
7 minute read
Excavator Automation Reaches Next Level
EXCAVATOR AUTOMATION Reaches NEXT
LEVEL
Advertisement
Many of the features on the most recent generation of excavators enable semi-automatic operation of critical functions. This increases operator efficiency and productivity.
“Grade control is quickly moving into the construction industry like a hurricane,” said Adam Woods, Manager of Innovation and Technology Integration, LBX. “Link-Belt recognizes this and has developed an integrated grading solution powered by Trimble Earthworks, called Link-Belt Precision Grade. The system works in unison and is seamlessly integrated into our proprietary hydraulic system, which is called Spool Stroke Control.
“Link-Belt Precision Grade was developed and launched for many purposes, but curbing the impending labor gap was one of them,” he continued. “With more of the seasoned operator
Case Construction Equipment now offers OEM-fit 2D or 3D machine control technology on Case D Series excavators, simplifying the acquisition process.
force retiring, the industry will see an increase in a younger generation coming in to fill those positions.” With this comes a need to educate, train and learn. This is where the integrated grading solution comes into the picture. “Taking new operators and getting them to productivity levels of seasoned operators in a matter of hours and/or days, Link-Belt Precision Grade looks to cut the learning curve to get customers productive and efficient as soon as possible.”
Automated features are a great tool for newer or less skilled operators. “It helps them maintain grade by aiding them once the bucket has reached grade and [allows them to] get the feel for it,” said Ryan Neal, Market Professional, Caterpillar Inc. “And for skilled operators, it is another tool in their belt. If they already understand reading the grade stakes and have a feel for
