
7 minute read
Vessel Performance
from Wavelength #84
Introduction
Performance has become a buzzword in the Maritime Industry in recent years. Vessel performance is not only closely related to energy efficiency and environmental impact, both of which are becoming increasingly regulated, but it is also related to vessel safety, cost efficiency and profit optimization.
Advertisement
Performance Parameters
A ship sailing through the sea is a complex process affected by many parameters that interact with each other. An easy way to categorize them is to distinguish between their design and operational parameters.
Design parameters
Hull form and propulsion system performance optimization is thoroughly studied in the design stage of new vessels. Hull form optimization is one of the major ways to influence a vessel’s performance. Progress in this field has recently been accelerated by the introduction of CFD (Computational Fluid Dynamics) analysis and faster computer processors. In this way, multiple models can be examined in a fraction of the time and effort that would be required with the traditional way of testing scaled models in a towing tank.
Operational parameters
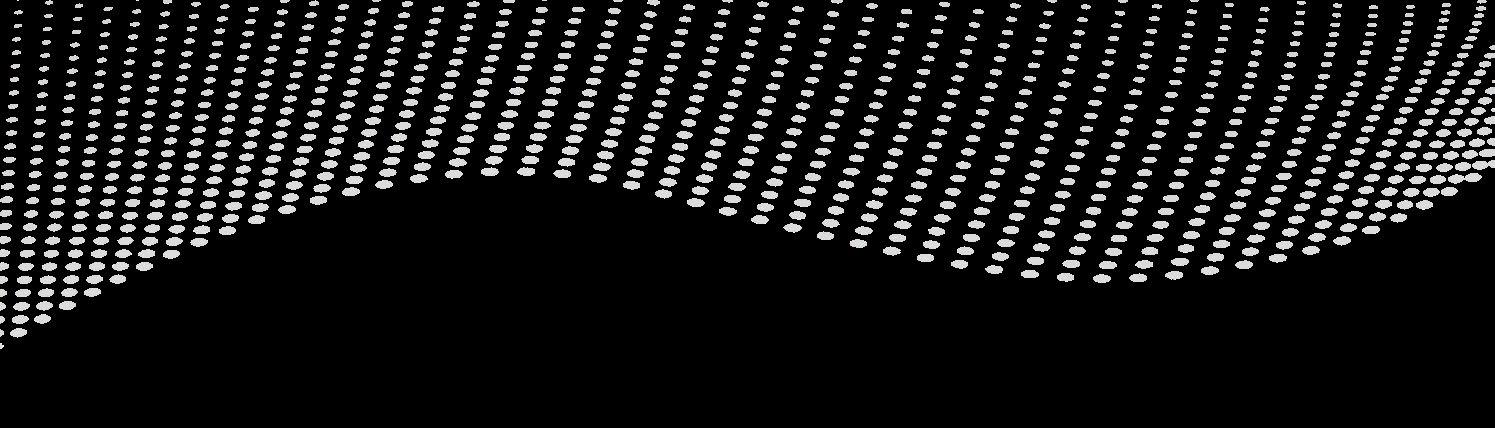
Hull form optimization consists of first determining a vessel’s capacity, principal dimensions and service speed and then the detailed hull geometry (Lines Plan). Hydrodynamic performance varies significantly with changes in draft and ship speed, so different sailing conditions are often studied at this stage. Apart from hull form optimization, but closely linked to it, the propulsion system should also be optimized for the specific project. Propeller characteristics (diameter, number of blades, pitch, etc.) and Main Engine characteristics (RPM and power output at the MCR (maximum continuous rated power output)) are determined for a specific hull form. However, hull and propeller performance cannot be studied separately as they interact significantly with each other. Similarly, the propeller and Main Engine need to have the same operating points for the enhancement of propulsion efficiency. The vessel’s performance optimization at this stage is an iterative procedure aiming to optimize the whole hull-propellerengine system performance.
Once the design parameters have been determined and a new vessel is built, performance evaluation is based on the operational parameters.
