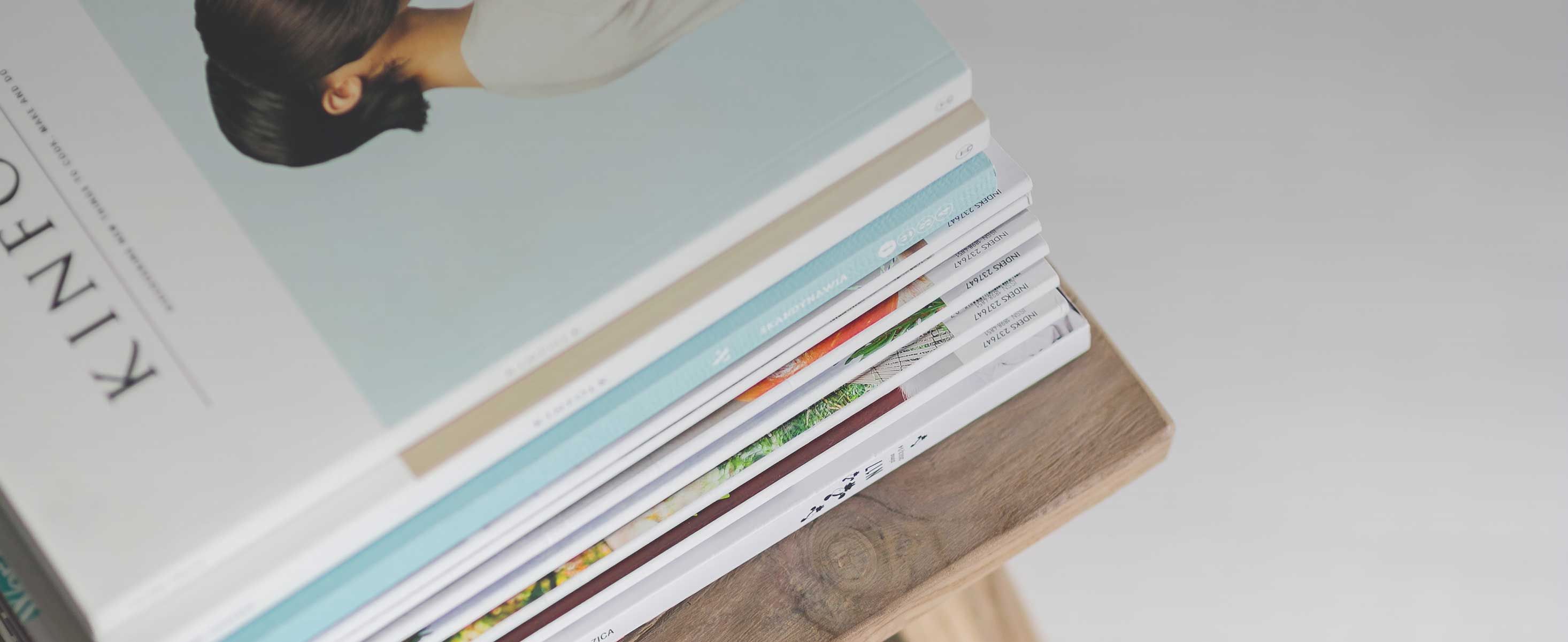
12 minute read
STATE OF THE INDUSTRY
Reports from Branch Presidents May 2022
AUCKLAND/ NORTHLAND
Auckland / Northland region had the annual fishing trip which was a great success again with two boats heading out full of members and suppliers to the Firth of Thames with clear skies and plenty of fish being caught.
Unfortunately, due to the latest explosion of Covid 19 pandemic in the Auckland area, we again had to cancel our meeting due to concerns of the virus spreading even further. However, we did replace it with a Zoom meeting with our guest speaker talking to us about the new H1 thermal regulations and the impact it makes on the joinery we manufacture. We have our next meeting / AGM planned for mid May, so fingers crossed.
The outbreak of Covid 19 in the community has had a huge impact on all our business, with staff absentees due to catching the virus or self-isolation. In some cases, staff have been absent up to 3 weeks. The supply chain has also been hit hard with stories of transport companies down 19 drivers out of 29.
