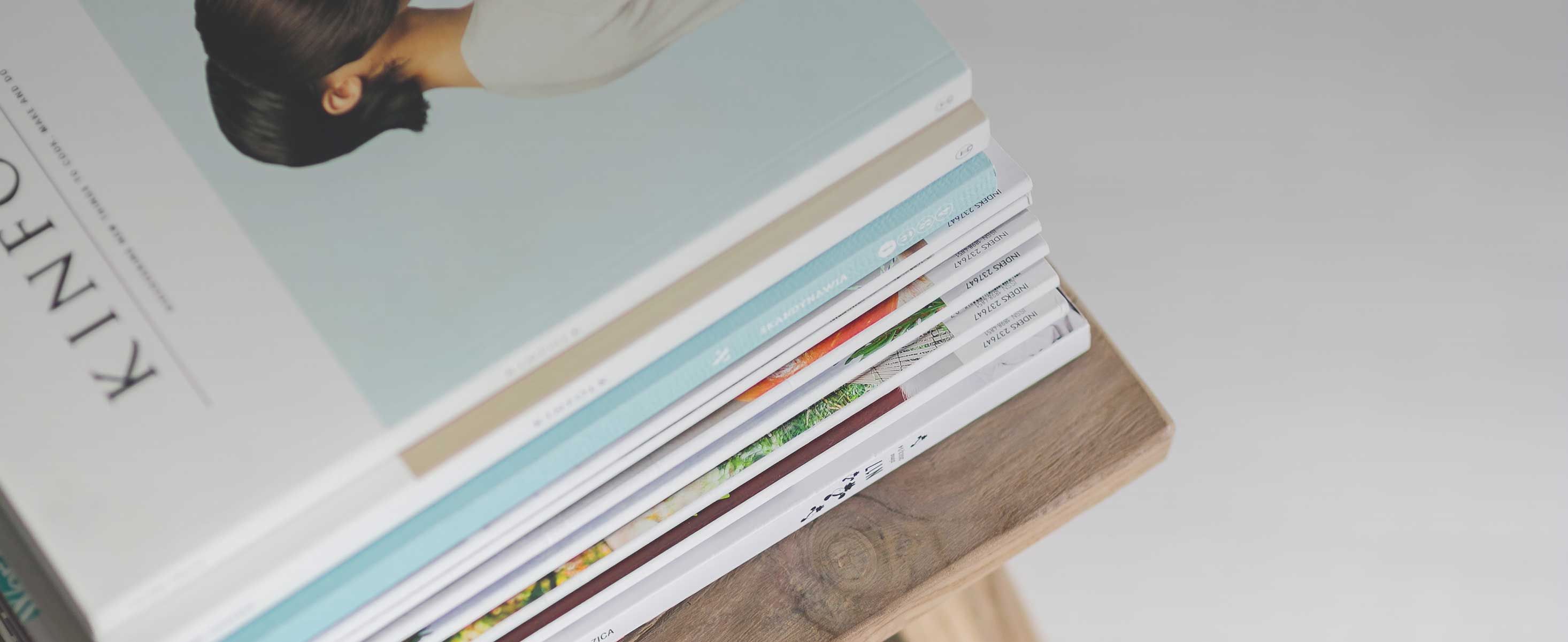
2 minute read
The world of edge banding
Woodworking machinery has come a long way in the last few decades no more so than in the field of edgebanding technology which has become a core part of the nested based approach to manufacture so widely adopted here in New Zealand. Business here in New Zealand has been brisk in recent times no more so for the sales of edgebanding machinery. Bob Nordgren recently caught up with Mike French from Technical Machinery Services Ltd (Techms) who hold the Holzher machinery agency here in New Zealand to find out more about modern edgebanders and what have been the key advances in their development.
You have some thirty years in the woodworking machinery business and have been involved in a dozen or so edgebander installs since Christmas in what has been a busy time for the woodworking machinery market. What do you see as the main developments going forward with edgebanding machinery?
“When it comes to edgebanders
I can only speak for what I sell which is the HolzHer range, with Holzher glue application system GJ301 there have been many changes and improvements to give us the best glue line in the industry and to keep the operator informed with glue levels and so on. The changes come in the level of accuracy, in our case down to 0.1 millimetre with CNC drive system adjustment, and the level of automation involved. A good example from our perspective is the Holzher 1308 Power edgebander which is accurate, fully automated as to processes, few moving parts so maintenance is minimal and has a relatively small footprint but still comparable to larger machines on the market as to what it can do (full hood down adjustment). That’s not to say bigger machines are not popular as well as they are. The industry has been part of a buoyant market in recent times.
The key change has been the ever improving software used in the edgebanding industry. All the manufacturers have produced their own software which goes in tandem with the automation levels of various machines. Our view has been that automation is crucial as it brings greater consistency and accuracy to the edgebanding process. These predetermined programmes make the edgebanding process far easier as well with the use of touch screens which has made operating the machine very easy and in turn makes diagnostics processes quicker and more effective in the event of an issue arising.
Edgebanding is also about the tape product you use and how it is applied. Heat activation methods have been a key process. In our laser system we use infrared technology to activate the glue. The right product will get the best result. The use of PUR and EVA glue with GJ301 and premill has been central to the ‘invisible’ finish so popular these days
These developments and trends are where the technology is moving, what is most important to you beyond them?
“For me it must be training and support post sale. No time limits apply when it comes to training staff even though it is relatively straight forward and only involves a few days in most cases. What is just as important is ongoing support. Being there when needed to fix anything and offer advice. Customer perception in the first couple of weeks is very important in establishing a good long term relationship between the supplier and the buyer. This starts with the install process where having a machine that is reliable on arrival with an easy install process makes a big difference. We have installed a number of Holzher 1308 edgebanders in recent times and they have all met these criteria.
I guess it is a trend we are seeing in that with all these constant improvements plug and play is looking more and more likely.”