CASE CONSTRUCTION EQUIPMENT depth and slope, this will only advance them in being more accurate for longer periods of time and help with operator mental fatigue.” Automation aids accuracy Standard Cat Grade with Assist automates boom, stick and bucket movements to deliver more accurate cuts Excavator automation technology with less effort. The operator simply sets reduces demands on operators the depth and slope into the monitor and simplifies their ability to and activates single-lever digging. “We offer our Cat Grade with Assist on achieve desired results. most of our lineup, from the 313 to the 352, as standard,” Neal said. “It enables By Curt Bennink the operator to maintain grade and keep the operator more accurate and less mentally fatigued from digging on grade all day. We have a standard 2D solution for those who want to maintain a specific depth, as well as a 3D solution from the factory or from a SITECH dealer. John Deere has simplified operation with SmartGrade technology. “We’ve equipped the 210G LC, 350G LC and 470G LC with SmartGrade to give operators at entry level of experience the ability to achieve grade quickly and confidently,” said Justin Steger, Solutions Marketing Manager, Site Development and Underground. “By controlling the boom and the bucket, this semiautomatic technology frees up the operator to concentrate on the arm function, resulting in fewer periodic grade checks every time. SmartGrade technology will make novice operators good and good operators great.” Komatsu’s intelligent Machine Control (iMC) excavator allows the operator to focus on moving material efficiently while semi-automatically tracing the target surface and limiting over excavation. “Starting with our PC210 LCi-11, we’ve launched iMC 2.0,” said Andrew Earing, Product Manager for Tracked Equipment. “With iMC 2.0, we’re going to be offering the bucket hold control as well as optional auto tilt bucket control, two primary features that are going to
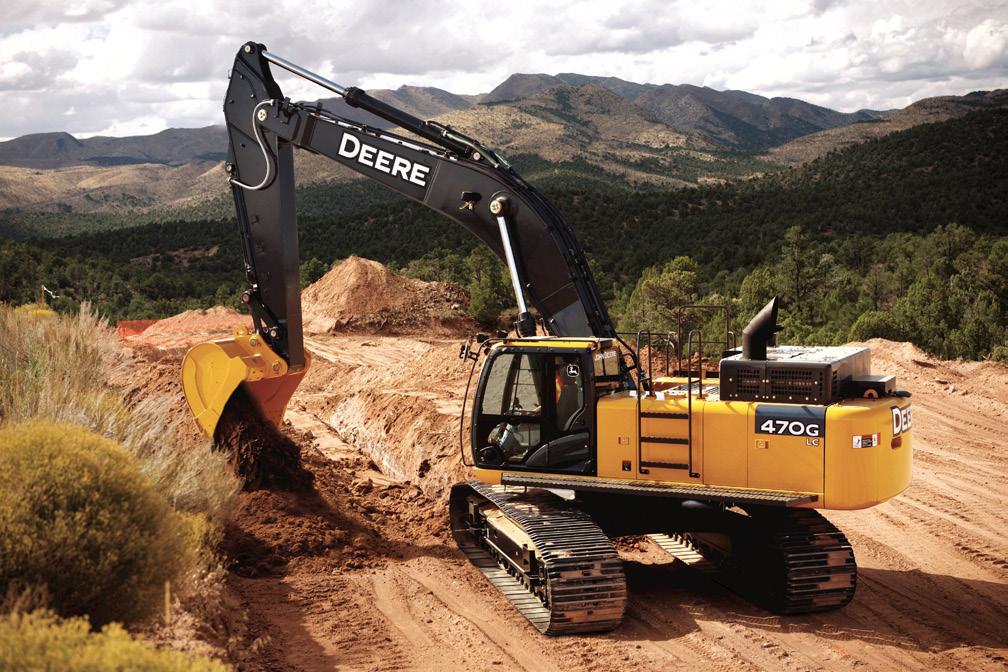
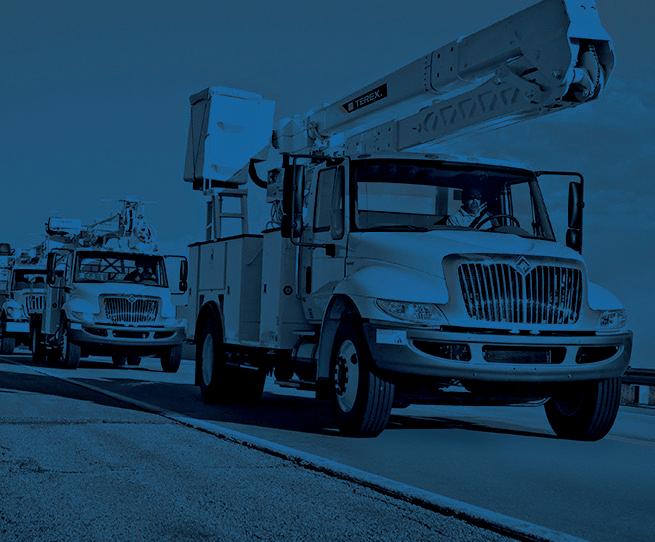
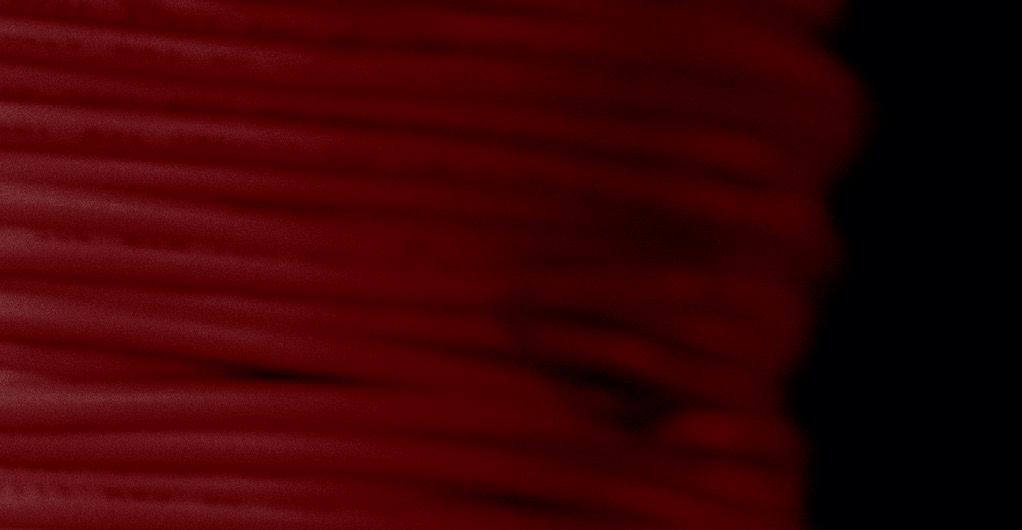
help with overall productivity and efficiency on the jobsite.”
