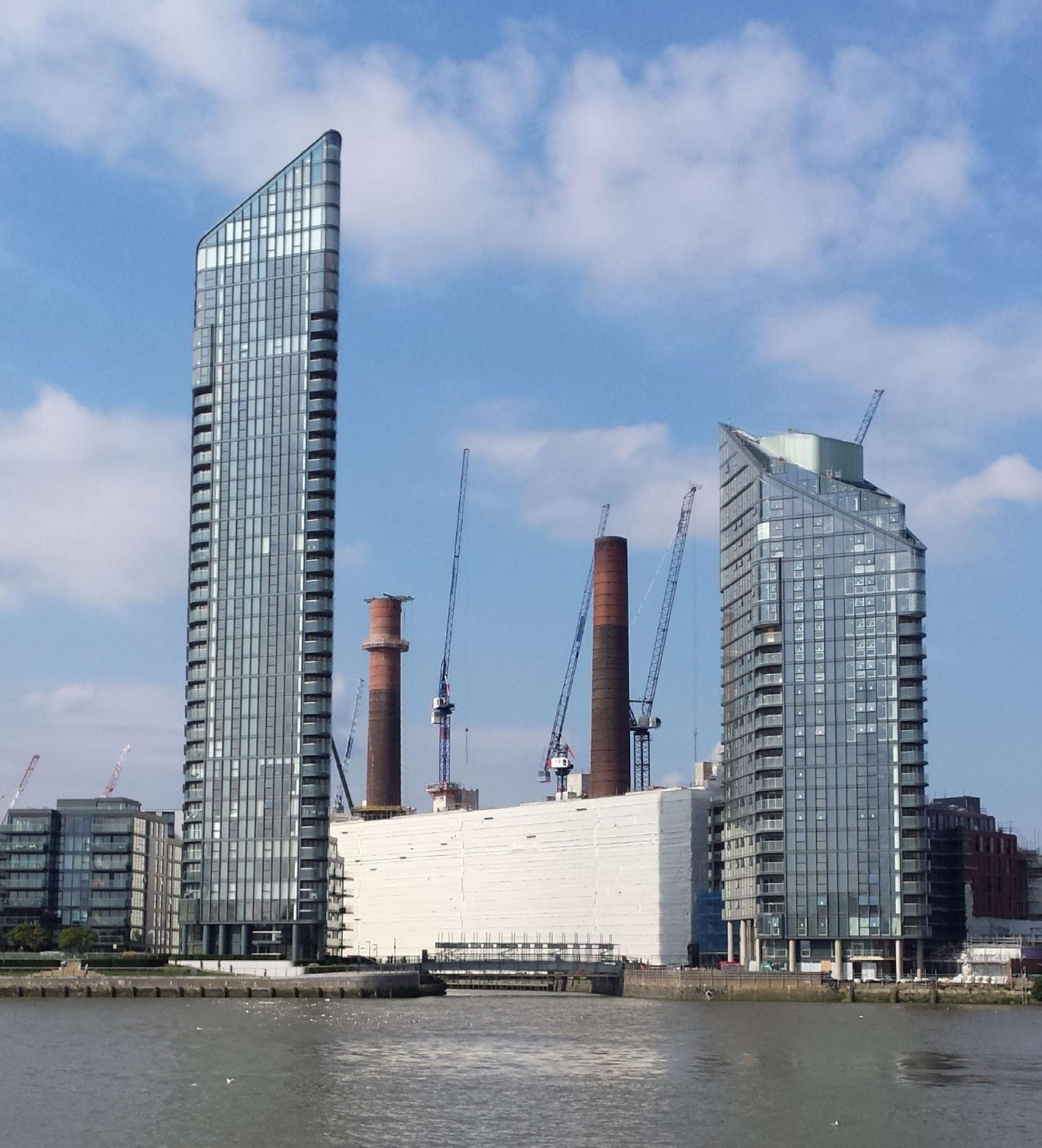
16 minute read
Schöck Isokorb
Schöck Isokorb meets a number of challenges at Lots Road
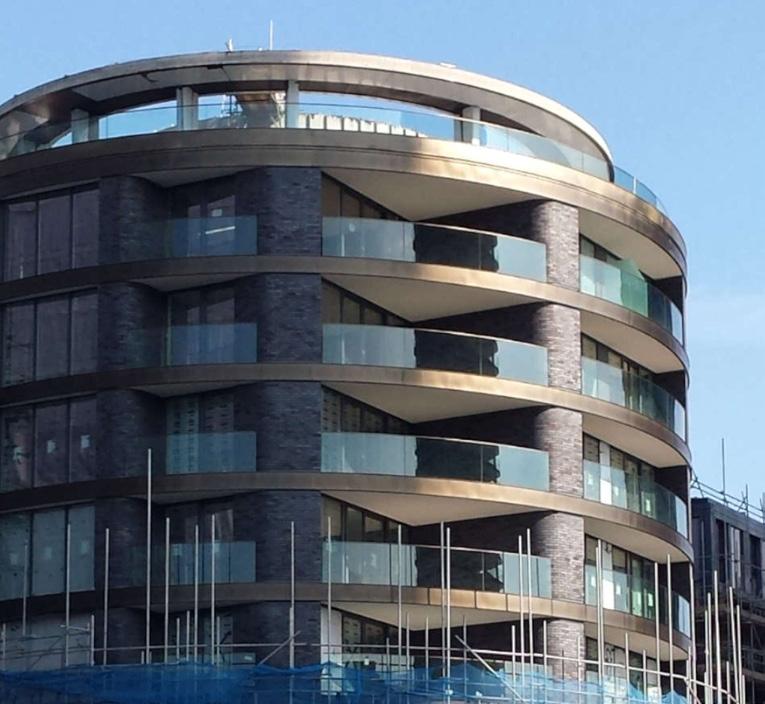
Advertisement

Once a neglected industrial site, Chelsea Waterfront in SW10, is being impressively transformed and minimising any risk of thermal bridging throughout has been key. In addition to meeting compliance with the Building Regulations, this is also important in meeting the criteria for the impending Future Homes Standard. The Isokorb load-bearing structural thermal break from Schöck offers the ideal solution in meeting all necessary compliances.
This is a two-phase development; the first being completed in 2019 and resulting in four riverside buildings and a 37-storey West Tower. The second phase is now well under way with the centrepiece being the old Lots Road Power Station, which first became operational in 1905 and eventually powered most of the London Underground for almost 80 years. The old Power Station is an iconic building and careful refurbishment will result in retention of the external walls, steel frame, chimneys and selected internal steelwork. When finished, the 13-storey building (now called the Metropolitan) will house 193 apartments and accommodate shops, restaurants and cafes along a 100 metre mall at ground floor level. Also, as part of this second phase, alongside the main Metropolitan Building there will be a 25 storey East Tower and two nine-storey refurbished residential buildings, one of which is a rotunda.
