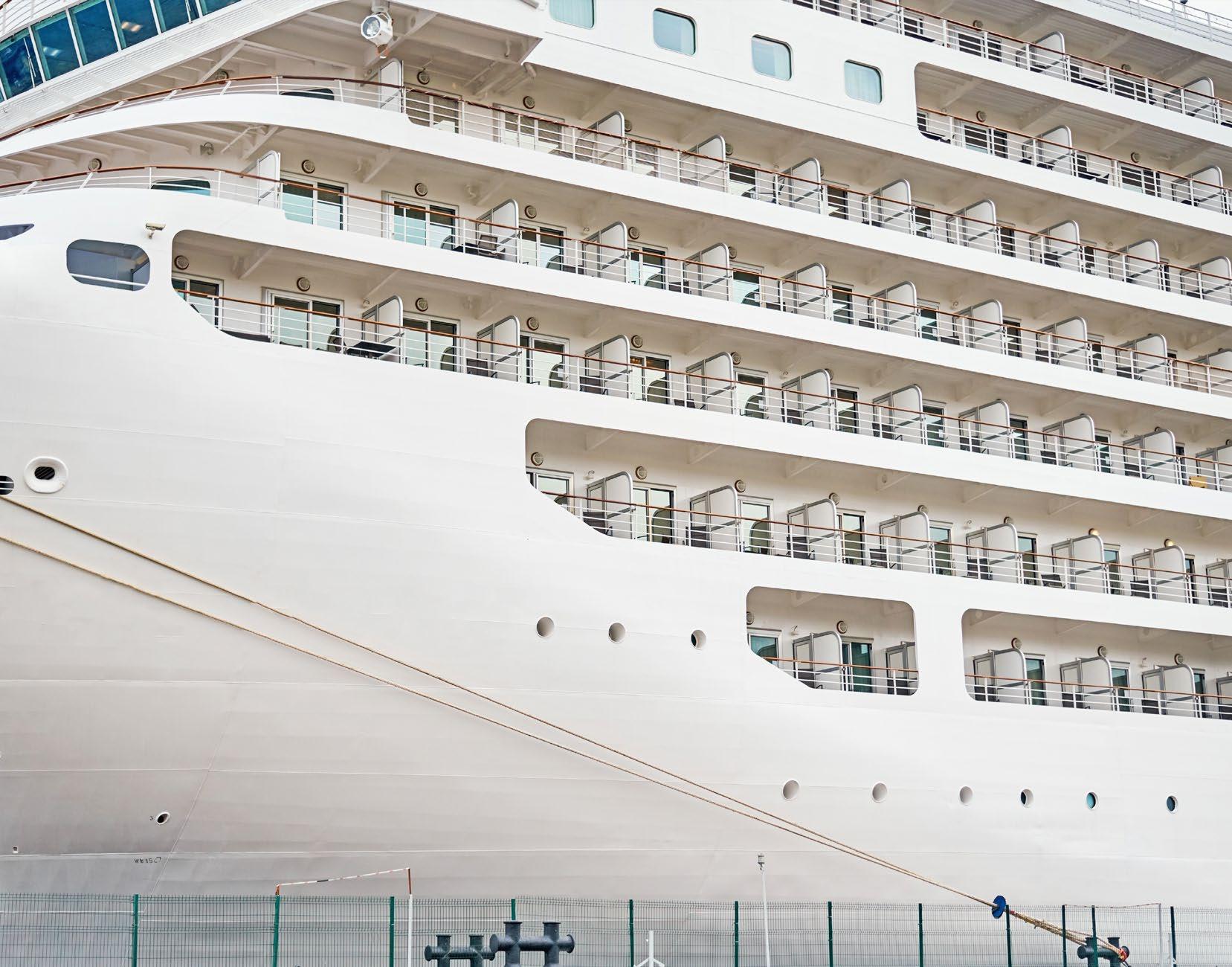
12 minute read
COATINGS
from CSI Summer 2021
by Maritime-AMC
Clean Shipping International explores how coatings manufacturers are doing their bit for the environment by improving a vessel’s hull performance
HULL PERFORMANCE IS KEY TO SUCCESS
Following the launch of Jotun’s HullKeeper, a proactive hull optimisation programme, Clean Shipping International spoke with Stein Kjølberg, the company’s Global Category Director Hull Performance.
