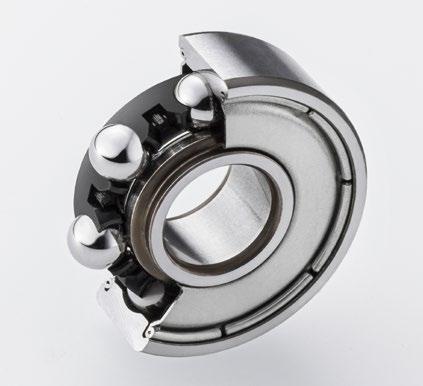
16 minute read
LOS SOPORTES HIDRÁULICOS Y LAS BOQUILLAS DE REDUCCIÓN DE SECO FACILITAN LA SUJECIÓN
De Las Herramientas
Los fabricantes deben superar los retos específicos del mecanizado de forma rentable. Con este objetivo en mente, Seco ofrece su completa gama de soportes hidráulicos y boquillas de reducción en tres versiones, cada una de las cuales puede adaptarse a diferentes tamaños de sanco, lo que permite reducir el inventario de herramientas. Gracias a una sujeción del sanco de la herramienta de 360° y un centrado preciso, los soportes hidráulicos y las boquillas de reducción de Seco garantizan una fiabilidad y un rendimiento de mecanizado excepcionales y la máxima vida útil de la herramienta.
Versátil y accesible
Para una sujeción de herramientas sencilla, versátil y accesible, Seco ofrece tres versiones de soportes hidráulicos: HC Convencional, HCr reforzado y HCS Slim. La versión convencional HC ofrece una sujeción precisa para el taladrado, el escariado y el fresado ligero. La versión HCr reforzado es una solución universal que proporciona una sujeción eficaz para cualquier tipo de aplicación, desde HSM hasta HPM, y para todo tipo de sancos de herramientas, como cilíndricos, Weldon y Whistle Notch. el soporte HCS Slim es ideal para acceder a cavidades de piezas profundas y estrechas durante el mecanizado de 5 ejes a altas velocidades.
«Los sistemas de sujeción de herramientas complejos no solo requieren un cuidado y una formación especiales para evitar lesiones al operador, sino que además acarrean tiempos de inactividad y costes adicionales», afirma el responsable de productos de Seco, Yves Heitz. «Los soportes hidráulicos y los casquillos reductores de Seco eliminan el riesgo de uso y el mantenimiento adicional de la herramienta para permitir al usuario realizar un corte más rápido y, al mismo tiempo, aumentar la versatilidad de sujeción de la herramienta con menos accesorios».
Para disponer de una mayor flexibilidad para adaptarse a una gran variedad de tamaños de herramienta de corte, los casquillos reductores ranurados 05FHC para soportes hidráulicos permiten el uso de sancos de distintos diámetros con un mismo soporte. Proporcionan refrigeración periférica o a través de la herramienta y funcionan con herramientas de tamaño métrico o en pulgadas.
Salto mínimo y alta precisión
Según Heitz, a altas velocidades del husillo, resulta imprescindible controlar el salto en el portaherramientas. Al mecanizar a velocidades de hasta 25 000 rpm, por ejemplo, los soportes hidráulicos y los casquillos reductores de Seco minimizan el salto y la vibración que se ocasiona. Los usuarios obtienen una perfecta sujeción de la herramienta sin necesidad de adquirir soportes especiales adicionales.
Para mantener la vibración bajo control, los soportes hidráulicos de Seco incorporan cavidades interiores en las que el aceite genera fuerzas de sujeción de la herramienta a 360° y actúa como un sistema natural de absorción de las vibraciones, que se conecta con el simple giro de un tornillo hexagonal. Además, los casquillos reductores se comprimen de manera uniforme y completa alrededor de los mangos de las herramientas para obtener un centrado preciso y una mayor fuerza de sujeción.
