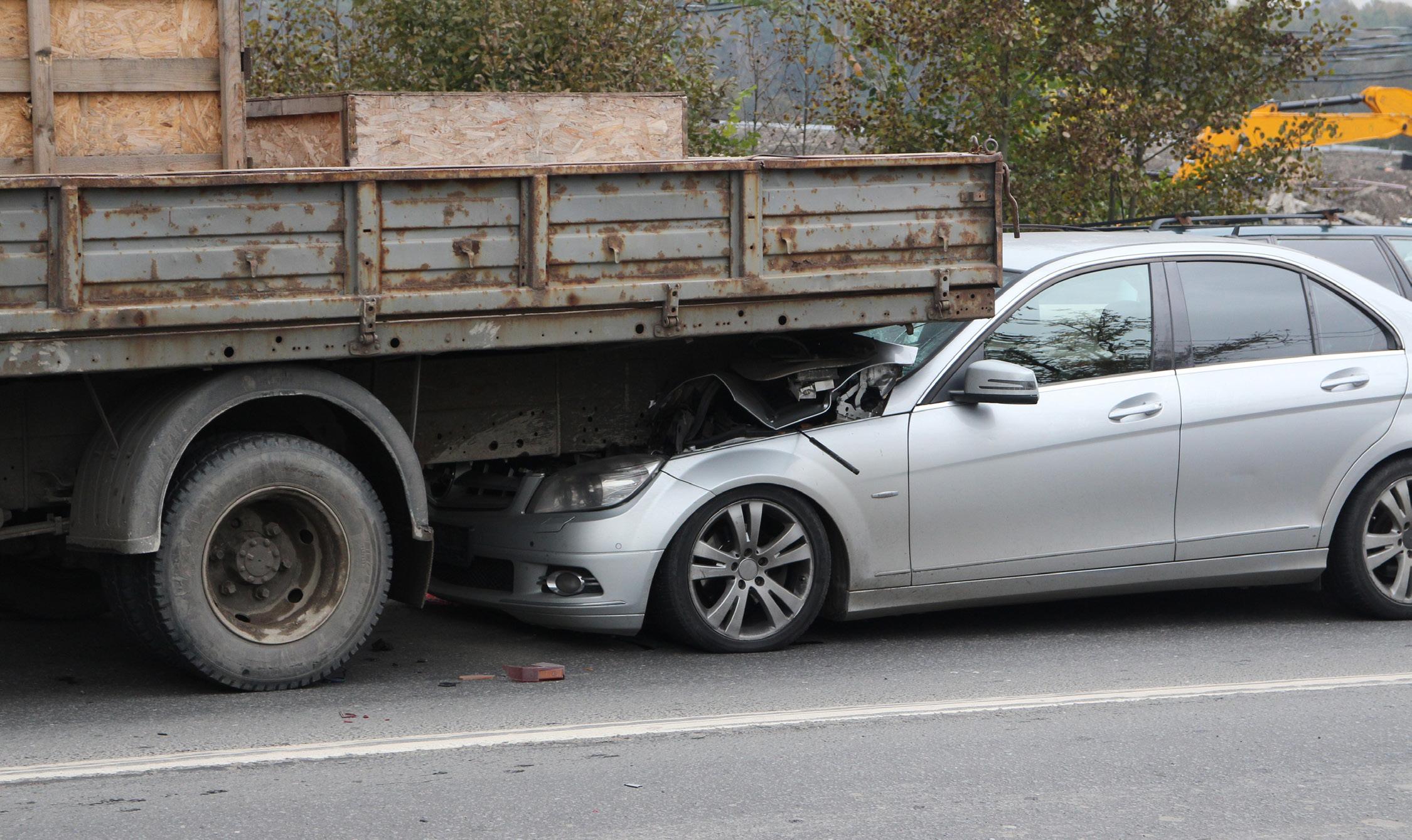
6 minute read
Your Rear Impact Guard Questions Answered
by David Smith PE, Alpine Engineering & Design, Inc.