A vessel’s performance is greatly influenced by the weather. Wind, waves and current add resistance to the vessel’s movement making it harder to achieve the desired speed and subsequently requiring more power output from the Main Engine. Of course, we cannot control the weather. What we can do, though, is to ensure the optimization of a vessel’s route based on the weather forecast. This often means avoiding bad weather conditions even by taking the longer route to reach the destination.
By Konstantina Fountouli
Another important operational parameter of a vessel’s performance is the condition of the hull and propeller. While ships sail through the sea, the submerged part of the hull gets fouled, increasing the hull’s friction through the water and subsequently its resistance. Similarly, when the propeller is fouled, its performance is degraded. Hull fouling usually consists of slime, grass, barnacles and mussels, while the most common finding in propeller fouling is slime.

In order to delay hull fouling, the hull is painted with high performance anti-fouling paints. Anti-fouling paints affect a vessel’s performance in two major ways: first, they provide minimum friction resistance through the water and second, they act as a deterrent for marine organisms that usually get attached to the hull. When fouling appears, a vessel’s performance can be restored with propeller superpolishing and/or hull cleaning.
Hull fouling is also influenced by the vessel’s operational profile. Long anchorage stays and sailing through tropical waters both facilitate the marine growth on the hull and propeller, while sailing at fast speeds and through cold waters can delay the appearance of fouling.
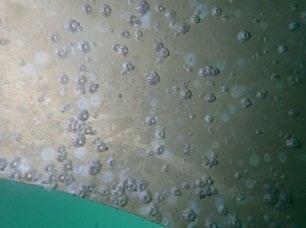
Just as importantly, the condition of the Main Engine has a direct effect on the overall performance of a vessel. An evaluation of the Main Engine’s performance is made based on the Maker’s recommendations. The main parameters involved in the performance evaluation of the Main Engine are:
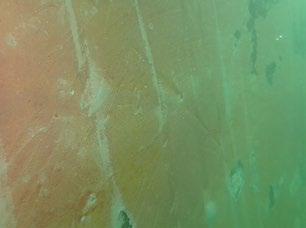
• Barometric pressure
• Engine speed
• Ship’s draught
• Mean indicated pressure
• Compression pressure
• Maximum combustion pressure
• Fuel pump index
• Exhaust gas pressures
