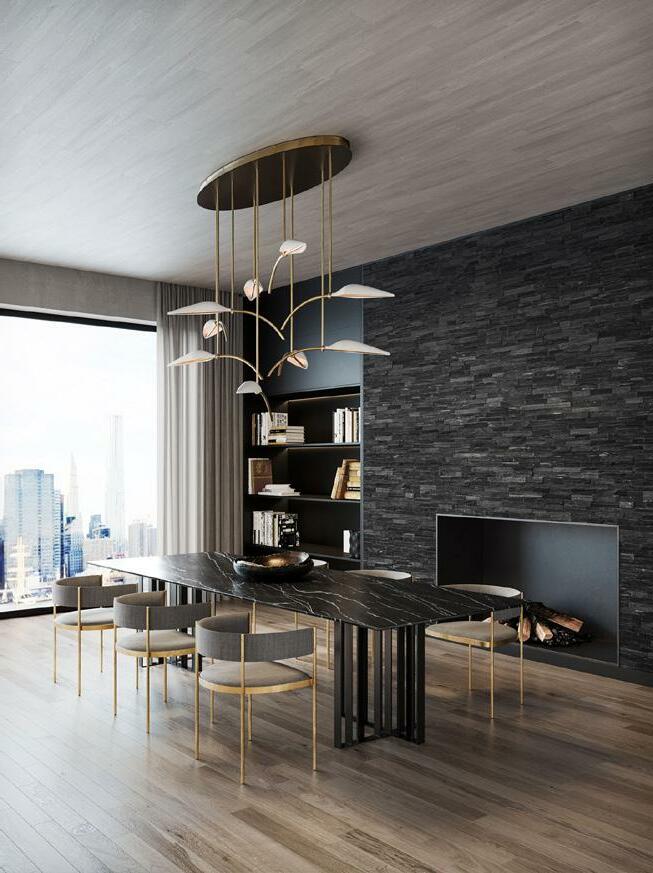
13 minute read
IN CONVERSATION Schuyler Sweet with Boyd Lighting
IN CONVERSATION Schuyler Sweet
PRODUCT DEVELOPMENT DIRECTOR, BOYD LIGHTING
Advertisement
AAnyone in the design industry who isn’t familiar with Boyd Lighting doesn’t know what they are missing. This multigenerational, 100-plus year old company produces some of the most beautifully-crafted, inspiring lighting fixtures in the country. But how they got from their humble beginnings to where they are now is a story worth telling.
When William Boyd founded Boyd Lighting Fixture Co. in 1921, fewer than half the homes in the United States had electricity. Most of those were in the East, far from his hometown of San Francisco. But Boyd had a vision. Inspired by a dazzling lighting display at the 1915 San Francisco World’s Fair, he immediately saw a future lit by this modern energy, freed from oil lamps and candles. The whole world of lighting design opened up to him.
From the beginning, Boyd sought out other visionaries to work with, including prominent architects of the day. Over the years, Boyd Lighting created electric lighting fixtures for some of the city’s landmark buildings, including the Castro Theatre and the War Memorial Opera House, the Olympic ski resort in Lake Tahoe, and the Iolani Palace in Oahu, Hawaii. Boyd Lighting also designed the electrical fixtures to light the U.S. Navy’s battleships in WWII.

Boyd Lighting started working directly with designers in the 1990s. The company co-created custom fixtures for special projects, providing personalized, one-ofa-kind fixtures and luxurious collections such as the glitzy Kentfield Collection in the 2000s. Boyd Lighting also launched Lightspace during that time, a division that works exclusively with architects.
Now entering its second century of business, Boyd Lighting is now based in Colorado and is led by third-generation Jay Sweet, and his son Schuyler Sweet, Product Development Director, who shares Jay’s passion for blending time-honored artistry with modern day technologies to create lighting for exceptional residential and commercial spaces.
Each of the FOUR
GENERATIONS to run the company had their own style, and I believe that mine is a HOMAGE TO OUR PAST, of classic modern, clean, and elegant design. You obviously grew up in a very creative and innovative environment, and lighting is inherent. When did you first get involved with the company?
My journey at Boyd started many years ago when my first-grade class came into the shop in San Francisco, and each of us was able to build a table lamp to take home. When we were on family vacations, if we were in a city with a design center, we would walk through them, say hi to our reps, and see what was new. It was so fascinating to see the creativity expressed in the unique products. During my middle school years, I would help build catalogs, sit at a table with my disc man, listen to Sublime and Eminem, and build finish samples. Occasionally I would assist AP if someone was on vacation for a week or two during the summer and send out order acknowledgments to reps and clients.
We recently sat down with Schuyler to learn more about his role and to give us a behind-thecurtain look at this iconic company and his plans for the future. I joined Boyd full time in January of 2012 as a Marketing Assistant and moved to a Regional Sales role a year later. After working on the road for five years, I realized that my passion was for design and working with designers and our team to create products that inspire and delight. I moved to CO four years ago to take
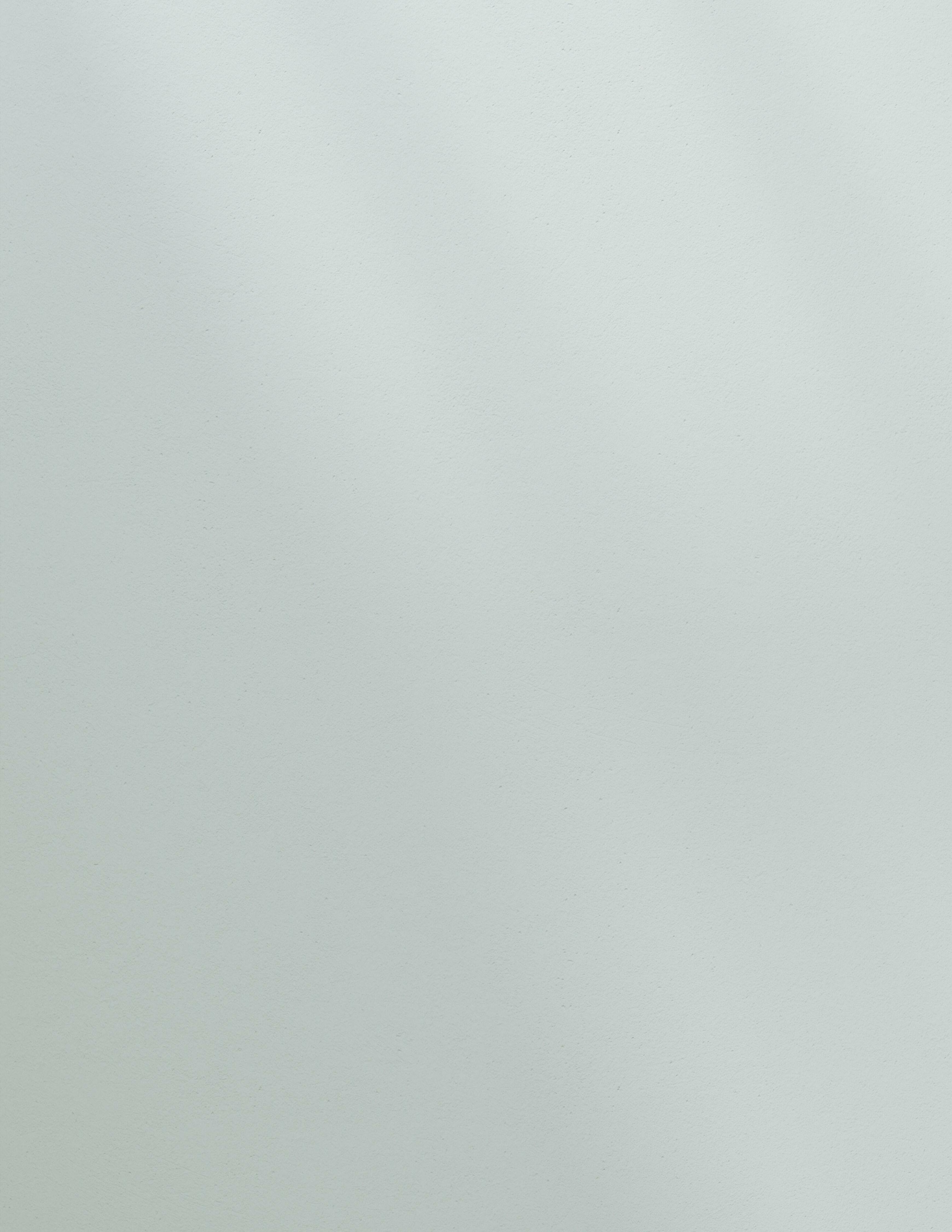
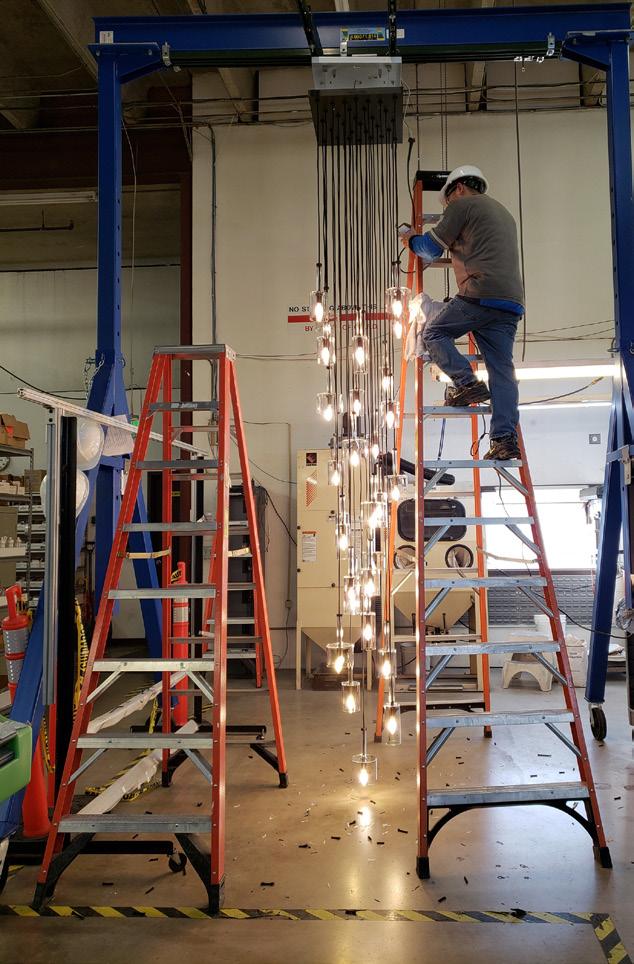


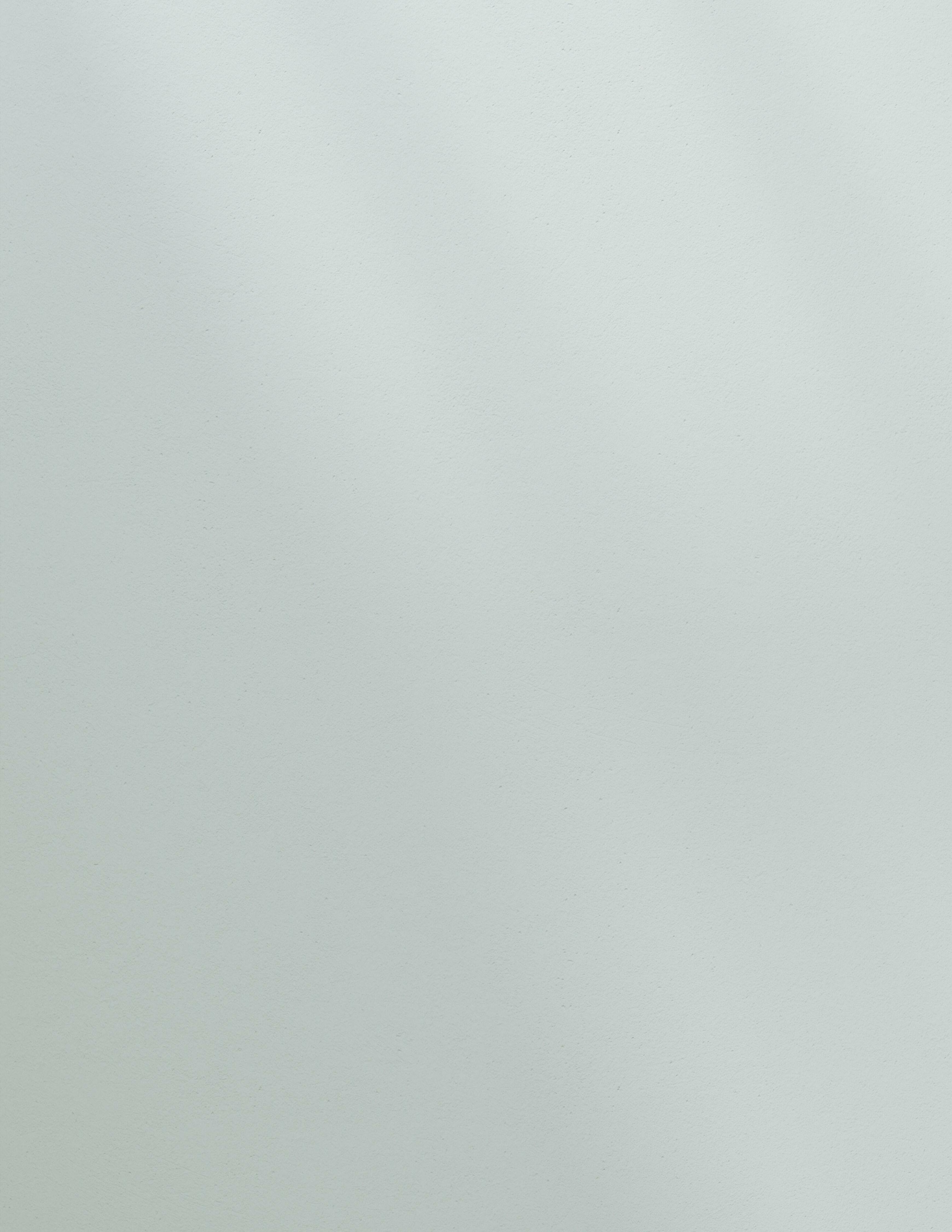
over New Product Development, and I have spent that time creating my vision for Boyd. Each of the four generations of my family to run the company had their own style, and I believe that mine is an homage to our past, of classic modern, clean, and elegant design. I wanted to bring levity to the brand and a softness, referenced in the radiused corners, less chunky materials, and utilizing LED's to design in new and different ways.
