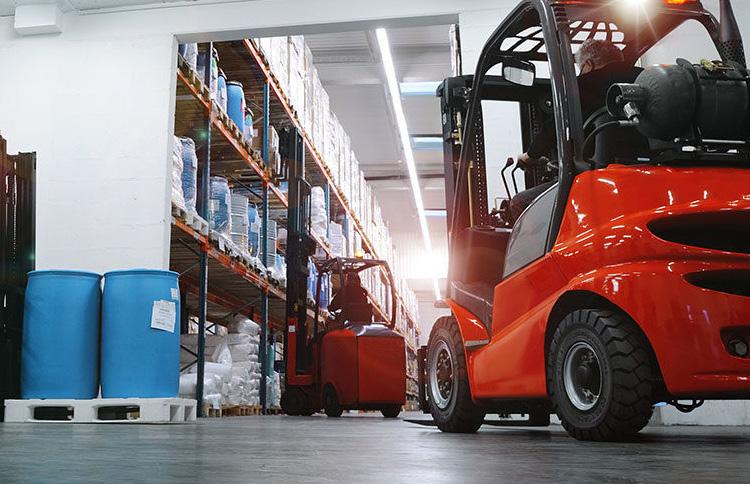
6 minute read
Overview of the hydrogen strategy
Manitou Group, a world reference in the handling, aerial work platform and earth moving sectors, presents its roadmap for research and development on hydrogen-powered machines. Its opportunity to present the first innovative prototype telehandler running on green hydrogen.
Energy transition acceleration
Advertisement
With a target of reducing greenhouse gas emissions by 34% per hour of use of its machines in 2030, Manitou Group has set off on an ambitious course, in line with the commitments of its low-carbon trajectory communicated in January 2022 and validated by the SBTi in July.
Following on from the recent electrification of its all-terrain platform and telehandler ranges, the Group is also looking to hydrogen as a medium-term alternative for its users.
Manitou Group wants to see its electric and hydrogen ranges side by side depending on each user’s applications, with a target of 43% low-emissions products marketed in 2030.
A dedicated hydrogen development plan
Manitou Group has presented its new facilities for making its hydrogen development plan a success to journalists and elected representatives. By kitting its test center out with a green hydrogen station, the Group now has the means for testing its brand new prototype telehandler.
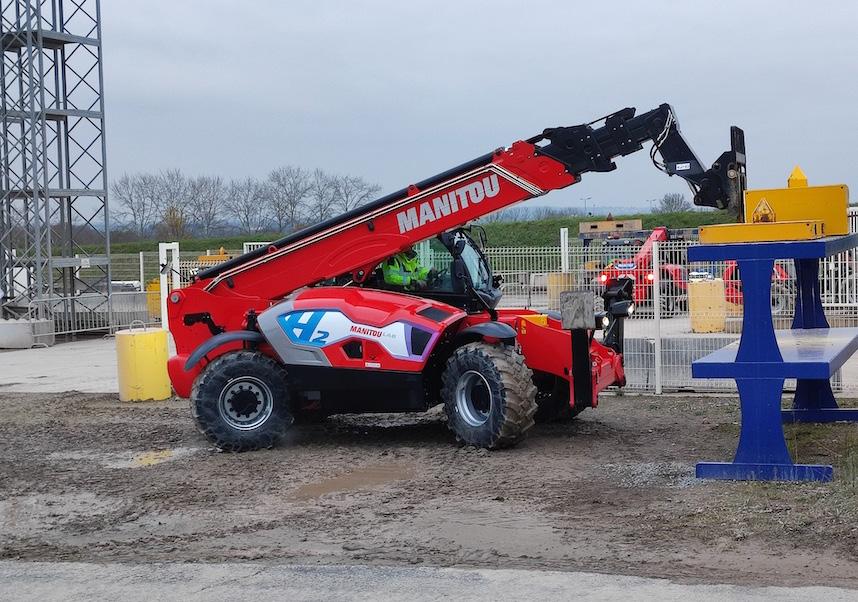
The first step of this plan involves guaranteeing range and reliability in real-life conditions, while testing the durability of components.
The Group based this first prototype on an existing model from its range of construction machines, capable of lifting loads up to 14 m.
