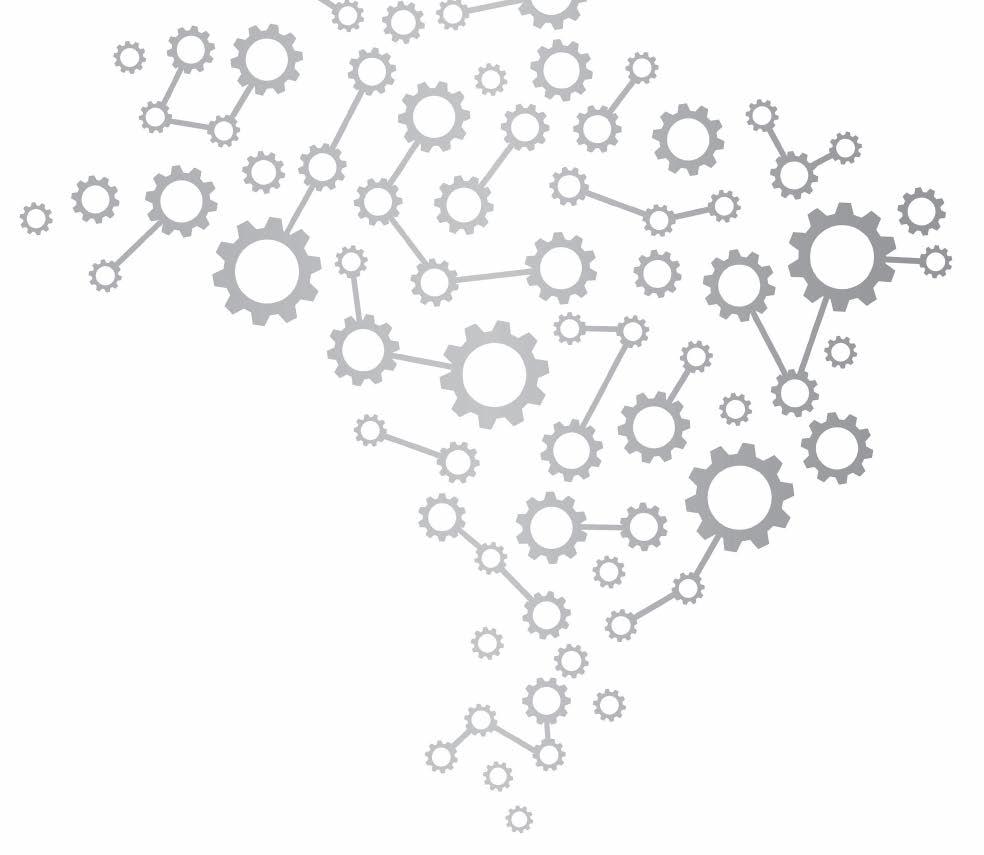
12 minute read
The Running-in Effect of CV Joint Grease
Ko Tanimura
Kyodo Yushi Co., LTD. 2-2-30 TSUJIDO KANDAI, FUJISAWA-SHI, KANAGAWA 251-8588, Japan
Introduction
Constant velocity joint (CV joint) is a generic term for a joint that transmits rotary movement at the constant speed irrespective of flexion angle. The main application of CV joints includes automotive drive and propeller shafts, where they are usually used in combination of a sliding-type joint such as tripod joints and double offset joints with a fixed-type joint such as ball fixed joints (BJ). Figure 11) shows the typical CV joint assembly.
CV joints are generally lubricated with a speciallydesigned lubricating grease. The performance requirements for the CV joint grease have become increasingly severe owing to the market demands for high-performance vehicles of small size and light weight. For instance, the sliding-type joint is required to have reduced vibration. Hatakeyama2) and Yoshihara3) focused on improving vibration performance and developed a low-friction grease with vibration reducing effect by employing some additives in combination. As for the fixed-type joint, a long “flaking life” is of great importance. The typical flaking observed in the fixed-type joint includes subsurface-initiated flaking and surfaceinitiated flaking. For the latter, effective running-in process is thought to be critical for flaking life extension. Taniguchi et al. provided a specific example of surfaceinitiated flaking resulting from insufficient running-in process and reported about a lubricating grease with enhanced flaking resistance developed by employing appropriate additives to improve wear property4).