HullKeeper is the latest in a series of initiatives and complements Hull Performance Solutions (HPS), launched in 2011, and Hull Skating Solutions (HSS), launched last year.
HPS combines Jotun’s most advanced antifouling system, digital capabilities and analytical and technical expertise, to help operators keep fuel costs under control and indeed to save money. It combines advanced antifouling technology, inspection and proactive cleaning to keep the hull free of fouling at all times.
Jotun’s HPS analysis service fully complies with ISO 19030, which is based on the methodology developed in HPS, and Jotun was very much involved in the development of this standard, Kjølberg says.
It isolates the impact of a ship’s underwater surfaces on its energy efficiency by tracking relative changes in the relationship between the power delivered to the propeller and speed through water over time.
HSS, meanwhile, was unveiled by Jotun in March last year. The first company to take advantage of this initiative was large containership operator, Mediterranean Shipping Co (MSC).
HSS is based on HullSkater, the first robotic technology (ROV) housed on a ship designed for proactive cleaning. It was specified for the specially developed highperformance SeaQuantum Skate antifouling, on the 14,000teu MSC Eva.
More recently, HullSkater was chosen to be fitted on board a series of 16,000teu containerships being built at Hyundai Heavy Industries for HMM Co.
Designed to help shipowners face the most severe biofouling challenges, it combines the antifouling and robotic proactive cleaner and is housed on board the vessel. Jotun operators control the HullSkater via a 4G connection, conducting
cleaning and inspections in line with individual vessel schedules developed through a proprietary algorithm and big data.
SeaQuantum Skate is a highperformance coating included with HullSkater. The antifouling is designed and thoroughly tested to work in perfect harmony with the ROV.
HullKeeper is a four-part programme designed by Jotun’s team of hull performance experts, which optimises hull performance, regardless of the chosen coating. Ship operators can take full control of their operations through hull monitoring, fouling risk alerts, inspections and advisory services. Operators can benefit from the complete package or select parts as they wish.
Kjølberg explains that Jotun takes a hull performance approach to coatings and gauges a ship’s efficiency by measuring a coating’s performance on the hull.
By using this approach, shipowners and operators have a tool whereby, for example, better and faster decision making can be made around worldwide trading patterns by using the alerts when a vessel is entering an area of heavy fouling.
In addition, by monitoring a coating’s performance in real time, Jotun can advise the owner or operator whether the hull is at risk of fouling, needs cleaning or is in perfect condition, thus keeping vessel costs under control and even offering savings on fuel consumption, and so on. The information is collated and analysed by an in-house hull assessor. By using this method,the coatings usage can be maximised following a drydocking or with a newbuilding’s antifouling.
To take further advantage of this service, a vessel will benefit from being fitted with sensors and a data logger. This way, monitoring according to ISO 19030 can provide an increased understanding of the hull’s performance.
The vast majority of ships still use the noon-day reporting system, which obviously only gives one data point per day.
Even this data, combined with AIS and oceanographic data, can provide good information for the owner to take better decisions faster.
HullKeeper is driven by Jotun’s proprietary fouling risk algorithm, supported by data from different sources to make fouling control and efficiency more predictable. By providing insight into issues before they occur, ship operators can take planned corrective actions. And as more data and information accumulate, best practices can be identified and implemented across the whole fleet.
The programme was introduced during the middle of last year and pilot tests were carried out with selected customers, which have since been expanded. “We are now in an expanded verification stage seeking a wider range of customers to gain momentum and insight, and the product should be ready for its full launch next year,” Kjølberg says.
Thus far, a containership operator with vessels on various fixed routes has been testing the system and Hafnia, Angelicoussis and HMM are also collaborating with testing of the various packages.
Jotun’s Global Digital & Data Director Andreas Krapp explains that increased fuel consumption related to biofouling accounts for about 9% of the 919m tonnes of CO2 and 21m tonnes of other greenhouse gases (GHG) emitted by shipping annually.
While he acknowledges that the industry is unlikely to reach its full potential reduction of 85m tonnes of GHGs, HullKeeper represents a genuine opportunity to help the industry make significant emissions reductions, he says.
The forthcoming International Maritime Organization’s Energy Efficiency Existing Ship Index (EEXI), due to become mandatory in 2023, will leave little or no room for sea margin flexibility, which is normally written into a charterparty. “This will really impact the shipping markets,” he says.
