Core
THE FUTURE STARTS HERE
MARCH/APRIL
Vol. 105 Issue 1223
Vol. 105 Issue 1226
MAN Engines: New workboat enigne
Thrusters: A novel combination

Future
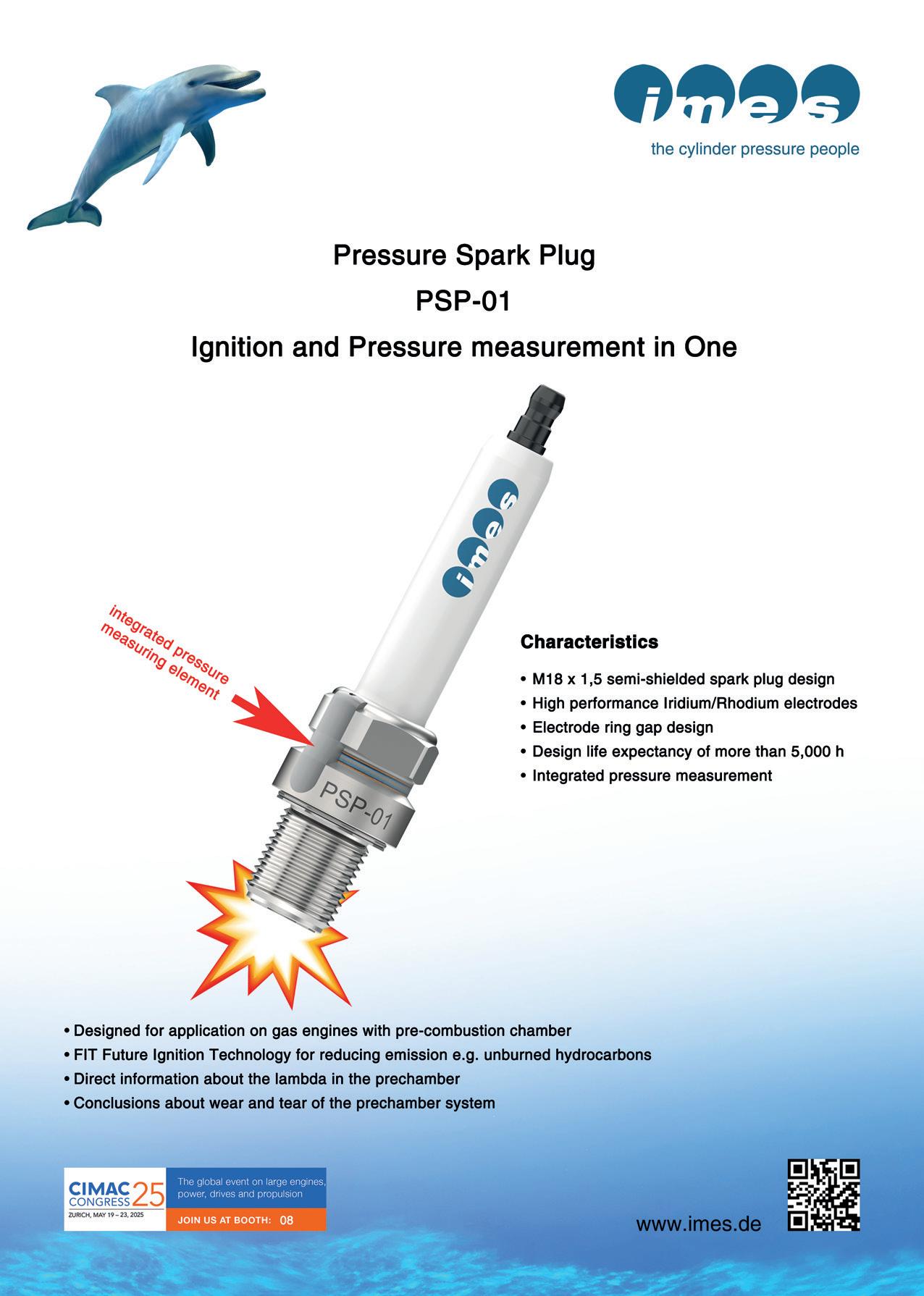
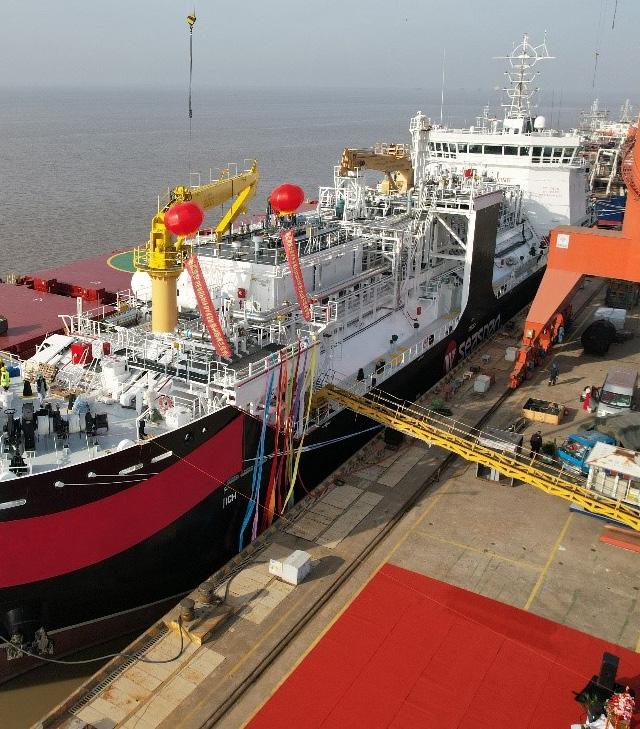
14
GTT Q1 LNG orders
GTT has announced multiple LNG orders in the first quarter of 2025, reinforcing the fuel’s position as a key player in the maritime industry.
37 GNV leverages machine learning for vessel optimisation
Its newest vessel GNV Polaris (see page 32 for more on this vessel) is testing RINA’s SERTICA Performance system to enhance vessel optimisation.
37 WinGD X-DF-A test
WinGD has confirmed the key performance parameters of its X-DF-A ammonia-fuelled engine design after full-load testing.
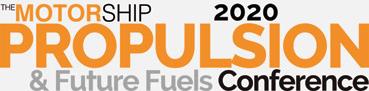
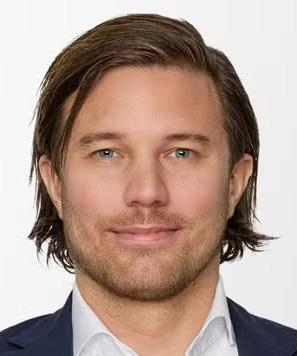
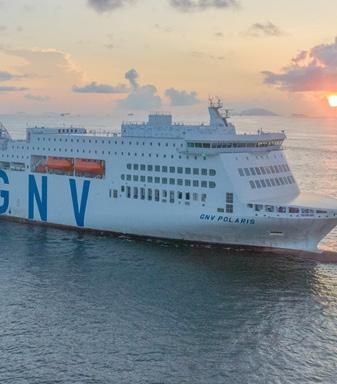
11
Leader Briefing
Cavotec, a provider of electrification and automation solutions, has appointed three new members to its Group Management team.
32
Ship Description
The GNV Polaris, the latest delivery to European principals is distinguished by its predominantly Chinese origination.
34
Design for Performance
On a par in size and capacity with a European-built vessel, the 324-metre Adora Magic City is China’s cruise ship contender.
38
50 Years Ago
The March 1975 issue of The Motor Ship covered shortages in oil supply leading to speculation about the future of the large oil tanker.

16
China advances ammonia shipping
China leads the world in ship owning and shipbuilding and ammonia is high on its agenda for the future.
20
CORE POWER’s vision for energy
Led by CEO Mikal Bøe, CORE POWER is spearheading a transformative initiative in the shipping industry through its Liberty program, which focuses on floating nuclear reactors.
22 LNG: From pipe-dream to mainstream
When the first Motorship Gas Fuelled Ships conference was held in Hamburg, LNG-fuelled propulsion was seen as a promising novelty, albeit with a limited market.
24
Thrusters and DP critical to WTIV operation
Kongsberg Maritime is supplying power, DP control and thruster technology for a string of wind turbine installation vessels, most recently for the U.S.-built Charybdis.
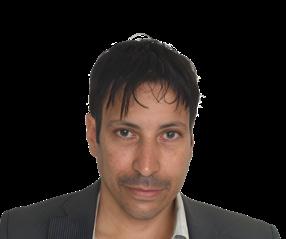
VIEWPOINT
DAVID STEVENSON | Editor dstevenson@motorship.com
China calling GTT’s Q1 LNG orders
With Trump’s inauguration at the end of January, many expected a repeat of the “China baiting” which was a hallmark of his last administration. They weren’t disappointed, and what has become known as the “Trump trade” was seized upon by investors looking to make hay from his pro-business policies.
One policy which was conceived during Biden’s time in office but accelerated with Trump’s arrival is targeting Chinese-made ships. Fines of up to $1.5 million per vessel have been proposed in a bid to boost the US’ domestic shipbuilding industry with, it seems, little regard for what such a punitive measure will mean for consumers of goods arriving on containerships (of which China has an 81% share of the global market). This move has already sparked significant concern from international shipping companies, many of which fear increased costs and potential retaliatory tariffs from China. If enacted, this policy could disrupt global supply chains and force companies to rethink their logistics strategies to mitigate financial impact.
In this issue, we see China’s influence over the shipping industry may be increasing and not limited to the container and bulk carrier segments (which the country has a 75% share of the market according to Veson Nautical). The trend is also evident in ship financing, where Chinese banks have been extending their reach, offering competitive loans to global operators looking to replace aging fleets. On page 34, David Tinsley reports how China is eyeing “Europe’s jewel in the crown,” this is to say the cruise market, arguably the last stronghold for European shipbuilding ambitions. I spoke to one of the famous shipyards mentioned in the article this week and when enquiring about China’s progress in this sector, I was given a polite but decidedly firm “no comment.” Make of that what you will.
Away from forays into previously uncharted waters for the Chinese, on page 32, David Tinsley gives us what should be a familiar account of China’s dominance of the large Ro-Pax market. But GNV’s new vessel Polaris breaks from the standard as hitherto ships in this segment were usually designed in Europe and just put together in China. This ship contains a number of examples of Chinese intellectual property, varying from its interior design to its heat recovery system developed by China Shipbuilding Corporation’s No711 Institute of Shanghai. The engines, despite being produced under license by China’s Shaanxi Diesel Heavy Industry, are reminders of Europe’s shipbuilding prowess, being MAN products. Industry insiders believe this shift towards Chinese design influence is an inevitable outcome of the nation’s investment in research and development, something European yards may struggle to match in the long run.
In the race for a net zero propulsion system, China is also most certainly in the mix. On page 16, Wendy Laursen gives us an update on China’s progress with ammonia, which has seen participation from COSCO Shipping under the guidance of China Classification Society (CCS). We learn that far from being late to the party, China has been studying and researching ammonia for a number of years, as seen with CCS issuing Guidelines for Ships Using Ammonia Fuel in 2022. Additionally, China’s push into alternative fuels extends beyond ammonia, with hydrogen and methanol-powered ship designs also gaining traction. China’s hegemony over global shipping may well extend to future fuels going forward.
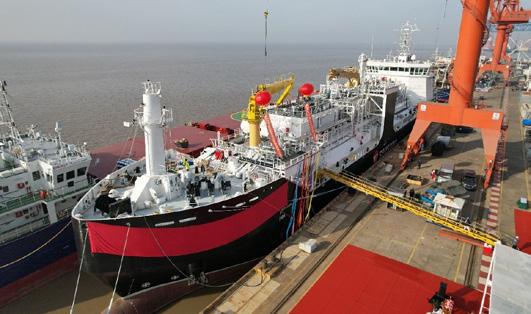
GTT has announced multiple LNG orders in the first quarter of 2025, reinforcing the fuel’s position as a key player in the maritime industry.
The orders involved collaborations with major shipyards across Asia and Europe, highlighting the increasing demand for advanced LNG containment systems.
An Asian shipyard has placed an order for the tank design of two new Liquefied Natural Gas Carriers (LNGCs) on behalf of an Asian ship-owner. Each vessel will have a total capacity of 174,000 m³ and will be equipped with a membrane containment system from the NO96 series, developed by GTT. The deliveries of these vessels are planned for the second and third quarters of 2027.
GTT has also secured an order from its Korean partner, HD Hyundai Heavy Industries, to design cryogenic fuel tanks for 12 new LNG-fuelled container vessels for a European shipowner. Each vessel will be fitted with LNG tanks offering a capacity of 12,750 m³, incorporating the Mark III Flex membrane containment system. These tanks will feature the “1 barg” design, allowing an effective operating pressure of up to 1 barg instead of the conventional 0.7 barg. This design will support compliance with future port regulations requiring vessels to be electrically connected to the quayside. Deliveries are scheduled between the second quarter of 2027 and the fourth quarter of 2028.
Additionally, Samsung Heavy Industries has commissioned GTT for the tank design of a new LNG carrier. This vessel will have a total
capacity of 180,000 m³ and will be equipped with GTT’s Mark III Flex membrane containment system. Another significant order comes from the Chinese shipyard Hudong-Zhonghua, which has contracted GTT to design tanks for six very large LNG carriers. These vessels will each have a total capacity of 271,000 m³ and will be fitted with GTT’s NO96 Super+ membrane containment system. Deliveries are scheduled across multiple years, including the second quarter of 2028, the second and third quarters of 2029, and the first and third quarters of 2031.
These orders underscore the ongoing trust between GTT and its shipbuilding partners, driven by a shared commitment to LNG as a strategic lever in maritime decarbonisation. The use of LNG as a fuel supports compliance with stringent emissions regulations, significantly reducing nitrogen oxides, sulphur oxides, CO₂, and fine particulates.
Philippe Berterottière, chairman and CEO of GTT, commented: “GTT is proud to place its innovation at the service of its customers and to support them in the energy transition of maritime transport. The Mark III Flex containment system and the ‘1 barg’ concept, which is being applied here for the second time, offer concrete solutions for optimising LNG propulsion and anticipating regulatory changes. These new orders demonstrate our partners’ confidence in our expertise and their commitment to more sustainable shipping.”
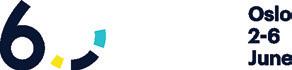


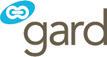
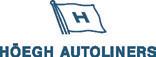

ZURICH, MAY 19 – 23, 2025
31st CIMAC WORLD CONGRESS
The Global event on large engines, power, drives and propulsion
The 31st CIMAC World Congress, taking place from May 19-23, 2025, in Zurich, Switzerland is a unique opportunity for stakeholders to keep up to date with the latest developments in the industry and to discuss technological challenges and solutions with other specialists and fellow colleagues.
220 presentations, approx. 20 Pecha Kuchas, some 60 posters, and ca. 50 exhibitors, along with keynote speakers such as Prof. Lynn Loo, CEO of the Global Centre for Maritime Decarbonisation (GCMD), and more await you.
Book now under cimaccongress.com and secure your place!

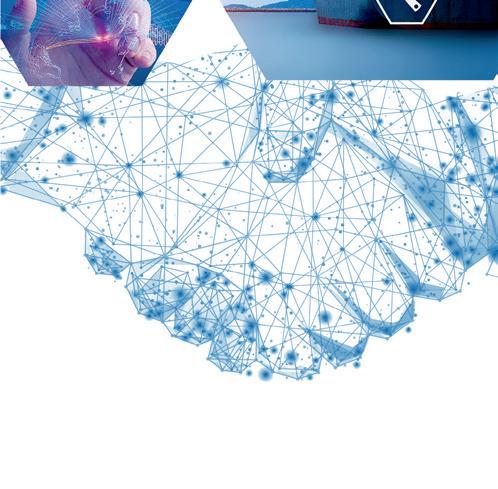
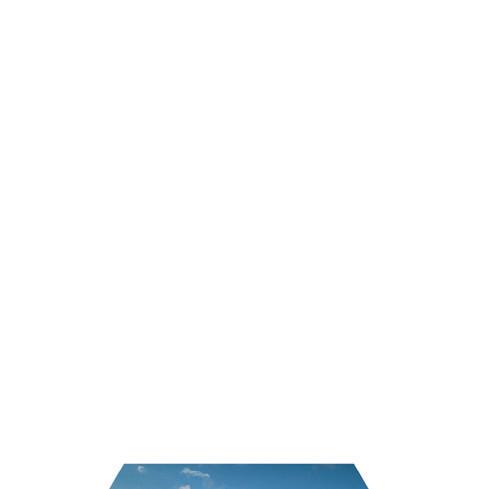
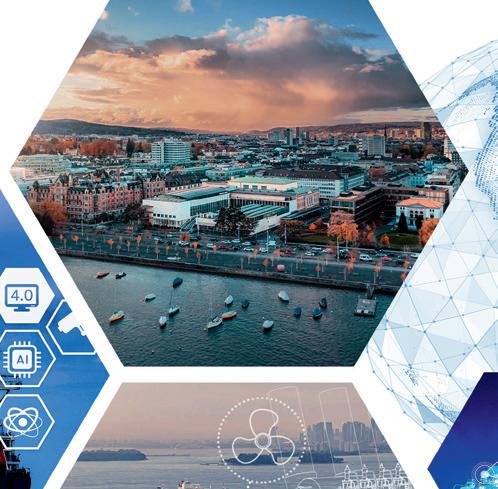