• Exhaust gas temperatures
• Scavenge air pressure
• Scavenge air temperature
• Turbocharger speed
• Exhaust gas back pressure in exhaust pipe after turbocharger
• Air temperature before T/C filters
• ∆p air filter
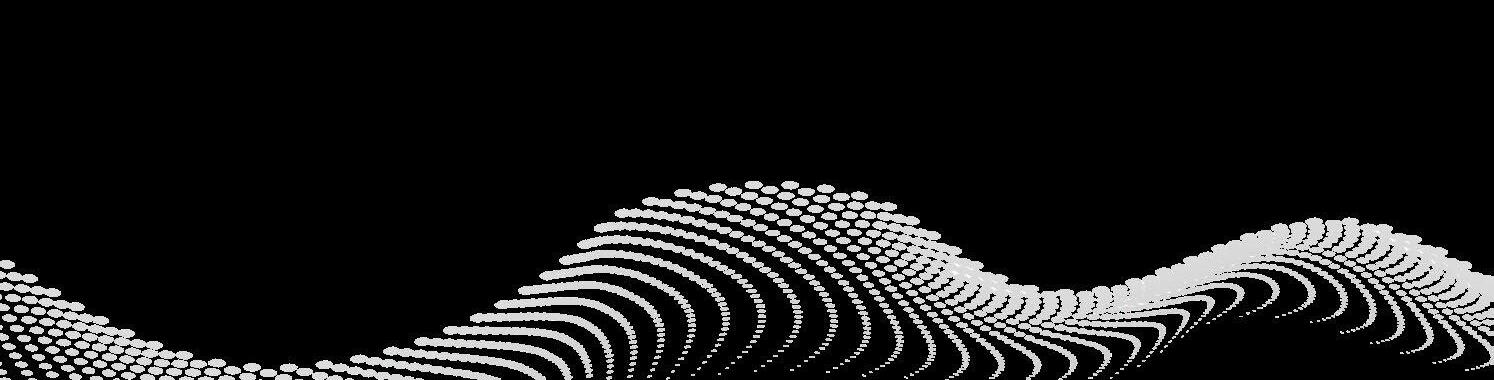
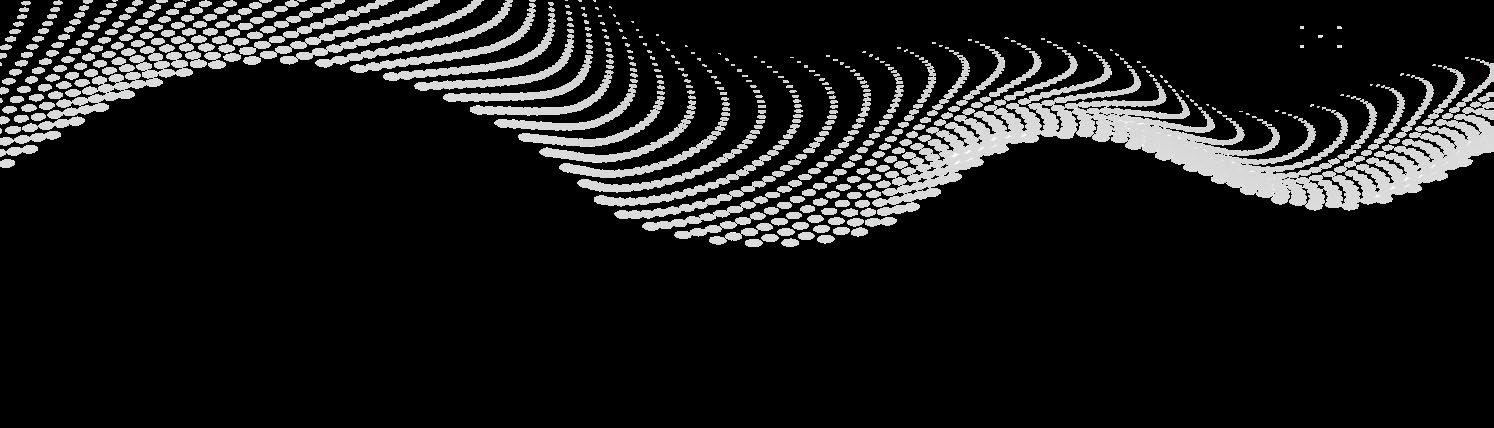
• ∆p air cooler
• Air and cooling water temperatures before and after scavenge air cooler
The observations of these parameters are documented in the Maker’s evaluation forms and are compared with earlier observations and the results of shop and sea trials of the specific engine in order to assess its condition. Deviations in the observations of the Main Engine’s current condition compared to earlier documented conditions are an indication of what engine components should be overhauled and when the overhauling should be carried out. However, not all parameters can be evaluated separately, because changes in one parameter can influence another parameter. For this reason, these parameters must be compared to the influencing parameters to ensure correct evaluations.
For instance, an impression of the Engine’s load can be depicted by the average Mean Indicated Pressure (pi). The Mean Indicated Pressure for each cylinder should not deviate a lot from the average value of all cylinders. The acceptable limit for this deviation is provided by the Maker.
The relation between the average Mean Indicated Pressure and the Engine’s speed is described by a model curve for each Engine. Deviations from the model curve show whether the propeller is light or heavy, i.e. whether the torque on the propeller is small or large for a specified speed. If this is compared to the draught and under the same weather conditions, then it is possible to judge whether the alterations are due to changes in the draught or an increase in the propulsion resistance due to hull fouling. In a similar way, the evaluation of all parameters is made taking into account how they interact with each other.
Turbocharger efficiency is also an important part of Main Engine’s performance. Turbocharger efficiency reductions can normally be related to “flow deterioration”, which can be counteracted by regular cleaning of the turbine side and possibly the compressor side.
