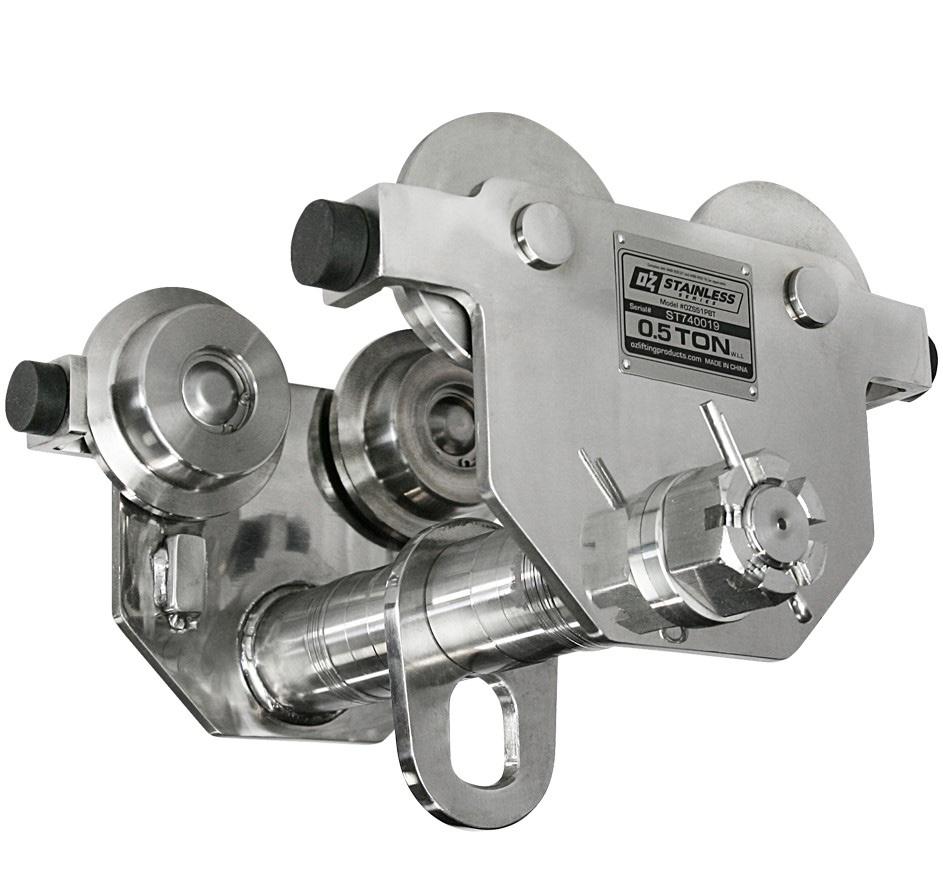
37 minute read
OZ Lifting 40 Profab Access
OZ Lifting Expands Stainless Steel Range
OZ Lifting Products LLC has added to its ever-growing stainless steel range with a 0.5-ton capacity manual chain hoist and trolley.
Advertisement
LEFT: OZ Lifting’s new 0.5-ton capacity stainless steel manual chain hoist. RIGHT: OZ Lifting’s new 0.5-ton capacity stainless steel trolley.
The Winona, Minnesota-based manufacturer already has 1-ton and 2-ton versions of both products, in addition to beam clamps in the same capacities, all of which are made from stainless steel.
The manual hoist is the centerpiece of the stainless-steel range. Like other products in the line, the 0.5ton version is designed for lifting and pulling. The hoist is lightweight and minimal effort is required to lift loads, but it is durable enough for some of the most demanding marketplaces. The trolley, meanwhile, fits most common I-, S- and W-beams; end users have different types of beams depending on the construction requirements of the building or structure where the lifting equipment will be installed and employed. Steve Napieralski, president at OZ Lifting, said: “We’ve had increasing demand for lower capacity products, so I’m pleased to offer 0.5-ton versions of both the manual chain hoist and trolley. As always, we will continue to listen to our dealers and end users, and I wouldn’t be surprised if 0.25ton, 3-ton and even 5-ton versions are put to market in the future.” The 3-ton and 5-ton capacity stainless steel hoist and trolley are already available as a special order. There is no specific application for this kind of manual hoist and trolley, beyond the fact that stainless steel is used in corrosive environments, including wastewater treatment plants, saltwater, or wash-down applications. Napieralski pointed out other key features of both products. Minimum headroom for the chain hoist is 14.8 in. with a head weight of only 16 lbs., offering 1.5 lbs. per ft. of lift. Standard heights of lift are 10 ft., 15 ft., 20 ft., and 30 ft., although custom lengths are available upon request. Regardless, all products are rigged in the USA. The trolley, meanwhile, weighs 19 lbs. and fits on a 2.6 in. flange width. The products require a similar maintenance program as their steel counterparts, Napieralski explained. He also stressed the importance of adhering to maintenance and inspection programs, especially if the equipment is being operated in a highly corrosive environment. OZ Lifting outlines these requirements in an owner’s manual, included with every shipment, along with test certification. As the documentation states, the product meets a range of standards, including the American Society of Mechanical Engineers (ASME).
Both the 0.5-ton capacity manual chain hoist and trolley are in stock and ready to ship.
Lifting Products to Manufacture GIS Crane Systems in the UK
UK-based Lifting Products Limited will provide a full line of slewing jib cranes, light crane systems, and crane track from Swiss manufacturer GIS AG.
Lifting Products will receive jib crane and other parts from Schötz, Lucerne, but will manufacture the range for the first time in the UK. GIS-owned Lift Turn Move (LTM), meanwhile, a supplier of lifting and rigging equipment to the industrial and entertainment event markets, will continue to be the UK supplier of its electric chain hoists, control systems, and additional material handling equipment.
James Porter, formerly of LTM, and managing director at Lifting Products, had earmarked the
UK as a potential hotbed for the full range of GIS products, but cited transportation costs as a barrier to entry for heavier equipment. However, the company has invested in infrastructure, primarily to facilitate onboarding of the GIS range of profiles and components for the jib crane and GISKB ranges. Over- and under-braced jib cranes will be offered from 125kg capacity at 2,000mm reach to 1,000kg capacity at 5,000mm reach. Customisations will be available upon request.
The company’s first jib crane build was for installation at the Holywell, Flintshire facility for handling steel sheets from the rack to load a plasma cutter. The new computer numerical control (CNC) cutter allows
Lifting Products to profile its own, 40mm-thick steel plate—double the thickness of jib crane base plates.
Subsequently, welding jigs were installed for repeat assembly processes. Manual and CNC lathes, a press brake, milling machine, and water-cooled welder are among other new tools that complete a state-of-the-art machine shop suite.
Porter said: “The combination of Swiss-designed products, that have been in use in some of highest specification manufacturing plants for over 30 years, combined with
UK manufacturing, provides a solid base to support our customers with. While these are new products for the UK market, they have been tried and tested for many years, and we can call on that knowhow to provide a comprehensive offering to the UK domestic market.”
Lifting Products partnerships
Erich Widmer, sales and marketing manager / deputy managing director, at GIS, said: “with or UK subsidiary LTM and their long-standing focus on the supply of GIS electric chain hoists and travel trolleys we have a solid base in the UK already, but Lifting Products can now support that existing offering, aided by the infrastructure to stock, cut, weld and paint. It’s well known that the two companies work closely together and LTM will supply the GIS hoists to go with Lifting Products’ crane systems. The collaboration strengthens the GIS brand in the UK; customers benefit from being able to buy GIS-designed jib cranes and lightweight track systems, in addition to GIS electric chain hoists and trolleys.” David King, managing director at LTM, added: “This is a win-win situation all-round, for GIS, LTM, Lifting Products and, most importantly, the customer and end user community. We have had great success providing [GIS] chain hoists to the UK market and, three years after GIS acquisition [of LTM], the partnership with our colleagues at Lifting Products continues its legacy here in the UK.” Lifting Products has, since inauguration in 2016, based its growth on high-profile partnerships. It initially serviced the UK and Irish market with Haacon equipment, focussing on off-the-shelf and bespoke winching, jacking, and handling equipment
Lifting Products Limited will provide a full line of slewing jib cranes, light crane systems, and crane track.
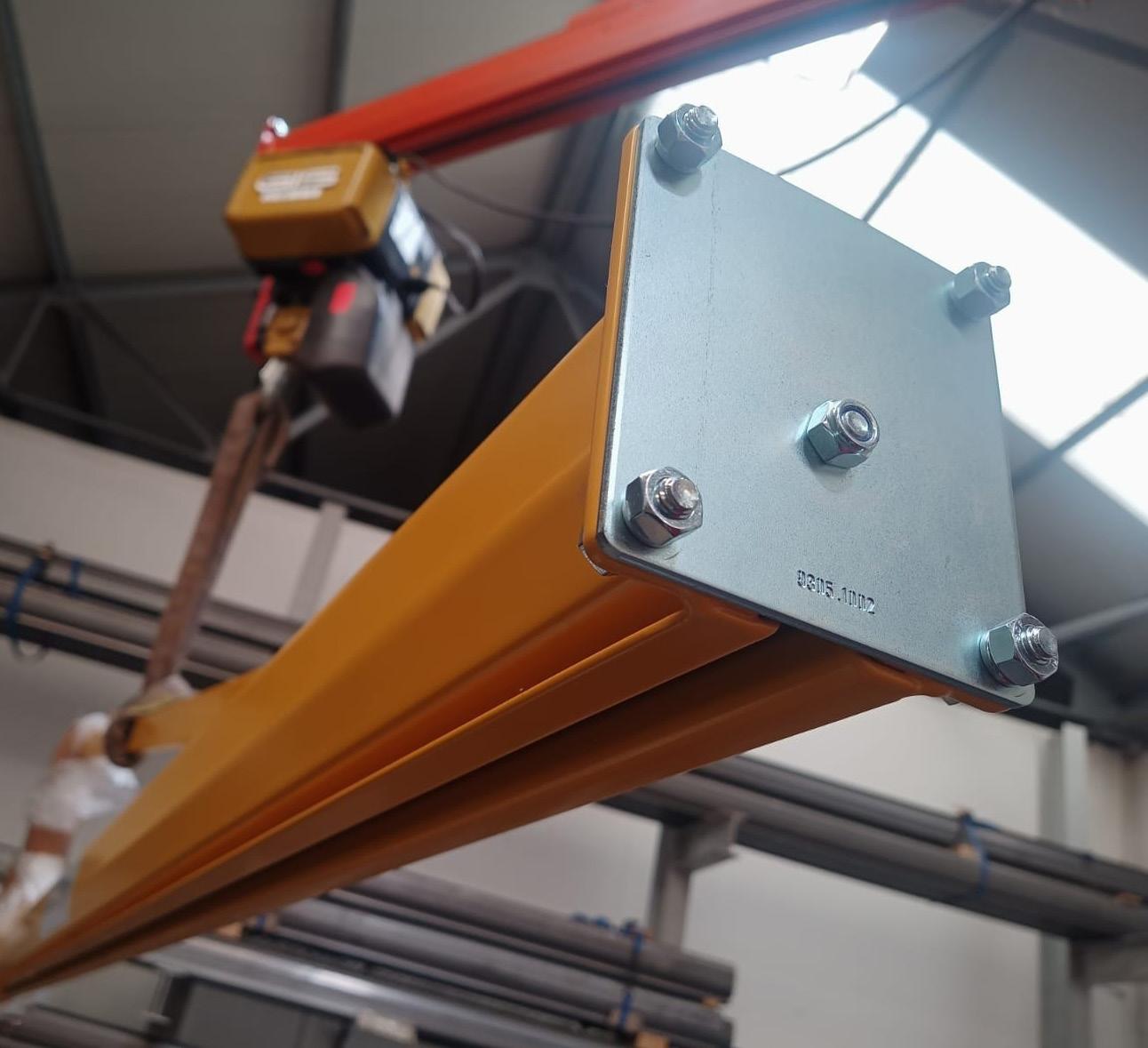
for water treatment, nuclear, offshore, waste, and other specialist markets. This expanded to Haacon’s container lifting and levelling systems, principally in the military sector. Lifting Products is also agent for Koester winches and Wittler safety brakes and cranks, common in agricultural machine making. Porter said: “We are already stocking GIS parts and can react quickly to customer demands, which will likely come from automotive, aircraft, utilities, construction, rail, and manufacturing. There is a standard range, but almost every jib crane built so far has some custom work involved. The track systems are standard parts but, again, they need to be machined to exact customer specifications. We have manufactured over 30 jib cranes in the last four months and supplied several lightweight crane systems, which, prior to our official [GIS] launch, gives me great confidence.” Porter joined LTM in 2008, before setting up Lifting Products in 2016 but his relationship with GIS goes back further to employment with Chester Chain, where he used to service and install the Swiss-manufactured electric chain hoists.
With around 120 employees, GIS AG of Switzerland is a well-known manufacturer of complete crane systems including hoists and vacuum lifters. The company has been developing and producing electric chain hoists for more than 55 years. Over the decades, numerous special versions have been realised to meet the needs of a wide range of market segments. With the current electric chain hoist models GP for industrial applications and LP for the entertainment industry, GIS has taken a pioneering role in the highly competitive market of lifting and handling technology. GIS hoists and crane systems are in use by the hundreds of thousands worldwide - stationary or mobile - indoors or outdoors.
lifting-products.com
Breaking down construction data silos with the click of a button
Novade, Asia’s leading field management software developer, today announced an integration with Autodesk Construction Cloud™, a portfolio of software and services that combines advanced technology, a builders network, and predictive insights for construction teams. The integration breaks down data silos between office and field teams on construction projects, seamlessly connecting information across Novade and BIM 360, a construction management software in Autodesk Construction Cloud. Making the announcement today, Denis Branthonne, CEO of Novade said, “This exciting integration between Novade and Autodesk Construction Cloud is the start of our journey to deepen relationships with technology partners built towards truly connected construction.” “Tech companies have to move with the times – our customers want their data to move seamlessly between their favourite systems and applications. The more we can help the construction industry remove data friction, the faster the industry will achieve digital transformation,” he said Novade digitises construction processes in the field such as safety inspections, permits to work, quality inspections or progress reports. Autodesk BIM 360® is widely adopted by construction teams across the globe looking to collaborate throughout all project stages – from design and construction through operations and maintenance. Both tools are trusted by many of the world’s largest contractors, property developers and facility operators – particularly across Europe and Asia.
