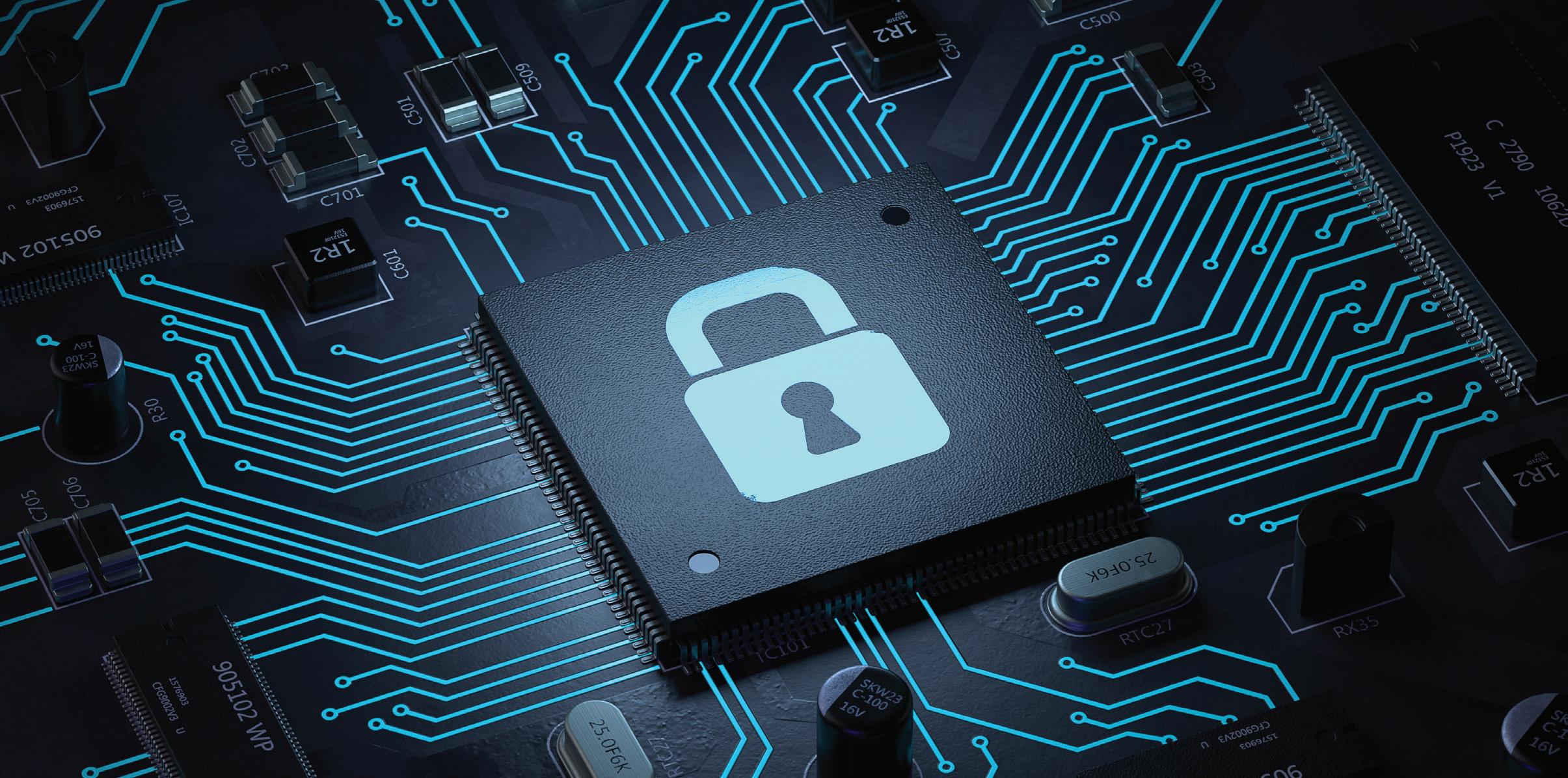
7 minute read
ULTRASOC AND CANIS LABS PARTNER TO SECURE THE CAN BUS
UltraSoC and Canis Labs partner to secure the CAN bus
by CANIS AUTOMOTIVE LABS Hardware-based detection and mitigation of “the When combined with UltraSoC’s semiconductor IP number one cybersecurity vulnerability in the for detection and mitigation of cyber threats, CANautomotive industry” HG allows designers to secure their CAN bus designs yield hardware-based intrusion detection and at the hardware level. The cybersecurity capabilities CAMBRIDGE, UK – 27 May 2020 UltraSoC and Canis enabled by the collaboration employ fast bits within Automotive Labs today announced a partnership the CAN-HG augmented part of a CAN frame to add that addresses one of the most serious cybersecurity security information to CAN frames. This can be used vulnerabilities in the automotive industry: the lack by UltraSoC’s protocol-aware monitoring hardware of security features within the CAN bus, which is to identify and block suspicious or unauthorized commonly used to interconnect in-vehicle systems traffic traveling over CAN. These new capabilities such as brakes, steering, engine, airbags, door locks, will be refined and proved for deployment as part and headlights. of Secure-CAV: an ambitious project that seeks The partnership between the two companies will connected and autonomous vehicles (CAVs). to improve the safety and security of tomorrow’s mitigation techniques for common exploits on Aileen Ryan, UltraSoC CSO, commented: “Automotive the CAN bus. These include automatic hardware cybersecurity requires an ecosystem approach. anti-spoofing; defence against bit-level attacks We’re delighted to add Canis Labs to our list of such as the Bus-Off attack and bit-glitching; and partners working in this area, which already resistance to denial of service (DoS) style attacks. The includes NSITEXE-DENSO and Agile Analog; as collaboration centers on the deployment of Canis well as our partners in the Secure-CAV project, Labs’ CAN-HG technology, a new fully-compatible Copper Horse and the Universities of Coventry and augmentation of the standard CAN bus protocol that Southampton. Up to now the industry has been includes bus guardian security features, and has the forced to use sticking plaster solutions to defend added benefit of being able to carry payloads twelve CAN interconnect, relying on software techniques times larger than standard CAN frames. or perimeter security. Incorporating Canis Labs’
