
96 minute read
Editorial
Mundo Ferrosiderúrgico Mercado, Ciencia y Tecnología EDITORIAL
AÑO XI EDICION N° 44 | JULIO 2022
Advertisement


Nos complace hacer llegar a todos nuestros lectores, la edición N.º 44 de la Revista Mundo Ferrosiderúrgico, la cual ene como obje vo, impulsar proyectos de inves gación, desarrollo tecnológico e innovación en el ámbito del mineral de hierro y la industria siderometalúrgica.
En la sección “Entrevista con Propósito” invitamos a la Dra. Ing. Gloria Basanta, Directora de Calidad e Inves gación de la empresa Siderúrgica del Orinoco “Alfredo Maneiro (SIDOR) y Gerente del Ins tuto de Inves gaciones Metalúrgica y Materiales de SIDOR, profesional con más de 35 años de trayectoria y experiencia en el área de Inves gación, Ciencia y Tecnología, quién además fue galardonada con el Premio Nacional de Ciencia y Tecnología del año 2022, “Mención Honorífica”. La Dra. Basanta mujer inves gadora mo vada e involucrada en los procesos produc vos industriales, considera como desa5o para este año, concien zar que los procesos de inves gación serán sensibles a la economía circular y los ahorros energé cos que son de vital importancia para la sustentabilidad, contribuyen a minimizar las emisiones de gases con efecto invernadero para el bienestar del ser humano.
En la sección “Perspec)vas de Mercado” se muestra la fluctuación que ha tenido el mineral de hierro en las industrias de China, en el primer semestre del año, que se han visto afectadas por un nuevo repunte de COVID-19. Pese a ello se han presentado restricciones, medidas de seguridad y control contra el virus, para tratar de fortalecer su economía y así ayudar a las pequeñas empresas a estabilizar el empleo y flexibilizar los controles en el mercado inmobiliario. (BRIQCAR). El referido trabajo de inves gación, cien>fico y tecnológico trata el estudio de costras a>picas, definidas por su acelerada ciné ca de crecimiento, formadas sobre el material refractario en el reactor de BRIQCAR con tecnología Midrex. Entre las conclusiones de la inves gación se determinó que “El proceso de formación de costras a>picas, se origina por presencia de factores ac vadores como poros y grietas en la superficie del material refractario y el crecimiento es propiciado por adhesión de par>culas mediante la generación de fases eutéc cas en la superficie externa de las par>culas”.


El segundo ar>culo, también del equipo de inves gadores del Ins tuto de Inves gaciones Metalúrgicas y Materiales – SIDOR, tulado “Comparación térmica de coque verde de petróleo, coque tratado térmicamente y antracita” donde se aplicaron técnicas de análisis térmicos que permi eron caracterizar, evaluar y comparar materiales carbonosos similares para establecer las principales diferencias térmicas que estos materiales presentan.
Finalmente, el ar>culo “Propuesta de fabricación por fundición de los componentes de tracción para vagones mineraleros de CVG Ferrominera Orinoco, C.A.” elaborado por Pedro Bonillo, tesista en la carrera de Ingeniería Metalúrgica de la Universidad Nacional Experimental Politécnica Antonio José de Sucre (UNEXPO), consis ó en elaborar propuesta para la fabricación (charnela y candado) de acople y tracción para vagones mineraleros a través de un proceso de fundición con moldes de arena. Como recomendación primordial realizar un análisis estructural mediante una simulación de los componentes en estado de operación para evaluar el rendimiento que estos ofrecen.
La Gerencia Centro de Inves gación y Ges ón del Conocimiento agradece a todos los inves gadores que comparten en la Revista Mundo Ferrosiderúrgico, sus estudios, información relevante y tangible del mineral de Hierro y de la industria Ferrosiderúrgico.
En la Sección I+D+i el primer ar>culo tulado “Estudio de formación de costras a+picas en reactor Midrex de BRIQCAR an)gua VENPRECAR” liderado por la Dra. Basanta en conjunto con profesionales en el área de la Metalurgia, perteneciente al Ins tuto de Inves gaciones Metalúrgicas y Materiales – SIDOR y de la Gerencia de Proyectos de la empresa Briquetera del Caroní


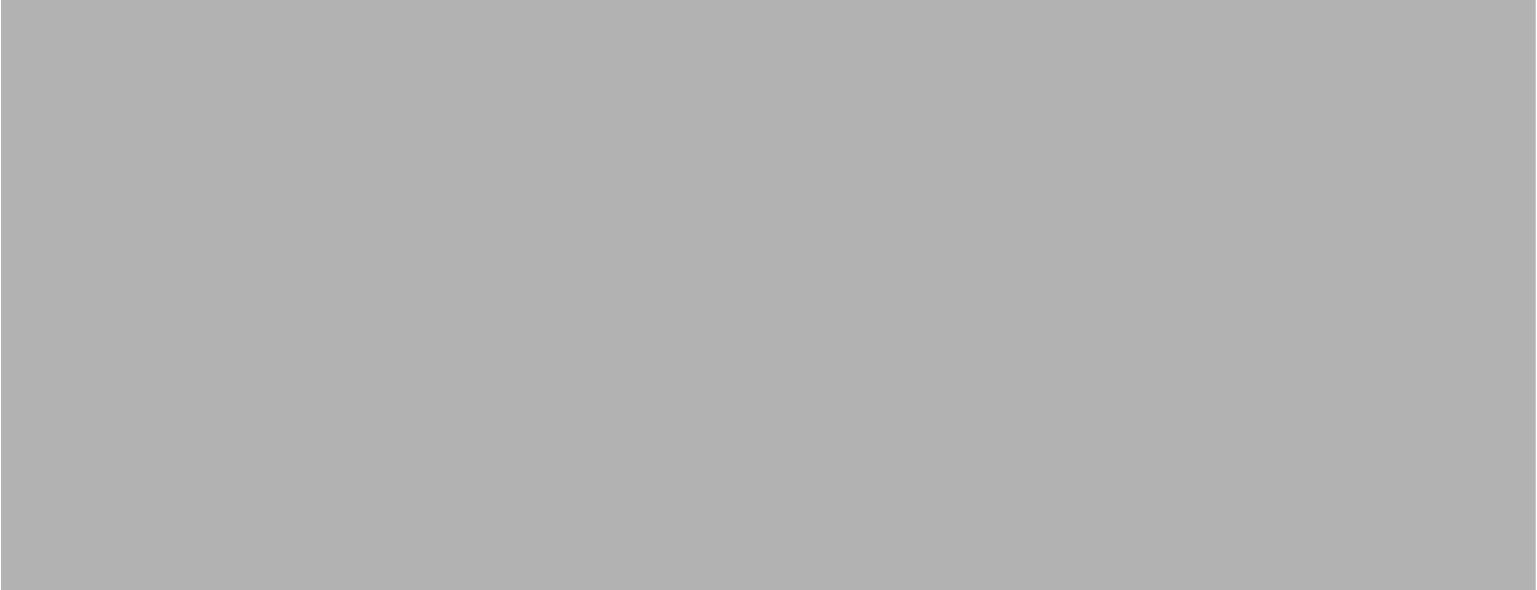
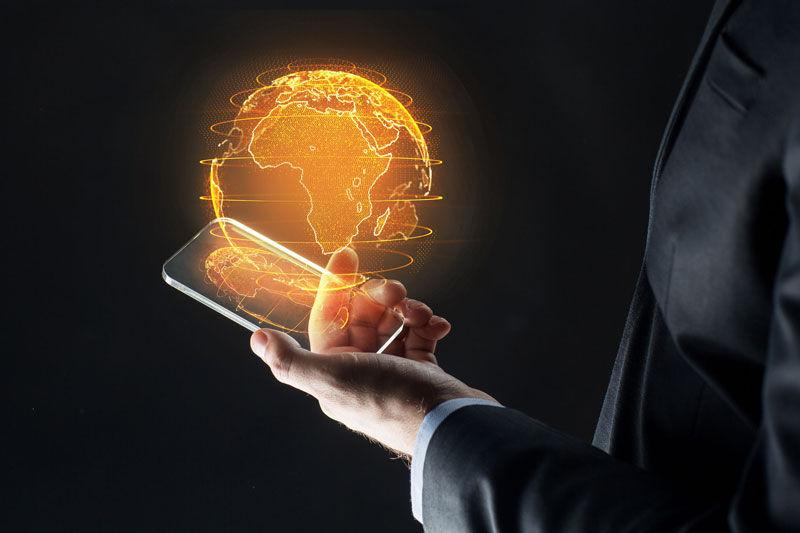
Fuente: Tomado de la Web.
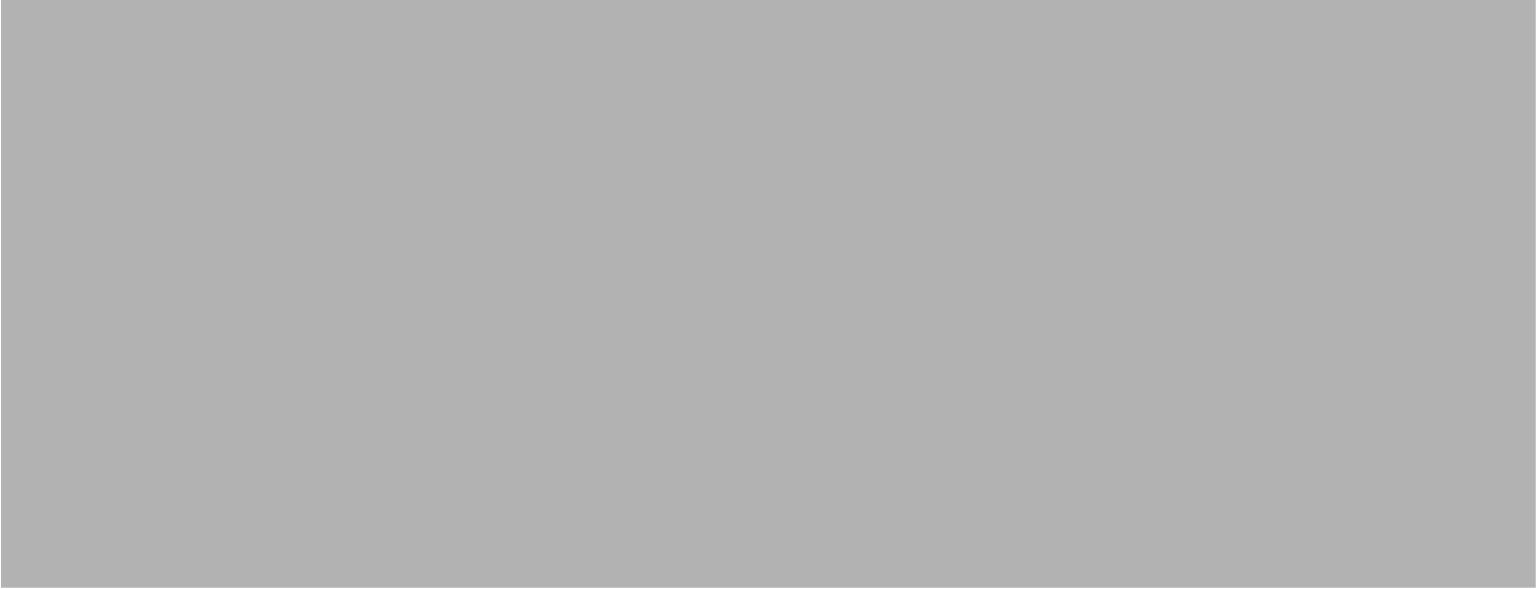
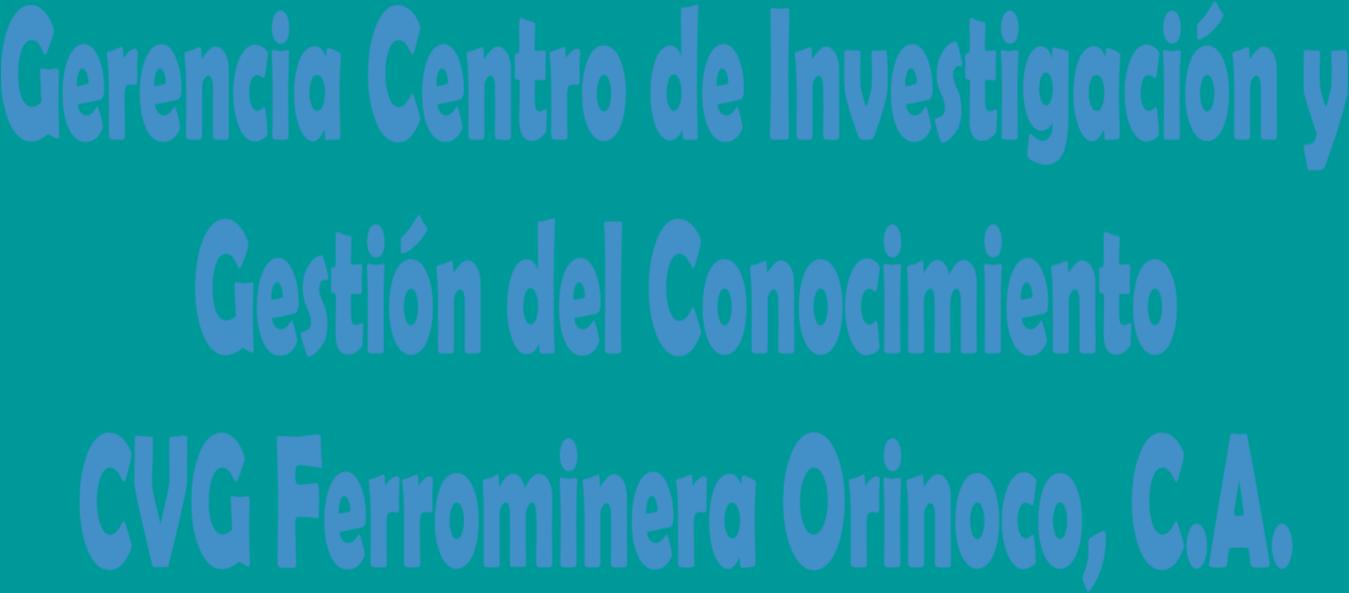

ENTREVISTA CON PROPÓSITO
E n e s t a s e c c i ó n presentamos un enfoque personalizado de los actores, que con su esfuerzo y experiencia protagonizan y consolidan el desarrollo de las i n d u s tri as d el se c tor F e r r o s i d e r ú r g i c o e n materia de investigación y desarrollo.
ENTREVISTA CON PROPÓSITO
“Se viene fortaleciendo de forma novedosa un nuevo modelo de gestión participativa y protagónica de los trabajadores que multiplican la actividad de investigación ... REVISTA MUNDO FERROSIDERÚRGICO | AÑO XI | NÚMERO 44 | JULIO 2022
En esta oportunidad, entrevistamos a la Dra. Gloria María Basanta, Ingeniera Metalúrgico, egresada de la Universidad Nacional Experimental Politécnica "Antonio José de Sucre"; Inves gador PEII B, acreditada por el Ministerio del Poder Popular para la Educación Universitaria, Ciencia y Tecnología y actualmente Directora de Calidad e Inves gación de la empresa Siderúrgica del Orinoco “Alfredo Maneiro” (SIDOR), Ciudad Guayana, Venezuela.
Realizó un Doctorado en Ciencia de la Ingeniería en dicha pres giosa casa de estudios, contando además, con una impecable trayectoria en la empresa SIDOR, siendo merecedora de un destacado reconocimiento por parte del Ministerio del Poder Popular para Ciencia y Tecnologías de Venezuela, con el Premio Nacional de Ciencia y Tecnología año 2022, mención honorífica del Grupo Consolidado de Inves gación.
A con nuación, resaltamos sus vivencias en el área de inves gación de la industria del acero, a través de la siguiente entrevista:
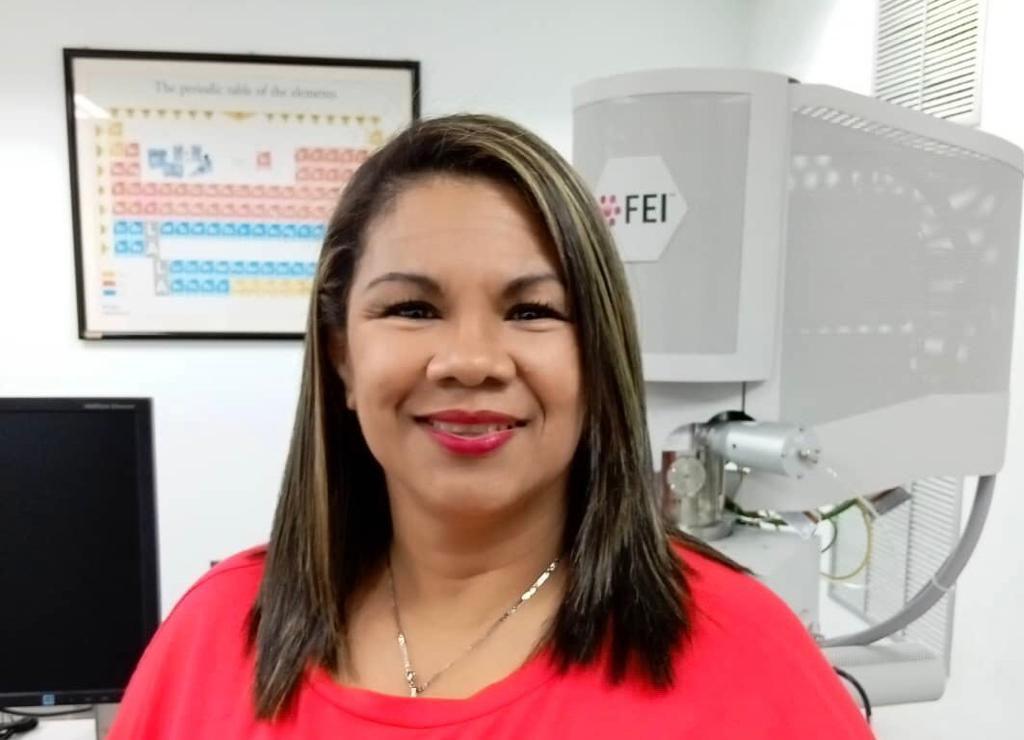
Dra. Ingeniera Gloria María Basanta, Directora de Calidad e Inves/gación de la Siderúrgica del Orinoco Alfredo Maneiro (SIDOR). Premio Nacional de Ciencia y Tecnología año 2022 mención Honorífica Grupo Consolidado de Investigación. Tomando en cuenta su trayectoria y años de experiencia en el área de inves gación en SIDOR, ¿Cuáles han sido los proyectos más importantes que han estado bajo su dirección?
Uno fue el rescate de la inves gación industrial en SIDOR y su con nuidad, que involucró adecuación de infraestructura, captar a un grupo de profesionales sensibles por la inves gación industrial o aplicada y con la importancia que representa para la empresa y para el país. Proyectos emblemá cos estudio de los defectos denominado “Minidesgarre en Hoja Estañada, Punto Marrón en Hoja Cromada”, estos exigieron la caracterización con dis ntas técnicas analí cas que condujeron sistemá camente a la iden ficación del origen, dado lo complejo del proceso industrial siderúrgico; además propiciaron el desarrollo de técnicas, formación de talento humano entre otros logros y lo fundamental acotar el origen de los defectos para generar planes de acciones que permita mejorar la calidad de los productos. El estudio de los aceros micro aleados al Nb, V, Ti así como aceros al V. Con estos proyectos se generó un conocimiento de aplicación para entender el comportamiento de estos aceros, así como los ajustes químicos o de procesamiento para su mejora. Finalmente, impulsar y liderar la inves gación colec va de la fac bilidad del uso del coque de petróleo venezolano, en la pele zación y en la aceración, lo que representa un logro de muchas sa sfacciones que hoy en día ya es una realidad. ¿Qué significa para usted haber recibido el Premio Nacional de Ciencia y Tecnología del año 2022, mención honorífica, por parte del Ministerio del Poder Popular para la Educación Universitaria, Ciencia y Tecnología?
Tiene un significado especial, ya que la Región Guayana merece que le reconozcan este trabajo colec vo de inves gación y en par cular, que se premie la cultura de inves gación del Sidorista, que se desarrolla desde el Ins tuto de Inves gaciones Metalúrgicas de Materiales, aperturado cuando se nacionalizó y rescató de las manos privadas la Siderúrgica Venezolana y cuyo reconocimiento me llena de orgullo como mujer inves gadora inspirada y mo vada en los procesos produc vos industriales.
“Se viene fortaleciendo de forma novedosa un nuevo modelo de gestión participativa y protagónica de los trabajadores que multiplican la actividad de investigación ... REVISTA MUNDO FERROSIDERÚRGICO | AÑO XI | NÚMERO 44 | JULIO 2022
Según sus vivencias, ¿Cómo es el proceso de formación de un inves/gador? Expónganos, ¿algunas reflexiones para los nuevos inves/gadores en el área industrial? El proceso de formación de un inves gador inicia por tener un perfil o sensibilidad hacia ese proceso de indagar, con el obje vo de ampliar el conocimiento de per nencia que permita solucionar o resolver situaciones y mejorar la calidad de vida, a través de la aplicación de una estructura metodológica, que parte de una hipótesis preliminar que debe ser comprobada. Con el estudio permanente en el área de interés, combinando la prác ca de ensayo y error asociado a los experimentos, van apareciendo las herramientas y se va moldeando al inves gador, con la escritura y reportes de los trabajos y los elementos de capacidad de síntesis para explicar y reportar las soluciones o explicaciones de las situaciones evaluadas. La inves gación contrario a lo que muchos piensan, es un trabajo colec vo, donde el trabajo en equipo, es otro elemento clave que delinea a un inves gador. Finalmente, a los inves gadores noveles, se les invita a fortalecerse en colec vo e incen var al máximo, el interés en los trabajos de inves gación, a la solución de problemas que eleven la calidad de vida del ser humano y con esto responder a los planes de la Nación Venezolana, expresados en el plan de la Patria.
Como actual Directora de Calidad e Inves/gación de una de las empresas más importantes de la región y del país como lo es SIDOR, ¿Cuáles han sido los avances en materia de inves/gación?
En el contexto actual del renacer de las empresas y par cularmente el solventar las limitaciones del suministro de materias primas o de partes y piezas, impuestas por el bloqueo económico; la ac vidad de inves gar con los dis ntos actores de la inves gación industrial que están en toda SIDOR, se ha centrado en líneas de trabajo orientadas a soluciones tecnológicas, que contribuyen a la con nuidad opera va de los procesos produc vos, lográndose la innovación en la sus tución de importaciones y el desarrollo del acero, entre otros. ¿Qué experiencia nos puede indicar en el área I+D+i en SIDOR? I+D+i, se en ende que son sistemas de ges ón que promueve la Inves gación, Desarrollo Tecnológico e Innovación, que cuentan con estructuras y procesos sistemá cos organizados, conforme al modelo de ges ón de la empresa a la que pertenecen. En SIDOR estamos conduciendo estos procesos, considerando la referencia de la Norma ISO 9001, la cual viene fortaleciendo de forma novedosa ese modelo, donde los trabajadores y trabajadoras de manera par cipa va y protagónica, se involucran en la ac vidad de inves gación. Con la incorporación de ellos, se logra la construcción colec va permanente de soluciones a los procesos produc vos, a través de la estructuración sistemá ca de los Equipos de Trabajo, Estudio, Inves gación y Resguardo (ETEIR) . Desde su perspec/va.. ¿Qué importancia /ene la ges/ón de los laboratorios de calidad, como parte del proceso de inves/gación para la Sus/tución de Importaciones de partes y piezas tanto en SIDOR como en las demás empresas tuteladas de CVG? ¿Cuál es su experiencia? Los laboratorios de calidad de las empresas CVG, son pilares fundamentales, que no solo garan zan que los productos cumplan con los parámetros de especificaciones de calidad exigidos, sino que también apoyan esta polí ca mediante la capacidad que enen para realizar los análisis 5sico-químicos de las materias primas, partes y piezas, con igual o mejor de los que se venían importando. De manera muy personal, ¿Cuál es el desa>o para este año 2022 en materia de Inves/gación y Desarrollo? Concien zar que; los procesos de inves gación, sean sensibles a la economía circular y el ahorro energé co es de vital importancia para la sustentabilidad y así minimizar las emisiones de gases con efecto invernadero para el bienestar del ser humano.
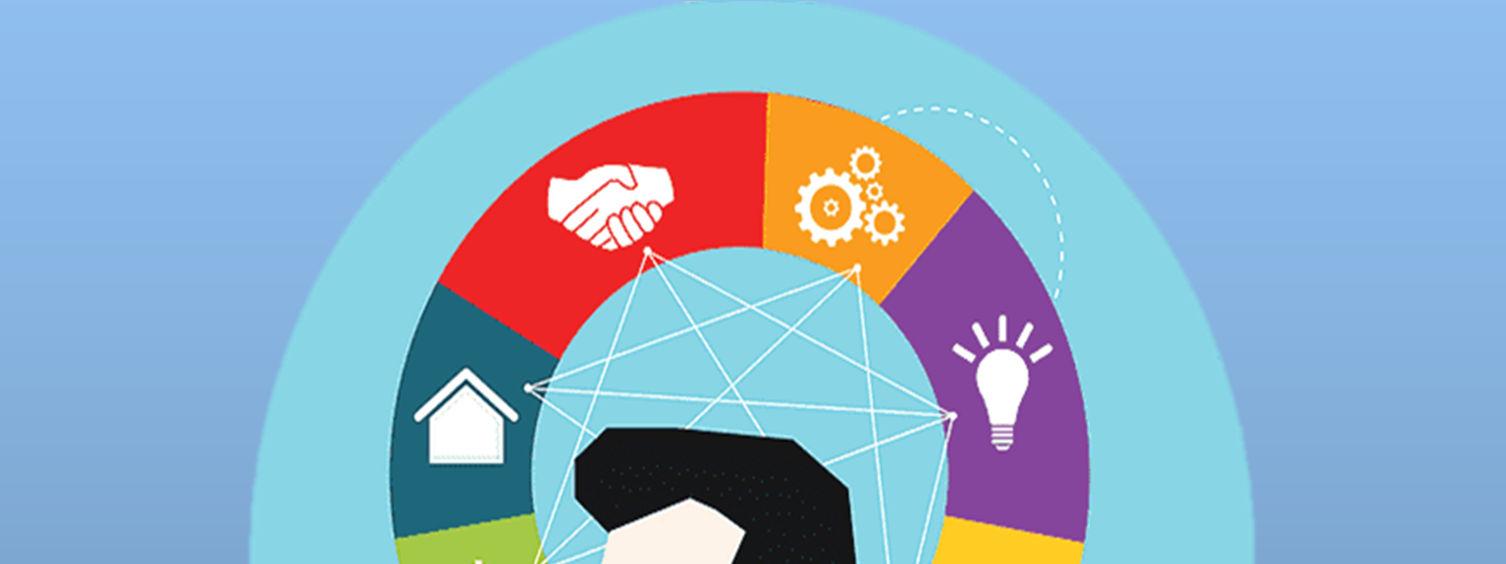
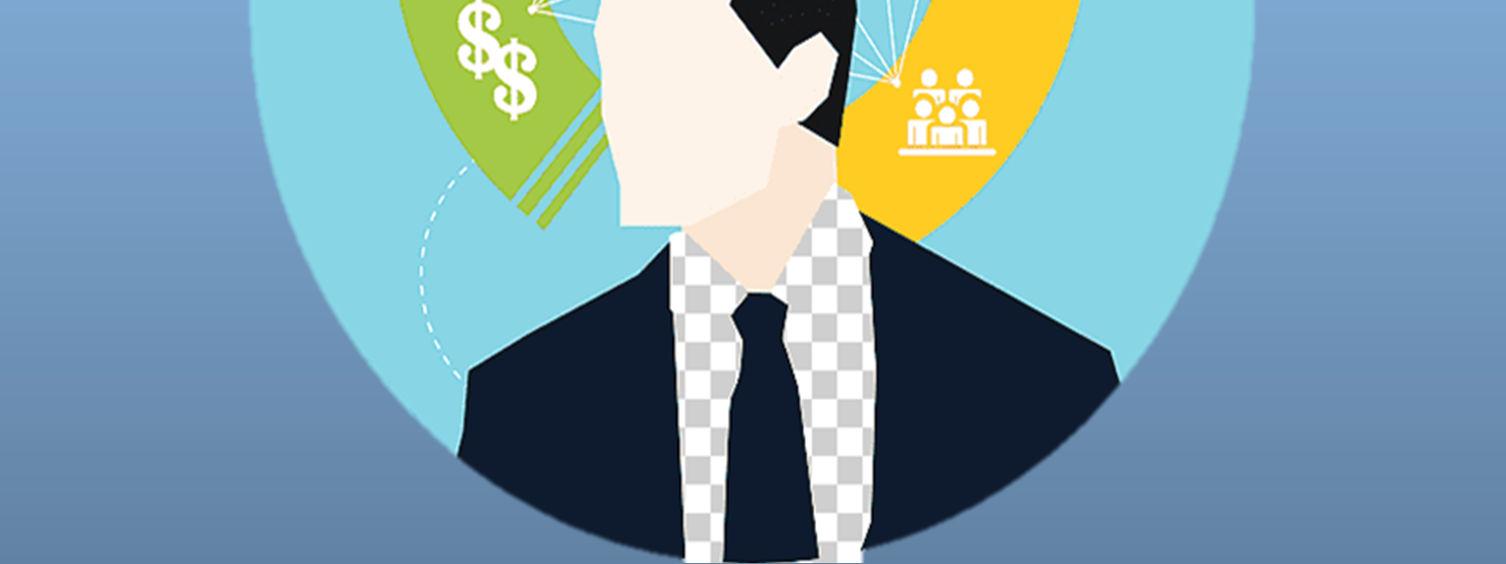
Fuente: Tomado de la Web.
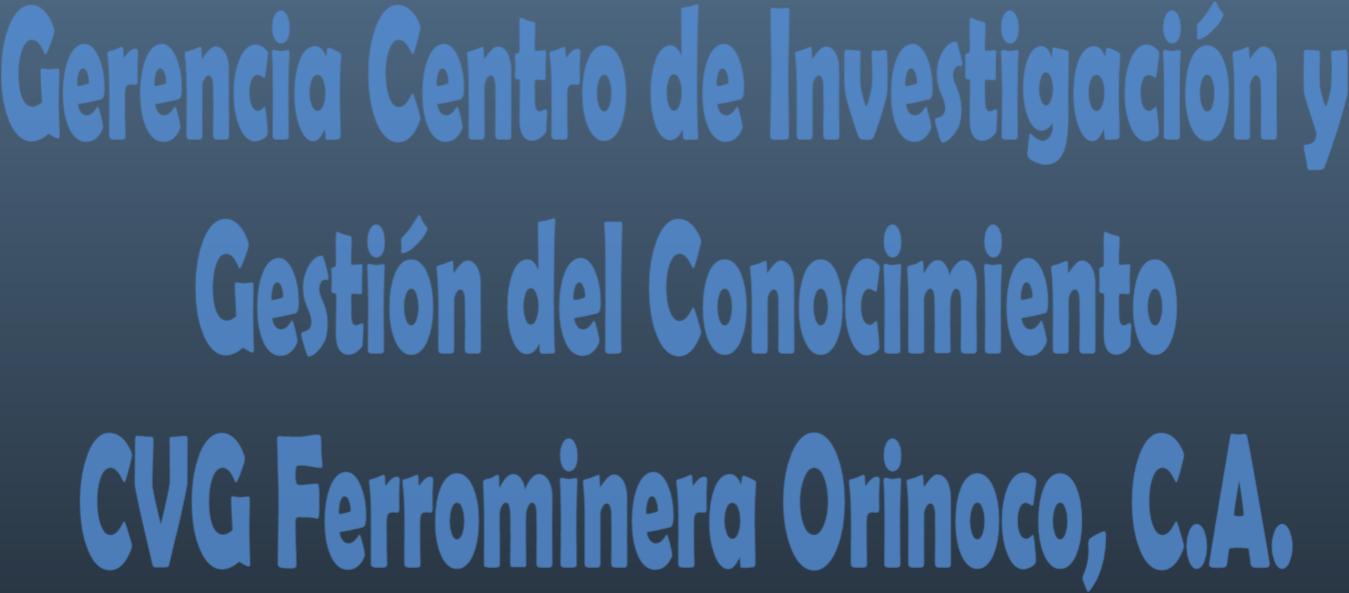
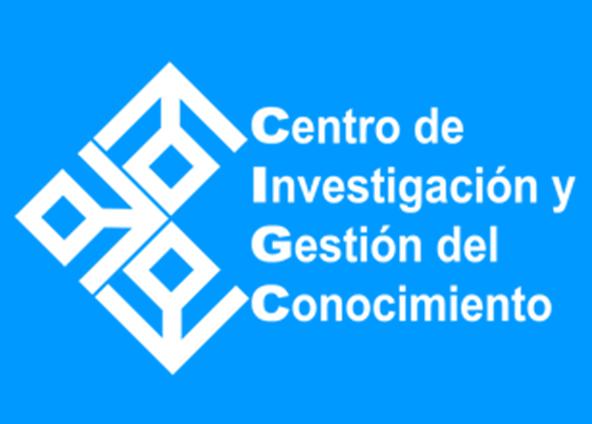
PERSPECTIVAS DE MERCADO
E s t a s e c c i ó n e s t á enmarcada en brindar soluciones y estrategias, a través de contenido, d o c u m e n t a l e s e i n f o r m a c i ó n d e actualidad, que permita el análisis avanzado de noticias y tendencias en el mercado del mineral de hierro.