EEXI will set a baseline reference and may require a vessel to retrofit energy saving devices or impose an engine power limit. In addition, the Carbon Intensity Index (CII) will be introduced to track and rate a vessel’s energy efficiency in real time, on an annual basis.
Kjølberg thinks that this is where high-quality antifoulings development could make all the difference. However, he says that the impact of new fuels going forward would have little or no effect on hull coatings. “There will still be a good antifouling needed,” he says.
Kjølberg further stresses that shipping company superintendents should talk about the impact of the antifoulings on their vessels and
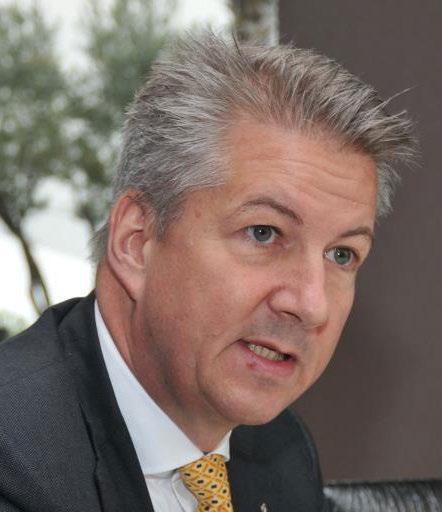
Stein Kjølberg, Jotun Global Category Director Hull Performance Andreas Krapp, Jotun Global Digital & Data Director

be prepared to increase the coating specification slightly to gain a better return on investment (ROI) in the long term.
He also warns shipowners and operators to plan the underwater cleaning process well in advance, as there are a growing number of areas of the world where this service is banned. The cost involved of deviating to an area where underwater cleaning is allowed could be “horrific”, he says.
As for propeller cleaning, Kjølberg advises that this should be undertaken twice a year. Spending just $2,000$3,000 will improve a vessel’s efficiency by keeping the roughness formation under control, thus not increasing the power needed from the main engine.
JAPANESE INITIATIVE
Elsewhere, while IMO has a policy of reducing greenhouse gas (GHG) emissions to half the level of 2008 by 2050, the Japanese government has gone a step further by implementing a policy to reduce the country’s GHG emissions to zero by 2028.
Nippon Paint Marine’s lowfriction coating system is just one of the environmentally friendly technologies that is being applied by shipping companies as a way of improving the carbon footprint of their vessel operations.
“We are continually developing marine coating systems in support of the ‘zero emission ship’ concept that many shipping companies look to develop,” says Hirokazu Kaji, Technology Director, Nippon Paint Marine.
The company introduced a new antifouling technology earlier this year, specifically to help shipowners further reduce CO2 emissions.
Fastar, Nippon Paint Marine’s fourth-generation antifouling paint, incorporates an advanced version of the water-trapping hydrogel technology used in its A-LF Sea system.
The fuel-saving A-LF Sea, launched in 2010, has been applied to the hulls of more than 3,500 vessels worldwide and received the Japanese Environment Minister’s Award for Global Warming Prevention, in 2019. “Fastar, however, takes our water trapping technology to a new level,” claims Kaji.
Designed to deliver around an 8% reduction in fuel consumption and CO2 from a coating that benefits from reduced film thickness and lower polishing rates, Fastar enables more precise control of the release of hydrolysis resin and biocide into the sea.
“The technology creates hydrophilic and hydrophobic nano domain structures in the coating,” Kaji says. “These are laid out in alternate molecular patterns so that the antifouling ion can spread through the hydrophilic domains of resin to improve the efficiency of biocides and antifouling performance.
“Essentially, it minimises the effect seawater temperatures, vessel speeds and other external factors have on coating performance, reducing drag, fuel consumption and, subsequently, emissions.
Nippon Paint tells Clean Shipping International that it is continuing to improve existing coatings and develop environmentally new ones capable zero coating elution by 2030.
“We hope to significantly and contribute to the zero-emission ship with a hull coating that will prevent fouling and drag completely,” Kaji concludes.