GNV leverages machine learning for vessel optimisation
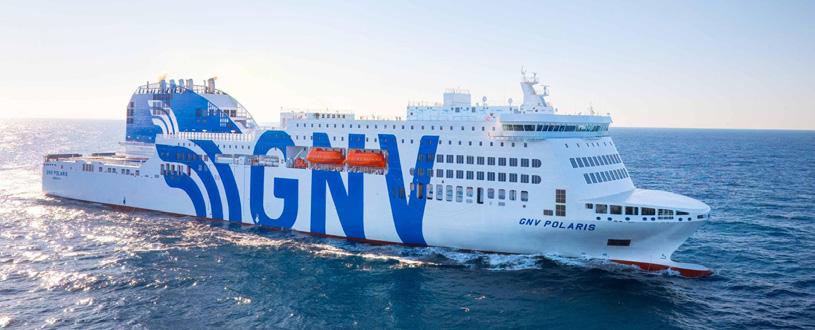
GNV has adopted RINA’s SERTICA Performance system to enhance vessel optimisation and energy efficiency, using machine learning and predictive modelling to improve vessel performance and reduce fuel consumption.
The newest ship in its fleet, the GNV Polaris (see page 32 for more on this vessel), is currently testing the advanced vessel monitoring system during its maiden voyage from China to Italy.
“GNV is making significant strides in sustainable shipping with their latest initiatives,” said Ivana Melillo, energy efficiency director at GNV.
“The GNV Polaris boasts high environmental standards and can achieve over 30% fuel savings, significantly reducing CO₂ emissions compared to the current fleet.”
Real-time data
RINA’s SERTICA Performance
DNV AiP for carrier
system collects real-time data to optimise fuel use, ensuring peak vessel performance. It enables GNV to define two optimal operating scenarios, minimising Specific Fuel Consumption (SFC) and serving as a benchmark for future operations.
The vessel monitoring system gathers data through onboard sensors, tracking fuel consumption, generator power and engine efficiency.
During its trial run, multiple operational scenarios are being tested, including alternating diesel and shaft generators, to determine the most fuel-efficient setup.
This approach helps to ensure the accuracy of machine learning for predictive modelling, allowing GNV to optimise energy use on its Genoa-Palermo route.
The system has so far demonstrated exceptional accuracy, serving as a valuable tool to track vessel performance, identify efficiency losses and
Wärtsilä supply ADM
■ The newest ship in GNV’s fleet, the GNV Polaris, is currently testing the advanced vessel monitoring system during its maiden voyage from China to Italy
simulate operational scenarios.
These data-driven insights can guide retrofit decisions, such as hull cleaning or engine maintenance, to sustain long-term efficiency of the vessel.
“The added value of SERTICA Performance lies in its ability to provide unparalleled data monitoring and analysis,” said Lars Riisberg, marine digital solutions executive director at RINA.
“With real-time dashboards and alerts, it enables advanced analytics, ensuring optimal vessel efficiency and fuel management.”
With SERTICA Performance now installed on over 800 ships, GNV said it continues to invest in digital solutions to modernise its fleet, with the aim of cutting emissions and acheiving a greener business model.
Nakilat 8 LNG carriers
WinGD X-DF-A test
WinGD has confirmed the key performance parameters of its X-DF-A ammonia-fuelled engine design after full-load testing.
The results provide crucial assurance as the first users prepare their vessels and auxiliary systems for ammonia fuel.
“Our well-structured development approach has paid off,” said WinGD vice president R&D, Sebastian Hensel.
“After intensive efforts to understand the principles of ammonia injection and combustion, we are the first two-stroke engine designer to demonstrate 100% ammonia operation with 5% pilot fuel consumption and such low emissions.”
Tests at WinGD’s Engine Research and Innovation Centre in Winterthur, Switzerland, confirmed the engine’s thermal efficiency on ammonia matches diesel. Pilot oil also in line with expectations; consumption was just 5% at full load.
Emissions data was promising: ammonia below 10ppm, N₂O under 3ppm, and NOx well below diesel levels. Notably, these low emissions were achieved without an ammonia slip catalyst, proving the engine can run on ammonia without additional after-treatment.
The first engines will be delivered from mid-2025 for ammonia carriers owned by Exmar LPG and bulk carriers operated by CMB.Tech. Nearly 30 orders have already been secured.
BRIEFS
MAN 175D for OSV
DNV has awarded AiP to Shell and Brevik Engineering for a 74,000 cbm LCO₂ carrier, designed for cost-effective CO₂ transport in Asia Pacific CCS projects. The vessel features 15 low-pressure tanks and future onboard CO₂ capture. At 290m long with a 12m draft, it supports growing regional demand for large-scale carbon transport solutions. It features 15 cylindrical tanks to store LCO2 at -50°C and 6-8 barg, with possible future OCCS.
Ports must be able to check the background of all vessels and show bodies such as OFAC that they have the technology to screen ships for suspected sanctions evasion
Wärtsilä will supply replacement engines for ADM Naviera Chaco’s tug pusher vessels, Decatur Lady and Tendota, operating in Paraguay. Each will be fitted with three fuel-flexible Wärtsilä 20 engines, reducing emissions and improving efficiency. The project supports ADM’s goal to cut emissions by 25% by 2035 while enhancing operational reliability and sustainability. The orders for the engines were booked in Q2 and Q4 of 2024.
Nakilat has begun construction on eight new 174,000 cbm LNG carriers at Hanwha Ocean Shipyard, supporting Qatar’s LNG fleet expansion. Fully owned by Nakilat and chartered to QatarEnergy affiliates, the vessels feature advanced technology for efficiency and sustainability. This milestone strengthens Nakilat’s position as a global leader in LNG shipping and maritime services. Last year the company signed a deal for 25 LNG carriers with QatarEnergy.
Poland’s Crist Shipyard has ordered six MAN 12V175D variable speed gensets for the Sea Dragon, an offshore support vessel for DOF. Set for delivery in early 2027, the 110m, ice-classed vessel will operate off Newfoundland. Featuring DP3 and capacity for 164 personnel, it will support drilling, crew changes, field safety, emergency towing, and ice management. It is cleared for operation on biofuels such as FAME and HVO.
SINGAPORE REGIONAL FOCUS
We asked Ansuman Ghosh, director of risk assessment for Singapore and Akshat Arora, senior risk assessor at UK P&I questions about the South-East Asian city state
How are regional decarbonisation efforts, such as Singapore’s push for green shipping corridors, influencing insurance and risk assessment for shipping companies?
Singapore is not only a dynamic market in its own right, but it is playing an active role in contributing to the maritime industry’s wider efforts to achieve its 2050 net-zero targets.
As well as proving to be an innovation hub for clean technology and alternative fuels, it has taken decisive steps in recent years to ensure the development of net-zero pathways. For example, Singapore has established multiple bilateral Green and Digital Shipping Corridors (GDSC) with the ports of Rotterdam, Los Angeles, Long Beach, Tianjin, Japan, Australia, and Shandong. These corridors aim to establish standards and best practices that will support the decarbonisation, digitalisation and growth of the maritime industry. This includes the development of alternative marine fuels such as ammonia, methanol, and hydrogen value chains to safely offer a range of alternative fuel technologies to the maritime industry within the region.
Singapore continues to lead in the development of alternative fuel technology and was an early adopter of LNG as a fuel, with the Maritime and Port Authority of Singapore (MPA) awarding its’ first LNG bunkering licence in 2016. In its efforts to support its Members in their decarbonisation journey, The UK P&I Club has collaborated with the Methane Abatement in Maritime Innovation Initiative (MAMII), part of the Lloyds Register’s SafetyTech Accelerator program. This partnership unites industry leaders, technology innovators, and maritime stakeholders to advance technologies that monitor, measure and mitigate methane emissions in the maritime sector.
With regards to broader alternative fuel initiatives, in 2024, the MPA – in collaboration with Fortescue – conducted the world’s first ammonia-diesel marine trial to support the development of ammonia bunkering within the region. The first simultaneous methanol bunkering and cargo operations (SIMOPS) were conducted at Tuas Port. Singapore also plans to release a Technical Reference for methanol bunkering in 2025 to address safety, competencies, and regulatory frameworks.
Of course, from a safety and risk management perspective, the introduction of alternative fuels into maritime operations – although vital – also poses unique challenges in terms of their evolving risk profiles. Emerging fuel technologies such as methanol and ammonia are distinctly toxic substances, which will require a new approach to crew training to ensure that seafarers are equipped with the knowledge and understanding that will promote the safe handling of new fuels onboard.
There currently exists a significant lack of operational experience for crews in handling alternative fuels, with no formal training programmes in place and a distinct lack of formalised regulatory frameworks that govern the safe handling and use of such alternative fuels. This means that there is a requirement for more operational training and guidelines to be developed to support the safe integration
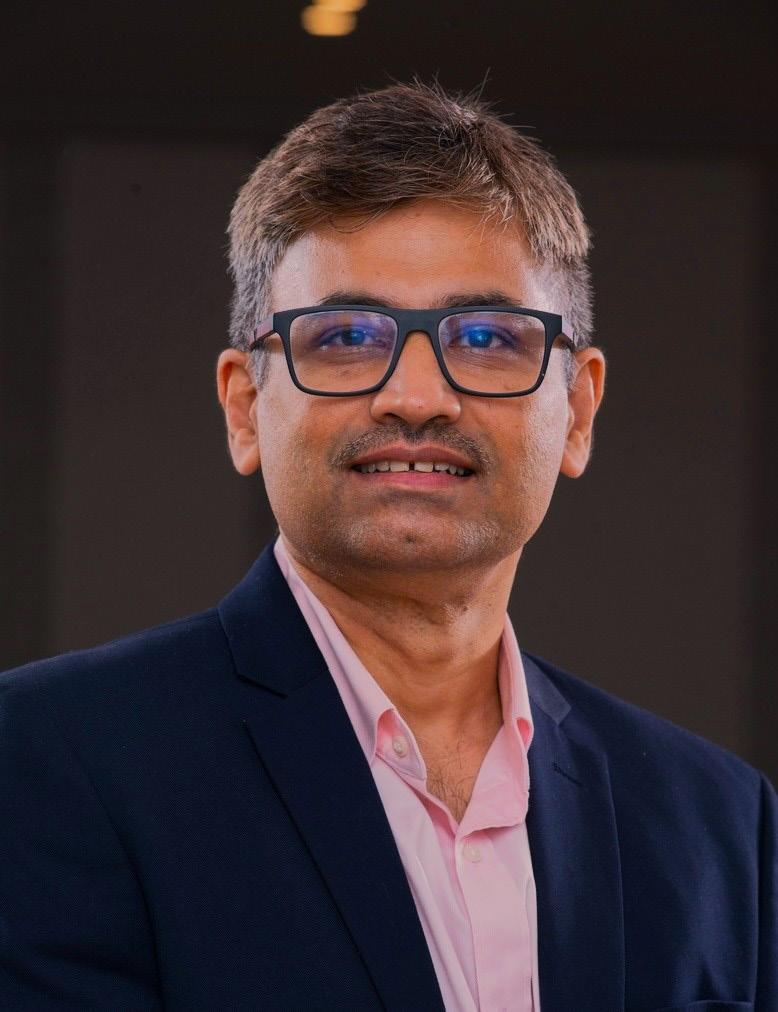
and operational handling of newly introduced fuel technology. The MPA has proactively addressed this competency gap by establishing Singapore’s Maritime Energy Training Facility (METF). This industry-supported facility will provide dedicated training to international seafarers on the safe handling, bunkering and management of incidents involving the use of alternative fuels.
The UK Club is also exploring potential collaborations to provide bespoke training that equips seafarers with knowledge and understanding of the risks associated with using ammonia as a fuel. Additionally, we are considering partnerships to create a learning portal for Club Members focused on alternative fuels, including ammonia. Alongside these initiatives, we are working on a structured 'Risk Focus' to produce guidelines highlighting the additional safety risks associated with using ammonia as a fuel. The objective is to improve the understanding of the risks associated with bunkering, carrying, and using ammonia, with a special focus on crew safety.
With Asia Pacific being home to some of the busiest ports in the world (like Singapore), how do you assess risks related to port congestion and infrastructure adequacy?
Singapore’s port terminal operators – PSAC and JPPL –are acutely aware of the challenges that they face as one of the busiest ports in the world. As a result, they have worked to deploy smart systems and solutions to enhance port operational efficiency to reduce idle or waiting time by vessels and vehicles at the port terminals. The most notable example is the implementation of a “Just-in-Time” (JIT) planning and coordination platform, which matches available berths upon arrival in Singapore to expedite any linked services such as bunkering, or husbandry. The implementation of JIT arrival protocols in Singapore helps to optimise vessel schedules and reduce the likelihood of congestion. Reducing idling time at anchorage also has environmental benefits. Quicker turnaround times means vessel are burning less fuel and therefore reducing emissions.
Singapore’s foresight in developing a smart port like Tuas Mega port highlights its commitment to addressing future capacity demands. However, unforeseen events such as extreme weather, cyber attacks, a global pandemic, or wider geopolitical events represent ongoing challenges and risk for our Members.
As a result, we are taking a proactive approach to assessing the risks associated with a port’s infrastructure adequacy and preparedness in handling these disruptions. For instance, with regards to cyber attacks, the Club is currently working with maritime cyber experts, CyberOwl, to develop an updated version of the “Risk Focus: Cyber” publication, to assist Members in identifying, managing, and mitigating evolving cyber risks.
Vigilance around navigational safety is a key concern for our Members operating in the Singapore Straits, due to the high traffic density. This requires a combination of technical and operational skills as well as behavioural competencies. We are seeing more digital navigation tools come into the market which are making this easier once they are fully integrated but there is still a need for holistic training which includes the human factors. To help support this, we collaborate with leading civil aviation trainers CAE to offer our Members human behaviour and decision-support training.
Expanding the behavioural theme, we also partner with award-winning psychologist, Dr Marcin Nazaruk. His innovative “Learning from Normal Work” methodology challenges traditional approaches to safety and risk management by focusing exclusively on identifying potential hazards, or improving through accident investigation, which helps companies to identify the sources of operational inefficiencies and the causes of accidents, before they happen.
A further risk that our Members face, is the potential for the detention of ships operating or anchoring in undesignated areas, particularly within Singapore’s Outer Port Limits (OPLs). Vessels operating in these areas risk detention by Malaysian or Indonesian authorities if the ship’s location is within their territorial waters. However, through our extensive network of local correspondents, The UK P&I Club is able to provide its Members with up-to-date information on designated anchorages and compliance requirements to avoid costly detentions and operational disruptions.
An additional safety and risk consideration is with regards to armed robbery, which remains prevalent in the Singapore and Malacca Straits. Shipping companies are advised to adopt heightened vigilance and follow Best Management Practises (BMP) protocols to mitigate such risks and the UK P&I Club remains closely engaged with maritime organisations like Singapore Shipping Associations (SSA), the
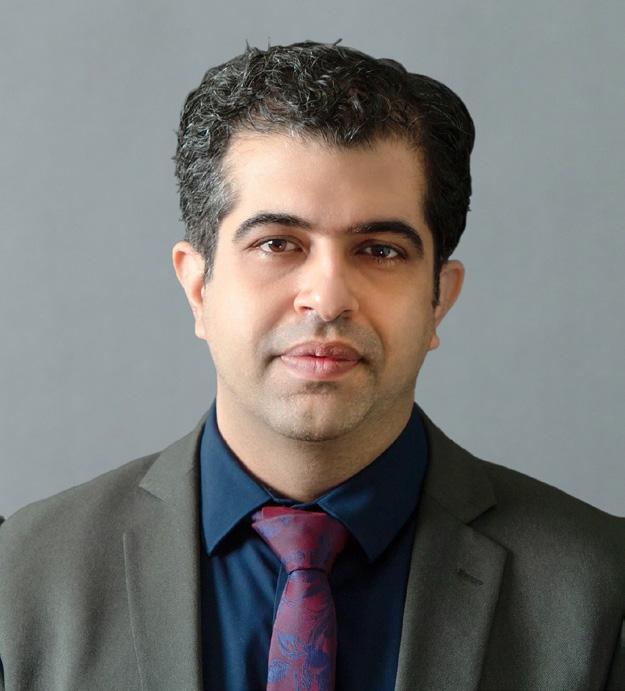
Singapore’s foresight in developing a smart port like Tuas Mega port highlights its commitment to addressing future capacity demands. However, unforeseen events such as extreme weather, cyber attacks, a global pandemic, or wider geopolitical events represent ongoing challenges and risk for our Members
Information Fusion Centre (IFC) and the Regional Cooperation Agreement on Combating Piracy and Armed Robbery against Ships in Asia (ReCAAP), to ensure we are able to offer the best assistance to Members within the region.
This myriad of challenges is an understandable reflection of Singapore’s position as the world’s largest transhipment hub, which is emphasised by its record high annual throughput of more than 40m TEUs in 2024. Against this backdrop, Singapore is an important hive of innovation in areas such as decarbonisation and digitalisation and is continuously setting new standards in port innovation. The UK P&I Club is excited to be part of these developments as we continue to collaborate with progressive companies that are operating in the region. By doing so, we can equip Members with the right support to improve operational safety and manage risk as market dynamics evolve.

Propulsion & Future Fuels is the longest-running technical conference in the ships & marine engineering sector providing senior executives with a meeting place to learn, discuss, and share knowledge of the latest developments in efficient propulsion technology and low flashpoint, low carbon fuels.

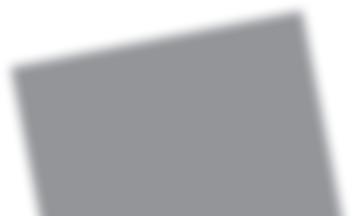


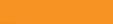


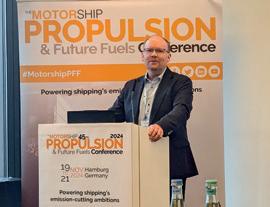
Sponsors:
Media supporters:


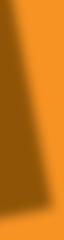
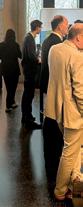

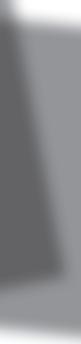
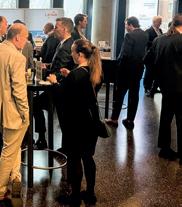
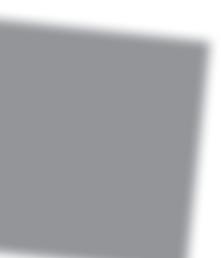
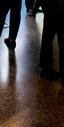
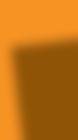
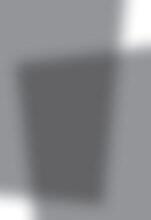

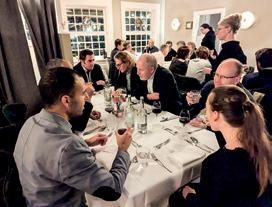
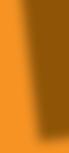
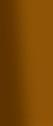

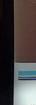
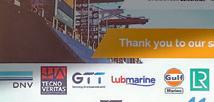
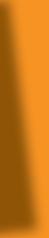
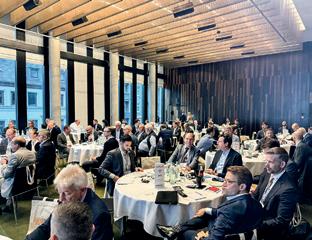


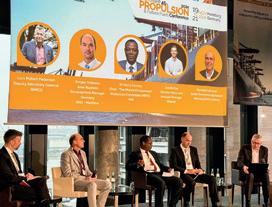
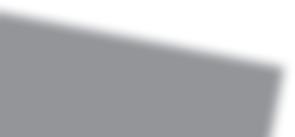
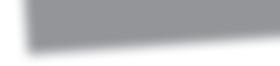

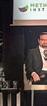


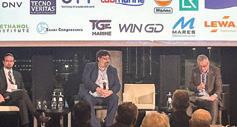
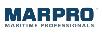
Visit: motorship.com/propulsion-and-future-fuels-conference
Contact: +44 1329 825335
Email: conferences@propulsionconference.com



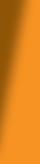

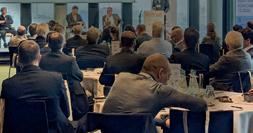
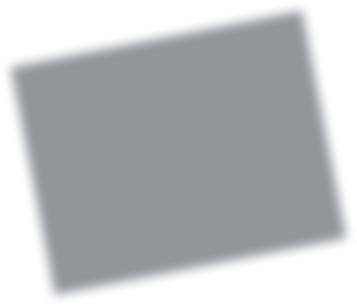
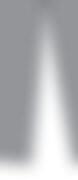

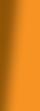
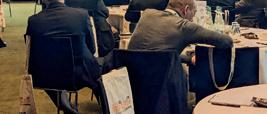

CAVOTEC CHANGES MANAGEMENT TEAM
Cavotec, a provider of electrification and automation solutions, has recently appointed three new members to its Group Management team, reinforcing its commitment to operational excellence, customer focus, and sustained growth
Jonathan Eriksson has been named senior vice president and head of the industry division, while Nicklas Vedin assumes the role of senior vice president and head of the ports & maritime division. Additionally, Patrick Mares, who has been a member of Group Management since 2019, has been appointed senior vice president, product management and Chief Technology Officer.
These appointments are part of Cavotec’s strategy to further strengthen its management structure and drive its ambitious goals of building long-term value and expanding its market presence. According to David Pagels, CEO and President of Cavotec, the new Group Management team brings a wealth of experience, energy, and industry knowledge to the company, helping it to create the right conditions for future growth. “We now have a Group Management team with a strong focus on customers and sales as well as operational excellence. We have a clear goal to build value and this requires high energy levels, experience, and good judgment. With our new Group Management, we have created good conditions to continue growing and creating value,” Pagels said.
Jonathan Eriksson and Nicklas Vedin, both internal promotions, have a deep understanding of Cavotec’s operations and the markets in which the company operates. Their expertise and leadership experience within Cavotec will be key to driving forward the company’s strategic priorities in both the industrial and maritime sectors.
Jonathan Eriksson brings significant experience to his new role as head of the industry division. Having joined Cavotec in 2020, he has held senior positions within the company, including vice president of the industry division, vice president and head of business development, and project director for global operations. One of his notable achievements was establishing Cavotec’s Indian operations, which officially launched in 2024. Prior to joining Cavotec, Eriksson worked as a management consultant at Roland Berger and as a project leader at Atlas Copco Industrial Technique. Born in 1992, he holds a Master of Science (M.Sc.) in Industrial Management and Engineering from the Royal Institute of Technology in Sweden.
Nicklas Vedin has been appointed Head of the Ports & Maritime Division, a role he is well-suited for due to his extensive experience in this sector. Vedin joined Cavotec in 2018 and has held key leadership positions, including vice president of sales in the ports & maritime division and vice president of product management for MoorMaster, Cavotec’s automated mooring system. One of his key accomplishments at Cavotec was expanding the MoorMaster technology to Asia and Latin America, positioning the company as a leader in the growing automated mooring market. Before joining Cavotec, Vedin worked as a management consultant at Ericsson in Sweden and the US. Born in 1991, he holds a Master of Science (M.Sc.) in Industrial Engineering and Management from Linköping University in Sweden.
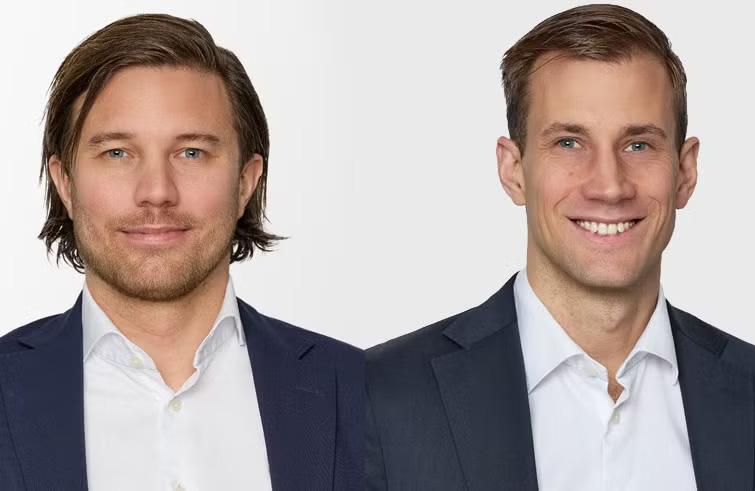
Patrick Mares, who has been part of Cavotec’s Group Management team since 2019, will continue in his new role as senior vice president, product management and Chief Technology Officer. Before joining Cavotec, Mares served in senior positions at several large companies, including as Vice President EMEA at Harsco Rail, vice president of sales & business development at GKN Land Systems, President EMEIA at Ingersoll Rand Security Technologies, and in various leadership roles at General Electric. Born in 1962, Mares holds a Master of Science (M.Sc.) in Engineering from the University of Leuven in Belgium.
Alongside these leadership changes, Cavotec has also appointed Gabriella Sereni as head of marketing and communications. Gabriella, who joined Cavotec in 2022 as group sales enablement manager, brings a wealth of experience in marketing communications and product marketing, having previously worked at Atlas Copco. In her new role, she will play a key part in shaping Cavotec’s brand and communicating its strategic vision to the wider market.
The remainder of the Group Management team remains unchanged. Patrick Baudin continues to lead Cavotec’s service operations, while Jörgen Ohlsson remains head of global operations. Vanessa Tisci continues as Chief Legal & Human Resources Officer, and Joakim Wahlquist remains Chief Financial Officer.
Cavotec is a leading cleantech company that develops connection and electrification solutions, enabling the decarbonisation of ports and industrial applications. Its innovative technologies are critical in supporting the global transition towards a more sustainable future. The company’s new Group Management team is well-positioned to drive forward Cavotec’s strategic objectives, leveraging their extensive expertise to deliver value to customers and stakeholders alike.
Book your place today
Conference speakers include:
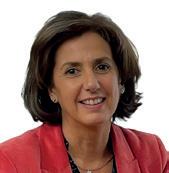
Director General, Spanish Shipowners’ Association (ANAVE) & President, Spanish Shortsea Promotion Center


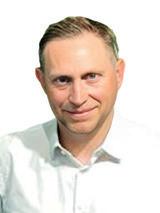
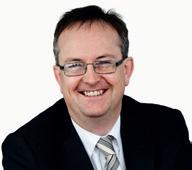
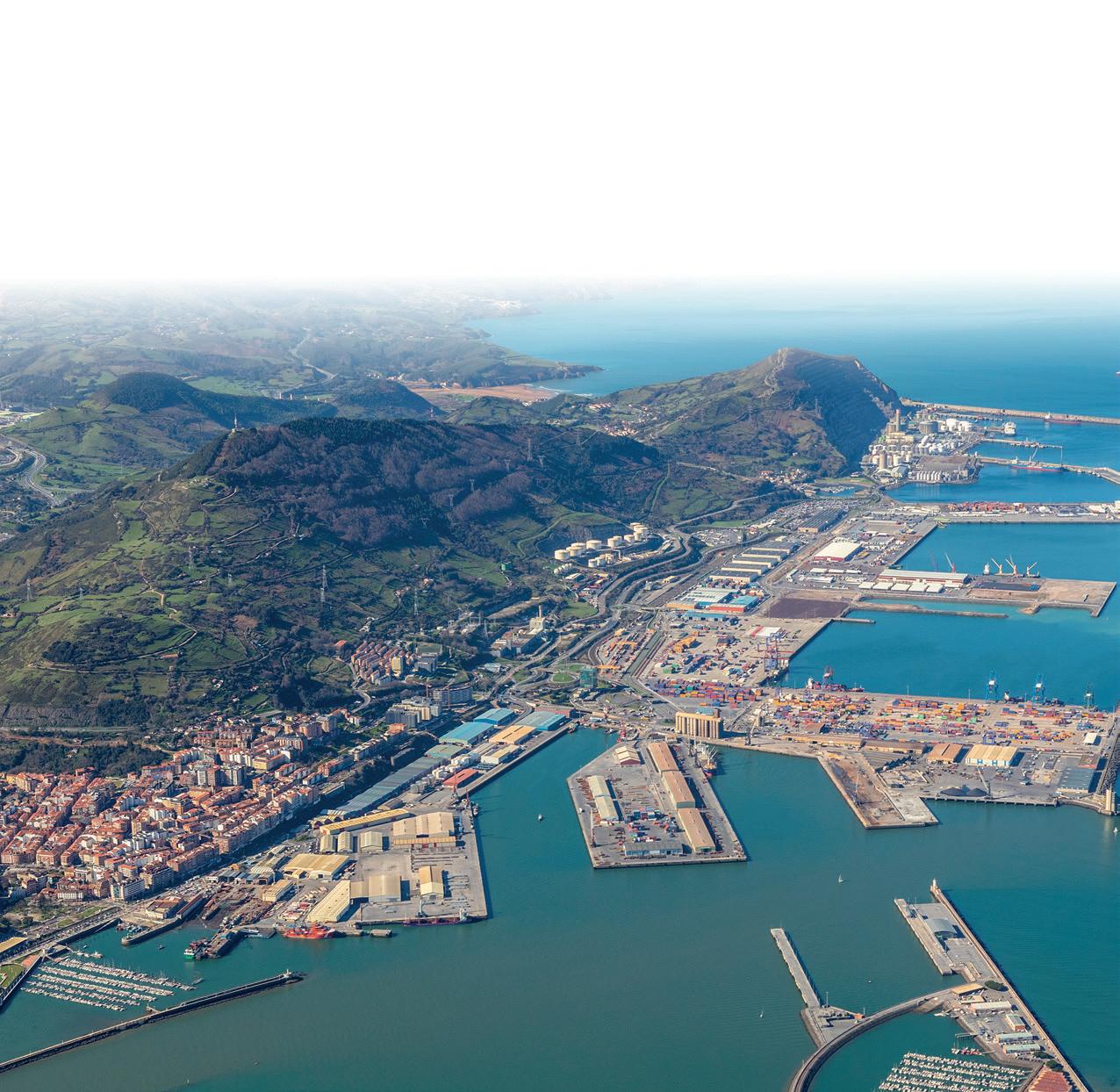
Supporters:
Topics include: Renaissance of Short Sea Shipping OPS Expansion: Increasing the pace to meet demand
Infrastructure development at ports to support short sea shipping
Expansion of green and digital corridors ETS Carbon Levy What do Shippers Want?