Minimising thermal bridging throughout
Throughout the entire development, improving the performance of the building envelope and minimising any risk of thermal bridging has been a key element in the design detailing. Quite apart from meeting compliance with the Building Regulations, this is increasingly important in meeting the criteria for the impending Future Homes Standard. Thermal bridges are localised areas of the building envelope, where the heat flow is usually increased in comparison with adjacent areas. As a result, the temperature of the interior surface near the thermal bridge is lower and if this area becomes too cold it can lead to condensation. Over time, mould is likely
to form, potentially damaging the building structure and even posing a health risk to the inhabitants. The ideal solution is the Isokorb load-bearing structural thermal break from Schöck, which has featured throughout since the start of the development. Primarily the requirement has been for conventional balcony detailing and involved the Isokorb T type K for concrete-to-concrete and the T type SK for concrete-to-steel. The SK is a complete system thermal break and is unique in being the only formally UK approved product that satisfies the loadbearing and thermal insulation requirements for this type of application. There were though a number of special demands as well.
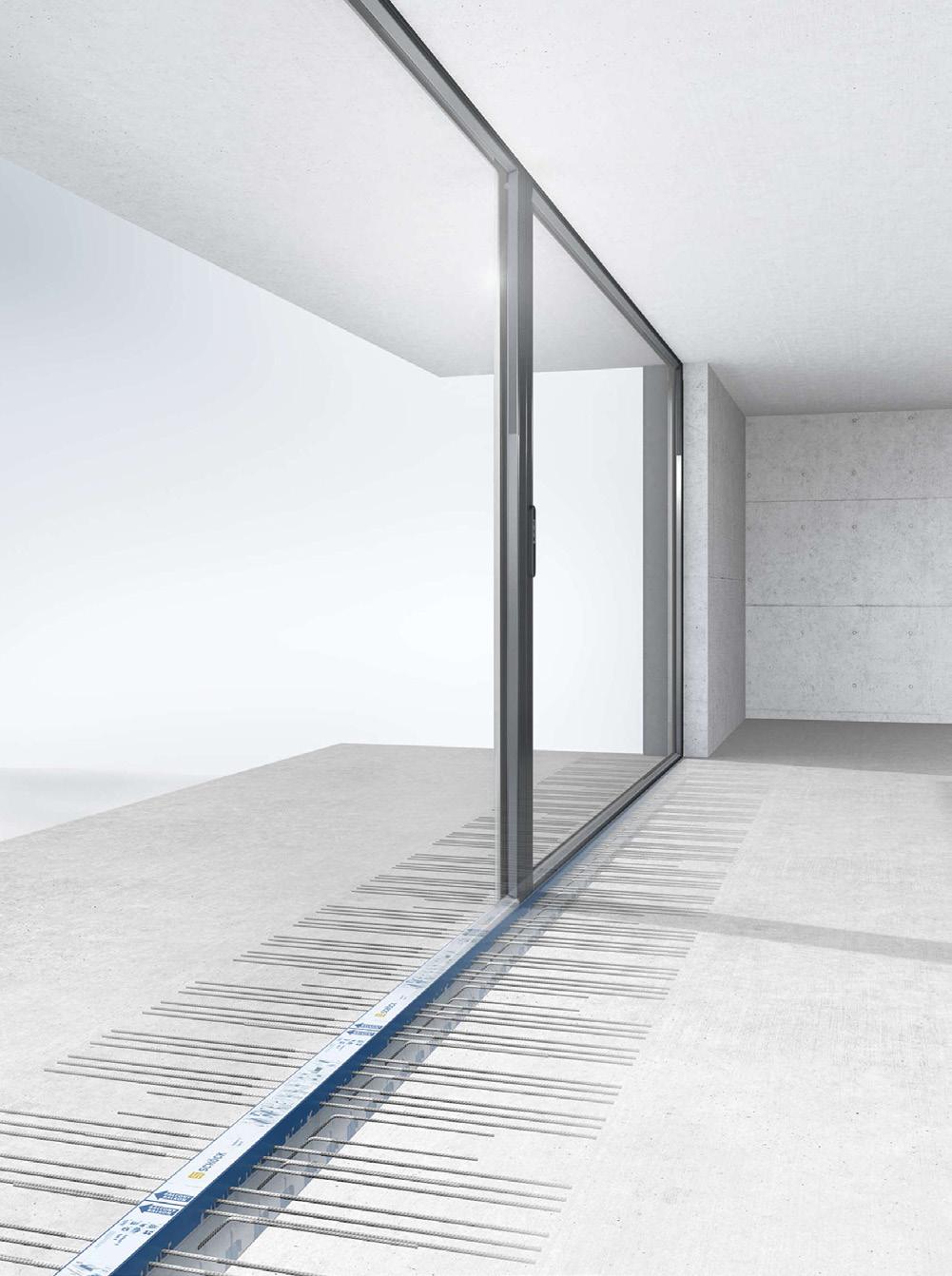
Meeting the challenges
The prominent corner plot on the site is an L-shaped building with a frontage on Lots Road and a wing extending towards the Creek. The interior features a continuous walkway and at the 90 degree intersection lateral forces had to be accommodated. To resolve the vertical and horizontal reactions a configuration was used that involved the Isokorb type HP (which transfers forces either parallel or perpendicular to the insulation layer) and type Q (for transferring shear forces on supported balconies and recessed balconies). In addition, there was also a slight castellation to the thermal break line, which had an impact on calculations involving the optimum cut lengths of the elements and their required load-carrying capacity. With the Rotunda, the contractor had opted to precast the ‘pie-shaped’ balconies where possible. However, for structural reasons, or because some were too large for precasting (one unit was so large it had to be split into two parts) it was necessary to cast insitu. This presented the Schöck team with load capacity considerations, as well as delivery scheduling challenges involving different sites. There was a major revision also involving the 13-storey Metropolitan Building. Isokorb units T type SQ, were to be incorporated at all levels to bolt the external steel walkways back to the concrete frame. However, there was a late design change to the project, which resulted in the steel walkways being converted to concrete on all but the first floor. This resulted in a complete review of the structural thermal break requirements and a tie force also had to be accommodated into the design to tie the balcony walkway structures back to the main structural frame.
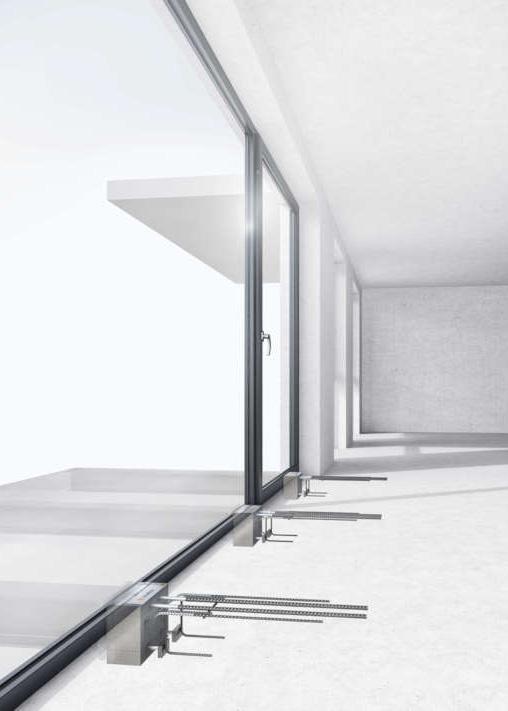
All products are fully compliant
The comprehensive Isokorb range offers solutions for concrete-to-steel, concrete-to-concrete, steel-tosteel and – and even a maintenance free alternative to wrapped parapets. Products meet full compliance with the relevant UK building regulations, have NHBC approval and offer LABC Registration. There is also the security of independent BBA Certification. The requirement that the temperature factor used to indicate condensation risk (fRSI) must be greater than, or equal to, 0.75 for residential buildings, is also easily met by incorporating the Isokorb.
