
16 minute read
Blends: Friend or Foe? Base oil Blends for Grease Formulations
Blends: Friend or Foe?
Base oil Blends for Grease Formulations
Mehdi Fathi-Najafi* Linda Malm, René Abrahams Luis Bastardo-Zambrano
*Corresponding author
Nynas AB Sweden
Abstract
ἀe introduction of Group II and III base stocks, with better oxidation stability and higher viscosity index than Group I base stocks, will create two main drawbacks; lack of solvency (solvent power) and lack of high viscosity. Highly naphthenic oils have been regarded as an excellent solution to these drawbacks. Put simply, it is possible to “kill two birds with one stone”. Nynas has, during the last years, in a number of publications offered some practical solutions to these forthcoming obstacles.
ἀe purpose of this work is to compare “side by side” three base oil blends where GrI, GrII and GrIII, in combination with naphthenic, were used for preparation of lubricating greases. Since the target viscosity was 150 mm2/s at 40 ºC, a naphthenic oil was used in order to reach this viscosity. Key parameters in this study were frictional and thermal stability of the base oil blends, as well as low temperature flowability, elastomer compatibility and rheological properties of the corresponding greases. Last but not least, an attempt was made to minimize the thickener content level.
ἀe prepared base oil blends have been thoroughly characterized. ἀe overall results obtained, reveal some interesting aspects of the use of Gr II as a substitute to Gr I for preparation of greases. ἀe outcome of this work emphasizes that blends should be regarded as a great opportunity for grease formulators who are looking for some further development of their current formulations and furthermore, the lubricating grease based on the blend of paraffinic Gr II and naphthenic oil performs better than others.
1. Introduction
ἀe base oil industry has been going through fundamental changes in the last decade. ἀese changes have been marked by the rapid growth in production capacity for Group II and Group III base oils. ἀe total production of Gr I is estimated to fall to about 40% of the total base oil production by the year 2020. ἀis global rationalization of Group I production, and its potential impact on the future availability of paraffinic bright stock, has led several lubricant formulators to start evaluating alternative products. Lubricating greases are, by far, one of the product types that strongly depend on highly viscous oils, especially for industrial and automobile applications. ἀere are of course a few alternatives to bright stocks, such as synthetic oils. But they are expensive, and furthermore, in some applications such as in the case of elastomer compatibility, PAO would probably cause some problems.
Mineral oils used by grease manufacturers can be divided into two major groups, naphthenic oils and paraffinic oils. Of course both categories of base oils have their own advantages and disadvantages. ἀe most important advantages of the naphthenic oils over the paraffinic oils, with the same viscosity and similar aromatic content, are better low-temperature flowability and better solvency.
ἀe contribution of having base oils with good solvency towards the thickener is that less thickener is needed to obtain a certain consistency of the finished product. It is notable that the higher soap content in greases
produced from paraffinic oils may contribute to the mechanical stability. A typical NLGI grade 2 lithium grease, based on a solvent neutral 500 (SN500) Gr I oil, may contain 11-13wt% thickener; while 6-8% thickener is required for an equivalent viscosity oil of naphthenic nature.
ἀe authors believe that the surplus of Group II and Group III base oils is one among a number of market trends that brings some great opportunities to the grease formulators, if they look for blends where naphthenic oils are regarded as part of the solution for a sustainable formulation. A number of key parameters important for the performance of the finished product could be obtained within reasonable cost.
2. Preparation and Characterization of the Base Oils
ἀe target for this study was to compare different oil mixtures, where the main focus was on the possible synergies of the blends between paraffinic oils and naphthenic oil. For this reason, three base oil blends have been prepared by using three paraffinic base oils, representing Gr I, Gr II and Gr III, with one naphthenic oil. ἀe paraffinic oils had different viscosities at 40 ºC; subsequently different wt% of the naphthenic oil was used to obtain 150 mm2/s in viscosity at 40 ºC. ἀe characterizations of the base oil blends cover a wide range of tests. Table 1 shows the characteristics of the three base oil blends that have been used for preparation of greases in this study.
