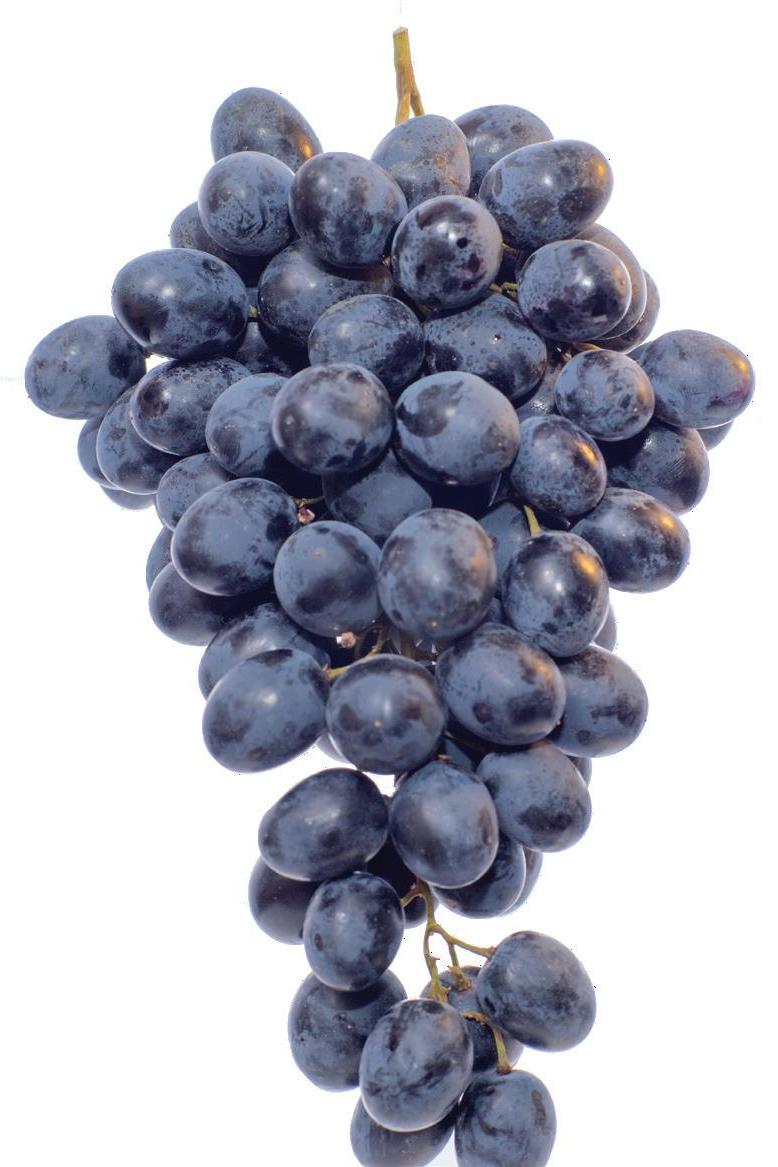
5 minute read
Nature-Forward Fashion
ALT-fab rics Grow in appeal
by Sofia naranjo
There is always something new popping up in sustainable fashion. Known fast fashion brands like Zara, Artiza and H&M have claimed to incorporate better practices. Brands like Stella McCartney, Rag & Bone, Coclico, Eileen Fisher, and Mara Hoffman have invested in meaningful changes to production and supply chain methods.
Whether it’s the fabrics they use, their production methods, their level of transparency, or their emphasis on safe, fair labor for workers, fashion brands are emphasizing sustainability now more than ever. We’ve heard about brands using organic cotton, recycled nylon, recycled polyester, Lyocell/Tencel, and other sustainable fabrics. Can it get more eco-conscious than that?