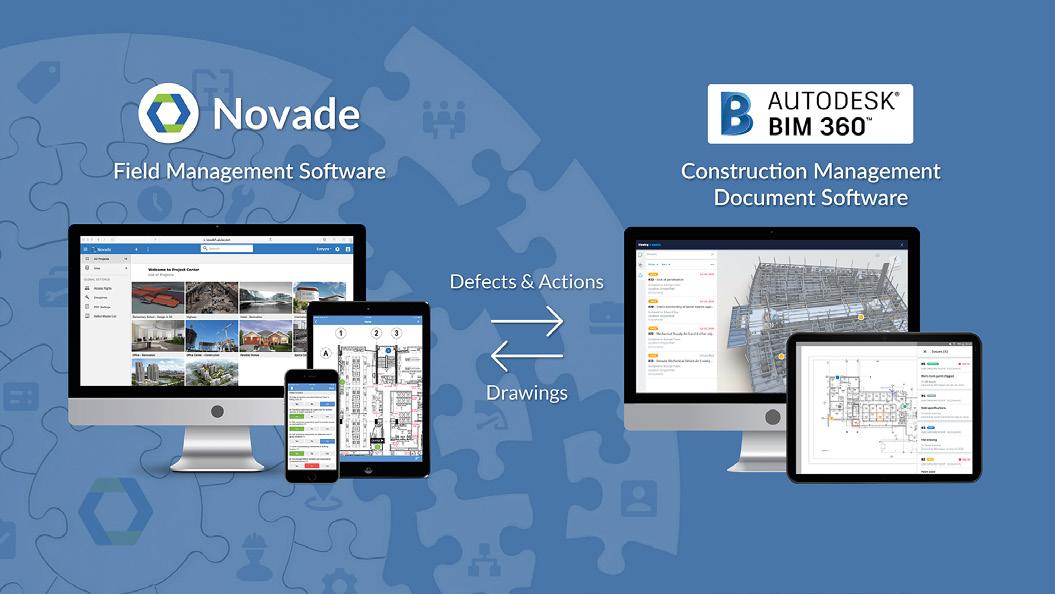
Novade announces integration with Autodesk Construction Cloud to connect office and field teams
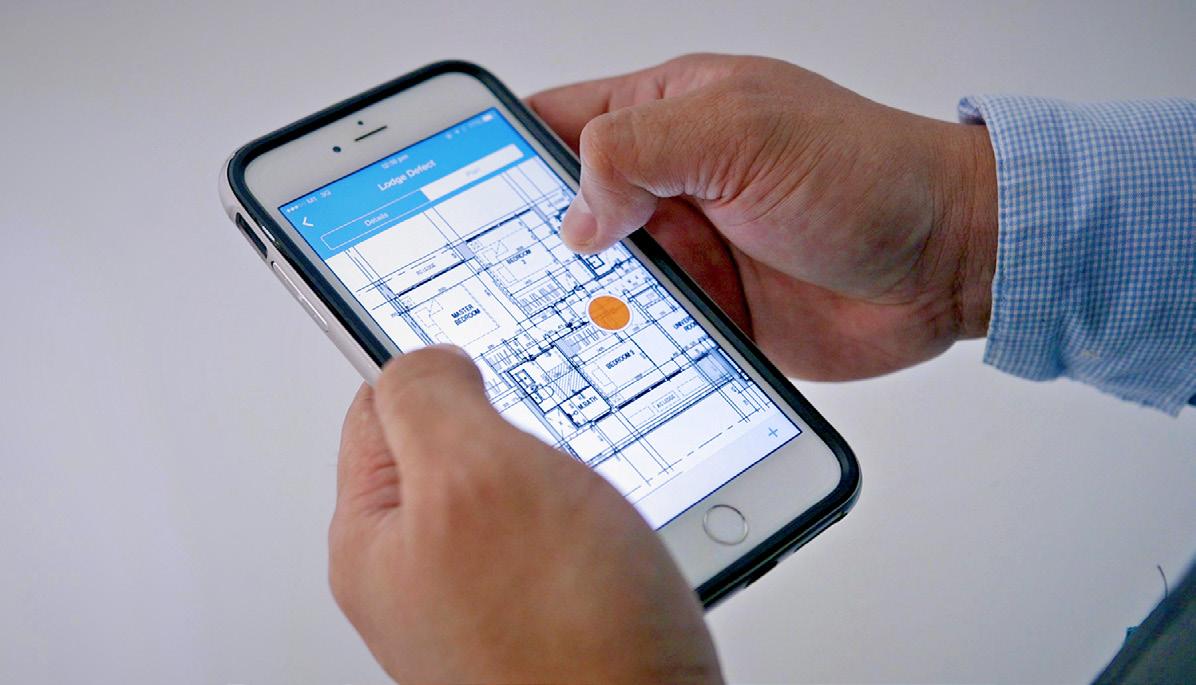
By connecting the Autodesk and Novade platforms, users can now share their safety and quality data from the field in Novade with other construction stakeholders in BIM 360. Novade users can also incorporate the latest drawings from BIM 360 within their field-based workflows and minimise rework headaches resulting from field teams using the wrong drawing. “Construction projects move quickly, so office and field teams need to remain in sync to ensure everyone is working from the latest information,” said James Cook, head of integrations at Autodesk Construction Solutions. “By enabling customers to connect their project data and documents between BIM 360’s construction management workflows and Novade’s field workflows, office and field teams can streamline collaboration to minimise miscommunications and rework.” Tiong Seng, one of Singapore’s largest building and civil contractors, is one of the early adopters of this new integration. Colin Tan, Deputy Managing Director of Tiong Seng Contractors Pte Ltd said, “Being able to share information between our existing data platforms is essential for us to reduce bottlenecks in our industry. Our teams now have full project and progress visibility whether they are on or offsite with access to real-time quality and safety data.” To make it easy for construction companies to streamline the enormous amounts of data they collect and manage, tech companies are looking at ways to synchronise, share and unlock their data. To address this, Novade recently launched a set of software integrations with Novade Connect, providing plug and play connectors with some of the world’s most trusted names in the industry.
Ballcock & Bits Dual-Brand Their Store With The IPG
Ballcock & Bits in Bracknell, Berkshire has become one of the latest IPG members to dual brand their store.
The IPG team are continuing their work to become a recognised brand amongst ALL plumbers, installers and DIY’ers. Their brand message is loud and clear, not only can you buy the best brands locally at great prices, the service you receive in an IPG member store is second to none.
When asked what his motivation was to become dual branded, Jay Lovejoy, Showroom Manager at Ballcock and Bits said: “Creating that sense of Identity across all IPG stores is important, we wanted to be at the forefront of this movement.” Jay was also asked if his customers understand who The IPG are and how that benefits them. He responded as follows: “When our customers see our IPG branding, they’re curious to find out what The IPG are and why we’re a member. Once we explain the concept and how it can benefit them as the customer i.e., competitive prices for the leading brands, they often put us to the test. We win business every time.” Jay went on to say: “We hope to continue to grow with The IPG and become more invested in the marketing side of things. It’s a company with great vision and we want to be a part of it.” Strong outdoor signs help you captivate potential customers’ attention as they travel down the street. Highly visible fascia’s make a big impact and can turn passers-by into a new customer. Ballcock & Bits signage is certainly very eye-catching.
For further information, contact Nike Lovell on 07954 302884 or visit www.the-ipg.co.uk
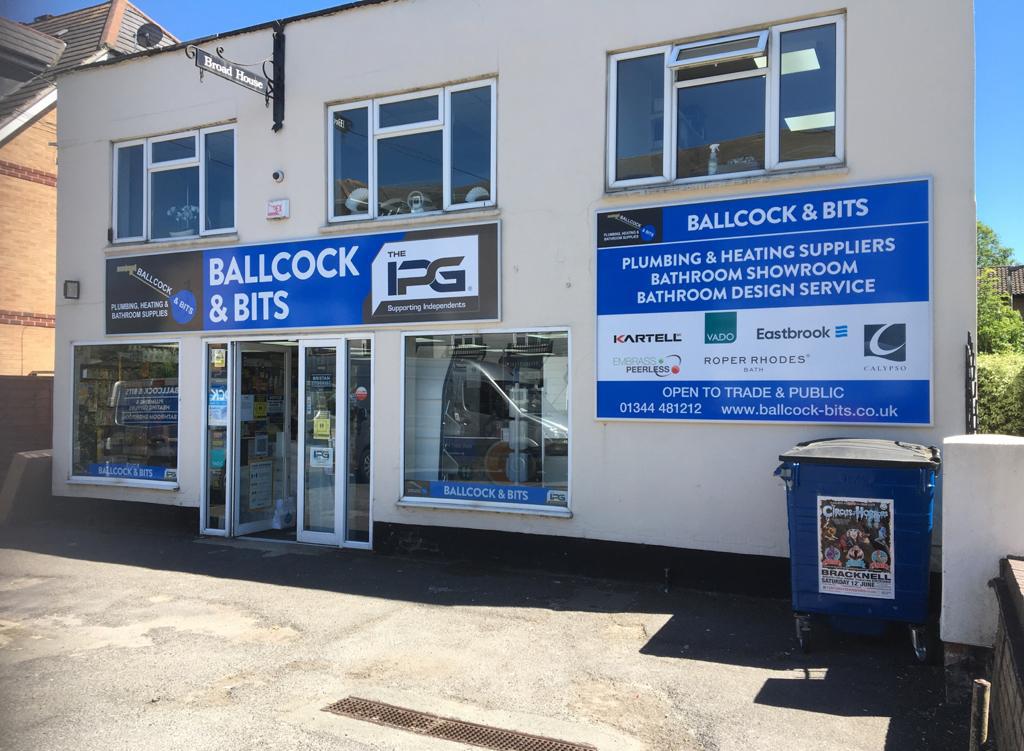
Copper as a force for good:

The population of the is UK ever-expanding and shows no sign of slowing down. The increase that occurs year after year has put pressure on the government to build more housing, even cheaper and quicker than in previous generations. As a result, despite copper being the professional choice, many construction firms and plumbers now disregard copper as a material, looking to cheaper and poorer alternatives such as plastic.
However, sustainability is coming to the forefront of the government’s strategies, having adopted the UN’s 2030 Agenda for Sustainable
Development and addressing social pressures as a result of the effects of global warming. With this in mind, copper is perfectly positioned to help meet new challenges set by the government to the construction industry which aims to improve the sustainability of the industry as a whole.
Copper as a sustainable material
Copper has a major advantage in its recyclability - it can be recycled again and again without losing any of its properties, performance, or value. Plastic, on the other hand, is made up of synthetic materials and polymers, making the recycling process considerably more complicated than that of copper. As a result, plastics manufacturers are still attempting to work out how to separate and re-use the components of plastics, any claims that plastic pipes are fully recyclable is simply an example of greenwashing. Where copper is concerned, this is not an issue as there is already an established scrap collecting infrastructure in place that has been around for centuries. Copper from redundant pipework, electrics and various structures is acquired to be melted, recast and repurposed, it is thought that two-thirds of copper produced
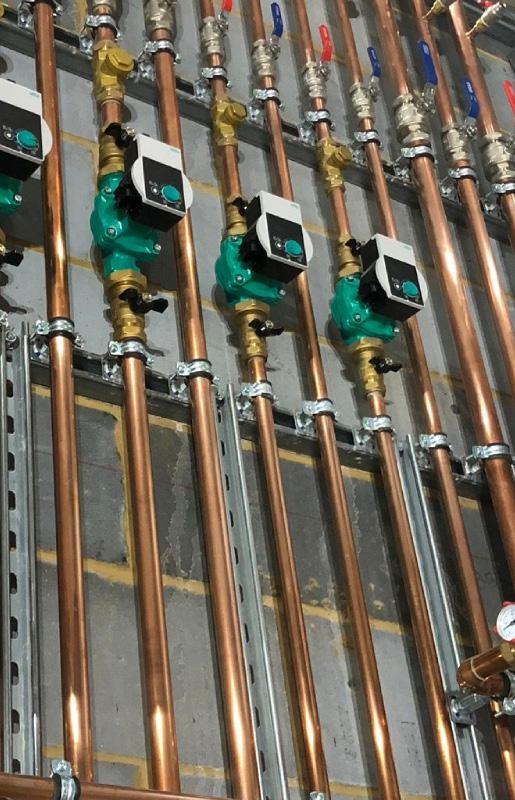
since 1900 – more than 350 million tonnes – is still in productive use today as a result of its proven recyclability. Recycled copper also accounts for 30% of global demand, and this statistic is only going to increase with the improvement of recycling technologies.
How is copper used in the plumbing and construction industries?
