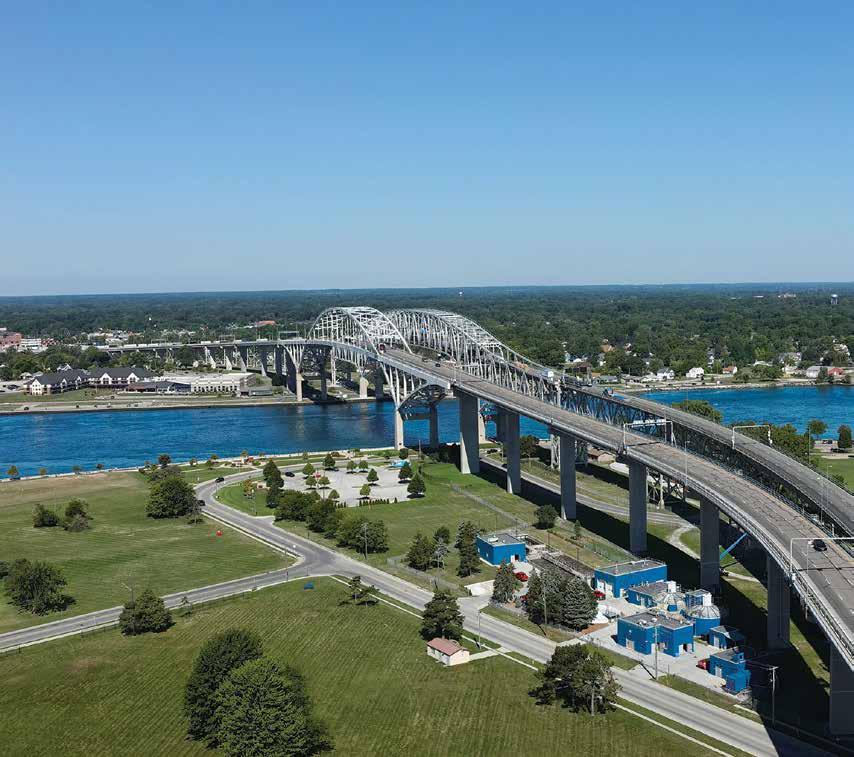
10 minute read
26 years Long-lasting asphalt performance on Blue Water Bridge
26 years Long-lasting asphalt performance on Blue Water Bridge
by James Careless
The three-lane second Blue Water Bridge, which is a continuous tied arch bridge with a total length of 1.85 km and a main span of 451 m, was built alongside the first Blue Water Bridge, which opened in 1938. On average, about 14,000 vehicles cross the two bridges daily, including 6,000 trucks.
Much has changed since the second Blue Water Bridge opened 26 years ago, but what hasn’t changed is the asphalt surface on the bridge’s concrete deck. The two lifts of asphalt (a 20 mm binder course lift and a 35 mm surface course lift) have endured an incredible volume of vehicles over the years without needing to be replaced until now.
“We do maintain the bridges really well,” says Rubara Chowdhury, Senior Project Engineer with the Federal Bridge Corporation Limited, the crown corporation that manages international bridges in Canada. (U.S. agencies manage the U.S. sides of international bridges.) “If there is a pothole that forms, we deal with it in a timely manner. Still, the original asphalt has stood up well after many years of service.”
In 1997, the second Blue Water Bridge was opened. Spanning the St. Clair River, the bridge connects the city of Sarnia, Ontario to the U.S. city of Port Huron, Michigan.
The Original Mix Design
According to Doug Woods, Construction Manager with Cope Construction at the time, Ellis Don served as the primary contractor of the approach spans as well as the paving of the Canadian side of the second Blue Water Bridge project. “I was the estimator responsible for putting the original tender together as a subcontractor,” he says. “We hired Ashwarren Engineering Services to help us review and prepare the asphalt mix designs. We were familiar with them through our relationship with OHMPA, now OAPC.”