Tell us a bit more about your current role.
As of now, I'm in charge of New Product Development, Marketing & Sales. When I took over NPD 4 years ago I wanted to distill Boyd back down to a simpler aesthetic, one that puts the emphasis and focus on clean lines, elegant details, and beautiful finishing.
What inspires your design decisions?
I'm inspired by nature, by art, by food, by travel, and by people I meet along the way. I'm inspired by the endless creativity of those that I have the luxury of calling peers. For our 100th year, I wanted the focus to be on materiality, which is why you see fixtures made of slip cast porcelain like the Spire, and the Nebula, featuring hand carved alabaster. I wish to create beautiful lighting that inspires and delights our discerning clientele by blending the most advanced LED technology, with amazing design, creating handcrafted fixtures, made to order in 6-8 weeks in our shop in Colorado.
It’s clear the artisans and craftspeople who create your pieces are exceptional. How many does Boyd currently work with and where do you discover new talent?
We have about 25 men and women on the shop floor who handcraft our amazing fixtures. Marzell is our Polishing Lead, who has been with us for 22 years. His claim to fame is that he dances while he polishes and always has a great time. Paul in Antiquing has been with us for seven
Wwe antique AS
years and, with his great eye, can match a lot of custom finishes; Christy in Wire and Assembly lays down the most amazing gold


leaf finishes. We have Linda, who runs a really tight ship in Pack & Ship, as we need these fixtures to show up when they are supposed to and undamaged.
Discovering new talent is not easy these days, so we often rely on the men and women in our shop to give us references. We also utilize the local schools where people are training to master skills that allow them to operate water jets, mills, and Haas machines.
Take us through the process from deciding on the design to the end product.
Once we've decided on a design, we will initially model the fixtures at the scale presented by the designer, then utilize one of our 3d printers to print the individual parts to see how they will go together and if the scale needs to change. We'll then work with the designer in our shop to work through the design details. During Covid, this wasn't possible, so we were sending 3d printed photos back and forth to Toronto with Jake Olivera on the Spire and Duet Series. The metal prototype is typically pretty close, but we will often need three proto's before we've worked out all of the kinks of the manufacturing process.
Tell us a bit about how new technologies have influenced this process - both negatively and positively.

Our shop utilizes both new and old technology. The beauty of technology is that it speeds up a lot of processes. It's much faster to 3d print prototypes to find the correct scale than to make them. We also leverage our two Haas machines to do a lot of the work of a manual mill. We still use our hand mills for simpler parts and awkward parts, and these mills, built over 50 years, last and they run like clockwork. We antique as we did in 1921, and we still gold leaf as we did 100 years ago. Our shop is a blend of old and new, both in processes and in our team. We leverage the knowledge of those around 15-33 years to teach those who have only been there 1-3 years.
LEDs have allowed us to design in new and different ways. Before, we had to design around an A Lamp and create a stick with a shade. Now we can embed thin LEDs in minuscule spaces, like our Branch/Axis/Ovalo Series, which features just a 5/8" brass tube. That being said, LEDs need a driver to power them, and drivers are not always as small as we'd like. As we are designing slimmer fixtures, drivers have less room, meaning that sometimes they have to be mounted remotely. Designers and architects need to be aware of this in advance to know where to put it.
It goes without saying that the past couple of years presented many challenges for businesses. What were some of the obstacles Boyd faced and how did you work through them?
I think all manufacturers faced a lot of similar challenges regarding obtaining the materials and parts needed to make the products. We've also faced huge price increases, as our cost of many parts and products have gone up 50-100% over the last two years. The good news for us is that we are a metal shop, so our greatest needs are sheet stock, bar stock, and tube stock. These are much easier to come by than full fixtures or assemble to order manufactured parts. We have all dealt with delays, and we have dealt with the great resignation. The good news is that we have an amazing core group of people that make the engine hum, and we have been able to utilize cross-training to ensure that if we lose someone, we can find someone else to fill the gap until we bring in someone new.
Do you see a shift in what designers are looking for with lighting?
Lighting is in many ways having a renaissance. There are so many amazing companies creating fantastic products. We know designers are always looking for something new and unique, which is what we try to create for them. It's important to layer the light in a space, so you need pendants, sconces, table, and floor lamps to accompany the architectural lighting. We want to provide all of those options to our clients to ensure they have what they need to create a warm, welcoming environment that works within their design
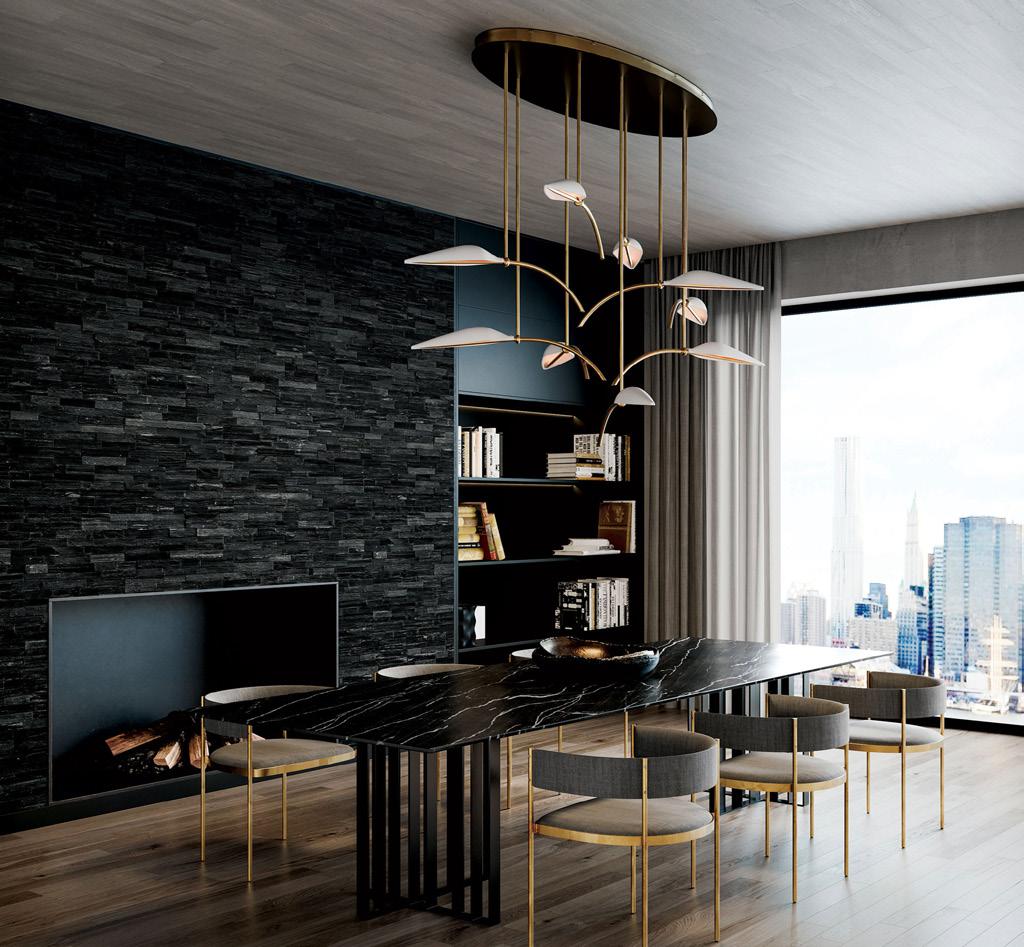
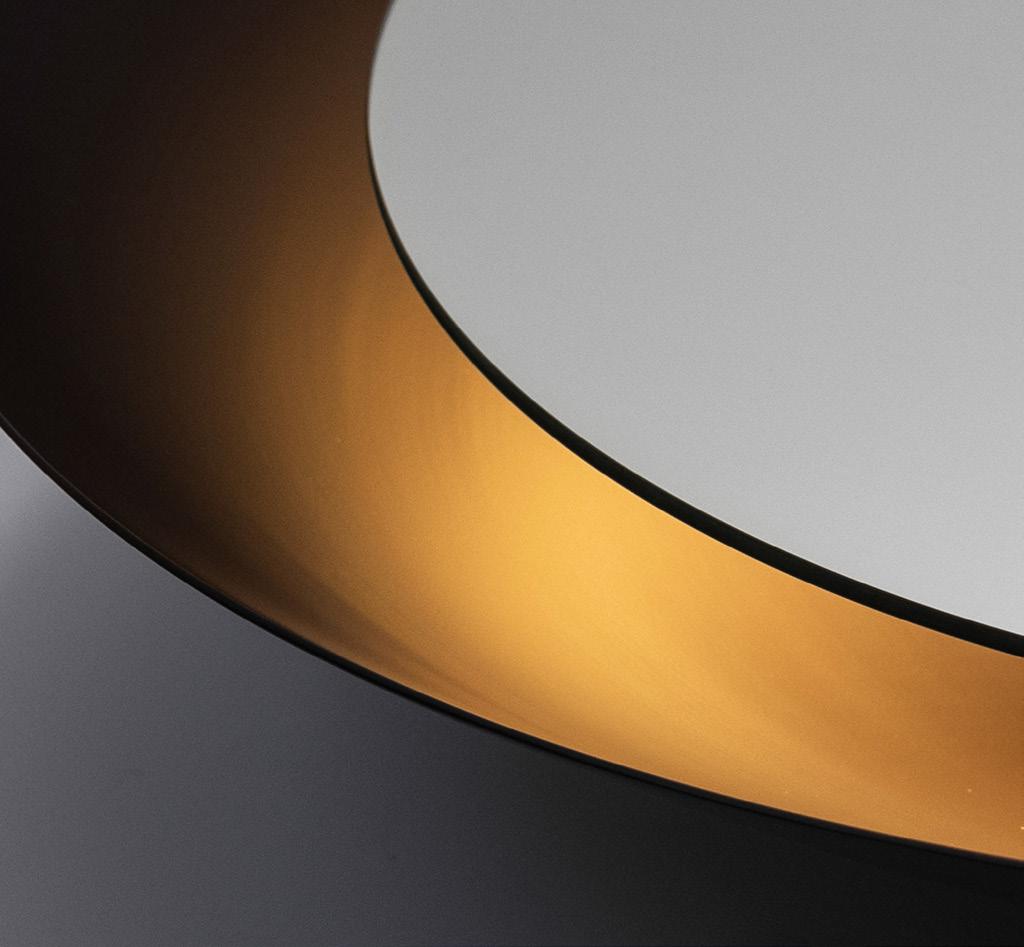
scheme.