innovative CAN-HG technology into UltraSoC’s products allows us to secure the vehicle ‘from the inside out’: within the underlying electronic hardware.”
Ken Tindell, Canis Labs’ CTO, added: “The most effective way to protect a CAN bus from attacks is to deploy a hardware security device – or better still, use semiconductor IP to incorporate hardware protections into the underlying system. We believe that the combination of UltraSoC and Canis Labs IP provides a robust solution to CAN security, which is one of the most pressing problems for any CAN bus user – whether they are in automotive, aerospace, or any other industry sector.”
CAN is a hugely successful interconnect protocol which emerged in the 1980s in response to the need for an efficient, lightweight interconnection method that could cope with the harsh environments found in vehicles. Today it remains a common choice not only in the automotive industry but also in industrial, cyberphysical and robotics applications, where safety is paramount. But while it is physically robust, CAN is almost entirely lacking in cybersecurity features.
Most existing approaches to CAN security are software-based, meaning that they are often unable to react quickly enough to prevent protocol-level attacks. Because it is hardware based, a joint Canis Labs / UltraSoC solution can react quickly enough to prevent an attack from completing. This has two implications. First, many exploits rely on creating a “window of opportunity” during which the system is in a vulnerable or unknown state. A fast reaction time can eliminate this window and significantly improve the overall robustness of cybersecurity defenses. Second, CAN bus is used in many cyberphysical systems, in which elapsed time equates to distance traveled. A faster response time therefore has significant benefits in terms of mitigating the physical consequences of an attempted intrusion, better protecting the safety of citizens and infrastructure.
