
15 minute read
Glycerol and tribology
GLYCEROL IS A PROMISING BASE FOR SUSTAINABLE LUBRICANTS
Speaking at the 23rd International Colloquium Tribology in January 2022, Dr Roland Larsson of Luleå University of Technology, Sweden, highlighted the potential of glycerol as a new, sustainable lubricant base
Currently over 1.5m3 of lubricant is manufactured per second around the world. In most cases, crude oil is used as the lubricant base. It provides appropriate viscosity at reasonable cost, and it is available in large quantities.
However, there are some drawbacks with oil. It is flammable, difficult to clean, slow to degrade, and toxic to some plants and animals. It has been estimated that approximately 50% of all lubricants sold worldwide end up in the environment via total loss applications, volatility, spills or accidents.
A rethink of petroleum-based lubricants is required, because they are not sustainable. Base stocks will slowly disappear, and their cost may become prohibitive. Customers may no longer wish to buy fossil products, and legislation may stop them from using them.
Therefore, the need for fossil-free lubricants will increase in the future. The need for sustainability will make it necessary to find new products, and so a new optimal lubricant formulation will be required.
When considering a new lubricant base, tribologists need to consider the tribo-optimisation of the whole system – not just the lubricant itself. Performance must be balanced between performance and cost, and sustainability or circularity is now an unavoidable goal. This may mean that, initially at least, sustainability becomes more important to what is optimal than price or performance.
Finding a new optimum for lubricant performance may therefore initially result in lower performance or higher costs as design strategies mature. For example, a more robust component may have a slightly higher weight, so energy consumption during manufacturing and operation will increase. This might be acceptable if the component doesn’t need replacement or if it can be reused. Both suppliers and customers aim for “eternal service life” but an optimal design may not be “design to the limit” and this creates milder triboconditions for a new lubrication to endure.
What are the options for renewable lubricant bases? We could re-condition oils, or find bio-based oils (rapeseed, sunflower), or other fossil-free alternatives, including water. We could use coatings and surface treatments instead of lubrication. But, why not do what has been done in the paint industry for many years? That is, use water-based or watersoluble lubricants.
One advantage of water-based lubricants is that there are many biomass base stock candidates to choose from. Water solubility also makes them easier to disperse in ground and water and makes it easier to keep surfaces and machines clean.
For myself and my colleagues in Division of Machine Elements at Luleå, Dr Marcus Björling, Dr Yijun Shi, and Dr Anders Pettersson, glycerol (C3H8O3) is a promising choice. It is non-toxic, water soluble, odourless, colourless, and
8 The high
performance of mineral oil-based lubricants’ lubricant fi lm properties will be challenging
generally obtained from renewable plant and animal sources where it occurs as triglycerides. It is fire-resistant if mixed with 10-20% water, and the addition of water changes the freezing point so that a wide range of viscosities can be achieved.
By adding different amounts of water, the viscosity of glycerol can be tuned to any viscosity between pure water (1 mPas) to pure glycerol (1400 mPas). Normal lubricants are around 10-300 mPas (depending on temperature), so the viscosities widely in use today can easily be achieved. Mixing water with glycerol also lowers the pour point. With some 30% water, it can be lowered to -50oC or lower.
Glycerol has a density if 1261 kg/m3 (compared to oil’s 900kg/m3). It has a melting point of 17.8°C and a boiling point of 290°C. Viscosity is 1.412 Pas @ 20°C, and heat capacity is approximately 2400 J/kg/K. It has a thermal conductivity of 0.28 W/m/K (compared to oil’s 0.15W/m/K) and a pressureviscosity of 4.7 GPa-1 (compared to oil’s 18GPa-1). Its bulk modulus is 4.5 GPa (compared to 1.3 for oil and 2.2 for water).
Glycerol’s antimicrobial and antiviral properties mean it is widely used in wound and burn treatments. It is also widely used as a sweetener in the food industry (additive E422) and as a humectant in pharmaceutical formulations.
One interesting and already commercially available source of glycerol is waste from bio-diesel production. One kilogram of glycerol is generated for every 10kg of bio-diesel produced. Biodiesel production has grown, and as glycerol is a waste by-product from that production, suddenly, we had much more glycerol available. It is even cheaper than oil sometimes.
