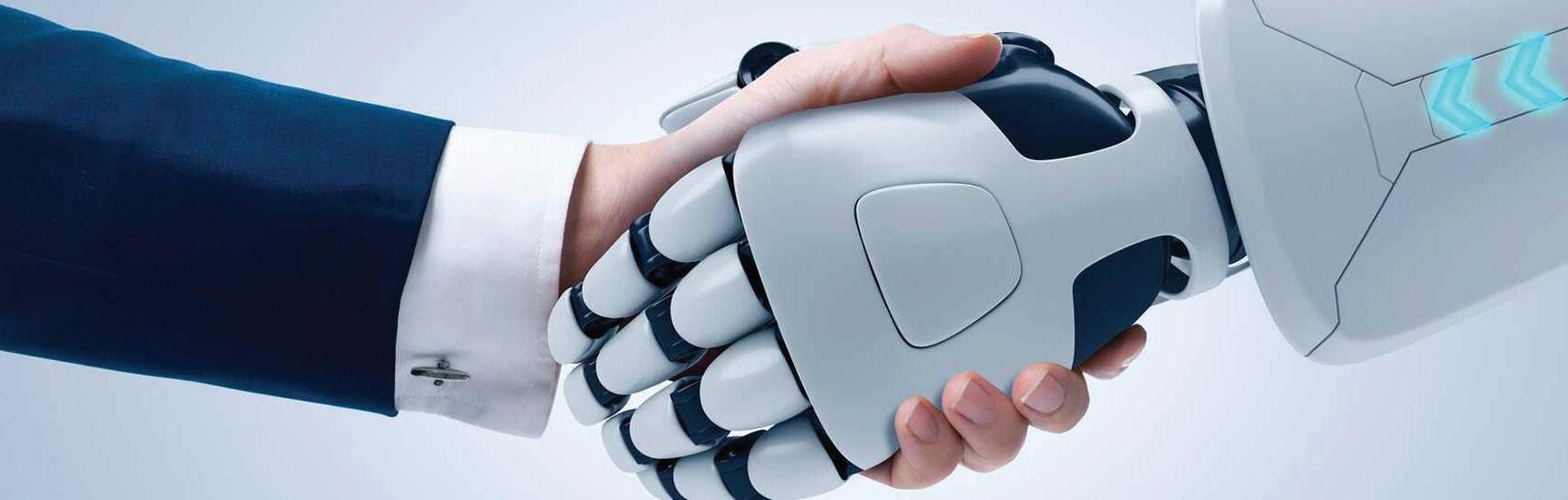
5 minute read
Man and Machine: Personal observations on the Implications for Mining’s Future of Work
- F Cawood; C Jean
The Changing World of Work
Advertisement
With the increasing use of technology in the workplace, it has become clear that “man and machine” must learn to work as a team. Although this has been anticipated for a long time, Covid 19 accelerated the ‘Future’ to become ‘Now’, causing a lack of transition, with no opportunity to test workplace dynamics and the human elements. This is especially true for Africa. In addition, many organisations have experienced a knee-jerk reaction, with a mindset of ‘we have to do this, the rest of the sector is doing it’. The catapulting of tomorrow to today is having a major impact on employee wellbeing –mostly because of the fear that ‘I am not prepared for this world of work’. This is because machines today ‘demand’ centre stage as the driver of change.
Today’s technology development must balance this and also look at what is happening around the machine. We see it everywhere with people literally living on their phones, unaware of their physical environment. The risks and hazards are selfevident. However, when dynamics intensify in a productive environment in transition, the possibility for damage and injury increases exponentially. This explains collisions and accidents between machines and humans in different settings.
Digitization has mostly been imposed and not co-developed with all stakeholders. This means that the transfer of specific skills for people and machines to work together has been a matter of survival of the fittest, thus whoever can learn and adapt the quickest can keep their job and be promoted. This is because the emphasis has been on the machine, rather than on the vocational path of the operator or the integrity of people and machines working together beneficially.
