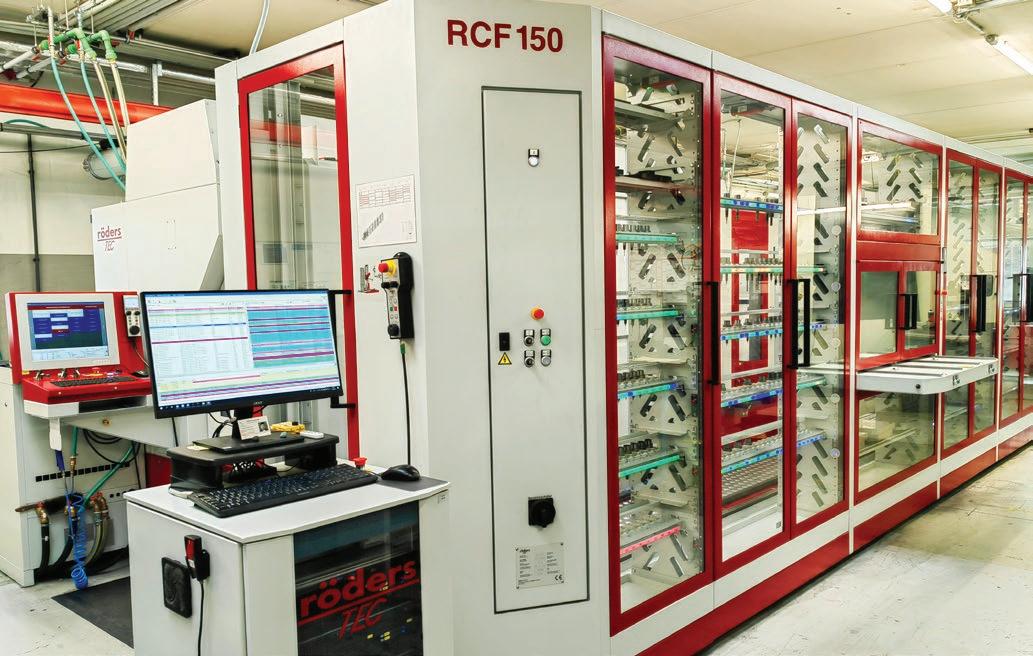
9 minute read
Izrada kalupa – turbo pojačanje pune automatizacije
from IRT3000 АДРИА #5
Švajcarska grupa SFS, koja posluje širom sveta, snabdeva brojne industrijske delatnosti sofisticiranim komponentama i sklopovima. Kako bi obezbedila kvalitet, kompanija se oslanja na sopstvenu radionicu u gradu Korneuburg (Austrija) za proizvodnju kalupova za injekciono presovanje. U ovoj radionici je početkom 2022. godine puštena u rad integrisana proizvodna linija sa sistemima za elektroerozionu obradu (EDM), glodanje, čišćenje delova i visoko precizno merenje. Razgovarali smo sa rukovodiocem radionice o iskustvu stečenom tokom ovog izuzetno izazovnog projekta.
„Grupa SFS snabdeva partnere u visokotehnološkim industrijama (npr. proizvodnja automobila, elektronika, avio-industrija, građevinska industrija i medicinska tehnologija) preciznim delovima ili kompletnim sklopovima napravljenim od plastike i/ili metala”, objašnjava Heinrich Ruckenbauer, rukovodilac odeljenja za izradu kalupova u kompaniji SFS u gradu Korneuburg (Austrija). Njegovo odeljenje fokusira se na proizvodnju složenih kalupa za injekciono presovanje za pogone grupe u Austriji i Mađarskoj. Plastični delovi koji se proizvode moraju da ispune najstrože zahteve. Ovo često podrazumeva bezbednosne funkcije, kao što su kočnice ili zatezači kaiša u automobilima. Kod komponenti za enterijer vozila, kao što su poluge za upravljanje vratima, površine moraju da budu najvećeg kvaliteta. Greške mogu da dovedu do ogromnih posledica, na primer ako bezbednosni delovi otkažu. Zahtevi u pogledu kvaliteta koje ovo odeljenje proizvodi samim tim su veoma strogi, pošto bi bilo kakav nedostatak na kalupu neizbežno mogao da se odrazi na proizvod.