Apparently so. Here are a few funky, attention-grabbing textiles that are being used by small apparel and accessories brands. To make their grape leather shoes, sustainable streetwear brand Pangaia repurposes the global wine industry’s 6.5 billion liters of waste. Production of grape leather shoes uses minimum amounts of water and vegetable tanning (a method using natural tannins which alter the protein, making it into leather). Grape skin is used for production, and the seeds and stalks are dispensed. The part-recycled rubber soles are made from industrial waste—samples, prototypes, burrs, and products that do not meet high-quality standards. The shoes, responsibly produced in Portugal, also include natural cotton laces with 100% recycled plastic tips. One compelling aspect of the process is that regenerating wine-industry-waste into textiles establishes a cycle between what we eat and wear. Using Pineapple leaves as fabric is nothing new and has history in Brazil, Hawaii, and Indonesia. However, it’s generally agreed that the practice originated in the Philippines.
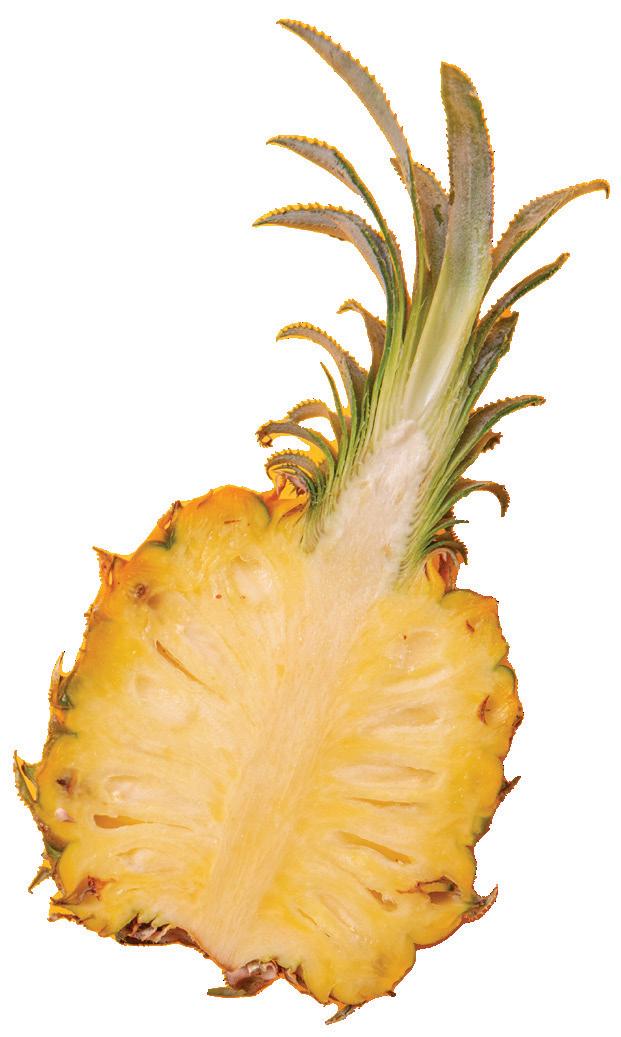
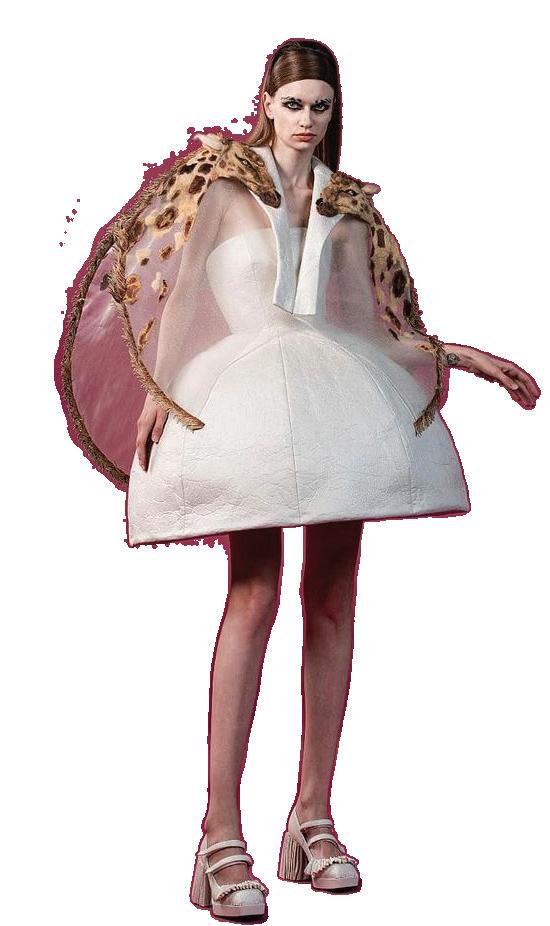
This fiber has not been widely used by American brands before because it takes a profound investment to produce, as cheap, harmful fabrics are easier to manufacture.