About UltraSoC UltraSoC is a pioneering developer of analytics and monitoring technology at the heart of the
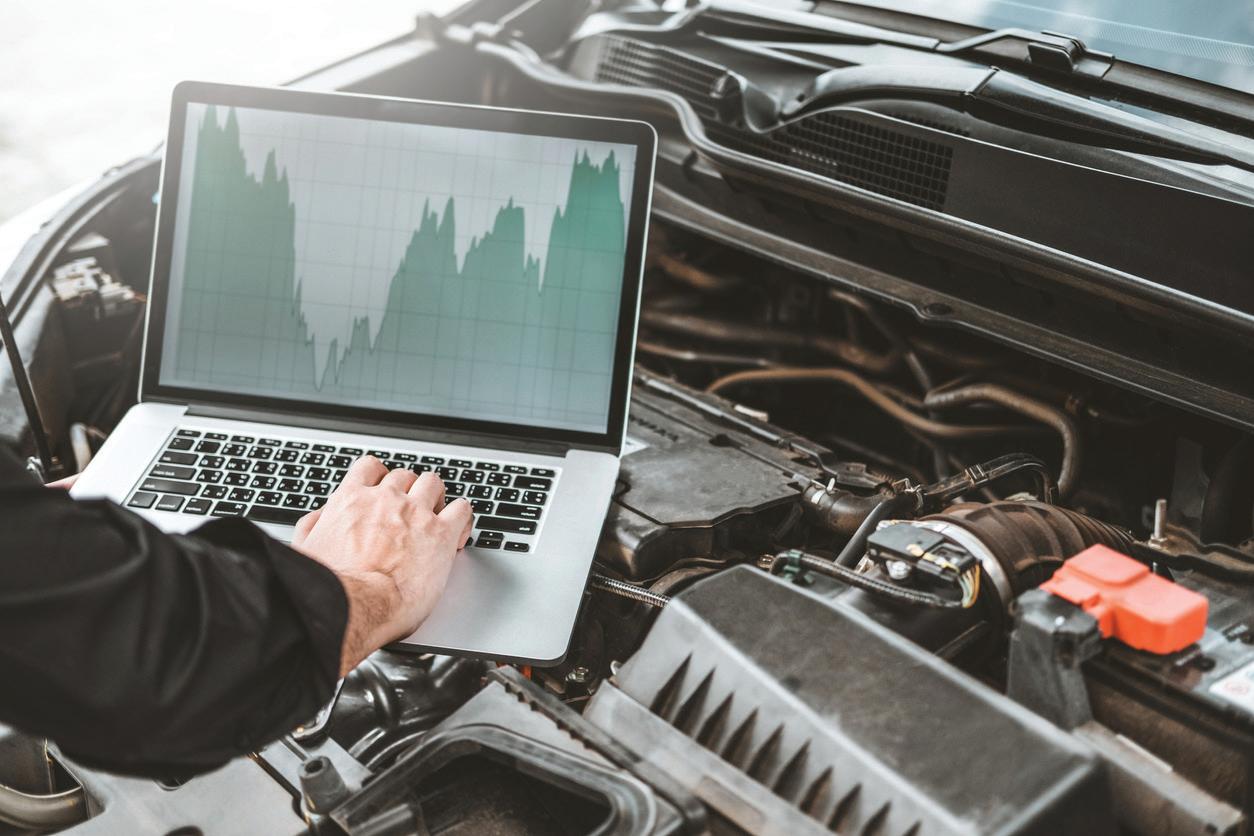
systems-on-chip (SoCs) that power today’s electronic products. The company’s embedded analytics technology allows product designers to add advanced cybersecurity, functional safety and performance tuning features; and it helps resolve critical issues such as increasing system complexity and ever-decreasing time-to-market. UltraSoC’s technology is delivered as semiconductor IP and software to customers in the consumer electronics, computing and communications industries. For more information visit www.ultrasoc.com.
