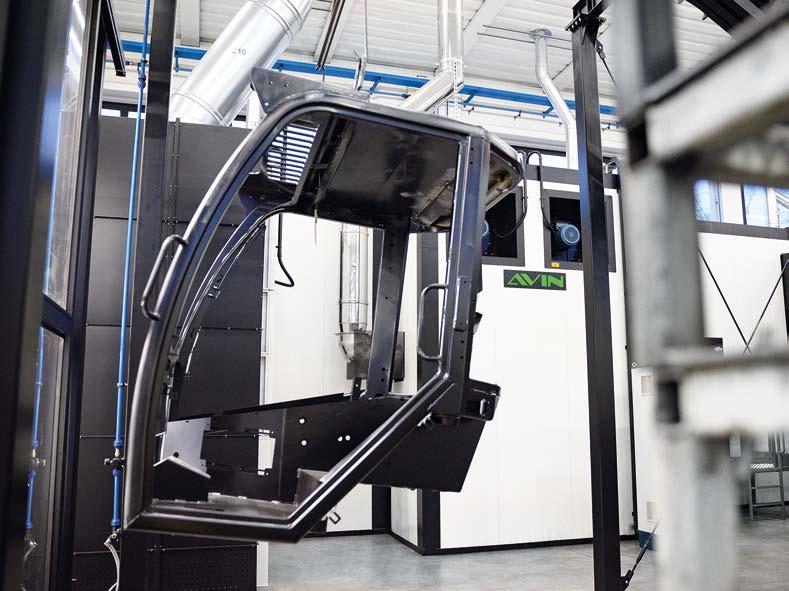
4 minute read
BUSINESS CARDS
La nuova linea ha permesso a Zoccarato di aumentare i ritmi produttivi per l’applicazione della finitura.
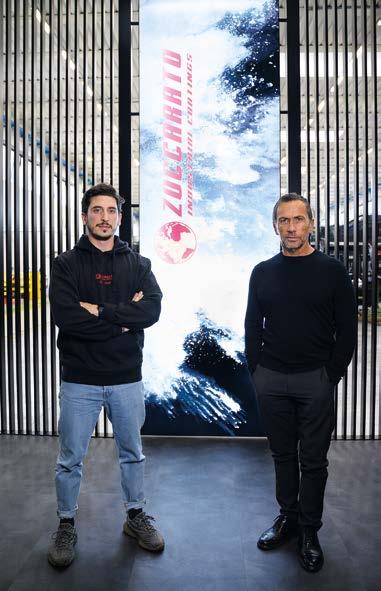
© Riccardo Sottoriva © Riccardo Sottoriva
Da sinistra, Vittorio e Alessio Zoccarato.
movimento basculante nel tunnel di pretrattamento a spruzzo composto da altre sette camere separate da porte scorrevoli dove avvengono in serie: sgrassaggio alcalino, doppio risciacquo con acqua di rete, attivazione, fosfatazione ai sali di zinco, passivazione e risciacquo finale con acqua demineralizzata. Questo pretrattamento – di cui ogni fase ha una durata di sei minuti – è stato studiato specificamente per cabine di macchine agricole e di movimento terra e altri componenti di grandi dimensioni e permette di conferire ai particolari ottime caratteristiche di adesione del film di vernice e resistenza alla corrosione. I pezzi sono poi traslati nella vasca di cataforesi con capacità di 70 m3, dove restano immersi per sei minuti e dove un sistema brevettato elimina eventuali bolle d’aria che potrebbero presentarsi su qualsiasi tipologia di articoli. A seguito della verniciatura cataforetica sono previsti due stadi di lavaggio e la cottura a 190° C nel forno di essiccazione con porte automatiche ad apertura verticale. Verniciatura di oltre 1.100 cabine a settimana
L’evoluzione di Zoccarato è sempre stata caratterizzata da investimenti volti ad aumentare i ritmi produttivi, ampliare l’offerta e migliorare la qualità dei propri servizi e ottimizzare i processi interni. L’impiego delle migliori tecnologie consente di conferire ai manufatti proprietà funzionali ed estetiche di alta qualità, ma esse richiedono anche un constate monitoraggio. “Avin si è occupata più volte della manutenzione e dell’aggiornamento dei nostri altri impianti, quindi eravamo già a conoscenza della loro professionalità e disponibilità. La scelta di affidarci a loro è stata naturale e i risultati non si sono fatti attendere: nel primo mese di avviamento abbiamo verniciato 800 cabine e oggi siamo in grado di trattare 1.100 cabine alla settimana su un solo turno lavorativo. L’impianto è inoltre strutturato per un ulteriore aumento dei volumi produttivi o per la produzione su due turni, come già avviene con gli altri impianti”, conclude soddisfatto Alessio Zoccarato.