One of the first industries you think of in regard to copper tubing is plumbing. Copper is the professional choice and is the most dependable and most commonly used material in the plumbing industry in the developed world. As well as it being infinitely recyclable, there are other attributes it has that makes it an ideal material for this industry. These include: • It is highly corrosion resistant, which is important in plumbing as many tubes find themselves underground in potentially corrosive environments
• It has superior strength and can withstand the stresses of freezing and thawing in the winter months, unlike plastic which is prone to cracks, ruptures, and leaks • It can be exposed to UV rays and can withstand the heat and intensity of the sun, whereas plastic tubing would fail and warp • It can withstand oxidising disinfectants and strong chemicals • It has natural antimicrobial properties, to discourage the growth of harmful organisms By opting to use copper instead of plastic tubing in the construction industry, contractors and builders alike can play a part in improving the sustainability of their industry, as well as obtaining all these additional benefits. It is also now an aesthetic trend to have exposed copper piping in modern bathrooms and kitchens, making it more desirable for a wider audience.
Producing plastic is no longer an issue, it’s a crisis. When looking at the statistics, only 16% of plastic
waste is recycled to make new plastics, while 40% is sent to landfill, 25% to incineration and
19% is dumped. When comparing these figures with copper, the industry has successfully reduced its CO2 emissions by cutting its unit energy consumption by 60% versus 1990. The industry is making progress, but is plastic?
Make the right choice. Choose copper. www.cuspuk.com
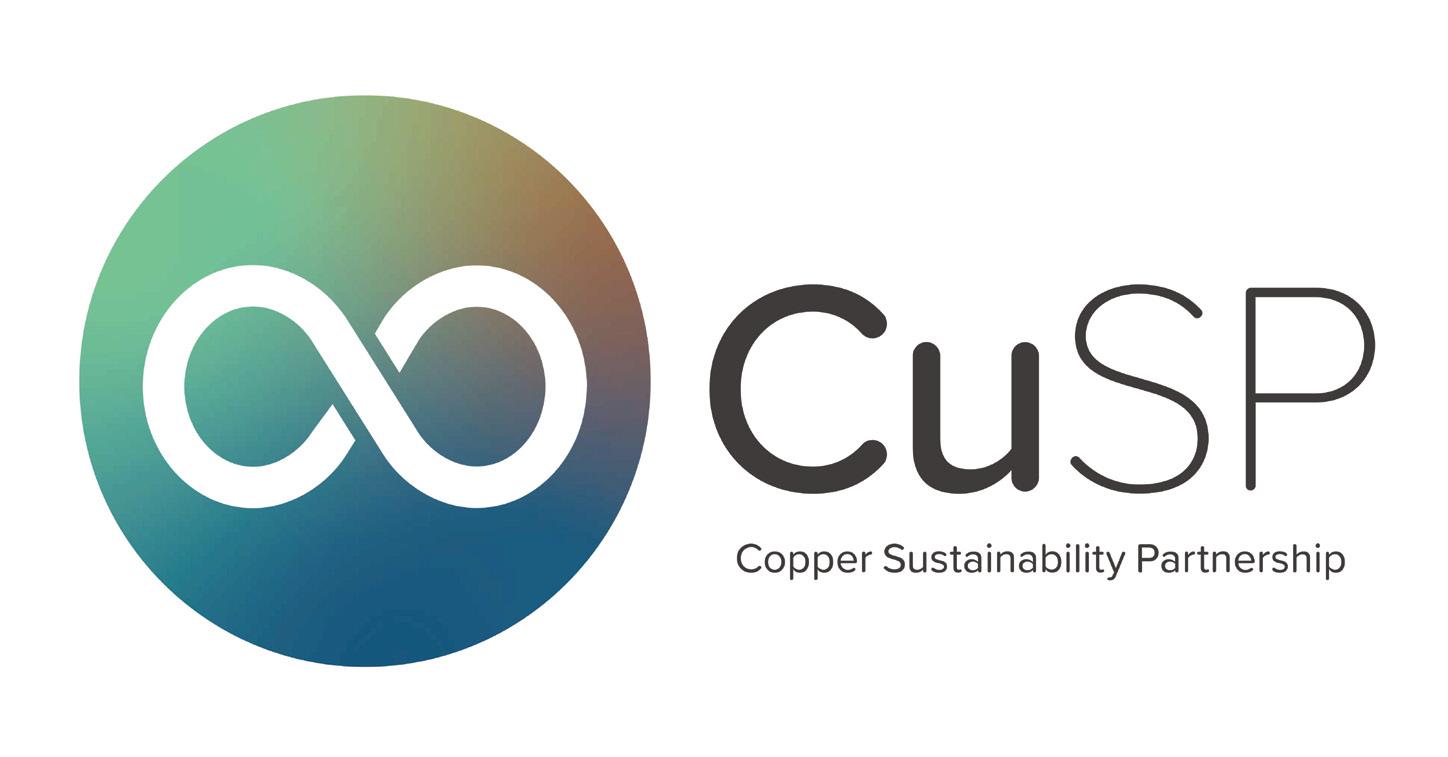
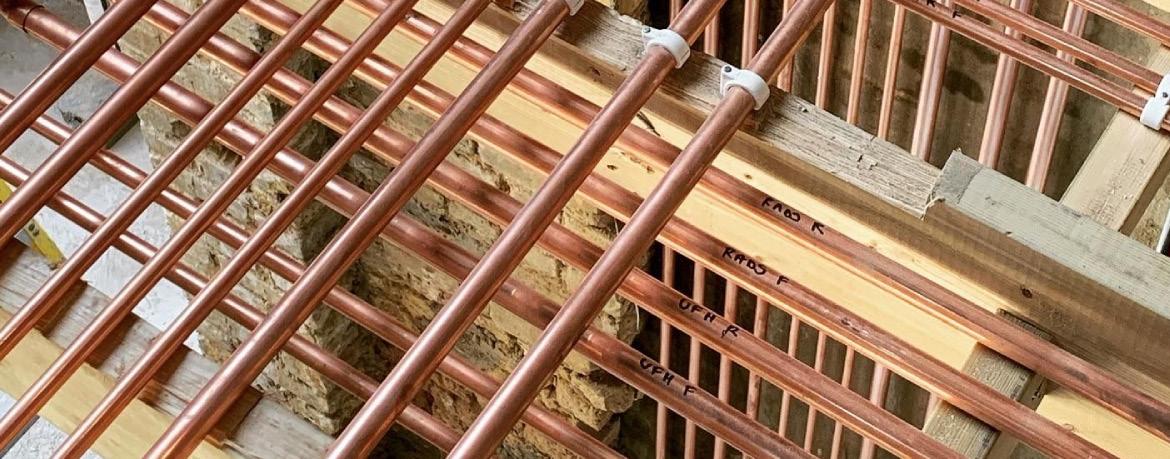
How to guide on designing the perfect bathroom with Imperial Bathrooms
Specialists in the design and manufacture of classic and contemporary British-made bathroom solutions, Imperial Bathrooms, offer its best advice on how to design the perfect bathroom whatever your style, space requirements and budget as the latest data shows the bathroom was the most popular room to renovate in lockdown.
To help you get started, Imperial Bathrooms present a step-by-step ‘How to guide to designing the perfect bathroom’, which outlines what you need to know when embarking on a bathroom remodel:
DO YOUR HOMEWORK – Before you commit to a particular style or look, gather together as much visual material as possible, keeping an open mind as you go. If you spot a colour scheme or period style in a magazine that appeals, cut it out and keep it to refer back to later on, and visit Instagram and Pinterest to get a feel for the kind aesthetic that you lean towards. Think about all the elements you need to bring together – taps, bath, shower area, ceramicware and storage. Once you have enough design inspiration, you can start to whittle it down until you’re ready to make some choices, such as the type of brassware finish you prefer or whether you prefer a high- or low-level cistern. STORE AND ORDER – Think carefully about how many people use the bathroom space, and exactly who they are – getting the right storage for their needs will have a direct bearing on the ultimate success of your design. Look for a vanity unit that can comfortably take all the toiletries, bottles and bath toys you need it to, so that you can always enjoy a clutter-free environment. Radiators with towel rails are also great places to keep towels and ensure they stay clean and dry. KEEP IT REAL – It’s easy to fall in love with the idea of a freestanding tub or a statement vanity, but it’s vital you don’t let your heart rule your head. Work out a budget and stick to it, and get out your tape measure and be realistic, remembering that all of the elements in the space will need good clearance for practical reasons. At Imperial Bathrooms we recommend allowing around 700mm of space around a bath and about 1000mm around a basin, and when it comes to selecting your mirror or mirrored cabinet, don’t opt for anything wider than the width of the basin or vanity below.
LOOK TO THE FUTURE – Your new bathroom is a long-term commitment, so you want your choices to stand the test of time. With this in mind, think about whether your family is likely to change shape so you can factor this into your plan. Also consider whether you might wish to sell your property at a later stage – it might be tempting to get rid of a bath and opt for just having a shower, but could this decision affect your chances of finding a buyer in the future?
IT’S GOOD TO TALK – If you have any questions, it’s important to ask someone. Plumbing is a specialist subject so if you’re thinking of changing the existing layout in any way, then check that the pipe feeds are located where they can serve the products you have in mind – as a general rule, it’s usually it’s best to leave the WC where it is. If you feel out of your depth, then think about hiring a designer. They will make sure that all your product choices are practical, work well together visually, and that details such as accessories aren’t overlooked. Bathroom suite, designed by Imperial Bathrooms featuring its timeless Drift Collection & Roseland Cast Iron Bath tub
Roann Limited appointed as lead worktop supplier for £130 million residential scheme
Wakefield-based granite and quartz worktop supplier, Roann Limited, has been appointed by Vinci Construction as the lead worktop contractor for residential scheme, New Victoria, in Manchester.
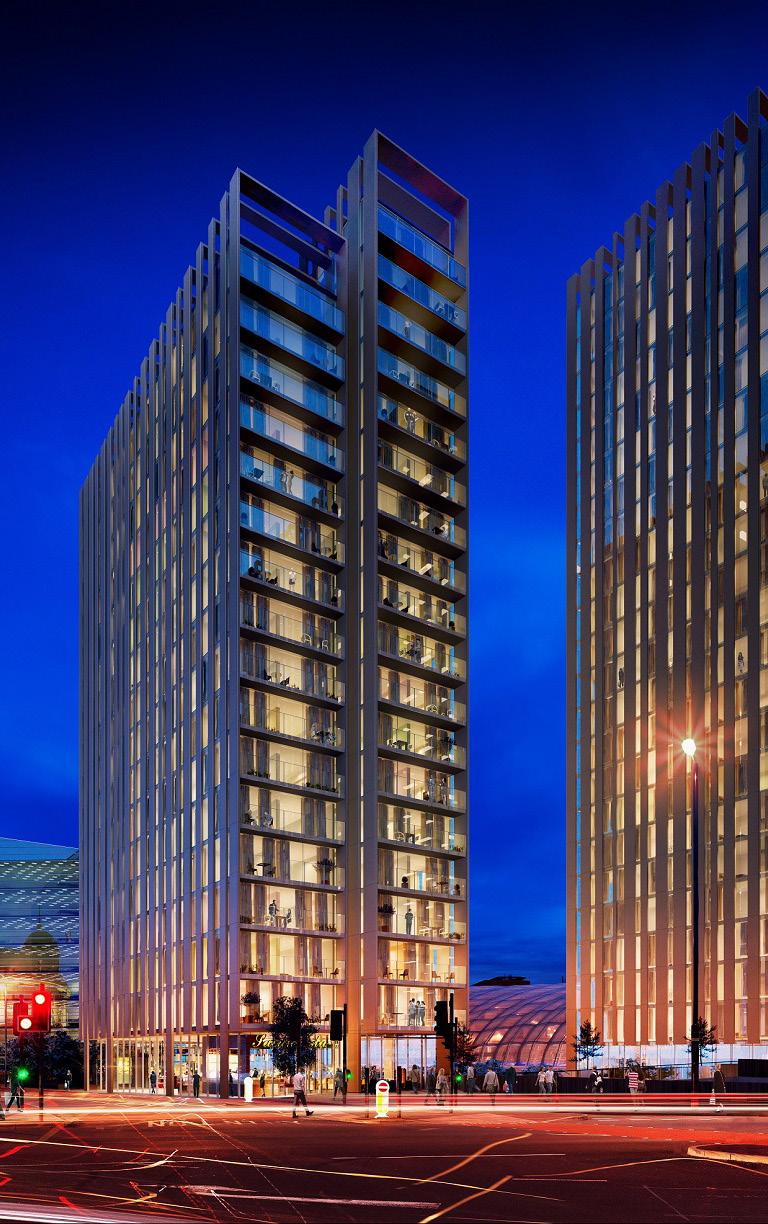
The £130 million project, delivered by Muse Developments, comprises 520 apartments, with 178 one-bed, 286 two-bed and 56 three-bed properties, as well as a 6,000 sq. ft commercial space. Roann Limited is supplying Silestone Blanco Norte 20mm for all kitchen worktops, upstands and splash backs, and Reginox Ohio 40x40 sinks in Atlantic Grey powder coated finish, to the entire 450,000 sq. ft residential component. Scheduled for completion in 2024, Roann Limited will begin installing a sample apartment in early September, before full site works begin in November 2021. Scott Wharton, Sales Director at Roann Limited, says “As the only dedicated high-rise residential worktop supplier in the UK, we’re really excited to be a part of this high-profile project. Working on this large-scale scheme in the heart of Manchester is a great reflection of our hard-working and dedicated team, as well as our business’ fast-paced growth. We’re really looking forward to seeing this project come together.” Gordon Maudsley, Senior Quantity Surveyor at Vinci Construction, adds “There was a lot of competition for the works, but Roann Limited stood out from the crowd. They made the whole precontract process a smooth and easy one and have continued to work with us now they’re involved in the scheme. Along with their pro-active attitude - they price competitively which made our decision to work with them an easy one!”