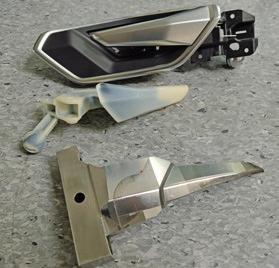
Dodatni izazovi
„Pored čisto geometrijske preciznosti delova proizvedenih kalupima za injekciono presovanje, za nas su ključni i troškovi i tehnologije”, dodaje H. Ruckenbauer. Kao i svi dobavljači, SFS treba da se istakne doslednim i beskompromisnim kvalitetom i cenama u odnosu na druge dobavljače sa ponekad znatno nižim troškovima rada. Pošto kalupi predstavljaju važnu stavku u rashodima, njegovo odeljenje mora stalno da traži načine da smanji troškove. Zato je ovo postalo imperativ u pogledu povećanja produktivnosti automatizacijom. Kompanija posledično traži rešenje koje bi omogućilo potpuno automatizovan rad sa više različitih tehnologija i najmanje 5.000 radnih sati godišnje.
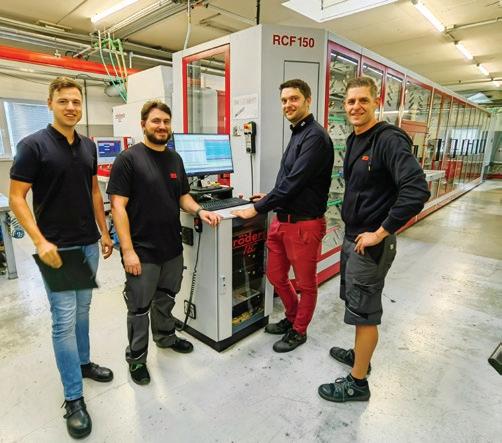
Još jedan aspekt bili su strogi zahtevi u pogledu palete materijala koji bi mogli da se obrađuju mašinski. Ovo se naročito odnosi na komponente alata napravljene od volfram-karbida. Udeo visoko abrazivnih mineralnih komponenti u savremenim plastičnim materijalima često dostiže i do 75%, što prebrzo dovodi do trošenja konvencionalnih čeličnih alata. Komponente od volfram-karbida u ovakvim slučajevima znatno produžavaju vek trajanja alata.
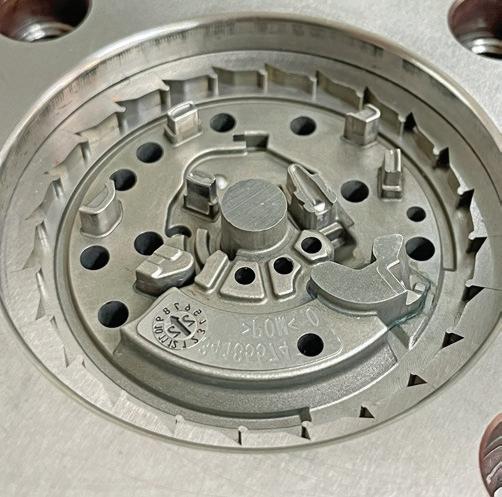
Potpuna rekonstrukcija proizvodnje kalupova
„Iz tog razloga smo želeli da našu prethodnu opremu, koja se sastojala od pojedinačnih mašina, zamenimo savremenom, potpuno automatizovanom proizvodnom linijom koja bi mogla da izvršava sve naše zadatke, uključujući sastavljanje steznih pribora”, kaže H. Ruckenbauer. Fokus je bio na najvećoj preciznosti mašina koje treba isporučiti, uključujući proizvodnju glavnih delova (mastera), kao i integraciju tehnologija glodanja, elektroerozione obrade, čišćenje obradaka i njihovo merenje pomoću automatizacije. Nakon temeljite preliminarne kontrole, doneta je odluka u korist rešenja koje je predložila kompanija Röders iz grada Soltau. Njihovi centri za glodanje postižu maksimalnu preciznost, a mogu da rade i sa volfram-karbidom.
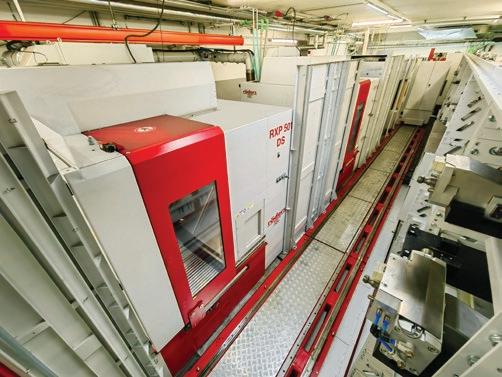
Osim komponenti kalupa za injekciono presovanje, nova linija proizvodi i držače, merne pribore, kao i glavne delove (mastere). Pojedinačne mašine grupisane su jedna za drugom, a opslužuje ih istančan sistem za rukovanje RCF 150 kompanije Röders na linearnoj šini dužine preko 11 metara. Linija sadrži petoosnu glodalicu Röders RXP 501 DS i troosnu glodalicu Röders RXP 501, EDM sistem Sodick AG 60 L, stanicu Erowa RoboSpa za automatsko čišćenje i koordinatni merni sistem Hexagon TIGO SF.
