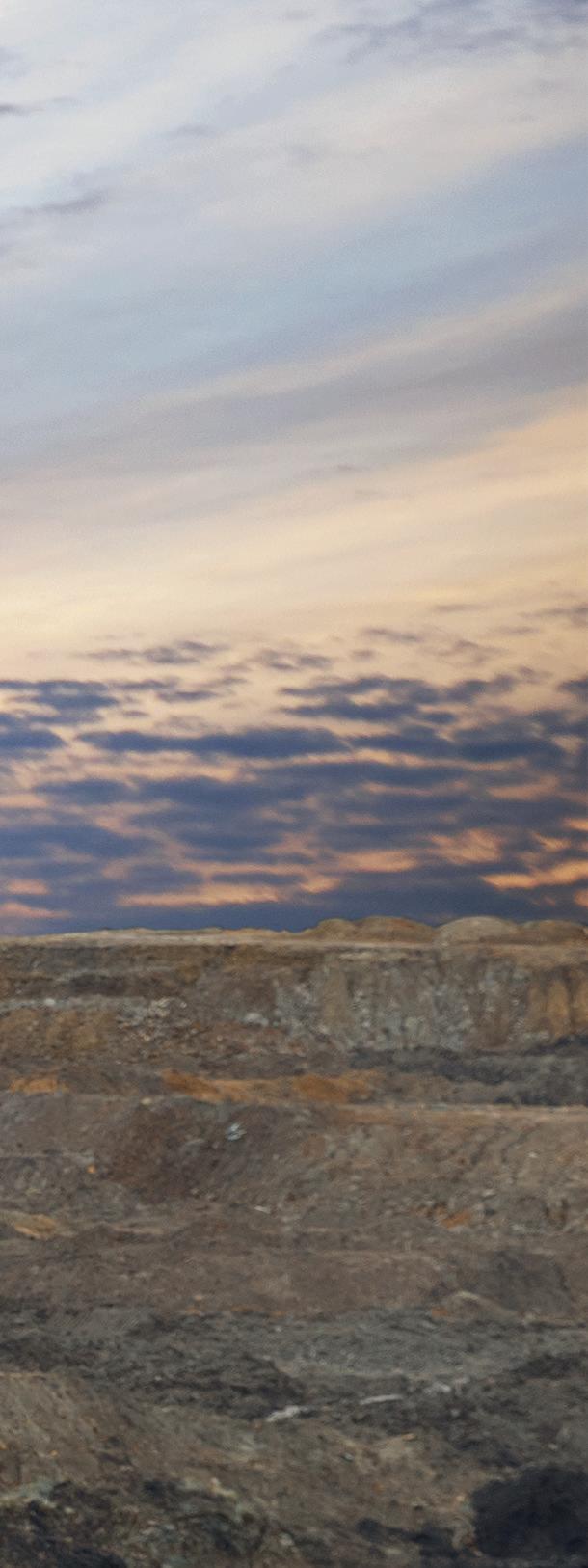
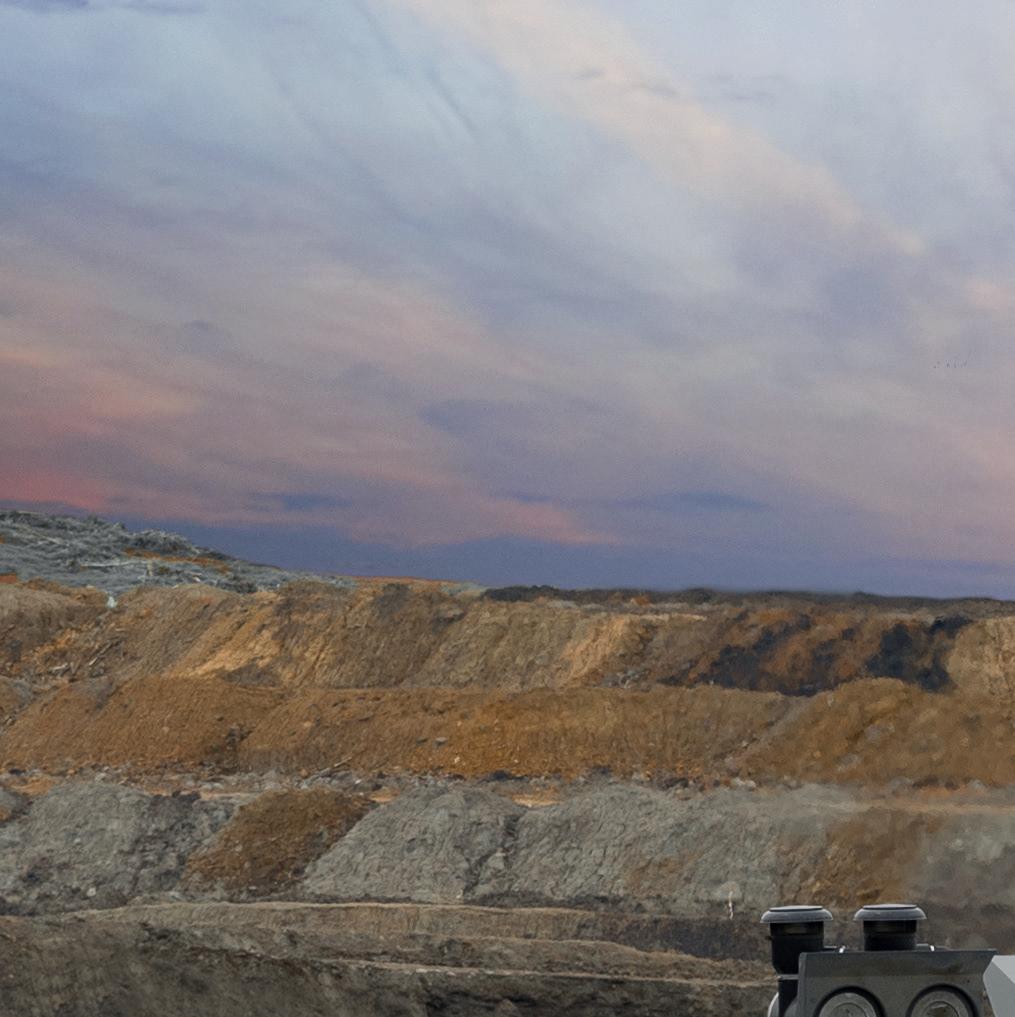
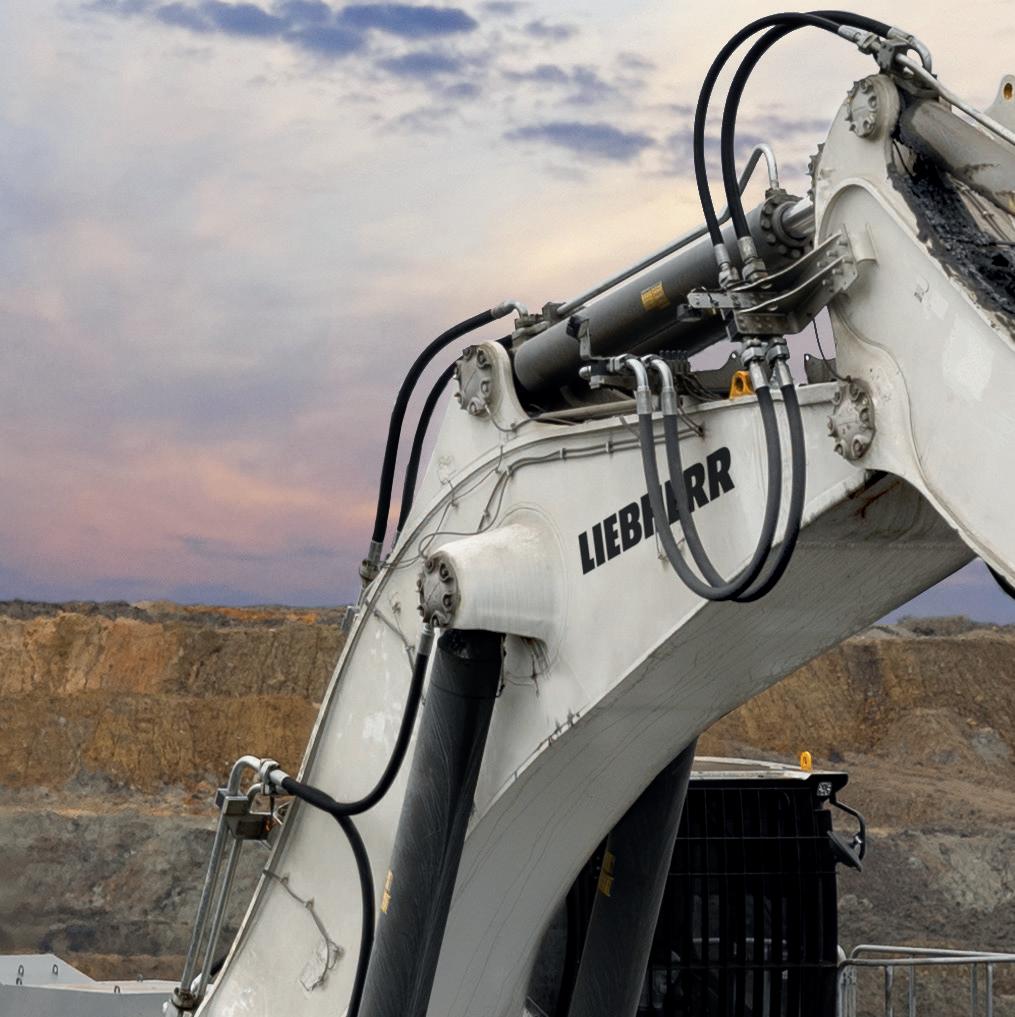
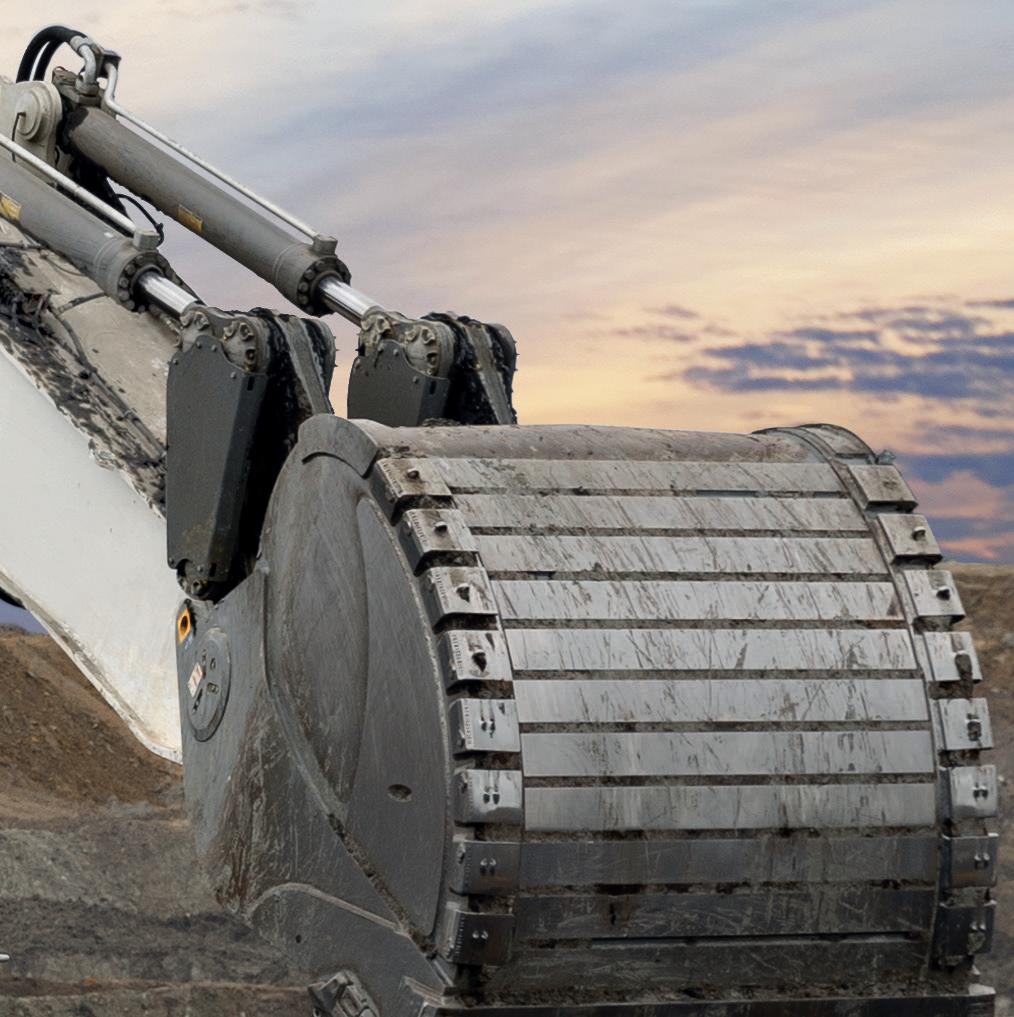

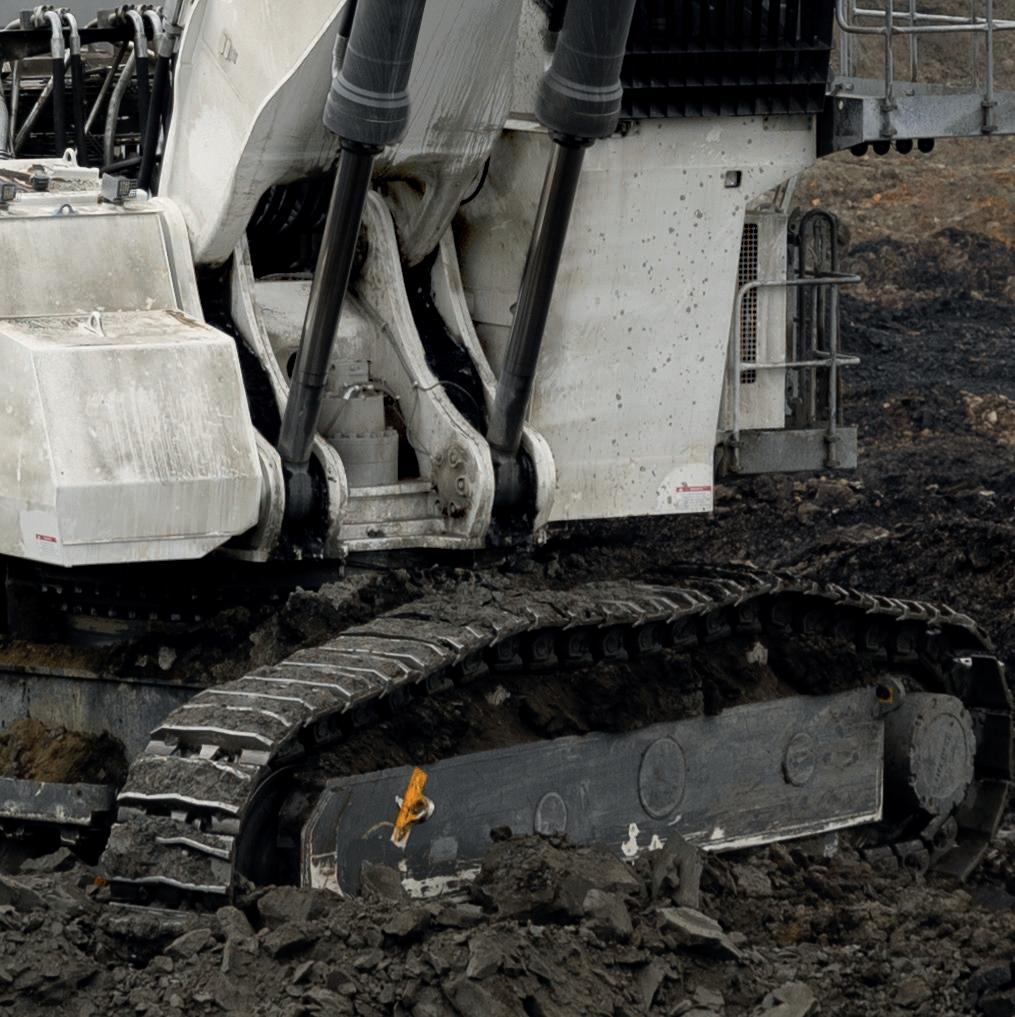
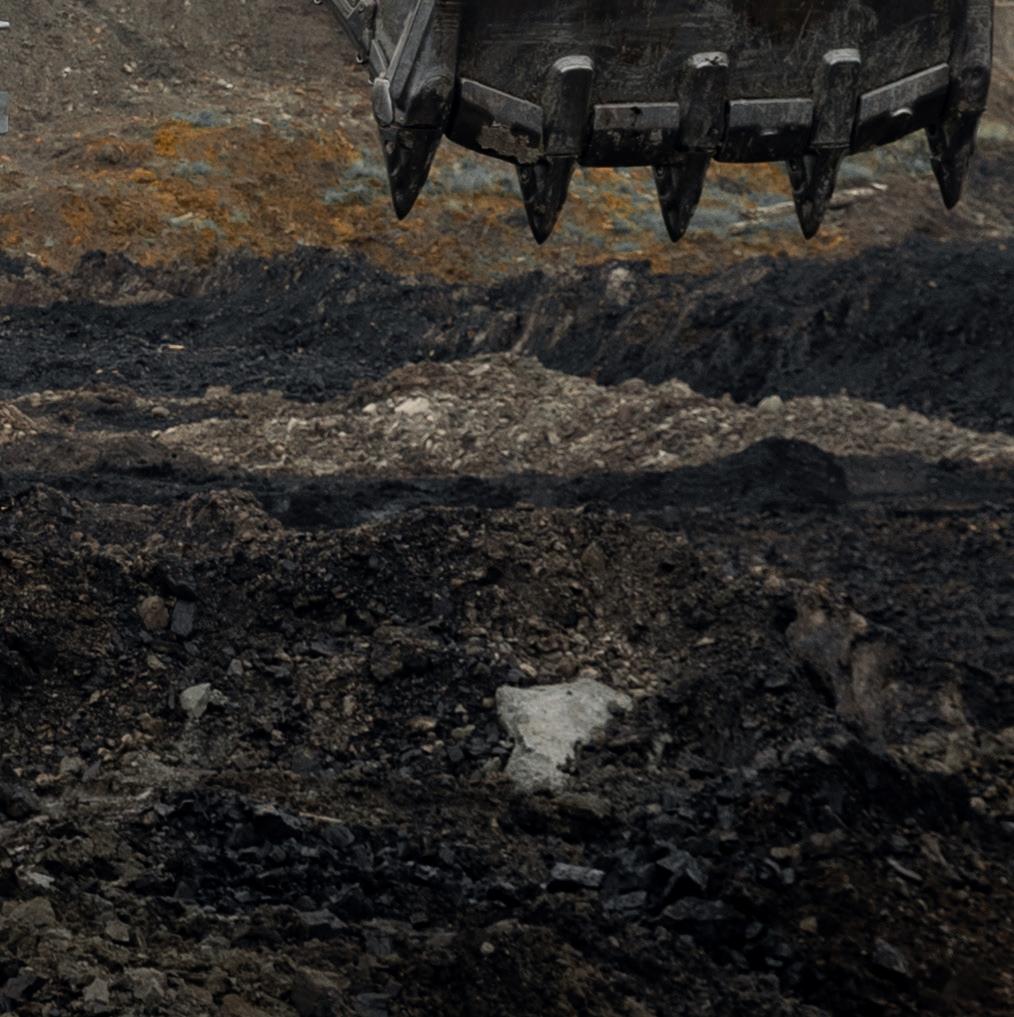
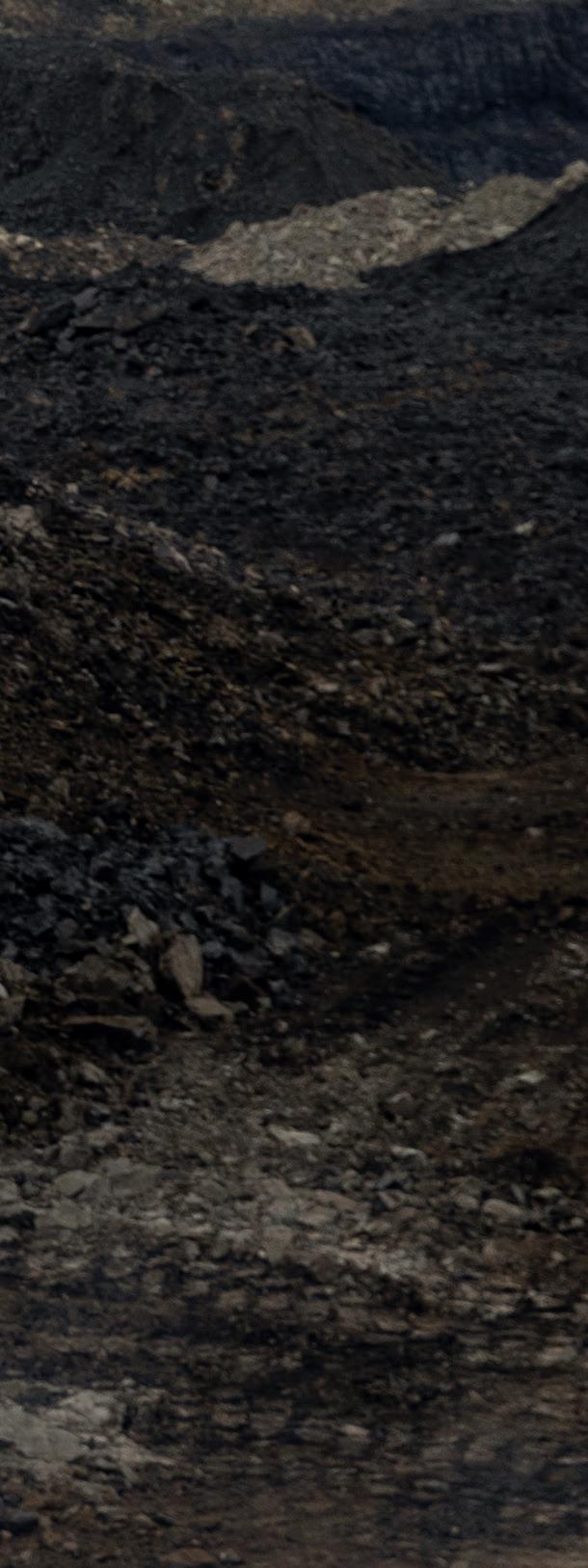
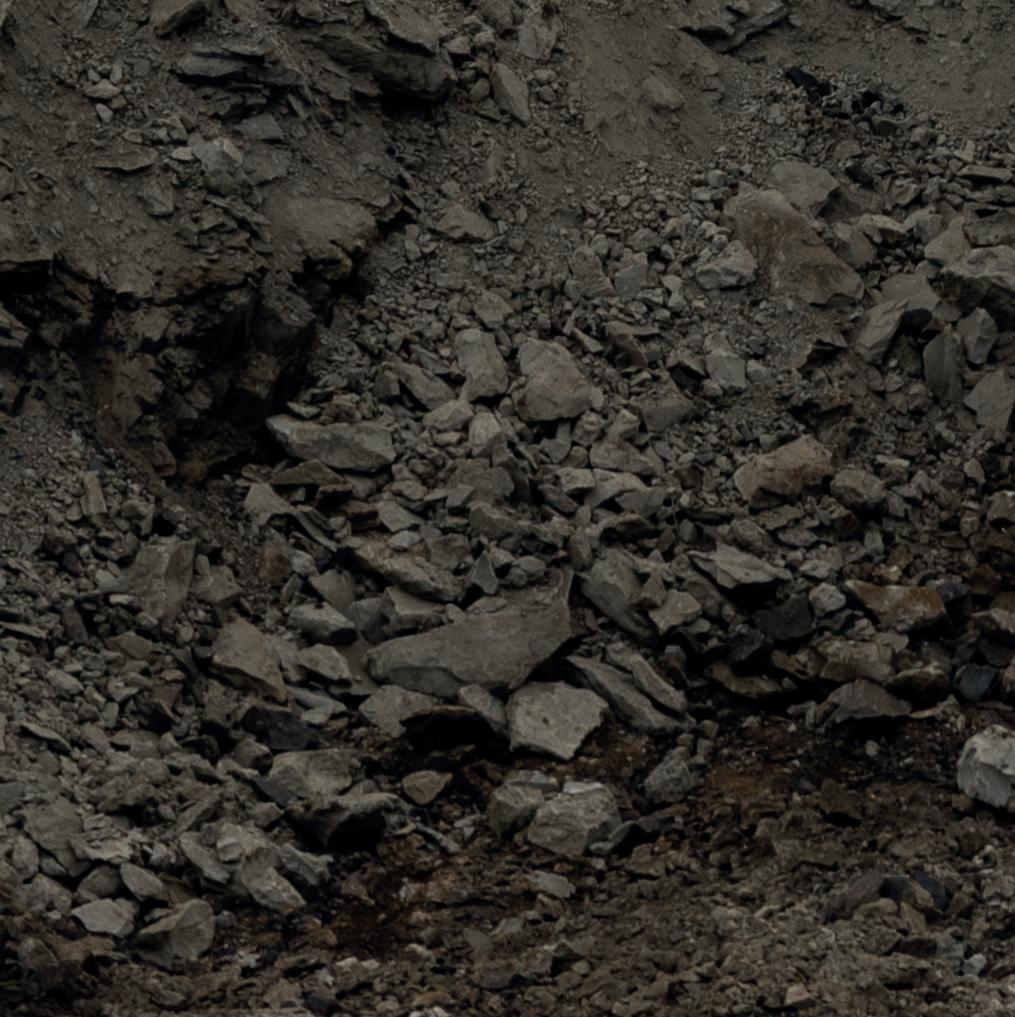
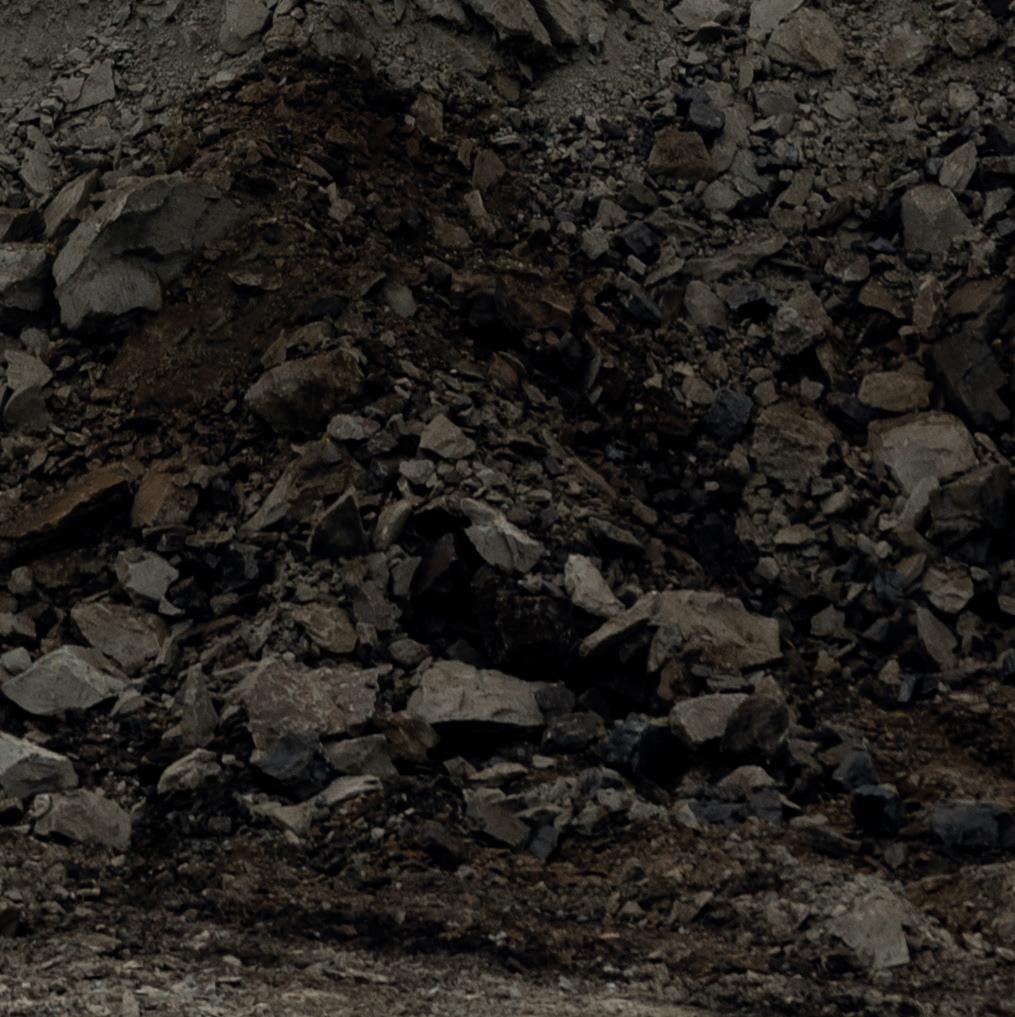
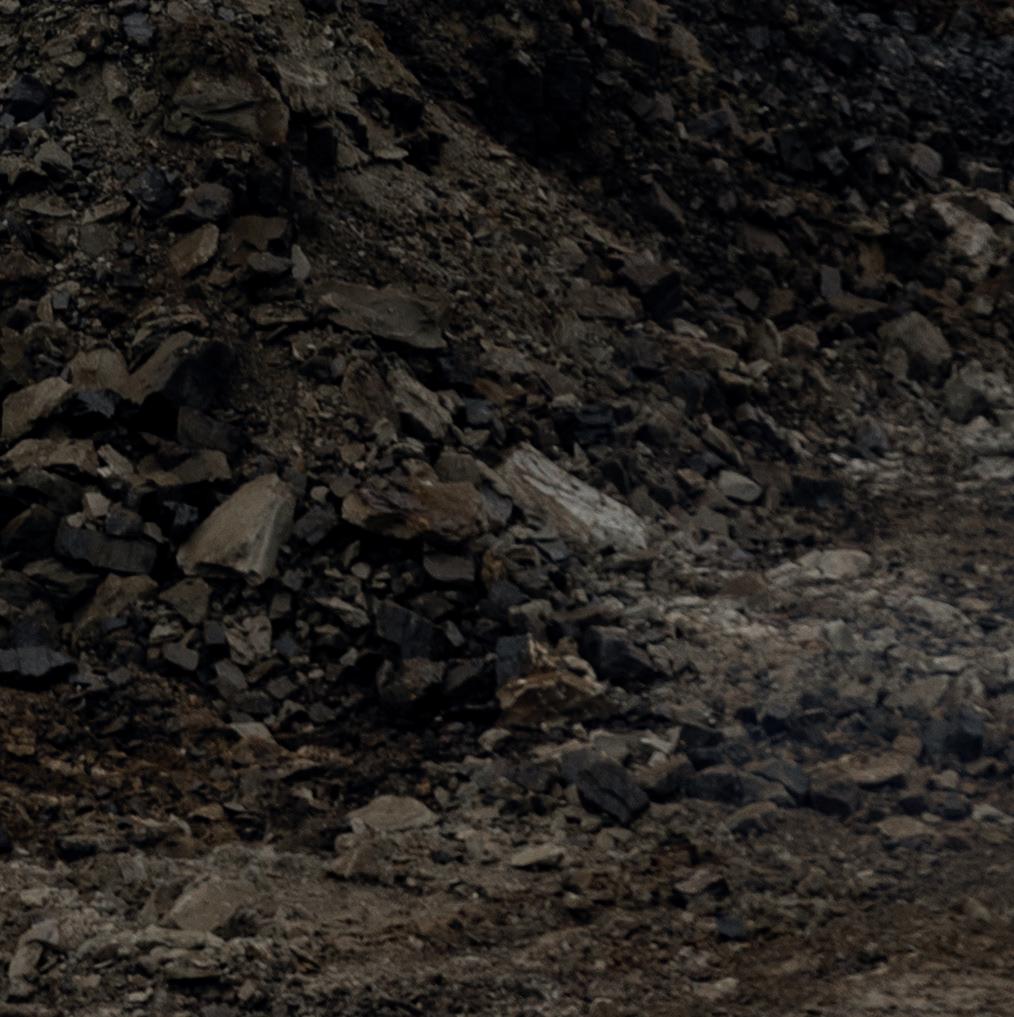
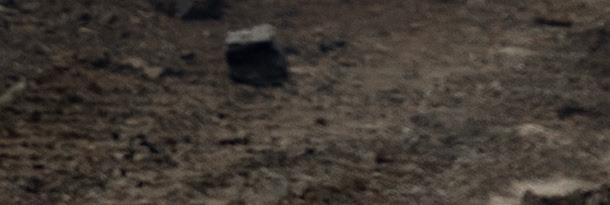
Experience the power of SaberEdgeTM, the ultimate solution for rope shovel lips that redefine excellence.
With unmatched durability and exceptional wear resistance, SaberEdge’s machined adapters result in a precise fit that you can install and forget, eliminating the need for re-tightening—you will only need to touch it again when it is time to remove it.
SaberEdge’s installation and removal require no welding or special tools—thanks to its simplified GET locking systems—enhancing onfield safety, saving time and extending machine availability.
Experience a new era of Whisler-style lips with SaberEdge. Let’s start the conversation.
crmining.com
F.S. Bergh, Howden Africa, and S.K. Ambrosio, Howden Ventsim, outline how to prepare a mines’ ventilation network to support expansion of underground operations.
21 The Future Of Rock Bolting
Robert Penczek, Federico Scolari, Dominik Dendl, and Dieter Glantschnegg, DSI Underground, EMEA, evaluates new opportunities in rock bolting based on pumpable resin and hollow bar.
27 Innovating Ground Support Solutions
Anthony Ferrenbach, Weber Mining & Tunnelling, Mexico, presents a case study of a pipe umbrella type system with resin injection.
30 A New Solution To Age-Old Problems
Michel Runser, Liebherr Mining, France, provides an overview of the R 9300 ‒ the company’s newest excavator ‒ that aims to provide a solution to the ever-increasing demand for greater efficiency and productivity in mining operations.
34 Exploring the Power of Uranium
Nicole Galloway Warland, Thor Energy Plc, Australia, explores the current challenges facing nuclear fuel supply, and how the complex combination of supply and demand factors means that uranium miners operating in friendly jurisdictions are certain to benefit.
39 Leading The Charge For Lithium
Chris Evans, Winsome Resources, Australia, reviews how James Bay has attracted global attention as an emerging lithium province.
Keizo Fujiwara and Takayuki Odawara, Synspective, Japan, and Alastair Bovim, Insight Terra, UK, details how satellite monitoring can improve mine safety and inform operations with data-driven analytics.
46 The Next Frontier
Peter Weaver, Orbital Sidekick, USA, examines how trust in the mining industry can be restored by utilising satellites to employ hyperspectral intelligence.
Liebherr Mining’s latest 250 t excavator, the R 9300, is now available for purchase! Since its market introduction at the 2022 Bauma exhibition in Munich, the R 9300 has demonstrated its reliability, productivity, and efficiency onsite.
Since 1937, Fletcher has been answering some of underground mining’s toughest questions. At Fletcher we provide more than solutions, we provide an atmosphere for an open dialogue with customers to ensure their operations are reaching maximum efficiency. Fletcher provides lifetime support through an experienced, knowledgable team of sales staff, engineers and field service technicans. Is your operation facing obstacles that mass produced equipment isn’t addressing? Get your custom solution started today. Learn more at www.jhfletcher.com
MANAGING EDITOR
James Little james.little@globalminingreview.com
SENIOR EDITOR
Callum O’Reilly callum.oreilly@globalminingreview.com
EDITOR
Will Owen will.owen@globalminingreview.com
EDITORIAL ASSISTANT
Isabelle Keltie isabelle.keltie@globalminingreview.com
SALES DIRECTOR
Rod Hardy rod.hardy@globalminingreview.com
SALES MANAGER
Ryan Freeman ryan.freeman@globalminingreview.com