Paul Lum, Technical Director with Colas USA, was an Ashwarren manager back in 1997. “Cope Construction hired our company to perform the mix design work for them so that they could pave the project to the contract specifications which had been prepared by the bridge designers Modjeski and Masters (American side) and Buckland & Taylor Ltd. (Canadian side).” ››
The same lay down and compaction equipment was used for the surface course as for the binder course. The surface course was more compactable requiring four passes each by the breakdown and intermediate rollers, followed by two passes by thefinishing roller to achieve a 93% compaction. (Doug Woods, 1997)
According to an article about the project written afterwards by Lum and then Cope Construction president John Williams entitled Paving of the Second Blue Water Bridge and Failures During Construction, the contract specifications for both the Ontario and Michigan road surface – including the waterproofing system and flexible pavement – were similar.
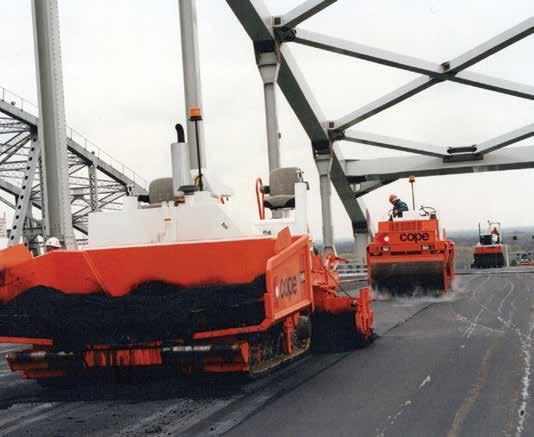
Both called for a base layer of polyester fabric sandwiched between two layers of hot-poured rubberized asphalt to a thickness of 5 mm on the bridge’s concrete deck. This was then covered by a sheet of No. 8 paper, 20 mm of High Stability HL 2 binder course mix and 35 mm of Modified HL 1 surface course mix, all of which was specified in the contract.
According to Woods, the specification for 55 mm of total asphalt surfacing was a deliberate choice. “The asphalt was viewed as a wearing surface rather than a road in line with the bridge designers’ goal of not adding any more ‘dead load’ (the weight of the bridge’s permanent non-moving elements) to the structure than they had to,” he says. “In fact, the concrete deck and asphalt paving were probably 25 to 30 per cent thinner on the second Blue Water Bridge than they were on the first.”
Creating the High Stability HL 2 mix brought challenges of its own. Cope Construction’s goal was for this mix to achieve a minimum stability of 16,000 N (Newtons). To meet this target, Cope Construction used an aggregate mix of 35 per cent 3/8 inch chips and 54.2 per cent manufactured sand from Redland Quarries, plus 10.8 per cent screenings from Michigan Limestone. But “even though 100 per cent quarried aggregates were used in the mix design, the stability of the mix did not meet the minimum specified requirements and the final blended aggregate Job Mix Formula (JMF) did not meet the overall gradation band,” says the Lum/Williams article.
The problem was the HL 2 specification which had been achieved on a previous bridge project using a coarse aggregate made out of blast furnace slag and an asphalt cement “heavily modified with polymer,” continues the Lum/Williams article. “The contractor offered to use those materials in order to meet the stability requirements for this contract. But, due to the increase in cost for those materials, the bridge’s consultant elected to reduce the minimum required stability to 14,000 N and approved the initial HL 2 (HS) Mix design.” As it turned out, the final HL 2 aggregate blend had a stability level of 14,6000 N, with asphalt cement making up 6.4 per cent of the total mix.
Fortunately, the Modified HL 1 surface course mix didn’t run into any issues. Its aggregate mix consisted of 41 per cent HL 1 stone from Smelter Bay Aggregates, 35.4 per cent asphalt sand from Lafarge, and 23.6 per cent screenings from Michigan Limestone. This top layer had a stability rating of 11,670 N, with asphalt cement accounting for 5.2 per cent of the completed hot mix.
The Original Application Method
While the second Blue Water Bridge’s original mix design played a big role in its 26 year record of durability, the way in which this asphalt was applied to the concrete deck also made a difference.