Los casquillos reductores ranurados están disponibles en versiones de refrigeración periférica y estanca, y los soportes hidráulicos son compatibles con todas las herramientas de Seco. Los soportes son compatibles con todas las conexiones a husillo de la herramienta de mecanizado más comunes, incluyendo HSK, DIN, bT, bT Taper/Face, CAT, CAT
Taper/Face y los sancos cilíndricos rectos. Las herramientas de sanco en mm se amarran directamente en el diámetro interior del soporte, mientras que los sancos en pulgadas se sujetan mediante el uso de casquillos reductores.
Para obtener más información sobre las características y especificaciones de los soportes hidráulicos y los casquillos reductores de Seco, póngase en contacto con un representante local de Seco o visite https://www.secotools.com/article/m_7244
INFORME TECNOLÓGICO: ¿RFID O CÓDIGO DE BARRAS?
¿HA HABIDO UN PUNTO DE INFLEXIÓN EN LAS SOLUCIONES DE IDENTIFICACIÓN UTILIZADAS EN AUTOMATIZACIÓN?
Dos tecnologías de identificación, RFID y código de barras, están compitiendo por el favor de los usuarios con la promesa de desempeñar un papel decisivo que haga realidad la automatización de la producción transparente y la cadena de suministro con el fin de cumplir los requisitos de la Industria 4.0. ¿Pero qué tecnología es la adecuada en la actualidad? ¿El código de barras ha sobrevivido más allá de su finalidad prevista? Este artículo analiza de forma crítica la situación actual de las modernas tecnologías de identificación.
¿r ecuerda cómo eran las cosas hace 20 años? Por entonces reinaba una atmósfera de positividad y la tecnología rFID disfrutaba de un verdadero boom? rFID (radio Frequency Identification) en realidad no es una tecnología nueva. La física en la que se basa se desarrolló a principios del siglo XX. Los primeros sistemas y productos para aplicaciones industriales ya estaban disponibles en la década de 1980 y consistían principalmente en soluciones propietarias en el rango de baja frecuencia (125 kHz). Las aplicaciones típicas por entonces, como identificación de animales, inmovilizadores electrónicos de vehículos e identificación de vehículos, siguen siendo vigentes y se han consolidado por completo.
el clásico y bien conocido código de barras se ha venido utilizando desde la década de 1970. en aquella época era una tecnología recibida con cierta controversia. Hoy cuesta creer que la identificación única de un producto por medio de un código de barras impreso provocara discusiones acerca de la continua vigilancia y la protección de datos. entretanto, el código de barras se utiliza en todas partes. Un mundo sin códigos de barras para etiquetar los productos, bien sea en el sector de consumo o de paquetería cuando el volumen de bienes comercializados por internet se ha multiplicado, es simplemente inimaginable.
el enorme protagonismo del código de barras, que es con mucha diferencia el medio de identificación más importante, se debe a su sencillez de uso. ello se debe a que es una etiqueta impresa, a su coste extremadamente bajo y, por último pero no por ello menos importante, su estandarización a escala mundial. el código de barras, que ya está disponible en varios formatos (como Data Matrix y código Qr), se ha convertido en un compañero omnipresente en nuestra vida diaria así como las aplicaciones industriales. No se vislumbra el fin de su continuo desarrollo, pero el código de barras tiene sus límites: para ser leído necesita una línea de visión directa. Además, una vez impreso el código de barras, el contenido de los datos, es decir, la información codificada, ya no se puede cambiar. es aquí cuando entra en escena rFID. esta tecnología fue desarrollada para hacer todo aquello que puede hacer el código de barras pero mucho mejor, y junto con otras ventajas convincentes lo ha ido superando de manera lenta pero segura. Las iniciativas de las compañías industriales que han intentado optimizar sus procesos mediante el uso de rFID, especialmente en la cadena de suministro, junto con los proveedores de tecnología que han propagado el uso de rFID en casi todas las áreas de aplicación, impulsaron el auge de rFID a principios del presente siglo. Se extendió la impresión de que rFID valía para todas las tareas de identificación y que a medio plazo sustituiría al código de barras. Mirando atrás, hay que decir que esta previsión tantas veces anunciada estaba llamada a equivocarse porque se basaba en muy poca experiencia práctica y en la subestimación de los límites físicos de la tecnología. e stos productos incorporan modernas interfaces de comunicación como buses de campo basados en ethernet o oPC UA , y por tanto son idóneos para cumplir los requisitos de la Industria 4.0, así como para ofrecer la capacidad de red y en la nube que necesita Internet Industrial de las Cosas.
