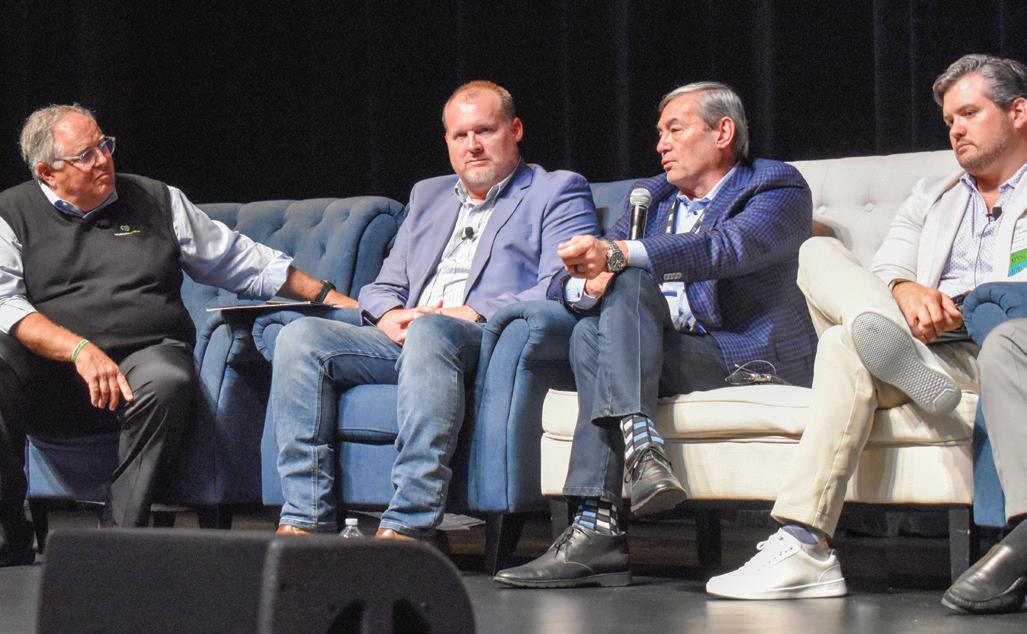
2 minute read
Builders Detail Industry Challenges During Biloxi Expo
HHigh demand for affordable homes nationwide coupled with labor challenges and supply chain disruptions have created longer-than-desired backlogs. However, builders continue to produce homes at an increasing rate, and find ways to simplify the process for buyers. Representatives from nine manufactured home builders met onstage at the IP Resort Spa in Biloxi,
Miss., in late March. It was the introductory discussion at The Biloxi Manufactured Housing Expo and addressed many of the industry’s primary concerns. Clayton Operations Manager Rick Boyd said even with added facilities and beefed up workforces, its homebuilding sites remain at capacity. “We’re up 364 hours across all of our plants,” Boyd said. Adding capacity, automating, and simplifying the construction process have all paid off in recent years to achieve that level of productivity.
However, a shortage of home insulation, for instance, can quickly eat up gains in daily production. “But nobody is going to build a new OSB plant, no one is going to build a new insulation plant,” Boyd said. “Those are $1 billion investments.”
Brent Cappaert of Cappaert Manufactured Housing said the industry hasn’t seen this level of need, and elongated wait times, since the 1970s. In other words, home building continues to pick up, but demand for new affordable homes is outpacing the market.
“You can’t mill what you don’t have,” Cappaert said. “I had to shut down a couple of weeks ago because I couldn’t get windows in. I pretty much have my labor situation worked out, so for us it’s all supply chain.”
Builders offer fewer floorplans as one road toward efficiency.
“We’re going to build what we’re good at, and we’re going to do it over and over again, and do a lot less of drawing on napkins,” Franklin Homes Sales Manager Blake Jackson said.
“The supply chain has been a nightmare and there are still challenges to come, but business is strong when you look at orders,” he said.
The panel members agreed labor, though recovering from the pandemic, will continue to be a challenge. Good labor is hard to find and harder to keep.
“We’re focusing on meeting our challenges,” Cavco Vice President of Sales Eric Coulter said. “Even if we built every home possible, we couldn’t transport them, we couldn’t get them set.”
Panel moderator Chris Nicely, president of ManufacturedHomes.com, asked how the manufactured housing industry could make itself a more alluring destination for trade labor, and workers in general. The panel talked about working with trade schools, tech schools, and providing younger students a sneak peek at industry opportunities, building better partnerships with local organizations.
“If 30% of high school students are going to college, what are the other 70% doing?” Kyle Bennett of Kabco Builders asked.
Nicely asked what it would take get the industry over the hump of 10% homestarts.
“If you had the ability to produce homes for single family rental, that would help get our product up to 15% or whatever the goal is,” Bennett said. MHV
Chris Nicely, left, of ManufacturedHomes.com, moderates a session in Biloxi with representatives from the nation's top factory home builders.