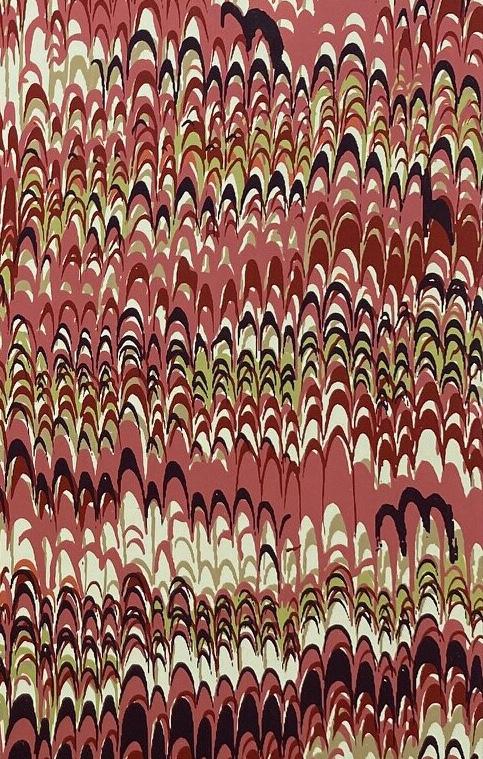
Boyd is always on the cutting edge, and we are not alone in our anticipation of what we can see from your company in the future. Can you share what we can look forward to this year and beyond?
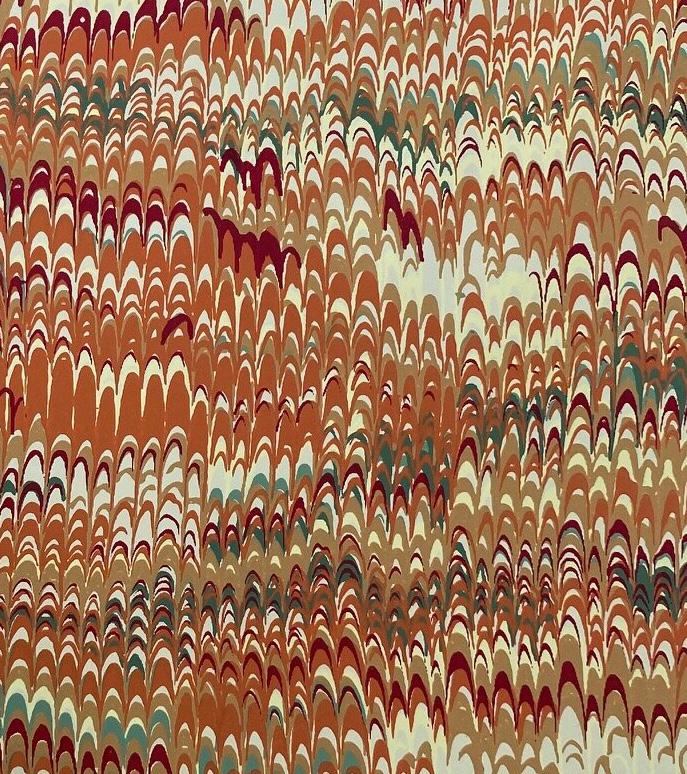
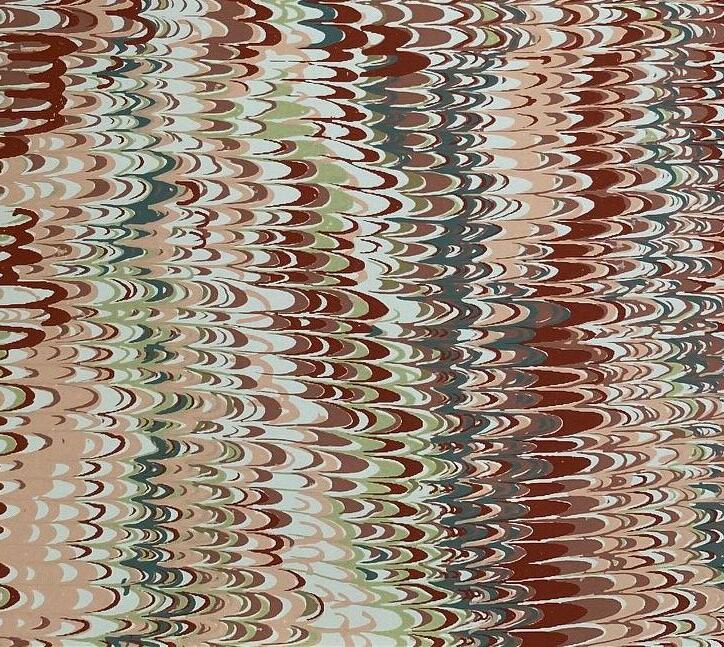


In January, we launched our first decorative illuminated mirror, the Eclipse, and the response has been great. We will be launching a second illuminated mirror in the summer that will be absolutely stunning. We are working to create a couple of art lights for the summer with custom-designed LEDs that are the best in the industry. We have a few other lighting collections that will continue to launch through summer and into fall, focusing on brass, glass, and alabaster materials. We are always inspired, discovering and planning for the future. So stay tuned!
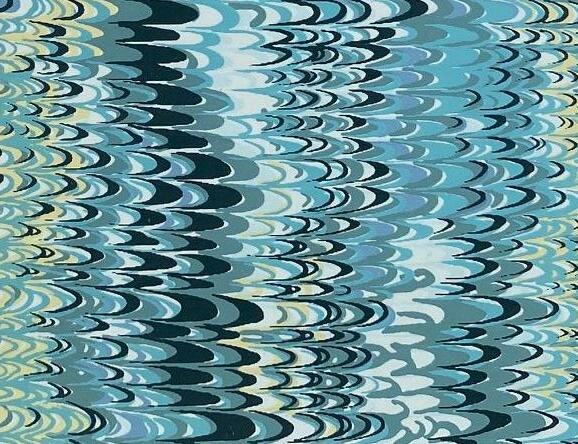
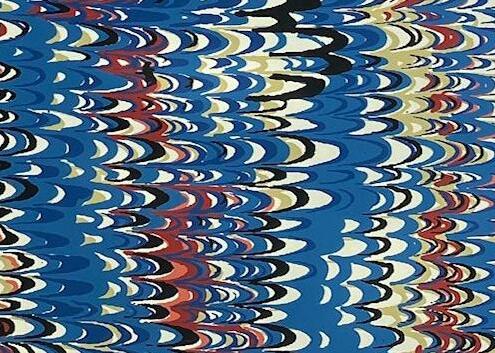
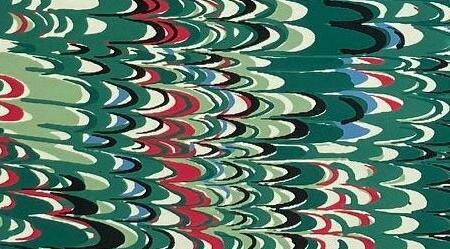
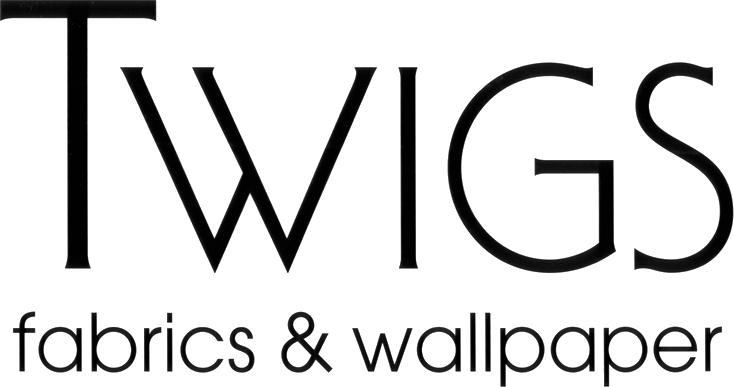
INSTALLATION SAVERS
Last Minute Details? No Worries. No Problem.
Many of the items available on the showroom floor are yours for the taking. Add one or all of these elements to your list to complete your installation day shopping bag.