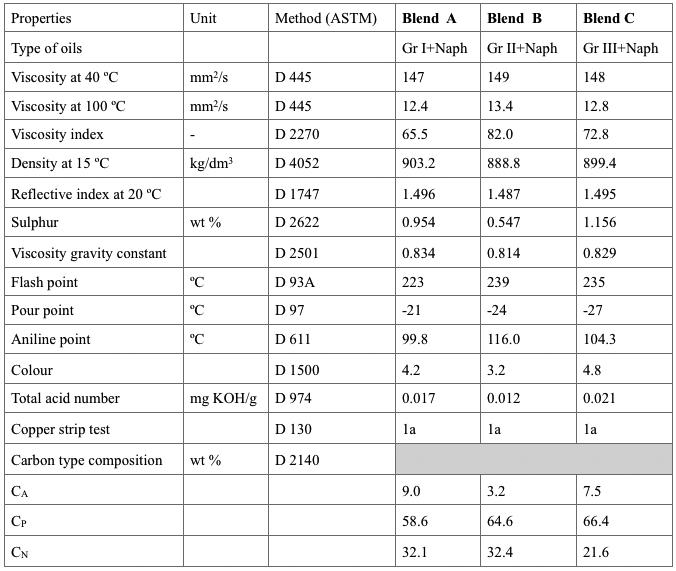
As can be seen in the Table 1, the viscosity of the blends at 100 ºC varies within 1 mm2/s, which is close enough to be regarded as equivalent to each other. It is notable that main impact of the naphthenic oil on the blends could be traced in the parameters such as sulphur content, pour point and aniline point.
2.1 ἀermal stability of the base oil blends
ἀe short term thermal stability of the base oil blends were studied by an in- house method. ἀe method consists of two parts; the first one with copper catalyst (8 grams copper wire) and the second one without. ἀe test duration was 48 hrs, however by loading two samples of each blend, the thermal stability could be controlled after half time or 24 hrs.100 grams of each blend were put in an open beaker in an oven at 100 ºC. ἀen the samples are analyzed, based on change of weight, total acid number (TAN) and colour.
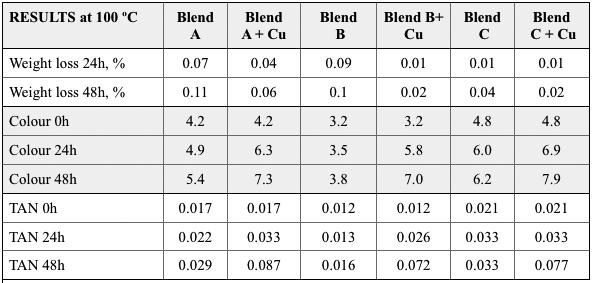
Table 2 shows the obtained results for all three blends
Weight loss: although the weight loss of Blend B and C seems to be slightly better than Blend A, the overall conclusion should be more or less very good for all three blends.
Colour change: ἀe colour was measured according to ASTM D 1500. All Blends with copper catalyst behave similar to each other, namely they ended up to almost the same colour, 7 to 8. However, blends without copper catalyst aged differently. Blend B shows less colour change, 0.6 after 48 hrs. followed by Blend A and Blend C, 1.2 and 1.4 respectively. ἀis colour change may be addressed to the amount of naphthenic oil used in these preparations, since in the last two blends the wt.% of naphthenic oils are higher than in Blend B.
Total Acid Number (TAN): TAN for all blends without copper catalyst are good; however the change of TAN for Blend B is about one third of the other two blends.
A mini traction machine (MTM2, PCS Instruments) has been used to measure the frictional properties of the base oil blends in a mixed rolling/sliding contact.
A load is applied to a steel ball, and with a force transducer the frictional force is measured as the ball is in contact with a steel disc. ἀe Slide to Roll Ratio (SRR) is defined as the percentage ratio between the
sliding speed (difference between the ball speed and the disc speed) and the mean speed. Consequently, 0 % is pure rolling and 200 % is pure sliding. Furthermore, by measuring the traction (friction) as a function of the mean speed at constant SRR, a Stribeck curve can be obtained.


Figure 1. Picture of the ball on the disc (MTM) Figure 2. discribes Stribeck curve
In this study, the friction measurements were performed in a steel/steel contact at 820 MPa and a steel ball with a diameter of 19.05 mm (3/4”) was used. Both the steel ball and the disc where of AISI 52100 steel and had a smooth finish with a roughness less than 0.01 µm (Ra). Four repeat runs were measured, each one after the other, and the mean value of the measurements is displayed. Two tests for each base oil blend were performed and very good agreement was observed for the tests. ἀe temperature was kept constant at 40 ºC for all MTM measurements.

Figure 3 shows the traction coefficient as a function of slide to roll ratio, measured at 40 ºC
Based on the obtained data, described in Figure 3, all three base oil blends show almost similar frictional behaviour at running conditions.
