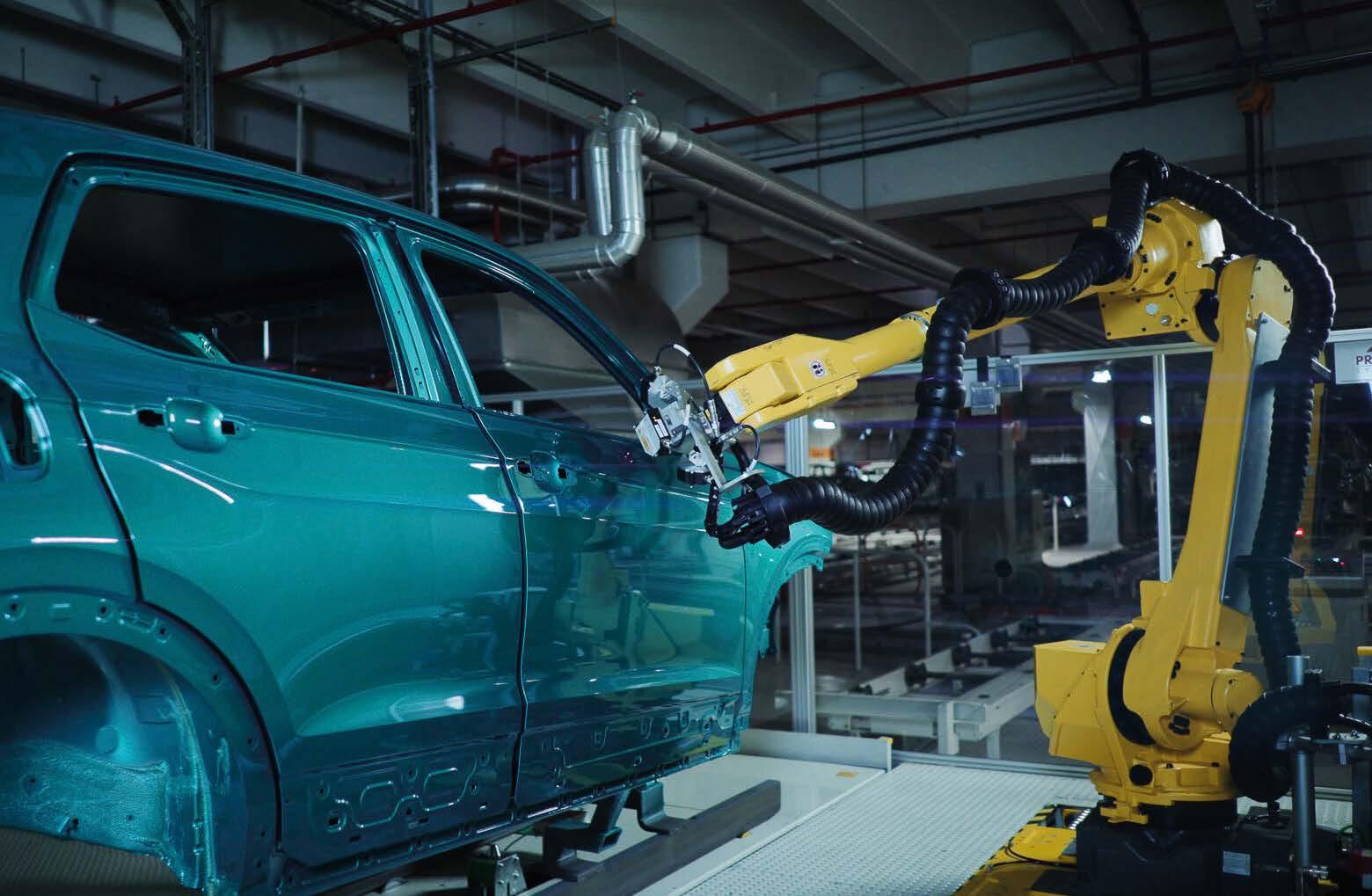
4 minute read
SUCCESS STORIES
fusione, quadri elettrici, mobili, sistemi di riscaldamento, ventilazione e condizionamento, attrezzature sportive e rimorchi.