Tras muchos años de mejoras técnicas y la larga experiencia acumulada en innumerables proyectos piloto en diferentes sectores y aplicaciones, r FID ha evolucionado hasta convertirse en una tecnología de identificación consolidada y fiable que puede aprovechar sus ventajas respecto al código de barras ya que las condiciones de la aplicación han sido analizadas minuciosamente y se han efectuado cálculos precisos de coste-beneficio.
Asimismo es bien conocido el funcionamiento de rFID bajo diferentes condiciones del entorno. Los sistemas modernos de UHF (860-960 MHz), por ejemplo, se pueden optimizar para casi todas las aplicaciones gracias a su mayor sensibilidad y sus numerosas opciones de configuración. Como resultado de ello, el uso de rFID en numerosos sectores industriales, como aplicaciones de rastreo y localización en automoción, monitorización total de procesos de producción y monitorización de ciclos de contenedores en logística, ha demostrado ser una tecnología potente y fiable una y otra vez y se ha consolidado como el estándar de facto para tareas de identificación. Aun así el código de barras sigue siendo el más utilizado en todos los sectores. Sus aplicaciones potenciales son casi ilimitadas. en muchos casos, sencillamente no se necesitan las ventajas que añade rFID.
Además, en el segmento de los escáneres 1D/2D, las cámaras inteligentes y los sistemas de visión, el mercado ahora ofrece productos extremadamente efectivos y concebidos a medida de muchas aplicaciones en sectores industriales.
Resumen
No ha habido un punto de inflexión. el mundo de las tecnologías de identificación se sigue caracterizando por la coexistencia pacífica de dos sistemas muy diferentes físicamente, cada uno de los cuales tiene sus propios méritos y que se complementan a la perfección en muchas aplicaciones. Se puede afirmar que el código de barras es el único medio de identificación utilizable universalmente y aceptado en todo el mundo, y cuya tecnología está muy estandarizado ya ha demostrado ser extremadamente fiable.
Las siguientes áreas siguen estando dominadas por la tecnología r FID: entornos exigentes (por ejemplo, sometidos a unas condiciones ambientales adversas con un alto grado de contaminación), detección simultánea de muchos soportes de datos en un grupo o reprogramación constante de etiquetas rFID en sistemas retornables dentro de un ciclo logístico cerrado.
Dado que una etiqueta rFID integra un circuito electrónico formado por una estructura de antena metálica y un microchip de silicio, el código de barras siempre tendrá la ventaja de tratarse de una tecnología con un menor coste de fabricación. especialmente en el caso de aplicaciones de gran volumen con soportes de datos de un solo uso, a menudo resulta muy difícil justificar el uso de etiquetas rFID desde el punto de vista del coste.
También vale la pena destacar que la sostenibilidad de las etiquetas rFID es un asunto muy vigente que se debe tener en cuenta al decidir qué tecnología utilizar. Las etiquetas rFID obtenidas a partir de materias primas están sometidas a la misma normativa de reciclaje que otros componentes y equipos electrónicos.
La elección entre rFID o código de barras no es inmediata. en la actualidad tenemos la suerte de optar por la tecnología que mejor se adapte a cada aplicación. Ambos sistemas han alcanzado la madurez tecnológica necesaria para ello. recae sobre nuestra responsabilidad tomar la decisión correcta en función del asesoramiento profesional y de un análisis minucioso.
Autor:
Oliver Pütz-Gerbig
Leuze electronic GmbH + Co. KG
Product Center Ident & Vision
www.leuze.com
Las Innovaciones De Nsk Contribuyen A La Sostenibilidad De La Industria
Los fabricantes de toda Europa están experimentando la gran presión económica que representa el aumento de las facturas de energía, lo que crea un dilema: absorber el coste o transferirlo a los clientes. Ninguna de las opciones es particularmente fácil. Como resultado, ahora es el momento ideal para que las empresas reduzcan sus costes de funcionamiento con máquinas correctamente alineadas y soluciones de rodamientos energéticamente eficientes de NSK.