Bucket Angle Hold and optional Auto-Tilt control are newer features on Komatsu iMC excavators. With Bucket Angle Hold, the operator sets the desired bucket angle and the system automatically maintains the angle throughout the grading pass. Auto-Tilt control automatically tilts the bucket to the design surface and returns it to horizontal to unload.
Auto Tilt control boosts jobsite efficiency. “No longer do you have to move the machine every single time you want to make a finish grading pass,” said Earing. “You can now do that from one position and still grade the surfaces with very high precision.”
Auto grade assist makes it easier to hit grade. The operator moves the arm, and the boom adjusts the bucket height automatically to trace the design target surface. This allows the operator to perform rough digging operations without worrying about the design surfaces and to fine grade by operating the arm lever only.
As a first step toward automation, CASE Construction Equipment entered the realm of factory fit machine control with its D Series excavators earlier this year. You can now order and take delivery of a Case excavator with 2D or 3D excavation system already installed and tested by the OEM.
“What we are doing here is matching, installing and testing 2D and 3D systems from Leica Geosystems with Case D Series excavators up to the CX 350D,” said Nathaniel Waldschmidt, Product Manager - Excavators. “It massively simplifies the acquisition process.
“Machine control has the ability to transform the productivity, efficiency and long-term profitability of excavators,” he continues. “We’re now making the addition of machine control with excavators completely turnkey, allowing contractors to experience those benefits in an extremely seamless experience with their Case SiteControl Certified dealer.”