This machine will be tested and sent out to construction sites by the end of 2023 with a view to collecting valuable feedback from users to improve on this prototype. Two types of hydrogen technology are currently being evaluated by the market, namely the combustion engine and the fuel cell.
The Group’s first prototype is built around a fuel cell, but the Group will choose the hydrogen solutions that best meet the needs of its customers. Michel Denis, Managing Director of the Group, explains: “We are studying all the hydrogenrelated technologies based on what users need. This prototype is only the first step. A second rotating telehandler prototype will be developed in the coming months. There are many benefits of green hydrogen with production possible using wind power that has no greenhouse gas emissions at all. This fits in perfectly with our lowcarbon trajectory”.
With this first prototype, the Group is showcasing its ability to innovate in order to measure the autonomy of this new energy while offering its customers the hydrogen solution that best meets their needs, but without compromising on performance. Almost 50 dedicated to this approach, which was launched in 2021. To come up with an innovative solution that can be fully industrialized, the Group hopes to rely on the support of the public authorities to develop an emerging ecosystem. Julien Waechter, VP R&D Manitou Group, explains: “The green hydrogen sector is gradually becoming more established with the entry onto this market of a number of players. All of the aid mechanisms proposed by the different governments will encourage the transition to hydrogen, and will speed up the development of the distribution network and ultimately the reduction in the usage costs of our machines using this energy”.
With these new facilities, Manitou Group hopes to offer its customers new innovative prospects, with a 100% hydrogen-powered telehandler available on the market by 2026.
Innovation in our DNA
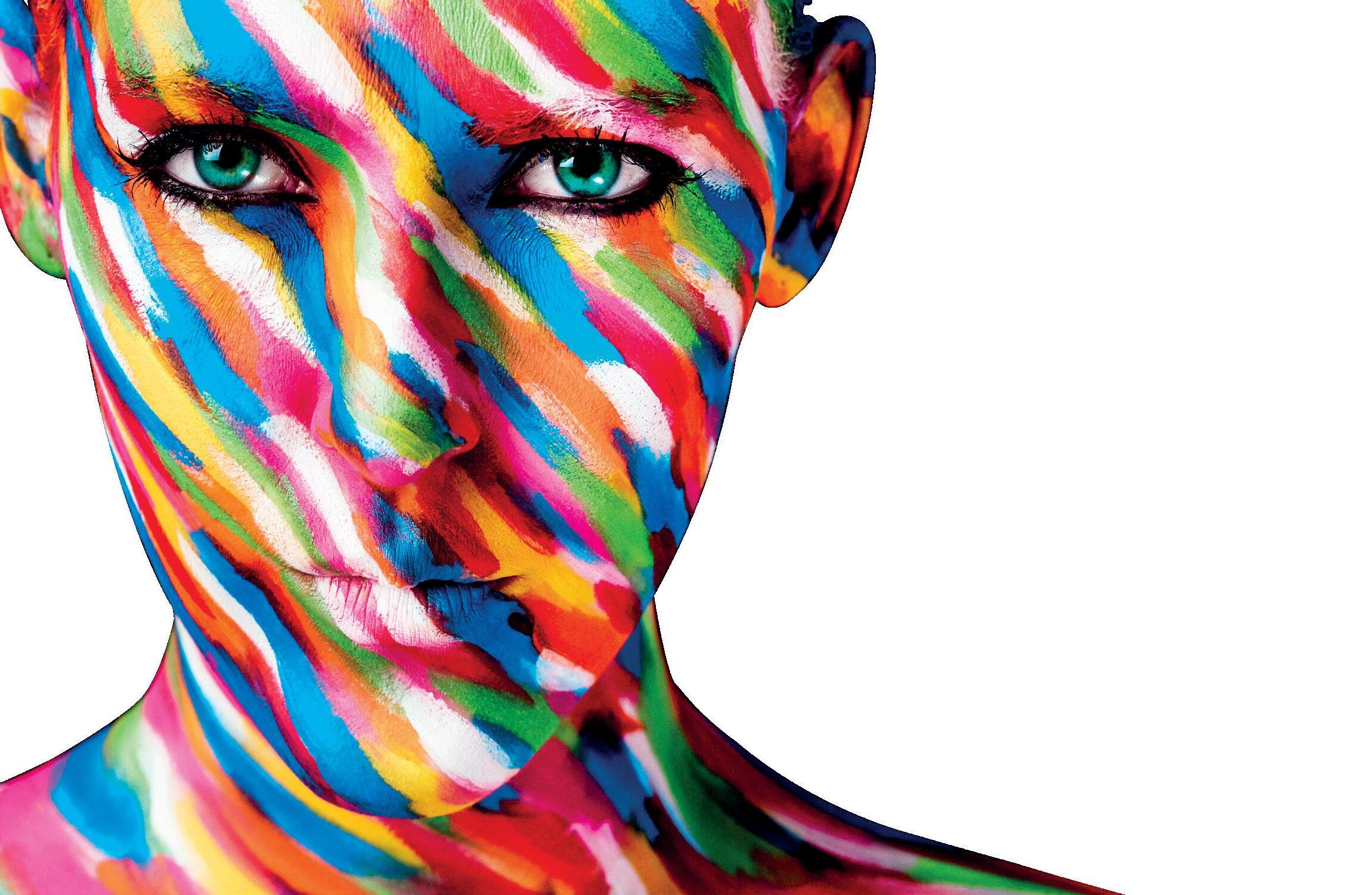
With over 350 engineers on its workforce, Manitou Group is constantly innovating by offering its users highadded-value solutions. To
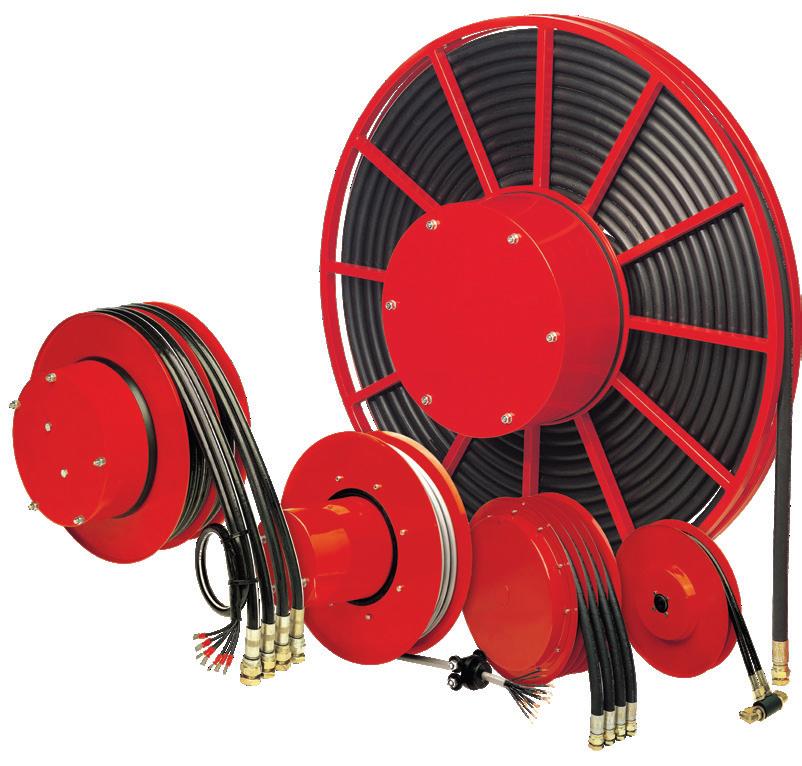
€60 million a year in all of its 10 R&D centers around the world. The modernization of its production units is also essential to ensure this ability to innovate.
This is demonstrated by the recent €150 million investment plan announced for the production sites in the US and France. The most recent aerial work platform factory opened in 2022 clearly illustrates this willingness.
Whether it concerns the choice of components, user comfort, or the attachment on the machine, innovation is everywhere.
An autonomous order-picking robot, electric all-terrain platforms, and 100% electric telehandlers are all examples of innovation.
To support this development, the Group incorporates engaging CSR criteria from the design stage to develop machines that are increasingly durable and responsible.