More information on Roann Limited and its products is available at www.roann.co.uk.
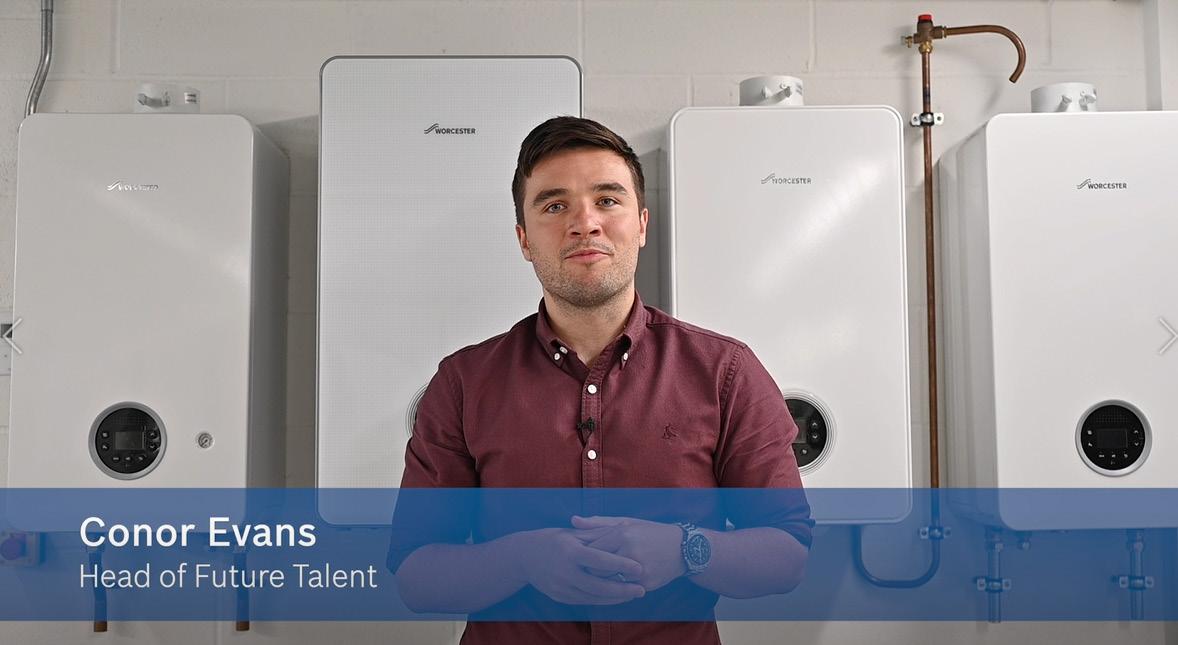
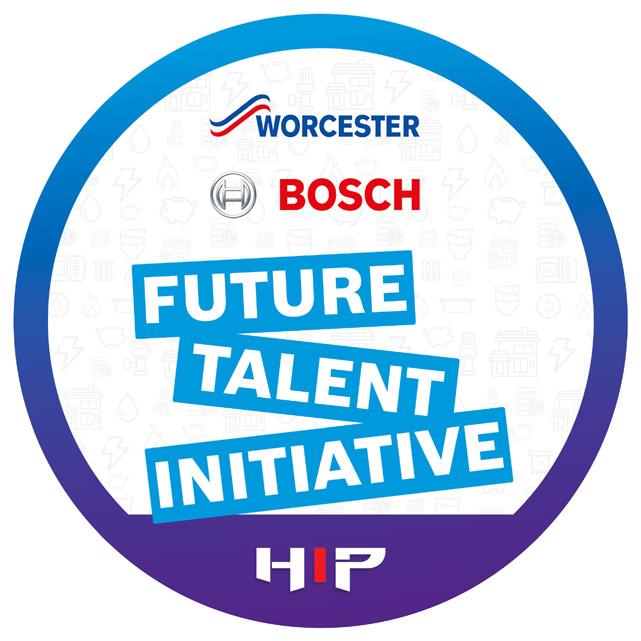
The UK’s leading boiler manufacturer Worcester Bosch are excited to announce the launch of their latest educational programme - the Future Talent Initiative (FTI).
The FTI is aimed specifically at supporting young installers, apprentices and those new to the sector, looking to deliver them the advice and information they need to succeed within the heating and hot water industry as it prepares to undergo significant change. As part of the initiative, the manufacturer has developed a robust content series, which sees experienced installers, Worcester Bosch professionals and third-party experts across different sectors, come together to offer their insight across three initial themes. The ‘0 to 20 in 60 Seconds’ series, offers quick-fire tips covering a range of topics including product installation, fault-finding and real-world insight. These are presented by a mix of Worcester’s training and technical support teams plus experienced installers. The ‘Forward Thinking’ series sees Worcester Bosch experts go into detail on where the heating industry is heading, including future technology and policy updates. Finally, ‘Life in the Fast Lane’ is a series of prerecorded webinars from experts outside of the heating industry. Etiquette expert William Hanson covers first impressions when entering customer homes, while Sales Advisor and Author Kieran Perry gives more general business advice. Finally, Wellbeing Consultant Neil Laybourn focuses on the importance of mental health. The series will see the videos be distributed across a number of months, from now into the new year. Also, Conor Evans from Worcester Bosch takes on the role of ‘Head of Future Talent’ as part of the Future Talent Initiative and is excited to support the installers of tomorrow. He commented; “We held a series of focus groups with young installers last year. They expressed the need for more support from manufacturers in their training and early career stages, which was really the inspiration behind the Future Talent Initiative. “Since then we’ve been working hard to develop our Initiative, identify what young installers want to hear more about and ultimately help them fast-track their careers.” Zoe Tanner, Managing Director of SNG – the publishing house behind HIP Magazine who are involved in the Initiative – added; “HIP is thrilled to be partnering with Worcester Bosch to promote the Future Talent Initiative. The educational tool combined with Worcester’s Headline sponsorship of HIP Learner of the Year 2022 demonstrates a huge commitment to support the next generation of installers and subsequently the future of the industry.” If you are a young installer, an apprentice, or just new to the industry, visit the Worcester Bosch YouTube here to access the Future Talent Initiative series. Alternatively follow HIP Magazine on Instagram (@hipmagazineuk), on Twitter (@HIPMagazine) for the latest updates and video releases. For more information on Worcester’s full range of gas and oil boilers, please visit: www.worcester-bosch.co.uk/. 31
Britcon Appointed to Deliver £16M Expansion For Ideal Heating
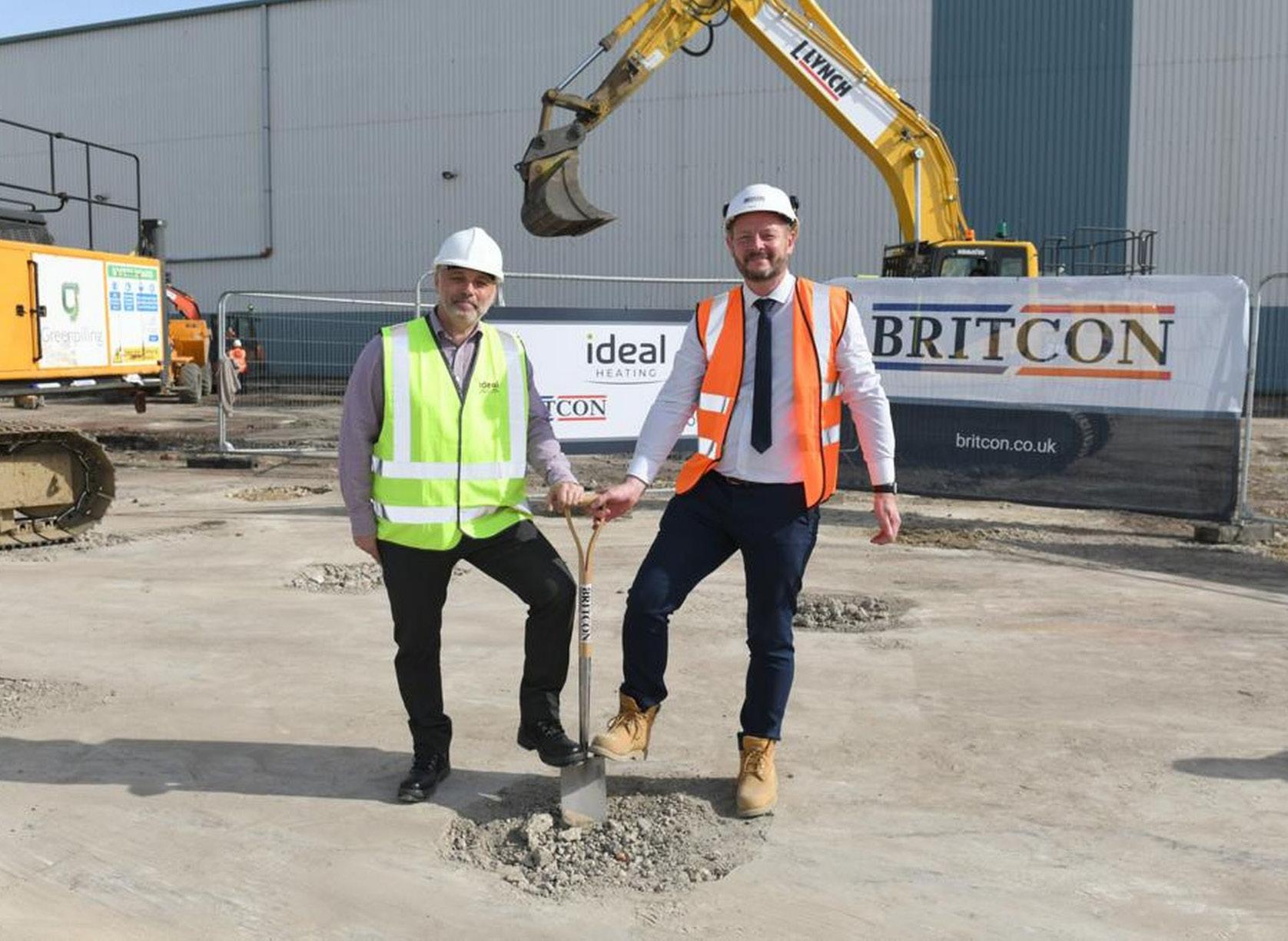
Construction company Britcon has been appointed main contractor to deliver a £16 million expansion for Ideal Heating at its headquarters in Hull.
The 116,000 sq ft expansion will more than double the size of the existing warehouse, allowing Ideal Heating to increase production of lowcarbon heating products. It will also include the construction of a new office building, car park and infrastructure works including a new access road to the site.
Founded over a hundred years ago, Ideal Heating is a market leader in high-performance heating solutions for domestic and commercial markets. It employs over 750 people in Hull and a further 250 elsewhere in the UK. In 2019 Ideal Heating became the world’s first boiler manufacturer to be certified to ISO 50001 for energy management, achieving this international standard through measures including the use of renewable materials and energy resources in its design and production process. Jason Speedy, chief operations officer at Ideal Heating, said: “This investment is part of a wider, ambitious plan to significantly grow our business through the introduction of low carbon products for the future. The expansion will enable us to step up production of these and other innovative new heating technologies, reinforcing our wellestablished green credentials and creating more highquality jobs in the city. “We are pleased to be working with Britcon as our strategic delivery partner following a rigorous competitive tender process where they were scored on delivery, safety, cost, and quality of submission. Following a number of site visits for comparable projects, we were very impressed with Britcon’s approach to health and safety, value engineering, and all-important commitment to local engagement.” Nick Shepherd, managing director of Britcon, added: “We are delighted to secure this contract as a local company and support Ideal Heating as it pursues its low carbon agenda. “We have a strong local supply chain and are excited to be working in partnership with our client and associated stakeholders in not only delivering this project, but also utilising our experience and resources to deliver local employment opportunities during the construction period. “This is a significant boost for Britcon as we emerge from the impact of Covid as well as Brexit and I am proud of how the business has evolved since I joined in 2019 to be able to compete at the highest level with impressive credentials and fantastic team of professionals.” GGP Consult is also appointed to work alongside Ideal Heating and Britcon to provide project management, structural, civil and architectural services on the project. Construction work will start this month with completion anticipated by Autumn 2022. @Britcon_Limited
Join the Heat Pump Revolution
Receive £750-worth of Heat Pump Training for just £45 from Panasonic and Optimum Energy during October 2021
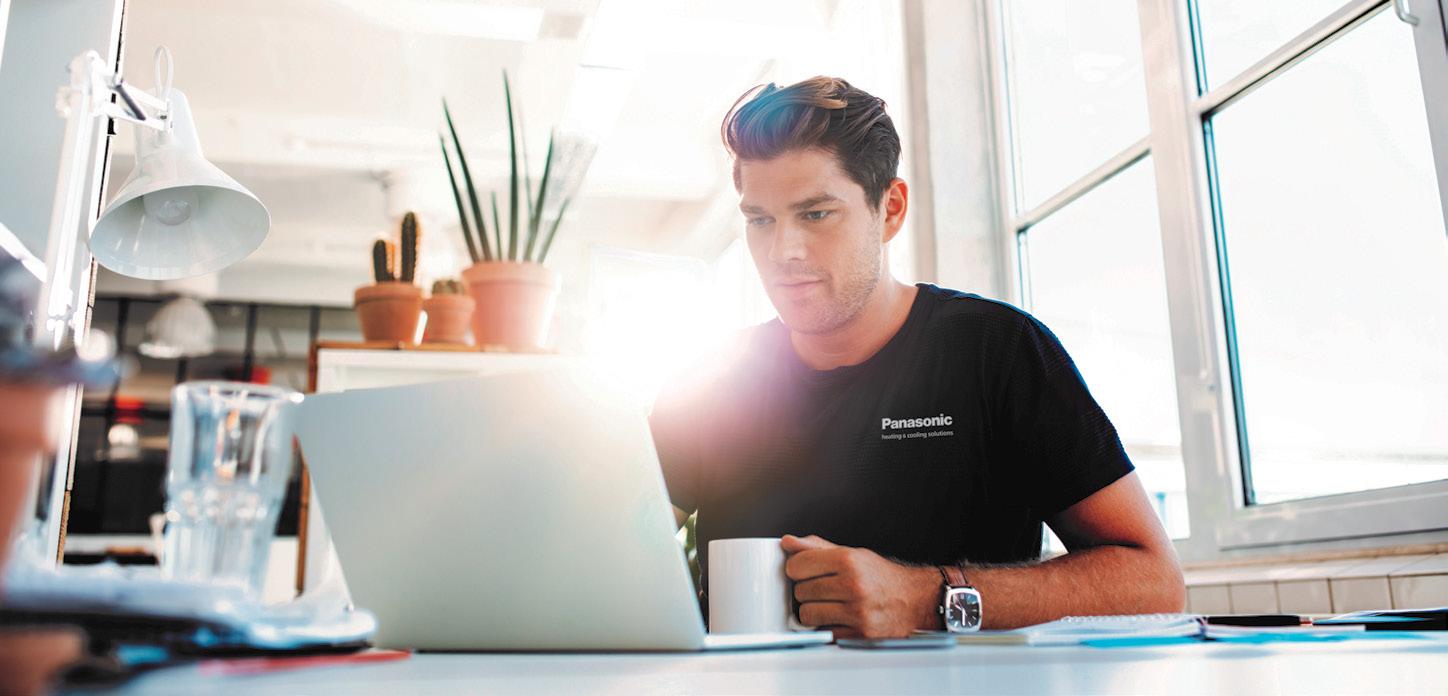
Ahuge opportunity exists for installers to upskill, partfunded by the government, and provided by Panasonic in association with Optimum Energy. Take advantage of this fantastic offer and book onto courses which normally cost £750 per person, for just £45 for dates throughout October.
