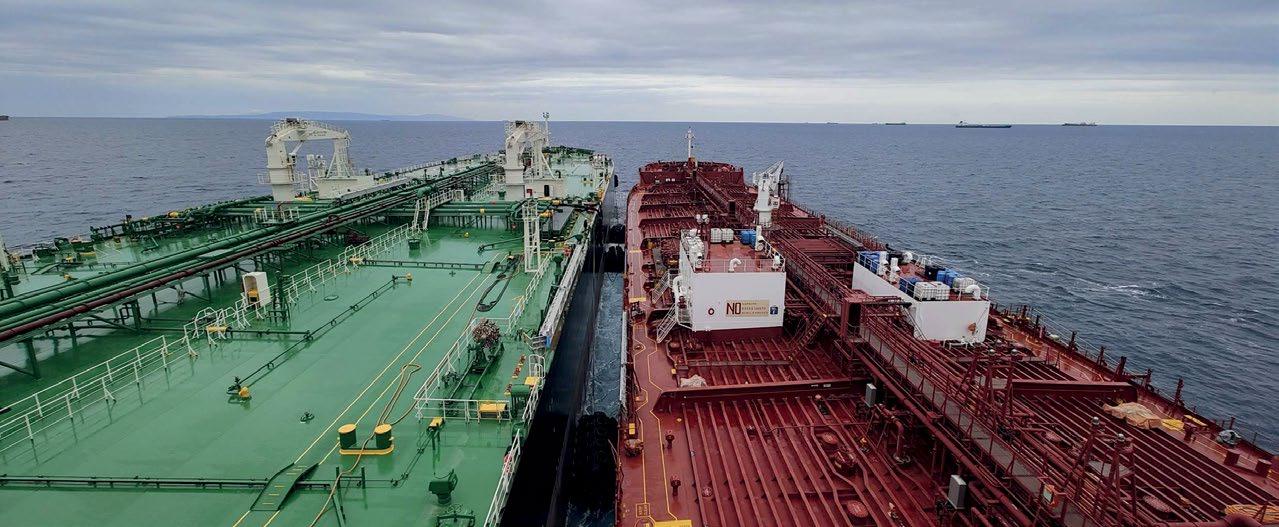
8 minute read
The Integral Role of the Person-in-Overall Advisory Control
from Wavelength #84
Introduction
Ship-to-ship (STS) operations are critical processes that enable the transfer of various types of cargo such as crude oil, refined petroleum products and liquefied gas between vessels at sea, or in designated port areas. These operations require meticulous planning, coordination, and adherence to safety protocols and environmental regulations. A key figure in ensuring the success and safety of STS operations is the Person-in-Overall Advisory Control (POAC). This article will explore the intricacies of STS operations and the essential role of the POAC in maintaining the safety and efficiency of these procedures.
Advertisement
Ship-to-Ship Operations
STS operations consist of several steps, including pre-planning and risk assessment, communication and coordination between participating vessels, mooring and fendering arrangements, cargo transfer, and unmooring. Throughout these stages, clear communication and collaboration between the vessels and shore-based support are crucial to ensure the safe and efficient execution of the operation.
Key Responsibilities of the POAC
By Captain Prashant Kumar
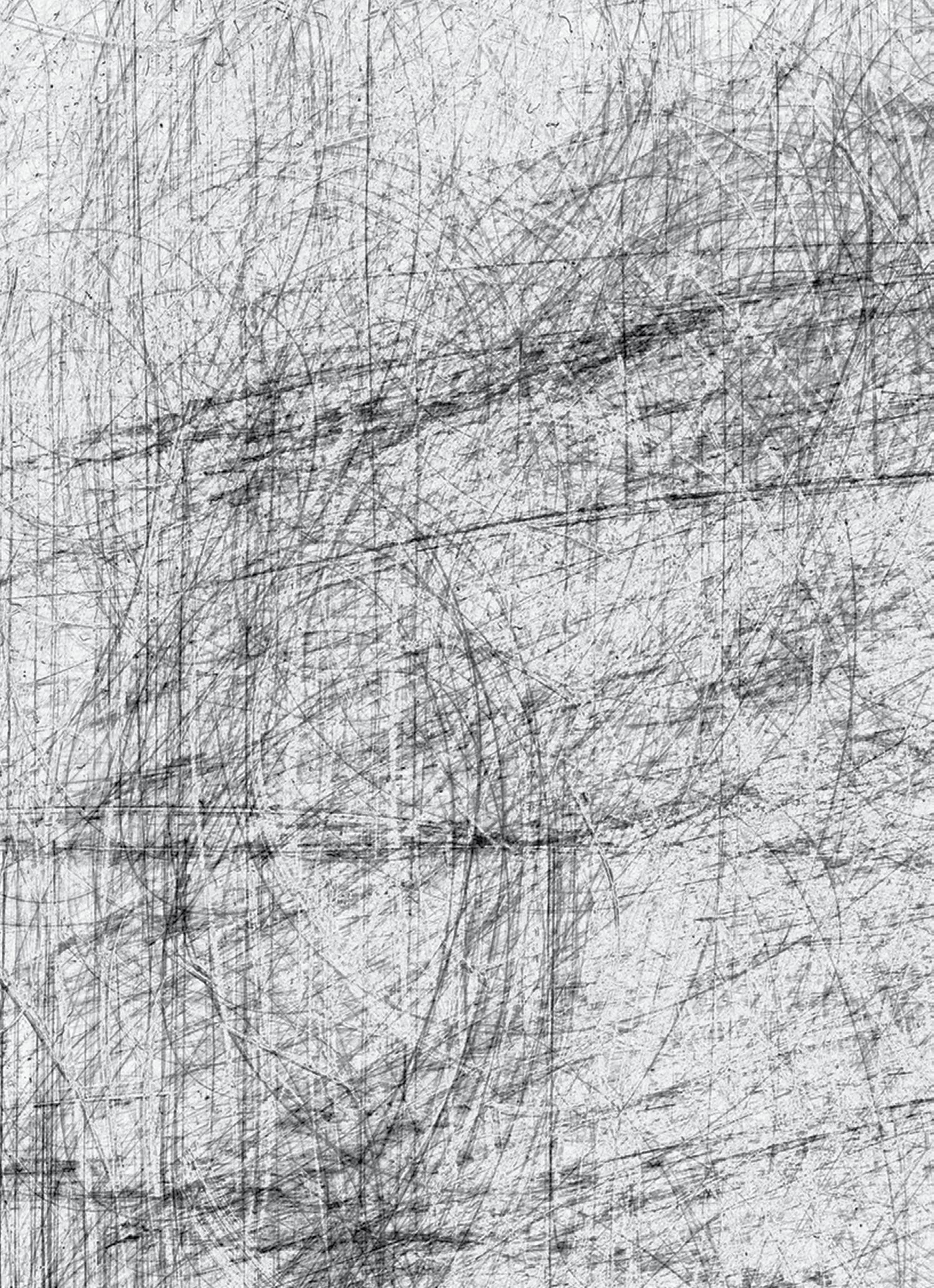
1. Risk Assessment and Planning: The POAC conducts a comprehensive risk assessment before the commencement of the STS operation. This assessment involves analyzing the compatibility of the vessels, weather and sea conditions, equipment, and personnel to identify potential hazards and implement suitable control measures.
2. Communication and Coordination: The POAC ensures seamless communication between the participating vessels, tugs, and shore-based support. This individual also coordinates the efforts of various parties involved, guaranteeing that all necessary preparations are made and that everyone is aware of their roles and responsibilities.