Manitou Group, +27 (0) 10 601 3000, info.msa@manitou-group.com
How to choose the correct clamp for your lifting application
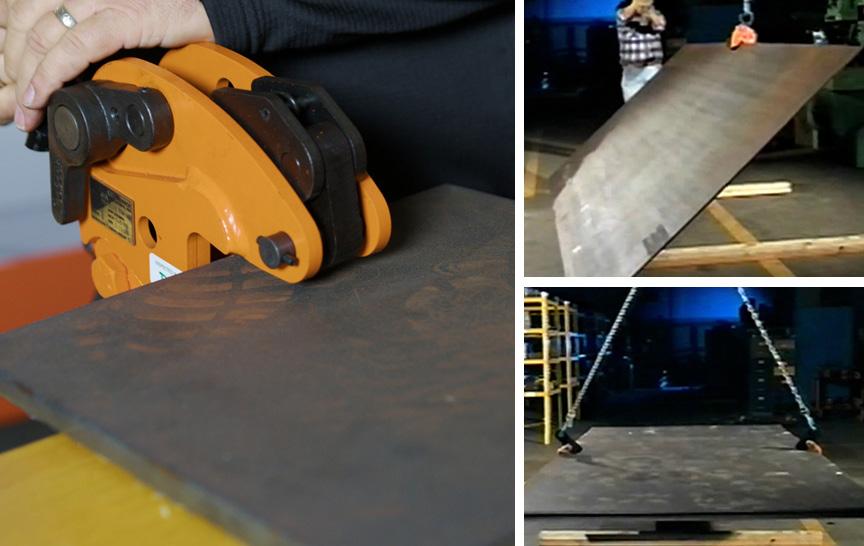
Do you need a new below-the-hook lifting device and think a clamp could be the right fit? When it comes to lifting clamps, there are plenty of options. However, when choosing a clamp, how do you know you’re picking the correct one for your lifting applications?
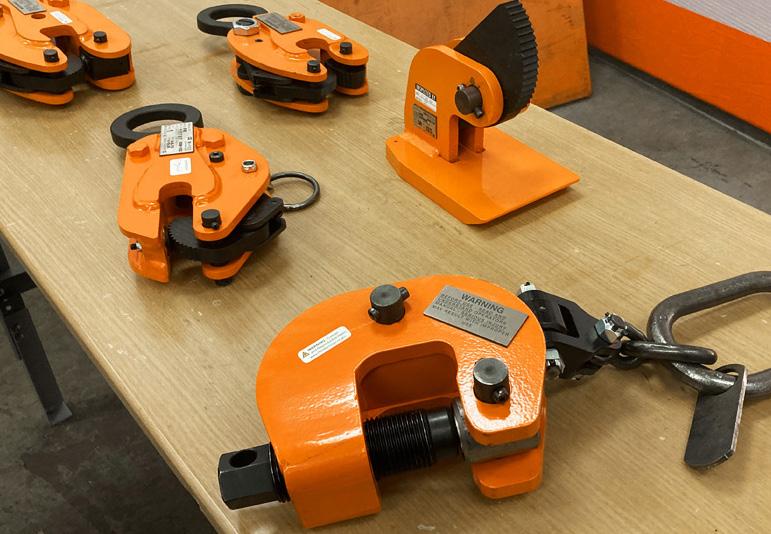
To answer this question properly, we reached out to engineering manager Dale Kelly of Caldwell / J.C. Renfroe Lifting Solutions in Rockford, Illinois to help outline what you need to know before choosing a clamp.
Factors you need to consider when choosing a clamp for your overhead lifts, including:
• Hardness of the metal
• How you plan on lifting with a clamp
• What kind of jaw opening is needed for your application
• The environment will the clamp be used
• Confirmation upon receipt of the clamp
Lifting is “MAJEC”
Really, there is no “magic” involved in overhead lifting and material handling, at least there shouldn’t be. It is part art, part science in which all details must be considered beforehand to help ensure safe lifts. However, the acronym “MAJEC” will help you choose the correct clamp needed to safely make your overhead lifts.