If glycerol is so promising, why hasn't it been used before now? One main reason is the vast availability of oils. Oils are cheap and are produced in large amounts, and they are good lubricants. So, industry has got used to them, and as lubricants are normally just there to make a machine function, nobody is inspired to change something that actually works well and can be trusted. But if oil cannot be used due to legislation, cost, environment, and sustainability, we run into a problem, and glycerol could be one important solution.
There will be challenges for tribologists to solve as we explore the potential of glycerol-based lubricants. Surfactants will be required, as will rust inhibitors and antifoaming agents. All these additives will need to be non-toxic and renewable, like the glycerol base they will be added to.
Glycerol has three times lower friction than rapeseed oil and five times lower friction than mineral oil. This will create engineering challenges that could be compensated for by making surfaces smoother. One important feature of glycerol and other water-based lubricants is that they do not have the same pressure-thickening effect as mineral oils. A mineral oil becomes extremely viscous (or even solid) when it experiences the extreme contact pressures found in a rolling bearing or in a gearbox. For friction, that is an advantage for glycerol. If you can maintain full separation of the surfaces, you then also get much lower friction than for an oil, as much as five times lower.
On the other hand, keeping surfaces apart from each other becomes trickier, since oil’s pressure-thickening effect helps to form a good lubricant film, separating the surfaces. Glycerol only achieves half the film thickness of oils. It may be necessary to increase its nominal viscosity and make the fluid 2.5 times thicker from the start. Another option is to make the components bigger, although this is a problematic option, of course.
New water-soluble additive technology would be required for glycerol to satisfy boundary lubrication requirements. Otherwise, the surface irregularities come into contact with each other and wear may occur.
Tribo-chemistry has evolved over a long time to produce the additives we have today for oil-based lubricants. (Oil additives been developed over 100 years with enormous budgets.) These compounds interact with surfaces and form protective layers that lower the wear rate and the friction when surfaces are in contact with each other. Similar additives are being developed for glycerol, but that journey has only just started. Therefore, this is a future research area of great importance.
Glycerol-water mixtures are not good for high-temperature applications such as engines, because the water will evaporate. However, they would work well for hydraulic systems onboard ships and perhaps for many of the rotating parts, especially those that may leak lubricant to the water, including stern tube bearings and propeller shaft bearings. Additionally, any total loss application is suitable for the glycerol including saw-chain lubricants, rail lubricants, and cutting fluids.