Two weeks were allocated for waterproofing and paving the second Blue Water Bridge’s concrete deck, with the work starting on May 14, 1997. Initially, a rubber tire asphalt paver had been specified to minimize damage to the water proofing system, but Cope Construction suggested using a rubber tracked crawler paver instead “since it would have lower ground pressure than a rubber tire paver,” says the Lum/ Williams article. “The force required to propel the paver and to push a loaded truck uphill would also be lower.”
A Blaw-Knox PF 410 crawler paver equipped with an Omni 1AS extendable screed was used instead of the rubber tire paver. This combination “operated satisfactorily with no damage to the waterproofing system,” the Lum/Williams article says.
The HL 2 course was laid in two lengthwise passes of 3.2 m each, followed by two more passes of 3.4 m each, for a total width of the combined four passes of 13.2 m between the bridge’s two curbs, all done in an uphill direction. “The breakdown roller was a Bomag BW 151AD double drum steel roller, the intermediate roller was a Caterpillar PS180, 9-tire pneumatic tire roller, and the finishing roller was a Dynapac CC142 double drum roller,” says the Lum/Williams article. A second CC142 was used for transverse rolling at the bridge joints.
On the first day of paving, the low ambient temperature on the bridge (about 7°C) combined with cool winds blowing off Lake Huron, meant that there was only about two minutes for the rollers to achieve the specified 93 per cent compaction. ››
To make matters worse, “it was found necessary to run the paver at the lowest possible speed in order to minimize the area of mat exposed, and to maintain the mat temperature as high as possible. Use of the screed vibrators did not prove beneficial and in fact reduced the mat compaction as determined by using a thin lift nuclear gauge and rolling compaction test strips,” says the Lum/Williams article.
Once the HL 2 binder course had been laid down, it took six passes by the breakdown roller, six passes by the intermediate roller, and two passes by the finishing roller to achieve the required 93 per cent compaction. All of the rollers operated in static mode due to concerns that vibrations could cause micro-cracking in the bridge’s concrete deck.
The weather warmed up to 12°C on May 20 and 21, 1997, when the rest of the HL 2 paving was completed. But variable cloud cover caused the deck temperature to vary between 19 and 42 degrees Celsius.
The 35 mm Modified HL 1 surface course was laid on May 22 and 23. This was done uphill in three passes of 4.8 m, 3.6 m and 4.8 m. These widths were chosen so that the longitudinal joints would align with the planned traffic lane markings.
“The same lay down and compaction equipment was used for the surface course as for the binder course but this layer was more easily compactable,” the Lum/Williams article notes. As such, it only required four passes each by the breakdown and intermediate rollers, followed by two passes by the finishing roller, to achieve a 93 per cent compaction rate.
Dealing with Unexpected Issues
“What we experienced was the fact that, when we had a truck parked waiting for its turn to load the paver for the HL 1 course, cracks would appear underneath the rear axle where the majority of the load was,” says Woods. “When temperatures got up over 30°C on the pavement surface, we started seeing indentation and cracking on the upside of the rear tandem trucks that were fully loaded with hot mix,” Lum adds. This problem was resolved by keeping the truck moving forward slowly in front of the paver. But why had the trucks’ rear wheels caused cracks in the HL 2 course at all? Some were serious: “The worst failure showed a crack approximately 12 mm wide on the uphill side and the asphalt was shoved up approximately 25 mm high on the downhill side of the tire footprint,” the Lum/Williams article says.
Rigorous quality control testing by Cope and Ashwarren eventually revealed the culprit: The 5 mm sandwich of paper and rubberized asphalt providing waterproofing between the concrete bridge deck below and the 55 mm of asphalt cement above. When the bridge surface got too hot, the waterproofing layer could be deformed or moved by heavy truck weight pressing down on the asphalt pavement, resulting in cracks and other issues.
“The deck temperature at the time of the failures was 42°C,” says the Lum/ Williams article. “There had been no problem in the morning when the deck temperature was in the range of 20 to 25°C.”
