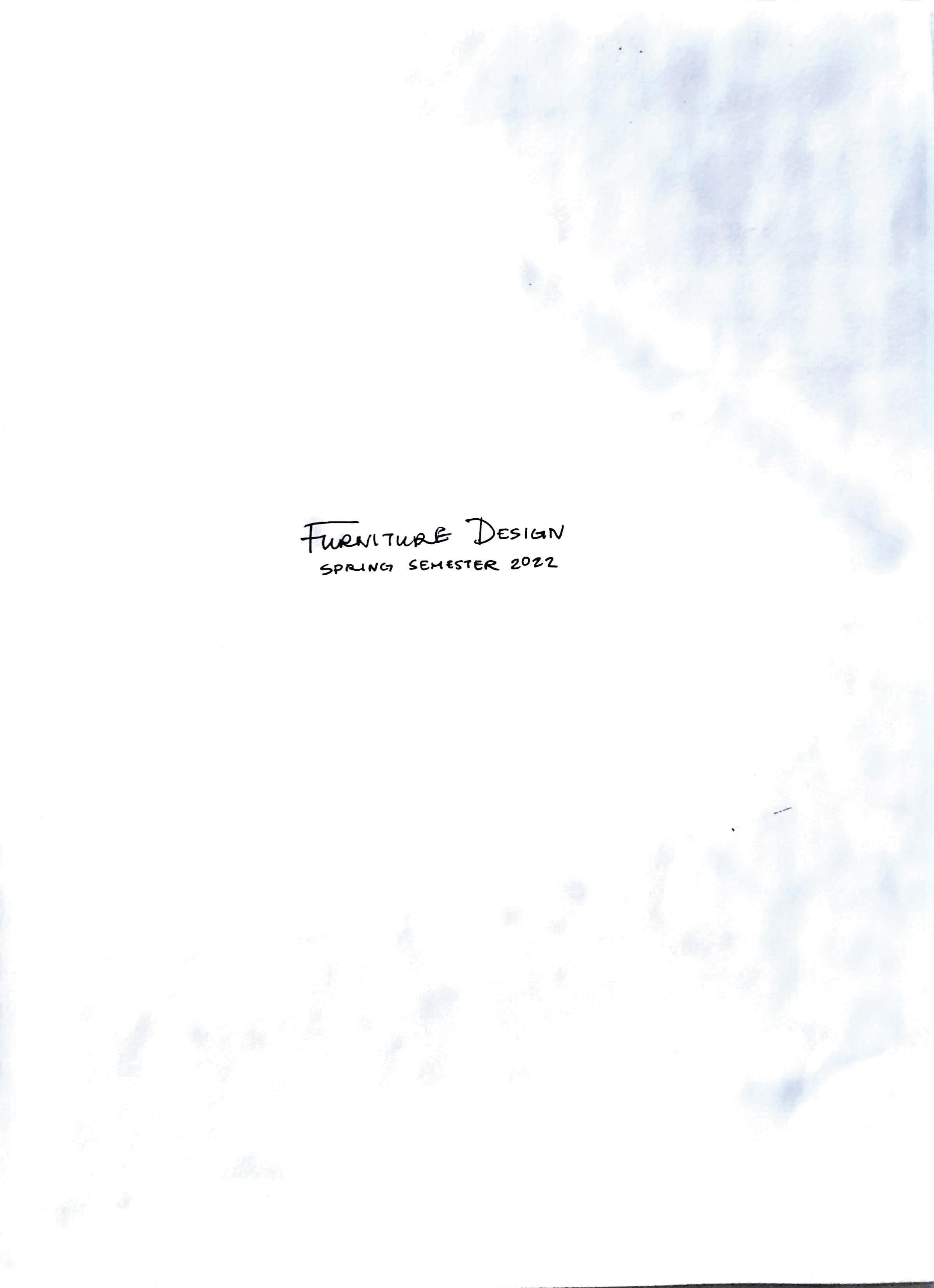
In the art history class, Women in Architecture, taught by Professor Vickery, I was properly introduced to Eileen Gray, an architect born in 1878, in Enniscorthy, Ireland. Gray began her career in woodworking and furniture making, as many women striving to be architects often did. In Professor Vickery’s class, we discussed how sexism in education and the professional environment led to a huge setback for women architects, and often pushed them into other fields that were less male-dominated. I reflected on this lesson and I am grateful for the way I began my architecture education in college as a young woman, and I am treated equally to my male peers.
I also felt a sense of admiration for the passion many architects, like Eileen Gray, had for furniture design. I soon realized how similar architecture and furniture design were.
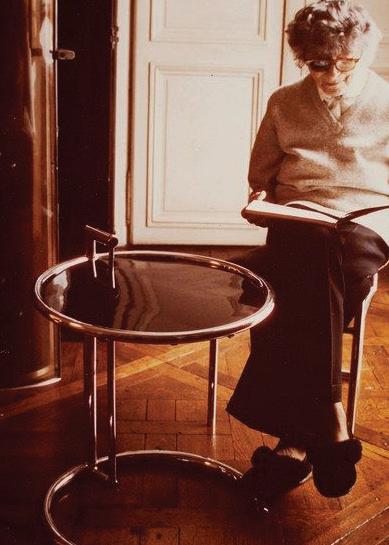
1. Designing a piece that combines function and form, not tied to any fads or trends, but using architecture theory to inform design decisions.
2. Understanding structure, mechanics, and assembly of all components.
3. Maximizing utility in a specific amount of volume/ area.
I believe to enhance an architectural space, you must also understand the architectural elements of the furniture and interior design. In this independent study I wanted to focus the three concepts listed, and create my own piece of furniture inspired by architecture.
EILEEN GRAY, photographed with the E 1027 table The Architect of Desire, W MagazineThrough a few email correspondences and a meeting, Professor Ray Mann signed on to be my independent study advisor. In our meetings discussing the scope of my semester, we set a limit to the size and complexity of my project. Professor Mann warned me about the difficulty of chairs, someone can spend their lifetime perfecting a chair design.



The first limit was to only work with wood. Limiting my materials also limits the complexity of the possible design, and UMass Amherst has a expansive wood-shop, available to anyone who needs it for academic purposes.
While I understood that I shouldn’t put all my energy into a chair design, I also wanted to challenge myself to do more than a table. During my furniture design research, I found myself constantly coming back to the idea of a nested furniture set, specifically a nesting vanity set. This means that the chair and table components can come together to create a compact unit. And under my project scope, I would design the chair to be a simpler stool design to allow me to focus on the entire design. The Dilly Dally Dressing Table Set by Luigi Massoni was a beautiful example. The design was a statement piece and had a gr way of maximizing it’s utility in a small volume.

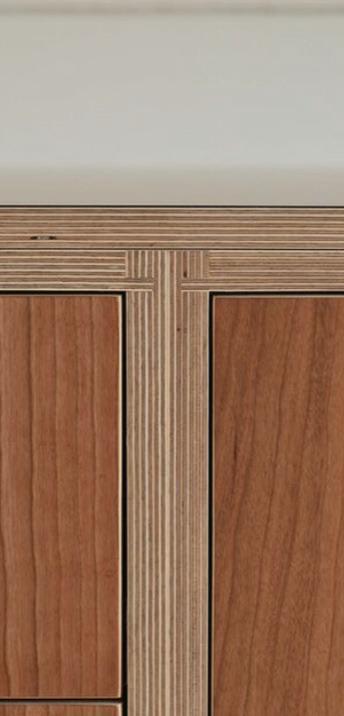

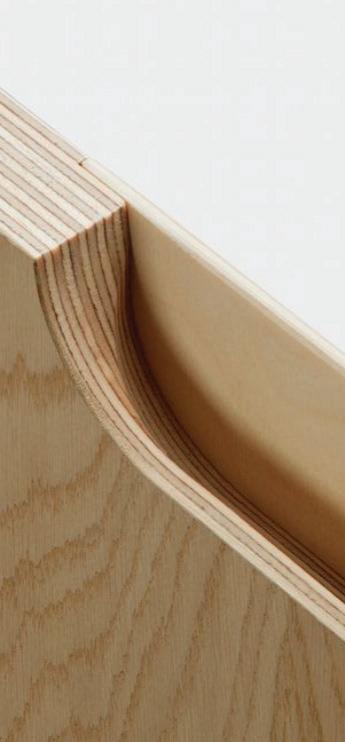
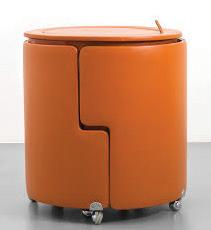
In my research I purchased two books that were recommended by furniture design education websites.