The performance of Auxiliary Machinery is equally important since all the pieces of equipment on board are linked to one another and the best way to ensure optimal performance is proper maintenance according to the Maker's recommendations.
How do we monitor our Vessels’ Performance?
A number of different techniques have been employed for the evaluation and optimization of our fleet’s performance. The most important of them are described below.
Propulsion optimization
Propulsion hydrodynamic improvements
26 of our 41 vessels are equipped with propulsion improvement energy efficiency devices like propeller ducts, rudder bulbs, propulsion improvement fins, etc. For five of these vessels, the energy efficiency devices were retrofitted during their 1st Special Survey.
Our latest Newbuilding vessels are equipped with SARB (Samsung Advanced Rudder Bulb), Saver Fins (Samsung Advanced Vibration and & Energy Reduction Fins), SAVER Stator-D (Partial Duct) and STAR Propeller for improved efficiency.
Hull & Propeller Maintenance

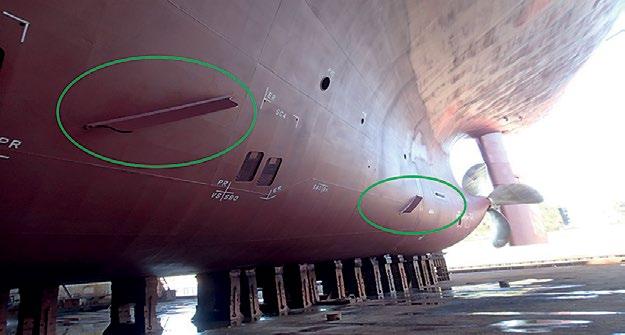
As per our planned maintenance policy and taking into account the obtained benefits in terms of reduced fuel consumption, hull underwater inspection and propeller superpolishing is scheduled to be carried out on all Company vessels with every 4-6 months.

Hull and propeller conditions are monitored using the software Fleet Manager and ANKO Performance developed by Helintec. The software produces Power-Speed and FOC-Speed diagrams with the present condition of a vessel in comparison with the expected performance based on the hull’s geometry, model test data and the vessel’s sea trials results. Deterioration of a vessel’s performance that can be detected using the software, is often an indication that the vessel is in need of propeller superpolishing and/or hull cleaning.
