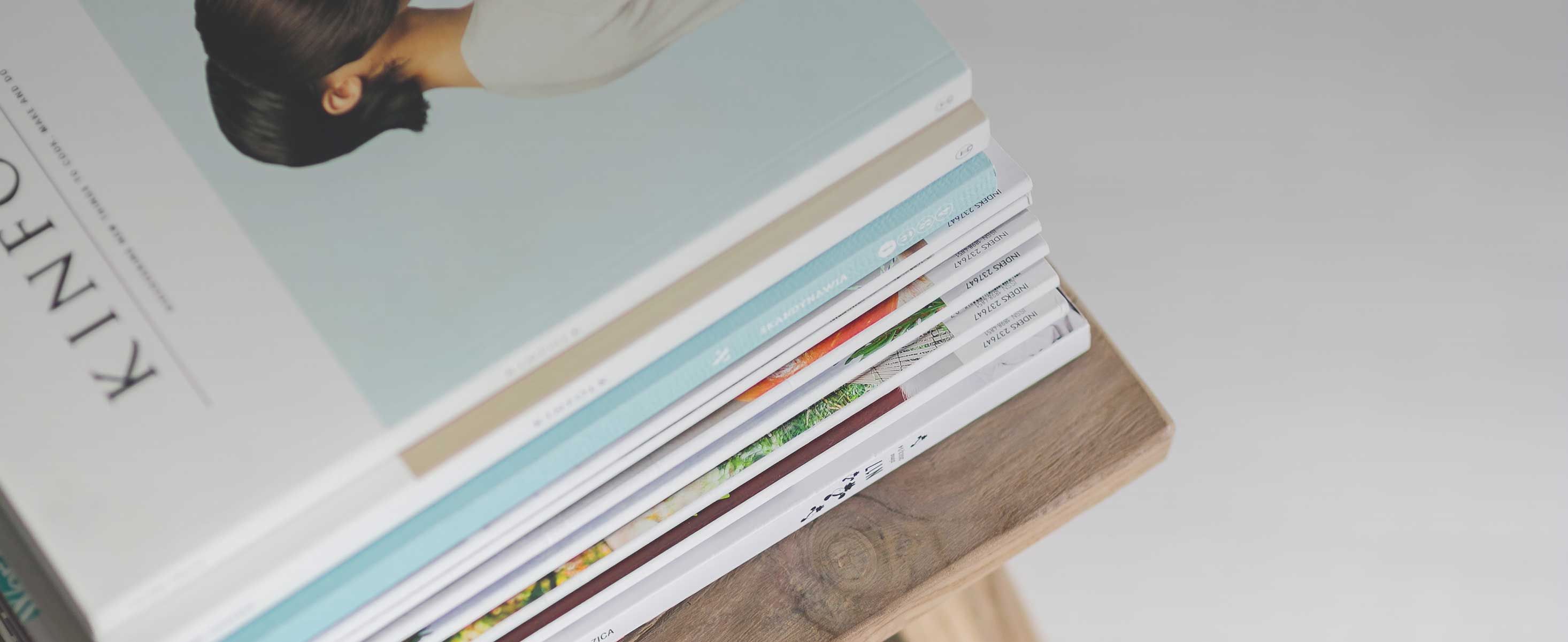
5 minute read
Meeting the Challenges Posed by Environmentally Acceptable Lubricants: Thickener Systems for Unsaturated Polyol Ester Based Oils Mark Wilkinson &
Meeting the Challenges Posed by Environmentally Acceptable Lubricants:
Thickener Systems for Unsaturated Polyol Ester Base Oils
Mark Wilkinson & Steve Nolan
R S Clare & Co Ltd Liverpool, Englandt
Introduction
ἀere has been an increasing and continuing trend in recent years towards biodegradable, low ecotoxicity greases. ἀe recent introduction of the Vessel General Permit (2013) regulations, which mandate the use of Environmentally Acceptable Lubricants, has focussed the grease industry’s attention on the issue of formulating such greases.
A wide range of biodegradable base oils has been available for many years. However, substantial market penetration has been limited by a combination of commercial and technical challenges. ἀe commercial challenge has been the high price of most biodegradable base oils; high performance esters, such as the fully saturated diesters used in hightemperature applications, are several times as expensive as typical Group I or Group II mineral oils. Even with regulation requiring the use of biodegradable base oils, such a price difference will present a substantial commercial obstacle to their use.
ἀe most commercially attractive – in other words, the cheapest – biodegradable base oils are vegetable oils and their synthetic analogues, the TMP esters. Vegetable oils have been assumed to present difficult technical challenges for manufacturers; the poor thermal and oxidative stability of the polyunsaturated component has deterred investigation of their use as bases for lithium soap greases. Synthetic TMP oleate appears to offer a useful compromise for such greases, with better stability than vegetable oils and lower price than saturated diesters.