Perspectivas de Mercado del Mineral de Hierro
1. El crecimiento de la producción mundial de mineral de hierro se acelerará hasta 2026 Simandou, es una de las mayores y más ricas reservas de mineral de hierro del mundo. (Imagen cortesía de NWR Civil and Mining).

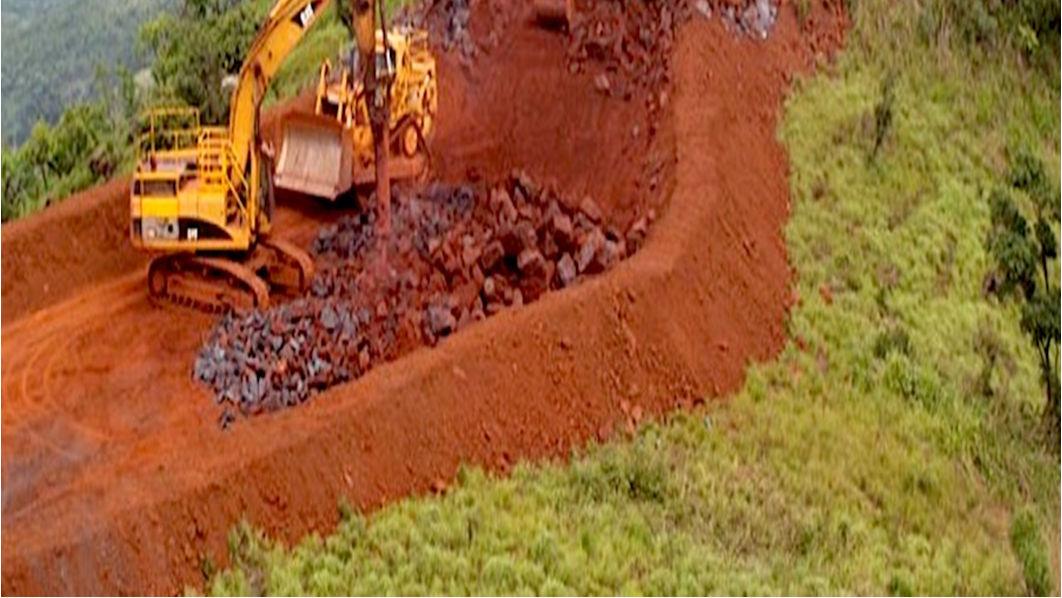
Fuente: MINING.COM Staff Writer 27 de junio de 2022
El crecimiento de la producción mundial de mineral de hierro se acelerará en los próximos años, poniendo fin al estancamiento que ha persis do desde que los precios del mineral de hierro alcanzaron un promedio mínimo de una década de 55 dólares por tonelada en 2015, afirma el analista de mercado Fitch Solu ons en su úl mo informe de la industria.
El crecimiento con nuo, aunque más lento, en Australia y más rápido en Brasil, aunado a la estabilización en la producción de mineral de China con nental, serán los principales impulsores del crecimiento, dice Fitch. China inver rá fuertemente en minas en el extranjero para mejorar la seguridad del suministro de importación de mineral de hierro y Guinea, será un importante beneficiario de esta tendencia, a través del proyecto Simandou.
Fitch pronos ca un crecimiento de la producción minera global en un promedio de 2,7 % entre 2022 y 2026 en comparación con -1,3 % en los cinco años anteriores.
Esto elevaría la producción anual en 361,7 millones de toneladas en 2026, en comparación con los niveles de 2022, aproximadamente el equivalente a la producción combinada de Rusia, India y Sudáfrica en 2022.
El crecimiento de la oferta será impulsado principalmente por Brasil y Australia, mientras que la minera brasileña Vale, S.A; ene planes de expansión agresivos, señala Fitch y agrega que las mineras en Australia, incluidas BHP, Rio Tinto y Fortescue, reinver rán las ganancias actualmente boyantes en producción adicional.
En China con nental, la producción de mineral de hierro, volverá a aumentar en los próximos tres o cuatro años, ya que el país trabaja para aumentar su autosuficiencia y reducir las importaciones australianas, que han disminuido significa vamente en los úl mos años, predice el analista.
Dado que los mineros de China operan en el extremo superior de la curva de costos del mineral de hierro y las leyes nacionales del mineral seguirán disminuyendo, Fitch espera que las empresas chinas den prioridad a la inversión en minas de mineral de hierro en el extranjero, como el depósito gigante Simandou en Guinea.
Se espera un crecimiento de la producción mundial del mineral de hierro, este avance se notará en los próximos años, poniendo fin al estancamiento que se venía suscitando desde 2015.
Tomando en consideración que China inver rá en minas en el extranjero que conllevará a un fortalecimiento en la importación del mineral de hierro, esta inversión está respaldada principalmente por los países Brasil y Australia.

Perspectivas de Mercado del Mineral de Hierro
2. El precio del mineral de hierro sube a medida que China alivia las restricciones de COVID-19.

Fuente: Reuters | 28 de junio de 2022 (Por Enrico De la Cruz; Editado por Rashmi Aich).
El mineral de hierro subió nuevos máximos de una semana, el martes 28 de junio de 2022, ya que China relajó algunos requisitos de cuarentena para las llegadas internacionales y Beijing y Shanghái no registraron nuevos casos locales de Covid-19, lo que provocó un repunte generalizado de los metales. El contrato del ingrediente siderúrgico en la Bolsa de Singapur subió un 4,1 % a 124,80 dólares la tonelada, a las 08:12 GMT, después de alcanzar su nivel más alto desde el 17 de junio de 2022, a 125 dólares.
En la Bolsa de productos básicos de Dalian de China, el contrato de mineral de hierro más negociado de sep embre, finalizó el comercio diurno con un aumento del 6,3 % a 809 yuanes (120,99 dólares) la tonelada, luego de alcanzar su nivel más alto desde el 20 de junio de 2022 a 812 yuanes.
China redujo a la mitad el empo de cuarentena para los viajeros entrantes en una importante flexibilización de uno de los bordillos Covid-19 más estrictos del mundo, que han disuadido los viajes dentro y fuera del país desde 2020 y ralen zado la ac vidad económica. Beijing y Shanghái, no informaron nuevas infecciones locales el martes 28 de junio de 2022, la primera vez que ambas ciudades estaban libres de problemas simultáneamente desde fines de febrero, después de meses de luchar contra los peores brotes de su historia.
El corrugado de acero para la construcción en la bolsa de futuros de Shanghái subió un 2,5 %, mientras que las bobinas laminadas en caliente subieron un 2,1 %. El acero inoxidable subió un 0,3 %.
El carbón coquizable de Dalian subió un 7,7 % y el coque avanzó un 5,6 %. “La presión para reducir la producción de acero crudo frenará la demanda de materias primas”, dijeron los analistas de Zhongzhou.
Por lo antes expuesto, “El precio del mineral de hierro toma un repunte en su aumento, debido a que China minimizo un poco las restricciones de los requisitos para viajeros entrantes al país, todo gracias a que Beijing y Shanghái no registraron nuevos casos de Covid-19, hasta ahora ambas ciudades están libres de brotes”, (Karla Aponte, 05 de julio de 2022).

Fuente: MINING.COM |29 de junio de 2022 con archivos de Reuters y Bloomberg) mineral de hierro enriquecido (Imagen de archivo)
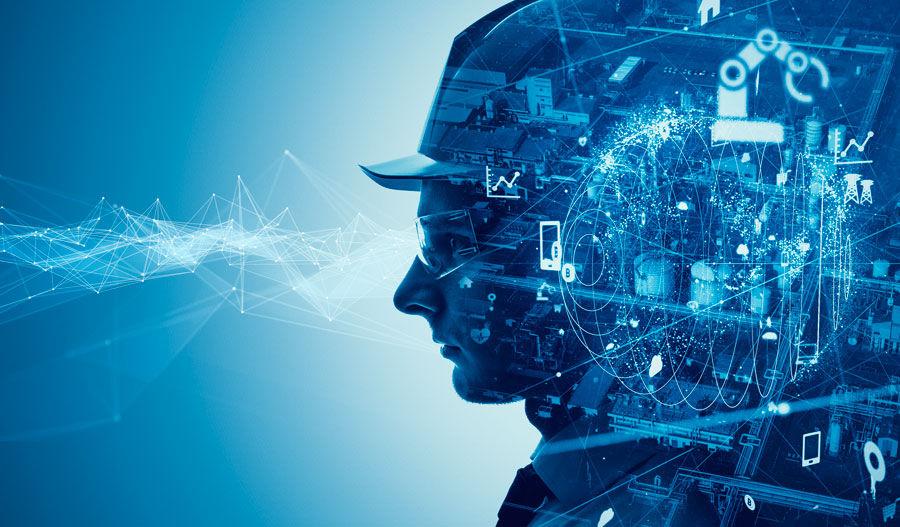
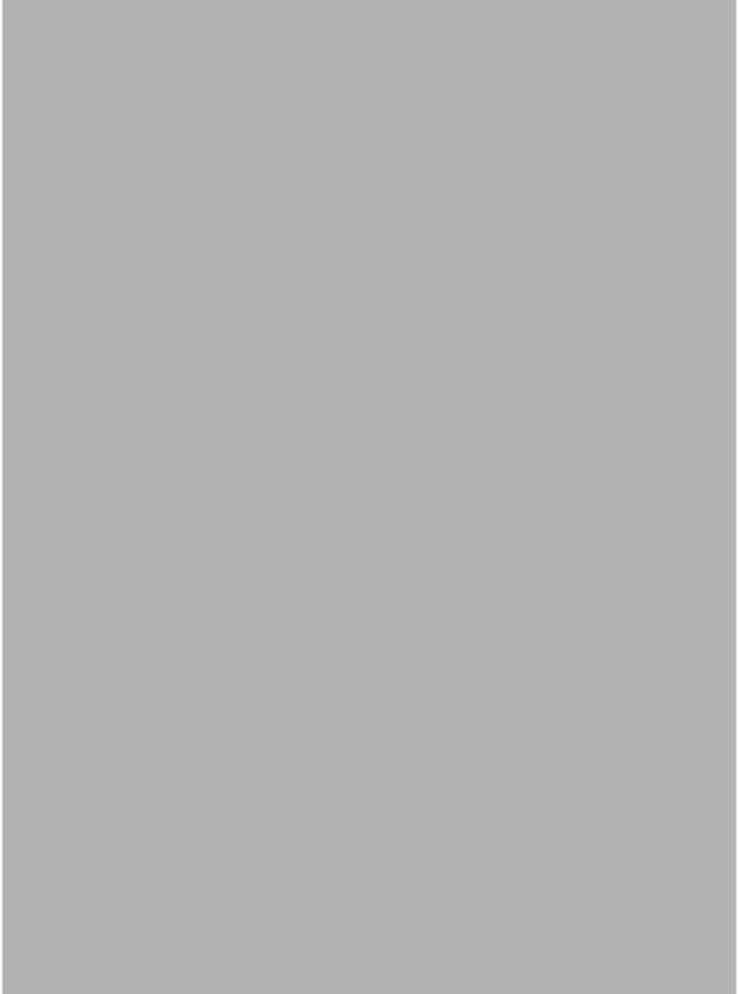
Fuente: Tomado de la Web.
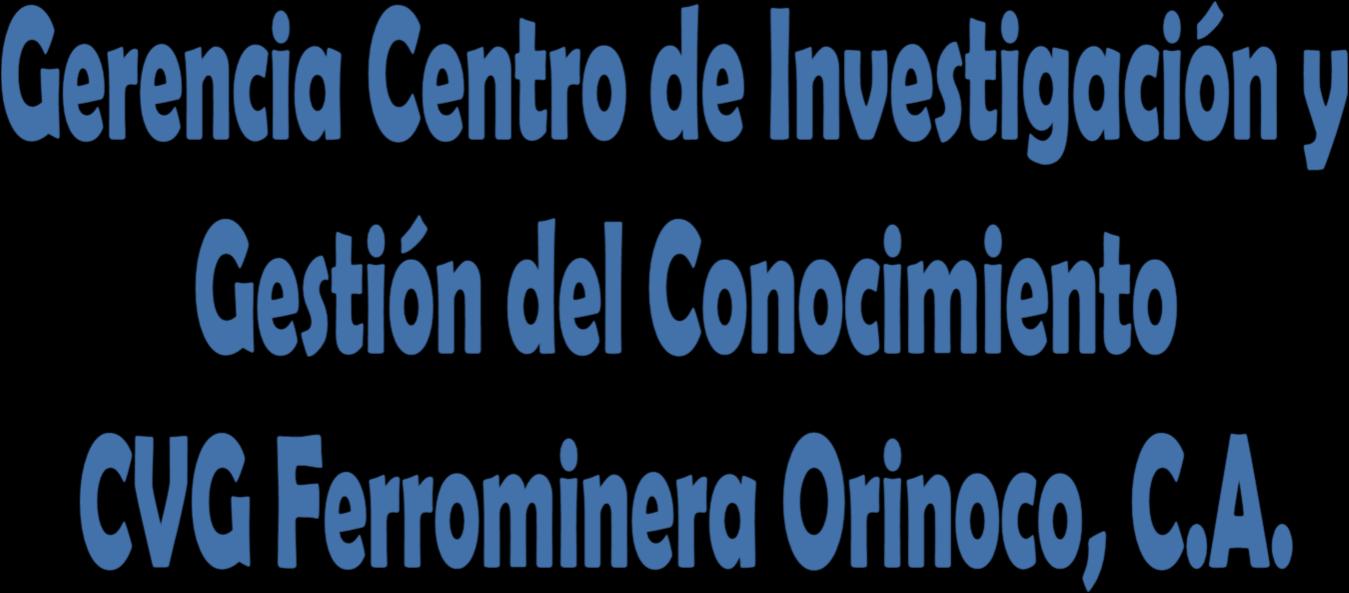
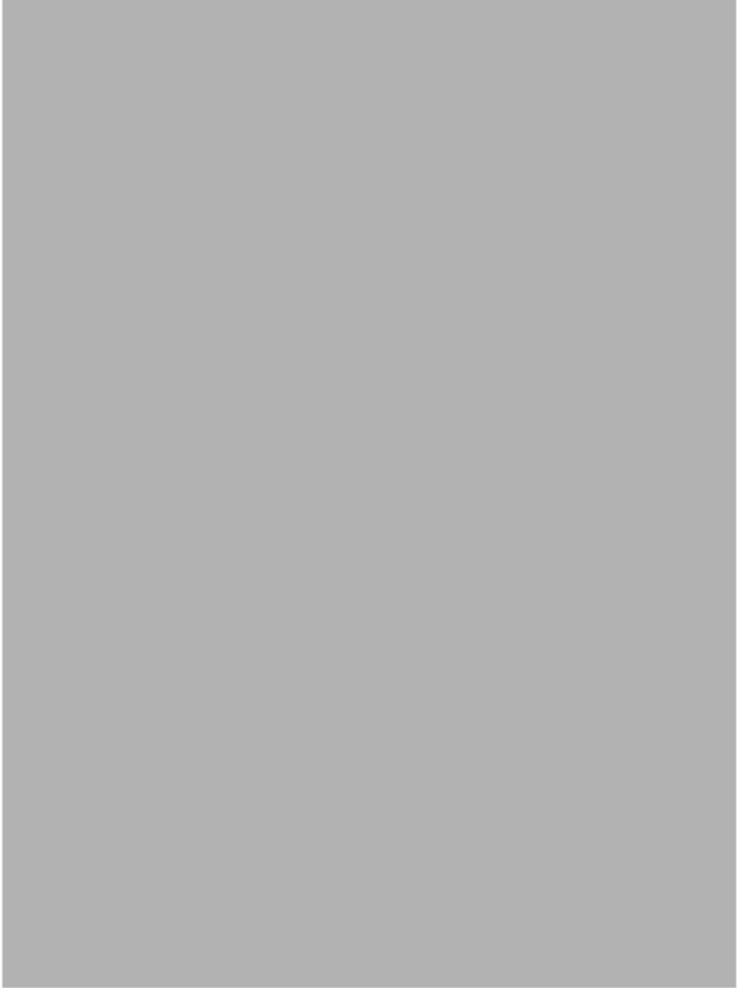
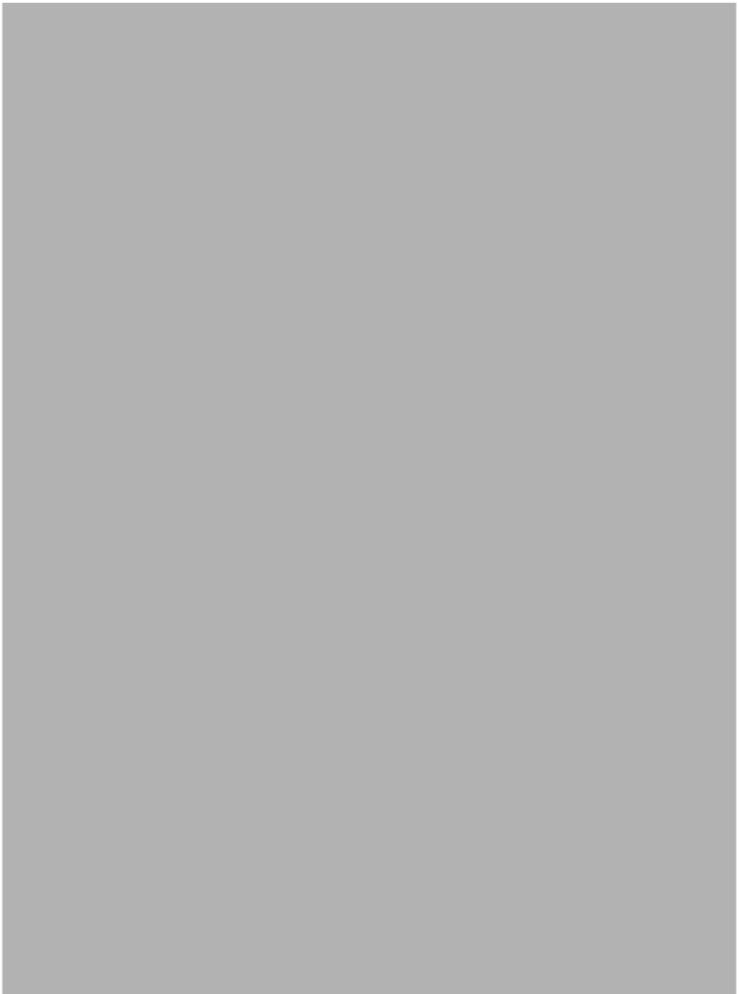
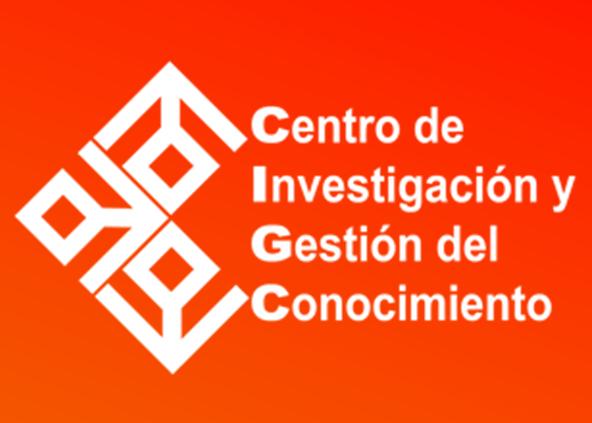
I+D+i
E n e s t a s e c c i ó n presentamos los desarrollos, i n n o v a c i o n e s e investigaciones know how plasmados en papel, tanto de los trabajadores de CVG Ferrominera Orinoco, C.A. como de las empresas h e r m a n a s d e l a Corporación Venezolana de Guayana y academias en pro de las mejoras de los p r o c e s o s o p e r a ti v o s y a d m i n i s t r a t i v o s d e l a industria del hierro y el acero.