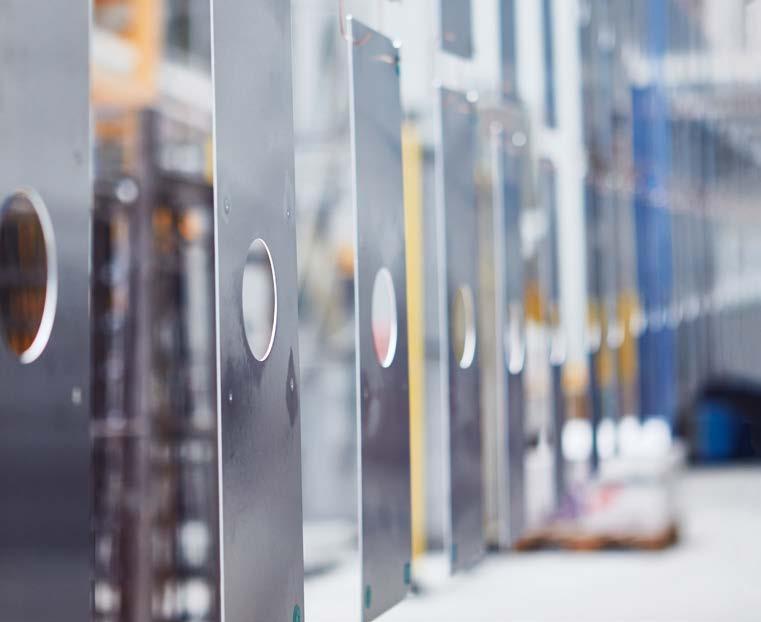
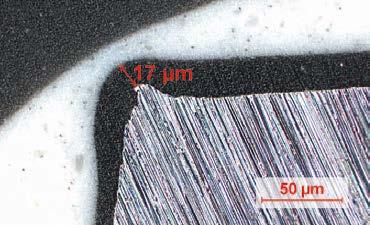

FOCUS ON TECHNOLOGY
SPECIAL ISSUE ON ACE & OFF ROAD VEHICLES
Balfor rivoluziona l’intero flusso produttivo aziendale con un nuovo impianto cartesiano di verniciatura in polvere
Gabriele Lazzari ipcm®
Grazie all’installazione di un nuovo impianto cartesiano di verniciatura in polvere manuale con un sistema di trasferimento automatico dei pezzi realizzato da Eurotherm, Balfor è ora in grado di effettuare dei cicli di verniciatura studiati su misura per ogni singolo pezzo. In questo modo l’azienda ha ottimizzato l’intero flusso produttivo e aumentato il volume di lotti verniciati, diminuendo al contempo i turni di lavoro e i consumi.
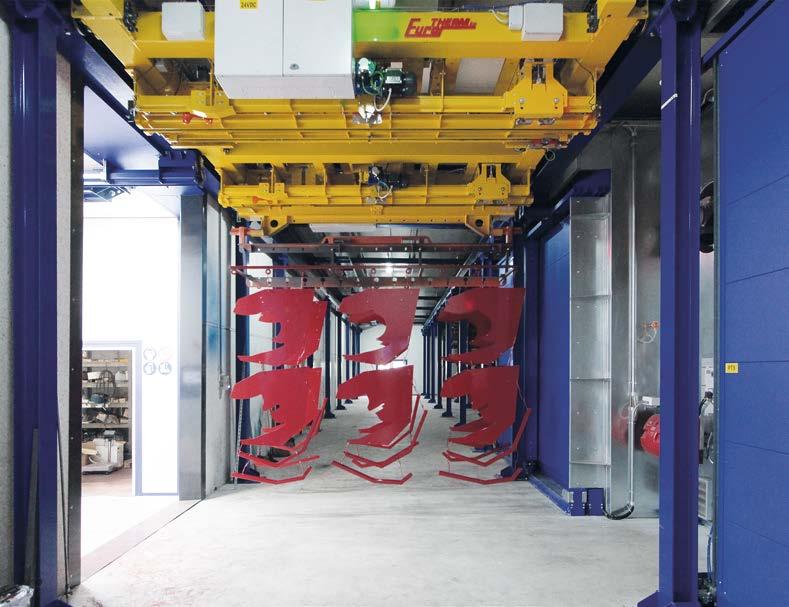
Il recente incremento del consumo globale di legna da ardere, che si attesta intorno ai 1,9 miliardi di metri cubi secondo una ricerca pubblicata dall’Organizzazione delle Nazioni Unite per l’Alimentazione e l’Agricoltura1 (FAO), ha generato anche l’aumento delle richieste per macchinari e attrezzature per il taglio della legna, sia a livello industriale sia domestico.