Diagrammatic example of the T type SK
Contact Schöck on 01865 290 890; or visit the website at www.schoeck.com for full details of the Isokorb range
Moving with the Times….
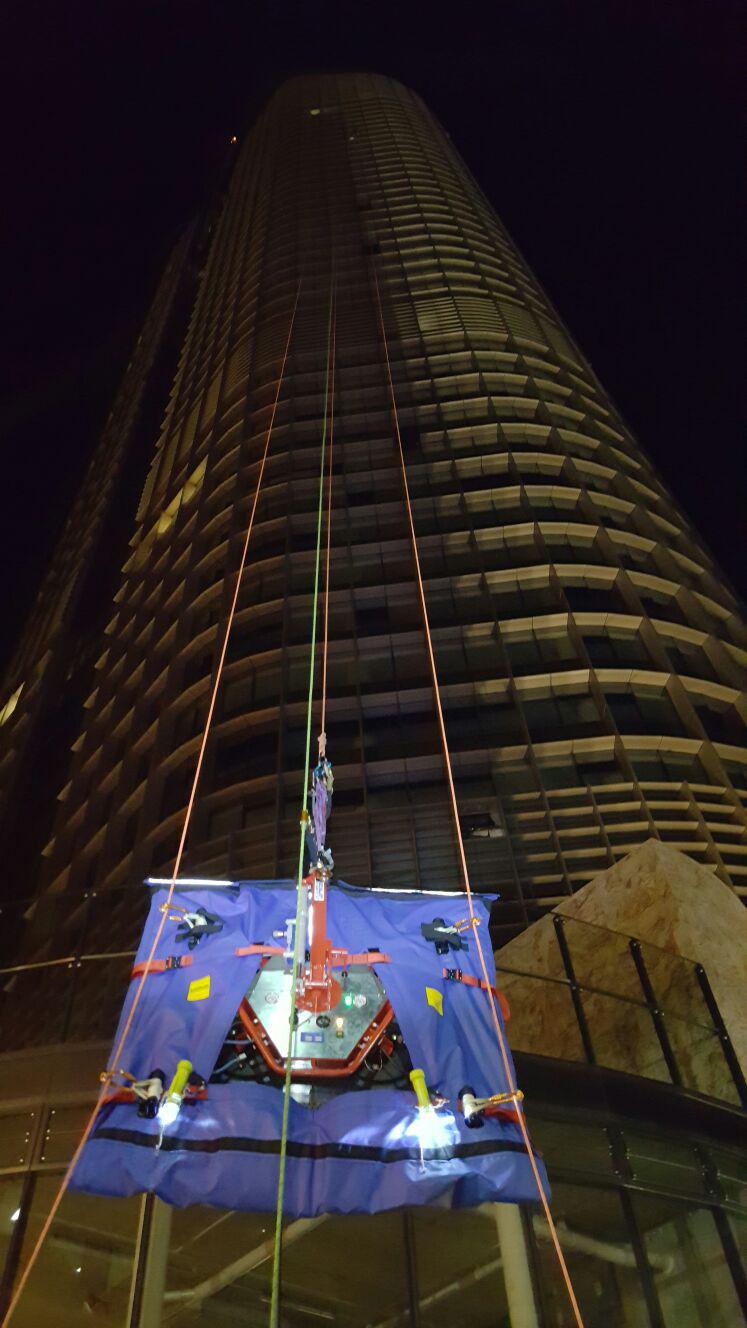
Industrial Lifting Bags are Evolving to Solve Lifting and Suspension Issues.
When glass panels needed to be replaced on a high building next to a busy road in Auckland, after a series of sucker failure incidents flagged a national pattern of events, PafBag was brought in to design and develop a comprehensive Secondary Safety Device (SSD) for this safety critical project. The brief was to not only catch a panel in the event of a primary sucker failure but also capture any shards of glass in the event of the panel shattering.
The bag was lined with cut resistant material and designed to allow easy installation to the face of the building. A fully rated lifting sling running through tunnels within the bag provided both integrity and confidence to the contractor, safety officials and client alike.
“This is an example of effective encapsulation – ensuring the load cannot fall out of the lifting system. And this philosophy drives our design and production methods to produce unique solutions and problem resolution”, says Richard Bartrop, Managing Director.
A simple, but equally important example of this concept was addressing the practise of tying winch ropes directly to the handles of tubs and buckets, with the inevitable result of handle failure and dropped contents. The Bucket Lifting PafBag and its EN1492-1 lifting sling provides safety critical integrity for the journey up to the deck, where the tub can be taken out and safely away. This method is a cheap solution as the one lifting bag at the winch can safely lift unlimited numbers of tubs.
Quite often, waterproof cases are used to deliver fragile tools, instruments or replacements to a high location. The PafSling cradle system is designed to convert that case into a lift-compliant load with a 100% guarantee of load security, even in a major tipping incident.
Pafbag has also provided a major service to the domestic solar panel installation industry in the UK by devising a solution that safely lifts multiple loads up a standard height domestic at the rate of one lift per minute. This bag can be opened out to lift loads up 2.4x1.2 metres.
PafBag is proud to be at the leading edge of this mini revolution of encapsulating goods ready to be lifted safely to height.
