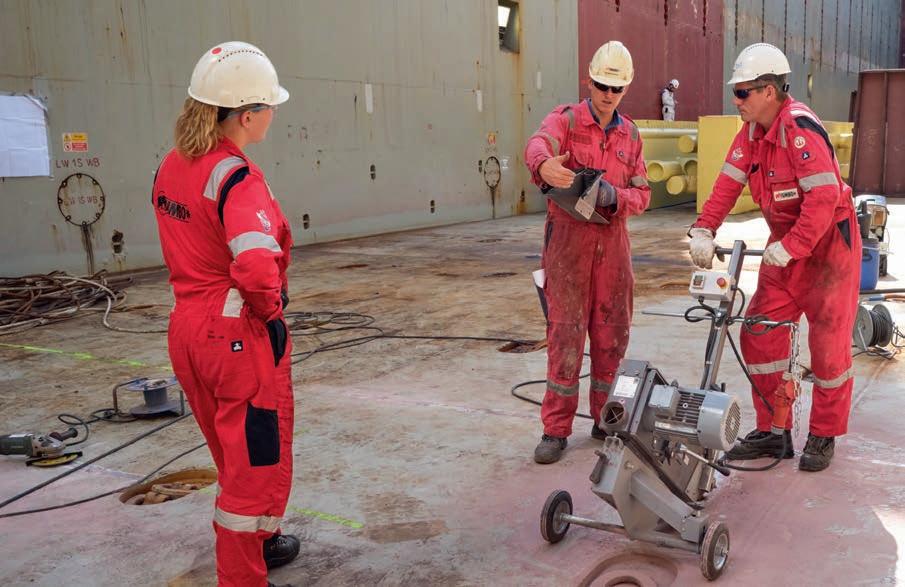
3 minute read
Jumbo’s innovatve prototype belt
Jumbo’s innovative prototype belt sander reduces fash rust
JUMBO IS PLEASED TO PRESENT AN IN-HOUSE DEVELOPED INNOVATION THAT GOES A LONG WAY TO SOLVE THE ISSUE OF PERSISTENT FLASH RUST CAUSED BY THE REMOVAL OF TEMPORARY WELDED SECURINGS ON BOARD ITS FLEET OF HEAVY LIFT VESSELS.
Advertisement
ALL PHOTOS COURTESY OF JUMBO. The prototype device was developed by one of Jumbo’s Chief Ofcers while working on his Master’s thesis. Inital results show that the device is not only faster than existng methods of removing temporary weldings, it is also cleaner for the environment, healthier for users, and improves the appearance of the ship.
Flash rust
While Jumbo’s nine heavy lif vessels are technically and operatonally in excellent conditon, their decks and hull sides have a decidedly rusty appearance. Known as fash rust, this has the potental to be detrimental to Jumbo’s reputaton for the proper management of its assets. Flash rust is caused by the corrosion of steel partcles dispersed during the removal of temporary welded securings, a process requiring the use of cutng, gouging, and grinding tools. The steel and paint partcles formed during the removal process can also be harmful to the environment and to human health. Further adding to the list of negatve consequences, the removal of the temporary welded securing is a tmeconsuming and uncomfortable task for the ships’ crews.
Users can walk behind the prototype in a standing position, which is better ergonomically-wise and produces far fewer vibrations.
Bob Heikoop, Chief Offcer at Jumbo, with part of his innovative prototype belt sander. In terms of sustainability, there are no particles entering the environment.

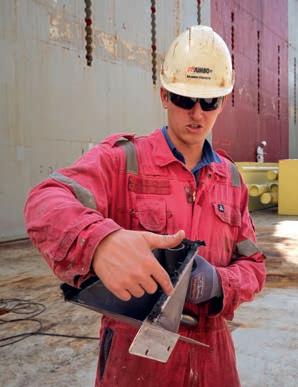

Practical problem with green potential
This situaton did not go unnotced to Mr Heikoop. He had started a Master’s degree in Marine Shipping Innovatons at the Maritme Insttute Willem Barentsz in the Netherlands in 2018, and was looking for a subject on which to focus his fnal thesis. “I wanted to combine a practcal problem that Jumbo was facing with a subject that was important to society in terms of sustainability”, he says. “Solving the fash rust problem could achieve both of these. Firstly, by reducing our environmental footprint by reducing the release of paint and steel partcles, and secondly by preventng, or at least reducing the rusty appearance.”
Innovative modifcations
Afer concluding that welding was the quickest, most efcient, and most costefectve way of securing the temporary seafastenings, the main queston that Mr Heikoop needed to address was a new way to remove the sea-fastenings that simultaneously collected steel and paint partcles. The soluton was a Fein GIMS-75 belt sander, which he modifed with the additon of a spark/molten steel partcle catcher, an extracton system, and a collecton container. The performance of the resultant prototype device was then verifed within four separate parameters: removal of paint layer, removal of top part of temporary welding, removal of botom part of temporary welding, and fatening of surrounding paint layer.
Multiple benefts
The results were overwhelmingly positve. “We were very enthusiastc about the outcome”, adds Mr Heikoop. “The modifcatons made to the GIMS-75 means that it catches and removes the steel and paint partcles. In terms of sustainability, there are no partcles entering the environment. But it is also much faster than the current way of working – on average three tmes as fast – which makes it very interestng commercially.” The prototype also yielded benefts in terms of human health, as Mr Heikoop explains, “For the person using the existng method, this meant spending the whole day working on hands and knees with an angle grinder on the deck of the ship, whereas users can walk behind this prototype in a standing positon. It is beter ergonomically-wise and produces far fewer vibratons.”
50 years of innovation
This latest Jumbo innovaton might be a small innovaton in physical terms, but in a practcal sense it illustrates the company’s proactve way of stmulatng in-house initatves. This philosophy was cemented into the company’s way of working with the establishment of the Jumbo Innovaton Program in 2011. This programme has two major aims: to develop innovatve transport and installaton solutons, and to advance Jumbo’s reliability, safety, and cost efectveness. “Jumbo is open to innovaton in terms of new techniques and new ways of working,” concludes Mr Heikoop. “Even though we’ve been in business for 50 years, we stll want to look where we can improve processes.”