At Luleå, will continue to improve glycerol’s performance under more severe conditions, including its boundary lubrication properties. At the moment, we are learning about its performance for gearboxes. We believe we can reduce lubricant losses in the gear, but we need to watch out for the potentially higher risk of wear, pitting, or scuffing. We are also working to develop a good hydraulic fluid that can be used in mobile machines that operate in sensitive environments such as forestry, marine, and farming.
When mineral oils can no longer be used as lubricants, we will see many different alternatives emerge. Natural oils will be used. Synthetic oils will be made, even electro-fluids (oils made from a carbon source and a green hydrogen source). These alternatives are still very expensive, making glycerol particularly promising.
Tribologists are facing a very exciting future!
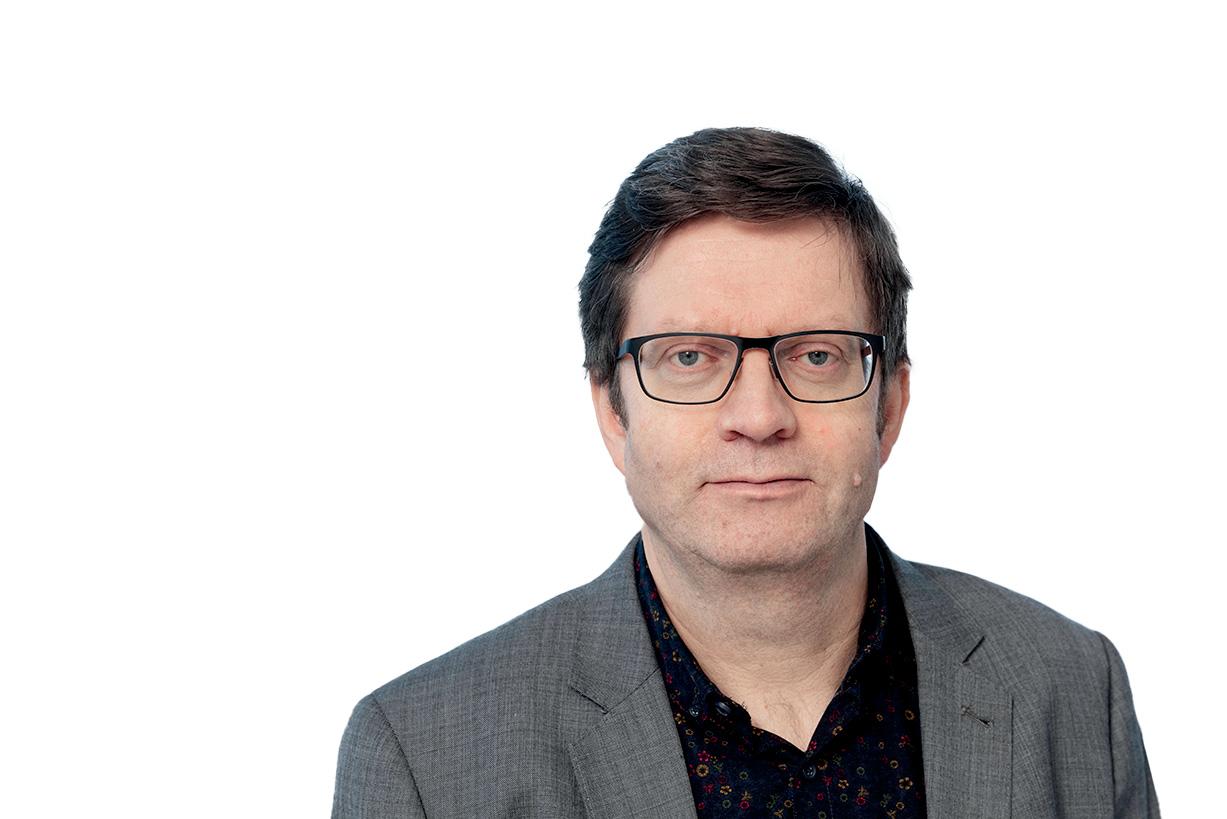
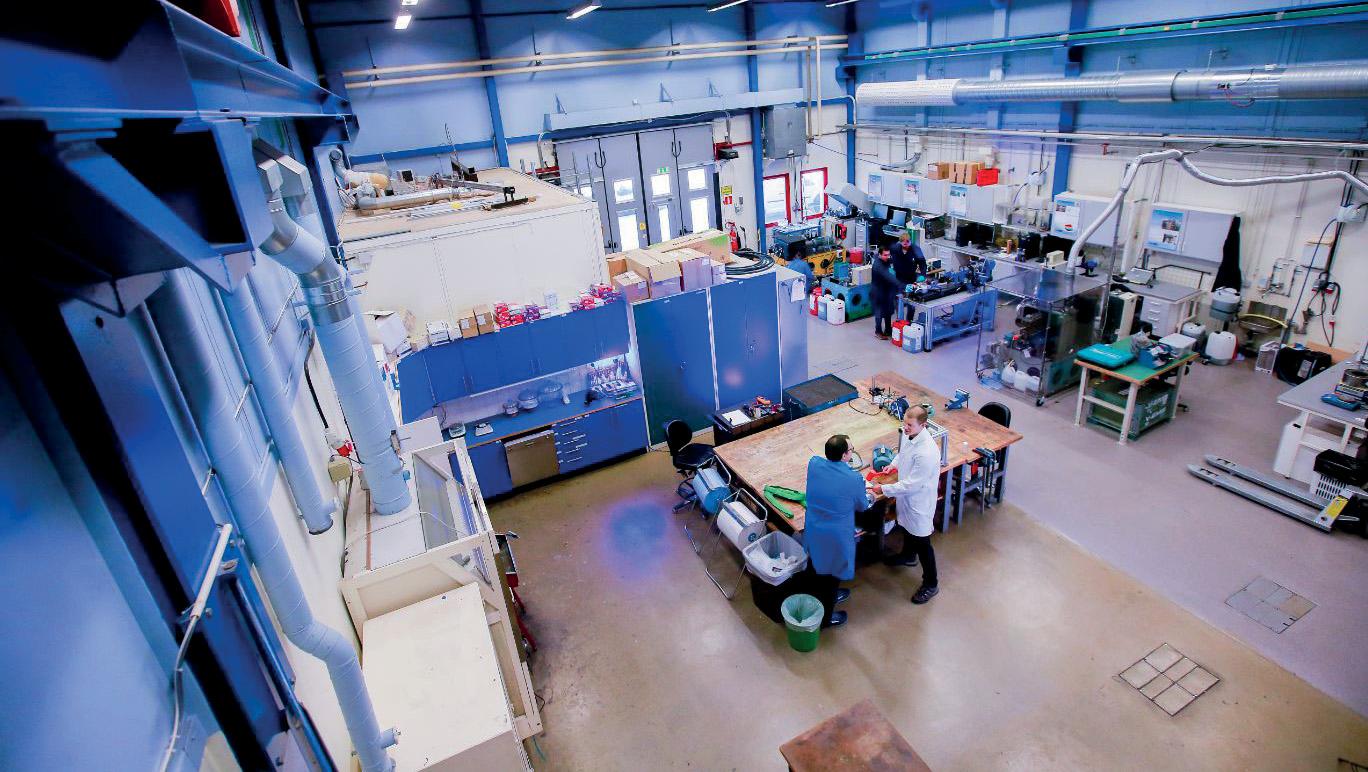
8 New water-
soluble additive technology would be required for glycerol to satisfy boundary lubrication requirements
8 Roland Larsson
TIME TO RETHINK OPTIMISATION OF LUBRICANTS
Industry’s focus on reducing GHG emissions paves the way for the development of environmentally friendly lubricants and a new strategy to reduce friction at a time when traditional oil-based lubricant development has achieved high enough performance to stifl e further innovation, says Prof. Dr Denis Mazuyer, a professor in tribology at the École Centrale de Lyon, France
It’s an opportunity, he says, to develop new lubricants and new surfaces. Through the IMOTEP project, Mazuyer works on the development of both oil-based and promising environmentally-friendly water-based lubricants with the ultimate aim of improving energy dissipation due to friction. IMOTEP (Clean Engine Innovation) is a project funded by the French agency for the environment and energy management (Ademe) in collaboration with manufacturers such as HEF, PSA, and Total. Underway since 2017, the participants conduct research by coupling new coatings, new surface patterns and new lubricating molecules formulation to improve the effi ciency of internal combustion engines used in cars and of any other mechanical components.
Water-based lubricants typically combine water with compounds such as polymers that act as surfactants. Water has a cooling effect within the lubricant, so the performance of a machine or component can sometimes be enhanced by operating at higher temperatures. Generally, though, the different properties of water compared to traditional oilbased lubricants means their performance needs to be enhanced. The aim is to reduce friction and therefore control energy dissipation in, for example, engine components.
