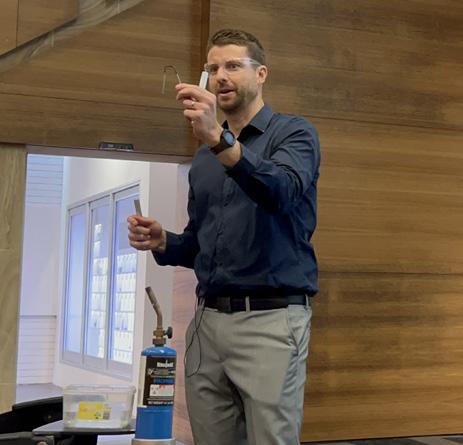
4 minute read
Profile: Dr Michael Bermingham ARC Future Fellow
Dr Michael Bermingham's research is primarily concerned with advanced manufacturing of metal materials. This also involves metal alloy development including understanding how the manufacturing process influences the structure and behaviour of the material and how alloy design can be optimised for the process. He has research expertise in solidification processing (including casting, welding, soldering and additive manufacturing), as well as subtractive metal machining technologies.
Michael was awarded his PhD from the University of Queensland in 2010 with a Dean's Award for Outstanding Higher Degree Theses. From 2010 to 2015 he completed a post-doctoral appointment sponsored by the then Defence Materials Research Centre (now DMTC Ltd) working with Australian manufacturers in the F-35 Joint Strike Fighter supply chain. This work principally centred on developing advanced machining technologies for titanium fabrication.
During this time Michael also completed a post-doctoral appointment investigating new materials and design solutions for implantable medical devices in collaboration with a multinational medical device manufacturer.
Michael became a Lecturer in the School of Mechanical and Mining Engineering at the University of Queensland in 2016 and has been a Senior Lecturer since 2020. He teaches into undergraduate and postgraduate courses in materials, manufacturing and design and has won a number of teaching awards including a 2020 Australian Award for University Teaching Citation for Outstanding Contribution to Student Learning.
Can you provide brief summary of your research career?
My research career began as a PhD candidate in the former CAST CRC trying to understand grain refinement science in cast titanium products. I was fortunate to be well supported in this research environment and had some incredible times and formed lifelong friendships.
After completing my PhD I joined the then Defence Materials Research Centre (now DMTC Ltd) working alongside SMEs in the F-35 Joint Strike Fighter supply chain to develop advanced machining techniques for fabricating aircraft parts.
I also held other postdoc appointments including working with Cook Medical Australia looking at materials and manufacturing related issues associated with medical devices.
In late 2015, I was fortunate to secure a continuing academic (teaching and research) position at the University of Queensland and a few days later an ARC Discovery Early Career Researcher Award (DECRA) – a truly fantastic week! Since then, my research in physical metallurgy has continued, and just recently I was awarded an ARC Future Fellowship.
What has been the most productive period in your research career and why?
During my ARC DECRA fellowship I had the opportunity to pursue my research interests in additive manufacturing (AM), which proved to be a productive period. I was able to grow and mentor a team that was working to understand how to control microstructure and properties during metal additive manufacturing. The flexibility afforded by the fellowship provided me with opportunities to travel and collaborate with others in the field.
How do you balance your time?
In a life before research, I worked in the brick manufacturing industry where among other things I learned to value my time and work efficiently. When my research journey started, I applied these same principles and found a healthy work-life balance that I still practice today.
My role has since evolved and there are more pressures on my time than previously, but I maintain a healthy balance. I have learned that it’s okay to say no to things that don’t bring value and joy.
What do you think are your most significant research accomplishments?
I’m proud of my research contributions to the field of grain size control in titanium alloys during solidification processing. I was fortunate that when I commenced my study in this area back in 2006 I had many world class solidification experts available to mentor me along this journey including Professor David StJohn.
The research we did in grain refining cast titanium product later proved useful in addressing the pressing issue of how to control large grain sizes and textures that develop during additive manufacturing.
Additionally, the cyclic heating and cooling associated with AM can embed microstructure and phase heterogeneity which creates issues in part-to-part consistency.
Recently, our team published our work in Science which outlined a pathway toward alloy design that incorporates methods to simultaneously control grain size, texture and phase heterogeneity which resulted in uniform properties in a class of titanium alloys.
What are the big issues in your research area?
My future fellowship focuses on understanding how we can develop fit-for-purpose products directly from AM by closely examining alloys. Most alloys used in AM were not developed for this process and some, including titanium alloys, were originally designed for thermomechanical processing.

However, AM is unique in its nature and offers the potential to unlock new possibilities. For instance, recent research has shown that certain compositions can be successfully processed by AM without forming deleterious segregation defects which is not achievable through conventional production routes. As a result, some of the traditional rules for how we approach alloy design can be redefined, taking advantage of the novel opportunities presented by metal AM. Exploring these possibilities is a key aspect of my fellowship.
If you were starting your project or research again today, what would you do differently?
I do not harbour any regrets towards the research career I’ve had. I have been very fortunate to have had long term supportive mentors and collaborators, particularly Professor Matthew Dargusch who has taught me so much about research and industry translation.
How do you feel about translating research outcomes to industry?
I am a firm believer that the research we do must add value to industry, and I am a strong proponent of translation. Some of my proudest research outcomes have never been published but have been directly adopted by the industry partner because the research has addressed critical issues facing them. As a researcher it is rewarding knowing that the discoveries we make are valuable to industry.
How do you feel about teaching? What is your teaching philosophy? Good teaching is critical and can profoundly influence students. Attracting students to materials engineering is an ongoing challenge that our discipline faces and I believe that all of us in teaching roles should do our best in attracting and educating the next generation of young materials engineers. When I was a student I didn’t initially know what materials engineering was and I never contemplated a career in it.
However, thanks to an exceptional teacher, Professor Arne Dahle, I became fascinated. I remember Arne would demonstrate material properties live in class by smashing ceramic mugs and throwing (and shattering) cryogenically frozen squash balls at the wall in a lecture theatre. I’ve been inspired by Arne to make materials and manufacturing interesting and I try to implement best practice pedagogies into my classes. I’m honoured to have won several teaching awards at the university and national level.