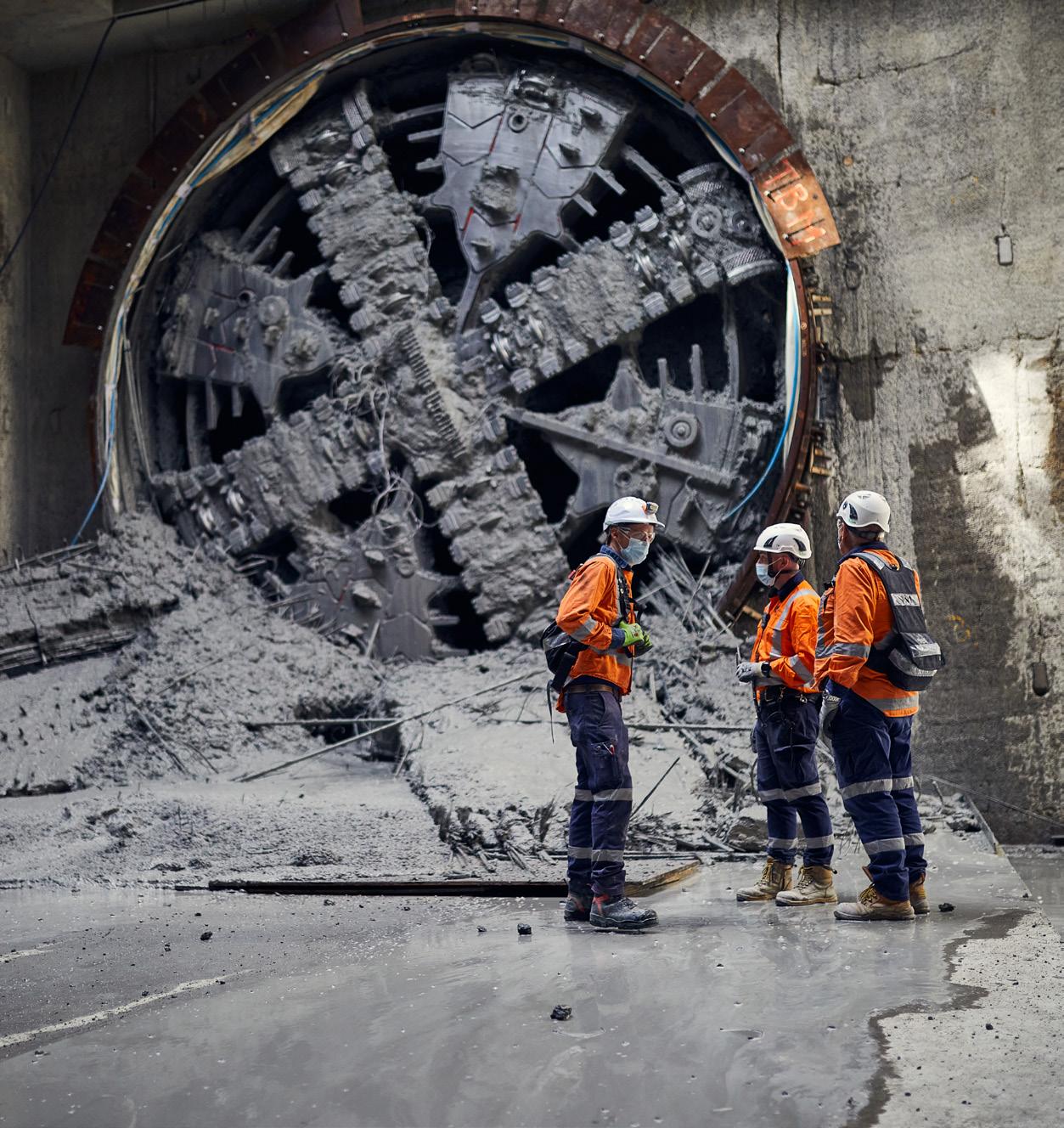
3 minute read
FROM OUR BUILDINGS YOU CAN SEE THE FUTURE.
from Link Alliance
Sustainability
Security
Fire & Life Safety
Building Management Systems
OT Cyber Security Services
Honeywell Building Technologies is transforming the way every building operates to help improve the quality of life. Our software, products and services are in more than 10 million buildings worldwide.
We provide connected building solutions that integrate comfort, security, safety and energy efficiency with easy-to-use dashboards that help turn building data into insights to drive results. We’re an industry leader in fire and life safety systems that improve responses to critical situations, and our integrated security systems provide access control, intrusion detection and video management to keep people safer.
For more information, please visit buildings.honeywell.com
APAC OUTLOOK:
CRL will double the number of people within 30 minutes of central Auckland – New Zealand’s biggest employment hub. When fully operational, 54,000 passengers an hour will use CRL stations at peak times. More than 2,000 people are building CRL; according to Dudouit, this project innovation and complexity is upskilling a workforce to benefit future generations, and an alliance delivery model was selected with due consideration to the size of the project, its complexity, and the risks.