Coastlink is a neutral pan-European network dedicated to the promotion of short sea shipping and intermodal transport networks. Learn from and network with international attendees representing shipping lines, ports, logistics companies, terminal operators, cargo handlers, and freight organisations.
For more information on attending, sponsoring or speaking contact the events team: visit: coastlink.co.uk contact: +44 1329 825335 or email: info@coastlink.co.uk

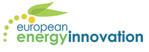




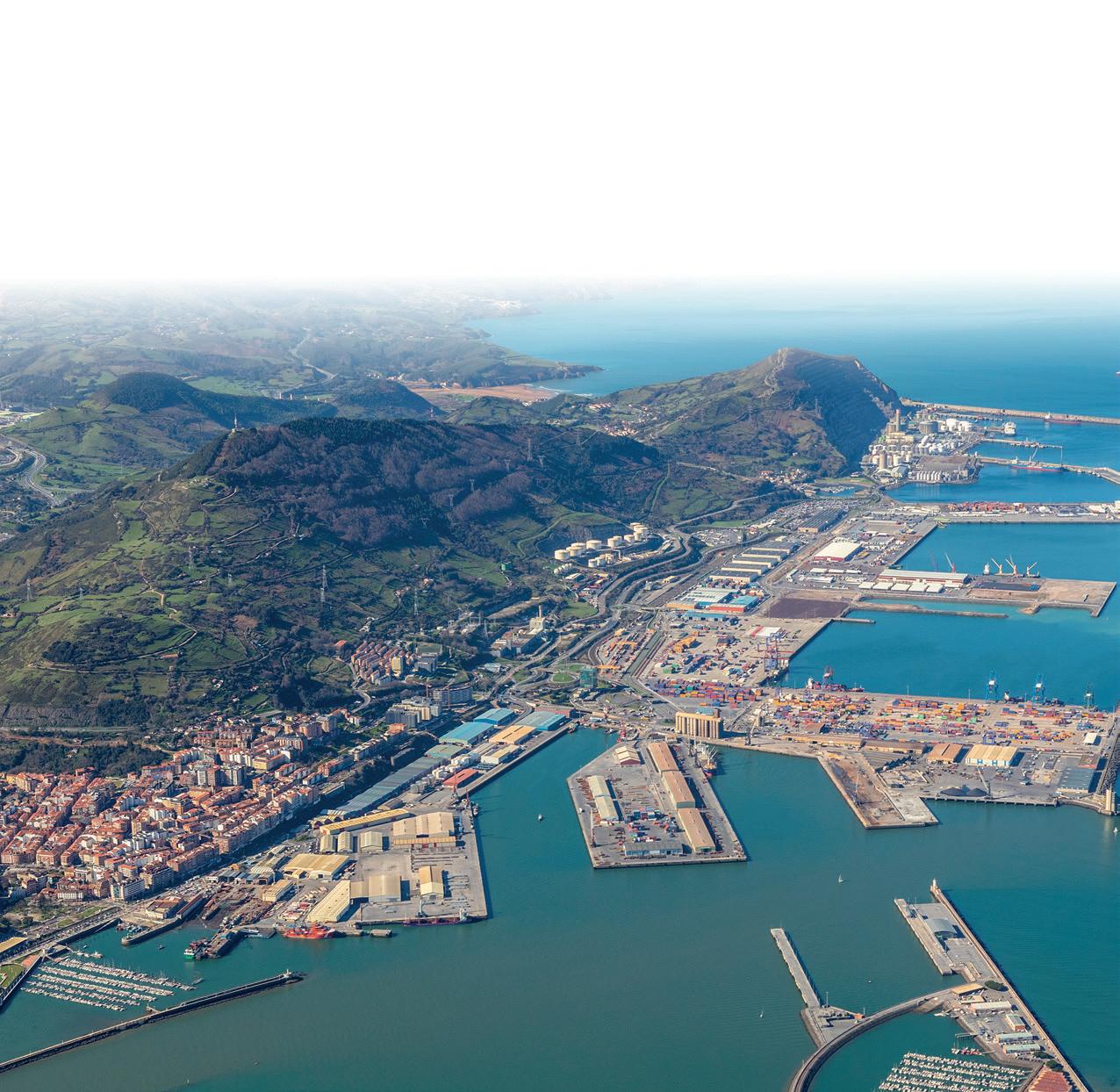
OCEANSCORE’S REGULATORY ANSWERS
The maritime sector is facing increasingly stringent regulations aimed at reducing emissions, with the EU’s FuelEU Maritime and the EU Emissions Trading System (EU ETS) taking centre stage
These regulations are intended to guide shipping companies in transitioning towards greener fuel sources, but they also bring significant challenges for operators who must navigate compliance, fuel choices, and costs. OceanScore, a company providing compliance solutions, is offering innovative ways to help shipping companies meet these challenges and optimise their compliance strategies.
Albrecht Grell, managing director of OceanScore, explains that the company’s approach is distinct in its ability to blend strategic planning with day-to-day operational management. While many companies in the market focus on providing compliance services, OceanScore’s unique proposition lies in its combination of a strategic planner and operational compliance tools.
OceanScore’s most recent offering is the Compliance Manager, a tool designed to handle the intricacies of both FuelEU Maritime and EU ETS in one package. It allows shipping companies to strategically plan their fuel choices, from biofuels to synthetic options, and optimise their operations accordingly. The Compliance Manager goes further by incorporating elements of financial management, ensuring that shipping companies can effectively manage risks, invoicing, and payments related to carbon allowances and fuel-related costs.
Part of this strategy, according to Grell, lies in OceanScore’s FuelEU Planner. This tool helps companies model various scenarios, including the use of biofuels, the costs of carbon credits, and the availability of different fuel types. “It’s a strategy optimiser,” says Grell, “helping companies draft the best approach to comply with FuelEU Maritime regulations and plan for future fuel use in a commercially viable way.” This tool sets OceanScore apart from competitors, as it’s specifically designed to integrate various operational and financial factors into a single planning solution, something other companies offering compliance services may not provide.
Different approach
While companies like Ahti Pool and BetterSea focus on offering fuel pooling services, OceanScore takes a more nuanced approach to pooling, offering it as a free service for clients rather than commercialising the process. Grell is firm in his belief that the pooling business model may not be as prominent as many expect, especially since many shipping companies already engage in pooling arrangements based on long-standing relationships. “Most pools will be internal,” he explains, “and I don’t think it’s necessary to commercialise that service.”
OceanScore's comprehensive approach ensures that clients can manage the complexities of both FuelEU Maritime and EU ETS regulations under one roof, streamlining compliance and reducing the administrative burden. The platform seamlessly integrates data from verifiers, commercial systems, and financial processes, giving operators complete transparency into their compliance status and financial positions.
A crucial aspect of compliance under EU ETS is managing
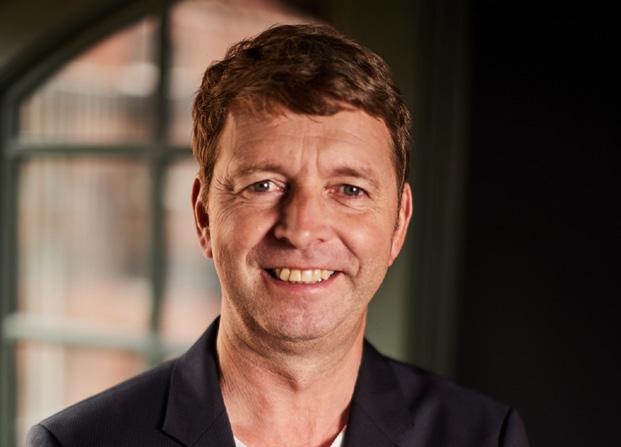
the price risk associated with carbon emissions allowances. Grell highlights the importance of hedging as a way for shipping companies to protect themselves against the volatility in the carbon credit market. By using forward trading and incremental purchases, companies can lock in prices for EUAs (EU Allowances) at an agreed-upon rate, mitigating the risk of price fluctuations as they fulfil their contractual obligations with customers. This kind of risk management is essential when operating in a market where the cost of carbon allowances can fluctuate significantly, impacting both profitability and compliance.
Moreover, Grell emphasises the interdependencies between FuelEU Maritime and EU ETS. While FuelEU focuses on fuel-related decisions, such as the use of biofuels, EU ETS is more concerned with the process of carbon credit trading. The two regulations are intertwined, and shipping companies must consider the impact of one on the other. For instance, switching to biofuels under FuelEU can reduce the EU ETS costs, but it also affects the overall fuel costs due to the calorific value differences of biofuels. As such, OceanScore’s Compliance Manager is designed to optimise both operational and strategic decisions in light of these interdependencies.
The introduction of new fuel types, such as biofuels, into the debate has been contentious. Given the recent protest to the IMO regarding the use of biofuels, many advocate for the reduction of these in maritime operations, especially nonwaste-based biofuels, Grell suggests that the conversation is somewhat academic. He acknowledges the need for sustainability but argues that biofuels, particularly waste-based types, remain a viable short-term solution. “The debate on waste-based versus non-waste-based biofuels is somewhat irrelevant now,” he notes, pointing out that the production process for biofuels has evolved and that waste-based biofuels can be made from previously non-waste sources.
ACCELLERON’S CEO ON CLIMATE
Coming from Switzerland, the International Year of Glacier Preservation and World Water Day’s glacier theme strike a chord with me. I have witnessed the alarming retreat of Swiss glaciers firsthand – a 65% ice loss since 1850, with 10% gone in just 2022-2023
Maritime has a front-row seat to glacial and polar melting, with rising sea levels, surging storms, and threats to coastal infrastructure. If the climate crisis escalates, supply chains and industries worldwide will face disruption.
The point is, this is a climate red flag. And it’s a call to unite like never before. Maritime’s strength has always been partnership, and in the past five years, together we have deployed efficiency technologies, dual fuel engines, and digitalization to curb emissions.
Yet, even with these efforts, progress is too slow, and two more red flags appeared last year. Global emissions should have peaked before 2025; instead, they hit an all-time high in 2024. It was also the first full year of 1.5°C warming.
One year of 1.5° is not a point of no return, but it raises the stakes ahead of 2030 emissions targets. Missing those could make future goals unattainable. On the other hand, meeting shipping’s 20-30% reduction target would prove that we can pull our weight.
A 2023 IMO study confirms we can, if we accelerate two key developments.
First, we have to go viral with fuel efficiency
The technology for maximum efficiency already exists—from speed optimization to hull cleaning, digital tools, and wind propulsion. Just derating engines with optimized turbochargers can save a conservative 3% in fuel and emissions. We have a customer that combined that with a propeller upgrade to save 25%. But in a global fleet averaging 13.1 years (weighted), only 37% of ships have energy saving technology (EST) retrofits.
We need to finish the efficiency job, and it only makes sense. Investing now will future-proof ships, cut fuel costs, and ensure compliance with new carbon regulations, avoiding wasted money on penalties.
Second, and not as easy, we need to solve the carbon-neutral fuel challenge
To meet the 2030 target, the IMO estimates 5-10% of the global fleet must also switch to carbon-neutral fuels. Consensus is growing around green methanol and ammonia, with new ships already designed for them. Theoretically, we could just scale up infrastructure for green hydrogen production and non-fossil carbon capture as feedstock, boosting green methanol and ammonia production and driving deep decarbonization toward net zero. Unfortunately, theory and reality are far apart, and the way forward is blocked by infrastructure and investment challenges.
Green shipping corridors help, by concentrating carbonneutral fuel availability, and in 2024, they grew 40% to 62 initiatives worldwide. Still, the actual fuel is in short supply.
As a result, LNG dual fuel technology now leads in new ship orders, Of course, we have to manage methane slips, but mitigation technologies exist. With no perfect path, a 25% emissions drop from conventional fuel is still progress, and onboard carbon capture (OCC) is gradually emerging which could further reduce CO2 emissions from LNG.
But it will not get us to net zero.

Navigating the fuel challenge requires a cross-industry compass
We are not alone in our infrastructure needs. Shipping accounts for 3% of global emissions, but combined with other hard-to-abate sectors—aviation, steel, cement, and chemicals—the total jumps to 25%. Adding power generation (34% of global emissions) and agriculture (12%) brings the total to over 70%, all reliant on green hydrogen and carbon capture. Some sectors, especially shipping, also depend on increased production of green methanol and ammonia.
Right now, infrastructure is critically lagging, and continuing with a fragmented, sector-specific approach will see green hydrogen demand outstrip supply by at least 900% in 2030, with carbon capture facing a similar gap. As major energy players are now scaling back renewable investments, that gap could well grow.
We must join forces to build critical mass Why not unite to shift the balance in our favor? A crossindustry initiative could consolidate demand and provide
Green shipping corridors help, by concentrating carbon-neutral fuel availability, and in 2024, they grew 40% to 62 initiatives worldwide. Still, the actual fuel is in short supply

market certainty, unlocking the requisite investment: $9 trillion for green hydrogen, $3.5 trillion for carbon capture, five times current methanol production, and a tripling of ammonia production by 2050.
Of course, demand alone will not suffice. With prohibitive costs and long payback periods, making green hydrogen and carbon capture cost-competitive also requires bold national leadership and large-scale incentives—like the ones that drove solar growth in Germany, and made it viable against fossil fuels.
Shipping, a natural starting point for a united fuel front
As stewards of 80-90% of global trade, shipping has a responsibility – and a unique position – to unite sectors,
aggregate demand, and amplify our collective voice with policymakers. When it comes to the climate challenge, we are all in the same ship, sailing the same ocean. Acting together now can turn the carbon-neutral fuel challenge into our greatest opportunity for net zero.
■ Daniel Bischofberger is CEO of Accelleron. With a 100-year heritage of innovation, Accelleron helps the world move further, more efficiently and sustainably through its turbocharging, fuel injection, and digital solutions for heavy-duty applications. The company serves marine and energy customers in more than 100 locations across 50 countries, continuously innovating to drive the energy transition forward and accelerate the decarbonization journey.
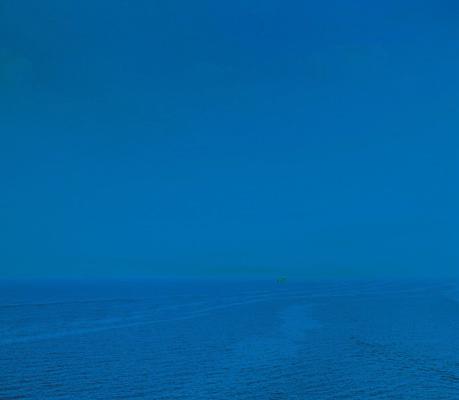
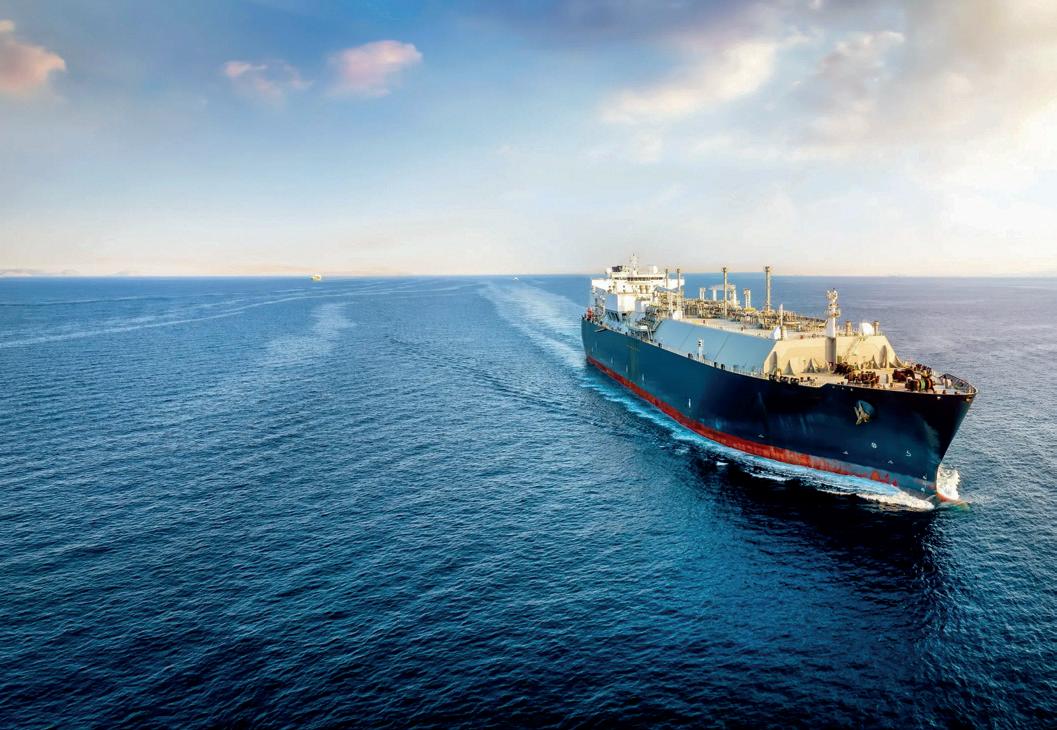
Leading the Future of Marine HVAC Systems
Sail Green, Breathe Clean
– Eco-Friendly HVAC Solutions for a Sustainable Voyage.
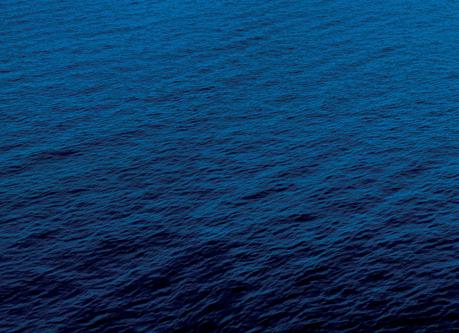
Please contact sales@hiairkorea.co.kr
CHINA ADVANCES AMMONIA FUELLED SHIPPING
China leads the world in ship owning and ship building, and ammonia is high on its agenda for the future

