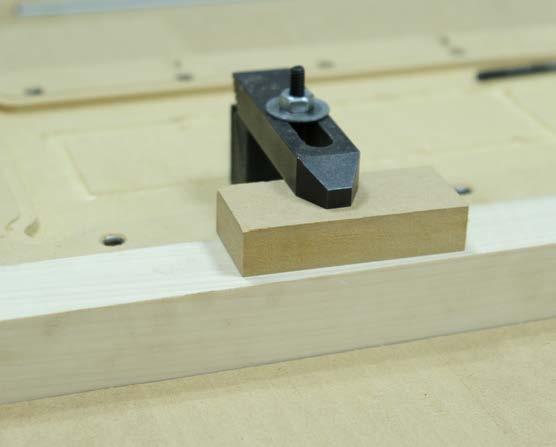
3 minute read
RESULTS + DISCUSSION
from Research by Design
Craft: Japanese Joinery
• Subtractive
Advertisement
• Time intensive
• Use of multiple tools
• Requires years of experience
• Human error
• Square tools
• Squared corners
• Expensive
• Tools intended for one material
• Full range of motion
Synergies:
Advanced Fabrication: CNC Routing
• Subtractive
• Efficient
• One tool
• Low barrier of entry
• Precise to 1/1000”
• Circular drill bit
• Rounded corners
• Cost effective
• Tool intended for multiple materials
• 3-axis
The two methods share little in common other than the obvious fact that they are both subtractive means of fabrication. Although this does not present ample opportunity, it does align the two methods within a common structure.
Bottlenecks and Opportunity:
Japanese joinery, though a beautiful and worth while craft, requires an amount of time and energy not suited for the 21st century. CNC routing can address the shortcomings of the craft through efficient and cost effective fabrication. Time spent on one joint through traditional means would yield dozens through advanced