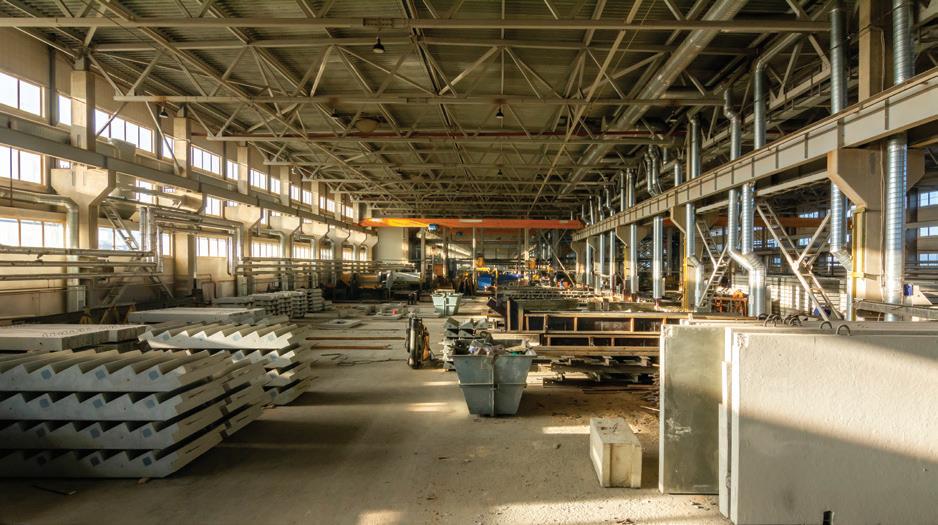
5 minute read
A SMALL BUSINESS GUIDE TO CONSTRUCTION ASSET MANAGEMENT
By DP Taylor
In construction management, your assets are indispensable. After all, you cannot efficiently clear a site without a bulldozer, you cannot quickly slice wood without a circular saw and you cannot easily share documents and pictures with stakeholders unless you have a computer.
Advertisement
Assets make a project possible and if you do not manage those assets properly, you risk running into problems that could set your project back or wipe out your profit margins. As anyone in construction project management knows, that happens all the time – and it is never a good feeling.
If you have ever been frustrated by a backhoe that was not available when your team needed it, or an over-expenditure on tools you ultimately did not need, it is time to get a handle on asset management.
Overview: What is construction asset management?
Construction asset management refers to the process of keeping track of equipment, vehicles, computers and facilities on a job site. It is a sub-set of construction resource management, which includes all resources used by a construction firm – not just assets.
Because assets are the driving force behind the activities on a job site, construction managers must manage them efficiently in order to eliminate waste and make sure workers have access to the right assets at the right time. This will prevent cost increases and delays to the construction schedule.
Types of assets in construction
Construction assets come in many shapes and sizes, but they generally have one thing in common: they are non-consumable objects necessary for the completion of your project.
1. Construction equipment
Construction equipment represents the high-expense assets companies use to do the heavy work on a job site, such as cranes, bulldozers, excavators, backhoes, trenchers, pavers and a host of other specialised equipment, depending on what kind of construction work is being done.
The size, value and fuel usage of these assets make them particularly important to manage.
2. Vehicles
While you might be tempted to lump all wheeled assets in with construction equipment, you should keep vehicles such as cars and trucks separate, particularly if they are used off the job site for running errands or general transportation.
3. Computers
Once a rare sight in construction, computers are ubiquitous on todayʼs job sites. Whether they are office computers, tablets or even mobile phones and wearable electronics, computers should be managed carefully not only because of their value and importance, but because of cybersecurity concerns.
4. Tools
You may be tempted to skip monitoring every hammer or screwdriver in your arsenal, but if a worker needs a tool to complete a project and has to go looking for it, that is costing you valuable work hours over the life of a project.