Most fixed-type joint greases are made from molybdenum disulfide (MoS2) 5). MoS2 is a representative solid lubricant well known for its good friction property and high load capacity. Nevertheless, very little information about the effect of MoS2 on CV joint flaking life can be found in literature.
This paper discusses the role of MoS2 in grease lubrication of fixed-type CV joint based on the results of the bench tests using a real CV joint and SRV friction wear tests to evaluate wear property.
Ball fixed joint - Lubrication condition and flaking resistance
Figure 2 shows the typical structure of BJ 5), which consists of an outer and an inner race, six balls, a cage, a boot and the lubricating grease filled inside the joint. Balls are placed between an outer and an inner race and kept by a cage from axial dropping. A boot is used to hold the grease and to keep out dust and water. Balls in rolling-sliding motion between the races travel back and forth in a short stroke. According to Garnham’s calculation of contact pressure for regular passenger cars based on the Hertz theory, the maximum Hertz pressure between the ball and the outer and the inner race are 2.7 GPa and 3.5 GPs, respectively6).
The fixed –type CV joint is in boundary lubrication with thin oil films because the rough track surface is exposed to high contact pressures at low speeds, and will supposedly be in mixed lubrication as runningin progresses and roughness projections are worn 7). Therefore, BJ needs to be highly resistant to flaking, wear and heat. It should be noted that one of the major requirements for the lubricating grease filled in BJ is flaking resistance. Figure 3 shows an example of flaking on CV joint track surface.
Lubricating Action by Molybdenum Disulfide
MoS2, the representative solid lubricant with a layer-lattice structure can effectively lubricate the fixedtype CV joints in boundary and mixed lubrication thanks to its good friction and wear preventive properties under high-load and/or boundary lubrication conditions. Bartz concluded that MoS2 prevents wear by cushion element action on friction surface or compound films produced by a chemical reaction with friction surface 8).
Contrary to his conclusions, it is also reported that the addition of MoS2 accelerated wear. Bartz suggested that such wear was brought on by antagonism between MoS2 and other EP additives9).
MoS2 in lubricating oil is considered to have a different effect depending on surface roughness. Cusano et al. reported that MoS2 on rough surface in pure sliding can effectively reduce friction by entering the contact area, but that on smooth surface cannot reach the contact area and so has no wear-reducing effect 10). According to their report, the surface roughness that MoS2 achieves the maximum friction/ wear reducing-effect varies with the size of particles11). It seems that, depending on the relation between the particle size and surface roughness which determines the accessibility of MoS2 to contact area, MoS2 sometimes reduces wear and sometimes not.
Some studies about the effect of MoS2 in lubricating oil and grease on flaking life produced different results in response to the lubrication
MoS2’s role in CV joint grease Evaluation on running-in effect using real CV joint
Bench tests were carried out to evaluate the running-in effect of CV joint greases. Grease A with MoS2 and grease B without MoS2 as shown in Table 1 were used to see if running-in process is affected by the presence or absence of MoS2. Grease A is a field-proven CV joint grease formulated with urea, MoS2, organic molybdenum and other additives in combination. Table 2 summarizes the test condition. The track between balls and races of tested CV joints were observed for surface roughness.
Figure 4 shows the surface roughness measurements of the inner race track after testing. Surface roughness was smaller with grease A than with grease B, confirming that roughness projections were worn by the effect of MoS2 and one of the MoS2’s roles in CV joint grease is to stimulate running-in process.
Wear property measurements
Wear that occurs during the initial period of CV joint operation is beneficial and referred to as runningin where roughness projections are worn. The early completion of running-in period associated with the rapid formation of smooth surface is desirable from the viewpoint of less stress to metal. On the other hand, in the subsequent steady state, wear accompanied by stress to metal has to be prevented as much as possible in order to maintain stable surface condition to prolong CV joint flaking life. Lubrication tests in a ball-onplate configuration was carried out using Optimol’s SRV test machine to evaluate wear property with consideration for change in surface roughness during CV joint operation. Two types of test plates with different roughness were used. One had a roughness of Ra0.2 μm (root-mean-square) to simulate lubrication condition during the initial period and the other was Ra 0.1μm found commonly in the steady state with worn roughness projections. Table 3 summarizes the test condition. Tested plates were observed for surface appearance and the roughness of the central part of wear track was measured using a laser microscope. In addition to greases A and B shown above, greases C, D and E with different combinations of additives as listed in Table 1 were tested to study how each additive affects the test results.