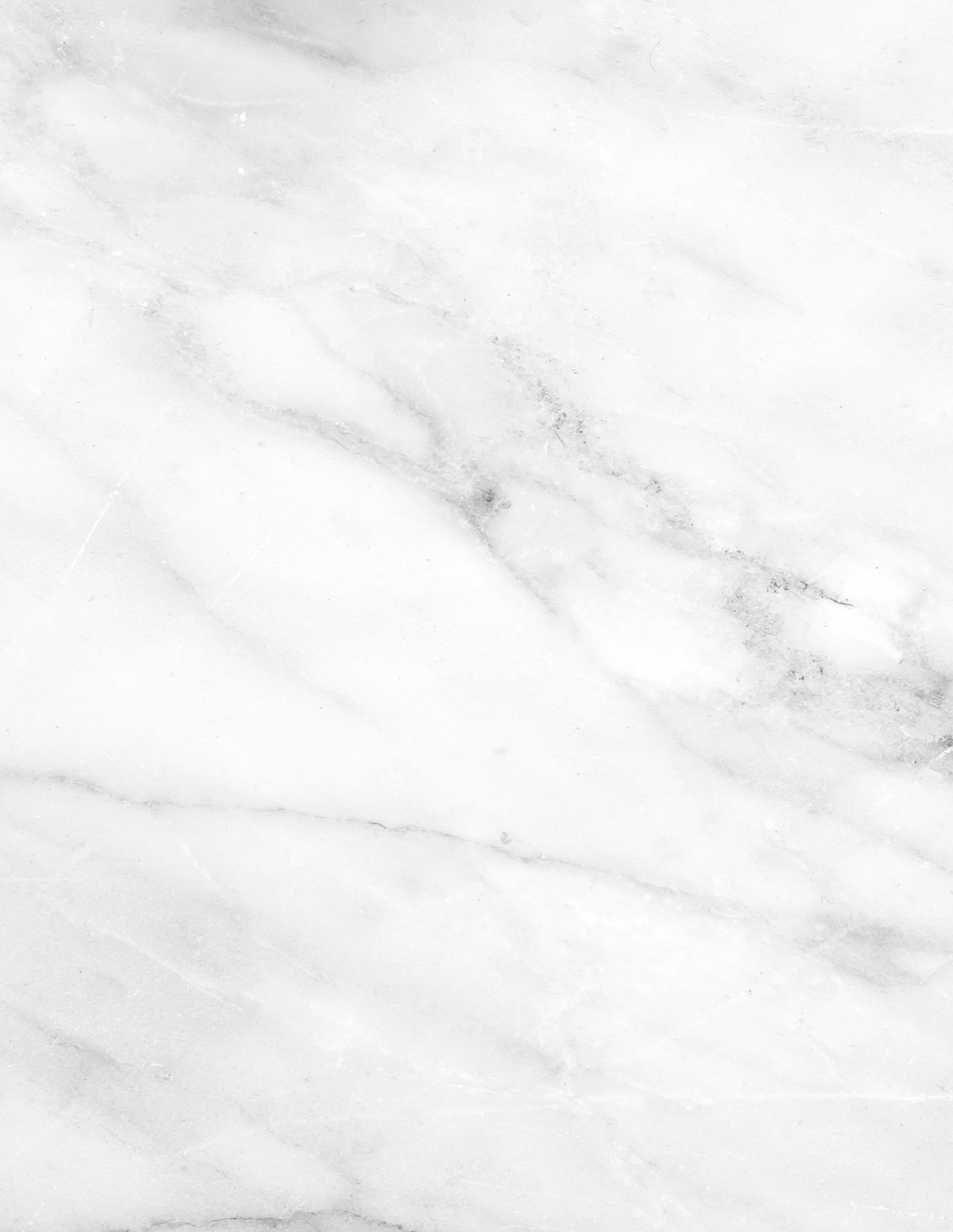
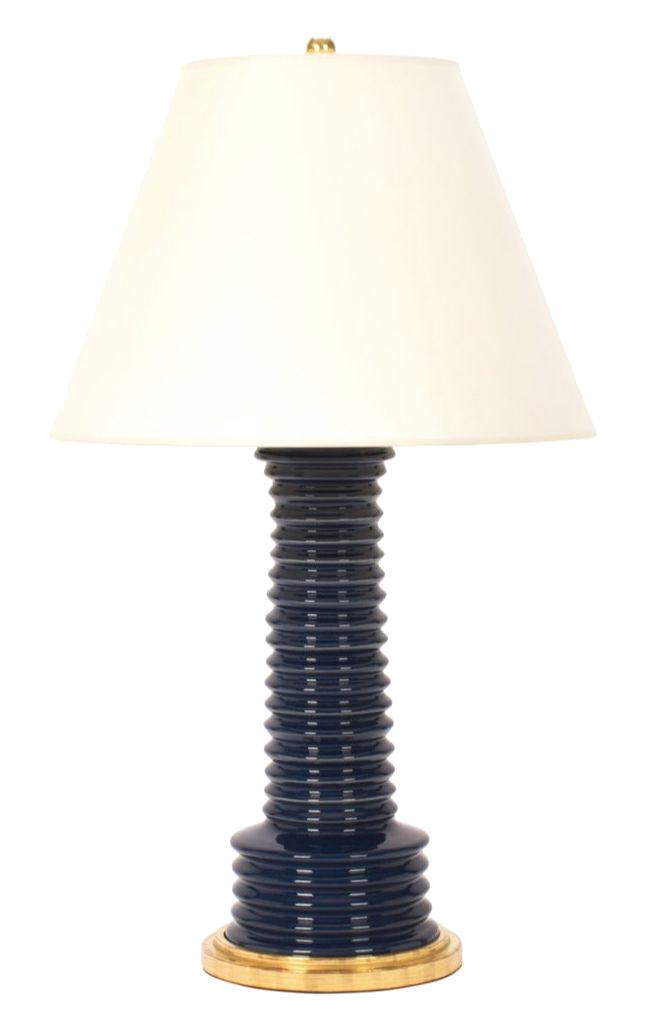
One-of-a-Kind Handmade Lamps The Perfect Drink Table

Last Minute Coffee Table Change?
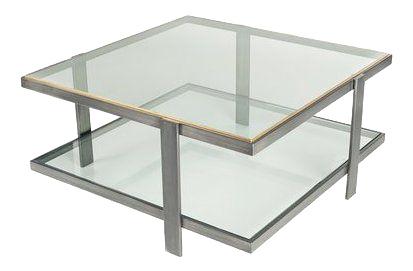
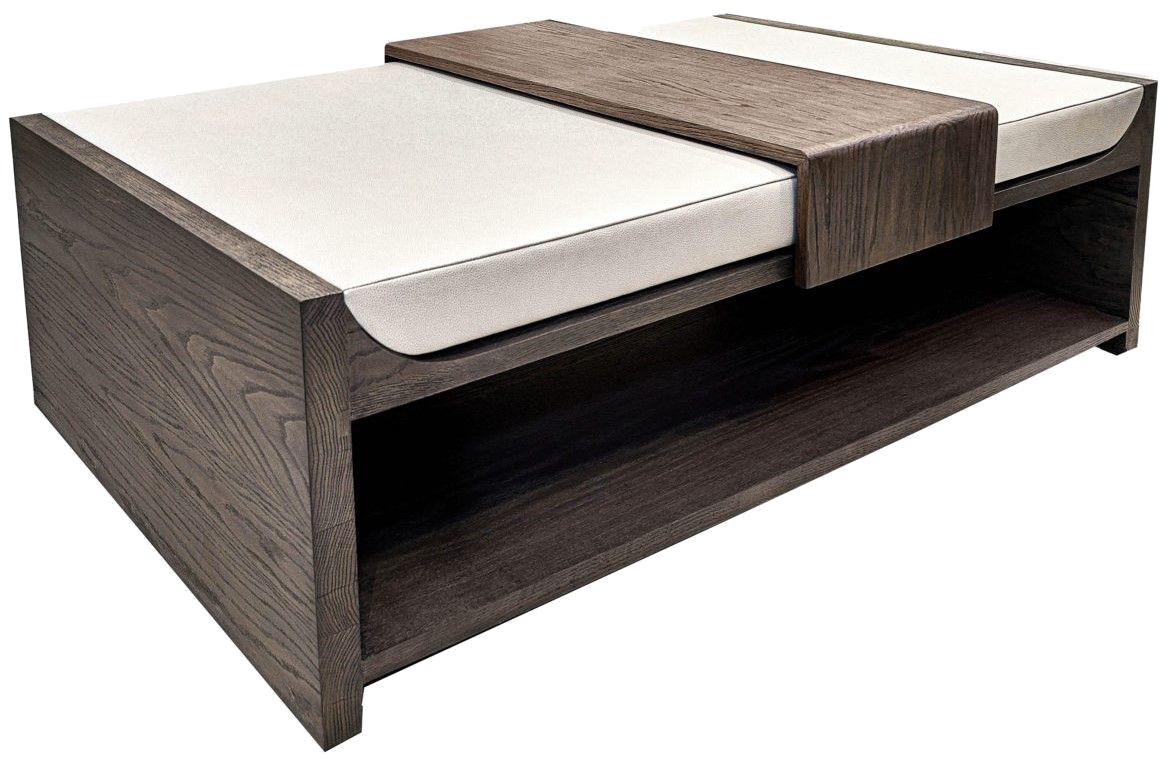
Or Try an Ottoman instead?
AMERICAN REPRODUCTIONS MADE TO LAST

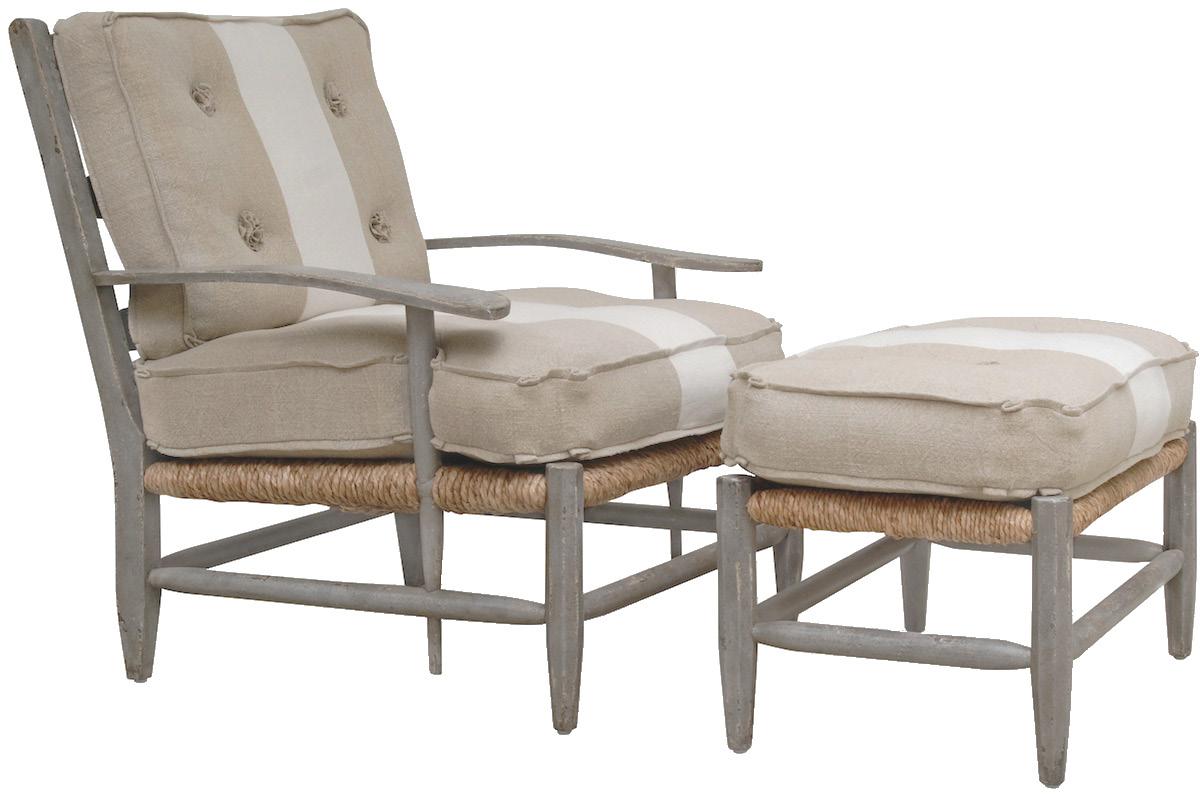
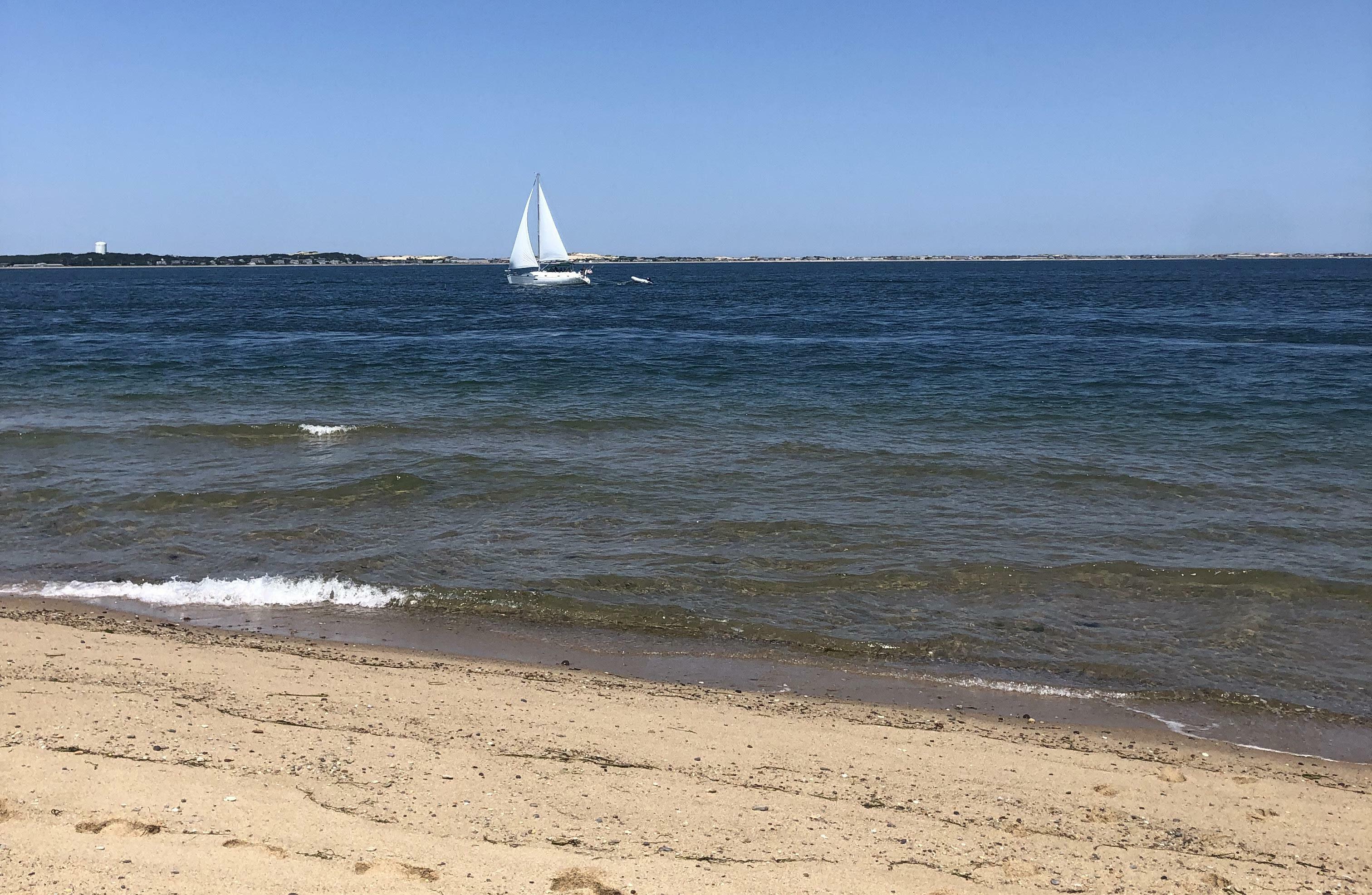
Traditional 2