“Delivery of the heavy civil works started mid-2019 and has progressed well in a COVID-19 environment with the project now transitioning to delivery of the architectural and system works,” he reveals.
Carving A Path
Large-scale tunnelling is a core operation within the project. The parallel tunnels MC30 and MC20, each with a drilled length of 1.6km, are located in the geological area called East Coast Bays Formation (ECBF). In the past, several tunnels had been dug with a tunnel boring machine (TBM) in the ECBF: Orakei Main Sewer, Rosedale Outfall and Waterview Connection. Based on this experience, an earth pressure balance (EPB) TBM supplied by German tunnelling machine manufacturer Herrenknecht AG was selected with a drilling diameter of 7.15m, a maximum pressure (Pm) of four bar, a cutting wheel equipped with ‘rippers’ and cutters for hard layers, and an opening percentage of 44 percent to overcome possible clogging.
FRANCOIS DUDOUIT, PROJECT DIRECTOR:
“After finishing my engineering studies, in 1986 I started to work on on a tunnel project as part of the Atlantic High-Speed line between Paris and Bordeaux in France. It was my first involvement on a major infrastructure project, and it was very exciting.
“I then started to work internationally in 1990. Since then, I have worked continuously abroad and gained experience on major and challenging infrastructure projects in Denmark, Hong Kong, the Netherlands and Sweden before arriving in New Zealand about five years ago. The great majority of the projects in which I was involved were underground and part of railway infrastructures for metro lines, ‘conventional’ passenger or freight lines or high-speed lines.”
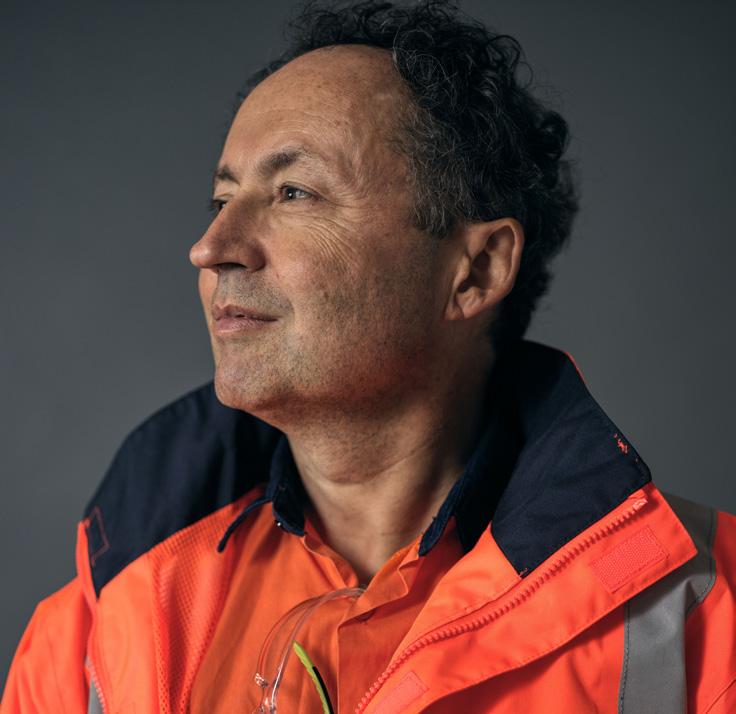
Spoil, the soil and rock excavated when tunnelling begins, was transported out of the TBM via a conveyor belt with a capacity of 600 tons-per-hour (Tph) and transport within the tunnel was mainly undertaken by electric vehicles (EVs).
