
6 minute read
Pre-Compensated Valve Platforms
Pre-Compensated Valve Platforms Offer New Benefits in Mobile Machine Development
Complete, compact pre-compensated valve platforms provide plug-and-play solutions for OEMs, enabling them to select the right hydraulic control valves for a specific machine application.
Advertisement
Contributed by Wladimir Kamschitzki, Product Management, and Roger Webel, Sales Product Manager, at Bosch Rexroth
BOSCH REXROTH
The Pre-Compensated Valve Platform from Bosch Rexroth is a complete, compact mobile machine control solution that leverages the efficiency and versatility of proven Rexroth mobile control valves.
In the realm of mobile equipment, pre-compensated hydraulic valves with load-sensing technology are often used in applications where compactness, robustness and versatile performance are needed. Equipment such as elevated working platforms and telehandlers, truck-mounted cranes, compact backhoes, excavators and other construction equipment, as well as the latest generation of forestry machines like feller bunchers and harvesters, all feature complex implements that need precise and highly-responsive hydraulic control.
Recent developments in pre-compensated valve technology are helping mobile machine builders accomplish these goals. In addition, these advances can help reduce the cost and weight of valve systems, simplify equipment engineering and component integration and aid in improving mobile machine energy efficiency.
A new generation of complete, compact pre-compensated valve platforms is replacing prior “mix and match” approaches to valve configuration with solutions that are nearly “plug and play,” enabling mobile machine builders to easily select and right-size hydraulic control valves according to specific functional and performance requirements.
Mobile machine operators can apply the advances these modular, multi-application valves offer to better control lifting, lowering, rotating and more.
Solving pre-compensated valve design challenges
Modular load-sensing valves remain widely used in mobile machine hydraulics. By incorporating both flow control and pressure control into the same valve, system design is simplified, flexibility is increased, and reliability is enhanced since there are fewer components and reduced hydraulic plumbing.
Although widely adopted, the use of load-sensing control valve technology can still present design and engineering challenges, such as right-sizing the valves to match the requirements of different applications within the same implement. This often leads to compromises where larger, more expensive valves are selected to serve the requirements of the actuator with the highest flow or pressure requirements, increasing costs and engineering complexity.
Today’s valve manufacturers can supply a range of valves with a broad range of pressure and flow ratings as well as other features, such as pilot valves and valve spool actuation options, including hydraulic, electromechanical and electronic. Selecting the right valve, or group of valves, can follow several approaches, depending on the mobile machine’s requirements.
A truck-mounted crane is a good

example: A single variable-displacement pump supplies the flow used to control the various functions of the crane, including the main arm, the articulated arm, the telescopic cylinder, the open gripper, the close/lower gripper, the slewing gear and the outrigger stabilizer.
For maximum machine productivity, multiple functions will operate simultaneously as the operator moves a load. The loads placed on each function can vary depending on materials being moved and the nature of movement. Some functions, like deploying the outrigger, are relatively simple, while grippers, articulated arm and telescoping cylinder are more dynamic.
A typical approach is to select one valve that can handle the largest, highest flow demand from the system, even if some actuators never require that flow rate. This one-size-fits-all design can lead to valves taking up more space in the machine and weighing more www.enmco.com (and costing more) than is necessary; it often leads to over-specifying valves with a higher-than-needed pressure rating or more features than a given implement function needs.
Some mobile machine builders will use multiple ELECTRONICS LCD HOUR METER/COUNTER COMBO valves to control HOURMETER COUNTER T39 specific parts ENM’s Series T39 LCD 6-DIGITS hour meter and of the machine, up counter instrument is ideal for any application that requires recording both time measurement selecting them and event count for maintenance schedule. based on pressure The two displays meter can operate independently or in parallel. This compact and flow ratings tamper-proof meter is protected from the environment to provide years of service. and other features that support a specific actuator’s operation. This closely matches the size and cost MADE IN THE U.S.A of the valve to its e-mail: application. customerservice@enmco.com TOLL FREE 888-372-0465
However, this approach can create engineering and design issues. If separate valves are selected, they need to be installed into tight machine spaces with separate hydraulic plumbing and controls wiring; this can add time and cost to machine integration and potentially lead to maintenance challenges over the life of the machine.