PRODUCTION MANAGER
Kyla Waller kyla.waller@globalminingreview.com
ADMINISTRATION MANAGER
Laura White laura.white@globalminingreview.com
EVENTS MANAGER
Louise Cameron louise.cameron@globalminingreview.com
EVENTS COORDINATOR
Stirling Viljoen stirling.viljoen@globalminingreview.com
DIGITAL ADMINISTRATOR
Leah Jones leah.jones@globalminingreview.com
DIGITAL CONTENT ASSISTANT Merili Jurivete merili.jurivete@globalminingreview.com
As the world transitions towards net zero, the mining industry has become increasingly focused on the critical minerals needed to power decarbonisation – such as copper, lithium, and nickel. However, there is a concern around the increased carbon emissions from extracting more of these minerals. The industry is working to minimise its carbon footprint through improved efficiencies and technological advances, in order to ensure that the transition to a lower carbon economy is as clean as possible.
Diesel-fuelled mining fleets are a major source of emissions for mining operations, accounting for 30 – 80% of direct emissions at a mine site, depending on the site geography and commodity being mined (ICMM, 2022). This is why Thiess is focused on investigating electrification and/or alternative fuels for our global fleet, as we work to decarbonise our operations and support our clients in achieving their sustainability targets.
In 2022, Thiess introduced five new electric-wheel drive Liebherr T264s in Chile and deployed a further six at its US operations. These new trucks are more efficient, and are an important first step towards further emissions reductions.
We are currently working with Scania to pilot battery-powered trucks, the first full production battery electric vehicle (BEV) units from the Swedish manufacturer, enabling 100% emission-free operations. These units represent a key class of production haul truck for Thiess, with more than 600 medium size trucks (40 – 50 t payloads) used at our operations in Indonesia. The pilot will deliver operational experience with battery-powered units, including charging infrastructure and practices across different applications. Thiess is also working with Scania’s autonomy group to understand how BEV and autonomous technology can be paired for even greater benefit.
Since 2012, Thiess has been involved in autonomous mining, which increases efficiencies and reduces fuel consumption. Over the past few years, we have partnered with leading suppliers to undertake a number of autonomous drilling and hauling trials, which has resulted in autonomous operations becoming an important part of our production capability. Thiess now has autonomous trucks, drills and dozers operating in production environments, with improved production, safety, and a reduction in emissions being key outcomes.
As a company we are continuing to investigate cleaner ways to fuel our existing fleet. We are trialling the use of renewable diesel and have hydrogen trickle-feed trials underway – a transitional technology where small amounts of hydrogen generated on board our mining fleet is captured and ‘trickle fed’ into the engine to improve combustion and reduce diesel usage and emissions.
Thiess is also working to bring dual-fuel retrofit technology to its clients. The project is trialling the conversion of diesel-fuelled trucks to a dual-fuel energy supply of gas and diesel – with the ultimate aim to capture methane gas from the mine for use in powering the trucks, in place of externally supplied gas. It is expected to reduce tailpipe emissions by up to 23%, contributing to Thiess’ efforts to remain at the forefront of sustainable mining.
The deep sea has been in the spotlight recently, with the failed expedition and subsequent implosion of OceanGate’s Titan sub, which made headline news and captivated audiences across the world.