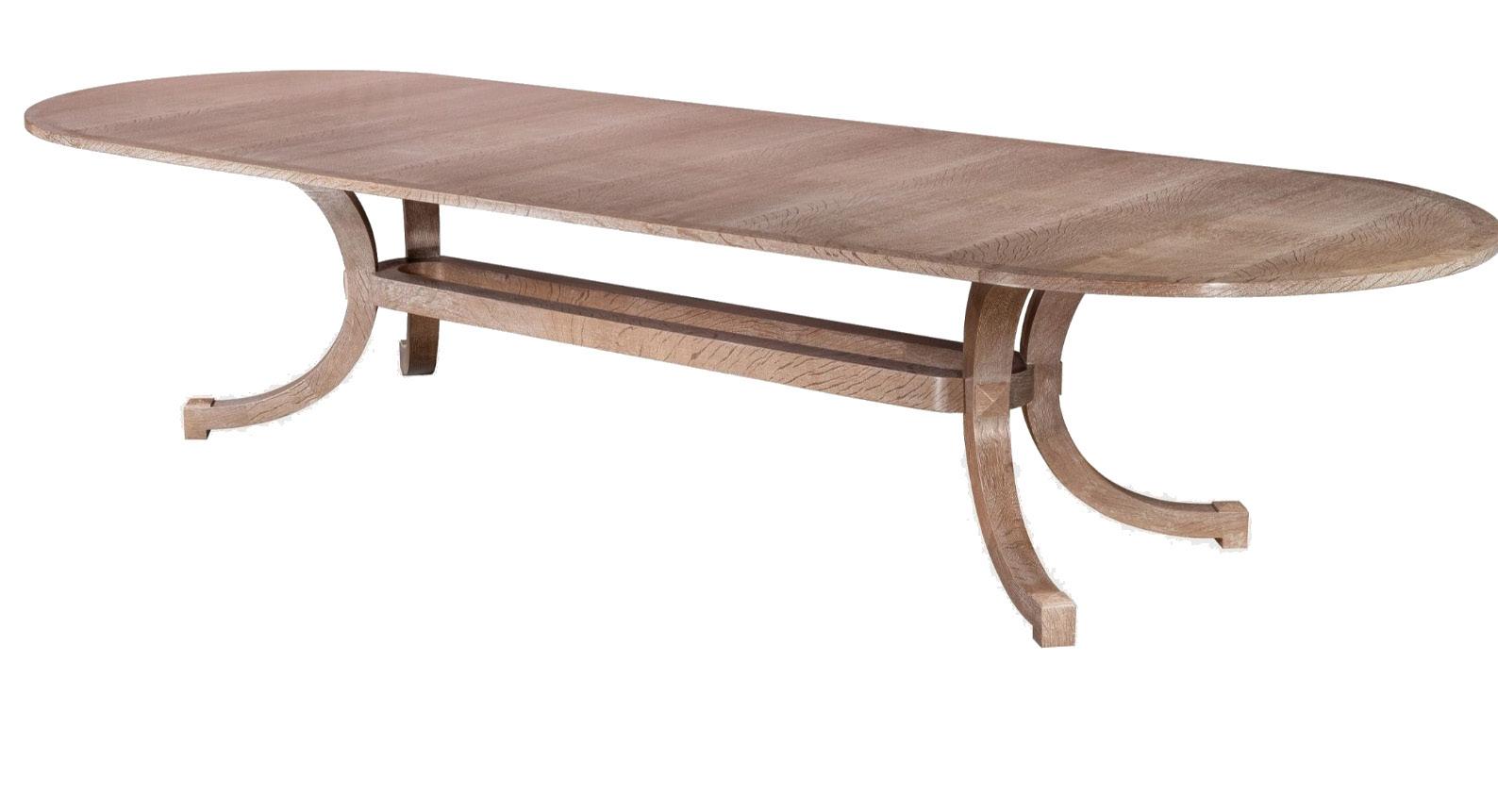
1
Order 6 RhythmProportion 8 Symmetry 5 7
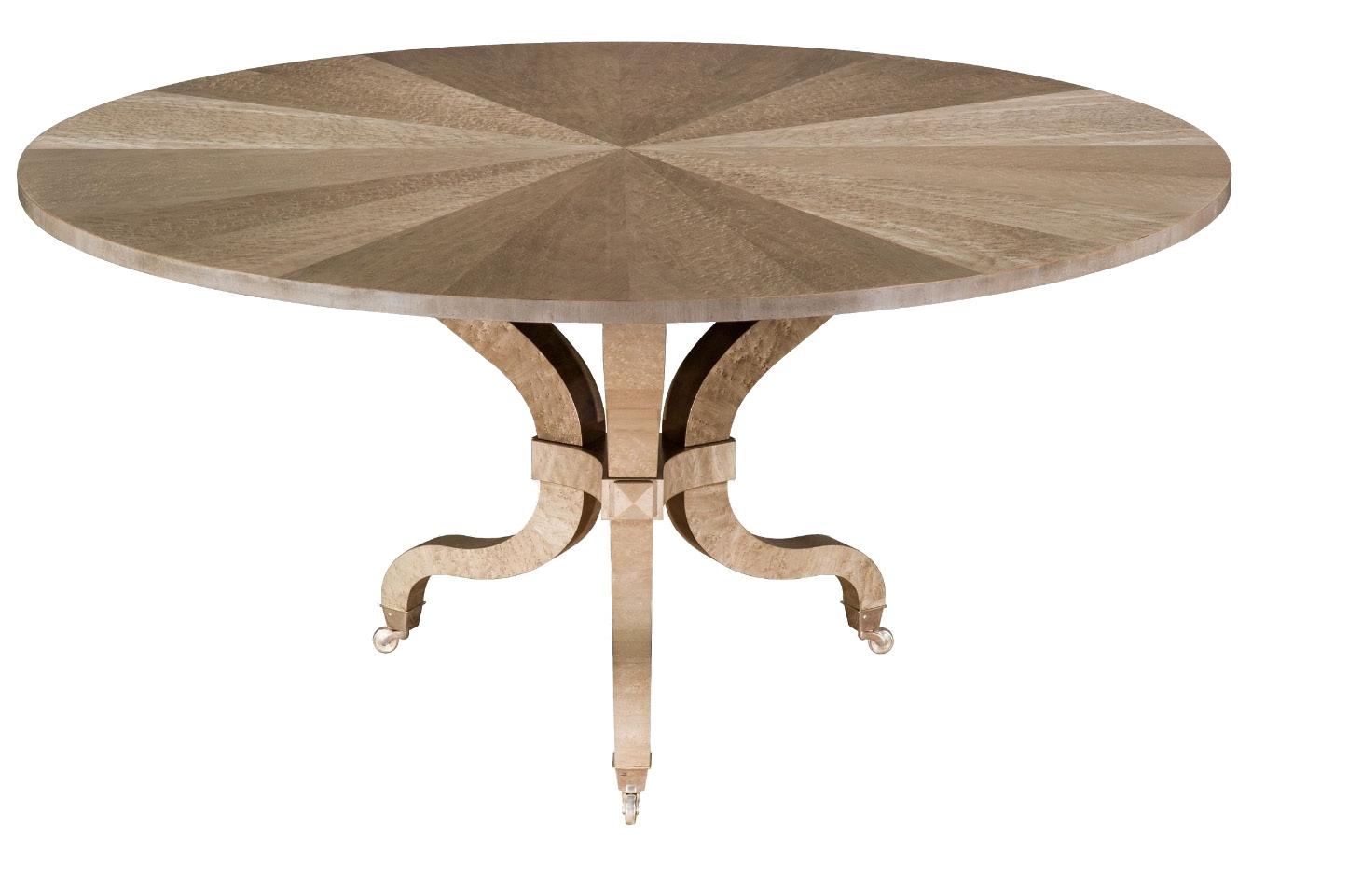
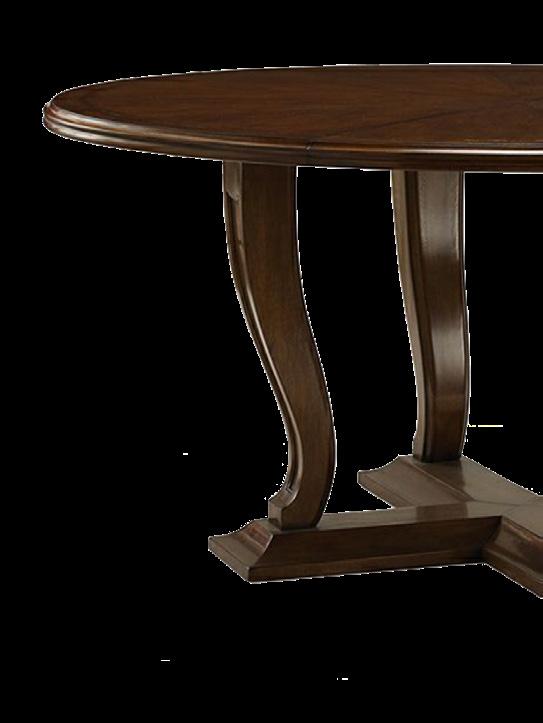
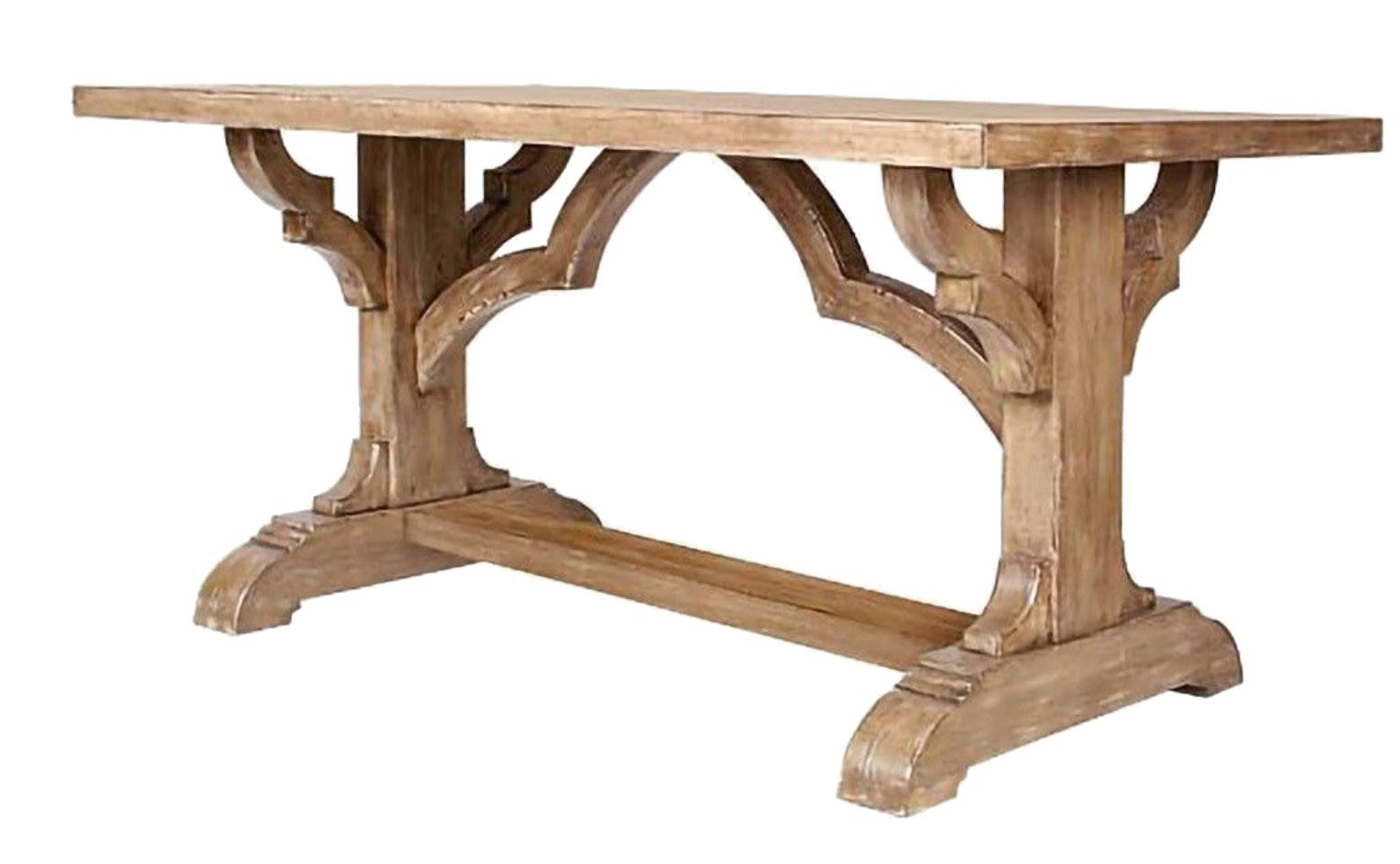
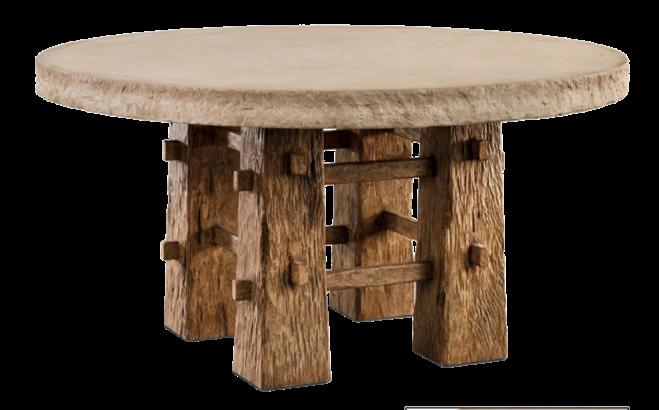
3
4
1 KEITH FRITZ FINE FURNITURE - Grecian 3 Dining Table | 2 KEITH FRITZ FINE FURNITURE - Nantucket 3 Dining Table | 3 MINTON-SPIDELL - Trestle Table | 4 JASPER FURNITURE AND FABRICS - MALEVICH GAME