Ammonia was bunkered for the first time in China late last year when Liaoning Suppliers refuelled the tugboat Yuantuo 1. It was one of very few ammonia bunker transfers to date globally, and the operation was conducted at the COSCO SHIPPING Heavy Industry terminal in Dalian thanks in part to guidance from China Classification Society (CCS).
The 5,500HP tugboat was the first ammonia-fuelled ship built in China, and CCS played a major role in the vessel design, including designing the ammonia fuel containment and supply system. The society also conducted research into the catalyst technology used in the vessel’s SCR, among other technical developments.
CCS released its Guidelines for Ships Using Ammonia Fuel in 2022 and continues to research safety and new vessel designs. It’s part of a national push. Also in 2022, China’s National Energy Administration released a "Medium and Long-term Plan for the Development of Hydrogen Energy Industry (2021-2035)" which actively promoted the advance of ammonia-fuelled vessels.
CCS has been involved in the development of a range of ship designs including a 16,000 TEU container ship designed by MARIC, a 3,500 TEU container ship designed by CSSC Huangpu Wenchong Shipbuilding, bunkering vessels by MARIC and DSDC, oil tankers by MARIC and DIMC ORIC and a bulk carrier by SDARI.
In November 2024, CCS granted AiP to China's first medium-speed high-power ammonia fuelled engine developed by CRRC Dalian Company. CCS was first to grant AiP for Wärtsilä’s W25DF ammonia engine. It has also granted AiP for WinGD and Dalian University of Technology engines,
for ammonia fuel valves to PK Valve & Engineering in South Korea, and for an ammonia fuel supply system by COSCO SHIPPING Heavy Industry Technology (Weihai).
In December last year, MSC 109 adopted amendments to the IGC Code to enable the use of ammonia cargo as fuel, and this has paved the way for vessel designs such as the 50,000 cubic meter ammonia carrier jointly developed by COSCO SHIPPING Energy and COSCO SHIPPING Heavy Industry. Primarily designed for ammonia cargo, it also has the capability to carry LPG simultaneously. The ammonia dual-fuel engine system is expected to achieve net-zero carbon emissions.
Price is key
Getting beyond the design stage for ammonia fuelled cargo vessels will require favourable economics, another area of research for CCS. The International Renewable Energy Agency (IRENA) has calculated the current cost of producing green ammonia at $700 to $1,300 per ton. That is expected to decrease to $450-$900 by 2030, a range confirmed by CCS’s own calculations. “After 2035, the economy of ships using green ammonia will begin to be equivalent to that of ships using fuel oil. After 2045, ships using green ammonia will generally be more economical than ships using fuel oil,” says Jin Ding, CCS Wuhan Rules & Research Institute.
Safety risks will need to be mitigated. Lei Wei, CCS Wuhan Rules & Research Institute, says toxicity is the primary risk to be controlled when using ammonia as fuel. This means controlling ammonia leakage and accumulation, preventing ammonia contact, and life-saving measures. Mitigation measures include the use double-walled pipes, avoidance of
threaded joints as much as possible, mechanical ventilation, water spraying, the division of toxic areas and restricted access to high-risk leakage areas.
Ammonia’s corrosive properties rule out the use of materials such as copper, zinc, nickel and their alloys, and plastics, so steel is commonly used as the metal in ammonia storage tanks, pipelines and fittings. For seals, nitrile rubber can be used instead of conventional rubber.
Ammonia has a relatively low risk of explosion as it is not easy to ignite and has a high lower limit of flammable concentration (15%). However, it can exacerbate the consequences of an explosion caused by other fuels or flammable materials, and it reacts with oxidants such as chlorine and bleach to produce explosive compounds.
Ammonia-fuelled vessels should be equipped with at least three sets of safety protection equipment, and each should be able to provide sufficient protection to allow entry into gas-filled areas. This means at least one self-contained positive pressure air respirator (including the entire mask) with a capacity of at least 1,200 litres of free air (without using stored oxygen), airtight protective clothing, boots, gloves, steel core rescue rope with belt and an explosion-proof lamp. Ammonia-fuelled vessels should also have safe shelters that can accommodate all personnel onboard in case of severe ammonia fuel leakage.
There is a certain foundation for the development of the regulations, rules, and standards related to ammonia-fuelled vessels worldwide, and the corresponding rules and standards have taken shape
The ammonia fuel tank and ammonia fuel preparation room should be located in areas where the hull structure is stable and not easily affected by external factors such as collision or grounding. They should be arranged outside of Class A machinery areas. When the ammonia fuel tank is located on deck, a coaming, water spray system, and independent ammonia water release system should be installed to avoid direct discharge of aqueous solutions containing liquid ammonia or dissolved ammonia overboard.
An instantly available water curtain should be installed at the entry to the ammonia fuel preparation room, and it should be able to be activated from outside the room. Gaseous ammonia has good solubility in water, so this measure can be effective in containing a leak.
An ammonia release management system is required to collect any ammonia releases during normal or reasonably foreseeable abnormal situations. This includes ventilation of double shut-off vent valves in ammonia fuel pipelines, release of safety valves in the ammonia fuel system and release of ammonia during pipeline purges.
Due to the toxicity of ammonia fuel, it may be better to adopt enclosed or semi-enclosed design for the ammonia fuel bunkering station, says Niu Song CCS Shanghai Rules & Research Institute. This contrasts with LNG and methanol bunkering stations that are preferably arranged in wellventilated areas such as open decks.
The IMO guidelines stipulate that regardless of whether the bunkering station is in an open area, semi-enclosed area, or enclosed area, a risk assessment must be conducted which considers factors such as the isolation of the bunkering
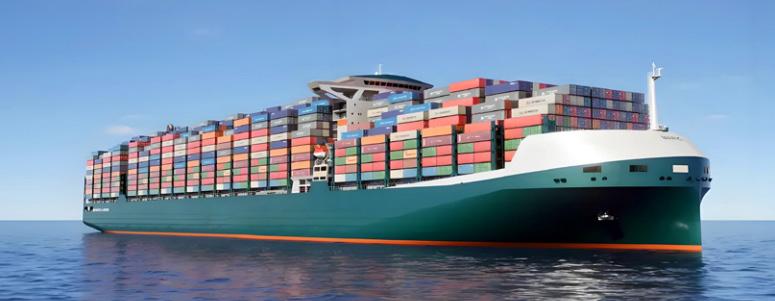
station from other areas of the ship, the division of hazardous and toxic areas, ventilation requirements, leak detection and safe measures. These can include direct monitoring or closed-circuit television monitoring of the bunkering station.
“As a preliminary application of a new system and technology, ammonia-fuelled vessels still lack the experience of onboard application despite their high technological maturity. It is necessary to adopt acceptable and recognized risk analysis techniques to assess the potential risks involved in the design of ammonia-fuelled vessels, in order to eliminate or mitigate their adverse effects on onboard personnel, environment, structural strength, or ship integrity,” says Nui.
On-going service
CCS has established a scientific research and service centre for the establishment of rules and standards, approval of ships and systems, risk analysis and carbon intensity assessments. Despite the advances made, the society sees some challenges ahead. For example, cost, safety, infrastructure, regulatory framework, technological maturity, and market acceptance. These challenges will need to be addressed through global cooperation, technological innovation, policy support, and investment.
“There is a certain foundation for the development of the regulations, rules, and standards related to ammonia-fuelled vessels worldwide, and the corresponding rules and standards have taken shape,” says Ma Dan CCS Wuhan Rules & Research Institute. “However, there are still deficiencies and improvement. In the future, in-depth research needs to be made in the following five aspects: the standards for specifications of marine ammonia fuel; the standards for ammonia fuel bunkering; the standards for testing ammonia fuel power plants (engines, boilers); the standards for design and testing of ammonia fuel supply system; the standards for design and testing of ammonia emission reduction system.”
For bunkering, CCS launched a research project titled "Research on Technical Standards for Ammonia Fuel Bunkering Ships and Operation" in 2024. The aim is to conduct research on technical standards for ammonia bunkering operations and ammonia bunkering ships. The work undertaken has already included development of technical standards for the arrangement of bunkering vessels, bunkering systems, cargo containment systems, related monitoring and safety systems, personnel protection, evacuation, and fire protection systems. "Guidelines for Ships Using Ammonia Fuel" and "Guidelines for Marine Ammonia Fuel Bunkering Operation" are expected to be released around the end of 2025.
Meanwhile, Chinese yards are already attracting orders globally for ammonia-fuelled vessels. Last year, CMB.TECH and Yara Clean Ammonia announced the order of the world’s first ammonia-powered container ship to be built at Qingdao Yangfan Shipbuilding. More recently, on February 19, Norway’s Skarv Shipping announced it had contracted an ammonia-fuelled general cargo vessel from Huanghai Shipbuilding for delivery in 2027.
A SAFE ROUTE TO THE AMMONIA ALTERNATIVE
As orders for ‘ammonia-ready’ ships accumulate, ClassNK’s work to overcome its crew safety challenge will be key role in realizing the fuel’s potential as a contributor to maritime decarbonization
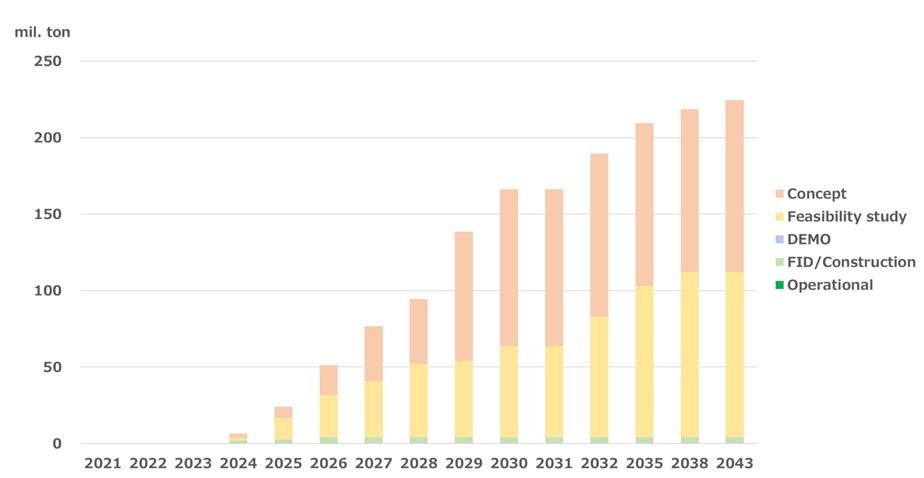
Latest published figures from Clarksons Research indicate that 25 ammonia-fueled ships were ordered during 2024.
Given that 50% of all 2024 ships ordered will burn alternatives to conventional fuels, ammonia’s contribution to a low CO2 emission future, therefore, appears modest, compared to 390 fueled by LNG, 119 by methanol, 72 by LPG (and 12 by hydrogen), and 206 with battery/hybrid propulsion.
However, the figure compares to just four ammonia-fueled ship orders in 2023, according to the same source, while a broader view counts 130 of the ships ordered in 2024 as ammonia ‘ready’. These add to 322 ammonia-ready ships on order at the start of 2024, according to Clarksons.
Numbers such as these suggest a market that is prepared to consider a greater commitment to ammonia as a fuel type at a later date.
Advocates for ammonia point to the fact that it does not emit CO2 when burned. Using renewable energy sources and electrolysis to create ‘green’ ammonia would result in a fuel that would cut GHG emissions through its lifecycle by up to 90% - meeting International Maritime Organization zero-carbon expectations even if translated to a ‘well-to-wake’ assessment.
Advances in ammonia
Research recently published by ClassNK shows that production capacity for green ammonia will reach around 220 million tons by 2043, taking account of all publicly announced projects – including those where the start-up has been most delayed.
If the number appears high (where the IMO estimates global ships of above 5,000GT consume around 215 million tons of fuel oil a year, though ammonia’s energy density
differs from oil), it reflects expectations that ammonia will provide an alternative fuel for coal-fired thermal power plants and will be used as a hydrogen carrier. Furthermore, since most projects are still in the conceptual or feasibility stages, it is unlikely that all will go ahead.
But toxicity, rather than availability, represents the first obstacle to ammonia’s acceptability as a marine fuel. Even in low concentrations. Ammonia has an adverse effect on human health in cases of repeated exposure.
And its uptake will depend on not only advances in design, technology and training that protect seafarers and the environment from ammonia’s risks in theory, but also the changes to maritime law that ensure that any usage upholds necessary and agreed standards in practice.
In December 2024, the IMO’s Maritime Safety Committee moved forward with interim guidelines covering the use of ammonia, and towards an international standard for ships using ammonia as fuel. The new guidelines are an important milestone in developing rules on ship design including the arrangement of fuel tanks, machinery space, piping, and containment, bunkering and fuel supply, as well as control, monitoring, and safety systems.
Work will continue on these guidelines, and on extending the IGF Code covering low-flashpoint fuels to include ammonia in 2025. Meanwhile, changes to the IGC Code will enter into force on 1 July 2026 that allows it as a fuel pathway.
Guidance on risk
Where technical support and the development of formalized ship and equipment design requirements are concerned, ClassNK has been in the vanguard of several projects
contributing to cumulative knowledge on the use of ammonia as a marine fuel.
For the maritime industry to move forward with the practical application of ammonia-fueled ships, it will be essential to incorporate comprehensive risk assessments in ship design. A recently published study offers a further reminder of ClassNK’s energetic work to advance the viability of ammonia as a future mainstream marine fuel. A key component of these assessments involves estimating the probability of ammonia leaks from various onboard components.
Conducted in a collaboration with the Society and Research Institute of Science for Safety and Sustainability (RISS), National Institute of Advanced Industrial Science and Technology (AIST), the study estimates the probabilities of leakages in ship fuel systems using ammonia.
Leakage frequency from piping, storage tanks, and associated equipment will vary depending on the type of gas in the fuel system. Deriving estimates for ammonia leakage is therefore an essential part of the design risk assessment process. The purpose of the study has been to develop a more robust and reliable basis for future risk assessment work on the prevention of leakages, with results also helpful for developing measures to protect crew safety and the surrounding environment.
Given the lack of existing ammonia-fueled ship systems, however, authors faced a practical challenge in estimation work. To overcome it they used the Bayesian method to estimate probabilities of leakage for each component by combining onshore ammonia leakage frequency data from the High Pressure Gas Safety Institute of Japan with leakage frequency data applied to risk assessments for LNG-fueled ships.
The result is the world’s first ammonia leak frequency estimates for onboard components for ammonia-fueled ships (valves, hoses, pipes, flanges, joints, etc. - see Table 1).
The study feeds into the knowledge bank at the disposal of the ClassNK Transition Support Services to support customers on their journey towards zero-emission emissions. In addition, leak frequencies associated with specific components have been included by ClassNK as an appendix to Part C of Guidelines for Ships Using Alternative Fuels (Edition 3.0).
Drawing on real projects to update its Guidelines for Ships Using Ammonia as Fuel, ClassNK is also amassing further food for thought for regulators working on how ammonia can be safely brought into use and take its place in The IGF Code and The IGC Code.
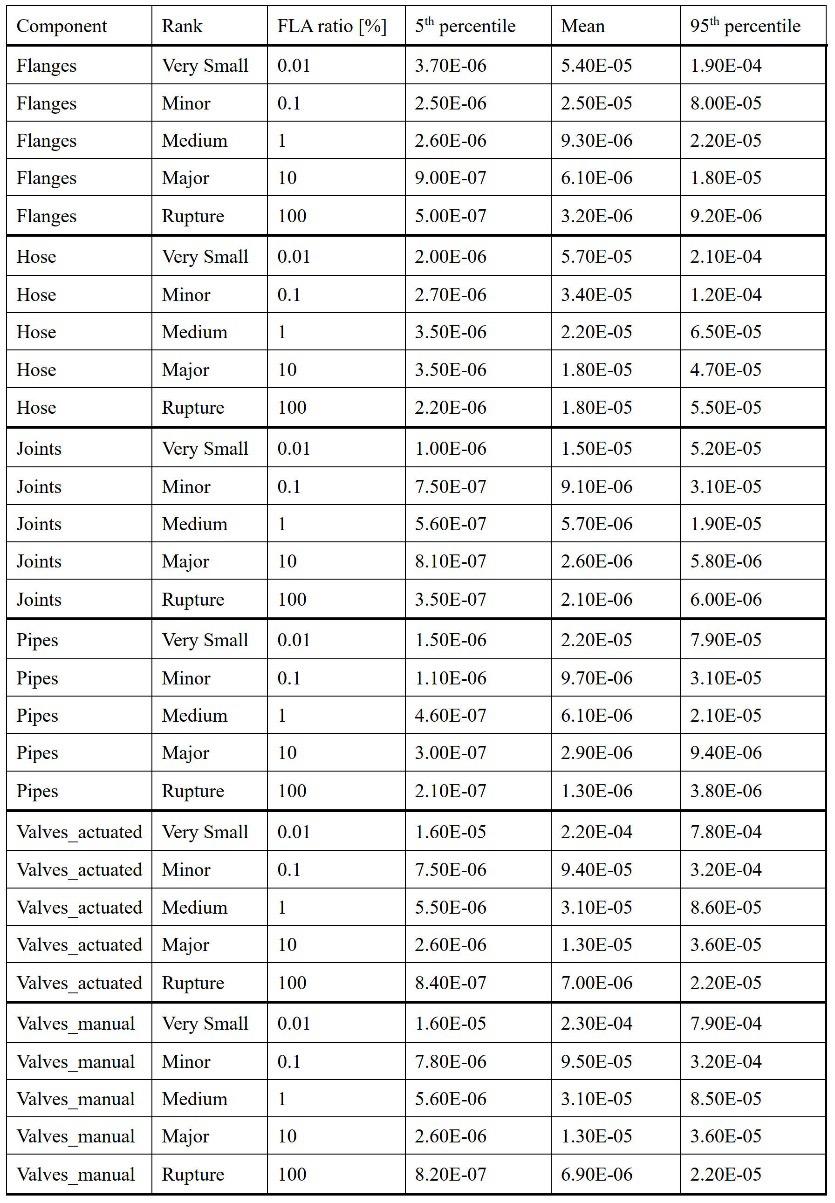
ClassNK’s updated Guidelines independently establish provisions for minimizing risks to ships, seafarers, and the environment, as well as standards for the equipment (including control and monitoring systems).
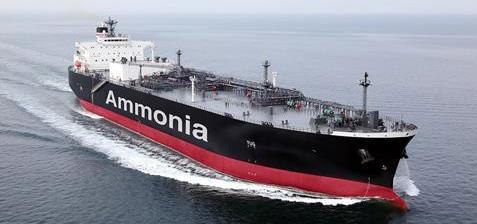
CORE POWER’S VISION FOR ENERGY
CORE POWER, led by CEO Mikal Bøe, is spearheading a transformative initiative in the shipping industry through its Liberty program, which focuses on floating nuclear reactors. These reactors, designed to be modular and cost-effective, are positioned as a viable solution to the pressing need for decarbonisation in maritime
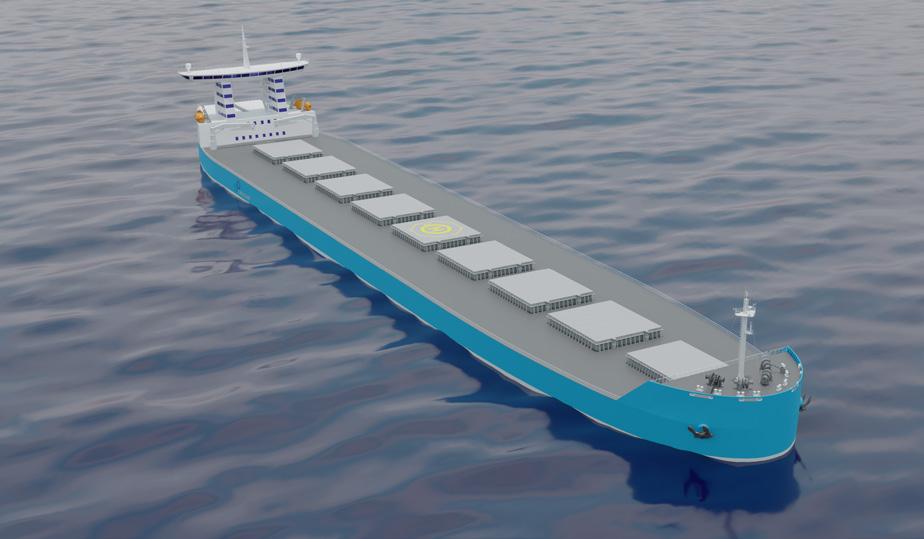
The urgency for change is clear. Thousands of vessels will need replacing by 2040, by which time international shipping will have to be 70% of its way to net zero, the final deadline for which is 2050. With the average ship lifespan being around 25 years, new builds will need to meet stringent emissions regulations, making conventional fuelpowered vessels obsolete.
According to Bøe, alternative fuels such as ammonia and methanol present significant energy inefficiencies and prohibitive costs. Instead, CORE POWER’s floating nuclear technology offers a high-energy-density solution that can ensure long-term sustainability and efficiency for global shipping and beyond.
At the heart of CORE POWER’s innovation is the molten chloride fast reactor (MCFR). Unlike conventional solid-fuel reactors, MCFRs utilise a fuel comprising a liquid solution of uranium and chloride salts. This design eliminates meltdown risks and ensures safer operations compared to traditional nuclear power. The reactors, on Floating Nuclear Power Plants measuring 160 metres in length and weighing 25,000 tons, will generate between 170-250 GWh of electricity annually –ar surpassing the efficiency of existing hydrocarbon-based fuels.
The case for nuclear in shipping
Bøe is a vocal advocate for nuclear power, challenging public perception and regulatory hurdles that have historically
hindered its adoption. There are many misconceptions about nuclear power that have their roots in groups that wanted nuclear weapons to be disarmed.
The current drive for nuclear power is because of the global imperative to decarbonise shipping and this technology is the ‘silver bullet’ that can help deliver that goal
“CORE POWER’s Liberty program envisages a two-stage approach to maritime decarbonisation. The first stage will focus on building floating nuclear power plants (FNPPs) in shipyards. FNPPs will operate in a similar way to existing power barges, being centrally manufactured then towed to wherever they are needed. Initial smaller-capacity designs will be able to be moored in ports, while later larger-capacity FNPPs will be anchored further offshore.
“Rolling out FNPPs will create the regulatory environment and operational expertise necessary for the second stage of the Liberty program - nuclear propulsion for civil ships.”
The fundamental driver behind nuclear adoption, Bøe contends, is its unparalleled energy efficiency. “Every single substantial change in human development, in human prosperity, is directly linked to how effectively we use energy,” he explains. “The way that we live today is entirely because of our immense ability to harness energy from fossil fuels in an efficient way.” The challenge, then, is to transition from fossil fuels to an energy source that is equally, if not more, effective—hence the shift towards nuclear.
While nuclear energy has come with high initial costs in the
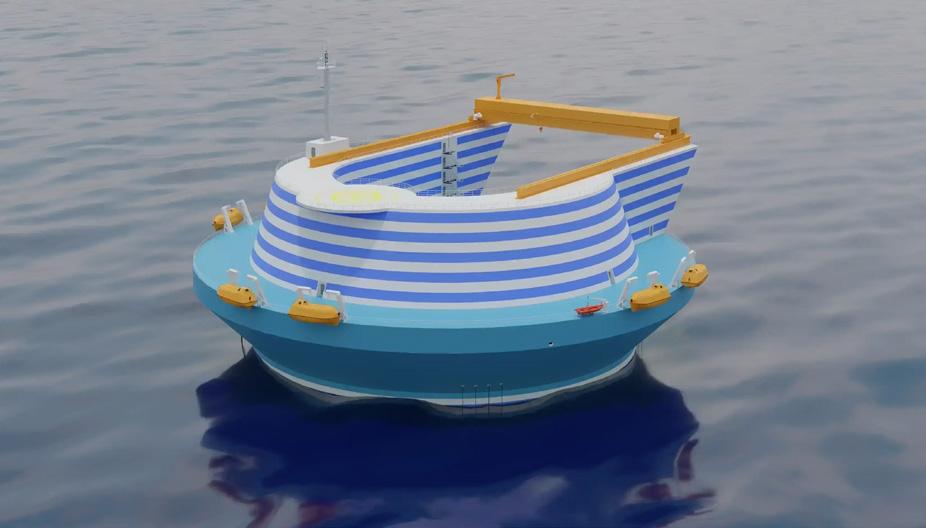
past, the advanced technology CORE POWER will be deploying will mean that these costs are far lower than for conventional nuclear technology. Also, nuclear energy’s economic model is the inverse of traditional bunkering models: while fossilfuelled ships may have a relatively low capex but substantial operational costs over time, the high capex costs of nuclear are significantly offset by its minimal operational costs. A ship using an advanced nuclear reactor will not need refuelling for its entire 25-year design life, Bøe says.
Compared to alternative fuels, nuclear energy density is staggering. “Ammonia and methanol have an energy density of between 17 and 19 megajoules per kilo, while bunker fuels range from 42 to 44 megajoules per kilo,” Bøe explains. “You would have to use between two and two and a half times as much fuel in order to get the same amount of power.” Given shipping’s main purpose is the transport of people or goods, larger tanks would mean less cargo space therefore future fuel adoption has a fundamental problem.
Overcoming industry challenges
The Liberty program is addressing the key barriers to nuclear adoption, including public opinion, regulatory concerns, and insurance. “Liberty is developing a new nuclear technology, which is the one that solves the liability, that solves the port access, which solves the public opinion piece,” says Bøe. Encouragingly, the International Maritime Organization (IMO) is revising its nuclear safety codes, and the International Atomic Energy Agency (IAEA) is setting up specific initiatives to facilitate floating nuclear power.
Market potential for floating nuclear stations is vast, with an estimated addressable value of $2.6 trillion by 2060.
CORE POWER’s model is built on a modular approach, ensuring reliable and timely delivery. Large technology companies, such as Google and Meta, are also eyeing floating nuclear power to support their energy-intensive data centres, which cannot afford the delays and costs associated with traditional nuclear plants.
When it comes to safety, CORE POWER’s long fuel cycle model eliminates the need for refuelling, thereby removing risks associated with spent nuclear fuel. “We’re not trying to impose a technology that doesn’t fit shipping,” Bøe states. His confidence in the technology’s viability is unwavering: “We
Rolling out FNPPs will create the regulatory environment and operational expertise necessary for the second stage of the Liberty program - nuclear propulsion for civil ships ‘‘
see the industry standing up and realising that this is not a question of if, it’s a question of how we do it.”
As the UK government considers legislative changes to support nuclear-powered shipping, CORE Power stands at the forefront of an energy revolution. Bøe remains sceptical about competing alternatives, particularly green ammonia. “The fact of the matter is physics and chemistry matter; you can't break the rules of nature. The laws of nature apply whatever you do,” he asserts.
Ultimately, CORE POWER’s floating nuclear solution offers an opportunity to redefine maritime energy, ensuring longterm sustainability and cost-effectiveness. With the support of leading shipyards in Japan and South Korea, as well as growing regulatory acceptance, the Liberty program is wellpositioned to drive the next generation of zero-emission
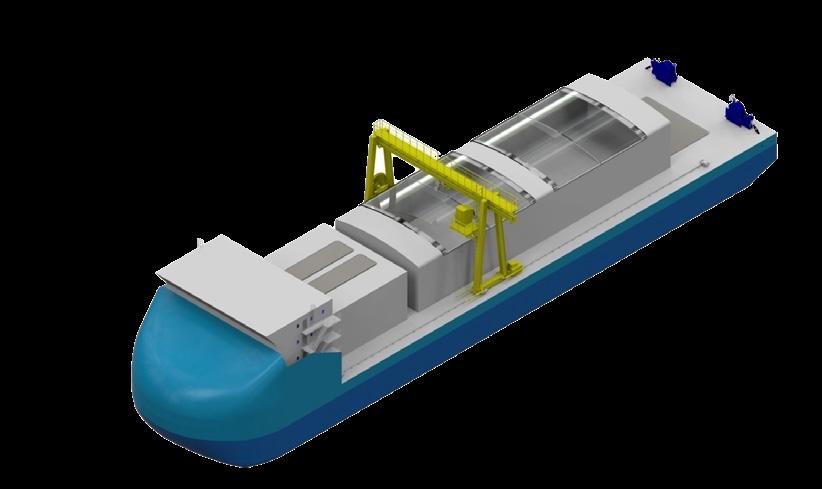
LNG – FROM PIPE-DREAM TO MAINSTREAM
Nearly 15 years ago, when the first Motorship Gas Fuelled Ships conference was held in Hamburg, liquefied natural gas-fuelled propulsion was seen as a promising novelty, albeit with a limited market
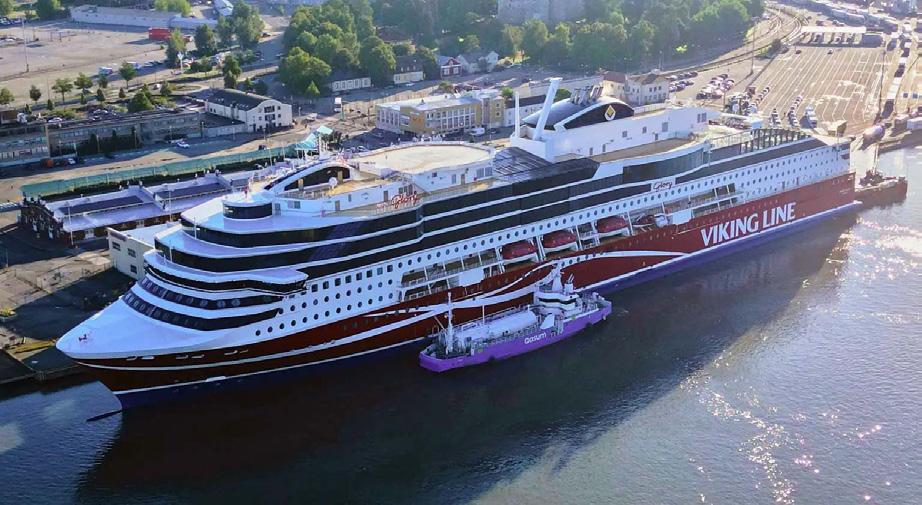
Fast forward to 2025, and the number of dual-fuel, LNG capable vessels afloat and on order has reached a number that would have seemed staggering in 2010. Then, LNG as fuel was solely the preserve of gas tankers, which could use cargo boil-off as fuel, as well as short-distance coastal ferries, such as those crossing the Norwegian fjords, where suitable and safe refuelling stations could be provided.
Although technology had proved burning gas as well as liquid fuels in the same engine was feasible, LNG was being considered for only a very few mainstream ship types. It was the infrastructure that was regarded as the main hurdle. Add to this the fact that, for ships travelling long distances between bunkering ports, LNG tank volumes would need to be far greater than for conventional fuels.
Maritime LNG industry collective Sea-LNG has recently published its analysis of the LNG-fuelled fleet. From a mere handful of ships 10 years ago, there are now 638 LNG-fuelled ships afloat. This may still be a small minority of the total world fleet – some 6-7% - but the figure is expected to almost double to 1200 by 2028.
Most marine engines are capable of being retrofitted for dual-fuel LNG use, but such activity has been very limited. This is no doubt due to the complexity of incorporating LNG fuel storage and handling systems on existing ships. So the growth in the gas-fuelled fleet is down to the number of newbuilding orders that are capable of dual fuel (LNG and oil fuel) operation. Sea-LNG notes that about 70% of alternativefuelled tonnage ordered in 2024 is capable of running on LNG. Those figures are even more noteworthy as they specifically exclude gas carrier ships.
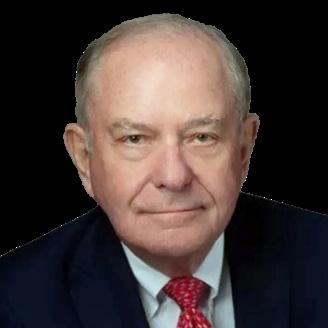
Such expansion has only been possible because of the rapid growth in the LNG fuelling infrastructure. In the early years of gas fuelled ships, longer voyages – initially just the maiden delivery voyage from Far Eastern shipyards to European operators – had to be meticulously planned, with road tankers ready at various ports en route, as insufficient locations were able to supply LNG in bulk. Sea-LNG’s analysis shows that by the end of 2024, LNG bunkers were available in nearly 200 ports worldwide, with plans in progress for full LNG bunkering facilities in an additional 78 location. There has been a considerable increase in LNG bunker ships - over 60 are currently operating today, marking a 22% increase from 2023’s figures. More still are being planned and delivered.
Many in the industry have moved from seeing LNG fuel as a novelty, appropriate in a few specialised markets, to an interim fuel, offering a bridge between fossil fuels and zeroemission alternatives, which still have a way to go before they too enter the mainstream. This is a view that is accepted by Sea-LNG, but the industry coalition sees a longer-term future, with synthetically (e-methane) or biologically produced (bio-methane) gas offering a net zero-emission virtual drop-in for LNG.
Sea-LNG chairman Peter Keller said: “Our latest [January 2025] ‘View from the Bridge’ report reaffirms the importance of the LNG pathway as a practical and realistic route to shipping’s decarbonisation now. We continue to believe that the shipping industry is heading towards a successful multifuel future where LNG will always play a critical role. To deliver net zero by 2050 across the global shipping fleet, a basket of fuels is required and the LNG pathway will continue to lead the way. This is not a case of my fuel versus your fuel but rather which fuel best allows the industry to reach its stated goals. The LNG pathway provides the path to net zero.”
According to Keller, bio-methane and e-methane are an important step along that pathway, allowing dual-fuel ships ordered today to burn, with little or no modification to engines or fuel systems, gaseous fuels complying with netzero well to wake specifications.
Methane slip
Sea-LNG’s analysis suggests that the FuelEU Maritime regulations, that started to take effect from the beginning of 2025, create a favourable climate for the LNG/bio-methane pathway. Running on LNG fuel, the latest dual-fuel vessels can immediately reduce GHG emissions by up to 23%, making them compliant until around 2039. Then, switching to liquefied bio-methane and e-methane can extend compliance beyond the IMO net-zero deadline of 2050. When such vessels are part of a Fuel EU Maritime pooling arrangement, the economics of running on gas can look highly attractive.
Although use of LNG fuel offers a significant reduction in carbon dioxide emissions, the main component of LNG –methane (CH4) – is a far more potent greenhouse gas than CO2, and there is a real danger that unburnt methane can be released into the atmosphere from LNG-fuelled engine exhausts. Methane slip, i.e. unburnt methane, has therefore tended to detract from the environmental contribution of gas fuelled ships.
The first dual-fuel engines were four-stroke units, operating on the lean-burn Otto cycle in gas mode and Diesel cycle in oil mode. Relatively high levels of methane slip were observed from such engines in gas mode. It should be noted that for gas-only, spark-ignited engines, methane slip is somewhat more tightly controlled, but such units, being limited to one fuel type, are less attractive for most maritime applications. For both types, methane slip increases significantly at low load – in the case of Otto cycle engines running at 25% load, methane slip has been found to increase by around a factor of four, according to a paper presented at the last CIMAC congress.
As dual-fuel marine engines developed, methane slip has been addressed in a number of ways. Safetytech Accelerator, which was established in 2018 by Lloyd’s Register and became an autonomous company in 2021, has taken a leading role through its Methane Abatement in Maritime Innovation Initiative (MAMII). In this initiative, four companies - Daphne Technology, CDTi Advanced Materials, Rotoboost, and Plenesys - were selected to take part in trials of a number of systems, in conjunction with shipping companies MSC, Seapeak and Capital Gas. Daphne Technologies’ SlipPure system is installed in the ship exhaust, and converts methane into water and CO2; CDTi offers a catalyst solution that oxidises the methane gas; Rotoboost’s system enables onsite pre-combustion low-carbon hydrogen production through thermo-catalytic decomposition, and Plenesys employs plasma torches to crack methane molecules.
In the trials, all have been found effective in cutting methane slip, by up to about 80%, while the Plenesys and Rotoboost methods reduced CO2 emissions as well. All were
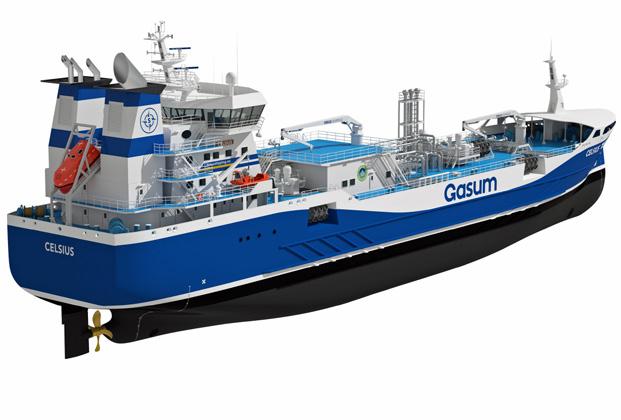
considered cost-effective ways of meeting the IMO emission goals.
MSC Group EVP Bud Darr said: “Information about how methane combustion performs under different conditions will be critical to solving the challenge of methane slip. Research insights from studies such as this one get the industry a step closer to understanding not only combustion performance but also what combination of onboard technologies can deliver significant methane emissions reduction. Improving the methane footprint of the global maritime fleet will be crucial to unlocking the net zero potential of bio and synthetic LNG. MSC is proud to support MAMII’s research focused on improving methane performance, which will ultimately support our efforts to achieving net zero decarbonisation by 2050.”
‘‘
To deliver net zero by 2050 across the global shipping fleet, a basket of fuels is required and the LNG pathway will continue to lead the way
Kaisa Nikulainen, CEO Rotoboost said: “The collaboration has been exceptional, bringing together charterers, ship owners, LR, and industry partners such engine/equipment makers, to expedite the decarbonisation process and reduce the carbon footprint of the assets”.
The story is somewhat different for dual-fuel two-stroke engines. MAN B&W’s first-to-the-market ME-GI operates on the Diesel cycle in both modes, with minimal methane slip in gas mode, thanks to a high-pressure fuel system. However, the cost and complexity of the system prompted the industry to look for simpler alternatives. Wärtsilä (now WinGD) offered its X-DF low-speed dual fuel engine with a much simpler lowpressure Otto cycle system, but that was affected in a similar way to the Otto-cycle four strokes. MAN B&W introduced the low-pressure ME-GA in competition, but this was short-lived and was withdrawn in 2024. However, with the engine designers’ own improvements to the combustion process as well as the separate developments highlighted in programmes such as MAMII, the methane slip problem is well on track to be significantly reduced, if not eliminated altogether.
Sea-LNG’s Keller concluded: “As LNG continues to gain widespread recognition as the current practical and realistic alternative fuel pathway, it is reassuring to see growing evidence that the challenge of methane slip will be eliminated within this decade.”
THRUSTERS AND DP CRITICAL TO WTIV OPERATION
Kongsberg Maritime is supplying power, DP control and thruster technology for a string of wind turbine installation vessels, most recently for the U.S.-built Charybdis