“Usually, hydrocarbon lubricants can support very high pressures due to their high viscosity – sometimes up to 30,000 times that of ambient pressure. With water, that’s not possible,” says Mazuyer. “If we want to move to sustainable lubricants based on water, we have to change the process to enable water to support these very high pressures. We can use polymers to form surface layers to help achieve that.”
Another aspect of tribology that holds promise for enhancing the performance of water-based lubricants is surface texturing. Through the university’s Laboratory of Tribology and System Dynamics, Mazuyer is able to use laser surface texture techniques to create effects at the nano scale, effects often based on biomimicry of properties found in nature. He is also able to map the impact of those surfaces at that scale – which essentially equates to the size of individual large polymer molecules.
“This is one of the very important challenges in tribology. If you want to see or control the effects of surface texturing on the friction force and friction dissipation, you have to change the surface at scales much finer than micrometres. That’s why we have developed new experimental techniques and new models and simulations to explore lubricant performance at the nanoscale.”
The laboratory, which has been building research capability for 30 years, is able to support lubricant development at pressures and velocities suitable for a wide range of applications, including marine engines and other shipboard equipment. The laboratory includes elastohydrodynamic machine that operates at high pressure and enables chemical analysis of the contact between surface and lubricant.
Mazuyer notes that the equipment he uses is capable of taking laboratory-scale developments to industrial or semiindustrial scale testing. Varying speed over 11 decades (from 0.01 nm/s to 1 m/s) and controlling the evolution of the load with time, including loads up to several thousand Newtons in less than a millisecond enables the research team to make a unique in situ analysis of contacts in all lubrication regimes. Thus the manufacturers will be able to validate their concepts for materials, surface treatments and lubricant formulations team for optimizing energy dissipation in all types of lubricated contact
Speaking at the 23rd International Colloquium Tribology in January 2022, Mazuyer detailed the IMOTEP research capabilities: 5 The simultaneous measurement of interfacial film rheology (viscoelasticity under pressure), film thickness and contact forces at high resolution (10nN and 0.01nm); 5 The accurate control of contact kinematics, the simultaneous measurement of contact forces and film thickness distribution as well as chemical analysis of the convergent and high-pressure zones by IR spectroscopy and contact visualization; 5 The measurement of friction torque, film thickness, temperature, and position, control of velocity, shaft alignment and stability characterization in a lab-scale bearing.