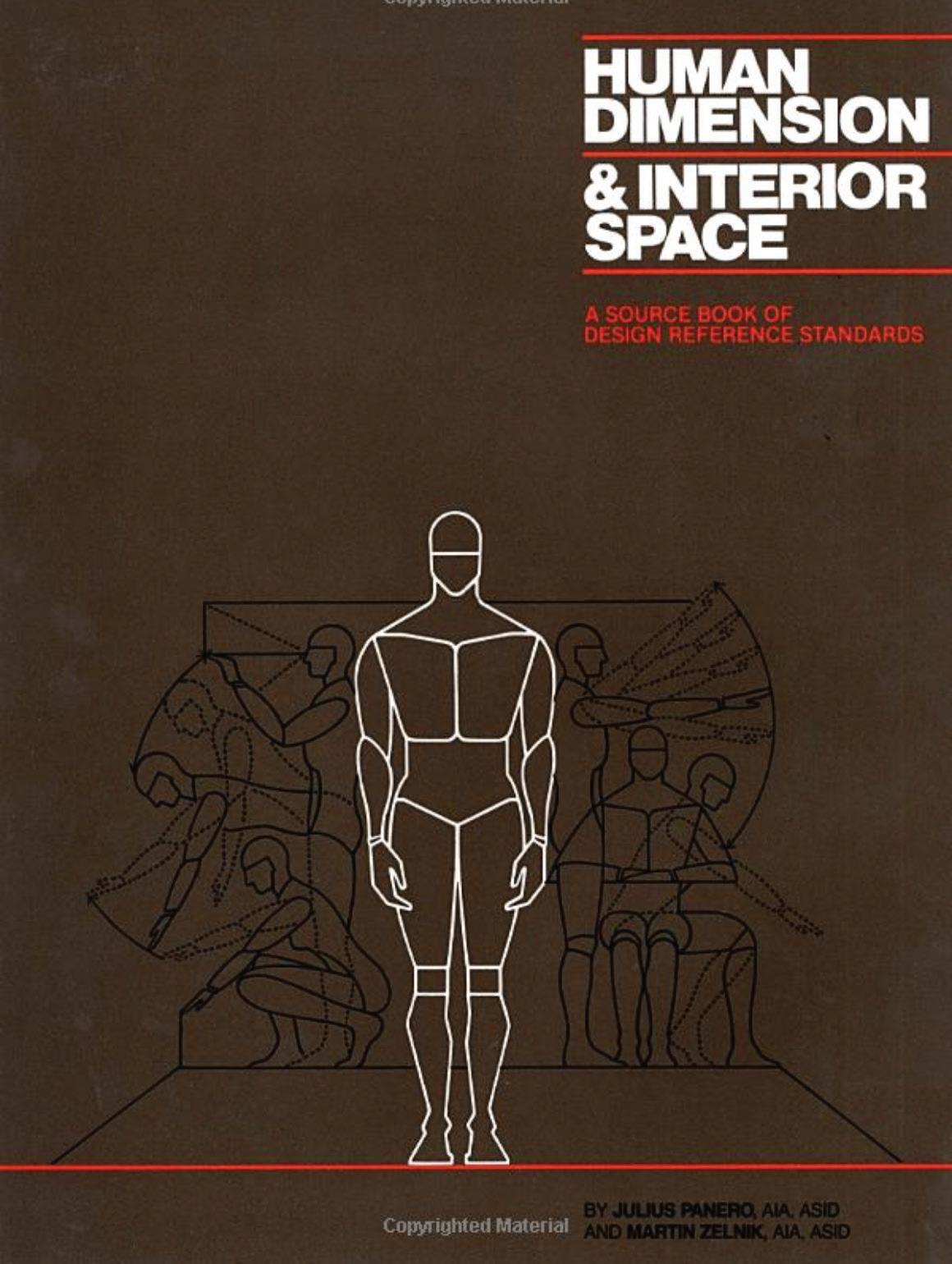
Furniture Studio, Jeffrey Karl Ochsner, 2012
The first, Furniture Studio, discusses a 2009 semester of furniture studio at the University of Washington. I read pieces that discussed the curriculum, problems students ran into, and how to create good designs.

Human Dimension & Interior Space Julius Panero and Marin Zelnik, 1979
The second book, was highly rated as a great reference for the dimension of furniture. While it is a fascinating book, the human dimensions