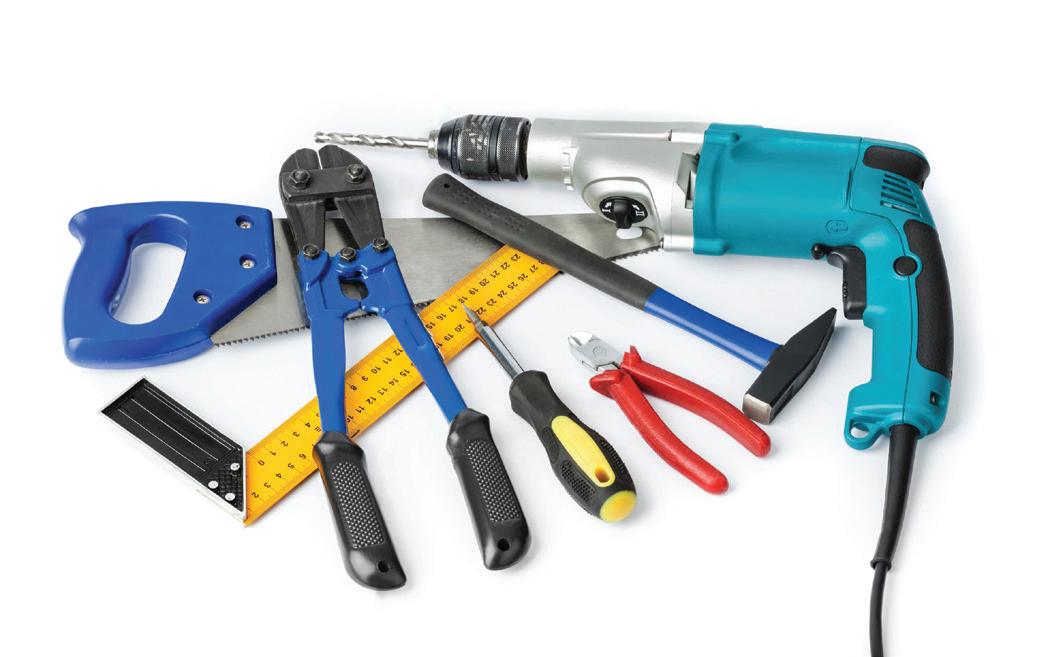
By keeping an accurate tool inventory and tracking their usage, you can ensure that your workers have everything they need at the right time. Moreover, some specialised tools are expensive and insured and should be tracked for that reason alone.
5. Facilities
Every job site has small facilities to help workers do their jobs, such as trailers, portable toilets and washing stations. These are also assets and should be tracked as part of your asset management plan.
Asset management strategies for construction companies
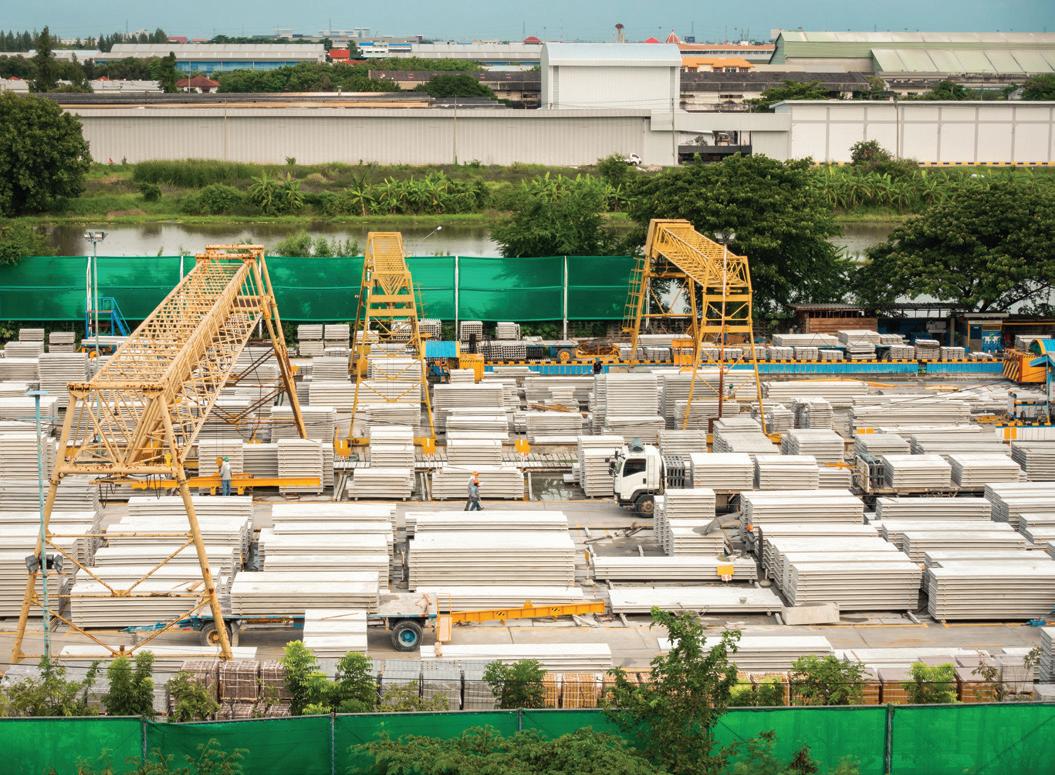
When it comes to managing these resources to maximise efficiency, these five strategies are critical:
1. Use software
Asset management becomes complicated quickly and, considering how important it is to your bottom line, you should use specialised software, rather than relying on spreadsheets.