The ill-fated tourist trip set sail on 18 June with the intention of diving 12 500 ft below the surface to view the wreckage of the Titanic. However, the voyage was doomed to never reach its destination. It is now thought that the sub imploded shortly after losing contact with the surface, and wreckage has been recovered from the ocean floor, not far from the Titanic itself. 1
The ocean floor has also been making headline news recently for other reasons, namely the July deadline for the International Seabed Authority (ISA), a branch of the UN, to try and agree on regulations relating to deep sea mining (DSM). At the time of writing, the assembly is debating regulations surrounding the exploitation of minerals from the high seas, a resource considered by the UN as the “common heritage of mankind.”
DSM is a highly controversial topic, and a growing list of countries have called for a moratorium, or, in the case of France, total ban on the practise – due to the widespread ecological ramifications associated with it. However, countries such as Norway, China, and Russia 2 are advocating for its advancement as the potential to extract millions of tonnes of ores and metals – such as nickel, cobalt, manganese, and copper – concentrated in grades that are seldom seen on land, is undeniably alluring. In fact, Norway is proposing opening up a 280 000 km 2 area in the Greatland sea, where it has discovered an estimated 38 million t of copper. 3
The metals in question are all crucial to the net zero transition, specifically for electric vehicles and the production of green energy from solar panels and wind turbines. This raises the question of how to balance rising demand with the risks associated with DSM and whether the required resources could instead be found on land.
The Clarion Clipperton Zone (CCZ), a 4.5 million km 2 area in the Pacific Ocean, West of Hawaii, is perhaps the most well-known area in which the potential for DSM is being explored. 16 of the 31 exploration permits issued by the ISA are concentrated in this area, which was described in a new report, ‘ Why The Rush?’ , from the Deep Sea Mining campaign as the “new wild west.” 4,5 This is concerning given that 5578 different species have been found there, 88 – 92% of which have never been seen before. 6 Thus, the ecological fallout from mining there has the potential to be astronomical.
One of the main points of contention is that DSM is conducted by a robot which is described in the Environmental Law Review journal as akin to a combine harvester – one that trundles along the seabed sucking up 10 cm of sediment alongside the potato sized polymetallic nodules of precious metals. 7 In addition to this, there are a host of other issues with DSM that scientists, NGOs, governments, regulatory bodies, and even global corporations (such as BMW and Google) are highlighting. 8 These include: the destruction of fragile and undisturbed ecosystems that have taken millions of years to form; sediment displacement; noise pollution which is harmful to whales, among other creatures; the potential release of carbon from marine snow (the sediment that falls and collects on the seabed); and mineral leakage and chemical spills affecting water quality, fisheries, and the wider food chain.
With ESG being such a key focus for the mining industry at large today, means of mineral extraction and the environmental harm they cause must be carefully evaluated.
While on-land mine reclamation is a well-established practice, restoring environments damaged by DSM has been shown to be much harder. This is evidenced by the long running DISCOL experiment, conducted in the South East Pacific Ocean off Peru, concerning the mining of a manganese nodule field. The experiment has observed that, even after 26 years, the ecosystem and marine biodiversity have still not recovered. 9 This presents DSM in a starkly different light to on-land mining, as the environmental damage could be irreversible.