Once the cause of the problem had been discovered, Cope and Ashwarren weighed their options and the associated costs, from repairing the damage to adding plastic geogrid or steel expanded metal between the concrete deck and the asphalt lifts.
“Here’s the crazy thing,” says Lum. “The areas that slipped, we repaired the asphalt in those areas and that was it. Then we waited and the problems did not recur. We stopped them on the job site by keeping the trucks moving. Once the bridge was open to traffic, it kept moving and the cracks didn’t happen again.”
From then until now, the asphalt pavement on the second Blue Water Bridge has held up. Whether its planned replacement – 50 mm of Superpave 12.5 FC2 – does as well remains to be seen. That work will begin next year, says Chowdhury, because 26 years of relentless use has finally taken its toll. And yes, asphalt was chosen for the new surface “due to the way the original asphalt performed,” she says.
James Careless is an Ottawa-based freelance writer with credits in the National Post, Toronto Star, and AI’s Asphalt magazine.
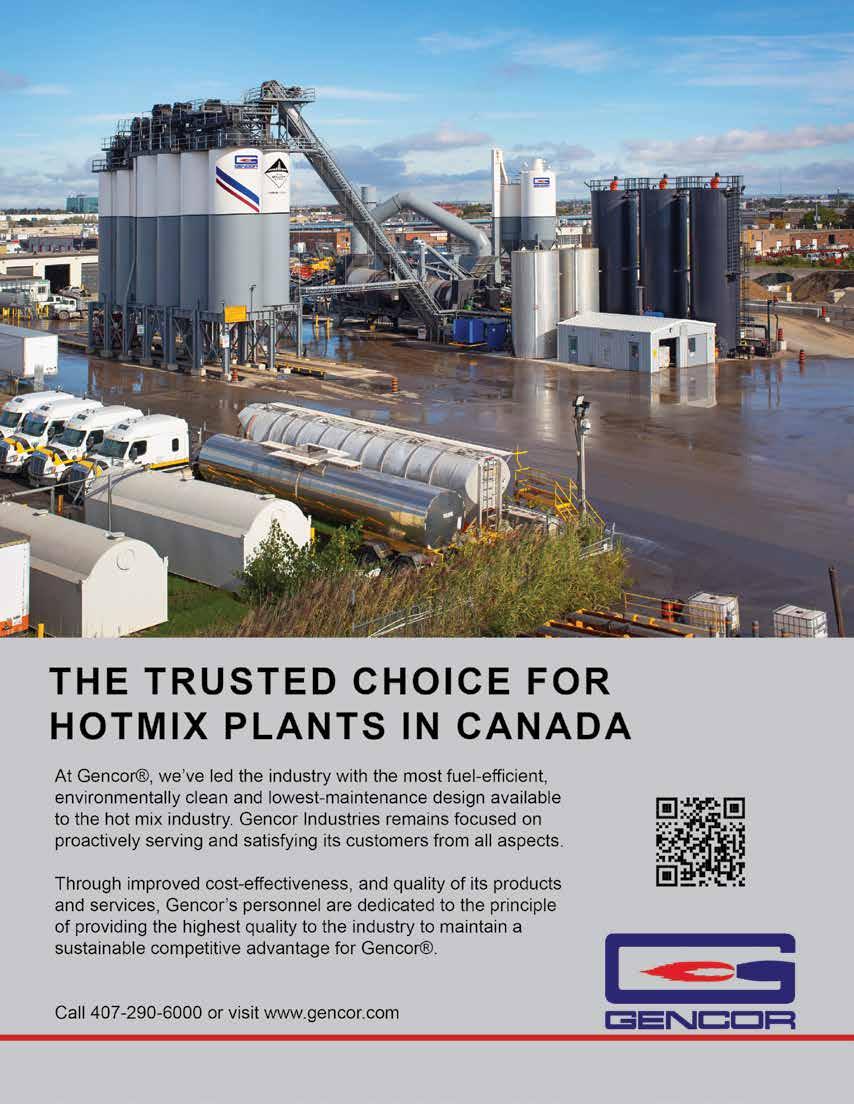