are incredibly outdated. This book also discusses the dimensions of furniture for dentists offices, restaurants, and other public spaces. It specifies differences in public space dimensions for males and females. Overall, this book is very interesting to flip through. But it is rather outdated and I would not recommend it to a prospective furniture student.
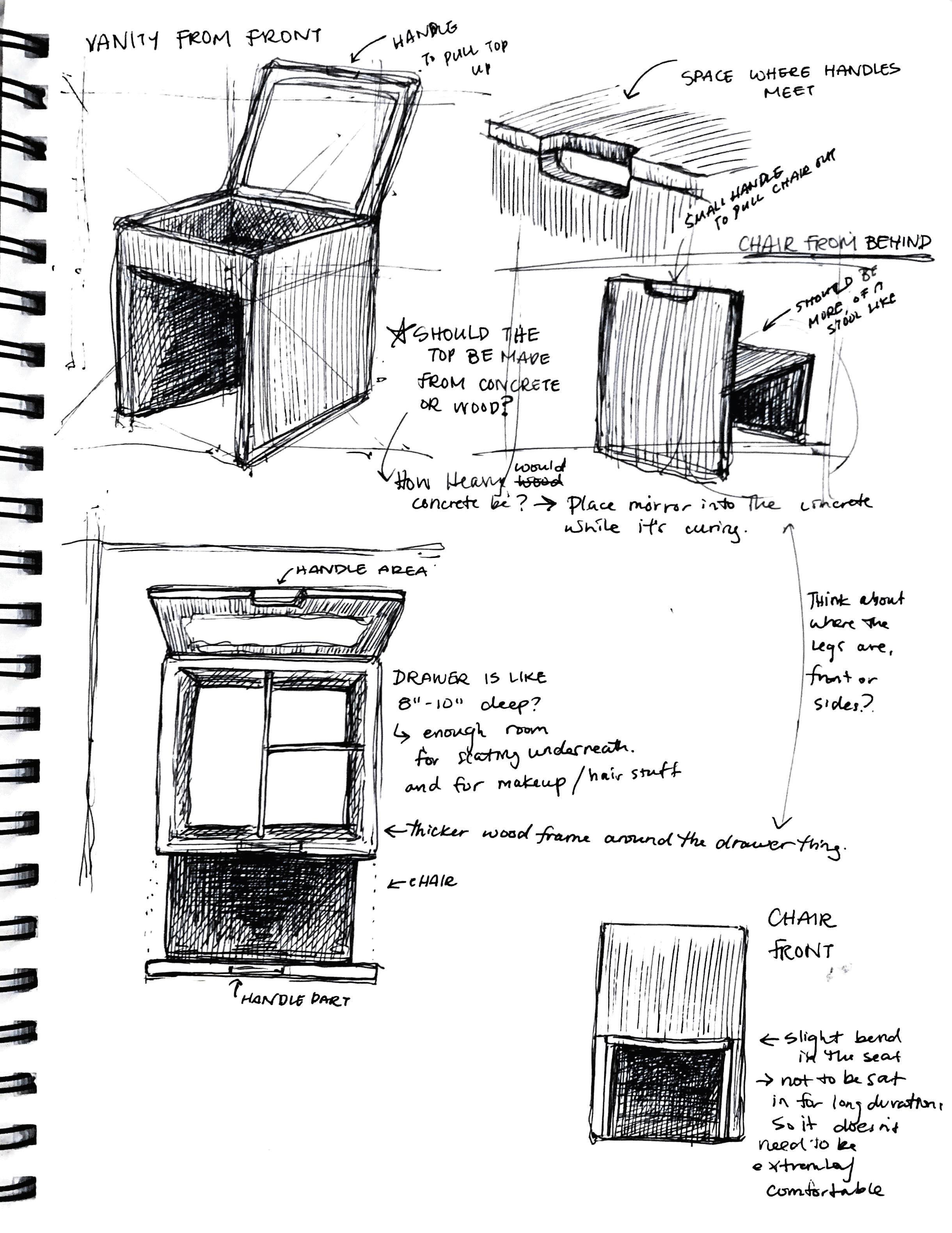
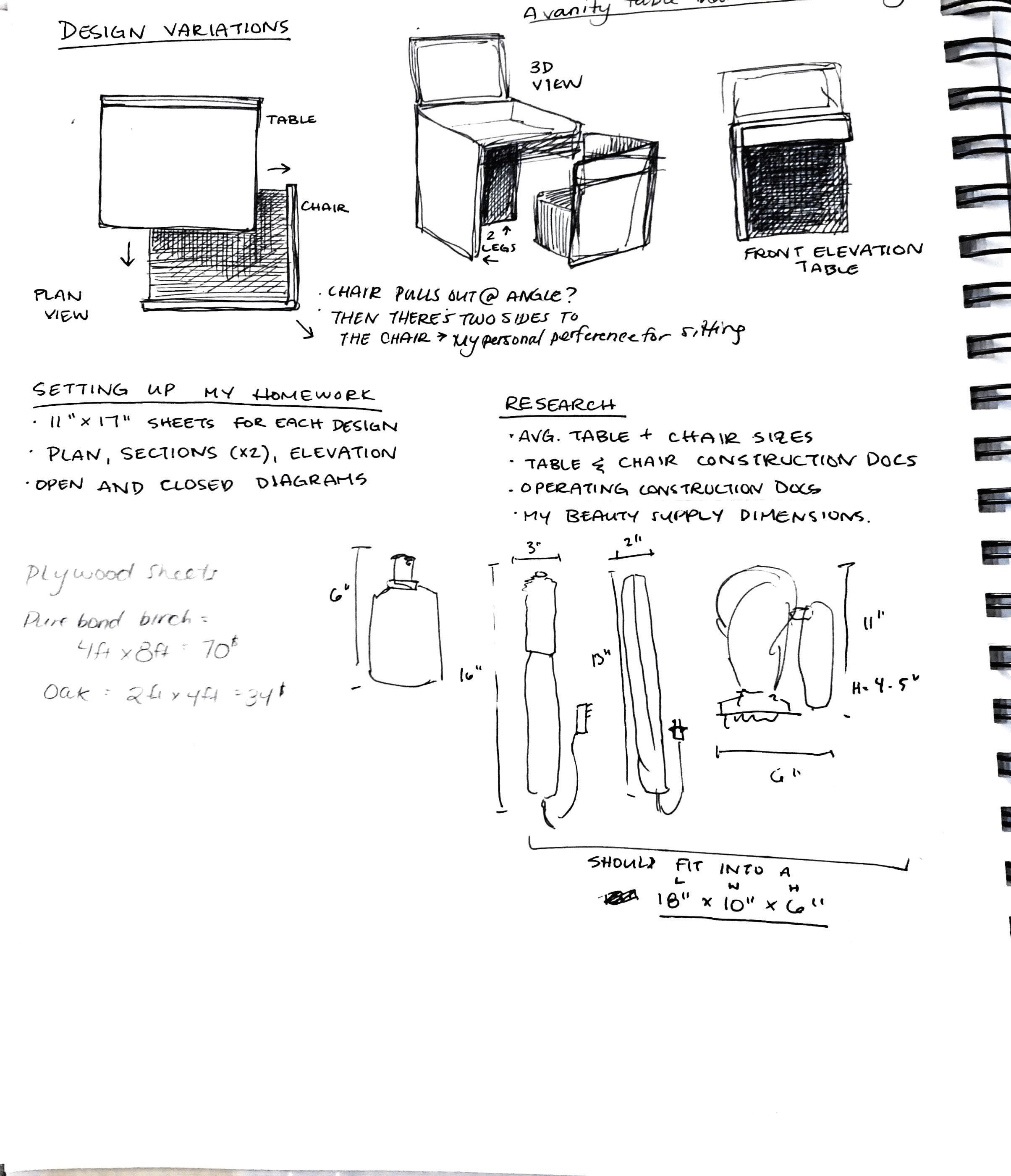



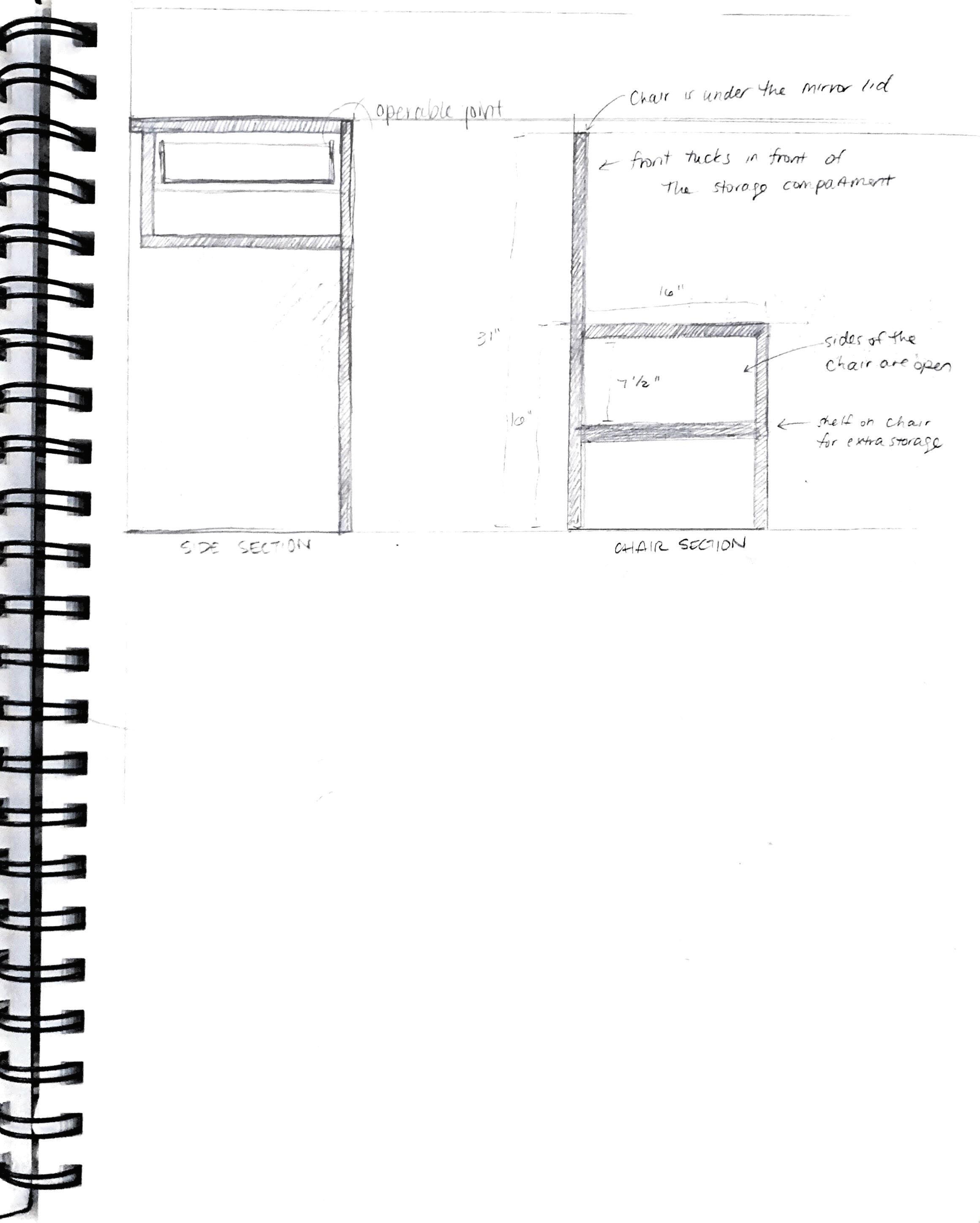