Employees at Oceangate tried to warn their CEO, Stockton Rush, of the risks associated with his Titan submersible, but their concerns fell on deaf ears and the fated mission went ahead as planned. To avoid another, altogether more damaging, marine disaster, decision makers around the world need to weigh expert opinion and evidence carefully and patiently before proceeding with DSM as a new avenue of mineral extraction. As conservation biologist Professor Richard Steiner, puts it: “It would be truly unfortunate if we allow the same industrial paradigm that destroyed much of the terrestrial ecosystems of our home planet to do the same in the deep sea. It is time to change this model.” 10
References
Available on request.
It is fair to say that, over the last decade, various filtration technologies have shown a significant evolution in terms of available sizes, reliability, and their level of automation. Diemme Filtration, headquartered in Italy, is a company that is heavily invested in this process.
In November 2021, the company launched the largest filter press in the world: the GHT5000F Domino equipped with 5000 x 5000 mm plates. This unit is now in operation at the Toquepala Copper mine in Peru, operated by Southern Copper Corp. (SCC), a majority owned subsidiary of Grupo Mexico.
The unit arrived in Peru in mid-2022 followed by onsite assembly and installation. The unit was started up and commissioned and was producing and discharging the first filter cakes before the end of the year. The overall design of the filter press, including all the components, facilitated a smooth installation for the site personnel thanks to detailed engineering which optimised features and minimised cabling.
SCC’s main goal for installing the Domino is to gradually transition to filtered tailings disposal. This approach will reduce the footprint of the tailings storage facility (TSF), while increasing water recovery and reducing the environmental risks for the surrounding area. The first Domino is a commercial size ‘pilot unit’ capable of handling over 8000 tpd of dry solids from the filtered tailings. Once the machine and the technology perform as expected, including achieving agreed moisture and productivity targets, SCC plans to install a much larger bank of up to 9 or 10 of these filter presses for a total capacity of over 80 000 tpd. The testing period will also allow SCC to get familiar with the machine operation and regular maintenance.
With a total filtration volume of 71 m3, and a filtration area of 2850 m2, the GHT5000F Domino remains the largest filter press available on the market. On large throughput projects, the GHT5000F Domino significantly improves the capital cost of a tailings filtration plant, compared with installing many smaller filter presses for the same task.
Because of the high market demand for projects requiring the treatment of large tonnages of product, Diemme Filtration has invested in the expansion of their manufacturing facilities in Lugo, Italy. The significant increase in manufacturing space to the existing factory will allow Diemme Filtration to double current production capacity, by using the most modern technologies while meeting all environmental standards. The new building addition will be equipped with the latest state of the art manufacturing equipment and ample space, in order to efficiently increase the production of the latest and largest models in the Diemme product portfolio – including the Domino.
In recent years the mining industry has shown an interesting trend: cooperation between parties that, in previous times, considered each other competitors. Today, especially in the fields where it is urgent to find strong solutions to serious problems (like tailings management), it is common to see joint efforts of clients and suppliers partnering with a common goal. Communication, transparency, and close cooperation and collaboration are the necessary elements for success in an industry which needs to move quickly and has little time to waste.
Caterpillar Inc. and Wheeler Machinery recently completed installation of a Cat® MineStar™ fleet management system (FMS) at the Kennecott Bingham Canyon Mine, located just outside of Salt Lake City, Utah. Rather than upgrading the mine’s previous fleet management system, Kennecott, a Rio Tinto Company, chose to deploy MineStar Fleet. This has optimised the mine site’s equipment tracking, production recording, material management and truck assignment, and it has further expanded the technology relationship between Caterpillar and Rio Tinto. Even though it was not the easiest route for the mine, the cost-benefit analysis showed significant benefits long-term using MineStar Fleet, including seamless integration with MineStar Terrain currently used by the mine.
Anglo American has announced that De Beers Group and the Government of the Republic of Botswana have reached an agreement in principle on a new 10-year sales agreement for Debswana’s rough diamond production (through to 2033) and a 25-year extension of the Debswana mining licences (through to 2054).
Debswana operates four diamond mines in Botswana and is a 50:50 joint venture between De Beers and the Government of Botswana.
De Beers and the Government of Botswana will work together to progress and implement the formal new sales agreement and mining licences. In the interim, the terms of the most recent sales agreement (which expired on 30 June) will remain in place.
AIMEX
05 – 07 September 2023
Sydney, Australia
www.aimex.com.au
High-Performance Mining Conference
07 – 08 September 2023
Aachen, Germany
www.hpm.academy-rwth.de
Mining Indonesia
13 – 16 September 2023
Jakarta, Indonesia
www.mining-indonesia.com
Iron Ore Conference
18 – 20 September 2023
Perth, Australia
www.ausimm.com/conferences-and-events/ iron-ore
China Coal & Mining Expo
25 – 28 October 2023
Beijing, China
www.chinaminingcoal.com
International Mining and Resources Conference (IMARC)
31 October – 02 November 2023
Sydney, Australia
www.imarcglobal.com
Resourcing Tomorrow
28 – 30 November 2023
London, UK
www.resourcingtomorrow.com
To stay informed about upcoming industry events, visit Global Mining Review’s events page: www.globalminingreview.com/events
Australian mining company, Northern Star Resources Ltd, has placed an order for a wide range of FLSmidth mineral processing technologies for its Kalgoorlie Consolidated Gold Mines (KCGM) mill expansion project.
KCGM Operations are located east-northeast of Perth in Western Australia, part of one of the richest goldfields in the world, the so-called Golden Mile, close to the city of Kalgoorlie-Boulder. The order is valued at approximately DKK 515 million and was booked in 2Q23. The equipment is due to be delivered during 2024.
Under the agreement, FLSmidth will supply a range of MissionZero products covering most of the flowsheet, including: SAG mill, Ball mill, primary crusher, pebble crushers, flotation cells, and a pre-leach thickener. In addition to these technologies, the order also includes spare and wear parts. Upon installation, these technologies will substantially reduce the mine’s energy consumption.
The 20 MW grinding mills will be the highest power, gear driven mills in the world, and the Ball mill will be the first gear driven 28 ft diameter Ball mill.
Micromine has successfully implemented its innovative fleet management system (FMS) and mine control solution, Micromine Pitram, at the new underground mine, Goldrush –part of the world’s largest gold mining complex owned and operated by Nevada Gold Mines (NGM).
For over two decades, the innovative technology suite has been in use at several NGM sites, including Cortez, Goldstrike, and Leeville. The implementation of Micromine Pitram at Goldrush, NGM’s flagship development project, is an important next step in enabling the organisation’s growth ambitions.
Phase 1 of the Micromine Pitram implementation was successfully deployed at the Goldrush operation, consolidating and monitoring production data, including shift and daily production schedules of loaders, trucks and drill fleets, in addition to improving accuracy on yield forecasting. As the site’s data backbone, Micromine Pitram also ensures operational teams and regional management have improved insight into shift and production activities to improve productivity and plan accuracy.
Located in the Elko region, Nevada, the expansive mining complex is the result of the historic joint venture between Barrick Gold Corp. and Newmont Mining Corp. On an annual basis, the network of 10 underground gold mines collectively moves more than 8 million t of minerals.
The Micromine Pitram team will continue to support NGM and looks forward to implementing solutions to additional NGM sites in the future, as part of their ongoing commitment to innovation and technology.
Automation and remote technologies have been rapidly gaining traction within the global mining industry. Over the last decade, this has been evident with dozens of mines investing in autonomous haulage operations. The advancement of new mining technologies has changed the nature of work and driven the redefinition of the human role in mining.
Amongst all this change, one thing that remains truly evident is that human performance plays a critical role in realising the full potential of autonomous technology. This is because automation in mining (as of today) typically relies on humans to interface with machines and provide some level of monitoring and guidance.
With fewer humans in the operation, the remaining roles are more responsible for tasks that were traditionally completed by all members of a crew; such as reporting spillage, sinking ground, or handling ambiguous situations which require elevated decision-making skills. This increased responsibility has raised the threshold for training in the new autonomous mining environment. More effective training and change management has been a high priority of autonomous haulage mines. Immersive Technologies’ simulation has been proven to be an effective tool for skills development from basic competency through to advanced skill optimisation, as it provides the ultimate in learning-by-doing with a high degree of learning transfer directly to the field. Immersive Technologies simulators provide measurable tracking of specific operator behaviours so that meaningful coaching can be provided, and performance can be optimised. Besides training for common every-day tasks, this also includes response to emergency events which are not easily replicated in the actual operation. Simulator training also reduces the amount of in-field training time, minimising impact to production and ensuring increased levels of safety.
With autonomous haulage system (AHS) technologies continually evolving at a rapid pace, the training requirements to reskill or upskill are not viewed as a one-off effort, but instead as ongoing change management process.
The following is a case study involving a large surface mine utilising autonomous haulage in South America.
Excavator operators were faced with productivity challenges related to managing new autonomous haulage requirements, in addition to their traditional responsibilities of managing the dig and load cycle. The complexity of their roles was evaluated and presented an opportunity for an operational improvement to be achieved through additional training. Objectives included increasing their proficiency in the use of the AHS by reducing autonomous truck loading and interchange time; and increasing instantaneous and production dig rates.
A targeted AHS excavator simulator training curriculum was developed by Immersive Technologies and a group of experienced operators were put through that training curriculum. In-pit data was taken for each excavator operator before and after training over a three month period.
In-pit results achieved by target group:
n 5% improvement in instantaneous dig rate.
n 12% improvement in production rate.
n 6% improvement in loading rate.
n 6% improvement in truck loading time.
Benedikt Sobotka, Eurasian Resources Group, Luxembourg, and the Global Battery Alliance, Belgium, discusses critical raw materials and Europe’s new industrial strategy.
The European mining industry has a long and varied history, playing a significant role in the development of European societies for thousands of years. For as long as people have settled on the European continent, they have been breaking ground in the search for rock, minerals, and precious metals.
Mining has been fundamental to the development of the modern European economy. In the 19th century, Europe accounted for approximately 50% of global mining output. European mines fuelled the first industrial revolution, changing the world forever. It was European mining that enabled nation states to grow into great global powers. From antiquity to today, mining, quarrying, and excavating has been central to the European story. Without mining, there would be no cities of stone, brick, or marble; no Athens or Rome to speak of.
Today, however, Europe’s mining sector represents a fraction of global mining production. It constituted just 5% of global output in 2020 and is reportedly one of the only regions in the world with a declining mining industry. Whilst a transition away from reliance on fossil fuels is a welcome development in the fight against climate change,
it is important to consider whether the managed decline of mining sectors in fact limits our collective ability to respond to the green energy transition. Put simply, is Europe, and the world more widely, readily equipped to cope with the increase in material demands for the net-zero transition?
To meet the goals of the Paris Agreement, the world’s developed economies must come together to undertake a second, but crucially more sustainable, industrial revolution. The continent must rethink and transform its manufacturing, transport, waste management, infrastructure, and construction industries. To this end, the mining industry must be ready to fulfil the biggest purchase order in modern history, as the demand for raw materials is set to grow exponentially.
The IEA has stated that sectors contributing to the green energy transition, such as transport and energy storage, will be responsible for 45% of total copper demand, 69% of cobalt demand, 61% of nickel demand, and 92% of lithium demand by 2040. The majority of this growth will come from EVs and battery storage, which are expected to add around 12.2 million t of demand for energy transition minerals by 2040.
And this is where Europe finds itself at a crossroads. Whilst the continent is blessed with an abundance of industrial resources, such as aggregates in Poland and iron ore in Sweden, it is heavily reliant on imports for many critical raw materials. Suppliers of these raw material imports are generally concentrated in a handful of countries, for both extraction and processing.
Take, for example, the EU’s trade relationship with China: the region imports over 95% of its magnesium from China. Furthermore, over 60% of cobalt is refined in China, often after being shipped from the Democratic Republic of the Congo (DRC) – a nation home to approximately 75% of the world’s total mined cobalt. This leaves Europe more vulnerable to supply risks and, in a worst-case scenario, even being held hostage in negotiations through minerals diplomacy and geopolitical bargaining. There have already been incidents of mineral-rich countries leveraging their position over buyers.
In the current import-max system, Europe needs its supply routes to be clear and operable at all times, or else the entire continent’s strategic autonomy could be threatened. Supply chain issues, such as the closing of a strategic trade passage, could see Europe suddenly cut off from the global supply of raw materials. Such an event would have adverse consequences for Europe’s technology, energy, security, defence, and mining industries.
So, what can, and should, be done? Firstly, Europe must learn to reconcile the dual objectives of significantly reducing carbon emissions, whilst simultaneously investing in its mining and mineral capabilities. Whilst European mining does not possess the strength of yesteryears, Europe is still home to a robust, innovative and vibrant mining economy, as well as some of the world’s leading mining operators. With new strategic partnerships across the globe and new commitments to responsible mineral exploration, Europe can start to build its own self-reliance concerning critical raw materials. If European mining companies were to account for a greater share of the global raw materials extraction and production market, this would in turn increase Europe’s strategic autonomy.
Moreover, as a major financier, Europe can support the financing and development of additional mining projects not just within Europe, but in higher risk jurisdictions where new reserves of critical minerals are being found. To meet huge demand for critical minerals, work in jurisdictions that are more complicated, with higher risk profiles, will be required. It is particularly important to take action now, given new mining prospects can typically take five to seven years to establish. Initiatives like the Battery Passport, which is being developed by the Global Battery Alliance (GBA), a 140-member strong multi-stakeholder initiative, can assist with operating in these jurisdictions. The GBA aims to establish a sustainable battery value chain by 2030. Its flagship Battery Passport will bring new levels of transparency to the sourcing and production of batteries and their components, tracking materials across the entire value chain and providing end-users with important data on the batteries’ provenance, chemical make-up, and ESG profile.
Luxembourg-headquartered natural resources group, Eurasian Resources Group (ERG), has taken a lead in mineral exploration across the globe, including both higher risk and more traditional environments. Earlier this year, ERG signed an agreement with Ma’aden, a leading state-owned mining company in the Kingdom of Saudi Arabia, to achieve tech-enabled mineral exploration across the country. Saudi Arabia has the largest mineral deposits in the Middle East, including deposits of key materials for the energy transition, like copper, aluminium, and iron, as well as gold, silver, and lead. Europe could consider following Saudi Arabia’s example and encourage funding in new green and socially responsible mining projects and mineral exploration, in order to meet the vast quantity of mineral demand.