I+D+i
ESTUDIO DE FORMACIÓN DE COSTRAS ATÍPICAS EN REACTOR MIDREX DE BRIQCAR ANTIGUA VENPRECAR. REVISTA MUNDO FERROSIDERÚRGICO | AÑO XI | NÚMERO 44 | JULIO 2022 Artículo de Investigación: ESTUDIO DE FORMACIÓN DE COSTRAS ATÍPICAS EN REACTOR MIDREX DE BRIQCAR ANTIGUA VENPRECAR
Díaz Ervis1, Amundarain Yannellys2, Barrios Willian3, Basanta Gloria4, Barrera Maritza5, Morales Jesús6
1 MSc. Ingeniería Metalúrgica, Especialista en Investigación, Gerencia Instituto de Investigaciones Metalúrgicas y Materiales, SIDOR. C.A., Ciudad Guayana, Venezuela. 2 TSU en Metalurgia, Técnico de Investigación. Gerencia Instituto de Investigaciones Metalúrgicas y Materiales, SIDOR. C.A. Ciudad Guayana,
Venezuela. 3 TSU en Metalurgia, Ingeniero Investigador. Gerencia Instituto de Investigaciones Metalúrgicas y Materiales, SIDOR. C.A. Ciudad Guayana, Venezuela. 4 MSc. Ingeniería Metalúrgica, Directora de Calidad e Investigación, Gerencia Instituto de Investigaciones Metalúrgicas y Materiales, SIDOR. C.A. Ciudad Guayana, Venezuela. 5 MSc. Ingeniería Metalúrgica. Gerente de IIMM, Gerencia Instituto de Investigaciones Metalúrgicas y Materiales, SIDOR. C.A. Ciudad Guayana,
Venezuela. 6 TSU en Química General, Superintendente de Control de Calidad, Gerencia de Calidad, BRIQCAR Ciudad Guayana, Venezuela. . Email: ervisd2987@gmail.com.; willianb58@gmail.com; mbarreras@sidor.com; gbasanta@sidor.com Fecha recibida: 27/05/2022 Fecha aprobado: 03/06/2022
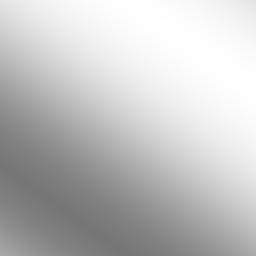
Correspondencia: Gerencia Centro de Investigación y Gestión del Conocimiento CVG Ferrominera Orinoco, C.A.— Ciudad Guayana, Estado Bolívar, Venezuela Teléfonos de contacto: +58 (286) 9304344


Resumen— El estudio de costras atípicas, definidas por su acelerada cinética de crecimiento, formadas sobre el material refractario en el reactor de BRIQCAR con tecnología Midrex, se basó en el análisis macro y microestructural de las mismas, con la complementariedad de Difracción de Rayos X, realizando comparación con costras típicas formadas en periodos anteriores que sirvan de referencia. En la caracterización macroscópica, se consideró el análisis de imagen para la determinación de los tamaños de las partículas y pellas presentes en las costras. Para la caracterización microestructural de costras atípicas, se consideraron la capa externa o zona expuesta en el reactor y la capa interna o adherida al refractario. Los resultados evidencian que las costras atípicas analizadas están constituidas por aglomerados de pellas de tamaños que van desde 10 mm hasta 26 mm; unidas por partículas finas y fragmentos de pellas fracturadas, cuyos enlaces se forman por fases eutécticas de bajo punto de fusión (CaO.SiO2.FeO) que propician adherencia de las partículas y crecimiento de las capas que forman las costras; se diferencian de la costra típica debido a que esta última no posee pellas y partículas de gran tamaño, deduciéndose que el acelerado proceso de crecimiento de las costras atípicas se relaciona a la presencia de pellas y partículas de tamaños que alcanzan 1”. Palabras claves— Costras, Pellas, Reactor Midrex, Ganga, Reducción.



I+D+i
ESTUDIO DE FORMACIÓN DE COSTRAS ATÍPICAS EN
Abstract: The study of atypical crusts, defined by their accelerated growth kinetics, formed on the refractory material in the BRIQCAR reactor with Midrex technology, was based on their macro and microstructural analysis, with the complementarity of X-Ray Diffraction, performing comparison with typical crusts formed in previous periods that serve as a reference. In the macroscopic characterization, image analysis was considered to determine the sizes of the particles and pellets present in the crusts. For the microstructural characterization of atypical crusts, the external layer or zone exposed in the reactor, and the internal layer or adhered to the refractory were considered. The results show that the atypical crusts analyzed are made up of agglomerates of pellets with sizes ranging from 10 mm to 26 mm; joined by fine particles and fragments of fractured pellets, whose bonds are formed by eutectic phases with a low melting point (CaO.SiO2.FeO) that promote adherence of the particles and growth of the layers that form the crusts; they differ from the typical crust because the latter does not have pellets and large particles, deducing that the accelerated growth process of atypical crusts is related to the presence of pellets and particles of sizes that reach 1”.
Keywords: Crusts, Pellets, Midrex Reactor, Gangue, Reduc on.


I. INTRODUCCIÓN
En el proceso de reducción de BRIQCAR, con tecnología Midrex, se originan de manera natural sobre el material refractario del reactor, formaciones de depósitos de baja ciné ca de crecimiento, con espesor menor a 15 mm, formada en un período aproximado de dos años (denominada costra >pica); sin embargo en el úl mo mantenimiento realizado, se detectaron costras de alta ciné ca de crecimiento, con formaciones de hasta de 10 cm de espesor formadas en un período menor a un año (denominada costra a+pica). En función a lo mencionado en el estudio, se consideran muestras significa vas de costras tanto >picas como a>picas.
Las variables que pueden afectar la formación de costras en los reactores son muchas, abarcando las variables inherentes al proceso, las cuales poseen el mayor impacto; así como también la variable asociada a la materia prima (pellas/mineral). Entre las variables que se asocian a la formación, se encuentran el refractario (asociando su porosidad), esfuerzo generado por la presión del reactor (esfuerzo normal) y por el movimiento de avance de pelets (esfuerzo cortante); temperatura, adición de cemento, po de pelets, porcentaje de metalización y carbono, velocidad angular, po de gas reductor, empo; conociéndose que mayor empo en el reactor, genera mayor degradación del pelets.
En el proceso, el HRD fluye plás camente y disminuye su porosidad a temperaturas mayores a 650 °C y se compacta a una presión mayor a 1000 Kg/cm2. Este fenómeno ocurre en los puntos de contactos entre los pelets y la pared del refractario, siendo la variable más importante, el esfuerzo cortante originado por el movimiento y el esfuerzo normal; el cual se ve incrementado en el contacto con superficies más porosas y de mayor área de contacto entre los pelets y la pared refractaria.
En el mecanismo de anclaje intervienen la generación de finos y su penetración en los poros para posterior sinterizado. En el crecimiento, el factor de relación entre las par>culas más grandes y las más pequeñas juega un papel importante por afectar el número de coordinación (puntos de contacto), regidas por la Ecuación de Rumpf [4]. CENTRO DE INVESTIGACIÓN Y GESTIÓN DEL CONOCIMIENTO PÁG. 12

I+D+i
ESTUDIO DE FORMACIÓN DE COSTRAS ATÍPICAS EN
Otro punto importante vinculado a la formación de costras es el S cking entre pelets, encontrándose factores que afectan el S cking y las variables de proceso, como la calidad de la materia prima; tanto pellas como de mineral de hierro. Los factores más importantes se relacionan a la temperatura y su interacción con el contenido de ganga, po y tamaño de mineral/pellas, contenido de hidrógeno en gas mezcla y por úl mo la forma externa de las par>culas [5].
II. MATERIALES Y MÉTODOS
Muestreo:
El análisis contempló el muestreo de dos pos de costras, las a>picas (con formaciones hasta 10 cm de espesor) y las >picas (no más de 15 mm de espesor) que fue re rada en su oportunidad en uno de los tornillos de la parte baja del reactor.
Análisis macroscópico:
Caracterización macroscópica de las costras a>picas, con análisis de imagen que permita determinar el tamaño de las pellas adheridas a las costras.
Análisis por DRX:
Se procedió a la pulverización de muestras de costras a>picas a malla 100, iden ficando los compuestos presentes en dos zonas dis nguibles y separadas entre sí:
Alta concentración de finos (región externa de la costra). Alta concentración de pellas (región más interna).
Análisis Microscópico:
Caracterización microestructural de costras >picas, que marquen una referencia visual/microestructural de las costras “esperadas” en el reactor.
Caracterización microestructural de las costras a>picas, en las dis ntas zonas detectadas. Análisis de varianza del comportamiento del patrón de carga de alimentación de pellas al reactor Midrex de BRIQCAR, por mes, desde enero de 2020 hasta junio 2021.
III. RESULTADOS Y DISCUSIÓN
Análisis microscópico
En las figuras 1A, 1B y 1C, se pueden observar las caracterís cas macroscópicas de las costras re radas del reactor de BRIQCAR, evidenciándose la presencia de pellas adheridas/incrustadas, con fracciones de pellas fragmentadas y finos entre los inters cios, además se observa una capa formada totalmente de finos; indicios de que en la formación de las costras existe una interacción entre los dis ntos tamaños de par>culas que ingresan al reactor. En la figura 1D, se puede observar que el 50 % de pellas adheridas/incrustadas en estas regiones de las costras, poseen tamaños comprendidos entre 15 y 19 mm, correspondiendo una can dad mayor al 70 % de pellas con tamaños superior a 5/8”, hallándose pellas que alcanzan tamaño de 1”.

Figura 1: A, B, C) Costras a>picas re radas del reactor de reducción de BRIQCAR; D) Distribución de tamaños de pellas adheridas/incrustadas en la costra.

I+D+i
ESTUDIO DE FORMACIÓN DE COSTRAS ATÍPICAS EN
Análisis por DRX Caracterís)cas microestructurales de la costra +pica
En la tabla 1, se pueden evidenciar los compuestos presentes en la costra a>pica, determinados mediante DRX. Se observa que en la capa más externa de la costra, formada principalmente de finos, presenta como compuestos mayoritarios hierro metálico (Fe°) y silicato de calcio-magnesio (CaMgSi2O6), indicios de altas proporciones de ganga en esta zona de la costra los cuales están ligados al hierro metálico (Fe°); además presenta contenidos significa vos de Fe2O3 asociados a finos de pellas o de mineral sin reducir; con la presencia de compuestos minoritarios como FeO y SiO2, los cuales son comunes en HRD.
En capa interna, cons tuida mayoritariamente por pellas adheridas/incrustada se puede observar que la fase mayoritaria y principal es el Fe°, indicios de que poseen un alto grado de reducción, posiblemente debido a que estas presentan un mayor empo de exposición en el reactor Midrex a los gases reductores, presenta además como fases minoritarias wus ta (FeO), magnesioferrita (Fe2MgO4) y sílice (SiO2), compuestos que se encuentran habitualmente tanto en las pellas como en el HRD.
Tabla 1: Compuestos en la costra a+pica.
Fe° Capa Externa (Finos) Capa Interna (Pellas)
CaMgSi2O6 ↑↑
Fe2O3
FeO
Fe2MgO4
SiO2
Fuente: Elaboración propia del autor. En las figuras 2A y 2B, se observa la microestructura de la costra >pica, una aglomeración de par>culas Fe° de sílice/ cuarzo y de ganga, posiblemente debido en su formación está asociada a fases líquidas en la superficie externa de las par>culas, el cual es impulsado por la presencia de ganga, que promueven la formación de fases eutéc cas de bajo punto de fusión (CaO.SiO2.FeO) que se adhieren a las pellas y a los finos de mineral de hierro [5].
El inicio de formación de estas costras, se relaciona con la interacción de finos de pellas/mineral con los poros o grietas del ladrillo refractario debido a los esfuerzos cortantes [5].
De lo observado en la costra >pica, la incidencia de la ganga sin transformar (sílice) así como la ganga presente (silicatos fundidos CaO.SiO2.FeO) son factores importantes a considerar en la formación y crecimiento de las costras generadas en el reactor.
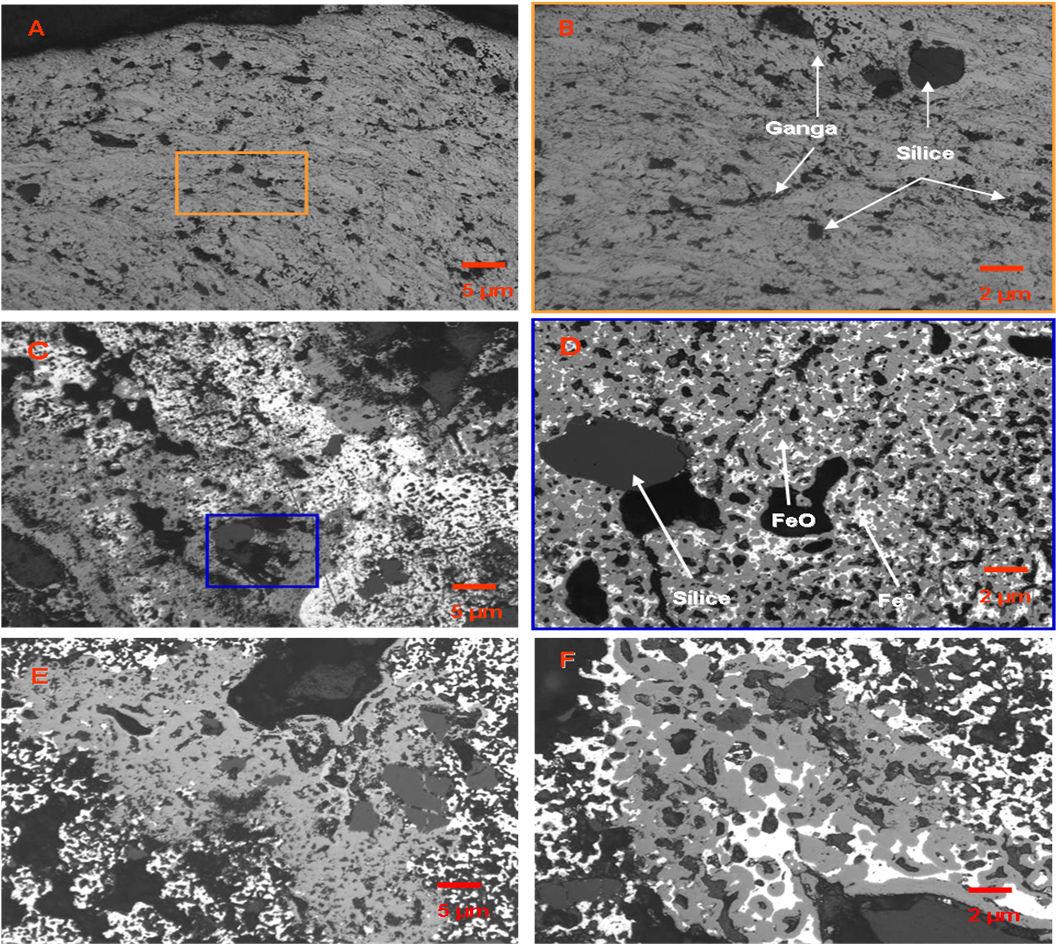
Figura 2: A y B) Microestructura de la costra típica; C y D) Microestructura de la costra atípica-última capa formada; E y F) Región interna.

I+D+i
ESTUDIO DE FORMACIÓN DE COSTRAS ATÍPICAS EN
REACTOR MIDREX DE BRIQCAR ANTIGUA VENPRECAR. REVISTA MUNDO FERROSIDERÚRGICO | AÑO XI | NÚMERO 44 | JULIO 2022
Caracterís)cas microestructurales de costra a+pica
En la figura 2C y 2D, se observa la microestructura de la capa de la costra que corresponde al borde, relacionándose a la úl ma capa formada, donde se puede evidenciar una estructura similar a la costra >pica con presencia de hierro metálico y wus ta, con un grado mayor de ganga en su estructura, detectándose por DRX la presencia de ganga compleja (CaMgSi2O6), además de sílice, que apuntan a que esta ul ma capa formada obedece al mismo mecanismo de formación que la costra >pica asociado a fase líquida en la superficie externa de las par>culas, reforzado aún más por mayor concentración de ganga en esta región.
En las figuras 2E y 2F, se observa la estructura del borde y del centro de las pellas adheridas a la costra en la zona interna, donde se puede evidenciar que la región del borde de la pella, guarda similitud con las regiones antes descritas, correspondiendo a una estructura porosa de hierro metálico y wus ta, con can dades significa vas de ganga y sílice; por su parte el centro de la pella presenta una porosidad aún mayor que en el borde, observándose también la presencia de ganga y sílice.
Este po de costra, se ha documentado en otros estudios; para procesos de reducción de lecho móvil; indicios de que la formación de este po de costras, son eventos naturales en los reactores de reducción; siendo lo más importante el control de la ciné ca de formación, a través de la inhibición de los elementos ac vadores.
Los análisis realizados no evidencian relación entre la formación de costras, con los combus bles sólidos empleados en la fabricación de pellas. Su formación se relaciona a la presencia de agentes ac vadores como poros y grietas en el material refractario, los cuales captan los finos que interactúan con la ganga para formar la primera capa, donde se adhieren pellas de dis ntos tamaños, siendo incrementada la ciné ca por presencia de pellas y par>culas de tamaños mayores a 1”. Análisis de varianza del comportamiento del patrón de carga de alimentación al reactor Midrex de BRIQCAR.
En las figuras 3A, 3B y 3C, se puede evidenciar el comportamiento de la carga de alimentación de las pellas producidas por SIDOR al reactor de BRIQCAR, donde se observa a par r de mayo de 2020, un incremento del porcentaje de pellas con tamaño mayor a 5/8” y ½”, aunado a disminución de la alimentación de pellas de 3/8”.
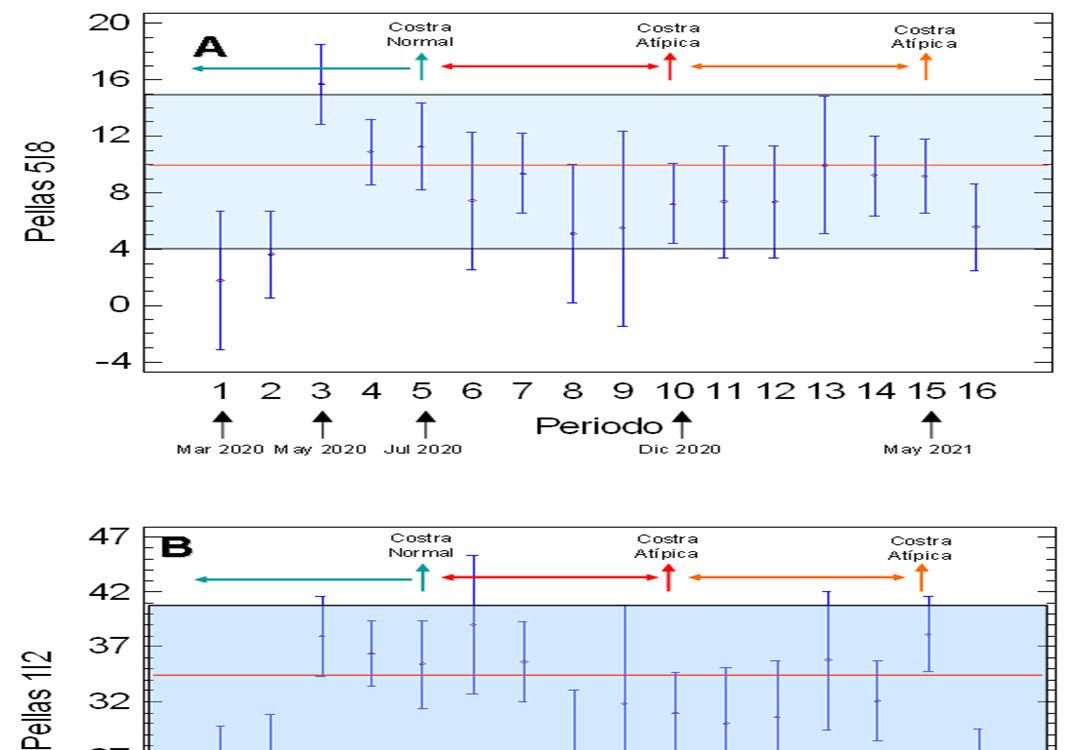

Figura 3: Comportamiento del patrón de carga de alimentación de pellas al reactor Midrex de BRIQCAR, A) Pellas 5/8”; B) Pellas ½” y C) Pellas 3/8”

I+D+i
ESTUDIO DE FORMACIÓN DE COSTRAS ATÍPICAS EN
REACTOR MIDREX DE BRIQCAR ANTIGUA VENPRECAR. REVISTA MUNDO FERROSIDERÚRGICO | AÑO XI | NÚMERO 44 | JULIO 2022
En general, la medida de los tamaños de pellas ingresadas al reactor incrementó, pudiendo estar relacionado a la formación de costras, donde se evidenciaron incrustadas/adheridas pellas de tamaño mayor a 5/8”.
En las pellas de mayor tamaño, superior a 16 mm (5/8”), se ha reportado que poseen menor densidad de poros ya que los mismos enden a coalescer, aunado a menor proporción de silicatos fundidos que actúen como puentes de unión entre los granos, además estas pellas son más propensas a formar estructuras dúplex y a generar grietas de contracción en la dirección radial durante el proceso de quemado; caracterís cas que las hacen menos resistentes por la diferencia de contracción de las fases; y más degradables, en los reactores; tendiendo a generar finos y pellas fragmentadas.
La presencia de pellas de tamaño mayor a 5/8”; propicia la generación de finos, y pueden estar relacionados al crecimiento acelerado de las costras; debido a que la interacción de pellas de gran tamaño con los finos presentes y los fragmentos de pellas aumentan el área superficial y el número de coordinación de las par>culas, incrementando la ciné ca de formación de cluster.
En las costras analizadas, se evidenciaron incrustadas/ adheridas pellas de tamaño mayor a 5/8”, alcanzando tamaños de 1”, rodeadas de finos y fragmentos de pellas; que validan lo mencionado. V. REFERENCIAS BIBLIOGRAFICAS
[1] Domingo, J., Ór z, U., Aguilar, J & Farías, L. (1995).
Mecanismo de formación de capas sobre las paredes de reactores de reducción directa.
Universidad Autónoma de Nueva León, México:
Tesis Doctoral en Ingeniería de Materiales.
[2] Ór z, U., Domingo, J., Aguilar, J & Farías, L. (2001, junio). Formación de capas de hierro en reactores de reducción directa. Parte I: Los Factores. Ingenierías,
IV, N° 11, pp. 11-19.
[3] Ór z, U., Domingo, J., Aguilar, J & Farías, L. (2001, sep embre). Formación de capas de hierro en reactores de reducción directa. Parte II: Ciné ca de
Crecimiento. Ingenierías, IV, N° 12, pp. 21-30.
[4] Mallol, J. (2005). Densificación y flujo de lechos de par>culas de cuarzo. Castellón, España: Tesis
Doctoral en Ciencias Químicas.
[5] Yi, L., Huang, Z & Jiang T. (2012, diciembre 3).
S cking of iron ore pellets during reduc on with hydrogen and carbon monoxide mixtures: Behavior and mechanism. Powder Technology, 235(2013), pp. 1001-1007.
[6] Dwarapudi, S., Devi, T., Mohan, S & Ranjhan, M. (2008). Influence of Pellet Size on Quality and
Microstructure of Iron Ore Pellets. ISIJ Interna onal, 48, pp.768-776.
IV. CONCLUSIONES
1. Las costras a>picas analizadas están cons tuidas por aglomerados de pellas de tamaños que van desde 10 mm hasta 26 mm; unidas por par>culas finas y fragmentos de pellas fracturadas.
2. El proceso de formación de costras a>picas, se origina por presencia de factores ac vadores como poros y grietas en la superficie del material refractario y el crecimiento es propiciado por adhesión de par>culas mediante la generación de fases eutéc cas en la superficie externa de las par>culas.
3. No se evidenció relación entre el combus ble sólido usado en la fabricación de pellas y la formación de costras en el reactor de reducción.
Mundo Ferrosiderúrgico Mercado, Ciencia y Tecnología
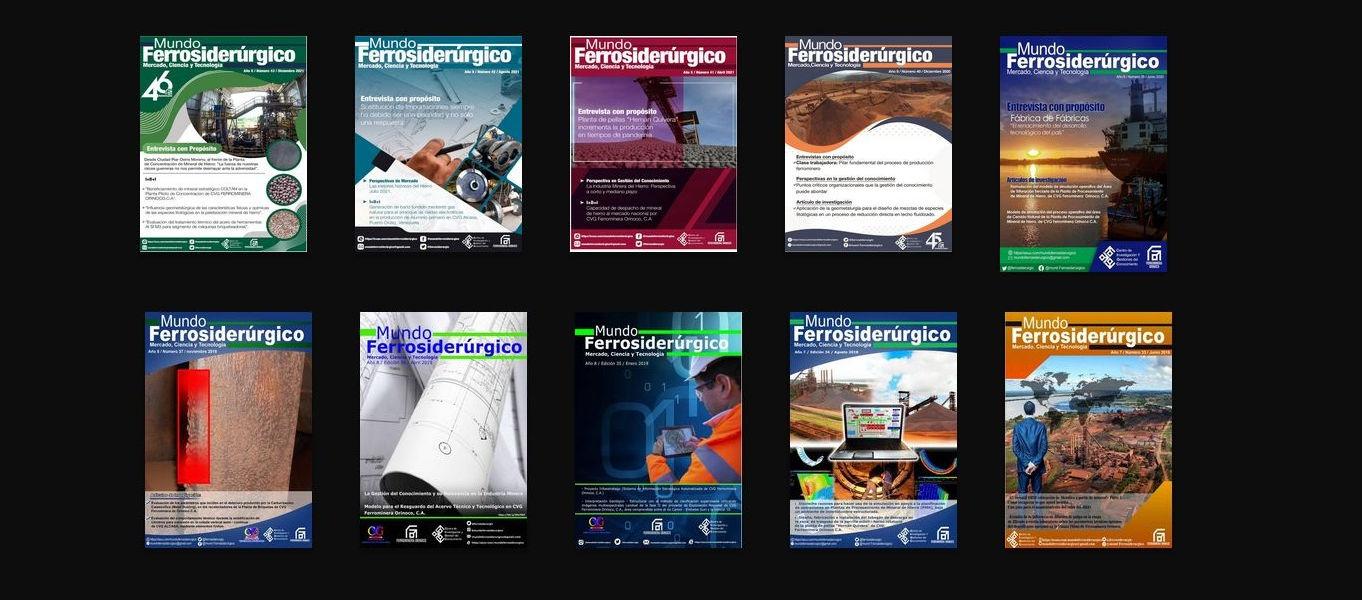
La Revista Mundo Ferrosiderúrgico, es una publicación de corte científico y tecnológico de la Gerencia Centro de Investigación y Gestión del Conocimiento de CVG Ferrominera Orinoco, C.A.
Política de Ciencia, Tecnología e Innovación de CVG Ferrominera Orinoco, C.A. Promover la investigación, para la generación, aplicación y divulgación de conocimientos, técnicas y tecnologías, con base a las necesidades de la organización en materia de ciencia, tecnología e innovación, mediante el fortalecimiento de las actividades de desarrollo tecnológico, vigilancia y resguardo de la información, transferencia y consolidación de redes de conocimientos y de apoyo en la ejecución y seguimiento de proyectos conjuntos de investigación, desarrollo e innovación; a los fines de incrementar el capital humano y aumentar su valor dentro del entorno organizacional, mejorar continuamente los procesos y la competitividad; así como fortalecer las redes entre los actores regionales, nacionales e internacionales, asociados a la gestión tecnológica.

I+D+i
Barrios Willian1 , Díaz Ervis2, Basanta Gloria3, Barrera Maritza4
1 TSU en Metalurgia, Ingeniero Investigador. Gerencia Instituto de Investigaciones Metalúrgicas y Materiales, SIDOR. C.A. Ciudad Guayana, Venezuela. 2 MSc. Ingeniería Metalúrgica, Especialista en Investigación, Gerencia Instituto de Investigaciones Metalúrgicas y Materiales, SIDOR. C.A., Ciudad Guayana, Venezuela. 3 MSc. Ingeniería Metalúrgica, Directora de Calidad e Investigación, Gerencia Instituto de Investigaciones Metalúrgicas y Materiales, SIDOR. C.A. Ciudad Guayana, Venezuela. 4 MSc. Ingeniería Metalúrgica. Gerente de IIMM, Gerencia Instituto de Investigaciones Metalúrgicas y Materiales, SIDOR. C.A. Ciudad Guayana,
Venezuela.