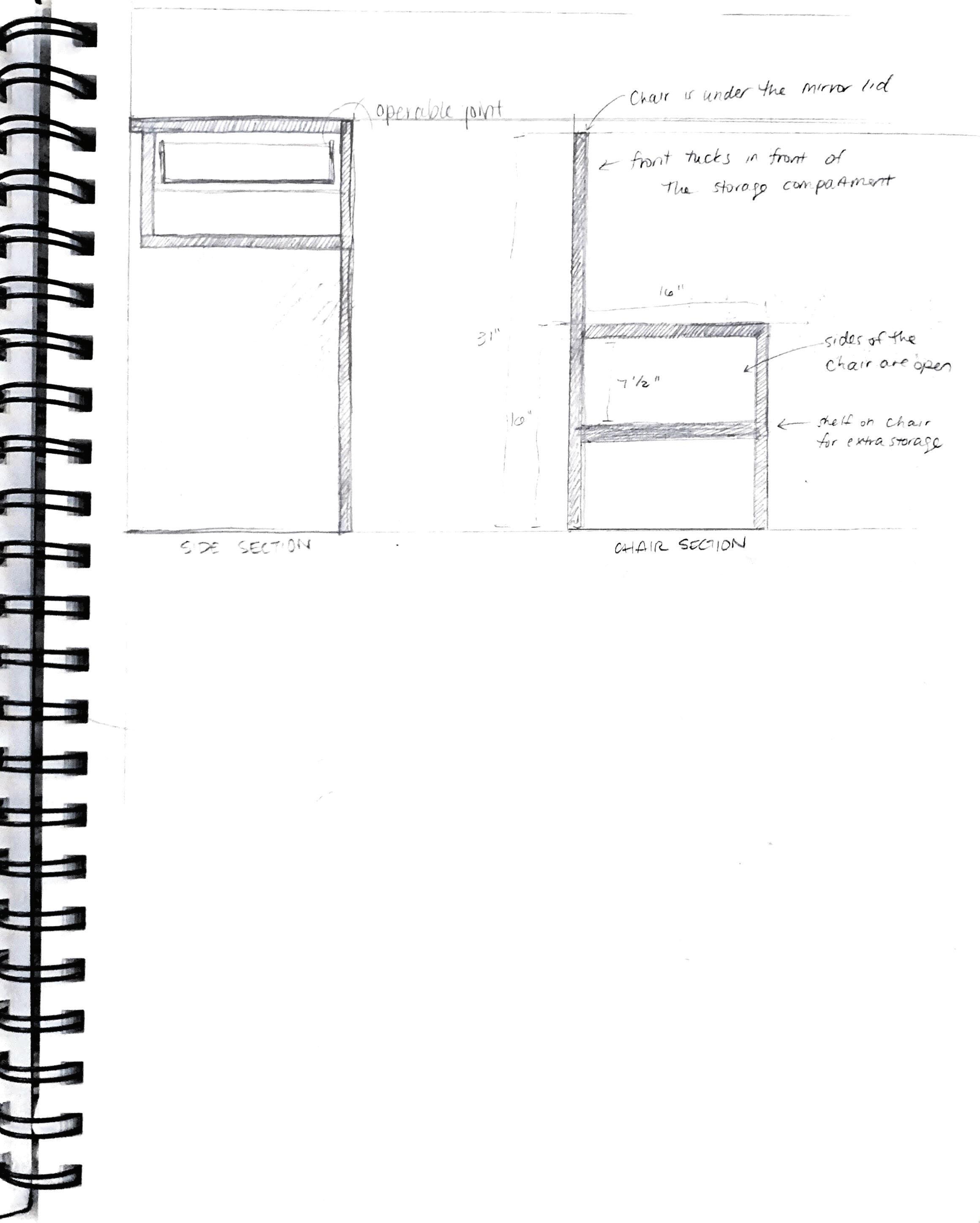
Scale Model, February 2022
I tried to push the boundaries of my design by adding asymmetry. I created scaled drawings to find dynamic shapes, and then built scale models to test the physics of the design. I decided to keep a linear design in hopes it would mean an easier assembly process.
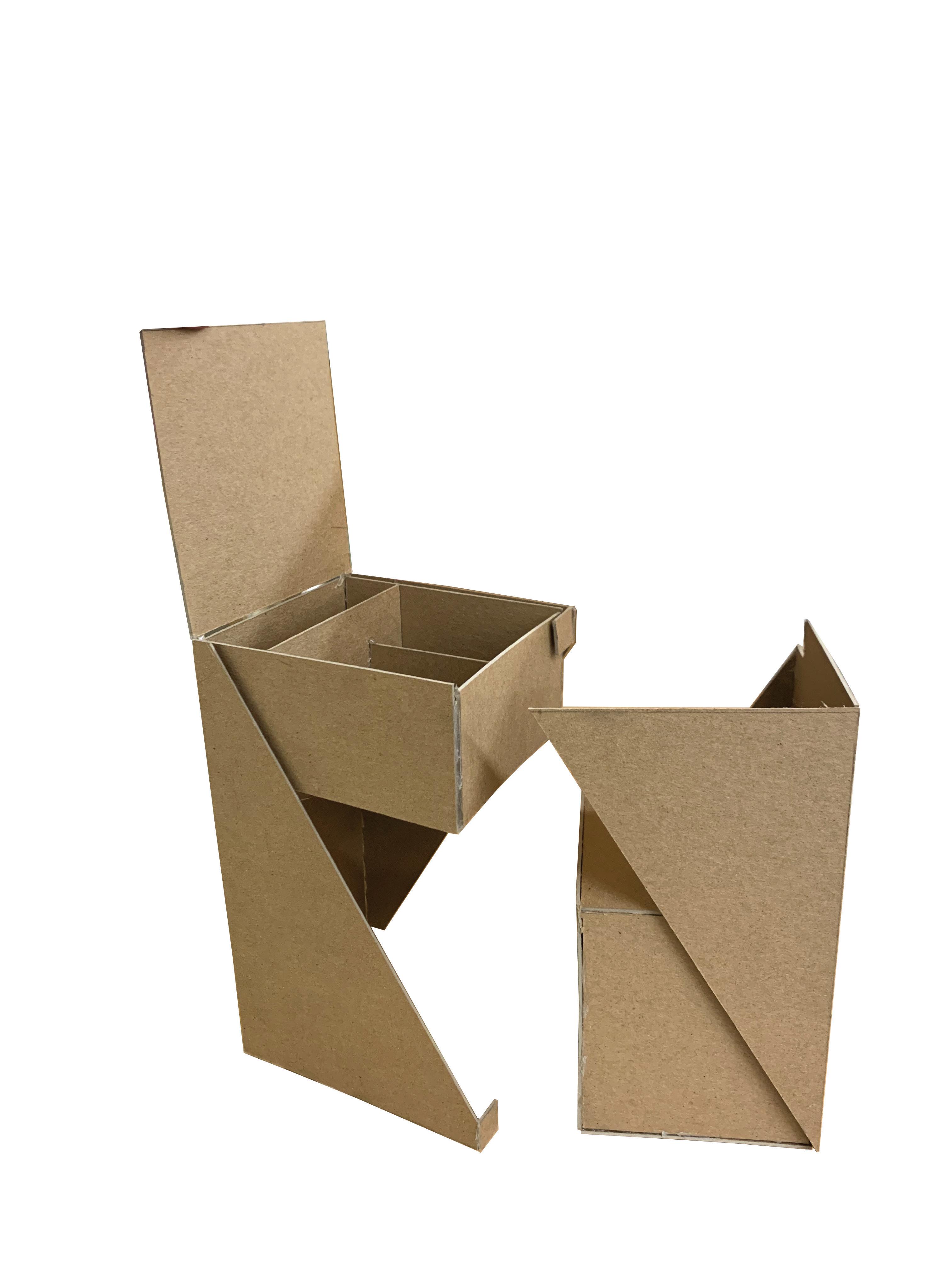
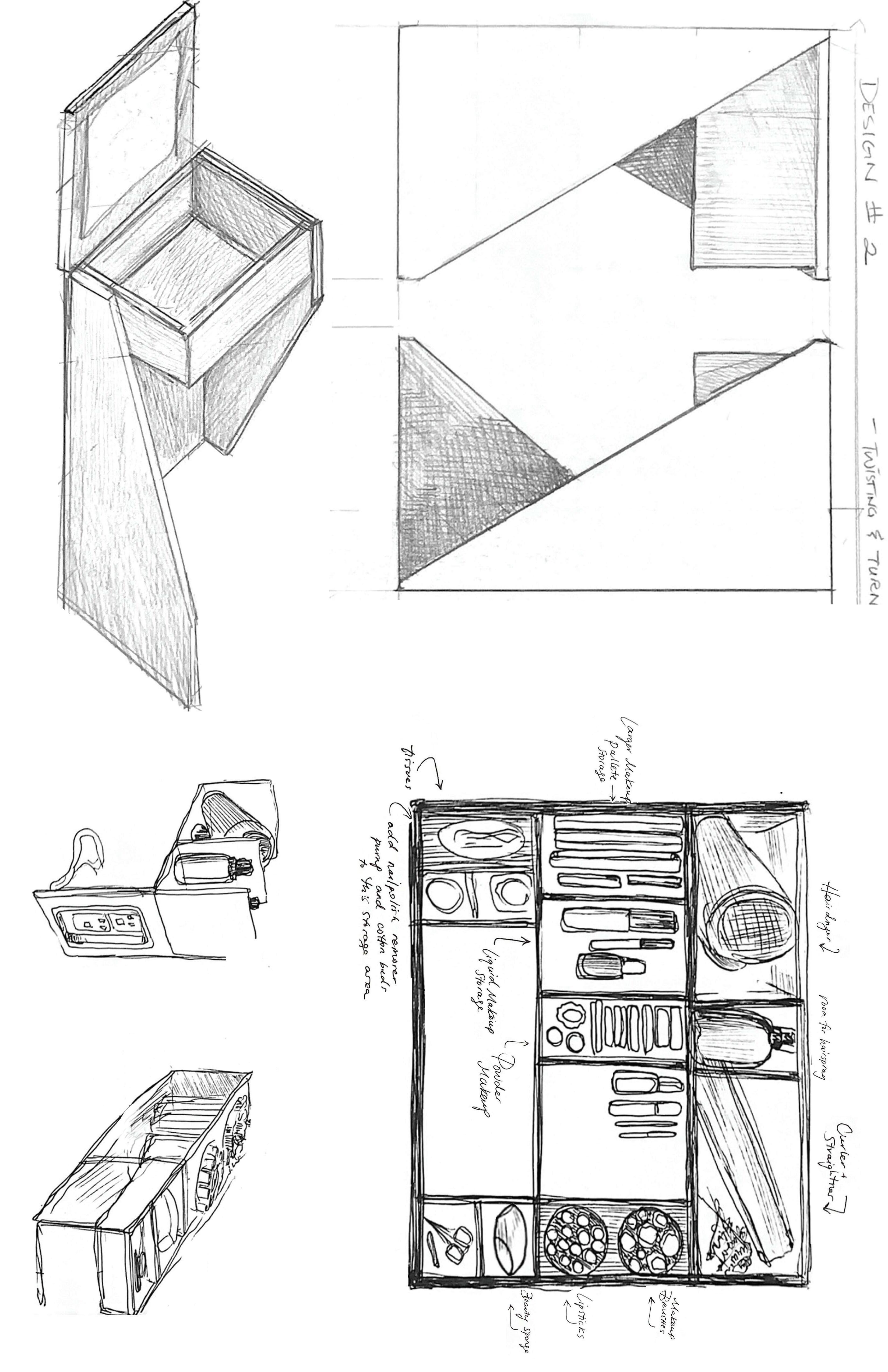
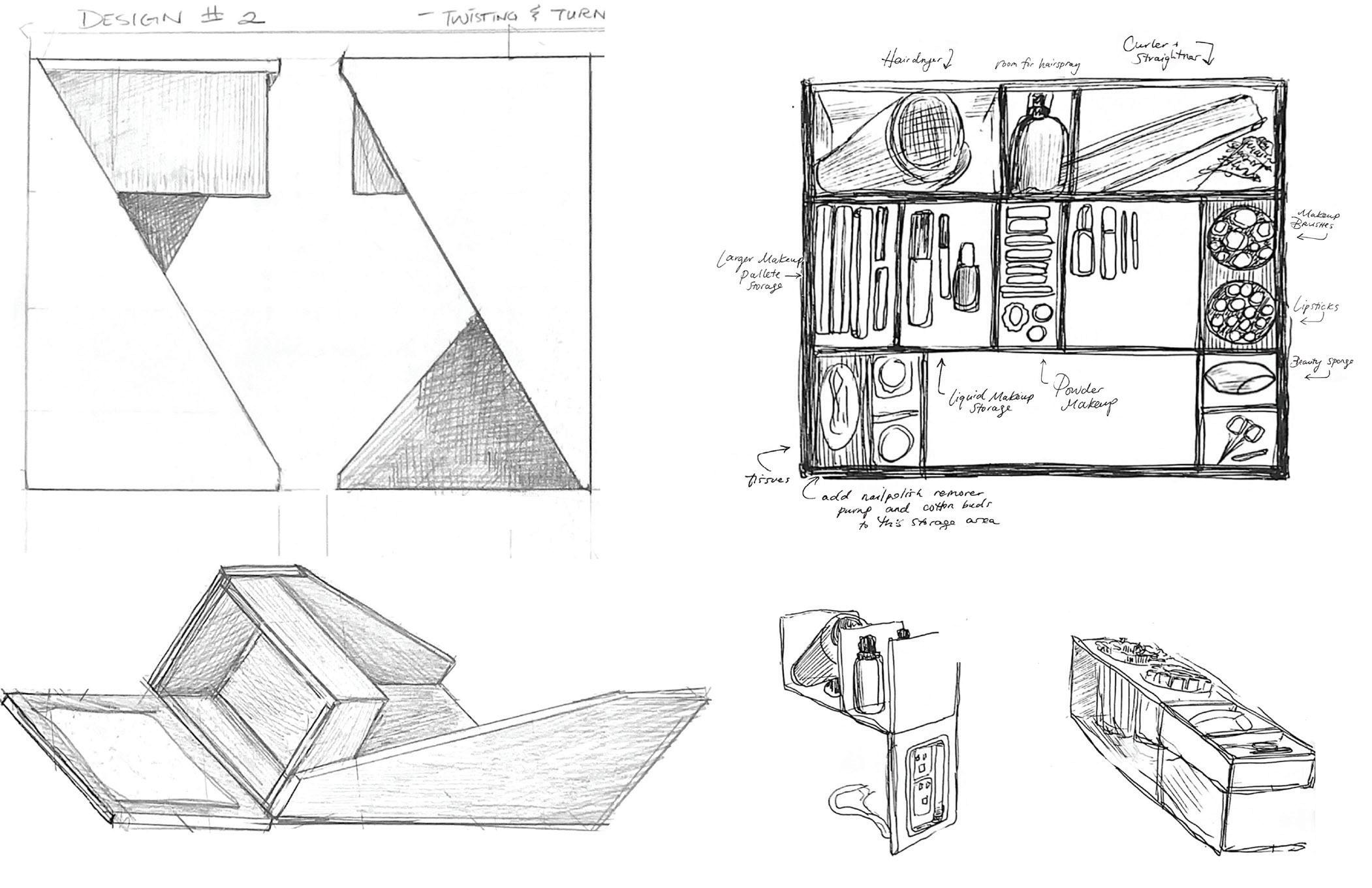
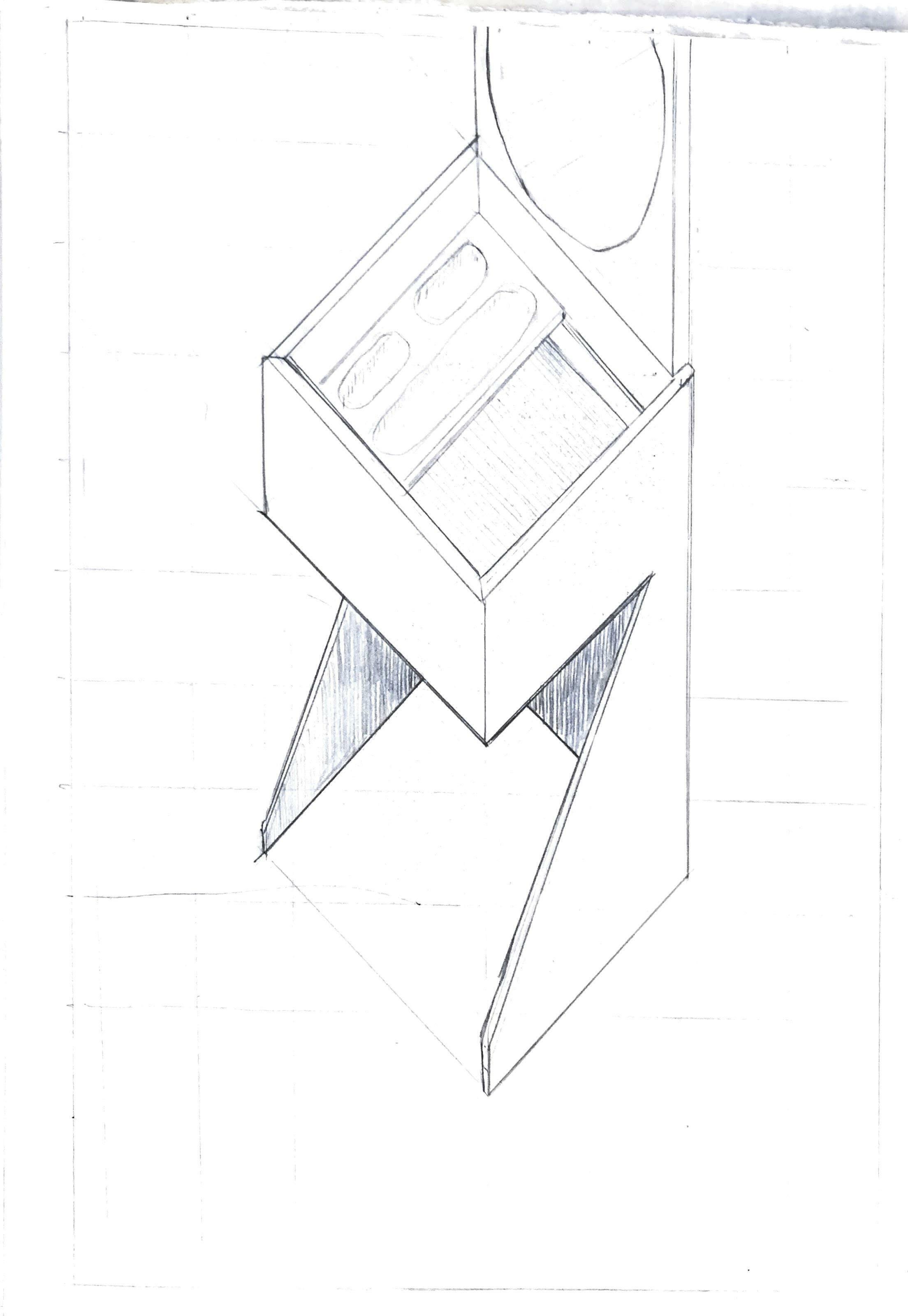
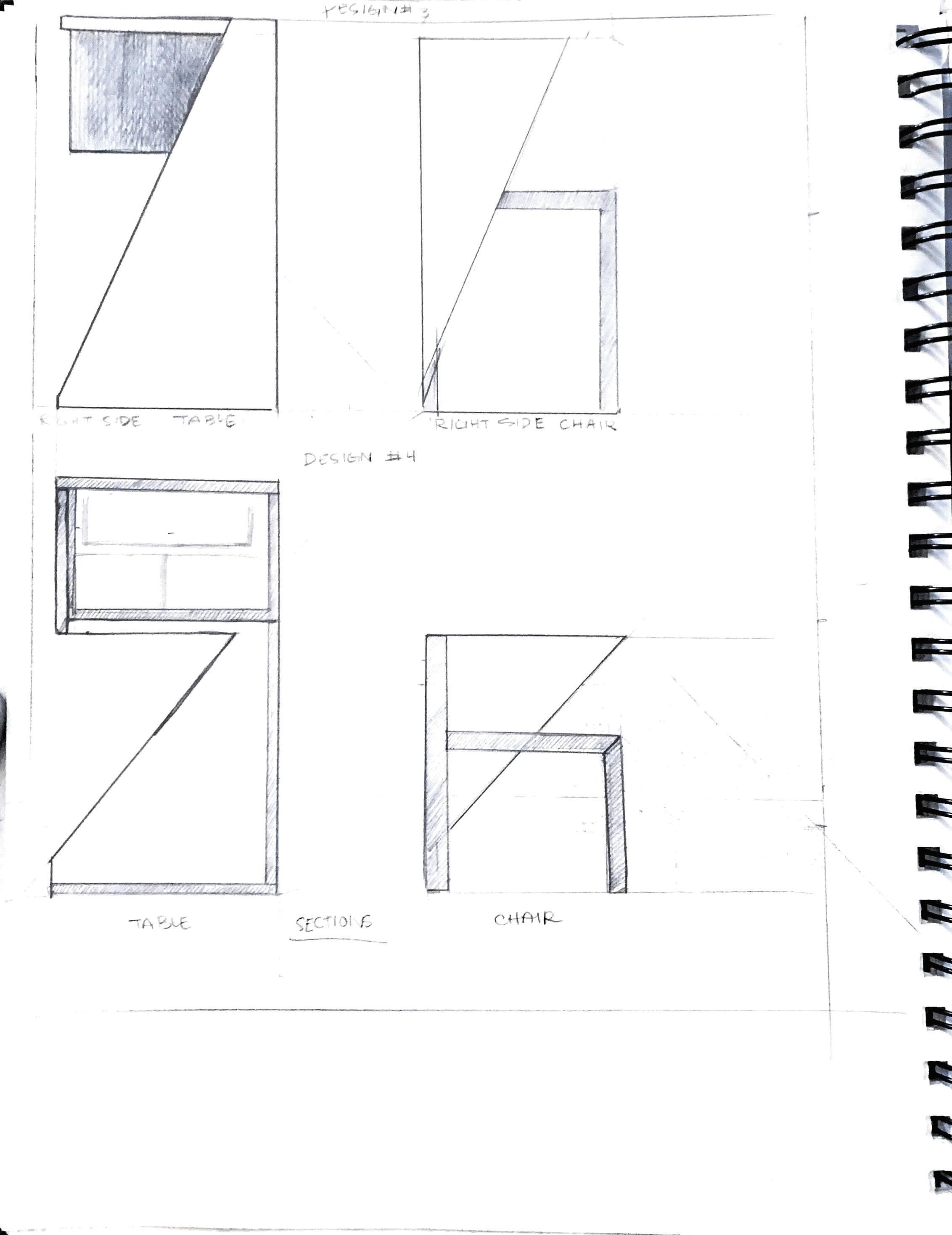