The EU’s Critical Raw Materials Act, unveiled by the European Commission in March, is a step in the right direction. For example, the 2023 Act rightly listed cobalt as a critical raw material. Both cobalt and copper are indispensable for the electrification of the mobility industry and vitally important to European interests over the coming decades. If the Act is ratified by the European Parliament and passes into law, the EU will have committed itself to developing a clean energy economy with enhanced security and diversification across critical material supply chains, whilst addressing heavy reliance on non-EU suppliers, such as China and the DRC.
According to the Cobalt Institute’s recent Cobalt Market Report, in 2022, Europe accounted for just 2% of mined cobalt, and 12% of global refined cobalt. Whilst the region may lack significant deposits of cobalt, the report notes that European refining capacity must still increase to drive strategic autonomy. The Act will seek to onshore the production of at least 10% of the EU’s annual consumption of strategic raw materials, and 40% of processed minerals demand, by 2030. Further, the Act recognises the importance of critical materials recycling, and will require EU nations to achieve at least 15% of material supply from European recycling plants.
Europe’s ability to protect its natural resources and ensure its access to a reliable and secure stream of critical raw materials will be central to the future prosperity of the continent’s economy. All of the devices that we know and love today – our phones, laptops, electric vehicles – are powered by key raw materials, in one form or another, and so our reliance on these resources should not be underestimated.
Mining will play a key role in Europe’s economic and net-zero future. It is paradoxical to think, and perhaps hard to accept, that whilst work must be done to reduce carbon emissions, more mining and excavating of critical resources than ever before must also take place. However, Europe cannot shy away from the mineral supply challenges posed by the green energy transition. The mining industry must stand ready, and policy makers must offer all the support they can to those prepared to responsibly mine for the future, and help lead the world to a greener energy transition.
AIMEX is the destination for the mining sector to collaborate and hear from industry thought leaders. AIMEX provides an unmatched opportunity to connect and do business with some of the best mining suppliers from around the world, while sourcing solutions to boost productivity and meet sustainability goals. New at AIMEX this year are the Transformative Technology Pavilion and the Decarbonisation Zone.
industry connections 6,000+ local and international suppliers
250+ expert speakers 50+
An undisclosed mine project has been in operation since 1966 and has workings extending approximately 1.2 km below surface. As a result of this depth, the geothermal properties of the host rock, the age of the operation and the age of ventilation infrastructure, and the underground conditions posed challenges to future plans for deepening the current workings. Thus, the operation began looking for a solutions partner that could support its drive towards zero harm, by designing and implementing a mine ventilation system that would enable and support its endeavours and plans for expansion. The final design provided by the chosen solutions partner, Howden, ensured the mine remained adequately ventilated to create workplaces which are safe and risk free to the health of employees.
To ensure that the ventilation simulations/ventilation models accurately reflect the mining operation, great care was taken to ensure the base parameters were accurate and based on proven research. Ventilation plans, as well as onsite measurements taken by Howden personnel, were used. The information provided by the operation was of a sufficient
nature that Howden was ultimately able to achieve balance of the model with airflows within 5% (and often closer) of those values indicated on the ventilation plan. The calibrated model can be seen in Figure 1.
In summary, the mine is supplied with 225.8 m³/s at its upcast shaft. A total of 76.4 m³/s is provided to
production commitments. A further 50.0 m³/s is provided to non-production commitments. Therefore, in total 126.4 m³/s is utilised by commitments. On this basis, a total system air utilisation of 56% is achieved, with wasteful leakage accounting for 99.4 m³/s of the total upcast capacity.
The most pertinent issue identified was damaged dampers within each fan drift. Numerous damper vanes were not in the fully open position, and this resulted in an unnecessary pressure loss of ±2500 Pa. The high pressures and increased system resistance caused by the damaged dampers indicated that the fans were operating at approximately 46% efficiency.
During the course of the underground surveys conducted, numerous incidences of leakage into the return and abandoned areas was observed. In the case of the latter, given the age of the workings and the unavailability of comprehensive survey plans, it was not always clear where this air was flowing to. Irrespective of this, there was an obvious argument to seal off all old workings and to address any leakages directly to the return. This is also advantageous from a safety point of view, as it prevents people from entering abandoned areas.
A pressure survey was conducted along the main return airway of the mine. This showed that a total of 2925 Pa is made available to the system by the surface fans. This is best described as the available force to overcome the resistance of the workings and allows ventilation to flow within them.
On Level 33/1, the available pressure drops to a negligible -25 Pa. There are two key observations that should be made from this:
n The surface fans are effectively being used to overcome the resistance of the area above Level 33/1 to surface.
n The remainder of the workings (i.e. lower than 33/1) is ventilated by some other mechanical means, as air movement is observed on these lower levels.
It is, at this point, necessary to appreciate the structure of the main return airway raise. There are three significant portions to the raise:
n From surface to Level 9, the return consists of a 4.0 m x 4.0 m (16.0 m²) steeply inclined airway (30° from the horizontal).
n From Level 9 to Level 35, the return consists of a series of Ø5.0 m (19.635 m²) near-vertical raises. The raises appear to have been blasted and not raise-bored. This means they have a relatively high friction factor.
– Fitted with Liebherr Mining’s most advanced innovations
– Designed to support greenhouse gas emission reduction targets: Liebherr Power Efficiency comes as standard to reduce fuel consumption, diesel engine is Tier 4/Stage V compliant, electric-drive powertrain already in development
– Strong parts commonality with existing excavator portfolio to reduce lifecycle costs and to simplify maintenance
New attachment design reduces overall machine weight resulting in faster cycle times and increased Approved Rated Suspended Load (ARSL) –
Introducing the latest cabin generation: enhanced ergonomics, large touch screens, and a new and improved control panel design
It is important to note that these raises are offset from one another. This results in small transition airways connecting each raise, which cause substantial shock losses due to the change in airflow direction.
n From Level 35 downwards, use is made of a variety of Ø2.0 m (3.142 m²) vertical raises.
From level 37 downwards, only two raises with a combined area of 6.284 m² are used. The return airway raise is therefore severely constrained by this bottleneck. The return airway system is depicted in Figure 2.
The changes in size, which varies from a maximum at 19.635 m² to as little as 3.142 m², provides additional severe shock losses to the system. Using the main return
line from surface to the lowest portion of the mine, this return has a combined length of ≈1970 m of varying dimensions. The main return airway raise has a combined resistance of 0.1431 Ns²/m⁸. Considering that the surface fans experience a resistance of 0.1923 Ns²/m⁸ without the resistance of the dampers (as explained in the surface fan section), this means the entire balance of the system has a resistance of 0.0492 Ns²/m.
Based on this, 75% of all fan energy expended on the system is being used to overcome the main return airway raise. Worse, if cognisance is taken of the resistance currently posed by the dampers, 86.5% of all fan energy is expended to overcome the main return airway raise and the fan dampers, leaving only 13.5% to ventilate the rest of the mine.
Later, in the survey, it was determined that the other issue detrimental to the system is the ‘mini’ booster fan installations that were installed at various production levels to boost the return airway. It should be noted that these booster installations perform two functions.
Firstly, they move the zero static pressure point further up the main return of the mine. In this case it is just below Level 33/1. Secondly, they create backpressure, which tries to push out of the return airway system back into the intake system. Later surveys by the mine confirmed this and the lower system is effectively recirculating. An example of one of these recirculation loops is shown in Figure 3.
As previously mentioned, the system is recirculating. In addition, there is insufficient ventilation of the lower workings to provide for sufficient dilution of heat and airborne pollutants. Figure 4 illustrates the severity of the problem, with airways in pink and purple exceeding 32.5 wet-bulb temperature.
The short-term improvement plan (STIP) aims to improve the efficiency of the existing system. Numerous significant changes to the system are required.
It is important to appreciate that the section that follows is not intended to be comprehensive, as it is difficult to show all changes.
Briefly, this required the operation to attend to the previously mentioned challenges at the primary fans. Such measures included the following:
n Repair the dampers in each fan drift.
n This alone should move the pressure point discussed lower than Level 33/1.
n Conduct a full engineering assessment of the surface fans and make any required remedial measures to allow fans to perform as per original OEM design.
As discussed previously, a significant amount of ventilation moves through the older workings. This poses
significant risk, not least of which is leakage possibly directly into the main return.
It was strongly recommended that the operation carry out the following:
n Systematically seal off each abandoned area on each level.
n Due regard should be given to ensure that access to the main return airway raise is accessible for the purposes of measurement and maintenance.
An example of the layouts supplied for each level can be seen in Figure 5.
In summary, the mine will now be supplied with 237.8 m³/s (up by 22.0 m³/s) at its upcast shaft. A total of 107.0 m³/s is provided to production commitments. A further 65.9 m³/s is provided to non-production commitments. Therefore, in total 172.9 m³/s is utilised by commitments. On this basis, the following system air utilisation is achieved: Total air utilisation = 72.7%.
Most importantly, however, is the fact that all ‘mini’ booster installations have been removed and that 32.0 m³/s now flows naturally to the lowest level. This resulted in a significant reduction in heat and pollutant build-up in the workings.
The medium-term improvement plan (MTIP) aimed, once again, to improve the efficiency of the existing system by making use of a booster fan installation in the middle region of the mine. These changes are significant from an improvement and cost perspective. It is important to appreciate that the section that follows is not intended to be comprehensive.
Firstly, a Ø5.0 m raise borehole needs to be established from Level 35/5 to Level 35. This will form the basis of a new return to the lower levels. This new raise bore will hole into the existing Ø2.0 m raise borehole.
Preliminary indications are that this raise will need to be reamed to Ø5.0m in any future expansion of the main return airway raise. Secondly, an additional airway connecting to the main return air raise needs to be mined. The size of this airway is at the operations discretion but should be able to accommodate the size of the proposed booster fans. Modelling suggested that 3 x Ø1600 315 kW dual stage – full blade booster fans and columns be installed. Two fans will be operational, while the third will be used as a spare (and possibly even operational in the life of mine).
These two fans combined should provide and upcast capacity at this location of ±175.0 m³/s. Preliminary indications are that with all three fans operational, these fans will deliver a combined upcast capacity of ±205.0 m³/s. Figure 6 shows the layout changes required in this area.
With installation of the booster fans complete, the amount of ventilation on Level 45/2 (lowest level) is anticipated to increase from 32.0 m³/s (in the STIP) to 60.0 m³/s. The balance is being used to ventilate other production levels. This is a substantial improvement, which allows for more heat and pollutant dilution at the lowest level.
In summary, the mine is now supplied with 269.0 m³/s (up by a further 31.2 m³/s) at its upcast shaft at an annual energy cost of US$2 628 307. This results in a ventilation unit cost of US$9771 per m³/s.
A total of 139.9 m³/s is provided to production commitments, whilst a further 61.8 m³/s is provided to non-production commitments. On this basis, a system air utilisation of 75% is achieved.
This article has described the short and medium-term improvement plans, as well as ventilation layouts and arrangements, that need to be put in place to ensure adequate ventilation is provided to all production sections of a mine. The outlined design ensures the mine remained adequately ventilated to create workplaces, which are safe and risk free to the health of employees.
A few of the highlights include:
n A 19% increase in total mine air utilisation.
n A 32m³/s increase in airflow on the lowest level of the workings, following phase 1 of the staged implementation plan. This will ultimately increase to 60m³/s following phase 2.
n A 6.2°C reduction in wet-bulb temperatures on the lowest level of the mine. This was realised without the addition of any mine cooling equipment.
n An 83% reduction in airborne pollutant contamination levels on the lowest level of the workings.
Robert Penczek, Federico Scolari, Dominik Dendl, and Dieter Glantschnegg, DSI Underground, EMEA, evaluates new opportunities in rock bolting based on pumpable resin and hollow bar.
The technical development of rock reinforcement constantly pursues increased operational safety and improved productivity to achieve a sustainable, economic excavation cycle. This article presents rock bolting solutions for challenging rock conditions based on a combination of innovative bonding resins and mining hollow bar rock bolts that
can be installed by a new generation of highly mechanised bolting rigs.
The traditional grouted rock bolt sequence fills the drilled hole with cement-based material or resin capsules before a solid bar rock bolt (pre-grout) is installed. Hollow bars and self-drilling anchors facilitate the injection of bonding grout after installation (post-grouting), with bonding materials flowing from the bottom to the surface.
Such a system allows the pumping adjusted volume of bonding material, compensating for geometrical irregularities of the drilled hole and filling voids created by cracks and joints in the rock. As soon as the bonding medium is visible, the hole is filled, and the rock bolt is embedded.
Post-grouted hollow bar/self-drilling anchors have been used in tunneling and geotechnical applications for decades, though always in combination with cement-based bonding materials. However, the manual solution was not particularly appealing for mining. It was only with the introduction of reliable and affordable thixotropic organo-silicate resins that it piqued the interest of innovators and major drill rig manufacturers began exploring how to mechanise this system. The organo-silicate resin is characterised by low viscosity to achieve high flow rates with relatively small pumps, making injection time fast and reliable. Gel and curing time are short and fully compatible with reducing the overall installation cycles. Unlike conventional rebar bolt and resin capsules, the self-drilling anchor installation sequence is simple: drill and inject. But even the hollow bar sequence is straightforward: drill, insert the bolt, inject ‒ and nut tightening is not strictly required either.
Thixotropic liquids show lower viscosity until shear forces are present in their flowing, though they rapidly increase viscosity in static conditions.
After mixing the two components, mineral bolt becomes a highly thixotropic liquid with pseudoplastic behavior, reaching high viscosity almost immediately after stopping its flow. During the flow, the resin fills nearby voids and cracks. Once the pump stops, however, it turns into a toothpaste-like texture, minimising spillage.
Local mining conditions, bolt geometry, resin flow, and installation procedures require an adequately balanced thixotropic effect (from strong to weak). Therefore, cooperation between all process stakeholders in the project’s initial phase is essential to arrive at an efficient, customised solution.
The Mineral Bolt, Silicate Injection Bolting Resins are specifically designed with the thixotropic behavior of the reacting mixture for mechanized bolting applications. Excellent corrosion protection. Environmentally safe when cured (inert system after reaction). Exceptional adhesive and mechanical properties. We reinforce progress – for our customers, and for the world.