1 https://agriculture.ec.europa.eu/data-and-analysis/markets/overviews/market-overview-sector_en Per fronteggiare le crescenti richieste del mercato e ottimizzare il processo di verniciatura delle proprie macchine per il taglio della legna da ardere, Balfor si è perciò affidata ad Eurotherm Spa, azienda di Volpiano (TO) specializzata nella fornitura di impianti su misura per ogni necessità di verniciatura. Attraverso la gestione anche da remoto – che permette di monitorare e intervenire per modificare il processo di verniciatura – e la suddivisione in stadi del nuovo impianto di verniciatura, che le permette di adattare i cicli alle singole esigenze dei lotti e dare precedenza alle urgenze, l’azienda ha interamente rivoluzionato il proprio flusso produttivo.
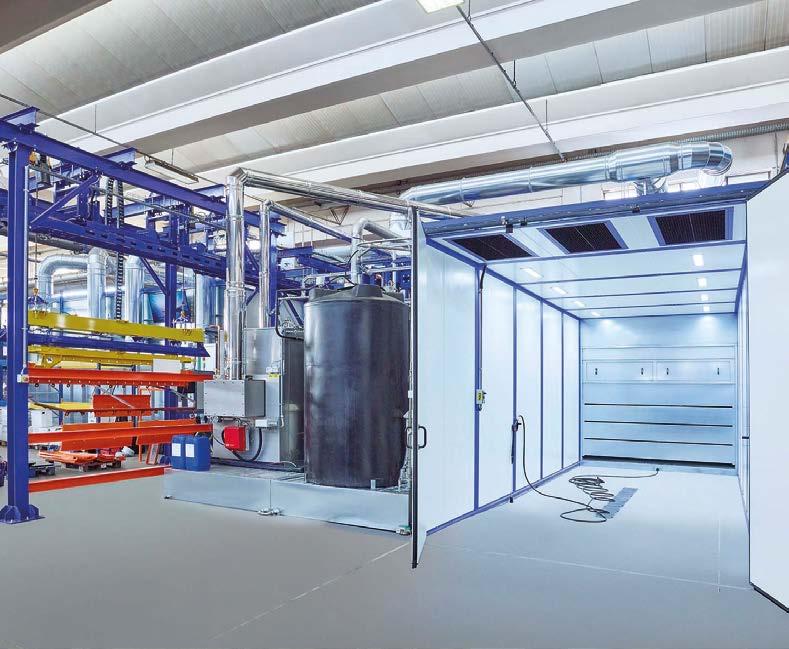
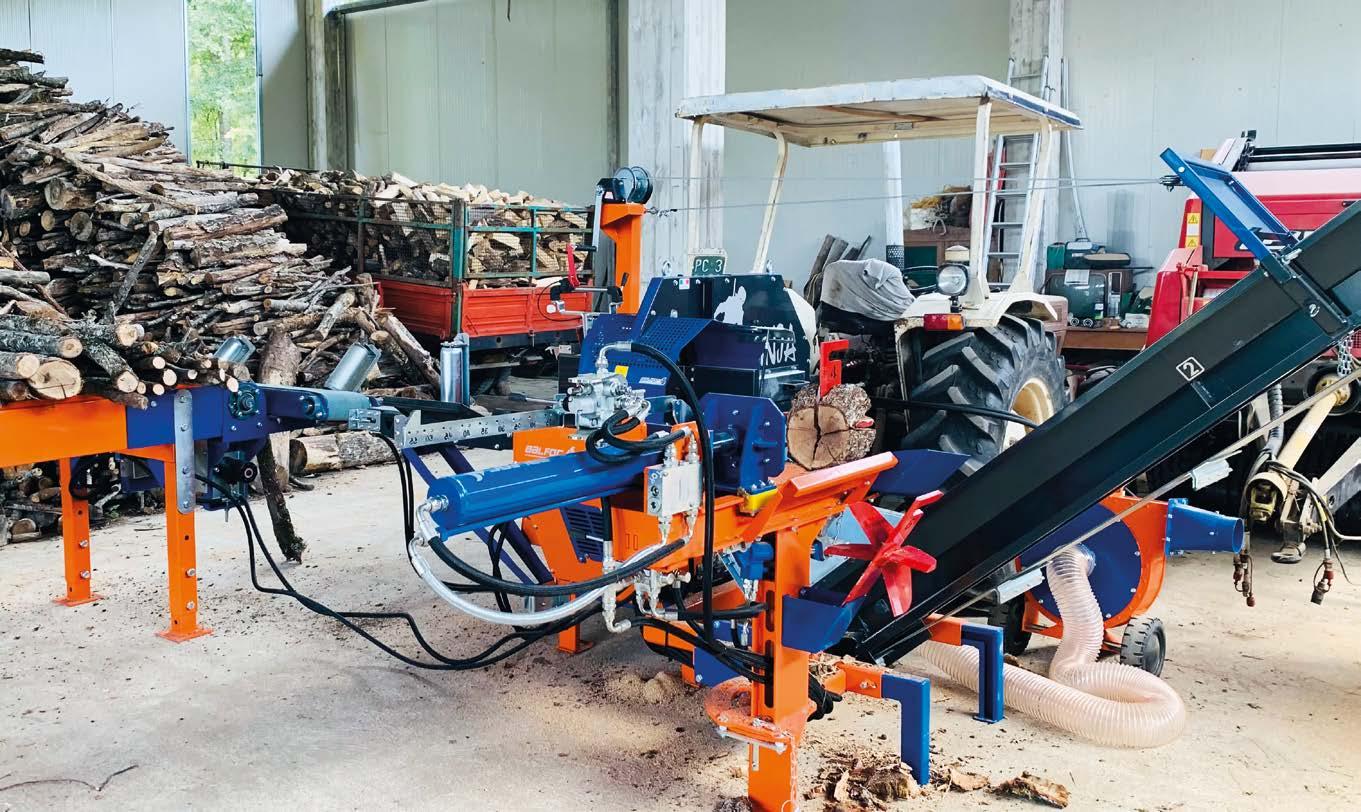
Dalla produzione artigianale all’espansione internazionale
Balfor fu fondata nel 1979 da Mario Ballario e Mario Forestello, due artigiani di Cuneo accomunati dalla passione per la realizzazione di strumenti per il taglio della legna. Inizialmente denominata Ballario e Forestello S.r.l, l’azienda con sede a Manta (CN) era specializzata nella produzione di macchinari con pistone idraulico per la lavorazione della legna da ardere. L’azienda iniziò ad espandere il proprio portfolio ad inizio anni Ottanta, includendo anche seghe circolari e a nastro, per fornire ad agricoltori e boscaioli una valida alternativa all’accetta manuale. La produzione di Ballario & Forestello si espanse poi anche all’estero, grazie ad una rete di rivenditori che si interfaccia ancora oggi direttamente con i clienti per comprenderne le specifiche necessità e progettare soluzioni su misura. “L’espansione all’estero fu un grosso incentivo alla crescita dell’azienda, che nel 1996 si trasferì in un nuovo stabilimento a Verzuolo (CN) per far fronte al crescente flusso produttivo e poi tornò a Manta nel 2008, quando ampliammo ulteriormente il nostro portfolio con impianti di grandi dimensioni per il taglio della legna da ardere e cambiammo il nome della società in Balfor S.r.l.”, esordisce Gianluca Ballario, figlio di Mario e attuale CEO di Balfor.
Macchinari per il mercato industriale e domestico
Gli oltre sessantacinque dipendenti di Balfor producono oggi macchinari e apparecchiature utilizzate per trasformare il tronco intero nei singoli ciocchi di legna da ardere, oltre a componenti dedicati ad altri strumenti agricoli.