Email: willianb58@gmail.com; ervisd2987@gmail.com; gbasanta@sidor.com; mbarreras@sidor.com. Fecha recibida: 06/06/2022 Fecha aprobado: 10/06/2022
Correspondencia: Gerencia Centro de Investigación y Gestión del Conocimiento CVG Ferrominera Orinoco, C.A. | Ciudad Guayana, Estado Bolívar, Venezuela Teléfonos de contacto: +58 (286) 930.43.44


Resumen— En la búsqueda del aprovechamiento de materiales carbonosos de origen nacional que suplan la demanda de combus ble sólido de la industria siderúrgica, como es el caso del coque verde de petróleo (CVP), que se puede u lizar para sus tuir aquellos materiales carbonosos que se importan, es transcendental estudiar y evaluar este material para comprender su comportamiento y su aplicabilidad en la industria siderúrgica; en relación a esto; con la ayuda de técnicas de análisis térmico como la termogravimetría (TGA) y calorimetría diferencial de barrido (DSC), se diseñan análisis que permiten caracterizar, evaluar y comparar térmicamente materiales carbonosos similares para establecer las principales diferencias térmicas que estos presentan. En tal sen do; se puede conocer que la temperatura de ignición y la velocidad de quemado para los combus bles sólidos estudiados, es muy variable entre ellos, por lo que el CVP presenta una temperatura de ignición de 365,5 °C, siendo esta la más baja pero con una mayor velocidad de quemado de 6,34 %/min; esto se debe primordialmente al alto contenido de volá les que presenta; por otro lado, el coque de petróleo tratado térmicamente (CPTT) presenta una temperatura de ignición superior a la del CVP con 492,5 °C, además se observa que el proceso de quemado del (CPTT), se da en dos etapas, la primera de ellas ocurre con una baja velocidad de reacción de 2,46 %/min (esta etapa podría estar relacionada al proceso de evolución de gases como CO2, CO y CH4, por liberación y quemado de los volá les) y la segunda etapa con 5,95 %/min que corresponde a la velocidad de quemado u oxidación del carbón, mientras que la antracita presenta una temperatura de ignición de mucho mayor 531,1 °C y como es de esperarse se reporta la más baja velocidad de quemado (4,79 %/min). Otra diferencia observada es que tanto el coque verde de petróleo como el coque tratado térmicamente presentan altos contenidos de azufre (3,29 % y 4,04 % respec vamente) con respecto a la antracita cuyo valor de azufre es de 0,37 %.

Palabras claves— Coque, Pellas, Antracita, Análisis Próximo, Punto de Ignición, Termogravimetría, Calorimetría Diferencial de Barrido.


I+D+i


Abstract: In the search for the use of carbonaceous materials of national origin that supply the solid fuel demand of the iron and steel industry, as is the case of green petroleum coke (CVP), which can be used to replace those carbonaceous materials that are imported, it is transcendental study and evaluate this material to understand its behavior and its applicability in the steel industry, in relation to this; with the help of thermal analysis techniques such as Thermogravimetry (TGA) and Differential Scanning Calorimetry (DSC) analyzes are designed that allow to characterize, evaluate and thermally compare similar carbonaceous materials to establish the main thermal differences that they present. In this sense, it can be known that the ignition temperature and the burning speed for the solid fuels studied are highly variable among them, so that the CVP has an ignition temperature of 365.5 °C, this being the lowest but with a higher burning rate of 6.34 %/min, this is primarily due to the high content of volatiles that it presents, on the other hand, the thermally treated petroleum coke (CPTT) has an ignition temperature higher than that of the CVP with 492 .5 °C, it is also observed that the CPTT burning process occurs in two stages, the first of which occurs with a low reaction rate of 2.46 %/min (this stage could be related to the evolution process of gases such as CO2, CO and CH4, due to the release and burning of volatiles) and the second stage with 5.95 %/min which corresponds to the speed of burning or oxidation of coal, while anthracite has an ignition temperature of much greater than 531.1 °C and as it is expected, the lowest burning rate is reported (4.79 %/min). Another difference observed is that both green petroleum coke and thermally treated coke have high sulfur contents (3.29 % and 4.04 %, respectively) with respect to anthracite, whose sulfur value is 0.37 %.

Palabras claves— Coke, Pellas, Anthracite, Proximity Analysis, Flash Point, Thermogravimetry, Differen al Scanning Calorimetry. I. INTRODUCCIÓN

En la búsqueda del aprovechamiento de materiales carbonosos de origen nacional, como es el caso del coque verde de petróleo, que se puedan u lizar para sus tuir aquellos materiales carbonosos que se importan, es transcendental estudiar y evaluar este material para comprender su comportamiento y aplicabilidad en la industria siderúrgica; en tal sen do se diseñan análisis que permiten caracterizar, evaluar y comparar térmicamente materiales carbonosos similares para establecer las principales diferencias térmicas que estos presentan. En la región existe una demanda de combus ble sólido para sa sfacer diversas necesidades de la industria siderúrgica, entre las cuales podríamos nombrar el
insuflado de antracita en las acerías de SIDOR, que actúa entre otras cosas como espumante de la escoria, también en la fabricación de pellas se emplea antracita como combus ble sólido que además de aportar (porcentaje de carbono) y generar poros en la pella, aporta energía en el horno de piroconsolidación de pellas; en estas aplicaciones de la antracita, es posible sus tuir en un 100 % este mineral por coque verde de petróleo, bien sea previamente tratado térmicamente o natural. Aunque son materiales carbonosos de origen muy diferente pues la antracita es un carbón mineral poco bituminoso, mientras que el coque verde de petróleo es un sólido carbonoso derivado como un subproducto de las unidades de coquización de las refinerías de petróleo o de otros procesos de craqueo [4;3], además poseen CENTRO DE INVESTIGACIÓN Y GESTIÓN DEL CONOCIMIENTO PÁG. 19

I+D+i
REVISTA MUNDO FERROSIDERÚRGICO | AÑO XI | NÚMERO 44 | JULIO 2022
calidad, que se mide a través del contenido de humedad, ceniza, vola lidad y poder calorífico, aunque para la mayoría de las aplicaciones es necesario conocer el perfil de quemado de cada combus ble sólido para determinar la temperatura de inicio de ignición, el momento en que entrega su máxima energía y el empo necesario de permanencia de materia en el sistema de combus ón para evitar las pérdidas de energía por calentamiento de la ceniza [5].
A través de técnicas de análisis térmico como la termogravimetría y la calorimetría diferencial de barrido fue posible obtener y comparar los perfiles térmicos de la antracita [1], coque verde de petróleo y coque tratado térmicamente, este úl mo es un coque verde que fue some do a temperaturas de 1000 ºC aproximadamente y se emplea para insuflarlo en la acería.
También fue posible calcular teóricamente el poder calorífico de estos materiales mediante una fórmula desarrollada por la Asociación de Ingenieros Alemanes para el cálculo del poder calorífico inferior (PCI) quienes se basaron en la Ley de Doulong Pe t para desarrollar este cálculo a través de datos experimentales del análisis elemental del combus ble. Todo esto contribuyo a generar los resultados que se analizaron y en función de estos se fundamentan las conclusiones exhibidas en este trabajo.
II. MATERIALES Y MÉTODOS.
Muestreo:
Para la comparación se tomaron tres muestras de materiales carbonosos:
1. Antracita (antracita importada). Empleado como combus ble sólido en la fabricación de pellas.
2. Muestra de CVP (coque verde de petróleo) proveniente de Petro San Félix suministrado por personal de CARBONORCA. Este material se emplea en la fabricación de pellas como sus tuto de la antracita. 3. Muestra de CPTT (coque de petróleo tratado térmicamente) hasta los 1000 °C en PROBASIN, muestra suministrada por personal de acerías. Cabe destacar que este material, es el que se emplea para insuflarlo en las acerías de SIDOR.
Análisis químico:
Determinar los porcentajes de carbono (C) y azufre (S) presente en cada una de las muestras para establecer sus diferencias.
Termogravimetría (TGA):
Esta técnica de análisis térmico, se emplea para obtener el análisis de cada muestra. Se realiza con el equipo de análisis térmico marca NETZSCH Júpiter F5, siguiendo el procedimiento de la norma ASTM E1131-08. Previo, secado y pulverización de la muestra, antes de ser calentada bajo una atmósfera inerte (N2) hasta los 100 °C, luego se man ene una isoterma a esta temperatura por espacio de 5 minutos; con la finalidad de determinar el porcentaje de humedad de la muestra y al culminar este empo, empieza a elevar la temperatura hasta los 950 °C y se realiza nuevamente un isoterma a esta temperatura bajo atmósfera inerte por 15 minutos para asegurar que el proceso de desvola lización sea completo, trascurrido este empo se cambia la atmosfera inerte a una atmósfera oxidante (O2) por 10 minutos para propiciar la combus ón del material y determinar porcentaje de carbón fijo.
Calorimetría diferencial de barrido (DSC):
Esta técnica de análisis térmico en conjunto al TGA, se emplea para determinar la Temperatura de Ignición, realizando un calentamiento no isotérmico bajo una atmósfera oxidante (O2) hasta los 1400 °C con el equipo de análisis térmico marca NETZSCH Júpiter F5, esto con la finalidad de observar el comportamiento térmico y determinar las temperaturas a la cual ocurre la descomposición del material y los eventos térmicos que pueden estar asociados a esta descomposición.

I+D+i
REVISTA MUNDO FERROSIDERÚRGICO | AÑO XI | NÚMERO 44 | JULIO 2022
III. RESULTADOS Y DISCUSIÓN
Análisis químico:
En la tabla 1, se observa que, en los materiales carbonosos evaluados, el porcentaje de azufre más elevado se encuentra en el CPTT con 4,04 % y en el CVP este valor es de 3,30 %, mientras que el porcentaje de azufre en la antracita es mucho más bajo con un valor de 0,38 %. También se observa que el porcentaje de carbono es mayor a 82 % en el CVP y CPTT mientras que en la antracita este valor es considerablemente más bajo con un 68,38 %. Tabla 1. Análisis químico del CVP, CPTT y antracita.
Muestra
Antracita % C
68,38 % S
0,377
CVP 82,03 3,294
CPTT 82,24
Fuente: Elaboración propia del autor. 4,040 Termogravimetría (TGA) y Calorimetría diferencial de barrido (DSC):
En la figura 1, se detalla el comportamiento térmico del coque verde de petróleo (CVP), antracita y coque de petróleo tratado térmicamente (CPTT) durante el análisis, destacándose una diferencia entre las muestras de coque y la antracita (curva roja), producto primordialmente del menor porcentaje de carbón fijo y alto contenido de cenizas presente en la antracita lo que a su vez explica el bajo poder calorífico que presenta la antracita con respecto al coque, ver tabla 2, se sabe que el contenido de cenizas en los carbones es inversamente proporcional a su poder calorífico [3].
Cabe destacar, que el poder calorífico reflejado en la tabla 2, es un cálculo teórico realizado mediante una fórmula desarrollada por la Asociación de Ingenieros Alemanes para el cálculo del poder calorífico inferior (PCI) basado en la Ley de Doulong Pe t para desarrollar este cálculo a través de datos experimentales del análisis elemental del combus ble, ver ecuación 1.
(Ecuación 1) PCI = 8.080xC +29.00 x (H-0/8) +2.500xS—600xH2O
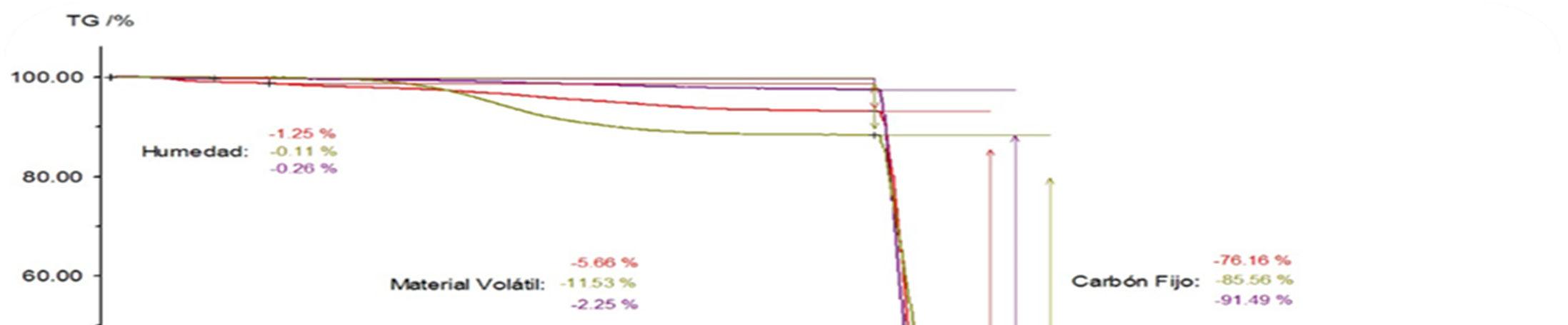
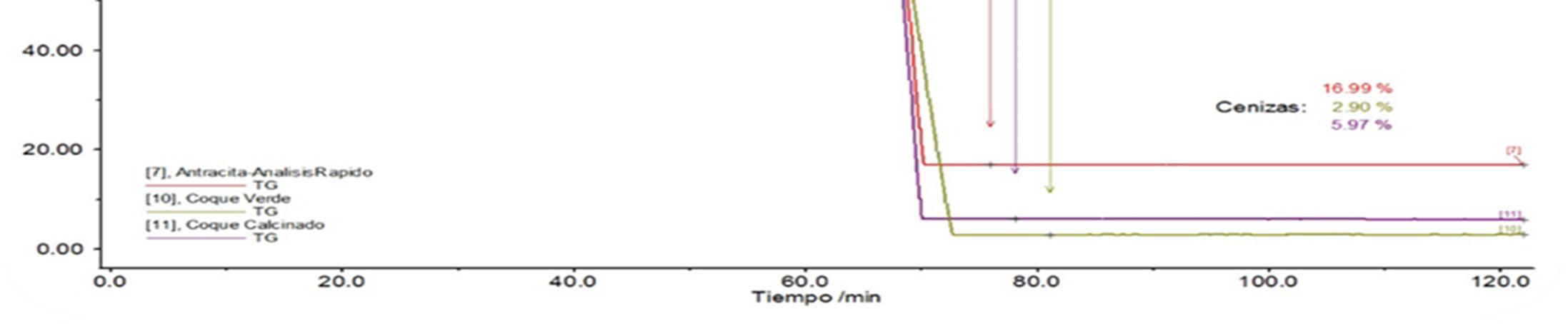
Figura 1. Curva termogravimétrica del análisis próximo del CVP, CPTT y antracita. Fuente: Elaboración propia del autor. CENTRO DE INVESTIGACIÓN Y GESTIÓN DEL CONOCIMIENTO PÁG. 21

I+D+i
COMPARACIÓN TÉRMICA DE COQUE VERDE DE PETRÓLEO, COQUE TRATADO TERMICAMENTE Y ANTRACITA
REVISTA MUNDO FERROSIDERÚRGICO | AÑO XI | NÚMERO 44 | JULIO 2022
Tabla 2. Análisis próximo del CVP, CPTT y antracita.
Muestra H2O % MV % Cf % CNZ %
PC (Kcal/Kg)
Antracita 1,25 5,66 76,16 16,99 6247
CVP 0,11 11,53 85,56 2,90 8022
CPTT 0,26 2,25 91,49 5,97 8519
Fuente: Elaboración propia del autor.
En las curvas de DTG (derivada de la termogravimetría), (ver figura 2), se muestra el perfil de quemado no isotérmico de las tres muestras some das a estudio, donde se observa que la liberación de humedad ocurre entre 0 y 150 °C destacando que la antracita es la que presenta la mayor liberación de humedad, en otras palabras, la antracita posee el mayor porcentaje de humedad coincidiendo con los resultados del análisis próximo mostrados en la tabla 2. Además se observa que los combus bles sólidos evaluados poseen velocidades máximas de quemado rela vamente dis ntas, siendo la antracita la que reporta la más baja velocidad de quemado (4,79 %/min) y el CVP presenta una velocidad mayor de quemado de 6,34 %/ min; esto se debe primordialmente al alto contenido de volá les que la primera de ellas ocurre con una baja velocidad de reacción de 2,46 %/min (esta etapa podría estar relacionada al proceso de evolución de gases como CO2, CO y CH4, por liberación y quemado de los volá les) y la segunda etapa con 5,95 %/min que corresponde a la velocidad de quemado u oxidación del carbón.[2;3;6].
En el CVP se observa una ganancia de peso muy marcada entre 250 y 300 °C, debiéndose a un proceso de quimiadsorción de oxígeno sobre la superficie de las par>culas de carbón, fenómeno que ocurre usualmente para que inicie la oxidación de la materia volá l y el carbono fijo [8].



Figura 2. Perfil de quemado del CVP, CPTT y antracita. Fuente: Elaboración propia del autor. CENTRO DE INVESTIGACIÓN Y GESTIÓN DEL CONOCIMIENTO PÁG. 22

I+D+i
COMPARACIÓN TÉRMICA DE COQUE VERDE DE PETRÓLEO, COQUE TRATADO TERMICAMENTE Y ANTRACITA
REVISTA MUNDO FERROSIDERÚRGICO | AÑO XI | NÚMERO 44 | JULIO 2022
A par r de la curva de calorimetría diferencial de barrido (DSC), (ver figura 3), se ob enen temperaturas caracterís cas como la temperatura de ignición de volá les (TI), temperatura pico (TP), la temperatura final de quemado (TF) y la entalpía. Además, a par r de estas temperaturas caracterís cas se pueden obtener otros datos como el calor involucrado para que se genere la reacción, la velocidad máxima de pérdida de peso, (dm/ dt)máx, de los combus bles sólidos analizados.
La temperatura de ignición para los materiales estudiados, es muy variable entre ellos y ésta propiedad depende de la can dad de volá les y carbón fijo que estos presentan. Como lo indica la tabla 3, el coque verde de petróleo (CVP) presenta una temperatura de ignición de 365,5 °C siendo esta la más baja con respecto a la antracita con 531,1 °C y el coque de petróleo tratado térmicamente (CPTT) con 492,5 °C.
Según los valores de (TP) temperatura pico obtenidos por calorimetría diferencial de barrido (DSC) y teniendo en cuenta la teoría de la rela vidad de Cumming [2; 3; 6], que establece que los carbones más reac vos son los que usualmente presentan menor temperatura pico, se ene que el coque verde de petróleo (CVP) (TP= 506,2 °C) es el más reac vo y el menos reac vo es la antracita (TP= 637,2 °C), mientras que en el coque de petróleo tratado térmicamente (CPTT) la temperatura pico es de 594,6 °C.
Tabla 3. Temperaturas caracterís cas del carbón.
Muestra Temp. Ignición (TI) ºC Temp. Pico (TP) ºC Temp. Final (TF) ºC TF-TI ºC Entalpía J/g
(dm/dt) m ax %/min.
Antracita 531,1 637,2 843,8 312,7 4,79 -10.049
CVP 365,5 506,2 620,2 254,7
CPTT 492,5 594,6 664,0 171,5
Fuente: Elaboración propia del autor. 6,34
2,46 - 5,95 -15.757
-14.264



Figura 3. Calorimetría diferencial de barrido del CVP, CPTT y antracita. Fuente: Elaboración propia del autor. CENTRO DE INVESTIGACIÓN Y GESTIÓN DEL CONOCIMIENTO PÁG. 23

I+D+i
COMPARACIÓN TÉRMICA DE COQUE VERDE DE PETRÓLEO, COQUE TRATADO TERMICAMENTE Y ANTRACITA
Por otro lado, la temperatura final que es u lizada como parámetro para determinar los empos de residencia del combus ble sólido en las calderas [5], se obtuvo que en la antracita el proceso de combus ón se finaliza a los 843,2 °C y para el CVP y CPC a 620,2 y 664 °C respec vamente.
La diferencia entre la temperatura final y la temperatura de ignición (TF-TI), se ha definido como el intervalo de reacción con el cual busca es mar el empo necesario para lograr la combus ón completa de la muestra [5].
De acuerdo con este parámetro, en la tabla 3 se observa que la menor diferencia entre la temperatura final (TF) y la temperatura de ignición (TI) se presentó en el coque de petróleo tratado térmicamente (CPTT) y la mayor diferencia la presentó la antracita. Lo que quiere decir que la antracita requiere mayor empo de reacción que el coque verde de petróleo (CVP) y coque de petróleo tratado térmicamente (CPTT) para reducir las pérdidas por inquemados cuando es some da a condiciones similares de oxidación.
IV. CONCLUSIONES
De acuerdo a lo observado mediante el análisis por TGA de las muestras de combus ble sólido evaluadas se ene que:
La temperatura de ignición para los combus bles sólidos estudiados, es muy variable entre ellos, por lo que el CVP presenta una temperatura de ignición de 365,5 °C siendo esta la más baja con respecto a la antracita con 531,1 °C y CPTT con 492,5 °C.
En la termogravimetría no isotérmica se obtuvieron las temperaturas pico para cada muestra, destacando que el CVP (TP= 506,2 °C) es el más reac vo y el menos reac vo es la antracita (TP= 637,2 °C), mientras que en el CPTT la temperatura pico es de 594,6 °C. El proceso de combus ón para la antracita finaliza a los 843,2 °C y para el CVP y CPTT a 620,2 y 664 °C respec vamente. Lo que significa que la antracita requiere mayor empo de reacción que el CVP y CPTT para reducir las pérdidas por inquemados cuando se somete a similares condiciones de oxidación, esto también se verifica con la diferencia entre la temperatura final (TF) y la temperatura de ignición (TI), que es el intervalo de reacción con el cual se busca es mar el empo necesario para lograr la combus ón completa de la muestra.
Tanto el coque verde de petróleo como el coque tratado térmicamente presentan altos contenidos de azufre (3,29 % y 4,04 % respec vamente) con respecto a la antracita cuyo valor de azufre es de 0,37 %.
En el perfil de quemado no isotérmico de las tres muestras some das a estudio la liberación de humedad ocurre entre 0 y 150 °C destacando que la antracita es la que presenta la mayor liberación de humedad.
Los combus bles sólidos evaluados poseen velocidades máximas de quemado rela vamente dis nta, siendo la antracita la que reporta la más baja velocidad de quemado (4,79 %/min) y el CVP presenta una velocidad mayor de quemado de 6,34 %/min y esto se debe primordialmente al alto contenido de volá les que presenta, mientras que el proceso de quemado del coque de petróleo tratado térmicamente (CPTT) se da en dos etapas, la primera de ellas ocurre con una baja velocidad de reacción de 2,46 %/min (esta etapa podría estar relacionada al proceso de evolución de gases como CO2, CO y CH4, por liberación y quemado de los volá les) y la segunda etapa con 5,95 %/min que corresponde a la velocidad de quemado u oxidación del carbón.

I+D+i
COMPARACIÓN TÉRMICA DE COQUE VERDE DE PETRÓLEO, COQUE TRATADO TERMICAMENTE Y ANTRACITA
V. REFERENCIAS
[1] ASTM E1131–08 Standard Test Method for Composi onal Analysis by Thermogravimetry.
[2] Cumming, J., McLaughlin, J., The thermogravimetric behaviour of coal., Thermochimica Acta, Vol. 57, 1982, pp. 253-272.
[3] Cumming, J. W., A DTG combus ón study on anthraci c and other coal chars., Thermochimica Acta, Vol. 155, 1989, pp. 151-161.
[4] BURGOS, A. F. R. GONZALES & J. M. BARRAZA. «Caracterís cas termogravimétricas de carbonizados obtenidos a altas velocidades de calentamiento.» Ingeniería e Inves gación, 2009: 25-34.
[5] Urhan, R. M., Mejora de la eficiencia de la combus ón de carbones u lizados en el Valle del Cauca mediante un estudio previo de su reac vidad., Informe final presentado a ECOCARBON – COLCIENCIAS, Universidad del Valle, Cali, 2000.
[6] Cumming, J. W., Reac vity assessment of coal vía a weighted mean ac va on energy., Fuel, Vol. 63, Oct., 1984, pp. 1436-1440.
[7] Fadzilah, O. N., Halim, S. A., Coal combus ón studies using thermogravimetric analysis., Jurnal Mekanikal, Vol. 15, 2003, pp. 97-107.
[8] Rojas, A., Barraza J., Caracterís cas termogravimétricas de carbonizados obtenidos a altas velocidades de calentamiento. Revista ingeniería e inves gación, Vol. 29, 2009, pp. 25 – 34.
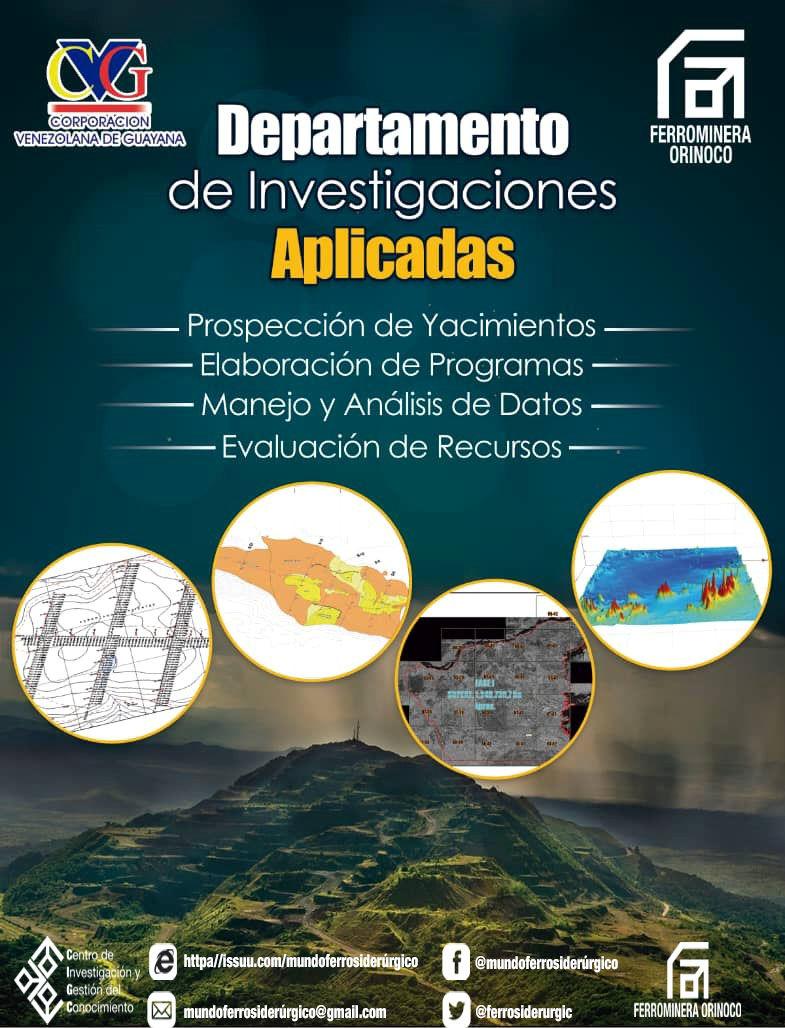

[9] T. LI, C. D.-XIA, Z. X. DONG, W. Y. QIANG, N. Y. HUI, Z. Z. BI. «Gasifica on reac vity of petroleum coke at high temperature.» Fuel Chemistry and Fuente: infotecarios.com. Technology, 2005. CENTRO DE INVESTIGACIÓN Y GESTIÓN DEL CONOCIMIENTO PÁG. 25
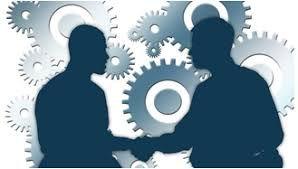
Mundo Ferrosiderúrgico Mercado, Ciencia y Tecnología
01 DE JUNIO XV Aniversario
Planta de Briquetas: 15 años agregando valor a nuestro mineral
El 01 de junio, la gran familia ferrominera encabezada por el presidente Abel Jiménez, celebró el XV aniversario, del día en que la dirección administrativa y operativa de Planta de Briquetas pasó a manos de CVG Ferrominera Orinoco, C.A., en un acto de soberanía productiva impulsado por el Gobierno Nacional.
Hoy por hoy, luego de cuatro años de paralización por mantenimientos de envergadura y gracias a la sustitución de importaciones, arrancó esta planta adscrita a la Gerencia General de Operaciones Siderúrgicas que genera el máximo valor agregado al mineral de hierro antes de convertirse en acero.
CVG Ferrominera Orinoco, C.A., felicita a los briqueteros con sello ferrominero, al Consejo Productivo de Trabajadores y Trabajadoras (CPTT), y a todas las unidades organizativas de la empresa involucradas en el fortalecimiento de la cadena de producción hierro-acero.
Valoramos el ingenio, creatividad, profesionalismo y mística de trabajo, para garantizar el suministro de Hierro briqueteado en caliente a nuestros aliados comerciales.
El hito definitivo fue marcado el 01 de junio de 2007, luego que la empresa Operaciones al Sur del Orinoco (OPCO), filial de la empresa japonesa Kobe Steel (Kobelco), realizara la entrega definitiva tras vencerse el contrato a manos de la estatal minera, con una capacidad de producción de 1 millón de toneladas anuales.

