
3 minute read
KRUEGER’S LATEST INVESTMENT IN CUTTING EDGE TECHNOLOGY.
STEVEN TEOFILO DIRECTOR OF ENGINEERING & SUPPLY CHAIN
To future proof its operations and continue to develop itself as an industry 4.0 manufacturer, Krueger Transport Equipment has recently installed and commissioned an HG Farley Laser Lab Marvel 12kW Fiber Laser cutting machine. The requirement for a laser cutting machine came about as its existing plasma cutting machine reached the end of its journey on Krueger’s manufacturing road map, and it was time to look to the latest technology in the steel cutting industry.
Naturally, this search took the company to the technology of laser cutting, and Krueger’s requirements were to take traditional laser cutting to the next level in terms of size and power of the machine. Such requirements would give Krueger uncompromised flexibility to be able to throw everything it needs at the new laser cutting machine in order to make best in class semi-trailers. The laser cutting machine ordered had 12kW
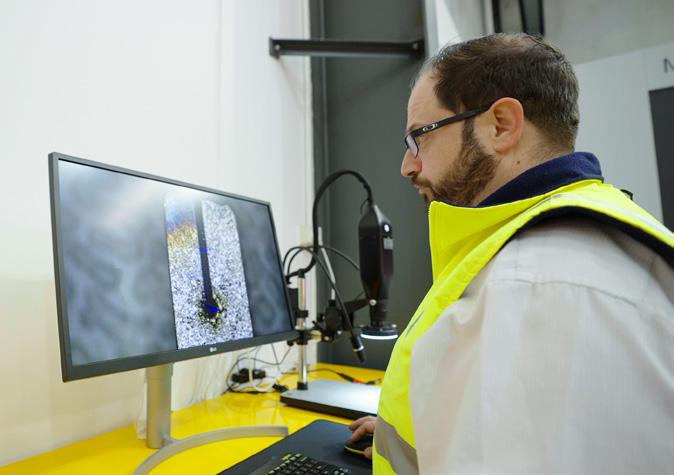
of power with a 2.55m x 10m bed. After finalising the specifications of the laser, the company moved to the installation phase of the project where Krueger partnered up with industry leading local suppliers to ensure that the new facility was built to a class leading level.
To compliment the new laser cutting machine’s size and power, it also has the flexibility of cutting with Nitrogen, Oxygen and Compressed Air. To supply the machine with these critical gases, Krueger partnered with Coregas to design a new compound to house the Nitrogen and Oxygen storage tanks. Krueger also worked very closely with Hitachi Global Air Power to install a pair of oil free scroll compressors, which would supply very clean compressed air, from almost silent compressors which are located inside the new laser cutting factory. (
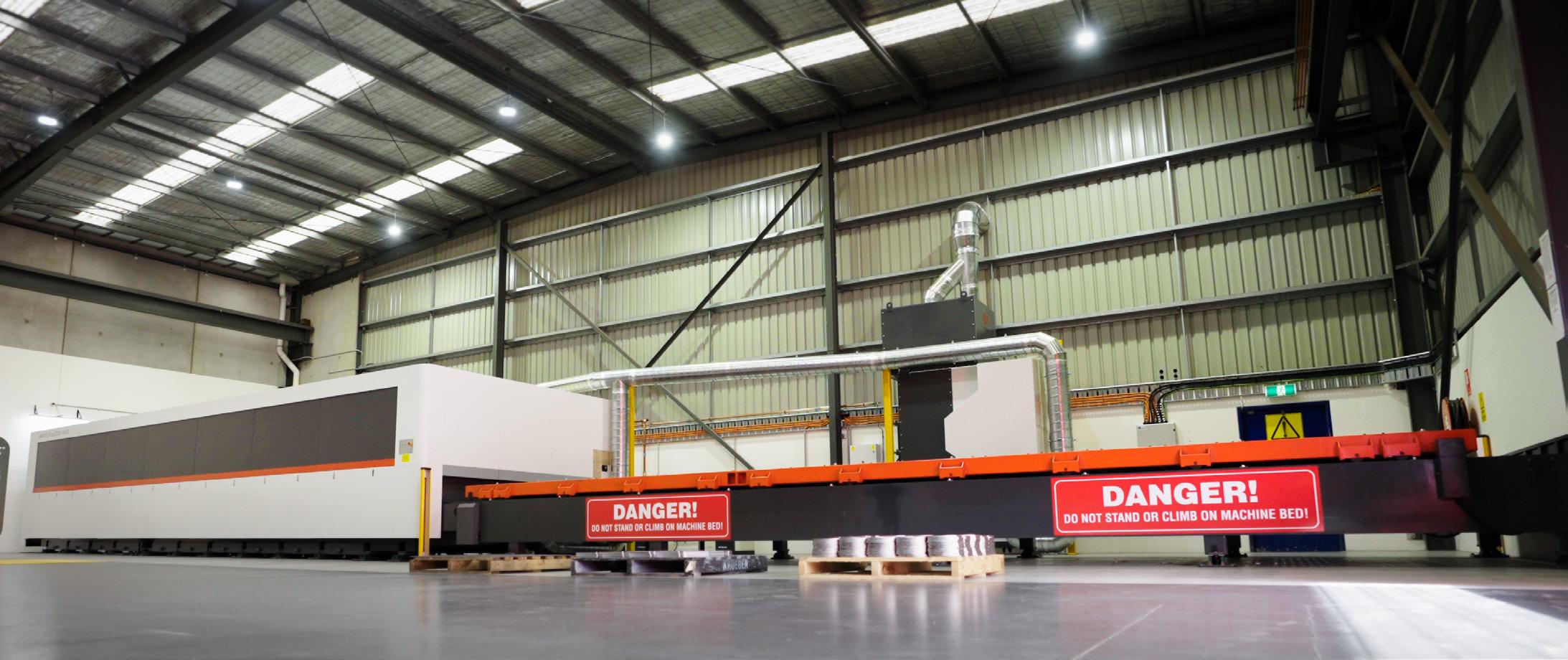
With the new laser cutting machine up and running, ongoing calibrations of the cutting nozzle are required to ensure the machine is running to optimum specifications to suit the job on hand. To perform such calibrations quickly and with a high degree of accuracy, the team sought expert input from Suba Engineering who is a leading expert in the field of industrial microscopes. With a SureScope Ultimate 4K in place, the team can not only perform accurate nozzle calibrations in short time but can also perform careful examinations of the laser cut quality, arising from the need to adjust the laser cutting machine parameters due to different materials and gases used in the cutting process.
Finally, to take full advantage of the laser cutting machine’s advanced cutting technology, Krueger has begun using the Metalix suite of CAM software with the support of the local supplier Punchtech who specialise in solutions for the sheet metal industry. The goal of seeking local support from Punchtech was to not only develop highly efficient nests to maximise raw material usage, but to exploit all the advanced features of the software and the laser cutting machine to get the most from them in terms of capability, handling high volumes of work, and optimising for best-in-class quality.

With Krueger Transport Equipment’s latest piece of industrial technology in place, our customers will continue to experience our ongoing pursuit for best-in-class manufacturing excellence, as our trailers are built faster and with a new level of precision that will set a benchmark for the industry.