The first-ever Jones Act compliant offshore wind turbine installation vessel (WTIV), the Charybdis, is nearing completion at Seatrium AmFELS in Brownsville, Texas. Upon delivery, it will be owned and operated by Blue Ocean Energy Marine, a subsidiary of Dominion Energy, and will start operation on the Coastal Virginia Offshore Wind project, the largest offshore wind project in the United States.
The self-propelled, self-elevating GUSTO NG-16000XL design vessel is 144 x 56 metres and has a draught of 11.5 metres. It is equipped with a crane capable of lifting up to 2,200 tonnes and has an accommodation capacity of up to 119 people.
WTIVs have distinct operating modes (loading, sailing, DP, jacking and installation). They need to lift the complete weight of the vessel during installation operations, so power systems need to support this as well as ensuring DP, sailing and manoeuvring capabilities are maintained to the highest standard.
Kongsberg Maritime has supplied an extensive and fully integrated equipment package to Charybdis including engines, thrusters, deck machinery, electrical systems, DP, marine automation, safety, navigation, and telecommunication systems. “The integration of these systems ensures seamless operation and enhanced reliability, leveraging proven technology specifically designed for this type of vessel,” said
at Kongsberg Maritime.
The propulsion system features six Bergen Engines (B33:45L8A) and a combination of Kongsberg Maritime Z-drive and combi thrusters, providing robust and efficient manoeuvrability. The thruster models are 4 x US 305 FP Z-drive /3,200kW/3.2m propeller, 2 x ULE 355 FP Combi/3,700kW/ 3.5m propeller and 1 x UL 355 FP/3,700kW/3.5m propeller.
The electrical system includes generators, medium and low voltage switchboards, propulsion drives, transformers, shore connection, and UPS, all designed to ensure a stable and reliable power supply.
“The dynamic positioning (DP2) and thruster control systems, along with marine automation and safety systems, offer precise control and enhanced safety. Additionally, the navigation and K-Bridge systems, along with a comprehensive telecommunication suite, ensure effective communication and operational efficiency. This integrated approach highlights Kongsberg Maritime's commitment to delivering advanced and reliable solutions for the offshore wind industry.”
ABS
standard
The project was enrolled into the U.S. Coast Guard’s NVIC 10-82 and 10-92 programs which delegated the majority of statutory inspections and plan approval to ABS. Rob Langford,
ABS Vice President, Global Offshore Renewables, said the DP system is built to ABS DP2 classification requirements and is a highly redundant system that can maintain the vessel’s position even if faced with a single component failure. “With our extensive knowledge of U.S. regulations and with our longstanding offshore industry leadership, ABS is the ideal partner for the Charybdis.”
As the first Jones Act WTIV, Charybdis would be available for projects in U.S. waters, eliminating the need for foreignflagged WTIVs to have local vessels deliver turbines to them to meet Jones Act requirements. The global WTIV fleet continues to grow in size and number as offshore wind projects get underway further from shore.
In August last year, Kongsberg Maritime secured a contract from COSCO Shipping Heavy Industry to supply a package of mission-critical technology for the latest WTIV which is currently under construction for Cadeler. This is the fifth Cadeler WTIV to be built at COSCO’s Qidong yard, all equipped with Kongsberg Maritime systems.
The new GUSTO NG-20000X design vessel will have a complete electrical, automation and propulsion system from Kongsberg Maritime which features nine thrusters, all with fixed-pitch propellers. The package comprises four UUC355FP main propulsion thrusters, two ULE355FP retractable azimuth thrusters, and two TT3300DPNFP tunnel thrusters to provide additional lateral manoeuvrability.
Kongsberg Maritime introduced the UUC355FP, a new member of its underwater mountable azimuth thruster range in July 2024. The thruster has a 3.7-metre propeller and 4.2MW power output. It features an integrated permanent magnet motor that delivers 81 tonnes of bollard pull while requiring less space in machine rooms than comparable systems. Other features of the new thruster included low noise operation, less lubricating oil volume, and no oil-to-sea interfaces.
The retractable thrusters provide the full manoeuvring and positioning capability of an azimuth thruster, without affecting the draft or running resistance of the vessel, when the propulsive power is not needed. They also provide redundancy and “take me home” capability to the vessel.
The electrical system includes generators, medium and low voltage switchboards, DC switchboards, energy storage system, and propulsion drives in addition to an integrated control system, including a DP system. Tailored energy control functions also optimise the vessel’s energy efficiency, and the battery-hybrid electrical system can reduce the number of engines required for crane operations and manoeuvring.
Cadeler latest deliveries include the P-class Wind Peak and sister vessel Wind Pace which also feature Kongsberg Maritime technology, as do the A-class Wind Ally, Wind Ace, and Wind Apex currently under construction.
Second wind
Wind Peak and Wind Pace can transport and install seven complete 15MW turbines or five sets of 20MW+ turbines. They are the largest vessels in the Cadeler fleet, and are 162 x 60 metres, have draught of 9.7 metres, a total deck space of 5,600 square metres, a payload capacity of over 17,600 tonnes, and a Huisman main crane capable of lifting more than 2,500 tonnes at 53 metres
Kongsberg Maritime is supplying the hybrid electric power and energy management systems. The vessels also feature four Kongsberg Maritime azimuth thrusters, two retractable thrusters and three tunnel thrusters. Kongsberg Maritime’s DP system cooperates with the integrated propulsion system, energy control system and sensors, to ensure accurate operation with heavy loads.
The company says its WTIV solution substantially reduces
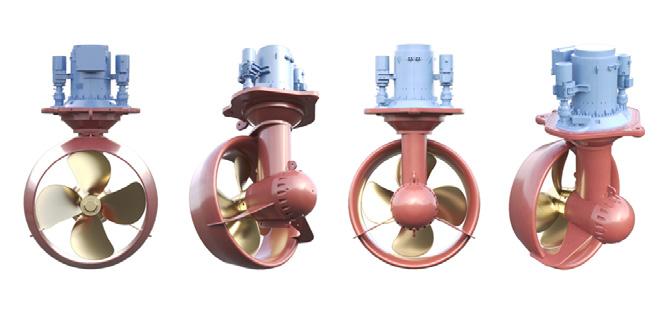
the costs associated with wind farm installation projects. Shipyards will save engineering hours and cabling and installation work, while owners and operators will see lower operating expenses. Tailored energy control functions optimise the vessels’ energy efficiency, and the batteryhybrid electrical system includes advanced ThrustAllocator™ and PowerBoost™ functionalities that can reduce the number of engines online and the amount of fuel required for crane operations and DP manoeuvring.
Kongsberg Maritime is now expanding into floating offshore wind construction technology with two new floating wind installation vessel designs (WTIVs): an anchor handler designed to handle large dragging anchors and a large subsea construction vessel with mooring system installation capabilities. The high-thrust propulsion for the large anchor handler is provided by a triple azimuth thruster configuration at the stern, which offers enhanced station keeping, high bollard pull of around 300 tonnes and DP redundancy.
The company has also developed Tow Assist which enables unpowered floating turbine structures to become DP-enabled during towing and positioning operations.
Martinus Løken, Kongsberg Maritime’s Aftermarket Sales Manager, says towing completed floating turbines to location is a key challenge for operators. With Tow Assist, temporary positioning equipment is installed onboard the turbine and linked wirelessly to the connected towing vessels, which are equipped with DP systems.
Real-time data on position and heading, along with thruster and winch status, is transferred wirelessly to the Tow Assist master computer, located on the lead vessel. Then the connected vessels, ideally three of them, act as thrusters for the floating structure.
“We’re essentially providing a decentralised DP operation to a floating object. We can measure the position of the floater and the position of the connected vessels, and then we can establish a model for the precise positioning of the unit, either for station keeping or moving along a trajectory in a controlled manner.
“This approach is particularly useful when getting the floating structure into the exact position for attaching anchors, or hook-up. However, we believe it should be used for the entire journey from shore to field, as it offers optimal performance of the vessels. We’re going to see more and more of these structures being transported in different parts of the world, where there will be different levels of seaborne traffic and other obstacles to navigate, so all parts of the towing journey can be enhanced.”
The key benefits of the Tow Assist System are optimised vessel usage, optimised operational efficiency, increased hook-up weather window, improved situational awareness, reduced fuel consumption and improved safety. In summer 2024, Kongsberg Maritime demonstrated the Tow Assist System’s capabilities during a successful trial at the Hywind Scotland offshore wind farm off the coast of Aberdeen, and the system is now set to be commercially available in 2025.
SHIP DESIGN AND THE CHANGING
ALTERNATIVE FUEL ‘SEASCAPE’
Designing the fleet of the future presents many challenges and risks, and no ship owner wants to invest in a multimillion-dollar ‘leap of faith’. Janne Huotari - Senior R&D Engineer at NAPA Design Solutions explains how simulation tools can be a gamechanger for ship design, helping the industry make the right decisions today for the vessels of tomorrow
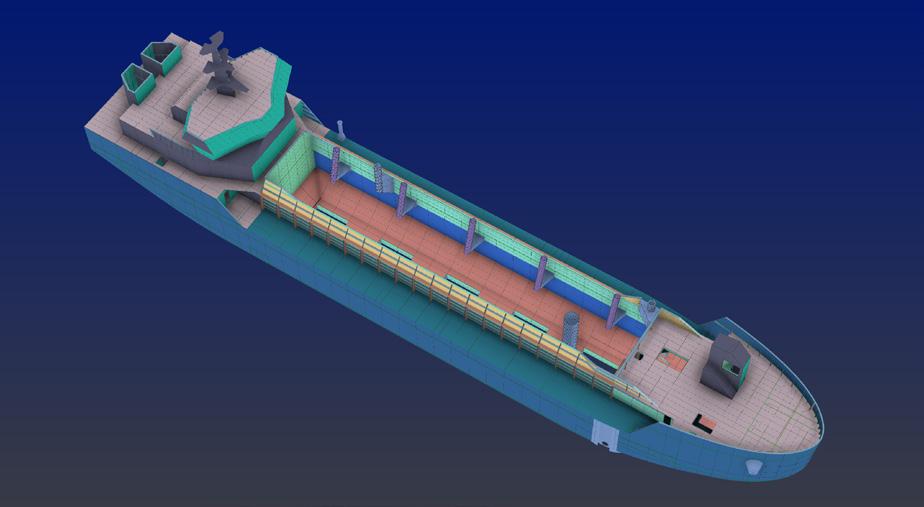
Shipping’s ‘seascape’ is changing and we’re seeing a new age of vessels hit the water. Defined by a greater emphasis on efficiency, innovation and decarbonisation, ship owners are looking to the future.
Throughout 2024, ship owners invested in alternative fuelled vessels, increasing the orderbook by more than 50% to 1,737 vessels. The number of in-service alternative fuelled vessels also grew by 18% to 1860 vessels.
While this is still a relatively small proportion of the global fleet - around 4.8% of all vessels in service and on order - this trend is no coincidence. The shipping industry recognises that global regulators, like the International Maritime Organization, and governing bodies of major ports and markets like the European Union, are ramping up the urgency to meet net zero by 2050.
In fact, the IMO’s 2030 target mandates that net zero, or near net zero, fuels make up 5 -10% of all shipping fuels by 2030. Introduced earlier this year, FuelEU Maritime also sets a requirement on the annual average GHG intensity of energy used by ships trading in the European Economic Area, with the aim of increasing the share of alternative fuelled vessels within the EU. This builds on existing European Union Emissions Trading System (EU ETS) which puts a direct price on carbon.
Beyond compliance, decarbonisation increasingly commands an economic and commercial rationale which ship owners are acutely aware of. Modern, energy-efficient vessels that comply with tightening regulations can secure better chartering rates than their older counterparts, with
premiums reaching several thousands of dollars per day, and even more for certain vessel types.
The correlation is, therefore, a linear one: as regulatory scrutiny increases, so will the business case for more efficient, alternative fuelled vessels. Poorly rated ships may struggle to secure business and financing, while top-rated vessels are likely to enjoy a competitive advantage.
That said, designing the fleet of the future isn’t without its challenges and risks, and no ship owner wants their multimillion-dollar investment to be a leap of faith. Getting it right is crucial, but balancing safety, stability, efficiency and more is no small feat. Fortunately, this is where simulation tools can be a gamechanger for ship design.
Carving a new path forward using 3D modelling
A commercial vessel’s lifespan can reach 20 to 30 years which means that the vessels designed and built today will still be operational in 2050. Given these timelines, ship owners want assurances that their investments will pay back, be compliant and safe.
In shipping’s multi-fuel future, there is no single pathway to building tomorrow’s fleet. Each design and fuel choice will be determined by a vessel’s unique operating requirements and constraints. This means that new ship designs are more complex than ever.
Innovation in ship design is essential, requiring a step change in the way ships are designed. There is already a fundamental (and digital) transformation taking place in shipyards that is contributing to a greater use of 3D models
Digital twins help bring to life the insights gained from operational simulations. They bring together 3D models and data on the vessel to test different design variations and model how they would behave in real life
to optimise workflows throughout the design process, from the early stages through to classification approvals, detail design, and all the way in downstream production design.
While 3D models themselves are not new to ship design, their deployment throughout the design process is a real gamechanger. It ensures that all disciplines involved in a vessel’s design can access “a single source of truth”, delivering better communication, saving time, and limiting the risk of errors. This more efficient workflow helps teams work collaboratively to deliver the best possible designs and innovate.
The greater use of 3D models also lays the groundwork for using next-generation simulation tools to test different fuel and clean technology options. Using operational data on actual weather conditions on the specific routes where the ship will be operated, we can model the implications of new energy systems for the ship’s configuration, cargo capacity, stability, and even its future performance. This helps engineers, naval architects and ship owners themselves to make the right choices for each vessel, while also providing a wealth of insights to help optimise performance after the vessel has left the shipyard.
Using digital twins with reliable data to evaluate the best ship design options
Digital twins help bring to life the insights gained from operational simulations. They bring together 3D models and data on the vessel to test different design variations and model how they would behave in real life.
For example, 3D model data values, combined with route and weather data, can be used to compare different configurations for alternative-fueled vessels and calculate the impact on the vessel’s future performance, fuel consumption, GHG emissions, stability parameters and hydrodynamic profile. This helps naval architects and engineers evaluate where additional tanks, for example, should be installed on a ship, accounting not only for the total volumes needed, but also where they need to be installed to ensure safety. These simulations can be done from the early concept design stages, and only increase in accuracy as more details are added throughout the process.
The next leap in the use of digital twins is being advanced by NAPA Studios in its cross-industry project with major shipyards and ship owners. The project is focused on creating a secure data-sharing framework between shipyards and shipowners for the use of a single digital twin throughout the ship’s lifecycle. This enables the use of a vessel’s unique design data to optimise efficiency and safety at sea. It also builds a feedback loop for operational data to be fed back to inform new designs.
For ship owners, these advancements in 3D modelling and digital twin technologies mean invaluable insight into their future vessel even before any steel has been purchased. This removes the “guess work” when planning for the future and supports decision making with data and evidence.
Operational data - what’s new?
No two vessels are the same which means that ship designers need to approach each project creatively and intelligently. And in shipping’s multi-fuel and multitechnology era, there will be a multitude of design variations based on a ship’s operational profile and the routes it will sail. This means that ship designers can no longer rely on data from similar vessels, which is often incomplete or based on simplified rules.
Looking ahead, combining operational and historical data can be used to simulate future vessels, including the range of speeds at which the future ship will be operated as well as its future fuel consumption. This helps determine the optimal engine power required, but also the size of the fuel tanks that will be needed for the vessel. Given that future fuels such as ammonia, hydrogen and methanol are less energy-dense than their fossil fuel equivalent, getting this assessment right is critical as it can minimise the loss of cargo space.
Simulation tools to model behaviour and compare fuel options
NAPA recently explored a potential new design framework in which simulation tools could be used to model a hypothetical future ship’s behaviour. Three design variations with different dimensions and configurations were tested, keeping the weight constant. Based on the modelled operational profile of the ship, 26 voyages for 2023 were simulated. The first step in the proposed framework was to build a hydrodynamic model using the 3D model to design the vessel. The second step is to define its operational plan, which is easier with retrofits but not impossible for newbuilds with the availability of AIS data in NAPA’s database. Finally, by combining this data with NAPA’s digital tools used for optimising real ship operations, ship designers can simulate realistic voyages including estimating speed, engine loads, fuel consumption, and emissions.
Taking this one step further, these simulations can inform estimations of future fuel consumption, allowing ship owners to compare the costs and emission reduction benefits of different fuel options for a specific vessel. They can also simulate different route options based on weather data. This approach highlights significant cost and emission differences between design variations, helping owners unlock substantial savings by accounting for new operational expenses but also factoring in EU ETS and FuelEU Maritime compliance.
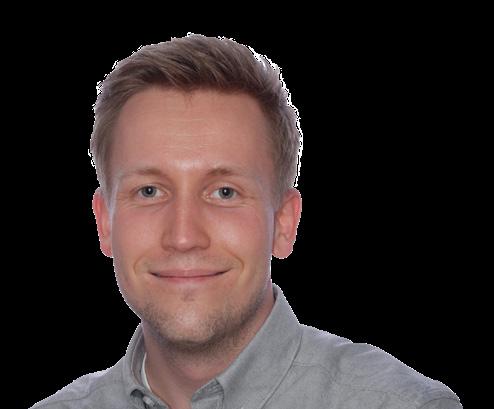
Shipping is transforming on every front but the two biggest drivers for change remain digitalisation and decarbonisation. They work hand in hand to push the industry to innovate and comply with changing regulations. But to reap the full benefits of this transformation, ship design needs to be a proactive and collaborative project with stakeholders across the value chain, from ship designers to ship owners and class.
The digital tools to build safer, smarter and more efficient vessels already exist and can be used to answer some of the industry’s most pressing questions around the energy transition. We need more innovative and creative thinking, as well as the technical expertise, to bring these solutions to life.
■ Janne Huotari, senior R&D engineer, NAPA
HOULDER’S ENGINEERING
MASTERY
Naval engineering and design consultancy Houlder has been working with clients providing innovative maritime solutions to a range of issues from propulsion to offshore wind construction for many years. We spoke to Jonathan Strachan, chief technology officer at the company about his role and the company’s ethos
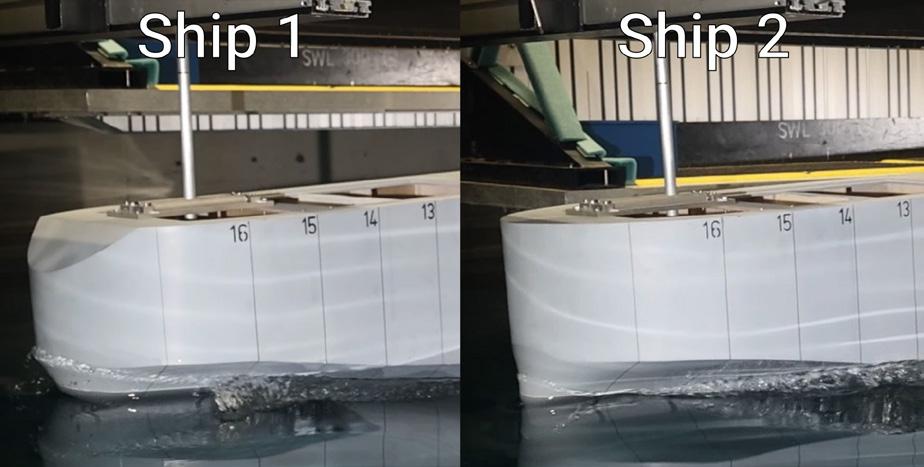
Jonathan Strachan joined Houlder in 2013 as a project director, having previously held various roles at maritime heavyweights including Lloyd’s Register (LR) and Carnival. On working for a class society and a shipowner, he says while LR makes sure the rules are applied and the statutory regulations abided by, alternatively “a shipowners focus [Carnival] is more on making sure that what it says in the spec is actually delivered, and making sure that what it says in the spec will do what you need it to do commercially.”
Having seen the maritime industry from these alternate viewpoints is a surely a boon when it comes to the world of design and engineering.
The Houlder name has a rich history in shipping dating back over 150 years to a previous incarnation Houlder Brother Shipping Line. Today’s Houlder diversified from its oil and gas roots put down in the 1970s and early successes include winning a contract for the design and build contract of six RoRo vessels that formed the UK Ministry of Defence Strategic Sealift Service worth over £1 billion.
The company’s therefore been around in one form or another since the 1860s, which is similar to one of its clients, German engineering giant Siemens. In 2016 Houlder was the first UK company to be awarded a contract working on offshore wind farms, in this case on the Siemens project, Galloper. The contract covered the design of blade rack, tower and nacelle fastenings to be used during the transport of Siemens 6MW turbines to the project site. The contract was a success and opened the door for Houlder to be involved with other projects in the sector. “It gave us a really good insight into all the various components for the wind
turbine generators, the transition, the monopiles and so on,” recalls Strachen. Given the size of the parts used in offshore wind farms, each blade has a length in excess of a football field for example, the transport of said components is an engineering feat in itself and Houlder was on hand to provide the technical expertise needed.
Innovation, IP and partners
Emanating from the company’s work for Siemens on the Galloper project came the development of the pile prop, in conjunction with another engineer, procurement and construction (EPC) player Caley. This is a specialised device used to temporarily stabilise and position a monopile (the main foundation pile for an offshore wind turbine) during installation, providing localised rigidity and preventing unwanted movement before the final grouting process secures it into the seabed.
These innovations reveal a characteristic about Houlder, this is its ability to partner with others in the pursuit of solutions. “We tend to work with clients who are developing their own tools and IP,” says Strachen. Another example would be the company’s work with SenseWind Technology, a wind power installation firm. This collaboration saw Houlder aid with the developing of a “crawler”, a device that walks up a turbine thereby negating the need for additional cranes during the installation process.
Ahead of the curve
One area that has hit the news recently but Houlder was involved in two years ago is the development of liquid
hydrogen carriers. For this endeavour the company was in partnership with energy major Shell and Houston, Texasbased EPC player CB&I. Strachan, speaking at the time, described the project as “very cool” adding drolly “both literally and metaphorically” in reference to hydrogen’s liquid state being at -253 degrees centigrade (only a few degrees above absolute zero). The concept received an AiP from DNV for the design of a liquid hydrogen cargo containment system. Houlder had also worked with Shell on hydrogen containment systems and carried out a ship piping and instrumentation review for ships carrying hydrogen as a cargo or as a fuel.
When it comes to what sets Houlder apart from other design and engineering companies, Strachan looks to home, this being Houlder’s Optimisation and Modelling Environment (HOME). This is the company’s in-house R&D technology which allows it, for example, to plot how a vessel will perform using fundamental naval architecture or physics when energy saving measures have been applied. “It allows owners to make informed decisions about what is a good option for them,” says Strachan about the department.
Given the tsunami of regulation hitting the shipping sector at the moment, Houlder has incorporated that into its forecasts and plans going forward. “Working on incorporating all available regulations, chart when the time certain fuels are going to make sense and working with clients to work out when certain fuels will be available and where,” says Strachan. This ethos may please shipowners looking to navigate FuelEU Maritime, a regulation which began its punitive measures to reduce emissions on 1 January this year.
But looking to future fuels to remain compliant is a costly solution and with the well-to-wake methodology being imposed by more regulators, even prima facie “green” fuels like methanol may come unstuck by the probing of the EU’s team of fuel verifiers. Houlder has released research into one tactic employed by fleets to increase fuel efficiency and thereby reduce emissions, slow steaming, which can be read here. Strachan talks about another area the company has been looking at to increase fuel efficiency and thereby reduce emissions. This is decreasing a ships resistance to waves in various sea-states.
The company’s COMLink project, in collaboration with Southampton University and Siem Car Carriers, is looking at changes made in the design stage of a ship using models incorporating CFD and other computer-based aids to decrease the resistance to waves of a vessel. Strachan says this is an area that has not been looked at before and given the “relatively low cost” he predicts shipowners would have

