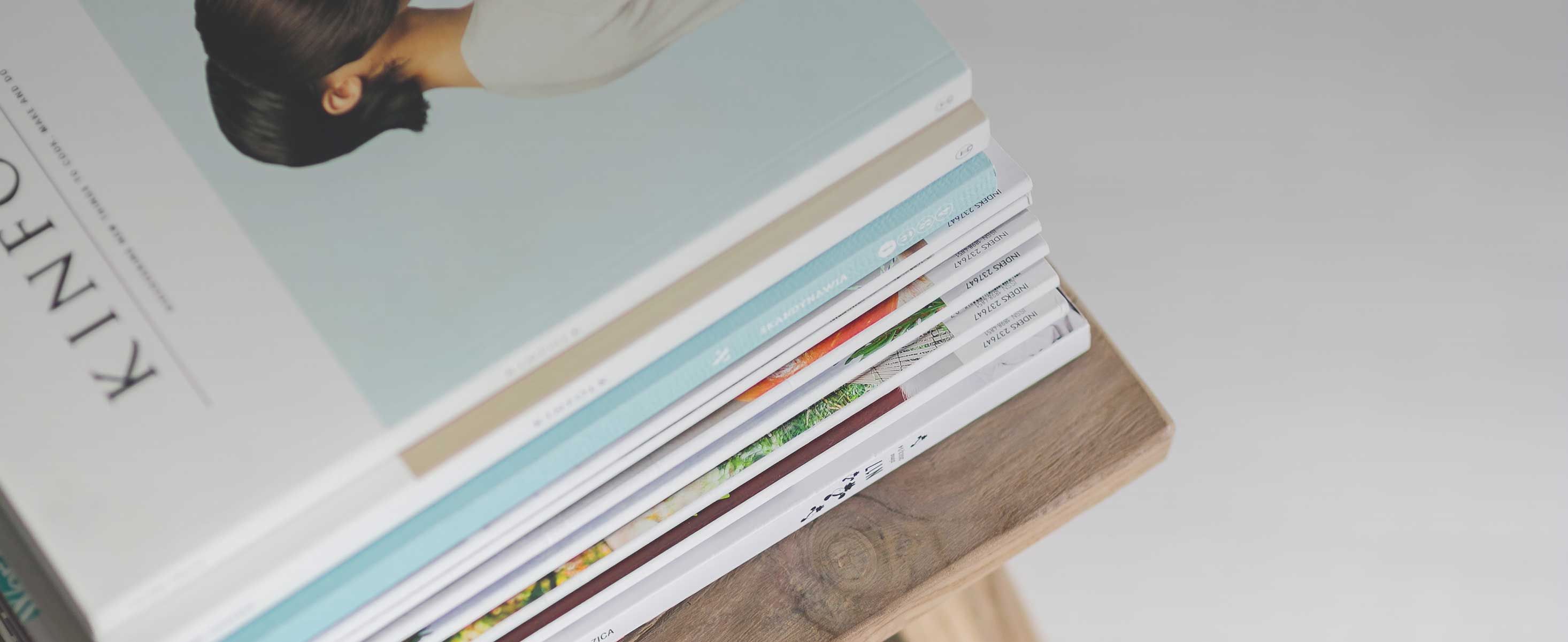
12 minute read
Hazard identification, risk assessment and risk control
Some WHS consultancy businesses offer a service where they attend your service and conduct an inspection. They may take photos and then write a report on any risks or hazards that are present at your centre. They also provide you with an action plan for implementing changes in the workplace.
Services could also subscribe to weekly newsletters which highlight WHS issues to keep them informed and up to date.
Advertisement
There are three steps for managing work health and safety in the workplace:
1. Spot the hazard — in other words, Hazard Identification.
2. Assess the risk — in other words, Risk Assessment.
3. Make the changes — Risk control.
Spot the hazard – hazard identification
A hazard is a source of potential harm or a situation with potential to cause loss, injury or illness.