The laboratory’s primary experimental capabilities include original tribometers, rotating machinery dynamics, contact fatigue, high-performance procedures, bio-engineering of living tissues, technical analyses of surfaces and materials, microscopes, simulators, and vibration test rigs.
The laboratory has over 350 staff and, as well as studying tribology, its researchers study structure and system dynamics (control of vibrations, control of system stability and mechanical parts), the mechanics of materials and processes (behaviour of materials and living tissues in relation to their microstructure, computational mechanics of surfaces) and geomaterials (structural and edifice analysis, soil mechanics).
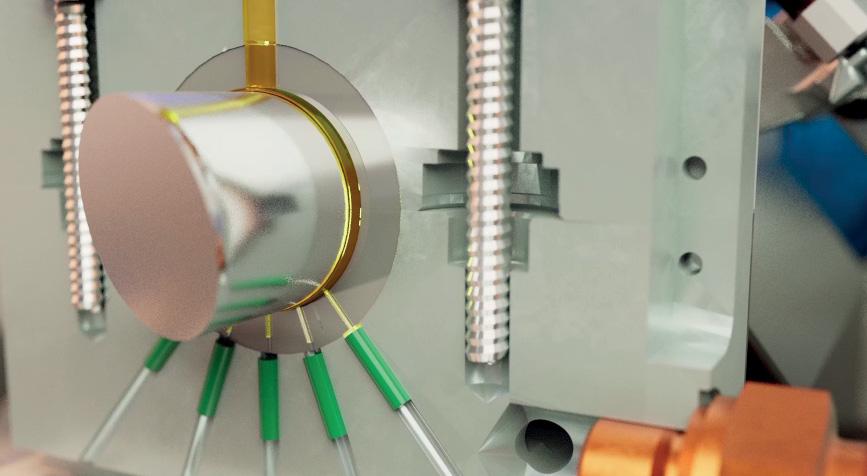
8 Research into
water-based lubricants is being stimulated by pressure to reduce GHG emissions from traditional lubricants
Marcus Schaerer, GM Technical & Services, Shell Marine discusses how next generation lubricants and technology will be needed to meet the transition
Shipping faces a difficult challenge. It must meet demands of the world’s growing population while radically reducing its own emissions. To do this, it must accelerate change to unlock a lower-carbon and more
efficient future.
Yet, its transition will not be easy. With alternative fuels critical for the marine energy transition, adjusting to a mosaic of fuels will undoubtedly impact the requirements of lubrication development, as well as how ship owners approach their lubrication requirements.
How will alternative fuels impact lubrication practices?
The emergence of future fuels will not alter the core role of lubricants – to prevent corrosive, adhesive, or abrasive wear and cleanliness. However, they are expected to increase the complexity of this role, since alternative fuels may contribute to an operating environment that demands lubricants with different qualities, such as increased detergency and improved thermal stability.
This uncertainty is leading to challenges along the whole value chain, from research & development and product approval to the availability of components and supply chain capabilities – all of which need to be carefully managed to avoid disruption.
At the same time, many will argue that internal combustion engines will persist in shipping for many years to come, especially for vessels of 2,000 deadweight tonnage (dwt) and above, and considering a strong order book for a new fleet with two-stroke and four-stroke engines.
We also know that dual fuel engines are becoming more common, requiring lubricant manufacturers to develop more flexible solutions that can be used effectively whether LNG, diesel or fuel sharing modes.
Coordination and cooperation: the value of productive ecosystems
To prepare for this alternative fuels future, manufacturers and operators must work together to review lubrication strategy. Firstly, to ensure that marine lubricants and associated technical or digital services continue to add value, but increasingly, so they can help the maritime value chain work towards its sustainability goals.
But to develop effective new products, we first need to understand how the sector is adapting their practices and decision making in response to the evolving regulatory, economic, and operational climate.
