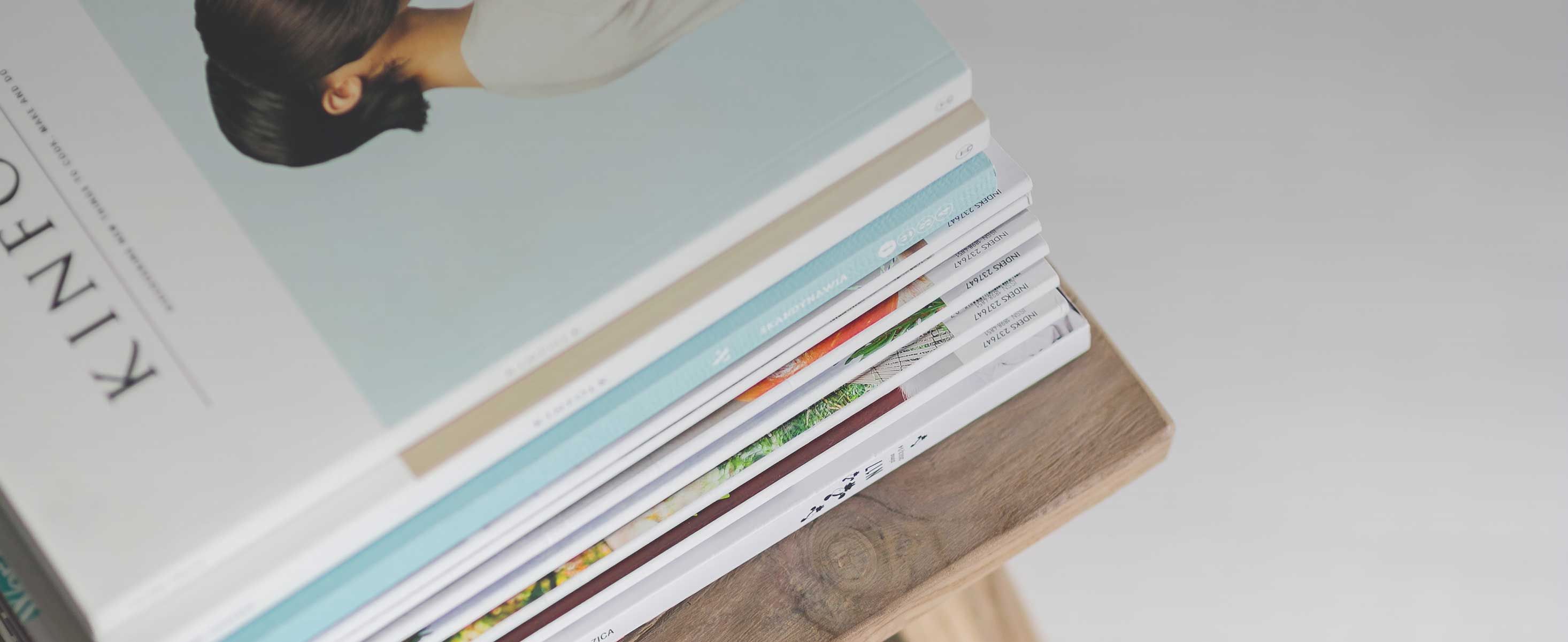
1 minute read
IDC Spring
which can be more sensitive to issues regarding heat input in the weld. Because pulsed MIG allows wire feed speed to be increased to match welding amperage, travel speeds will also increase. Travel speed is one of the main drivers of heat input; when travel speed goes up, heat input goes down. The higher travel speeds of pulsed MIG help reduce heat input, which helps reduce distortion and burn-through.
Is out-of-position welding common in the operation?
Pulsed MIG delivers better weld quality and puddle control when welding out of position with solid or metal-cored wires. This results in less part handling and helps reduce operating costs.
Is the operation frequently welding aluminum?
As stated above, the pulsed MIG process can provide benefits for aluminum welding because of the ability to increase travel speed and lower heat input. Aluminum transfers heat away from the weld at a faster rate than many materials (like steel), making it more difficult to establish a weld puddle. And because the material has a relatively low melting point, it’s prone to burnthrough and warping on thinner sections where there simply isn’t enough mass to transfer the heat. Pulsed MIG can be an excellent option for welding thick and thin aluminum, since it offers increased control of the weld puddle.
Pulsed MIG benefits to save time and money
While not every welding application is well suited to pulsed MIG welding, the process can deliver benefits for many manufacturing operations. If the operation doesn’t already have pulsed-MIGcapable welding power sources, it may require an investment in new equipment. But the move can quickly provide a return on that investment through improved productivity, reduced rework and easier setup and training.
For more information, visit MillerWelds.com.