Silicate resins develop bonding strength much faster than the usual cement grouts. Initial strength develops within minutes, and maximum mechanical strength is achieved in hours. The load/displacement curve shows excellent bond strength after five minutes, exceeding the strength of steel. The shape of the curve reflects the bolt’s steel properties, with no sign of failure or slippage in the bonding resin.
Many lab tests have shown mineral bolt performance to be much less sensitive to the bolt-to-borehole-diameter ratio and water presence, eliminating an existing problem when using resin capsules.
Self-drilling anchors and hollow bar bolts feature ‘R’-type threads (rope cross-section), which fit tunneling organo-mineral resins and develop a strong bonding effect.
Short encapsulation tests conducted in a lab and under actual mine conditions have shown that maximum tensile strength in the steel cross-section can be achieved at a bonded length of 30 – 50 cm, depending on the hollow bar type.
‘Setting time’, referring to the minimum time needed to retain the bolt in the hole, is easily controlled by adjusting the formula. For manual installation or long bolts, miners prefer a longer setting time measured in minutes. In contrast, it is essential to speed up the installation cycle for high-performance, fully mechanised bolting systems, so the mineral bolt has an adjustment time of just a few seconds. A modern bolting system equipped with a fast rock drill, a pumping time of 10 – 15 seconds, and a set time of 20 – 30 seconds, can install a 2.4 m bolt in less than four minutes (approximately 10 – 15 bolts per hour/rock drill installed).
The load-bearing capacity, displacement requirements, and energy absorption depend on rock type, depth, and stress field. Typical parameters are listed in Table 2.
The Norwegian University of Technology in Trondheim uses a proven method to
test the combined tensile and shear strength at a joint or concrete block and simulate joint displacement.
Comparing this system (hollow bar and mineral bolt) with more common solutions – in this case, a 20 mm bolt and polyester capsules – the results confirm the compatibility between the two systems, as shown in Table 3.
The risk of rock bursts and the presence of micro-seismicity have brought several mines to consider the utilisation of rock bolts that can absorb a sudden release of energy. DSI’s research and development activities focus on combining rock bolts and chemical bonding resins. The design is a dynamic R28 with two bonded sections and a de-bonded area in the middle. Furthermore, the bolt features different ductility from the other parts. This design demands a rigid bonding material able to withstand the high-peak loads created during a rock burst. Extensive testing in dynamic drop tester has proven that this combination can absorb large deformations (up to 200 mm in a 2.4 m hollow bar bolt) and withstand a busy load of 34 kJ.
Injectable organo-silicate resins, associated with hollow bars and self-drilling anchors, represent the next generation with:
n Much faster installation cycles.
• Surface deposits exploration and resource valuation
• Heap leach resource valuation and process enhancement
• Waste rock pile resource valuation
• Tailings resource valuation
• Gold placer deposit large diameter continuous sampling
• Geo-technical and environmental drilling
• Pre-collars for diamond drilling in tough overburden geology
n Easier installation procedure.
n Higher cycle repeatability.
n Better bolt encapsulation.
n Safer and more constant rock support.
n Better corrosion resistance.
New fully mechanised bolting rigs capable of capitalising hollow bar/self-drilling anchors and injectable resin have been available for a few years. They feature resin tanks for the two components, pumps, flow and pressure meters, static mixer cleaning systems, and fully computerised control systems. The results are promising, and some major mining companies are currently testing this new system.
During the development of a long tunnel, a mining operation encountered a problem in an area with a ground convergence of 5 cm/d. The ground consisted of coal deposits with straightened and heterogeneous sedimentary layers, making consolidation difficult. Traditional consolidation methods, such as
cement with anchors, could not be used due to the rapidity of the convergence, which meant that it would not set in time to stop it.
Weber Mining & Tunnelling was approached to find a quick and efficient solution. It decided that a pipe umbrella type system would be used, which consists of
self-drilling anchors (SDAs) that are injected with Marisil Thixo® resin after installation. This system allows very fast installation and tensioning, as the anchors themselves perform the drilling. In addition, Marisil Thixo resin is a specialised thixotropic resin for anchor injection, which transforms into a gel when injection starts, allowing the resin to stay in the borehole even when pumped vertically in the roof section and a rapid tensioning of the anchors.
The methodology employed consisted of using a pipe umbrella type system to SDAs with resin injections, which is a pre-support measure used in weak ground conditions in conventional and mechanised tunnels. Its function is to support and transmit the concentrated loads over the tunnel, reducing the major principal stress at the excavation face. The pipe umbrella type system is also known as the ‘canopy tube method’ or ‘long fore-poling’. In this case, the SDAs were installed on the outer perimeter of the excavation face at the front, parallel to the geometry to be excavated later, resulting in an umbrella or canopy support acting over the working area. The pipe umbrella type system with resin injection is suitable for highly disturbed ground, soft ground, ground prone to subsidence, urban tunnels, fault zones, sediments and slopes, frequent changes in ground conditions, and excavation of collapsed sections of tunnels.
The pipe umbrella type system consists of SDAs which are hollow bars that allow resin injection after installation. Once the SDA column is installed, pumpable resin is injected through the SDAs, filling the borehole from the back to the collar. The use of SDAs with Marisil Thixo reduces installation cycle times and increases load capacity.
There are two installation methods: pre-drilling and cased hole drilling. In the pre-drilling method, a borehole is drilled first and then the SDAs are inserted, which can induce large deformations and often requires time-consuming re-drilling. In contrast, self-drilling cased systems feature
immediate auger wall support, resulting in moderate deformations and stress relaxation. This soil-preserving installation method is preferred in weak soil conditions, which is why it was chosen in this particular application.
The pipe umbrella type system was installed segment by segment due to the limited length of the jumbo drill arm, so the SDAs were connected together during installation with an adapter. Both special machines and conventional drilling jumbos can install the SDAs.
Key advantages of the pipe umbrella type system with SDA anchors are maximum safety due to fully mechanised installation, the efficiency of the self-piercing installation technology, the speed of the SDA installation, the ability to install with conventional drilling machines, the implementation drilling with onsite personnel, reliable and robust system components, the installation of self-piercing in sections allowing flexible lengths, and the easy application in confined spaces.
In this particular application, the pipe umbrella type support system was implemented with an installation length of 8 m of SDA anchors. From a design perspective, the support measures can be divided into three different effects: the subdivision of the unsupported area, the radial support effect, and the longitudinal support effect. Their interactions result in the support of the working area and the excavation face. The loads in this critical section are transferred by each SDA in the longitudinal direction to its foundation: the soil before excavation and the already installed primary lining. Pipes are mainly loaded by bending, so the relevant design parameter is the maximum elastic moment of the system.
The pipe umbrella type system with SDA anchors involves several stages. First, the drill bit is assembled on the drill arm with the first SDA, the adapter, and the drill string. Then, the first SDA is installed, and the next drill string is connected with a self-drilling extension anchor to the previously installed anchor to continue the drilling process. This last step is repeated until the designed length of the pipe umbrella has been installed, followed by the removal of the drill adapter.
The injection system is then connected to the last SDA in the column, with the adapter assembled to the injection equipment (hoses and pump), and the resin is injected. This can be done until the resin reaches the plate or as soon as the pump pressure increases, followed by disconnection of the injection equipment from the SDA.
n Step 1: Installation of each pipe umbrella line.
n Step 2: Marisil Thixo resin injection.
n Step 3: After the first 5 m of advance, proceed with the second line of pipe umbrella.
n Step 4: Injection of the second line of pipe umbrella.
In addition to the pipe umbrella type system, fan-shaped self-drills were used as the traditional method with the same Marisil Thixo to ensure the radial bolting. In the same way as the pipe umbrella type system, each borehole was drilled with the self-drills and injected with Marisil Thixo for immediate tensioning. Due to the drilling template, all these pipes are intertwined, forming a matrix around the future excavation head.
In conclusion, the combination of the pipe umbrella type system, self-drilling anchors, and Marisil Thixo resin injection provided an effective and efficient solution for managing ground convergence in the tunnel development, showcasing its potential for similar applications in the future.
Michel Runser, Liebherr Mining, France, provides an overview of the R 9300 ‒ the company’s newest excavator ‒ that aims to provide a solution to the ever-increasing demand for greater efficiency and productivity in mining operations.
Mining companies are under increasing pressure to provide greater output while simultaneously reducing resource consumption, improving fuel efficiency, decreasing operating costs, and increasing onsite productivity. As such, all new equipment entering mines must contribute to these goals.
Liebherr Mining, a multi-national original equipment manufacturer (OEM), understands these challenges and has sought to provide a solution with the R 9300 – the latest hydraulic excavator in its portfolio. The R 9300 will replace the R 9250 in the 250 t class once it enters serial production. Instead of simply releasing an updated version of the R 9250, the OEM elected to create an entirely new machine.
The company had to start from scratch for the R 9300 because the technical base of the R 9250 could not be reused to design a machine in line with current expectations. Because a large number of existing, field-validated parts, components, and functions could be repurposed, the development period for the R 9300 was much shorter than usual. First discussions
about the R 9300 took place in 2018 and the project team finalised the specifications a year later. After three years of manufacturing and factory testing, the machine was introduced to the industry at the 2022 Bauma exhibition in Munich. The R 9300 is powered by a 1007 kW engine and is an efficient pass match for 100 t, 130 t, and 180 t mining trucks.
To provide an excavator that meets current fuel efficiency requirements, Liebherr Mining needed to develop and manufacture a machine optimised for fuel efficiency at all levels. This meant incorporating fuel efficiencies everywhere from the physical elements of the R 9300 to the technological innovations built into the machine.
Improving fuel efficiency at the componentry level involved designing the hydraulic circuit to reduce pressure losses within the hydraulic lines. This was achieved by minimising bends within the circuit and using hydraulic hoses with a larger diameter than those in the R 9250. Furthermore, the
amount of oil required by auxiliary systems – such as air-conditioning in the cab – was minimised to dedicate as much engine power as possible to the hydraulic pumps. The cooling component was also thoroughly reworked, ensuring the best possible heat exchange while reducing fan usage.
Technology also plays a significant role in the improved fuel efficiency of the R 9300. Liebherr Mining’s proprietary engine and hydraulic management system – Liebherr Power Efficiency (LPE) – helps increase fuel efficiency of Liebherr machines and comes as standard on the R 9300. The LPE system uses sensors and piloting signals to automatically adapt the engine and the hydraulics to different working phases, while also decreasing engine load profile.
Combined, these technology and hardware advancements have increased the fuel efficiency of the R 9300 by 25% compared to the R 9250.
Globally, industries reliant on fossil fuels are taking strides to reduce their carbon footprints. Although new solutions and approaches for becoming emissions-free are currently in advanced testing and validation phases – and more solutions will emerge from human inventiveness – companies must be able to cover the transition phase.
Liebherr Mining investigated ways the R 9300 could reduce costs per t, as reducing operational expenditure for mining operators is of the utmost importance. The two main avenues for this were parts commonality with the existing excavator portfolio and a significant reduction in fuel consumption.
Parts commonality with Liebherr’s existing excavator range was an important consideration while designing the R 9300 as when mining equipment can share spare parts with other machines in its fleet, machine maintenance and onsite inventory can be optimised, therefore helping to decrease costs.
The R 9300 and R 9200 share the same powertrain, only the engine in the R 9300 is slightly more powerful. Both the R 9300 and R 9600 share the same electronic platform dedicated to the integration of advanced technology products such Liebherr’s assistance systems and semi-automated digging functions. And the R 9300 and R 9250 share the same undercarriage components to help reduce the inventory required for customers with R 9250s in their fleets.
Fuel costs account for approximately one third of operational expenditure and so lowering the amount of fuel needed to run the R 9300 was important. The R 9300 consumes 15% less fuel than Liebherr’s previous generation of 250 t excavator thanks to the LPE system. This reduction in fuel consumption results in this machine achieving 25% better fuel efficiency than the R 9250.
Maintenance costs also represent a significant portion of operational costs. To decrease these for the R 9300, Liebherr Mining focused on component optimisation to simplify maintenance and repairs for technicians. In this latest excavator, the greasing tank was enlarged to achieve a minimum of 250 hours between refilling. In the event of component failure, Liebherr’s engineers designed a new hydraulic tank to make cleaning easier. Additionally, to allow for safer and more straightforward access to vital components, a 45° hydraulic staircase comes as standard with the R 9300. Liebherr has also ensured that all error codes –and several diagnostic dashboards – can be managed and viewed within the R 9300’s main screen to help streamline troubleshooting processes. To further simplify troubleshooting, signal panels have been installed at different points to monitor electrical signals and to make locating the source of a signal interruption much easier. The R 9300 also facilitates information sharing between the excavator and customers’ off-machine devices so staff can monitor the machine’s condition.
Liebherr Mining has a reputation for building productive excavators. In a climate where the mining industry is expected to extract more resources, more quickly, it is crucial that Liebherr defends its market position by delivering equipment
that provides consistent onsite productivity. When developing the R 9300, a range of methods were used to boost its productivity by 5% over the R 9250.
One of the methods for increasing productivity was to design a lighter and stronger attachment than that of the R 9250. The attachment has a new stick and boom design with serial implementation of high-performance components such as aluminium covers, cast steel elements, and hollow pins. All of these improvements reduce the weight of the attachment and therefore increase the attachment’s approved rated suspended load (ARSL). As a result, the R 9300 is able to lift a higher load than the R 9250. The lighter attachment also reduces cycle times because less force is needed to lift it, and therefore it is able to move more quickly.
A direct benefit of the increased ARSL is the ability to make the bucket size of the R 9300 bigger than the R 9250. The standard bucket sizes of 16.5 m3 in backhoe configuration and 16 m3 in face shovel configuration –at 1.8 t/m3 with heavy-duty wear package – make the excavator an effective pass match for trucks with 100 t, 130 t, and 180 t payloads.
The new attachment also includes inertial measurement units (IMUs) which help manage cylinder dampening while also providing vital information to Liebherr’s assistance systems, like the Truck Loading Assistant. The Truck Loading Assistant needs to know the attachment’s position in space. While different systems can be used for this, the IMUs was chosen because they bring additional benefits. For example, IMUs are a key component of future automation developments, as they can provide angle and acceleration signals that other systems cannot.