Na suprotnoj strani su police s glodalima, robotski hvatači kao i palete Erowa za elektrode i obratke u tri različite veličine. RCF robot radi sa obracima mase do 150 kg. Celokupnom linijom upravlja se preko sistema RMSMain za upravljanje nalozima, koji je takođe razvila kompanija Röders, a koji prihvata NC programe od CAM sistema (Visi) kroz automatski uvoz podataka.
Naročito se ističe kompaktnost sistema za rukovanje – zahvaljujući posebnom projektovanju ruke sa obrtnim spojevima, širok je samo 1,5 metar. Prema rečima rukovodioca radionice, ovo je primetna prednost sistema Röders ako se uzme u obzir ograničena podna površina u radionici.
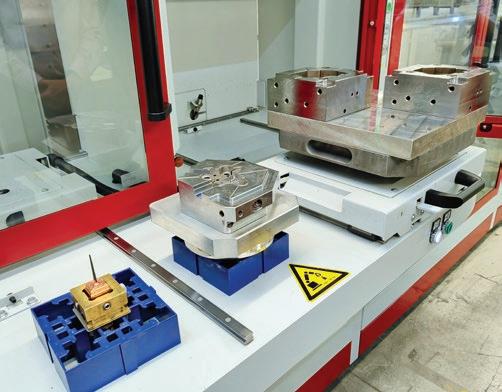
Povećanje proizvodnje u roku od samo mesec dana
„Pre nego što smo doneli odluku, dobronamerno smo upozorili da bi moglo da potraje do šest meseci da dođemo do okolnosti koje bi nam omogućile proizvodnju pomoću sistema”, uz osmeh navodi H. Ruckenbauer. Ipak, komande i upravljanje nalozima bili su toliko prilagođeni korisniku, a obuka toliko efikasna, da smo mogli da proizvedemo prve pojedinačne delove glodanjem već dve sedmice nakon puštanja u rad. Još dve sedmice je potrajalo do početka potpuno automatskog rada. Nakon toga, zahvaljujući stručnoj telefonskoj podršci kompanije Röders, linija je brzo povećala proizvodnju na ciljnih 400 radnih sati mesečno. Svakako je bila prednost to što je kompanija Röders obezbedila sve ključne komponente linije – glodalice, manipulacionog robota, kao i centralni program za upravljanje nalozima i program za otpremanje. H. Ruckenbauer kaže da je time smanjen obim posla u pogledu nužnosti implementacije sučelja za sisteme različitih proizvođača, što često podrazumeva veći rizik za greške i kašnjenja.
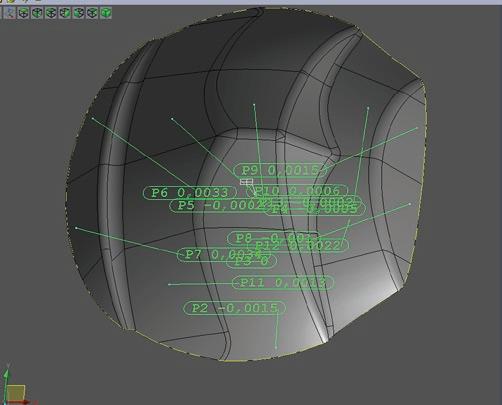
Kompaktan i svestran – linearni manipulacioni robot RCF 150
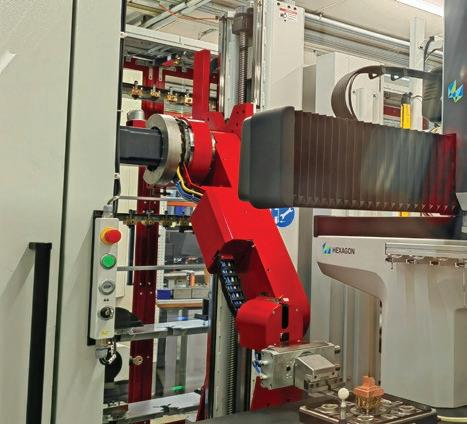
U većini radionica nedostaje prostora. Prilagodljiv i tanak manipulacioni robot RCF 150 projektovan je da doprinese prevazilaženju ovih ograničenja. Prenosi i obratke i alate. Širinom ramena tek jedan metar i sa izuzetno dinamičnim pogonima, pomera se po svojoj linearnoj šini između mašina i niza polica širine tek 50 cm. Međutim, njegova ruka dopire do 1.750 mm duboko u radni prostor pojedinačnih mašina, čak i uz maksimalno opterećenje (150 kg). Zahvaljujući ovom konceptu kojim se štedi prostor, moguća je realizacija veoma kompaktnih automatizovanih linija.