The management of hazards in the work environment is a key attribute of WHS management systems. Each organisation will establish its own systematic approaches to managing hazards within legislative requirements and frameworks.
It is important to identify hazards so that they can be controlled. Hazard identification is all about good quality information. This information can be gleaned from a number of sources and may be considered in two categories: • external sources, which include regulatory authorities, industry bodies, employer groups, unions, OHS specialists, legislation, codes of practice and standards, databases, journals, websites and manufacturers’ manuals and specifications • information within the workplace, which includes historical data, procedures and registers and the results of monitoring and workplace inspections. Sources of information for hazard identification available in most workplaces include: • hazard, incident and injury reports • investigation reports, workplace inspections • maintenance records • risk registers • minutes of meetings • risk assessments • workplace policies and procedures • reports and audits • sick leave and personnel records • organisational data such as insurance records, enforcement notices and actions, worker’s compensation data • Safety Data Sheets (SDSs) and chemical registers.
Some sources of information are more useful for particular hazards. Maintenance records will be important for plant hazards and sick leave and personnel records may give indications of psychosocial hazards.
Workplace inspections
A key source of information in identifying specific hazards is direct observation, or more specifically, informed direct observation of the workplace and its various tasks. Workplace inspections, walk-through surveys and the use of checklists can assist in the risk identification process.
Examples of workplace hazards in education and care services include:
• untidy office store rooms • untidy playground storage sheds where large heavy items are stored at a height • frayed electrical cords which could result in an electric shock
• used syringes in playgrounds after a weekend break.
Source a checklist as a starting point
Hazard-specific workplace inspection checklists may be available in the workplace or may be accessed from the WHS regulator, industry bodies, similar workplaces or WHS consultants. Even if there is an existing checklist(s) in the workplace, it is important to regularly ‘benchmark’ to check if there are better or more useful checklists available.
Codes of practice are a useful resource. By their definition, they give guidance on how to comply with regulatory requirements. Most hazard-specific codes of practice include one or more tools to assist in hazard identification. These tools may be generic or may be adapted to suit specific industries. While codes of practice should be followed unless there is an equal or better way, the checklists still need to be reviewed to ensure that they are appropriate for a particular situation.
Simple hazard identification checklists may identify hazards such as:
• obstructed doorways • defects in flooring • spills • misplaced or broken machinery guarding, e.g. a kiln • frayed or trailing electrical cables • damaged or faulty portable lamps, hot glue guns, microwaves • hazardous chemicals not adequately contained.
Examples of health hazards are: • lifting and handling heavy children • tripping over children • high noise levels due to buildings not being designed for children • heat • radiation • harmful dusts or vapours • work-related stress and other psychosocial hazards such as workplace violence and bullying • other hazards such as fatigue due to long and unreasonable shifts.
This hazard identification list is specifically for WHS, and not for the health and safety of children, although invariably these will overlap in a final hazard checklist for an early childhood centre.
Outside
Playground is free of syringes that may pierce a worker’s shoe.
Sandpit has been cleaned to ensure it is free of animal faeces.
Paths and paving surfaces are free of slipping hazards, e.g. sand. Is there any non-slip covering on ramps to prevent slipping when it is wet?
Soft-fall and grassed areas are free from hazards.
Tyres and other equipment with recessed areas are free of snakes and spiders. Tick
Inside
Exits are clear.
Heaters are maintained.
Training has been given to workers on lifting children while changing their nappies. Tick
Review the checklist
Any hazard-specific checklist should be reviewed prior to use to ensure that it: • is relevant to the industry or type of work • suits the workplace • addresses all the required areas or items • is usable by the people in your workplace.
The people who should be involved in the review include: • the educators or staff members who will use the checklist • the educators or staff members who do the work • WHS consultants.