The drive to replace the huge number of fossil-fuel boilers (mains gas, oil and LPG) currently installed in homes across the country has just got serious and low carbon heating (and cooling) systems have never been more in demand.
Panasonic is teaming up with Optimum Energy to offer installers the chance to get certified to enable you to install the thousands of heat pumps that will be required over the coming years to meet the target set by the government. According to a recent report by the Committee for Climate Change[1], approximately 19 million households could adopt this new technology by 2050, with current predictions of approximately one million heat pumps installed by 2030, resulting in the UK meeting its net zero target by 2050.
Get qualified now…
Panasonic has partnered with BEIS (The Department for Business, Energy and Industrial Strategy) and Optimum Energy Solutions to help installers access the necessary training for heat pump projects. COVID-safe, online training, over two days, dates are available from early October, running weekly until the end of the month. Places are limited, so don’t miss out - book your place now.
The courses cover:
• Introduction to heat pumps: explaining the science behind this renewable technology • How to conduct heat loss surveys • How to correctly size an Air Source
Heat Pump.
In addition, delegates will receive free access to industry software and calculators worth hundreds of pounds and £100-off the cost of the LCL Heat Pump Part 1 course. Furthermore, help with MCS accreditation will be on hand if required. Richard Bishop, Head of Marketing for Panasonic UK and Ireland commented, “We are excited to be able to provide such a great offer to installers and to be working in partnership with BEIS and Optimum Energy Solutions to be able to provide this heat pump training throughout the UK during October and help contribute to a low carbon future - a top priority for Panasonic.” Panasonic’s Aquarea range of air source heat pumps is known for being a highly efficient solution, utilising the air as a 100% renewable energy source to provide heating, cooling and domestic hot water. The range itself is huge, offering a heat pump solution for many different homes, whatever the heating demand. The latest Aquarea heat pumps use R32 refrigerant for increased savings and better environmental results. R32 is easy to recycle, has zero impact on the ozone layer and 75% less impact on global warming, helping to lower the carbon footprint of residential homes.
The Panasonic Aquarea J Generation features a heating efficiency with a COP of 5.33 and a Domestic Hot Water (DHW) COP of up to 3.3. The range is rated A+++ in low temperature operation, which is the highest energy class, according to the new Energy Labelling Directive 2010/30/EC. There are also models available that provide cooling as well as heating and hot water provision.
The average household in the UK emits 2.7 tonnes of CO2 every year[2] from heating alone. Switching to air to water heat pumps to provide heating to our homes could help lower housing emissions significantly, plus residents can save up to 50% on their fuel bills. Air to water heat pumps are the future for the housing sector and an essential step in challenging the climate change problem.
REGISTER TODAY
Registration for the above training can be found via our PRO Club site – please click here to register or email uk-aircon@eu.panasonic.com.
Panasonic is a world leader within the heating and cooling industry, with over 60 years of experience of producing innovative products. The company invests heavily in R&D to develop new solutions to advance the market, with a huge emphasis on environmental impact, hence the investment in emerging low carbon technologies such as air source heat pumps.
For more information on the Panasonic range of low carbon solutions, please visit www.aircon.panasonic.eu.
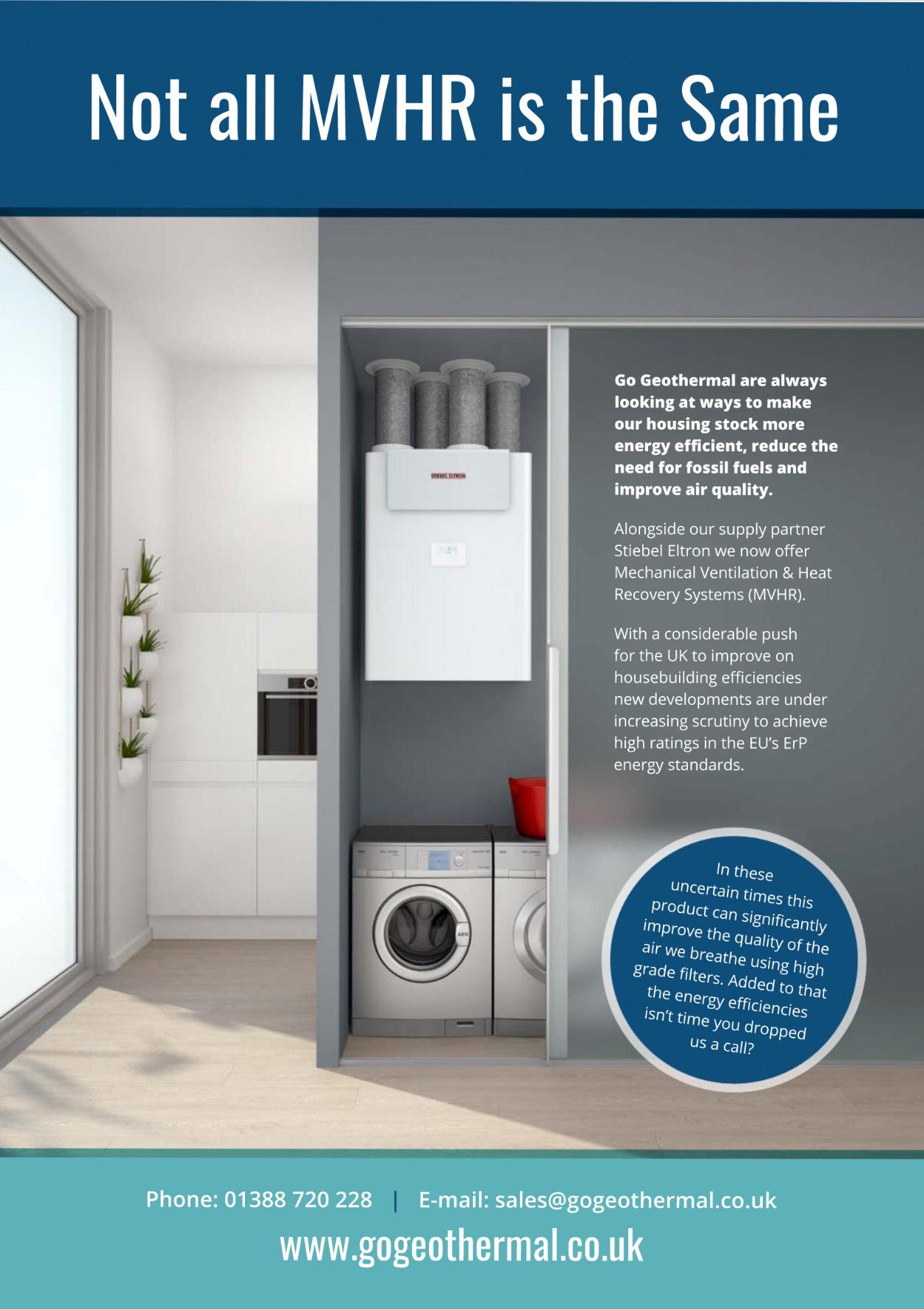
Milestone Reached at £26 Million Great Yarmouth Marina Development
Morgan Sindall Construction has hosted a milestone topping out event to mark progress on Great Yarmouth’s £26m ‘once in a generation’ Marina Centre development.
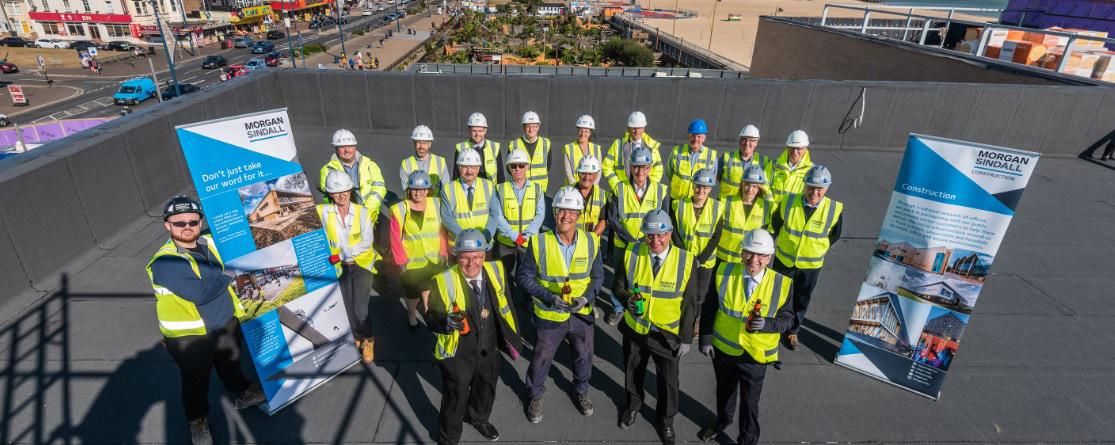
Once completed, the scheme will provide a new destination attraction along Great Yarmouth’s famous Golden Mile. It is being delivered by Morgan Sindall Construction on behalf of Great Yarmouth Borough Council and will occupy the site of the town’s former and now demolished leisure centre.
Work started on the project in January 2020. The new health and fitness centre will comprise a 25 metre swimming pool suitable for competitions and galas, along with a learner pool with moveable floor, leisure water with fun play features, a water confidence area and two water flumes.
The complex will also be equipped with a health suite, incorporating a four-court sports hall, fitness studios and spin studios, a 100-station gym, an indoor climbing zone and a café with views to the seafront.
The development is intended to act as a catalyst for further investment as well as providing an important community and tourist hub for the promotion of both indoor and outdoor activity. It has been hailed by Great Yarmouth Borough Council as a ‘once in a generation opportunity’ to regenerate the town’s seafront promenade.
Since work commenced on the site, Morgan Sindall Construction has hosted a number of events to ensure local residents and the wider Great Yarmouth community are involved in the project. Recently this included giving councillors and local stakeholders a virtual site tour, along with arranging a site tour for Women into Construction to help support a more inclusive construction sector. Students from Suffolk New College were also given the opportunity to attend the site and see what it’s like to work on a large-scale construction project.
Alister Broadberry, area director for Morgan Sindall Construction East, said: “It is fantastic to be marking this key stage in the development of a transformational project for Great Yarmouth. We are heavily invested in making sure the Great Yarmouth community engages with the project and reaps as much benefit as possible from it. “We will continue to work closely with Great Yarmouth Borough Council to realise their vision of a next generation, inclusive leisure facility that acts as an anchor attraction for the region.”
Great Yarmouth Borough Council leader Cllr Carl Smith said: “We’ve now reached an exciting milestone in the construction of this landmark building. This new state-of-theart visitor destination will be a major year-round boost for Great Yarmouth and the surrounding area, bringing great benefits in supporting the health and wellbeing of our community and visitors for many years to come. It is also a stunning addition to our seafront.
“We are hugely grateful to the New Anglia LEP and to Sport England for their financial support of this important project which was crucial in enabling us to push forward with it, and to our contractors Morgan Sindall Construction for continuing to deliver results on schedule and on budget.”
Construction work is expected to complete on the Great Yarmouth Marina Centre in 2022.