3. Supervision of Mooring and Fendering Operations: The POAC supervises the positioning, mooring, and fendering of the vessels, ensuring that they are securely and accurately positioned to prevent any risk of collision, grounding, or other hazards.
The Role of the Person-in-Overall Advisory Control (POAC)
The POAC is a highly skilled and experienced individual with an indepth knowledge of STS operations, regulatory requirements, and safety procedures. This person’s main responsibility is to serve as the central point of communication and decision-making during the STS operation. Therefore, the POAC collaborates closely with the Masters of both vessels and other involved parties, such as terminal operators and third-party service providers.
4. Cargo Transfer Monitoring: During the cargo transfer process, the POAC closely monitors the operation, ensuring that transfer rates and procedures are maintained within safe limits and that all safety precautions are observed. They also address any issues that may arise during the transfer process, such as leaks, spills, or equipment failures.
5. Emergency Response: In case of an emergency, the POAC is responsible for coordinating the emergency response efforts of both vessels and any other involved parties, ensuring that appropriate action is taken to mitigate any risks and minimize potential consequences.
Conclusion
The POAC is a vital figure in ship-to-ship operations, acting as the central point of coordination, communication, and decisionmaking throughout the process. The POAC’s expertise and careful oversight ensure that STS operations are carried out safely and efficiently, minimizing the risk of accidents and environmental incidents. As the shipping industry continues to adapt and overcome new challenges, the role of the POAC remains paramount in maintaining the highest standards of safety and operational excellence.