PROPUESTA DE FABRICACIÓN POR FUNDICIÓN DE LOS COMPONENTES DEL MECANISMO DE TRACCIÓN PARA VAGONES MINERALEROS DE CVG FERROMINERA ORINOCO, C.A. REVISTA MUNDO FERROSIDERÚRGICO | AÑO XI | NÚMERO 44 | JULIO 2022
Bonillo Pedro1 , Yánez Oscar2, Aguedo Arteaga 3
1 Ingeniero Metalúrgico, Tesista UNEXPO, Gerencia de Ferrocarril, CVG FERROMINERA ORINOCO, C.A., Ciudad Guayana, Venezuela. 2 Ingeniero Metalúrgico, Vicepresidente, Complejo Industrial Fábrica de Fábricas “Hugo Chávez Frías”, Anaco, Venezuela. 3 Ingeniero Metalúrgico, UNEXPO Vice-rectorado Puerto Ordaz, Jefe del Departamento de Ingeniería Metalúrgica, Asesor de Sustitución de
Importaciones en CVG, Ciudad Guayana, Venezuela. Email: pjabonilloc@gmail.com., Fecha recibido: 23/05/2022 Fecha aprobado: 28/05/2022
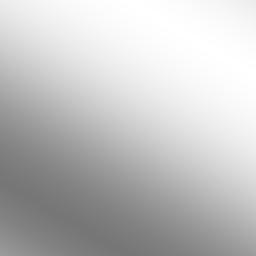
Correspondencia: Gerencia Centro de Investigación y Gestión del Conocimiento CVG Ferrominera Orinoco, C.A. | Ciudad Guayana, Estado Bolívar, Venezuela Teléfonos de contacto: +58 (286) 930.43.44
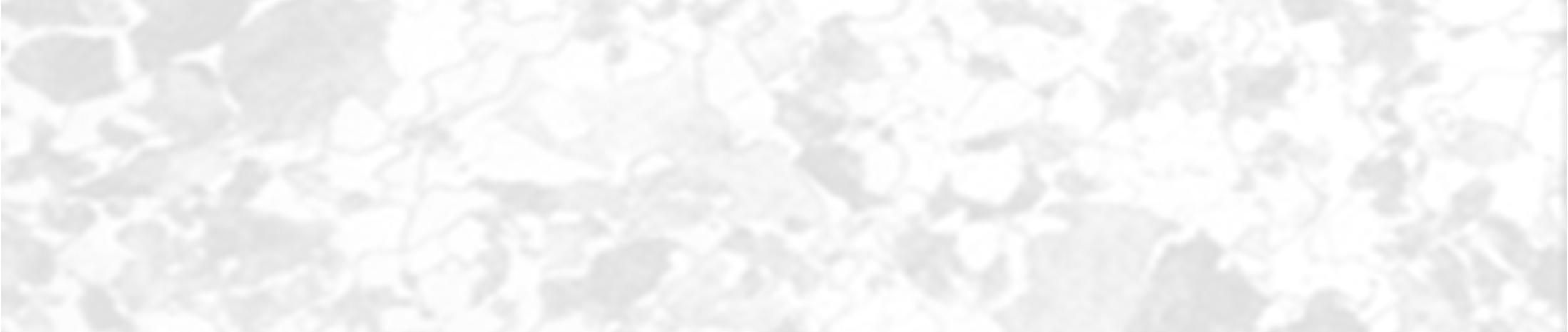
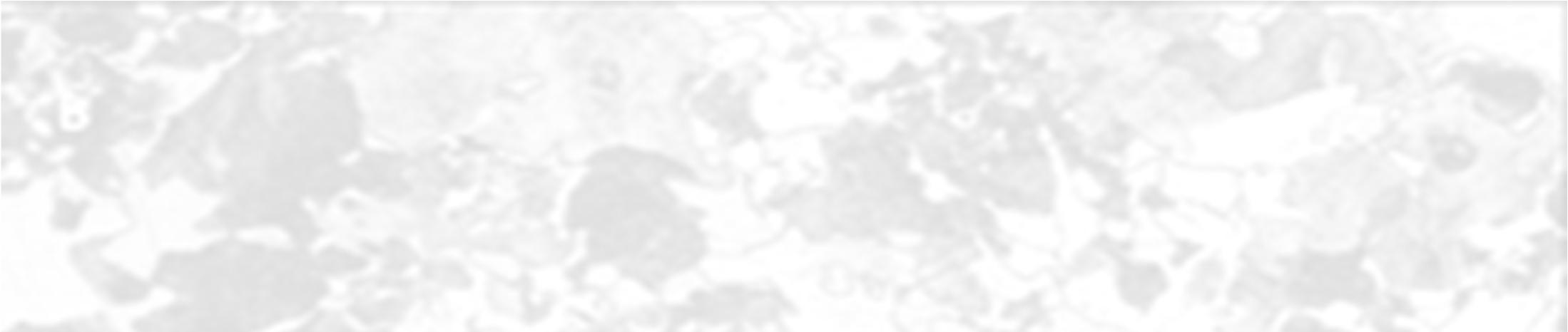

Resumen— La finalidad de la propuesta, es la fabricación de los mecanismos de acople y tracción (charnela y candado), para vagones mineraleros de CVG Ferrominera Orinoco, C.A., a través de un proceso de fundición con moldes de arena, donde los resultados obtenidos de la caracterización metalúrgica de los componentes, se comparan con los estándares requeridos por la Asociación Norteamericana de Ferrocarril (Normas AAR). Se diseñaron los modelos de las simulaciones de solidificación y colada, determinándose así, la ubicación de las mazarotas; y mediante los cálculos generales de fundición, se logró obtener las dimensiones de los elementos del sistema de alimentación y colada. Se elaboró un plan de moldeo y fusión en base a las normas, que contempla el acero a u lizar, los materiales del molde, po de moldeo, tratamiento térmico y ensayos de control de calidad. Por otro lado, al verificar los resultados de la caracterización metalúrgica, contra lo exigido por las Normas AAR, las propiedades de las muestras, difieren entre ellas, por tratarse de elementos con propiedades equiparables, considerando que los diseños se realizaron tomando como referencia, las medidas de los componentes que actualmente se encuentran en uso. Estos resultados se muestran en las figuras dinámicas de cambio de fase.


Palabras claves— Fundición, Diseño CAD, Ferrocarril, Acoplador, Simulación.
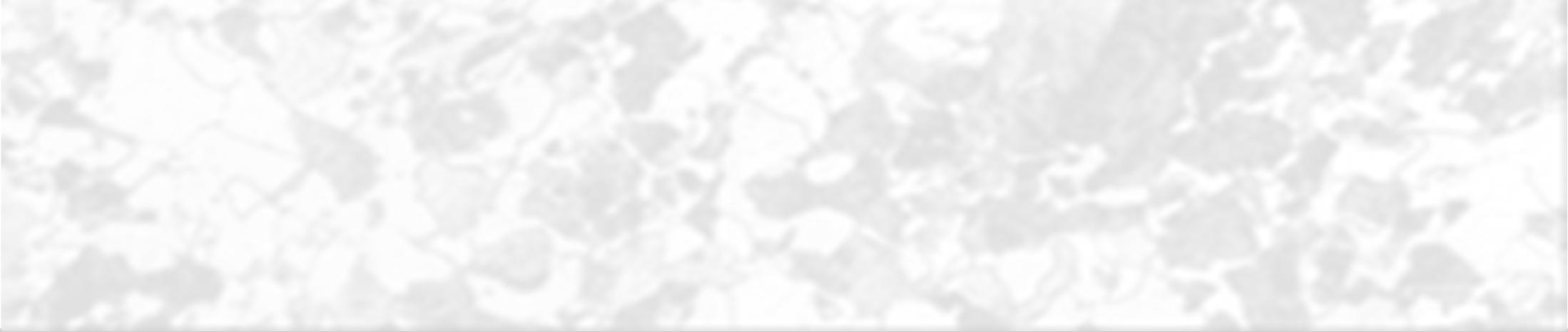



PROPUESTA DE FABRICACIÓN POR FUNDICIÓN DE LOS COMPONENTES DEL MECANISMO DE TRACCIÓN PARA VAGONES MINERALEROS DE CVG FERROMINERA ORINOCO, C.A. REVISTA MUNDO FERROSIDERÚRGICO | AÑO XI | NÚMERO 44 | JULIO 2022
Abstract: The purpose of the proposal is the manufacture of the coupling and traction mechanisms (hinge and padlock), for ore wagons of C.V.G Ferrominera Orinoco, through a casting process with sand molds, where the results obtained from the metallurgical characterization of components are compared to the standards required by the American Association of Railroads (AAR Standards). Solidification and casting simulation models were designed, thus determining the location of the risers; and by means of general casting calculations, it was possible to obtain the dimensions of the elements of the feeding and casting system. A molding and fusion plan was developed based on the standards, which includes the steel to be used, the mold materials, type of molding, heat treatment and quality control tests. On the other hand, when verifying the results of the metallurgical characterization, against what is required by the AAR Standards, the properties of the samples differ among them, because they are elements with comparable properties, considering that the designs were made taking as reference, the measurements of the components that are currently in use. These results are shown in the dynamic phase change figures.
Keywords- Cas ng, CAD Design, Railway, Coupler, Simula on


I. INTRODUCCIÓN
A lo largo del empo, la industria de la fundición ha evolucionado y sus procesos han cambiado favorablemente, adoptando nuevas tecnologías para sa sfacer las demandas industriales y de fabricación de este siglo. Las empresas de fundiciones suministran partes y piezas fabricadas a una amplia gama de sectores, incluidos el sector aeroespacial, automovilís co, sector ferroviario y de generación de energía.
Así mismo, el sector ferroviario depende de las empresas fundidoras quienes les proporcionan partes y piezas, garan zando que la industria pueda funcionar con el máximo efecto para sa sfacer la demanda.
En el caso del transporte de carga pesada; los operadores de trenes deben sen rse seguros con la integridad de las piezas, esto incluye a las empresas encargadas de trasladar el mineral de hierro.
La Gerencia de Ferrocarril de CVG Ferrominera Orinoco, C.A., ene como propósito garan zar el transporte del mineral de hierro y sus derivados desde la recepción de producción Puerto Ordaz, procesamiento de mineral, hasta los clientes. El sistema ferroviario comprende un total de 320 Km de vía férrea, cons tuyendo la mayor red ferroviaria del país. . La inves gación se basa en una propuesta para fabricar las partes y piezas del mecanismo de tracción charnela y candado, en CVG Complejo Industrial Fábrica de Fábricas “Hugo Chávez Frías” (CIFFHCF), ubicado en el sector El Guache en la población de Anaco, estado Anzoátegui, a través de un proceso de fundición en moldes de arena, garan zando la disponibilidad de partes y piezas para restablecer el funcionamiento de los vagones fuera de servicio.

Fuente: Amsted rail [2]. Sistema de amor guación conectada entre el bas dor central y el mecanismo de acople.

PROPUESTA DE FABRICACIÓN POR FUNDICIÓN DE LOS COMPONENTES DEL MECANISMO DE TRACCIÓN PARA VAGONES MINERALEROS DE CVG FERROMINERA ORINOCO, C.A. REVISTA MUNDO FERROSIDERÚRGICO | AÑO XI | NÚMERO 44 | JULIO 2022
II. MARCO TEÓRICO.
A. Asociación Norteamericana de Ferrocarriles. AAR
La Asociación Norteamericana de Ferrocarriles (AAR) es un grupo comercial de la industria que representa especialmente a los principales ferrocarriles de carga de América del Norte (Canadá, México y Estados Unidos).
La AAR trabaja para mejorar la eficiencia, seguridad y el servicio de la industria ferroviaria, por ejemplo, a través de su responsabilidad en las reglas de intercambio de la industria y las especificaciones del equipo, así como también en el control de unidades múl ples de locomotoras.
B. Sistema de choque y tracción
Es el conjunto detrás del acoplamiento en cada extremo del vagón, que permite cuidar las fuerzas de compresión y tensión entre los vagones de los trenes. Este sistema está cons tuido por una estructura robusta que se divide en dos secciones de acuerdo a la funcionalidad. La primera sección corresponde al mecanismo de acople, un cuerpo metálico con diversos componentes que permite el enganche y sección de amor guación (aparejo de tracción), encargado de absorber los impactos asociados al enganche y tracción de los vagones y locomotoras.
C. Acoplamiento ferroviario o acoplador
El acoplador está diseñado como un cuerpo de acero hueco, albergando en su interior parte de los componentes que actúan como eslabones del mecanismo en sí. Consta de una palanca de acción ubicada fuera del cuerpo y anclada al bas dor, permi endo que el operador pueda accionar el mecanismo; esta se encuentra conectada al rotor y a su vez se conecta con un elemento denominado gira rotor; su función es similar al de una leva, levantando el candado y permi endo que se separe de la charnela, liberando su rotación; además, el movimiento de ascensión del candado confiere que el mismo “empuje” al lanzador o “ ra muela”, gire la charnela ocasionando el desenganche.
D. SoSware de diseño CAD
Es una técnica y representación de diseños y modelos 2D y 3D para diversos fines, u lizando una aplicación de sofware, por diferentes industrias para crear varios componentes. Se basa en la representación computacional del modelo, que permite realizar automá camente, el dibujo a detalle y la documentación del diseño facilitando la u lización de métodos numéricos para realizar simulaciones sobre el modelo, como una alterna va a la construcción de proto pos.
E. Proceso de fundición en arena
La fundición, es la técnica metalúrgica conformado de materiales más an gua existente; conocida por el ser humano desde el siglo IV a.C. Arteaga (2003), en su manual de procesos de fundición expresa que: “la fundición es un arte que se remonta a su nacimiento muchos siglos atrás, donde ya aplicaban las técnicas como el moldeo a la cera perdida u lizado por los chinos, egipcios y griegos, de igual manera se designa como fundición la fábrica donde se realizan estas transformaciones del metal.”
Este método consiste en un conjunto de procedimientos que inicia con la fusión y posterior ver do del material fundido en una cavidad o molde que ene la forma deseada, el cual permanece hasta su solidificación.
Generalmente este molde se hace en arena, consolidado por el apisonador manual o mecánico alrededor de un modelo. No hay limitaciones en tamaño de las piezas que puedan colarse, variando desde pequeñas piezas de prótesis dental, con peso en gramos, hasta los grandes bas dores de máquinas de varias toneladas.

PROPUESTA DE FABRICACIÓN POR FUNDICIÓN DE LOS COMPONENTES DEL MECANISMO DE TRACCIÓN PARA VAGONES MINERALEROS DE CVG FERROMINERA ORINOCO, C.A. REVISTA MUNDO FERROSIDERÚRGICO | AÑO XI | NÚMERO 44 | JULIO 2022
III. METODOLOGÍA
A. Implementar métodos de caracterización que permitan conocer las propiedades de la charnela y el candado
Mediante diversos análisis se logró obtener una descripción básica de las partes y piezas estudiadas, detallando información a comparar con la norma y a u lizar en la fabricación. Los datos obtenidos de la pieza corresponden al peso, la dureza, microestructura, composición química y las propiedades obtenidas de la revisión documental.
Los ensayos para la obtención de los datos se realizaron de la siguiente manera:
Peso
Para el pesaje de las muestras se implementaron tres equipos. El candado se pesó con dos balanzas diferentes, el primero se realizó en una balanza electrónica de mesa de uso comercial con capacidad para 40 Kg y posteriormente verificado usando una balanza electrónica colgante.
La charnela, por otra parte, se pesó en el Departamento de Control de Calidad de CVG Ferrominera Orinoco, C.A., implementando una balanza electrónica con control de peso, uso industrial Modelo GFK 600aM. Se pesaron dos modelos de charnela diferentes para comparar los valores y conocer la diferencia de masa entre ambas; además de los modelos de charnela sólida ( po A), siendo de interés para la inves gación y el modelo que posee aliviadores en la zona superior (zona de enganche) e inferior ( po C). Dureza
El ensayo de dureza para muestra de la charnela, se realizó en el Ins tuto de Inves gaciones Metalúrgica y Materiales, IIMM SIDOR , implementando un microdurómetro “Wilson” modelo Tukon 1202 desarrollado por Buehler, obteniendo medidas de dureza en la escala Vickers (HV). El candado, por otra parte, se ensayó en CVG Complejo Industrial Fábrica de Fábricas “Hugo Chávez Frías” (CIFFHCF), implementando un durómetro Rockwell HR-150A aplicando una carga de 150 Kgf con una precarga de 10 Kgf, u lizando un indentador de diamante cónico de 120º, obteniendo las medidas en escala HRC.
Análisis metalográfico
Seleccionadas las muestras, se cortó de forma manual con el uso de una segueta aplicando agua para evitar el calentamiento a la probeta obtenida de la charnela. Se le realizó un montaje en frío para facilitar su manipulación. Posteriormente, en el Ins tuto de Inves gaciones Metalúrgica y Materiales SIDOR (IIMM), se realizó una preparación metalográfica iniciando con un desbaste grueso en una lijadora de bandas, u lizando lijas de 80 y 120, para luego realizar un lijado manual con un set de lijas número 240, 320, 400 y 600. Para la visualización de su microestructura se realizó el ataque químico con Nital al 3 % e implementación del microscopio inver do “Nikon Eclipse MA200” con aumentos de 100x, 200x y 500x en conjunto con el sofware de análisis de imagen Omnimet.
Análisis químico
La composición química se determinó por espectroscopia de emisión óp ca. Para ello analizaron tres muestras de diferentes componentes, siendo la charnela la muestra A, el candado la muestra B y la muestra C el ramuela; que sirvió de complemento para analizar la composición química de todos los componentes.
Las muestras A y B se analizaron en CVG Complejo Industrial Fábrica de Fábricas “Hugo Chávez Frías” (CIFFHCF). La muestra C, se analizó en el laboratorio de acería de palanquillas del Complejo Siderúrgico Alfredo Maneiro, SIDOR. Adicionalmente, se le realizó a la muestra C un ensayo de fluorescencia de rayos x ( XRF siglas en inglés).

PROPUESTA DE FABRICACIÓN POR FUNDICIÓN DE LOS COMPONENTES DEL MECANISMO DE TRACCIÓN PARA VAGONES MINERALEROS DE CVG FERROMINERA ORINOCO, C.A. REVISTA MUNDO FERROSIDERÚRGICO | AÑO XI | NÚMERO 44 | JULIO 2022
B. Desarrollar un modelo de fundición a los componentes en estudio implementando un soSware computacional de modelado en CAD, considerando las contracciones volumétricas que experimenta el metal al solidificar
El desarrollo de los modelos de las muestras en estudio, siguió una metodología simple, que se basa en la medición de muestras de servicio y su comparación, con datos obtenidos en la revisión documental y la metodología aplicada, expresada como se observa en la figura 1.
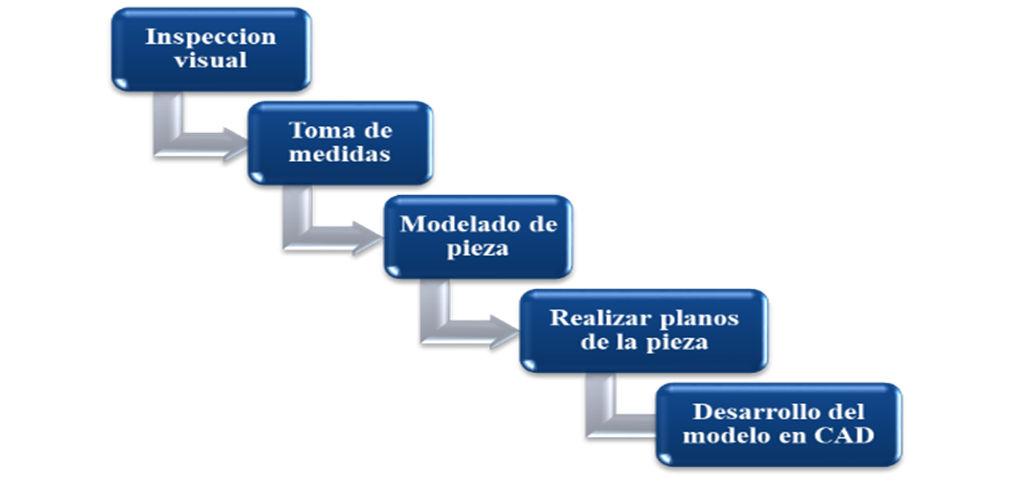
Figura 1: Flujograma proceso de diseño de modelos en CAD. Fuente: Elaboración propia del autor
En la inspección visual, se implementó la selección de las piezas charnela y candado a u lizar como patrón, aquellas cuyas dimensiones y geometrías no posean variaciones considerables, dado su uso, puesto que al encontrarse en servicio, están expuestas a diferentes pos de esfuerzos e impactos repe vos. Luego de esto, se tomaron medidas de las muestras seleccionadas y en el caso de la charnela, se eligieron cinco (5) piezas diferentes y promediando su valor; por otra parte, en el caso del candado, se escogió una muestra en buen estado y sin defectos superficiales que pudieran alterar los valores.
Para el modelado de la charnela y el candado, se implementó un sofware de diseño en CAD, iniciando con la realización del boceto de las muestras que cotejará el perfil, conteniendo en este la geometría superficial de las piezas, seguidamente se u lizaron las dis ntas herramientas que ofrece el programa, principalmente las de extrusión, corte y barrido para la elaboración del modelo. Los planos resultantes se obtuvieron exportando las vistas de la charnela y el candado añadiendo sus respec vas medidas. Los modelos con sobre medidas se elaboraron a par r de diseños de las piezas originales, exportándolo a otro espacio de trabajo y escalando sus dimensiones un 2 % por encima del original y añadiendo los valores por conicidad.
C. Determinar el perfil de solidificación de la charnela y el candado a través de una simulación del proceso de solidificación implementando un soSware computacional para establecer la posición de las mazarotas en el modelo de fundición
El proceso se realizó en 2 etapas: la primera constó en determinar el correcto posicionamiento de los sistemas de alimentación y colada, con ello eliminar o disminuir la mayor can dad de defectos des nando la simulación a la visualización del avance de la solidificación y la detección de puntos calientes, prediciendo los defectos que podrían aparecer, a fin de op mizar el proceso, ahorrando gastos de materiales e insumos que puedan necesitar en los ensayos de prueba-error. La segunda etapa constó con el cálculo y dimensionado de los elementos de alimentación para el desarrollo del modelo de colada.
El programa u lizado para este proceso, corresponde a un sofware de análisis de elementos finitos, mediante su apartado de CFD (siglas en inglés para Dinámica de Fluidos Computacional) trabajando con un modelo de VOF (volumen de fluido), donde se esquema zó primeramente los pasos requeridos para realizar el proceso de fundición con la carga del diseño preliminar a analizar para su normalización, que posteriormente se cargaría en el apartado CFD para la simulación.
En primera instancia, el proceso fundición requiere de un modelo de fundición prioritario. Para el caso de la charnela, se realizó un diseño para simulación que solo contempla la mitad de la pieza, esto debido a la simetría que posee, disminuyendo considerablemente el requerimiento computacional y facilitando el proceso. El candado, por otra parte, fué simulado con el diseño previsto.