Figure 5 shows photographs of the tested Ra0.2 μm plates in which roughness of wear track in Ra is indicated. The ball on test plate reciprocated in sliding motion perpendicular to grinding marks.
As for grease A, the surface roughness decreased after testing as roughness projections were worn. Grease B without MoS2 and grease C without organic molybdenum had no major change in surface roughness, which means that no wear occurred. These results suggest that MoS2 and organic molybdenum can positively affect running-in process.
Following this, the same tests were performed with Ra0.1 μm plates (Figure 6). Greases A, B and C had no major change in surface roughness after testing. Unlike Ra0.2 μm plates, wear did not progress
even when lubricated with grease A containing MoS2 and organic molybdenum.
To sum up these results of all test plates with different roughness, MoS2 and organic molybdenum can promote wear on roughness projections at high local contact pressure, but have no appreciable effect on a smooth sliding surface. MoS2 and organic molybdenum are likely to prolong the flaking life by promoting wear on the roughness projections of unworn surface during the initial period as shown in the CV joint bench tests. At the same time, they can effectively support the formation of robust reaction films in the steady state where surface roughness decreases and wear progresses no further.
Considering that MoS2 functions to smooth the lubricated surface by promoting wear on rough projections, SRV tests were performed under the same test condition as the previous SRV tests as shown in Table 3 to study how the smoothing behavior is affected by the difference in MoS2 particle size and content in grease formulation. Tested greases had the same additive composition as grease A but with different MoS2 particle diameters of 1.9 μm and 12.5 μm in median size and different MoS2 content. The particle size distribution was measured by electrical resistivity method. Two types of test plates were used: one had a surface roughness of Ra 0.2 μm and the other was Ra 0.45μm. Fig. 7 shows the change in wear track roughness before and after testing by grease type. Lower roughness means further progression of wear on roughness projections. Both MoS2s with different particle diameters at low content promoted wear. MoS2 of a larger particle diameter did not promote wear when the content increased confirming that wear on roughness projections is related to MoS2 content. Two test plates of different roughness had the largest wear volume at different MoS2 content indicating that the most suitable MoS2 content for each surface roughness can optimize running-in effect.