Crew Department
Cenmar Ukraine Relocated in Romania
Following the outbreak of war in Ukraine in February 2022, the Company and the Cenmar office staff had to take an urgent decision about how crewing operations could continue without problems. This resulted in several colleagues from Cenmar Ukraine being relocated in Tulcea, Romania for a few months before their second move to Constanta.
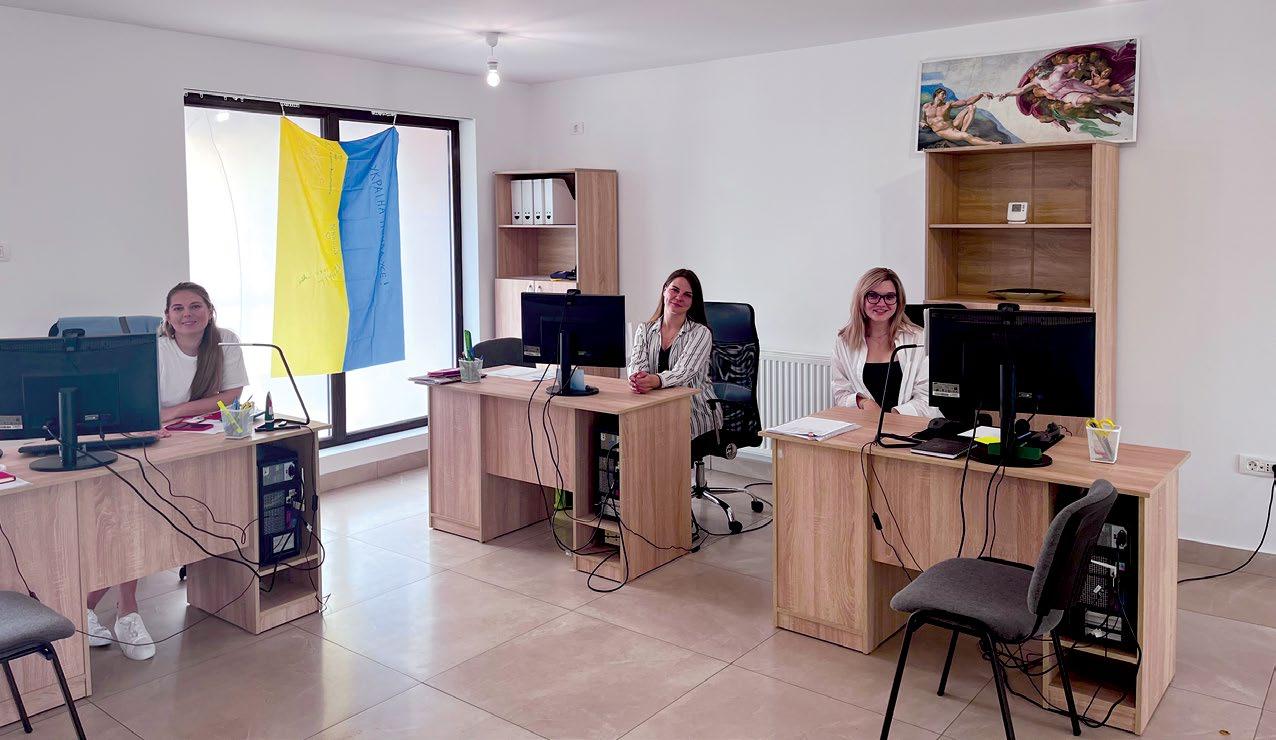
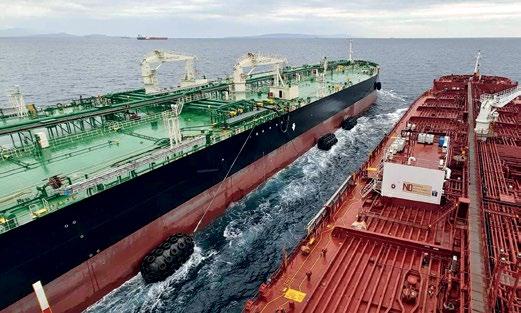
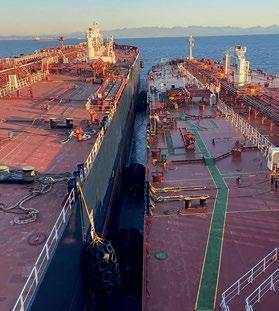
In Constanta, Yelyzaveta Koslova, Natasha Gribniuk, Khrystyna Vshyvtsova and Alla Dekhtyarenko were able to work together again, communicate with Ukranian crew in Europe or still in Ukraine, organize crew changes, arrange physical and online training activities and perform all other operations as if they were still working in Odessa.