PROPUESTA DE FABRICACIÓN POR FUNDICIÓN DE LOS COMPONENTES DEL MECANISMO DE TRACCIÓN PARA VAGONES MINERALEROS DE CVG FERROMINERA ORINOCO, C.A. REVISTA MUNDO FERROSIDERÚRGICO | AÑO XI | NÚMERO 44 | JULIO 2022
Para el caso de ambos modelos, en el mallado se implementó una geometría no estructurada y mediante el tanteo, se obtuvo un tamaño adecuado, considerando el área superficial de cada diseño, de modo que la asimetría resultante, sea lo más baja posible, sin que el tamaño de malla sea excesivamente pequeño y así no suponer una carga innecesaria para el equipo disponible.
En las configuraciones de los parámetros para la simulación CFD (siglas en inglés para dinámica de fluidos computacional), se u lizó un algoritmo de solución basado en la presión, siendo este el único compa ble con los métodos de solución a u lizar en este proyecto; además del dominio de empo, el cual se trabajó en estado transitorio.
Los modelos u lizados son: el modelo de solidificación y fusión, siendo estos los principales del proyecto; permi endo visualizar la transición durante la solidificación y el avance de la interfase sólido-líquido, a par r del resultado de este método, se observamos los puntos calientes que pueden generarse en la pieza.
Además, se trabajó con el modelo de energía, debido a que este se ac va por defecto al vincularlo con el modelo de solidificación y fusión. Por otra parte, el modelo de viscosidad se realizó de acuerdo a los parámetros más comunes u lizados en las simulaciones de po CFD.
Una vez obtenidos los resultados de la simulación de solidificación y establecida la ubicación de las mazarotas, se procedió a calcular las dimensiones, considerando los elementos auxiliares restantes, para el posterior diseño de un modelo general que abarque cada uno de los componentes y así poder simular la etapa de llenado del molde. En desarrollo de esta etapa se realizó aplicamos las ecuaciones per nentes del cálculo de elementos adicionales al modelo, promoviendo una solidificación direccional que impida la formación de rechupes y porosidades en la pieza, considerando el rápido llenado del molde que permita evitar el sobrecalentamiento del metal, además, de la erosión de moldes y machos. D. Estudiar el comportamiento del metal durante la colada a través de una simulación mul)fásica, para predecir posibles defectos asociados con el llenado del molde
Se basó en la visualización del flujo de colada, a través de una simulación mul fásica, observando el paso a paso del llenado del molde y así poder predecir la ubicación de las zonas en las cuales es necesario establecer salidas de presión por donde puedan escapar los gases presentes dada la baja permeabilidad de la arena y verificar que el flujo de colada no presente turbulencia que pueda afectar el molde. Para el desarrollo de este obje vo aplicamos una metodología similar a la usada en el anterior.
Los modelos de estudios implementados corresponden a un modelo mul fásico, que permite trabajar con diferentes pos de estado de la materia o diferentes materiales. La formulación u lizada en este modelo corresponde a volumen de fluido, que trata con dos o más fluidos inmiscibles entre sí, dando como resultado la fracción volumétrica de cada fluido en un instante de empo en todo el dominio, además del modelo de viscosidad que se trabajó de acuerdo a los parámetros más comunes u lizados en las simulaciones de po CFD (siglas en inglés para dinámica de fluidos computacional).
E. Proponer un plan de modelo y fusión, tomando como referencia las propiedades de las piezas en servicio y los estándares establecidos por la AAR
La ejecución de este obje vo se basó en el análisis de los datos obtenidos, apoyándose en la revisión documental u lizada en el desarrollo de la inves gación. Comprende principalmente realizar una lista donde se dan especificaciones para cada etapa del proceso que engloba, desde la selección de la materia prima, hasta el acabado final. Para establecer los parámetros se realizó un diagrama de flujo (ver figura 2) que muestra de manera gráfica las etapas del proceso de fabricación; cada uno de estos pasos será desarrollado permi endo así una breve explicación.

PROPUESTA DE FABRICACIÓN POR FUNDICIÓN DE LOS COMPONENTES DEL MECANISMO DE TRACCIÓN PARA VAGONES MINERALEROS DE CVG FERROMINERA ORINOCO, C.A. REVISTA MUNDO FERROSIDERÚRGICO | AÑO XI | NÚMERO 44 | JULIO 2022
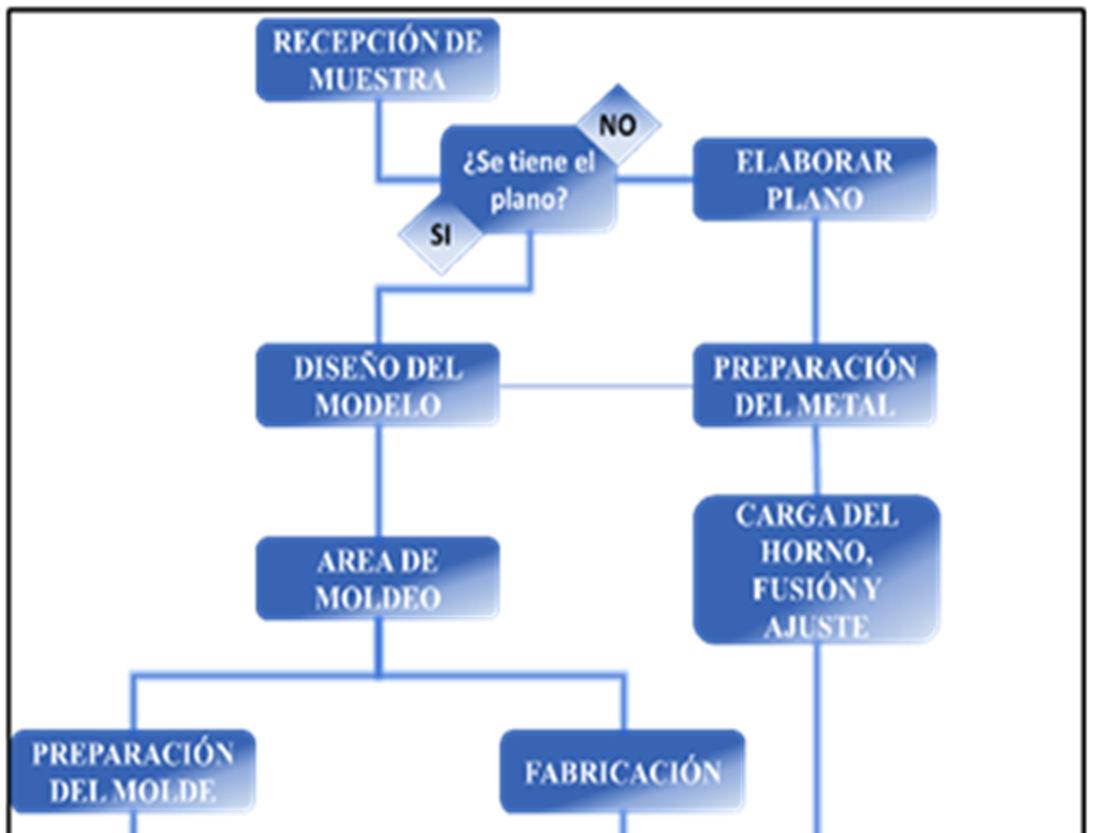
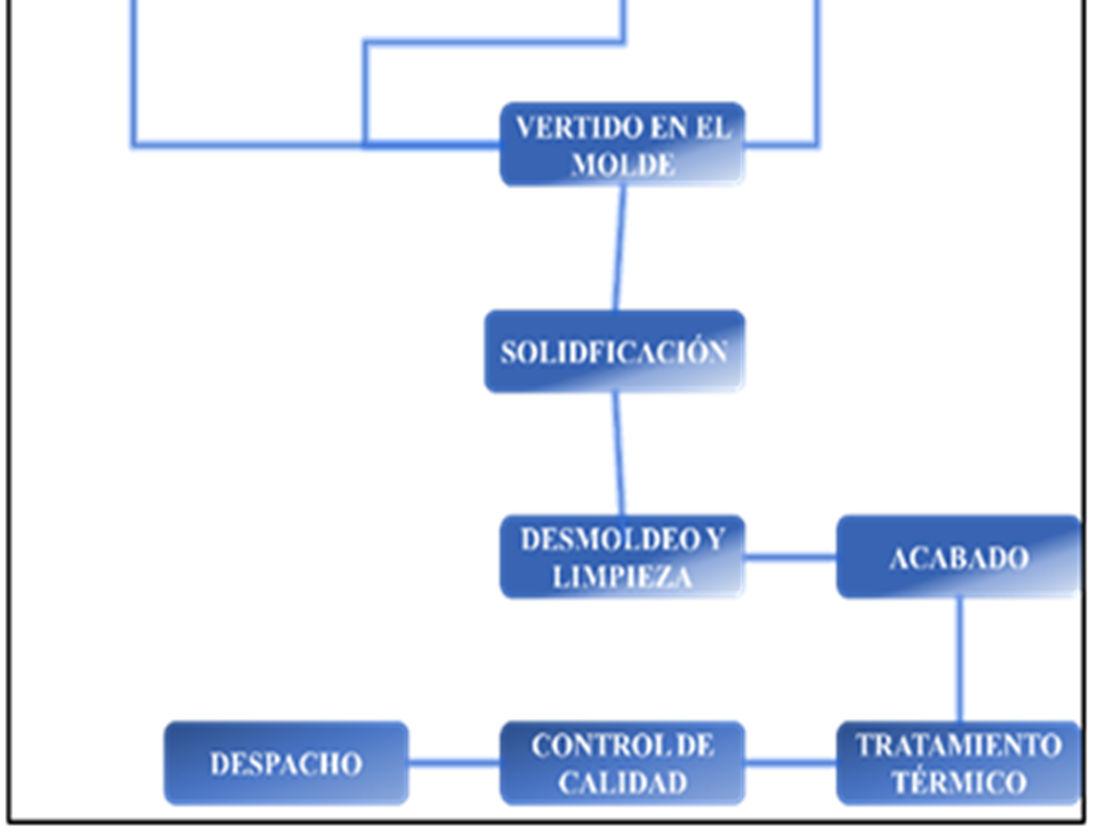
Figura 2: Diagrama de flujo de la metodología de fabricación por fundición Fuente: Elaboración propia del autor.
IV. RESULTADOS
A. Implementar métodos de caracterización que permitan conocer las propiedades de las piezas en estudio
En la figura 3, se puede observar la microestructura de la charnela estudiada. El ensayo reveló que se trata de una estructura baini ca; descartando la presencia de martensita en la muestra dado los valores de dureza, considerando que la martensita posee valores de dureza mayores a 50 HRC (aproximadamente 480 HB). La fineza del grano requiere de grandes aumentos para poder diferenciar con facilidad sus fases. Este po de microestructura, es esperada a la hora de analizar estos elementos, debido a las propiedades mecánicas requeridas por la norma.
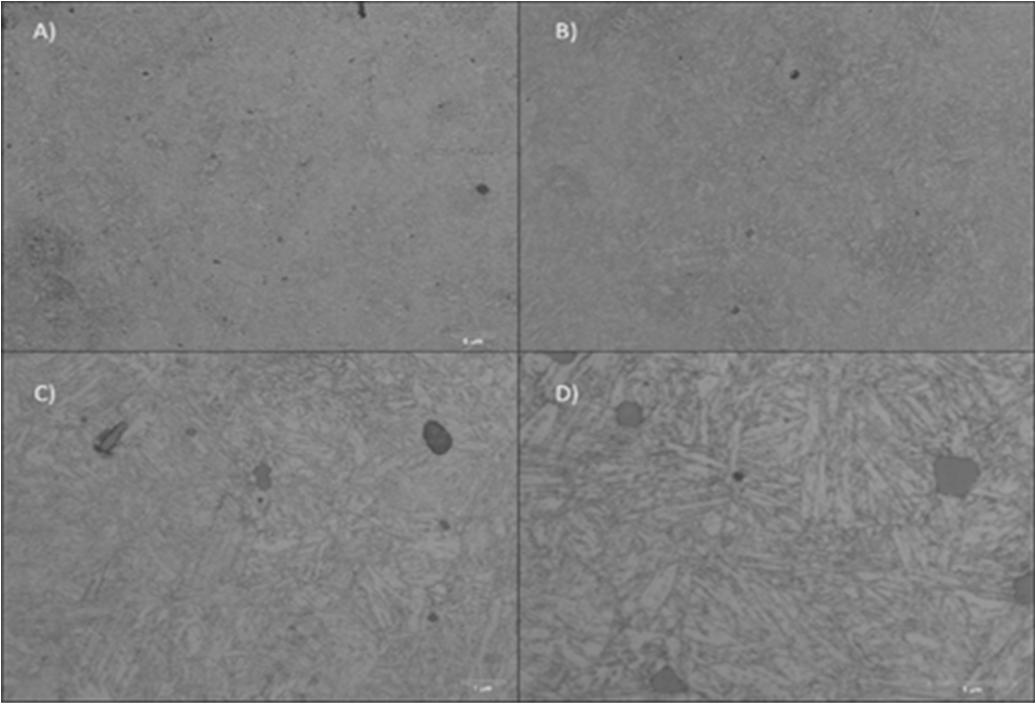
Figura 3: Microgra5a de la muestra correspondiente a la charnela A) Magnificación de 100x B) Magnificación de 200x C) Magnificación de 500X D) Magnificación de 1000x. Fuente: Elaboración propia del autor.
En la figura 4, se muestra una estructura ferrita-perlita >pica de un acero hipoeuteco de, donde el carbono está presente como perlita fina adyacente a los granos de ferrita proeutectoide. Los granos perlí cos reflejan menos luz que los ferrí cos y por lo tanto se muestran más oscuros. A simple vista se pueden diferenciar las fases presentes, es mando una mayor presencia de ferrita proeutectoide en comparación a la perlita. Se debe considerar que se excedió el empo recomendado (50 segundos) para el ataque químico, por lo que la muestra se visualiza levemente “quemada” oscureciendo con ello algunos granos ferrí cos.
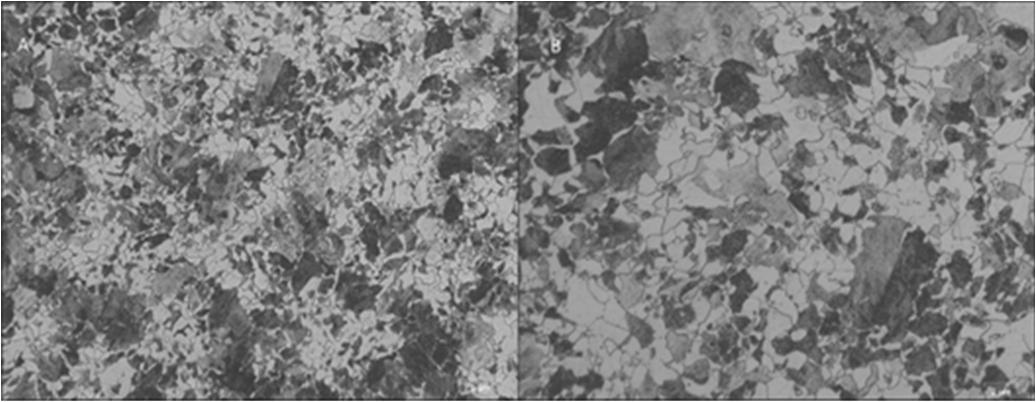
Figura 4: Muestra correspondiente al candado A) Magnificación de 100x B) Magnificación de 200x Fuente: Elaboración propia del autor.

PROPUESTA DE FABRICACIÓN POR FUNDICIÓN DE LOS COMPONENTES DEL MECANISMO DE TRACCIÓN PARA VAGONES MINERALEROS DE CVG FERROMINERA ORINOCO, C.A. REVISTA MUNDO FERROSIDERÚRGICO | AÑO XI | NÚMERO 44 | JULIO 2022
Los valores de dureza obtenidos en el análisis de la charnela son elevados. La dureza de la pieza debe encontrarse en el rango de 241-311 HB. Observando los datos de la tabla I se puede notar que los valores exceden el rango, la alta dureza de la pieza puede ocasionar fragilidad y para un elemento en un estado de tracción, impacto y compresión es perjudicial.
Tabla I: Valores de dureza Vickers (HV) de la charnela. Los resultados obtenidos mediante la caracterización, indican que la charnela posee propiedades acordes con la norma y el candado, a pesar de no cumplir con la norma, es u lizable debido a su función, sin embargo, este se verá afectado por los esfuerzos producidos, ocasionando deformación o fractura tempranamente, por lo que su empo de vida ú l es menor.
Como se puede observar en la tabla III, existe una diferencia considerable entre las muestras, siendo la muestra A la única que permanece dentro del rango de composición del acero recomendado, debido al contenido de carbono (C) presente en las muestras. Sin embargo, la AAR permite la variación química siempre y cuando éstas cumplan con las propiedades mecánicas solicitadas.
Además, se puede observar como la muestra B, a pesar de poseer mayor contenido de carbono (C) y manganeso (Mn), posee un nivel de dureza menor a la muestra A, dejando en evidencia que a la pieza no se le realizó el tratamiento térmico requerido.
Tabla III: Resultado de análisis químicos y comparación con la norma.
Equivalencia del promedio en Brinell: 332,27 HB Fuente: Elaboración propia del autor.
Prueba 1 2 3 4 5 6 7 8 9 10 Promedio
Dureza (HV)
334,4 328,1 344,5 54,1 332,4 322,6 344,5 333,0 369,9 342,6 340,51
Para el caso del candado, como se visualiza en la tabla II, el ensayo de dureza confirma lo esperado dada la microestructura observada, el grado de dureza obtenido se encuentra por debajo de lo requerido, de acuerdo a la AAR, la pieza corresponde a un acero de grado C, debido a que se encuentra en el rango de dureza de 179-241 HBN; siendo piezas que no están capacitadas para soportar el acarreo de mineral. El estudio indica que la pieza no cumple con las propiedades necesarias para trabajar correctamente. El empo de vida de estos componentes, es en promedio de 600.000 ciclos de uso, luego de esos ciclos las piezas se ven debilitadas debido a la fa ga, por consiguiente, extender el plazo de uso por encima del empo de vida ú l, puede resultar en un accidente. Los esfuerzos máximos de impacto soportados por las piezas, disminuyen provocando agrietamientos o fracturas.
Tabla II: Valores de dureza Rocwell (HRC) del candado.
Prueba 1 2 3 4 5 6 7 8 9 10 Promedio
Dureza (HV) 9,5 10 8 8 8,5 9 8 7 10 12 9
Equivalencia del promedio en Brinell: 179 HB. Fuente: Elaboración propia del autor. Elemento Muestra A Muestra B Muestra C Norma
OES OES XRF OES AA M-201
C 0,29 0,36 0,119 0,37 0,32 Mn 1,39 1,56 0,853 0,671 1,85 Cr 0,44 0,24 0,116 0,104 P 0,03 0,05 0,015 0,017 0,04 S 0,02 0,02 0,014 0,0106 0,04 Si 0,45 0,5 0,181 0,199 1,50 Ni 0,07 0,12 0,036 0,042 - Cu 0,12 0,17 0,116 0,104 - Mo 0,18 0,06 0,003 0,014 -
Fuente: Elaboración propia del autor.

PROPUESTA DE FABRICACIÓN POR FUNDICIÓN DE LOS COMPONENTES DEL MECANISMO DE TRACCIÓN PARA VAGONES MINERALEROS DE CVG FERROMINERA ORINOCO, C.A. REVISTA MUNDO FERROSIDERÚRGICO | AÑO XI | NÚMERO 44 | JULIO 2022
B. Desarrollar un modelo de fundición a los componentes en estudio implementando un soSware computacional de modelado en CAD, considerando las contracciones volumétricas que experimenta el metal al solidificar
Para la realización de los diseños se tomaron en cuenta ciertos factores, principalmente, que las piezas se sujeten en el lugar des nado a su trabajo dentro del bas dor de manera que no interfieran con ningún otro componente; el comportamiento de las piezas durante la tracción de los vagones y la interacción entre estas; y por úl mo la holgura que deben poseer estos elementos al estar acoplados de modo que puedan trabajar correctamente. (acción floja).
Modelado de pieza El cambio realizado en la zona inferior ene la intención de permi r extraer el modelo del molde fácilmente sin afectar a este y a su vez otorga un diseño sencillo de trabajar por simetría.
Un punto importante a tomar en cuenta, son las variantes existentes en los modelos de la charnela, que puede tener secciones de la pieza que estarían huecas para disminuir su peso. Se lograron diferenciar tres modelos, la primera es la u lizada como modelo base y corresponde a la charnela completamente sólida ( po A), siendo esta la de mayor peso. La segunda es una charnela con solo una sección hueca en la zona de acople o “gancho” ( po B). El tercer modelo ( po C) es una charnela con dos secciones huecas ubicadas en la zona superior e inferior de la pieza. Siendo el modelo po A, la presente en la inves gación.
En la figura 6, el diseño del candado, es único; si bien existen variantes en los cuales el “bloque” superior encargado de realizar la función de bloqueo es parcialmente hueco, no se consideró necesario estudiar el diseño del mismo, dado que no es completamente compa ble con los acopladores po F.
El modelado de la pieza permi ó inferir aquellas medidas que, aunque no son estrictamente necesarias, aportan información importante para la realización de los cálculos y el modelo. Si bien se u liza el mismo programa, la realización de los diseños es completamente diferente.
En la figura 5, se observa el modelado de la charnela, cuyo diseño se realizó por simetría, siendo esto beneficioso puesto que la pieza ene cierto grado de complejidad. No obstante, a pesar de poseer gran simetría, el diseño varió en la sección trasera, por tener cortes diferentes en sus lados y en el ángulo de ambos se nota la inclinación.

Figura 5: Dis ntas vistas de la charnela modelada en CAD. Fuente: Elaboración propia del autor. Figura 6: Diseño computarizado del candado po F visto desde cuatro ángulos diferentes. Fuente: Elaboración propia del autor.
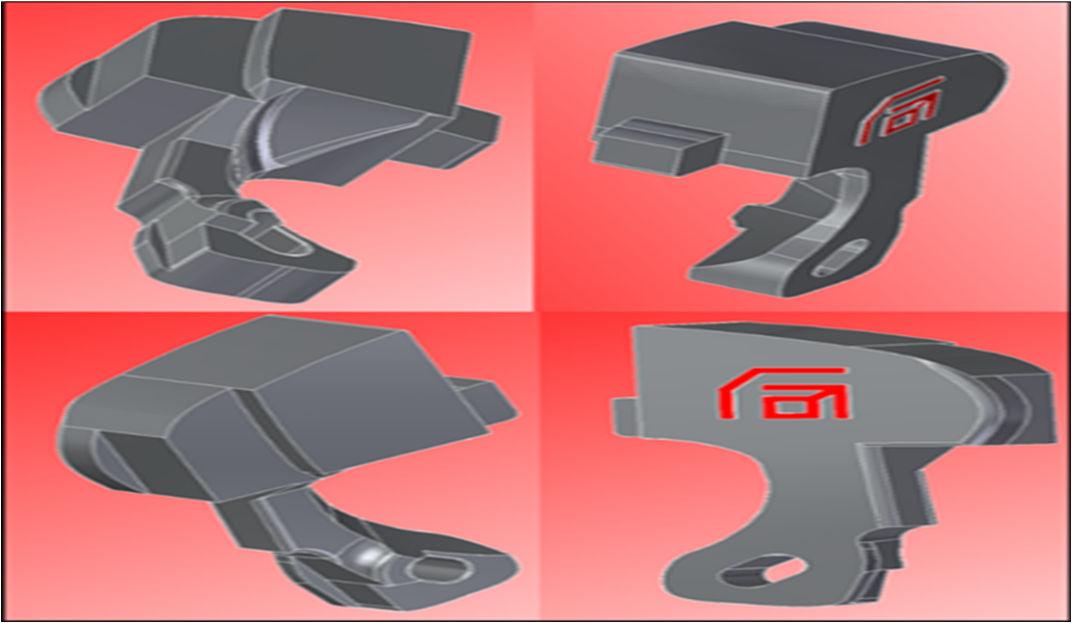
Durante el diseño de la pieza se consideró importante establecer los radios de curvaturas correctos en la zona interna del mango, debido que esta es una de las zonas que entra en contacto con la charnela a la hora de asegurar el acople, un error en el diseño puede significar CENTRO DE INVESTIGACIÓN Y GESTIÓN DEL CONOCIMIENTO PÁG. 35

PROPUESTA DE FABRICACIÓN POR FUNDICIÓN DE LOS COMPONENTES DEL MECANISMO DE TRACCIÓN PARA VAGONES MINERALEROS DE CVG FERROMINERA ORINOCO, C.A. REVISTA MUNDO FERROSIDERÚRGICO | AÑO XI | NÚMERO 44 | JULIO 2022
significar que la pieza quede inclinada y esto puede ocasionar que el mecanismo se quede trabado a la hora de accionar la palanca y realizar el desacople de los vagones. El diseño de la figura 6 se desarrolló sin ningún cambio significa vo.
Diseño del modelo
Para el diseño del modelo de la charnela (figura 7) se optó por empezar implementando un modelo bipar do. La simetría de la pieza permite establecer una línea de par ción con claridad. Adicionalmente, al seccionar el modelo permite trabajarlo con mayor facilidad considerando su tamaño. Cabe destacar que la forma de la pieza, facilita el diseño del modelo, sus curvas, ángulos y cortes le dan la forma requerida para re rar el modelo del molde sin necesidad de realizar modificaciones extremas.
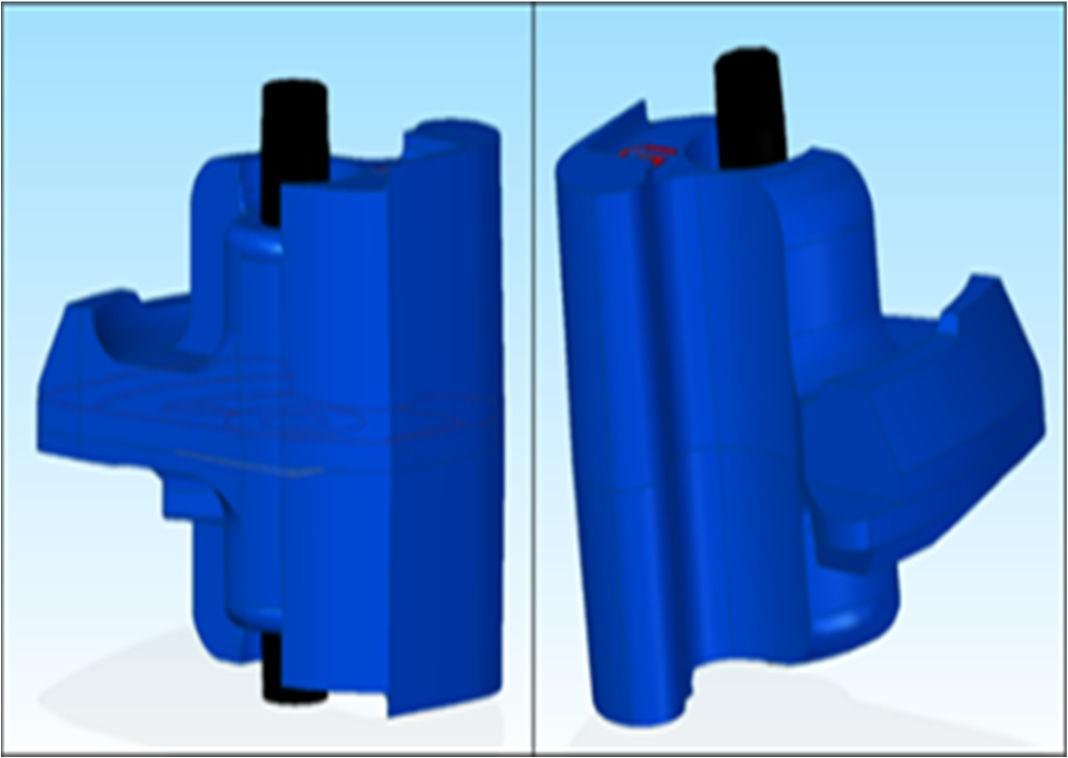
Figura 7: Modelo de la charnela diseñado en CAD Fuente: Elaboración propia del autor.
El candado, (figura 8) por otra parte, se diseñó implementando un modelo de pieza suelta; esto debido a que una de sus caras es completamente plana, razón por la cual, el diseño a plasmar en el molde se encuentra en una sola dirección, la pieza suelta corresponde a la saliente del “bloque”, cuya función es hacer tope al momento de elevarlo y genera con ello un giro que permite golpear el “ ra muela” para hacer girar la charnela.