When I committed to the asymmetrical design, I began investigating how I would use the interior of the vanity. The deep dimensions were derived from makeup products I was planning on storing inside the table. I also added a large back piece to store hair tools, and add weight to the back of the table to balance the asymmetrical structure.
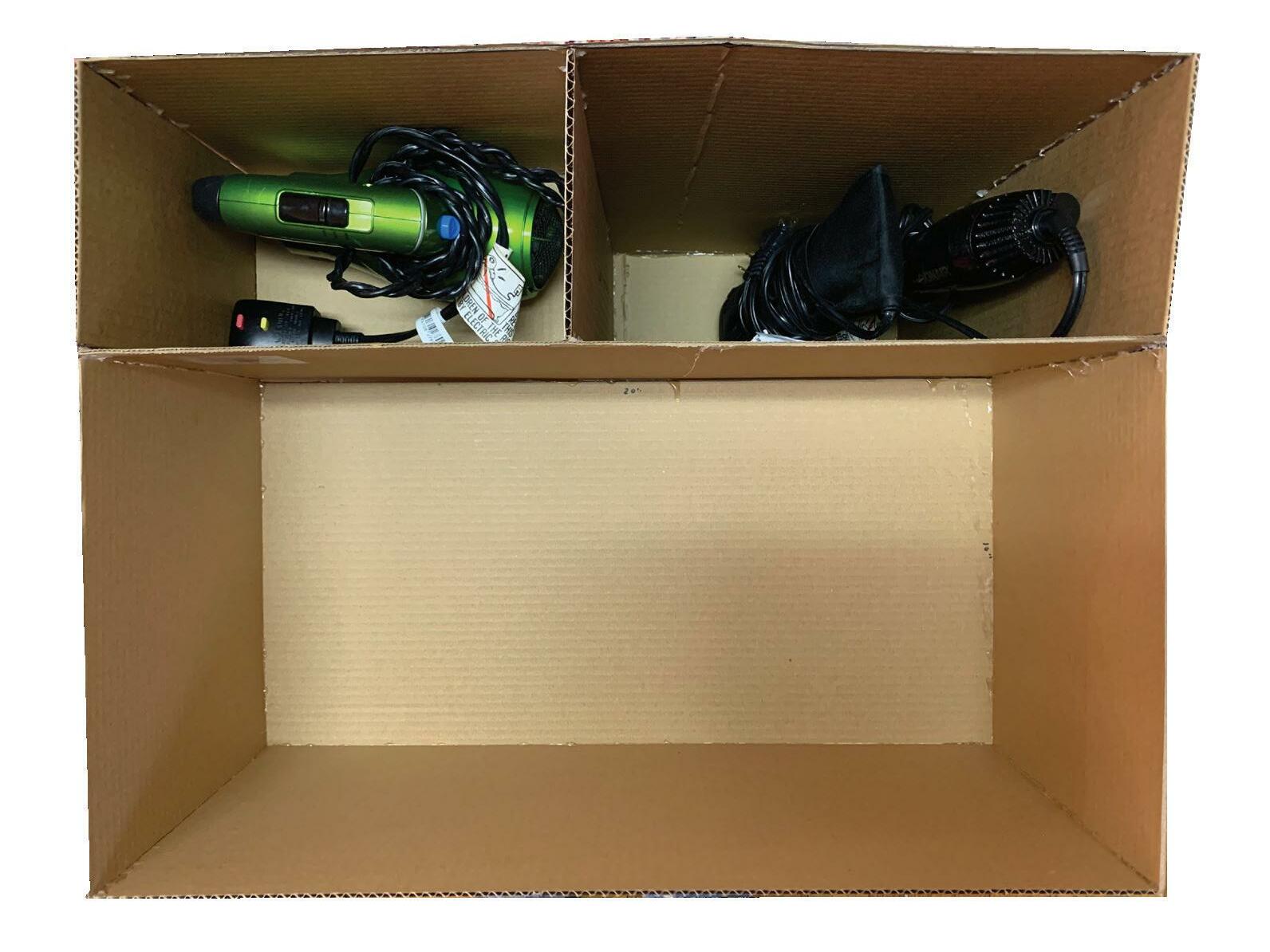
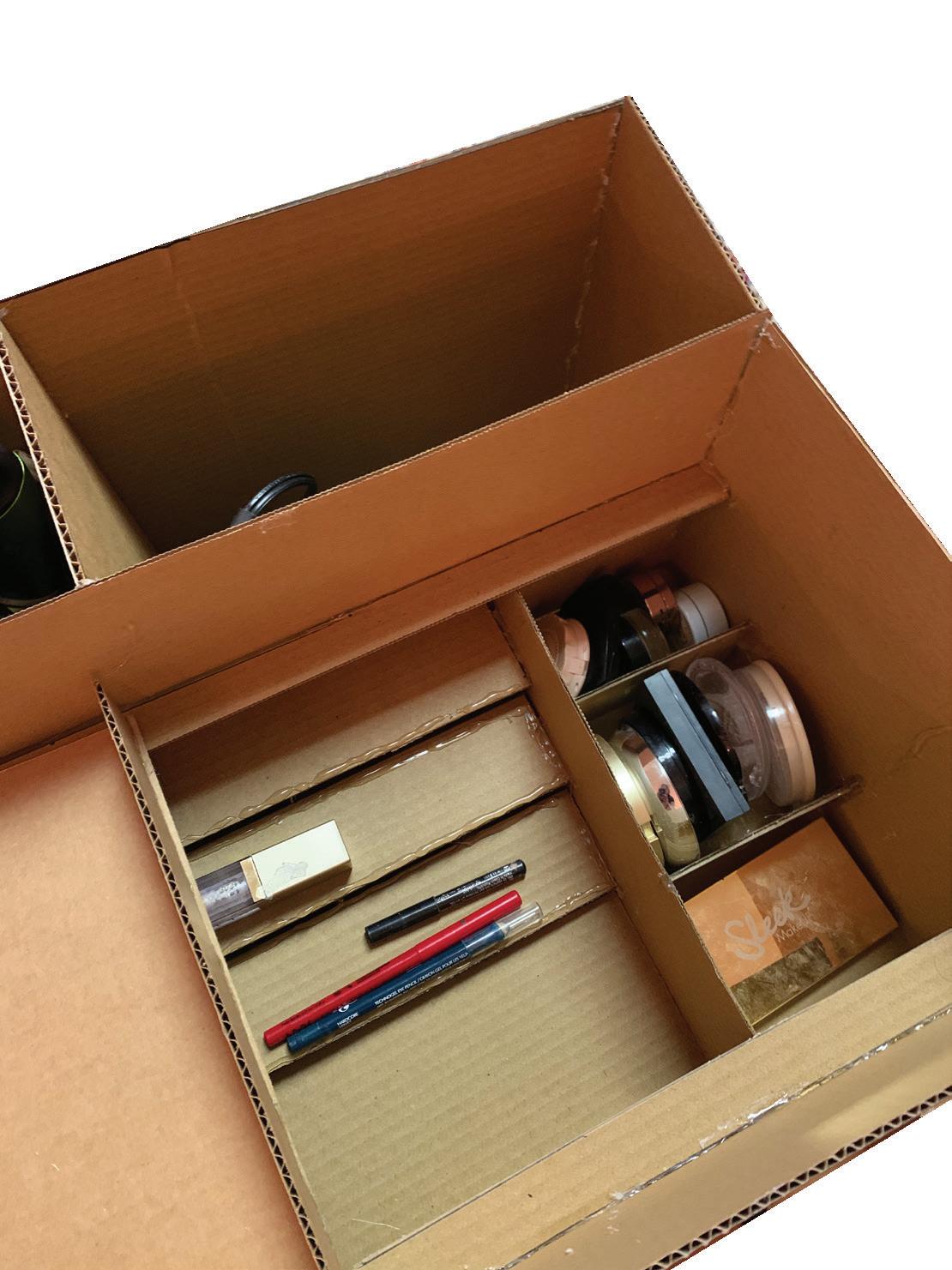
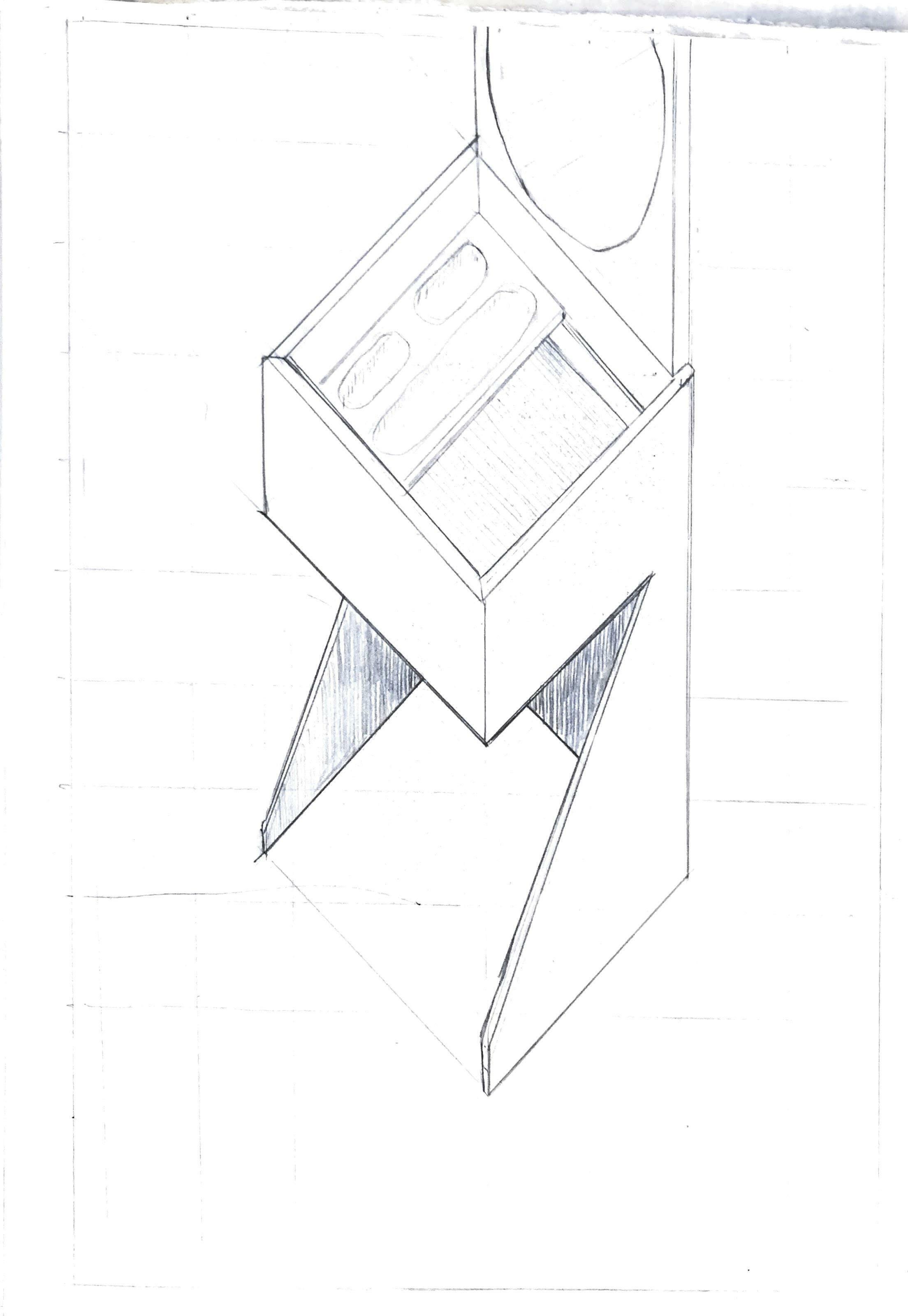
