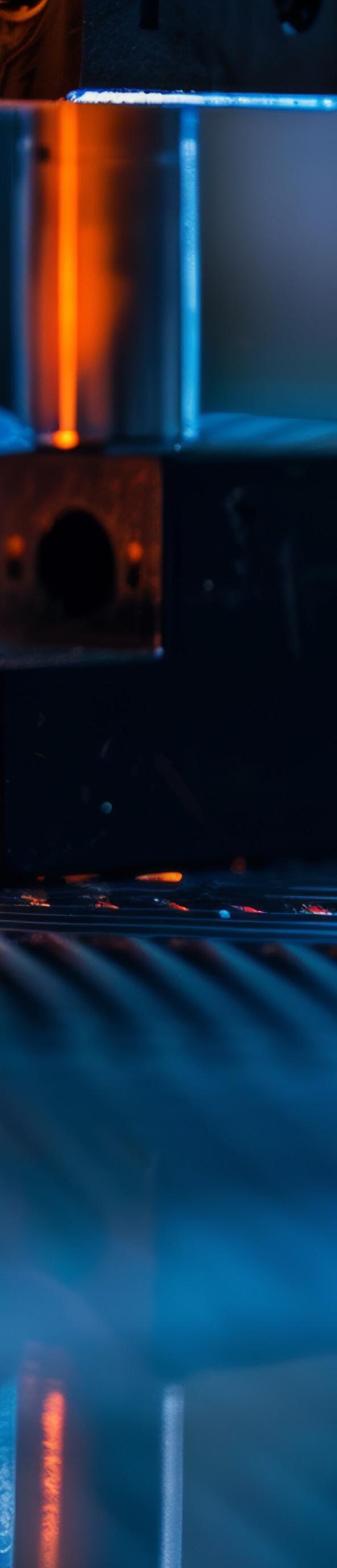
2 minute read
The Additive Revolution: Transforming Manufacturing Layer by Layer
Additive manufacturing, more commonly known as 3D printing, is reshaping the industrial landscape. Once a tool for rapid prototyping, AM now stands at the heart of innovation in aerospace, healthcare, automotive, and construction, offering unmatched design freedom, material efficiency, and customisation.
In an era where customisation and sustainability dominate industrial discourse, additive manufacturing has emerged as a cornerstone of modern production. By 2030, the global additive manufacturing market is projected to reach US$84 billion, driven by its ability to create complex, lightweight components and streamline supply chains.
From 3D-printed rocket engines to patient-specific medical implants, this technology is redefining what’s possible in manufacturing. Australia, with its thriving research ecosystem and strategic industry partnerships, is playing a pivotal role in this technological evolution.
What is Additive Manufacturing?
Manufacturing has always been about turning ideas into objects, but the methods have evolved dramatically. Traditional manufacturing is largely subtractive— cutting, drilling, or milling away material to achieve the desired shape.
Additive manufacturing, by contrast, builds objects layer by layer from digital models, using metals, polymers, ceramics, or composites. This fundamental shift enables the creation of complex geometries, reduces waste, and allows for on-demand, localised production. As global supply chains face increased scrutiny for resilience and sustainability, AM is rapidly moving from the periphery to the core of advanced manufacturing.
At its core, additive manufacturing is a process where digital designs are translated into physical objects by depositing material layer upon layer. The technology encompasses several methods, including Stereolithography (SLA), Fused Deposition Modelling (FDM), Selective Laser Sintering (SLS), and Direct Metal Laser Sintering (DMLS), each with distinct advantages for different materials and applications. While the technical details differ, the underlying principle is the same: material is added, not removed, to create a finished part.
This approach allows for unprecedented design flexibility, enabling engineers to create structures that are lighter, stronger, and more intricate than those possible with traditional techniques. It also supports mass customisation, making it ideal for applications such as patientspecific medical implants or bespoke aerospace components.
A Brief History of Breakthroughs
Early Ideation and Foundations
The conceptual roots of additive manufacturing reach back further than many realise. In 1859, François Willème, a French photo sculptor, pioneered 3D scanning by photographing objects from multiple angles—a precursor to the digital modelling essential in today’s additive manufacturing workflows.
By 1892, Joseph E. Blanther had filed a patent for creating 3D topographical maps using a layering technique, foreshadowing the core concept of additive fabrication.
The 1980s: From Theory to Practice
The 1980s marked the transition of additive manufacturing from theory to practice. In 1980, Hideo Kodama developed methods for producing 3D plastic models using UV light to harden photopolymer resin, laying the groundwork for Stereolithography (SLA).
In 1984, Charles (Chuck) Hull patented the first commercial SLA process, launching 3D Systems Corporation and releasing the SLA-1 printer. SLA’s ability to create detailed prototypes from digital designs was revolutionary, introducing the nowfundamental concept of layer-by-layer fabrication.
Shortly after, Scott Crump invented Fused Deposition Modelling (FDM), which extrudes thermoplastic material through a heated nozzle to build objects layer by layer. FDM’s simplicity and versatility have made it one of the most widely adopted additive manufacturing technologies.
Selective Laser Sintering (SLS), developed by Carl Deckard and Joe Beaman at the University of Texas, introduced the use of lasers to sinter powdered materials, opening the door to a broader range of printable substances, including metals and ceramics.