Figura 8: Modelo del candado diseñado en CAD. Fuente: Elaboración propia del autor.
Se optó diseñar mediante un modelo de pieza suelta por la “protuberancia”, presente en la pieza, ésta quedaría atrapada por la arena a la hora de moldear y establecer un ángulo de salida que permita re rar el modelo del molde, por el contrario siendo un modelo entero podría causar que las paredes del molde sean afectadas.
C. Determinar el perfil de solidificación de la charnela y el candado a través de una simulación del proceso de solidificación implementando un soGware computacional para establecer la posición de las mazarotas en el modelo de fundición
Al observar el avance de la solidificación en las piezas, se logra predecir la ubicación de los posibles rechupes ocasionados por la contracción del metal.
De acuerdo a la teoría, la solidificación de una pieza inicia a par r de las paredes del molde y avanza hasta llegar al centro del mismo, considerando además que las zonas de menor módulo, sea por una mayor área superficial o menor volumen, solidificarán primero.
En la figura 9 se puede observar el avance de la solidificación de la charnela, mostrando la ubicación de la úl ma zona en solidificar, en la cual es probable que se forme una cavidad debido a la contracción.

PROPUESTA DE FABRICACIÓN POR FUNDICIÓN DE LOS COMPONENTES DEL MECANISMO DE TRACCIÓN PARA VAGONES MINERALEROS DE CVG FERROMINERA ORINOCO, C.A. REVISTA MUNDO FERROSIDERÚRGICO | AÑO XI | NÚMERO 44 | JULIO 2022
En la misma figua, solo se observa el cambio de fracción líquida sin tomar en consideración la temperatura total de la pieza. Por otro lado, la figura 10, muestra el contorno de temperatura total de la charnela, la temperatura del punto caliente al cabo de los 45 minutos se man ene a 1437 ºC (1710 ºK) y las zonas más frías se encuentran a 1267 ºC (1540 ºK).
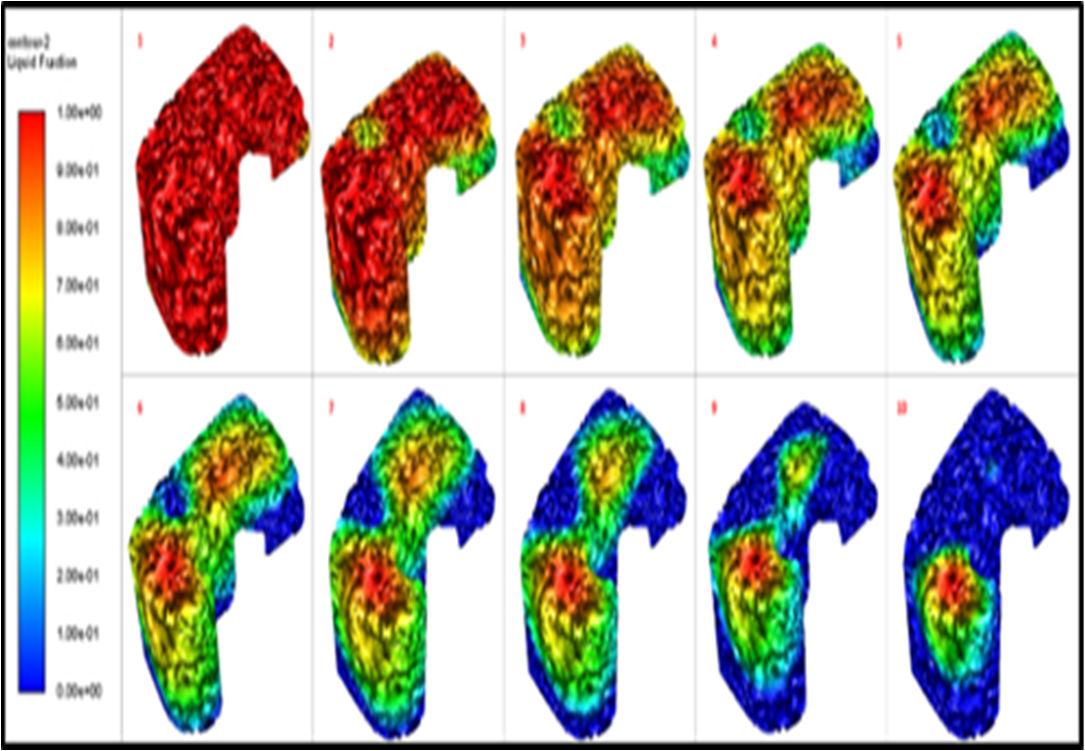
Figura 9: Variación de fracción líquida de la charnela. Fuente: Elaboración propia del autor.
Figura 10: Contorno de temperatura total de la charnela. Fuente: Elaboración propia del autor.
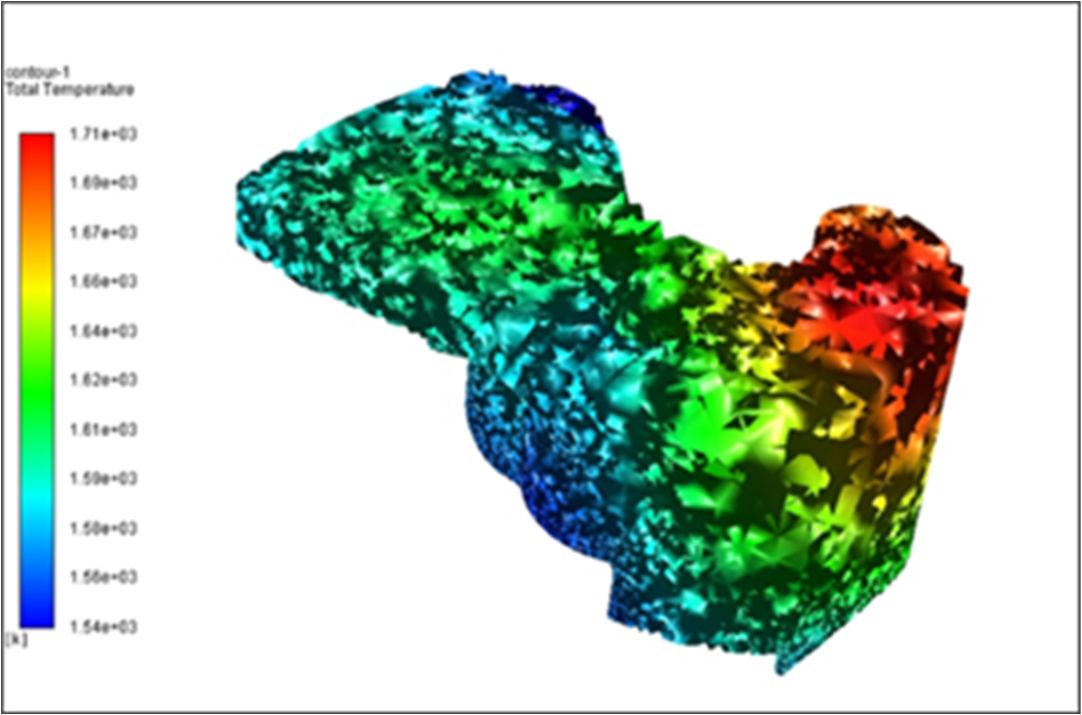
Se debe considerar que la imagen mostrada solo contempla la mitad de la pieza, por consiguiente, la superficie observada representa el centro de la misma. La figura 11, muestra cómo se forman dos puntos calientes a par r de la separación de la fracción líquida, debido a la solidificación de las zonas delgadas adyacentes al macho. Esto indica que es posible la formación de defectos en dichas zonas. En ese orden, se requieren ubicar dos mazarotas lo más cerca posible de estos puntos calientes.
La simulación del candado muestra como la solidificación inicia desde el extremo del mango y avanza a lo largo hasta alcanzar el bloque; De igual manera, la pequeña protrusión del bloque solidifica primero.
Este proceso de solidificación, sigue la analogía de la cuña en escalera, donde el escalón menor se alimenta del mayor, dejando en evidencia como el bloque será lo úl mo en solidificar. Se asume que implementando una mazarota en esa zona es suficiente para compensar la contracción.

Figura 11: Variación de fracción líquida del candado. Fuente: Elaboración propia del autor.
Las temperaturas en el punto caliente rondan los 1400 ºC (1670 ºK) y las zonas más frías de las piezas se encuentran a 957 ºC (1230 ºK) como lo indica la figura 12.
En este punto la pieza se encuentra completamente sólida, considerando el empo final de la simulación, siendo de 40 minutos.

PROPUESTA DE FABRICACIÓN POR FUNDICIÓN DE LOS COMPONENTES DEL MECANISMO DE TRACCIÓN PARA VAGONES MINERALEROS DE CVG FERROMINERA ORINOCO, C.A. REVISTA MUNDO FERROSIDERÚRGICO | AÑO XI | NÚMERO 44 | JULIO 2022
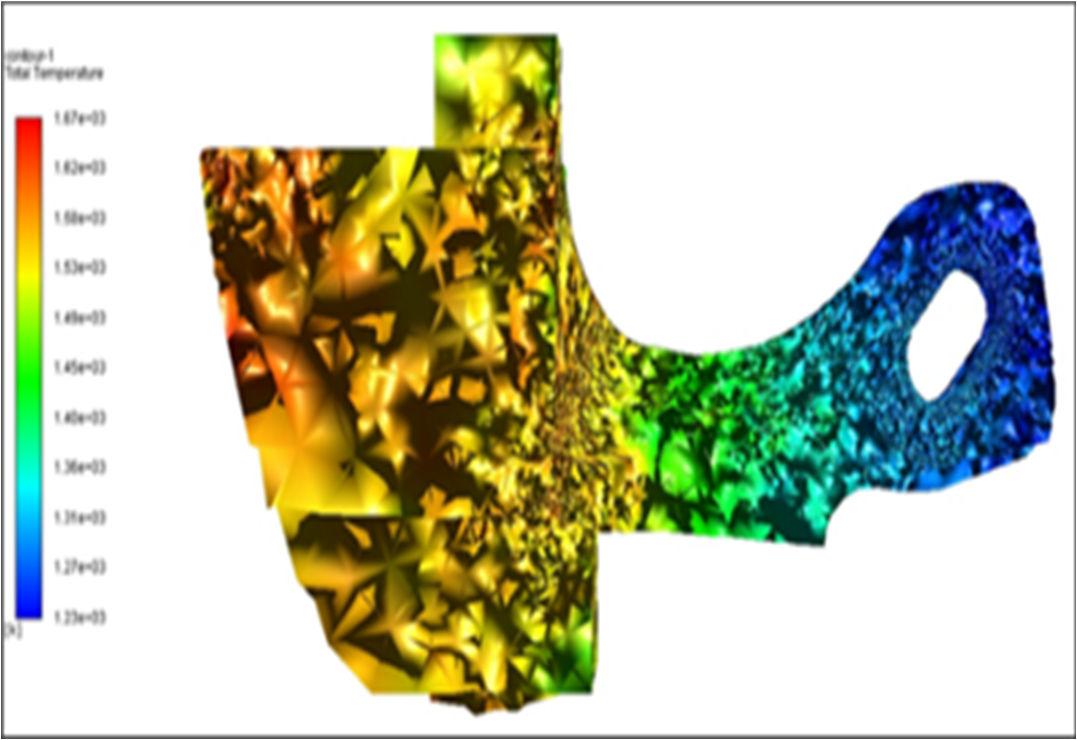
Figura 12: Contorno de temperatura total del candado. Fuente: Elaboración propia del autor.
Con los puntos ya establecidos, es necesario darles dimensiones a los elementos auxiliares.
El diseño planteado se realizó en función de la simulación, a fin de compensar el metal necesario durante la solidificación, esto direccionando dicho proceso desde las paredes hacia las mazarotas (ver figura 13). Seleccionado un modelo de mazarotas abiertas que permita, el escape de los gases generados durante el proceso de colada, debido a la baja permeabilidad de la pieza.
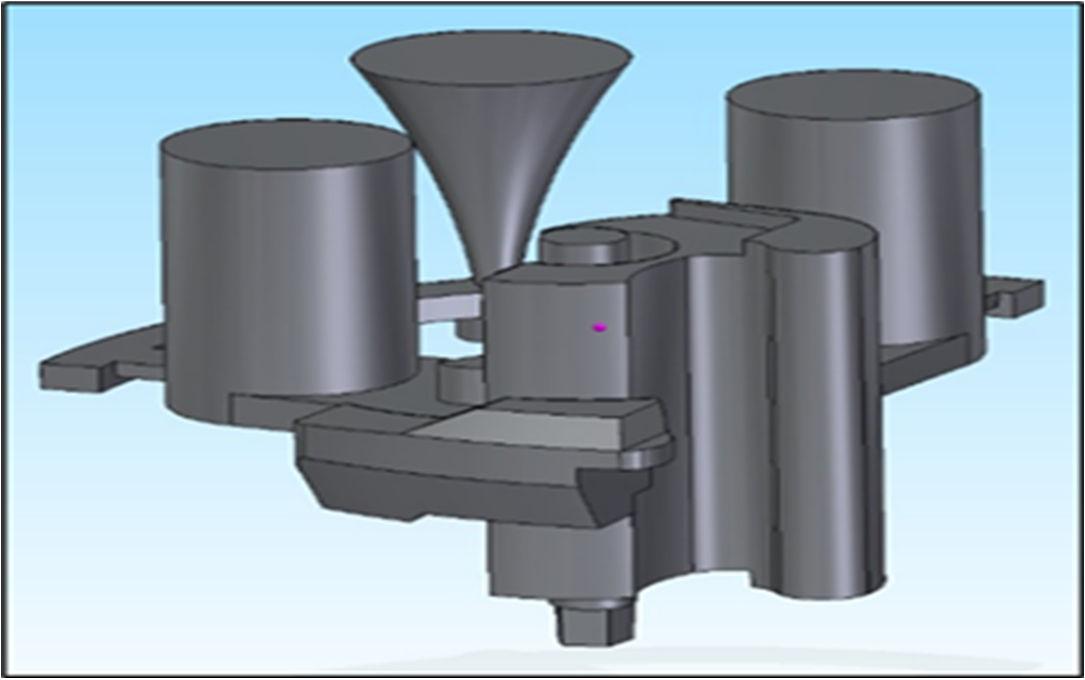
Figura 13: Diseño de fundición de charnela con dos mazarotas. Fuente: Elaboración propia del autor. Se realizaron dos diseños del candado (ver figura 14), a par r de los cálculos, que varían simplemente por la posición de la mazarota, donde muestra un diseño con una mazarota superior y otro con una mazarota lateral. La entrada del metal es a par r del mango de la pieza.
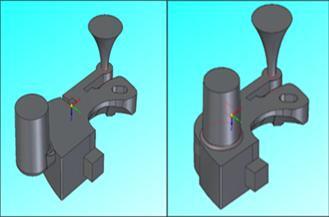
Figura 14: Diseños de fundición del candado con mazarota lateral y superior. Fuente: Elaboración propia del autor.
El diseño más conveniente, es el que corresponde a la mazarota superior, debido a que se encuentra completamente sobre la zona de solidificación final de la pieza y no posee un cuello de contacto que pueda formar un “cuello de botella” durante la solidificación, impidiendo el paso del metal líquido desde la mazarota hacia la pieza, además de que simplifica el diseño del modelo y la realización del molde.
D. Estudiar el comportamiento del metal durante la colada a través de una simulación mul/fásica, para predecir posibles defectos asociados con el llenado del molde
Para este caso se establecieron paredes de baja permeabilidad que muestren las zonas en las cuales existe la mayor acumulación de gases durante el proceso y una velocidad de entrada dependiente de la gravedad, considerando además que el diseño se realizó con mazarotas abiertas.

PROPUESTA DE FABRICACIÓN POR FUNDICIÓN DE LOS COMPONENTES DEL MECANISMO DE TRACCIÓN PARA VAGONES MINERALEROS DE CVG FERROMINERA ORINOCO, C.A. REVISTA MUNDO FERROSIDERÚRGICO | AÑO XI | NÚMERO 44 | JULIO 2022
A medida que el metal líquido se asienta al fondo del molde, “empuja” el aire hacia arriba, forzándolo a salir a través de las mazarotas, (ver figura 15); y una vez que el metal sobrepasa los cuellos de contacto ubicados a la altura de la línea de par ción, el aire ende acumularse en la zona superior del molde.
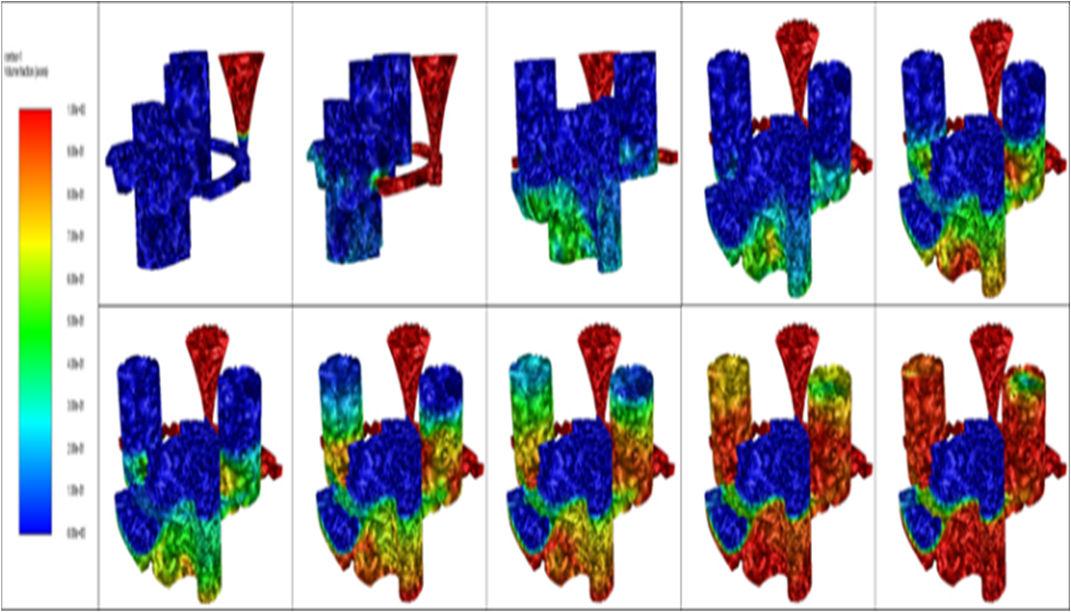
Figura 15: Simulación de colada de la charnela, ilustración de cambio volumétrico del metal líquido. Fuente: Elaboración propia del autor.
La presión resultante de este aire en combinación con los gases liberados en el proceso, puede provocar la ruptura del molde, además de la formación de defectos po sopladura debido al llenado incompleto de la pieza, (ver figura 16).
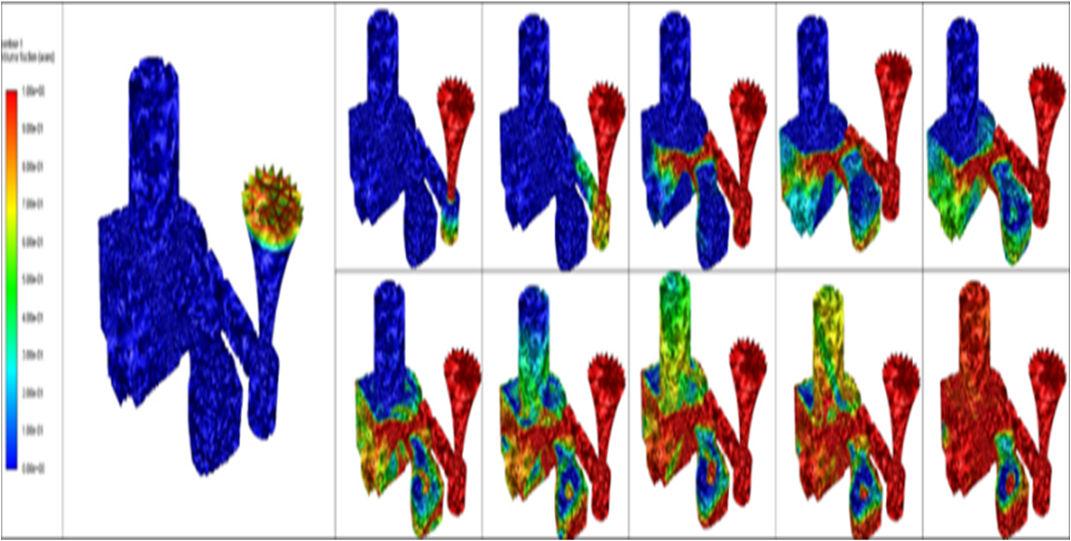
Figura 16: Simulación de colada del candado, ilustración de cambio volumétrico del metal Fuente: Elaboración propia del autor.
El caso del candado es diferente, el diseño abarca una mazarota superior en la zona de mayor concentración de fluido; por consiguiente, permite con facilidad la salida de los gases. El candado solo ocupa la semicaja inferior del molde y considerando que la unión entre el modelo y la mazarota se encuentra en la línea de par ción, la salida de gases seguiría siendo a través de la mazarota. No obstante, en la zona del mango (donde inicia la solidificación) se observa una mancha azul en la úl ma etapa del llenado, siendo esto un indica vo de la presencia de gas en esa zona.
E. Proponer un plan de modelo y fusión, tomando como referencia las propiedades de las piezas en servicio y los estándares establecidos por la AAR
Preparación del molde y fabricación de machos
Para la fabricación del molde, se plantea u lizar como base, arena de sílice lavada y seca, libre de impurezas, mezclada con resina furánica y un catalizador ácido de po orgánico para un proceso con arena de endurecimiento rápido. El mezclado lo realizará una turbo mezcladora que posteriormente liberará la arena en las cajas de moldeo.
Las dimensiones del molde vienen determinadas por la forma y tamaño del modelo de fundición, donde se debe asegurar que la cavidad formada por el modelo, se encuentre al menos a 5 cm de distancia de las paredes y fondo del molde. Además, se debe proporcionar espacio suficiente para la colocación de las guías.
El modelo del macho (figura 17), se realizó implementando un diseño simple, con portadas a los lados de manera que pueda sujetarse de ambas partes del molde, el soporte principal corresponde al de mayor tamaño; está diseñado para incrustarse en el molde inferior y fijarlo para evitar movimiento a la hora de colocar el semi-molde superior.
Figura 17: Vista espacial macho principal de la ranura del pivote. Fuente: Elaboración propia del autor.

PROPUESTA DE FABRICACIÓN POR FUNDICIÓN DE LOS COMPONENTES DEL MECANISMO DE TRACCIÓN PARA VAGONES MINERALEROS DE CVG FERROMINERA ORINOCO, C.A. REVISTA MUNDO FERROSIDERÚRGICO | AÑO XI | NÚMERO 44 | JULIO 2022
Materia prima Tratamiento Térmico
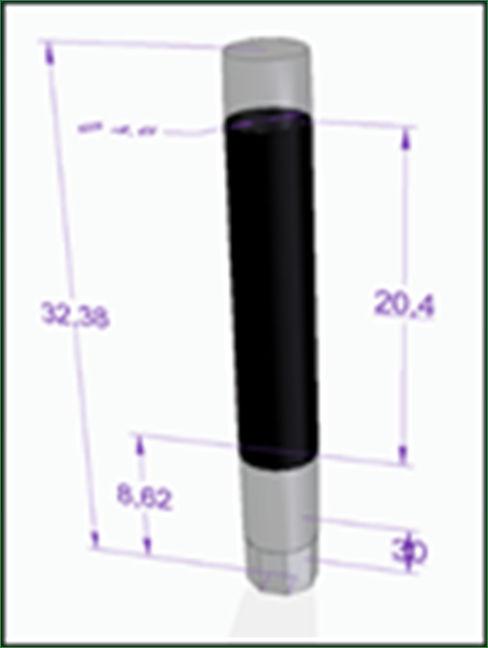
La materia prima a u lizar proviene de ejes y ruedas de vagones de clase C, fuera de servicio, que cumplen con los estándares AAR M-107 /M-208. La composición química de este acero, está en el rango de los denominados SAE-AISI 1070 de acuerdo al porcentaje de carbono (C) y manganeso (Mn) presente.
Horno y fusión del metal
Para la etapa de fusión, enen a disposición hornos eléctricos de inducción con capacidades de 2500 Kg, 800 Kg y 450 Kg.
De acuerdo a la teoría, la temperatura de fusión de la aleación es aproximada a 1460 °C, para garan zar el empo suficiente de operación y ver do del metal. Considerando el ver do del metal del horno al cucharon y posterior colada al molde, la temperatura de colada recomendada es 60 °C y 100 °C superior a la temperatura de fusión. En la prác ca, los operadores suelen trabajar con temperaturas que rondan los 1560 ºC.
Limpieza y acabado
Desmolde: Se puede realizar de forma manual o con ayuda de mesas vibratorias para romper el molde. En caso de que la vibración no sea suficiente como para re rar el macho, se puede implementar cualquier medio que permita romperlo o aflojarlo de modo que pueda salir al llevar la pieza nuevamente a la mesa de vibración.
Limpieza: Para el proceso de desbarbado se recomienda el uso de equipos de oxicorte de modo que se puedan re rar con facilidad los elementos del sistema de alimentación. Para eliminar imperfecciones y rebabas, u lizar equipos abrasivos como esmeriles o máquinas de desbaste.
Acabado: Dado que la pieza no requiere de un acabado superficial en concreto, dejar con el obtenido por el molde. Se propone someter a las piezas a un proceso de normalizado, siguiendo los estándares de la Norma IRAM 1070. Considerando la temperatura crí ca superior Ac3 = 743 °C, calentar las piezas a temperaturas que se encuentren en el rango de los 800 °C. Para el caso de la charnela se recomienda el mantenimiento de la pieza en el horno entre cuatro y cuatro horas y media; para el candado, un empo máximo de tres horas y media debe ser suficiente para asegurar la homogenización de la pieza. Posteriormente dejar enfriar las piezas al aire.
Tabla IV: Cuadro compara vo entre las propiedades de un acero AAR grado E y AISI 1070 normalizado.
Acero AAR grado E vs AISI 1070 AAR Grado E AISI 1070
Resistencia a la tracción (MPa) 827 870-1030
Límite elás)co (MPa) 690 500-590
Alargamiento 14 12-20 % Reducción de área. 30 20-35
Dureza HB 241-311 261-313
Fuente: Elaboración propia del autor.
Control de calidad
Inspección visual: Realizar una inspección superficial de los elementos asegurándose de que estos no posean grietas, porosidades o deformaciones. Verificar además que las dimensiones sean las correctas.
Análisis con )nta penetrante: Verificar la presencia de microgrietas que no puedan verse a simple vista en la inspección visual.
Análisis por ultrasonido: Permite analizar la integridad interna de la pieza, comprobando que no existan defectos internos como porosidades, inclusiones, vacancias o agrietamientos.