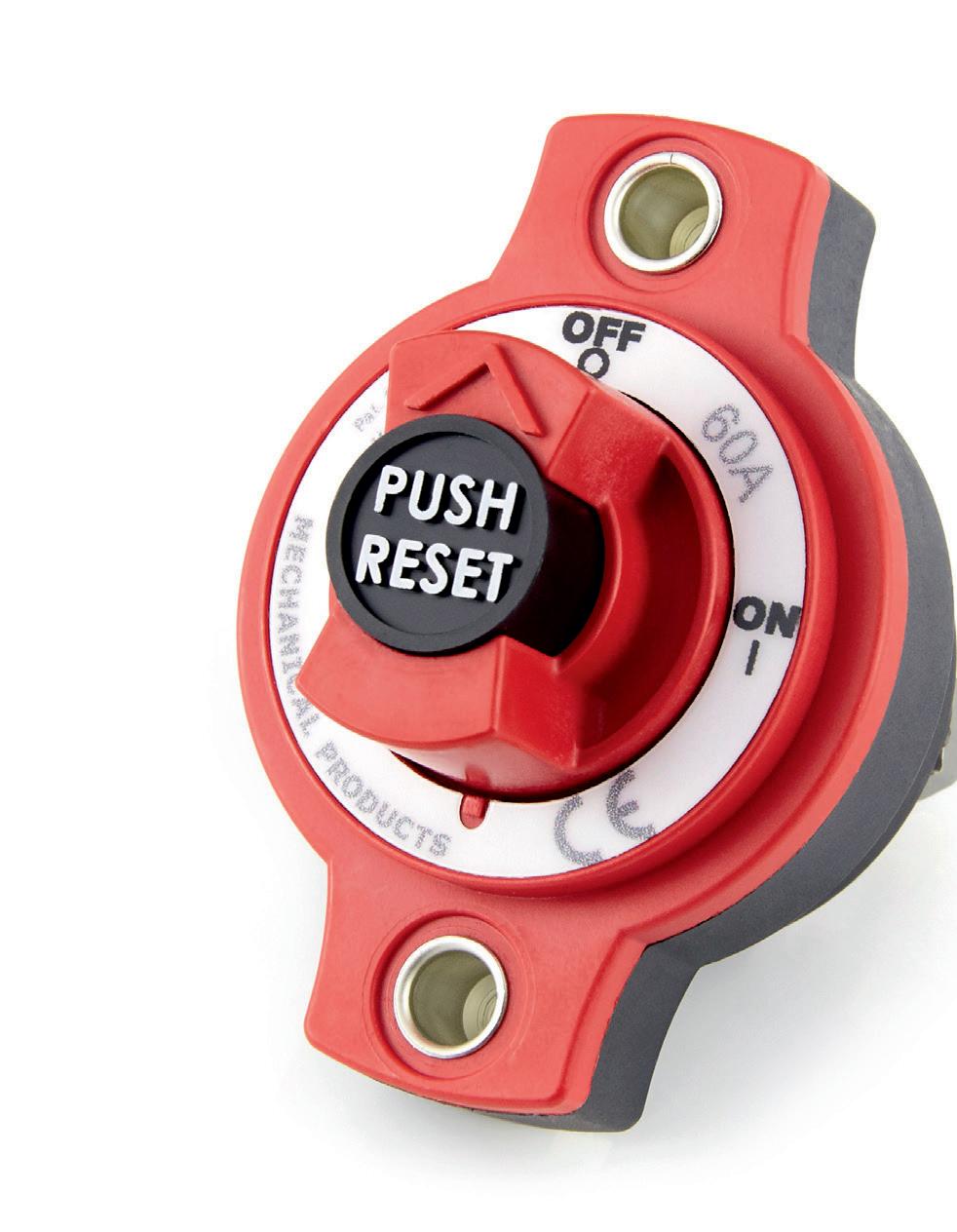
Measurable productivity improvements
Tests performed by several of the major excavator OEMs demonstrate impressive productivity enhancements when implementing semi-automated grade control functions.
“In a controlled planar slope grading test, we measured speed and accuracy for a novice and experienced operator in manual mode vs. [John Deere’s] SmartGrade 3D control. The results were SmartGrade made the novice operator 90% more accurate and 34% quicker. It made the
Battery Switching and Circuit Protection in a Single Device!
The Series 53 Branch Disconnect/ Circuit Breaker from Mechanical Products provides a quick means to disconnect downstream circuits while preventing battery drain, and allows for disconnected battery power during storage and maintenance.
• OEM cost savings by eliminating added compontents • Ignition protected
For stocking information call 800-328-2724 or visit www.waytekwire.com
experienced operator 58% more accurate and 10% quicker,” said Steger.
Productivity and efficiency studies show gains that are hard to ignore. “When we’ve done case studies in the past, we find anywhere up to 63% improvement in time,” said Komatsu’s Earing. “The reason we are able to get there is this technology greatly reduces or even eliminates staking. Grading is much more efficient, and inspection can literally be done with this technology instead of having to bring somebody back out on site.” As-built verification can be performed by the excavator. “Overall, the time savings are huge.”
The technology also greatly compresses the learning curve. “The days
Smart Hydraulics. Easy Business.
Precise, Flexible and Safe
Load-holding valves type OSCA
Visit HAWE
May 2 - 5, Houston, TX Booth 1101
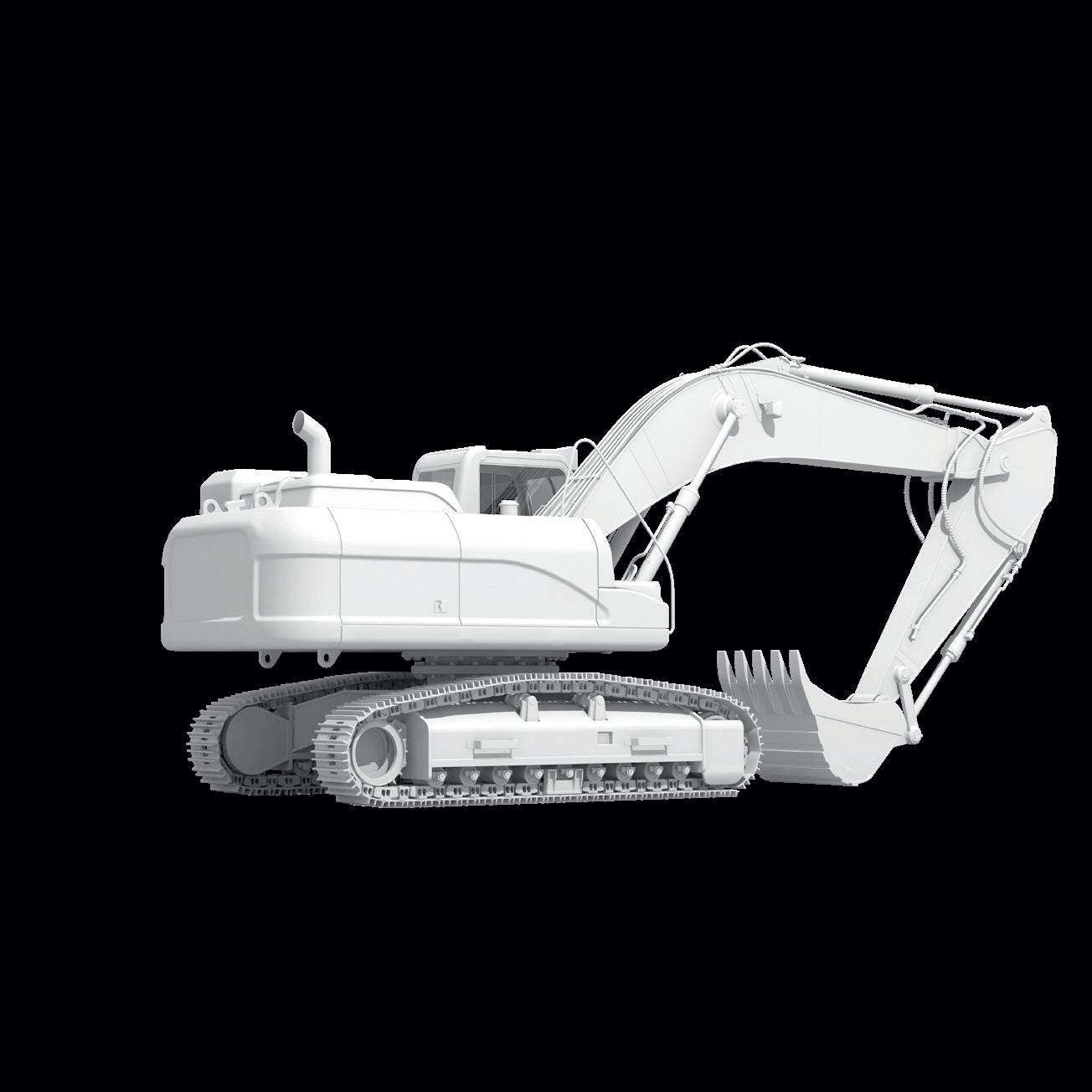