fabrication. CNC routing also requires the use of circular bits, limiting the range of motion at interior corners. Consequently, CNC joints are more effectively joined through curved or filleted edges, a geometry not easily replicable with hand tools. On the other hand, hand tools allow the carpenter to produce joints through subtraction at multiple planes. The capabilities of a 3-axis CNC machine does not.
Needs:
• Rhino 7
• CNC machine
• Wood shop
• 2x2 poplar
• 4x4 poplar, oak
• Resin blocks
Exploration: Setup
Shop Sabre 4896 Triple-Axis CNC
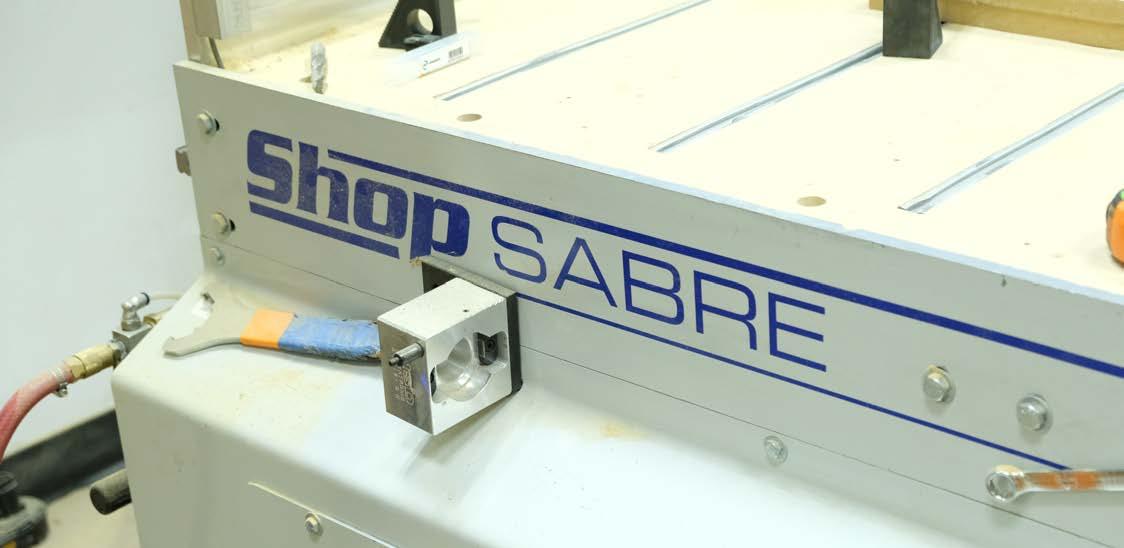
Precedent 1: “Tsugite”, The University of Tokyo
Tsugite is an interactive system used to aid in the design and fabricattion of wood joints for framed structures developed by Maria Larsson, Hironori Yoshida, Nobuyuki Umetani, and Takeo Igarashi at the University of Tokyo. The user interface generates custom joints that are output as 3d models and CNC mill paths for digital fabrication. The interface consists of a 3d grid of voxels that allow “geometrical analysis and combinatorial search”.1