Currently there is a good amount of forward work and plenty of activity, however, there are concerns where 2022 may end up, with inflation, increasing interest rates and the housing values plateauing and even decreasing in areas.
We are still hearing in the market that building projects are being put on hold or cancelled mainly due to the ever-increasing cost of materials across the building sector which is putting projects well over budget and no longer affordable.
Hardware suppliers are now bracing themselves for more supply chain issues, as parts of China have been or are in complete lock down, affecting production. Along with this in late April it was reported that 20% of the world’s roughly 9,000 active ships are currently sitting in traffic jams outside congested ports. Close to 30% of that backlog alone is in China.
We are seeing continuing price increases in local and imported timber, due to domestic inflation and world supply and demand and the current cost of shipping. Selected sizes of timber are also very limited, resulting in joiners having to use uneconomical sizes and thus increasing their costs of manufacture. - Rob
Pickup
Canterbury
If 2021 was crazy then 2022 has been unprecedented (to use the most overused word of the last three years). Everyone’s workloads have been extremely busy. Staff shortages as well as absenteeism have added to the stresses of the year. Shortages and delays in supplies have been testing to all of us. Many of us have become magicians at being able to source other products or, in some cases, lead our clients in a different direction towards other products that are available.
Covid has disturbed our lives and our workplaces. With isolating taking its toll on work production, it’s also impacted negatively on people’s mental health. We have all had to deal with increased workloads to cover for those that are sick or have had to look after sick children. Some have also had to deal with multiple isolation periods due to government health regulations.
We held our May meeting and AGM last week and had a great turn out. It has been quite a while since we have held a meeting in person. It’s always great to catch up in person with fellow joiners and discuss the world’s problems. We have had to hold our previous meetings by Zoom. We have tried to support our members as much as possible and have been able to discuss supply issues, covid concerns and staffing shortages.
Our Canterbury Master Joiner Awards have been set down for Friday 12th August. This is our chance to shine and showcase the amazing work we all produce.
With National Conference being in Blenheim this year, so close to us here in Canterbury, it will be a great chance for us to get to enjoy conference with like minded people.
My three years as President of Canterbury Master Joiners is coming to an end. I have thoroughly enjoyed my time as president, learnt so much and meet so many new people. I have grown as a person and as a business owner. I look forward to continuing my challenge as National Vice President.
April has been really busy on the farm. The weather has been playing ball, with the sun shining and having more warmer days than normal for this time of year. Heifers have gone to wintering blocks and the calves have been transitioned onto fodder beet for the winter.
Central
but a good chance to share stories and information in our industry.
- Nathan Busch
This quarter instead of just putting my thoughts down on paper, I reached out to a mixture of different members in our region to gain their thoughts.
Of the members that I talked to, the industry is still going really well. Enquires are still flowing in and there is plenty of work out there to be done. Covid has been an issue for everyone with staff needing a week to two weeks off isolating at home. The vibe is that everyone has managed to get through this and is feeling more positive.
Our apprentices in the region are going really well. They are eager to learn and really engaged which is fantastic. In the last year Central has seen over 20 new apprentices signed up which really is great and gives us promise for the future.
Supply issues in the building sector are causing issues for our members with jobs that were booked in being delayed. Some members are finding this as a blessing, as it is giving them time to catch up on work.
The feeling is that clients are not as accepting of the wait times as they have been. This, along with constant price increases, means that client relations is key at the moment. Overall, the Central Region is still performing well and members are happy which is fabulous. -
Kristine Holmes
HAWKES BAY / POVERTY BAY
It’s a Mixed Bag. It’s been another year of ups and downs. Supply chain seems to have pulled back a little but not all the way and as we all thought the cost increases have followed also.
Our region’s Master Joiners are still keeping busy, with some noticing a slow up. No doubt the cause being the increase in interest rates. Inflation is at the highest it has been in a long time, if not ever.