Hull coating systems
In the last 10 years, antifouling paints based on “silyl acrylate” technology have been applied to the underwater hull part of our vessels.
The main benefits of the silyl acrylate SPC antifouling paints are the following:
• Controlled polishing rate
• Excellent application properties
• Reduction of hull roughness because of the polishing and smoothing action of SPC antifouling.
• Anticipated average annual fuel savings of approximately 3-4% compared to conventional antifouling paints. On our latest Newbuilding vessels, antifouling paints of silyl methacrylate technology have been applied.
Machinery Optimization
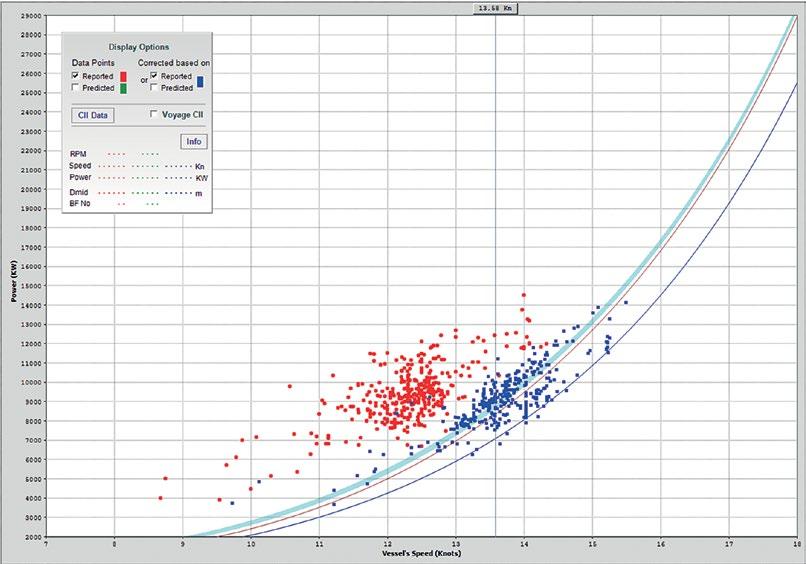
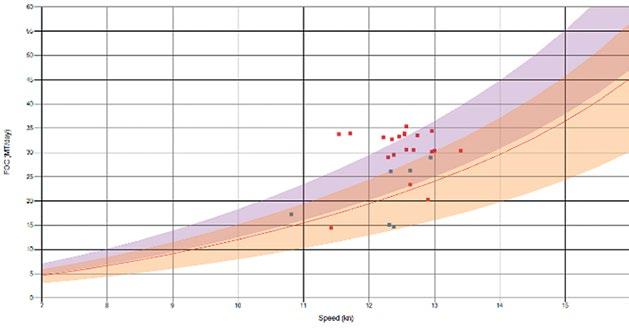

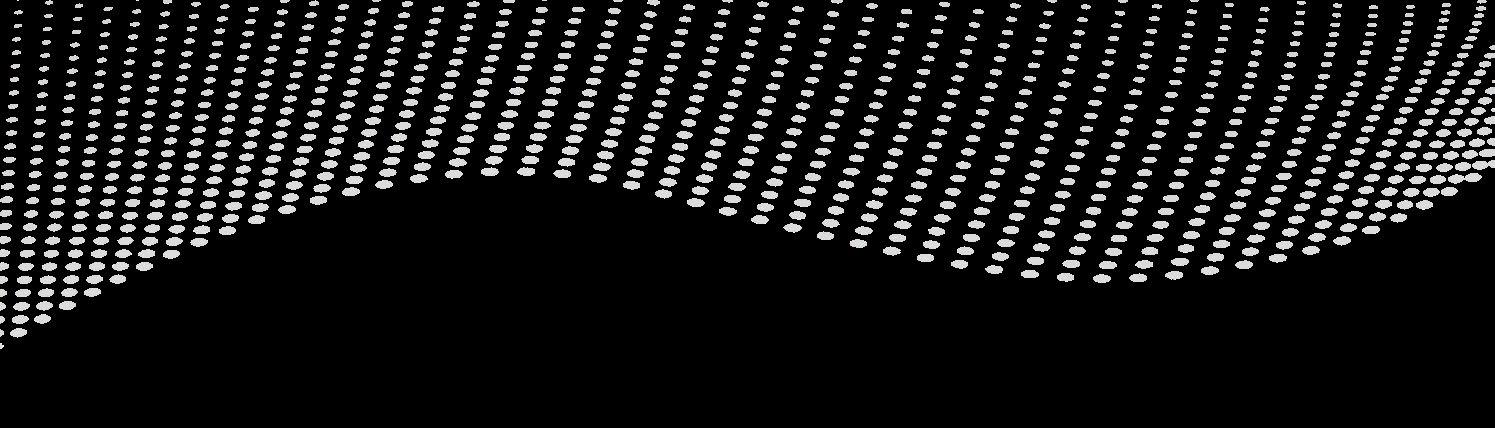
Machinery Maintenance
The Company’s PMS (Planned Maintenance System) for the maintenance of the Main Engine and auxiliary machinery is based on the Makers’ recommendations ensuring optimal machinery performance. The PMS, based on operational experience and the Makers’ revised maintenance instructions, is updated / amended as required.
In addition to the Planned Maintenance System, Condition Monitoring techniques are used to maintain the optimal performance of the machinery. Vibration Monitoring and Infrared Thermography surveys by specialized companies are scheduled regularly on our vessels. Condition monitoring is also achieved with lube oil (LO) analyses, hydraulic oil analyses and drain oil analyses from the Main Engine, which are carried out at periodic intervals. If the LO analysis result is “Caution” or “Urgent”, corrective measures are taken in order to restore the LO to normal condition.