Joints are able to be edited through a number built in parameters all while being provided real-time graphical feedback based on performance metrics like slidability, fabricability, and durability Once a joint design is finalized, it can be fabricated with a 3-axis CNC machine by
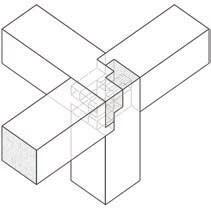
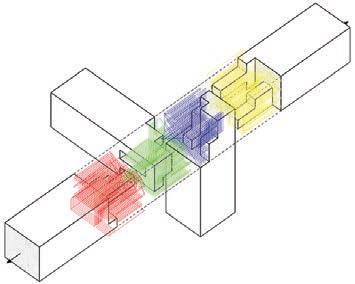
Precedent 2: “Desigining Timber Connections for CLT Panels”, Gabriella Joyce

In her paper, Joyce focuses on the intersection of sus tainability and modern fabrication techniques. cally, she develops a novel connection system for CLT panels through digital fabrication. The connections used are inspired by tradional Japanese joinery but have been “adapted to be used for the panel construction of CLT structures”.1 Fittingly, the system uses CLT offcuts as a connection material in an effort to reduce design is evaluated at multiple scales to ensure scalabil ity and practicalaity in the real world. The research found that simplicity was key to a successful system as it al lows for quicker and cheaper fabrication and installation.
1 Finding the Key: Designing Timber Connections for CLT Panels. 2019. Accessed October 17, 2022. https://search.ebscohost.com/login.aspx?direct=true&Auth