PROPUESTA DE FABRICACIÓN POR FUNDICIÓN DE LOS COMPONENTES DEL MECANISMO DE TRACCIÓN PARA VAGONES MINERALEROS DE CVG FERROMINERA ORINOCO, C.A. REVISTA MUNDO FERROSIDERÚRGICO | AÑO XI | NÚMERO 44 | JULIO 2022
Además de los ensayos mencionados, es recomendable realizar ensayos destruc vos a las piezas de pruebas, de modo que se puedan verificar sus propiedades mecánicas. De ser posible también se recomienda realizar ensayos de: impacto, tracción, dureza y análisis metalográfico.
V. CONCLUSIONES
Los análisis metalográficos determinaron que la charnela posee propiedades acordes con lo establecido en las normas AAR, a pesar de tener un grado de dureza elevado, de 332 HB con respecto al máximo de 311HB que dicta el manual, con una estructura boní ca de grano fino. El candado, por otra parte, obtuvo un valor promedio de 179 HB y considerando la microestructura observada se asume que no cumple con los requerimientos estructurales, lo que supone que sus propiedades mecánicas no cumplen los estándares.
Se lograron diseñar los modelos computarizados de acuerdo a las dimensiones requeridas a par r del desarrollo general de las piezas en CAD obteniéndose un modelo bipar do para la charnela y un modelo de pieza suelta para el candado.
Las simulaciones arrojaron la información requerida sobre la dirección de la solidificación iden ficando con ello la ubicación en las que pueden formar defectos po rechupe.
Con la simulación de colada, se observó las zonas de acumulación de gas en los moldes. La velocidad de colada en ambos casos se considera aceptable.
El plan de fusión y modelo de los moldes se adecuó a los materiales y equipos presentes en la empresa fundidora, cumpliendo con los estándares establecidos por la AAR y proponiendo además, la fabricación, implementando un acero AISI-1070 normalizado ofreciendo propiedades similares a lo establecido. VI. RECOMENDACIONES
Proponer la fabricación por fundición del bas dor las partes y piezas que trabajan en el mecanismo de tracción de los vagones.
Establecer los parámetros de fabricación para los modelos de charnela po B y po C, de modo que sea posible el ahorro de material.
Realizar un análisis estructural mediante una simulación de las partes y piezas en operación para evaluar el rendimiento que ofrecen los mismos.
VII. REFERENCIAS
[1] Arteaga Aguedo (2003) Diseño de fundición de piezas ferrosas. [Trabajo de ascenso]
Departamento de ingeniería metalúrgica.
UNEXPO.
[2] Amsted rail (2014) Heavy haul impacts call for highperformance protec on. Recuperado de: hgps:// www.amstedrail.com/wp-content/ploads/2019/08/
EndofCar-Brochure.pdf
[3] Angelillo Tomas (2013) Fundición. Recuperado de: hgp:materias.fi.uba.ar/7204/teoricas/fundicion.pdf
[4] G, Hua; Y, Wang; W, li (2017) Contact analysis of
Type17 coupler based on finite element method.
Recuperado de: Contact analysis of Type17 coupler based on finite element method - ScienceDirect.
[5] H, Santoyo; J, Barreto, S, García. (2010) Simulación matemá ca de la operación de vaciado de acero líquido en un horno eléctrico de arco. Recuperado de :hgps://www.researchgate.net/publica on/ 285220987_Simulacion_matema ca_de_la_operaci on_de_vaciado_de_acero_liquido_en_un_horno_el ectrico_de_arco.

PROPUESTA DE FABRICACIÓN POR FUNDICIÓN DE LOS COMPONENTES DEL MECANISMO DE TRACCIÓN PARA VAGONES MINERALEROS DE CVG FERROMINERA ORINOCO, C.A. REVISTA MUNDO FERROSIDERÚRGICO | AÑO XI | NÚMERO 44 | JULIO 2022
[6] José Chacón (2013) Estudio de la influencia de diferentes diseños de los sistemas de alimentación y compensación en la fundición en arena. Recuperado de: Estudio de la influencia de diferentes diseños de los sistemas de alimentación y compensación en la fundición en arena (us.es)
[7] J.C, Torres (2005) Diseño asis do por ordenador.
Recuperado de: hgps://udesprocesos.webnode.es/ _files/200000031-861d88718e/Dise%C3%B1o% 20CAD%20CAM.pdf
[8] Manuel Garcés (2016) Diseño, construcción y simulación del llenado de un molde en arena en verde para fundición de piezas de aluminio blanco.
Recuperado de: Repositorio Digital - EPN: Diseño, construcción y simulación del llenado de un molde en arena en verde para fundición de piezas de aluminio blanco
[9] Mikell P. Groover (2010) Fundamentals of modern manufacturing: materials, processes and systems (4ta. Edición.) Estados Unidos.
[10] Oscar Dávila (2005) Estudio y compresión de los fenómenos de transporte asociados a la operación del drenado de ollas de acero líquido. Recuperado de hgps: // tesis.ipn.mx / bitstream /handle / 123456789 /1103/563_2005_ESIQIE_MAESTRIA_os car_davila.pdf?sequence=1&isAllowed=y
[11] Ramírez Alan (2018) Propuesta de material didác co para el área de fundición. Recuperado de: hgp: // www.ptolomeo.unam.mx:8080 / xmluibistream / handle / 132.248.52.100/15218/
PROPUESTA% 20DE% 20MATERIAL% 20DID% C3% 81CTICO% 20PARA% 20EL% 20% C3% 81REA% 20FUNDICI%C3%93N.pdf?sequence=6
[12] S, Chunduru; M, Kim, C, Mirman (2011) Failure zanalysis of railroad couplers of AAR type E.
Recuperado de: Failure analysis of railroad couplers of AAR type E. (ScienceDirect) [13] T, Prajapa ; R, Desai. (2018) Design and analysis of ga ng system for cas ng of sprocket. Recuperado de: DESIGN AND ANALYSIS OF GATING SYSTEM FOR
CASTING OF SPROCKET (ijser.org)
[14] Y, Díaz; A, Fiol; J, Arzola (2010) Simulación del proceso de solidificación del acero en las instalaciones de vaciado con nuo. Recuperado de: (PDF) Simulación del proceso de solidificación del acero en las instalaciones de vaciado con nuo (researchgate.net).
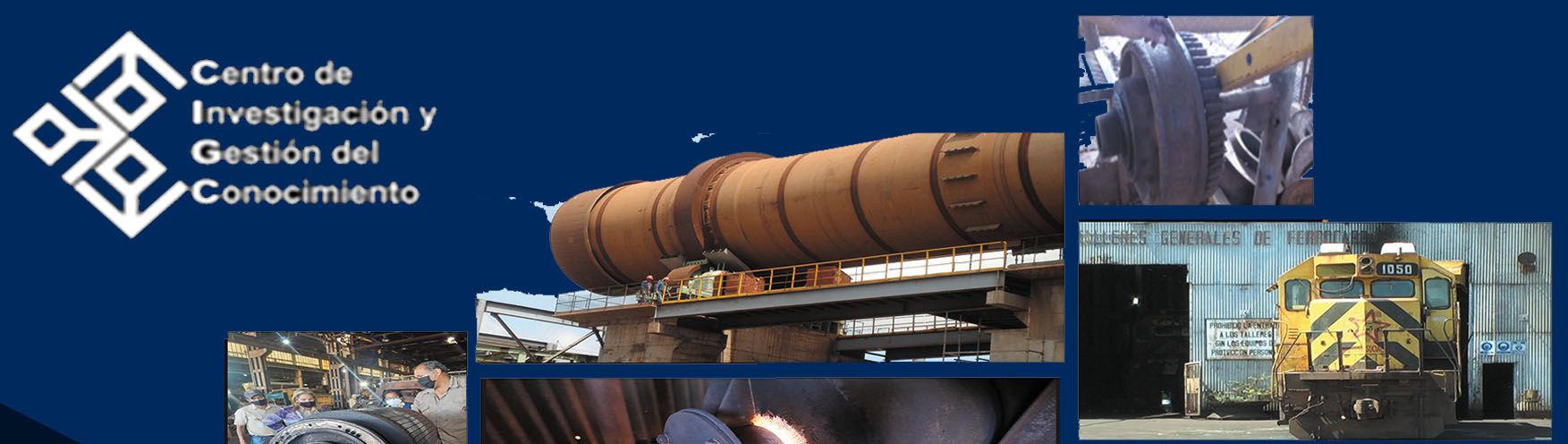

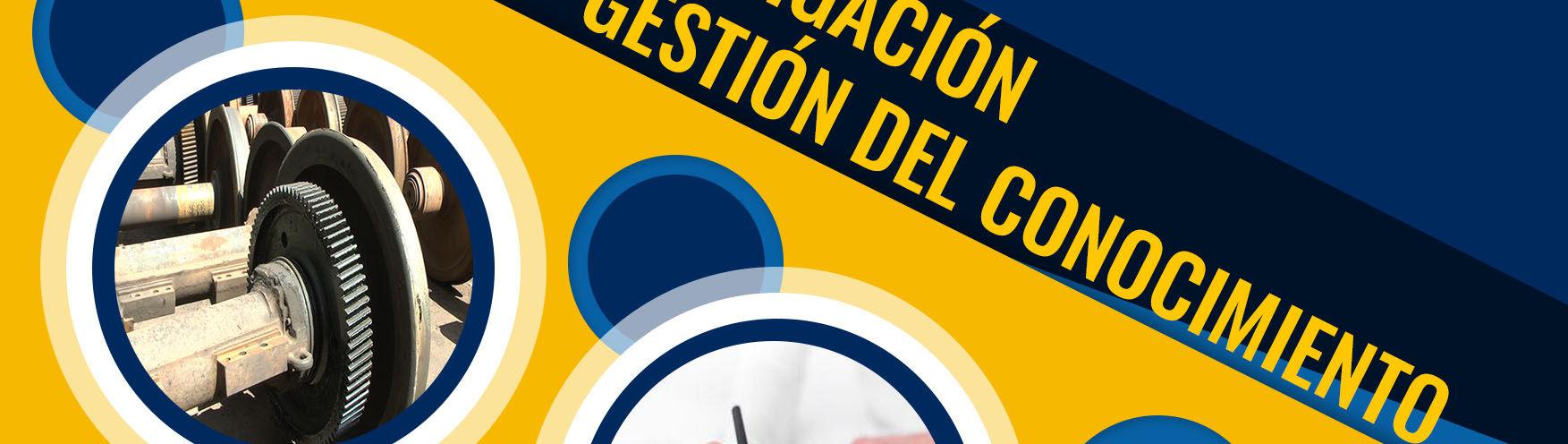
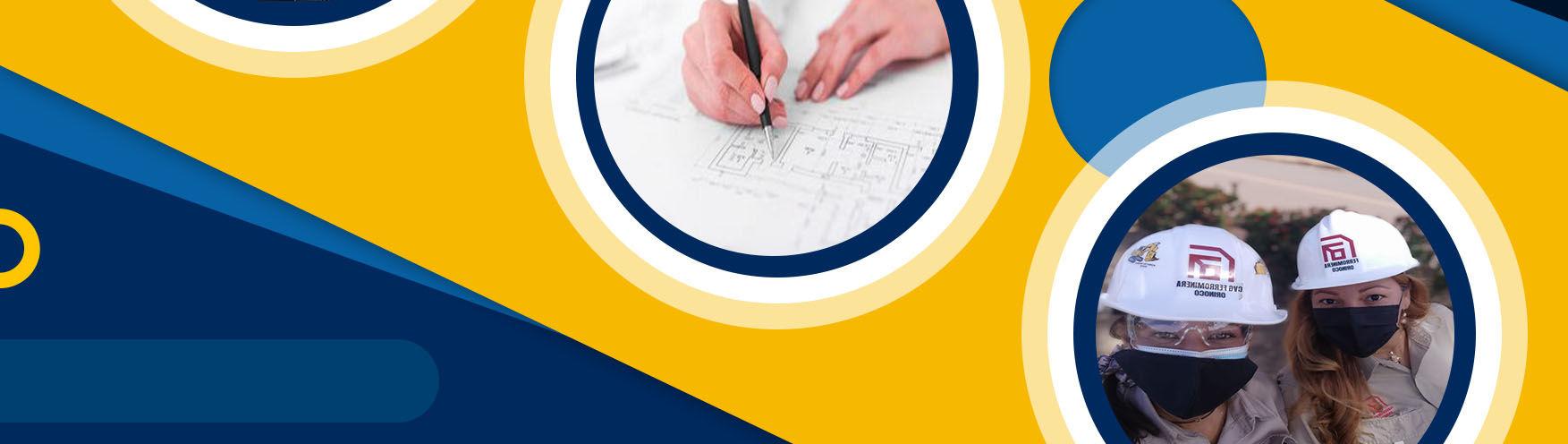
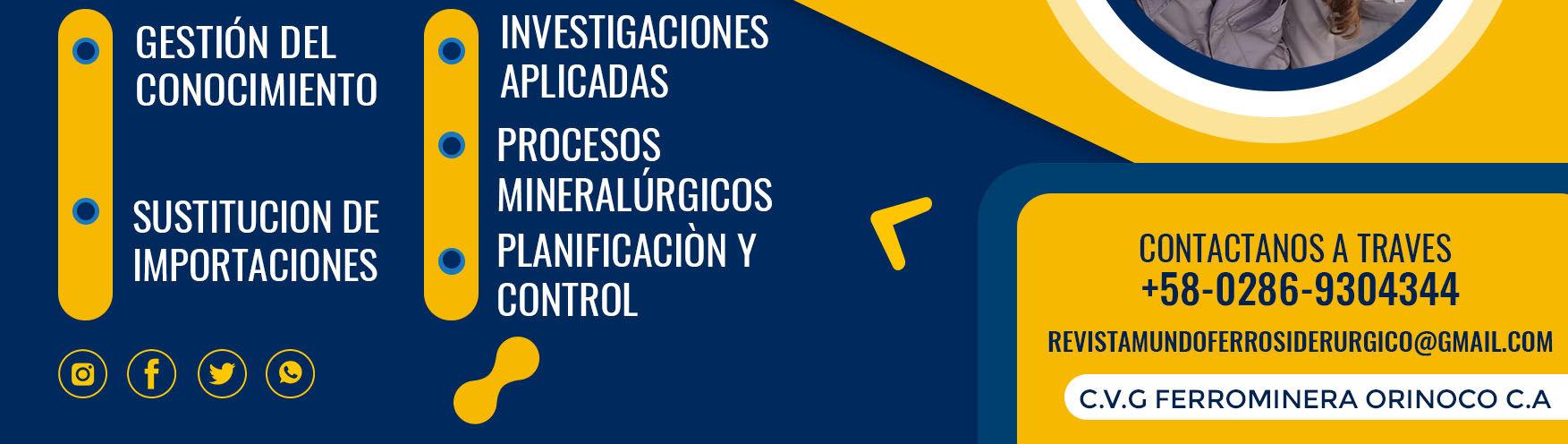
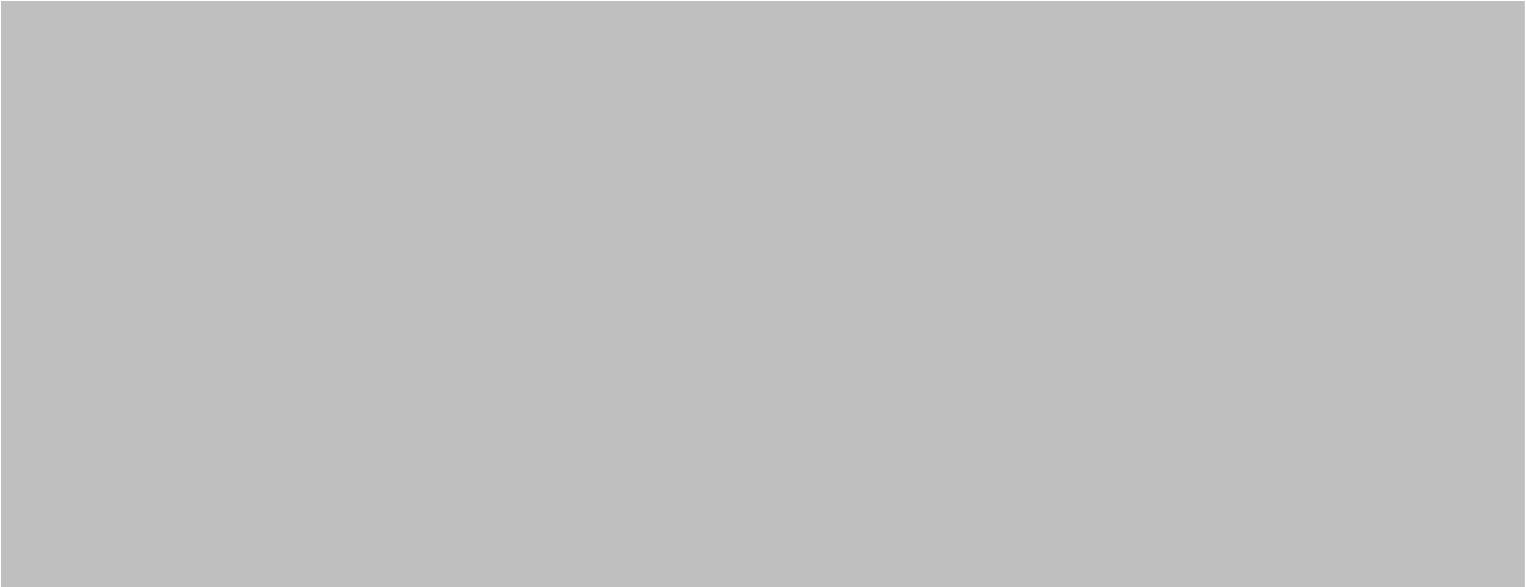
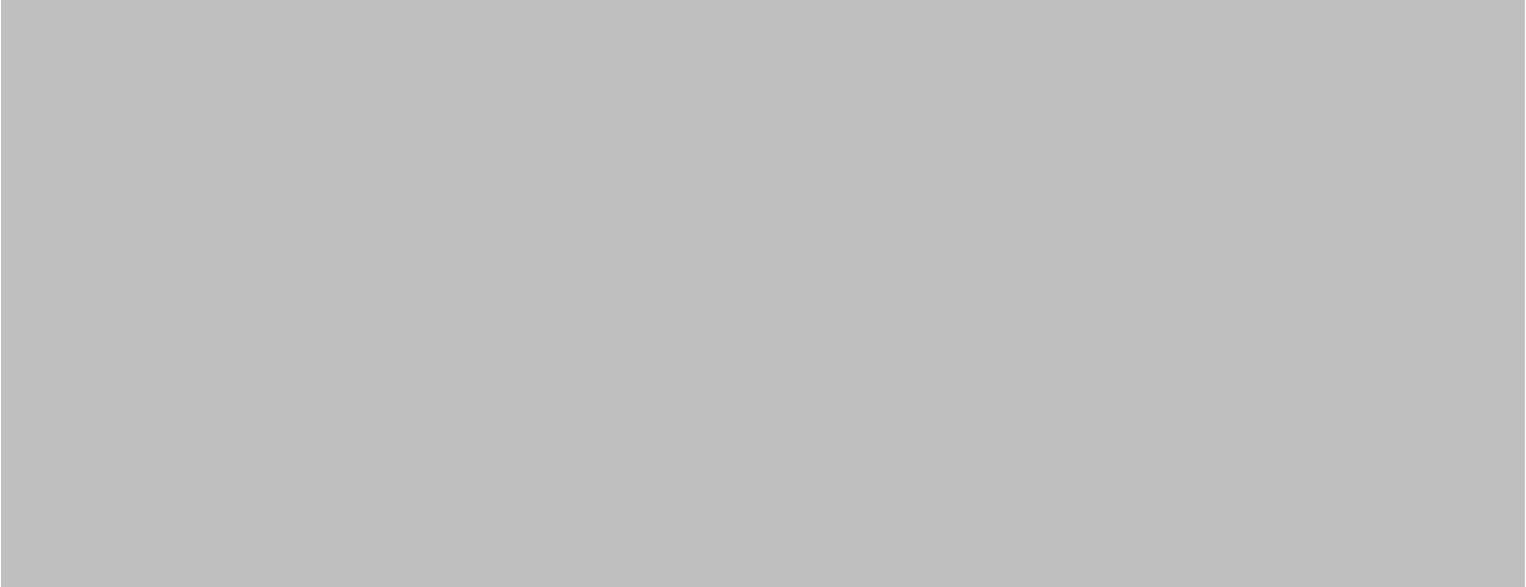

Fuente: Tomado de la Web.
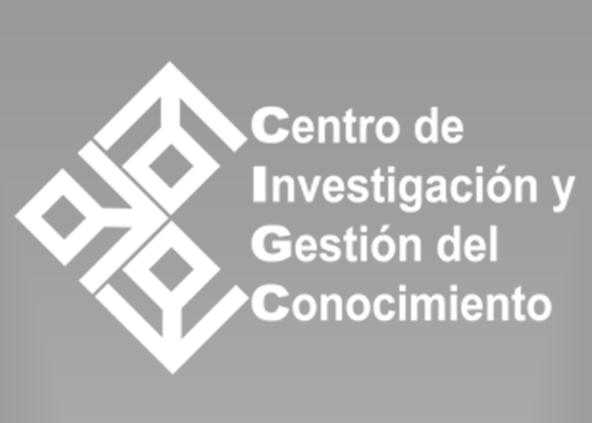
Breves noticias de Ciencia y Tecnología
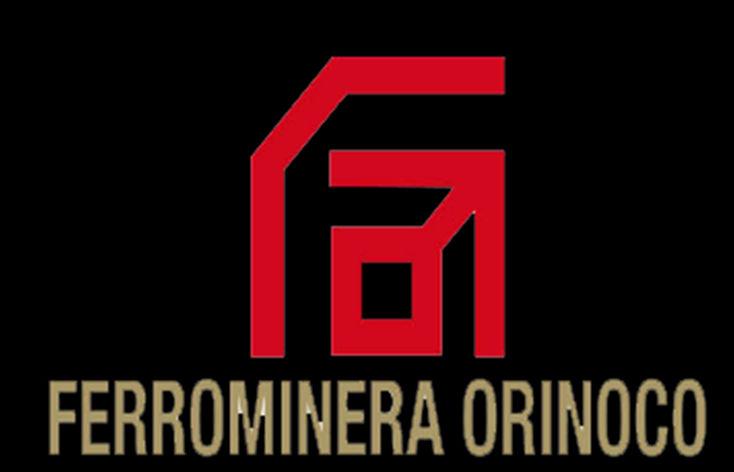
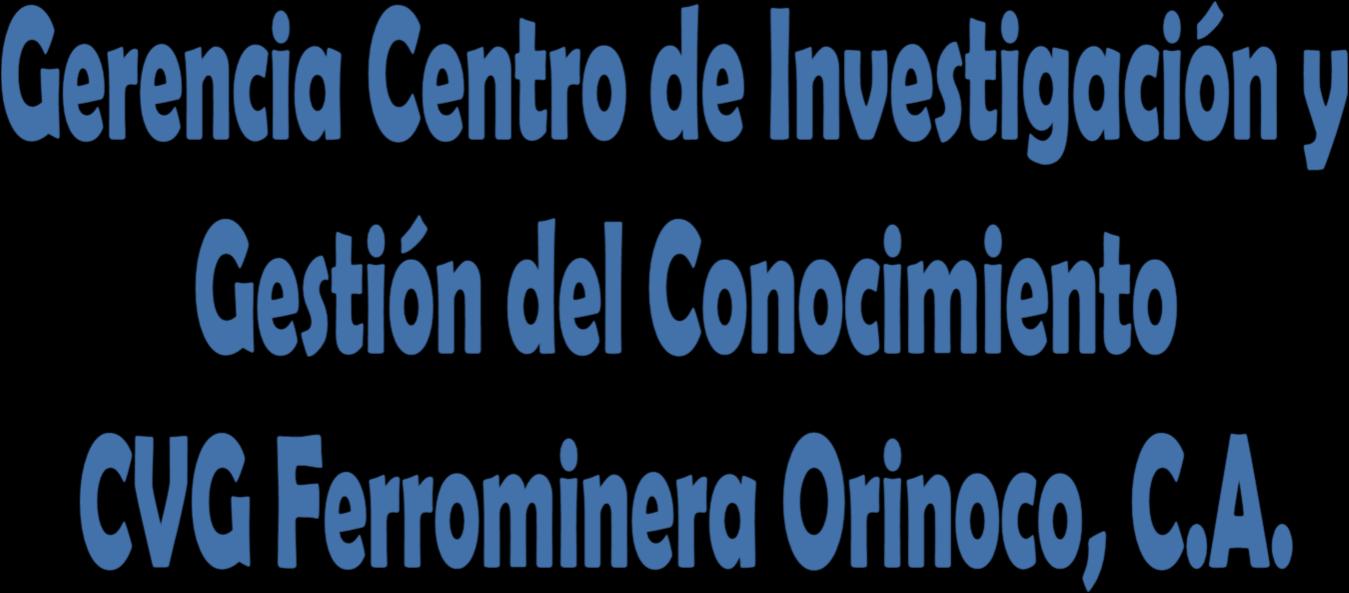
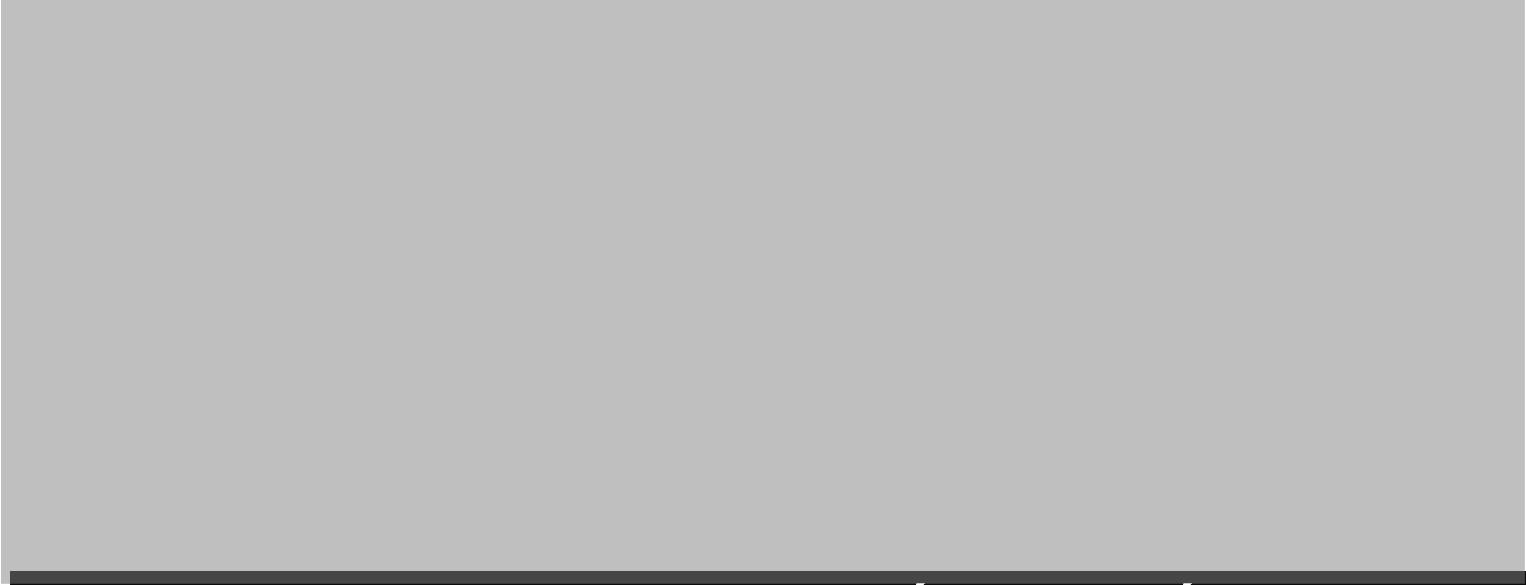
E n e s t a s e c c i ó n presentamos las noticias mas resaltantes a nivel mundial relacionadas con la Ciencia, Tecnología e Innovación en el sector Ferrosiderúrgico.