Our region has had some fun at our meetings with land yachting and mini golf. Nothing taken seriously
Together we are stronger. As an association, the knowledge we share among ourselves should be taken advantage of, we often do similar work but may do something a little different from others. It’s these little tips, tricks or systems that we do that helps us to run our businesses more smoothly. Last week I called into a few workshops and was encouraged by how open we are to each other, friendly banter, share a whinge or tour of the workshop. These are all good things, it’s good to share the pressures and joys that we face. Not many mortals would.
The apprenticeship scheme the government has been running is there to be taken advantage of. This needs to be extended. This is the only way to get an advantage in our labour force, as these numbers have been dwindling over recent years. With overseas workers filling a needed gap in the meantime.
The phrase ‘cherry picking’ is what we need when it comes to school leavers, the ones that show an interest in being creative and hands on. Planting the seed that a Joiner is a great trade to the younger students would be a better goal. A trade with a future. -
Greg Rabbitte
NELSON / MARLBOROUGH
Big increases in material costs and freight, lots of communication with clients on increases and tags in prices and quotes.
April was a quiet month for the branch with Easter and ANZAC holidays. We had an online survey which participating members had feedback sessions on, which was very useful for strategic planning going forward.
Covid staff absences are being managed but are affecting delivery dates for completions / installs etc There is a distinct hold up with workloads due to material supply, mainly Gib board. This means there is constant re jigging of factory output planning. An aluminium window manufacturer probably summed it up, what used to be 4 weeks from measure to install is now 11-12. Lots of communication around whether they are ready for measure, if not they go to the end of the queue.
Perhaps a bit of light at the end of the Covid Tunnel. Perhaps a slight easing in enquires with the increases in cash rates etc, watch this space. Workload, bookings forward
• workloads … months … years
• calendars for most seem full
• designers seem busy and enquiries continuing
• fewer larger projects at present
Key themes, new builds versus alterations, materials supply
• mixture of new builds and renovations, bathrooms
• some are choosing work as they are restricted in volume so are targeting the most profitable type of jobs so to maximise return
• materials supply: it is what it is, just manage it!
Other themes from ‘normal’, payments good?
• most have good contracts and conditions in place for payments
• staff movement still a problem
• the older staff are retiring
• employees wage expectations are increasing; they have worked it out that they are valuable as there is no one there to employ. LOOK OUT $$$
• if you want to keep doing what you are doing the cost of doing it is about to go up. You have the orders that need to be filled
• the opportunities are around for everyone, they can chase another profession that pays better. Building companyproject manager is who we are competing against. Pay, Ute, working conditions. -
Phil Agnew
OTAGO / SOUTHLAND
The Otago Southland region has continued to perform well over the first half of this year. Across the region strong workloads and a steady supply of incoming work tend to be the common themes. There remains positive news on a number of fronts – apprentice numbers are strong, and the supply chain appears to be settling.
The industry has benefitted from the Covid lock downs – leaving most at home and contemplating upgrades.
Our AGM and mid-year dinner is just around the corner – in Dunedin on the 17th of June. That’ll mark the end of my tenure as regional president. It has been a few years now and it is time to cycle the seat again. I’d like to thank those members who have helped me over the years, notably Peter Fisher and Peter Leith. Appreciated as always. I’d like to think that we’ve moved forward. Meeting numbers are up, and we’ve all enjoyed a period of networking and cooperation. Long may that continue.
All the best for the rest of the year. I look forward to catching up with you all again soon.
Taranaki
- Reuben Bogue
Well, as we head into the winter months with darker mornings and the sun setting earlier, the weather can have a big impact on how we feel. Christmas seems like it was ages ago and the crock pot recipes are slowly emerging.
Most firms have been hit by Covid creating staff shortages at times, putting pressure on them to keep their production on schedule and getting products delivered on time.
Most of our members still have steady work loads heading into the winter months. Getting materials can still be a problem with some shortages and more price increases on the horizon. Receiving couriered products within a reasonable timeframe can still be a problem, recently we have had things couriered to the wrong town or only getting half of the order, and if you are lucky, the other half turns up a couple of days later. With the war overseas, we may also find further shortages of even more products over the next year, and more likely heavy price rises. We see ourselves having to consider using alternative products and trying new things to stay current and keep production flowing. Diversity can be our friend as long as we maintain our high standards and protect our individual brands, as well as the integrity of the Joinery sector as a whole.