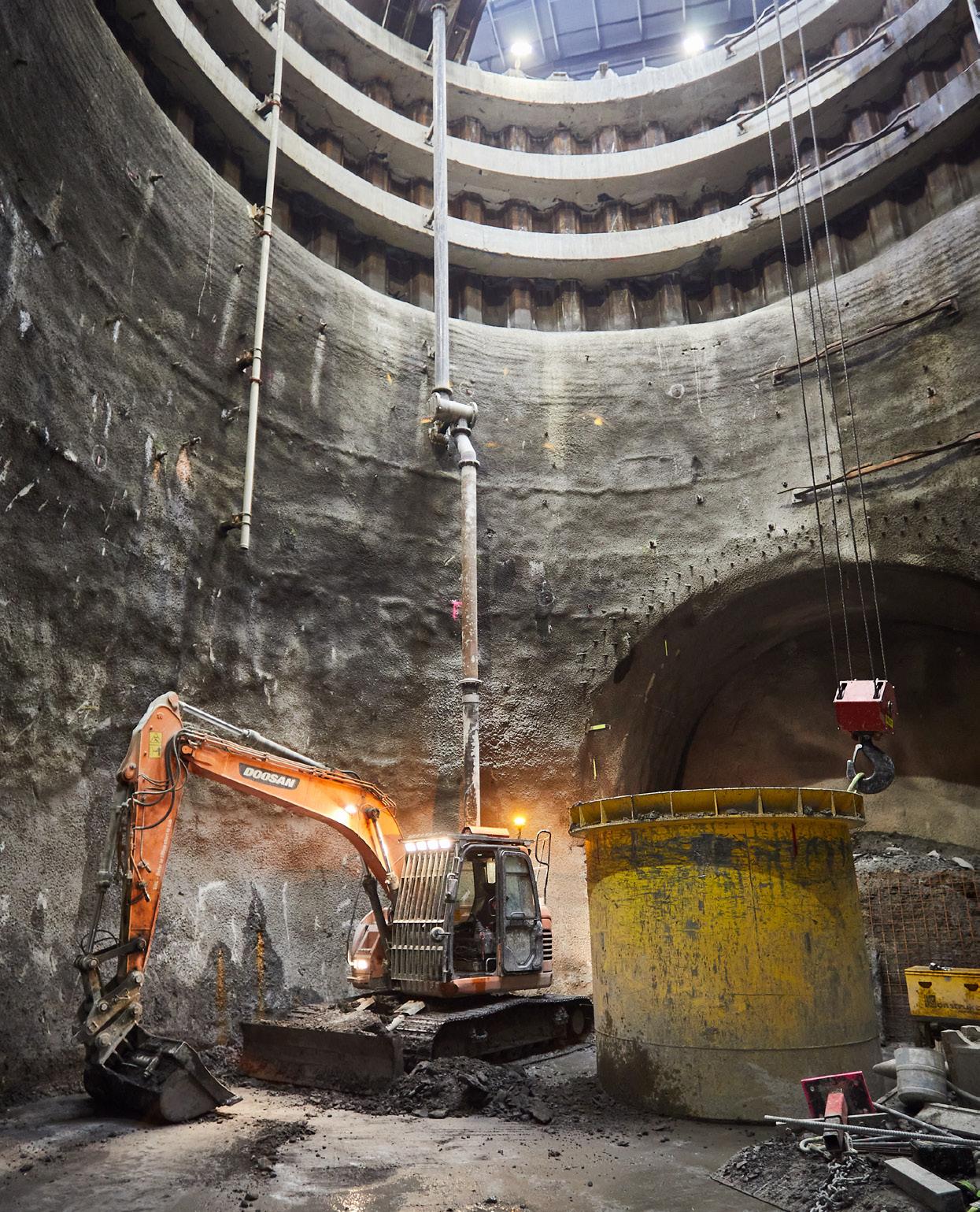
“The tunnel lining consists of precast rings, each 30 centimetres (cm) thick and reinforced with steel fibres, with the exception of special areas where reinforced cages were used,” Dudouit elaborates. “There were multiple primary technical challenges when it came to the bored tunnels.
“The first of these was tunnelling on a downward slope of 3.5 percent, and an alignment with a very tight radius (140m), even when starting the TBM. The TBM and tunnel equipment and the tunnel lining had to be designed specifically for such a small radius.”
A passage was also undertaken beneath the most important motorway junction in the city of Auckland (a 200m wide corridor with 11 lanes of traffic). In this area, the TBM
CRL – A GREENER RAIL NETWORK
Beyond significant technical and engineering challenges and the innovations required to deliver such a project, Link Alliance has developed a unique and inclusive culture which embraces Māori values. The project has also set itself very ambitious environmental and sustainability objectives.
The integration of decarbonisation into decision-making has yielded a projected 60,500 tons of carbon dioxide equivalent (tCO2e) reduction in total carbon footprint over the CRL’s 100-year design lifespan, a 19 percent reduction in the expected carbon payback time once the CRL is operational to under six years. CRL is projected to reduce Auckland’s transport emissions by 28,000 tCO2e, every year.
To ensure decarbonisation was prioritised by all alliance participants, sustainability was formally integrated across the management system so that all decisions, including design, construction, whole-of-life cost, procurement and change management considered the carbon footprint implications.
Industry-leading decarbonisation measures that have contributed to this reduction include lowering the amount of cement in concrete, changing the mined tunnel designs to reduce excavation works, material reuse, using self-adjusting ‘smart’ lighting and ventilation systems to minimise station operational footprints.
progressed very quickly while being in closed mode, and settlements were limited to two millimetres (mm).
Subterranean Servicing
On top of this, there posed the issue of navigating passage regarding the anchors – steel strands cast-in construction supports - of the Aotea Centre, a performing arts and events centre located in the heart of Auckland.
According to Dudouit, these anchors were installed several decades ago during the construction of the Aotea Centre and left in the ground. Investigation work was necessary to ensure the number, position, length, technical characteristics, and that they were no longer under tension. Due to problems of access and utilities diversion, it was hardly feasible to remove the anchors from the surface.