Another approach combines multiple valves into a single control assembly, simplifying installation and providing a more compact solution. In some cases, different valves from different suppliers are selected, especially if one supplier can’t satisfy all the requirements.
Combining these disparate valves into one block presents another challenge: Custom adapter plates must be obtained or machined to align the different valve ports and inlet flows, requiring specialized engineering and fabrication efforts.
Complete platform offers major advantages
A new solution to these challenges involves a complete, compact pre-compensated valve platform that combines valves into a single, scalable implement control solution. This platform can be custom-configured from one supplier, combining valves with different flow and pressure thresholds.
The advantage of this approach is having a single, multivalve solution from one supplier rather than having multiple, different and potentially noncompatible solutions. More importantly, the platform gives mobile machine builders the ability to right-size the valves in the platform to more closely align with each function’s operating requirements.
Valve platforms offer the greatest value if the different families that make up the platform are engineered for easy integration, with minimal need
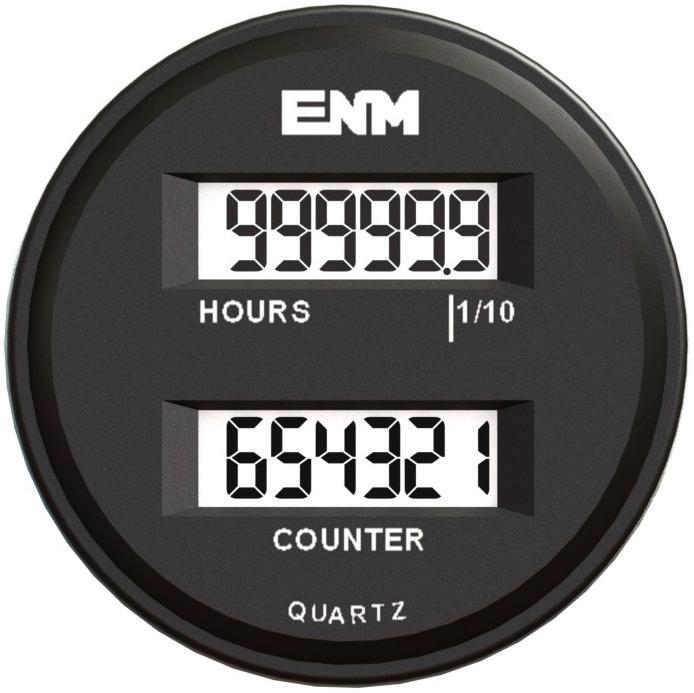
for adapter plates or special, one-off modifications. The valves used in these platforms should also cover a full range flow and pressure rates and support other features. In this way, one platform can satisfy virtually all the functional and operational demands of today’s mobile machines.
For example, Bosch Rexroth is able to supply a complete, compact solution based on three proven, high-performance groups of compact load-sensing valves: • The compact EDG directional control valve, which supports flows up to 40 liters per minute (lpm)/10.6 gallons per minute (gpmM) and up to 350 bar working pressure. • The RM-10 and RM-15 compact, general purpose directional control valves, with flow rates of 90 and 150 lpm (23.8 and 39.6 gal./min.), respectively, and 280 bar (4,061.06 psi) working pressure. • The M4-12 control block, supporting up to 130 lpm/34 gpm and 400 bar working pressure for medium- and high-pressure applications. The M412 features a wide range of accessories, such as adjustable mechanical flow limiters, CAN actuation, spool position sensing and load-sensing pressure limiters on each port.
To build these complex platforms, it makes sense to work with valve suppliers that offer state-of-the-art online or downloadable configuration tools with extensive component libraries and intuitive, step-by-step processes for configuring the valve platform, so engineers can more easily create a solution that fits their requirements.
These new pre-compensated hydraulic valve platforms can help OEMs create more versatile and sophisticated mobile machines. They are solutions that can save engineering time and cost, practically eliminate the need for custom adapter plates and provide a more compact valve platform.