It gave us a really good insight into all the various components for the wind turbine generators, the transition, the monopiles and so on ‘‘
to incur with a newbuild to incorporate these measures, could be a crucial initiative for maritime.
With its roots in the oil and gas industry of the 1970s but today with a command of a multitude of sectors, Houlder continues to push the boundaries of naval engineering. Its commitment to innovation, collaboration, and sustainability ensures it remains at the forefront of the maritime industry’s evolution. Whether through pioneering offshore wind solutions, advancing hydrogen transport technology, or optimising vessel efficiency, the company’s expertise positions it as a trusted partner in shaping the future of shipping. With the industry facing increasing regulatory and environmental challenges, Houlder’s ability to anticipate and adapt to these changes will undoubtedly keep it ahead of the curve for years to come.
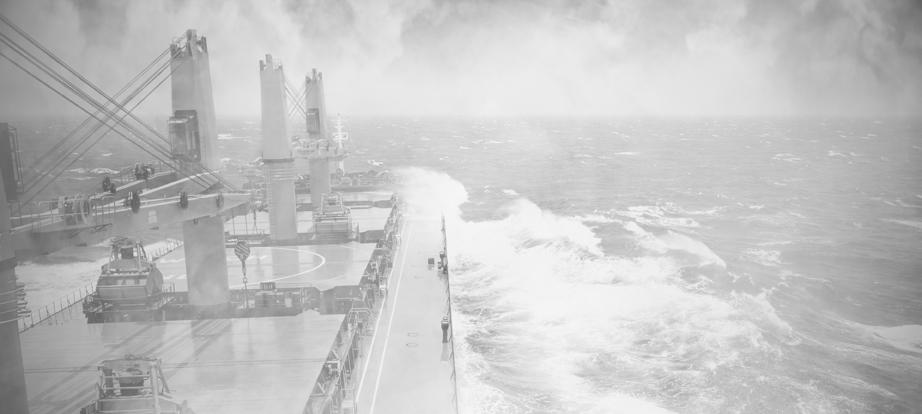
■ Houlder underlined uncertainty in the shipping industry during a survey
NIPPON PAINT MARINE
BIOCIDAL-FREE
COATING
The International Convention on the Control of Harmful Anti-Fouling Systems on Ships from the IMO was intended to protect sea life from harmful substances applied to hulls. Long gone are the days when lime and arsenic were attached to the hulls of sailing ships but biocidal coatings have persisted. We spoke to Kazuaki Masuda, corporate officer in the technical division of Nippon Paint Marine about its AQUATERRAS solution, a biocide-free coating applied to ships to stop barnacles and other obstructions attaching and thereby reducing vessel speed
How does AQUATERRAS contribute to environmental sustainability compared to traditional biocidal antifouling paints?
Our AQUATERRAS solution is a pioneering development in coatings technology from our R&D team. It represents the world’s first hull coating that provides industry leading protection, whilst remaining 100% biocide-free. Taking inspiration from innovation in wider sectors, our research team developed AQUATERRAS's biocide-free self-polishing coating with technology and material originally developed in the pharmaceutical sector, by using medical antithrombogenic polymer technology.
Our R&D team developed a new form of hydrolysis by combining hydrophilic and hydrophobic micro-domain structure on the coating’s surface to prevent biofouling. As a result, AQUATERRAS naturally repels any biological adhesion onto its surface through the constant exposure of its active micro-domain structure that is realised by the fine-tuned continuous self-polishing.
What performance data can you share regarding fuel savings and fouling prevention achieved with AQUATERRAS?
The combination of a hydrophilic and hydrophobic micro-domain structure creates a unique reaction which continually smooths the water flow around the hull surface as it travels in the sea, which has been found to reduce emissions by up to 14.7%, thanks to an average speed loss of just 1% over a 60-month period. The market average speed loss over a similar time period is 5.9%.
We have conducted extensive testing of the AQUATERRAS product to ensure its credentials as truly a biocide-free solution. Our research team studied its impact on marine fish, bivalves, crustaceans and seaweed, we found that none were impacted by the coating, which confirmed that AQUATERRAS posed no negative impact to marine life.
Are there any specific considerations or challenges when applying AQUATERRAS compared to conventional coatings?
No, one of the key characteristics of our AQUATERRAS coating is its ease of application. The coating has good workability and doesn’t require any special application apparatus or technical painting practices.
How has the market responded to AQUATERRAS since its launch, and what feedback have you received from shipowners and operators?
Since its release in 2017, through testing and application on more than 100 vessels, AQUATERRAS has received a
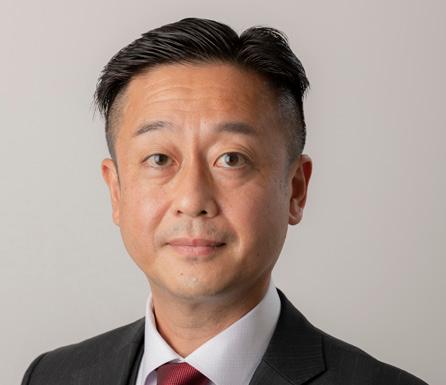
fantastic response from our customers and the wider industry. In fact, in 2021, AQUATERRAS was announced as the winner of the SAFETY4SEA’s Technology Award as well as the Seatrade Maritime Award, in 2023. The awards recognised the coating’s contribution to improving efficiencies, lowering operating costs and reducing emissions for the shipping industry.
An example of the trust that the market has in the technology was demonstrated in 2024, when we applied AQUATERRAS to Mitsui OSK Lines Ltd’s (MOL) 36,030 GT carrier, the Courageous Ace. Due to the vessel having to operate in multiple conditions around the world, the customer required a coating that could optimise performance in the harshest environments, which meant that AQUATERRAS was the ideal solution.
The coating was applied to the flat bottom, vertical bottom, and boottop of the vessel, which represented the first time MOL has used AQUATERRAS, and although it’s too soon to share detailed results, the initial feedback from the client is extremely positive.
Does AQUATERRAS comply with international regulations, such as the IMO's AFS Convention, and have you obtained certifications from classification societies?
Yes, our industry leading research and development teams are committed to innovating our product lines to ensure that our coating systems adhere to the highest industry standards. Our AQUATERRAS series complies with the IMO-AFS2001 Convention on the Control of Harmful Antifouling Systems on Ships as a tin-free coating system, and has received certification from leading class societies, including the Japan Paint Manufacturers Association, DNV, Lloyd’s Register, and Korean Register.
subscriptions available from £22 per month
Discover The Motorship today
Unlock full access to The Motorship today with our online subscription. The Motorship is the multi-media platform dedicated to all aspects of the shipping industry. Stay up-to-date with new products, innovations and developments which impact their business.
Informing over 31,000
shipping professionals around the world
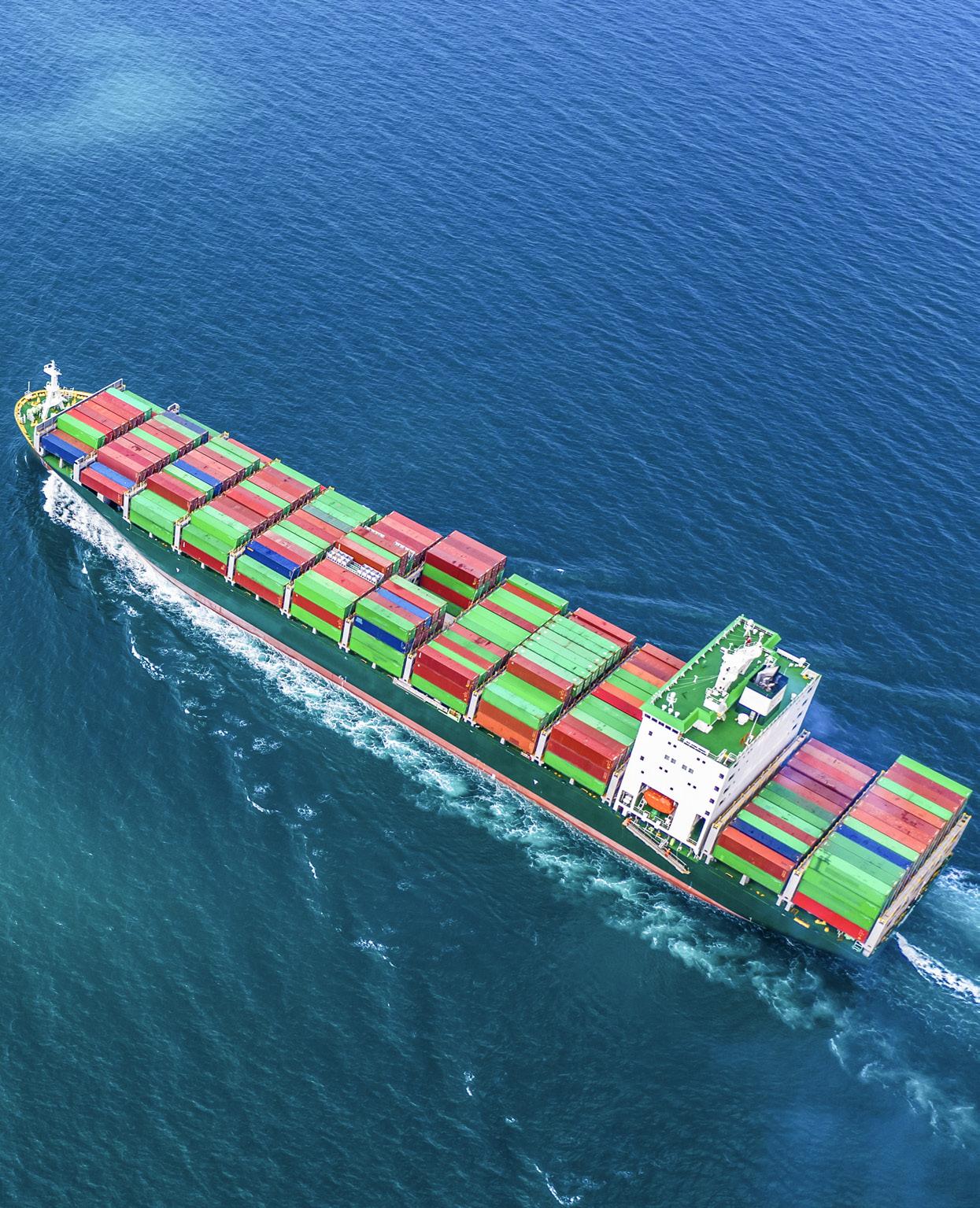
Register now for free and enjoy one month of complimentary unlimited access to our news archive, podcasts, webinars, and articles on innovations and current trends in the shipping industry.