Pineapple fiber manufacturing is a slow and beautiful process and should be appreciated for the number of steps that it carries. The fabric is made first by detaching the leaves from the trunk of the fruit, then separating the fibers by hand using a scraping tool, and then washing the cellulosic strands and hanging them to dry. They are then waxed to release any leftover entanglements and plant tissues, and lastly, the strands are knotted one by one to create a connected thread of yarn. According to The Sustainable Fashion Collective, “A kilo of leaves can provide up to 15-18 pieces of white, creamy lustrous fibre [...] This is a hand labourintensive slow process that can often involve 30 people in total.” Next, it is left to the artisans to weave up the fabric.
The company most known for producing pineapple fabric is Pinatex. Pinatex manufactures nonwoven textiles from waste pineapple leaves as an alternative to leather and other synthetic materials. Pinatex is also PETA-approved and registered by the Vegan Society. You can purchase Pinatex by the meter online. The company supports and works closely with rural farmers, as the pineapple fabric is sourced in the Philippines. As such, Pinatex develops a stream of income for the farmers who keep the tradition alive.
Currently, the only cactus-based leather brand available on the market is Desserto. As you might suspect, the cactus is durable, withstands extreme conditions, and grows where other plants cannot. The cactus species naturally restores soil, which prevents overharvesting. According to Desserto’s website, it takes three leaves of cactus to create one linear meter of Desserto. They only cut mature leaves to avoid damaging the plants, which means a harvest every six to eight months. They grow their plants in “the fertile and mineral-rich region of Zacatecas, Mexico.”
Founders Adrián López Velarde and Marte Cázarez point out, pragmatically, that climate change could lead to “prolonged droughts and desertification,” seriously affecting farmers and small producers of low income. They warn, “if people want to survive these harsh conditions, their crops must tolerate drought, high temperatures and poor soils.” Desserto currently manufactures handbags, footwear, apparel, interiors, and sportsgear with alternative leather. They use ecoconscious practices to develop their fabric, which is “distinguished by its great softness [..] while offering a great performance for a wide variety of applications and complying with the most rigorous quality and environmental standards.” According to Vogue, Mylo is “the future of fashion.” This brand looks like the most eco-conscious company in the fashion industry at the moment. Mylo produces leather made from mycelium, a member of the fungi kingdom that grows underground and essentially holds the planet together. Mycelium is soft and bouncy and of course non-harmful. Production is based in California by engineers and scientists at Bolt Threads. Mycelium has been growing beneath us for billions of years, providing nutrients for plants and trees. Mycelium is renewable, and also crucial, because it holds like a branch supporting the earth’s surface.