Meanwhile, Anastasia Sokolovska and Tatyana Pusova opted to remain in Odessa and operate from there, while Olga Orlova relocated in Germany, from where she has been working remotely for the SQE Department.
We wish to praise all our Cenmar staff for their resilience in these difficult times. We would also like to say that it has always been a pleasure for all the Crew Department staff to work closely with such optimistic, smiling and energetic colleagues.
MESSAGE FROM THE DPA: Incident Free Vessels
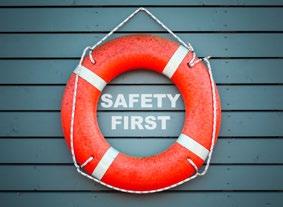
Dear seafarers,
I am happy to commend your colleagues on board the following vessels, who kept their safety intact and their safety culture on the rise: • On board 7 of our vessels since these were delivered • On board 14 of our vessels within the year 2022
Since delivery (7 vessels)
M/V Philippos A. – Since 2011
Remains accident free over the past 11 years!
M/T Merapi • M/V Alliance
M/V Andonis • M/V Danae
M/V Duke II • M/V Smyrna
Keep up the “SAFE” work!
I wish you safe voyages and a safe return home,
Elli Moretti
Within 2022 (14 vessels)
M/T Apanemo • M/T Captain A.Stellatos
M/T CE-Bermuda • M/T Kapsali • M/T Merbabu
M/T Mikela P. • M/T Pserimos • M/T Semeru
M/T Sereno • M/T Sundoro • M/V Calliope P.
M/V Evgenia P. • M/V Irina • M/V Nilos
Have you seen our new Enclosed Space Entry Permit?
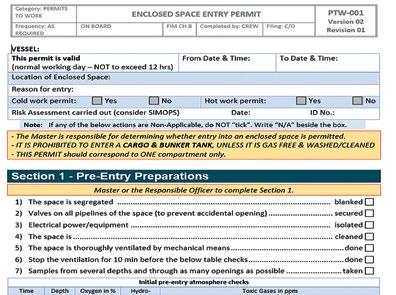
I hope it will become a valuable tool to boost your safety onboard. It may go on for 5 more pages, but we hope these are “user-friendly” pages. The SQE Dept. will highly appreciate your feedback after you have used it. Is it improved? Is it clear? Is it easy to use?
In addition to the new permit, we have also updated relevant FIM Chapter B, Section 2
Entry into enclosed spaces continue to claim seafarers’ lives on board regardless of the type of vessel
The Rightship global vetting team have investigated a selection of 360 incidents involving 385 fatalities since 2019. 31 of these happened in enclosed spaces. They found that all of these could have been avoided if certain preventative or mitigating controls had been in place.

Case 1 – H2S Intoxication within a cargo tank
The vessel was loaded with crude degummed soybean oil. After discharging, vessel drifted for 8 days. During this time, all tanks were washed, except cargo tanks 4 Port and Starboard, where the residues/slops were accumulated. Once the voyage orders were received, the crew continued tank cleaning.
After washing and mopping operations were carried out in cargo tank no.4 Starboard, the 4 Port cargo tank washing water was
Source: Rightship.com/ Safety insights discharged into the sea. Entry into the cargo tank was scheduled for after the discharge and freshwater wash completion. There was no issued instruction to the deck crew regarding tank entry, cleaning, or mopping.
At 5:30 PM, Able Bodied Seaman no. 1 (AB1) notified the Chief Officer that he saw the Bosun and Able-Bodied Seaman no..2 (AB2) lying on the floor of the 4 Port cargo tank. He added that he suspected they may have fallen into the tank. A general announcement was made, and the Chief Officer arrived at the scene joined by other crew members. The Master arrived a few minutes later, accompanied by the Chief Engineer.
They witnessed Able Bodied Seaman no 1 (AB1) lying on the tank floor next to the Bosun and Able-Bodied Seaman no..2 (AB2). It was evident that he had attempted to rescue them without waiting for assistance and/or evaluating the situation. The Master, ignoring the crew's attempt to stop him, rushed into the tank without Personal Protective Equipment (PPE), whereupon he immediately collapsed. The rescue team commenced a rescue operation following relevant procedures and lifted the casualties out of the tank.

On their arrival, the shore medical/rescue team completed atmosphere measurement and observed the presence of Hydrogen Sulphide (H2S) inside the tank. Upon their examination of the casualties, the Master, Bosun, and Able-Bodied Seaman no.2 (AB2) were pronounced dead. Able Bodied Seaman no.1 (AB1) was evacuated to a shore hospital.