Interior of vanity sketches and model, February 2022
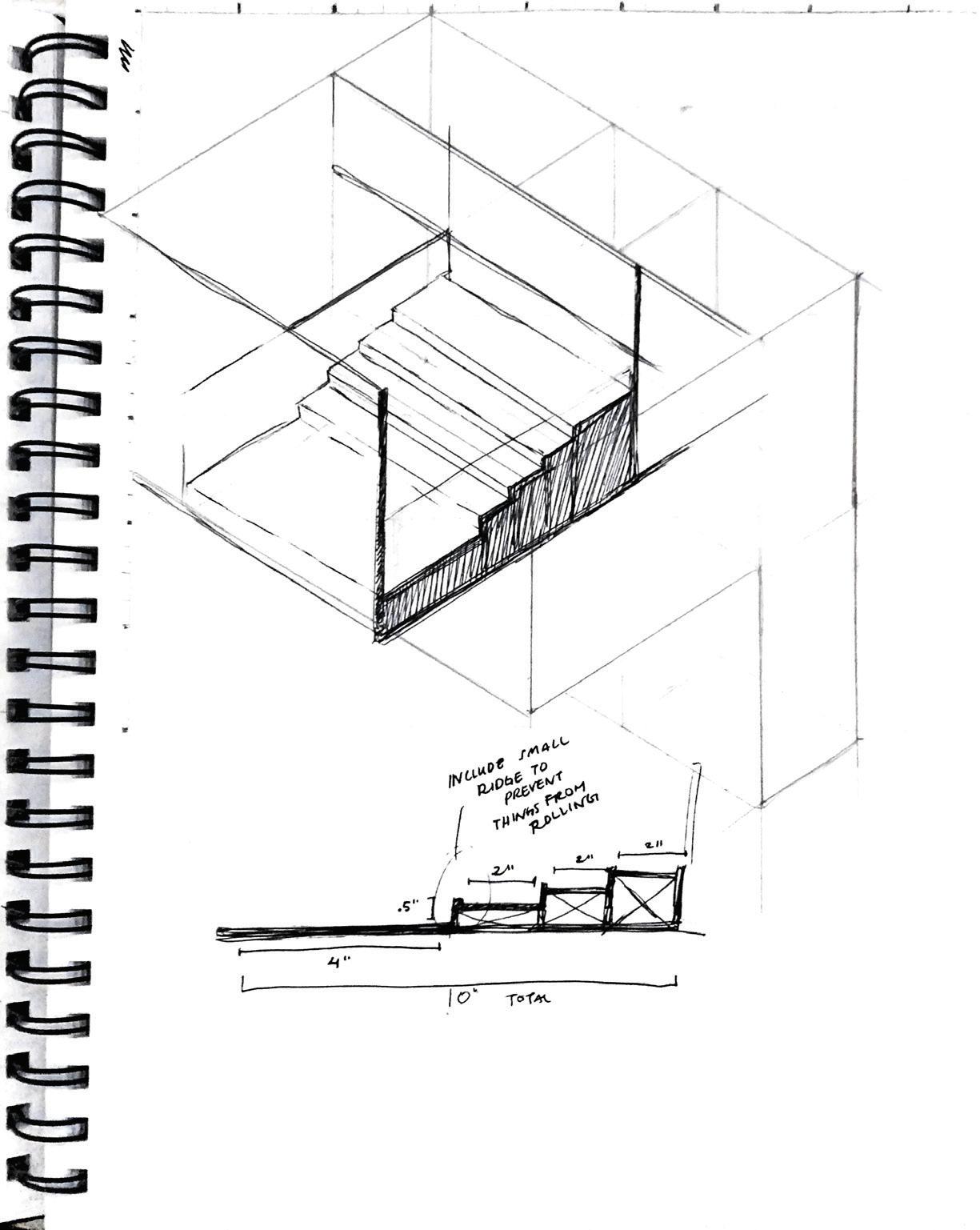
To refine my designs, I built sketchup models and printed out plans and sections. This is an example of my first design. Some important things to notice - I do not have any of my cuts planned, I do not have any joinery sketched out, I included a 2x4 as part of the cantilever support which was completely unnecessary. This was a fun attempt at a first pass but I still didn’t have a good idea of how to construct a piece of furniture.