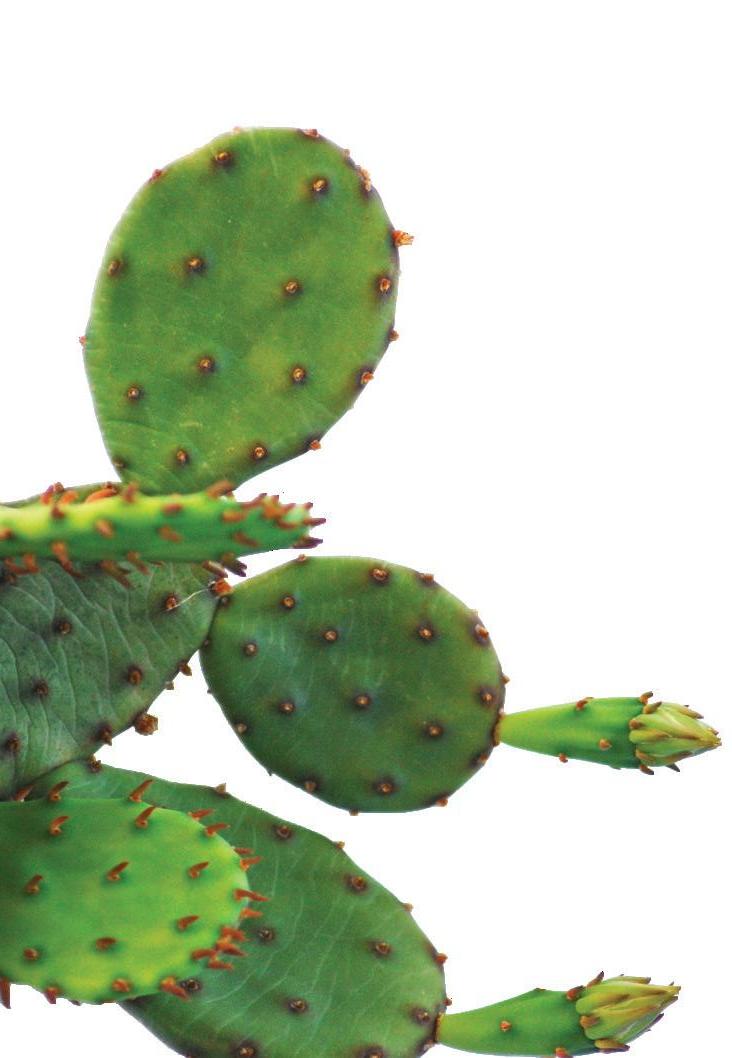
Mycelium is an alternative to leather made by simulating what usually happens under the forest floor in a controlled indoor environment. It is kept at a strict temperature and fed sawdust and other organic substances. The harvest begins after the mycelium grows a foamy layer that is used to manufacture most mycelium products. A sheet of this foam is dyed and used to make leather-like goods. At-home kits are available to anyone who wants to try making it themselves, but Mylo is not available for sale at the moment because it is still in the testing stages. Nevertheless, impending collaborations with Stella McCartney, Adidas, and Lululemon bode well for 2022. Orange Fiber identifies itself as “the world’s first brand to produce sustainable fabrics from citrus juice byproducts.” The brand Salvatore Ferragamo, one of the biggest faces of Italian fashion, created a capsule collection in 2017 using the fiber. According to Orange Fiber’s website, the company partnered with Lenzing Group (a global producer of wood-based fibers) to create the first TENCEL Lyocell fiber made of orange and wood pulp.
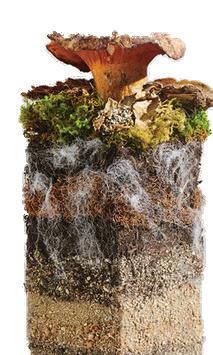
Why citrus? According to Orange Fiber’s research, about 40-60% of citrus fruit ends up being discarded, and 110-120 million tons of citrus waste are produced worldwide every year.
There is a six-step process for converting the juicy fruit into the fabric, which includes orange groves, citrus juice leftovers, cellulose extraction, fiber making, fiber spun into yarn, and then yarn woven into a fabric. The fashion industry has been very intrigued by Orange Fiber over the past few years, as the company has collaborated with H&M, Salvatore Ferragamo, and E.Marinella, and has been showcased in exhibitions in V&A Museum, Fashion For Good Exhibit, Deutsches Hygiene Museum, and the Museo Salvatore Ferragamo.