About Canis Automotive Labs Canis Automotive Labs is a creator of hardware IP for the automotive industry, focused primarily on augmenting CAN bus. The company was founded in 2016 by automotive veterans Antal Rajnak, CEO and instigator of the LIN protocol, and Dr. Ken Tindell, CTO and creator of Deadline Monotonic Analysis for CAN bus. For more information visit www.canislabs. com.
Contacts Andy Gothard andy.gothard@ultrasoc.com +44 7768 082 044
David Marsden david.marsden@ultrasoc.com +44 7968 407 739 Twitter: @ultrasoc
Canis Labs contact Ken Tindell ken.tindell@canislabs.com
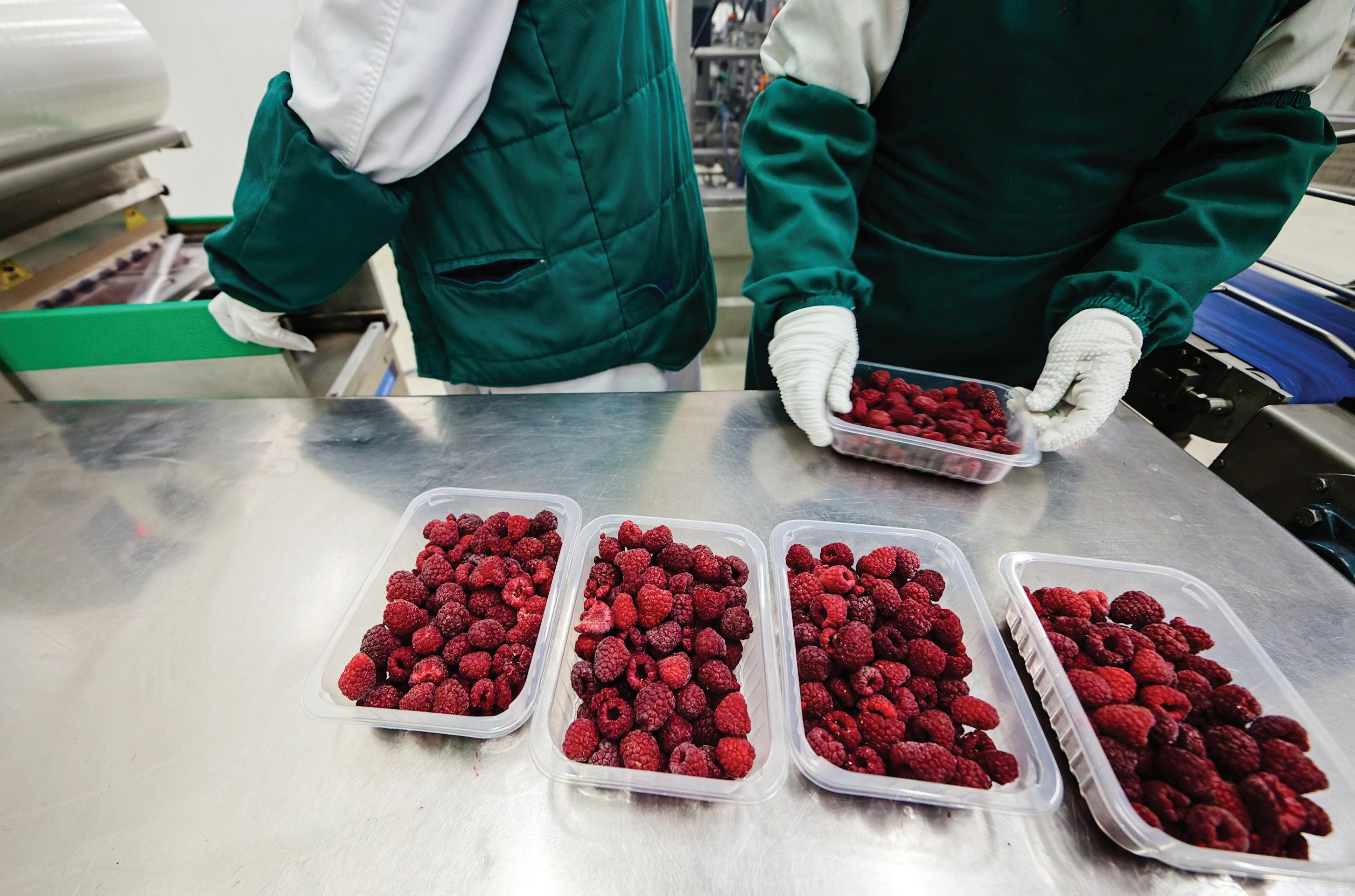
MATERIAL HANDLING: A MISNOMER
by TR CUTLER Hands free, touchless, and material flow are the themes of manufacturing and distribution both now during the height of COVID-19 and forever thereafter.