Visit motorship.com
Email subscriptions@mercatormedia.com Or Call +44 1329 825335









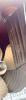
CHINESE SELF-RELIANCE REACHES NEW LEVEL
China’s domination of the international market for the construction of large ro-pax ferries has gained a new edge through the delivery of the first in a series of almost entirely home-grown vessels for an Italian owner. By David Tinsley
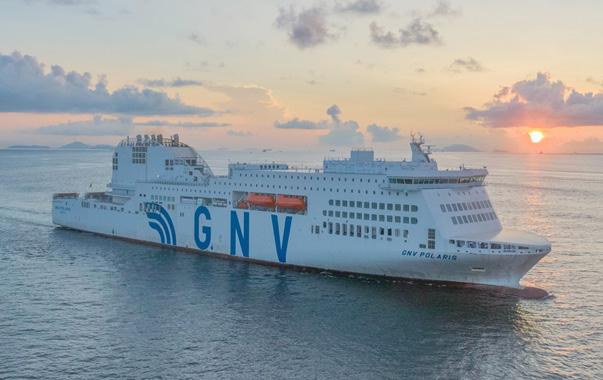
Whereas export production in the sector has hitherto relied extensively on foreign design and technological input, the latest delivery to European principals is distinguished by its predominantly Chinese origination.
Ordered by Geneva-based MSC Group on behalf of Italian affiliate Grandi Navali Veloci (GNV), contractor Guangzhou Shipyard International (GSI) was entrusted with the development and design of the series. Chinese self-reliance expressed in the project also includes the interior architecture, interior materials and furnishings, as well as the widest recourse to locally manufactured and designed equipment. First of four contracted to GNV’s account, the 218-metre GNV Polaris has put down a marker for Chinese marine technologies in a number of spheres.
The 45,900gt GNV Polaris accordingly ranks as the first large-scale export vessel in her category incorporating Chinese intellectual property (IP) rights. China’s competitiveness relative to other shipbuilding nations has therefore assumed a new intensity, whereby independent know-how complements all the other elements that have brought its industry to the fore on the world stage.
The design drawn up by Shanghai Merchant Ship & Research Institute (SDARI) in conjunction with the shipowner’s stipulations and parameters provides the GNV Polaris with capacity for 1,500 passengers and a total 3,100 lane-metre ro-ro payload on three fixed decks, corresponding to 600 cars or 200 HGVs/trailers. The follow-on and subsequent
vessels incorporate increased provision for passengers and a somewhat lower vehicular intake.
While suited to, and intended for, deployment across GNV’s Mediterranean network, GNV Polaris has initially been assigned to the Genoa/Palermo route, which the legacy Grimaldi organisation promoted with fast, innovative ro-ro tonnage as far back as 1970 by way of the Grandi Traghetti sisters Freccia Blu and Freccia Rosa. A veritable sea highway, extending the length of Italy’s western shores, the service provides a dependable north/south domestic transportation option.
Next generation
The incoming generation of four ships, comprising an alldiesel first pair, and an LNG-capable second pair, will realise not only a hike in fleet productivity and capacity, but also a big gain in environmental standard. GNV Polaris, which is equipped with comprehensive exhaust gas treatment plant plus a cold-ironing facility and silicone antifouling, promises a carbon footprint reduction of up to 30% relative to existing company tonnage.
GNV Polaris is installed with four diesel-only MAN mediumspeed, in-line engines of the 48/60CR series. Each ninecylinder four-stroke turns out just over 10,000kW, to give a power concentration in excess of 40,000kW, delivered through twin-input, single-output gearboxes to twin controllable pitch propellers for a speed of 25 knots at some 83% maximum continuous rating.
■ Distinctive in form, the Chinesedesigned and -built GNV Polaris series will strengthen the owner’s expanding Mediterranean network
The plant is arranged in two compartments, within the B/5 fore-and-aft bulkheads and separated by a centreline bulkhead, and thereby Safe Return to Port (SRtP)-compliant.
Notwithstanding the otherwise domestic sourcing of the vessel’s technical equipment and interior outfit, the Augsburg plate on the propulsion trunk engines is affirmation of German engineering export prowess. The four MAN gensets, though, were produced under licence by Shaanxi Diesel Heavy Industry. Besides the diesel-alternator aggregates, the ferry is equipped with a steam turbogenerator set, of 900kW output capacity, that makes full use of waste heat from the main engines. The heat recovery system was developed by China Shipbuilding Industry Corporation’s (CSIC) No711 Institute of Shanghai (SMDERI).
The vessel is fitted to allow connection to the local grid when berthed, so as to ensure a continuous supply of electrical power for shipboard needs without having generators running.
The huge funnel casing aft is a dominant feature, and design signature, of the newbuild class. Its exceptional size is a factor of the need to accommodate both NOx catalysers and SOx scrubbers and silencers as well as an exhaust gas energy recovery system and all associated pipework. The SOx afterteatment solution tackles not only the exhaust lines from the four main engines but also the streams produced by the gensets and auxiliary boilers.
While the corporate bid for an elevated, long-term environmental standard is the determinant of the engineering specification, the nature of the arrangements on GNV Polaris are apposite to the IMO’s categorisation of the Mediterranean Sea as a SOx Emission Control Area (ECA) effective from 1 May 2025.
The third and fourth newbuilds in the programme will differ in propulsion machinery from GNV Polaris and secondof-class GNV Orion through the owner’s decision to opt for LNG dual-fuel engines, entailing a slightly larger bore size. Design modifications involve giving up underdeck space so as to house the LNG fuel storage, using two C-type tanks.
Drawing on experience gained over the past 20 years in the production of ro-pax vessels, predominantly for clients in the export market, GSI has paid particular attention to levels of comfort and habitability aboard GNV Polaris and subsequent newbuilds. The standards applied have been such as to comply with RINA class notations COMF-VIB-B and COMF-NOISE-B. The result is that noise in the cabin areas is less than 55dB, and no more than 60dB in the public spaces, when the ship is sailing at full service speed.
Local knowledge
In the context of technology pertinent to shipboard comfort and ro-ro security, local content includes the retractable fin stabilisers, developed by CSIC’s No704 Research Institute. Growing industrial self-reliance as regards the outfitting of the passenger spaces is expressed in the manufacture of lifts and escalators by the shipyard contractor’s subsidiary GSI Elevator Electromechanical Equipment.
The array of RINA accreditations also includes the society’s Biosafe Ship notation, which embraces a whole range of systems, components and operative procedures aimed at preventing and controlling possible onboard infection outbreaks. The vessel is equipped to provide complete isolation wards and quarantine areas that meet the latest biosecurity standards, and the design of the air conditioning and ventilation arrangements is tailored accordingly.
GNV Polaris is thought to be the first ro-pax built in China to RINA’s Biosafe criteria. The certification was earlier secured by GNV for two of its existing ferries and by MSC Cruises as
PRINCIPAL PARTICULARS - GNV Polaris
Length overall 218.0m
Length bp 205.9m
Breadth, moulded 29.6m
Depth 10.0m
Draught, design 6.5m
Gross tonnage 45,909t
Deadweight 9,568t
Decks 12
Passenger capacity 1,500
Passenger cabins 239 Ro-ro capacity 3,100 lane-m
Vehicle capacity 600 cars or 200 HGVs/trailers
Propulsion system Diesel-mechanical
Main engine power 4 x 10,350kW
Speed 25kn
Class RINA
Class notations C+, +AUT-UMS, Biosafe Ship, COMF-NOISE-B, COMF-VIB-B, Green Plus, Inwatersurvey, MON-SHAFT, SRtP
Crew 85
Flag/registry Italy/Genoa
an additional class notation for the French-built MSC Grandiosa.
Ro-ro handling is effected via the stern only, using two axial ramps of different widths that span almost the full breadth of the transom. The larger portside ramp feeds the main deck and the fixed ramp leading to the upper vehicle deck, whereas the narrower starboard ramp gives access to the main deck garage and the lower hold. Fore and aft of the centreline casing that rises through the ro-ro decks, there is adequate space for commercial vehicles to turn and exit via the stern.
The original building cost for all four vessels was about EUR500m ($515m), on the basis of a common specification, but the figure increased to some EUR600m ($618m) due to changes subsequently stipulated for the ships to follow GNV Polaris. Besides the nomination of dual-fuel power for the third and fourth ferries, second-of-class GNV Orion will have nearly twice as many cabins as the lead ship and an increased passenger complement.
Nominally owned by Compania Naviera Allegro, GNV Polaris is operated and managed by Grandi Navali Veloci of Genoa. The latter had been established by Aldo Grimaldi in 1992, and was identified from the outset with high-grade vessels of the cruise ferry genre, produced by the now defunct shipbuilding firm of Cantieri Nuovi Apuania at Marina di Carrara. In 2010, GNV came under the control of the MSC Group.
The second of the newbuilds, GNV Orion, is fitting out in China in preparation for spring 2025 handover and anticipated entry alongside GNV Polaris on the Genoa/Palermo run. The LNG-capable, third and fourth ships, GNV Virgo and GNV Aurora, are due in 2026 and their allocated route has yet to be confirmed.
Besides the immediate impact of the first pair on the service linking northern Italy with Sicily, the introduction of new tonnage will benefit other Mediterranean routes through vessel rotation and cascading, the GNV network having been much expanded in recent years.
By the nature of the fleet investment programme, GNV and its parent organisation are helping to force the pace of change in Italy, where the authorities have come under criticism for a perceived dilatory approach to the development of the national port LNG supply infrastructure and at-berth electrical power availability.
CHINA EYES EUROPE’S JEWEL IN THE CROWN
In less than two and a half decades – one generation – China has come to dominate global shipbuilding. The 2020s, and 2024 especially, have been banner years for Chinese shipyards. The country now commands around 60% of the worldwide mercantile tonnage orderbook, compared with just 10% in 2000. By David Tinsley

Notwithstanding structural changes in the Chinese economy, evidence of a slowing in the growth momentum, and recent talk of the incoming US political administration imposing tariffs on Chinese-built vessels, China’s increasingly adept shipbuilding sector looks set to consolidate its centrestage global position, abetted by government industrial strategy. Ever-improving product quality and contractual performance achieved at the competitive prices obtainable can only continue to draw in fleet investors.
Having shown its mettle across all types of merchant vessel, including specialised and more complex tonnage, the industry is now set on generating higher added-value from its collective endeavour, and creating a stronger business platform for the future, by expanding the homegrown technological and design content.
At the same time, the delivery of a major cruise ship expresses a move to broaden the commercial reach still further. On a par in size, capacity and standard with the European-built product, the 324-metre Adora Magic City has signalled determination to break into what is generally regarded as the most prestigious field of civil vessel construction, a segment in which the European shipbuilding industry is supreme.
China’s entry to the international market for large, luxury cruise vessels, and the attendant plan to develop a fleet to meet vigorously expanding domestic demand, has been underpinned by foreign know-how input.
But growing self-reliance in all technical disciplines and
craft trades associated with tonnage of the sophistication and outfitting intensity of passenger ships, can be expected to give added dimension to Chinese production in the coming years, and provide global players in the cruise business with an alternative and lower-cost option to having vessels built in Europe. Capabilities have already been graphically illustrated by China’s rise as the most prominent world supplier of large ro-pax ferries, with European operators as the main customers.
For the drive on the cruise ship front, China State Shipbuilding Corporation (CSSC) and Anglo-American company Carnival Corporation formally inaugurated a joint venture in November 2018 under the name CSSC Carnival Cruise Shipping, wherein CSSC ranked as the majority shareholder.
The creation of the undertaking was accompanied by the finalisation of an agreement for two vessels, initially specified as sisterships of 135,500gt, to be built by Shanghai Waigaoqiao Shipbuilding and crafted for the Chinese market. The two-ship deal was valued at about $1.5bn, and provided CSSC Carnival Cruise Shipping with the option to extend the build programme in China by up to four more vessels.
A separate joint venture was established by CSSC and Italian international shipbuilding group Fincantieri to provide the technical foundation for the cruiseship newbuilds in China, encompassing a technology licence for the ship model platform and support to Shanghai Waigaoqiao throughout the build process. The new, diesel-electric ships were accordingly laid down based on the proven Vista-class
■ Chinese-built using a foreign template: the nascent secondof-class for Adora Cruises
design, multiple examples of which have been produced in Italy for various brands of the Carnival Group.
ABB supplied an integrated package, the per-ship delivery having included two Azipod propulsors, five gensets, main switchboards, distribution transformers, and propulsion controls. The shipbuilding contractor has clearly gained appreciably from working with a European electrical engineering group so prominent in developing and providing complete, complex systems to cruise vessels.
CSSC Carnival Cruise Shipping subsequently became Hong Kong-domiciled Adora Cruises, which brought the first of the newbuilds, Adora Magic City, into service at the beginning of 2024. Fitted with 2,125 cabins for an adjustable passenger complement of between 4,250 and 5,246, the Adora Magic City made her commercial debut with a sevenday voyage out of the Wusongku International Cruise Liner Terminal, a contemporaneous development in Shanghai’s Baoshan district.
Making of a magic city
Construction of the Adora Magic City represented a pronounced learning curve for Shanghai Waigaoqiao, with Fincantieri acting as technical consultant, and was conducted at a deliberately methodical pace—over-and-above the time impediment occasioned by the effect of the Covid pandemic on yard personnel and material supplies—so as to ensure understanding and minimise re-working.
Illustrative of Chinese application to knowledge acquisition, the planned construction period for the second ship has been shortened by eight months relative to the first vessel, notwithstanding the post-contract decision to increase overall length by 17.4 metres. The enlarged volume (resulting in a gross measurement of 141,900t) has allowed for 19 more passenger cabins, raising the total to 2,144.
Float-out of the Adora Flora City is scheduled for June 2026, with a view to delivery towards the end of that year. The ship’s 2027 itinerary is expected to start with a voyage from Guangzhou Nansha International Cruise Port in Guangdong.
China’s track record in luxury vessels goes back further with a smaller category of tonnage, the pioneering SunStone series of polar-class expedition-type cruise ships. China Merchants Heavy Industry (CMHI) delivered the first of the 80-passenger capacity, 104-metre Infinity class in 2019, and subsequent vessels followed at intervals through to 2023.
Through the nomination of an Ulstein design, the most distinctive feature of these ‘high-end’ cruise vessels is the Ulstein-developed X-Bow. To support the shipbuilder’s first foray into the cruise market, Bureau Veritas provided an extensive design review, including regulatory compliance, structural and stability analyses. During the build process, BV specialists assisted with project management and quality control issues.
The Infinity and Adora programmes, together with the growing export reference list for ro-pax ferries, denotes an increasing Chinese capacity to pair value-for-money with a high-grade product. This is drawing wider attention from overseas cruise ship operators. The fact that the premier European players in cruise vessel construction have orderbooks stretching into the 2030s, against the backcloth of buoyant market demand, could also play to the advantage of Chinese yards.
One dark cloud on the horizon, though, with possibly negative consequences for tonnage sourcing, stems from the report that the Trump administration is considering imposing levies on Chinese-built ships calling at US ports.
Among the factors contributing to the pre-eminence of the European shipbuilders in large, luxury cruise ships is the
DESIGN FOR PERFORMANCE
well-developed industrial eco-system, encompassing designers, outfitting subcontractors and trade skills, onboard systems, equipment and engineering, complemented by a policy of amply resourcing R&D and investing in innovation. Sustained European competitiveness is also a factor of project management capabilities and production control, vital not only in ensuring contractual performance, but in realising the requisite financial outcome for the yard.
In fact, the continuity of one of the industry’s most august players, the hitherto family-owned Meyer Werft, which has consistently ploughed earnings back into the business, has only been assured by public sector intervention. In September 2024, the German Federal Government and the state of Niedersachsen signed contracts giving them about 80% control of the cash-strapped shipbuilder.
Given the Italian and French state holdings in Fincantieri and Chantiers de l’Atlantique, respectively, national involvement in the organisations keeping Europe to the fore in luxury cruise ship construction has accordingly become even more substantive.
Market dynamics
China’s burgeoning middle class and increasing disposable income fuelled the growth of tourism until the Covid pandemic, when China ranked as the world’s second biggest source of cruise passengers. After a four-year hiatus, market recovery is now well in evidence, with passenger numbers reported to have increased by 15% in 2024. Domestic and international cruises constitute an ever-more popular choice of vacation, and the projections are for substantial year-onyear growth in demand.
In a newbuild context, it is inconceivable that China would seek to develop fleet capacity by ordering abroad. The nurturing of domestic capabilities in the design, production and outfitting of cruise vessels is thereby keyed not only to penetrating a high added-value sector of the global shipbuilding business, but also to meeting the home market’s evolution and realising economic benefit to the regions involved.
Chinese ambition as to the international market for luxury passenger ships is coloured by achievements to date in the large ro-pax ferry segment, which calls for particular capacities and strengths in the supplier network, the outfitting trades and project management, as well as the practical and design skills relating to complex shipboard systems.
Now the pre-eminent global force in ro-pax ferry, deepsea and short-sea ro-ro vessel construction, collectively a field that had at one time been a major business area for European yards, China has come close to annihilating the European competition. As elsewhere, Chinese wage and material costs are certainly rising, but so is the quality and contract performance afforded at a still significant price differential with Europe. Moreover, ro-pax production has come to embrace vessels of high technological standard.
The two most recent examples of Stena Ro-Ro’s E-Flexer series are a case in point, as multi-fuel, hybrid ferries incorporating the highest battery capacities to date together with bespoke internal design and configuration tuned to the long-term charterer’s requirements.
Stena RoRo has commended builder China Merchants Jinling Weihai for quality and delivery performance, befitting the fact that the tally of E-Flexer contracts has reached 15, all underpinned by long-run charters to operators in North Europe, the Mediterranean and Atlantic Canada. Commonality of many elements coupled with serial production, of course, bears on price competitiveness, and potentially on yield per ship for the yard.