Parece poco probable que se reduzca el coste de la energía. Por ello, un número cada vez mayor de empresas industriales recurren a las últimas tecnologías de control de movimiento como medio para mejorar los niveles de eficiencia y así poder reducir las facturas. Los rodamientos son un ejemplo claro de componentes que pueden mejorar directamente la eficiencia energética de la maquinaria, al igual que la configuración optimizada de ejes y correas. La alineación óptima entre una máquina y un motor eléctrico, por ejemplo, permite un funcionamiento más eficiente desde el punto de vista energético.
La alineación importa
Las estimaciones sugieren que más del 50% de las máquinas y equipos industriales trabajan con ejes desalineados en relación con la normativa ISo. Pero ¿cuál es la causa de la falta de alineación? bien, los problemas generalmente comienzan cuando los ejes acoplados se colocan de manera que su espaciado o juego libre están fuera de los límites aceptables. Como consecuencia, los ejes trabajan descentrados, lo que conduce a una mayor carga, una generación excesiva de calor y un mayor consumo de energía.
Los indicios de una desalineación son un aumento de la temperatura, vibraciones, pernos de acoplamiento flojos y fugas excesivas de lubricante en los sellados de los rodamientos. es casi seguro que cualquier máquina o sistema que muestre estos signos tendrá un efecto negativo en la rentabilidad final como consecuencia de un mayor consumo de energía.
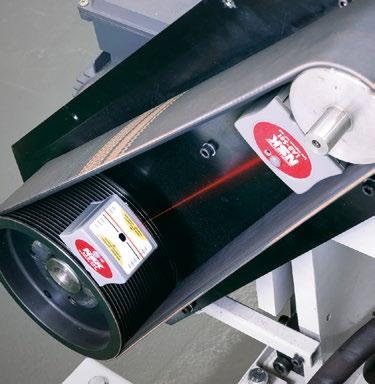
NSK ofrece herramientas de alineación láser avanzadas para ejes (LAS-Set) y correas (LAb-Set) que ayudan a garantizar una alineación rápida y perfecta en todo momento. Los equipos LAS-Set utilizan láseres de dos líneas para facilitar el ajuste, incluso en grandes distancias, así como sensores digitales de alta resolución para conseguir una gran precisión. LAb-Set alberga dos transmisores láser lineales, lo que permite que la alineación sea mucho más precisa que las soluciones de un solo cabezal láser.
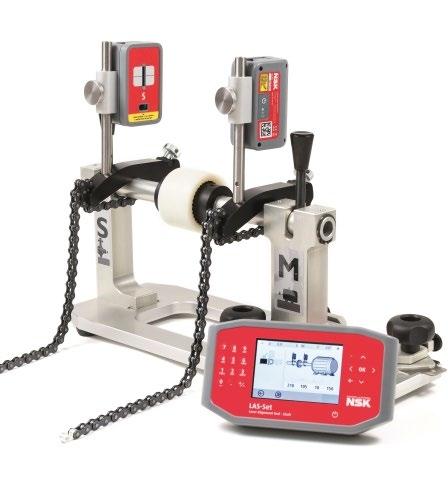
La adopción de estas herramientas no solo contribuye a la eficiencia energética, sino que también reduce el desgaste de piezas críticas de la máquina, como acoplamientos y sellados, lo que minimiza los períodos de inactividad de la máquina y maximiza la productividad.
Las líneas de producción que aprovechan los beneficios de las herramientas de alineación láser de NSK han registrado ahorros de energía de hasta un 17%, lo que permite un rápido retorno de la inversión (roI).