Budući da je konstruisan modularno, sistem se može brzo montirati i raširiti po fazama. Hvatači u stanici se mogu zameniti u bilo kom trenutku. Maksimalne dimenzije obratka su 320 mm × 320 mm. Dostupna je i opcija identifikacije čipom. Robotom se upravlja pomoću softvera za upravljanje nalozima na host računaru, ali se za rad pojedinačne mašine njime može upravljati preko sistema za upravljanje mašinom.
Ključna uloga radne snage
„U ovakvim projektima zaposleni su izuzetno važni. Bez njihovog pristanka i aktivnog uključivanja, uspeh projekta ne bi bio toliko upečatljiv.” podseća H. Ruckenbauer. Njegov tim nije trebalo samo da se upozna sa novim sistemom upravljanja, nego je bilo potrebno da usvoji novi način organizacije rada. Prethodno bi određeni zaposleni samo izvršavao određene segmente u lancu procesa, kao što je CAM programiranje, glodanje ili erodiranje. Međutim, oni su sada odgovorni za sprovođenje svih neophodnih koraka koje treba izvršiti za dati obradak, od CAM programiranja do pokretanja završnog merenja.
U tom pogledu morali su da napuste ustaljene navike. Ranije, ako zaposleni ne bi postigao željeni rezultat u dobijenom NC programu, obično bi „na brzinu” izmenio nekoliko nizova neposredno na mašini. Ovaj deo je tada bio prihvatljiv, ali nije bilo povratne sprege sa CAM arhivom, a time ni reproduktivnosti proizvodnog procesa, ako bi se odgovarajuća komponenta ponovo proizvodila. Od uvođenja nove linije, svaki član našeg tima saglasan je da ovakve izmene više ne bi trebalo izvršavati ručno, već ih uvek treba najpre primeniti u CAM sistemu. Ćelija pruža optimalnu podršku, pošto se svi neophodni radni koraci, kao što su čišćenje i pranje, uvek izvršavaju bez ručnih intervencija.
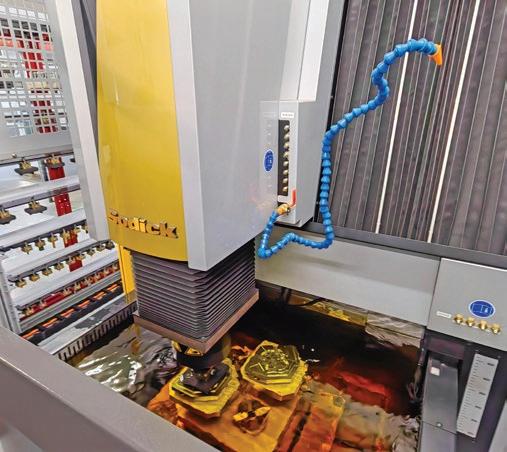
„Izuzetno zadovoljni” rezultatima
„Nakon više od godinu dana rada mogu da kažem da smo izuzetno zadovoljni rezultatima projekta”, sumira H. Ruckenbauer. Kada je reč o preciznosti, napravljen je izvanredan korak napred. Tamo gde je tim obično govorio o stotim delovima milimetra, sada se rasprave svode na mikrometre. Izmerene vrednosti delova danas se navode sa četiri decimalna mesta, čak i kod delova koji su napravljeni na glodalici Röders RXP 501 DS sa pet osa. Stopa odbijanja/ pritužbi takođe se smanjila za više od 50% od uvođenja nove linije.
Tačnost linije sada se rutinski pažljivo prati, a provera kalibracije pokreće se u sistemu svaka tri dana kao poseban zadatak. Utvrđene su i neke zanimljive korelacije. Na primer, tolerancije su znatno manje kada se palete smenjuju automatski pomoću robota u odnosu na tolerancije prilikom ručne promene. Ispostavilo se i da su glodala CBN za kopirno glodanje preciznija od karbidnih glodala prilikom mašinske obrade slobodnih površina mikrometarskom preciznošću.
Pored toga, došlo je do znatnog skoka u produktivnosti od oko 30% uz isti broj zaposlenih. Takođe smatra da treba istaći i proizvođačev visok nivo spremnosti za rad. U poređenju sa situacijom pre uvođenja ove automatizovane proizvodne linije, došlo je od ogromnog unapređenja u svakom pogledu.