As we are learning more about workplace hazards all the time, all checklists should be reviewed on an ongoing basis to ensure that they allow for emerging issues and reflect current industry knowledge and practice. Remember, the conditions that lead to the loss of control of a hazard may develop over quite long periods of time and come directly from, or through the interaction of, one or more of the following five sources: • the physical environment • the leadership and management • equipment • policies and procedures • people and human error.
Checklists usually focus on the physical environment. In reviewing the checklist, consider to what extent it includes items that address the other four sources listed above.
Identifying hazards and the preconditions that may result in loss of control of the hazard should be a collaborative effort. Where possible, workplace inspections are best conducted by a team. There may be two people for each inspection, and it may mean rotating the people who do the inspection so that ‘fresh eyes’ are applied from time to time. It may also mean bringing in someone from outside the workplace to accompany a person who is familiar with the workplace and the tasks. A team approach allows for a more comprehensive and collaborative review of the work and the environment. The team may include (not necessarily at the same time): • educators and other staff members including the cooks/chefs • the WHS representative • WHS consultants • ‘fresh eyes’ – maybe a WHS representative from another centre • an authorised officer.
Conduct the inspection
Inspections should be repeated at regular intervals. They should also be conducted at unscheduled times to pick up on the items that may not be apparent when scheduled inspections occur. There is a danger that the checklist may ‘blinker’ the people doing an inspection or the format may limit the extent of the comments or notes. Also, there is the ‘tick and flick’ approach that results in a pile of paper, but little effective hazard identification.
While checklists are a vital tool in hazard identification, some hazards may not be identified if the process is totally checklist driven. All workplaces should consider seeking expert input to the hazard identification process, especially at key times such as: • when a new centre is opened or purchased • during self-assessment phases • before changes are made to the buildings or playgrounds.
Risk assessment
Risk assessment is the process of working out the likelihood that a hazard will hurt someone and how serious that injury could be.
Educators should ask themselves two questions: • How likely is it that the hazard could harm me or someone else?
• How severely could I or someone else be harmed?
It is important to communicate any hazards you cannot fix, especially if the hazard could cause harm to you or anyone else.
A safe workplace doesn’t just happen by chance or by guesswork. It requires a systematic approach to finding and fixing hazards and risks. This approach ensures the highest level of protection is in place for people at work. It begins with identifying the hazards. Once you have identified hazards, you should: • undertake the process of risk assessment using a risk assessment template (see below) • tell your approved provider, manager, leader or health and safety representative if you think a work practice is dangerous.
The following tables will assist you in determining the likelihood of the hazard. Risk assessments ask you to assess the probability of an accident occurring.
Descriptor Description
Certain It is expected to occur in all circumstances.
Almost certain It is expected to occur in most circumstances.
Likely Will probably occur in most circumstances.
Possible Might occur at some time.
Unlikely Could occur at some time, but unlikely and only in exceptional circumstances.
Determine the consequences
Level of effect Example of each level
Insignificant/ Acceptable No effect – or so minor that effect is acceptable
Minor First aid treatment only
Moderate Medical treatment
Major Extensive injuries, loss of production, e.g. a fire
Catastrophic Death
Risk Matrix
Likelihood
Almost certain
Likely
Possible Unlikely
Rare Consequence
Insignificant Minor Moderate Major Catastrophic
Moderate High High Extreme Extreme
Moderate Moderate High Extreme Extreme
Low Moderate High High Extreme
Low Low Moderate High High
Low Low Low Moderate High
Extreme – Act now – Urgent – do something about the risks immediately. Requires immediate attention.
High – the highest management decision is required urgently.
Moderate – follow management instructions.
Low – OK for now. Record and review regularly, and check if any equipment/people/materials/work processes or procedures change.
You would then complete the following risk assessment template using the above tools.
Below is an example of a risk assessment for an excursion to a local park where educators have chosen to take the children bike-riding. This risk assessment is for the safety of the educators and for the safety of the children.
Excursion to Sunnyside Park
Risk assessment
Activity Hazard identified Risk assessment Elimination/control measures Who When?