A single multivalve solution with load-sensing technology supporting multiple flow and pressure rates makes it easier to right-size the valve controls for each machine, delivering hydraulic power to the actuators as efficiently as possible. This helps the overall machine to be more energy efficient and provides a more scalable, “plug-andplay” control valve solution that can enhance mobile machine performance and value. |
Scan here to read more https://oemoh.co/2dttsc

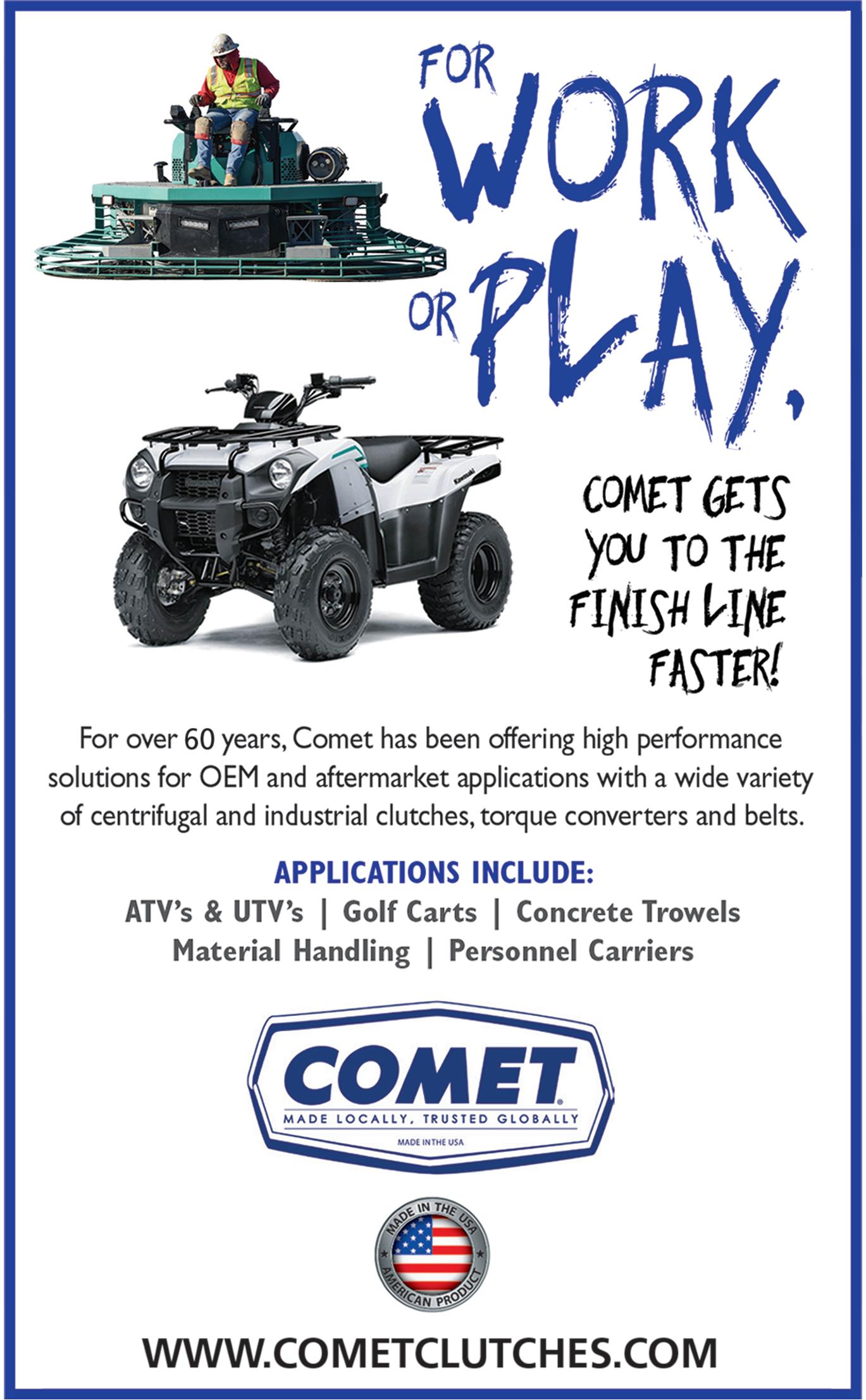