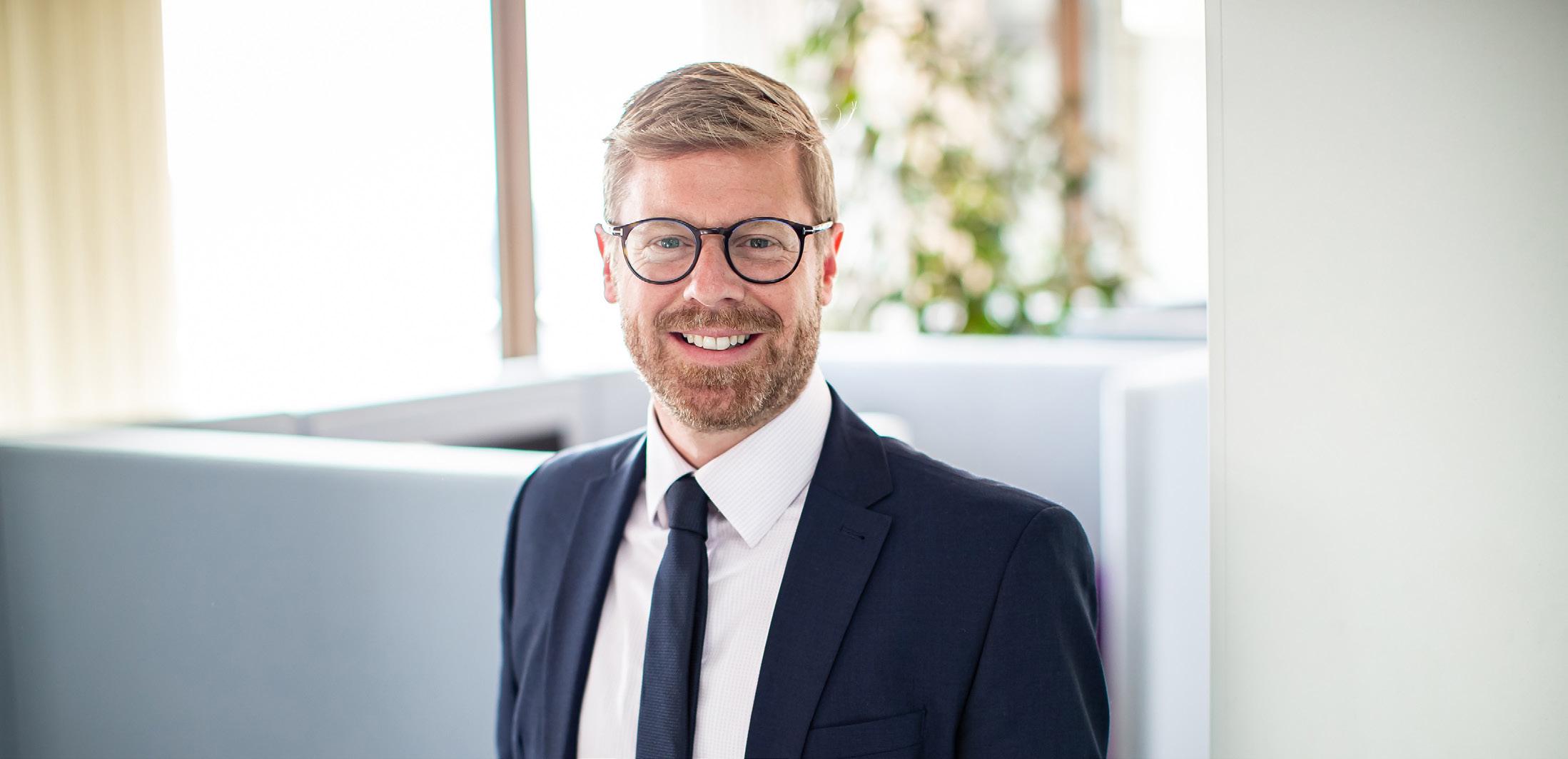
NEC Eyes Expansion into New Sectors with Appointment of New Users’ Group Chair
The industry-leading provider of procurement contracts to the construction sector, NEC, has appointed the Deputy Director of Crown Commercial Service (CCS) for Construction, John Welch, as its Users’ Group Chair.
Alongside his role at CCS, John will drive further collaboration across sectors as NEC Users’ Group Chair, facilitating more streamlined implementation of procurement contracts, along with extending into new areas such as manufacturing. With over 20 years’ experience working in civil service roles, John has vast knowledge of establishing the best commercial solutions for Central Government Departments and Wider Public Sector organisations in procuring for construction and infrastructure projects. John has worked across all tiers of the supply chain and across multiple sectors including building, infrastructure, petro-chemical and nuclear, and will bring strategic direction aimed to increase NEC’s growth and usage worldwide. Prior to joining CCS, John was Head of Procurement at Cavendish (Babcock) Nuclear, where he transformed the procurement function of major organisations such as EDF Energy. During his time there, he worked on significant projects such as Hinkley Point C, along with decommissioning projects such as Sellafield’s Magnox facility. Rekha Thawrani, Global Head of NEC said; “Following the pandemic and the turbulence of the last two years for the construction industry, developing strong working relationships and good collaboration needs to continue to be the foundation for enhancing project outcomes. “John’s experience in public sector roles makes him perfectly positioned to navigate NEC’s outreach into new markets both nationally and globally. “Having worked on numerous major projects across a wide expanse of sectors, we’re confident that John will bring the expertise needed to support the growth of NEC”. John said: “NEC has already forged a reputation as the leading procurement contract provider to the construction industry, which gives me confidence in its ability to expand its reach globally and into new sectors. “In the future, I want NEC to be synonymous with carbon reduction, and it’s extremely reassuring to see that it’s already heavily on the agenda industry wide. “The collaboration and flexibility that NEC offers means it already plays a vital role in the industry, and it’s promising to see that this will only continue. “After what’s been a difficult past two years, industry and government bodies have grown closer than ever, and I’m pleased to be working with NEC at a time when the sector is in such a fortunate position”. To find out more about NEC, visit the website.
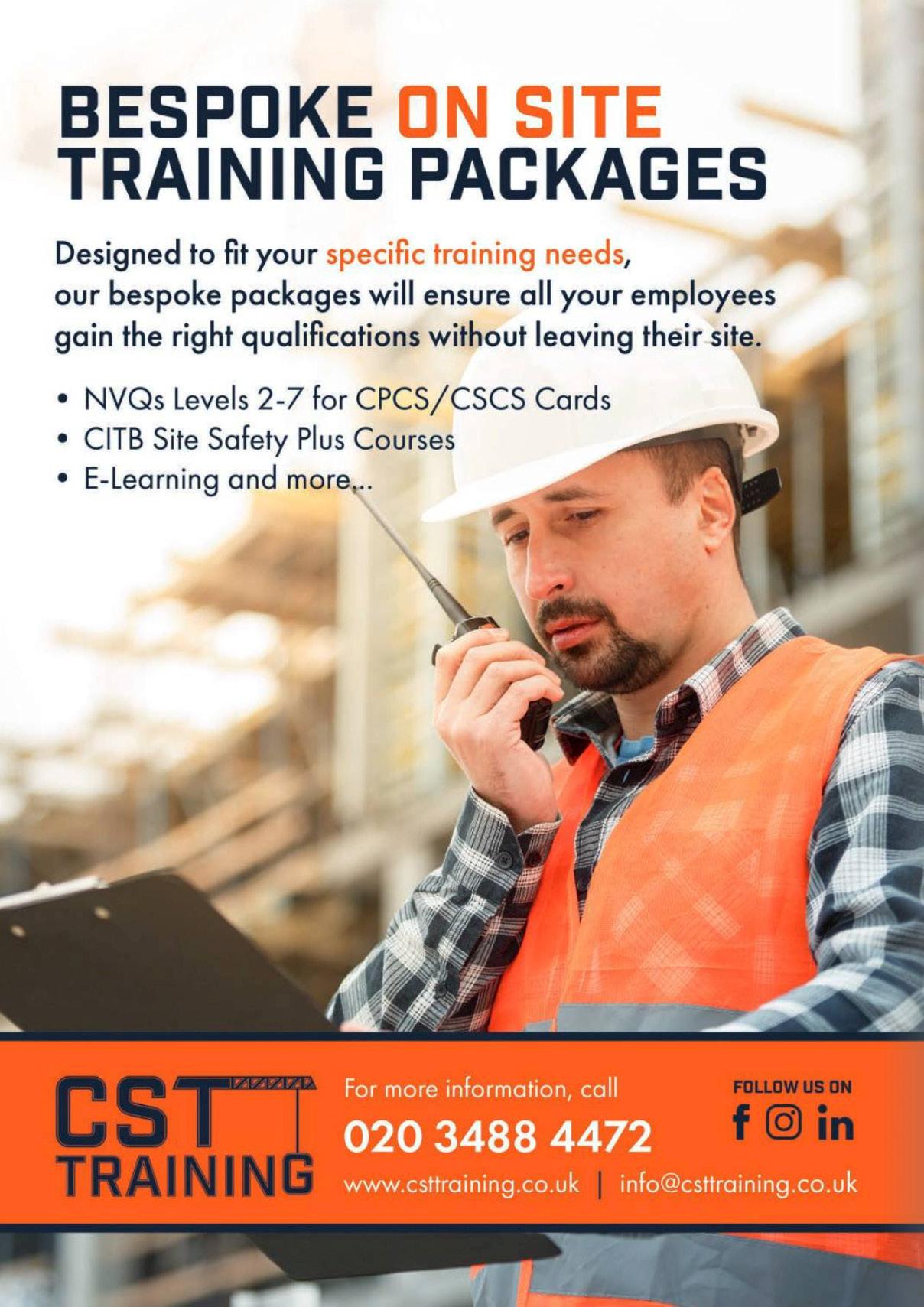
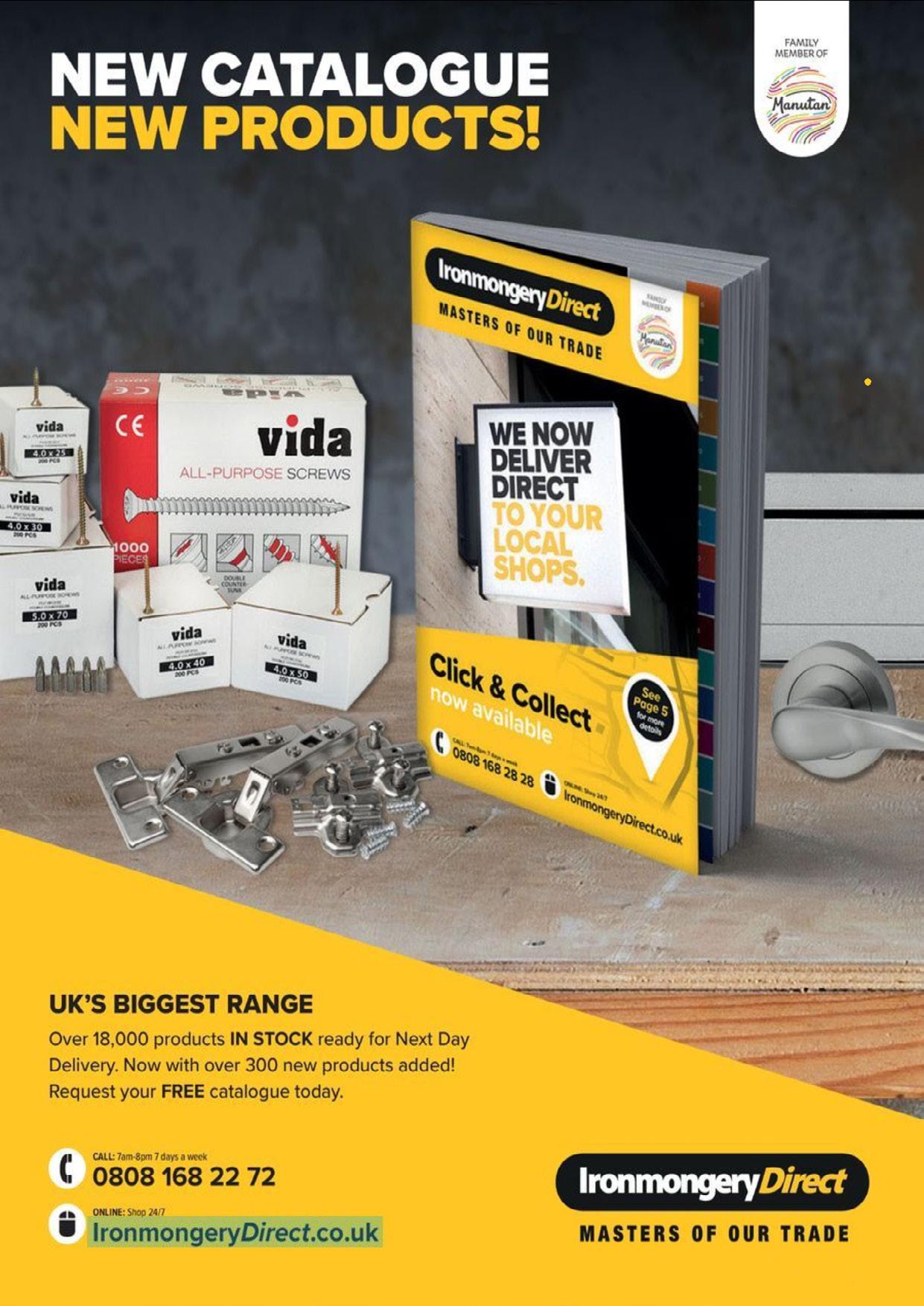
Profab Access introduces industry first for fire integrity and installation
Profab Access has launched a revolutionary certified frame system that sets a new standard for innovation, fire performance and functionality, making installation on site safer, faster and simpler.
The only product of its kind currently available, the expertly engineered PRECISION adjustable frame completely transforms the installation process for construction professionals and streamlines the specification process for architects and specifiers. This is achieved through the product’s unique construction, which enables the frame to be fully adjusted to meet the specific dimensions of each structural opening, not only ensuring the installation is fit for purpose by providing the highest standards in accuracy, but subsequently removing the requirement for plastic packers for a safer, faster and simpler installation process.
