
3 minute read
Finishing Systems for Trailer Manufacturers
Tracks Intellifinishing: Flexible, Automated Finishing Systems for Trailer Manufacturers
John Claman, IntelliFinishing Sales
Load Trail recently faced a significant challenge trying to improve the quality and throughput of their agricultural trailers within the finishing process. Their trailers range from 24 to 53 feet in length and weigh up to 10,000 lbs. Most traditional automated finishing systems would not be able to handle trailers of this size, or a large system would need to be installed, exceeding the available footprint Load Trail desired for their system.
To help solve the problem of powder coating trailers of this size and streamline their finishing, IntelliFinishing installed a dual shuttle system at their Sulphur Springs, Texas facility.
The finishing system IntelliFinishing installed for Load Trail features nine lanes that run above their final weld cells. After final assembly and weld, trailers are loaded immediately on a carrier above the weld cells from one of those nine lanes. The trailers are then transported directly ahead by 53 feet long conveyorized carriers onto a large primary shuttle which moves to each of the finishing processes. IntelliFinishing systems use a friction tube rather than a chain to move carriers. By using the friction-tube-driven shuttle, the trailers can move laterally from process to process with no U-turns, saving a tremendous amount of floor space. The frictiontube conveyor also moves carriers into and back out (forward and reverse) of each process. This eliminates large bulb turns and return sections of chain track, as seen with many traditional finishing systems.
Processes on Load Trail’s shuttle system include automatic and manual shot blast booths, an automatic two-stage cabinet wash booth, a dry-off oven, several final prep and quality control stations, prime and topcoat powder booths, three final cure ovens, dual unload stations on either side of the main shuttle, and a secondary 52-foot carrier return shuttle to transport empty carriers back to the original nine weld and loading cells.
IntelliFinishing systems are completely automated (with the exception of the occasional manual process), which means each of Load Trail’s processes within the system is controlled with

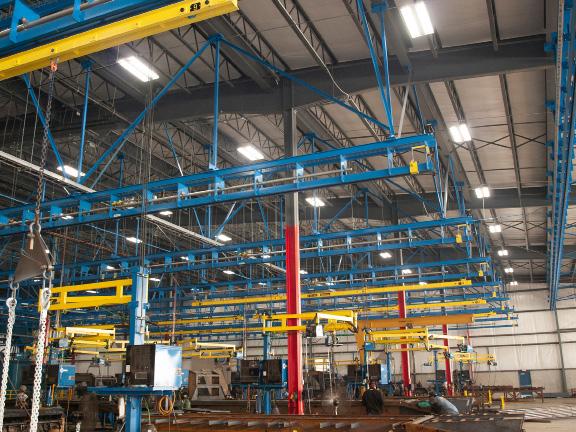
“recipes”. With a recipe-based system like IntelliFinishing, each trailer carrier moving through a system can be treated differently based on the process data entered into the system as its recipe.
Recipes are created by entering commands or process instructions for each part family or group of similar parts. The recipe is selected manually or automatically for each trailer loaded from a weld cell. All trailers with the same recipe will receive the same process. If the next carrier loaded on the system has a different trailer type requiring a different recipe, the operator simply selects the correct recipe for that trailer at the load-area HMI screen. When that carrier gets to a process area, the system will automatically run the selected process for that part family. These intuitive controls ensure every trailer and trailer part achieve its own optimal finish.
IntelliFinishing takes pride in providing the most flexible, modular, customized, automatic finishing systems that can address unique finish, parts, and footprint needs. Other system customers include Caterpillar, Altec, Hyster Yale, Boeing, Raytheon, Hytrol, and others.
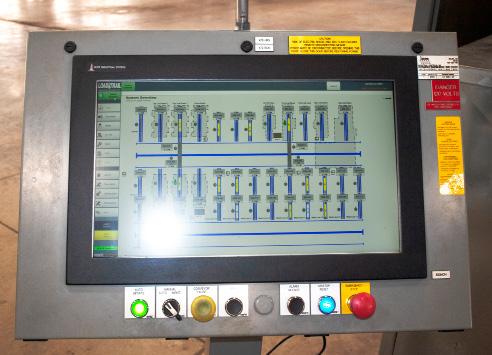
With a recipe-based system, each trailer carrier moving through a system can be treated differently based on the process data entered.
To view a short video of the Load Trail system visit: www.Intellifinishing.com/trailers. If you’d like to discuss if an IntelliFinishing system might be right for you, please call (785) 309-0356.
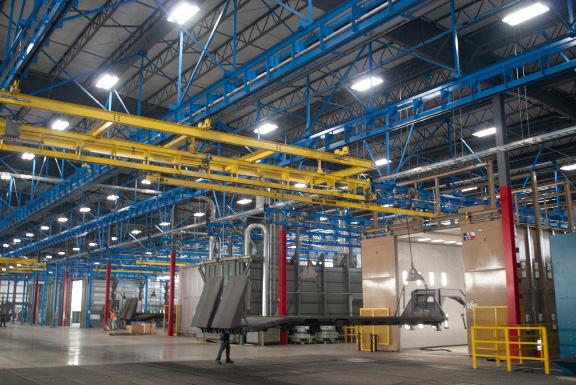