TABLE | 5 MULLIGAN’S - Provincetown Pedestal Table | 6 ARTIFACTS INTERNATIONAL - Mill Valley Round Table | 7 DAKOTA JACKSON - Executive Suite Dining Table | 8 JASPER FURNITURE AND FABRICS - FRENCH DINING TABLE
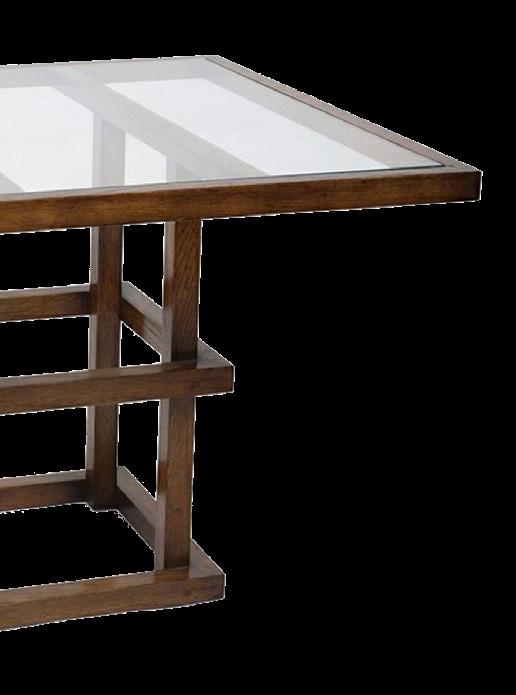

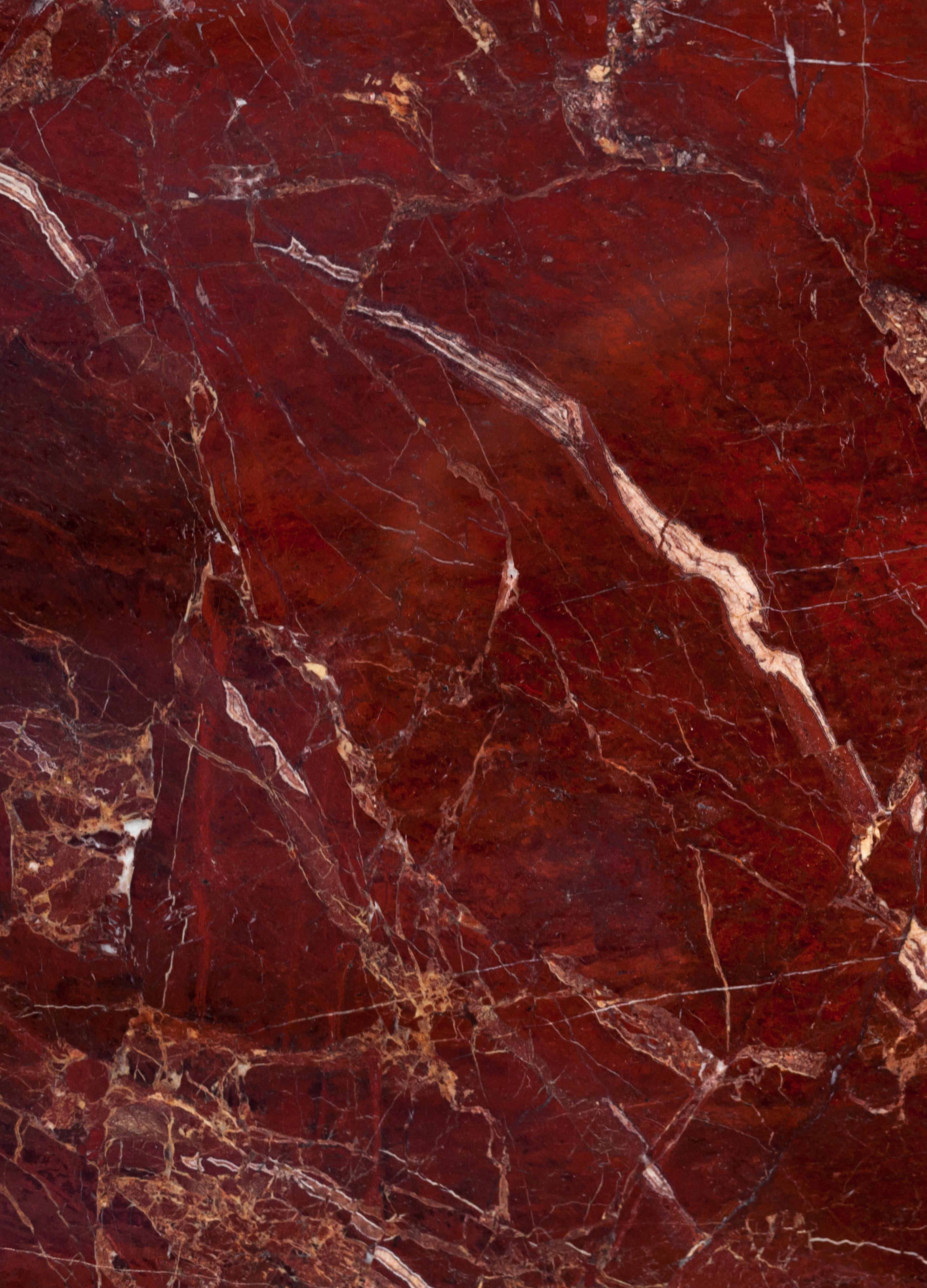
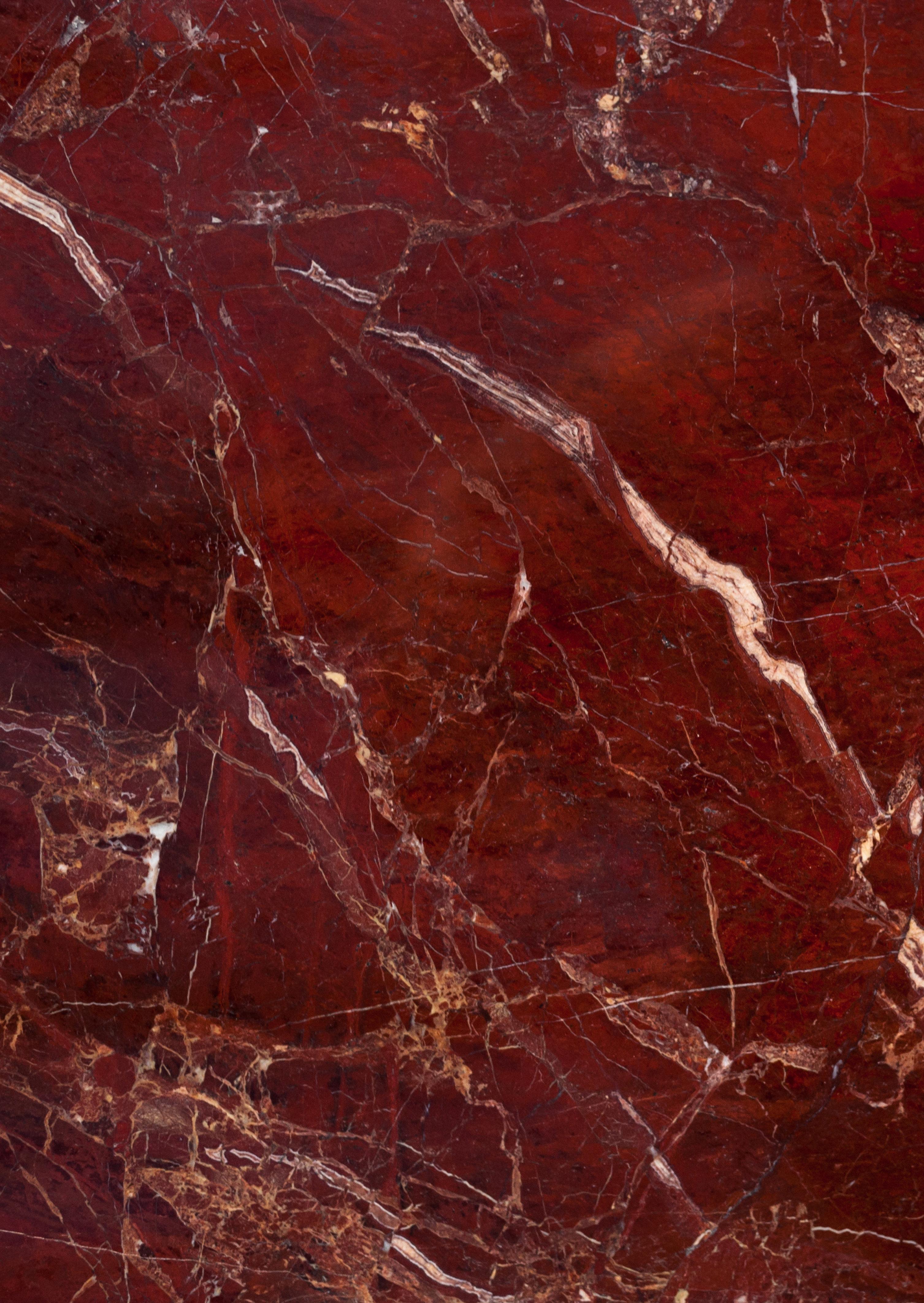
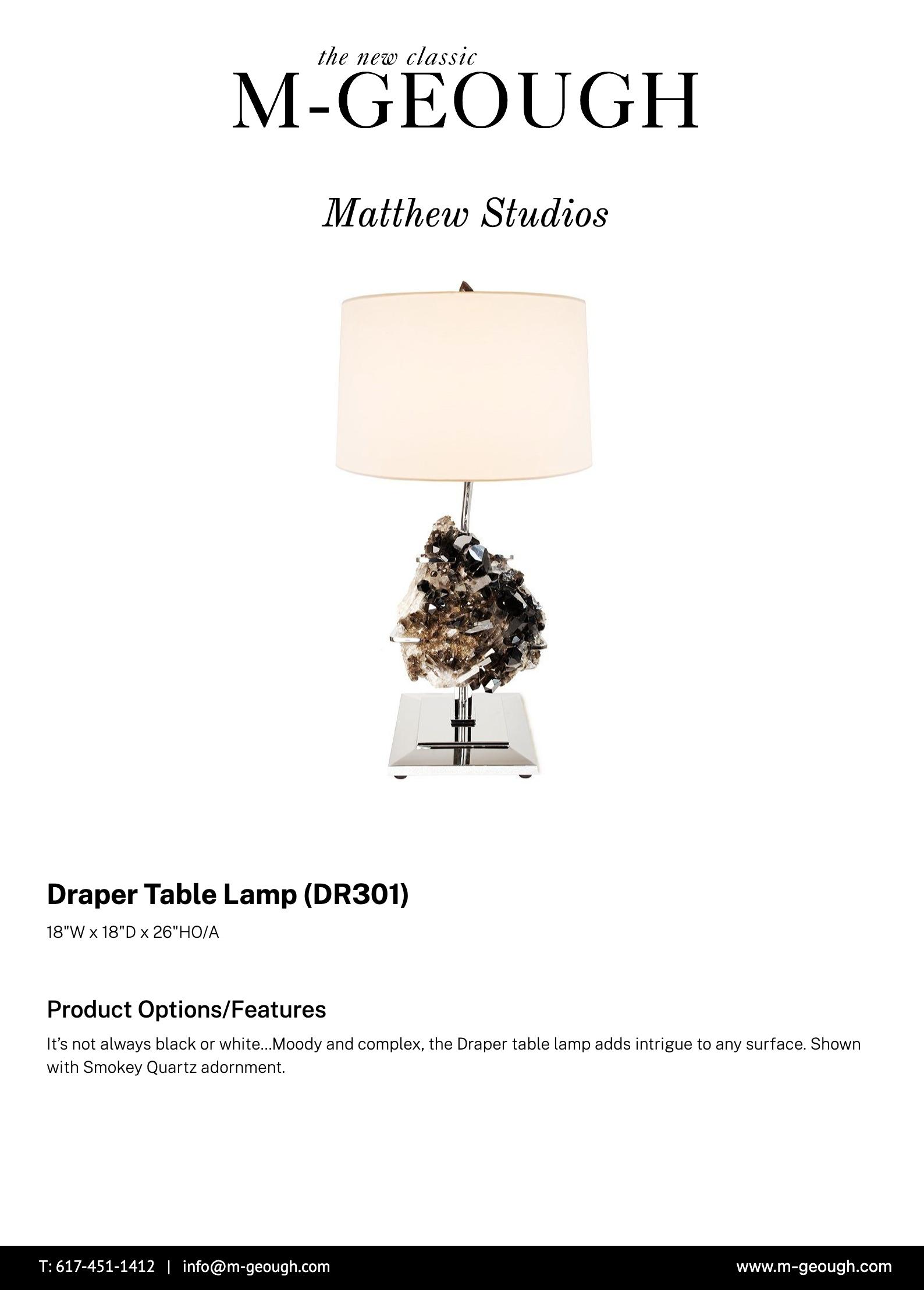


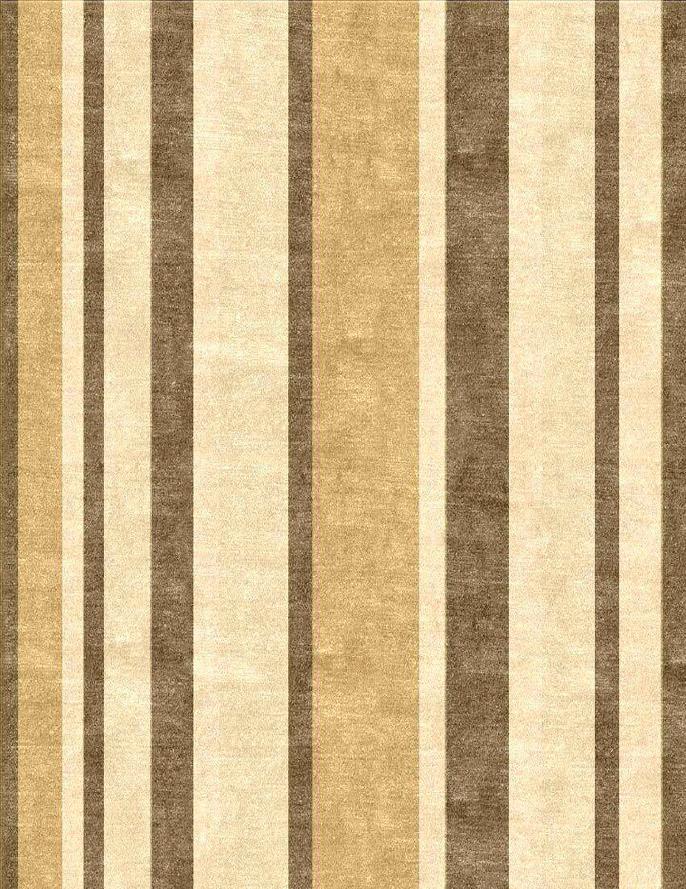