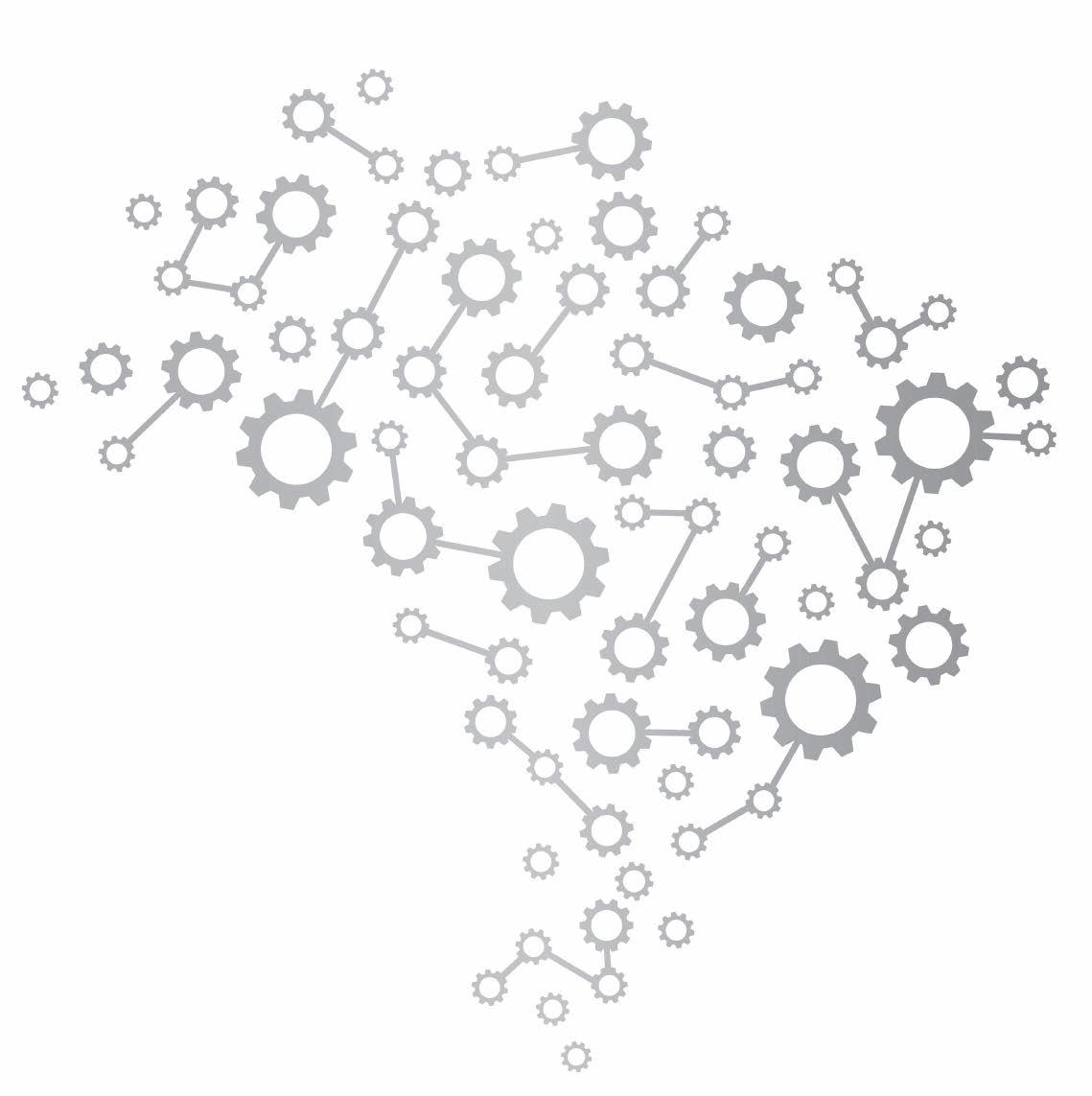
Discussion
The results of the tests discussed in 4.1 and 4.2 proved that MoS2 stimulates running-in process by promoting wear on projections to achieve a stable surface condition. Although it seems contradictory to the well-known wear preventive property of MoS2, it often promotes wear when used in combination with EP additives as mentioned above9).
It is evident from no wear progression with grease B (with additives other than MoS2) that other additives in the formulation exhibited wear preventive property. As for grease A, MoS2 probably overwhelmed the wear preventive property of other additives and promoted wear on projections due to antagonism with other additives as indicated by Bartz.
In the SRV tests discussed in 5, the wear behavior of 12.5 μm MoS2 varied more with changes in content compared to 1.9 μm MoS2. Again, the wear behavior at low content seemed to be attributed to antagonism with other additives. It should be considered that wear did not progress further when MoS2 content increased because the wear preventive property inherent in MoS2’s nature dominated the action of other additives. Given the fact that MoS2 is known to exhibit wear preventive property through the cushion action of solid particles8), larger MoS2 particles could have filled the surface pits to form apparent smooth surface and avoided wear on projections.
For the purpose of flaking life extension, selecting the appropriate MoS2 particle size and content depending on lubrication condition and track surface roughness can ensure sufficient wear on projections with a minimum contact pressure.
Conclusion
In this study, MoS2 and organic molybdenum were found to have a beneficial effect on running-in process through the bench and SRV tests to evaluate wear property of CV joint greases. Improved running-in process to mitigate stress concentration on projections is of benefit in flaking life extension. MoS2 has long been used in a CV joint grease and there has so far been no candidate additive to replace MoS2. In today’s circumstances where automotive parts are becoming smaller and lighter giving themselves severe condition than ever before and flaking life extension has been one of the most important issues, MoS2 is expected to remain the primary additive to ensure reliable CV joint operation.