Semplice integrazione negli impianti esistenti e prestazioni comprovate grazie all’esperienza sul campo
La tecnologia VIANT offre un’elevata praticità nell’esecuzione del processo applicativo. In generale, non è necessario investire ingentemente in costose apparecchiature speciali o eseguire analisi sofisticate. Il rivestimento è applicato per immersione, a cui segue un risciacquo in due fasi con acqua demineralizzata. L’essiccazione avviene a una temperatura di 200° C per 20 minuti. Un’altra caratteristica di questo nuovo processo è la sua elevata stabilità. Si possono evitare difetti dovuti alla mancanza di contatto elettrico tra il componente e la bilancella. Lo spessore è riproducibile e molto uniforme – all’interno e all’esterno. Degno di particolare menzione in questo contesto è il rivestimento completo delle superfici interne (con lo stesso spessore del film secco dell’esterno) e lo spessore dello strato rivestimento notevolmente superiore sui bordi, anche taglienti. Tutto ciò è stato già testato con successo con i clienti.
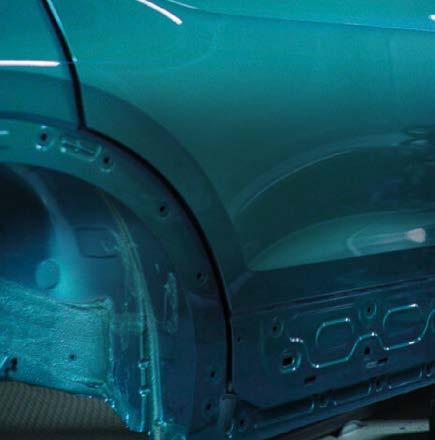
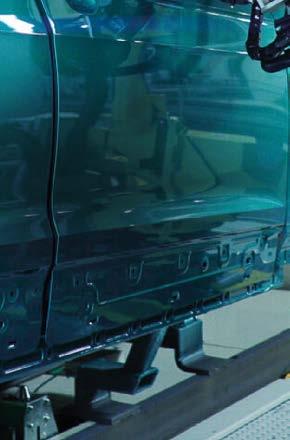


© Chemetall

Il processo VIANT è molto robusto e solitamente facile da integrare nella configurazione di una linea esistente.
Lo spessore dello strato è riproducibile e molto uniforme, all'interno e all'esterno.
Verniciatura a liquido di cilindri idraulici più efficiente grazie all’elettrostatica
KMF Kemptener Maschinenfabrik, produttore di cilindri idraulici di alta qualità per l’industria delle macchine agricole e movimento terra, ha installato un innovativo sistema di verniciatura a liquido con tecnologia di applicazione, dosaggio e miscelazione di WAGNER per aggiornare la precedente linea di verniciatura.
KMF Kemptener Maschinenfabrik è un’azienda di medie dimensioni con sede a Kempten, nella regione tedesca dell’Algovia, specializzata in ingegneria meccanica. Con circa 200 dipendenti, produce dal 2002 cilindri idraulici di alta qualità, piastre a cambio rapido per pale gommate, movimentatori telescopici e gruppi idraulici personalizzati per l’industria delle macchine agricole e movimento terra. L’azienda fu fondata originariamente nel 1954 come stabilimento produttivo di componenti per Fendt. Il suo core business attuale è però la produzione di sollevatori anteriori e posteriori per veicoli commerciali nel settore agricolo. La difficoltà
C’è un alto livello di integrazione verticale nel sito di Kempten: qui avviene anche la verniciatura, che è fondamentale per la protezione dalla corrosione dei cilindri. KMF ha requisiti elevati: superfici non porose e lisce, spessori uniformi e un elevato livello di brillantezza. In passato, i pezzi erano verniciati manualmente. Bernhard Wirnharter, un membro del team di progetto di KMF, ricorda: “La precedente linea di verniciatura risaliva agli anni ‘60 e il processo semplicemente non era più conveniente. Per rendere la produzione più efficiente, ne abbiamo automatizzato delle fasi”. A marzo 2020 l’azienda ha investito circa 4 milioni di euro nella costruzione di un nuovo stabilimento produttivo di 800 m2 che comprende un innovativo impianto di verniciatura a liquido con tecnologie di applicazione, dosaggio e miscelazione di WAGNER. La verniciatura in polvere era fuori questione perché i pezzi montati con, ad esempio, le guarnizioni non avrebbero resistito alle alte temperature richieste per polimerizzarla. L’obiettivo di KMF era quello di fare il miglior uso possibile delle risorse. Inoltre, l’azienda deve applicare un’ampia varietà di colori, poiché spesso i clienti richiedono che i componenti siano verniciati con gli esatti colori dei propri brand, ad esempio nella tonalità “Nature Green” per i componenti Fendt.