RIGHT
BACK
After getting feedback from Professor Mann, I chose to change my design to an asymmetrical table and chair. This construction document was used to make my first full scale mock up model. For my mock up model materials, I used a 4’x8’ sheet of 1/2” sheathing plywood, and a 4’x8’ sheet of 3/4” cabinet grade plywood. I chose these materials because first, I was recommended to not use 1/4” plywood for a structural element, and 1” plywood is very expensive. And second, the sheathing and cabinet grade plywood were the cheapest option from homedepot.
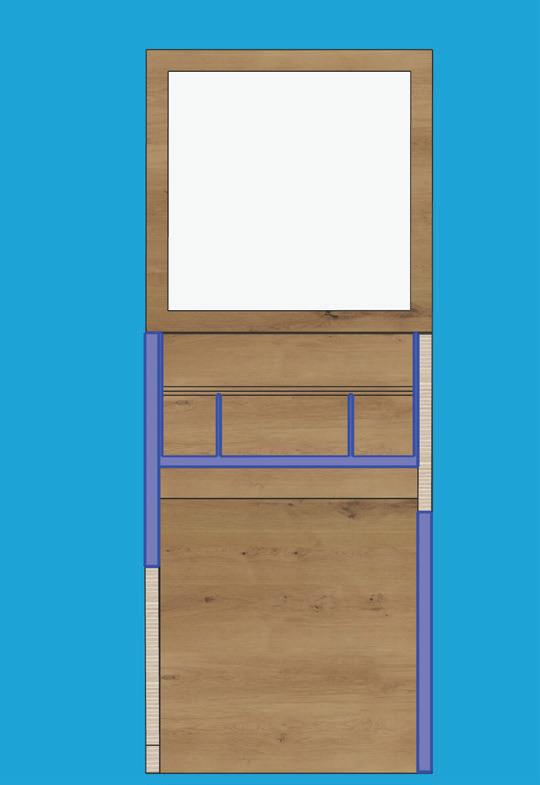


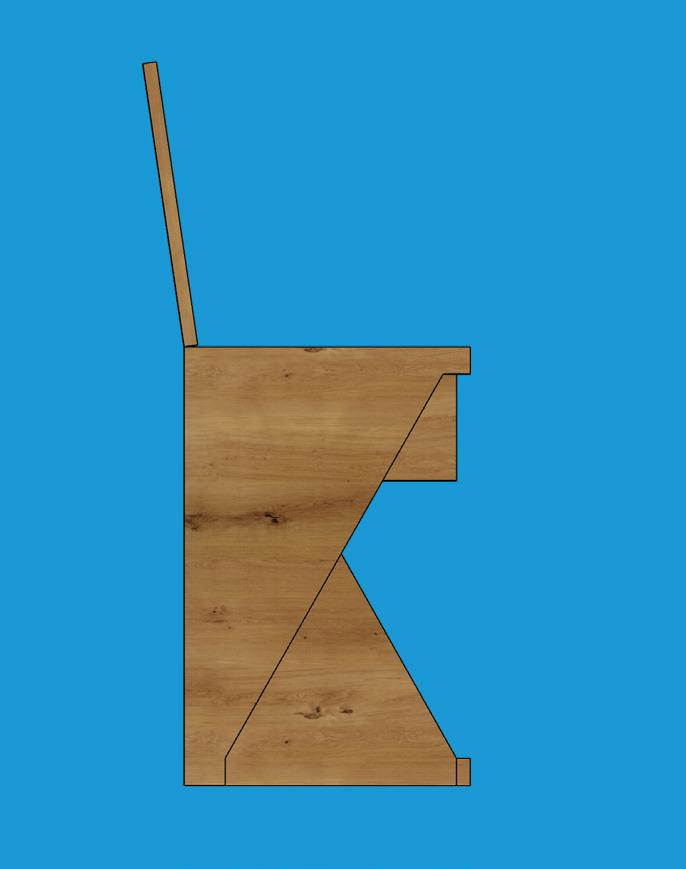
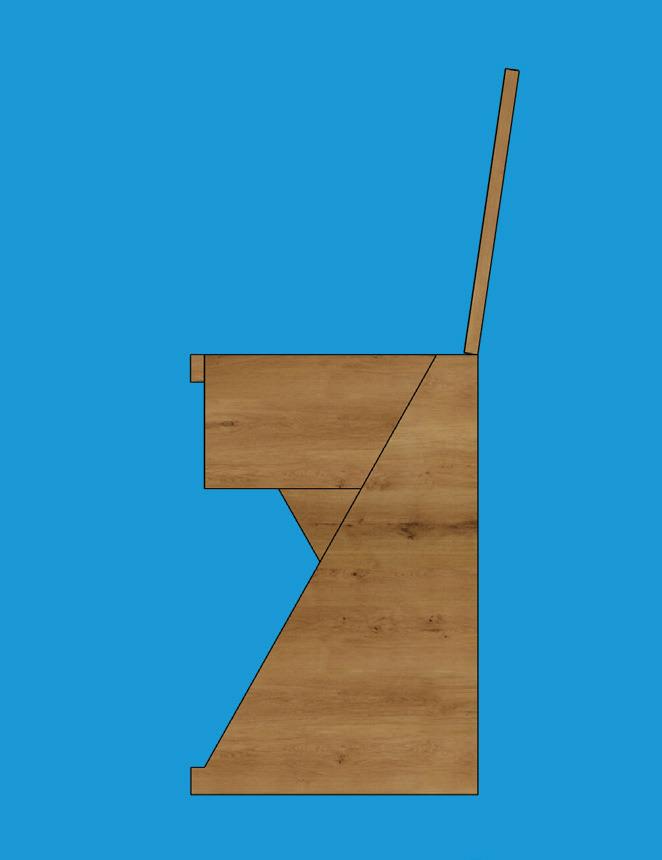
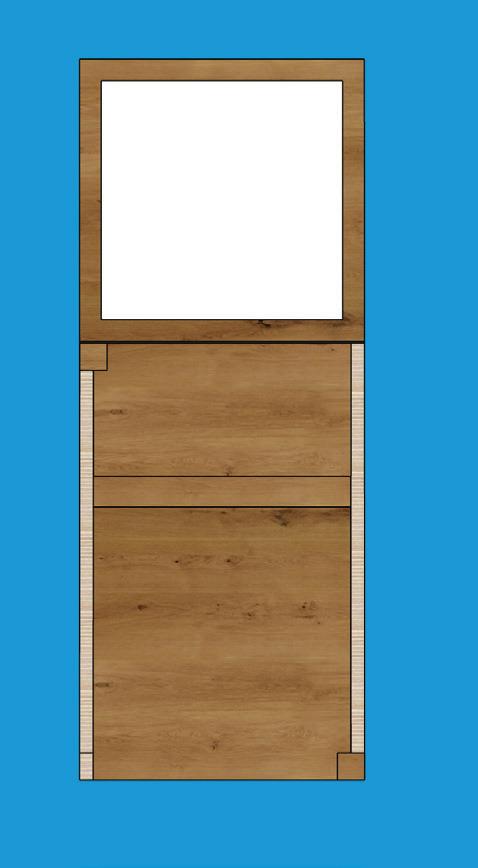
Reference image of wood joinery types.
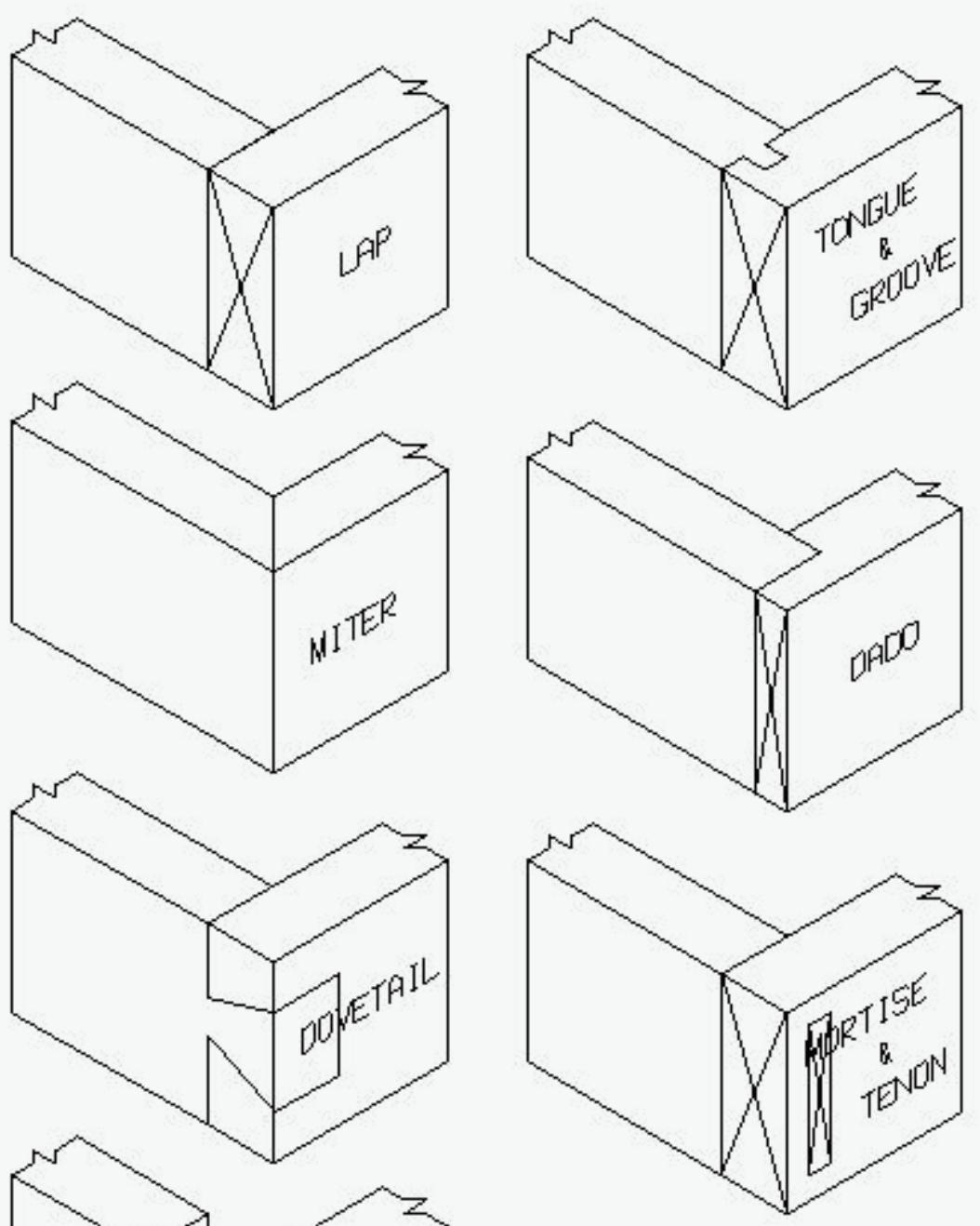
In any wood craft, joinery is a key element. Since I was using plywood, I needed to think about how I would implement the end grain into my design. I didn’t want to conceal my construction by using edge banding to cover the end grain. Using the material to my advantage, I decided to use miter and dado joints throughout my piece.