Todayʼs construction management software uses GPS equipment-tracking to tell you where each asset is, allows workers to clock them in and out, and does many other tasks that would simply be too much for a manager to manually track.
Free asset-tracking software exists, although you will have to do without the more advanced tools.
2. Track the life of your assets
Assets create an additional challenge that labour, materials and other resources do not, so you need to track their lifespans and plan accordingly. Assets are only useful for a certain time-frame which differs greatly, depending on the type of asset and how gently it is used.
By accurately predicting asset life, you can calculate when new equipment will be necessary. This will help to avoid lag time between when equipment breaks down and when you buy a replacement. It can also prevent safety incidents caused by ageing equipment.
Tip: Factor in total life-cycle costs in addition to the purchase price. Determine how much fuel the asset will use, how much you will spend monthly on maintenance and any other costs you can think of.
3. Make someone accountable for the asset
By making an individual responsible for the maintenance and usage of the asset, you will make it easier to track.
If you have a team of three workers who use a backhoe regularly, for example, assign the most senior worker the responsibility of checking fuel levels, keeping up with the maintenance schedule and logging hours. Create a manual on how to do that, or provide access to your software to help them.
Tip : Set up a regular accountability schedule with the designated individual. Make it clear what information you want them to show you, such as usage logs and maintenance events. Follow up and meet with that individual on the assigned dates to ensure that they are tracking equipment and other assets as agreed.
4. Review assets regularly
As the construction manager, the buck stops with you. Now that you have assigned people to track your assets and you have drafted a plan that takes lifespan into account, you should review your assets on a regular basis to determine whether they are being maintained and that they are depreciating at the rate you expected.
If you find irregularities, identify why and whether you need to make changes – either to your process or to your expectations.
Tip: Create a checklist to increase the efficiency of your review. Set aside a couple of hours every few weeks or so to go through that checklist at the job site. Allot some extra time for meetings with the equipment managers, should you come across irregularities.
Make adjustments
If you are closely tracking assets and regularly reviewing them, you will notice some things that need changing. Perhaps equipment is declining at a faster rate than expected and there is nothing you can do except adjust your expectations in your next project plan.
Or perhaps equipment is being misplaced too frequently and you need a software platform that does a better job of tracking. Either way, regularly make adjustments and tweak your operations to improve your asset management.
Tip: Set aside a quarterly meeting to review the asset management plan with stakeholders and brainstorm ways of improving it.
Software will give you asset management ideas
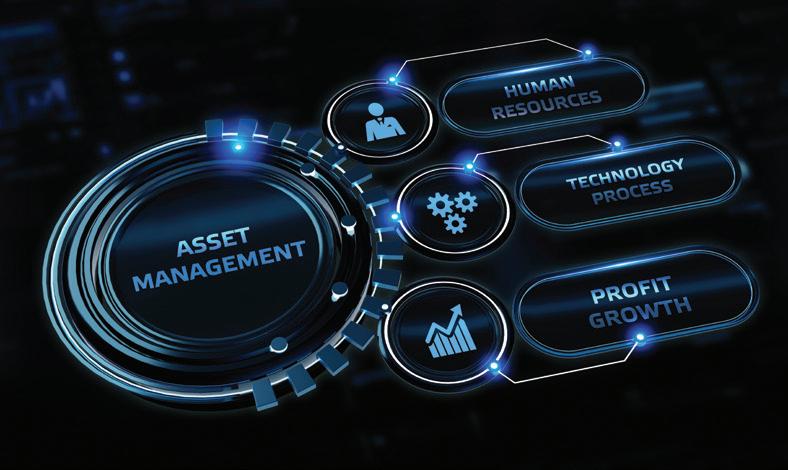
A good way of working out how to manage more effectively is by seeing how today's software does it. Give a few construction software options a try and evaluate their asset management tools. See how their equipment tracking system works in monitoring equipment asset resources.
Then evaluate your own processes to identify the differences in your approaches and settle on the methods that work best for you and your business.