An alternative approach would be to reduce the thermal stress on the oil by use of a different soap. A lithium/calcium mixed base soap would typically reduce the maximum temperature required during processing by 10-15 °C; using an anhydrous calcium soap would reduce the temperature by 50 °C or more compared to a pure lithium soap. Where the grease is not intended to be subjected to high temperatures – and this will include most marine applications impacted by the VGP regulations – such thickener systems would seem to be appropriate.
We have therefore decided to
investigate the formulation and behaviors of three base oils: rapeseed oil as a typical lowcost commercial vegetable oil, high oleic sunflower oil as a mid-range low polyunsaturated vegetable oil, and trimethylolpropane trioleate as the high stability synthetic analogue. ἀese have been prepared in combination with three thickener systems: a pure lithium 12-hydroxystearate soap, a mixed base lithium/calcium 12-hydroxystearate soap, and a pure anhydrous calcium 12-hydroxystearate soap.
Our initial intent was to concentrate on the physical properties of the basic greases – penetration, shear stability, oil separation, etc. - and to investigate the impact of adjustments in the soap formation step of the manufacturing process, especially with regard to the mixed base grease. However, some unanticipated – indeed, rather surprising – initial results led us to focus more on the stability and performance of the pure lithium grease.
Initial Formulations
All nine of the initial greases were intended to be prepared to a common formulation. ἀe stages were:
• 600g of base oil and 80g of commercial 12-hydroxystearic acid heated to 90°C with stirring on a hotplate • A suspension of the base (either 10g of calcium hydroxide, 5g of calcium hydroxide and 5.7g of lithium hydroxide monohydrate, or 11.4g of lithium hydroxide monohydrate) in 20g of water added to the oil/acid mix • ἀe temperature was held at 90-95°C for 2 hours to ensure complete reaction of the base and acid • ἀe temperature was increased to 130°C and held for 30 minutes to dry the soap • ἀe temperature was increased to completely melt / dissolve the soap (150°C for the pure calcium soap, 195°C for the mixed base soap, 205°C for the pure lithium soap) and held for 15 minutes • ἀe grease was shock chilled by addition of 310g of base oil and allowed to cool to 100°C • ἀe grease was sheared at 1500 rpm in a mixer for 15 minutes and allowed to stand overnight before testing.
Initial Results
(Limited to visual observations and basic test data – much further data to follow in final paper)
ἀ e first unanticipated result was that it appears that conventional production method cannot form an anhydrous calcium grease in either of the vegetable oils. ἀe calcium 12-hydroxystearate, upon melting, will not dissolve or disperse in, even at elevated temperatures; it remains as a viscous and separate phase. Addition of the chilling oil
precipitated the soap as a solid. As a result, no testing of the physical properties was possible or meaningful. It was possible, with difficulty, to produce a grease-like consistency with the calcium soap in TMP trioleate; however, the soap dispersed very poorly and the consistency of the end product was semi-fluid, with an unworked penetration of ??? mm/10.
ἀe mixed base soaps did disperse adequately at 195°C, and formed a grease on shock chilling. ἀe greases were less solid than we had initially expected, although this was less of a surprise following the pure calcium soap results.
ἀe unworked penetration results for the greases are:
Lithium/calcium in rapeseed oil: 338 mm/10
Lithium/calcium in high oleic sunflower oil: 331 mm/10
Lithium/calcium in TMP trioleate: 319 mm/10
ἀe lithium soaps formed well. ἀe unworked penetration results for the greases are:
Lithium in rapeseed oil: 271 mm/10
Lithium in high oleic sunflower oil: 259 mm/10
Lithium in TMP trioleate: 264 mm/10
ἀese soaps provided us with our second unanticipated result. ἀere was much less discoloration due to thermal and oxidative damage than we had anticipated; despite the higher processing temperature, the pure lithium soap greases appeared to be in better condition than the mixed base soap greases. ἀe rapeseed oil grease had only discolored slightly, and the high oleic sunflower oil grease showed no sign of discoloration.
Second Phase results
Following the initial results, we decided to refocus our investigation on the properties and performance of the pure lithium soap greases, since it seemed that they offered the best possibility of a conventional grease using these polyol base oils.
(more data to be assembled – rheology, wear & weld, basic antioxidant packages & performance, spectroscopy)
Conclusion
(to be expanded as later data develops)
It seems that the optimal soap thickener for vegetable oils and synthetic polyol analogues, despite the high temperatures involved, is a pure lithium soap. Conventional manufacturing techniques are adequate, and oxidation appears to be much less of a problem than has been expected. High oleic base stocks, both synthetic and vegetable, appear very well suited for use within the normal temperature ranges expected of a conventional simple lithium greases. Common commodity vegetable oils such as rapeseed oil appear to offer an economical option for greases that are not expected to be exposed to temperatures much above ambient, and approach cost parity with mineral oil formulations.