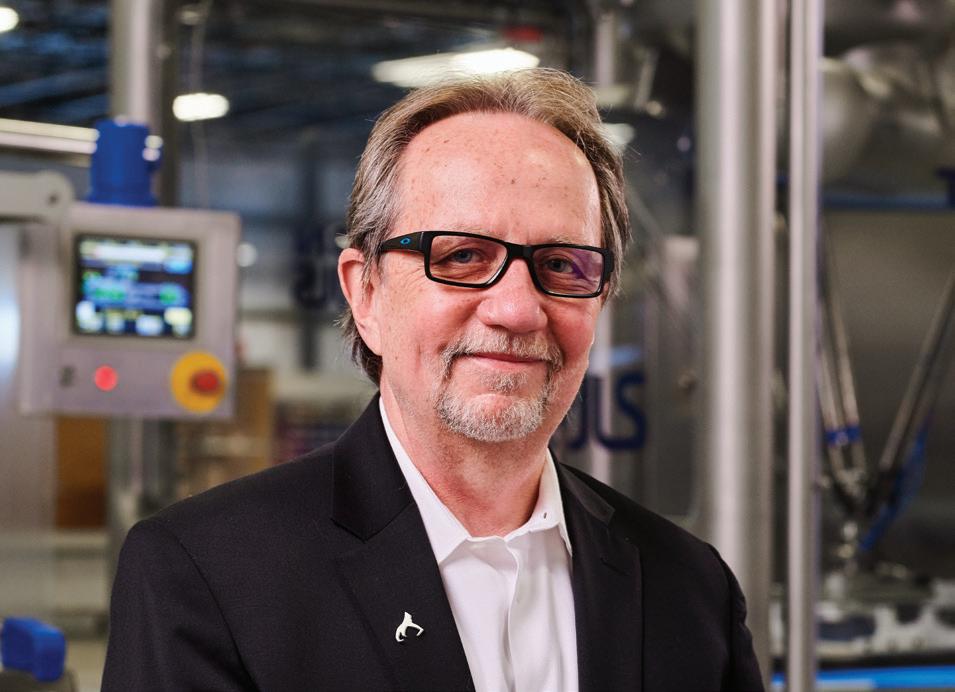
3 minute read
Ken Harding Solving the challenges of thermoformer loading
from JLS Magazine #2
Talon® pick-and-place systems address hygiene and product orientation issues.
For easy-opening features on the package, you can have peel headers, where you have a complete unsealed edge to hold onto or smaller peel corners. Sometimes, there are other more unique thermoformed features depending on the packaging requirements. A thermoformer will provide a high level of versatility with a simple tooling change. You can make a wide variety of packages on one compact machine.
Q: What are the challenges for loading products into thermoformed pouches?
KEN HARDING, DIRECTOR OF APPLICATIONS
ENGINEERING AND SPECIAL PROJECTS at JLS® Automation, discusses how JLS mitigates the challenges of thermoformer loading while saving costs, materials and floor space for its customers. Harding holds more than 25 years of experience in packaging and food processing with a strong foundation in hygienic design, food applications and is an expert in thermoforming.
Q: How many thermoforming applications have you seen in your 25 years?
Harding: I’ve seen hundreds, if not thousands of thermoformers in operation. I’m sure there is an application I haven’t seen, but not many.
Q: Are there specific product applications that are better for thermoformed pouches versus a flow wrapper or other format?
Harding: For food applications, you’ve got the ability to produce a modified atmosphere or vacuum package for extending shelf life. A thermoformer also provides you with a multitude of film options from rigid trays to flexible pouches and skin packaging.
Harding: There are several challenges with auto-loading thermoformers. One being that thermoformers are intermittent operating packaging machines. This means they do not run continuously like how a flow wrapper does. Loading a thermoformer, you generally load products into the thermoformer packages while the machine is in dwell, in between web advances or during both dwell and during the web advance while tracking the acceleration and deceleration of the web. This makes managing infeed product delivery, calculating cycle rates and capacities, as well as balancing throughput requirements a little tougher compared to most other packaging applications. Other challenges include providing adequate access to the thermoformer and providing hygienic design, because you’re typically packaging either a raw or a ready-to-eat (RTE) product such as a sandwich or deli meat. These applications require the most stringent hygienic design.
Q: How is loading achieved while ensuring product integrity and accurate placement within the pocket?
Harding: It is typical for us, as well as in the general application of loading a thermoformer, to track the index or track the web as it’s moving through the machine. Then, knowing what the die array pattern is gives you fixed targets that you are placing a product into. The key is to pick and load the product with the appropriate end-of-arm-tool to match the application needs. For instance, whether it’s uncooked/raw chicken versus a draft of sliced cheese, the end-of-arm tool requirements are quite different.
Q:
How does the JLS ® Talon® accurately load products in various orientations?
Harding: If you are loading chicken drumsticks, for example, you would pick and target those with the robotic vision system in a manner where the end-of-arm tool would rotate the product and place it into the package opposing one another. You would generally perform multiple picks to load all of the product in a layer that’s facing one direction and then come back with a subsequent placement of products facing in the opposing direction.