References
1. Ikeda, T., NTN Technical review, 70, 8 (2002)
2. Hatakeyama, K., NLGI spokesman, 56, 232 (1992) 3. Yoshihara, M., NLGI spokesman, 76, 5, 14 (2012) 4. Taniguchi, A., Kondo, S., and Dong, D., NLGI spokesman, 68, 11, 12 (2005) 5. Fish, G., Euro Grease, May/June, 26 (1997) 6. Garnham, J.E., SAE Technical paper, 960572, (1996) 7. Sayles, R. S., Proceedings of the Institution of Mechanical Engineers, Part J, 209.149 (1995) 8. Bartz, W. J., ASLE Transactions., 15, 207 (1972) 9. Bartz, W. J., NLGI spokesman, 53, 9, 408 (1989) 10. Cusano, C., and Sliney, H. E., ASLE Transactions., 25, 2, 190 (1982) 11. Cusano, C., Goglia, P. R., and Sliney, H. E., ASLE Transactions., 27, 3, 227 (1983) 12. Kuhnell, B.T., and Stecki, J.S., Tribology Transactions, 31, 3, 324 (1988) 13. Soda, N., and Yamashita, M., Junkatsu , 21, 2, 116 (1976) 14. Nagamura, K., Terauchi, Y., Nagasaki, Y.,, and Ninomiya, S., The Japan Society of Mechanical Engineers(C), 58, 548, 223 (1992)
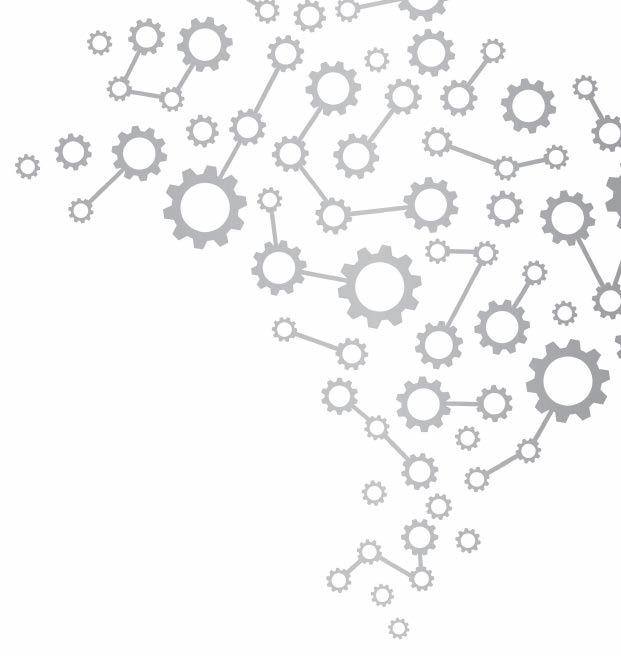