A Stribeck curve was obtained by measuring the Traction coefficient of the blends as a function of speed at constant SRR (50%), see Figure 4. ἀis Figure indicates a slightly lower traction coefficient for blend B.
Electrical Contact Resistance (ERC): ERC describes the degree of separation between the Ball and the Disc in a MTM. Hence, when they are fully separated from each other the voltage at the disc will be the same as the applied one (15 V) and if they are fully separated (100%) e.g. by base oil, then the balance resistor will be 0 V.
Based on the measured ECR, at different speeds, for the three blends, see Figure 5, a better performance for the Blend B at lower speeds can be observed. ἀis measurement reveals that the film thickness of Blend A and C are reduced significantly at lower speeds.
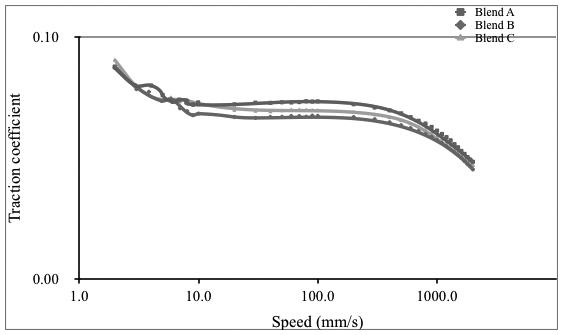
Figure 4 shows the traction coefficient as a function of speed, measured at 40 ºC
Figure 5 shows the separation of disc and ball during the Stribeck run.
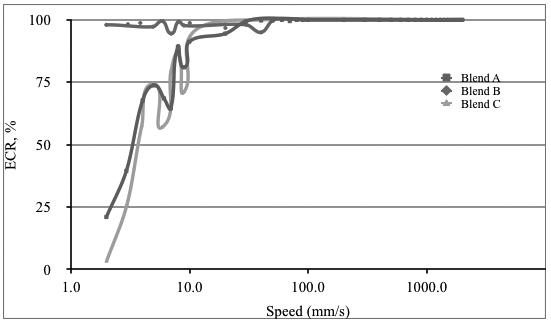
ἀe three base oil blends (A, B and C) have been used for preparation of lithium based greases in an open kettle. Grease A corresponds with base oil Blend A, Grease B with base oil Blend B and finally Grease C with base oil Blend C.
In order to make the comparison easier, each blend was used during the entire production of the grease, meaning a blend was used in both cooking and cooling stages.
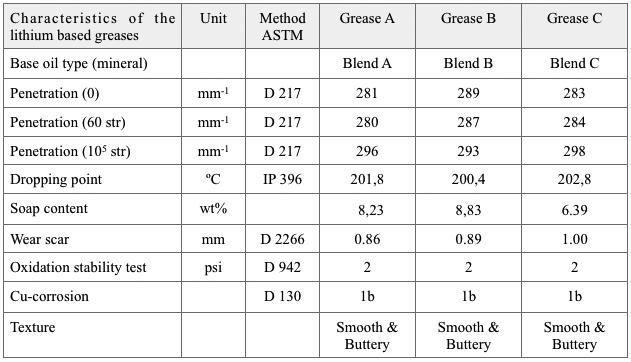
Table 4 shows some of the typical characteristics for the lithium based greases produced with the blends.
Based on the obtained results shown in Table 4, some conclusions may be drawn. Firstly, the moderate level of soap combined with good mechanical stability after 100,000 strokes, although Grease C shows about 25% less soap thanks to higher amount of naphthenic oil; secondly the excellent oxidation stability of all the greases.
ἀe four ball wear tests were carried out by applying a load of 400 N for 60 minutes. ἀe rotational speed was higher 1400 rpm instead for 1200 rpm which is recommended in ASTM D 2266 which may increase the wear scar, however, the measured wear scar for all three greases are in-line within the expected wear scar for a naked lithium based grease.
3.1. Rheological measurements
It is well known that lubricating grease is a viscoelastic material, in other words a material with a viscous part (the base oil) and an elastic part (the thickener). Parameters such as temperature and shear stress affect the oil and the thickener differently. ἀus, flowability of the grease sample under controlled conditions can generate valuable information, such as the storage or elastic modulus (G´) of the grease, which could be interpreted as the real consistency of the grease, at the applied temperature.