Machinery performance is also evaluated by the Makers. For Alfa Laval Purifiers, inspection by the Maker’s service engineers is made occasionally as part of their “Harbor Support Program”. Performance sheets are evaluated by the Makers of Stern Tube Air Seal type systems, ICCP and MGPS systems and Teamtec incinerators.
Performance of our latest newbuilding vessels is monitored through Samsung’s SVESSEL monitoring tool in real time.
Main Engine Performance
The performance of the Main Engine is evaluated by the following means:
• Monthly Main Engine Performance Report (ENG-004)
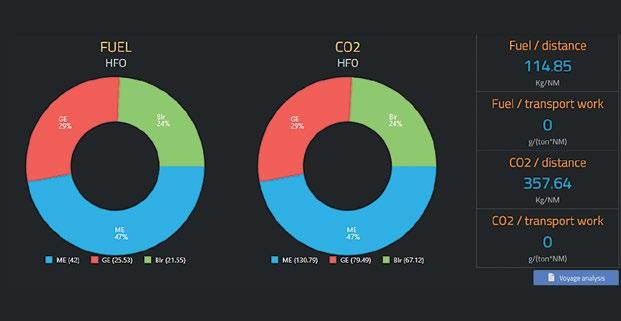
• Diesel analyzers for measuring performance of the Main Engine
• For vessels equipped with ME-C engines, Main Engine Performance is also monitored through MAN’s computerized performance monitoring system Primeserv Engine Vault.
The reported performance of Main Engines is evaluated in the Technical Department’s monthly Performance Monitoring Meetings.