The acronym, “MAJEC” stands for:
• Material Hardness
• Attitude of the lift
• Jaw opening
• Environment
• Confirmation through reading the manual, inspections and size (witness marks)
By going over the topics in the acronym, you can learn most of everything you need to know about how to choose the appropriate clamp for your application. Knowing this acronym will help develop a greater understanding of your:
• Materials
• Lifts
• Clamps
• Surroundings
• Processes
Breaking Down the Components of “MAJEC” Metal Hardness
If the hardness of the metal is above 300 Brinell, which is measured on a machine or the certification that comes with the metal, the teeth of a clamp can’t penetrate into the steel. That will prevent the clamp from being able to do its job.
Caldwell / J.C. Renfroe has special clamps designed for plates above 300 Brinell, and those clamps are part of the non-marring series.
They have a smooth jaw and a higher grip ratio that can grip the plate without slipping. Non-marring clamps have smooth jaws, and they will not leave marks on your plates. Therefore, it can be used on softer materials as well. This is especially true for plates that are sensitive to teeth marks where you need a polished surface. If the plate metal is below 300 Brinell, clamps with teeth on them can be used for lifting. These teeth must remain sharp, and the properly sized clamp will grip the plate, penetrate the steel, and allow it to lift and do the job that needs to be done.
Attitude of the Lift
What “attitude” refers to is how you want to lift your plates. The following questions must be asked and answered to ensure you have the proper clamp for your lifts:
• Are you lifting plates vertically?
• Do you want to turn the plate during the lift?
• Do you need to flip the plates over during the lift?
• Is there another type of orientation that you must have to lift a plate?