Efficient, Reliable and Durable
Variable displacement axial piston pump type C40V
Industry Leading Performance
Proportional directional spool valve PSL-CAN
HAWE Hydraulik manufactures the highest quality hydraulic components, constructed to minimize space and maximize product durability for the mobile, industrial and oilfield markets.
Partner with HAWE to always have the right solution!
We are Partners.
www.hawe.com | info@haweusa.com | 704-509-1599
Several operations opportunities available now. Visit the HAWE Job Market online to apply today. of waiting months and years for new operators to gain the skills required to cut accurate, precise grades are gone,” said Woods. “Months and years now become hours and days with the help of Link-Belt Precision Grade semi-autonomous Machine Control and indicate Machine Guidance systems.”
The technology shortens cycle times, as well. “By relying on the machine and system to do all of the exact calculations and thinking, the operator can get into the dig and out quicker by allowing the machine to do the fine grading function for them,” Woods explains. “With the system always staying on the operator’s correct depth and slope path, the function is completed more efficiently without guesswork.
“Productivity has been tested and studied to show improvements as high as 50%, depending upon the job application,” he notes. “Automation clearly takes the guesswork out of the task on the jobsite, allowing operators to focus on other things. Automation also enables jobsites to function without the need for additional surveyors and grade checkers within the working area. This vastly reduces the chances and risk of bystanders being injured during previously routine operations.” |
Scan here to read more https://oemoh.co/ma8w6e