Bike riding Can children ride?
Can staff ride?
What if someone falls off their bike? Moderate 1.Survey parents before the excursion to determine the children’s bike-riding skills so they can be grouped accordingly. 2.Carry a first aid kit for any accidents.
3.Each educator to carry a phone when groups are split up. 4.On the day, group children according to skill level and allocate them to one educator for supervision. Director/
Coordinator
Leaders and managers should ensure that staff members do not have a pre-existing condition that would be exacerbated by bike riding.
Bike riding Extreme heat Moderate 1.Children and staff must have sunscreen applied before leaving for the park. 2.Children and staff must wear hats.
3.The time of the excursion could be changed to earlier in the morning so it is not too hot. 4.If it gets too hot, ring bus driver and ask them to pick up the group earlier. 5.If one child or staff member is too hot and seems to be suffering from heat exhaustion, the group will leave.
6.Organise for a parent/staff member to arrive with icy poles for the children.
Bike riding Insect bites Moderate 1.Bring an insect repellent on the excursion.
Bike riding Snakes Low 2.Ensure that the first aid kit has some ‘Stingoes’. 1.Ensure that children and staff members stay on the main path and do not go into the areas of long grass.
2.Ensure that staff know the first aid procedures for snake bites.
3.Ensure that everyone wears appropriate shoes.
Risk assessment
Activity Hazard identified Risk assessment (use matrix) Elimination/control measures Who When
Risk assessments are not undertaken just for excursions, but may be undertaken for certain pieces of equipment either inside or outside the building. Once a risk assessment demonstrates that there is risk involved, then this risk should be managed.
Make the changes – risk control
It is the responsibility of the PCBU to fix hazards. Sometimes educators will be able to rectify simple hazards, if they don’t put themselves at risk. For example, if you notice a frayed cord on a piece of electrical equipment, you may decide to throw out that piece of equipment. That is called ‘elimination’ and is one of the steps in a process called the hierarchy of control, which includes the following: • elimination • administrative controls • substitution • engineering controls Elimination Eliminate the risk (so far as is reasonably practicable). The best option is to remove the risk completely, so you should always try to do this at first. Elimination might occur with faulty electrical appliances. Substitution If you can’t remove the risk, think about substituting the equipment or processes that you are using. What could you use as a substitute? For example, if you used a hot glue gun as an adhesive and an adult burns their finger, you might suggest that they use a PVA glue instead.
• PPE.
Most e ective
Least e ective
Hierarchy of Controls
Elimination
Physically remove the hazard
Substitution
Engineering Controls
Administrative Controls
PPE
Replace the hazard
Isolate people from the hazard
Change the way people work
Protect the worker with Personal Protective Equipment
Engineering controls Engineering controls include adjusting the equipment or building structures that may be hazardous. Engineering controls may be used if a staff member hurts themselves on something in the centre. For example, if an adult walked into an outside pole, rather than remove the pole (which is holding up the shade sail), you may surround it with padding.
Administrative controls You may need to review your processes to remedy hazards. Administrative controls include policies, procedures, training, supervision, signs, flags, rostering practices and safe storage of chemicals.
Personal protective equipment (PPE)
Educators and staff members may need protective equipment so that they can undertake their work effectively. For example, the service may supply staff members with hats and sunscreen for outside supervision.
In practice, a combination of control measures will be required to reduce the risk to an acceptable level. You must always apply the hierarchy in order from the top down, as far as practicable. Always consider elimination first as an option and only consider PPE as an additional, least reliable resort.
Risk controls should be monitored and reviewed for any residual risk. Residual risk is simply any level of risk left after treatment measures have been taken.
Once the risks have been assessed and rated, you may enter your results into a safety action plan.
You could use the template below.
Safety issue or hazard Action required Person responsible Date of action to be completed Review date and comment
SAFETY ACTION PLAN
High priority
Medium priority
Low priority