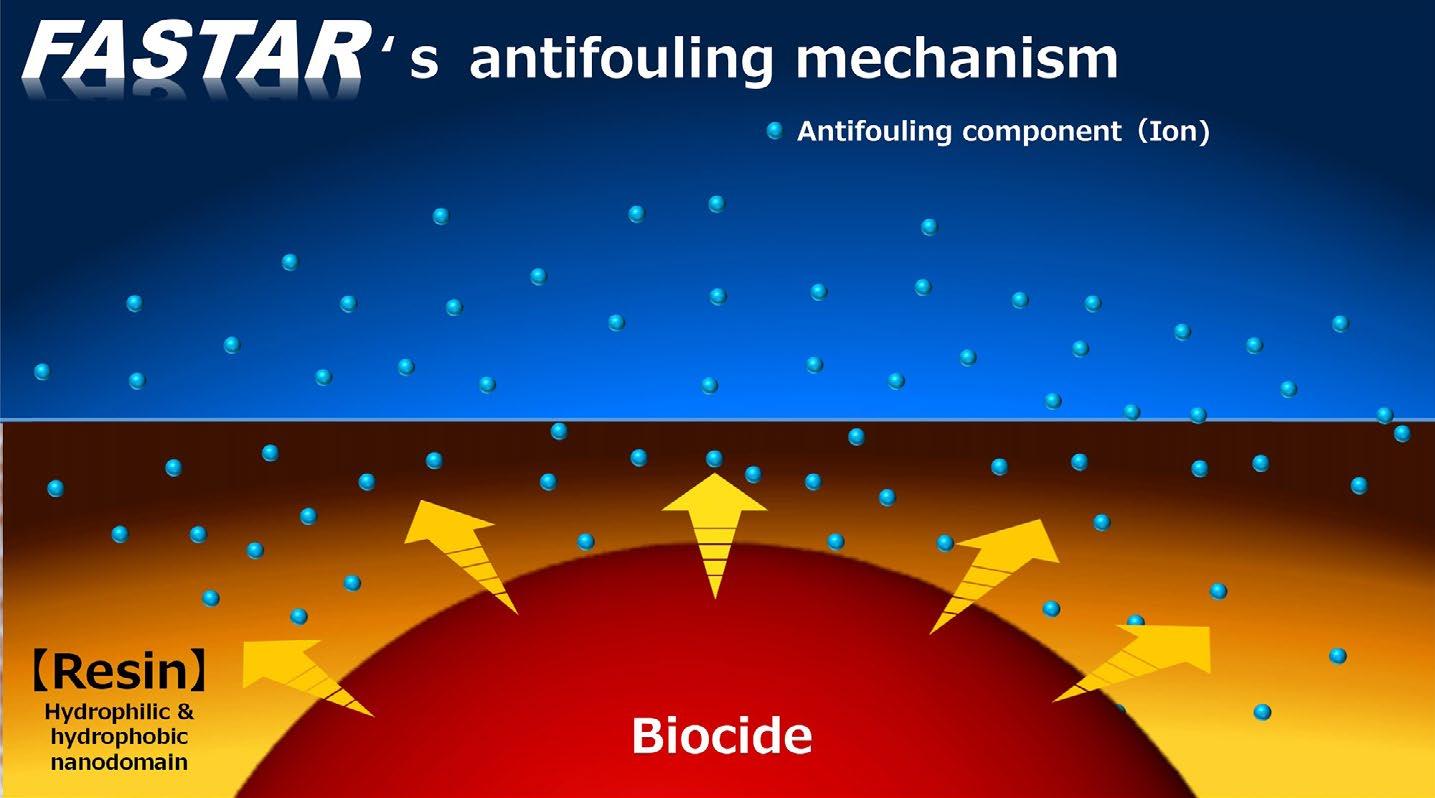
FASTAR mechanism schematic
EFFICIENCY GAINS
Speaking about the IMO’s GHG goals, Andreas Glud, Group Segment Manager, Dry Dock, Hempel, says: “We welcome this evolution towards a more sustainable future and strongly believe that coatings have a fundamental role to play in minimising fuel use and emissions, as well as improving operations.
“It is well known that fouling and mechanical damage to the hull can increase the engine power a vessel needs to maintain a defined speed by as much as 18% — and potentially more over a five-year sailing interval.
“Therefore, it is clear that to remain competitive and to meet and measure emissions reductions against new efficiency and environmental targets, vessel owners need to apply coating solutions that minimise fouling. They also need to fully understand the performance of the ship’s hull itself,“ he says.
Choosing a hull coating — which reduces drag, minimises downtime, enhances physical durability and protects assets for the longest period of time — is one of the simpler ways to achieve efficiency gains.
Hempel is currently offering solutions that deliver all of this, Glud claims. “Our flagship coating Hempaguard®X7, launched in 2013,
delivers 6% in fuel savings — compared with a market average — and a maximum speed loss of 1.4% across a five-year docking interval.