In my first mock-up, I tested these joints. I built the insert of the vanity with a series of dado joints, and I built the chair with a series of miter joints. I wanted to see the different difficulty level of assembly for each joint.
Both the miter and the dado were difficult to cut. The warp of my plywood only made it more difficult.
During a glue-up, the miter joints slip past each other. It was necessary to use a combination of standard clamps and DIY jigs to hold the corners together.
During a glue-up with a dado joint, the glue caused the wood to swell slightly and made it difficult to fit two pieces together. However, it was easier to keep the joint together because of the shape – there is less slippage.
The divider in the insert caused the sides of the insert to pinch. This therefore caused the table legs to pinch inward that the bottom. The squareness of the table failed.
I also didn’t build the vanity insert the same as a drawer. A drawer is dado’d into the sided to add more mechanical support. I had constructed the bottom of my insert with a rabbet joint which could lead to more stress on the glue and possibly breakage in the future.
Vanity Mock Up Model, February 2022
The construction process for the vanity insert consisted of many rabbet cuts holding the bottom, front and sides together.

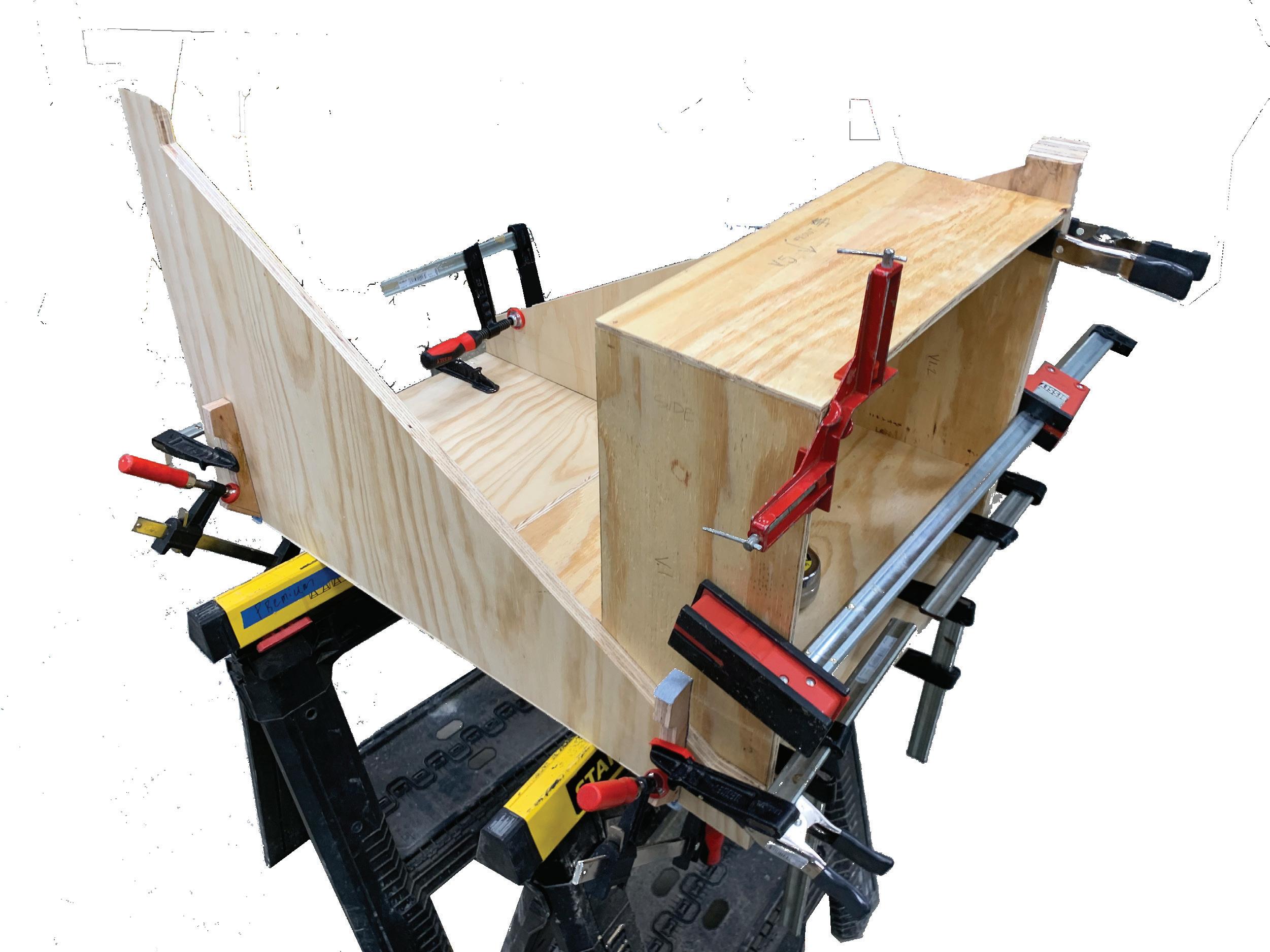
I dado’d the divider between the two side pieces. And I connected the insert to shell of the vanity with a series of dado’s.
I glued all the pieces of the insert together at once, and then used it to glue the shell of the vanity together.
The end result was rough. To start, the plywood sheets had been standing on their short side, vertically, for about 2 weeks. They had a huge warp, making them extremely difficult to work with.
Many of my measurements were off and caused some of the pieces to be resized on the fly.
After the vanity squareness failed, Evan James, the wood-shop manager made 90° angle jigs to improve the quality of glue-ups.
The number of clamps shows just how difficult this wood was to work with. The warp in the plywood was extremely difficult to work with. And the bevel edges of this design also made the glue-up extremely difficult.
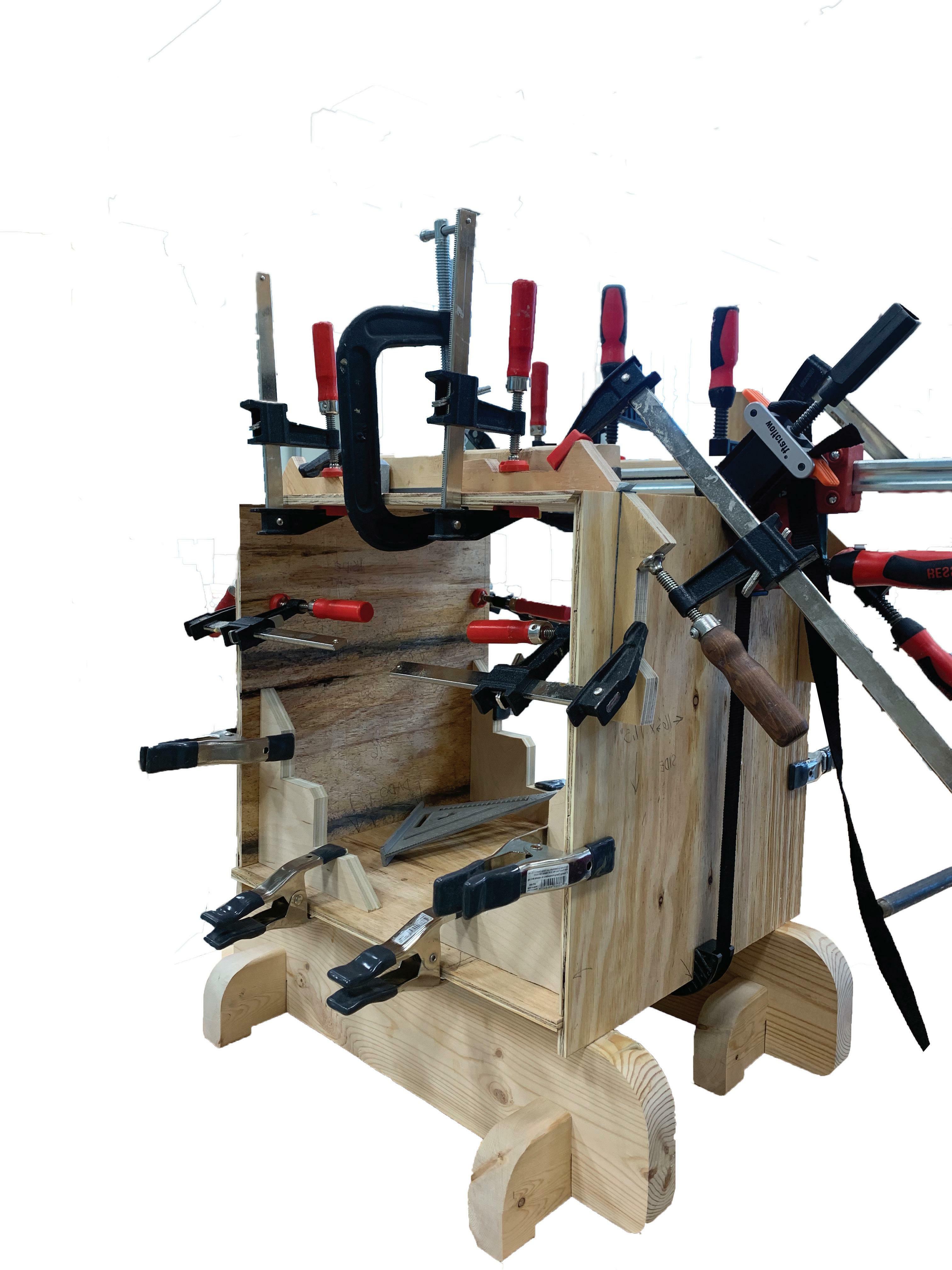
In this piece, I did change the construction of the bottom in order to reflect a typical drawer base. I dado’d it into the sides and back of the chair, prodiving more mechanical support.
Due to the quality of the table, as well as the warp with the 3/4” plywood, I decided not to fully construct the chair during the mock-up phase. I knew that it would not be worth the time, and I felt like I learned a lot from what I had constructed.