Implications for Mining and Mineworkers
When it comes to mining, it is evident that there are many more impacts than we realised at first. Technology adoption and digitization has hit the mining industry as a kind of sound bomb: it explodes internally and then sends off sound waves that work through an entire system, sometimes slowly, sometimes quickly depending on proximity and access.
The question can be asked:
When did we first observe the problems regarding this? The answer for most industries, is that we either didn’t or we were slow to realise what is actually happening. We were sold a premise that technology is an answer to safety and productivity problems and a coherent solution to mine longevity. This premise was easy to sell to management because big tech and digital evolution brought autonomous machinery and artificial intelligence for optimal production. However, at lower levels, where education and access to sophisticated technology is not as seamless, the threat to livelihood is real.
When mines adopt new technology, there is force causing a segmented reaction, depending on where a person is in their career path and how technology-rich the existing work environment is. It is also role-dependent, resulting in different responses to the integration of technology. At the lower levels, workers are hearing from their friends about what has happened in other mines. This unchecked hearsay is building up fear in the mind of the worker before the change comes. In the mind of the worker, the machine has replaced the person and the person has nowhere else to go. change in a traditionally collective environment of “I take care of you, you take care of me,” the important social fabric that is required for a safety culture to thrive is quickly undermined.
Regarding the central health and safety imperative, there is a behavioural theory that the breaking down of natural human communication also contributes to accidents. In addition, the human takes the backseat when new technology is brought in because the machine ‘speaks for itself’ when it comes to productivity. Power then shifts to the controller of the device; we no longer see each other (in the truest sense of the word); our world becomes a virtual one that is too digital (or game-like) to appreciate real hazards. With this
Let us compare this scenario to the past: The operator did not have devices. We used our voice, flags, canaries and skills in an integrated system. This required continued awareness and interaction because there was nothing else to rely on. Arguably, we had superior communication from human to human taking place. In contrast, the controller of the device vs. the operator has now become the driver and leader of workplace activity.
We do not have another pair of eyes watching our backs; a device has replaced our eyes and so we do not look to ‘see’. The emphasis is now on the digital, inanimate platforms and not the physical capabilities of the person. This is often where the conflict takes place.
At the level of the bluecollar operator, who leans more to manual labour, the threat to workplace value is real and significant. At a professional level, the connection with the realities of the physical environment is limited. Workers in these roles generally embrace the benefits of software that can do automated calculations, planning, projections etc. Consequently, the bluecollar mineworker is going to be far less adaptable. As a worker, the message is ‘my skills are no longer valued, although I might have been very good at what I am doing’. The worker may even be the top performer, but with the new machine arriving, he or she is forced to adapt.
This change is affecting everything - future career, children’s future, pay and life. It is easy to see why “man and machine walking together” is not the ideal picture for our workers at the mining face.
Recommendation and Conclusion
The rapid adoption of digital technology has certainly made life better, more convenient, and more efficient. It has also led to a shrinking of jobs and resentment. However, human beings and technology can work together if our differences and similarities are recognized and considered in the design process. Technology and digitization is not going anywhere. It is one of our inventions – so we must fix things.
The machine does not have a family to feed or a soul to develop. A person does. The person does not have the ability to continue working without affirmation and community. The machine does. Fixing means a human-centric design that considers a safe space for all, and the ability to cultivate and produce value over profit.
Man and machine walking together then may not be such a far-off dream.
Technology is not a winlose situation – it is a win-win situation if one adapts. It requires change management through adult learning to create capacity for strategic change and doing the right work, right.
Who we are:
We are experienced in bring policy, strategy and adult learning together in a manner that reduces risk and adds value to stakeholders.
Charlotte is a learning and development practitioner with diverse management consulting experience, while Fred has worked in academia and industry, with governments and international bodies as a professional advisor in the interest of responsible mining.
Both have a keen interest in making Africa ‘better’ through specialised adult learning and development. We believe that responsible mining is the foundation on which Africa’s future dependsand development starts with the development of Africa’s people.