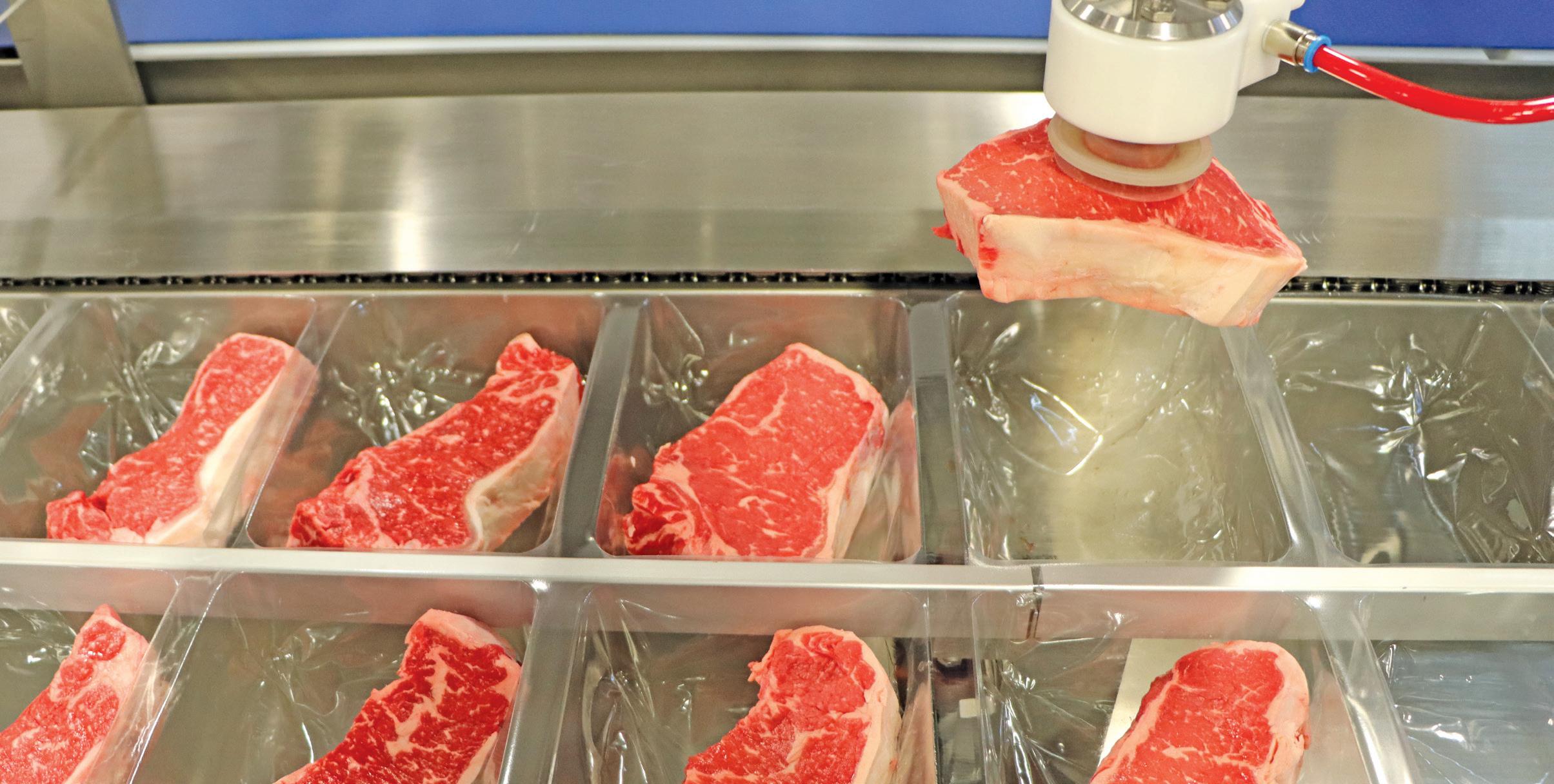
Q:
What Talon features ensure hygienic design?
Harding: The Talon begins with a hygienic design open-channel frame construction, so there is no hollow tubing or harborage areas. We are diligent in our design process to ensure that the entire robot frame assembly, the IP69K Codian robot and the robot tooling are hygienic, accessible for washdown and sanitation and accessible for inspection. All areas can be swabbed for verification that there is no bacteria on board. Standard hygienic design features like sloped surfaces for easy runoff, standoffs for component attachments and open cable management are employed.
Q:
What’s on the horizon for JLS with thermoformer loading?
Harding: There are a number of challenging applications that JLS is developing where the product is hard to predict and control when it enters the robot picking area. To address this, we are working on innovative mechanical tooling and product delivery conditioning systems so that we can pick up difficult products, consolidate them and put them into a thermoformer pocket successfully.
To learn more, visit www.jlsautomation.com/talon