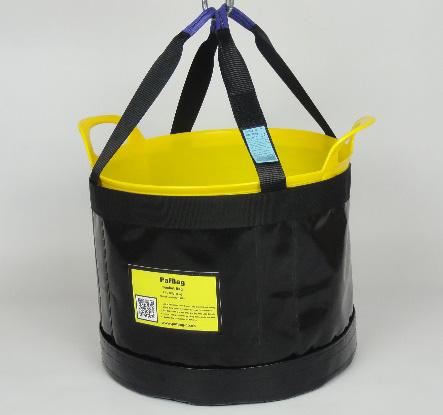
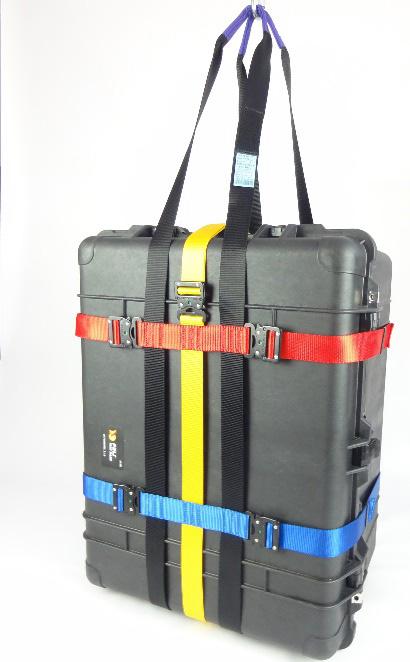
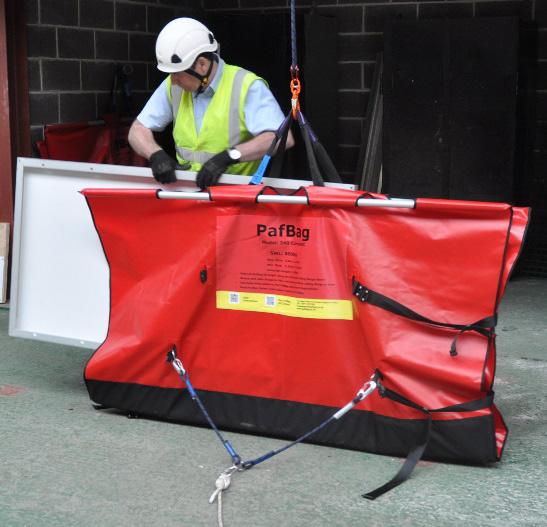
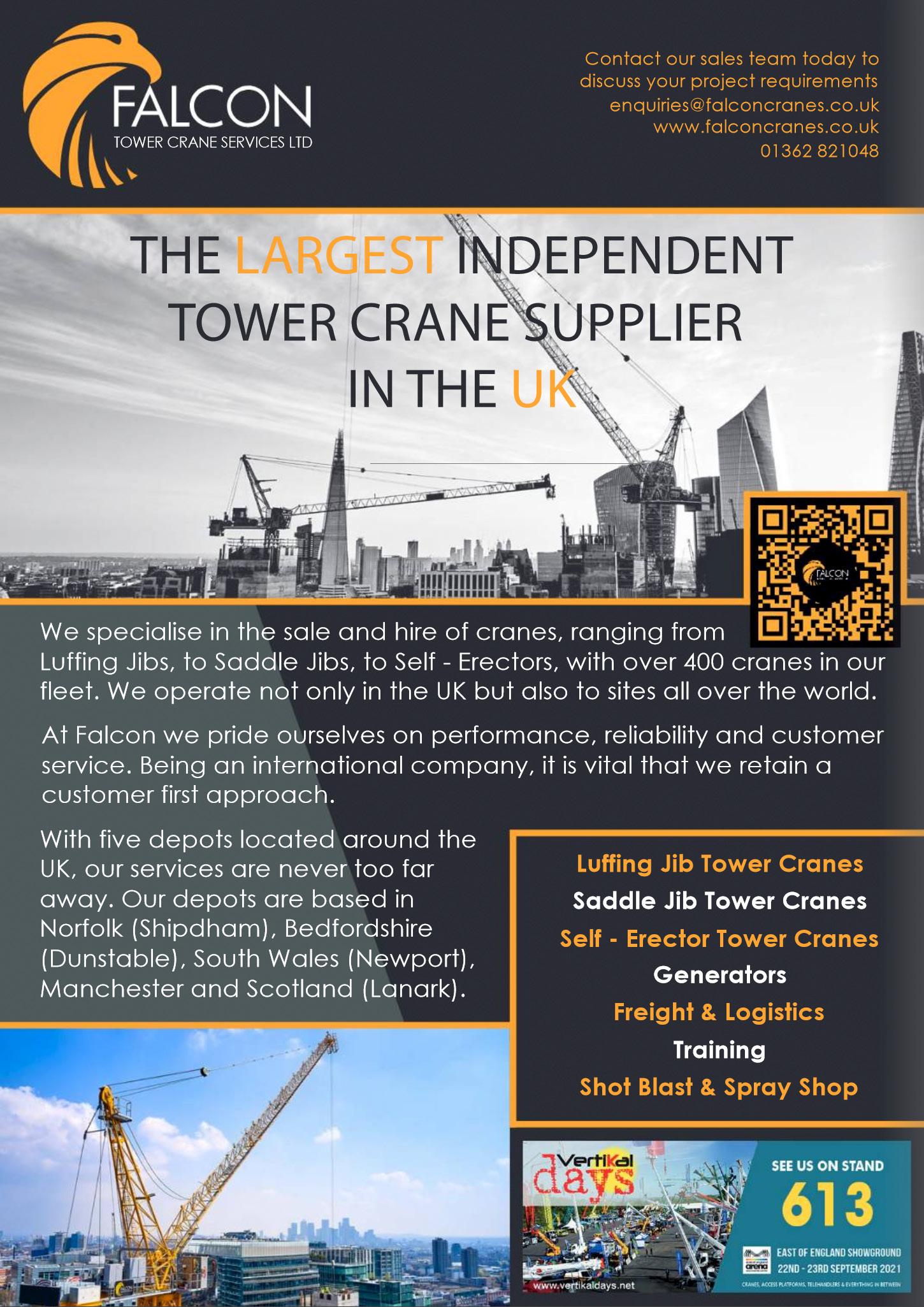
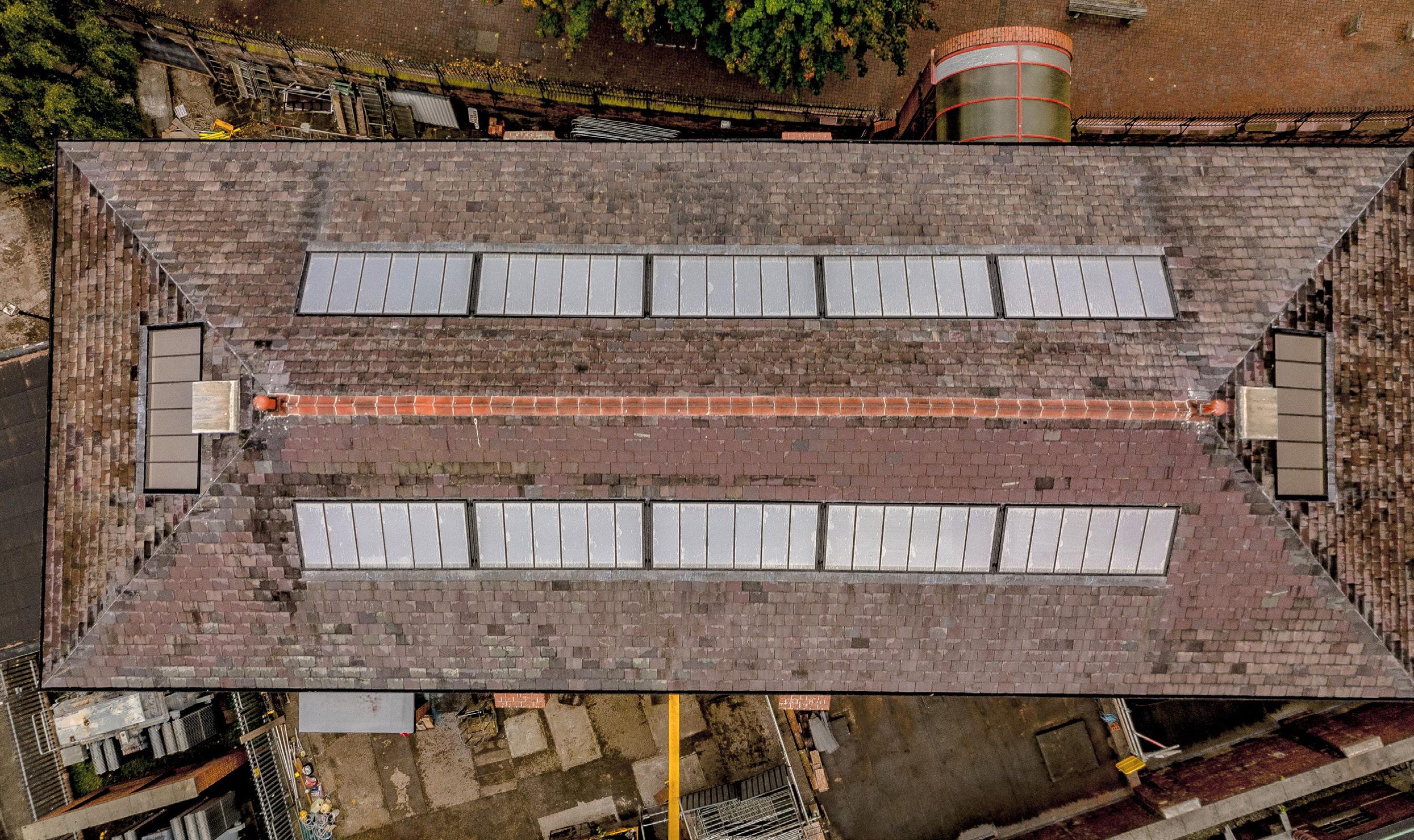
Stella Rooflights Breathe New Life into Historic Railway Pumping Station
Shore Road Pumping Station is a Grade 2 Listed building in Birkenhead on the Wirral peninsular, Merseyside. The threestorey Italianate style building was designed by engineers James Brunlees and Charles Douglas Fox and constructed in conjunction with the Mersey Railway in order to house steam pumping engines, which drew water from the rail tunnels.