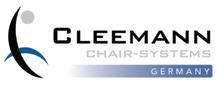
•Bilge water monitors & filtration
•Seals and bearings
•Dry dock services
•Underwater repairs
•Additives to prevent leakage


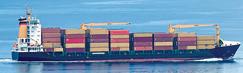







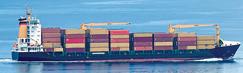
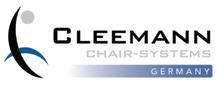

9 High quality upholstery with individual
9 Adjustable armrests
9
9 Infinitive
9
9
Tel: +49-2938-98769-0 info@chair-systems.com http://www.pilotchairs.com

To advertise here and online at www.motorship.com/ directory Call the Motorship Team on +44 1329 825335 sales@motorship.com
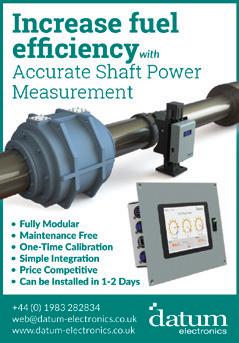
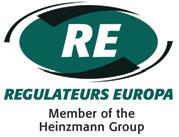
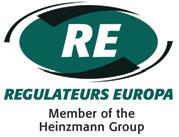
Maintaining the highest possible standards for our customers. Service, upgrades and retrofits.
● Governors / Actuators
●
● Support for all Viking based products and our new simple to install Viking352G upgrade pack (below)
● Spare parts & Service
● OEM quality overhauls and service exchange units
● Propulsion Controls
● Generator Controls
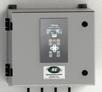
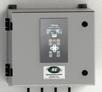
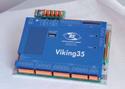
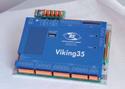


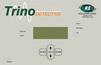
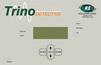
Regulateurs Europa Limited Port Lane, Colchester. CO1 2NX UK Phone +44 (0)1206 799556
Fax +44 (0)1206 792685Email sales@regulateurseuropa.comWeb www.regulateurseuropa.com
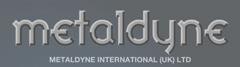
your
RIVERTRACE produces a range of products that meet and exceed the I.M.O. resolutions MEPC 107(49) and MEPC 108 (49) relating to water discharges from ships.
Torsional Vibration Dampers
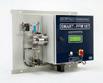

Maintenance and Repair of Crankshaft Torsional Viscous Vibration Dampers
Tel: +44 (0)1422 395106 Fax: +44 (0)1422 354432 davidwhitaker@metaldyne.com www.metaldyne.co.uk
Formerly Simpson Ind - Holset Dampers
Telephone: +44 (0) 1737 775500 Sales enquiries: sales@rivertrace.com www.rivertrace.com/en-gb/marine
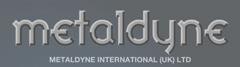

Torsional Vibration Dampers

Tel: +44 (0)1422 395106 Fax: +44 (0)1422 354432 davidwhitaker@metaldyne.com www.metaldyne.co.uk
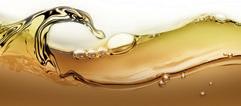

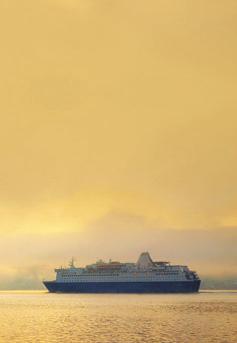


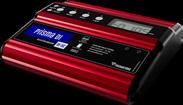
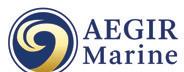
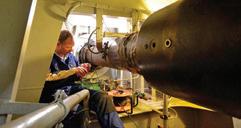

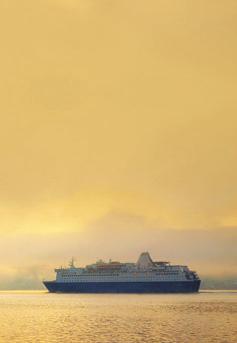
Maintenance and Repair of Crankshaft Torsional Viscous Vibration Dampers
Formerly Simpson Ind - Holset Dampers Is your damper providing engine protection?
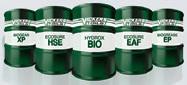
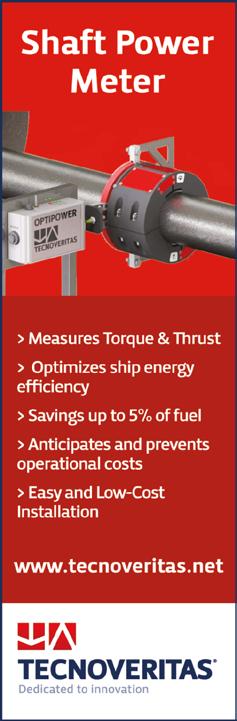

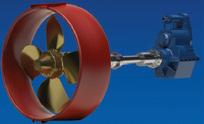
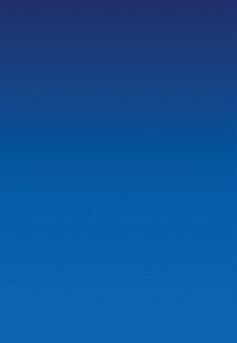
enough to handle it Small enough to care
Your Ship Repair Yard in Lisbon
Estaleiro da Rocha Conde de Óbidos 1399 –036 Lisboa –PORTUGAL
Tel. Yard (+ 351) 213 915 900 www.navalrocha.com navalrocha@navalrocha.pt

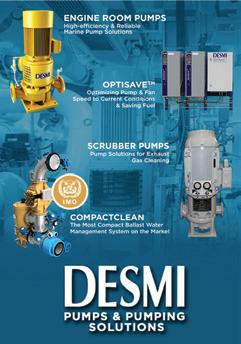
High quality underwater repairs
Hydrex offers underwater repair solutions to shipowners around the globe. Our experienced teams are qualified to perform all class-approved repair procedures in even the harshest conditions.
Hydrex headquarters
Phone: +32 3 213 53 00 (24/7) E-mail:hydrex@hydrex.be www.hydrex.be
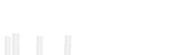
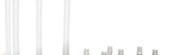

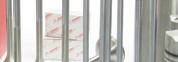
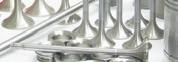
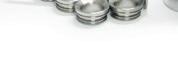
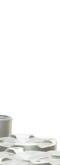
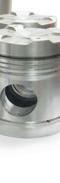
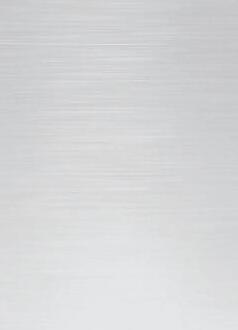
Hermann-Blohm-Str. 1 · D-20457 Hamburg Phone +49 40 317710-0 · Fax +49 40 311598 E-mail info@nds-marine.com www.nds-marine.com

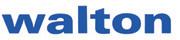
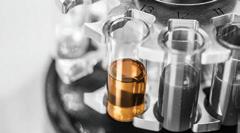

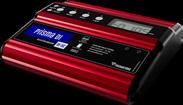

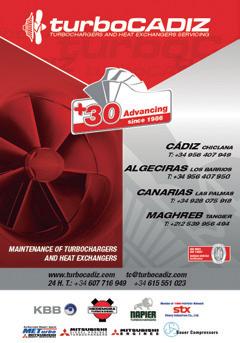


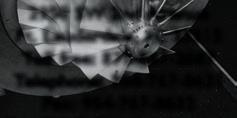
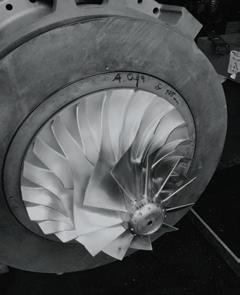


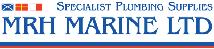
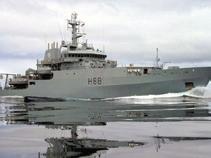
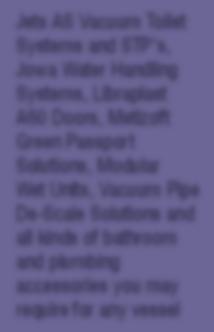
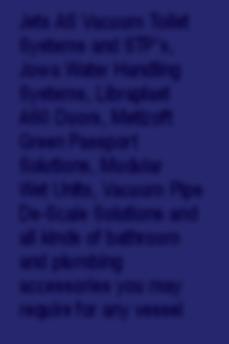

TRAINS ONBOARD SHIP
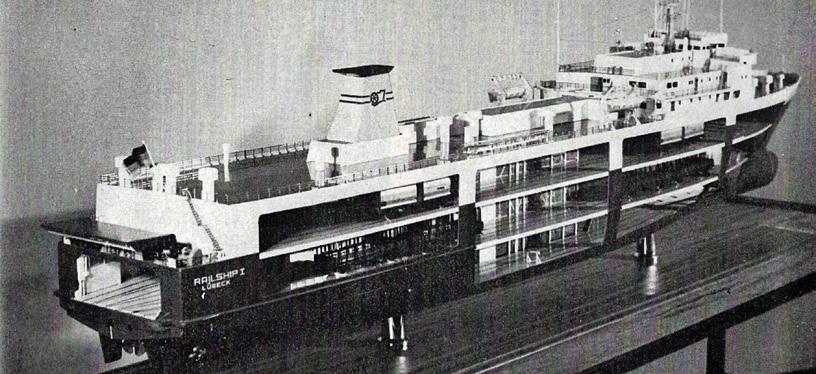
During the 1970s shortages in oil supply, imposed in part by high prices and in part by the producing countries, there had been much speculation about the future of the large oil tanker.
However, the March 1975 issue of The Motor Ship took a positive view, confirmed in a report by consultant Eggar Forrester. Both felt that as the producers had achieved their aims in production and price levels, they would turn attention towards shipping the oil and building refineries. This would result in changes to the tanker industry, in that rather than moving large quantities of crude oil, product tankers would grow both more numerous and larger. 150,000 dwt product tankers were seen as a distinct possibility, but in order for such vessels to be viable, there were challenges to be overcome in terms of tank coatings and cargo handling. And reopening of the Suez Canal should being about a new breed of tanker, the so-called ‘Suezmax’.
The main ship description concerned a ship type that is uncommon in today’s industry – a train ferry. A consortium of German, Swiss and Finnish rail companies had commissioned, from the Rickmers yard, a 6,000gt rail ferry, Railship 1, said to be the largest of its type. With three cargo decks, up to 60 rail wagons could be loaded through the stern door via a five track link span. Wagons were transferred from lower to upper decks by hydraulic lifts. One problem was differing rail gauges between the European and Finnish systems, overcome by changing the wheels on the wider Finnish wagons, a common practice on through international freight. Six specially-designed diesel shunting locomotives were carried on board Railship 1. With such heavy cargo, a sophisticated trim and heel system was provided.
For such a novel ship, its machinery was relatively conventional. Main engines were four MaK 8M51AK medium speed units, each rated 5,000 bhp, driving two Lips CP propellers. Total investment in the project was said to be in the order of DM 85m (£15.4m), much of which went into the shore facilities at Travemunde and Hanko. Whether the venture would prove viable was unknown – but if the ship failed as a rail venture, there was the possibility of converting it to carry road vehicles.
A second rail-owned ferry featured in the March
1975 issue, this being St Edmund, a ro-ro freight vessel for the Sealink Harwich-Hook of Holland service. The 131m long ship was the largest in the British Rail fleet, and the first to be powered by Stork-Werkspoor main engines, most of the others relying on Pielstick power.
On the machinery side, it was reported that the ‘3 Maj’ works in the former republic of Yugoslavia had reached a total output of 1m bhp of Sulzer engine. Sulzer had granted 3 Maj the licence in 1954 for low-speed two-stroke RD type engines. The first, delivered in 1961, was a 7,800 bhp 6RD76, for a Polish cargo vessel. By the end of 1974, 88 engines had been completed, with a Russian order for a 6RND90, due to be delivered in April 1975, reaching the 1m bhp milestone. Future prospects looked good, with the works being capable of building later Sulzer RND-M designs, including the largest version, the RND105M. Alongside the Sulzer production, the plant undertook various machining work for outside customers, and the parent company had taken on a licence for SEMT Pielstick, with the first, a pair of 12PC3 engines, to be built at 3 Maj.
Beside the engine works, the 3Maj shipyard had seen expansion, allowing a production line process for building blocks, with numerically controlled machinery.

The international magazine for senior marine engineers
EDITORIAL & CONTENT
Editor: David Stevenson dstevenson@mercatormedia.com
Correspondents
Please contact our correspondents at editor@motorship.com
Bill Thomson, David Tinsley, Wendy Laursen
SALES & MARKETING
Brand manager: Sue Stevens sstevens@mercatormedia.com Tel: +44 1329 825335
Production
David Blake, Paul Dunnington production@mercatormedia.com
EXECUTIVE
Chief Executive: Andrew Webster awebster@mercatormedia.com
TMS magazine is published bi-monthly by Mercator Media Limited Spinnaker House, Waterside Gardens, Fareham, Hampshire PO16 8SD, UK
t +44 1329 825335 f +44 1329 550192
info@mercatormedia.com www.mercatormedia.com
Subscriptions: Register and Subscribe at www.motorship.com
Annual subscriptions from: £248.00 Single user: Full online access to The Motorship with digital magazine issues.
For multi-user access: Subscriptions@mercatormedia.com
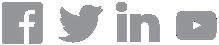
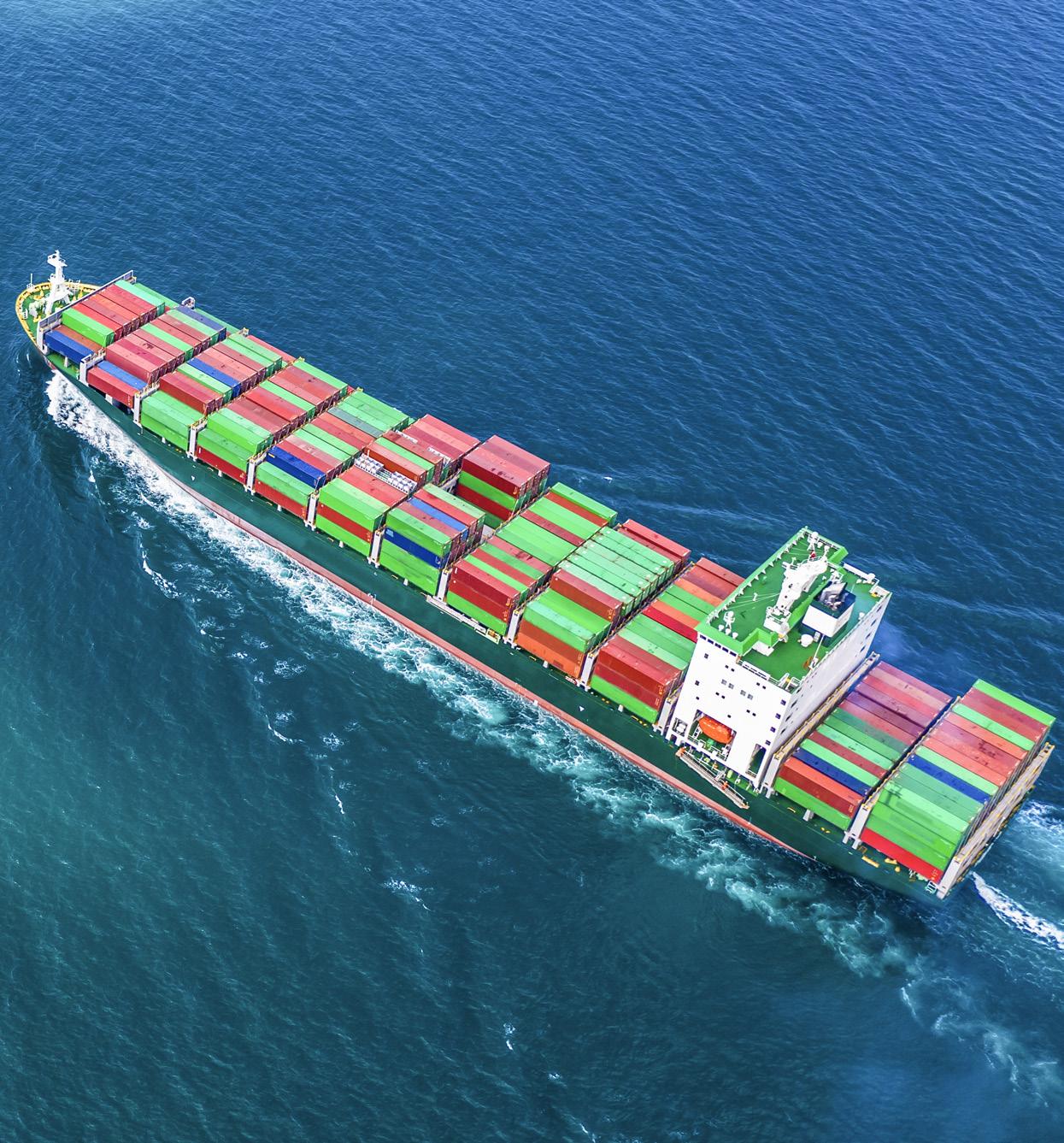
7 – 9 October 2025
Kobe, Japan
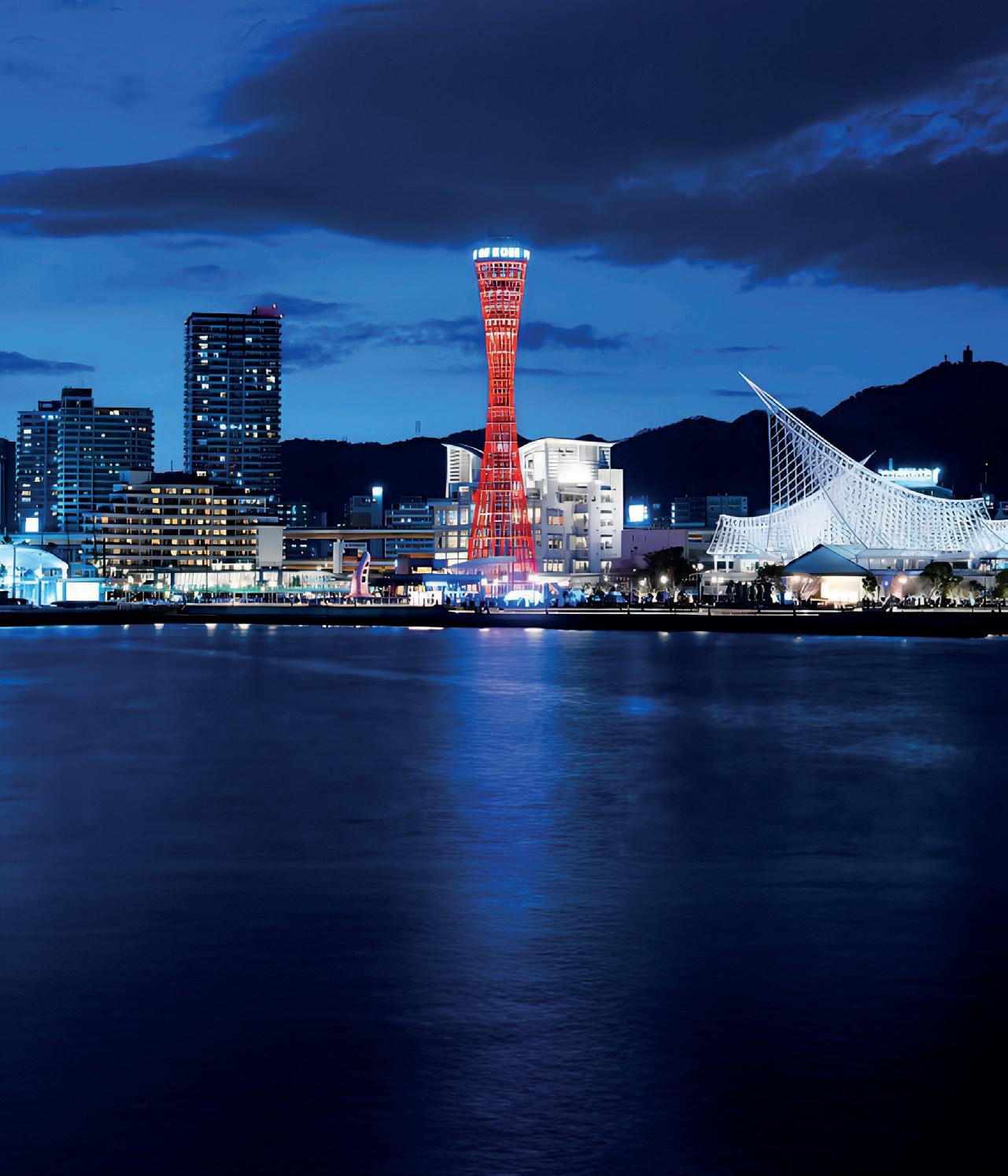
BOOK NOW
As the Association celebrates its seventieth anniversary, IAPH looks forward to welcoming you to Japan and the city of Kobe, where its roots can be found. Following the symbolic idea of establishing world peace through world trade, and world trade through world ports, this 70th annual meeting at the #IAPH2025 World Ports Conference will reunite global port leaders with their counterparts from policy makers, financial institutions, ship and cargo owners, and service providers, delivering a forum for networking, knowledge sharing and debate.
To secure your delegate place or further information on attending/sponsoring contact the events team:
visit: worldportsconference.com contact: +44 1329 825335 or email: wpc@mercatormedia.com #IAPH2025