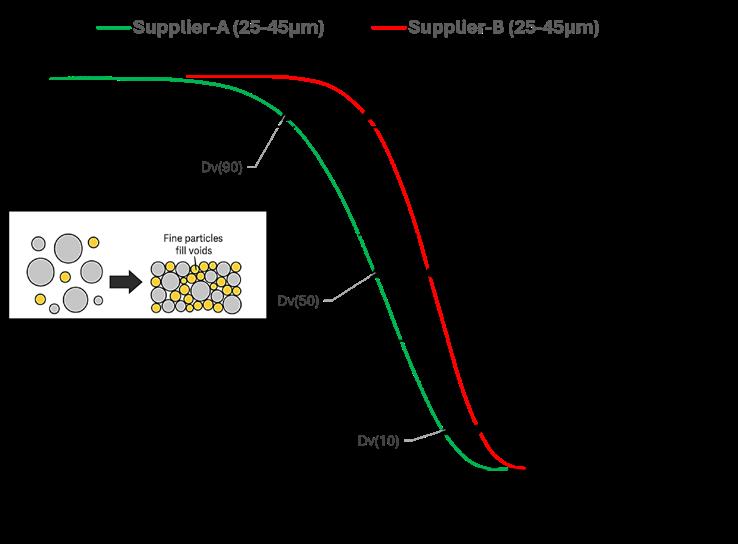
2 minute read
FEATURE – Advances in Additive Manufacturing
2.0 The Packing Puzzle: Particle Size Matters
A key variable influencing layer density is PSD. It is well known that a broader PSD—where smaller particles fill the gaps between larger ones—can improve packing efficiency. However, it’s a delicate balance: too many fines can lead to increased agglomeration, reducing flowability, while too few fines result in a loose and porous layer.
Using cumulative distribution analysis and powder-bed capsule tests, we found that an optimal level of fine particles (around 30% by weight) was necessary to achieve stable, dense packing (Fig. 3). Powders below this threshold exhibited reduced packing density and an increase in both surface and internal defects. Notably, morphology alone did not predict performance. While Supplier B’s powder was more spherical (55.49% highly spherical compared to 42.57% for Supplier A), it had a narrower PSD, resulting in lower powder-bed layer density.
Figure 3: Cumulative particle size distribution (PSD) curves for Ti-6Al4V powders from Suppliers A and B in the 25–45 µm range. Supplier A exhibits a broader PSD with a higher proportion of fine particles (Dv(10) = 27.3 µm) and a larger maximum size (Dv(90) = 44.6 µm), enabling more efficient packing. In contrast, Supplier B's narrower PSD (Dv(10) = 30.4 µm, Dv(90) = 41.3 µm) leads to lower powder-bed layer density, despite similar Dv(50) values (~37 µm).
3.0 Measuring the Invisible: The Powder Capsule Method
So, how can manufacturers measure powder-bed layer density during builds? We combined the powder-bed capsule approach, proposed by researchers at the National Institute of Standards and Technology (USA) [2], with micro-computed tomography (micro-CT) to measure the powder-bed layer density. During PBF-LB/M, the internal cavity in the capsule traps powder during each layer's spread. After the build, we tap the capsule as per ASTM Standard B527-22 [3] and measure the cavity volume in the capsule using micro-CT. Then, we empty the powder and determine the total internal volume of the capsule. Finally, we calculate the average powder-bed layer density and tap density. The procedure is shown in Fig. 4.
This in-situ method proved far more informative than traditional tap density or flowability measurements. Critically, despite similar tap densities (~2.9 g/cm³), the actual layer densities differed significantly.
Our findings suggest that powder-bed layer density should be a primary selection metric, not an afterthought. For PBF-LB of
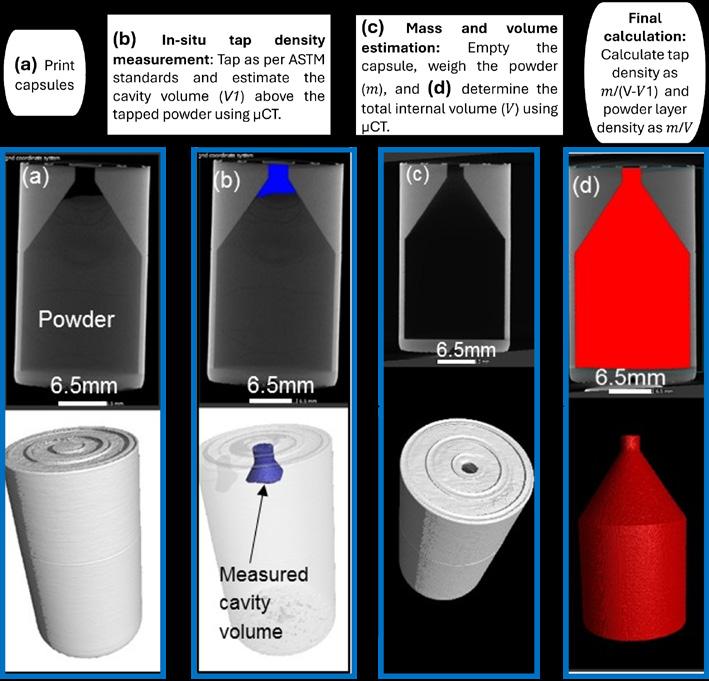
Figure 4: Schematic of the powder-bed capsule method for measuring insitu powder layer and tap density. (a) Capsules are printed with powder. (b) The tapped cavity volume (V₁) is estimated using μCT. (c) After weighing the powder (m) and measuring total volume (V), (d) tap and layer densities are calculated as m/(V–V₁) and m/V, respectively.
Ti-6Al-4V, we propose a benchmark powder-bed layer density of at least 65% of the theoretical density (4.43 g/cm³) as the minimum requirement for quality builds in SLM Solutions® systems.
4.0 What About Defects?
The link between poor powder packing and defect formation is clear. Samples printed with lower powder-bed layer density showed more and larger pores, particularly elongated ones near the part surface. These defects, mostly associated with insufficient fusion and poor melt pool stability, contributed to reduced tensile strength and ductility.
Importantly, powder characteristics—not just machine parameters—were the root cause. Our research found that, under identical print conditions, changing the powder—even when it had a similar tap density—significantly altered both the defect density and type.
5.0 Practical Takeaways for the AM Community
For metal powder suppliers and metal AM part producers, particularly in sectors like aerospace, biomedical, and defense, where part quality is critical, our research offers a fresh perspective on virgin powder selection. Additionally, as powder reuse and cost reduction become increasingly important, understanding how powders perform across multiple recycles, suppliers, and spreaders will be essential
• Denser layers, better parts
Achieving a high and uniform powder-bed layer density across the build area is critical for quality builds. A powder that appears ideal under a scanning electron microscope may not necessarily result in a high powder-bed layer density—often, it does not