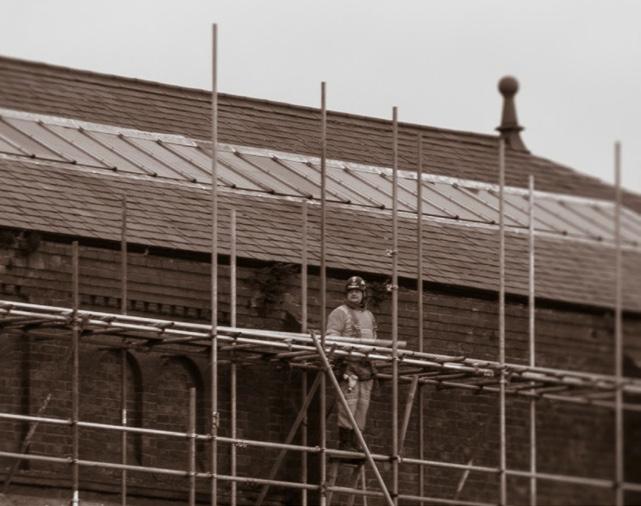
The building housed two ‘Grasshopper’ Beam Engines (manufactured by Andrew Barclay of Kilmarnock), which powered pumps designed to remove water from the railway tunnel under the River Mersey. These steam driven pumps have today been replaced by modern electric versions, however one of the original pumps, the ‘Giant Grasshopper’, remains in the building, although it is no longer operational. Up until 2014 the building served as a public museum, however today the building is closed to the public and maintained and operated by Network Rail. The property is primarily constructed from red brick and comprises six bays of blind arcading with engaged brick columns and round headed arches subdivided by brick buttresses to the longitudinal elevations and three bays to the gables elevations. Each elevation is supplemented by small round arched single glazed metal framed windows, decorative brick dentils / articulation and stone hood moulds / string courses. To the south-west gable end of the main building is a single storey duo pitched roof outshoot of similar style. The roof structure is of hipped construction covered with Welsh slate and clay ridge tiles, supplemented by ornamental finials at each apex. The internal roof structure is of timber queen post construction (a truss in which two posts are placed on a tie beam to support the principle rafters above, with the vertical posts held in place laterally by a collar beam). These roof trusses are in turn engaged into the external masonry walls. Shore Road Pumping Station is located within the Hamilton Square Conservation Area – an area designated in recognition of the architectural qualities and historic significance of the realised portion of the Grand Georgian Development. Network Rail is currently undertaking an extensive package of works to the Shore Road Pumping Station building to secure the building’s fabric in a historically appropriate and sensitive manner. As such, a programme of works were recently authorised for the refurbishment of the building, consisting of the replacement/ repair of various elements of damaged fabric.
As a major part of the refurbishment and preservation
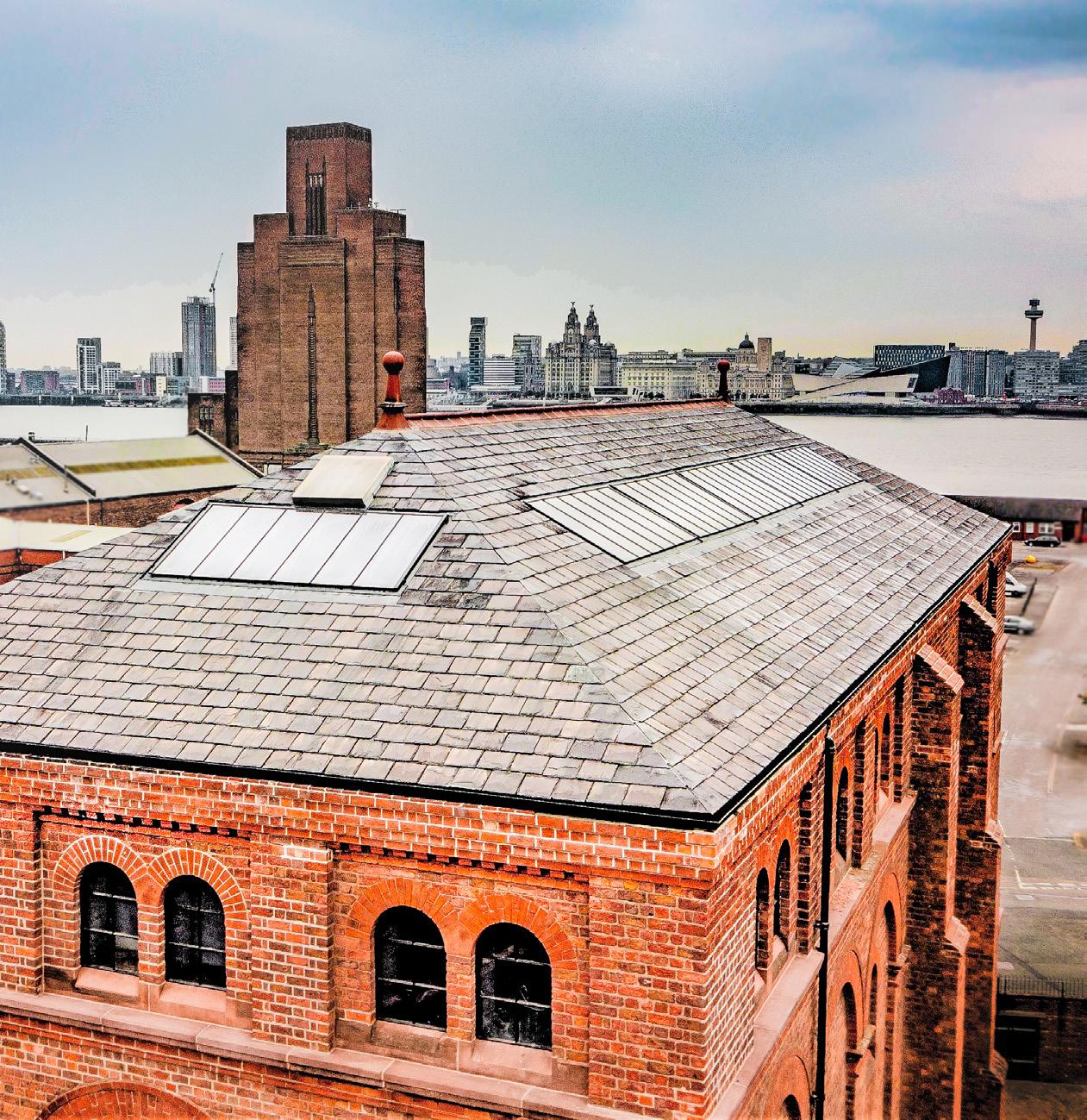
2 x Bespoke Stella Conservation Rooflights
• Manufactured From 316 Stainless Steel • Size 2842mm (w) x 1304mm (h) • Outer Frame in Single Section • 5 Glazing Bars / 6 Double Glazed Units • Fixed (Non-Opening) Design • Black Powder Coat Finish In C5 Application • American Ash Interior Liners
2 x Bespoke Stella Conservation Rooflight
• Manufactured From 316 Stainless Steel • Overall Rooflight Size 15,260mm (w) x 1304mm (h) • Outer Frame In 5 Sections / Linked
With 316 Stainless Capping • 5 Glazing Bars / 6 Double Glazed Units
Per Section (30 Panes Per Rooflight) • Fixed (Non-Opening) Design • Black Powder Coat Finish In C5 Application • American Ash Interior Liners
work, contractors MFG Construction appointed Stella Rooflight to design and manufacture the Conservation rooflights to replace the original skylights sited in the principle roof slopes of the buildings’ Welsh slate roof.