El reto del cero neto o tra innovación es la grasa eA7 de NSK, que reduce la fricción interna, aumenta la eficiencia energética y duplica el intervalo de servicio de los motores eléctricos. Junto con el llenado de grasa optimizado, este lubricante de baja viscosidad y fricción reducida ofrece la solución perfecta para cualquier línea de producción que busque reducir el par, minimizar las pérdidas de potencia y reducir las emisiones de carbono. Además, en comparación con las grasas convencionales, la e A7 ofrece propiedades lubricantes mejoradas en presencia de microvibraciones. o tro factor que contribuye al rendimiento de los rodamientos energéticamente eficientes es la tecnología de sellado sin contacto de NSK. Cuando los ingenieros se dedican a diseñar sistemas de accionamiento energéticamente eficientes, deben estar atentos a los rodamientos porque es fácil comprometer la eficiencia de la transmisión debido a la fricción inherente que se deriva del contacto del sellado convencional. NSK tiene productos que ofrecen propiedades de sellado eficientes sin aumentar el par de fricción ni la temperatura de funcionamiento. entre los últimos desarrollos de NSK se encuentra el primer rodamiento del mundo equipado con una jaula fabricada en un 100% de bioplástico derivado de plantas para su uso en los motores de los ventiladores de equipos de aire acondicionado. estos rodamientos ultrasostenibles ayudan a que el motor del ventilador gire suavemente, lo que reduce el consume energético y permite ahorrar energía. https://www.nskeurope.es/es.html
La eficiencia energética está actualmente en el punto de mira, ya que la industria se enfrenta a la presión de lograr emisiones de carbono netas cero. Si bien el camino hacia el cero neto presenta muchos desafíos, la transición tiene el potencial de impulsar la inversión, la innovación, las ganancias y la creación de empleo. Los motores eléctricos y los sistemas que soportan representan más del 40% del consumo a nivel mundial de electricidad. Teniendo en cuenta estas consideraciones, hay disponibles algunas posibilidades bastante obvias.
NSK fabrica varios rodamientos energéticamente eficientes que no solo ahorran dinero a través de bajos costes de funcionamiento de la máquina, sino que también reducen las emisiones de Co2 y contribuyen a un funcionamiento más sostenible. Un ejemplo de ello son los rodamientos rígidos de bolas de NSK, que reducen las pérdidas de energía hasta en un 80% cuando se implementan en motores eléctricos. en comparación con los rodamientos de bolas de ranura profunda convencional, los rodamientos NSK de alta eficiencia presentan un 60% menos de fricción cuando se utilizan con jaulas de acero y un 80% con jaulas plásticas.
Beneficios para la industria entre los que más se pueden beneficiar se encuentran los fabricantes de equipos originales para automóviles (oeM), que siempre están buscando mayores ganancias en la eficiencia energética en los sistemas de transmisión de sus vehículos. La mayor demanda del mercado de rodamientos de bajo índice de fricción proviene de segmentos como la producción de lavadoras, donde los fabricantes que logran una clase de eficiencia favorable tienden a disfrutar de mayores ventas.
Para indicar un mercado emergente, los rodamientos de NSK también presentan una gran demanda para mejorar el rendimiento en rotación a alta velocidad de los motores de vehículos eléctricos (eV). Aquí, las innovaciones como las jaulas de plástico, más ligeras que las jaulas de acero, ofrecen menores pérdidas mecánicas, y disfrutan de unas excelentes propiedades de autolubricación y un bajo índice de fricción. Todas estas características contribuyen a aumentar la eficiencia energética y la sostenibilidad.
Las soluciones que contribuyen a la sostenibilidad no solo preservan el planeta para las generaciones futuras, sino que también permiten reducir costes y aumentar la rentabilidad final. NSK, con su serie de innovaciones de productos respetuosos con el medio ambiente, está comprometida en alcanzar una sociedad neutra en carbono.
COMPACTAS Y FLEXIBLES: GUÍAS LINEALES CON ACCIONAMIENTOS DE CORREA DENTADA DE NORELEM
Dimensiones mínimas, alta resistencia, poco peso. En este artículo, Marcus Schneck, CEO de norelem, explica cómo las guías lineales con accionamiento de correa dentada aseguran el movimiento automatizado con sencillez y precisión para una inmensa variedad de aplicaciones de ingeniería y en la producción.
Las precisas guías lineales de norelem son una solución estandarizada disponible en almacén para automatizar movimientos lineales de manera fácil. Son adecuadas para su uso en líneas de producción, montaje, embalaje, logística y almacenamiento o en máquinas industriales especiales. Un accionamiento de correa dentada asegura la transmisión suave y sincronizada incluso con cargas pesadas y constantes.