3.1.1. Strain Sweep:
In an attempt to compare the dynamic (Shear) stability of the greases rheologically, a strain sweep program was applied in which the frequency and the temperature were kept constant (10 rad/s and 25 °C respectively), and the strain was increased logarithmically from 0.01 to 1000%.
As can be seen in Figure 6 G´ for C, at the starting point, is significantly lower than the other two greases, 13179 (Pa) versus 21794 (Pa) for Grease A and 21626 (Pa) for Grease B, which reflects the level of the thickener content of the greases.
Furthermore, the Linear Viscoelastic Region of Grease A is slightly wider than for Grease B and significantly wider than for the Grease C, which indicates the better shear stability of Grease A. ἀis can also be verified by comparing the Flow point of the Greases, see Table 5.

Table 5 shows the measured Elastic modulus at various stages of the oscillatory tests
ἀe Flow point is obtained when G´=G´´ and/or the phase angle reaches 45 º. At this point the structure of the grease is destroyed and it starts to flow. ἀe higher flow point, the more shear stable the grease is supposed to be. Hence based on the measured data, Grease A is more shear stable than Grease B and C. Furthermore, Grease B and C show the same shear stability despite having significantly different thickener content (about 24% less for Grease C). It is notable that this result doesn’t support the shear stability of the greases after 100000 strokes, see Table 4.

Figure 6 describes the elastic (storage) modulus and the viscous modulus as a function of the strain for the greases.
3.1.2. Temperature sweep:
ἀe low temperature behaviour of the greases was investigated by using a temperature sweep program, from +40 to -25 °C. ἀen the change of G´ as a function of temperature was measured.
Based on the measured storage modulus, Figure 7, all three greases more or less show the same good behaviour down to about -17 ºC, however, as the temperature is dropped further Grease A shows a steep increase of the elastic modulus, or in other words the consistency of Grease A increases faster than the other greases below -17 ºC, while this deviation could not be found in the case of the other two greases (B & C).
Using pour point of the base oil as a tool in order to predicate the performance of a lubricant questioned in the past [4] and the authors recommend rheological measurements should be used instead which is in-line with the finding in e.g. Figure 7.
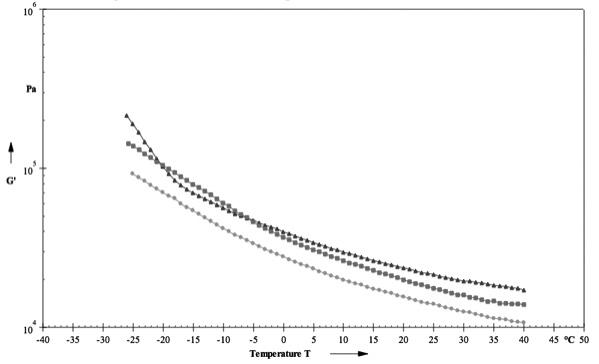
Figure 7. ἀe measured elastic modulus as a function of temperature
Based on the measured storage modulus, Figure 7, all three greases more or less show the same good behaviour down to about -17 ºC, however, as the temperature is dropped further Grease A shows a steep increase of the elastic modulus, or in other words the consistency of Grease A increases faster than the other greases below -17 ºC, while this deviation could not be found in the case of the other two greases (B & C).
Using pour point of the base oil as a tool in order to predicate the performance of a lubricant questioned in the past [4] and the authors recommend rheological measurements should be used instead which is in-line with the finding in e.g. Figure 7.
4. Flow Pressure measurements
In order to simulate the pumpability of the greases, the flow pressure (FP) of the greases at two different temperatures (-20 ºC and -35 ºC) have been measured, according to DIN 51805. ἀe test setup consists of
a conical nozzle that is filled with grease. ἀe nozzle is placed in the measuring instrument, equilibrated for 2-3 hours at a desired temperature, and then an increasing pressure is applied to the nozzle. ἀe threshold pressure at which grease starts to flow through the nozzle is recorded.
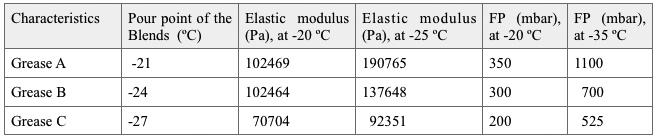
Table 6 shows the low temperature properties of the greases based on different temperatures.
Based on the Rheological study and Flow pressure measurements, all the combinations show very good low temperature properties. However, Grease C (based on Gr III + Naphthenic Oil) shows superior low temperature behavior, followed by Grease B (Gr II + Naphthenic oil), when compared with Grease A (Gr I + Naphthenic).