MFG commissioned Stella to produce four bespoke rooflights, of two sizes, the first two with a size of 15,260mm (w) x 1310mm (h) and the second pair at 2842mm (w) x 1304mm (h). Stella divided the large rooflight into five frames to ensure that framework was kept to a minimum and the amount of glazing maximised, while still providing manageable sizes. Each section consisted of five glazing bars and six glass units giving a total of 30 panes for each rooflight. The smaller rooflights were produced as single frames with a total of six glass units. Each pair of rooflights were linked together with a 316 stainless capping, giving the impression of two large individual rooflights, sitting adjacent to each other in the roof structure.
Due to the height of the building and the inaccessibility of the rooflights, regular cleaning was not going to be straightforward, therefore carbon or mild steel frames were not an option due to the problems that can occur with rusting if they are not regularly maintained. As all Stella rooflights are manufactured using a Marine Grade 316 stainless steel frame and finished with a C5 marine powder coating, they were the ideal choice for the project. Furthermore, the flush fit offered by the thin lines of steel and genuine glazing bars on each unit, would perfectly replicate the original Victorian design and satisfy the Planning and Conservation officers involved.
As the rooflights needed to be individually designed to exactly match the size of the originals, a set of complex, detailed drawings were created by Stella, each showing the full assembly of the linked frames as well as files for each individual component, based on the precise measurements provided. Due to the sheer size and weight of each rooflight, one of the major challenges for the MFG team was the positioning and installation of the rooflights, three storeys up in a building situated on a busy main road. To help overcome this challenge Stella allowed for four lifting eyes, which were welded to each individual frame during the manufacturing process, allowing the contractor to lift the frames into position with a crane. The entire design and manufacture process took a total of 8 weeks, despite facing the unprecedented challenges that the early stages of the Covid-19 crisis posed. Having the entire supplier, manufacturing and assembly process based in the UK, enabled Stella to overcome these challenges and ensure that the remaining refurbishment works were unaffected by any delay. For more information visit www.stellarooflight.co.uk or contact us on 01794 745445 or info@stellarooflight.co.uk
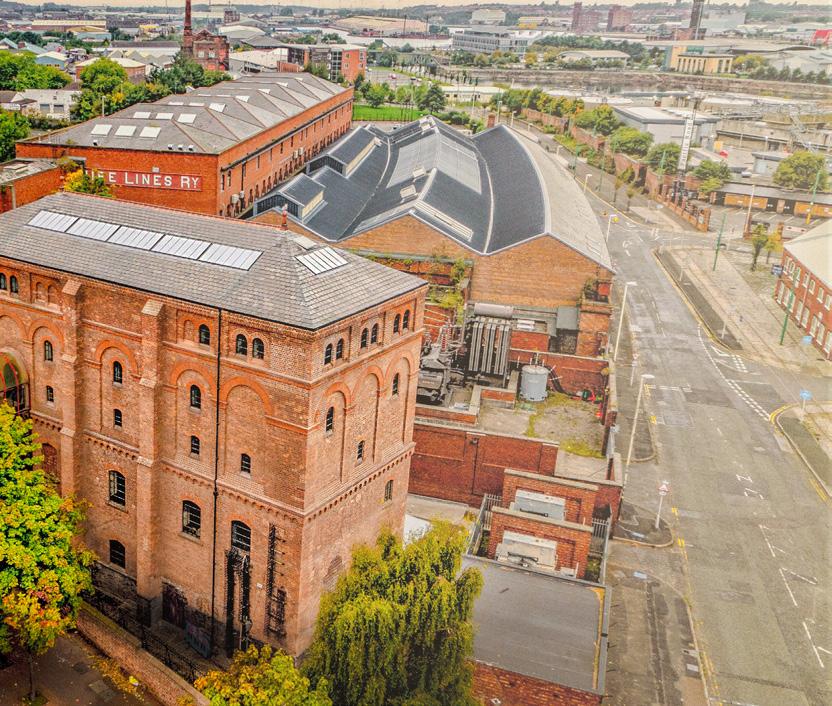
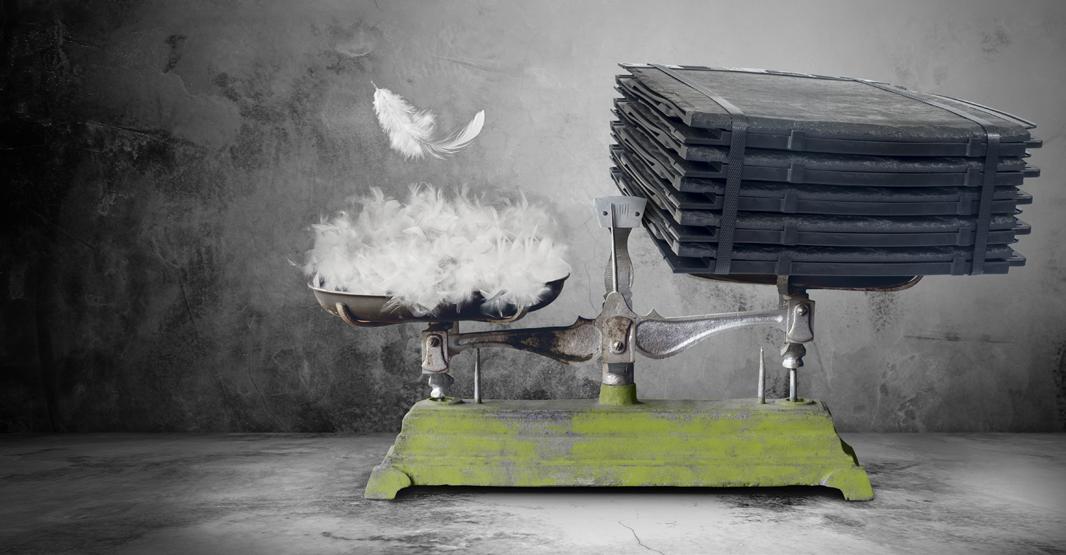
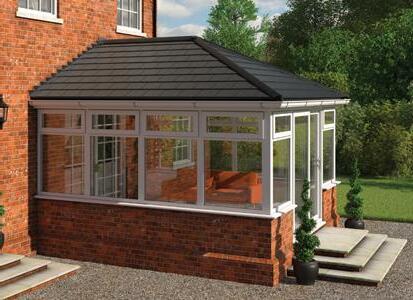
GIVE YOUR BACK A BREAK
Weighing in at just 20% the weight of a standard concrete tile, Envirotile is the lightest roof tile on the market. Made from 75% recycled materials, its light on your shoulders and not so
heavy on the environment.