If you want to lift a plate vertically, Caldwell / J.C. Renfroe’s FR clamp is a good choice. It’s a vertical-only lifting clamp meant to lift a plate on edge, straight up and down.
The next style of clamp is called the vertical plus 90. The Caldwell / J.C. Renfroe Model TL Clamp is rated to turn a plate from flat to 90° and back through the same angle. It has a locking lever on it that maintains constant pressure on the plate so the teeth can always penetrate during no-load conditions. Such conditions include when a plate is standing straight up and resting on the ground.
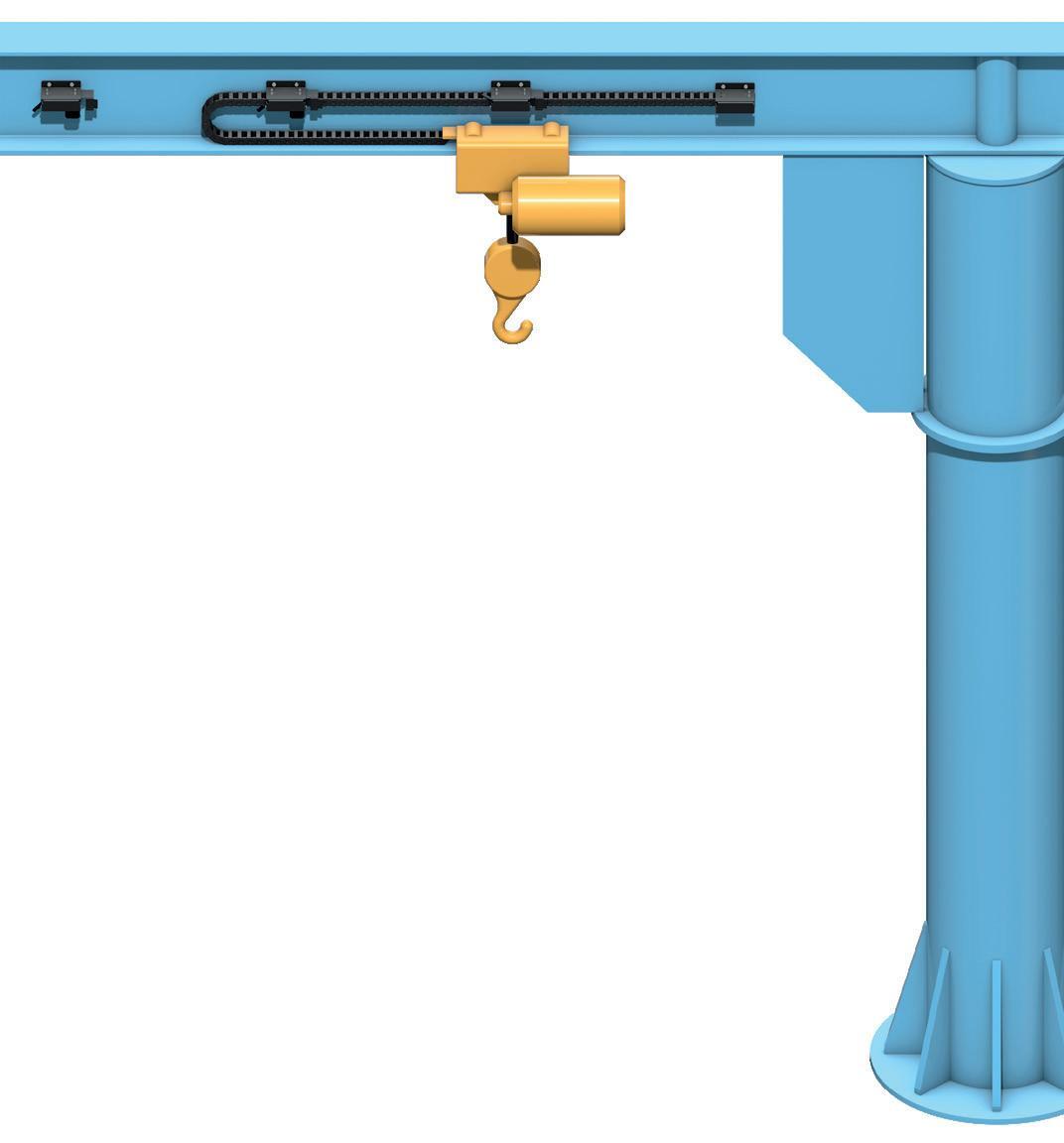
Also, Caldwell / J.C. Renfroe offers you clamps that can flip plates over completely. They have the following components that allow them to function properly:
• A pivoting jaw
• Lock
• Additional lock
Clamps for Special Lifting Conditions
The additional lock is a good safety feature, as when you’re flipping a plate completely over, if you happen to hit an obstruction, the clamp won’t unlock and disengage from the plate. The Caldwell / J.C. Renfroe JPA Model comes with a pivoting shackle that allows it to be used in pairs with a central lift point.
For plates that are lifted in a flat manner, meaning they are hoisted straight up and straight down, horizontal clamps should be used. You use these in pairs, and they are for lifting plates in a flat manner, straight up and straight down, and for transport through the shops. It does not turn, and there’s no side-loading allowed.
Caldwell / J.C. Renfroe has an SCPA model, and this clamp is rated to turn 180°. It has a pivoting shackle, so you can use it in pairs with a central hoist and a spreader beam when lifting a plate that’s standing vertically. As an added bonus, the robustness of this clamp is good for high vibration environments, and that’s where Caldwell / J.C. Renfroe clamps start to break down and become more specialized throughout the product line.
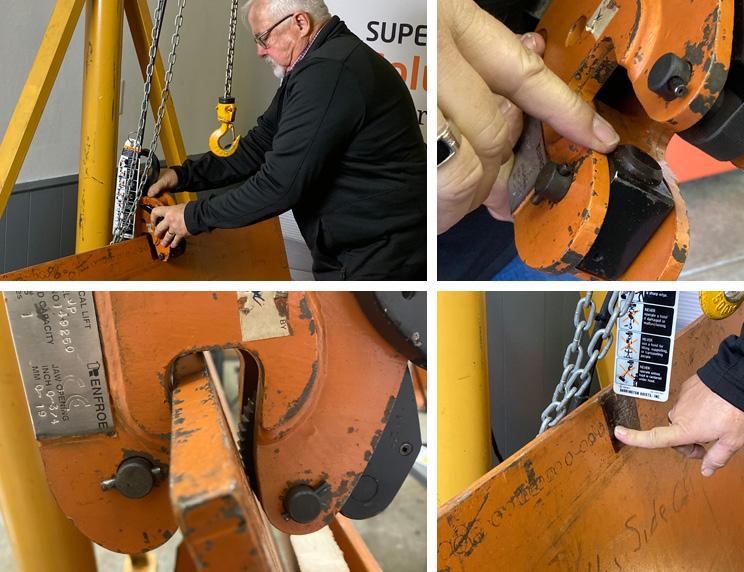