The patent pending PRECISION adjustable frame is now supplied as standard with Profab Access’ high quality steel INTEGRA 4000 Series Fire Rated Riser Door.
The PRECISION frame dramatically reduces fitting times and eliminates the risk of using noncompliant components throughout installation, which may not have been tested in conjunction with the riser door itself. Factory applied intumescent strips to the outer frame also eliminate the need for additional intumescent mastic when installing the frame into a flexible or solid wall construction.
Profab Access is the UK’s first manufacturer to have its concealed Riser Doors bidirectionally fire tested and certified by an accredited third party. The PRECISION adjustable frame has also been bi-directionally fire tested as an entire doorset with the INTEGRA 4000 Series Riser Door for up to 120 minutes, receiving the CERTIFIRE accreditation for installation in unlined shaft walls and solid wall construction.
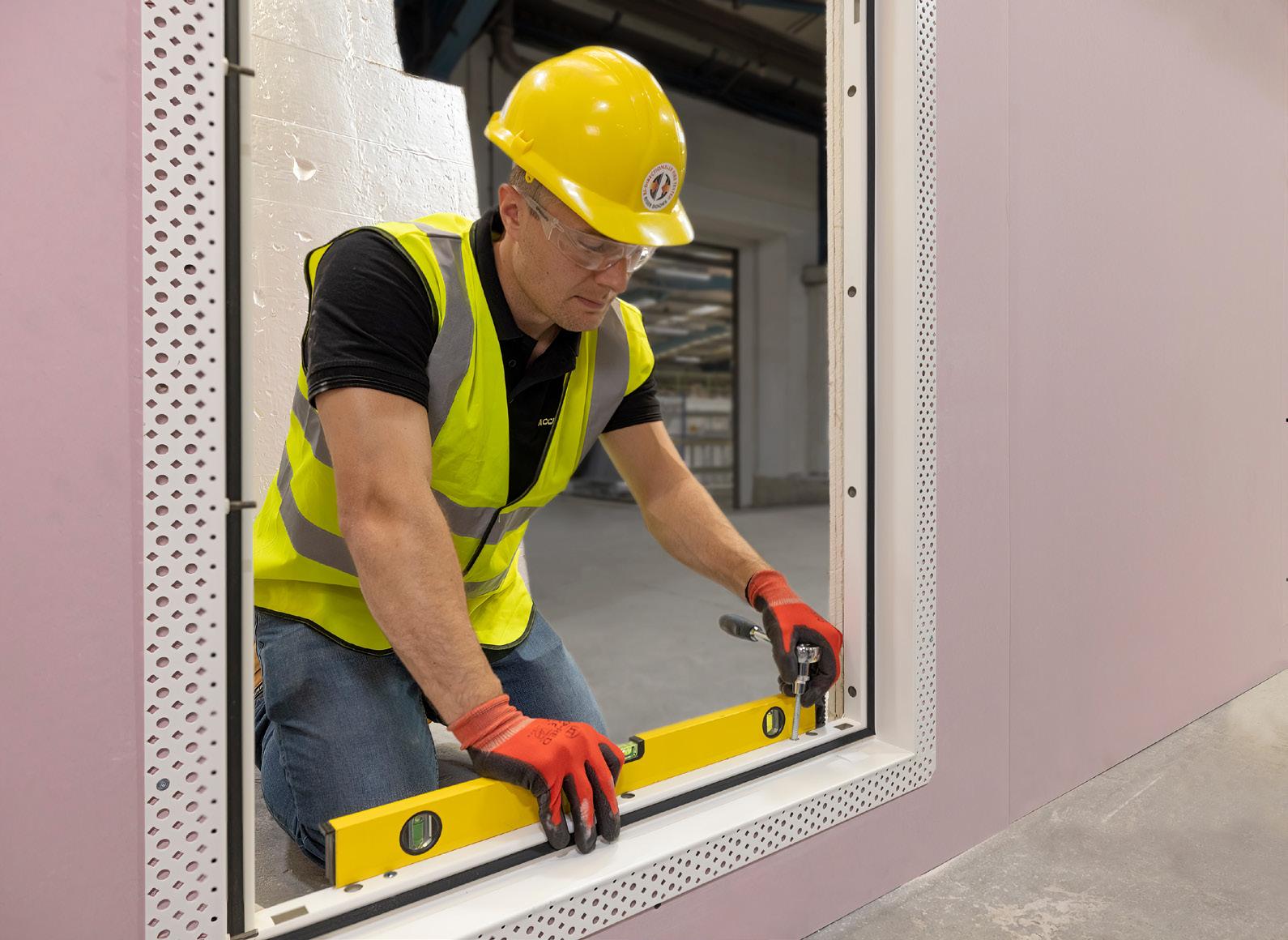
This provides architects, specifiers and contractors with a completely certified solution, as both the frame and the riser door have been bidirectionally tested as a single doorset and are supplied with comprehensive documentation to evidence their performance credentials and adherence to all relevant regulations, including BS EN 1634-1:2014 +A1:2018.
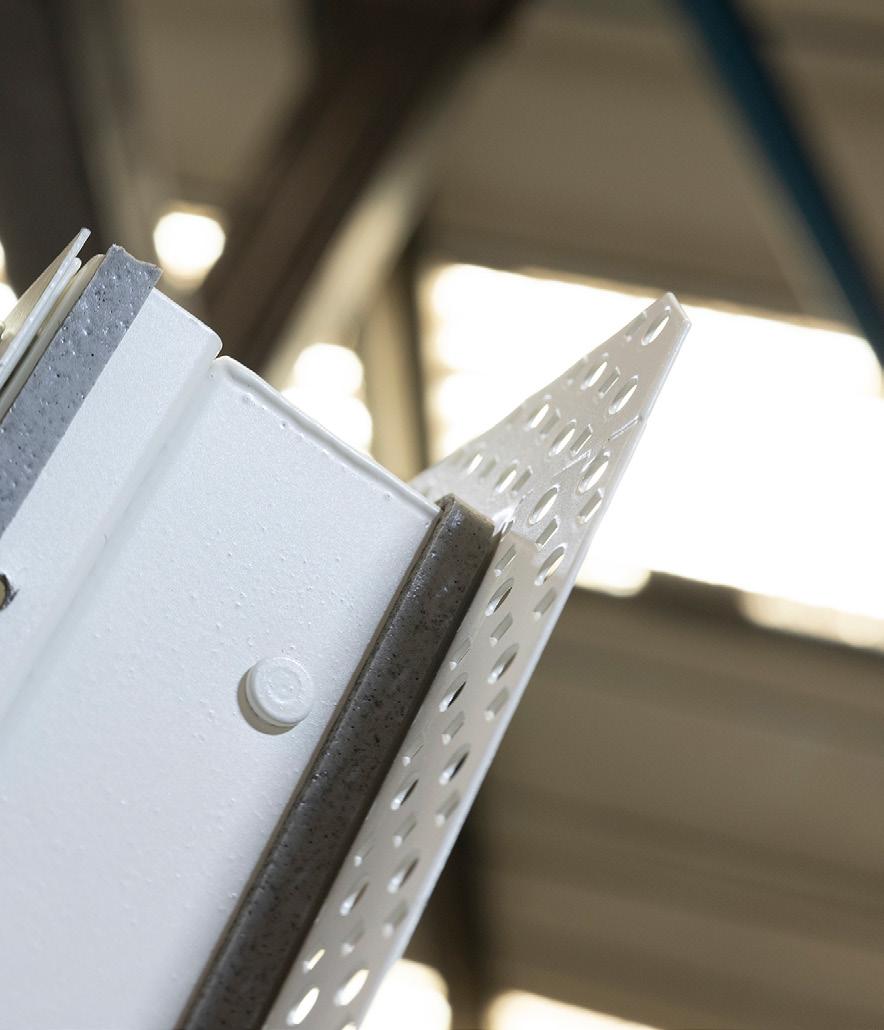
Marcus Parnham, Commercial Director at Profab Access, said: “As one of the industry’s leading manufacturers, we have a responsibility to push the boundaries of this product category and ensure every access solution we supply delivers the highest standards in performance and compliance.
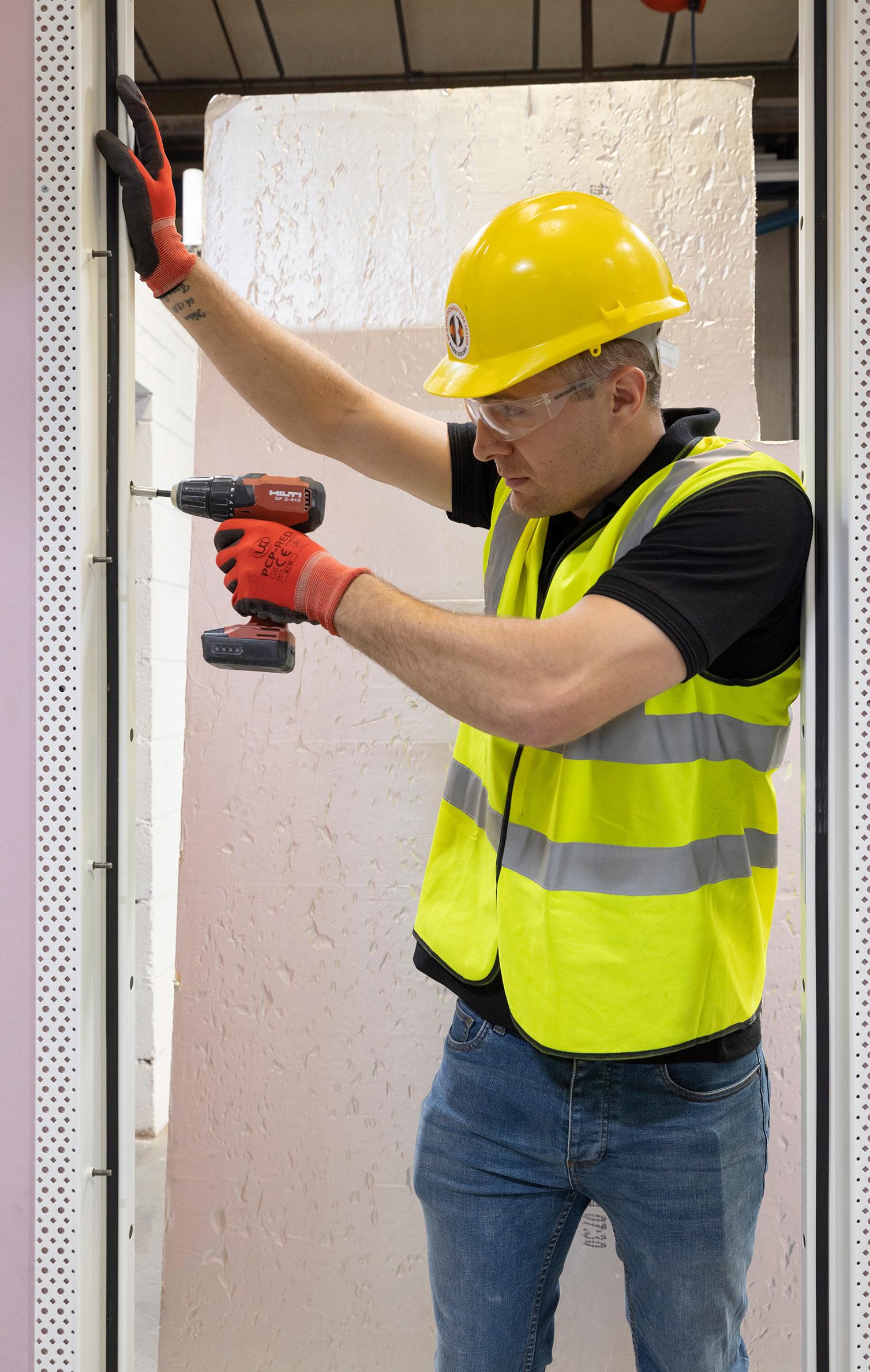
“Our new patent pending PRECISION adjustable frame represents a real step change for the industry, supporting professionals in fulfilling their duty of care by going above and beyond current legislation in delivering the highest standards of due diligence and achieving constant compliance for the entire doorset, including the materials used throughout the installation process. The frame is the result of our unwavering commitment to innovation and providing the built environment with the very highest standards in access solutions.”
The PRECISION adjustable frame is constructed with an all-in-one smoke, intumescent and acoustic FS1000 seal, eliminating the need for additional intumescent mastic when installing the frame into a flexible or solid wall construction. This cost efficient and sustainable material contains no halogen compounds and will not emit toxic gas when heated, ensuring the safety of building occupants in the event of a fire.
As an official Made in Britain member, Profab Access’ comprehensive portfolio of Riser Doors and Access Solutions are manufactured at its headquarters in Atherstone by its experienced team of design and engineering experts.
For further information on Profab Access and its range of riser doors, access panels, and steel doors, call +44(0)1827 718222 or visit www.profabaccess.com.