GOOD FOR 40 YEARS. GUARANTEED.
We’re so confident in our product, we recently increased our guarantee from 25 years to 40. That’s good for you and good for the customer.
SAFE IN A STORM. GALE FORCE GUARANTEE.
Designed to withstand the worst of weathers, Envirotile is fully guaranteed to perform in severe UK wind loads and has been weather tested up to 147 miles per hour. We also offer a free replacement service for any tiles dislodged by gale force winds up to 65 mph. Peace of mind for you and the customer.
THE ANSWER TO DIFFICULT ROOMS & PROBLEM PITCHES
Performing on pitches as low as 12.5 degrees and good for all roof types, Envirotile is perfect whatever the job. So whether it’s a main frame roof or a lightweight conservatory, Envirotile’s easy lock together system will get the job done.
MINIMAL MAINTENANCE
Enjoy the look you want with minimal maintenance. The ground breaking anti-fungal properties of our product mean it repels moulds and funghi that accumulate over time, reducing your maintenance in years to come.
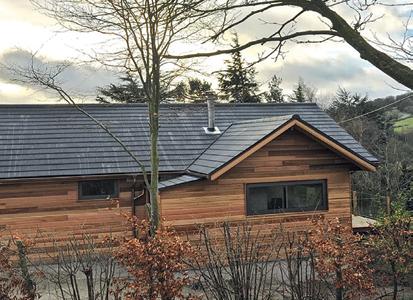
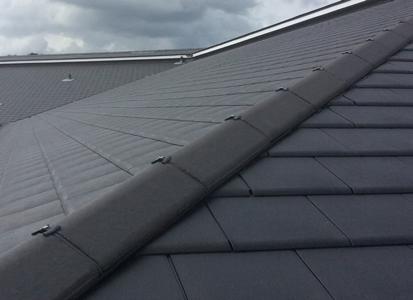
Snickers Workwear and EMMA Safety Footwear Lead the Way with Sustainable Practice.
These forward-thinking brands are pioneering sustainable business practices in their industries.
Did you know that bridging the ‘The Circularity Gap’ by embracing the circular economy could shrink global greenhouse gas emissions by 39%!* That’s why Emma Safety footwear has become a leader in sustainability having created the world’s very first ‘100% Circular’ safety footwear range.
While Snickers Workwear is at the forefront of sustainability in the workwear industry by sourcing the highest quality, most hardwearing products with as little environmental impact as possible. Ensuring garments are made from ‘preferred fibres’, enhances durability and comfort to create hard-wearing workwear with a long product lifetime which is key to reducing waste.
The combined result is environmentally-friendly, ergonomically designed dual-purpose working clothes and footwear that are not only designed to meet the physical demands that tradesmen and women face at work but are also ideal for some sports and leisure activities – and reducing your carbon footprint too!
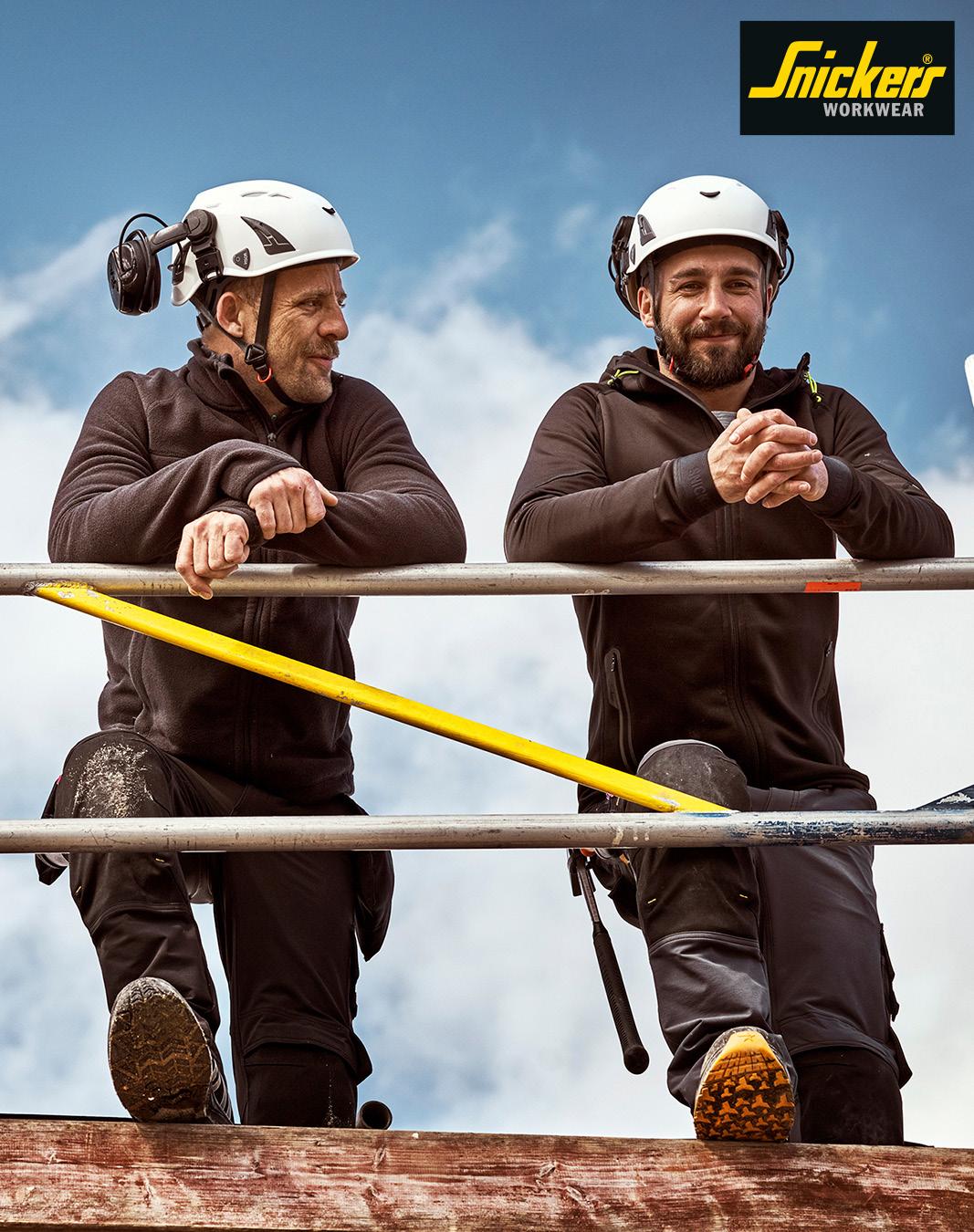
Getting more information on the Snickers Workwear clothing range is easy. You can call the Helpline on 01484 854788; check out www.snickersworkwear.co.uk and download a digital catalogue or email sales@hultaforsgroup.co.uk
RSS Names Tony Teeder Director
Rope and Sling Specialists Ltd. (RSS) has named Tony Teeder a company director.
