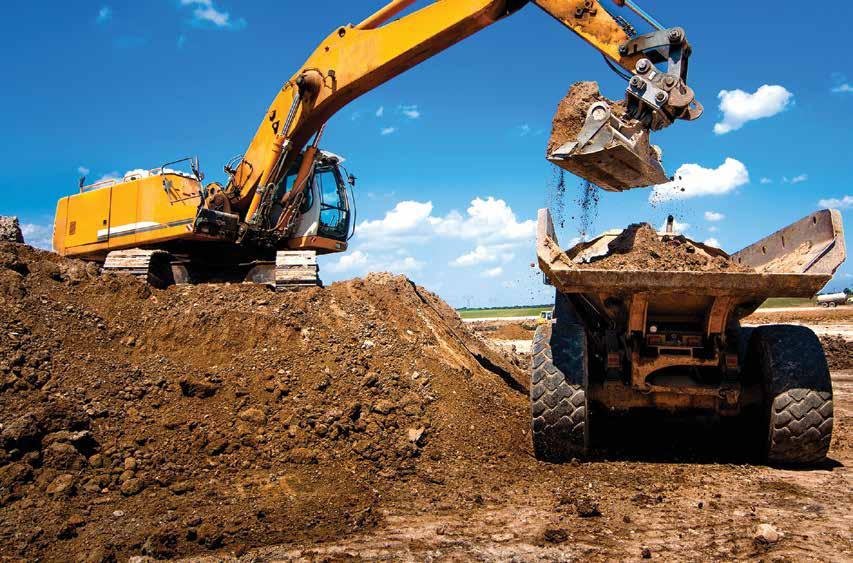
4 minute read
EXCESS SOIL REGULATION O. REG. 406
It is crucial to accurately define excess soil and ensure that only actual soil is included in the calculations of the excess soil volume. This ensures that the calculations are precise and reflective of the true amount of soil requiring management. Different volumes of excess soil have varying implications for the project. For instance, if the volume of excess soil is less than 100 cubic metres, it may be permissible to directly transport it to a landfill with minimal sampling. However, this is subject to the approval of the landfill. Moreover, if the soil volume falls below 2,000 cubic metres, there may be exemptions from certain planning requirements as outlined in Section 8 of the regulation. This exemption translates to reduced reporting obligations and less stringent sampling requirements. It is also important to note that the volume of soil to be generated can impact the sampling frequency. Specifically, if the volume exceeds 10,000 cubic metres or 40,000 cubic metres, there are implications on the frequency of sampling that needs to be considered and addressed accordingly.
Destination
When selecting a destination site for excess soil from your project, there are several factors to consider. One of the primary considerations is the proximity of the destination site to your project site. Opting for a destination site that is closer to your project site can result in cost and time efficiencies. Additionally, it is crucial to evaluate the requirements set forth by the receiving sites. Many receiving sites have specific
by
fill management plans that outline the criteria for accepting soil, including quality standards and other relevant factors. Engaging a Qualified Person to review the Fill Management Plan is advisable to ensure that the soil being transported aligns with the receiving site’s requirements. This step helps prevent any discrepancies or issues upon arrival. Furthermore, it is essential to recognize that the receiving site likely has its own Qualified Person who will assess the information and reports regarding the excess soil before its arrival. Providing the necessary documentation and reports ahead of time allows for a smoother process and facilitates compliance with the receiving site’s protocols.
Reports And Timing
Once the soil volume has been determined and the reporting requirements have been established, it is essential to have a clear understanding of the time required to complete the sampling and reporting processes. If Section 8 of O. Reg. 406/19 applies, and reports such an Assessment of Past Uses, Sampling and Analysis Plan and Soil Characterization Report are necessary, it is typically advisable to initiate the excess soil-related work at least four weeks before on-site excavation activities commence. This precautionary measure helps prevent any potential delays.
Early and transparent discussions with your Qualified Person, once the project has been awarded, are crucial in planning and meeting the excess soil requirements in a timely manner.
In some cases, there may be an option for rush sampling to expedite the process if time efficiency is paramount. However, it is important to note that this can significantly increase costs, with laboratory rates potentially rising up to 100 per cent. Therefore, careful consideration should be given to balancing time efficiency with budget constraints.
By proactively addressing the time requirements for sampling and reporting, collaborating with a Qualified Person, and establishing clear communication channels, you can effectively manage the excess soil-related tasks and maintain a smooth workflow for your road building project.
Sampling Methodology
In the initial stages of construction projects, it is common for excess soil removal to be a crucial step. However, when considering time efficiency, sampling at the start of excavation is generally not the most optimal approach as it results in a delay in the start of excavation activities until the time the environmental sampling, testing and reporting are completed. If done ahead of time, methods such as drilling with a drill rig or test pitting with an excavator are typically necessary for proper sampling. Hand dug test pits are an option for very shallow depths with soft cover which can be broken through with a shovel. These methods allow for the collection of accurate soil samples while ensuring the integrity of the surrounding infrastructure. It is essential to conduct utility locates prior to the commencement of sampling to avoid any potential damage or interference with underground utilities.
By employing drilling or test pitting techniques and completing utility locates before initiating the sampling process, you can ensure a more efficient and systematic approach to excess soil sampling in road construction projects. This consideration helps maintain the overall progress and timeline of the project while complying with the regulatory requirements for soil sampling and analysis.
Leachate Sampling
The leachate methodology referenced in the Excess Soil Regulation 406/19 is the ministry’s Synthetic Precipitation Leaching Procedure (mSPLP). However, it is important to note that most licensed landfill permits typically refer to the Total Characteristic Leachate Potential (TCLP) which is a more commonly used methodology. If there is a possibility of soil disposal to landfill, it is advisable to also conduct TCLP analyses in addition to mSPLP. This analysis helps confirm whether the soil is non-hazardous and whether the landfill will accept this soil.
Tracking System
It is important to implement a tracking system that documents essential information for each load of soil leaving the project area and being transported to the designated destination site. This tracking system captures important details on each load such as date, time, quantity, and quality of soil. Recently, electronic systems based on smartphone applications or similar technologies have proven to be more robust and efficient in collecting and managing this information. These electronic tracking systems offer advantages in terms of cost-effectiveness and timing. They streamline the data collection process, enhance accuracy, and facilitate seamless communication between stakeholders involved in the soil transportation process.
Solutions When Contamination Is Found
If unexpected issues arise during the excess soil management process, particularly concerning contamination, there are potential solutions that a Qualified Person can provide. These solutions may include resampling, resampling with averaging, BRAT tool (part of O. Reg. 406/19) and delineation studies. Additionally, exploring alternative approaches like on-site reuse of excess soil can also be considered.
Final Words
The implementation of O. Reg. 406/19 has brought about significant changes in how excess soil is handled, particularly on construction and road building sites. Understanding the implications of this regulation to your projects is crucial. Engaging Qualified Persons throughout all phases of your projects is highly recommended to ensure compliance and effectively navigate the complexities associated with excess soil management.
Salman Bhutta, Ph.D.,P.Eng. is Principal , Hammad Din, P.Eng. is Manager, Environmental Group, and Sina Varamini, Ph.D., P.Eng. is Director, Pavements and Materials Group, at Engtec Consulting Inc.
UNSUNG HEROES by Steve Pecar