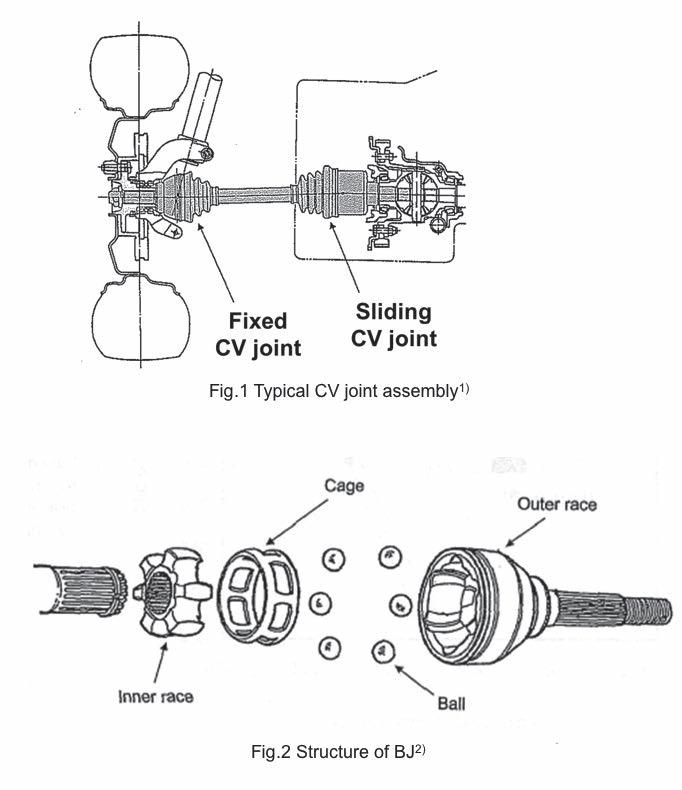
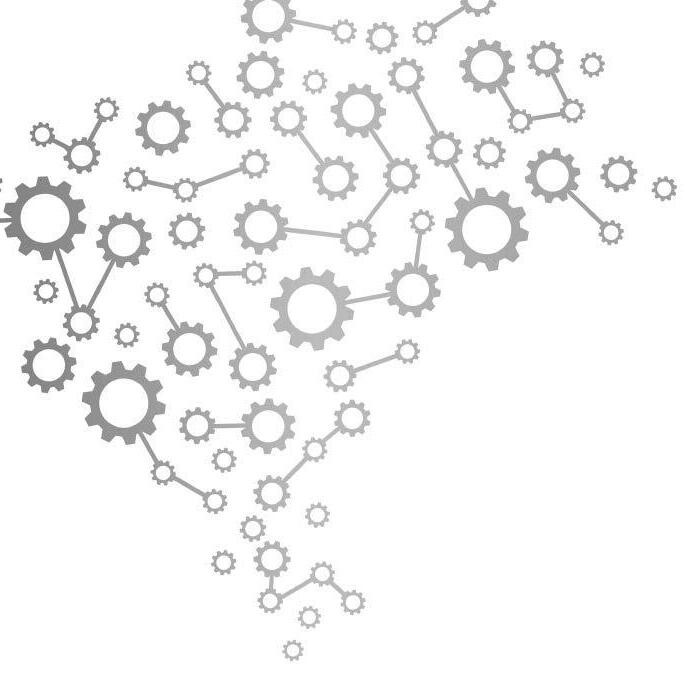
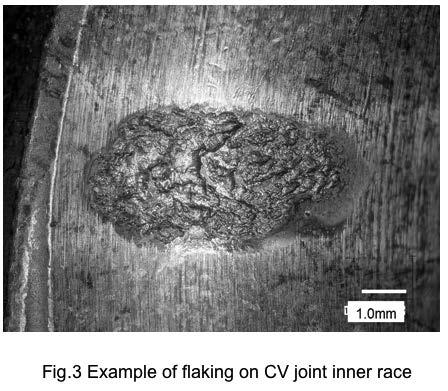

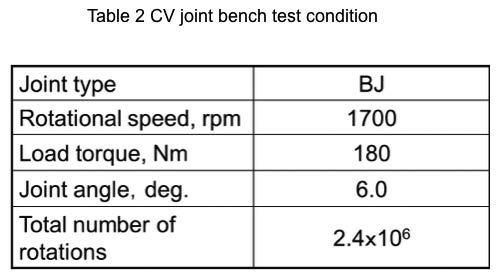


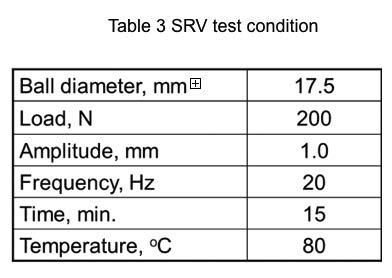
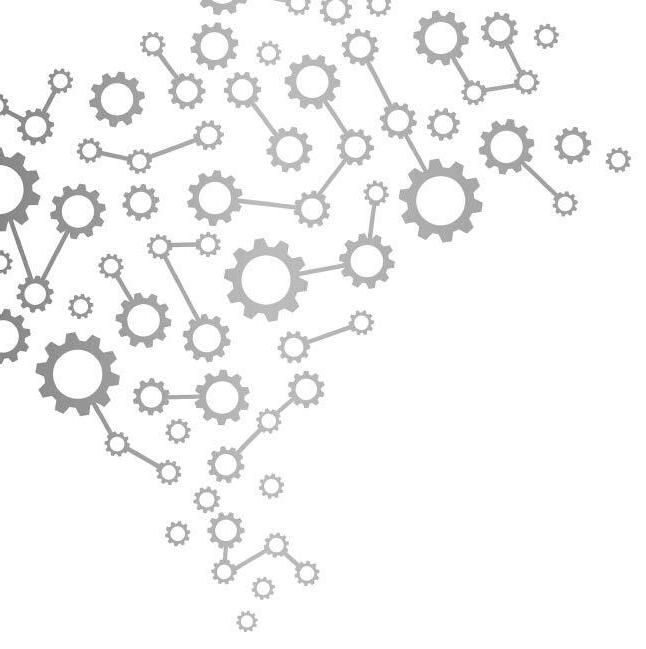
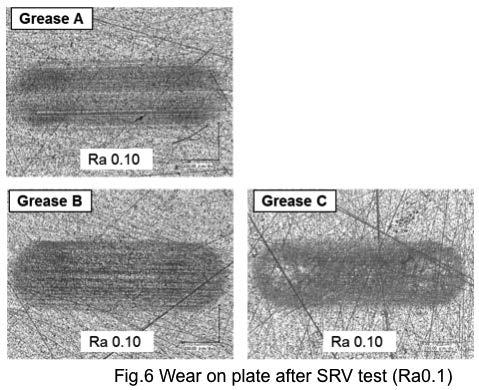
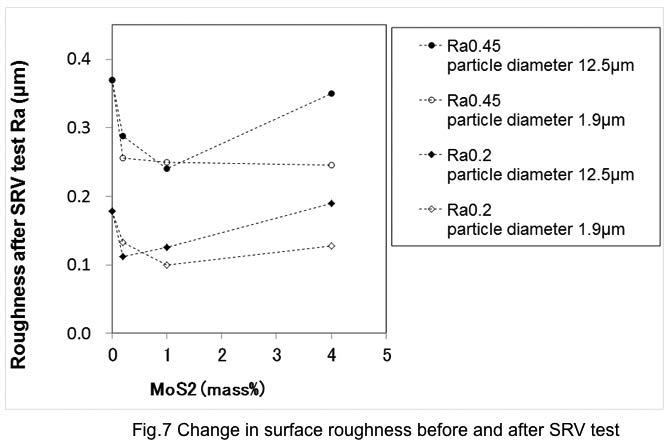
Missed the 2015 NLGI Annual Meeting?
You missed a great meeting! We hope you can join us next year as we go to the historic Homestead Resort, which will be celebrating its’ 250th Anniversary!
The Homestead Resort Hot Springs, Virginia, USA June 11 - 14, 2016 http://www.omnihotels.com/hotels/homestead-virginia
StatementofOwnership,Management,andCirculation
Publication Title: NLGI Spokesman Filing Date: 10/30/2015 Publication No.9331-900 Issue Frequency: Bi-Monthly
No. of Issues Published Annually: 6 Annual Subscription Price: $65.00 Domestic, $109.00 International Complete Mailing Address:
NLGI 249 SW Noel Street, Suite 249, Lee's Summit, MO 64063 Editor (Name and Complete Mailing Address)
Kimberly Hartley 249 SW Noel Street, Suite 249, Lee's Summit, MO 64063 Publication Name:NLGI Spokesman Issue Date for Circulation Data Below:September/October 2015
Extent and Nature of Circulation AverageNo.CopiesEachIssue DuringPreceding12Months ActualNo.CopiesofSingleIssue PublishedNearesttoFilingDate
TotalNo. Copies (NetPress Run)
TotalPaidand/orRequestedCirculation 1200 1200 930 930
Total Free Distribution byMail 14 14
Total Distribution 944 944
Copies Not Distributed(leftovers)
PercentPaidand/orRequestedCirculation 256
256 98.52% 98.52%
SignatureandTitleofEditor,Publisher,BusinessManagerorOwner Date

10-30-2015
The 2014 NLGI Grease Production Survey is here!
The NLGI Grease Production Survey is now available for purchase. Members may download the Survey free of charge by visiting the Members Area of the NLGI Website, for non-member companies the cost is $150. The Survey covers the calendar years 2014, 2013, 2012, and 2011. For ordering information, please visit the NLGI website, https://www. nlgi.org/NLGI_store/