Teeder, who is currently regional manager— midlands, London, and the south, joined RSS in the spring of 2016 from a major equipment rental company that was part of the GAP Group. A decade in the lifting and materials sector prior to that also included roles at Speedy and other equipment-focussed businesses. At the time, he oversaw the newly opened Hayes depot, near Heathrow Airport, west of the UK’s capital. It was the company’s then fifth facility and its second in the south of England, where it also has a presence in Aylesford, Kent. Teeder stepped into a wider, regional role following the tragic passing of Tim Panter in 2018. Today, Tony Mills runs operations in Heathrow, reporting directly to Teeder. Including its Gemmak Engineering business, based on the same industrial site as de facto headquarters in Pyle, South Wales, RSS has eight national facilities, the most recent of which to open is in Roborough, Plymouth. Teeder said: “Actually, me and Steve have talked about this for some time now and with the contract gains we continue to make, we feel that the timing is right. The promotion will enable me to get into the hierarchy of the major projects and companies to demonstrate exactly what we can do, and offer as a business, while still overseeing London and the south as a region. Between my teams and depots in London, we have managed to expand in terms of customers and employees in both locations. We have continued on a gazelle growth curve even mid-pandemic.”
At your service
Teeder attributes this success to the company’s ongoing ability to manage customer relationships and deliver world-class service. Its radio-frequency identification (RFID) online-based tagging reporting system has been popular too, he said. It means that RSS most commonly provides a complete package to major infrastructure and other projects—Thames Tideway and HS2 standout—built on hire equipment and equipment service. Steve Hutin, managing director at RSS, said: “Tony’s performance and commitment has been exemplary over the last five years, and he has taken our business in London to
Tony Teeder (left) is welcomed to the Rope and Sling Specialists boardroom by Steve Hutin, managing director.
another level. He takes responsibility and full accountability, which gives him the DNA that is consistent with our other directors. We’re now looking to Tony to continue to build on what he has achieved in London in the midlands and develop relationships further with major project decision makers.” Teeder added: “Business is thriving at present, and it will continue to grow in various sectors, not just here in London, but across the UK. It’s true that, as a company grows and commands the respect of higher profile buying decision makers, that business must become more corporate. Of course, though, we must remain true to our roots and the values that have made us the first-choice supplier to so many people.” Teeder joined Hutin; Alan Varney, operations director; Angela Holmes, financial director; Sean Maslen, sales director; and Matthew Rogers, engineering services director, in the boardroom.
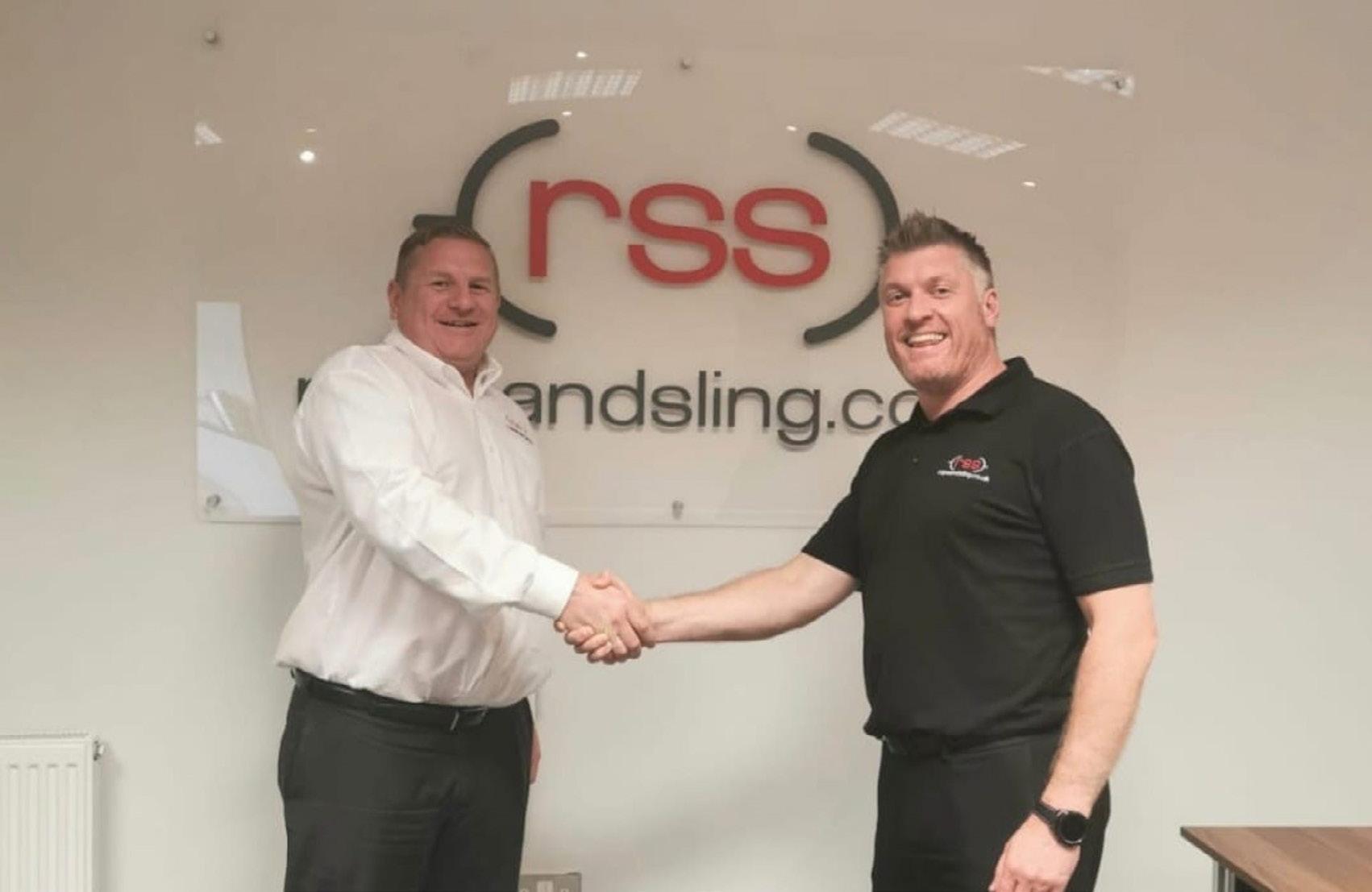