Diesel Generators performance optimization
The performance of Diesel Generators is evaluated by the following means:
• Monthly Diesel Generators Performance Report (ENG-005)
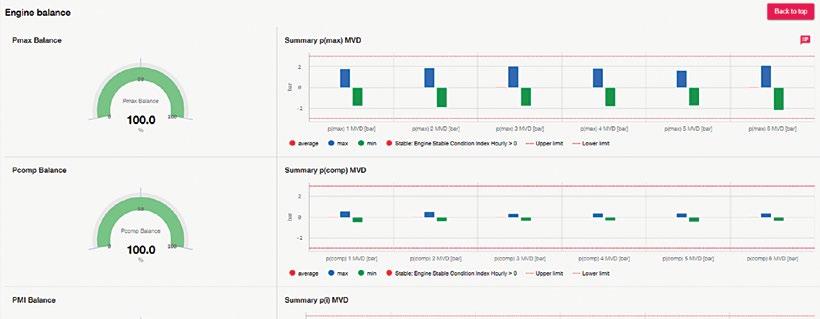
• Diesel Analyzers for measuring performance of Diesel Generators
• Computerized performance monitoring system “SHIPSWEB” of Yanmar is provided on vessels with Yanmar Diesel Generators. The reported performance of Diesel Generators is evaluated in the Technical Department’s monthly Performance Monitoring Meetings.
Energy Performance Indicators (EnPIs)
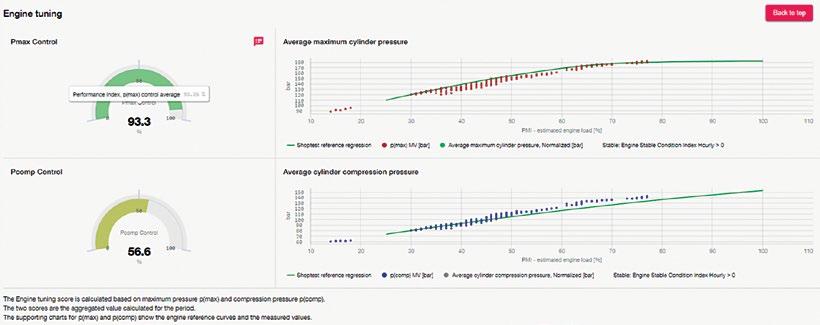
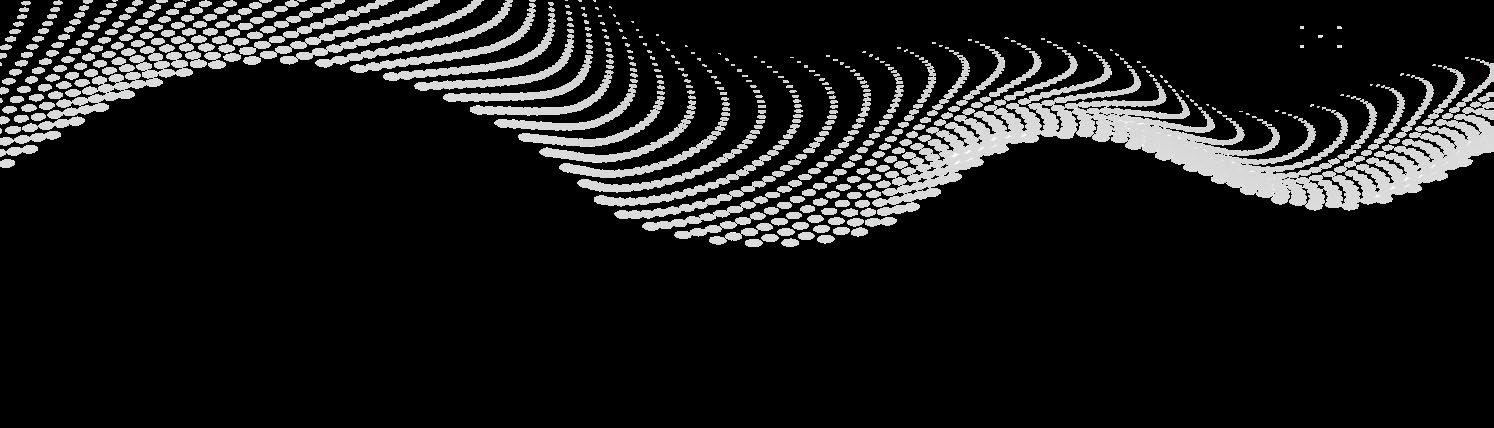
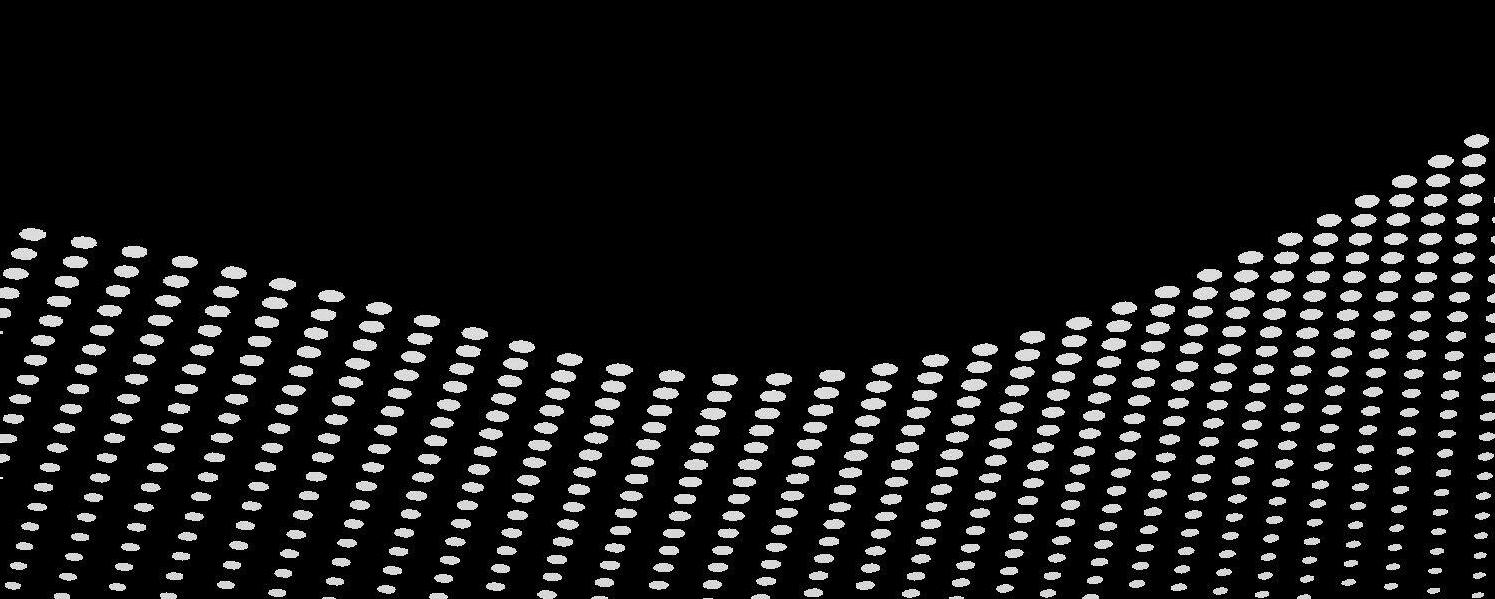
The following Energy Performance Indicators (EnPIs) have been developed and are monitored by the Company yearly in the annual review and self-evaluation of SEEMP (Ship Energy Efficiency Management Plan) and the Company’s Management Review Meetings (MRMs):