Las guías lineales, conocidas también como ejes lineales, con accionamiento de correa dentada y guía de perfil, ofrecen a los clientes muchas ventajas gracias a su forma compacta y su poco peso, pero al mismo tiempo convencen por su altísima rigidez. e l accionamiento de correa dentada asegura un accionamiento suave y sincronizado. «Los accionamientos de correa dentada se utilizan en accionamientos de posicionamiento, entre otros, porque funcionan de manera repetitiva gracias a su acoplamiento positivo», explica Marcus Schneck, C eo de norelem. «Además, pueden diseñarse para no tener juego, en cuyo caso el accionamiento de correa dentada se utiliza como guía». Gracias a los rodamientos sellados, el mantenimiento de las guías lineales de norelem es muy bajo. Las correas mismas son de fácil acceso para que los usuarios puedan ajustar la tensión o sustituirlas si fuera necesario. Las longitudes de carrera estándar llegan a los 1960 mm, y las guías lineales pueden diseñarse bajo pedido con longitudes especiales hasta 4000 mm.
Diseño de las guías lineales el cuerpo principal está formado por un perfil de aluminio extrusionado autoportante con guía de perfil integrada.
es un perfil estandarizado de la serie I con medidas 60 x 60 mm u 80 x 80 mm. el sistema de guías puede absorber las más elevadas cargas en todas las direcciones, tiene bajo desgaste y ofrece un funcionamiento óptimo cuando se trata de mover grandes masas. La parte exterior del perfil de aluminio tiene ranuras para un montaje fácil y seguro y para sujetar accesorios. el ancho de la ranura es de 6 u 8 mm. Debido a su diseño simétrico el eje lineal facilita la instalación de motores y engranajes en los cuatro costados de las carcasas de rodamiento. La guía de aluminio de la guía lineal tiene cuatro agujeros roscados para el montaje de elementos adicionales. Los orificios adicionales de centrado facilitan un montaje preciso.
Las correas dentadas con elementos de tensión de acero permiten una transmisión de elevada potencia y, al mismo tiempo, una elevada precisión de posicionamiento. La correa dentada discurre por ranuras guía en la parte de arriba del perfil de aluminio y, de esta manera, protege contra suciedad todas las piezas del perfil.
Correas dentadas y poleas de correa dentada
«Las correas dentadas combinadas con poleas de correas dentadas de norelem se utilizan en la ingeniería mecánica, la industria de automatización y en el sector manufacturero», explica Marcus Schneck. «Muestran sus ventajas allí donde se requiere de una transmisión de grandes fuerzas, una elevada aceleración, un posicionamiento exacto y consistencia de sincronización». Su fiabilidad y bajo mantenimiento, su funcionamiento suave y la alta eficiencia energética convierten las correas dentadas en el medio de accionamiento preferido. norelem dispone no solo de una amplia gama de tamaños estandarizados, sino que, además, ofrece correas de transmisión a medida.
Las poleas de transmisión combinadas con las correas forman un accionamiento compacto con una elevada densidad de potencia y una eficiencia excelente. Tienen un bajo mantenimiento y un bajo nivel de ruido, son resistentes a una amplia gama de factores ambientales y, si tienen la longitud correcta, son extremadamente duraderas. «Las correas de transmisión sin fin se utilizan generalmente para soluciones de accionamiento», detalla Marcus Schneck. «Aseguran un perfil consistente de alto rendimiento además de estabilidad longitudinal».
Disponibles también a medida
Las correas a medida, disponibles también en norelem, se utilizan principalmente para convertir el movimiento rotativo de una polea de correa de transmisión en un movimiento lineal. en este caso, los extremos se juntan con las guías en movimiento mediante placas de sujeción. Si las correas se sueldan para formar una correa sin fin, los valores de resistencia se reducen aproximadamente un 50% debido a que los componentes de tensión se separan en el punto de soldadura. Por ello, esto no es adecuado para aplicaciones que requieran de precisión y transmisión de fuerzas altas y uniformes. Las correas se fabrican en longitudes estandarizadas de 100 metros y se pueden suministrar en la longitud deseada. el rango de temperatura para el uso de las correas es de -30 ºC a +100 ºC. Las correas tienen una resistencia química extraordinaria, por ejemplo, a la grasa y el aceite.