Type=ip,shib&db=edsoai&AN=edsoai.on1155918750&site=eds-live&scope=site
4.2.2 star
Wedged star prototype (Joyce 2019)
This key follows designs and repeated pattern of this design work. As shown an exact fit is strength in the acknowledge tolerances. where the designs not occur when Though this key as a joint, fabrication Despite being the arrangement that there a lot cut the key. The to cut and the is, however, a
Precedent 3: “Advancing Craft: A Translation to Modern Tectonics”, Jasmine Tran
1In her thesis, Tran explores the intersection of traditional Japanese joinery and advance fabrication methods. How the two can be transposed to create a modern usecase is at the central focus of the thesis. Tran proposes using CNC machining to produce kits that consumers could use to make modest improvements to their homes, build basic furniture, and make simple repairs.
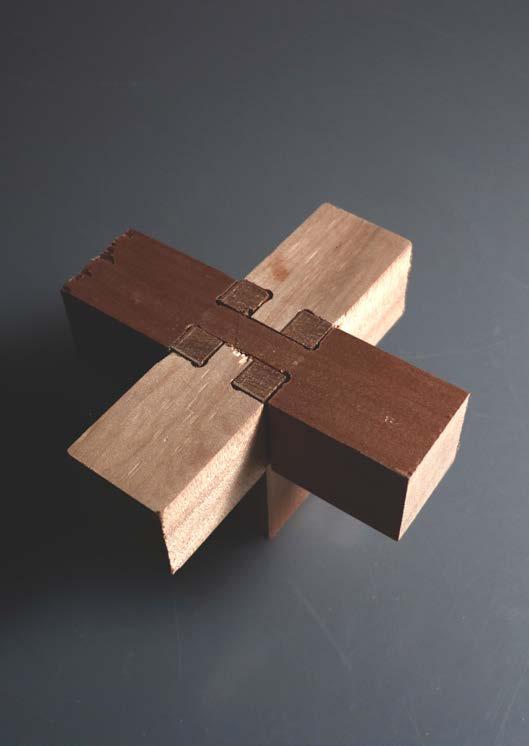
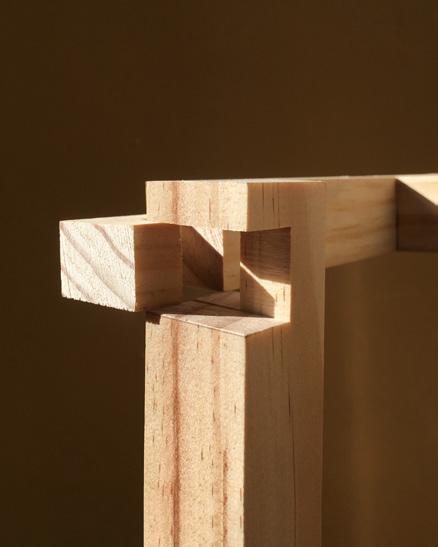
1 Advancing Craft: A translation to modern tectonics. 2020. Accessed October 17, 2022. https://search.ebscohost.com/login.aspx?direct=true&AuthType=ip,shib&db=edsoai&AN=edsoai.on1224565172&site=eds-live&scope=site