Clockwise from bottom left: MCLAIN WIESAND - Gerrit End Table | A. RUDIN - Sofa 2771 | A. RUDIN - Walnut Dining Chairs 815 | BOYD - Eclipse Mirror Pendant | ERINN V. - Plaza Cabinet | MATTHEW STUDIOS - Draper Table Lamp | KEITH FRITZ FINE FURNITURE - Hexagon 2 Dining Table | MARVIC TEXTILES - Perses Lichen | MARVIC TEXTILES - Lalitha Bronze | ERIC HAYDEL - Second Line Gold Beige Area Rug | JULIAN CHICHESTER - X Chair 6137 | BOYD - San Miguel Chandelier | ERIC HAYDEL - Masquerade Camel Area Rug | MARVIC TEXTILES - Razia Bronze

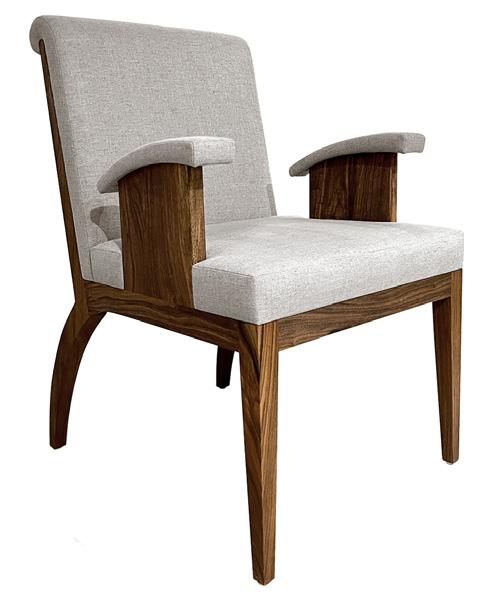

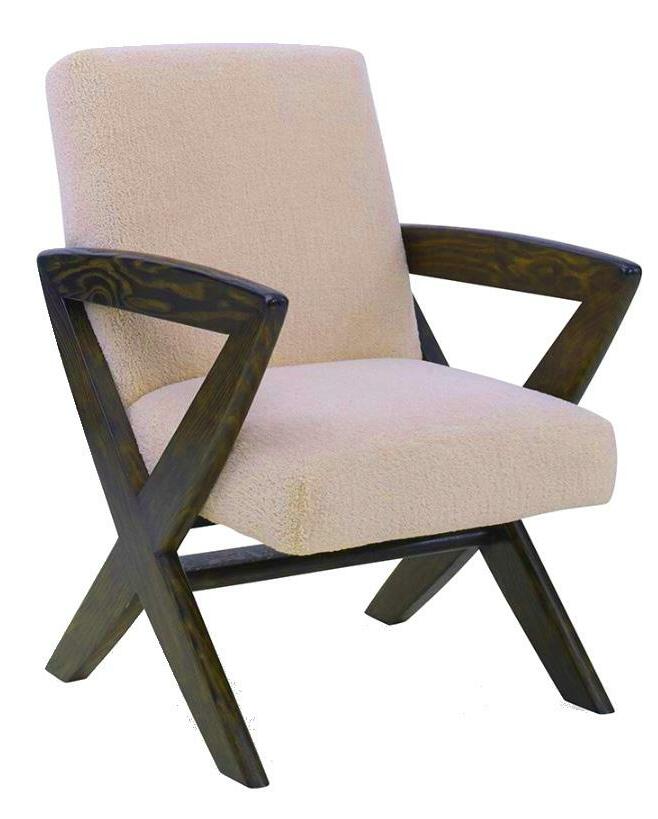



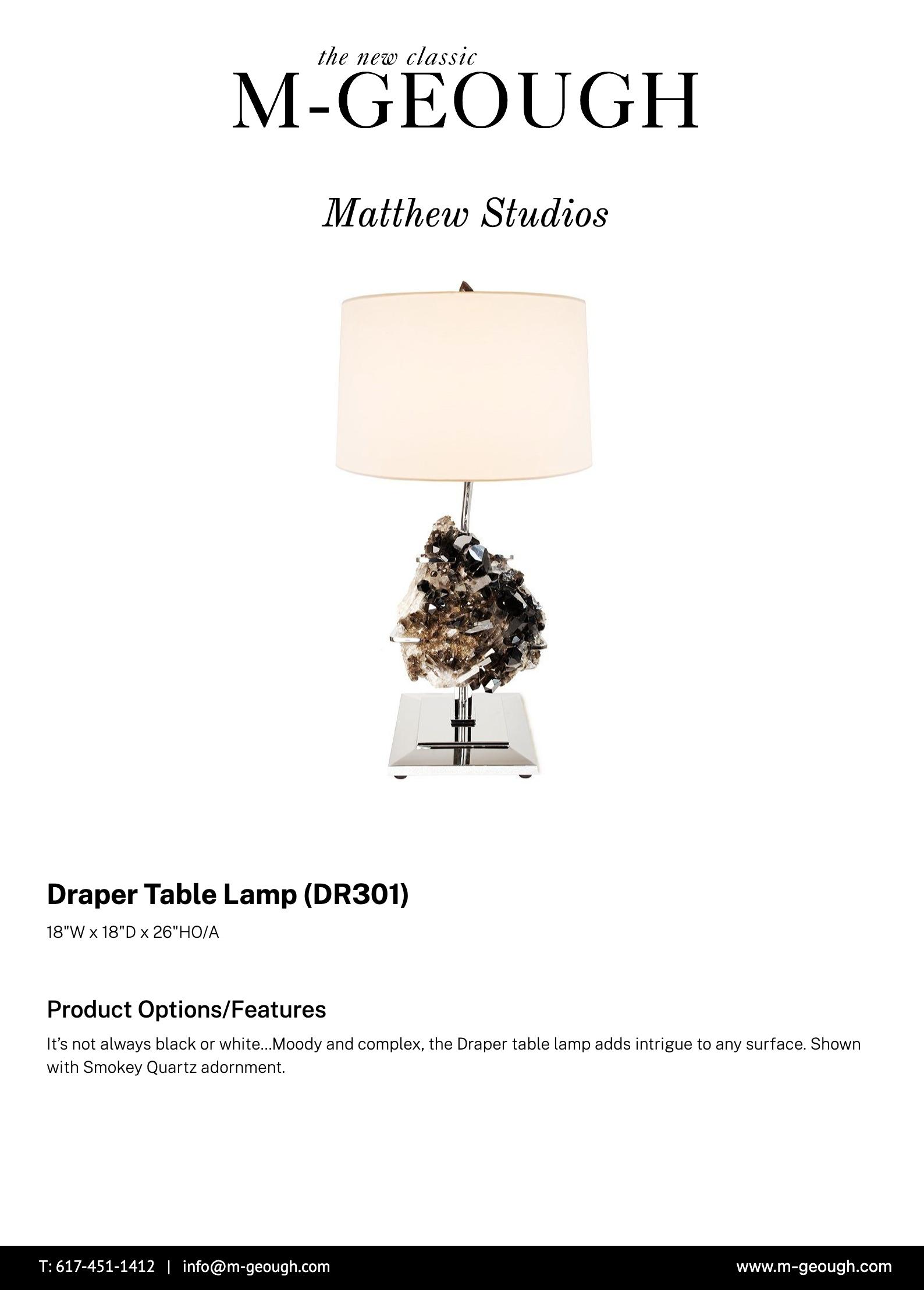
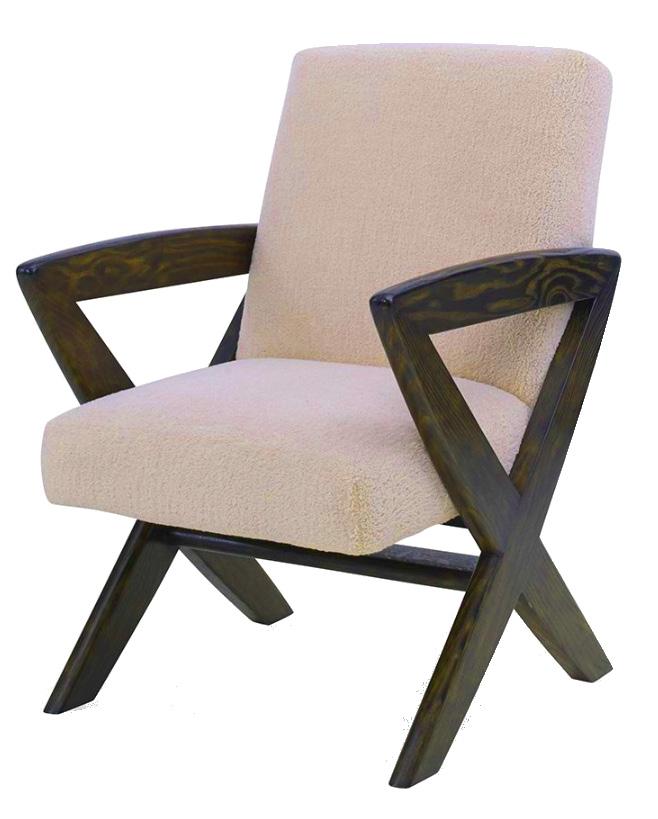
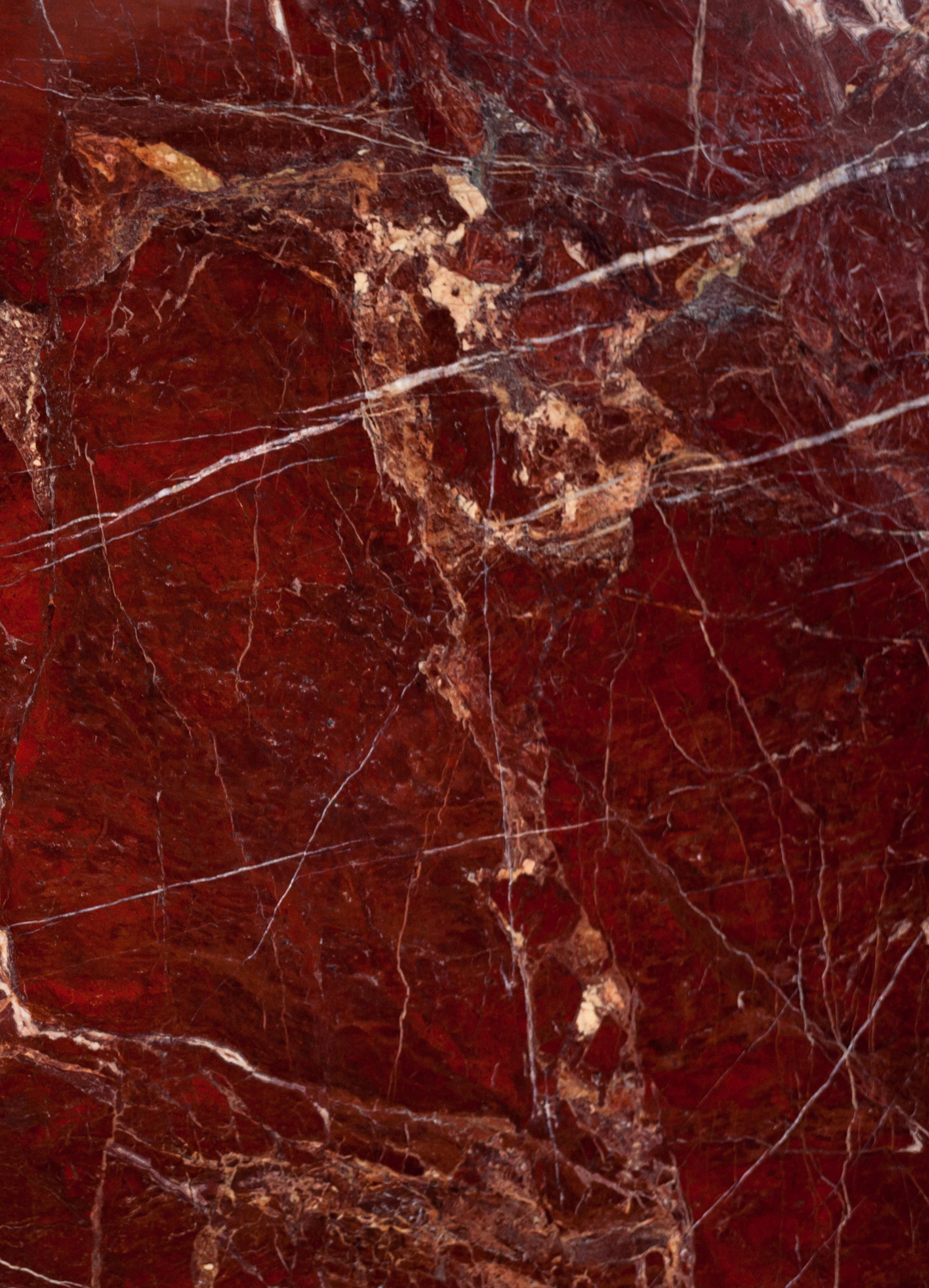
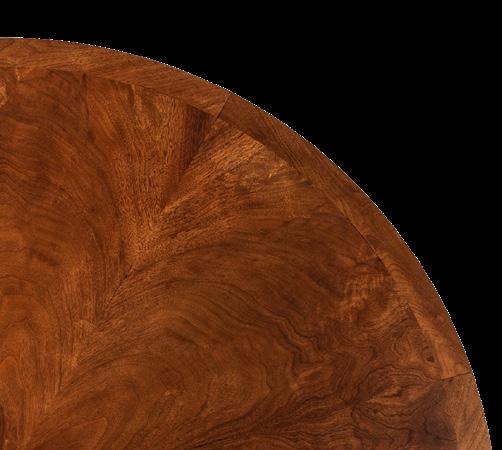

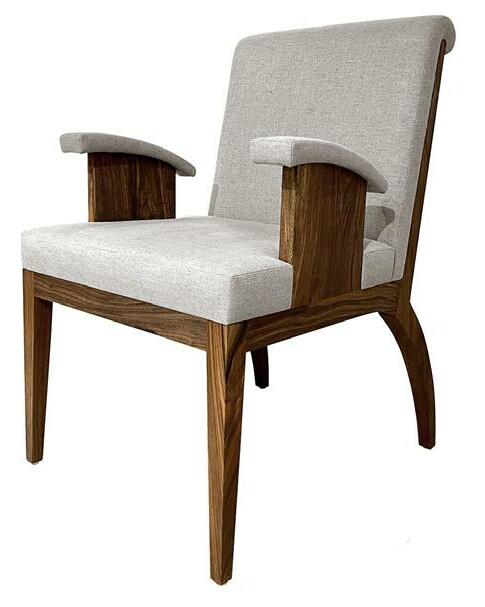

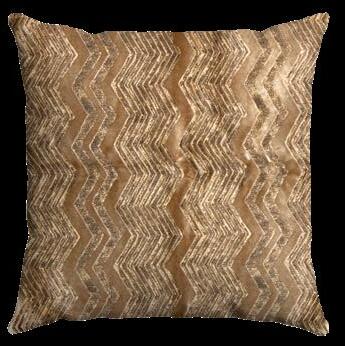