Builders seem to be worse off, with gib board holding builds up from finishing. Taranaki is still steady in the house building, most of the commercial builds seem to be long term at the moment with some still years away from completion. There does not seem to be too much new commercial building being started at the movement. Other industries seem to be steady as well, they are still drilling offshore for gas, and have hit some large pockets of gas, so that’s great news.
Finding staff is an on-going headache that our sector faces. There is a huge shortage of ‘Detailers’ who do the drawings on the computer and get it ready to go, and also tradesmen, to work on the factory floor. It is interest to consider how many skilled people are leaving and why. In Taranaki not many apprentices are being taken on, it seems to be very hard to find that right young person to take on the responsibility. We need to look after our staff and be responsive employers to ensure we keep them!
Let’s hope the winter days, will not be too cold or wet, but it’s going to be a very interesting few months to see where things are heading. Be kind and stay safe. -
Bryan Frank
WAIKATO / BAY OF PLENTY
The Waikato/BOP region has experienced fantastic summer weather with very few rain days so far this year. This has been one positive for the building industry of late! Heavy workloads are being reported around the region’s members although the inconsistent workflow and constant rescheduling of projects continues to make day to day management difficult. Ongoing shortages of workers, particularly in specialised roles requiring a level of experience, continues to be another major challenge. And, of course, the price increase notices which continue to plague our Inboxes. The challenges of the wider building industry are having a huge impact on our businesses this year.
To better understand the challenges our builders are facing and how the trades can best support each other through this period, we are planning to have a Panel Discussion at our AGM to openly share our concerns and ideas. The Waikato President of Master Builders and others will be there to share their insight and listen to the members.
As Covid restrictions start to ease and we can move around more freely, we are planning to focus on bringing our members together again in person, with Events and Meetings that will reconnect us as a Community of Master Joiners. We have certainly missed this over the past two years. - Cherie van der Poel & Craig Mackie
Waitaki
The Waitaki region has just been hit with the effects of the Covid Virus with many businesses being left with managing workloads with reduced staff numbers making it difficult to meet client’s delivery dates. While most, if not all, have good forward work loads, a number have struggled to get many contracts started with construction also struggling to get contracts ready for site measure due to the lack of lining materials (gib board mainly).
Staffing is still and will continue to be an ongoing issue in this region. Large number of factories are looking for experienced trade staff, but a number indicated that they would hold off with any future employments to see how material supply goes moving forward. Locally there are several companies training a number of apprentices.
Once again materials, in particular timber supply, has been an issue for a number and hardware supplies are proving problematic. A number of companies are getting deposits in advance which enables purchasing of material in advance at the quoted price but generally members are working through these issues with alternatives or securing product early.
Keeping up with constant price increases has been a battle and extremely difficult to communicate to clients about with product quotes being valid for very short time frames.
All the members indicate that clients are generally paying on time which is good management in these difficult times.
All indications in the Waitaki area seem to be pointing to a busy year, members having full workbooks from mid to late 2022. - Mark Albert
Wellington
What a frantic start to the year. All members are reporting a very large workload. I have heard from a number of members that 2021 was a record-breaking year on top of a record breaking 2020 ... long may it last.
It seems there is a never-ending email stream of price increases and many of the cost increases are now in double digits. As most contracts are at fixed prices and the level of inflation has exceeded expectations, gross margins will be significantly eroded, and some companies are already making losses on projects where profits were previously envisaged. With the recent collapse of a large construction company in Wellington, it is a prudent reminder to mitigate your risk with deposits and progress claims and to secure stock as early as possible. It seems everyone is being held up with building material delays and shortages with lingering uncomplete jobs and companies facing space issues. Some companies are going as far as placing storage containers in their yard to hold completed jobs. Maybe it is time to look at other, non-fixed price contracts or at least a rethink until everything stabilises.
- Grant Smith