On Jan. 1, 1953, the first federal regulation for rear impact protection—Regulation 393.86—went into effect. The regulation required heavy vehicles to have a device that was “substantially constructed and firmly attached.” The device was intended to prevent excessive underride if a passenger car collided with the rear of the heavy vehicle. Today, these devices go by several different names including rear impact guards (RIG), underride guards, Interstate Commerce Commission (ICC) bumpers, Department of Transportation (DOT) bumpers, and Mansfield bars.
As time went on, there was an apparent trend of increasing injuries and fatalities due to rear collisions despite the regulation. In 1967, rulemaking efforts were initiated to improve safety for passenger car occupants involved in collisions with the rear of heavy vehicles. However, the efforts were terminated in 1971 as the National Highway Traffic Safety Administration (NHTSA) Administrator concluded, at the time, that the safety benefits achieved in terms of lives and injuries saved would not be commensurate with the cost of implementing the proposed rule. In 1976, the popular American actress Jayne Mansfield was traveling on US Highway 90 from Mississippi to New Orleans with her attorney, three kids, and their driver. In the very early morning, the Buick crashed at high speed into the rear of a tractor-trailer that had slowed behind a truck spraying mosquito fogger which was shrouded in an insecticide fog. The three adults in the front seat died instantly. The children, asleep in the back seat, survived with minor injuries. Thus, the term “Mansfield Bar” was coined for the underride guard.
Around the same time, the Insurance Institute for Highway Safety was conducting tests to show that excessive underride is preventable with specially designed high strength, low weight, low-cost underride guards.
Subsequently, the efforts to create new and better laws for rear impact protection resumed in 1977 and involved significant amounts of testing, analysis, and data collection. Today, the governing law for rear impact protection is 49 CFR § 571.223224 in the United States and CRC c. 1038-223 in Canada.
Federal law requires that all trailers in the United States with the following requirements “shall be equipped with a rear impact guard certified as meeting FMVSS No 223, Rear Impact Guards (§571.223) (49 CFR §571.224)”:
• Gross vehicle weight rating (GVWR) greater than 10,000 lbs.
• Rear-most surface of tires is more than 12” from back of trailer
• Is not a low chassis vehicle (low chassis vehicles have a transverse horizontal member behind the wheels, the bottom of which is no higher than 22” above the ground) • Vehicle is not a special purpose trailer
• Vehicle is not a pole trailer
• Vehicle is not a pulpwood trailer
• Vehicle is not being used in a driveaway-towaway operation
• The flow chart below can help determine if a certified rear impact guard is required for your trailer.
The US standard exempts low chassis vehicles, special purpose trailers, pulpwood trailers, pole trailers, and trailers used in driveaway-towaway operations, as defined in 49 CFR.
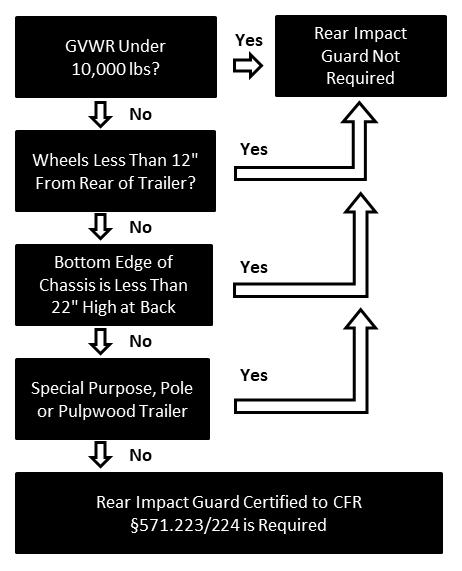
The testing that was performed during the creation of the standard revealed that there are two competing failure modes, and for the guard to actually increase safety, it must be designed to a sweet spot. The obvious danger is that if the guard is too flimsy, it will not stop excessive underride, which often results in decapitation. On the other hand, if the guard is designed to be overly rigid, it causes rapid decelerations similar to running into a brick wall, which results in head injuries even when wearing a seat belt.
To ensure that RIGs increase safety, the standard has requirements for both strength and energy absorption. They also require a label indicating compliance with the standard. The requirements are summarized below:
• Horizontal member shall have a height of at least 100 mm (about 4 inches) when viewed from the back. • Must resist force levels of 50,000 Newtons at P1 and P2 (outside edge and center of guard), and 100,000 Newtons at
P3 (point load at the guard supports). • Must not deflect more than 125 mm during any of the force applications. • Must absorb at least 5,650 Joules by plastic deformation at each test location. • A label on the forward-facing surface of the horizontal member placed 305mm (12”) in from the outside edge.