The autopsy revealed pulmonary oedema in all casualties, a common result of exposure to high concentrations and intoxication of H2S. Furthermore, toxicology revealed lethal levels of thiosulfate, which resulted from metabolism of H2S.
Unfortunately, there were no survivors …
This case is re-enacted in a short but very impactful video which you find in: https://youtu.be/bEqthx4a7gQ
Case 2 – Asphyxiation within the cargo hold
The vessel arrived at her nominated discharging port’s outer anchorage area partly loaded with Silver concentrate (Hecla Silver) inside cargo hold no.2, and bulk concentrate inside cargo hold no.1 and cargo hold no. 4.
That morning, the vessel’s Chief Mate along with Able Bodied Seaman no.1 (AB1) conducted daily deck maintenance checks. They started at the Bosun’s store, before moving to the cargo holds. The Chief Mate intended to enter cargo hold no.2 to check the hatch cover watertightness. Able Bodied Seaman no.1 (AB1) was ordered to open the manhole for ventilation. After 30 minutes the Chief Mate went down the ladder through the open manhole while Able Bodied Seaman no.1 (AB1) remained outside.
A few minutes later, AB1 shouted out to the Chief Mate a couple of times, yet there was no response. Able Bodied Seaman no. 1 (AB1) then decided to enter cargo hold no.2 to check on the Chief Mate. While climbing down the ladder, about two metres into the cargo hold, he realised it was difficult to breathe. He saw the Chief Mate lying unconscious on the second platform. Able Bodied Seaman no. (AB1) exited the cargo hold, went back to the accommodation, and called for assistance.
The Master and crew members gathered on the poop deck to conduct the rescue operation. Crew members commenced opening the cargo hold hatch covers. This took longer than expected due to the pre-tightened securing cleats. The hatch cover was opened, and the Chief Mate was recovered, but there was no pulse. The crew performed CPR for almost 1 hour without success and the Chief Mate was pronounced dead.
Case 3 – Three fatalities during cargo hold sampling
This tragic incident took place on board a bulk carrier berthed at port. The ship arrived with a cargo of wheat bran pellets. The receiver’s representative requested the vessel provide samples from all holds. The Chief Mate along with Third Officer and AbleBodied Seaman no.1 (AB1) went to collect the requested samples. They took samples from holds no. 1 and no.2, but not hold no.3 as it contained the same cargo as hold no.1. At this point, the Third Officer went to place the samples at the accommodation ladder. Upon learning that one of the stevedores was selling phone cards, the Third Officer went to the ship’s office. When he returned, he could not find the Chief Mate or Able-Bodied Seaman no.1 (AB1). Feeling suspicious, he then looked inside the hold no.4 booby hatch and found both lying unconscious below. He then went back to raise the alarm and seek help.
While the crew were preparing for the rescue operation with both the Third Officer and Chief Engineer in attendance, the Master rushed to the site. Despite advice not to enter the hold, he entered the tank and he too fell unconscious. This incident resulted in all three as fatalities.
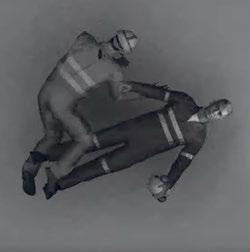
What went wrong?
Poor procedures / Lack of Permit - Inadequate/inappropriate entry into enclosed space SMS procedures, lack of familiarisation with the existing procedures, lack of training
Incomplete risk assessment - Failure to evaluate/understand/ communicate risks associated with certain types of cargoes, lack of understanding/appreciation of the risks associated with fumigation
Incorrect atmosphere testing - Gases and vapours that are higher in density than air (such as H2S) sink to the bottom, resulting in a higher gas concentration further from the top of the tank. Conversely, lighter gases and vapours rise up and result in a higher concentration at the top area of the tank. Gases and vapors also tend to have a higher concentration in areas where ventilation is least effective such as corners, and under inspection way/platforms. In one particular case, the investigation revealed that large and dangerous concentrations of H2S can in specific circumstances be present within tank residues and only manifest themselves when the top "skin" of the residue has been disturbed, for example, by a person stepping into the residues.
Human Factor - Improper decision-making, absence of proper safety culture, over-reliance on a false sense of safety (i.e. ‘we have always done it this way with no problems’), cultural differences/ considerations wherein lower ranks are unable to challenge wrong decisions made by senior officers, crew behaviour when commercial pressure is exercised.
Commercial pressure - reportedly felt by crew to complete hold/tank cleaning in a time window that otherwise would not be considered adequate. As a result, crew members knowingly deviated from entry into enclosed spaces requirements and best practices to complete the task on time and meet the deadlines.