5. Elastomer compatibility
Chloroprene rubber is one of the most common elastomers used in constant velocity joints application. Hence, the rubber interactions with the lithium grease, based on the three Blends, were conducted through total immersion of the rubber sample in the greases. ἀe test duration was 168 hours at 100 ºC. ἀe change in hardness and weight of the chloroprene rubber samples was measured. Hardness is a measurement of a rubber’s ability to resist penetration of a specified metal rod with a specifically shaped tip or end. In order to measure the change in hardness of the rubber, the IRHD (International Rubber Hardness Degrees) method was used. ἀe scale runs from 0 to 100 degrees were 0 is an extremely soft material and 100 is an extremely hard material. Common rubber values are 30-85 degrees.
Previous publications have shown that the Aniline point of the oil has significant influence on the interaction between the oil, the corresponding grease and the rubber. For example, in the case of Nitrile butadiene rubber, an oil with low aniline point is recommended, while high aniline point is desired for Chloroprene rubber. ἀis part of the work confirms that recommendation. Oil Blend B, used for Grease B, has the highest aniline point (116 ºC), and this is reflected in the obtained results, see Figures 7 and 8.
Figure 7 and 8 show the impact of different greases on Chloroprene rubber after various time at 100 ºC.
6. Summary
ἀree base oil blends have been prepared by using a naphthenic oil and three paraffinic oils, one from each group (Gr I, Gr II and Gr III). ἀe characterization of the blends emphasizes that all three blends have similar properties. However, the thermal stability test which is in fact a static test, and MTM measurements, indicate slightly better performance for Blend B, which contains paraffinic Gr II oil.
ἀe three lithium based greases, which are corresponding with the three base oil blends, show good performance in a number of tests. In the rubber compatibility test, Blend B shows less impact, and therefore should be regarded as a better candidate. Regarding the low temperature behavior of the greases, Grease C seems to be a better product. According to the rheological measurements, see Figure 6, Grease A appeared to be more shear stable than Grease B and Grease C.
ἀis study emphasizes the potential of taking advantage of the ongoing fundamental change within the base oil industry, which has created, and will continue to create, new opportunities to upgrade the current (old) grease formulations, by using blends of paraffinic oils, preferably Gr II, and naphthenic oil.
ἀe surplus of paraffinic Gr II oil, and availability of severely processed naphthenic oils, offers a cost effective solution with extended performance for demanding applications such as in the automobile industry.
Reference
[1] Salomonsson, L., et. al, Oil/ἀickener interaction of chloroprene and nitrilebutadiene rubber with lubricating greases and base oil. Lubricating oil, 2006. 21(54). [2] Serra-Holm V., Development of a novel naphthenic base oil for application in
CVJ greases, NLGI 73rd Annual Meeting, October 2006, FL (US). [3] Sullivan, T., Tighter base oil supply expected in Europe. Lube report 2012. [4] Fathi-Najafi, M., et al., Low temperature tribology. A study of the influence of base oil characteristics on friction behaviour under low temperature conditions. EUROGREASE, 2012. [5] Bastardo-Zambrano L. et.al, Base oil blends to meet the new demands of the lubricant industry, Lubes Magazine No.115 June 2013 [6] Fathi-Najafi M. et.al, When the going gets tough... A heavy specialty oil for grease formulations (Part II), NLGI 80th Annual Meeting, June 2013, AZ (US). [7] http://www.pcs-instruments.com/mtm/accessories/mtm-ecr. shtml#page=page-1
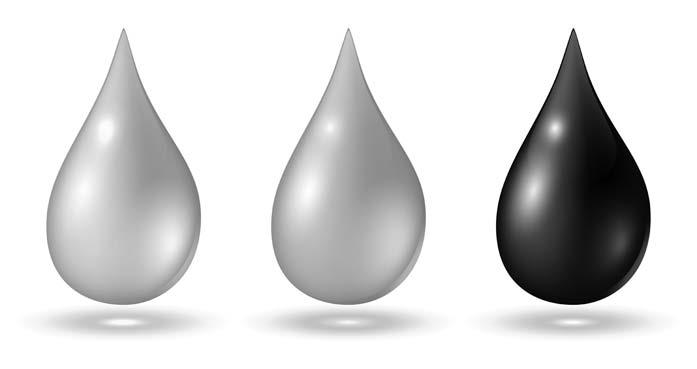