“Built on our Actiguard technology, which took over five years to develop, it is the first paint to combine both silicone-hydrogel and advanced biocide control in a single coating,” he explains.
Hempaguard X7 has been applied to more than 2,000 vessels, enabling those vessels to collectively reduce their fuel consumption by 7.6m tonnes, lowering fuel costs by at least $2.6bn and CO2 emissions by 23.5m tonnes.
But using an advanced hull coating is not the only way to make a difference. In order to fully commit to de-carbonisation, a mix of eco-efficient technologies should be adopted alongside the ability to better understand and measure actual performance, says Glud.
Hard data and analysis play an important role, which is why Hempel offers a more holistic approach through its proprietary hull performance system Shape (Systems for Hull and Propeller Efficiency).
Designed to follow the principles of ISO 19030, Shape monitors a vessel’s long-term trends using in-service key performance indicators. This provides detailed data, allowing the shipowner or operator to make fact-based operational decisions.
Combined with expert performance analysis of the vessel’s hull and propeller efficiency conducted by Hempel’s team of chemists, physicists and hydrodynamicists, Shape can deliver documented fuel savings, an improved return on investment and a programme of continuous improvement, Glud claims.
This level of detailed data interpretation allows Shape to suggest a more flexible, optimised and tailormade coating solution for each individual vessel.
As importantly, it also encourages each owner to maximise their efficiency and enhance their return on investment. INVASIVE SPECIES
Hard biofouling creates some the highest levels of hydrodynamic drag on a vessel hull, thought to add around 110m tonnes of excess carbon emissions annually across the industry.
A 2011 study conducted by Michael P Schultz quantified that a naval vessel with 10% barnacle fouling requires 36% more power to maintain the same speed.
In 2020, a study conducted by I-Tech and independent marine coatings consultant Safinah Group, estimated that hard biofouling adds some $6bn to the shipping industry’s annual bunker bill.
Another often overlooked cost is the maintenance and upkeep of a fleet significantly impacted by biofouling in “niche” areas. Niche areas, such as boot tops, sea chests and gratings, could account for as much as 10% of the total underwater hull surface of the global shipping fleet.
The I-Tech/Safinah Group study found that while flat underwater hull surfaces vary in their hard fouling coverage, 95% of the vessels surveyed had heavily fouled niche areas. Not only does this impact efficiency, but it also means that ships with otherwise smooth hulls could be vectors for the spread of invasive species.
These areas are comparatively challenging when it comes to effective antifouling coatings, partly due to the complex nature of their location and composite structure. There seems to be a lack of awareness as to how vital these areas are.
Many of these niche areas are home to core engine wear and operations. For example, should fouling build up in a sea chest, the function of a box cooler — which is designed to support the temperature control of a ship — can fail, compromising or even destroying its capabilities. This could mean that, if compromises are made during the choice of antifouling system — other vessel efficiency efforts may very well be in vain.
To mitigate the risk of biofouling, some owners could benefit from using coatings that include high performing active antifouling agents, such as Selektope®.
Thanks to its role in transporting invasive aquatic species, hull biofouling poses a significant biosecurity threat to marine ecosystems.
According to the IMO, several studies have determined that vessel biofouling has been a comparable, if not more significant, factor than untreated ballast water for introduction of invasive aquatic species.
In some parts of the world, evidence suggests that 70-80% of invasive species introductions have occurred through biofouling.
While the spread of invasive species may not be on the top of everyone’s agenda, the matter is far from hidden. There is an increasing amount of regionally focused legislation that aims to preserve local marine ecosystems.
In California, port authorities estimate that 60% of invasive marine species are transferred by fouled hulls. Consequently, since October, 2017, all vessels of 300gt or more have been required to complete and submit a “Vessel Reporting Form” at least 24 hours before their first arrival of the calendar year at a Californian port.
And from January, 2018, ships must also present a Biofouling Management Plan and record all management actions in a Biofouling Record Book.
Authorities in New Zealand have taken a more stringent approach to preserving marine ecosystems. In 2017, the 33,752dwt South Koreanowned bulk carrier DL Marigold had to leave New Zealand waters after its hull was deemed a biosecurity threat with dense barnacles and tube worm coverage on its underwater surfaces.
Under new biosecurity rules that came into force in May, 2018, all international vessels arriving into New Zealand must have a “clean” hull.