These are the very minimum standards for RIGs as outlined in 223 that are legal requirements. Having and retaining documentation showing that RIG designs meet these minimum qualifications is critical for liability if there ever is an accident.
How to make sure your RIG complies
Often, a rear impact guard is designed for a particular trailer. But designing the rear impact guard to meet all of the requirements of the standard is not so simple. There are many ways a trailer manufacturing company may approach the task. The worst thing that could be done is to install an underride guard that is not
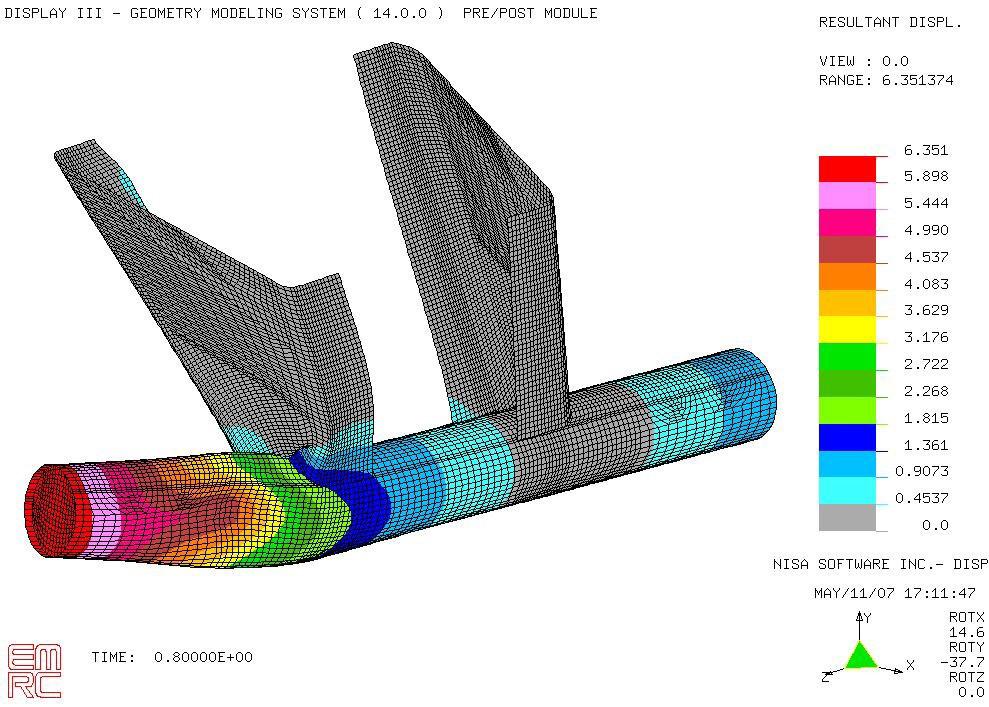
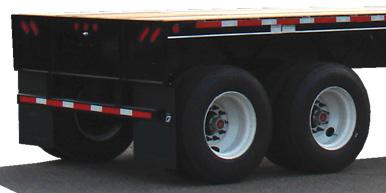
An example of a rear underride guard.
known or in compliance. This is even worse than not having a guard because it produces the illusion of safety, where no such safety actually exists.
The first way to ensure a safeguard complies with the regulations is a “guess and check” method. Here, the manufacturer would build a guard, test it, make adjustments when it fails, build a new guard, test the new guard, make more adjustments when it fails again, etc. As you can imagine, this can take a significant amount of time and money, whether you have the equipment and do the testing on your own or send it out to a third party. However, if you have a design that you think meets the requirements and only lack the paperwork to show that, this may be a viable option.