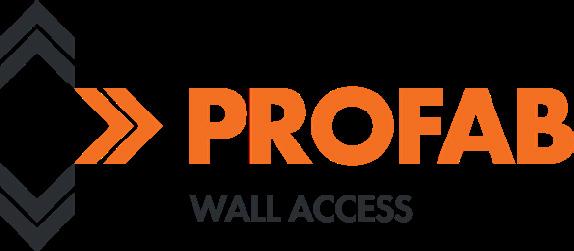
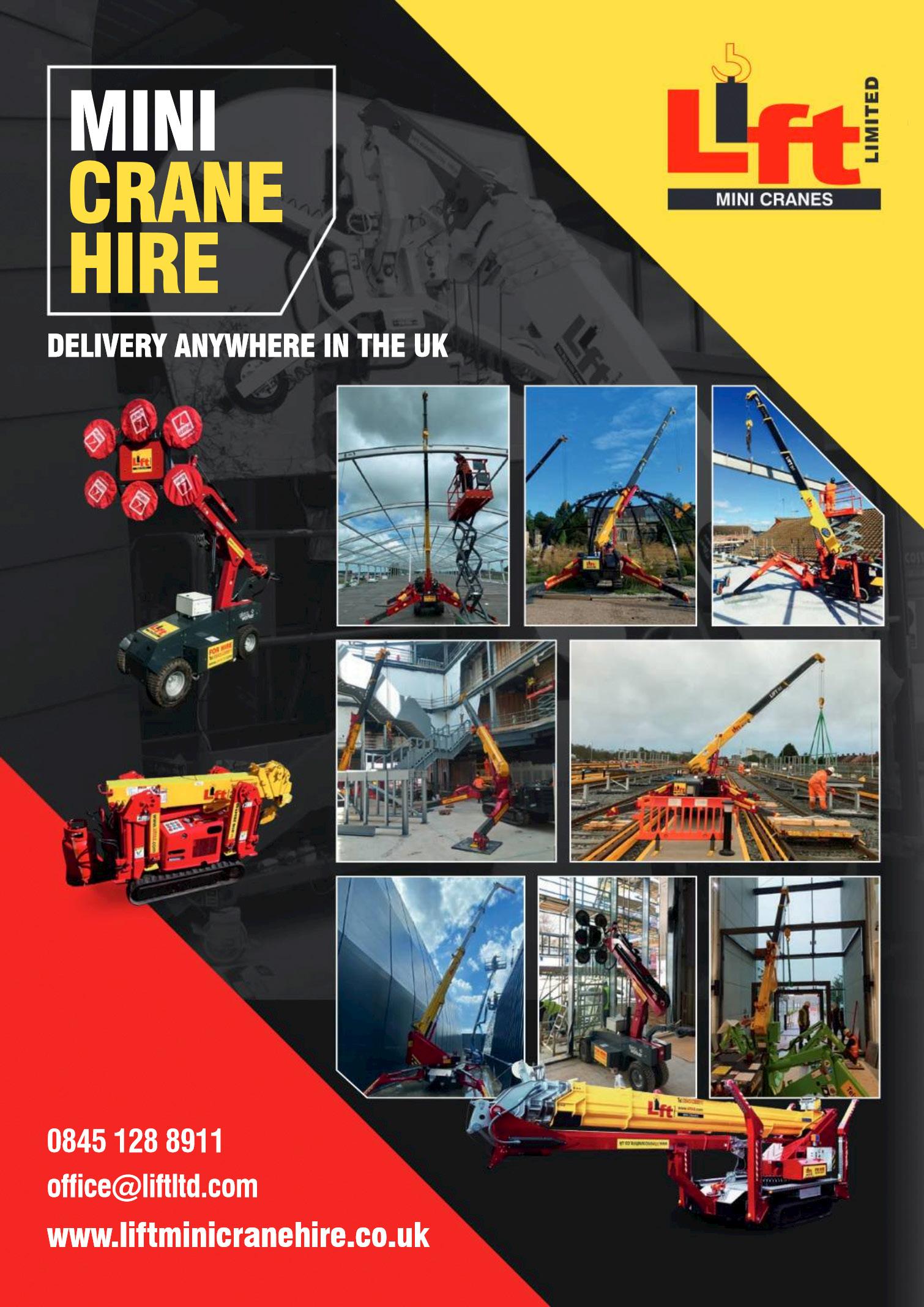
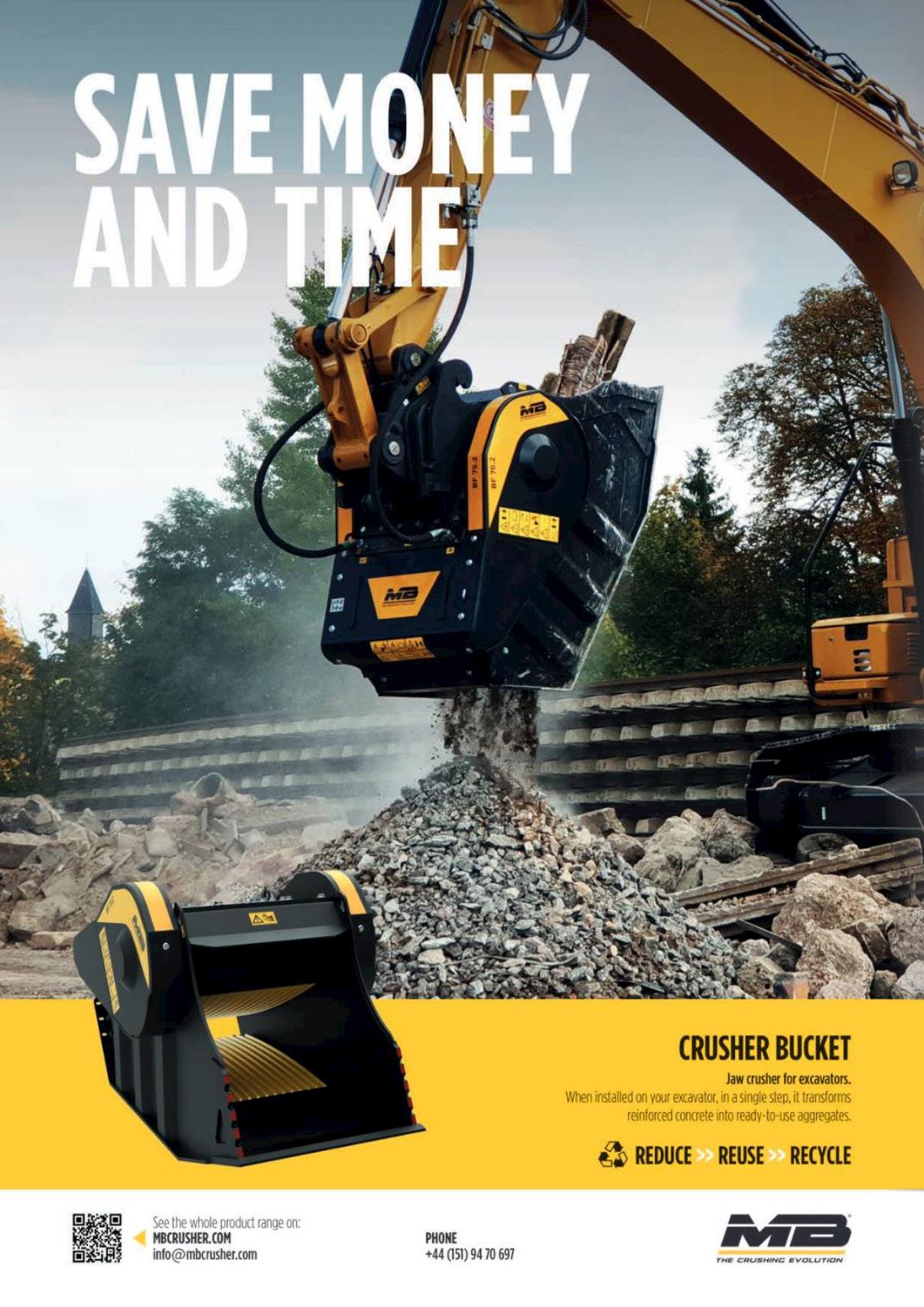

Dust extraction specialist to demonstrate problem-solving capabilities at eagerly anticipated SHE Show South 2021
Dustcontrol UK will be demonstrating its problem-solving capabilities at The SHE (Safety, Health and Environment) Show South 2021.
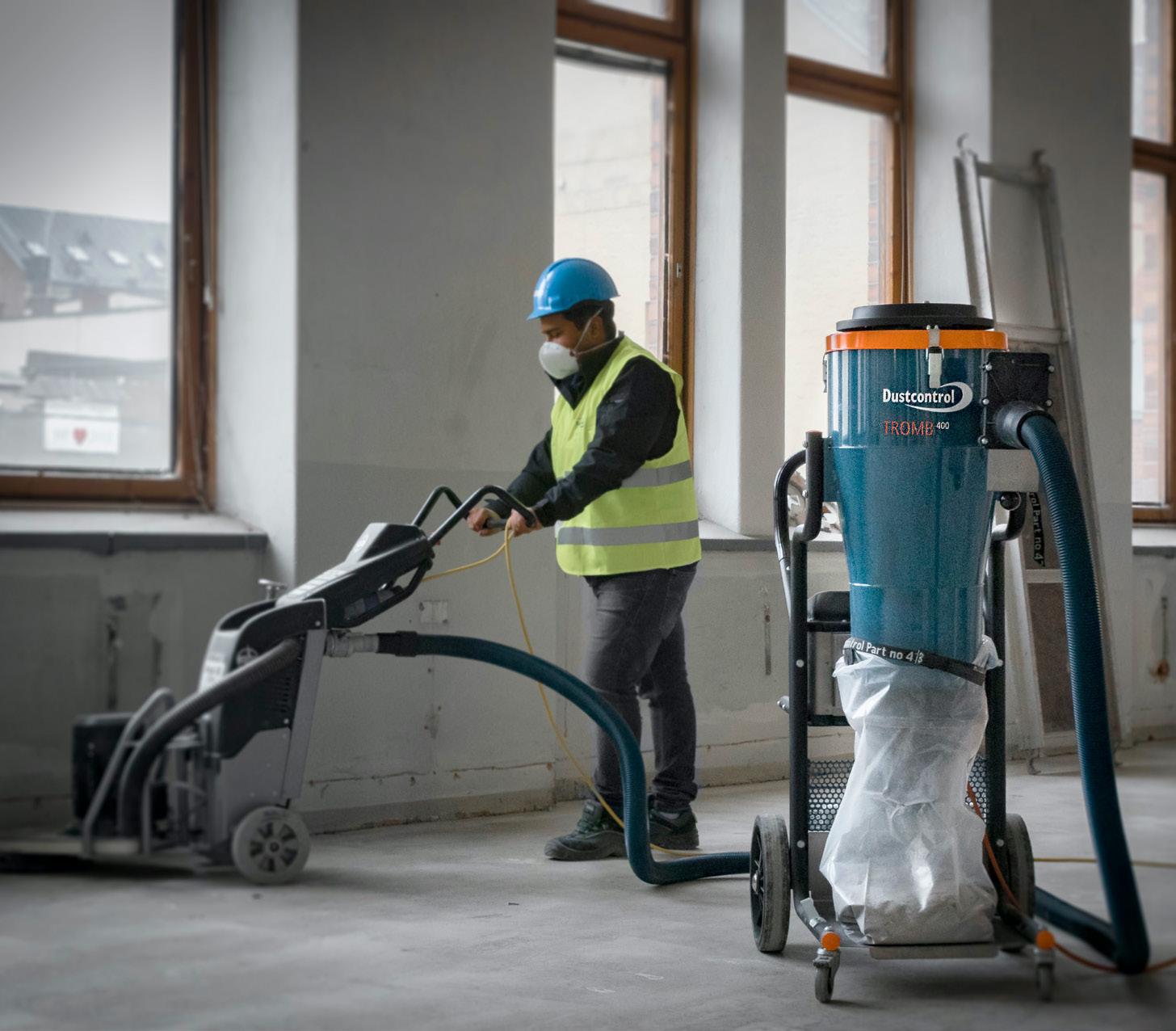
Taking place on Tuesday, 23rd November at MK Stadium, Milton Keynes, Dustcontrol UK will be showcasing its vast experience in helping companies to achieve efficient production processes, increased productivity, improved product quality, and a safer working environment, at stand 22.
Demonstrating its range of mobile and centralised vacuum equipment, including HEPA filtered, ATEX-rated and cyclone based industrial dust extractors, the Dustcontrol team will share how its robust machines can capture and extract different kinds of particles and pollutants with the highest level of filtration to achieve better results.
James Miller, Managing Director of Dustcontrol UK, said: “We’re looking forward to sharing our wealth of experience in creating and maintaining healthy environments to industry leaders at this year’s SHE Show South event. Our product range consists of portable dust extractors for industrial and construction use, fixed extraction installations, discharge arrangements, and accessories. All our machines are ideal for extraction of dust or particulate at the point of its production, as well as for powerful vacuuming or air cleaning. “Ultimately, everything runs so much more smoothly when you avoid being stopped or disturbed by dust and other pollutants, not to mention the better air quality that is the result of professional dust extraction.” The company, based in Milton Keynes, has almost 50 years of experience in developing dust extraction solutions and centralised vacuum systems to fit client requirements in the construction/rental marketplace, as well as production companies. These range from bakeries, cereal manufacturers, tea blenders, spice companies, and pharmaceutical manufacturers to heavy metal manufacturing plants. They are experts in problem-solving with a high technical capability of capturing dust at its source, then containing and transporting it to a convenient discharge solution. Attracting around 250 delegates, The SHE Show Conference and Exhibition is an annual series of events all about people, behaviour, and culture change. It focuses on six key elements: inspirational leadership, climate change and sustainability, mental health and wellbeing, behaviour and culture change, overcoming adversity and resilience, and legal advice and updates. James concluded: “At Dustcontrol UK, we’re not satisfied with just selling products. We manufacture and customise portable dust extractors and industrial extraction systems to fit all client requirements, achieving safer and healthier work environments.”
For further information on Dustcontrol UK’s products, please call 01327 858001, or email sales@dustcontrol.co.uk.
For further information on Dustcontrol UK, visit www.dustcontroluk.co.uk, or for more information on The SHE Show South, visit https://thesheshow.com/south/.