The efficacy and urgency for automation has changed. Solutions which empower material flow, throughput, and productivity have been popular for the past decade. That said, pre-pandemic, the seminal question was an ROI (return on investment) calculation.
Now material HANDLING is anachronistic; new linguistics are needed to describe the value proposition of products which support the back-to-work safely paradigm for many generations to come.
Until COVID-19 few Americans knew the acronym PPE (Personal Protection Equipment.) Now that vernacular is repeated thousands of times a month. Ultimately material movement includes any process that involves the movement between vehicles, conveyors, storerooms, and other forms of logistics support where employees are involved to some extent. The extent of employee involvement will vary by operation and may include manual, automated, and semi-automated material handling events. The safety required to reopen manufacturing operations means the amount and frequency of manual contact must be significantly reduced if not eliminated.
Before COVID-19, the foundation for a safe workplace started with policies and procedures as a requirement of EHS (Environmental Health and Safety) or OHS (Occupation Health and Safety) senior management team
member. Comprehensive health and safety policies include the appropriate level of guidelines on material movement and the associated employee training programs.
That requirement, as seen recently in meat packing plants, has reached a stage 4 metastasis. People are dying in plants, and without a flair for dramatics, material HANDING must be called material flow or material movement.
A key portion of the policy would be the safety compliance activity that is essential for the business to operate. As new OSHA requirements are updated, there is a need to effectively communication these new policies informing the entire workplace team about the shared responsibilities of each employee in keeping the workplace safe.
Material management encompasses the entire company where employee safety risks frequently encountered in distribution centers, warehouses, shop floors and loading docks. The mitigation of safety risks starts with proper training in awareness, procedures, and safety equipment.
Before COVID-19, safety training was mandated for all employees involved with lifting, carrying, loading, or transporting materials in any form. In addition to new hire training, the safety risks and potential safety compliance rules required re-certification on an annual or other regular time cycle.
Since COVID-19, daily safety training, new protocol processes, and mitigation strategies are the norm.
Before COVID-19, the day-to-day procedures of materials management were to ensure an accident-free or injury-free workplace. Safety procedures were monitored to ensure they were consistently followed.
Since COVID-19, the fast-changing frequently modified procedures start with awareness of the specific risks involved and the proper safety equipment for the situation. Procedures would cover the types of material, and the conditions of the work area including social distancing, PPE, and temperature checks.
Author Profile: Thomas R. Cutler is the President and CEO of Fort Lauderdale, Floridabased, TR Cutler, Inc., celebrating its 21st year. Cutler is the founder of the Manufacturing Media Consortium including more than 8000 journalists, editors, and economists writing about trends in manufacturing, industry, material handling, and process improvement. Cutler authors more than 1000 feature articles annually regarding the manufacturing sector. More than 4200 industry leaders follow Cutler on Twitter daily at @ThomasRCutler. Contact Cutler at trcutler@trcutlerinc.com.
The Manufacturing & Business Podcast Network
MFGTALKRADIO.COM
OUR PODCASTS:
LISTEN TO OUR PODCASTS AT:
www.jacketmediaco.com