Diferentes materiales y perfiles
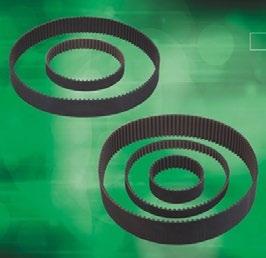
Las correas dentadas están disponibles en norelem con diferentes perfiles y hechas de distintos materiales. Los perfiles en T y AT están hechos en poliuretano (PU) con hilo de acero. en el perfil HTD la parte dentada y la exterior de la correa están hechas en caucho de cloropreno (Cr), y los cables de tensión de la correa de transmisión están hechos de fibra de vidrio. el material de recubrimiento del diente es poliamida.
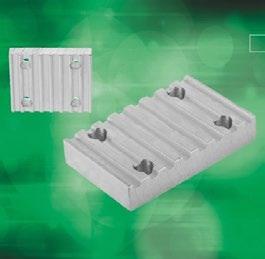
Las poleas dentadas están hechas en aluminio de alta calidad o acero, según el diseño, con las mínimas tolerancias. Las poleas están centradas o pretaladradas. Se pueden mecanizar posteriormente orificios de ajuste y chavetas, si fuera necesario. Además, norelem ofrece ejes dentados con los que se pueden producir poleas dentadas y placas de sujeción propias para sujetar las correas dentadas abiertas.
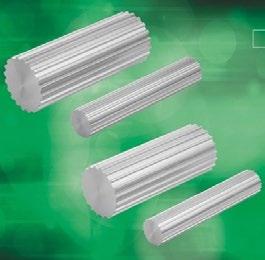
Una amplia gama de accesorios para guías lineales norelem ofrece numerosos de accesorios para las guías lineales con accionamiento de correa dentada. Las mesas con ranuras, por ejemplo, ofrecen un número infinito de opciones de montaje en la guía de carro gracias a las ranuras de perfil. Además, norelem ofrece kits de montaje de motores que proporcionan una solución sencilla y económica de conectar motores eléctricos. Las tapas protectoras protegen contra el polvo de manera efectiva los extremos abiertos de los ejes mientras que los perfiles de aluminio facilitan una conexión sencilla de las guías lineales. Los kits de sincronización permiten la sincronización de dos guías lineales montadas en paralelo. Y por último, norelem dispone en almacén de sensores inductivos de distancia que se pueden montar y atornillar desde arriba.
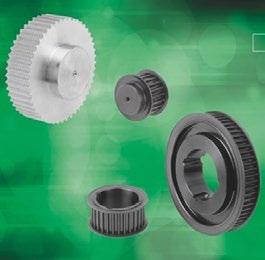
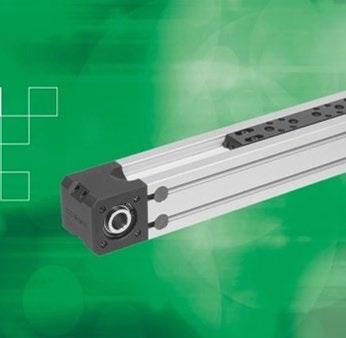
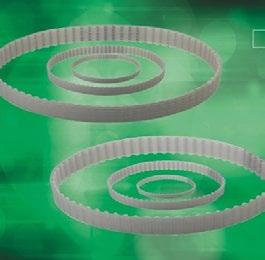
Las unidades lineales con accionamiento eléctrico o neumático también están disponibles en norelem. Son convincentes gracias a sus ventajas específicas según la aplicación. Aquellos que no estén seguros deben consultar con un asesor especializado de norelem. en la base de datos exclusiva y de acceso libre de la norelem ACADeMY los ingenieros pueden informarse acerca de las ventajas de las distintas soluciones en el apartado «eje lineal con accionamiento de correa dentada», y también por libre.
Consulte la gama completa de productos de norelem en www.norelem.es