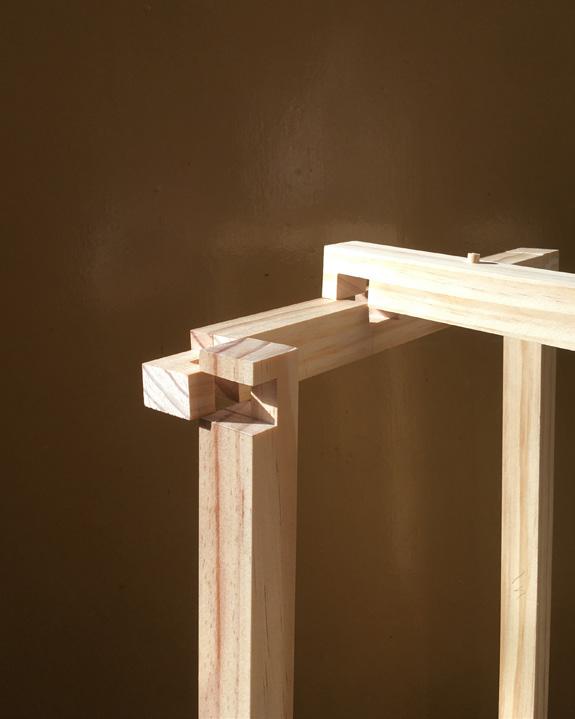

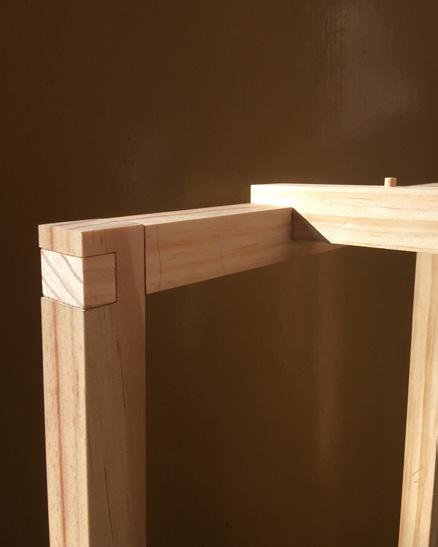
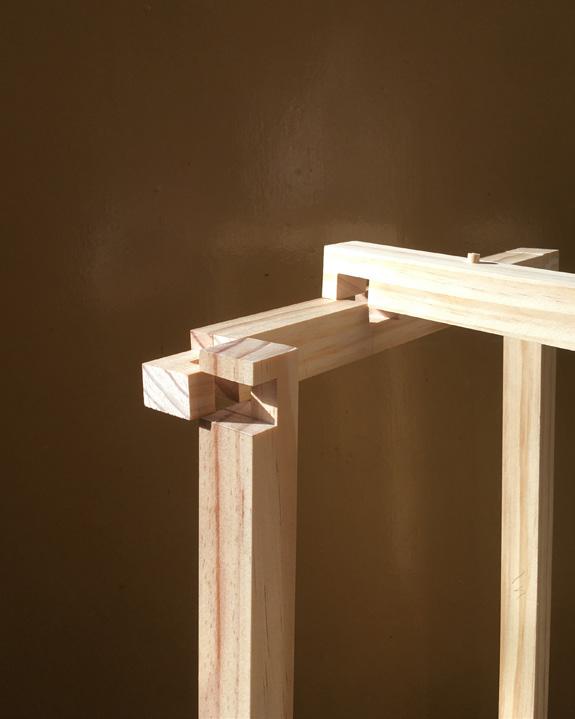
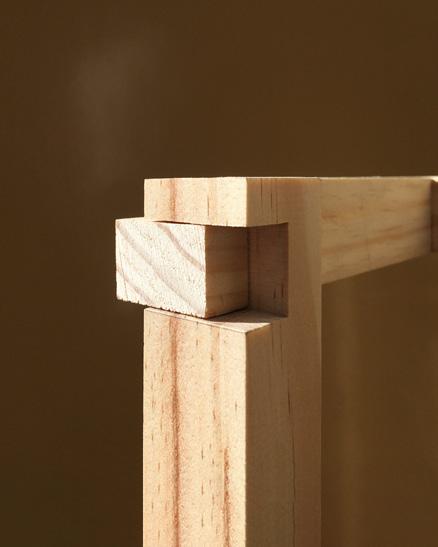
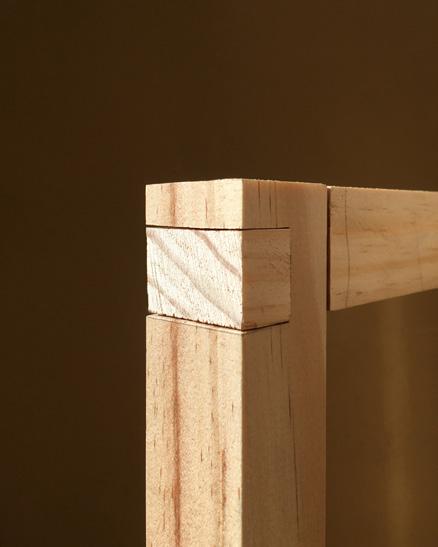
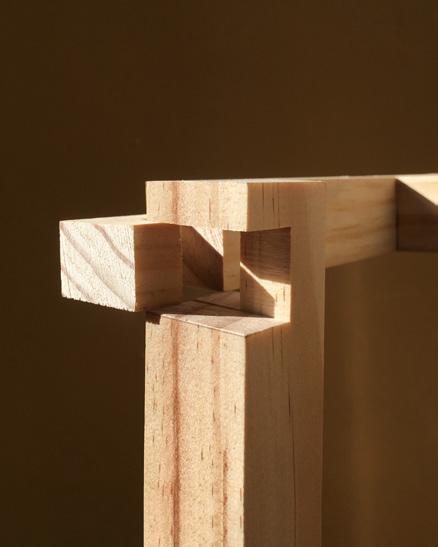
Exploration: Replication
The half lapped gooseneck joint is also used to extend mudsills and roof joists. As is with many Japanese joints, the dimensions of the various cuts are based on shared proportions. Due to the size of my material, it was necessary to widen the “neck” of the joint to maintain structural integrity during the routing of the wood.
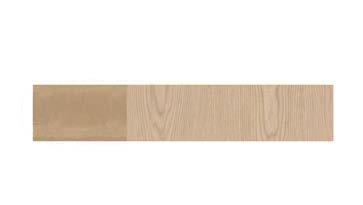
half lapped gooseneck joint
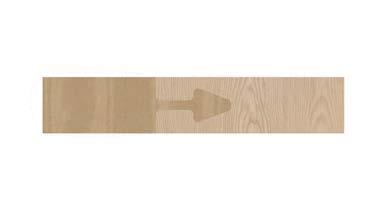
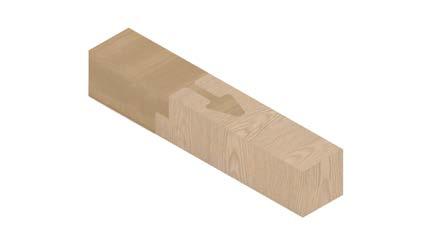
Top Scale: 1/4”=1’-0”
Exploded Isometric Scale: 1/2”=1’-0”
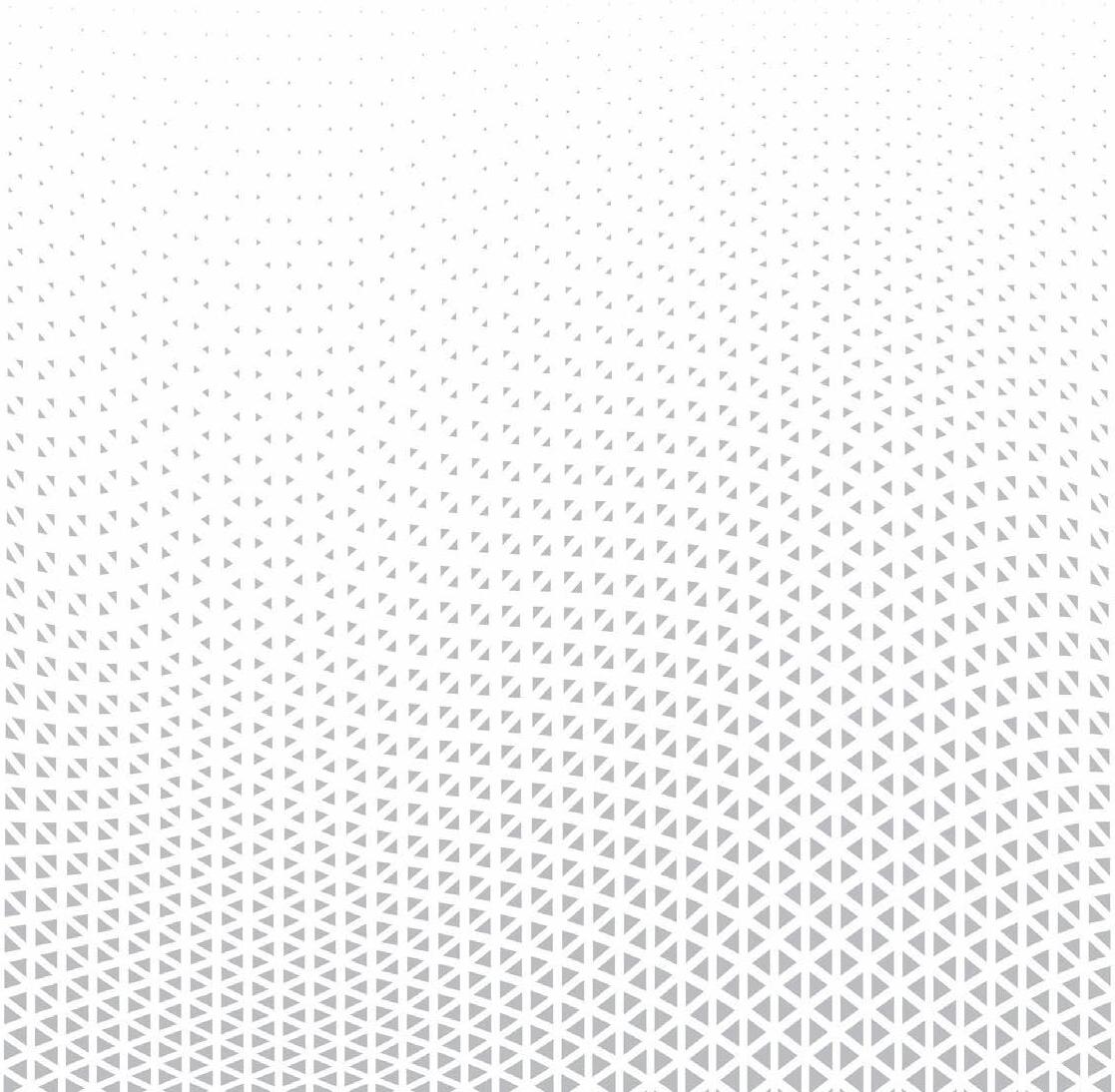
Isometric Scale: 1/4”=1’-0”
Bottom Scale: 1/4”=1’-0” required a forced mill due to its’ size

The CNC machine cannot cut 90 degree angels at interior corners, so all corners are radiused. The curves must be modeled to ensure precision.