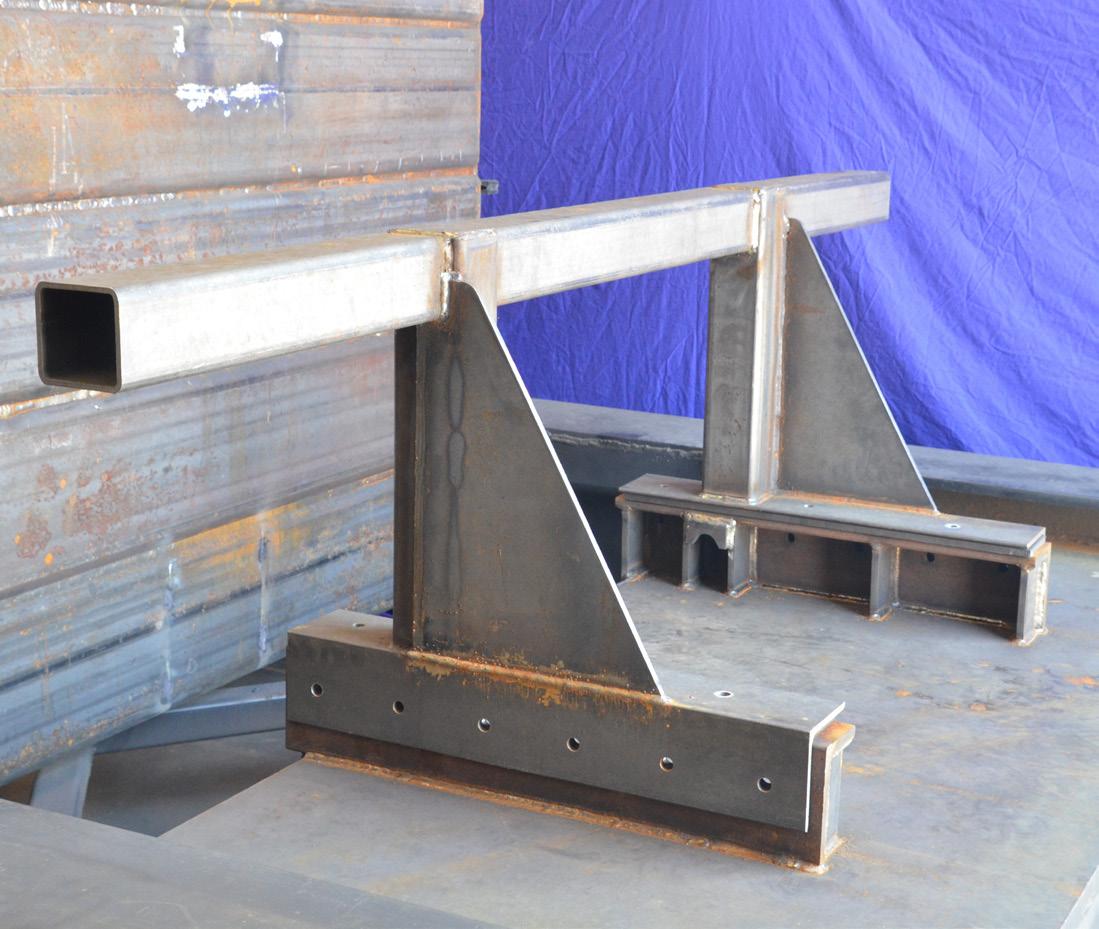
A second option would be to use a combination of advanced computer simulation and testing. Using non-linear finite element analysis (FEA), you can apply loads and measure deflection, even when you are dealing with permanent plastic deformation right on your computer. This can be a much more cost-effective way of getting to a design you are confident will pass the test as you can iterate without actually buying metal, fabricating a guard, or going through destructive testing. Some people think that computer simulations are sufficient analysis for certification, but the standards require that the design be physically built, mounted, and tested. This makes sense as computer simulations which can be very good, are at best only approximations.
Alpine Engineering and Design has been providing engineering consulting services in the trailer industry for over 20 years. The company understands the rear impact guard regulations and has the qualifications, skills, experience, and equipment to simulate RIGs using FEA, conduct physical tests, and certify designs that pass so trailer manufacturers can rest easy knowing they comply with the most up-to-date standards. If you would like help navigating the process and certifying your rear impact protection, contact Alpine Engineering and Design by visiting www.AlpineEng.com or call (801) 763-8484.