La soluzione
Nel nuovo impianto, i pezzi sono trasportati da bilancelle con un tempo ciclo di 7,5 minuti dal tunnel di pretrattamento attraverso un forno di asciugatura e poi nella prima cabina di verniciatura, dove si applica il primer in modo completamente automatizzato. Per ridurre le emissioni di COV, in origine doveva essere utilizzata una vernice a base acqua, per la quale l’aria di alimentazione della cabina avrebbe dovuto essere accuratamente condizionata al fine di applicare la vernice in modo affidabile. Ciò sarebbe però stato un fattore di costo immenso. KMF ha quindi optato per la vernice a base solvente in virtù di una sua più facile gestione. Per risparmiare solventi l’azienda impiega vernici ad alto contenuto di solidi. Poiché sono più produttive di quelle con un contenuto di solidi inferiore, il consumo di primer e di finitura è inferiore, il che porta ad una riduzione dei costi. Il primer è preparato dall’intuitivo sistema di miscelazione e dosaggio elettronico 2K Smart. La misurazione esatta del flusso di materiale tramite celle di dosaggio a ingranaggi e il dosaggio preciso garantiscono rapporti di miscelazione costanti e riproducibili. Per l’applicazione del primer, l’azienda utilizza la pistola AirCoat GA 5000 EAC montata su robot con l’unità di controllo VM 5000. Grazie all’elettrostatica e all’atomizzazione omogenea, si ottiene un’efficienza applicativa molto elevata con poco overspray per i componenti idraulici con un’ampia superficie. Il getto a spruzzo morbido ricopre anche le curve e le aree difficili da raggiungere in modo molto affidabile. La tecnologia AirCoat aiuta quindi a garantire che la vernice a base solvente sia utilizzata con parsimonia, riducendo così sia le emissioni di COV sia i costi dei materiali. La finitura è applicata manualmente in una seconda cabina. Poiché solo il 50% dei pezzi primerizzati richiede il topcoat, KMF
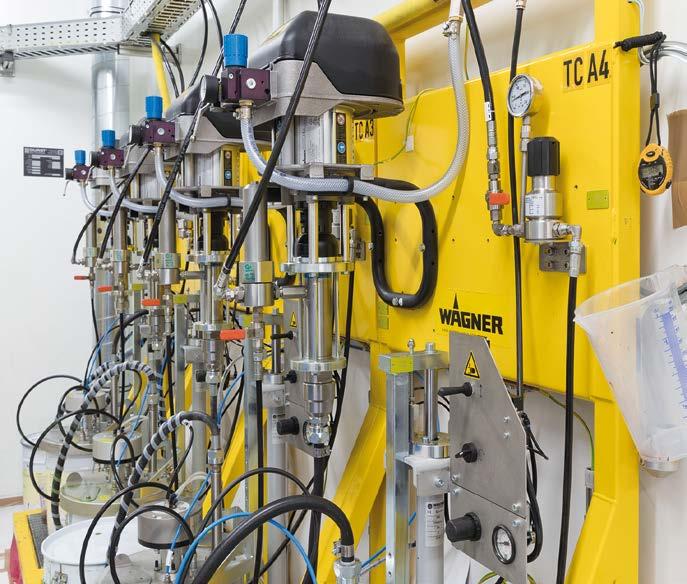
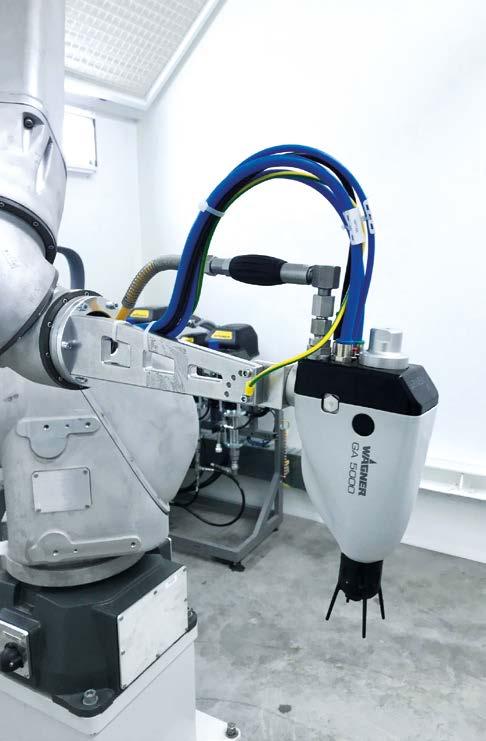
Applicazione del primer nella cabina di verniciatura automatica.
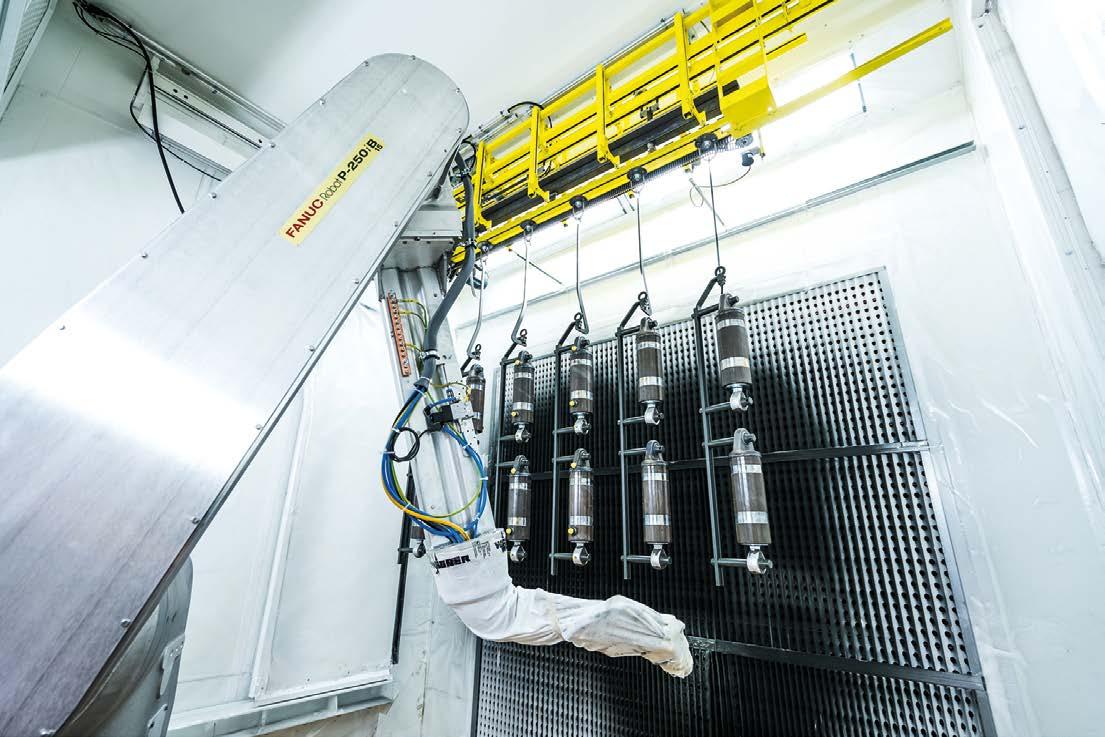
© WAGNER
Alimentazione di vernice con pompe a pistoni ad alta pressione di WAGNER.
© WAGNER