That’s why it’s so important for lubricant manufacturers, like Shell, to work together with both the customers who are facing a tougher operating environment, and the OEMs who are developing higher efficiency engines as a result.
Why intelligent monitoring is key to understanding complexity
OEMs are offering new design and retrofit options that allow operators to use a wide range of fuels. And while every engine-fuel combination has its own challenges, several common factors are driving lubricant developments, such as increased thermal stress and a higher risk of deposit build-up – all of which are underpinned by a need for optimal cleanliness performance.
To meet this need, detailed monitoring of specific engine performance markers and characteristics is critical. Because, whether loading, contamination, wear debris, or lubrication (i.e., lack of base number) related, most machinery failures can in fact be avoided by regular sampling and structured data management.
It is why manufacturers are aligned on the need for constant lubrication monitoring to establish baselines that can help operators react to changes immediately. Engine monitoring programmes, such as Shell LubeMonitor and Shell VitalyX, therefore become a key piece of the modern operator’s toolkit in adapting to the alternative fuel evolution.
Previously, operators may have felt compelled to focus on reducing cylinder
LUBRICATION WILL PLAY A KEY ROLE IN DECARBONISATION
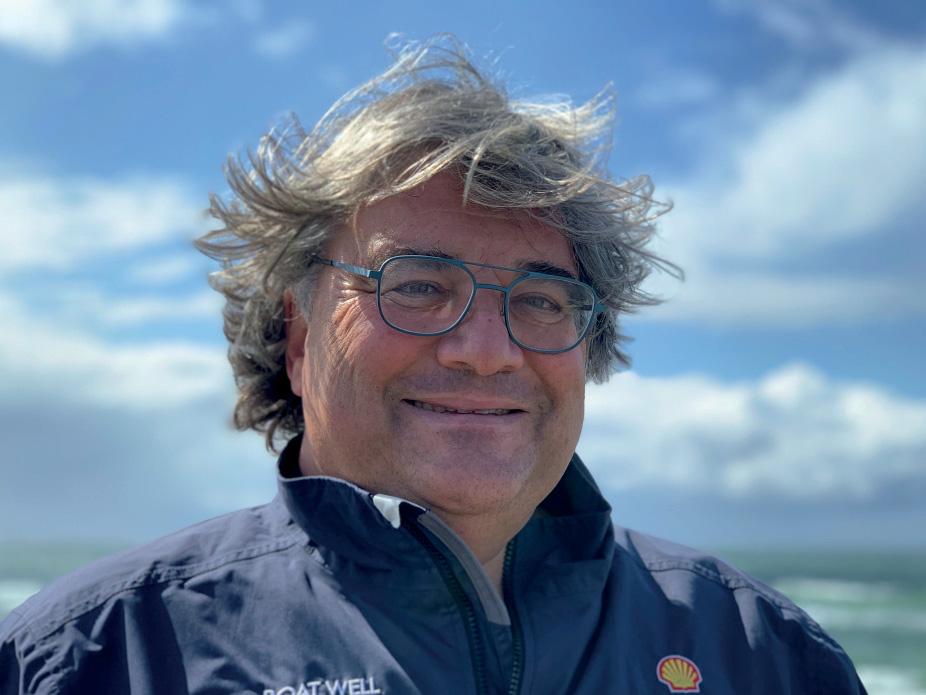
lubrication feed rates despite potentially risking engine performance. Direct monitoring tools like Shell LubeMonitor, however, use both onboard and onshore tests to help identify the lowest possible feed rate and optimum wear rate combination, helping save time and money.
Meanwhile, Shell VitalyX combines the industrial internet of things with artificial intelligence to present insights based on real-time sensor data. In turn, operators are provided predictive information, so they can make proactive decisions on maintenance planning while extending equipment life.
Set a course now or risk falling behind
Shipping's energy transition will have a profound impact on the industry with difficult challenges to navigate, and clearly, collaboration throughout the value chain will be needed.
For lubricant manufacturers, this means working with stakeholders to develop solutions that can unlock efficiencies in the engine room today, while developing marine lubricants which help maintain optimal engine performance and lower costs long term.
And for marine operators, not only must these next-generation lubricants become a vital part of the maintenance toolkit, but the sector must shift from traditional “cylinder condition monitoring” programmes to integrated, real-time engine monitoring programmes.
This will allow the sector to prepare for its decarbonisation journey, regardless of which fuels emerge to drive shipping forward.