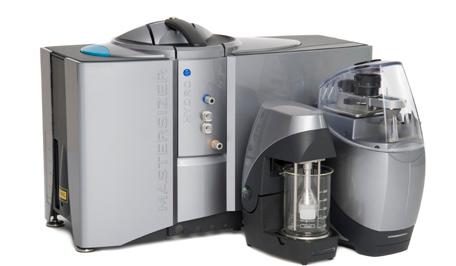
4 minute read
Powder Characterisation: Reliable methods for consistent quality in Additive Manufacturing
Source: ATA Scientific Pty Ltd
Additive Manufacturing (AM) describes the methods that convert a 3D model into a real part by the layer upon layer addition of material. AM is ideal for rapid prototyping and can enable the faster, cheaper and more efficient manufacturing of complex parts like customised medical components or engine parts, often with improved strength and durability.
As exciting as the possibilities are in AM, the process itself is not without its challenges. Problems with final product consistency and a narrow range of expensive raw materials are some of the biggest obstacles to the widespread adoption of AM. Up to one-third of the production cost is the cost of the powder used, while poor powder quality or contaminants can lead to pores, cracks and inclusions, severely impacting the end product. To maintain consistent high quality components it is necessary to not only certify manufactured parts for their physical and chemical properties, but also to certify raw material.
Laser Diffraction and Image Analysis are essential techniques for certifying both feedstock powders and printed parts, as cited in ISO/ASTM 52907 standard Additive manufacturing — Feedstock materials — Methods to characterise metal powders. This is the main standard for metal powder characterisation for AM and can be applied across the entire AM value chain including academic research, metal powder manufacture and component manufacture.
Particle size distribution - choose Mastersizer 3000
Particle size distribution is critical for powder bed AM processes since it affects several characteristics of the powder including bulk density, flowability, moldability and compressibility, which impact final component properties. Figure 1 illustrates the packing density of different sized balls in a box. Too many large particles will reduce the packing density, while too many small particles can be problematic for health and safety as well as reduce flowability due to the cohesion of the powder particles. Additionally, there is a compromise for additive layer manufacturing as it’s important to ensure a consistent layer thickness and for that reason, a narrower particle size distribution is usually preferred.
The Malvern Mastersizer 3000 uses laser diffraction, an established technique for measuring the particle size distribution of metal, ceramic and polymer powders for additive manufacturing, and is employed by powder producers, component manufacturers and machine manufacturers worldwide to qualify and optimise powder properties. A complete high-resolution particle size distribution is provided in a matter of minutes (from 10 nm to 3.5 mm) using either wet or dry dispersion. Closely matching results between dry and wet measurements of the same sample can be obtained and comparing the two allows the primary particle size, and indeed the whole size distribution, to be validated. The technique can also be integrated into a process line (Insitec) to provide real-time particle sizing.