The updates to the lighting design of the new attachment also increase the number of lumens within the design by 60%, compared to R 9250. Liebherr Mining collaborated with key industry players to improve the lighting design of the attachment and enhance the safety of the R 9300 when it is operating during night shifts and bad weather.
Another way that Liebherr Mining improved the onsite performance of the R 9300 was to increase its service life by 33% ‒ one of the initial targets of this project. Machine life is directly linked to the engine life. Today, modern engines consistently achieve 18 000 – 20 000 hours in operation before requiring overhaul. Therefore, increasing the service life of the whole R 9300 from 45 000 to 60 000 hours allows the engine service life to better align with the lifespan of the machine. Not only did the service life of the R 9300 increase, but the periods between components needing to be replaced also expanded.
Given the wide range of design improvements
Liebherr Mining included within the R 9300 to increase its performance above the R 9250, the OEM is excited to see how efficient and productive the excavator can be once in the field. The R 9300 is now available for purchase and will enter serial production in 2024. The backhoe configuration will become available in 1Q24, with the face shovel configuration available in 2Q24.
Stantec can help you use limited resources like water and energy efficiently. Your net zero challenge may not be straightforward, but our solution can be.
stantec.com/net-zero-mining
The price of uranium is expected to rise ‘significantly higher’ than current levels due to a myriad of reasons, including rising demand for clean energy and the need to secure local energy supplies due to ever-evolving geopolitical tensions.1 This puts Thor Energy in the perfect position to aid the shift to a green energy economy and help re-draw global supply routes, as the company focuses on uranium in the US and energy metals in Australia.
The global energy market has reached an inflection point, where the urgent need for cleaner power sources is finally being recognised. To meet the conditions of the 2015 Paris Agreement, carbon dioxide emissions from electricity generation must be close to non-existent by 2050. To achieve this, whilst simultaneously increasing electricity
Nicole Galloway Warland, Thor Energy Plc, Australia, explores the current challenges facing nuclear fuel supply, and how the complex combination of supply and demand factors means that uranium miners operating in friendly jurisdictions are certain to benefit.
demand by expanding its use in heating, transportation and industrial use, a complete overhaul of the current energy infrastructure will be needed.
Although nuclear power is not considered renewable energy, it is considered by the EU, amongst others, as ‘green’ in lieu of its ability to generate a huge amount of power whilst emitting limited greenhouse gases. Nuclear is therefore considered a key climate change solution. It has been widely recognised as having the highest capacity factor of any other energy source, as it produces maximum power for more than 92% of the year.2
It also has a minimal carbon footprint of roughly 15 – 50 g of CO2 per KWh, compared to the 450 CO2/KWh for a gas-powered generator, and 1050 CO2/KWh for coal.3
As the recognition of the benefits of nuclear power has increased, the supply side has struggled to keep up. De-weaponised stockpiles have been largely depleted, and uranium mining has not met reactor demand since the end of the Cold War. As there is an increase in nuclear reactors being authorised by national governments to be constructed globally, the limited supply of uranium is becoming a pressing issue. As nuclear power starts to generate a larger supply of the world’s energy, mining companies that are highly leveraged to uranium are poised to benefit.
This has led many countries to actively encourage uranium mining exploration, with the US achieving this through its Inflation Reduction Act. The Inflation Reduction Act proposes investments in energy technologies, including: hydrogen, renewables, and nuclear. A major benefit of the legislation is the provision of tax credits for the production of zero-emission nuclear power. The Act, through tax incentives and investments, guarantees a long-term commitment to nuclear energy by the US (and hence the domestic supply of uranium), as the country transitions to net zero emissions.
Thor Energy will directly benefit from these incentives and investments through the increased funding dedicated to upskilling the clean energy workforce. One example of the initiatives is the Clean Energy Innovator Fellowship Programme, which matches new energy professionals and recent graduates to organisations to help advance clean energy solutions.
With global demand for uranium heavily outweighing supply, the problem becomes exacerbated further when looking at the geopolitical tensions across supply chains. There is an over-reliance on limited supply, with some of the top producers being Kazakhstan, Canada, Australia, Namibia, and Russia. These countries account for 70% of the world’s uranium production, leaving it extremely vulnerable to supply chain issues.4
With the media predominantly focused on the global reliance on Russia’s gas, oil and coal, the Russian invasion of Ukraine has also shown us how exposed and vulnerable the current global uranium supply chain is.
For example, in 2021, The US Energy Information Administration examined how the US imports almost all of its uranium supply, with over 14% of it coming from Russia. Additionally, 35% of US imports rely on Kazakhstan, and, as it is landlocked, thus depends on supply routes through Russia to ship uranium to Europe and then back to the US.5 If sanctions are imposed on Rosatom, Russia’s civilian nuclear firm, it could cut off exports of uranium to the US’ nuclear industries.
In mid-February 2023, the probability of a ban on Russia’s uranium supply “drastically increased” following discussions in the European Parliament and US Congress.1 Therefore, the global dependency on a limited number of
The celebrated Iron Ore Conference returns to Perth in 2023. Welcoming geologists, engineers, metallurgists, mining leaders and executives from across the globe to address the challenges impacting the technical and management aspects of the iron ore industry.
The 2023 conference program will align to the conference theme ‘transitioning to a green future’. Reviewing the solutions required to address the carbon footprint of iron and steel mining. Presentations across the three days will focus on genesis, geology, exploration, mining and processing of iron ores.
Save $100 off your conference registration with code FeSAVE100PP Register at: ausimm.com/iron-ore
Hear brilliant keynote presentations
8 industry luminaries to present
Access a superior technical program showcasing global excellence
Experience an immersive trade exhibition
Showcasing the latest technologies and innovations
Build your professional network at the conference networking functions
countries’ nuclear fuel-production capacity must be re-evaluated, and it is essential that alternative supply chains are found to guarantee countries’ energy security.
The US is the world’s largest consumer of uranium, accounting for 28% of global demand. This is due to their desire for a secure energy supply. However, the US is currently over-reliant on uranium imports, with domestic uranium production levels falling short of this demand.
Thor Energy is one of the companies helping to shift the balance of these global supply chains, aiming to bring more uranium supply and production to the US. The focus on its uranium and energy metals even led it to change its name from Thor Mining Plc to Thor Energy Plc earlier this year.
With the move to regionally and nationally secure supply chains in the nuclear and battery metals industries,
Thor Energy is well placed to leverage off its North American and Australian portfolios.
Whilst also having exposure to uranium, nickel, copper, lithium and gold projects in Australia, Thor Energy holds a 100% interest in three uranium-vanadium projects in the highly prospective Uravan Mineral Belt on the border of Utah and Colorado in the US.
The Wedding Bell Project and the Radium Mountain Project are both in Colorado and comprise of 199 mineral claims over areas of historical high-grade uranium and vanadium production. The Vanadium King Project in south-east Utah comprises of 100 mineral claims, approximately 4 km north of the town of Moab.
Since acquiring the projects in 2020, Thor Energy has completed thorough geological reviews of the claims. It secured high-grade sampling of up to 1.25% U3O8 and vanadium up to 3.4% V2O5. Initial drilling confirmed uranium mineralisation at shallow depth and preparation for the next phase of drilling is underway.
At the Wedding Bell and Radium Mountain uranium projects in the US, the intersection of uranium-bearing, reduced sandstones at the greenfields Section 23 prospect means exciting times ahead, as do the lateral continuity of high-grades along strike of historic workings at both the Rim Rock and Groundhog prospects.
As well as these promising geological results, the proximity of Thor Energy’s projects also means it is well placed to benefit from the US’ transition to a domestic nuclear energy supply. Located approximately 100 km from the Wedding Bell Project in Blanding, Utah, is the White Mesa Mill. Operated by Energy Fuels Inc., the White Mesa Mill is the only fully licensed and conventional uranium processing plant in the US.
It is reported to be the largest producer of uranium in the US and has historically accepted toll milling agreements, as well as purchase programmes for processing ores from third-party mines.
The US still has a long way to go to scale its capacity to produce enough enriched uranium, and to decrease its reliance on uranium imports. However, there is much to be optimistic about in light of discussions in the community, as well as at the top levels of government about the importance of domestic uranium mining and production. It is imperative to prioritise projects that will help achieve energy security, aid the green energy transition, and reduce the US’ exposure to the global nuclear fuel supply chain. References Available upon
Chris Evans, Winsome Resources, Australia, reviews how James Bay has attracted global attention as an emerging lithium province.
The James Bay region in Quebec has a long history of mining, dating back to the early 1900s when copper and gold were first discovered in the area. By the 1950s, several gold mines were in operation, and the region experienced a copper mining boom in the 1960s and 1970s. Large-scale hydroelectric projects in the 1950s supported mining operations, leading to the development of major
projects like the Raglan nickel mine, which is still in operation today.
Fast forward half a century and the region is now riding high on the global lithium boom, attracting new explorers and investors to this historical mining area. Lithium is a critical component in the production of batteries used for electric vehicles and renewable energy storage, and with
the global transition to a low-carbon economy underway, demand for lithium is expected to surge in coming years. The James Bay region is attracting particular attention from exploration and development companies as it hosts one of the largest and most prospective pegmatite provinces in the world.
The lithium exploration rush in the region began with Nemaska Lithium’s 2009 discovery of the Whabouchi deposit, roughly 800 km north of Quebec City. Whabouchi is widely considered one of North America’s richest hard rock lithium deposits, containing proven and probable reserves of 36.7 million t, with an average grade of 1.3% Li2O.
Its discovery lit the fuse for the current boom that has seen global resource companies set up shop in James Bay, with Australian resource companies leading the charge and staking claims over much of the prospective pegmatite zones.
One such company is Winsome Resources, which was in the first wave of ASX listed explorers to enter the region. The company continues to advance its aggressive drilling and exploration programme, as it undertakes one of the fastest pathways to a maiden resource. Holding more than 850 km2 of highly prospective tenements, Winsome will continue to undertake extensive drilling throughout 2023, currently operating with four drill-rigs onsite, albeit having some operational pauses through June due to wild fires affecting Quebec.
So, why are Australian listed companies packing up their pickaxes and looking towards North America in search of lithium riches? A lot of the prime pegmatite regions in Australia have already been staked and claimed, and even if you are able to secure a prospective tenement, the cost of acquiring and then exploring these remote areas, combined with Australia’s tight labour market, make Canada a much more attractive option for a company of Winsome’s size.
The maturity of the US and Canadian mining sector, political stability, and low sovereign risk are also key factors contributing to ASX-listed juniors finding a comfortable second home in North America.
Local governments are supportive, offering attractive tax rebates and funding incentives, while one of the most exciting benefits is access to Quebec’s world class hydro-power energy supply – which generates more than 90% of Quebec’s electricity.
Winsome holds a world-class exploration portfolio in the James Bay region, which includes a 100% interest in the Cancet, Adina, Sirmac-Clappier, and Tilly projects. The Adina and Cancet projects are the most advanced in Winsome’s portfolio, with the company carrying out aggressive exploration campaigns in tandem across both properties targeting already identified lithium bearing pegmatites. Indeed, the activities at Adina and Cancet have yielded promising results, further cementing belief in the potential of these projects to contribute significantly to the global lithium supply. Adina covers 79 claims, approximately 300 km north-east of Nemaska’s Whabouchi project, and drilling to-date has delivered some impressive results; including 1.34% Li2O over 107.6 m from 2.3 m to 109.9 m, and as high as 1.92% Li2O over 30 m. Recent assays from the east of the project area confirmed high-grade lithium mineralisation some 1.9 km east of the main zone, bringing the total strike length of the lithium mineralised trend at Adina to over 3 km. What is exciting is that mineralisation at Adina remains open to both the east and west of reported intercepts to date, highlighting the significant upside potential at the project. The assay results Winsome has received to date have confirmed the impressive tenor and thickness of the lithium mineralisation at Adina, placing the project in a good position for development to supply future North American lithium demand. The company is now aggressively drilling towards a maiden resource at Adina later in 2023.
Cancet lies 150 km to the west of the Adina project area, covering 395 claims, and Winsome is carrying out a similar
aggressive exploration campaign to that taking place at Adina. Metallurgical test work results show a very high recovery at a course crush size using dense media separation (DMS) is achievable at Cancet. Recent drilling at Cancet has been focused on additional targets to the west and east of prior drill campaigns with the potential to significantly increase lithium tonnage. Winsome is a bit more advanced in its exploration at Adina compared to Cancet, but exploration work carried out to date has provided the company with further confidence in the quality of the lithium portfolio it has assembled.
Positive results from drilling at Adina and Cancet led Winsome to expand its acreage position in the area, acquiring the Tilly project in April this year, which lies just 20 km south-east of the Adina Project and comprises 91 claims covering 47 km2. It also signed an option agreement in June to acquire the Jackpot Property, which sits adjacent to Adina and, if exercised, would increase the company's Adina project area by 50%.
The company takes a methodical approach when assessing new project acquisitions, adhering to a rigorous evaluation process to assess whether such projects would further bolster the development of its flagship assets. Tilly met these criteria, given its close proximity and similar geological setting to Adina – meaning initial work programmes can be integrated into what plans there are for Adina in the next field season. In the longer term, any discoveries made at Tilly could then be incorporated into the development plans for Adina and Cancet.
With the company set to deliver its maiden resource estimates this year for Adina, Winsome will soon turn attention to developing a mining plan and completing a preliminary economic analysis (PEA) to determine the economic viability of the projects. While there is still work to be done before Winsome gets to this stage, there is a lot of internal confidence about the potential of the region to host world-class lithium developments and the opportunities that lie ahead.
In the meantime, Winsome is focused on building relationships with local communities and stakeholders to ensure its mining operations are conducted in a socially and environmentally responsible manner. The company believes responsible mining practices are not just a nice-to-have, but a necessity. Winsome’s ESG strategy reflects its commitment to minimising its environmental impact and ensuring its operations benefit all stakeholders; from local communities to company shareholders. For example, all stages of the project lifecycle are being approached with a focus on keeping emissions to a minimum, utilising Quebec’s hydro-power network, and targeting the use of benign reagents for any future ore processing across the company’s project portfolio.