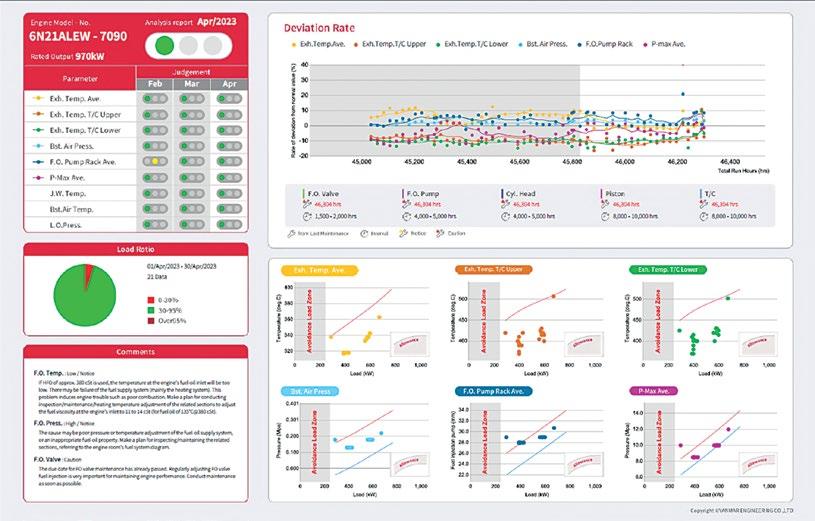
• Yearly total bunker consumption
• Bunker consumption per nautical mile in ballast condition
• Bunker consumption per nautical mile in laden condition
• Diesel Generators OperationalOptimizing Index showing the number of Diesel Generators working per day during sailing
• Average bunker consumption per vessel for each vessel group.
The Energy Performance Indicators are compared for same size vessels and evaluated accordingly every year. New targets for improved performance and energy efficiency are set every year. The maintenance and improvement of our vessels’ performance is a continuous and challenging task that requires effort from multiple sources and perhaps the most valuable input comes from our people on board who operate the vessels and know their strengths and weaknesses better than anyone.
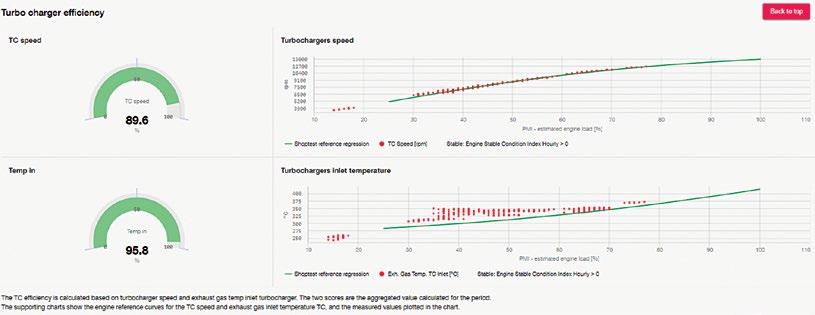