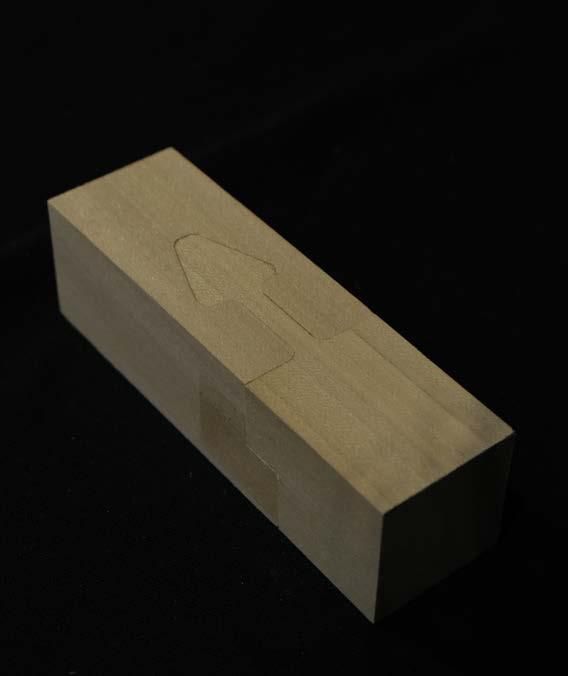
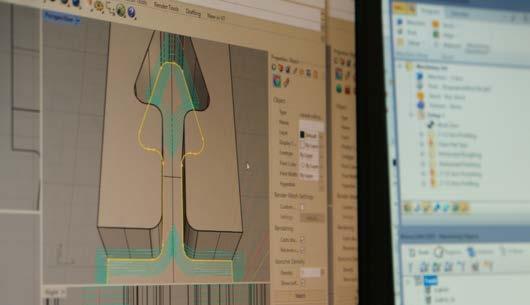
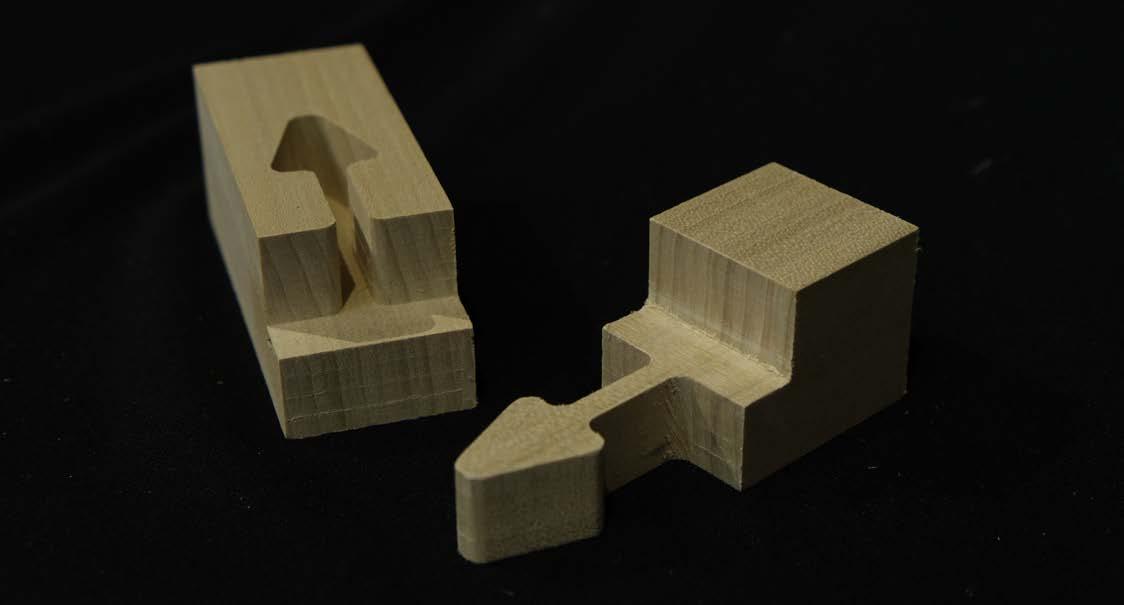
Exploration: Replication
The half lapped dovetail joint is commonly used for mudsills and roof joists as an extending joint. A lap or hip is made at the midpoint of the wood member to join the male and female pieces.
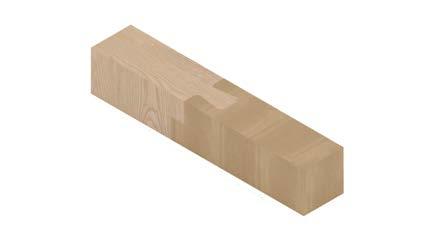