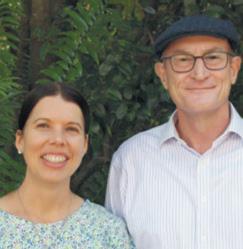
WE ARE LOOKING FOR RESELLERS!
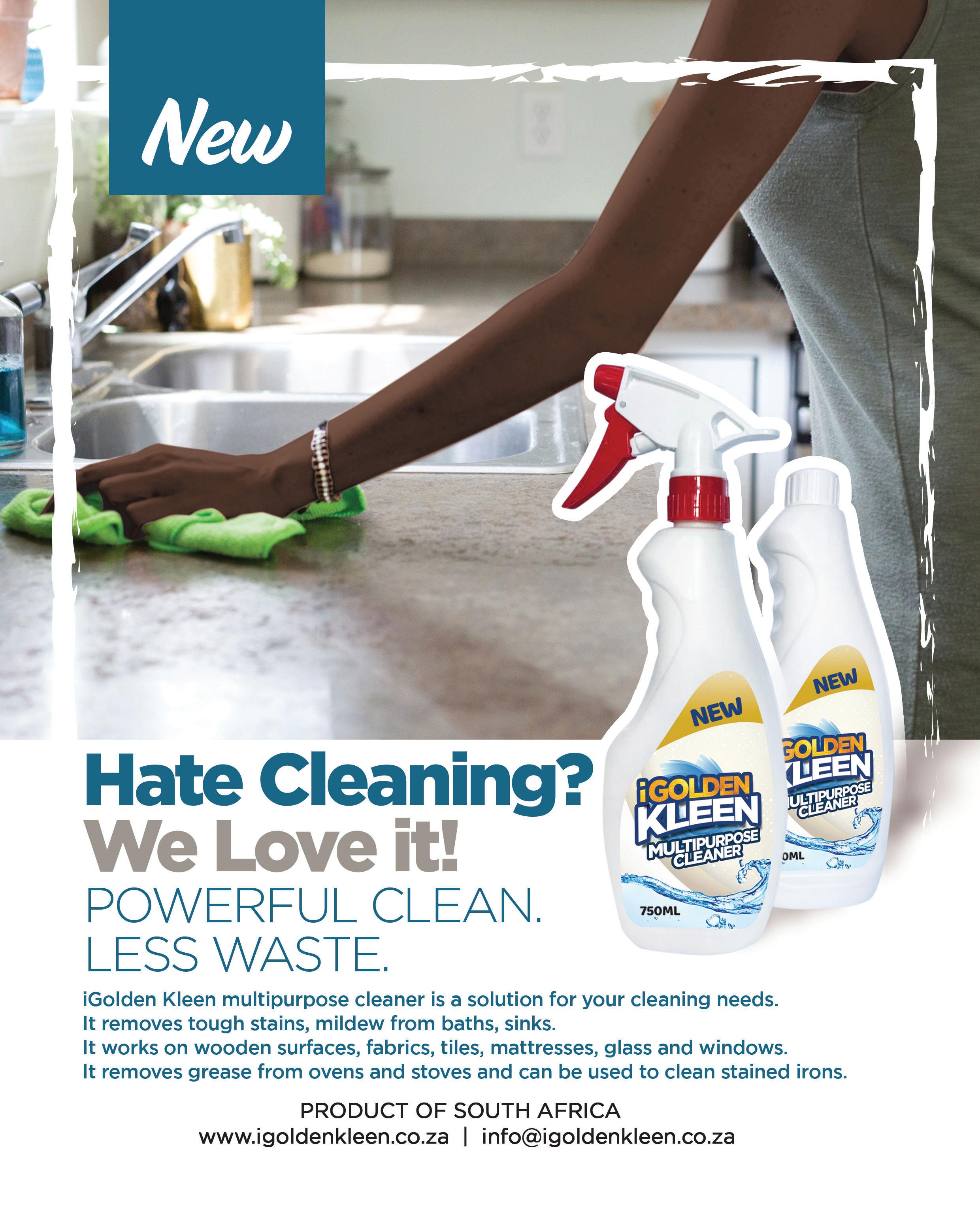