ESG was front of mind when Winsome first began building its lithium portfolio, and another of the reasons it was drawn towards Quebec’s James Bay region. Indeed, Quebec has one of the most advanced renewable energy
offerings in the world, generating more than 90% of electricity via hydropower. This presented a significant opportunity for Winsome to align itself with sustainable development practices and meet the increasing demand for ESG-conscious mining practices.
Winsome is also conscious of its social licence to operate and has established positive relationships with the Quebec Government and First Nations Cree people, traditional owners of the lands on which it operates. It is extremely important to the company to build long-term, trusting relationships with the traditional landowners and ensure mutual benefit for not only itself and its shareholders, but the local community. The company has made a commitment to understand and protect local heritage, as well as identify and offer opportunities to local people to work with and alongside Winsome as its operations continue to grow.
With global lithium supply struggling to keep up with demand, Winsome is well placed to capitalise on growing demand as it progresses its projects towards development. Lithium is truly the metal of the future. As the world shifts towards renewable energy and electric vehicles, there will be a surge in demand for lithium, making the exploration and development of lithium resources in regions like James Bay increasingly vital.
Though mining operations may typically be concerned with drilling underground or excavations of the Earth’s surface, mine owners, engineers, and operators should also be making greater use of both space-based and terrestrial technology to reduce their geo-environmental risks.
Modern Earth observation (EO) satellites that are fitted with powerful remote sensing radars can now deliver data and imagery at a volume, granularity, and accuracy that was previously unheard of in the mining industry only a couple of years ago. Such analysis complements ground-based, geotechnical sensors that monitor a variety of surface and subsurface environmental variables for potential failures of tailings facilities, mine pit walls and water dams, among others.
Despite the availability of this kind of technology for some years, it is not yet being used more widely or effectively. The tragic 2019 Brumadinho dam disaster in Brazil highlighted to the world the importance of accurate monitoring of mine sites, specifically tailings and slurry management. One outcome of the Brumadinho disaster was the publication of a new Global Industry Standard for Tailings Management, which, although not mandatory, does provide mine owners and operators a detailed framework for adopting the best practices for tailings design, monitoring, and management.
So how does a mine site begin to adopt modern practices and implement a monitoring operation that can keep it, its workers, and local communities safe? It starts with effective and efficient data gathering and analysis. Data collected at the mine and tailings sites can, for example, give information about the cause of a flood, or provide advance warning of a flood if the right data is handled effectively. With the increase of digitisation in all aspects of mining operations, including the adoption of cloud technologies, a major challenge with the increase of data is to effectively turn data into actionable information and insights.
To maximise the benefit of data collection, consolidation and comprehensive analysis of all sensor data and other monitoring data sources is essential. The mining industry can benefit from time-series, continuous data that employs machine learning (ML) and artificial intelligence (AI) algorithms. This would allow civil engineers to optimise
Keizo Fujiwara and Takayuki Odawara, Synspective, Japan, and Alastair Bovim, Insight Terra, UK, details how satellite monitoring can improve mine safety and inform operations with data-driven analytics.
their processes and focus their energies on other valuable areas of work.
There are various methods for monitoring mines, such as geotechnical instrumentation, drones, aircraft, and satellites. However, as mines are often remotely located, ground and aerial monitoring are generally expensive, and it is often hard to pinpoint exactly where to place sensors. On the other hand, EO satellites have unique capabilities for collecting accurate and consistent imagery data as they pass over the Earth’s surface and offer a convenient and readily available monitoring option that does not require a costly terrestrial set-up. Moreover, satellite data, which enables more stable monitoring of a wide area, has a high affinity with the aforementioned ground and aerial data, and combining multiple wide-area, high-frequency, and high-precision data can be expected to bring new insights for mine management.
To understand how this data can be most effectively utilised, the role of EO satellites should first be considered.
Low Earth orbit (LEO) satellites – the type used for Earth observation – orbit at altitudes between 160 and 2000 km above the Earth and provide full coverage of the planet’s surface, meaning remoteness is not a barrier.
Earth observation falls into several categories, the two most well-known of which are optical and synthetic aperture radar (SAR). Optical satellites use cameras operating in the visible part of the electromagnetic spectrum and capture images for apps like Google Earth. However, cloud cover and low or no visibility at night restrict their effectiveness.
SAR satellites overcome the hurdle of cloud cover and low visibility at night by detecting reflections from the ground. They achieve this by emitting radio waves of wavelengths that penetrate clouds and other atmospheric conditions. SAR satellites can monitor ground activity 24/7 – penetrating through rain, cloud, and smoke cover –allowing them to acquire data in any weather, and at any time of day or night.
Conventional land-based ground deformation monitoring techniques that use automated electronic theodolites and distance meters have been around for a long time. While they are highly precise, they have relatively high implementation costs and, more significantly, provide limited area coverage. SAR satellite technologies provide comprehensive monitoring coverage over a wide area at
millimeter levels of accuracy and at lower cost. SAR is also advantageous in assessing mining areas and tailing dams that have been abandoned, providing the only economical and practical method of evaluating these sites to guide and prioritise subsequent onsite assessments.
Accessibility issues, due to geography or safety, can lead to land displacement remaining unmonitored and increased risks of physical asset damage. To overcome this challenge, SAR satellites constellation can be used to regularly monitor and survey large inaccessible areas, with frequent revisit rates at high resolution.
In addition to satellite-based Earth observation, geotechnical sensors that monitor mines and their tailings facilities provide a complementary and essential additional component of geo-environmental risk reduction for mine operators. Correlating this data with the data collected by SAR satellites can provide operators with vital information to support data-driven decisions and thus improve the safety of operations at their mining sites. This is achieved by providing key data and actionable insight into the critical controls used to manage a mine’s operations and infrastructure.
The use of cloud-based, near real-time data processing platforms that curate, consolidate, and analyse data from a myriad of sources make it possible to carry out much more effective risk management than has traditionally been possible. By digitising the data processing and offering high-frequency, high-confidence data every few hours, better accuracy and greater insight can be achieved. Having ownership of the data once it is received – as well as the ability to analyse developing trends and micro-trends in the curated data, in addition to past incidents – a civil engineer at the mine can use the platform to continuously improve its operations, enhance mine safety, and preserve the integrity of the monitored infrastructure.
In the context of an integrated satellite and terrestrial monitoring solution, it is important to understand the critical contribution of ground-based, geotechnical monitoring to the overall risk-based management of a mine and its tailings facilities. SAR satellite data provides insight of land displacement and ground deformation that has occurred, while near real-time curation and analysis of data provides insight into why the displacement occurred, and even provides early warning of possible future land displacement or deformation. This is why the combination of these two techniques is so powerful.
The rapidly accelerating demand for critical minerals to support the global decarbonisation agenda translates directly into wider and more intense mining activity. Achieving zero harm to the environment and communities affected by mining requires a significant improvement in monitoring critical operational controls, especially those related to tailings dams.
Tailings dams are some of the largest and most complex civil engineering structures on Earth, and also represent the most significant existential threat to a mine’s continued safe and profitable operation. The integration of high-frequency SAR satellite observation and near real-time data, delivered to a single cloud-based platform, provides the most comprehensive enterprise solution to this critical requirement.
The global mining industry has long been a critical supplier for nearly every industry. The recent emergence of scaled electric vehicle production and other expansive electrification projects have become critical drivers of mushrooming new demand for critical minerals for battery production, notably lithium, cobalt, nickel, and manganese, among others. And yet continued high organic growth in semiconductors, military, aerospace, and communications equipment is further adding to the growing demand for these materials.
We are living through a historic opportunity for expanded production, compounded by geopolitical pressure toward increasingly democratic geopolitical production regions. However, in the public eye, the mining industry finds itself at a crossroads, with increasing opposition from growing reputational challenges just as these new demands drive expanded operations into new communities. Even beyond standard-issue industry opposition found throughout cities and suburbs around the globe, multiple high-profile mining incidents over the past few years – including the highly publicised destruction of Aboriginal caves in Western Australia, water misuse in Chile, and multiple tailings dam failures – have undermined mining's social license to operate in many locales and materially eroded public trust. As entering new communities becomes a looming necessity on multiple fronts, it begs the question: how does the mining industry restore public goodwill?
One powerful solution lies in the embrace of new technology, with newly available access to satellite imagery – and space-based hyperspectral data and analytics in particular – being especially well-timed to accomplish the task.
A chronic community trust deficiency has arisen from steadily growing perceptions from decades of broken promises, including failed commitments to leave sites better than their original conditions, undelivered financial benefits to communities assured of profit-sharing, and community resource depletion such as overuse of local aquifers. Beyond more traditional public concerns about environmental and financial damage, new expectations are arising for mining operators to mitigate climate impact worries. In order to overcome these concerns and meet expectations, operators can today embrace technology capable of preventing missteps and facilitating better communication.
That is where satellite technology comes in: new access to persistent, customised satellite monitoring and analytics offers mining operators a cost-effective mechanism to expand and monitor current assets. This provides operators access to advanced monitoring for their own benefit, enabling regulatory compliance, enhanced operational
efficiency, and better-informed communities on how projects are being stewarded and promises are being kept.
Satellite monitoring and analytics give mining operators a powerful tool to establish trust within communities, including a capability to deliver objective evidence of their environmentally responsible mine operations, closures, and site rehabilitation achievements. Sharing such information in a coordinated manner with targeted interest groups offers operators an avenue to foster an environment of trust and transparency across the entire process. Establishing a sense of confidence that regulations and promises are being met has never been more essential to gaining support from community leaders.
There are several satellite-monitoring technologies that may be considered, with hyperspectral imagery being especially well-suited for the solution of monitoring the lifecycle health of mining operations. Space-based hyperspectral imaging is not new and has been used by the US government for many years. However, it is just now becoming commercially available, notably with Orbital Sidekick’s deployment of a constellation of six commercially-focused hyperspectral sensors this year, three of which have begun operations already.
First developed for satellite usage in the 1970s by NASA’s Jet Propulsion Laboratory, hyperspectral sensors are able to capture hundreds of colour bands, rather than only the three primary colours detected by the human eye, and across a wider range of the spectrum than visible light. In practice, hyperspectral imaging enables operators to depict chemical fingerprints at the surface of the earth, identifying objects, minerals and vegetation, based on their molecular makeup. Significantly, the technology can locate critical features and phenomena undetectable to the human eye or traditional monitoring methods, such as oil spills and methane emissions, even including some that occur below the surface.
Falling satellite production costs combined with increased ease of third-party space launches have led to a growing number of companies offering satellite-based imaging for new commercial applications. For example, space-based hyperspectral imaging has already proven extremely valuable in the energy sector, where Fortune 500 companies are proactively embracing the solution to monitor pipelines and reduce methane emissions. The technology translates to nearly all industries, and the mining sector is no exception.
Across the lifecycle of a mining project, hyperspectral insights are uniquely positioned to help operators ensure they are conducting mining operations safely and sustainably. Beyond the obvious health and environmental benefits, this is
Peter Weaver, Orbital Sidekick, USA, examines how trust in the mining industry can be restored by utilising satellites to employ hyperspectral intelligence.
absolutely crucial to regaining public trust and a social license to operate. Unsafe operations and well-known environmental disasters by some in the industry are largely behind mining’s image problem and so employing technology that addresses this is a crucial step. As previously mentioned, operators can then go even a step further and share this information with the local community and its leaders to foster a relationship built on transparency and trust, if they choose to do so.
Take deforestation, which may correspond with new mining operations. Space-based hyperspectral imagery and analytics provides operators a tool for improved tracking and data. This can help better assess the impacted acreage and provide an avenue for better community reporting, as well as help establish accurate and effective goals for creating offsets.
Acid mine drainage is another example. This drainage is a leading cause of contamination and can severely impact fish, animals, vegetation, and human drinking water – as seen at the Zortman Landusky mine in Montana. Despite the significant damage caused, acid drainage is not detected for two to five years in most cases, and sometimes not at all. This is an area where space-based hyperspectral monitoring can play a key role given that it can chemically fingerprint materials. In a situation with acid mine drainage, hyperspectral imaging can identify water pollution via changes in water composition, while also monitoring the surrounding vegetation for responses that occur when exposed to pollutants. Through this in-depth analysis, operators can be alerted in near real-time, helping spark immediate action and preventing years’ worth of damage to local communities.
In addition to the environmental harm caused by prolonged leaks, surrounding communities have historically not been provided sufficient information on the risks present and the damage done. With space-based hyperspectral monitoring, an opportunity for better transparency and community communication is also presented, if operators so choose.
In June 2023, Mike Werner, Google’s Head of Circular Economy, observed that it takes “an average of 17 years to develop a new copper mine, suggesting that humanity is already far behind in making the investments required to ramp up virgin production”, and this long lead time is consistent across all critical metals. And yet, communities still do not want these projects for the reasons discussed. A path forward largely boils down to re-establishing trust and social license to operate in communities across the globe. Leveraging satellite technology to improve mining operations and open the door for transparent communication provides one powerful avenue to accomplish this.
With hyperspectral offerings now available commercially, and community trust and social license to operate growing ever more important as expansion looms, the time for mining leaders to explore, experiment with, and most importantly adopt this new technology is now. Space-based hyperspectral imaging is quickly emerging as a top solution for mining, and more and more companies in the industry will soon begin adopting the technology as a critical tool for moving their organisations forward.
JENNMAR designs and manufactures a wide range of dependable ground control products, from bolts and beams to channels and trusses, resin, rebar, and more. We’re proud to make products that make the mining, tunneling, civil, and construction industries safer and more efficient.
Because we understand the ever-changing and demanding conditions above and below ground we have built the richest portfolio of diverse and complementary brands. JENNMAR sets the bar in every industry we serve and as we continue to grow, our focus will always be on the customer.
We feel it is essential to develop a close working relationship with every customer so we can understand their unique challenges and ensure superior customer service. Our commitment to the customer is guided by three words: SAFETY, SERVICE, and INNOVATION . It’s these words that form the foundation of our business. It’s who we are.
It’s a big milestone for a piece of rubber. But Linatex ® is so much more than that. It’s unlike anything else, using a unique 95% natural latex formula that has made Linatex ® the strongest rubber in mining for the last century – exactly as nature intended. So, here’s to 100 Years Strong, and the next 100 to come.
Learn more at linatex100.weir