Particle shape and compositionMalvern Morphologi 4-ID

Powder bed density and powder flowability are influenced by particle size and shape. Particle morphology is therefore another important metric for powder bed additive manufacturing, with smooth, regular-shaped particles preferable as they can flow and pack more easily than those with a rough surface and irregular shape which reduce flowability via interparticle friction and mechanical interlocking.
Suitable for particles from approximately 0.5 μm to > 1 mm, the Malvern Morphologi 4-ID enables automated optical image analysis to classify and quantify the size and shape of metal, ceramic and polymer powders. It provides a range of different shape parameters, including circularity, elongation, convexity, and solidity. It can also support customised classifications to examine features such as satelliting. The fully integrated Raman spectrometer also enables component-specific morphological descriptions of chemical species.
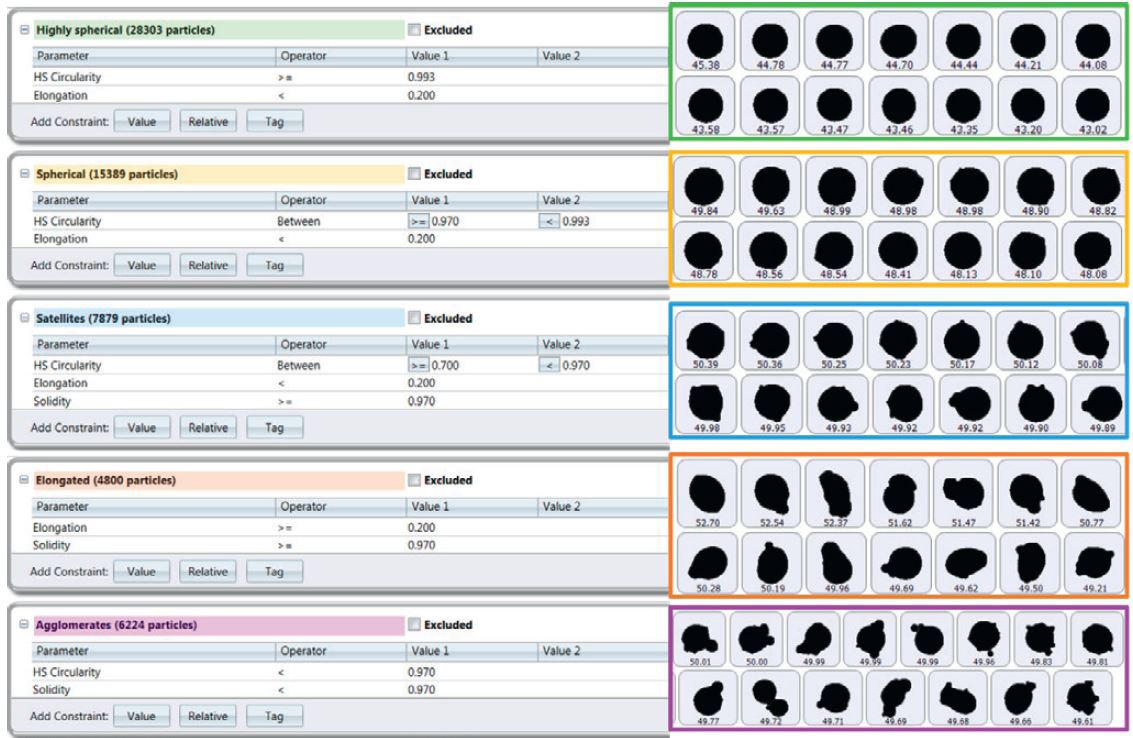

The Phenom ParticleX AM is a specialised high-resolution desktop scanning electron microscope (SEM) dedicated to optimising AM metal powders and final product quality. This fully integrated system is simple to operate and eliminates the need for outsourcing for quality checks, speeding up time-to-market. By combining an imaging resolution of <8nm and magnifications up to 200,000x together with X-ray analysis (EDS) for elemental composition, properties such as structural integrity, print resolution, surface uniformity, phases and the presence of impurities or defects can be identified and their location logged to contribute unique insights not possible with other systems. A scanning area of 100x100mm grants a large degree of freedom to image and assess the size and shape of whole parts or sections of a larger component simultaneously.
Molecular structure, Malvern OMNISEC Multidetector GPC/SEC
The physical properties and behaviour of polymeric powders and photopolymer resins depends on the properties of the polymer molecules themselves. By assessing their molecular weight and distribution, molecular size and structure and controlling these properties, manufacturers can control polymer production and quality. Historically, accurate measurement of polymer molecular weight via Gel Permeation Chromatography (GPC) has been dependent on having standards of the same polymer but the introduction of advanced detection techniques such as light scattering and intrinsic viscosity have made absolute measurements possible.
Malvern’s OMNISEC system is a multi-detector GPC system that combines light scattering (RALS/ LALS), refractive index (RI), ultraviolet (UV) and intrinsic viscosity (IV) detectors to generate a large amount of information about a sample simultaneously enabling measurements using less sample with lower molecular weights than ever before.
In figure 4, the light scattering chromatogram (RALS) indicates a shoulder at low retention volume (ca.15mL) for Nylon 12-recycle sample only. As no corresponding peak in the RI is observed, a high molecular weight species is likely present in the recycle sample at very low concentrations which can indicate chemical modifications may be occurring during processing.
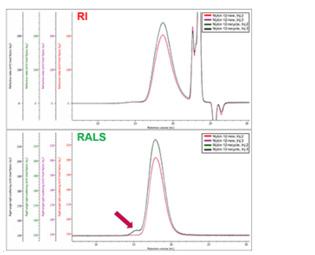
These analyses facilitate a deeper understanding of how many times a powder can be recycled, as well as the optimum powder refresh rate (used/new powder ratio) to use in the process. This helps to ensure the quality of the powder bed, and therefore the quality of the final part is not compromised.
Go further together
At ATA Scientific, we don’t just sell our instruments – through collaboration with a broad range of industries and academic institutions, we play a key role in the AM ecosystem. We support our customers by providing optimal material characterisation techniques used in AM together with key insights into the application, measurements and analysis to fully understand material behaviour.
Contact us for more information today!
ATA Scientific Pty Ltd
+61 2 9541 3500 enquiries@atascientific. com.au